Improve Quality: The Ultimate Work Glove Manufacturer Guide (2025)
Introduction: Navigating the Global Market for work glove manufacturer
In today’s global market, sourcing high-quality work gloves can pose significant challenges for B2B buyers, particularly when navigating diverse supplier landscapes across regions such as Africa, South America, the Middle East, and Europe. With varying standards, materials, and safety regulations, the process of selecting a reliable work glove manufacturer requires careful consideration and strategic planning. This guide aims to equip international buyers with the insights necessary to make informed purchasing decisions, ensuring they find the right gloves to meet their specific industry needs.
Our comprehensive exploration covers various types of work gloves, including cut-resistant, chemical-resistant, and insulated options, tailored for different applications from construction to medical use. We delve into critical aspects such as supplier vetting processes, highlighting essential criteria to assess quality and reliability. Additionally, the guide provides an overview of cost factors and pricing structures, enabling buyers to effectively budget for their procurement needs.
By leveraging the information presented in this guide, international B2B buyers can streamline their sourcing processes, mitigate risks, and foster successful partnerships with reputable manufacturers. Whether you are a buyer in the bustling markets of Brazil or the UAE, this resource is designed to empower you with the knowledge and tools needed to navigate the complexities of the work glove manufacturing landscape.
Understanding work glove manufacturer Types and Variations
Type Name | Key Distinguishing Features | Primary B2B Applications | Brief Pros & Cons for Buyers |
---|---|---|---|
Leather Work Gloves | High durability, excellent grip, and abrasion resistance | Construction, manufacturing, and agriculture | Pros: Long-lasting, good protection. Cons: Higher cost, less flexibility. |
Cut-Resistant Gloves | Made with materials like Kevlar or Dyneema, designed to resist cuts | Metal fabrication, glass handling, woodworking | Pros: Enhanced safety, compliance with regulations. Cons: Can be heavier and less breathable. |
Chemical-Resistant Gloves | Specialized coatings for protection against chemicals | Chemical processing, janitorial services, laboratories | Pros: Protects against hazardous materials. Cons: Limited dexterity, can be expensive. |
Thermal Insulated Gloves | Insulation for extreme temperatures, often lined with materials like Thinsulate | Cold storage, outdoor work, food processing | Pros: Keeps hands warm, suitable for cold environments. Cons: Reduced tactile sensitivity. |
Disposable Gloves | Made from latex, vinyl, or nitrile, designed for single use | Healthcare, food service, cleaning | Pros: Cost-effective, hygienic, and easy to use. Cons: Limited durability, not suitable for heavy-duty tasks. |
What are the characteristics and suitability of leather work gloves for B2B buyers?
Leather work gloves are renowned for their durability and excellent grip, making them ideal for high-impact environments such as construction, manufacturing, and agriculture. The natural material provides a good level of abrasion resistance and can withstand rough handling, which is crucial in demanding tasks. B2B buyers should consider leather gloves for long-term use, especially in industries where hand protection is non-negotiable. However, the higher upfront cost and reduced flexibility compared to synthetic options may be a drawback for some businesses.
How do cut-resistant gloves enhance safety in B2B applications?
Cut-resistant gloves are engineered with advanced materials like Kevlar or Dyneema, which provide superior protection against cuts and lacerations. These gloves are particularly suited for industries such as metal fabrication, glass handling, and woodworking, where sharp objects are commonplace. For B2B buyers, the investment in cut-resistant gloves can significantly reduce workplace injuries and comply with safety regulations. However, they may come at a higher price point and could be heavier, potentially affecting worker comfort during extended use.
Why are chemical-resistant gloves crucial for certain industries?
Chemical-resistant gloves are specifically designed with specialized coatings to protect workers from hazardous substances. They are essential in sectors like chemical processing, janitorial services, and laboratories, where exposure to harmful materials is frequent. B2B buyers must evaluate the specific chemicals their workers will encounter when selecting these gloves. While they offer vital protection, the trade-off often includes reduced dexterity and a higher price, which could impact budget considerations.
In what scenarios are thermal insulated gloves necessary for B2B buyers?
Thermal insulated gloves are critical for operations in extreme cold environments, such as cold storage facilities, outdoor work, and food processing. These gloves often feature insulation materials like Thinsulate, providing warmth without sacrificing too much dexterity. B2B buyers in industries that expose workers to low temperatures should prioritize these gloves to ensure safety and comfort. However, it’s essential to note that while they provide warmth, they can limit tactile sensitivity, which may affect precision tasks.
How do disposable gloves serve various B2B industries effectively?
Disposable gloves are made from materials like latex, vinyl, or nitrile and are intended for single-use applications. They are widely used in healthcare, food service, and cleaning industries due to their cost-effectiveness and hygienic properties. For B2B buyers, the convenience of disposable gloves makes them an attractive option for tasks that require frequent changes and high levels of hygiene. However, their limited durability means they are not suitable for heavy-duty applications, which should be a consideration when making purchasing decisions.
Related Video: Coated Work Gloves Mass Production Factory. Korean Work Glove Manufacturing Process
Key Industrial Applications of work glove manufacturer
Industry/Sector | Specific Application of Work Glove Manufacturer | Value/Benefit for the Business | Key Sourcing Considerations for this Application |
---|---|---|---|
Construction | Safety gloves for heavy-duty tasks | Reduces workplace injuries, enhances worker safety | Compliance with local safety regulations, durability |
Manufacturing | Cut-resistant gloves for assembly line work | Protects workers from cuts, improves productivity | Material quality, comfort, and ergonomic design |
Oil & Gas | Chemical-resistant gloves for handling materials | Protects against hazardous substances, ensures safety | Compliance with industry standards, resistance to specific chemicals |
Agriculture | Protective gloves for handling chemicals | Reduces risk of chemical exposure, improves safety | Sourcing from certified manufacturers, comfort in wet conditions |
Logistics and Warehousing | General-purpose gloves for material handling | Enhances grip and reduces hand fatigue | Cost-effectiveness, availability in bulk, compatibility with other PPE |
How Are Work Gloves Used in the Construction Industry?
