Improve Quality with the Best Homogenizer Manufacturer (2025)
Introduction: Navigating the Global Market for homogenizer manufacturer
In today’s competitive landscape, sourcing the right homogenizer manufacturer can be a daunting task for international B2B buyers, especially those operating in diverse markets across Africa, South America, the Middle East, and Europe. The challenge lies not only in identifying high-quality equipment that meets specific production requirements but also in navigating a complex web of suppliers, regulations, and pricing structures. This comprehensive guide aims to demystify the global market for homogenizers, providing actionable insights into the types of homogenizers available, their applications across various industries, and effective strategies for supplier vetting.
Understanding the nuances of homogenizer technology is crucial for making informed purchasing decisions. This guide will delve into the various types of homogenizers, from high-pressure to ultrasonic models, and their respective applications in sectors such as food and beverage, pharmaceuticals, and cosmetics. Additionally, we will explore essential factors influencing costs, including material quality, energy efficiency, and after-sales support, enabling you to budget effectively.
By equipping international B2B buyers with the knowledge needed to evaluate suppliers and products critically, this guide empowers companies from Nigeria to Mexico to optimize their procurement processes. Whether you are seeking to enhance product consistency, improve texture, or ensure compliance with local regulations, our insights will help you navigate the intricacies of sourcing homogenizers, ultimately driving operational efficiency and product quality.
Understanding homogenizer manufacturer Types and Variations
Type Name | Key Distinguishing Features | Primary B2B Applications | Brief Pros & Cons for Buyers |
---|---|---|---|
High-Pressure Homogenizers | Utilize high pressure to achieve particle size reduction | Food & beverage, pharmaceuticals | Pros: Efficient, versatile; Cons: High initial cost, maintenance-intensive |
Ultrasonic Homogenizers | Use ultrasonic waves for emulsification and dispersion | Cosmetics, pharmaceuticals, food processing | Pros: Precise control, low energy; Cons: Limited capacity, costly for large volumes |
Batch Homogenizers | Process small quantities in batches | Small-scale production, research labs | Pros: Flexible, easy to operate; Cons: Slower processing, not ideal for large volumes |
Inline Homogenizers | Continuous operation for large volumes | Dairy processing, chemical manufacturing | Pros: High throughput, consistent results; Cons: Higher complexity, requires careful setup |
Rotor-Stator Homogenizers | Mechanical mixing using a rotor and stator system | Food processing, biotechnology | Pros: Cost-effective, simple design; Cons: Limited particle size reduction, potential heat generation |
What are High-Pressure Homogenizers and Their B2B Benefits?
High-pressure homogenizers are designed to reduce particle size and improve the stability of emulsions and suspensions. They operate by forcing materials through a narrow gap under high pressure, achieving a uniform product. These machines are particularly suited for industries like food and beverage, where quality and consistency are paramount. When considering high-pressure homogenizers, B2B buyers should evaluate the initial investment against potential productivity gains and maintenance costs, especially in high-demand environments.
How Do Ultrasonic Homogenizers Enhance Product Quality?
Ultrasonic homogenizers leverage high-frequency sound waves to create microscopic bubbles in liquids, leading to effective emulsification and dispersion. They are ideal for applications in cosmetics and pharmaceuticals, where precise formulation is critical. Buyers should consider the operational cost and energy efficiency, as ultrasonic homogenizers can offer significant benefits in terms of quality and precision, albeit with a higher price tag.
Why Choose Batch Homogenizers for Smaller Operations?
Batch homogenizers are suitable for processing smaller quantities and are often used in research labs or for small-scale production. Their flexible operation allows for easy adjustments to meet specific product requirements. However, they may not be the best choice for large-scale operations due to slower processing times. B2B buyers in niche markets should weigh the benefits of flexibility and ease of use against the limitations in throughput.
What Advantages Do Inline Homogenizers Offer for High Volume Production?
Inline homogenizers are designed for continuous processing, making them ideal for industries such as dairy and chemical manufacturing where large volumes are required. They provide consistent results and high throughput, which are essential for maintaining production efficiency. However, B2B buyers must consider the complexity of installation and the need for careful monitoring to ensure optimal operation.
Are Rotor-Stator Homogenizers a Cost-Effective Solution?
