Improve Quality with the Best Aluminum Extrusion Supplier (2025)
Introduction: Navigating the Global Market for aluminum extrusion supplier
In today’s global market, sourcing a reliable aluminum extrusion supplier can be a daunting task for international B2B buyers, particularly those operating in Africa, South America, the Middle East, and Europe. With the increasing demand for high-quality aluminum products across various industries, buyers often grapple with challenges such as identifying trustworthy suppliers, ensuring product quality, and managing logistics. This guide aims to demystify the complexities of navigating the aluminum extrusion landscape, providing insights into different types of aluminum extrusions, their applications, and essential criteria for vetting suppliers.
From understanding the nuances of various aluminum profiles to exploring cost implications and evaluating supplier capabilities, this comprehensive resource equips buyers with the knowledge necessary to make informed purchasing decisions. By addressing critical questions such as “What are the key factors to consider when selecting an aluminum extrusion supplier?” and “How can I ensure the quality of the aluminum products I source?”, this guide serves as a vital tool for businesses looking to optimize their supply chain and enhance their operational efficiency.
With a focus on actionable insights, this guide empowers B2B buyers to navigate the global aluminum market confidently, ensuring that they can access the best products while minimizing risks and maximizing value. Whether you are a manufacturer, contractor, or architect, understanding the dynamics of aluminum extrusion sourcing will be pivotal in achieving your project goals.
Understanding aluminum extrusion supplier Types and Variations
Type Name | Key Distinguishing Features | Primary B2B Applications | Brief Pros & Cons for Buyers |
---|---|---|---|
Standard Aluminum Extruders | High volume production, standardized profiles | Construction, automotive, and furniture industries | Pros: Cost-effective, quick delivery. Cons: Limited customization options. |
Custom Aluminum Extruders | Tailored designs, specific dimensions | Aerospace, specialized machinery, and custom builds | Pros: Unique solutions, precise specifications. Cons: Higher costs, longer lead times. |
Architectural Aluminum Suppliers | Focused on aesthetic and structural performance | Building facades, window frames, and railings | Pros: Enhanced visual appeal, durable. Cons: May require more detailed specifications. |
Recycled Aluminum Suppliers | Use of recycled materials, eco-friendly practices | Green building projects, automotive parts | Pros: Sustainable sourcing, lower environmental impact. Cons: Potential quality variability. |
Integrated Supply Chain Providers | Full-service solutions from design to delivery | Large-scale construction and manufacturing | Pros: Streamlined processes, reduced lead times. Cons: May have higher upfront costs. |
What Are the Characteristics of Standard Aluminum Extruders?
Standard aluminum extruders are characterized by their ability to produce high volumes of standardized profiles, making them a popular choice for industries like construction, automotive, and furniture. These suppliers often have established production lines, enabling quick turnaround times and cost-effective solutions. When considering a standard extruder, buyers should evaluate their volume needs and whether they can accept the limitations in customization, as these suppliers typically focus on mass production rather than bespoke designs.
How Do Custom Aluminum Extruders Differ in Suitability?
Custom aluminum extruders specialize in producing tailored designs and specific dimensions that meet unique project requirements. They are particularly suitable for industries such as aerospace, where precision and adherence to strict specifications are critical. Buyers should consider the potential for higher costs and longer lead times when opting for custom solutions. However, the ability to receive a product that perfectly fits their needs often justifies these trade-offs.
Why Choose Architectural Aluminum Suppliers?
Architectural aluminum suppliers focus on providing products that combine both aesthetic appeal and structural integrity. They cater to applications such as building facades, window frames, and railings, where design plays a crucial role. Buyers should assess the visual and performance requirements of their projects when selecting an architectural supplier. While these products may offer superior aesthetics, they may also necessitate more detailed specifications to ensure compatibility with design intentions.
What Are the Benefits of Working with Recycled Aluminum Suppliers?
Recycled aluminum suppliers utilize eco-friendly practices by sourcing materials from recycled aluminum. This approach is increasingly favored in green building projects and automotive applications, where sustainability is a priority. Buyers should be aware of the potential for quality variability, as recycled materials can differ in properties compared to virgin aluminum. However, the environmental benefits and often lower costs make recycled suppliers an attractive option for many businesses.
How Do Integrated Supply Chain Providers Enhance the Purchasing Process?
Integrated supply chain providers offer a comprehensive service that encompasses everything from design and engineering to manufacturing and delivery. This model is particularly advantageous for large-scale construction and manufacturing projects, where streamlined processes can lead to significant time and cost savings. Buyers should weigh the potential for higher upfront costs against the benefits of reduced lead times and improved coordination across the supply chain.
Related Video: Extrusion 101: Aluminum Extrusion Process Explained by ILSCO Extrusions Inc.
Key Industrial Applications of aluminum extrusion supplier
Industry/Sector | Specific Application of Aluminum Extrusion Supplier | Value/Benefit for the Business | Key Sourcing Considerations for this Application |
---|---|---|---|
Construction | Structural Components for Buildings | Lightweight yet strong materials reduce transport costs and enhance safety. | Ensure compliance with local building codes and certifications. |
Automotive | Chassis and Frame Components | Improved fuel efficiency and reduced weight lead to cost savings. | Look for suppliers with experience in automotive-grade materials. |
Renewable Energy | Solar Panel Frames | Durability and corrosion resistance enhance lifespan and reduce maintenance. | Verify supplier capabilities in custom extrusion for specific designs. |
Consumer Electronics | Enclosures and Heat Sinks for Devices | Enhanced thermal management improves device performance and longevity. | Assess the supplier’s ability to produce precision extrusions. |
Aerospace | Aircraft Components | Weight reduction contributes to fuel efficiency and operational cost savings. | Ensure adherence to stringent aerospace standards and certifications. |
How is Aluminum Extrusion Used in Construction?