In the construction sector, work gloves are essential for protecting workers during heavy-duty tasks. These gloves are designed to withstand wear and tear while providing superior grip and dexterity. By utilizing high-quality safety gloves, businesses can significantly reduce workplace injuries, thus enhancing overall safety and productivity. International buyers should prioritize sourcing gloves that comply with local safety regulations and standards, ensuring that they meet the specific needs of their workforce.
What Are the Benefits of Cut-Resistant Gloves in Manufacturing?
In manufacturing environments, cut-resistant gloves are vital for workers on assembly lines where sharp objects are prevalent. These gloves not only protect employees from cuts and lacerations but also help maintain productivity by allowing for precise movements. For B2B buyers in this sector, it is crucial to consider the material quality, comfort, and ergonomic design of gloves to ensure that they meet the demanding requirements of manufacturing processes, especially in regions like Europe and South America where regulations can vary.
How Do Chemical-Resistant Gloves Enhance Safety in Oil & Gas?
The oil and gas industry frequently requires handling hazardous materials, making chemical-resistant gloves indispensable. These gloves protect workers from exposure to harmful substances, thus ensuring their safety while complying with stringent industry standards. International buyers should focus on sourcing gloves that offer resistance to specific chemicals relevant to their operations, as well as those that meet safety certifications in their respective regions, such as the Middle East and Africa.
Why Are Protective Gloves Important in Agriculture?
In agriculture, protective gloves are necessary for safely handling chemicals and pesticides. These gloves minimize the risk of chemical exposure, ensuring the health and safety of agricultural workers. Buyers should look for gloves sourced from certified manufacturers that guarantee durability and comfort, especially in wet or humid conditions common in many agricultural settings. This is particularly relevant for buyers in regions like Brazil, where agricultural practices are vital to the economy.
How Do General-Purpose Gloves Benefit Logistics and Warehousing?
In logistics and warehousing, general-purpose gloves are essential for material handling tasks. These gloves enhance grip, reduce hand fatigue, and protect against minor abrasions. Businesses can benefit from increased efficiency and safety when employees are equipped with the right gloves. When sourcing these gloves, B2B buyers should consider cost-effectiveness, availability in bulk, and compatibility with other personal protective equipment (PPE) to ensure comprehensive safety solutions for their workforce.
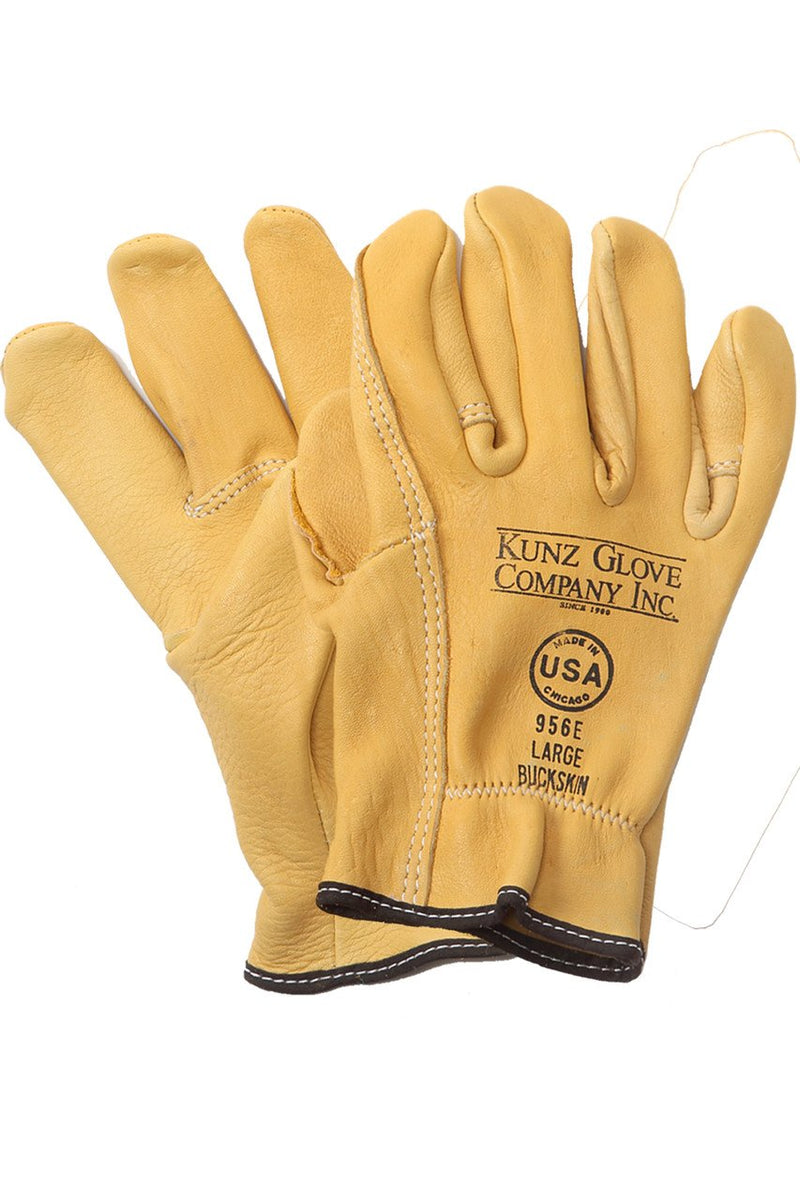
A stock image related to work glove manufacturer.
Related Video: Process of Making Coated Work Gloves. Glove Factory in Korea.