Rotor-stator homogenizers utilize a simple mechanical design to mix and emulsify products. They are widely used in food processing and biotechnology due to their cost-effectiveness and ease of operation. While they provide a good solution for many applications, buyers should be aware of their limitations in achieving fine particle sizes and the potential for heat generation during operation. Assessing the specific needs of their production process will help buyers make informed decisions regarding rotor-stator systems.
Key Industrial Applications of homogenizer manufacturer
Industry/Sector | Specific Application of Homogenizer Manufacturer | Value/Benefit for the Business | Key Sourcing Considerations for this Application |
---|---|---|---|
Food & Beverage | Emulsification of sauces and dressings | Improved texture and consistency, enhanced shelf life | Quality of materials, compliance with food safety standards |
Pharmaceuticals | Formulation of creams and ointments | Precise particle size control, uniform distribution | Regulatory compliance, certification, and validation processes |
Cosmetics | Production of lotions and serums | Enhanced absorption and efficacy of active ingredients | Ingredient compatibility, packaging options, and scalability |
Chemical Processing | Homogenization of paints and coatings | Improved stability and performance of final products | Equipment durability, maintenance support, and customization |
Biotechnology | Cell disruption for extraction processes | Increased yield of valuable compounds | Process efficiency, energy consumption, and equipment versatility |
How Are Homogenizers Used in the Food & Beverage Industry?
In the food and beverage sector, homogenizers are essential for emulsifying sauces and dressings. They ensure a uniform texture and consistent quality, which are critical for consumer satisfaction. By reducing particle size, homogenizers enhance the stability and shelf life of products, preventing separation. International buyers, particularly from regions like Africa and South America, should prioritize sourcing equipment that meets stringent food safety standards and offers robust material quality to withstand frequent cleaning and processing demands.
What Role Do Homogenizers Play in Pharmaceuticals?
In the pharmaceutical industry, homogenizers are crucial for formulating creams and ointments. They provide precise control over particle size, ensuring uniform distribution of active ingredients. This uniformity is vital for therapeutic efficacy and patient safety. For B2B buyers in the Middle East and Europe, it’s essential to consider equipment that complies with local regulatory requirements, including certifications and validation processes, to avoid potential liabilities and ensure product quality.
How Are Homogenizers Utilized in Cosmetic Production?
In the cosmetics sector, homogenizers are employed in the production of lotions and serums. They enhance the absorption and efficacy of active ingredients by creating stable emulsions. This results in a superior product that meets consumer expectations for performance. Buyers, especially from emerging markets like Nigeria and Mexico, should look for suppliers that offer customization options and packaging solutions that align with their specific product lines and scalability needs.
What Benefits Do Homogenizers Provide in Chemical Processing?
Homogenizers are instrumental in the chemical processing industry, particularly for the homogenization of paints and coatings. They improve the stability and performance of final products, ensuring that they meet quality standards. For international B2B buyers, considerations should include the durability of the equipment, availability of maintenance support, and the ability to customize the homogenization process to fit specific formulations or production requirements.
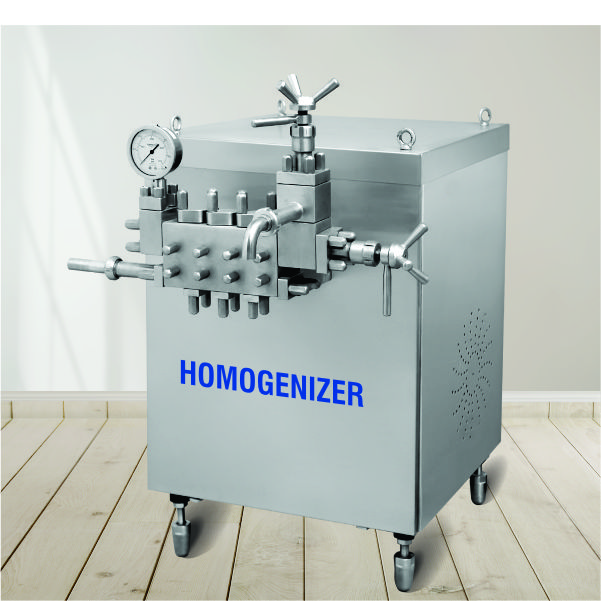
A stock image related to homogenizer manufacturer.
