Improve Quality: The Ultimate Guide to Flange Manufacturers (2025)
Introduction: Navigating the Global Market for flange manufacturer
In today’s competitive global market, international B2B buyers face the significant challenge of sourcing high-quality flanges that meet diverse industrial standards and applications. Understanding the intricacies of flange manufacturing—from identifying the right type of flange to ensuring compliance with regional specifications—can be daunting. This guide serves as a comprehensive resource for buyers seeking to navigate the complexities of flange procurement, whether you are in Africa, South America, the Middle East, or Europe, including regions like Australia and Egypt.
We will explore various types of flanges, such as welding neck (WN), slip-on (SO), and blind flanges (BL), along with their specific applications across industries. Additionally, the guide delves into the essential aspects of supplier vetting, providing criteria that help assess the reliability and capability of manufacturers. Understanding cost factors, including material quality and production standards, is also critical for making informed purchasing decisions.
By equipping B2B buyers with actionable insights and a clear framework for evaluating flange manufacturers, this guide empowers you to make informed choices that align with your operational needs and budget constraints. Whether you are looking to streamline your supply chain or ensure compliance with international standards, this resource is designed to enhance your procurement strategy and foster successful partnerships in the global marketplace.
Understanding flange manufacturer Types and Variations
Type Name | Key Distinguishing Features | Primary B2B Applications | Brief Pros & Cons for Buyers |
---|---|---|---|
Welding Neck Flange (WN) | Has a long neck that provides additional strength; welded to the pipe. | Oil and gas, chemical processing | Pros: High strength, suitable for high pressure. Cons: More expensive due to additional materials. |
Slip-On Flange (SO) | Slides over the pipe and is welded at the top; easier to install. | Water supply, HVAC systems | Pros: Cost-effective, easy installation. Cons: Less strength compared to WN flanges. |
Blind Flange (BL) | Solid disc used to close the end of a piping system; no opening. | Maintenance and piping isolation | Pros: Easy to install, prevents flow. Cons: Not reusable; requires more effort to remove. |
Threaded Flange (TH) | Features internal threads; connects to threaded pipes. | Low-pressure systems, small pipe diameters | Pros: No welding required, easy to install. Cons: Limited to low-pressure applications. |
Socket Welding Flange (SW) | Has a socket for the pipe to fit into; welded around the joint. | Chemical and petrochemical industries | Pros: Stronger than slip-on, good for high pressure. Cons: Requires precise alignment during installation. |
What Are the Characteristics of Welding Neck Flanges (WN)?
Welding Neck Flanges (WN) are characterized by their long tapered neck, which provides enhanced strength and stability when welded to pipes. They are ideal for high-pressure applications in industries such as oil and gas, where integrity is critical. When purchasing WN flanges, buyers should consider the materials used (often carbon or stainless steel) and the specific pressure ratings required for their applications, as these factors influence performance and longevity.
How Do Slip-On Flanges (SO) Compare to Other Types?
Slip-On Flanges (SO) are designed to fit over the pipe and are welded at the top. This design makes them easier and quicker to install compared to other flange types, making them a popular choice in water supply systems and HVAC applications. Buyers should weigh the cost-effectiveness of SO flanges against their lower strength compared to WN flanges, especially in high-pressure environments.
Why Choose Blind Flanges (BL) for Piping Systems?
Blind Flanges (BL) are solid discs used to seal the end of a piping system. They are commonly employed in maintenance and isolation applications where it is necessary to stop the flow of fluids. While they are easy to install, buyers should consider that blind flanges are not reusable and may require more labor to remove, which could impact maintenance costs over time.
What Are the Benefits of Threaded Flanges (TH)?
Threaded Flanges (TH) feature internal threads that allow them to connect to threaded pipes, making them suitable for low-pressure systems and smaller pipe diameters. Their installation does not require welding, which simplifies the process. However, buyers should recognize that their use is limited to low-pressure applications, which might not meet the needs of more demanding industrial environments.
How Do Socket Welding Flanges (SW) Perform in High-Pressure Applications?
Socket Welding Flanges (SW) are designed with a socket that the pipe fits into, providing a strong joint when welded. They are favored in chemical and petrochemical industries where high-pressure applications are common. Buyers should ensure precise alignment during installation to maximize the strength of the joint, as improper installation can lead to failures under pressure.
Related Video: Orifice Flange and Long Weld Neck Flange – Including Installation
Key Industrial Applications of flange manufacturer
Industry/Sector | Specific Application of flange manufacturer | Value/Benefit for the Business | Key Sourcing Considerations for this Application |
---|---|---|---|
Oil and Gas | Flanges for pipeline connections | Ensures safe and efficient transportation of fluids | Material compatibility, pressure ratings, and certifications |
Chemical Processing | Flanges in reactors and storage tanks | Enhances safety and reliability in handling chemicals | Compliance with industry standards and corrosion resistance |
Water Treatment | Flanges in water distribution systems | Facilitates effective water management and delivery | Durability, pressure ratings, and environmental regulations |
Power Generation | Flanges in turbines and heat exchangers | Increases efficiency and reliability of power systems | High-temperature resistance and material specifications |
Construction and HVAC | Flanges in piping systems for heating and cooling | Supports structural integrity and energy efficiency | Size specifications, pressure ratings, and installation ease |
How Are Flanges Used in the Oil and Gas Industry?