3 Common User Pain Points for ‘work glove manufacturer’ & Their Solutions
Scenario 1: Inconsistent Quality Across Different Suppliers
The Problem: International B2B buyers often face the challenge of inconsistent quality when sourcing work gloves from various manufacturers. This inconsistency can lead to significant operational disruptions, especially for industries that require reliable protective gear, such as construction, logistics, and manufacturing. When one batch of gloves fails to meet safety standards or is of inferior quality, it not only puts workers at risk but can also result in financial losses and damage to reputation.
The Solution: To combat this issue, buyers should prioritize establishing long-term partnerships with reputable work glove manufacturers who have a proven track record in quality assurance. Conduct thorough due diligence by reviewing certifications, customer testimonials, and factory audits. It’s advisable to request samples before placing large orders to evaluate the product’s performance firsthand. Additionally, implementing a robust quality control process that includes regular inspections and feedback loops can help ensure that the products consistently meet the required standards. Engaging with manufacturers that offer customization options can also help align the product specifications with the specific needs of your workforce, thereby enhancing overall satisfaction.
Scenario 2: Difficulty in Sourcing Sustainable Work Gloves
The Problem: As global awareness of environmental issues increases, many B2B buyers are under pressure to source sustainable work gloves. However, finding manufacturers that not only provide eco-friendly options but also adhere to ethical labor practices can be a daunting task. Buyers may struggle to identify products that genuinely meet sustainability criteria, leading to concerns about greenwashing and the authenticity of claims.
The Solution: To effectively source sustainable work gloves, buyers should focus on manufacturers who provide transparent supply chain practices. Look for certifications such as OEKO-TEX, Global Organic Textile Standard (GOTS), or similar eco-labels that validate the sustainability of materials used. Engage in direct communication with manufacturers to understand their sourcing processes and labor practices. Additionally, considering regional suppliers from Africa or South America who prioritize sustainability can yield more reliable options. Establishing relationships with organizations that advocate for sustainable practices can also provide valuable insights and resources, helping you make informed purchasing decisions while aligning with your company’s sustainability goals.
Scenario 3: Inadequate Product Knowledge and Support
The Problem: B2B buyers often encounter inadequate support and product knowledge from manufacturers, leading to challenges in selecting the right work gloves for specific applications. This lack of guidance can result in purchasing gloves that do not meet the necessary safety standards or are unsuitable for the intended tasks, increasing the risk of workplace injuries and compliance issues.
The Solution: To mitigate this challenge, it is crucial to partner with work glove manufacturers that offer comprehensive product training and support. When evaluating potential suppliers, inquire about their educational resources, such as product guides, training sessions, and customer support channels. Manufacturers who invest in educating their clients about the various materials, designs, and safety features of their gloves demonstrate a commitment to customer success. Additionally, consider leveraging technology by using virtual consultations or webinars for training purposes. This approach not only helps in selecting the right gloves but also ensures that your workforce understands how to use them effectively, thereby enhancing safety and productivity. Regularly engaging with suppliers for updates on new products or innovations can also keep your organization at the forefront of safety standards in your industry.
Strategic Material Selection Guide for work glove manufacturer
When selecting materials for work gloves, it is essential to consider various factors that influence performance, durability, and suitability for specific applications. Here, we analyze four common materials used in the manufacturing of work gloves, focusing on their properties, advantages, disadvantages, and considerations for international B2B buyers, particularly those from Africa, South America, the Middle East, and Europe.
What Are the Key Properties of Leather in Work Gloves?
Leather is a traditional material known for its durability and comfort. It offers excellent abrasion resistance and can withstand a wide range of temperatures, making it suitable for various industrial applications. Leather gloves typically have a temperature rating of up to 300°F (149°C) and provide good grip in both dry and wet conditions.
Pros & Cons: Leather gloves are generally more durable than synthetic alternatives, providing long-lasting performance. However, they can be more expensive due to the cost of raw materials and manufacturing processes. Additionally, leather requires special care to maintain its properties, which may complicate maintenance for some users.
Impact on Application: Leather gloves are ideal for heavy-duty applications, such as construction, welding, and metal handling. They are less suitable for environments involving chemicals or extreme moisture, where synthetic materials might perform better.
Considerations for International Buyers: Buyers should ensure that the leather used complies with local regulations regarding animal welfare and environmental impact. Standards such as ASTM F2413 for protective footwear may also apply.
How Does Nitrile Provide Benefits for Work Glove Applications?
Nitrile is a synthetic rubber that offers excellent chemical resistance, making it a popular choice for gloves used in industries such as oil and gas, automotive, and food processing. Nitrile gloves can withstand temperatures up to 200°F (93°C) and are resistant to punctures and tears.
Pros & Cons: The primary advantage of nitrile is its chemical resistance, which allows for safe handling of hazardous materials. However, nitrile gloves may not provide the same level of dexterity as leather or cotton gloves, potentially limiting their use in tasks requiring fine motor skills.
Impact on Application: Nitrile gloves are particularly effective in environments where exposure to oils, solvents, or chemicals is common. They are less effective in high-temperature settings, where heat-resistant materials may be necessary.
Considerations for International Buyers: Ensure compliance with local safety standards, such as EN 374 for chemical protection in Europe. Buyers in regions with stringent environmental regulations should also verify that nitrile production meets local compliance requirements.
What Advantages Do Cotton and Blended Fabrics Offer?
Cotton and blended fabrics are often used in lighter-duty work gloves. They provide good breathability and comfort, making them suitable for tasks that require dexterity and prolonged wear. Cotton gloves typically have a temperature rating of up to 180°F (82°C).
Pros & Cons: The main advantage of cotton gloves is their comfort and affordability, making them an excellent choice for tasks requiring frequent glove changes. However, they offer limited protection against cuts, abrasions, and chemicals, which may not be suitable for all applications.
