Improve Quality & Reduce Costs: Welding Machine China Guide (2025)
Introduction: Navigating the Global Market for welding machine china
Navigating the global market for welding machines from China presents a unique set of challenges for international B2B buyers. Sourcing high-quality, reliable welding machines can be daunting, especially when considering factors such as varying standards, supplier credibility, and logistics. This guide aims to demystify the complexities involved in purchasing welding machines from China, providing actionable insights tailored specifically for buyers from regions including Africa, South America, the Middle East, and Europe, such as Argentina and the UK.
Within this comprehensive guide, we will explore various types of welding machines available in the Chinese market, their applications across different industries, and the importance of supplier vetting to ensure product quality and reliability. Additionally, we will discuss cost considerations, including pricing trends and potential hidden expenses that may arise during the procurement process. By equipping B2B buyers with essential knowledge and tools, this guide empowers them to make informed purchasing decisions, minimizing risks and maximizing value.
Understanding the intricacies of sourcing welding machines from China not only enhances operational efficiency but also strengthens competitive advantage in a rapidly evolving marketplace. With the right insights, international buyers can navigate this landscape with confidence, ensuring they secure the best solutions for their welding needs.
Understanding welding machine china Types and Variations
Type Name | Key Distinguishing Features | Primary B2B Applications | Brief Pros & Cons for Buyers |
---|---|---|---|
MIG Welding Machine | Uses a continuous wire feed; easy to use | Automotive, manufacturing, and construction | Pros: High speed, versatility. Cons: Less effective on thick materials. |
TIG Welding Machine | Provides precise control; uses tungsten electrode | Aerospace, art, and high-quality fabrication | Pros: Clean welds, suitable for thin materials. Cons: Slower process, requires skill. |
Stick Welding Machine | Simple, portable, and versatile; uses coated electrodes | Heavy industrial work, maintenance, and repair | Pros: Effective on rusty or dirty surfaces. Cons: More cleanup required post-welding. |
Multi-Process Welder | Combines MIG, TIG, and Stick capabilities | Various industries needing flexibility | Pros: All-in-one solution, adaptable. Cons: Can be more expensive and complex. |
Plasma Cutting Machine | Uses a high-velocity jet of ionized gas | Metal fabrication, automotive, and HVAC | Pros: Fast cutting speed, precise cuts. Cons: Higher operational costs, requires specific training. |
What are the Characteristics and Suitability of MIG Welding Machines?
MIG (Metal Inert Gas) welding machines are favored for their user-friendly operation and speed. They employ a continuous wire feed, making them suitable for high-volume production environments such as automotive manufacturing and construction. B2B buyers should consider the machine’s duty cycle and wire feed speed, as these factors influence productivity. While MIG welding excels in speed and versatility, it is less effective on thicker materials, making it essential to assess the specific welding requirements of your projects.
Why Choose TIG Welding Machines for Precision Work?
TIG (Tungsten Inert Gas) welding machines offer exceptional control and produce high-quality welds, making them ideal for applications in aerospace and artistic metalwork. This method requires a skilled operator, as it involves manual feeding of the filler rod and precise control of heat. Buyers should evaluate the machine’s amperage range and compatibility with various materials, especially if working with thin metals. Although TIG welding is slower than other methods, its clean results justify its use in demanding environments.
How Do Stick Welding Machines Benefit Heavy Industrial Work?
Stick welding machines are known for their portability and versatility, making them a popular choice in heavy industrial applications, maintenance, and repair work. They utilize coated electrodes, allowing for effective welding on rusty or dirty surfaces, which is often encountered in fieldwork. B2B buyers should assess the machine’s amperage settings and electrode types to ensure compatibility with their specific tasks. While stick welding is robust, it does require more cleanup after welding, which can impact overall efficiency.
What Advantages Does a Multi-Process Welder Offer?
Multi-process welders provide the flexibility to switch between MIG, TIG, and stick welding, making them an excellent investment for businesses that handle diverse projects. This adaptability is particularly useful in industries that require varied welding techniques without the need to invest in multiple machines. Buyers should consider the machine’s weight and portability, especially if mobility is necessary for their operations. Although multi-process welders can be more costly, they simplify inventory management and training.
Why Invest in Plasma Cutting Machines for Metal Fabrication?
Plasma cutting machines are designed for high-speed and precise cutting of metal, making them essential in metal fabrication and automotive industries. They utilize a high-velocity jet of ionized gas to achieve clean cuts, which can significantly reduce post-processing work. B2B buyers should look into the machine’s power requirements and cutting thickness capabilities. While plasma cutting offers speed and precision, it comes with higher operational costs and necessitates specific training for operators, which should be factored into the overall investment.