In the oil and gas sector, flanges play a crucial role in connecting pipelines, valves, and equipment. Their primary function is to create a tight seal that prevents leaks during the transportation of oil, gas, and other fluids. For international buyers, particularly from Africa and the Middle East, sourcing flanges requires attention to material compatibility with various fluids and adherence to safety standards. Additionally, understanding the pressure ratings, such as ANSI or ASME classes, is vital to ensure operational safety and efficiency.
What Are the Applications of Flanges in Chemical Processing?
Flanges are integral to chemical processing, used in reactors, storage tanks, and transfer lines. They help maintain the integrity of systems that handle volatile chemicals under high pressure and temperature. Buyers in South America and Europe must prioritize flanges that comply with international standards, such as ASME or API. Corrosion resistance is another critical factor, as many chemicals can degrade materials over time, potentially leading to catastrophic failures if not properly addressed.
How Are Flanges Utilized in Water Treatment Facilities?
In water treatment plants, flanges are used in various applications, including the connection of pipes, valves, and filtration systems. They ensure a secure and leak-proof fit, which is essential for maintaining water quality and pressure. International buyers, especially in regions like Africa, should consider sourcing flanges that meet environmental regulations and standards for potable water systems. Durability and maintenance ease are also key factors, as these systems require regular inspection and upkeep.
Why Are Flanges Important in Power Generation?
In the power generation industry, flanges are employed in turbines, heat exchangers, and cooling systems. They are critical for maintaining high-pressure and high-temperature environments, ensuring efficient energy production. Buyers from Europe and the Middle East should focus on flanges with high-temperature resistance and durability to withstand the operational demands of power plants. Additionally, understanding the specific material requirements, such as stainless steel or alloy options, can significantly enhance system performance and longevity.
How Are Flanges Applied in Construction and HVAC Systems?
Flanges are widely used in construction and HVAC systems to connect piping for heating, ventilation, and air conditioning. They provide structural integrity and facilitate easy installation and maintenance of piping systems. For international buyers, especially in Europe and Australia, it is essential to consider size specifications, pressure ratings, and the ease of installation when sourcing flanges. Compliance with local building codes and standards is also crucial to ensure safety and efficiency in HVAC applications.
Related Video: Piping Flange Types, Faces, and Surfaces – Explained!
3 Common User Pain Points for ‘flange manufacturer’ & Their Solutions
Scenario 1: Sourcing High-Quality Flanges that Meet International Standards
The Problem: International B2B buyers often struggle to find flange manufacturers that can consistently provide products compliant with various international standards, such as ASME, DIN, or JIS. This challenge is exacerbated for companies in regions like Africa and South America, where local suppliers may not adhere to stringent quality controls. Inconsistent quality can lead to project delays, increased costs, and potential safety hazards, causing significant frustration for procurement managers.
The Solution: To address this problem, buyers should prioritize sourcing from manufacturers with proven certifications and a robust quality assurance process. Start by asking for documentation of compliance with relevant international standards, and consider suppliers that have undergone third-party audits. Additionally, leverage online platforms and industry networks to identify reputable manufacturers with positive reviews. Engaging in direct communication to discuss specific needs and quality expectations can also help establish a more reliable partnership. Consider requesting samples before committing to large orders, ensuring that the products meet your required specifications.
Scenario 2: Navigating Complex Flange Specifications and Customizations
The Problem: B2B buyers often face difficulties when dealing with complex flange specifications, especially when customizations are required for unique applications. Manufacturers may use different terminologies for flange types, pressure ratings, and materials, leading to confusion and potential miscommunication. This issue can lead to incorrect orders, wasted resources, and delays in project timelines.
The Solution: To effectively navigate this complexity, buyers should invest time in understanding the specific requirements of their applications, including the types of flanges needed (e.g., welding neck, slip-on, or blind) and the relevant pressure ratings (e.g., Class 150, Class 300). Creating a detailed specification sheet can aid in communicating requirements to manufacturers. When reaching out to suppliers, provide them with clear drawings and any relevant industry standards. Additionally, consider partnering with a technical consultant or utilizing software tools designed for industrial applications to ensure that the selected flanges will fit seamlessly into your projects. Regularly updating your knowledge on flange standards and types can also streamline future procurement processes.
Scenario 3: Managing Lead Times and Delivery Issues
The Problem: Timely delivery is critical in the B2B sector, yet many buyers experience long lead times from flange manufacturers, which can disrupt project schedules. This issue is particularly pronounced when sourcing from overseas manufacturers, where shipping delays and customs clearance can add to lead time uncertainty. The inability to plan for these delays can cause cascading issues in project management and client satisfaction.
The Solution: To mitigate lead time issues, buyers should establish clear communication channels with manufacturers, discussing realistic timelines based on past performance. It can be beneficial to build relationships with multiple suppliers, allowing for flexibility in sourcing and the ability to switch if delays occur. Consider placing orders well in advance of project deadlines, and utilize forecasting tools to better predict your needs based on historical data. Additionally, inquire about the manufacturers’ production capacities and stock availability. Opting for suppliers who offer expedited shipping options or local warehousing can also provide a buffer against unforeseen delays, ensuring that projects remain on schedule.