In the construction sector, aluminum extrusion suppliers provide structural components such as beams, columns, and window frames. These components are favored for their lightweight nature and high strength, which help reduce transportation costs and improve safety on job sites. International buyers, especially from regions like Africa and South America, should consider suppliers that comply with local building codes and offer certified materials to ensure quality and safety in their projects.
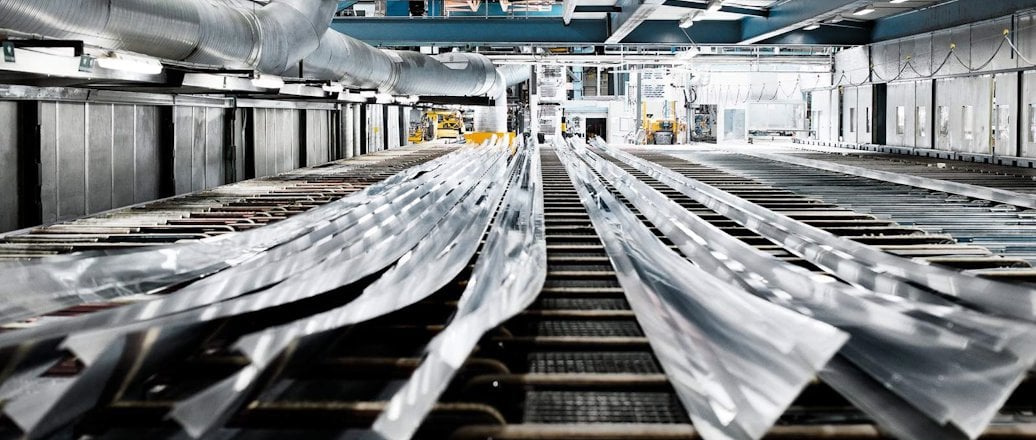
A stock image related to aluminum extrusion supplier.
What are the Applications of Aluminum Extrusion in the Automotive Industry?
Aluminum extrusions are critical in the automotive industry for manufacturing chassis and frame components. The lightweight properties of aluminum significantly enhance fuel efficiency, leading to cost savings over a vehicle’s lifespan. Buyers from Europe and the Middle East should prioritize suppliers with expertise in automotive-grade materials, ensuring that the products meet rigorous industry standards for safety and performance.
How Does Aluminum Extrusion Benefit the Renewable Energy Sector?
In renewable energy, aluminum extrusion suppliers produce solar panel frames that are both durable and corrosion-resistant. These properties enhance the lifespan of solar installations, thereby reducing maintenance costs and improving return on investment. B2B buyers in regions with growing solar markets, such as Africa, should verify that suppliers can offer custom extrusions tailored to specific project requirements, ensuring optimal performance.
What Role Does Aluminum Extrusion Play in Consumer Electronics?
For consumer electronics, aluminum extrusion suppliers provide enclosures and heat sinks that improve thermal management. This is crucial for maintaining device performance and longevity, especially in compact designs. International buyers should assess suppliers’ capabilities in producing precision extrusions to meet specific design needs and ensure compatibility with advanced electronics.
How is Aluminum Extrusion Used in the Aerospace Industry?
In the aerospace sector, aluminum extrusions are employed for various components, including structural frames and fittings. The lightweight nature of aluminum contributes to fuel efficiency, which is vital for reducing operational costs in aviation. Buyers from Europe and the Middle East should ensure that their suppliers adhere to stringent aerospace standards and possess the necessary certifications, ensuring the highest quality and safety in their aerospace applications.
3 Common User Pain Points for ‘aluminum extrusion supplier’ & Their Solutions
Scenario 1: Navigating Quality Assurance Challenges with Aluminum Extrusions
The Problem:
B2B buyers often face significant challenges related to the quality and consistency of aluminum extrusions. In sectors such as construction or manufacturing, subpar materials can lead to project delays, increased costs, and safety issues. For example, a manufacturer in South America may order a batch of aluminum profiles for a new product line, only to discover that the profiles do not meet specified tolerances or quality standards. This not only affects production timelines but can also damage the company’s reputation if the final products fail to perform as expected.
The Solution:
To effectively navigate quality assurance challenges, it’s crucial for buyers to establish clear quality criteria and specifications before placing an order. Engage with the aluminum extrusion supplier early in the design phase to communicate these requirements. Utilize standardized testing methods such as tensile strength and corrosion resistance tests. Additionally, consider suppliers who provide detailed documentation and certifications for their products, such as ISO 9001. This not only ensures the quality of the extrusions but also builds trust between the buyer and supplier. Regular audits and quality checks can further ensure compliance with the agreed standards.
Scenario 2: Addressing Lead Time and Delivery Delays in Global Supply Chains
The Problem:
International buyers often struggle with lead times and delivery delays, particularly when sourcing aluminum extrusions from suppliers in different regions. For instance, a construction company in Europe may find that delays in shipping or customs clearance lead to a bottleneck in their project timeline. Such delays can result in financial losses and missed deadlines, creating frustration and uncertainty in project management.
The Solution:
To mitigate lead time issues, buyers should develop a robust supply chain strategy that includes multiple suppliers and backup plans. Engaging local suppliers when possible can significantly reduce shipping times and complexities. Establishing clear communication channels with suppliers regarding production timelines and potential delays is essential. Buyers can also utilize logistics management software to track shipments in real-time, which helps in anticipating delays. Additionally, negotiating favorable terms for expedited shipping can provide a buffer for urgent projects, ensuring timely delivery of aluminum extrusions.