Related Video: VETRON 5064//5164 Ultrasonic Welding Machine
Key Industrial Applications of welding machine china
Industry/Sector | Specific Application of Welding Machine China | Value/Benefit for the Business | Key Sourcing Considerations for this Application |
---|---|---|---|
Automotive Manufacturing | Assembly of vehicle frames and components | Enhanced structural integrity and safety | Ensure compatibility with local standards and regulations |
Construction | Fabrication of steel structures and frameworks | Increased durability and load-bearing capacity | Look for machines that can handle various metal thicknesses |
Shipbuilding | Welding of hulls and structural components | Improved resistance to harsh marine environments | Verify machine specifications for corrosion resistance |
Oil & Gas | Pipeline construction and repair | Reliable connections in high-pressure environments | Assess the machine’s ability to operate in extreme conditions |
Aerospace | Joining of lightweight materials for aircraft parts | Reduction in weight and improved fuel efficiency | Confirm precision capabilities and certifications for aerospace standards |
How is ‘Welding Machine China’ Used in Automotive Manufacturing?
In the automotive sector, welding machines from China are extensively used for assembling vehicle frames and components. These machines facilitate the joining of various metals, ensuring that the final products meet safety and performance standards. International buyers, particularly from regions like Africa and South America, should prioritize machines that adhere to local automotive regulations and standards. Additionally, they must consider the machine’s adaptability to different vehicle designs and production scales.
What Role Does ‘Welding Machine China’ Play in Construction?
In construction, Chinese welding machines are crucial for fabricating steel structures and frameworks. They provide the necessary strength and durability required for buildings and bridges, which are subjected to significant stress. Buyers in Europe and the Middle East should focus on sourcing machines capable of handling a range of metal thicknesses and types, as well as those equipped with advanced features for efficiency and precision. Understanding the local construction codes is essential to ensure compliance.
How Are ‘Welding Machines from China’ Utilized in Shipbuilding?
In the shipbuilding industry, welding machines are employed to weld hulls and structural components, ensuring vessels are robust enough to withstand harsh marine conditions. The ability to create strong, waterproof seals is critical. Buyers, especially from coastal regions, should look for machines that demonstrate corrosion resistance and can operate effectively in maritime environments. Compatibility with various welding techniques, such as MIG and TIG, is also a key consideration.
What Applications Exist for ‘Welding Machine China’ in Oil & Gas?
In the oil and gas sector, welding machines are vital for pipeline construction and repair. They create reliable and durable connections necessary for high-pressure environments, minimizing the risk of leaks and failures. International buyers must evaluate the machine’s performance in extreme conditions, including temperature variations and corrosive environments. Additionally, sourcing machines that comply with industry safety standards is crucial for operational success.
How is ‘Welding Machine China’ Essential in Aerospace?
In aerospace manufacturing, welding machines are used to join lightweight materials for aircraft parts, significantly contributing to fuel efficiency and overall performance. Precision is paramount in this sector, as even minor defects can lead to catastrophic failures. Buyers in Europe should seek machines that meet stringent aerospace certifications and offer advanced technology for high-precision welding. Understanding the specific material requirements and tolerances is essential for successful sourcing.
Related Video: What is MIG Welding? (GMAW)
3 Common User Pain Points for ‘welding machine china’ & Their Solutions
Scenario 1: Inconsistent Quality of Welding Machines from China
The Problem:
International B2B buyers often encounter significant discrepancies in the quality of welding machines sourced from Chinese manufacturers. Many businesses invest in equipment that fails to meet industry standards, leading to operational inefficiencies and increased costs due to repairs or replacements. This inconsistency can stem from a lack of quality control during manufacturing, varied production standards among different suppliers, or miscommunication regarding specifications.
The Solution:
To mitigate the risk of receiving subpar welding machines, buyers should conduct thorough due diligence before finalizing any purchases. Start by identifying reputable manufacturers with a proven track record in the welding industry. Utilize platforms like Alibaba or Global Sources, where you can filter suppliers based on ratings, reviews, and certifications such as ISO 9001. Request samples or pilot machines to assess quality firsthand. Additionally, consider hiring third-party inspection services in China to conduct pre-shipment inspections. This proactive approach ensures that the machines meet your specific requirements and adhere to international quality standards, thus safeguarding your investment.
Scenario 2: Language Barriers Affecting Communication with Suppliers
The Problem:
Language barriers can pose significant challenges for B2B buyers when dealing with Chinese suppliers. Misunderstandings can arise regarding product specifications, delivery schedules, and payment terms, leading to delays and frustration on both sides. This situation is particularly problematic for businesses in Africa, South America, and Europe, where English may not be the primary language of communication.
The Solution:
To overcome language barriers, buyers should invest in professional translation services or use bilingual intermediaries who understand both the technical jargon and the cultural nuances of business communication. When initiating contact with suppliers, provide clear and concise specifications accompanied by diagrams or images. Utilize communication tools that facilitate real-time translation, such as WeChat, which is widely used in China. Establishing a dedicated contact person who can address queries in the buyer’s preferred language can significantly enhance communication efficiency and reduce the chances of misinterpretation.
Scenario 3: Lack of After-Sales Support and Warranty Issues
The Problem:
One of the major concerns for international buyers sourcing welding machines from China is the lack of reliable after-sales support and warranty services. When issues arise, such as equipment malfunctions or the need for replacement parts, buyers often find themselves struggling to receive timely assistance. This lack of support can severely disrupt production schedules and lead to lost revenue.