How Are Homogenizers Used in Biotechnology?
In biotechnology, homogenizers facilitate cell disruption for extraction processes, which is essential for obtaining valuable compounds like proteins and enzymes. This process increases the yield and quality of the extracts, making it a crucial step in biomanufacturing. B2B buyers in this field should focus on sourcing equipment that offers high process efficiency and low energy consumption, as well as versatility to adapt to different types of biological materials.
Related Video: Uses Of Polymers | Organic Chemistry | Chemistry | FuseSchool
3 Common User Pain Points for ‘homogenizer manufacturer’ & Their Solutions
Scenario 1: Navigating Complex Sourcing Challenges in Homogenizer Purchases
The Problem: B2B buyers often face significant challenges when sourcing homogenizers. This difficulty is exacerbated by a lack of clear specifications and understanding of the technology behind different homogenizer models. Buyers from regions like Africa and South America may encounter additional hurdles due to limited access to reputable suppliers and manufacturers. This can lead to confusion, wasted resources, and the risk of purchasing equipment that does not meet their operational needs.
The Solution: To effectively navigate the sourcing landscape, buyers should begin by conducting thorough research on homogenizer manufacturers. Utilize online platforms such as industry-specific forums, supplier directories, and trade shows to gather information on various brands. Create a detailed specification sheet that outlines your operational requirements, including capacity, viscosity, and product type. This will serve as a benchmark when comparing different models. Engage directly with manufacturers to ask targeted questions about their equipment’s capabilities and seek recommendations based on your unique needs. Additionally, consider third-party reviews and case studies to validate supplier claims. This comprehensive approach will help ensure you select a homogenizer that aligns perfectly with your production goals.
Scenario 2: Understanding the Technical Aspects of Homogenizer Operation
The Problem: Many B2B buyers, particularly those new to the industry, struggle to understand the technical specifications and operational requirements of homogenizers. This lack of knowledge can lead to improper usage, resulting in subpar product quality, increased downtime, and potential financial losses. For instance, a food processing company in the Middle East may invest in a homogenizer without fully grasping the importance of settings like pressure and flow rate, leading to inefficiencies.
The Solution: To overcome this knowledge gap, buyers should prioritize comprehensive training for their staff on homogenizer operation. Manufacturers often provide training sessions or user manuals that detail the operational parameters and maintenance best practices. Additionally, consider investing in online courses or workshops focused on homogenization techniques. Establishing a partnership with the manufacturer for ongoing support and troubleshooting can also prove beneficial. By ensuring your team is well-versed in the operational aspects of homogenizers, you can optimize performance, enhance product quality, and minimize downtime.
Scenario 3: Addressing Maintenance and Support Issues Post-Purchase
The Problem: After acquiring a homogenizer, many B2B buyers encounter unexpected maintenance challenges. In regions like Europe, where regulations and quality standards are stringent, any malfunction can lead to severe compliance issues and costly production delays. Buyers may find themselves without adequate support from manufacturers, leading to frustration and increased operational costs due to downtime.
The Solution: To mitigate maintenance issues, it is crucial for buyers to establish a clear service agreement with their homogenizer manufacturer prior to purchase. This agreement should outline the level of support, response times for repairs, and availability of spare parts. It’s also advisable to inquire about the manufacturer’s maintenance schedules and whether they offer on-site service. Consider implementing a regular maintenance program that includes routine inspections and preventative maintenance to prolong the life of the equipment. Additionally, joining industry groups or networks can provide access to shared experiences and solutions regarding maintenance challenges. This proactive approach will help ensure consistent operation and compliance with industry standards.
Strategic Material Selection Guide for homogenizer manufacturer
When selecting materials for homogenizers, international B2B buyers must consider various factors that can significantly influence product performance and longevity. The choice of material affects not only the homogenizer’s operational efficiency but also its compatibility with different media, manufacturing complexity, and overall cost. Below, we analyze several common materials used in the manufacturing of homogenizers, focusing on their properties, advantages, disadvantages, and specific considerations for buyers in Africa, South America, the Middle East, and Europe.
What Are the Key Properties of Stainless Steel in Homogenizers?
