Improve Quality: The Ultimate Envelope Manufacturer Guide (2025)
Introduction: Navigating the Global Market for envelope manufacturer
In today’s interconnected world, sourcing high-quality envelopes can present significant challenges for B2B buyers, particularly those operating across diverse markets in Africa, South America, the Middle East, and Europe. Understanding the nuances of the global envelope manufacturing landscape is crucial for making informed purchasing decisions. This comprehensive guide delves into various types of envelopes, their applications, and the critical factors to consider when vetting suppliers. From eco-friendly options to specialized formats for direct mail campaigns, our guide offers insights tailored to meet the unique needs of international buyers.
Navigating the complexities of cost structures, production timelines, and regulatory compliance can be daunting, especially when entering new markets. This guide empowers B2B buyers by providing actionable strategies for evaluating suppliers, understanding pricing models, and ensuring quality control throughout the procurement process. By addressing key concerns such as sustainability, material sourcing, and technological advancements in manufacturing, buyers can optimize their purchasing strategies and align them with their operational goals.
Whether you are based in Egypt, Poland, or any other global hub, this guide serves as an essential resource for making strategic decisions in envelope procurement. Equip yourself with the knowledge necessary to streamline your supply chain and enhance your business communications, ensuring that your envelope needs are met with precision and reliability.
Understanding envelope manufacturer Types and Variations
Type Name | Key Distinguishing Features | Primary B2B Applications | Brief Pros & Cons for Buyers |
---|---|---|---|
Standard Envelope Manufacturers | Produce common envelope sizes and styles, such as #10, A4, and C5. | Office supplies, direct mail, invoices | Pros: Widely available, cost-effective. Cons: Limited customization options. |
Custom Envelope Manufacturers | Offer bespoke designs, sizes, and finishes tailored to specific needs. | Branding materials, promotional items | Pros: High customization, unique branding. Cons: Higher costs, longer lead times. |
Eco-Friendly Envelope Manufacturers | Focus on sustainable materials and production methods. | Green business practices, eco-conscious marketing | Pros: Appeals to environmentally aware customers. Cons: Potentially higher prices. |
Specialty Envelope Manufacturers | Create unique envelopes for specific uses, like security or padded envelopes. | Legal documents, sensitive materials, shipping | Pros: Enhanced protection, specific functionality. Cons: May not be suitable for general use. |
Digital Envelope Manufacturers | Utilize digital printing technology for small runs and personalized envelopes. | E-commerce, personalized marketing campaigns | Pros: Quick turnaround, variable data printing. Cons: Higher cost per unit for small orders. |
What Are the Characteristics of Standard Envelope Manufacturers?
Standard envelope manufacturers are the backbone of the envelope industry, producing widely used sizes and styles like #10, A4, and C5. They cater primarily to businesses looking for bulk purchases of generic envelopes for everyday office use, such as invoices and direct mail. When considering these manufacturers, B2B buyers should weigh the benefits of cost-efficiency against the limited customization options available, making them ideal for companies that prioritize budget over branding.
How Do Custom Envelope Manufacturers Differ from Others?
Custom envelope manufacturers specialize in tailoring products to meet specific client needs, offering a wide range of designs, sizes, and finishes. This type of manufacturer is particularly beneficial for businesses looking to enhance their branding through unique envelopes for promotional items or corporate communications. However, buyers should be prepared for potentially higher costs and longer lead times, which could impact project timelines.
What Should B2B Buyers Know About Eco-Friendly Envelope Manufacturers?
Eco-friendly envelope manufacturers prioritize sustainability, using recycled materials and environmentally friendly production processes. This type of manufacturer appeals to businesses committed to green practices and those looking to enhance their corporate social responsibility. While the initial costs may be higher, the long-term benefits include improved brand reputation and customer loyalty among environmentally conscious consumers.
When to Choose Specialty Envelope Manufacturers?
Specialty envelope manufacturers focus on producing envelopes designed for specific applications, such as security envelopes or padded envelopes for shipping. These products are essential for businesses that handle sensitive documents or require extra protection for their shipments. Buyers should consider the specific needs of their operations, as these envelopes provide enhanced functionality, although they may not be suitable for general use.
What Are the Advantages of Digital Envelope Manufacturers?
Digital envelope manufacturers leverage advanced printing technologies to produce small runs of personalized envelopes quickly. This approach is particularly advantageous for e-commerce businesses and marketing campaigns that require variable data printing for targeted outreach. While the cost per unit may be higher for small orders, the benefits of rapid turnaround and customization can outweigh the expenses, especially for campaigns needing immediate execution.
Related Video: Types of Contracts • Different Contracts Explained
Key Industrial Applications of envelope manufacturer
Industry/Sector | Specific Application of Envelope Manufacturer | Value/Benefit for the Business | Key Sourcing Considerations for this Application |
---|---|---|---|
Financial Services | Secure Document Delivery Envelopes | Ensures confidentiality and security of sensitive documents | Customization options for branding and security features |
E-commerce | Shipping and Packaging Envelopes | Cost-effective shipping solutions that enhance customer experience | Durability and weight considerations for shipping costs |
Education | Admission and Notification Envelopes | Professional presentation of important documents to students | Options for bulk orders and quick turnaround times |
Government | Official Correspondence Envelopes | Compliance with legal standards for document handling | Need for specific sizes and materials for official use |
Marketing & Advertising | Promotional Envelopes for Direct Mail | Increased engagement through eye-catching designs | Flexibility in design and print options for branding |
How Do Envelope Manufacturers Serve the Financial Services Sector?