Impact on Application: Cotton gloves are ideal for assembly work, packaging, and light handling tasks. They are not recommended for environments where heavy-duty protection is necessary.
Considerations for International Buyers: Buyers should look for gloves that comply with standards such as EN 420 for general safety requirements. In regions like Africa and South America, where cotton production is prevalent, sourcing locally can reduce costs and improve supply chain efficiency.
How Do PVC Coated Gloves Enhance Performance?
PVC (polyvinyl chloride) coated gloves are designed to provide excellent grip and protection against water and certain chemicals. They are commonly used in agricultural, construction, and manufacturing settings. PVC gloves can withstand temperatures up to 150°F (65°C) and offer good abrasion resistance.
Pros & Cons: PVC gloves are cost-effective and provide a good balance between protection and dexterity. However, they can be less breathable than other materials, leading to discomfort during extended use.
Impact on Application: These gloves are particularly effective in wet or oily conditions, making them suitable for tasks such as gardening, fishing, and food processing. They may not be ideal for high-temperature applications.
Considerations for International Buyers: Ensure compliance with relevant standards such as EN 388 for mechanical risks and EN 374 for chemical risks. Buyers should also consider the environmental impact of PVC production and disposal.
Summary Table of Material Selection for Work Gloves
Material | Typical Use Case for work glove manufacturer | Key Advantage | Key Disadvantage/Limitation | Relative Cost (Low/Med/High) |
---|---|---|---|---|
Leather | Heavy-duty applications (construction, welding) | Excellent durability and abrasion resistance | Higher cost and maintenance | High |
Nitrile | Chemical handling (oil, gas, automotive) | Superior chemical resistance | Limited dexterity | Medium |
Cotton/Blends | Light-duty tasks (assembly, packaging) | Comfortable and cost-effective | Limited protection | Low |
PVC Coated | Wet or oily conditions (gardening, food processing) | Good grip and water resistance | Less breathability | Medium |
This guide provides actionable insights for international B2B buyers in selecting the right materials for work gloves, ensuring compliance with local standards and meeting specific application needs.
In-depth Look: Manufacturing Processes and Quality Assurance for work glove manufacturer
What Are the Main Stages of Manufacturing Work Gloves?
The manufacturing of work gloves involves several critical stages that ensure both functionality and safety. Each stage is essential for producing high-quality gloves that meet the rigorous demands of various industries. Below are the primary stages involved in the manufacturing process:
Material Preparation: What Materials Are Commonly Used in Work Gloves?
The first step in manufacturing work gloves is the careful selection and preparation of materials. Common materials include:
- Leather: Known for its durability and comfort, often used in heavy-duty gloves.
- Synthetic Fibers: Such as nylon and polyester, which offer flexibility and resistance to wear and tear.
- Rubber and Latex: Frequently used in gloves designed for wet or chemical environments due to their waterproof properties.
- Kevlar: This high-strength material is used for cut-resistant gloves, providing excellent protection against sharp objects.
Once the materials are selected, they undergo processes such as cutting and treating to enhance their performance characteristics. This might include processes like water-proofing leather or adding coatings to synthetic materials for additional grip.
How Are Work Gloves Formed and Assembled?
After material preparation, the next step is forming the gloves. This involves several techniques:
- Cutting: The prepared materials are cut into specific patterns that form the glove’s shape. Precision cutting is essential to ensure uniformity and fit.
- Sewing: The cut pieces are then sewn together using industrial sewing machines. This stage requires skilled labor to ensure strong seams, which are critical for the glove’s durability.
- Molding: For rubber or latex gloves, molding techniques may be employed to create the glove’s shape. This process involves pouring liquid latex into glove-shaped molds and allowing it to cure.
The assembly process culminates with the attachment of additional features such as cuffs, coatings, or grip enhancements, depending on the glove’s intended use.
What Finishing Processes Are Involved in Work Glove Manufacturing?
Finishing is a crucial stage that enhances the glove’s performance and aesthetic appeal. Common finishing processes include:
- Coating: Some gloves receive a coating to improve grip or chemical resistance. This can involve dipping or spraying techniques.
- Quality Inspection: Before packaging, gloves undergo visual inspections to check for defects and ensure they meet quality standards.
The finishing stage not only ensures that the gloves are visually appealing but also that they meet the specific functional requirements dictated by industry standards.
How is Quality Assurance Implemented in Work Glove Manufacturing?
Quality assurance (QA) is critical in the work glove manufacturing process. It ensures that the final product meets both international and industry-specific standards. Here’s how QA is structured:
What Are the Relevant International Standards for Work Gloves?
International standards play a significant role in quality assurance for work gloves. Key standards include:
- ISO 9001: This standard outlines a framework for quality management systems, ensuring consistent product quality and customer satisfaction.
- CE Marking: Required in Europe, this indicates that the gloves meet health and safety requirements.
- API Standards: Particularly relevant in industries such as oil and gas, API standards specify performance criteria for gloves used in hazardous environments.
By adhering to these standards, manufacturers can ensure that their gloves are safe and reliable for end-users.
What Are the Key Quality Control Checkpoints in Work Glove Manufacturing?
Quality control (QC) checkpoints are established throughout the manufacturing process to identify and rectify defects early. The three critical checkpoints are:
- Incoming Quality Control (IQC): Materials are inspected upon arrival to ensure they meet specified standards before production begins.
- In-Process Quality Control (IPQC): Continuous monitoring during the manufacturing process helps catch defects as they occur. This includes checking stitching quality and material integrity.
- Final Quality Control (FQC): The finished gloves are subjected to rigorous testing, including visual inspections and functional tests, to ensure they meet quality standards before packaging.
What Common Testing Methods Are Used to Ensure Work Glove Quality?