Scenario 3: Overcoming Miscommunication and Specification Errors
The Problem:
Miscommunication regarding specifications is a common pain point that leads to costly errors in aluminum extrusion orders. A buyer in Africa might specify a particular alloy or finish, but due to unclear communication or misunderstanding, the supplier delivers the wrong product. This can halt production and necessitate reordering, adding significant costs and time to the project.
The Solution:
To overcome miscommunication, buyers should implement a structured specification process. This includes creating detailed drawings and documentation that outline exact requirements such as dimensions, tolerances, and surface finishes. Utilizing digital tools like CAD software can help in providing clear visual references. Regular meetings and updates with suppliers throughout the order process are essential to ensure alignment on specifications. Furthermore, utilizing a contract that includes detailed product specifications and penalties for non-compliance can safeguard against such errors. Investing time in building strong relationships with suppliers will also enhance communication and reduce the likelihood of misunderstandings.
Strategic Material Selection Guide for aluminum extrusion supplier
What Are the Key Properties of Common Materials for Aluminum Extrusion?
When selecting materials for aluminum extrusion, understanding the properties of commonly used materials is crucial for ensuring optimal product performance. Here, we analyze four prevalent materials: 6061 Aluminum, 6063 Aluminum, 7075 Aluminum, and Anodized Aluminum. Each material has unique characteristics that affect its suitability for various applications.
1. 6061 Aluminum: A Versatile Choice
Key Properties:
6061 aluminum is known for its excellent mechanical properties and good weldability. It has a temperature rating of up to 200°C and exhibits moderate corrosion resistance, making it suitable for various environments.
Pros & Cons:
The advantages of 6061 aluminum include high strength-to-weight ratio and ease of fabrication. However, it can be more expensive than other alloys and may not be as corrosion-resistant in highly saline environments.
Impact on Application:
This material is often used in structural applications, automotive components, and marine environments. Its moderate corrosion resistance means it is suitable for applications that do not involve prolonged exposure to seawater.
Considerations for International Buyers:
Buyers should ensure compliance with international standards such as ASTM B221 and consider local preferences for specific applications. In regions like Africa and South America, where marine applications are common, understanding the corrosion resistance is vital.
2. 6063 Aluminum: Ideal for Architectural Applications
Key Properties:
6063 aluminum is characterized by its excellent extrudability and surface finish. It has a lower strength compared to 6061 but offers superior corrosion resistance, making it ideal for architectural applications.
Pros & Cons:
The main advantage of 6063 aluminum is its aesthetic appeal and ability to be anodized for enhanced durability. However, its lower strength limits its use in structural applications where high loads are expected.
Impact on Application:
This alloy is widely used in window frames, door frames, and other architectural elements. Its corrosion resistance is particularly beneficial in humid or coastal environments.
Considerations for International Buyers:
For buyers in Europe, adherence to EN standards for architectural applications is crucial. In the Middle East, where aesthetics are important, the ability to anodize and finish 6063 aluminum can significantly influence purchasing decisions.
3. 7075 Aluminum: High-Strength Applications
Key Properties:
7075 aluminum is known for its exceptional strength and is often used in aerospace applications. It has a temperature rating of up to 120°C and offers good fatigue resistance.
Pros & Cons:
The primary advantage of 7075 aluminum is its high strength, making it suitable for load-bearing applications. However, it is more challenging to weld and is generally more expensive than other aluminum alloys.
Impact on Application:
This material is commonly used in aerospace, military, and high-stress applications. Its strength makes it ideal for components that require minimal weight without compromising performance.
Considerations for International Buyers:
Buyers must be aware of compliance with aerospace standards such as AMS 4045. In regions like Europe and Australia, where aerospace regulations are stringent, ensuring the material meets these requirements is essential.
4. Anodized Aluminum: Enhanced Durability and Aesthetics
Key Properties:
Anodized aluminum undergoes an electrochemical process that enhances its corrosion resistance and surface hardness. This process allows for a variety of colors and finishes, making it aesthetically pleasing.
Pros & Cons:
Anodized aluminum is highly durable and resistant to wear and corrosion. However, the anodizing process can add to the cost and may limit the material’s recyclability.
Impact on Application:
It is widely used in consumer products, architectural applications, and electronics due to its durability and aesthetic flexibility.
Considerations for International Buyers:
International buyers should consider local regulations regarding anodizing processes and waste disposal. In Europe, compliance with environmental standards is critical, while buyers in Africa may focus on the material’s longevity in harsh climates.
Summary Table of Material Selection for Aluminum Extrusion
Material | Typical Use Case for Aluminum Extrusion Supplier | Key Advantage | Key Disadvantage/Limitation | Relative Cost (Low/Med/High) |
---|---|---|---|---|
6061 Aluminum | Structural components, automotive parts | High strength-to-weight ratio | Higher cost, moderate corrosion resistance | Medium |
6063 Aluminum | Architectural applications, window frames | Excellent surface finish, corrosion resistance | Lower strength than 6061 | Medium |
7075 Aluminum | Aerospace, military applications | Exceptional strength | Difficult to weld, high cost | High |
Anodized Aluminum | Consumer products, electronics, architectural elements | Enhanced durability and aesthetics | Higher cost, limited recyclability | Medium |
This guide provides a comprehensive overview of material selection for aluminum extrusion, ensuring international B2B buyers can make informed decisions based on their specific needs and regional considerations.
In-depth Look: Manufacturing Processes and Quality Assurance for aluminum extrusion supplier
What Are the Key Stages in the Aluminum Extrusion Manufacturing Process?
