Improve Quality: The Ultimate Guide to Wire Rope Manufacturer (2025)
Introduction: Navigating the Global Market for wire rope manufacturer
Navigating the global market for wire rope manufacturers presents a unique set of challenges, particularly for international B2B buyers from diverse regions like Africa, South America, the Middle East, and Europe. Sourcing high-quality wire rope products that meet specific operational demands can be a complex process, often hindered by varying standards, supplier reliability, and cost considerations. This guide aims to demystify the wire rope procurement landscape by providing a comprehensive overview of the types of wire ropes available, their applications across various industries, and best practices for supplier vetting.
As you delve into this guide, you will uncover crucial insights into the latest market trends, enabling you to make informed purchasing decisions. We will explore essential factors such as pricing strategies, logistical considerations, and regulatory compliance that are particularly relevant to buyers in Italy, Colombia, and beyond. Additionally, we will provide actionable tips on evaluating suppliers to ensure you partner with manufacturers that not only meet your quality standards but also align with your business goals.
By equipping you with the necessary knowledge and tools, this guide empowers you to navigate the complexities of the wire rope market confidently. Whether you are looking to enhance your supply chain efficiency or ensure safety in your operations, our insights will pave the way for successful procurement strategies tailored to your specific needs.
Understanding wire rope manufacturer Types and Variations
Type Name | Key Distinguishing Features | Primary B2B Applications | Brief Pros & Cons for Buyers |
---|---|---|---|
Standard Wire Rope | Composed of multiple strands twisted together; available in various diameters and materials. | Construction, mining, and maritime industries. | Pros: Versatile and widely available. Cons: May not be suitable for extreme conditions. |
Specialty Wire Rope | Tailored for specific applications; includes variations like corrosion-resistant and high-strength ropes. | Oil and gas, aerospace, and heavy lifting. | Pros: Customizable to meet specific needs. Cons: Higher cost and longer lead times. |
Coated Wire Rope | Features a protective coating (e.g., plastic or vinyl) to enhance durability and reduce wear. | Lifting equipment, cranes, and outdoor applications. | Pros: Increased lifespan and reduced maintenance. Cons: Potential for coating damage under heavy use. |
Braided Wire Rope | Made by interweaving multiple strands; offers flexibility and strength. | Rigging, marine applications, and transportation. | Pros: Excellent flexibility and resistance to kinking. Cons: More complex to manufacture and may be pricier. |
High-Performance Wire Rope | Engineered for extreme conditions; often made from advanced materials like composite fibers. | Heavy-duty lifting, mining, and construction. | Pros: Superior strength and lightweight. Cons: Limited availability and higher investment required. |
What Are the Characteristics of Standard Wire Rope?
Standard wire rope is the most commonly used type, featuring multiple strands twisted together to form a strong, flexible cable. It is available in various diameters and materials, making it suitable for a broad range of applications. B2B buyers should consider the specific requirements of their projects, such as load capacity and environmental conditions, when selecting standard wire rope. Its versatility makes it a go-to choice for industries like construction and mining, but its performance may be limited under extreme conditions.
How Do Specialty Wire Ropes Cater to Unique Needs?
Specialty wire ropes are designed for specific applications, including high-strength variants and those resistant to corrosion. These ropes are ideal for industries such as oil and gas, aerospace, and heavy lifting, where standard options may fall short. When purchasing specialty wire ropes, B2B buyers should assess the unique conditions their operations face, such as exposure to harsh chemicals or extreme temperatures. Although they offer tailored solutions, buyers should be prepared for potentially higher costs and longer lead times.
Why Choose Coated Wire Rope for Durability?
Coated wire rope incorporates a protective layer, such as plastic or vinyl, to enhance durability and reduce wear. This type is particularly advantageous in lifting equipment, cranes, and outdoor applications where exposure to the elements is a concern. For international B2B buyers, the increased lifespan and lower maintenance requirements of coated wire ropes can translate to long-term cost savings. However, it’s crucial to consider the potential for coating damage under heavy use, which may require periodic inspection and maintenance.
What Are the Benefits of Braided Wire Rope?
Braided wire rope is characterized by its unique interweaving of multiple strands, which provides excellent flexibility and strength. This type is often employed in rigging, marine applications, and transportation. B2B buyers should evaluate the specific needs of their operations, as braided wire rope is less prone to kinking, making it easier to handle. However, its more complex manufacturing process can result in higher costs, which buyers must factor into their overall budget.
How Does High-Performance Wire Rope Stand Out?
High-performance wire rope is engineered to withstand extreme conditions, often made from advanced materials like composite fibers. This type is primarily used in heavy-duty lifting, mining, and construction, where traditional ropes may not suffice. Buyers should consider the specific demands of their operations, as high-performance wire ropes offer superior strength and a lighter weight. However, the limited availability and higher investment required for these ropes may be a barrier for some businesses, making it essential to conduct thorough market research before purchasing.
Related Video: Incredible Manufacturing Process Of Industrial Wire Rope
Key Industrial Applications of wire rope manufacturer
Industry/Sector | Specific Application of wire rope manufacturer | Value/Benefit for the Business | Key Sourcing Considerations for this Application |
---|---|---|---|
Construction | Lifting and hoisting equipment for heavy materials | Increases efficiency in project timelines and reduces labor costs | Compliance with safety standards and load capacity requirements |
Mining | Cable systems for ore extraction and transportation | Enhances productivity and operational safety | Durability in harsh environments and resistance to wear and tear |
Marine and Offshore | Mooring lines and rigging for vessels | Ensures stability and safety of maritime operations | Corrosion resistance and compliance with marine regulations |
Oil and Gas | Rigging for drilling operations and material handling | Improves operational efficiency and safety in hazardous conditions | High tensile strength and reliability under extreme conditions |
Telecommunications | Support for aerial and underground cable installations | Facilitates reliable communication networks | Adaptability to environmental conditions and load requirements |
What Are the Key Industrial Applications of Wire Rope in Construction?