Testing methods vary depending on the intended use of the gloves. Common testing methods include:
- Cut Resistance Testing: Measures the glove’s ability to resist cuts from sharp objects.
- Abrasion Resistance Testing: Evaluates how well the gloves can withstand wear from friction.
- Chemical Resistance Testing: Determines the gloves’ effectiveness in protecting against various chemicals.
These tests provide valuable data about the glove’s performance and help manufacturers make necessary adjustments before final production.
How Can B2B Buyers Verify Supplier Quality Control?
For international B2B buyers, especially from regions like Africa, South America, the Middle East, and Europe, verifying the quality control practices of suppliers is crucial. Here are actionable steps:
What Steps Can Buyers Take to Verify a Supplier’s Quality Control?
- Conduct Supplier Audits: Regular audits of suppliers’ facilities can help ensure compliance with quality standards. This includes assessing their manufacturing processes and quality control measures.
- Request Quality Reports: Buyers should ask for documented quality control reports that detail testing results, compliance with international standards, and any corrective actions taken.
- Engage Third-Party Inspectors: Utilizing independent third-party inspection services can provide unbiased assessments of a supplier’s quality control processes and product quality.
What Are the Nuances of QC and Certifications for International Buyers?
When dealing with international suppliers, it’s important to understand the nuances of quality control and certifications:
- Regional Compliance: Different regions may have varying compliance requirements. For example, CE marking is essential in Europe, while other certifications may be needed in the Middle East or Africa.
- Language Barriers: Documentation and reports may be in different languages. Buyers should ensure they can understand and verify the information provided.
- Cultural Differences in Quality Standards: Understanding cultural attitudes towards quality assurance can help buyers navigate negotiations and expectations more effectively.
By leveraging these insights, B2B buyers can make informed decisions when selecting work glove manufacturers, ensuring they receive products that meet their quality and safety standards.
Practical Sourcing Guide: A Step-by-Step Checklist for ‘work glove manufacturer’
In the competitive landscape of sourcing work gloves, international B2B buyers must navigate a range of considerations to ensure they partner with the right manufacturers. This guide provides a practical checklist to streamline your sourcing process, helping you to identify quality suppliers and negotiate effectively.
Step 1: Define Your Technical Specifications
Establishing clear technical specifications is essential before reaching out to manufacturers. Consider factors such as materials (e.g., leather, synthetic), glove type (e.g., cut-resistant, insulated), and compliance with safety standards relevant to your industry. This clarity will not only help you communicate your needs effectively but will also assist in evaluating supplier capabilities.
Step 2: Conduct Market Research
Understanding the market landscape is critical for informed decision-making. Investigate potential suppliers in your target regions—Africa, South America, the Middle East, and Europe—by reviewing industry reports and trade publications. Pay attention to regional trends and local regulations that may affect pricing and availability.
Step 3: Evaluate Potential Suppliers
Before committing to a supplier, a thorough evaluation is necessary. Request detailed company profiles, including their manufacturing capabilities, production capacity, and experience in your specific glove type. It’s also beneficial to seek references from other buyers in similar industries or regions to gauge reliability and service quality.
Step 4: Verify Supplier Certifications
Compliance with international safety standards is non-negotiable when sourcing work gloves. Ensure that potential suppliers hold relevant certifications, such as ISO 9001 for quality management and CE marking for safety compliance in Europe. This verification mitigates risks and assures you of the product quality you will receive.
Step 5: Request Samples for Testing
Before placing a bulk order, request samples to assess the quality and functionality of the gloves. Testing samples allows you to evaluate factors such as comfort, durability, and fit, which are crucial for end-users. This step can prevent costly mistakes and ensure that the gloves meet your operational requirements.
Step 6: Negotiate Terms and Conditions
Effective negotiation is key to a successful sourcing relationship. Discuss pricing, payment terms, delivery schedules, and after-sales support. Be clear about your expectations regarding order quantities and lead times, as this can significantly impact your supply chain efficiency.
Step 7: Establish a Communication Plan
Once you select a supplier, establish a robust communication plan to facilitate ongoing collaboration. Regular check-ins and updates can prevent misunderstandings and ensure that any issues are addressed promptly. Consider setting up a system for tracking order statuses and quality checks to maintain transparency throughout the process.
By following this checklist, international B2B buyers can enhance their sourcing strategies for work gloves, ensuring they partner with reputable manufacturers who can meet their specific needs.
Comprehensive Cost and Pricing Analysis for work glove manufacturer Sourcing
What Are the Key Cost Components in Work Glove Manufacturing?
Understanding the cost structure of work glove manufacturing is essential for international B2B buyers aiming to make informed purchasing decisions. The primary cost components include:
-
Materials: The choice of materials significantly impacts the overall cost. Common materials used in work gloves include leather, synthetic fabrics, and rubber. Higher-quality materials may lead to increased costs but can provide better durability and protection.
-
Labor: Labor costs vary widely depending on the region. In regions like Southeast Asia, labor is often cheaper, whereas countries in Europe and the Middle East may incur higher labor costs. It’s crucial to assess the skill level required for the production process, as specialized skills may raise labor costs.
-
Manufacturing Overhead: This includes costs associated with utilities, rent, and equipment maintenance. Manufacturers with advanced machinery may have higher overhead but can produce gloves more efficiently.
-
Tooling: The initial cost for molds and other tools used in the production process can be significant, especially for customized designs. This cost is often amortized over large production runs, making it more economical for bulk orders.
-
Quality Control (QC): Implementing rigorous QC processes ensures that the gloves meet industry standards and buyer specifications. However, this adds to the production cost. Buyers should inquire about the QC measures in place to ensure they receive a reliable product.
-
Logistics: Shipping costs can vary based on the distance from the manufacturer to the buyer and the mode of transportation used. Additionally, duties and tariffs may apply, influencing the total logistics cost.