Strategic Material Selection Guide for flange manufacturer
What Are the Key Properties of Carbon Steel Flanges?
Carbon steel is one of the most commonly used materials in flange manufacturing due to its excellent mechanical properties and cost-effectiveness. It typically offers a good balance of strength, ductility, and weldability. Carbon steel flanges can withstand high temperatures and pressures, making them suitable for a variety of applications in industries such as oil and gas, chemical processing, and water supply.
Pros and Cons: The primary advantages of carbon steel include its durability and affordability. However, it is prone to corrosion, which can limit its use in certain environments without proper protective coatings or treatments. For international buyers, especially in regions with high humidity or corrosive media, additional considerations for corrosion resistance are essential.
Impact on Application: Carbon steel flanges are compatible with various media, including water, oil, and gas. However, they may not be suitable for highly corrosive substances unless treated. Buyers in Africa and South America should be aware of local environmental conditions that may affect the longevity of carbon steel products.
How Does Stainless Steel Compare for Flange Manufacturing?
Stainless steel, particularly grades like 304 and 316, is favored for its superior corrosion resistance and aesthetic appeal. These materials can handle a wide range of temperatures and pressures, making them ideal for applications in food processing, pharmaceuticals, and marine environments.
Pros and Cons: The key advantage of stainless steel flanges is their resistance to rust and corrosion, which enhances their lifespan in harsh environments. However, they are generally more expensive than carbon steel and can be more challenging to manufacture due to their hardness. Buyers in Europe and the Middle East often prefer stainless steel for applications requiring hygiene and resistance to aggressive chemicals.
Impact on Application: Stainless steel flanges are compatible with a wide range of media, including corrosive chemicals and high-purity applications. International buyers should ensure compliance with relevant standards such as ASTM and DIN when sourcing stainless steel products.
Why Are Alloy Steel Flanges Important in High-Pressure Applications?
Alloy steel is used in flange manufacturing for applications requiring high strength and resistance to extreme conditions. Materials like ASTM A182 F11 and F22 are often utilized in high-pressure and high-temperature environments, such as power generation and petrochemical industries.
Pros and Cons: The main advantage of alloy steel flanges is their ability to withstand high stress and temperature, making them suitable for critical applications. However, they can be more costly and complex to manufacture compared to carbon steel. Buyers in regions like the Middle East, where oil and gas extraction is prevalent, should consider alloy steel for its performance in demanding environments.
Impact on Application: Alloy steel flanges are compatible with high-pressure steam, oil, and gas. Buyers should be aware of the specific alloy composition required for their applications to ensure compliance with industry standards.
What Is the Role of Plastic Flanges in Various Industries?
Plastic flanges, often made from materials like PVC or CPVC, are increasingly used in applications where corrosion resistance and lightweight properties are essential. They are suitable for chemical processing, water treatment, and other applications where metal flanges may corrode.
Pros and Cons: The key advantage of plastic flanges is their excellent resistance to chemicals and lightweight nature, which can reduce installation costs. However, they are not suitable for high-pressure applications and can be less durable than metal alternatives. Buyers in South America and Africa should consider local chemical compatibility and temperature ratings when selecting plastic flanges.
Impact on Application: Plastic flanges are ideal for corrosive environments but may not perform well in high-temperature or high-pressure scenarios. Compliance with local standards and regulations is crucial for international buyers.
Summary Table of Material Selection for Flange Manufacturing
Material | Typical Use Case for flange manufacturer | Key Advantage | Key Disadvantage/Limitation | Relative Cost (Low/Med/High) |
---|---|---|---|---|
Carbon Steel | Oil and gas, water supply | Durable and cost-effective | Prone to corrosion | Low |
Stainless Steel | Food processing, pharmaceuticals | Excellent corrosion resistance | Higher cost and manufacturing complexity | High |
Alloy Steel | High-pressure applications | High strength and temperature resistance | More expensive and complex to manufacture | Medium |
Plastic | Chemical processing, water treatment | Lightweight and corrosion-resistant | Not suitable for high-pressure | Low |
This guide provides international B2B buyers with critical insights into material selection for flanges, ensuring informed purchasing decisions aligned with specific application needs and regional standards.
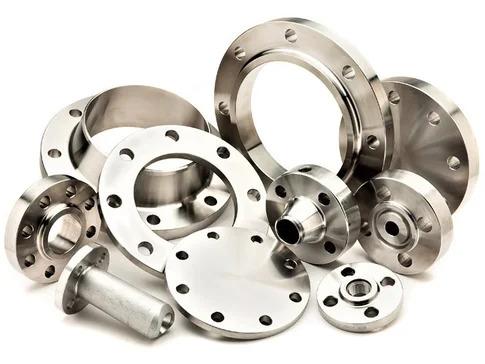
A stock image related to flange manufacturer.
In-depth Look: Manufacturing Processes and Quality Assurance for flange manufacturer
What Are the Main Stages in the Manufacturing Process of Flanges?
The manufacturing of flanges involves several critical stages that ensure the final product meets industry standards and customer specifications. Here’s a breakdown of the typical manufacturing process:
Material Preparation: What Materials Are Used for Flange Production?
The initial stage of flange manufacturing involves selecting high-quality raw materials. Common materials include:
- Carbon Steel: Often used due to its strength and cost-effectiveness. Standards such as ASTM A105 and ASTM A694 are commonly referenced.