In the construction industry, wire ropes are essential for lifting and hoisting heavy materials, such as steel beams and concrete blocks. They streamline operations, significantly improving project timelines while reducing labor costs. Buyers in this sector must prioritize sourcing ropes that comply with stringent safety standards and possess adequate load capacity to meet specific project requirements.
How is Wire Rope Used in Mining Operations?
In mining, wire ropes are crucial for ore extraction and transportation systems. They enhance productivity by allowing for the efficient movement of heavy loads, while also ensuring operational safety in challenging environments. International buyers should focus on sourcing durable wire ropes that can withstand harsh conditions, including high wear and tear, to ensure longevity and reliability in their mining operations.
What Role Does Wire Rope Play in Marine and Offshore Industries?
Wire ropes are integral to marine and offshore operations, serving as mooring lines and rigging for vessels. They provide stability and safety in various maritime applications, from anchoring ships to supporting offshore platforms. When sourcing wire ropes for this sector, businesses must consider corrosion resistance and compliance with marine regulations to ensure their equipment remains functional and safe in salty, harsh environments.
Why is Wire Rope Important in Oil and Gas Industries?
In the oil and gas sector, wire ropes are used for rigging in drilling operations and material handling. Their role is vital in enhancing operational efficiency and safety, especially in hazardous environments. Buyers should seek wire ropes with high tensile strength and reliability, as these characteristics are critical for sustaining operations under extreme conditions typical in this industry.
How Does Wire Rope Support Telecommunications Infrastructure?
In telecommunications, wire ropes support aerial and underground cable installations, ensuring that communication networks remain reliable and effective. The adaptability of wire ropes to various environmental conditions and their ability to meet load requirements are essential factors for international B2B buyers. Selecting the right wire rope can significantly impact the reliability and efficiency of telecommunications infrastructure.
Related Video: Amazing Manufacturing Process Of Industrial Wire Rope | Incredible Fast Wire Rope Splice Methods
3 Common User Pain Points for ‘wire rope manufacturer’ & Their Solutions
Scenario 1: Quality Assurance in Wire Rope Manufacturing
The Problem:
B2B buyers often struggle with ensuring the quality of wire rope products. This challenge is particularly pronounced in regions like Africa and South America, where local suppliers may not meet international standards. Buyers face the risk of receiving subpar products that can lead to operational failures, safety hazards, and significant financial losses. The lack of uniformity in quality assurance processes among manufacturers can create confusion and mistrust, making it difficult for buyers to select a reliable supplier.
The Solution:
To mitigate quality issues, buyers should establish a thorough vetting process before engaging with wire rope manufacturers. Start by requesting certifications such as ISO 9001, which indicates adherence to international quality management standards. Additionally, consider conducting factory visits or audits to assess manufacturing practices and quality control measures firsthand. Implementing a trial order system can also be beneficial; purchasing a smaller batch initially allows buyers to evaluate the wire rope’s performance in real-world applications without committing to a large order. Finally, leverage technology by utilizing online platforms that provide reviews and ratings of manufacturers to gain insights into the reliability and quality of potential suppliers.
Scenario 2: Navigating Import Regulations for Wire Rope
The Problem:
For international B2B buyers, especially those in the Middle East and Europe, navigating complex import regulations can be a daunting task. Wire ropes, often classified under various trade categories, may encounter tariffs, customs documentation, and compliance issues that can delay shipments and inflate costs. This bureaucratic maze can lead to frustration and loss of business opportunities, particularly for buyers who are not familiar with local and international trade laws.
The Solution:
To effectively navigate import regulations, buyers should invest time in understanding the specific customs requirements of their region. Engaging a local customs broker can be invaluable; these professionals are familiar with import regulations and can help expedite the process by ensuring all paperwork is in order. Additionally, buyers should stay informed about any trade agreements or tariffs that may affect wire rope imports. Resources such as government trade websites or industry associations can provide up-to-date information. Developing a strong relationship with the wire rope manufacturer can also facilitate smoother transactions, as they may assist in providing the necessary documentation and guidance for customs clearance.
Scenario 3: Selecting the Right Type of Wire Rope for Specific Applications
The Problem:
Choosing the appropriate wire rope type for specific applications is a common pain point for B2B buyers. Different industries, from construction to marine, require various wire rope specifications, such as tensile strength, flexibility, and resistance to environmental factors. The challenge lies in understanding these requirements and ensuring that the selected wire rope meets the operational demands. Misjudgments in this selection process can lead to equipment failure, increased maintenance costs, and potential safety risks.
The Solution:
To make informed decisions, buyers should conduct a thorough needs assessment before selecting a wire rope. This involves understanding the specific application requirements, such as load capacity, environmental conditions, and any regulatory standards that must be met. Collaborating closely with the wire rope manufacturer is essential; experienced suppliers can provide valuable insights and recommendations based on their knowledge of materials and applications. Additionally, buyers should consider investing in training sessions or workshops offered by manufacturers to better understand the technical aspects of wire ropes. Utilizing tools like load calculators and engaging in discussions with industry peers can also enhance decision-making processes and ensure that the right type of wire rope is selected for the job.
Strategic Material Selection Guide for wire rope manufacturer
When selecting materials for wire rope manufacturing, international B2B buyers must consider various factors that influence performance, durability, and cost. This guide analyzes four common materials used in wire rope production, focusing on their properties, advantages, disadvantages, and specific considerations for buyers from Africa, South America, the Middle East, and Europe.