In the financial services industry, secure document delivery envelopes are crucial for maintaining confidentiality. These envelopes are designed to protect sensitive documents such as bank statements, tax forms, and legal notices from unauthorized access. International B2B buyers, particularly from regions like Africa and Europe, should consider sourcing envelopes that offer customization options, including tamper-evident seals and unique branding features to enhance security and trust.
What Role Do Envelopes Play in E-commerce Shipping Solutions?
E-commerce businesses rely heavily on shipping and packaging envelopes for cost-effective delivery solutions. These envelopes not only protect products during transit but also contribute to a positive customer experience when receiving their orders. Buyers from South America and the Middle East should focus on the durability and weight of the envelopes to optimize shipping costs while ensuring that products arrive in excellent condition.
Why Are Envelopes Important in the Education Sector?
In the education sector, admission and notification envelopes are essential for presenting important documents to students and parents. These envelopes ensure that communications, such as acceptance letters and exam results, are delivered professionally. For international buyers, especially in Europe, it is important to consider options for bulk orders and quick turnaround times to meet academic deadlines and ensure timely communication.
How Do Government Agencies Utilize Envelopes?
Government agencies utilize official correspondence envelopes to comply with legal standards for document handling. These envelopes often need to meet specific requirements regarding size, material, and security features. Buyers from Africa and the Middle East should prioritize sourcing envelopes that align with governmental regulations, ensuring that they convey professionalism and trustworthiness in official communications.
How Can Promotional Envelopes Enhance Marketing Efforts?
Promotional envelopes used for direct mail campaigns can significantly increase engagement rates with potential customers. By utilizing eye-catching designs and high-quality materials, businesses can capture attention and drive response rates. B2B buyers from Europe should look for flexibility in design and print options when sourcing promotional envelopes, enabling them to create unique marketing materials that reflect their brand identity effectively.
Related Video: Uses and Gratifications Theory
3 Common User Pain Points for ‘envelope manufacturer’ & Their Solutions
Scenario 1: Inconsistent Quality of Envelopes
The Problem: One of the most pressing challenges faced by B2B buyers when sourcing envelopes is the inconsistency in quality. For businesses, especially those in sectors like finance or legal services, using high-quality envelopes is essential for maintaining a professional image. However, many manufacturers offer products that fail to meet the specified standards, resulting in envelopes that tear easily, have poor adhesive properties, or exhibit discoloration. This inconsistency not only affects the packaging but can also lead to reputational damage if clients receive subpar materials.
The Solution: To mitigate this issue, buyers should prioritize sourcing envelopes from manufacturers who provide samples before making large orders. Requesting samples allows businesses to evaluate the material, durability, and overall quality of the envelopes firsthand. Additionally, buyers should look for manufacturers with ISO certifications or other quality assurance processes in place. Establishing a clear communication channel with the manufacturer about quality expectations can further ensure the product meets the required standards. Regular quality checks and audits on bulk orders can also help in maintaining consistency, ensuring that the envelopes delivered align with the promised specifications.
Scenario 2: Delays in Delivery Times
The Problem: Timely delivery is crucial in the B2B sector, and delays in envelope manufacturing can disrupt entire supply chains. Buyers often face the frustration of waiting for their orders to arrive when they have urgent deadlines to meet, such as sending out invitations for a corporate event or fulfilling client contracts. These delays can stem from various factors, including production bottlenecks, logistical issues, or miscommunication between the buyer and the manufacturer.
The Solution: To avoid such delays, B2B buyers should conduct thorough research on potential manufacturers’ delivery timelines and reliability. Engaging with manufacturers who have a proven track record of meeting deadlines is essential. It is advisable to set clear expectations regarding delivery timelines during the initial negotiation phase and to include penalties for late deliveries in contracts. Additionally, buyers can explore the option of establishing a buffer stock with manufacturers to ensure that they always have a supply of envelopes on hand, allowing for more flexibility in case of unexpected demand.
Scenario 3: Limited Customization Options
The Problem: Many B2B buyers require customized envelopes that align with their branding, including specific sizes, colors, and printing options. However, not all envelope manufacturers offer a wide range of customization options, leading to frustration for buyers who wish to present their brand professionally. This limitation can force businesses to compromise on their branding or settle for generic solutions that do not meet their needs.
The Solution: To address this pain point, buyers should seek out envelope manufacturers who specialize in custom orders. When communicating with potential suppliers, it is vital to inquire about the range of customization options available, including different materials, sizes, and printing capabilities. Buyers should also ask for a portfolio or examples of previous custom work to assess the manufacturer’s capability. Building a partnership with a manufacturer that understands branding and design can also enhance the customization process. Establishing a collaborative approach where the buyer can provide input during the design phase can lead to a final product that truly reflects the company’s identity.
Strategic Material Selection Guide for envelope manufacturer
When selecting materials for envelope manufacturing, international B2B buyers must consider several factors that impact product performance, cost, and compliance with regional standards. Below is an analysis of four common materials used in envelope production, focusing on their properties, advantages, disadvantages, and specific considerations for buyers in Africa, South America, the Middle East, and Europe.
What Are the Key Properties of Paper in Envelope Manufacturing?
Paper is the most traditional material used in envelope manufacturing. It is characterized by its lightweight nature and versatility. Key properties include:
- Weight and Thickness: Commonly available in various weights (e.g., 70-120 gsm), affecting durability and feel.
- Surface Finish: Options like smooth, textured, or glossy can enhance printability and aesthetics.