- Stainless Steel: Provides excellent corrosion resistance, making it suitable for harsh environments. Grades like ASTM A182 F304 and F316 are popular.
- Alloy Steel: Used for applications requiring enhanced mechanical properties. Examples include ASTM A182 F22 and F91.
Once selected, these materials undergo cutting to the required dimensions, ensuring they meet the specifications outlined in the engineering drawings.
How Is the Forming Process Conducted for Flanges?
Forming is a crucial step that shapes the raw materials into the desired flange configuration. This can be achieved through various techniques, including:
- Forging: Often used for high-strength applications, forging involves shaping the metal using compressive forces. This method enhances the material’s mechanical properties.
- Casting: For complex shapes, casting is employed, where molten metal is poured into a mold. This is typically used for larger flanges.
- Machining: After forming, flanges are machined to achieve precise dimensions and surface finishes. CNC (Computer Numerical Control) machines are commonly utilized for accuracy.
What Happens During the Assembly and Finishing Stages?
Once the individual components are formed, they are assembled if necessary. For instance, multi-part flanges may require welding or bolting together. The finishing stage includes:
- Surface Treatment: Techniques such as sandblasting, polishing, or coating (e.g., galvanizing) are applied to enhance corrosion resistance and aesthetic appeal.
- Quality Checks: Each flange undergoes inspections during the finishing process to ensure it meets specified tolerances and surface quality.
What Quality Assurance Measures Are Essential in Flange Manufacturing?
Quality assurance (QA) is vital to ensure that flanges are safe, reliable, and compliant with international standards. Here are key QA measures employed in the industry:
Which International Standards Should Flange Manufacturers Comply With?
Flange manufacturers often adhere to several international quality standards, including:
- ISO 9001: This standard focuses on quality management systems and emphasizes customer satisfaction and continuous improvement.
- API Standards: For flanges used in the oil and gas industry, compliance with American Petroleum Institute (API) standards is crucial.
- CE Marking: For products sold within the European Economic Area, CE marking indicates conformity with health, safety, and environmental protection standards.
What Are the Key Quality Control Checkpoints?
Quality control (QC) is typically structured around several checkpoints throughout the manufacturing process:
- Incoming Quality Control (IQC): Materials are inspected upon arrival to ensure they meet specified standards.
- In-Process Quality Control (IPQC): This involves monitoring the manufacturing process at various stages to catch defects early.
- Final Quality Control (FQC): The finished flanges are thoroughly inspected and tested before shipment, ensuring they meet all specifications.
How Are Flanges Tested to Ensure Quality?
Testing is a crucial part of the QC process. Common testing methods include:
- Visual Inspection: A basic assessment to identify surface defects or irregularities.
- Dimensional Testing: Using calipers and gauges to ensure the flanges meet specified dimensions and tolerances.
- Pressure Testing: Conducted to verify that flanges can withstand the required pressure levels without leaking.
- Non-Destructive Testing (NDT): Techniques such as ultrasonic testing or radiography to detect internal defects without damaging the flange.
How Can B2B Buyers Verify Supplier Quality Control?
For international B2B buyers, especially those from Africa, South America, the Middle East, and Europe, verifying supplier quality is essential. Here are actionable steps:
What Auditing Procedures Can Buyers Implement?
- Supplier Audits: Conducting on-site audits of the manufacturing facility helps assess compliance with quality standards and production capabilities.
- Requesting Quality Reports: Ask suppliers for documentation regarding their quality control processes, including IQC, IPQC, and FQC reports.
How Can Third-Party Inspections Enhance Trust?
Engaging third-party inspection agencies can provide impartial verification of product quality. This can include:
- Pre-Shipment Inspections: A thorough inspection before shipment can ensure compliance with agreed specifications.
- Certification Verification: Request copies of certifications related to ISO, API, and other relevant standards to confirm the supplier’s credibility.
What Are the Nuances of Quality Certification for International Buyers?
When sourcing flanges internationally, buyers should be aware of the following nuances:
- Regional Standards Variability: Different regions may have specific standards that affect the type of flanges required. For example, European standards may differ from those in the U.S. or Asia.
- Material Traceability: Ensure that suppliers can provide documentation tracing the materials used in production, as this is often a regulatory requirement.
Conclusion
Understanding the manufacturing processes and quality assurance measures of flange production is essential for B2B buyers looking to source reliable products. By familiarizing themselves with the stages of production, relevant international standards, and effective verification methods, buyers can make informed decisions that align with their operational needs and regulatory requirements.
Practical Sourcing Guide: A Step-by-Step Checklist for ‘flange manufacturer’
To effectively procure flanges from a manufacturer, international B2B buyers—especially from regions such as Africa, South America, the Middle East, and Europe—should follow a systematic approach. This guide outlines essential steps to ensure that your sourcing process is efficient, cost-effective, and meets your specific requirements.
Step 1: Define Your Technical Specifications
Before reaching out to manufacturers, it’s crucial to have a clear understanding of your technical requirements. This includes the type of flange you need (e.g., WN, SO, BL, TH, LJ, SW), material specifications (such as carbon steel, stainless steel, or alloy steel), and pressure ratings (e.g., Class 150, Class 300).
– Why It Matters: Clear specifications help prevent miscommunication and ensure that the product you receive meets your operational needs.