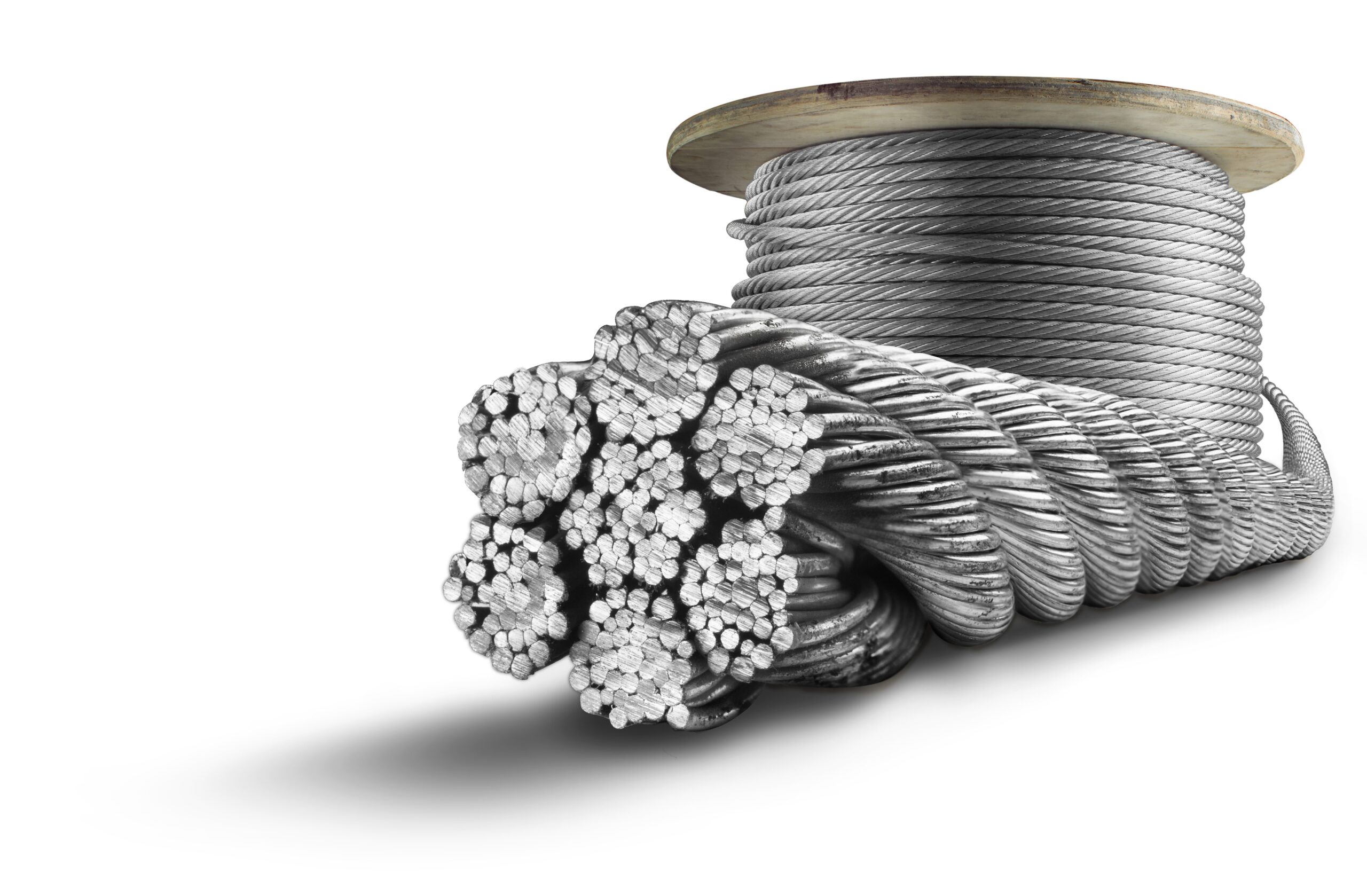
A stock image related to wire rope manufacturer.
What Are the Key Properties of Steel Wire Rope?
Steel is the most widely used material for wire ropes due to its excellent mechanical properties. It typically exhibits high tensile strength, making it suitable for heavy lifting applications. Steel wire ropes can withstand extreme temperatures and pressures, and they demonstrate good resistance to wear and fatigue. However, they are susceptible to corrosion, which can be a significant drawback in humid or marine environments.
Pros & Cons: Steel wire ropes are durable and cost-effective, making them ideal for various applications, including construction and mining. However, their susceptibility to corrosion can lead to increased maintenance costs and reduced lifespan, particularly in corrosive environments.
Impact on Application: Steel wire ropes are compatible with a wide range of media, including water and oil. However, they may not perform well in environments with high saline content unless specifically treated or coated.
Considerations for International Buyers: Buyers should ensure compliance with international standards such as ASTM A1023 for steel wire ropes. In regions like Europe, adherence to EN standards is crucial, while buyers in Africa and South America should consider local regulations regarding material specifications.
How Does Synthetic Fiber Compare to Steel Wire Rope?
Synthetic fibers, such as polyester and nylon, are increasingly popular in wire rope manufacturing due to their lightweight nature and excellent corrosion resistance. These materials can operate effectively in a wide temperature range and are less prone to fatigue compared to steel.
Pros & Cons: Synthetic fiber ropes are highly durable and resistant to UV light and chemicals, making them suitable for marine and outdoor applications. However, they generally have lower tensile strength compared to steel, which may limit their use in heavy lifting scenarios.
Impact on Application: Synthetic ropes are compatible with various media, including water and chemicals, making them versatile for different industries. Their lightweight nature also allows for easier handling and installation.
Considerations for International Buyers: Buyers should look for compliance with ASTM D4269 for polyester ropes or similar standards. In Europe, EN 1492-1 is a relevant standard for lifting applications. Buyers in the Middle East should consider the environmental conditions that may affect the longevity of synthetic materials.
What Are the Benefits of Using Galvanized Wire Rope?
Galvanized steel wire ropes are coated with a layer of zinc to enhance corrosion resistance. This makes them suitable for outdoor applications where exposure to moisture and chemicals is a concern.