Stainless steel is one of the most widely used materials in homogenizer manufacturing due to its excellent mechanical properties and resistance to corrosion. It typically has a high-temperature rating, making it suitable for applications involving heat-sensitive materials. The most common grades used are 304 and 316, with 316 offering better corrosion resistance, particularly in saline or acidic environments.
Pros: Stainless steel is durable, easy to clean, and can withstand high pressures. It is also compliant with various international standards, making it a preferred choice for food and pharmaceutical applications.
Cons: The main drawback is its cost, which can be higher than other materials. Additionally, while it is resistant to corrosion, it is not completely immune, especially in harsh chemical environments.
Impact on Application: Stainless steel is compatible with a wide range of media, including food products, pharmaceuticals, and chemicals, making it versatile for various industries.
Considerations for International Buyers: Buyers should ensure compliance with local standards such as ASTM or DIN, particularly in regions like Europe and the Middle East, where regulatory scrutiny is high.
How Does Plastic Compare as a Material for Homogenizers?
Plastic materials, such as polypropylene and polycarbonate, are increasingly used in homogenizers, especially for applications requiring lightweight and cost-effective solutions. They offer good chemical resistance and are less prone to corrosion compared to metals.
Pros: Plastics are generally less expensive and lighter than metals, making them easier to handle and transport. They also provide good insulation properties, which can be advantageous in certain applications.
Cons: The primary limitation of plastic is its lower temperature and pressure tolerance compared to metals. This can restrict its use in high-performance applications.
Impact on Application: Plastics are suitable for homogenizing non-viscous liquids and certain food products but may not be appropriate for high-temperature or high-pressure processes.
Considerations for International Buyers: Buyers should check for compliance with food safety standards, especially in regions like Africa and South America, where regulations can vary widely.
What Are the Advantages of Titanium in Homogenizer Manufacturing?
Titanium is a high-performance material known for its exceptional strength-to-weight ratio and outstanding corrosion resistance. It is particularly advantageous in applications involving aggressive chemicals or extreme conditions.
Pros: Titanium offers superior durability and longevity, making it ideal for demanding applications. Its resistance to corrosion extends its service life significantly.
Cons: The major downside is the high cost of titanium, which can be prohibitive for smaller manufacturers or less demanding applications. Additionally, manufacturing processes involving titanium can be complex and require specialized equipment.
Impact on Application: Titanium is particularly suited for high-performance applications in industries such as pharmaceuticals and chemicals, where media compatibility is critical.
Considerations for International Buyers: Buyers must consider the availability of titanium and its compliance with international standards, particularly in regions with stringent regulations like Europe.
What Role Does Carbon Steel Play in Homogenizer Applications?
Carbon steel is a cost-effective option for homogenizer components that do not require high corrosion resistance. It is often used in applications where the homogenizer is not exposed to harsh chemicals or extreme conditions.
Pros: Carbon steel is relatively inexpensive and has good mechanical properties, making it suitable for various applications.
Cons: The primary limitation is its susceptibility to corrosion, which can lead to shorter product life and increased maintenance costs.
Impact on Application: Carbon steel is best suited for applications involving non-corrosive media, such as certain industrial liquids.
Considerations for International Buyers: Buyers should be aware of the need for protective coatings or treatments to enhance corrosion resistance, especially in humid climates found in parts of Africa and South America.
Summary Table of Material Selection for Homogenizers
Material | Typical Use Case for homogenizer manufacturer | Key Advantage | Key Disadvantage/Limitation | Relative Cost (Low/Med/High) |
---|---|---|---|---|
Stainless Steel | Food and pharmaceutical applications | Excellent corrosion resistance | Higher cost compared to plastics | High |
Plastic | Lightweight, non-viscous liquid applications | Cost-effective and lightweight | Lower temperature/pressure tolerance | Low |
Titanium | Aggressive chemical environments | Superior durability and longevity | High cost and manufacturing complexity | High |
Carbon Steel | Non-corrosive industrial liquids | Cost-effective | Susceptible to corrosion | Medium |
In conclusion, selecting the right material for homogenizers is crucial for ensuring optimal performance and compliance with industry standards. International B2B buyers should carefully evaluate their specific application needs, material properties, and regional regulations to make informed decisions.