Step 2: Conduct Market Research for Suppliers
Identify potential flange manufacturers by conducting thorough market research. Utilize online platforms, industry directories, and trade shows to compile a list of suppliers that specialize in the type of flanges you require.
– What to Look For: Focus on suppliers with a proven track record and those who cater to your specific geographic market. Consider regional suppliers that understand local standards and regulations.
Step 3: Evaluate Potential Suppliers
Before committing to any supplier, perform a comprehensive evaluation. Request company profiles, product catalogs, case studies, and references from previous clients, particularly those in your industry or region.
– Why This Is Important: This step helps verify the supplier’s credibility and reliability. A thorough vetting process minimizes the risk of engaging with an unqualified manufacturer.
Step 4: Verify Supplier Certifications and Compliance
Ensure that the manufacturers you are considering possess the necessary certifications and comply with international standards, such as ISO, ASME, or ANSI. Ask for documentation that confirms their compliance with quality management systems and industry-specific standards.
– What to Check: Look for certifications relevant to your industry and specific applications, which can indicate a commitment to quality and safety.
Step 5: Request Samples for Quality Assessment
Before placing a bulk order, request samples of the flanges you intend to purchase. This will allow you to assess the quality of materials, workmanship, and adherence to your specifications.
– Importance of Sampling: Evaluating samples can prevent costly mistakes and ensure that the products meet your quality expectations before the full order is fulfilled.
Step 6: Negotiate Terms and Conditions
Once you have identified a suitable supplier, engage in negotiations regarding pricing, payment terms, delivery schedules, and warranties. Clear agreements can help protect both parties and outline expectations.
– Key Considerations: Discuss potential discounts for bulk purchases, payment methods (such as letters of credit), and penalties for late delivery.
Step 7: Establish a Communication Plan
Finally, set up a communication plan to maintain ongoing dialogue with your supplier throughout the production and delivery phases. Regular updates can help address any issues promptly and ensure that the project stays on track.
– Why Communication Is Key: Effective communication fosters a stronger relationship and can lead to better collaboration in future projects.
By following this checklist, B2B buyers can streamline their sourcing process for flange manufacturers, ensuring that they procure high-quality products that meet their operational needs while minimizing risks.
Comprehensive Cost and Pricing Analysis for flange manufacturer Sourcing
What Are the Key Cost Components in Flange Manufacturing?
Understanding the cost structure of flange manufacturing is crucial for international B2B buyers. The primary cost components include:
-
Materials: The choice of material significantly impacts the cost. Common materials include carbon steel, stainless steel, and alloy steel, each with varying price points based on market demand and availability. For instance, stainless steel flanges typically command higher prices due to their corrosion resistance.
-
Labor: Labor costs can vary widely depending on the region and the skill level required. In regions like Africa and South America, labor may be less expensive, while in Europe, it could be higher due to stringent labor laws and higher living costs.
-
Manufacturing Overhead: This includes utilities, equipment maintenance, and facility costs. Efficient manufacturing processes can help reduce overhead costs, leading to more competitive pricing for buyers.
-
Tooling: Custom tooling can be a significant upfront cost, especially for specialized flange designs. Buyers should consider whether the supplier has the capability to produce the required tooling in-house to reduce costs.
-
Quality Control (QC): Implementing robust QC processes ensures that flanges meet required specifications. The cost of QC can vary based on the complexity of the product and the certifications needed, such as ISO or API standards.
-
Logistics: Shipping costs are a critical factor, especially for international buyers. The distance from the manufacturer and the chosen Incoterms can significantly affect the overall cost.
-
Margin: Suppliers typically add a margin to cover their costs and profit. Understanding the supplier’s margin expectations can help buyers negotiate better terms.
How Do Price Influencers Affect Flange Sourcing?
Several factors influence the pricing of flanges, particularly for international B2B buyers:
-
Volume and Minimum Order Quantity (MOQ): Larger orders often lead to lower per-unit costs. Buyers should negotiate for favorable terms if they plan to order in bulk.
-
Specifications and Customization: Custom flanges tailored to specific applications may incur higher costs. Buyers should weigh the benefits of customization against potential price increases.
-
Material Selection: The material chosen impacts both cost and performance. Understanding the properties of different materials can help buyers select the best option for their needs without overspending.
-
Quality and Certifications: Flanges with higher quality standards or specific certifications (like ASME or ASTM) may carry a premium. Buyers should assess the necessity of these certifications based on their application.
-
Supplier Factors: The supplier’s reputation, location, and production capacity can influence pricing. Established suppliers may charge more due to reliability, while newer suppliers might offer lower prices to attract business.
-
Incoterms: The chosen Incoterms dictate who is responsible for shipping costs, insurance, and risks. This can greatly affect the total cost of ownership for the buyer.
What Are the Best Negotiation Tips for International Buyers?
-
Understand Total Cost of Ownership (TCO): Consider all costs associated with sourcing flanges, including purchase price, shipping, duties, and potential downtime. This holistic view can help justify higher initial costs if they lead to long-term savings.
-
Leverage Market Knowledge: Being informed about current market trends and material costs can strengthen your negotiation position. Knowledgeable buyers are less likely to overpay.