Pros & Cons: The primary advantage of galvanized wire ropes is their enhanced durability in corrosive environments. However, the galvanization process can increase manufacturing complexity and costs.
Impact on Application: Galvanized wire ropes are ideal for applications in marine environments or industries where exposure to chemicals is prevalent. They maintain their strength while providing an additional layer of protection against corrosion.
Considerations for International Buyers: Compliance with ASTM A475 for galvanized steel wire ropes is essential. Buyers from regions like South America and Africa should ensure that the galvanization meets local standards to avoid premature degradation.
Why Choose Stainless Steel Wire Rope for High-Performance Applications?
Stainless steel wire ropes offer superior corrosion resistance and are ideal for high-performance applications. They maintain their strength and integrity in extreme environments, including high temperatures and corrosive media.
Pros & Cons: The primary advantage of stainless steel wire ropes is their exceptional durability and resistance to rust and corrosion. However, they are more expensive than other materials, which may be a limiting factor for some buyers.
Impact on Application: Stainless steel wire ropes are suitable for use in marine, chemical, and high-temperature environments, ensuring reliability and safety in critical applications.
Considerations for International Buyers: Buyers should ensure compliance with ASTM A313 for stainless steel wire ropes. In Europe, EN 10088-3 outlines the requirements for stainless steel materials, which is vital for maintaining quality standards.
Summary of Material Selection for Wire Rope Manufacturing
Material | Typical Use Case for wire rope manufacturer | Key Advantage | Key Disadvantage/Limitation | Relative Cost (Low/Med/High) |
---|---|---|---|---|
Steel | Construction, mining | High tensile strength | Susceptible to corrosion | Medium |
Synthetic Fiber | Marine, outdoor applications | Lightweight and corrosion-resistant | Lower tensile strength | Medium |
Galvanized Steel | Marine, chemical industries | Enhanced corrosion resistance | Increased manufacturing complexity | Medium to High |
Stainless Steel | High-performance, critical applications | Superior durability and corrosion resistance | Higher cost | High |
This guide provides a strategic framework for international B2B buyers to make informed decisions regarding material selection for wire rope manufacturing, ensuring compliance and suitability for their specific applications.
In-depth Look: Manufacturing Processes and Quality Assurance for wire rope manufacturer
What Are the Key Stages in the Manufacturing Process of Wire Rope?
The manufacturing process of wire rope involves several critical stages, each designed to ensure the final product meets the stringent quality and performance standards required by various industries. The primary stages include material preparation, forming, assembly, and finishing.
-
Material Preparation: The process begins with selecting high-quality raw materials, typically high-carbon steel wire. The wire undergoes various treatments, including annealing, to enhance its ductility and tensile strength. During this stage, manufacturers also perform metallurgical analysis to ensure that the material composition meets industry standards.
-
Forming: In this stage, the prepared wire is drawn through dies to achieve the desired diameter. This process often involves multiple passes to ensure precision. Wire drawing is followed by the stranding process, where multiple wires are twisted together to form strands. The number of strands and the way they are twisted can vary, affecting the wire rope’s flexibility and load-bearing capacity.
-
Assembly: After forming the strands, they are assembled into a wire rope. This involves laying the strands around a core, which can be a fiber or steel core, depending on the application. The assembly process is critical, as it impacts the overall strength and performance of the wire rope.
-
Finishing: The final stage involves applying protective coatings, such as galvanization or polymer coatings, to enhance corrosion resistance. The wire rope is then cut to specified lengths and undergoes a final inspection before packaging. This stage ensures that the wire rope is ready for transportation and use in demanding environments.
How is Quality Assurance Integrated into Wire Rope Manufacturing?
Quality assurance (QA) is a pivotal aspect of the wire rope manufacturing process, ensuring that each product meets the required safety and performance standards. International and industry-specific standards play a crucial role in shaping these QA processes.
-
International Standards: Many wire rope manufacturers adhere to ISO 9001, which outlines the requirements for a quality management system. This certification demonstrates a commitment to quality and continuous improvement. Compliance with ISO standards also facilitates easier international trade and acceptance in various markets.
-
Industry-Specific Standards: In addition to ISO 9001, wire rope manufacturers may need to comply with specific standards such as CE marking for products sold in the European market or API specifications for those used in the oil and gas industry. These certifications ensure that the wire ropes can withstand the specific conditions of their intended applications.
What are the Quality Control Checkpoints in Wire Rope Production?
Quality control (QC) checkpoints are integrated throughout the manufacturing process to identify and rectify defects early on. The typical QC checkpoints include:
-
Incoming Quality Control (IQC): At the start of the manufacturing process, incoming materials are inspected for quality and compliance with specifications. This stage is crucial, as the quality of the raw materials directly impacts the final product.
-
In-Process Quality Control (IPQC): During the manufacturing stages, periodic checks are performed to monitor the dimensions, tensile strength, and other critical parameters. This real-time monitoring helps detect deviations from quality standards before they propagate through the production process.
-
Final Quality Control (FQC): Once the wire ropes are completed, they undergo a final inspection. This includes testing for tensile strength, flexibility, and corrosion resistance. Manufacturers often use standardized tests, such as the breaking load test, to ensure the ropes meet performance expectations.
Which Testing Methods Are Commonly Used in Wire Rope Quality Assurance?
Several testing methods are employed to ensure the quality and reliability of wire ropes. These methods include:
-
Tensile Testing: This test measures the maximum load a wire rope can bear before breaking. It is crucial for ensuring that the rope can handle the expected loads in its application.
-
Bending Fatigue Testing: This method evaluates how well the wire rope can withstand repeated bending, which is essential for applications where the rope will be frequently moved or flexed.
-
Corrosion Resistance Testing: Wire ropes are often exposed to harsh environments. Tests such as salt spray tests are conducted to determine the effectiveness of protective coatings against corrosion.