The Solution:
To address this issue, buyers should prioritize suppliers that offer robust after-sales support and clear warranty policies. Before purchasing, inquire about the availability of spare parts and the process for obtaining technical support. Establishing a contractual agreement that outlines warranty terms, response times for service requests, and penalties for non-compliance can also provide a safety net. Moreover, consider suppliers who have established local partnerships or service centers in your region, as this can greatly enhance the responsiveness of after-sales support. Regularly follow up with suppliers post-purchase to ensure they maintain their commitment to customer service, thereby fostering a reliable long-term relationship.
Strategic Material Selection Guide for welding machine china
What Are the Key Materials Used in Welding Machines from China?
When selecting welding machines from China, understanding the materials used in their construction is crucial for ensuring optimal performance and longevity. Below, we analyze four common materials: steel, aluminum, copper, and plastic composites. Each material has distinct properties, advantages, and disadvantages that can significantly impact the performance of welding machines.
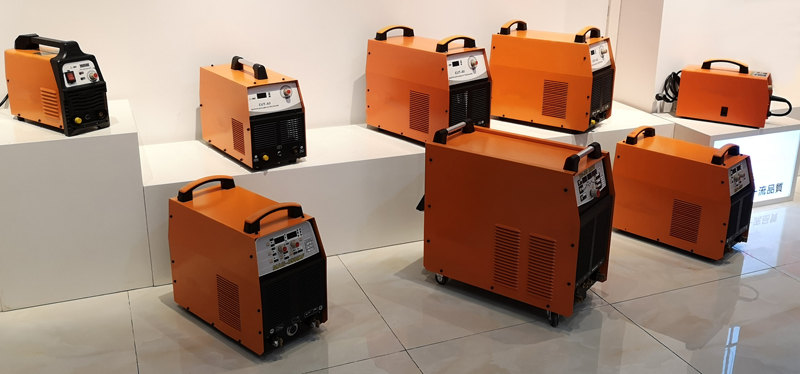
A stock image related to welding machine china.
How Does Steel Perform in Welding Machines?
Steel is one of the most widely used materials in the manufacturing of welding machines due to its high strength and durability.
- Key Properties: Steel can withstand high temperatures and pressures, making it suitable for heavy-duty applications. It also offers good corrosion resistance when treated with coatings.
- Pros & Cons: The durability of steel ensures a long lifespan, but it can be heavy and more expensive compared to other materials. Manufacturing complexity can increase due to the need for specialized welding techniques.
- Impact on Application: Steel is compatible with various welding processes, including MIG and TIG welding. It is particularly effective for structural applications in construction and manufacturing.
- Considerations for International Buyers: Buyers must ensure compliance with international standards such as ASTM and DIN. In regions like Europe and the Middle East, steel quality and certifications are critical factors in procurement.
What Advantages Does Aluminum Offer in Welding Equipment?
Aluminum is increasingly popular in welding machines due to its lightweight and corrosion-resistant properties.
- Key Properties: Aluminum has a lower melting point than steel, which allows for faster welding processes. It is also resistant to corrosion, making it ideal for outdoor applications.
- Pros & Cons: The main advantage of aluminum is its lightweight, which facilitates portability. However, it is less durable than steel and can be more expensive, particularly for high-grade alloys.
- Impact on Application: Aluminum is ideal for applications in automotive and aerospace industries, where weight savings are essential.
- Considerations for International Buyers: Buyers should be aware of the specific alloy grades and their compliance with international standards. In regions like South America, where environmental conditions may vary, aluminum’s corrosion resistance can be a significant advantage.
Why Is Copper Important in Welding Machines?
Copper is often used in the electrical components of welding machines due to its excellent conductivity.
- Key Properties: Copper has a high thermal and electrical conductivity, making it ideal for components such as cables and connectors.
- Pros & Cons: The primary advantage of copper is its efficiency in conducting electricity, which can enhance the performance of welding machines. However, it is relatively expensive and can be prone to corrosion if not properly treated.
- Impact on Application: Copper components are critical in applications requiring high power output, such as industrial welding operations.
- Considerations for International Buyers: Buyers need to consider the cost implications of copper and its susceptibility to corrosion in humid environments, particularly in regions like Africa and South America.
How Do Plastic Composites Enhance Welding Machine Design?
Plastic composites are increasingly being used in welding machines for their lightweight and versatile properties.
- Key Properties: These materials can be engineered to provide specific characteristics such as impact resistance and thermal insulation.
- Pros & Cons: Plastic composites are lightweight and can reduce manufacturing costs. However, they may not offer the same durability as metals and can be less effective in high-temperature applications.
- Impact on Application: These materials are often used in non-structural components of welding machines, such as housing and insulation.
- Considerations for International Buyers: Buyers should evaluate the specific types of plastics used and their compliance with relevant safety standards, especially in Europe where regulations are stringent.
Summary Table of Material Selection for Welding Machines
Material | Typical Use Case for welding machine china | Key Advantage | Key Disadvantage/Limitation | Relative Cost (Low/Med/High) |
---|---|---|---|---|
Steel | Structural components in heavy-duty machines | High strength and durability | Heavier and more complex to manufacture | Medium |
Aluminum | Automotive and aerospace applications | Lightweight and corrosion-resistant | Less durable and potentially more expensive | High |
Copper | Electrical components and connectors | Excellent electrical conductivity | High cost and corrosion susceptibility | High |
Plastic Composites | Non-structural components like housings | Lightweight and cost-effective | Less durable and limited high-temperature use | Low |
This guide provides a comprehensive overview of the materials used in welding machines from China, equipping international B2B buyers with the insights needed to make informed purchasing decisions.