-
Build Relationships with Suppliers: Establishing strong relationships can lead to better pricing and terms. Suppliers are often more willing to negotiate with repeat customers.
-
Be Open to Alternative Suppliers: Diversifying your supplier base can create competition, which may lead to better pricing and terms.
-
Request Price Breakdowns: Understanding the components of the price can help identify areas for negotiation, such as reducing overhead or logistics costs.
Disclaimer on Pricing
Prices for flanges can vary significantly based on multiple factors, including market conditions and specific buyer requirements. Therefore, the prices discussed in this analysis are indicative and should be verified with suppliers for accurate quotations. Always request detailed quotes to ensure all potential costs are accounted for.
Alternatives Analysis: Comparing flange manufacturer With Other Solutions
When evaluating the options available for connecting piping systems, it is essential to consider various alternatives to traditional flange manufacturers. Each alternative presents unique benefits and drawbacks, which can significantly influence project outcomes, particularly for international B2B buyers in Africa, South America, the Middle East, and Europe.
Comparison Aspect | Flange Manufacturer | Alternative 1: Welded Connections | Alternative 2: Threaded Connections |
---|---|---|---|
Performance | High pressure tolerance; suitable for diverse applications | Excellent for high-pressure systems; permanent | Moderate; suitable for low-pressure applications |
Cost | Generally higher due to manufacturing and material costs | Lower material costs, but requires skilled labor | Cost-effective for small installations; material costs vary |
Ease of Implementation | Requires precise alignment and installation | Complex; requires welding skills and equipment | Simple installation; no special tools required |
Maintenance | Moderate; regular inspections recommended | Low maintenance; permanent solution | Moderate; may require periodic checks for leaks |
Best Use Case | Industrial applications, chemical processing | Oil and gas pipelines, high-pressure systems | Residential and low-pressure applications |
What are the Advantages and Disadvantages of Welded Connections?
Welded connections provide a robust alternative to flanges, especially in environments requiring high pressure and reliability. One of the primary advantages is their ability to create a seamless connection that minimizes the risk of leaks, making them ideal for critical applications such as oil and gas pipelines. However, the complexity of welding processes requires skilled labor and specialized equipment, which can increase project timelines and costs. Additionally, once welded, these connections are permanent, making them less flexible for future modifications or repairs.
How Do Threaded Connections Compare to Flange Manufacturers?
Threaded connections are a widely used alternative, particularly in smaller installations. Their primary advantage lies in their ease of installation; no specialized tools are required, and they can be assembled quickly. This makes them a cost-effective solution for residential or low-pressure applications. However, their performance is generally limited in high-pressure scenarios, as the risk of leaks increases with the pressure exerted. Moreover, threaded connections may require periodic maintenance to ensure they remain leak-free, which can add to the long-term costs.
Conclusion: How Should B2B Buyers Choose Between Flange Manufacturers and Alternatives?
Choosing the right solution depends on several factors, including the specific application, pressure requirements, and budget constraints. For high-performance and high-pressure applications, flange manufacturers may be the best choice, offering durability and reliability despite higher costs. Conversely, for projects with lower pressure demands or those requiring quick installation, welded or threaded connections may provide a more economical and practical solution. Ultimately, international B2B buyers should assess their unique needs, consider the long-term implications of each method, and consult with industry experts to make an informed decision that aligns with their operational goals.
Essential Technical Properties and Trade Terminology for flange manufacturer
What Are the Key Technical Properties for Flange Manufacturers?
When selecting flanges, understanding the technical properties is crucial for ensuring compatibility with your application and maintaining system integrity. Here are some essential specifications:
-
Material Grade
Flanges are typically made from materials such as carbon steel, stainless steel, and alloy steel. The material grade affects not only the strength and durability of the flange but also its resistance to corrosion and temperature variations. For instance, ASTM A105 is a common carbon steel grade, while ASTM A182 F304 is widely used for stainless steel applications. Choosing the right material ensures that the flange can withstand the operational environment, which is particularly important for industries like oil and gas, chemical processing, and water treatment. -
Pressure Class
Pressure class is a key specification that indicates the maximum pressure the flange can withstand. Common classes include 150, 300, and 600, which correspond to various pressure ratings. For example, a Class 150 flange can handle a nominal pressure of approximately 2.0 MPa. Understanding the pressure class is vital for ensuring that the flange will perform safely under operational conditions, particularly in high-pressure systems. -
Tolerance
Tolerance refers to the permissible variation in dimensions of the flange. This specification is critical for ensuring proper fit and sealing when the flange is installed. Standard tolerances are defined by various international standards (such as ASME and ISO). Proper tolerance levels reduce the risk of leaks and failures, thus enhancing the reliability of the entire piping system. -
Surface Finish
The surface finish of a flange can significantly influence its sealing capability. Common finishes include smooth, rough, or coated surfaces. A smooth finish is essential for achieving effective sealing with gaskets, while a rough finish may be used for better grip in specific applications. Selecting the appropriate surface finish based on the sealing method employed can prevent leaks and extend the service life of the connection. -
Bolt Hole Configuration
The number and arrangement of bolt holes on a flange are critical for ensuring that it can be securely fastened to other components. Standard configurations include different patterns such as the number of holes and their spacing. Understanding bolt hole configuration is essential for compatibility with existing piping systems and ensuring structural integrity during operation.