How Can B2B Buyers Verify Supplier Quality Control?
For B2B buyers, particularly those from Africa, South America, the Middle East, and Europe, verifying a supplier’s quality control practices is essential. Here are actionable steps to ensure that suppliers meet quality standards:
-
Supplier Audits: Conducting audits of potential suppliers can provide insight into their manufacturing processes and QC practices. This can include reviewing their certifications, quality management systems, and production capabilities.
-
Requesting Quality Reports: Buyers should request detailed quality reports that outline the QC measures taken during production, including test results and compliance with relevant standards.
-
Third-Party Inspections: Engaging third-party inspection services can provide an unbiased assessment of a supplier’s quality control processes. This is particularly useful for buyers who may not have the resources to conduct thorough inspections themselves.
What Are the Quality Control Nuances for International B2B Buyers?
International B2B buyers must navigate various quality control nuances when sourcing wire ropes from different regions. Here are some considerations:
-
Regulatory Compliance: Different countries may have specific regulatory requirements for wire ropes. Understanding these regulations is essential to ensure compliance and avoid legal issues.
-
Cultural Differences: Quality expectations may vary across regions. Buyers should be aware of these differences and communicate their quality requirements clearly to suppliers.
-
Logistics and Supply Chain Considerations: The quality of wire ropes can be affected by transportation conditions. Buyers should work closely with suppliers to ensure that the products are adequately packaged and protected during shipping.
By understanding these manufacturing processes and quality assurance measures, B2B buyers can make informed decisions when sourcing wire ropes, ensuring they partner with reliable manufacturers who meet their quality expectations.
Practical Sourcing Guide: A Step-by-Step Checklist for ‘wire rope manufacturer’
This guide aims to provide international B2B buyers with a practical sourcing checklist for procuring wire rope manufacturers. By following these steps, buyers can ensure they select a reliable supplier that meets their specific needs and standards.
Step 1: Define Your Technical Specifications
Before reaching out to potential suppliers, clarify your technical requirements. Determine the type of wire rope needed, including diameter, material, and intended use. Specificity in your requirements can prevent misunderstandings and ensure that the manufacturer can meet your expectations.
- Consider factors like tensile strength, corrosion resistance, and compliance with industry standards (e.g., ISO, ASTM).
- Document your requirements in detail to facilitate accurate quotes from suppliers.
Step 2: Research and Shortlist Suppliers
Compile a list of potential wire rope manufacturers based on your specifications. Utilize online directories, industry associations, and trade shows to identify suppliers with a solid reputation.
- Look for companies with positive reviews and a proven track record in your industry.
- Pay attention to suppliers that specialize in the type of wire rope you require.
Step 3: Evaluate Potential Suppliers
Before committing to any supplier, conduct a thorough evaluation. Request detailed company profiles, product catalogs, and case studies showcasing their experience.
- Ask for references from other businesses in your region or industry to gauge reliability.
- Verify their capacity to handle your order size and any custom requirements.
Step 4: ✅ Verify Supplier Certifications
Ensure that the manufacturers you are considering possess relevant certifications. This is critical for compliance with international quality standards and regulations.
- Look for certifications such as ISO 9001 for quality management and ISO 14001 for environmental management.
- Confirm that their products meet regional safety and quality regulations pertinent to your market.
Step 5: Request Samples and Test Quality
Before finalizing your purchase, request samples of the wire rope. Testing samples can provide insights into the quality and suitability of the product for your applications.
- Evaluate the samples for durability, flexibility, and compliance with your specifications.
- Consider conducting stress tests if applicable, especially for high-stakes applications like construction or marine use.
Step 6: Negotiate Terms and Conditions
Once you have identified a suitable supplier, engage in negotiations regarding pricing, payment terms, and delivery schedules. Clear communication at this stage can prevent future disputes.
- Discuss bulk purchase discounts and warranty conditions.
- Ensure that all agreements are documented to provide clarity and protection for both parties.
Step 7: Establish Communication and Support Channels
After selecting a supplier, establish clear communication channels for ongoing support. This is essential for addressing any future issues or inquiries regarding your orders.
- Define points of contact for technical support and customer service.
- Regularly update your supplier on your needs and any changes to your project specifications.
By following these actionable steps, international B2B buyers can effectively navigate the sourcing process for wire rope manufacturers, ensuring they make informed decisions that align with their operational goals.
Comprehensive Cost and Pricing Analysis for wire rope manufacturer Sourcing
What Are the Key Cost Components in Wire Rope Manufacturing?
Understanding the cost structure of wire rope manufacturing is crucial for international B2B buyers. The primary cost components include:
-
Materials: The quality and type of raw materials significantly influence pricing. Steel wire, coatings, and lubricants are essential inputs, with prices fluctuating based on global demand and local market conditions. Buyers should consider sourcing from regions with lower raw material costs, or negotiate bulk purchasing agreements to reduce material expenses.
-
Labor: Labor costs can vary widely by region. In countries with higher labor standards, such as those in Europe, costs may be greater than in regions like South America or Africa. Assessing the skill level and productivity of the workforce can help buyers understand labor implications on overall pricing.
-
Manufacturing Overhead: This includes costs related to facilities, utilities, and administration. Efficient manufacturing processes can lower overhead, so it’s beneficial to partner with manufacturers who invest in modern equipment and lean production methodologies.
-
Tooling: The initial investment in tooling can be substantial, especially for custom wire rope specifications. Buyers should inquire about tooling costs and whether they can amortize these costs over larger production runs to achieve better pricing.
-
Quality Control (QC): Stringent QC processes ensure product reliability but can add to costs. Buyers should weigh the benefits of higher QC standards against the potential risks of lower-quality products, especially in critical applications like construction or mining.