In-depth Look: Manufacturing Processes and Quality Assurance for welding machine china
What Are the Main Stages in the Manufacturing Process of Welding Machines from China?
The manufacturing process for welding machines typically involves several critical stages, ensuring that each component meets the necessary performance and quality standards. Understanding these stages can help international B2B buyers assess the quality and reliability of their suppliers.
1. Material Preparation
The first step in manufacturing welding machines is material preparation. Raw materials such as steel, aluminum, and copper are sourced, often from local suppliers, to reduce costs and lead times. These materials undergo initial quality checks to ensure they meet specifications. B2B buyers should inquire about the origin of materials and any certifications they carry, as this can impact the machine’s overall quality.
2. Forming and Fabrication
Once the materials are prepared, they enter the forming stage. This involves cutting, bending, and machining components into their required shapes. Advanced techniques like laser cutting and CNC machining are commonly employed to achieve high precision. During this phase, it’s crucial for buyers to understand the machinery and technology used, as this directly affects the end product’s durability and performance.
3. Assembly
After fabrication, the components are assembled. This stage may involve both manual and automated processes, depending on the complexity of the welding machine. For instance, sophisticated models may require robotic arms for precise assembly. Quality assurance checks at this stage, such as visual inspections and alignment tests, help ensure that the components fit together correctly, which is vital for the machine’s performance.
4. Finishing
Finishing processes, including painting, coating, and surface treatment, enhance the welding machine’s durability and aesthetics. The application of protective coatings is crucial, especially for machines intended for harsh environments. B2B buyers should ask about the finishing processes used, as these can impact the machine’s lifespan and maintenance needs.
How is Quality Assurance Implemented in Welding Machine Manufacturing?
Quality assurance (QA) is essential in manufacturing welding machines to ensure that they meet both international standards and customer expectations. Several key components make up a robust QA process.
Relevant International Standards: What Should Buyers Know?
Manufacturers of welding machines must adhere to various international standards to ensure product quality and safety. The most common standards include:
- ISO 9001: A quality management system standard that ensures consistency in manufacturing processes.
- CE Marking: Indicates compliance with EU safety, health, and environmental protection standards.
- API Standards: Particularly relevant for machines used in the oil and gas industry, ensuring they meet specific operational requirements.
Buyers should verify that their suppliers have the necessary certifications and understand how these standards apply to their products.
What Are the Key Quality Control Checkpoints in the Manufacturing Process?
Quality control (QC) checkpoints are strategically placed throughout the manufacturing process to catch defects early. These include:
- Incoming Quality Control (IQC): At this stage, raw materials are inspected to ensure they meet specifications before production begins.
- In-Process Quality Control (IPQC): Ongoing inspections during manufacturing help identify issues in real-time, preventing defective products from proceeding to the next stage.
- Final Quality Control (FQC): Before shipping, the finished product undergoes thorough testing and inspections to ensure it meets all quality standards.
B2B buyers should request information on these QC checkpoints and the methods used to conduct inspections.
What Testing Methods Are Commonly Used for Welding Machines?
Testing methods are vital to ensure the functionality and safety of welding machines. Common testing techniques include:
- Performance Testing: Evaluates the machine’s operational capabilities under various conditions.
- Safety Testing: Ensures that the machine meets safety standards to protect operators.
- Durability Testing: Assesses the machine’s ability to withstand prolonged use without failure.
Buyers should inquire about the specific testing procedures employed by manufacturers and whether they can provide test reports.
How Can B2B Buyers Verify Supplier Quality Control?
B2B buyers can take several steps to verify the quality control processes of their suppliers in China:
1. Conducting Audits
Regular audits of manufacturing facilities can provide insights into the production processes and quality control measures in place. Buyers can assess compliance with international standards and best practices during these visits.
2. Reviewing Quality Reports
Suppliers should provide detailed quality reports that outline inspection results, testing procedures, and compliance with standards. Buyers should request these documents before finalizing orders.
3. Engaging Third-Party Inspectors
Using third-party inspection services can offer an unbiased assessment of the manufacturing processes and product quality. These inspectors can conduct thorough evaluations before shipping, ensuring that the products meet the buyer’s expectations.
What Are the Nuances of Quality Certification for International Buyers?
For international B2B buyers, especially those from Africa, South America, the Middle East, and Europe, understanding quality certification nuances is essential. Different regions may have specific requirements or preferences for certifications that impact their purchasing decisions.
- Regional Standards: Buyers should be aware of local regulations that may differ from international standards. For example, certain countries may require additional certifications for imported machinery.
- Cultural Considerations: Understanding the cultural context of suppliers can also influence negotiations and quality expectations. Building relationships based on trust and transparency can lead to better outcomes.
In conclusion, a comprehensive understanding of the manufacturing processes and quality assurance practices for welding machines from China is crucial for international B2B buyers. By focusing on these aspects, buyers can make informed decisions, ensuring they procure high-quality equipment that meets their operational needs.