- Environmental Impact: Many paper types are recyclable and biodegradable, appealing to environmentally conscious consumers.
Pros & Cons:
– Advantages: Cost-effective, easy to print on, and widely available. It can be produced from recycled materials, appealing to sustainability-focused markets.
– Disadvantages: Limited moisture resistance and durability compared to synthetic materials. It may not withstand harsh conditions during shipping.
Impact on Application: Paper envelopes are suitable for lightweight items such as letters and documents. However, they may not be ideal for shipping items that require higher protection.
How Do Plastic Materials Enhance Envelope Durability?
Plastic materials, such as polyethylene and polypropylene, are increasingly used in envelope manufacturing. Their key properties include:
- Water Resistance: Excellent moisture barrier properties, protecting contents from environmental factors.
- Durability: High tensile strength and tear resistance, making them suitable for heavy or bulky items.
Pros & Cons:
– Advantages: Long-lasting and suitable for various applications, including mailing items that require extra protection. They are also lightweight, which can reduce shipping costs.
– Disadvantages: Higher production costs and potential environmental concerns regarding plastic waste.
Impact on Application: Plastic envelopes are ideal for sending items that are sensitive to moisture or require enhanced protection, such as photographs, documents, or small products.
What Are the Benefits of Using Kraft Paper for Envelopes?
Kraft Paper is a strong and durable material made from wood pulp. It is known for its natural brown color and robust properties. Key properties include:
- Strength: High tear resistance and ability to hold heavier contents.
- Sustainability: Often made from recycled materials and fully recyclable.
Pros & Cons:
– Advantages: Cost-effective and environmentally friendly. It provides a rustic appearance that appeals to certain markets.
– Disadvantages: Limited color options and less formal appearance compared to coated papers.
Impact on Application: Kraft paper envelopes are suitable for shipping heavier items, such as catalogs or promotional materials, and are favored in eco-conscious markets.
How Does Tyvek® Material Improve Envelope Security?
Tyvek® is a synthetic material made from high-density polyethylene fibers. Its properties include:
- Lightweight Yet Strong: Offers superior strength while remaining lightweight.
- Water and Tear Resistance: Provides excellent protection against moisture and tearing.
Pros & Cons:
– Advantages: Highly durable and resistant to wear, making it ideal for shipping valuable items. It can also be printed on, allowing for branding opportunities.
– Disadvantages: Higher cost compared to traditional paper materials and limited biodegradability.
Impact on Application: Tyvek® envelopes are perfect for sending important documents, contracts, or sensitive materials that require extra security during transit.
Summary Table of Material Selection for Envelope Manufacturing
Material | Typical Use Case for envelope manufacturer | Key Advantage | Key Disadvantage/Limitation | Relative Cost (Low/Med/High) |
---|---|---|---|---|
Paper | Letters and documents | Cost-effective and widely available | Limited moisture resistance | Low |
Plastic | Moisture-sensitive items | Excellent durability and water resistance | Higher production costs | Med |
Kraft Paper | Shipping catalogs and promotional materials | Environmentally friendly and strong | Limited color options | Low |
Tyvek® | Important documents and sensitive materials | Highly durable and tear-resistant | Higher cost and limited biodegradability | High |
By understanding the properties and implications of these materials, international B2B buyers can make informed decisions that align with their product requirements and regional standards.
In-depth Look: Manufacturing Processes and Quality Assurance for envelope manufacturer
What Are the Main Stages in the Manufacturing Process of Envelopes?
The manufacturing of envelopes involves several critical stages, each contributing to the final quality of the product. Understanding these stages helps international B2B buyers assess potential suppliers effectively.
Material Preparation: What Materials Are Used in Envelope Manufacturing?
The first step in envelope production is material preparation, which typically involves selecting the right paper or specialty materials. Common materials include:
- Paper Types: Most envelopes are made from various grades of paper, including recycled, kraft, and specialty papers designed for durability and aesthetic appeal.
- Adhesives: Depending on the envelope type (self-sealing, gummed), different adhesives are used to ensure a secure closure.
- Printing Inks: For custom branding, high-quality printing inks are selected to maintain color integrity and vibrancy.
Quality control begins at this stage, as the right materials are essential for producing envelopes that meet international standards.
Forming: How Are Envelopes Shaped and Structured?
The forming stage is where raw materials are transformed into envelope shapes. This process includes:
- Cutting: Sheets of paper are cut to the desired size using precision cutting machines. This step is crucial for ensuring uniformity in size.
- Folding: Automated folding machines create the envelope’s flaps, ensuring consistent angles and alignment.
- Gluing: For envelopes requiring adhesive, this step applies glue to the appropriate areas, which is critical for maintaining structural integrity.
Advanced technology, such as die-cutting and laser cutting, can also be used to create custom shapes or features, enhancing product offerings for B2B buyers.
Assembly: What Techniques Are Used in Envelope Assembly?
The assembly stage is where the individual components come together. Techniques include:
- Automated Assembly Lines: High-speed assembly lines can produce thousands of envelopes per hour, increasing efficiency and reducing labor costs.
- Quality Checks: Inline quality checks (IPQC) are performed to ensure that each envelope meets design specifications before moving to the next stage.
B2B buyers should inquire about the assembly technology used by suppliers to ensure they can meet volume and customization requirements.
Finishing: How Do Finishing Processes Impact Envelope Quality?
Finishing processes enhance the envelope’s appearance and functionality. This includes:
- Printing: Custom printing can include logos, designs, or information, using techniques like offset or digital printing.