-
Logistics: Shipping costs can significantly impact the total price, particularly for international transactions. Factors such as distance, shipping mode (air vs. sea), and customs duties should be considered. Collaborating with suppliers who have efficient logistics can mitigate these costs.
-
Margin: Suppliers typically add a margin to cover their costs and profit. Understanding the market average margins for wire rope can help buyers negotiate better prices.
How Do Price Influencers Affect Wire Rope Sourcing?
Several factors can influence the pricing of wire rope:
-
Volume and Minimum Order Quantity (MOQ): Larger orders often lead to lower per-unit costs. Buyers should assess their needs and consider bulk purchasing to leverage volume discounts.
-
Specifications and Customization: Custom wire rope solutions may incur higher costs due to unique manufacturing requirements. Buyers should clearly define specifications to avoid unnecessary alterations that could inflate prices.
-
Material Quality and Certifications: Premium materials and certifications (like ISO or CE) can raise costs but are essential for certain applications. Buyers in Europe, for example, may prioritize certifications for compliance with safety regulations.
-
Supplier Factors: The reputation and reliability of a supplier can influence pricing. Established manufacturers may charge more due to their proven track record, while lesser-known suppliers may offer lower prices but with higher risk.
-
Incoterms: Understanding shipping terms is vital. Incoterms dictate who bears the cost at various stages of transportation. Buyers should clarify these terms to avoid unexpected charges.
What Are the Best Buyer Tips for Cost Efficiency in Wire Rope Sourcing?
International B2B buyers should adopt strategic approaches to enhance cost efficiency:
-
Negotiate Effectively: Develop strong negotiation skills to secure favorable pricing. Understanding market trends and competitor pricing can provide leverage during discussions.
-
Consider Total Cost of Ownership (TCO): Evaluate not just the purchase price, but also maintenance, durability, and potential downtime costs associated with the wire rope. A higher upfront cost may result in lower TCO if the product lasts longer and requires less maintenance.
-
Pricing Nuances for International Buyers: Different regions have varying pricing structures due to local economic conditions. For instance, buyers from Africa may face different cost challenges than those from Europe. Understanding these nuances can help buyers make informed decisions and avoid pitfalls.
-
Disclaimer for Indicative Prices: Always remember that prices can fluctuate based on market conditions. It’s advisable to request current quotations from multiple suppliers to ensure competitive pricing.
By comprehensively analyzing these cost components and pricing influencers, B2B buyers can make informed sourcing decisions that optimize their procurement strategies for wire rope manufacturing.
Alternatives Analysis: Comparing wire rope manufacturer With Other Solutions
Understanding Alternatives to Wire Rope Manufacturing
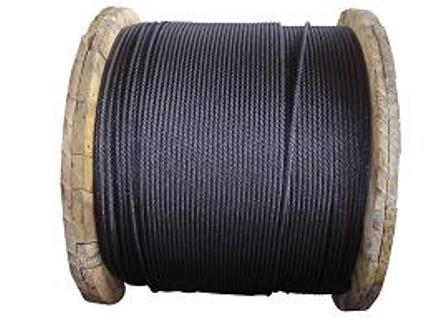
A stock image related to wire rope manufacturer.
In the realm of industrial lifting and rigging solutions, wire ropes have long been a staple due to their strength and versatility. However, buyers should consider various alternatives that may offer distinct advantages depending on specific operational needs. This section explores several viable alternatives to traditional wire rope manufacturing, enabling B2B buyers to make informed decisions that align with their operational requirements and budget constraints.
Comparison Aspect | Wire Rope Manufacturer | Synthetic Rope | Chain Solutions |
---|---|---|---|
Performance | High tensile strength; fatigue-resistant | Good tensile strength; lightweight | Very strong; less flexible |
Cost | Moderate to high initial cost; long-term durability | Generally lower initial cost; may require more frequent replacement | Moderate initial cost; maintenance can add up |
Ease of Implementation | Requires specialized installation; heavy | Easier to handle and install; lightweight | Requires heavy-duty equipment for installation |
Maintenance | Low maintenance; corrosion resistant with proper care | Moderate maintenance; sensitive to UV and chemicals | High maintenance; prone to wear and tear |
Best Use Case | Heavy-duty applications; mining, construction | Marine applications; recreational use | Industrial lifting; construction sites |
What are the Advantages and Disadvantages of Synthetic Rope?
Synthetic Rope: Synthetic ropes, made from materials like nylon or polyester, are notable for their lightweight and flexibility. They are easy to handle, making them ideal for applications where weight is a concern, such as marine and recreational settings. However, synthetic ropes can be sensitive to environmental factors like UV radiation and chemicals, which may affect their lifespan. While they generally have a lower initial cost, their durability may not match that of wire ropes in heavy-duty applications, leading to more frequent replacements.
How Do Chain Solutions Compare to Wire Ropes?
Chain Solutions: Chains are another alternative that offers exceptional strength and durability for heavy lifting tasks. They are particularly well-suited for industrial applications and environments where high load-bearing capacity is crucial. However, chains can be cumbersome, requiring heavy-duty equipment for installation. Maintenance can be more demanding, as chains are prone to wear and need regular inspection to ensure safety. Additionally, they offer less flexibility compared to wire ropes, which may limit their application in certain scenarios.
Choosing the Right Solution for Your Needs
When determining the best solution for your specific needs, consider the unique demands of your industry and operational environment. Wire ropes are often the go-to choice for heavy-duty applications requiring high durability and performance. However, if your operations prioritize weight and ease of handling, synthetic ropes may be more suitable. Meanwhile, for industries focused on maximum strength and durability, chain solutions could be the preferred option, despite their maintenance demands.
Ultimately, the decision should align with your operational goals, budget, and the specific conditions under which the lifting equipment will be used. Engaging with suppliers and industry experts can also provide invaluable insights, ensuring you choose the most efficient and cost-effective solution for your business.