Practical Sourcing Guide: A Step-by-Step Checklist for ‘welding machine china’
Introduction
Navigating the procurement of welding machines from China can be a complex process for international B2B buyers, especially those from Africa, South America, the Middle East, and Europe. This checklist serves as a practical guide to help you systematically approach sourcing, ensuring that you make informed decisions and secure high-quality equipment that meets your operational needs.
Step 1: Define Your Technical Specifications
Before initiating the sourcing process, clearly outline the technical specifications of the welding machines you require. This includes power output, welding type (MIG, TIG, arc), portability, and safety features. Having a detailed list of specifications helps narrow down potential suppliers and ensures that the machines you consider will meet your operational demands.
Step 2: Research and Identify Potential Suppliers
Utilize online platforms, trade shows, and industry directories to compile a list of reputable suppliers in China. Look for manufacturers with a strong track record, positive reviews, and a comprehensive product range. Pay attention to suppliers who specialize in exporting to your region, as they are more likely to understand your specific requirements and compliance standards.
Step 3: Evaluate Supplier Certifications and Compliance
Ensure that the suppliers you are considering have the necessary certifications, such as ISO 9001, CE, or other relevant quality and safety standards. This step is crucial as it indicates the manufacturer’s commitment to quality and compliance with international regulations. Request copies of these certifications for verification.
Step 4: Request Quotes and Compare Pricing
Contact shortlisted suppliers to request detailed quotes, including pricing, terms of delivery, and payment conditions. Comparing multiple quotes allows you to gauge the market rate and assess the value offered by each supplier. Be wary of prices that seem too good to be true; they may indicate lower quality or hidden costs.
Step 5: Conduct Due Diligence on Supplier Reputation
Investigate the reputation of each supplier by looking for reviews, testimonials, and case studies from previous clients. Engage with other businesses that have sourced similar equipment from the suppliers you are considering. This insight can reveal potential issues and provide assurance of the supplier’s reliability.
Step 6: Negotiate Terms and Conditions
Once you have identified a preferred supplier, negotiate the terms of the contract. This includes payment terms, warranties, return policies, and delivery timelines. Establishing clear expectations at this stage can prevent misunderstandings and ensure a smoother transaction process.
Step 7: Plan for Quality Control and Inspection
Before finalizing your order, consider implementing quality control measures. Arrange for an inspection of the welding machines either at the factory or upon arrival. This step is vital to confirm that the products meet your specifications and quality standards, ultimately protecting your investment.
By following these steps, you can streamline the sourcing process for welding machines from China, ensuring that you select the right supplier and equipment for your business needs.
Comprehensive Cost and Pricing Analysis for welding machine china Sourcing
What Are the Key Cost Components in Sourcing Welding Machines from China?
When sourcing welding machines from China, understanding the cost structure is essential for making informed purchasing decisions. The main components that contribute to the overall cost include:
-
Materials: The choice of materials significantly influences the price. High-quality metals and components can increase costs but result in better durability and performance.
-
Labor: Labor costs in China are generally lower than in many Western countries. However, skilled labor for specialized welding equipment can command higher wages, affecting the overall cost.
-
Manufacturing Overhead: This includes the costs associated with running the factory, such as utilities, maintenance, and administrative expenses. Efficient factories may offer competitive pricing due to lower overhead costs.
-
Tooling: The initial cost of tooling for manufacturing specific welding machines can be substantial. Custom tooling can lead to higher upfront costs, but it may be necessary for unique specifications.
-
Quality Control (QC): Implementing strict quality control measures ensures that the machines meet international standards. While this may increase costs, it can prevent future losses due to faulty equipment.
-
Logistics: Shipping costs from China to international destinations can vary widely. Factors such as distance, mode of transport, and current fuel prices will impact these logistics costs.
-
Margin: Suppliers typically add a profit margin on top of their costs. Understanding their pricing strategy can help you negotiate better terms.
How Do Price Influencers Affect the Cost of Welding Machines?
Several factors can influence the pricing of welding machines sourced from China:
-
Volume/MOQ (Minimum Order Quantity): Ordering in bulk can lead to significant discounts. Suppliers often offer lower prices per unit as the order quantity increases.
-
Specifications and Customization: Custom features or specifications can add to the base cost. Clearly defining your requirements upfront can help suppliers provide accurate quotes.
-
Materials and Quality Certifications: Machines made from higher-grade materials or those that meet specific certifications (like ISO) may come at a premium. Buyers should weigh the benefits of enhanced quality against the costs.
-
Supplier Factors: Different suppliers have varying pricing structures based on their market positioning, reputation, and experience. Researching suppliers thoroughly can reveal options that fit your budget.
-
Incoterms: The terms of shipping can affect the final cost. Understanding Incoterms like FOB (Free on Board) or CIF (Cost, Insurance, and Freight) can help you calculate total expenses accurately.
What Are the Best Negotiation Tips for International Buyers?
Effective negotiation can lead to better pricing and terms when sourcing welding machines from China. Here are several actionable tips:
-
Research and Benchmarking: Know the market rates for similar machines. This knowledge allows you to negotiate from a position of strength.