In-depth Look: Manufacturing Processes and Quality Assurance for homogenizer manufacturer
What Are the Main Stages of Manufacturing a Homogenizer?
The manufacturing process of homogenizers involves several critical stages, each essential for ensuring the final product meets quality and performance standards. Understanding these stages can help international B2B buyers make informed decisions when sourcing homogenizers.
1. Material Preparation
Material preparation is the first step in the manufacturing process. Manufacturers typically use high-grade stainless steel and other corrosion-resistant materials that can withstand high pressure and temperature. The selection of materials is crucial, as it impacts the durability and efficiency of the homogenizer. Suppliers should provide certifications confirming the material specifications and compliance with international standards.
2. Forming Techniques
After preparing the materials, the next stage involves forming techniques, which may include processes like machining, casting, or forging. For homogenizers, precision machining is often employed to create the various components, such as valves and pumps. This step requires advanced CNC (Computer Numerical Control) technology to ensure tight tolerances and high-quality finishes. B2B buyers should inquire about the equipment used in this stage and the skill level of the technicians involved.
3. Assembly
The assembly stage involves bringing together the various components manufactured in the previous step. This process requires skilled labor and precise procedures to ensure that all parts fit together correctly and operate as intended. Assembly may also involve integrating electronic controls and monitoring systems. It’s essential for buyers to assess the manufacturer’s assembly process, including the training of assembly personnel and the use of assembly jigs and fixtures.
4. Finishing Processes
Finishing processes are vital for enhancing the performance and aesthetic appeal of homogenizers. Techniques such as polishing, anodizing, and coating are commonly used to improve surface quality and corrosion resistance. Buyers should ask manufacturers about their finishing processes and any additional treatments that may enhance the longevity of the equipment.
How Is Quality Assurance Implemented in Homogenizer Manufacturing?
Quality assurance (QA) is a critical component in the production of homogenizers, ensuring that the final products meet both international and industry-specific standards. Buyers need to understand the QA processes in place to evaluate potential suppliers effectively.
What International Standards Should Buyers Be Aware Of?
International standards play a significant role in the quality assurance of homogenizers. ISO 9001 is the most recognized standard, focusing on quality management systems and customer satisfaction. Additionally, industry-specific certifications like CE (Conformité Européenne) and API (American Petroleum Institute) standards may apply, particularly for homogenizers used in the food, pharmaceutical, or chemical industries. Buyers should verify that their suppliers hold relevant certifications and understand the implications of these standards.
What Are the Key Quality Control Checkpoints?
Quality control (QC) checkpoints are integrated throughout the manufacturing process to ensure quality is maintained at every stage. Common checkpoints include:
- Incoming Quality Control (IQC): This involves inspecting raw materials upon arrival to ensure they meet specified requirements.
- In-Process Quality Control (IPQC): This stage includes monitoring the manufacturing processes to detect any deviations in real-time.
- Final Quality Control (FQC): Before shipping, finished products undergo rigorous testing and inspection to confirm they meet all specifications and standards.
B2B buyers should inquire about the frequency and rigor of these QC checks and whether they are documented.
What Testing Methods Are Commonly Used for Homogenizers?
Testing methods are critical to validating the performance and safety of homogenizers. Common testing methods include:
- Hydraulic Testing: To ensure that the equipment can withstand the pressures for which it is designed.
- Performance Testing: Assessing the homogenization efficiency and consistency of the product output.
- Durability Testing: Evaluating the equipment’s longevity under various operational conditions.
Buyers can request detailed testing reports from manufacturers to assess the reliability of their products.
How Can B2B Buyers Verify Supplier Quality Control?
Verifying the quality control processes of suppliers is essential for mitigating risks associated with international purchases. Here are actionable steps buyers can take:
Conduct Supplier Audits
Buyers should perform supplier audits to evaluate the manufacturing facilities and processes. This can include visiting the factory, reviewing production lines, and assessing the quality management systems in place. Audits can reveal a lot about a supplier’s capabilities and commitment to quality.
Request Documentation and Reports
Manufacturers should provide comprehensive documentation, including quality control reports, certificates of compliance, and testing results. Buyers should ensure that these documents are current and align with their quality expectations.