Essential Technical Properties and Trade Terminology for wire rope manufacturer
Understanding the technical specifications and trade terminology associated with wire rope manufacturing is essential for B2B buyers looking to make informed purchasing decisions. This guide outlines the critical properties of wire ropes as well as common industry terms that facilitate effective communication between manufacturers and buyers.
What Are the Key Technical Properties of Wire Rope?
1. Material Grade: Why Is It Important for Performance?
Wire ropes are typically made from carbon steel, stainless steel, or other specialized alloys. The material grade directly affects the rope’s strength, flexibility, and corrosion resistance. For buyers, selecting the appropriate material grade ensures that the wire rope meets the specific demands of their applications, whether in construction, mining, or maritime industries.
2. Rope Diameter: How Does It Affect Load Capacity?
The diameter of the wire rope is a critical factor that influences its load-bearing capacity. Thicker ropes can handle heavier loads but may also be less flexible. Buyers should consider the intended application and the expected load to select the right diameter, balancing strength with flexibility.
3. Construction Type: What Are the Different Configurations?
Wire ropes can be constructed in various configurations, such as 7×19, 6×36, or 8×25. Each configuration denotes the number of strands and wires, affecting the rope’s flexibility, strength, and fatigue resistance. Understanding these configurations helps buyers choose a wire rope that best suits their operational needs.
4. Tolerance: Why Is Precision Crucial in Wire Rope Manufacturing?
Tolerance refers to the allowable deviation in the wire rope’s dimensions, which can impact performance. Higher tolerance levels ensure consistency in quality, reducing the risk of failure during use. For B2B buyers, specifying tolerance levels in their orders can lead to better reliability and safety in their applications.
5. Breaking Strength: How to Assess Safety Margins?
Breaking strength is the maximum load a wire rope can withstand before failure. It is crucial for buyers to understand this specification to ensure that the selected wire rope can safely handle the required loads, taking into account safety margins and operational conditions.
What Are Common Trade Terms in Wire Rope Manufacturing?
1. What Does OEM Mean in Wire Rope Manufacturing?
OEM stands for Original Equipment Manufacturer. In the context of wire rope, it refers to companies that produce wire ropes for other brands or manufacturers. Understanding this term helps buyers identify reputable suppliers who can provide quality products tailored to specific requirements.
2. What Is MOQ and Why Does It Matter?
MOQ stands for Minimum Order Quantity. This term indicates the smallest quantity of wire rope that a manufacturer is willing to sell. For B2B buyers, knowing the MOQ is essential for budgeting and inventory management, especially when sourcing from international suppliers.
3. How to Use RFQ Effectively?
RFQ, or Request for Quotation, is a formal process where buyers request pricing and terms from suppliers. Utilizing RFQs can streamline the procurement process, allowing buyers to compare offers and negotiate better terms, ultimately leading to cost savings.
4. What Are Incoterms and Their Relevance in International Trade?
Incoterms, or International Commercial Terms, define the responsibilities of buyers and sellers in international transactions. Understanding these terms helps B2B buyers clarify shipping costs, insurance, and delivery responsibilities, reducing the risk of misunderstandings in cross-border transactions.
5. What Is Lead Time and Why Should Buyers Consider It?
Lead time refers to the time taken from placing an order to delivery. For B2B buyers, considering lead times is crucial for project planning and ensuring timely availability of materials. Long lead times can disrupt operations, making it vital to choose suppliers with reliable delivery schedules.
By grasping these technical properties and trade terms, international B2B buyers can enhance their purchasing strategies, ensuring they select the right wire ropes for their specific needs while fostering smoother communication with manufacturers.
Navigating Market Dynamics and Sourcing Trends in the wire rope manufacturer Sector
What are the Key Market Dynamics and Trends Affecting the Wire Rope Manufacturer Sector?
The wire rope manufacturing sector is experiencing a transformative phase influenced by various global drivers. One significant trend is the increasing demand for high-performance wire ropes across industries such as construction, mining, and oil and gas. This surge is driven by infrastructure development in emerging markets, particularly in Africa and South America, where construction projects are on the rise. Additionally, technological advancements, such as the integration of IoT in wire rope monitoring systems, are reshaping sourcing strategies. These innovations enable manufacturers to offer enhanced product tracking and performance monitoring, thereby increasing operational efficiency and safety for international buyers.
Moreover, the trend towards digitalization is becoming more pronounced. B2B buyers are increasingly seeking suppliers that leverage e-commerce platforms and digital marketplaces to streamline procurement processes. This shift not only enhances accessibility for international buyers, particularly in regions like the Middle East and Europe, but also promotes transparency in the supply chain. Additionally, sustainability is becoming a core consideration, with buyers favoring manufacturers who adopt eco-friendly practices and materials. As a result, wire rope manufacturers are aligning their production processes with sustainability goals, which resonates well with conscientious buyers across various regions.
How is Sustainability Impacting the Wire Rope Manufacturing Sector?
Sustainability is a critical concern for international B2B buyers, and the wire rope manufacturing sector is no exception. The environmental impact of production processes, including energy consumption and waste generation, is under scrutiny. Buyers are increasingly prioritizing suppliers who adhere to sustainable practices, thus driving manufacturers to evaluate their operations critically. This includes adopting energy-efficient technologies and reducing carbon footprints throughout the production cycle.
Ethical sourcing is another focal point. B2B buyers are looking for manufacturers that maintain responsible sourcing practices, ensuring that raw materials are obtained from suppliers who comply with environmental regulations and labor standards. Certifications such as ISO 14001 for environmental management systems or certifications related to responsible sourcing can enhance a manufacturer’s credibility. Furthermore, the utilization of ‘green’ materials—such as recycled steel for wire ropes—can significantly appeal to environmentally conscious buyers in regions like Europe and South America, where sustainability regulations are stringent.
What is the Historical Context of Wire Rope Manufacturing?