Which Trade Terms Are Essential for Flange Manufacturers?
Familiarity with industry-specific terminology can streamline the procurement process and improve communication with suppliers. Here are some key trade terms:
-
OEM (Original Equipment Manufacturer)
An OEM refers to a company that produces parts or equipment that may be marketed by another manufacturer. In the context of flanges, buyers may seek OEMs for custom or proprietary flange designs that meet specific application requirements. -
MOQ (Minimum Order Quantity)
This term indicates the smallest quantity of a product that a supplier is willing to sell. Understanding MOQ is vital for budgeting and inventory management, especially for international buyers who may need to import large quantities to meet their operational needs. -
RFQ (Request for Quotation)
An RFQ is a document issued by a buyer to solicit price quotes from suppliers for specific products. Including detailed specifications in an RFQ helps ensure that responses are accurate and meet the buyer’s requirements, facilitating a smoother purchasing process. -
Incoterms (International Commercial Terms)
Incoterms are a set of predefined international trade terms that clarify the responsibilities of buyers and sellers in international transactions. Terms like FOB (Free on Board) and CIF (Cost, Insurance, and Freight) define who is responsible for shipping costs, insurance, and risks at various points during transport. Understanding these terms is essential for effective negotiation and risk management in global supply chains. -
Lead Time
Lead time refers to the time it takes from placing an order to receiving the product. Knowing the lead time is crucial for planning project timelines and ensuring that materials arrive when needed, especially in industries with tight schedules.
By grasping these technical properties and trade terms, international B2B buyers can make informed decisions, enhance their procurement processes, and establish successful partnerships with flange manufacturers.
Navigating Market Dynamics and Sourcing Trends in the flange manufacturer Sector
What are the Key Market Dynamics and Trends Affecting the Flange Manufacturer Sector?
The flange manufacturing sector is experiencing significant transformations driven by global industrial demands and technological advancements. Key market drivers include increased infrastructure investments in developing regions such as Africa and South America, which are expanding their energy and construction sectors. The Middle East continues to focus on oil and gas projects, while Europe emphasizes sustainability and energy efficiency. These factors collectively contribute to a growing demand for high-quality flanges that meet diverse industrial applications.
Emerging technologies are reshaping sourcing strategies for international B2B buyers. The integration of Industry 4.0 technologies, including IoT and AI, is enhancing supply chain visibility and operational efficiency. Buyers are increasingly leveraging digital platforms for sourcing, enabling them to compare suppliers, assess quality, and streamline procurement processes. Additionally, the rise of e-commerce in B2B transactions facilitates quicker decision-making and reduces lead times, which is crucial for projects with tight timelines.
Furthermore, evolving regulations and standards, particularly in Europe, are compelling manufacturers to innovate and produce flanges that comply with stringent quality and safety requirements. This shift is creating opportunities for manufacturers who can offer customized solutions that align with these standards.
How is Sustainability Influencing Sourcing Decisions for Flange Manufacturers?
Sustainability has emerged as a pivotal consideration in the flange manufacturing sector. The environmental impact of production processes is under scrutiny, prompting buyers to prioritize suppliers with eco-friendly practices. Ethical sourcing is becoming increasingly important, as businesses aim to build resilient supply chains that minimize carbon footprints and promote social responsibility.
Buyers are encouraged to seek out manufacturers that utilize sustainable materials and practices, such as recycled metals and energy-efficient manufacturing processes. Certifications such as ISO 14001 (Environmental Management) and LEED (Leadership in Energy and Environmental Design) are essential indicators of a supplier’s commitment to sustainability. These certifications not only enhance a manufacturer’s credibility but also align with the growing consumer demand for environmentally responsible products.
Moreover, the trend toward circular economy principles is gaining traction. Manufacturers that adopt practices such as waste reduction, reuse of materials, and product lifecycle management can differentiate themselves in a competitive market. For international B2B buyers, collaborating with sustainable suppliers can yield long-term benefits, including cost savings, improved brand reputation, and compliance with evolving regulatory frameworks.
What is the Historical Context of the Flange Manufacturing Sector?
The flange manufacturing sector has a rich history that dates back to the industrial revolution when the need for robust piping systems became paramount. Initially, flanges were crafted from wrought iron, evolving over the years to include a variety of materials such as carbon steel, stainless steel, and alloyed metals to meet the increasing demands of diverse industries.
The 20th century witnessed significant advancements in manufacturing techniques, including the introduction of standardized flange dimensions and pressure ratings, which facilitated global trade. The development of international standards, such as ANSI and ISO, further streamlined the specifications for flange production, ensuring compatibility across different regions and applications.
As the industry has progressed, the focus has shifted towards improving product quality and performance, driven by advancements in metallurgy and manufacturing technologies. Today, the flange sector stands at the intersection of tradition and innovation, continuously adapting to meet the demands of modern industries while embracing sustainability and ethical sourcing practices. This evolution is crucial for international B2B buyers looking for reliable, high-performance products in an increasingly competitive landscape.
Frequently Asked Questions (FAQs) for B2B Buyers of flange manufacturer
-
How do I choose the right flange type for my application?