- Lamination and Coating: Some envelopes undergo lamination for added durability or special coatings for aesthetic purposes.
- Packaging: Final packaging ensures that envelopes are delivered in pristine condition, ready for distribution.
What Quality Assurance Standards Should B2B Buyers Look For?
Quality assurance is critical in maintaining product integrity and compliance with international standards. Here are key aspects to consider:
What International Standards Apply to Envelope Manufacturing?
- ISO 9001: This standard focuses on quality management systems and is essential for ensuring consistent quality in manufacturing processes.
- CE Marking: For products sold in the European Economic Area, CE marking indicates conformity with health, safety, and environmental protection standards.
- API Standards: In specific cases where envelopes are used for sensitive documents, adhering to API standards may be necessary.
Buyers should verify that their suppliers possess relevant certifications, indicating compliance with these standards.
What Are the Key Quality Control Checkpoints in Envelope Production?
Quality control checkpoints are integral to the manufacturing process. Common checkpoints include:
- Incoming Quality Control (IQC): This involves inspecting raw materials upon arrival to ensure they meet specifications.
- In-Process Quality Control (IPQC): During manufacturing, regular checks are conducted to catch defects early, reducing waste and rework.
- Final Quality Control (FQC): Before packaging, a final inspection ensures that envelopes meet all specifications and quality standards.
Each checkpoint plays a vital role in minimizing defects and ensuring customer satisfaction.
How Can B2B Buyers Verify Supplier Quality Control Practices?
For international B2B buyers, verifying a supplier‘s quality control practices is crucial to ensuring product reliability. Here are effective methods:
What Are the Best Practices for Conducting Supplier Audits?
- On-site Audits: Visiting the manufacturing facility allows buyers to assess processes, equipment, and quality control measures firsthand.
- Third-Party Inspections: Engaging third-party inspection services can provide unbiased evaluations of a supplier’s quality control processes.
- Reviewing Quality Reports: Suppliers should provide detailed quality reports and metrics, including defect rates and compliance certifications.
These practices help mitigate risks associated with poor quality and ensure that the supplier can meet the buyer’s needs.
What Are the Common Testing Methods Used in Envelope Quality Control?
Testing methods vary based on the intended use of the envelopes. Common tests include:
- Burst Strength Testing: Measures the pressure an envelope can withstand before bursting, ensuring it can handle contents securely.
- Seal Integrity Testing: Ensures that adhesive seals maintain their integrity under various conditions, preventing accidental openings.
- Print Durability Testing: Evaluates how well printed designs withstand wear and tear, especially important for branded envelopes.
B2B buyers should ask suppliers about their specific testing methods and the results of such tests to ensure product reliability.
How Do Quality Control Nuances Affect International B2B Buyers?
For international B2B buyers, understanding the nuances of quality control can significantly impact purchasing decisions:
- Cultural Differences: Quality expectations may vary by region, so understanding local standards and practices is essential.
- Regulatory Compliance: Different countries have unique regulations that can affect product specifications, necessitating thorough checks on compliance.
- Logistics Considerations: Quality control processes may differ based on shipping methods, making it vital to align with suppliers on logistics and quality expectations.
By being informed about these aspects, B2B buyers can make better decisions and foster stronger partnerships with envelope manufacturers globally.
Practical Sourcing Guide: A Step-by-Step Checklist for ‘envelope manufacturer’
When sourcing an envelope manufacturer, it is essential to follow a systematic approach to ensure you select a reliable partner that meets your business needs. This step-by-step checklist will guide international B2B buyers from regions such as Africa, South America, the Middle East, and Europe through the crucial phases of the sourcing process.
Step 1: Define Your Technical Specifications
Clearly outline the specific requirements for the envelopes you need, including dimensions, materials, and printing options. This step is vital as it helps streamline communication with potential suppliers and ensures that you receive accurate quotes. Consider factors such as:
– Material: Do you need recycled paper, kraft, or premium options?
– Size Variations: What sizes do you require (e.g., A4, C5, custom sizes)?
Step 2: Research Potential Suppliers
Conduct thorough research to identify envelope manufacturers that operate in your target regions. Utilize online B2B marketplaces, industry directories, and trade shows to compile a list of potential suppliers. Pay attention to:
– Experience: Look for manufacturers with a proven track record in producing envelopes.
– Market Presence: Consider suppliers with a strong reputation in your specific geographic area.
Step 3: Evaluate Supplier Capabilities
Before committing, it’s crucial to vet suppliers thoroughly. Request company profiles, case studies, and references from buyers in similar industries or regions. Key aspects to assess include:
– Production Capacity: Ensure the supplier can meet your volume requirements.
– Technology and Equipment: Check if they use modern machinery that can handle your specifications.
Step 4: Verify Compliance and Certifications
Ensure that potential suppliers comply with international quality standards and regulations. This step is important to mitigate risks associated with product quality and legality. Look for:
– ISO Certifications: Such as ISO 9001, which indicates a commitment to quality management.
– Environmental Compliance: Certifications like FSC or PEFC for sustainable sourcing.
Step 5: Request Samples
Always request samples before finalizing your order. This allows you to assess the quality of the envelopes firsthand. When evaluating samples, focus on:
– Material Quality: Check the thickness, texture, and overall feel.
– Printing Quality: Ensure that the printing aligns with your design expectations.
Step 6: Discuss Pricing and Terms
Engage in discussions about pricing, payment terms, and delivery schedules. This step is critical to establishing a mutually beneficial agreement. Consider:
– Bulk Discounts: Inquire about pricing tiers based on order volumes.