The aluminum extrusion process involves several critical stages that ensure the final product meets the required specifications and quality standards. Understanding these stages is essential for international B2B buyers who seek reliable suppliers. Here are the main stages involved:
1. Material Preparation
The process begins with the selection of high-quality aluminum billets, which are typically made from aluminum alloy. These billets are cut to the desired length and heated in a furnace to around 400-500 degrees Celsius, making the material malleable. The heating time and temperature are carefully controlled to ensure optimal extrusion properties.
2. Forming
Once the billets are heated, they are transferred to the extrusion press, where they are forced through a die to create the desired profile. This stage involves the use of hydraulic or mechanical presses, which can exert thousands of tons of pressure. The choice of die design is crucial, as it dictates the shape and dimensions of the extruded aluminum.
3. Cooling and Cutting
After extrusion, the aluminum profiles are rapidly cooled, often using water sprays or air cooling methods. This quick cooling helps to stabilize the dimensions of the extruded product. Once cooled, the profiles are cut to the specified lengths, ready for further processing.
4. Finishing
Finishing processes may include anodizing, painting, or powder coating to enhance the aesthetic appeal and corrosion resistance of the aluminum profiles. This stage is vital, particularly for products intended for outdoor use or in harsh environments.
5. Assembly
In some cases, extruded components are assembled into final products. This can involve welding, mechanical fastening, or adhesive bonding, depending on the design requirements.
How Is Quality Assurance Implemented in Aluminum Extrusion?
Quality assurance (QA) is a critical aspect of the aluminum extrusion process, ensuring that products meet international and industry-specific standards. Here are the key components of an effective QA program:
Relevant International Standards
For B2B buyers, it is essential to verify that suppliers adhere to international quality standards such as ISO 9001. This standard outlines the requirements for a quality management system (QMS) and emphasizes continuous improvement and customer satisfaction. Additionally, industry-specific certifications like CE marking for products sold in the European market and API certification for oil and gas applications can also be relevant.
Quality Control Checkpoints
Quality control (QC) checkpoints are implemented at various stages of the manufacturing process:
-
Incoming Quality Control (IQC): This involves inspecting raw materials and components upon arrival to ensure they meet specified standards.
-
In-Process Quality Control (IPQC): During the manufacturing process, regular checks are conducted to monitor parameters such as temperature, pressure, and dimensions.
-
Final Quality Control (FQC): After production, finished products undergo rigorous testing to verify that they meet quality standards. This may include dimensional checks, visual inspections, and functional testing.
What Common Testing Methods Are Used in Aluminum Extrusion Quality Control?
A variety of testing methods are employed to ensure the integrity and performance of extruded aluminum products:
-
Mechanical Testing: Tensile strength, yield strength, and elongation tests are conducted to assess the mechanical properties of the aluminum.
-
Dimensional Inspection: Precision measuring tools are used to ensure that the extruded profiles conform to the required specifications.
-
Visual Inspection: A thorough visual examination helps identify surface defects such as scratches, dents, or irregularities.
-
Non-destructive Testing (NDT): Techniques such as ultrasonic testing and radiographic testing can be employed to detect internal defects without damaging the product.
How Can B2B Buyers Verify Supplier Quality Control Processes?
For international B2B buyers, particularly those from Africa, South America, the Middle East, and Europe, verifying a supplier’s quality control processes is crucial. Here are actionable steps:
Conduct Supplier Audits
Regular audits of potential suppliers can provide insights into their manufacturing processes and quality assurance protocols. During an audit, buyers should assess the supplier’s adherence to international standards, evaluate their QC checkpoints, and examine their documentation practices.
Request Quality Reports
Buyers should request detailed quality reports that outline the results of various testing methods and inspections. This documentation should include information on batch traceability, which links specific products to their production history.
Engage Third-Party Inspectors
Utilizing third-party inspection services can add an extra layer of assurance. Independent inspectors can evaluate the supplier’s processes and products, ensuring compliance with international quality standards. This is particularly valuable for buyers operating in regions with strict regulatory requirements.
What Are the Quality Control and Certification Nuances for International B2B Buyers?
Understanding the nuances of quality control and certification is crucial for B2B buyers who operate across different regions. Here are key considerations:
-
Local Regulations: Different countries may have varying regulatory requirements for aluminum products. Buyers should familiarize themselves with these regulations to ensure compliance.
-
Cultural Differences in Quality Perception: Quality expectations can vary significantly by region. For instance, European buyers may prioritize aesthetic quality, while buyers in Africa may focus more on durability and functionality.
-
Language and Communication Barriers: Effective communication is vital for conveying quality requirements. Buyers should ensure that technical specifications and standards are clearly understood by both parties to avoid misunderstandings.
Conclusion: Ensuring Quality in Aluminum Extrusion Supply Chains
By understanding the manufacturing processes and quality assurance measures in aluminum extrusion, international B2B buyers can make informed decisions when selecting suppliers. It is essential to prioritize suppliers that adhere to recognized quality standards and demonstrate a commitment to continuous improvement. By implementing thorough verification processes, buyers can mitigate risks and secure high-quality aluminum products that meet their specific needs.
Practical Sourcing Guide: A Step-by-Step Checklist for ‘aluminum extrusion supplier’
To successfully procure aluminum extrusions, international B2B buyers must navigate a complex landscape of suppliers, regulations, and product specifications. This step-by-step checklist is designed to help you streamline the sourcing process, ensuring that you make informed decisions that align with your business needs.
Step 1: Define Your Technical Specifications
Before reaching out to suppliers, clearly define your technical requirements. This includes dimensions, tolerances, alloy types, surface treatments, and any specific design features. Having precise specifications helps in receiving accurate quotes and ensures that the products meet your project needs.
- Consider the end application: Different industries may require specific grades of aluminum, so understanding your application can guide your specifications.
- Assess your volume needs: Determine whether you need small or large quantities, as this can affect supplier selection.