Selecting the appropriate flange type hinges on several factors, including the intended use, pressure requirements, and compatibility with existing piping systems. Common flange types include welding neck (WN), slip-on (SO), and blind flanges (BL). Assess your application’s temperature, pressure, and fluid characteristics to ensure the flange can withstand operational conditions. Consulting with your flange manufacturer or a technical expert can provide additional insights tailored to your specific needs. -
What are the international standards for flanges?
Flange standards vary globally, with the most recognized being the American Society of Mechanical Engineers (ASME) standards, such as ASME B16.5 and B16.47, and the European standard EN 1092. Understanding these standards is crucial for ensuring compatibility and compliance in international markets. When sourcing flanges, verify that the manufacturer adheres to the relevant standards to avoid complications during installation and operation. -
How can I vet a flange manufacturer before making a purchase?
Vetting a flange manufacturer involves assessing their certifications, quality control processes, and customer reviews. Request documentation of compliance with international standards and inquire about their production capabilities. Additionally, visiting their facility or asking for references from previous clients can provide insights into their reliability and product quality. Establishing clear communication about your requirements will also help gauge their responsiveness and expertise. -
What is the minimum order quantity (MOQ) for flanges?
Minimum order quantities for flanges can vary significantly based on the manufacturer and the specific type of flange. Generally, MOQs range from a few pieces to several hundred. Discussing your needs directly with the manufacturer can lead to negotiated terms, especially if you’re considering a long-term partnership. For smaller projects, some manufacturers may offer stock options or allow for mixed orders to meet MOQ requirements. -
What payment terms should I expect when sourcing flanges internationally?
Payment terms for international flange purchases can vary widely. Common practices include advance payment, letter of credit, or payment upon delivery. Discussing terms upfront with your manufacturer is essential to ensure clarity and alignment. Additionally, consider the currency fluctuations and transaction fees associated with international payments, which may impact your overall costs. -
What quality assurance processes should a flange manufacturer have?
A reputable flange manufacturer should implement robust quality assurance processes, including material inspections, dimensional checks, and pressure testing. Certifications such as ISO 9001 or API standards indicate adherence to quality management principles. Requesting documentation of these processes can help ensure that the flanges meet your required specifications and performance standards.
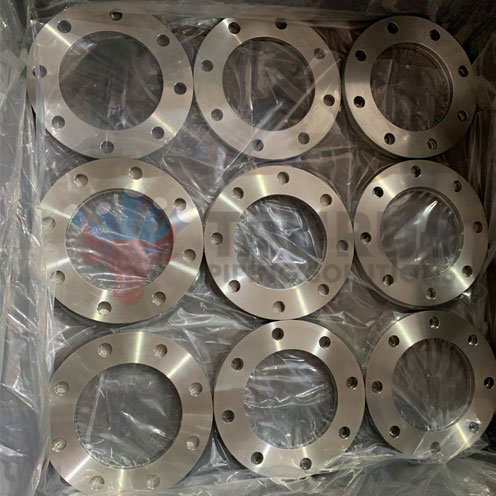
A stock image related to flange manufacturer.
-
How do logistics and shipping impact flange sourcing?
Logistics play a critical role in flange sourcing, particularly in terms of delivery timelines and costs. It’s essential to discuss shipping options with your manufacturer, including freight forwarders and potential customs duties. Understanding lead times for production and shipping will help you plan your project timelines effectively. Additionally, consider the geographical location of the manufacturer and how it may influence shipping costs and delivery times. -
Can flanges be customized for specific applications?
Yes, many flange manufacturers offer customization options to meet specific application requirements. This can include modifications in size, material, pressure ratings, and surface finishes. When discussing customization, provide detailed specifications and any relevant industry standards to ensure that the manufacturer can meet your needs. Engaging in early discussions about your requirements can help facilitate a smoother production process.
Important Disclaimer & Terms of Use
⚠️ Important Disclaimer
The information provided in this guide, including content regarding manufacturers, technical specifications, and market analysis, is for informational and educational purposes only. It does not constitute professional procurement advice, financial advice, or legal advice.
While we have made every effort to ensure the accuracy and timeliness of the information, we are not responsible for any errors, omissions, or outdated information. Market conditions, company details, and technical standards are subject to change.
B2B buyers must conduct their own independent and thorough due diligence before making any purchasing decisions. This includes contacting suppliers directly, verifying certifications, requesting samples, and seeking professional consultation. The risk of relying on any information in this guide is borne solely by the reader.
Strategic Sourcing Conclusion and Outlook for flange manufacturer
In today’s competitive global market, strategic sourcing of flanges is not just a necessity but a pathway to achieving operational excellence. By understanding the various flange types such as WN (welding neck), SO (slip-on), and BL (blind flanges), international B2B buyers can make informed decisions tailored to their specific industry needs. The emphasis on quality standards, such as those from ANSI and DIN, ensures that procurement aligns with both local regulations and international best practices.
Additionally, leveraging relationships with reputable manufacturers can lead to enhanced supply chain resilience and cost-effectiveness. Buyers from Africa, South America, the Middle East, and Europe must prioritize partnerships that emphasize quality, reliability, and sustainability. This not only fosters a competitive edge but also supports long-term growth in emerging markets.
As we look to the future, the importance of strategic sourcing will only increase. International B2B buyers are encouraged to actively engage with manufacturers and suppliers to stay abreast of innovations and trends in flange technology. Embrace this opportunity to enhance your procurement strategy and secure your position in the global marketplace.