The evolution of wire rope manufacturing can be traced back to the mid-19th century, primarily driven by the industrial revolution. Initially used in mining and lifting applications, wire ropes have since diversified into various sectors, including construction and maritime. Over the decades, advancements in metallurgy and manufacturing processes have significantly improved the performance and durability of wire ropes.
As industries grew, so did the complexity of wire rope applications. The introduction of specialized coatings and treatments has allowed for increased resistance to corrosion and wear, catering to the diverse needs of international buyers. Today, wire rope manufacturers are not only focused on traditional applications but are also innovating to meet the demands of modern industries, ensuring that they remain competitive in a global market that is increasingly leaning towards sustainability and ethical practices.
By understanding these dynamics, B2B buyers can make informed sourcing decisions that align with their operational needs and corporate values.
Frequently Asked Questions (FAQs) for B2B Buyers of wire rope manufacturer
-
How do I assess the quality of wire ropes from manufacturers?
When evaluating the quality of wire ropes, consider several critical factors: certification standards (such as ISO or ASTM), material specifications (like steel grade), and testing procedures. Request samples to conduct independent tests for tensile strength, fatigue resistance, and corrosion resistance. Additionally, review the manufacturer’s history and reputation in the industry. Engaging with previous clients can also provide insights into the quality and reliability of the products offered. -
What are the key factors to consider when selecting a wire rope manufacturer?
Key factors include the manufacturer’s experience in the industry, production capacity, range of products, and customization options. Verify their certifications and compliance with international standards. It’s also essential to assess their supply chain reliability and logistics capabilities, especially for international shipping. Lastly, consider their customer service and after-sales support, as these can significantly impact your purchasing experience. -
What customization options are available for wire ropes?
Most wire rope manufacturers offer a variety of customization options, including diameter, length, construction (number of strands and wires), and coating (galvanized or non-galvanized). Some manufacturers may also provide specialized designs for unique applications, such as marine or heavy lifting. It’s advisable to communicate your specific requirements early in the sourcing process to ensure that the manufacturer can meet your needs. -
What is the minimum order quantity (MOQ) for wire ropes?
The minimum order quantity can vary significantly between manufacturers, typically ranging from a few hundred meters to several tons. Factors influencing MOQ include the type of wire rope, production processes, and inventory levels. For international buyers, it’s beneficial to negotiate MOQs, especially if you are looking to test the market with smaller orders initially. Discussing your long-term purchasing plans with the manufacturer can also lead to more favorable terms. -
What payment terms should I expect when dealing with wire rope suppliers?
Payment terms can vary widely among manufacturers. Common practices include upfront payments, partial payments upon order confirmation, and balance payments before shipment. For international transactions, letters of credit and escrow services are often used to mitigate risk. Always clarify payment terms and conditions before placing an order and consider negotiating terms that provide security for both parties. -
How can I ensure timely delivery when sourcing wire ropes internationally?
To ensure timely delivery, establish clear communication with the manufacturer regarding lead times and shipping schedules. It’s crucial to understand their production capacity and current order backlog. Work with logistics partners who have experience in international shipping and customs clearance to avoid delays. Including penalties for late delivery in your contract can also incentivize the manufacturer to adhere to agreed timelines. -
What are the best practices for vetting wire rope suppliers?
Begin by researching potential suppliers through industry directories and trade shows. Request references and conduct background checks to verify their legitimacy and financial stability. Assess their production capabilities through factory visits or virtual tours. Additionally, evaluate their compliance with international quality standards and certifications. Utilizing third-party auditing services can also provide an objective assessment of the supplier’s operations. -
What quality assurance measures should I expect from a wire rope manufacturer?
Reputable manufacturers implement rigorous quality assurance protocols, including raw material inspections, in-process quality checks, and final product testing. Look for manufacturers that offer detailed quality documentation, such as certificates of compliance and test reports. Regular audits by third-party inspectors can also enhance trust in the manufacturer’s quality assurance processes. Inquire about their approach to addressing quality issues and customer complaints, which reflects their commitment to product excellence.
Important Disclaimer & Terms of Use
⚠️ Important Disclaimer
The information provided in this guide, including content regarding manufacturers, technical specifications, and market analysis, is for informational and educational purposes only. It does not constitute professional procurement advice, financial advice, or legal advice.
While we have made every effort to ensure the accuracy and timeliness of the information, we are not responsible for any errors, omissions, or outdated information. Market conditions, company details, and technical standards are subject to change.
B2B buyers must conduct their own independent and thorough due diligence before making any purchasing decisions. This includes contacting suppliers directly, verifying certifications, requesting samples, and seeking professional consultation. The risk of relying on any information in this guide is borne solely by the reader.
Strategic Sourcing Conclusion and Outlook for wire rope manufacturer
In the ever-evolving landscape of wire rope manufacturing, strategic sourcing emerges as a vital component for international B2B buyers. By prioritizing quality, sustainability, and supplier reliability, companies across Africa, South America, the Middle East, and Europe can effectively mitigate risks and enhance operational efficiency. Engaging with manufacturers who prioritize innovation and compliance with international standards not only ensures product longevity but also fosters long-term partnerships that can lead to cost savings and improved service delivery.
What are the key benefits of strategic sourcing for wire rope procurement? By leveraging data-driven decision-making and focusing on supplier capabilities, businesses can navigate market fluctuations and secure competitive pricing. Establishing a clear framework for evaluating suppliers based on quality, lead times, and service levels is essential for optimizing procurement strategies.
As we look ahead, the demand for high-performance wire ropes is poised to grow, driven by advancements in technology and increased infrastructure projects. B2B buyers are encouraged to stay informed about market trends and to proactively engage with manufacturers that align with their strategic goals. Embracing a collaborative approach in sourcing will not only enhance supply chain resilience but also position companies for success in a competitive global marketplace.