Step 2: Conduct Market Research for Suppliers
Research potential suppliers through industry directories, trade shows, and online platforms. Look for companies with a strong reputation in aluminum extrusion manufacturing.
- Check geographical relevance: Suppliers from Africa, South America, the Middle East, or Europe may offer different advantages in terms of logistics and regulatory compliance.
- Gather reviews and ratings: Look for testimonials from other buyers to gauge reliability and product quality.
Step 3: Evaluate Potential Suppliers
Before committing, it’s crucial to vet suppliers thoroughly. Request company profiles, case studies, and references from buyers in a similar industry or region. Don’t just rely on their website.
- Assess production capabilities: Ensure the supplier has the machinery and expertise to meet your specific extrusion needs.
- Request samples: If possible, ask for product samples to evaluate quality firsthand.
Step 4: Verify Supplier Certifications
Ensure that the suppliers you consider have the necessary certifications that comply with international standards. Certifications such as ISO 9001 for quality management systems or specific industry standards can be a good indicator of a supplier’s commitment to quality.
- Inquire about environmental certifications: In today’s market, sustainability is increasingly important; check for compliance with environmental standards.
- Understand their quality control processes: Ask about their inspection and testing procedures to ensure they maintain high quality throughout production.
Step 5: Request Quotes and Compare Pricing
After narrowing down your list of potential suppliers, request detailed quotes from each. Ensure that the quotes include all relevant costs, such as shipping and duties.
- Analyze the total cost of ownership: Don’t just consider the upfront price; factor in potential shipping delays, customs fees, and payment terms.
- Negotiate terms: Engage in discussions about bulk discounts or long-term contracts to secure the best pricing.
Step 6: Assess Logistics and Delivery Capabilities
Evaluate each supplier’s logistics capabilities, including lead times, shipping options, and delivery reliability. Effective logistics management is crucial for ensuring that your materials arrive on time and in good condition.
- Understand their distribution network: Suppliers with established logistics can often offer better shipping rates and faster delivery times.
- Discuss packaging requirements: Ensure that the supplier can provide suitable packaging to prevent damage during transit.
Step 7: Finalize Contracts and Terms
Once you have selected a supplier, ensure all terms are clearly defined in a contract. This should include payment terms, delivery schedules, quality expectations, and penalties for non-compliance.
- Consult legal advice if necessary: If your procurement involves significant investment, having a legal expert review the contract can safeguard your interests.
- Establish a communication plan: Set clear channels for ongoing communication to address any issues that may arise post-purchase.
By following this checklist, B2B buyers can navigate the complexities of sourcing aluminum extrusion suppliers, ensuring they select partners that align with their operational and strategic objectives.
Comprehensive Cost and Pricing Analysis for aluminum extrusion supplier Sourcing
What Are the Key Cost Components in Aluminum Extrusion Supplier Pricing?
When evaluating the cost structure of aluminum extrusion suppliers, it’s essential to consider several components that contribute to the final pricing. The primary cost components include:
-
Materials: The price of aluminum is influenced by global market trends, availability, and purity levels. Buyers should keep an eye on the London Metal Exchange (LME) prices for real-time updates.
-
Labor: Labor costs vary significantly depending on the region. Countries with higher labor costs may reflect this in their pricing, while regions with lower labor costs may offer more competitive rates.
-
Manufacturing Overhead: This encompasses the indirect costs associated with production, such as utilities, rent, and equipment maintenance. Efficient operations can help mitigate these costs.
-
Tooling: Custom tooling for specific extrusion profiles can be a significant upfront investment. Understanding the tooling costs associated with your specific needs is crucial for accurate budgeting.
-
Quality Control (QC): Ensuring product quality can involve additional costs related to inspections and certifications. Suppliers with robust QC measures may charge higher prices but provide better assurance of product reliability.
-
Logistics: Transportation costs vary based on distance, mode of transport, and the complexity of the supply chain. Incoterms will also affect logistics costs and responsibilities.
-
Margin: Suppliers typically include a profit margin in their pricing. This margin can vary based on competition, market demand, and supplier reputation.
How Do Price Influencers Affect Aluminum Extrusion Costs?
Several factors can influence the pricing of aluminum extrusion products, particularly for international buyers:
-
Volume and Minimum Order Quantity (MOQ): Suppliers often provide discounts for larger orders. Understanding the MOQ can help buyers negotiate better pricing.
-
Specifications and Customization: Custom profiles or specific alloys can incur additional costs. Clear communication of requirements can prevent unexpected pricing changes.
-
Material Quality and Certifications: Higher quality materials and certifications (like ISO or ASTM) can increase costs but may be necessary for specific applications, especially in industries with stringent regulations.
-
Supplier Factors: The supplier’s reputation, reliability, and production capabilities can impact pricing. Established suppliers may charge a premium for their services.
-
Incoterms: The chosen Incoterms dictate who is responsible for shipping costs, insurance, and risks. Selecting favorable terms can significantly impact overall costs.
What Are the Best Negotiation Strategies for B2B Buyers?
To ensure cost-efficiency when sourcing aluminum extrusions, international buyers should consider the following negotiation strategies:
-
Establish Clear Requirements: Clearly outline specifications, expected volumes, and delivery timelines. This can help suppliers provide more accurate quotes.
-
Leverage Multiple Quotes: Obtaining quotes from several suppliers allows buyers to compare prices and services, creating leverage during negotiations.
-
Discuss Long-Term Partnerships: Suppliers may be more willing to negotiate prices for buyers who commit to long-term partnerships, ensuring steady business for them.
-
Evaluate Total Cost of Ownership (TCO): Look beyond initial pricing to consider the total cost of ownership, including maintenance, logistics, and potential downtime costs. This holistic view can guide better purchasing decisions.