– Payment Flexibility: Understand their payment terms, such as upfront deposits versus payment upon delivery.
Step 7: Establish a Communication Plan
Once you select a supplier, set up a clear communication plan to ensure smooth collaboration throughout the production process. This includes:
– Regular Updates: Agree on how often you will receive updates regarding production status.
– Point of Contact: Designate a specific person from both sides to streamline communication.
By following this checklist, B2B buyers can effectively navigate the complexities of sourcing an envelope manufacturer, ensuring a successful partnership that meets their business objectives.
Comprehensive Cost and Pricing Analysis for envelope manufacturer Sourcing
Understanding the cost structure and pricing dynamics of envelope manufacturing is crucial for international B2B buyers, especially those from regions like Africa, South America, the Middle East, and Europe. A comprehensive analysis can empower buyers to make informed decisions and negotiate effectively.
What Are the Key Cost Components in Envelope Manufacturing?
When evaluating the cost structure of envelope manufacturing, several critical components come into play:
-
Materials: The primary material for envelopes is paper, which can vary in quality, weight, and type (e.g., recycled, kraft, or specialty paper). The choice of material significantly impacts the overall cost. Specialty materials or environmentally friendly options typically incur higher costs.
-
Labor: Labor costs are influenced by the local wage rates in the manufacturing country. In regions with higher labor costs, such as parts of Europe, manufacturers may pass these costs on to buyers. Conversely, sourcing from countries with lower labor costs might offer more competitive pricing.
-
Manufacturing Overhead: This includes expenses related to running the factory, such as utilities, rent, and equipment maintenance. Overhead costs can vary widely depending on the efficiency of the manufacturing process and the technology employed.
-
Tooling: Custom tooling for specific envelope sizes or styles can be a significant upfront investment. This cost is often amortized over the production run, so larger orders can result in lower per-unit costs.
-
Quality Control (QC): Ensuring product quality is vital, especially for buyers requiring specific certifications. QC processes add to the overall cost but are essential for maintaining standards and minimizing defects.
-
Logistics: Shipping costs can vary dramatically based on distance, shipping method, and Incoterms. For international buyers, understanding these costs is crucial, as they can affect the total cost of ownership.
-
Margin: Manufacturers typically add a profit margin to cover their risks and ensure profitability. This margin can vary based on market competition and the perceived value of the product.
How Do Pricing Influencers Affect Envelope Costs?
Several factors influence the pricing of envelopes that B2B buyers should consider:
-
Volume/MOQ (Minimum Order Quantity): Higher order volumes typically lead to lower per-unit costs due to economies of scale. Negotiating favorable terms for bulk purchases can yield significant savings.
-
Specifications and Customization: Custom sizes, colors, or printing requirements can increase costs. Buyers should weigh the benefits of customization against the additional expenses.
-
Material Quality and Certifications: Higher-quality materials or certifications (e.g., FSC certification for sustainable sourcing) can raise costs. Buyers must assess the necessity of these features for their end-use.
-
Supplier Factors: The reputation and reliability of suppliers can influence pricing. Established manufacturers may charge a premium for their proven track record, while newer suppliers might offer lower prices to gain market share.
-
Incoterms: Understanding the implications of different Incoterms can affect the total landed cost. Terms like FOB (Free on Board) or CIF (Cost, Insurance, and Freight) can shift responsibilities and costs between buyers and suppliers.
What Are the Best Buyer Tips for Sourcing Envelopes Internationally?
-
Negotiate Wisely: Leverage volume commitments and long-term relationships to negotiate better pricing. Be clear about your needs and explore multiple supplier options to enhance bargaining power.
-
Focus on Cost-Efficiency: Analyze the total cost of ownership rather than just the purchase price. Consider logistics, potential tariffs, and long-term reliability when evaluating supplier offers.
-
Understand Pricing Nuances: Be aware that prices may fluctuate based on market conditions, material availability, and regional economic factors. Stay informed about market trends to anticipate changes.
-
Establish Clear Specifications: Providing detailed specifications can help suppliers give more accurate quotes, reducing the risk of unexpected costs later in the process.
-
Consider Local Suppliers: When possible, explore local manufacturers to reduce logistics costs and improve turnaround times, particularly if they can meet your quality standards.
Disclaimer on Indicative Prices
It’s important to note that prices for envelope manufacturing can vary significantly based on the factors mentioned above. Buyers should seek quotes from multiple suppliers and conduct thorough due diligence to ensure they are getting the best value for their specific needs.
Alternatives Analysis: Comparing envelope manufacturer With Other Solutions
When evaluating the options available for businesses in need of envelope solutions, understanding the alternatives to traditional envelope manufacturing is crucial. Various methods and technologies can provide similar functionalities, catering to different business needs, budgets, and operational efficiencies. This analysis will compare envelope manufacturers with two viable alternatives: digital document solutions and custom packaging services.
Comparison Table
Comparison Aspect | Envelope Manufacturer | Digital Document Solutions | Custom Packaging Services |
---|---|---|---|
Performance | High-quality, durable envelopes tailored for various uses | Efficient for digital communication, no physical product | Custom designs enhance branding and protection |
Cost | Moderate initial investment, bulk pricing available | Low to moderate depending on software and usage | Higher cost due to customization and materials |
Ease of Implementation | Requires setup of manufacturing processes | Quick setup with software; training may be needed | Moderate; requires design input and order processing |
Maintenance | Low; ongoing material supply needed | Software updates and maintenance | Regularly requires design adjustments and material sourcing |
Best Use Case | Bulk mailing, physical correspondence | E-documents, invoices, and newsletters | Unique branding needs, product shipping |
What Are the Benefits and Drawbacks of Digital Document Solutions?