-
Leverage Relationships: Building rapport with suppliers can lead to better deals. Long-term relationships often yield benefits such as preferential pricing and priority service.
-
Discuss Total Cost of Ownership (TCO): Highlight the importance of TCO, which includes purchase price, maintenance, and operational costs. Suppliers might be more willing to negotiate on price if they see the potential for long-term business.
-
Be Clear on Specifications: Providing clear and precise specifications helps avoid misunderstandings that could lead to increased costs later on.
-
Consider Payment Terms: Negotiating favorable payment terms can improve cash flow and lessen financial strain.
What Pricing Nuances Should International Buyers Be Aware Of?
International buyers, particularly from regions like Africa, South America, the Middle East, and Europe, should be aware of several pricing nuances:
-
Currency Fluctuations: The exchange rate can significantly impact the final cost. It’s wise to monitor currency trends and potentially lock in rates with forward contracts.
-
Import Duties and Taxes: Understand the local import regulations and taxes that may apply upon receiving the equipment. These can add significantly to the total cost.
-
Shipping Delays: Unforeseen delays in shipping can increase costs. Building in buffer time in your supply chain can mitigate risks associated with late deliveries.
-
Regulatory Compliance: Ensure that the equipment meets local regulations and standards. Non-compliance can lead to additional costs for modifications or even fines.
Disclaimer on Indicative Prices
Prices for welding machines sourced from China can vary widely based on the factors discussed above. The information provided is indicative and should be used as a guideline for budgeting and planning purposes. Always request detailed quotes from suppliers to obtain accurate pricing tailored to your specific needs.
Alternatives Analysis: Comparing welding machine china With Other Solutions
When considering welding solutions, B2B buyers often face a plethora of options, including various types of welding machines, each with unique characteristics. This analysis focuses on comparing the “Welding Machine China” against two viable alternatives: MIG Welding and TIG Welding. Each method serves specific industrial needs, and understanding their distinctions can significantly influence purchasing decisions.
Comparison Aspect | Welding Machine China | MIG Welding | TIG Welding |
---|---|---|---|
Performance | High output with consistent results | Fast welding speed, suitable for thicker materials | High precision, ideal for thin materials |
Cost | Generally affordable, low initial investment | Moderate cost, with operational savings | Higher initial cost due to equipment complexity |
Ease of Implementation | Simple setup and operation | Requires some training but generally user-friendly | More complex setup, requires skilled operators |
Maintenance | Low maintenance, readily available parts | Moderate maintenance needs | High maintenance, sensitive equipment |
Best Use Case | General manufacturing and fabrication | Heavy-duty applications like automotive and shipbuilding | Aerospace, art, and thin materials |
What Are the Pros and Cons of MIG Welding?
MIG Welding (Metal Inert Gas) offers a blend of speed and ease of use, making it a popular choice for various industries. The primary advantage lies in its ability to weld thicker materials quickly, which can enhance productivity in high-volume manufacturing settings. However, the process requires a certain level of operator skill and may not provide the same level of precision as TIG welding, especially when working with thinner materials. Additionally, while the operational costs can be lower, the initial investment in quality equipment can be moderate.
How Does TIG Welding Compare in Terms of Precision?
TIG Welding (Tungsten Inert Gas) stands out for its precision and control, making it the preferred choice for applications where aesthetic quality and integrity are paramount, such as in aerospace or artistic projects. The main benefits include the ability to weld a variety of materials, including aluminum and stainless steel, with minimal distortion. On the downside, TIG welding requires highly skilled operators, and the initial equipment costs are generally higher. Maintenance can also be more demanding due to the complexity of the machinery.
Conclusion: How to Choose the Right Welding Solution?
Selecting the right welding solution hinges on understanding your specific operational requirements and budget constraints. If your projects involve general manufacturing with a focus on affordability and ease of use, a Welding Machine from China may be the best choice. However, if your applications demand speed and efficiency for thicker materials, MIG welding could be more beneficial. For projects requiring high precision and quality, particularly with thinner materials, investing in TIG welding may offer the best long-term value. By aligning your selection with your operational needs and workforce capabilities, you can ensure optimal results and efficiency in your welding operations.
Essential Technical Properties and Trade Terminology for welding machine china
What Are the Key Technical Properties of Welding Machines from China?
When sourcing welding machines from China, understanding their technical properties is crucial for making informed purchasing decisions. Here are some essential specifications to consider:
1. Material Grade
The material grade of the welding machine components, such as the frame and internal parts, directly affects durability and performance. Common materials include steel, aluminum, and plastic composites. High-grade materials ensure longevity and resistance to wear, which is particularly important for industrial applications.
2. Input Voltage and Power Rating
Welding machines come with varying input voltage specifications (e.g., 110V, 220V, or 400V) and power ratings (measured in kilowatts). It is vital to select a machine compatible with local power supply standards to avoid operational issues. A higher power rating generally translates to increased welding speed and efficiency, making it a key consideration for larger projects.
3. Duty Cycle
The duty cycle indicates the percentage of time a welding machine can operate without overheating. For instance, a machine with a 60% duty cycle can be used for 6 minutes out of every 10 minutes of operation. Understanding this property helps in selecting a machine suitable for specific workloads, ensuring that it can handle the demands of the intended applications.