-
Stay Informed on Market Trends: Understanding the aluminum market, including global supply chain disruptions or price fluctuations, can provide insights during negotiations.
What Should International Buyers Keep in Mind?
For international B2B buyers, particularly from Africa, South America, the Middle East, and Europe, there are unique pricing nuances to be aware of:
-
Currency Fluctuations: Be mindful of currency exchange rates, as they can affect the final pricing of aluminum products.
-
Import Duties and Taxes: Consider additional costs related to tariffs, taxes, and customs duties when importing goods.
-
Cultural Considerations: Understanding cultural nuances in negotiation styles can enhance communication with suppliers from different regions.
Disclaimer on Pricing
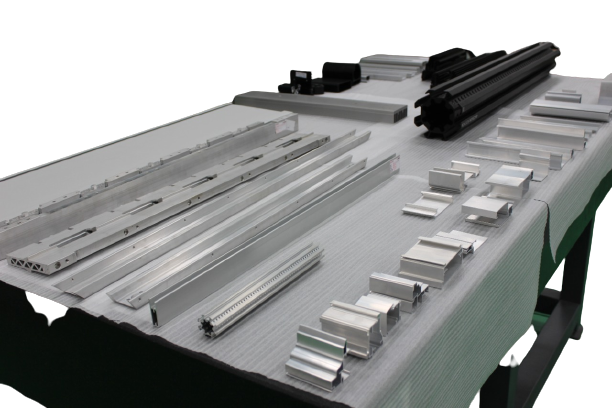
A stock image related to aluminum extrusion supplier.
Prices for aluminum extrusion products can fluctuate due to various factors, including market conditions and supplier pricing strategies. Therefore, it is advisable for buyers to obtain up-to-date quotes and consider all relevant cost components when making purchasing decisions.
Alternatives Analysis: Comparing aluminum extrusion supplier With Other Solutions
When considering solutions for structural and design needs, it’s essential to evaluate various alternatives to aluminum extrusion suppliers. Each option presents unique advantages and challenges that can significantly impact project outcomes. Understanding these alternatives can help international B2B buyers make informed decisions tailored to their specific requirements.
Comparison Table of Aluminum Extrusion Supplier vs Alternatives
Comparison Aspect | Aluminum Extrusion Supplier | Steel Fabrication | Plastic Injection Molding |
---|---|---|---|
Performance | High strength-to-weight ratio, excellent durability | Very strong but heavier; can rust without treatment | Versatile shapes, good for lightweight applications |
Cost | Moderate to high, depending on complexity | Generally lower upfront costs but higher long-term maintenance | Low to moderate, highly dependent on volume |
Ease of Implementation | Straightforward, requires specialized equipment | Requires more labor and time for assembly | High initial setup, but quick for mass production |
Maintenance | Low maintenance; corrosion-resistant finishes available | Requires regular maintenance to prevent rust | Minimal maintenance, but can degrade under UV exposure |
Best Use Case | Ideal for architectural elements, automotive, and aerospace | Best for heavy-duty applications, construction, and machinery | Excellent for consumer products, packaging, and components with complex shapes |
What Are the Advantages and Disadvantages of Steel Fabrication?
Steel fabrication involves the construction of metal structures by cutting, bending, and assembling processes.
Pros:
– Cost-effective for large projects: Steel typically has a lower upfront cost compared to aluminum, making it attractive for large-scale applications.
– Strength: Steel’s high tensile strength allows it to support significant loads, making it ideal for heavy-duty applications.
Cons:
– Weight: Steel is considerably heavier than aluminum, which may lead to higher transportation costs and structural support requirements.
– Corrosion: Without proper treatment, steel can rust, necessitating regular maintenance and protective coatings.
How Does Plastic Injection Molding Compare?
Plastic injection molding is a manufacturing process that involves injecting molten plastic into a mold to create complex shapes.
Pros:
– Versatility: This method can produce intricate designs and is suitable for high-volume production runs.
– Low production costs: For large quantities, the cost per unit is significantly lower compared to aluminum extrusions.
Cons:
– Material limitations: While lightweight, plastic may not be suitable for high-strength applications and can degrade under UV light exposure.
– Initial setup costs: The initial investment for molds can be high, making it less viable for small production runs.
How to Choose the Right Solution for Your Needs
Selecting the appropriate solution requires careful consideration of your project’s specific requirements. For instance, if your application demands high strength and durability with a lightweight advantage, aluminum extrusion might be the best option. Conversely, if cost and heavy load-bearing capacity are your priorities, steel fabrication could be more advantageous. For projects requiring intricate designs and mass production, plastic injection molding may offer the best value.
Ultimately, assessing factors such as performance, cost, ease of implementation, maintenance, and best use cases will lead to a more informed decision, ensuring your investment aligns with your business goals.
Essential Technical Properties and Trade Terminology for aluminum extrusion supplier
What Are the Key Technical Properties of Aluminum Extrusion?
Understanding the critical specifications of aluminum extrusion is essential for international B2B buyers. These properties not only influence the performance and durability of the products but also affect cost and manufacturing processes. Here are some key properties to consider:
1. Material Grade: How Does It Impact Quality?
Aluminum is categorized into various grades, with 6061 and 6063 being the most common in extrusion applications. The grade affects strength, corrosion resistance, and machinability. For example, 6061 is often preferred for structural applications due to its higher strength, while 6063 is favored for architectural applications due to its aesthetic finish. Selecting the right material grade ensures that the product meets the specific requirements of your project.