-
Margin: Manufacturers will add a profit margin to cover their costs and ensure sustainability. This margin can vary based on the supplier’s market positioning and the competitive landscape.
How Do Price Influencers Affect Work Glove Costs?
Several factors can influence the pricing of work gloves in the B2B marketplace:
-
Volume/MOQ (Minimum Order Quantity): Bulk purchases typically lower the per-unit cost. Understanding the MOQ can help buyers negotiate better pricing.
-
Specifications and Customization: Customized gloves tailored to specific needs can incur additional costs. Buyers should clearly define their requirements to avoid unexpected expenses.
-
Material Quality and Certifications: Higher-quality gloves that comply with safety certifications (like EN388 or ANSI standards) may have higher prices. Buyers should weigh the benefits of certification against the cost.
-
Supplier Factors: The manufacturer’s reputation, reliability, and production capabilities can affect pricing. Established suppliers may charge a premium for their assurance of quality and service.
-
Incoterms: The terms of trade defined by Incoterms (International Commercial Terms) dictate the responsibilities of buyers and sellers in shipping and logistics. Understanding these terms is crucial to avoid hidden costs.
What Tips Can Help International Buyers Optimize Costs?
When sourcing work gloves, particularly from regions like Africa, South America, the Middle East, and Europe, buyers can leverage the following strategies:
-
Negotiation: Building a strong relationship with suppliers can lead to better pricing. Don’t hesitate to negotiate terms, especially if ordering in bulk.
-
Total Cost of Ownership (TCO): Look beyond the initial purchase price. Consider the longevity and performance of the gloves, as well as potential replacement costs. A higher upfront cost may result in lower TCO if the gloves are more durable.
-
Pricing Nuances for International Buyers: Understand the local market conditions and currency fluctuations that can affect prices. Additionally, be aware of the specific regulations and compliance requirements in your region to avoid costly penalties.
Disclaimer on Indicative Prices
Prices for work gloves can vary significantly based on the factors discussed. The information provided here serves as a guideline. It’s essential for buyers to conduct thorough research and obtain quotes from multiple suppliers to ensure they are making cost-effective decisions tailored to their specific needs.
Alternatives Analysis: Comparing work glove manufacturer With Other Solutions
Understanding the Importance of Alternatives in Work Glove Solutions
In the landscape of industrial safety, selecting the right protective gear is crucial for ensuring worker safety and productivity. While traditional work glove manufacturers offer a range of products, it’s essential for international B2B buyers to consider alternative solutions that may better fit their operational needs. Evaluating various options helps in making informed decisions that align with both budget constraints and performance expectations.
Comparison Table of Work Glove Manufacturer and Alternatives
Comparison Aspect | Work Glove Manufacturer | Smart Wearable Technology | Safety Training Programs |
---|---|---|---|
Performance | High durability and protection | Enhanced monitoring of hand movements | Improves safety awareness and compliance |
Cost | Moderate to high, depending on materials | High initial investment, but potential long-term savings | Low to moderate, depending on the program |
Ease of Implementation | Straightforward, widely available | Requires integration with existing systems | Varies based on organization size and training complexity |
Maintenance | Regular inspections needed | Requires software updates and maintenance | Ongoing training refreshers needed |
Best Use Case | General industrial applications | High-tech industries needing real-time data | All industries aiming for compliance and safety culture |
What are the Advantages and Disadvantages of Smart Wearable Technology?
Smart wearable technology, such as gloves equipped with sensors, provides real-time data regarding hand movements and potential hazards. The primary advantage of this technology is its ability to enhance workplace safety through data analytics. It can alert workers to unsafe practices or environmental risks instantly. However, the initial cost of these smart devices can be significantly higher compared to traditional work gloves. Additionally, integrating this technology into existing workflows may require training and adjustment, which can be a barrier for some organizations.
How Can Safety Training Programs Complement Work Glove Solutions?
Safety training programs are essential for fostering a culture of safety within an organization. These programs educate workers on the correct use of protective equipment, including work gloves, which can enhance their effectiveness. While the cost of these programs is generally lower than that of purchasing high-tech solutions, their effectiveness relies heavily on the ongoing commitment of the organization to refresh and update training regularly. The main drawback is that without proper reinforcement, knowledge can fade, leading to potential safety oversights.
Conclusion: How to Choose the Right Solution for Your Business?
Selecting the appropriate solution for hand protection in industrial settings requires a thorough understanding of the specific needs of your workforce and operational environment. B2B buyers should assess the performance and cost implications of traditional work glove manufacturers against innovative alternatives like smart wearables and safety training programs. Ultimately, the best choice will depend on factors such as budget, the complexity of tasks, and the level of safety culture within the organization. By weighing these options carefully, companies can ensure that they invest in solutions that not only protect their workforce but also enhance overall productivity and compliance.
Essential Technical Properties and Trade Terminology for work glove manufacturer
What Are the Key Technical Properties of Work Gloves?
Understanding the technical specifications of work gloves is crucial for B2B buyers, especially when selecting products that meet specific industry requirements. Below are several critical specifications that influence glove performance and suitability for various applications.
1. Material Grade: Why Does It Matter?
The material grade of work gloves significantly impacts durability, comfort, and protection. Common materials include leather, synthetic, and textile. For example, leather gloves are often preferred in heavy-duty applications due to their abrasion resistance, while synthetic materials like nitrile provide excellent chemical resistance. Buyers should consider the specific tasks their workforce will perform to select gloves made from the appropriate material grade.
2. Cut Resistance Rating: How Is It Measured?
Cut resistance is a vital property, particularly in industries such as manufacturing and construction. This rating is measured using standards like the ANSI/ISEA 105, which classifies gloves from A1 (lowest) to A9 (highest). Understanding cut resistance helps buyers ensure that their workforce is adequately protected from sharp objects, minimizing the risk of injuries and associated costs.