4. Welding Process Compatibility
Different welding machines are designed for specific welding processes, such as MIG, TIG, or Stick welding. Buyers should assess which type of welding is most commonly used in their operations. Selecting a machine compatible with the desired welding process ensures optimal performance and quality of welds.
5. Weight and Portability
For businesses that require mobility, the weight of the welding machine is an important consideration. Lighter machines are easier to transport, while heavier models may provide more stability during operation. Understanding the balance between weight and functionality can help buyers select a machine that meets their operational needs.
What Are Common Trade Terms in the Welding Machine Industry?
Familiarity with industry-specific jargon can facilitate smoother transactions and negotiations. Here are some essential terms:
1. OEM (Original Equipment Manufacturer)
This term refers to companies that manufacture products that are sold under another company’s brand. For buyers, working with OEMs can ensure high-quality equipment and parts that meet specific standards and specifications.
2. MOQ (Minimum Order Quantity)
MOQ indicates the smallest quantity of a product that a supplier is willing to sell. Understanding MOQ is critical for budgeting and inventory management, especially for businesses looking to minimize excess stock while still meeting production needs.
3. RFQ (Request for Quotation)
An RFQ is a formal document sent to suppliers requesting pricing and other relevant details for specific products. Submitting an RFQ can help buyers compare offers from different manufacturers, ensuring they receive the best value for their investment.
4. Incoterms (International Commercial Terms)
Incoterms are standardized trade terms used in international contracts to clarify the responsibilities of buyers and sellers. Familiarity with these terms helps buyers understand shipping costs, insurance obligations, and risk management, which are crucial for international transactions.
5. Lead Time
Lead time refers to the time it takes from placing an order to receiving the product. Understanding lead times is vital for project planning and ensuring timely delivery, particularly in industries with tight deadlines.
By mastering these technical properties and trade terms, international B2B buyers can make more informed decisions when procuring welding machines from China, ultimately leading to more successful purchasing outcomes.
Navigating Market Dynamics and Sourcing Trends in the welding machine china Sector
What Are the Current Market Dynamics and Key Trends in the Welding Machine Sector?
The welding machine sector, particularly in China, is experiencing a significant transformation driven by technological advancements and global demand. International B2B buyers, especially from Africa, South America, the Middle East, and Europe, are increasingly focusing on automation and advanced welding technologies. The integration of AI and IoT in welding machines is enhancing precision and efficiency, making automated solutions more appealing. Moreover, the push for Industry 4.0 is influencing buyers to seek suppliers that offer smart manufacturing capabilities.
Another emerging trend is the growing emphasis on mobile and portable welding solutions, catering to the needs of various industries, including construction and repair services. Buyers are also favoring suppliers that provide comprehensive after-sales support and training, as this helps to ensure operational continuity and maximize the return on investment. Additionally, the rise of e-commerce platforms is simplifying the sourcing process, allowing buyers to compare products and prices more effectively.
In terms of market dynamics, the demand for welding machines is expected to rise due to increasing infrastructure projects and the expansion of manufacturing sectors in developing regions. However, buyers should be aware of fluctuating raw material prices and potential supply chain disruptions that can affect lead times and costs.
How Can International Buyers Ensure Sustainability and Ethical Sourcing in Welding Machines?
Sustainability is becoming a crucial consideration for international B2B buyers in the welding machine sector. The environmental impact of manufacturing processes is under scrutiny, prompting companies to adopt greener practices. Buyers should prioritize suppliers that adhere to sustainable manufacturing standards, which not only minimize waste and energy consumption but also enhance the overall efficiency of operations.
Ethical sourcing is equally important, as buyers are increasingly concerned about the social implications of their purchases. This includes ensuring fair labor practices and safe working conditions throughout the supply chain. Certifications such as ISO 14001 for environmental management and ISO 45001 for occupational health and safety can serve as indicators of a supplier’s commitment to ethical practices.
Moreover, the adoption of ‘green’ materials and technologies in welding processes can further support sustainability goals. Buyers should inquire about suppliers’ use of low-emission welding rods and energy-efficient machines, which can contribute to reducing the carbon footprint of their operations.
What Is the Evolution of the Welding Machine Industry in China?
The welding machine industry in China has evolved significantly over the past few decades. Initially focused on basic manufacturing, the sector has rapidly advanced to incorporate cutting-edge technologies and automation. In the early 2000s, China emerged as a global manufacturing hub, leveraging its vast labor force and resources. This growth has been fueled by increased investments in research and development, allowing Chinese manufacturers to innovate and improve the quality of their products.
Today, China is not only a major supplier of welding machines but also a leader in developing new technologies, such as robotic welding systems and smart welding solutions. This evolution has positioned Chinese manufacturers favorably in the global market, enabling them to meet the diverse needs of international B2B buyers while adhering to stricter quality and sustainability standards.
Frequently Asked Questions (FAQs) for B2B Buyers of welding machine china
-
How do I choose the right welding machine supplier from China?