2. Tolerance: Why Is Precision Important?
Tolerance refers to the permissible limit or limits of variation in a physical dimension. In aluminum extrusion, tight tolerances are critical for ensuring that parts fit together correctly, especially in complex assemblies. For B2B buyers, understanding tolerance specifications helps in assessing whether a supplier can meet the precision required for their projects, thereby minimizing potential production issues.
3. Surface Finish: What Options Are Available?
The surface finish of extruded aluminum can significantly affect both aesthetics and functionality. Common finishes include anodizing, powder coating, and mill finish. Anodizing enhances corrosion resistance and can provide a decorative finish, while powder coating offers a wide range of colors and textures. Buyers should specify their desired surface finish to ensure the final product aligns with their branding and functional needs.
4. Alloy Composition: How Does It Affect Performance?
The alloy composition determines the mechanical properties of aluminum extrusions, such as strength and ductility. For instance, adding copper improves strength but may reduce corrosion resistance. Understanding the composition helps buyers select materials that align with their performance requirements while balancing cost and durability.
5. Extrusion Ratio: What Is Its Significance?
The extrusion ratio is the ratio of the cross-sectional area of the billet to that of the final extruded profile. A higher extrusion ratio generally leads to better mechanical properties and surface finish. Buyers should inquire about the extrusion ratio when assessing suppliers, as it can indicate the quality of the extrusion process.
What Are Common Trade Terms Used in Aluminum Extrusion?
Familiarity with industry terminology can facilitate smoother negotiations and better communication with suppliers. Here are some key terms that B2B buyers should understand:
1. OEM (Original Equipment Manufacturer): What Does It Mean?
An OEM is a company that produces parts or equipment that may be marketed by another manufacturer. In the context of aluminum extrusion, an OEM supplier provides extruded profiles that are incorporated into larger assemblies. Knowing whether a supplier operates as an OEM can help buyers assess their capabilities and the potential for customization.
2. MOQ (Minimum Order Quantity): Why Is It Relevant?
MOQ refers to the smallest quantity of a product that a supplier is willing to sell. This term is crucial for buyers to understand, especially when sourcing custom extrusions, as it can impact inventory costs and project feasibility. Negotiating MOQs can lead to better pricing and flexibility in purchasing.
3. RFQ (Request for Quotation): How Should It Be Used?
An RFQ is a document that buyers send to suppliers to request pricing and terms for specific products or services. This process is essential for comparing multiple suppliers and understanding market rates. Providing detailed specifications in the RFQ can help ensure accurate and competitive quotes.
4. Incoterms: What Are They and Why Do They Matter?
Incoterms are international commercial terms that define the responsibilities of buyers and sellers in the shipping process. Understanding terms like FOB (Free On Board) or CIF (Cost, Insurance, Freight) is vital for managing shipping costs and risks. Buyers should clarify Incoterms with suppliers to avoid misunderstandings regarding delivery and payment responsibilities.
5. Lead Time: How Does It Affect Project Planning?
Lead time refers to the time taken from placing an order to delivery. This is a crucial factor in project management and can impact timelines significantly. Buyers should inquire about lead times during the sourcing process to ensure that suppliers can meet their delivery schedules.
By familiarizing themselves with these technical properties and trade terms, international B2B buyers can make informed decisions when selecting aluminum extrusion suppliers, ultimately enhancing project success.
Navigating Market Dynamics and Sourcing Trends in the aluminum extrusion supplier Sector
What Are the Current Market Dynamics and Key Trends in the Aluminum Extrusion Supplier Sector?
The aluminum extrusion sector is witnessing significant growth driven by various global factors. The demand for lightweight materials across industries such as automotive, construction, and consumer goods is a primary driver. B2B buyers, particularly from Africa, South America, the Middle East, and Europe, are increasingly prioritizing aluminum due to its recyclability and durability. The rise of electric vehicles and sustainable construction practices is further propelling the need for aluminum products.
Current sourcing trends include a shift towards digital procurement platforms, enabling buyers to streamline the purchasing process. Technologies such as blockchain are gaining traction for ensuring transparency in supply chains, which is particularly crucial for international buyers who want to verify the origin and quality of materials. Furthermore, the emphasis on just-in-time manufacturing and lean inventory practices is reshaping how suppliers operate, making it essential for buyers to maintain strong relationships with their suppliers to ensure timely deliveries.
Emerging markets in Africa and South America are beginning to establish themselves as hubs for aluminum production, creating opportunities for local and international partnerships. European suppliers are also focusing on innovation, developing new alloys and profiles that meet specific industry standards, which can be advantageous for buyers looking for customized solutions.
How Can Sustainability and Ethical Sourcing Influence Your B2B Purchasing Decisions?
Sustainability is becoming a critical factor in sourcing decisions within the aluminum extrusion sector. The environmental impact of aluminum production, including energy consumption and greenhouse gas emissions, has led many suppliers to adopt more sustainable practices. Buyers are increasingly looking for suppliers that demonstrate a commitment to reducing their carbon footprint, utilizing recycled materials, and adhering to environmental regulations.
Ethical sourcing is equally important. Buyers should seek suppliers that maintain transparency in their supply chains, ensuring that the materials sourced are not only environmentally friendly but also ethically produced. Certifications such as ISO 14001 for environmental management and the Aluminium Stewardship Initiative (ASI) certification can provide assurance of a supplier’s commitment to sustainability and ethical practices.
By prioritizing suppliers with strong sustainability credentials, B2B buyers can not only enhance their brand reputation but also meet the growing demand from consumers for responsible sourcing. This trend is particularly relevant in Europe, where regulations on sustainability and environmental impact are becoming stricter.
What Is the Historical Context of the Aluminum Extrusion Industry?