Consider Third-Party Inspections
Engaging third-party inspection services can provide an unbiased evaluation of the supplier’s quality control processes and product quality. These services can conduct random inspections and testing, ensuring that the products meet agreed-upon standards before shipment.
What Are the Quality Control and Certification Nuances for International Buyers?
International buyers should be aware of certain nuances regarding quality control and certification that may affect their purchasing decisions:
- Regional Standards: Different regions may have varying standards and regulations. For example, CE marking is mandatory for products sold in the European market, while other regions may have different compliance requirements.
- Documentation Language: Ensure that all quality documentation is available in a language that is understandable to the buyer to avoid misinterpretation of critical information.
- Cultural Considerations: Understanding the cultural context can help in communication with suppliers, especially when negotiating quality terms or addressing concerns.
By gaining a thorough understanding of the manufacturing processes and quality assurance practices in homogenizer production, B2B buyers can make more informed decisions, ensuring they select reliable suppliers who meet their quality standards.
Practical Sourcing Guide: A Step-by-Step Checklist for ‘homogenizer manufacturer’
This sourcing guide is designed to assist international B2B buyers in effectively procuring homogenizers from reputable manufacturers. Whether you are in Africa, South America, the Middle East, or Europe, following these actionable steps will help you navigate the complexities of sourcing homogenizers tailored to your specific needs.
Step 1: Define Your Technical Specifications
Clearly outlining your technical requirements is the first step to successful sourcing. Consider factors such as the desired homogenization process, the materials to be processed, and production capacity. A well-defined specification will help you communicate your needs to potential suppliers, ensuring they can meet your expectations.
- Homogenization Type: Decide whether you need high-pressure or low-pressure homogenizers based on your application.
- Material Compatibility: Ensure the homogenizer can handle the specific types of materials you plan to process.
Step 2: Research Potential Suppliers
Conduct thorough research to identify manufacturers with a strong reputation in the homogenizer market. Utilize online resources, industry directories, and trade shows to compile a list of potential suppliers. Pay attention to their market presence and customer reviews.
- Industry Experience: Look for suppliers with extensive experience in your industry.
- Geographic Considerations: Consider suppliers located in regions with established manufacturing capabilities, such as Europe or the Middle East.
Step 3: Evaluate Supplier Capabilities
Before making a commitment, it’s crucial to assess the capabilities of potential suppliers. Request detailed company profiles, product catalogs, and case studies. This information will provide insight into their manufacturing processes and quality control measures.
- Production Capacity: Ensure the supplier can meet your volume requirements.
- Quality Assurance: Verify their quality management systems, such as ISO certifications.
Step 4: Verify Supplier Certifications
Certifications can indicate a supplier’s commitment to quality and safety standards. Check for relevant certifications such as ISO 9001 or CE marking, which are essential for ensuring compliance with international standards.
- Compliance with Regulations: Ensure the supplier adheres to industry-specific regulations in your region.
- Sustainability Practices: Look for certifications related to environmental management if sustainability is a priority for your company.
Step 5: Request Samples and Conduct Tests
To evaluate the performance of the homogenizer, request samples for testing. This step is critical as it allows you to assess the machine’s efficiency, durability, and suitability for your specific applications.
- Test Results: Analyze how well the homogenizer meets your technical specifications through performance tests.
- User Experience: Gather feedback from your operational team on the usability and functionality of the samples.
Step 6: Negotiate Terms and Pricing
Once you have identified a suitable supplier, engage in negotiations to establish favorable terms and pricing. Be clear about your budget constraints and seek value-added services such as installation, training, and after-sales support.
- Payment Terms: Discuss flexible payment options that work for both parties.
- Warranty and Support: Ensure that warranty terms and customer support are clearly outlined in the agreement.
Step 7: Establish a Communication Plan
Effective communication is essential throughout the procurement process. Establish regular check-ins with your supplier to discuss progress, address concerns, and ensure that timelines are being met.
- Point of Contact: Designate a key contact person on both sides to facilitate smooth communication.
- Feedback Mechanism: Implement a system for providing feedback during and after the procurement process to enhance future collaborations.
By following this checklist, international B2B buyers can make informed decisions when sourcing homogenizers, ensuring that they partner with reliable manufacturers who can meet their specific needs.