Choosing the right welding machine supplier from China involves thorough research and vetting. Start by checking the supplier’s credentials, including their manufacturing certifications and industry experience. Utilize platforms like Alibaba or Global Sources to view customer reviews and ratings. Consider visiting trade shows or exhibitions to meet suppliers face-to-face and inspect their products. Additionally, request samples and assess their quality before making any large commitments. Ensuring the supplier has a reliable quality assurance process is crucial for long-term partnerships. -
What should I look for when vetting a welding machine manufacturer?
When vetting a welding machine manufacturer, focus on several key factors: production capacity, quality control processes, and compliance with international standards. Verify their certifications, such as ISO 9001, which indicates a commitment to quality management. Evaluate their experience in exporting to your region, as this can impact logistics and support. Finally, assess their customer service responsiveness and willingness to customize products according to your specific needs, which can significantly enhance your operational efficiency. -
What are the typical payment terms when sourcing welding machines from China?
Payment terms for welding machines sourced from China can vary widely, but common practices include a 30% deposit upfront and the remaining 70% before shipment. Some suppliers may offer more flexible terms such as letters of credit or payment via secure platforms like PayPal for smaller orders. It’s essential to negotiate terms that protect your interests while also being acceptable to the supplier. Ensure that all payment details are clearly outlined in the contract to avoid misunderstandings later. -
How can I ensure quality assurance when buying welding machines from China?
To ensure quality assurance when purchasing welding machines from China, establish a clear set of quality standards with the supplier before production begins. Request detailed documentation of their quality control processes, including inspections at various production stages. You might also consider hiring a third-party inspection service to verify product quality before shipment. Additionally, inquire about warranties and after-sales support, as these can be indicators of the supplier’s confidence in their product quality. -
What is the minimum order quantity (MOQ) for welding machines from Chinese suppliers?
Minimum order quantities (MOQ) for welding machines can vary significantly depending on the supplier and the specific machine type. Typically, MOQs can range from a single unit for standard models to several dozen for customized machines. It’s advisable to clarify the MOQ during the initial discussions with suppliers. If your needs require smaller quantities, look for suppliers who specialize in smaller batch production or are willing to negotiate terms based on your specific requirements. -
How do I handle logistics and shipping for welding machines sourced from China?
Handling logistics and shipping for welding machines from China involves coordinating with your supplier on the most efficient shipping method. Common options include sea freight for large shipments or air freight for smaller, urgent orders. Ensure that you understand the Incoterms agreed upon, such as FOB (Free on Board) or CIF (Cost Insurance and Freight), as they define responsibilities for shipping costs and insurance. Additionally, consider engaging a freight forwarder to assist with customs clearance and to navigate the complexities of international shipping. -
Can I customize welding machines according to my specific requirements?
Yes, many Chinese manufacturers offer customization options for welding machines. When discussing your needs, be specific about the features you require, such as voltage, power output, or additional functionalities. Ensure that the supplier has the capability to accommodate your customizations, as this can influence production timelines and costs. Keep in mind that extensive modifications may lead to higher MOQs or longer lead times, so plan accordingly to avoid disruptions in your operations. -
What are the common challenges faced by international buyers when sourcing welding machines from China?
International buyers often encounter challenges such as language barriers, cultural differences, and varying quality standards when sourcing welding machines from China. To mitigate these issues, establish clear communication channels and consider using professional translation services if needed. Additionally, familiarize yourself with Chinese business practices and negotiation styles. It’s also important to conduct thorough due diligence on suppliers to avoid fraud and ensure reliability, which can save you time and resources in the long run.
Important Disclaimer & Terms of Use
⚠️ Important Disclaimer
The information provided in this guide, including content regarding manufacturers, technical specifications, and market analysis, is for informational and educational purposes only. It does not constitute professional procurement advice, financial advice, or legal advice.
While we have made every effort to ensure the accuracy and timeliness of the information, we are not responsible for any errors, omissions, or outdated information. Market conditions, company details, and technical standards are subject to change.
B2B buyers must conduct their own independent and thorough due diligence before making any purchasing decisions. This includes contacting suppliers directly, verifying certifications, requesting samples, and seeking professional consultation. The risk of relying on any information in this guide is borne solely by the reader.
Strategic Sourcing Conclusion and Outlook for welding machine china
In the competitive landscape of welding machinery, strategic sourcing remains a cornerstone for international B2B buyers seeking to optimize their procurement processes. By leveraging China’s robust manufacturing capabilities, companies from Africa, South America, the Middle East, and Europe can access high-quality welding machines at competitive prices. It is essential to conduct thorough market research to identify reliable suppliers and assess their compliance with international standards.
What are the key factors to consider when sourcing welding machines from China? Buyers should prioritize factors such as supplier reputation, product certifications, and after-sales support. Engaging in trade shows like WELDING KOREA + AUTOMATION can provide invaluable networking opportunities and insights into the latest technologies and trends in the welding industry.
Looking ahead, the demand for innovative and efficient welding solutions is expected to rise. As industries continue to evolve, buyers must remain agile and proactive in their sourcing strategies. Embrace the opportunity to collaborate with Chinese manufacturers to enhance operational efficiency and product quality. Now is the time to act—invest in strategic sourcing to stay ahead in the welding machine market and drive your business growth in the coming years.