The aluminum extrusion industry has evolved significantly since its inception in the early 20th century. Initially dominated by a few key players, the market has expanded globally, particularly post-World War II, as aluminum became a preferred material for its lightweight and corrosion-resistant properties. The introduction of advanced extrusion techniques and technologies has allowed for greater customization and efficiency, catering to diverse industrial needs.
In recent decades, the push for sustainability has reshaped the industry, prompting suppliers to innovate in recycling processes and the development of eco-friendly products. As global markets continue to shift towards sustainable practices, the aluminum extrusion sector is positioned to play a pivotal role in meeting these demands, offering opportunities for B2B buyers to engage with suppliers who prioritize innovation and sustainability.
Frequently Asked Questions (FAQs) for B2B Buyers of aluminum extrusion supplier
-
How do I choose the right aluminum extrusion supplier for my business needs?
When selecting an aluminum extrusion supplier, consider their industry experience, production capabilities, and product range. Review their certifications and quality assurance processes to ensure compliance with international standards. It’s also beneficial to request samples to evaluate material quality. Additionally, assess their ability to customize products based on your specifications and their responsiveness to inquiries, which can indicate their level of customer service. -
What are the typical minimum order quantities (MOQs) for aluminum extrusion products?
Minimum order quantities can vary significantly among suppliers, often depending on the complexity and customization of the extrusions. For standard profiles, MOQs might range from 100 to 500 kilograms, while more specialized or custom designs may require higher quantities. It’s essential to discuss your specific needs with suppliers to find a balance between your order requirements and their MOQ policies. -
What payment terms should I expect when sourcing aluminum extrusions internationally?
Payment terms can vary by supplier and region but typically include options such as advance payment, letters of credit, or net payment terms (e.g., net 30 or net 60 days). When negotiating, consider the financial stability of the supplier and the risks associated with international transactions. Always clarify currency exchange rates and any additional fees that may apply, especially for cross-border payments.
-
How can I ensure quality assurance when sourcing aluminum extrusions?
To guarantee product quality, request certifications such as ISO 9001 or other relevant industry standards from your supplier. Establish clear quality control measures, including specifications for tolerances, surface finishes, and testing methods. Consider arranging third-party inspections or audits to verify the supplier’s processes. Additionally, reviewing customer testimonials and case studies can provide insight into their reliability and product quality. -
What customization options are available for aluminum extrusion products?
Many suppliers offer extensive customization options for aluminum extrusions, including varying shapes, sizes, and surface finishes. You can also request specific alloy compositions to meet unique strength or corrosion resistance requirements. It’s crucial to communicate your design needs clearly to the supplier, including any technical drawings or specifications, to ensure they can meet your expectations. -
What are the logistics considerations when importing aluminum extrusions?
When importing aluminum extrusions, consider shipping methods, lead times, and customs clearance processes. Work with suppliers who have experience in international shipping to ensure compliance with regulations and documentation requirements. Additionally, evaluate the total landed cost, including shipping fees, duties, and taxes, to avoid unexpected expenses. Establish a clear communication channel for tracking shipments and resolving any logistics issues. -
How do I handle disputes with my aluminum extrusion supplier?
To effectively manage disputes, establish clear communication channels and document all agreements and transactions. If issues arise, address them promptly with the supplier to find a resolution. Consider mediation or arbitration as potential solutions if direct negotiations fail. It’s also advisable to include dispute resolution clauses in contracts to outline procedures and responsibilities in case of disagreements. -
What are the environmental considerations when sourcing aluminum extrusions?
When sourcing aluminum extrusions, it’s important to consider the supplier’s environmental practices. Look for suppliers that use recycled aluminum, which can significantly reduce the carbon footprint of your products. Additionally, inquire about their waste management practices and compliance with local and international environmental regulations. Partnering with eco-friendly suppliers not only supports sustainability but can also enhance your brand’s reputation in the marketplace.
Important Disclaimer & Terms of Use
⚠️ Important Disclaimer
The information provided in this guide, including content regarding manufacturers, technical specifications, and market analysis, is for informational and educational purposes only. It does not constitute professional procurement advice, financial advice, or legal advice.
While we have made every effort to ensure the accuracy and timeliness of the information, we are not responsible for any errors, omissions, or outdated information. Market conditions, company details, and technical standards are subject to change.
B2B buyers must conduct their own independent and thorough due diligence before making any purchasing decisions. This includes contacting suppliers directly, verifying certifications, requesting samples, and seeking professional consultation. The risk of relying on any information in this guide is borne solely by the reader.
Strategic Sourcing Conclusion and Outlook for aluminum extrusion supplier
What Are the Key Takeaways for B2B Buyers in Aluminum Extrusion?
In the dynamic landscape of aluminum extrusion, strategic sourcing emerges as a vital approach for international buyers. Understanding supplier capabilities, assessing quality standards, and considering logistical efficiencies are critical to forming successful partnerships. Buyers from Africa, South America, the Middle East, and Europe must prioritize suppliers that demonstrate flexibility, quick turnaround times, and a commitment to sustainability. These factors not only enhance product quality but also foster long-term relationships that can adapt to evolving market needs.
How Can Strategic Sourcing Shape Your Business Future?
As the demand for aluminum products continues to grow, leveraging strategic sourcing can lead to significant cost savings and improved supply chain resilience. Buyers should actively engage with suppliers to explore innovative solutions, including customized products and services tailored to specific project requirements. This proactive engagement will not only streamline operations but also position businesses favorably in competitive markets.
What’s Next for International B2B Buyers?
Looking ahead, international buyers are encouraged to cultivate robust partnerships with aluminum extrusion suppliers who are not just vendors but collaborative allies. By investing in relationships that emphasize quality, reliability, and sustainability, businesses can secure their place in the global marketplace. Start your strategic sourcing journey today to unlock new opportunities and drive success in your projects.