3. Grip and Dexterity: Why Are These Important?
The grip offered by work gloves can vary based on the material and design. For example, textured surfaces enhance grip in wet or oily conditions. Dexterity refers to the gloves’ ability to allow fine motor skills, crucial for tasks requiring precision. Selecting gloves that balance grip and dexterity is essential for maximizing productivity and ensuring worker safety.
4. Tolerance and Size Specifications: How Do They Affect Fit?
Tolerance refers to the allowable deviation in dimensions during manufacturing. A precise fit is crucial for comfort and functionality. Gloves that are too tight can lead to fatigue, while those that are too loose may compromise safety. Buyers should request detailed sizing charts and tolerances to ensure proper fit and performance in their specific work environments.
5. Thermal Resistance: When Is It Necessary?
Thermal resistance indicates how well gloves can protect against extreme temperatures, whether hot or cold. This property is especially important in industries such as food processing or metalwork, where workers may be exposed to high heat. Buyers should assess the thermal resistance ratings to ensure that their employees are adequately protected from temperature-related hazards.
What Trade Terminology Should B2B Buyers Understand?
Familiarity with industry jargon is essential for effective communication and negotiation. Here are some commonly used terms in the work glove manufacturing sector.
1. OEM (Original Equipment Manufacturer): What Does It Mean?
An OEM is a company that produces components or products that are marketed by another company under its brand. For B2B buyers, understanding OEM relationships can lead to better pricing and customization options. Engaging directly with OEMs can also streamline the supply chain.
2. MOQ (Minimum Order Quantity): Why Is It Important?
MOQ refers to the smallest quantity of a product that a supplier is willing to sell. Knowing the MOQ is crucial for budget management and inventory planning. Buyers should negotiate MOQs that align with their purchasing capacity and demand forecasts to avoid excess stock or shortages.
3. RFQ (Request for Quotation): How Does It Work?
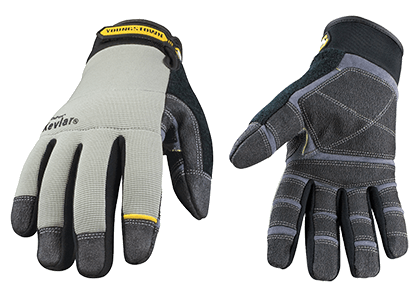
A stock image related to work glove manufacturer.
An RFQ is a document issued by buyers to solicit price quotes from suppliers for specific products or services. For B2B buyers, crafting a clear and detailed RFQ can lead to competitive pricing and ensure that all suppliers understand the requirements. It serves as a foundation for negotiation and contract terms.
4. Incoterms (International Commercial Terms): Why Are They Critical?
Incoterms define the responsibilities of buyers and sellers in international trade, including shipping, insurance, and tariffs. Understanding these terms helps buyers manage risks and costs associated with international procurement. Properly negotiated Incoterms can facilitate smoother transactions and reduce potential disputes.
Conclusion
By comprehensively understanding the essential technical properties and trade terminology related to work gloves, B2B buyers can make informed decisions that enhance safety and productivity in their operations. This knowledge not only aids in selecting the right products but also ensures effective communication with suppliers, ultimately leading to better business outcomes.
Navigating Market Dynamics and Sourcing Trends in the work glove manufacturer Sector
What Are the Current Market Dynamics in the Work Glove Manufacturing Sector?
The work glove manufacturing sector is experiencing a notable shift driven by various global factors. Increasing safety regulations across industries, particularly in construction, manufacturing, and logistics, are propelling demand for high-quality work gloves. Additionally, the rise of automation and advanced manufacturing technologies is influencing design innovations, leading to gloves that offer enhanced dexterity and protection.
Emerging technologies such as 3D printing and smart textiles are transforming product development, enabling manufacturers to create customized solutions tailored to specific industry needs. For international B2B buyers, especially those from Africa, South America, the Middle East, and Europe, understanding these technological advancements is crucial for sourcing products that meet evolving safety standards and user preferences.
Market dynamics are also shaped by the fluctuating cost of raw materials, including synthetic and natural fibers. Buyers must stay informed about global commodity prices and supply chain disruptions that can affect availability and pricing. Furthermore, the COVID-19 pandemic has heightened awareness around health and hygiene, leading to an increased demand for disposable gloves, which adds another layer to the sourcing landscape.
How Is Sustainability Impacting Sourcing in the Work Glove Sector?
Sustainability has become a cornerstone in the sourcing strategies of B2B buyers in the work glove manufacturing sector. As environmental concerns gain traction globally, manufacturers are prioritizing sustainable practices throughout their supply chains. This includes the use of eco-friendly materials, such as recycled plastics and organic cotton, which significantly reduce the environmental footprint of production.
Ethical sourcing is equally important, as international buyers increasingly seek suppliers who adhere to fair labor practices and social responsibility. Certifications such as Global Organic Textile Standard (GOTS) and OEKO-TEX® Standard 100 are becoming essential for buyers aiming to ensure their products are not only safe for consumers but also produced in environmentally responsible ways.
Moreover, many manufacturers are adopting circular economy principles, promoting the reuse and recycling of materials. This trend is particularly relevant for buyers in regions like the Middle East and Africa, where regulations on waste management are tightening. By prioritizing suppliers with strong sustainability credentials, B2B buyers can enhance their brand reputation while contributing to global sustainability efforts.
How Has the Work Glove Manufacturing Sector Evolved Over Time?
The work glove manufacturing sector has undergone significant transformations since its inception. Initially dominated by simple designs made from leather and basic fabrics, the industry has evolved with advancements in material science and technology. The introduction of synthetic materials in the late 20th century revolutionized the market, allowing for greater durability and performance.