Digital document solutions represent a modern approach to communication, allowing businesses to send documents electronically. The primary advantage of this alternative is its efficiency; businesses can save on printing and postage costs while facilitating faster communication. However, it may not be suitable for all scenarios, particularly those requiring physical documentation or where brand presence is crucial. Additionally, the reliance on technology means businesses must invest in software and training, which can be a barrier for some organizations.
How Do Custom Packaging Services Compare?
Custom packaging services provide an alternative that focuses on branding and protective needs. This option allows companies to create envelopes or packaging that align with their brand identity, enhancing their market presence. While custom solutions can improve customer perception and protection of contents during transit, they often come with higher costs and longer lead times compared to standard envelope manufacturing. Businesses looking to stand out in competitive markets may find this option beneficial, but they should weigh the additional costs against their budget constraints.
How Should B2B Buyers Choose the Right Solution?
For international B2B buyers, particularly those from regions like Africa, South America, the Middle East, and Europe, choosing the right envelope solution involves evaluating specific business needs against the advantages and disadvantages of each option. Factors such as budget, required performance, and the nature of communications should guide decision-making. Companies focused on bulk mailing may favor traditional envelope manufacturers for their cost-effectiveness, while those prioritizing brand presentation might lean towards custom packaging services. Conversely, businesses seeking to streamline operations and reduce physical mailing costs may find digital document solutions to be the most effective choice.
In conclusion, the decision for B2B buyers hinges on a careful assessment of their unique needs, operational capabilities, and market positioning. By understanding the alternatives available, businesses can make informed choices that align with their strategic objectives.
Essential Technical Properties and Trade Terminology for envelope manufacturer
What Are the Key Technical Properties for Envelope Manufacturing?
When evaluating envelope manufacturers, understanding the critical technical properties of envelopes is essential for international B2B buyers. Here are some key specifications that should be considered:
1. Material Grade: What Types of Paper Are Used?
The material grade refers to the type and quality of paper used in envelope production. Common materials include kraft paper, coated paper, and recycled paper. Each type has its own weight (measured in grams per square meter, or GSM) and characteristics, influencing durability, printability, and environmental impact. Selecting the appropriate material is crucial for ensuring that the envelope meets the intended use, such as mailing sensitive documents or promotional materials.
2. Tolerance: Why Is It Important in Envelope Production?
Tolerance indicates the permissible limits of variation in dimensions and weight during manufacturing. For envelopes, this includes width, height, and flap size. Tighter tolerances ensure consistent quality and functionality, reducing the risk of production errors that could lead to increased costs or customer dissatisfaction. Buyers should specify tolerance levels to ensure that the envelopes fit their machines and applications perfectly.
3. Closure Type: What Are the Options?
Envelope closure types vary, including self-seal, peel-and-seal, and gummed flaps. Each closure method offers different levels of security and ease of use. For instance, self-seal envelopes are quick and convenient, while gummed flaps may provide a more secure seal for important documents. Understanding these options helps buyers choose the right envelope for their specific needs.
4. Weight Capacity: How Much Can an Envelope Hold?
Weight capacity refers to the maximum weight an envelope can safely carry without tearing or compromising its integrity. This is particularly important for envelopes used in bulk mailing or shipping heavier items. Buyers should confirm the weight capacity to avoid potential issues during transit, which could lead to delays or lost packages.
5. Printing Specifications: What Should Be Considered?
Printing specifications include the type of printing (e.g., digital, offset), ink type, and color options. These factors affect the visual appeal and branding of the envelope. Buyers should discuss their printing needs upfront, including any custom designs or branding requirements, to ensure compatibility with the manufacturer’s capabilities.
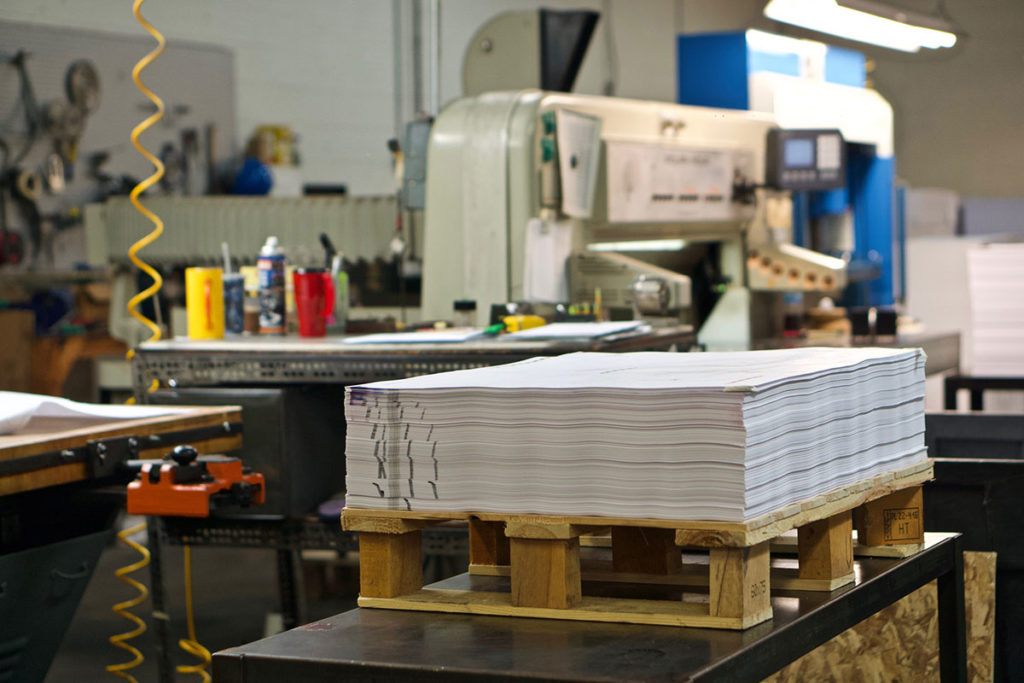
A stock image related to envelope manufacturer.