The last two decades have witnessed a surge in innovation, with manufacturers focusing on ergonomics, user comfort, and specialized functionalities. The rise of smart gloves equipped with sensors and connectivity features reflects the sector’s response to the demands of modern workplaces. As industries continue to evolve, work gloves are becoming integral to enhancing worker safety and productivity, underscoring the importance of staying abreast of trends for B2B buyers in this competitive landscape.
Frequently Asked Questions (FAQs) for B2B Buyers of work glove manufacturer
-
How do I choose the right work glove manufacturer for my business needs?
Selecting the right work glove manufacturer requires a thorough evaluation of their product range, quality certifications, and industry experience. Start by identifying your specific requirements, such as the type of glove material (latex, nitrile, leather), the intended use (construction, medical, industrial), and any relevant safety standards. Request samples to assess quality, and check for reviews or testimonials from other international buyers, especially those in your region. Engaging directly with potential manufacturers can also provide insight into their production capabilities and responsiveness. -
What are the common customization options offered by work glove manufacturers?
Many work glove manufacturers offer customization options to meet specific client needs. These may include altering glove sizes, colors, materials, and features such as grip enhancements or additional padding. Some manufacturers can also incorporate branding elements like logos or custom packaging. When discussing customization, clearly communicate your requirements and inquire about the minimum order quantities (MOQ) and lead times for customized products to ensure they align with your business timeline. -
What should I know about minimum order quantities (MOQ) when sourcing work gloves?
Minimum order quantities (MOQ) can vary significantly between manufacturers. Typically, MOQs are set to ensure cost-effectiveness in production. As an international buyer, it’s crucial to understand these terms early in negotiations. Some manufacturers may offer flexible MOQs for first-time orders or samples, while others may have strict policies. Always clarify the MOQ during discussions and consider how it fits within your inventory management and cash flow strategies. -
What payment terms should I expect when working with international glove suppliers?
Payment terms with international suppliers can vary widely. Common arrangements include upfront payments, partial payments (e.g., 30% deposit), or payment upon delivery. It’s essential to negotiate terms that align with your cash flow and risk tolerance. Additionally, consider using secure payment methods such as letters of credit or escrow services, especially for larger orders. Be sure to discuss any potential fees associated with currency exchange and international transactions. -
How can I ensure quality assurance when sourcing work gloves from manufacturers?
Quality assurance is critical in B2B transactions, especially for safety gear like work gloves. Look for manufacturers with relevant quality certifications, such as ISO 9001 or EN standards, which indicate adherence to international quality benchmarks. Request detailed product specifications, including material safety data sheets (MSDS). Additionally, consider implementing a third-party inspection service to verify product quality before shipment, particularly for large orders or when working with new suppliers. -
What logistics considerations should I keep in mind when importing work gloves?
Logistics is a key factor in international trade, impacting delivery timelines and costs. Understand the shipping methods available (air freight vs. sea freight) and their associated costs and transit times. Work with a reliable freight forwarder who can navigate customs regulations specific to your region, especially if you’re importing to Africa, South America, the Middle East, or Europe. Additionally, consider the implications of tariffs and duties that may apply to your shipments. -
What are the key safety standards and certifications for work gloves?
Safety standards for work gloves can vary by region and industry. Common certifications include the ANSI/ISEA standards in the U.S., EN 388 for mechanical risks in Europe, and ASTM standards. Familiarize yourself with the specific requirements relevant to your industry and region. When sourcing gloves, ensure the manufacturer provides documentation proving compliance with these standards, as this will help safeguard your workers and protect your business from liability issues. -
How can I build a long-term relationship with a work glove manufacturer?
Building a long-term partnership with a work glove manufacturer involves clear communication and mutual trust. Start by establishing a solid foundation with open dialogues about your needs and expectations. Regularly provide feedback on product performance and service quality, which helps manufacturers improve their offerings. Consider collaborating on product development or joint marketing initiatives, as this can foster loyalty and lead to better pricing and priority service for your future orders.
Important Disclaimer & Terms of Use
⚠️ Important Disclaimer
The information provided in this guide, including content regarding manufacturers, technical specifications, and market analysis, is for informational and educational purposes only. It does not constitute professional procurement advice, financial advice, or legal advice.
While we have made every effort to ensure the accuracy and timeliness of the information, we are not responsible for any errors, omissions, or outdated information. Market conditions, company details, and technical standards are subject to change.
B2B buyers must conduct their own independent and thorough due diligence before making any purchasing decisions. This includes contacting suppliers directly, verifying certifications, requesting samples, and seeking professional consultation. The risk of relying on any information in this guide is borne solely by the reader.
Strategic Sourcing Conclusion and Outlook for work glove manufacturer
In summary, strategic sourcing for work gloves is essential for international B2B buyers seeking to enhance their supply chain efficiency and cost-effectiveness. By focusing on quality, supplier reliability, and market trends, companies can ensure they select the right manufacturers to meet their specific needs. Emphasizing sustainable practices and compliance with local regulations will not only enhance product quality but also strengthen brand reputation across diverse markets.
How Can Buyers Leverage Strategic Sourcing to Gain Competitive Advantage?
B2B buyers from Africa, South America, the Middle East, and Europe should prioritize building strong relationships with manufacturers who understand local market dynamics and regulatory requirements. Engaging in transparent communication and collaboration with suppliers can lead to better negotiation outcomes and innovation in product development.
What’s Next for B2B Buyers in the Work Glove Market?
As the global market evolves, so too should your sourcing strategies. Keep an eye on emerging trends such as smart gloves and eco-friendly materials that can set your business apart. Take proactive steps now to refine your sourcing approach, ensuring you are well-positioned to capitalize on future opportunities. Embrace the future of work glove procurement with confidence and diligence, and watch your business thrive in an increasingly competitive landscape.