What Are the Common Trade Terms Used in Envelope Manufacturing?
Understanding industry jargon can enhance communication with suppliers and streamline the purchasing process. Here are some commonly used terms:
1. OEM (Original Equipment Manufacturer): What Does It Mean?
OEM refers to companies that produce products that are sold under another company’s brand name. In the context of envelope manufacturing, this means that a manufacturer may produce envelopes that are branded with the buyer’s logo or specifications. This is important for businesses looking to maintain brand identity in their communications.
2. MOQ (Minimum Order Quantity): Why Is It Relevant?
MOQ refers to the smallest quantity of products that a manufacturer is willing to produce or sell. For envelope manufacturers, this can significantly impact order planning and inventory management. Buyers should inquire about MOQs to ensure that they can meet production requirements without overcommitting resources.
3. RFQ (Request for Quotation): How Should It Be Used?
An RFQ is a document that buyers send to suppliers to request pricing information for specific products. For envelopes, an RFQ should include details about material, size, quantity, and any special requirements. This helps streamline the procurement process and ensures accurate pricing.
4. Incoterms (International Commercial Terms): What Are They?
Incoterms are internationally recognized rules that define the responsibilities of buyers and sellers in the shipping process. They clarify who is responsible for costs and risks during transport. Understanding these terms helps buyers negotiate shipping arrangements and manage logistics effectively.
5. Lead Time: How Does It Affect Ordering?

A stock image related to envelope manufacturer.
Lead time refers to the time taken from placing an order to delivery. In envelope manufacturing, lead times can vary based on order complexity and quantity. Buyers should always confirm lead times to ensure they align with their project timelines and avoid delays in delivery.
By grasping these technical properties and trade terms, B2B buyers from Africa, South America, the Middle East, and Europe can make informed decisions and foster successful partnerships with envelope manufacturers.
Navigating Market Dynamics and Sourcing Trends in the envelope manufacturer Sector
What Are the Key Market Dynamics and Sourcing Trends in the Envelope Manufacturing Sector?
The envelope manufacturing sector is experiencing a transformative phase driven by various global factors. The rise in e-commerce and digital communication has paradoxically increased the demand for physical mail, leading to a resurgence in envelope usage. This demand is amplified by the need for personalized marketing materials, which require high-quality, customized envelopes. International B2B buyers, particularly from regions like Africa, South America, the Middle East, and Europe (e.g., Egypt and Poland), should be aware of these trends to make informed sourcing decisions.
Emerging technologies, such as automation and digital printing, are reshaping the production landscape. Automation not only boosts production efficiency but also reduces labor costs, which is critical for manufacturers aiming to maintain competitive pricing. Furthermore, digital printing enables smaller batch sizes without significant cost increases, catering to the personalized needs of businesses. Buyers should seek suppliers who leverage these technologies to ensure they receive cost-effective and timely deliveries.
Another important trend is the move towards integration of supply chains. As manufacturers look to optimize their operations, international buyers should consider suppliers that offer streamlined logistics and inventory management solutions. This integration not only reduces lead times but also enhances flexibility in responding to market changes.
How Is Sustainability Influencing Sourcing in the Envelope Manufacturing Sector?
Sustainability has become a pivotal consideration for international B2B buyers in the envelope manufacturing sector. The environmental impact of packaging materials is under increasing scrutiny, prompting manufacturers to adopt more eco-friendly practices. This includes sourcing recycled materials and utilizing sustainable production processes, which can significantly lower a company’s carbon footprint.
Ethical sourcing is equally crucial, as buyers increasingly prefer suppliers who adhere to ethical labor practices and maintain transparency in their supply chains. Certifications such as FSC (Forest Stewardship Council) and PEFC (Programme for the Endorsement of Forest Certification) are becoming essential indicators of a manufacturer’s commitment to sustainability. These certifications not only enhance brand reputation but also fulfill growing consumer demand for environmentally responsible products.
Moreover, the adoption of biodegradable and compostable materials is gaining traction in the envelope sector. Buyers should actively seek out manufacturers who provide such materials, as they align with global sustainability goals and can enhance a company’s marketability.
What Is the Historical Context of the Envelope Manufacturing Industry?
The envelope manufacturing industry has evolved significantly since its inception. Initially, envelopes were crafted by hand, often from paper or parchment, and used primarily for formal correspondence. The industrial revolution in the 19th century marked a turning point, as mechanization allowed for mass production, making envelopes more accessible to the general public.
In the late 20th century, advancements in printing technology and paper production led to a diversification of envelope types, including window envelopes, padded envelopes, and custom designs. This evolution reflects the changing needs of businesses and consumers, particularly with the rise of direct mail marketing.
Today, the envelope manufacturing sector stands at a crossroads, balancing traditional methods with modern demands for sustainability and technological innovation. Understanding this historical context can provide valuable insights for B2B buyers as they navigate the current market dynamics and sourcing trends.
Frequently Asked Questions (FAQs) for B2B Buyers of envelope manufacturer
-
How do I choose the right envelope manufacturer for my business needs?
Selecting the right envelope manufacturer involves assessing several factors. First, evaluate the manufacturer’s experience and reputation within the industry. Look for testimonials or case studies that demonstrate their ability to meet quality standards. Additionally, consider their production capacity to ensure they can handle your order volume, especially during peak seasons. Lastly, inquire about their customization options, as tailored solutions can significantly enhance your branding efforts. -
What types of envelopes can I order from an envelope manufacturer?
Envelope manufacturers typically offer a variety of envelope types, including standard, custom-sized, and specialized envelopes like window envelopes, padded envelopes, and eco-friendly options. When sourcing, clarify your specific needs regarding size, material, and purpose. Customization options, such as printing and finishing, can also be discussed to enhance your marketing efforts. Always request samples before placing large orders to verify quality. -
What should I know about minimum order quantities (MOQ) from envelope manufacturers?
Minimum order quantities (MOQ) can vary significantly among envelope manufacturers. Some may have a low MOQ, suitable for small businesses or startups, while others cater to larger corporations with higher MOQ requirements. When sourcing, clarify the MOQ and assess whether it aligns with your budget and inventory needs. Negotiating the MOQ may be possible, especially if you are willing to establish a long-term partnership. -
How do I verify the credibility of an envelope manufacturer?
To verify an envelope manufacturer’s credibility, conduct thorough research. Start by checking their business licenses and certifications, which can indicate compliance with industry standards. Additionally, read reviews on platforms like Google and industry-specific forums. Request references from previous clients to gauge their satisfaction with the manufacturer’s service and product quality. If possible, visit the manufacturing facility to assess their operations firsthand. -
What payment terms should I expect when working with an envelope manufacturer?
Payment terms can vary widely between manufacturers. Common terms include upfront payment, partial payment upon order confirmation, and balance upon delivery. Some manufacturers may offer credit terms for established clients. It’s crucial to discuss and negotiate payment terms upfront to avoid misunderstandings later. Ensure all terms are documented in the contract, including any penalties for late payments.
-
What is the typical lead time for envelope production and delivery?
Lead times for envelope production depend on the complexity of the order, the manufacturer’s capacity, and your location. Generally, standard envelopes may take 2-4 weeks for production, while custom envelopes could take longer. It’s essential to communicate your timeline requirements clearly to the manufacturer. Inquire about expedited options if you have urgent needs, but be aware that this may incur additional costs. -
How can I ensure quality assurance from my envelope manufacturer?
To ensure quality assurance, establish clear specifications for your envelope orders, including material, dimensions, and printing standards. Request samples before full production to assess quality. Additionally, inquire about the manufacturer’s quality control processes and certifications, such as ISO 9001. Regular communication during production can also help address any potential issues early on, ensuring the final product meets your expectations. -
What logistics considerations should I keep in mind when sourcing envelopes internationally?
When sourcing envelopes internationally, consider logistics factors such as shipping costs, import duties, and delivery times. Work with manufacturers who have experience in international shipping and can provide options for freight forwarders. Understand the customs regulations of your country to avoid delays. It’s also wise to discuss packaging options to minimize damage during transit. Establishing a reliable logistics plan will help ensure timely delivery and reduce unforeseen costs.
Important Disclaimer & Terms of Use
⚠️ Important Disclaimer
The information provided in this guide, including content regarding manufacturers, technical specifications, and market analysis, is for informational and educational purposes only. It does not constitute professional procurement advice, financial advice, or legal advice.
While we have made every effort to ensure the accuracy and timeliness of the information, we are not responsible for any errors, omissions, or outdated information. Market conditions, company details, and technical standards are subject to change.
B2B buyers must conduct their own independent and thorough due diligence before making any purchasing decisions. This includes contacting suppliers directly, verifying certifications, requesting samples, and seeking professional consultation. The risk of relying on any information in this guide is borne solely by the reader.
Strategic Sourcing Conclusion and Outlook for envelope manufacturer
What Are the Key Takeaways for International B2B Buyers in Envelope Manufacturing?
In conclusion, strategic sourcing in the envelope manufacturing sector is essential for international B2B buyers seeking to optimize their supply chains. Understanding the diverse landscape of suppliers across Africa, South America, the Middle East, and Europe allows buyers to leverage competitive pricing and quality variations. By focusing on supplier reliability, sustainability practices, and technological advancements, businesses can ensure they are not just meeting current demands but are also preparing for future growth.
How Can Buyers Enhance Their Sourcing Strategies?
Investing in relationships with manufacturers who prioritize innovation and sustainability will yield long-term benefits. B2B buyers are encouraged to explore partnerships with envelope manufacturers that offer customizable solutions, eco-friendly materials, and efficient logistics. This proactive approach not only enhances product offerings but also aligns with the growing consumer demand for environmentally responsible practices.
What Does the Future Hold for Envelope Manufacturing?
Looking ahead, the envelope manufacturing industry is poised for transformation, driven by technological advancements and shifting market demands. International buyers should stay informed about emerging trends, such as digital printing and automated production processes, which can significantly impact product quality and turnaround times. Engaging with forward-thinking manufacturers will empower businesses to remain competitive and responsive to market changes.
In summary, strategic sourcing is not merely a procurement function but a critical component of business strategy. Buyers from regions like Egypt and Poland are urged to leverage this guide to refine their sourcing approaches, ensuring they are well-positioned to capitalize on future opportunities in the envelope market.