Comprehensive Cost and Pricing Analysis for homogenizer manufacturer Sourcing
What Are the Key Cost Components in Sourcing a Homogenizer Manufacturer?
When sourcing homogenizers, understanding the underlying cost components is essential for international B2B buyers. The primary factors influencing the total cost include:
-
Materials: The choice of materials significantly affects pricing. High-quality stainless steel and specialized alloys may increase costs but offer better durability and performance.
-
Labor: Labor costs vary by region and impact the overall price. Countries with lower labor costs may present opportunities for more competitive pricing, but quality control can be a concern.
-
Manufacturing Overhead: This includes factory operation costs, utilities, and administrative expenses. Efficient manufacturing processes can reduce overhead, which in turn lowers prices.
-
Tooling: Custom tooling is often necessary for specialized homogenizers. The cost of designing and producing these tools can be substantial, particularly for unique specifications.
-
Quality Control (QC): Rigorous QC measures ensure product reliability and compliance with international standards. While this adds to the upfront cost, it can prevent costly failures in the long run.
-
Logistics: Transportation costs can fluctuate based on distance, shipping methods, and fuel prices. International buyers should consider these variables when assessing total costs.
-
Margin: Suppliers will include their profit margin in the final price. Understanding typical margins in your target market can help you negotiate better.
How Do Price Influencers Affect Homogenizer Costs for International Buyers?
Several factors can influence the pricing of homogenizers, particularly for buyers in Africa, South America, the Middle East, and Europe:
-
Volume and Minimum Order Quantity (MOQ): Larger orders often lead to lower per-unit costs. Buyers should assess their needs against supplier MOQs to optimize pricing.
-
Specifications and Customization: Custom features or specifications can drive prices up. Clearly defining your requirements from the start can help manage costs.
-
Materials and Quality Certifications: Higher-grade materials and certifications (like ISO standards) add to costs but can enhance product longevity and compliance with regulatory standards.
-
Supplier Factors: Supplier reputation, experience, and location can influence pricing. Established suppliers may charge a premium for reliability and service.
-
Incoterms: The chosen Incoterms can significantly impact total costs. Understanding terms like FOB (Free On Board) or CIF (Cost, Insurance, and Freight) is crucial for budgeting.
What Tips Can Help B2B Buyers Negotiate Better Prices for Homogenizers?
For international buyers, especially those in emerging markets, effective negotiation and cost management strategies are vital:
-
Engage in Thorough Market Research: Understand the pricing landscape and supplier capabilities in your target regions. This knowledge will empower you during negotiations.
-
Focus on Total Cost of Ownership (TCO): Consider not only the purchase price but also long-term costs associated with maintenance, energy consumption, and potential downtime. A higher initial investment might yield lower TCO.
-
Build Relationships with Suppliers: Establishing a strong rapport can lead to better pricing and terms. Long-term partnerships often result in loyalty discounts and prioritized service.
-
Leverage Volume Purchasing: If feasible, consolidate purchases with other companies to meet MOQs and negotiate bulk pricing.
-
Be Open to Alternative Suppliers: Diversifying your supplier base can provide leverage in negotiations and reduce dependency on a single source.
What Should International Buyers Consider Regarding Indicative Prices?
It’s important to note that prices for homogenizers can vary significantly based on the factors outlined above. Always request detailed quotes and be wary of indicative prices that do not account for your specific requirements. Engaging multiple suppliers for comparative quotes can help you identify fair pricing and ensure you receive the best value for your investment.
Alternatives Analysis: Comparing homogenizer manufacturer With Other Solutions
Understanding the Importance of Alternative Solutions in Homogenization
In the world of manufacturing and processing, homogenization plays a critical role in achieving desired product consistency and quality. While selecting a homogenizer manufacturer is common, it’s essential to explore alternative solutions that might better suit specific operational needs or budget constraints. This section compares traditional homogenizer manufacturers with other viable methods, enabling B2B buyers to make informed decisions tailored to their requirements.
Comparison Table: Homogenizer Manufacturer vs. Alternative Solutions
Comparison Aspect | Homogenizer Manufacturer | High-Shear Mixer | Ultrasonic Processor |
---|---|---|---|
Performance | Excellent for emulsions and suspensions | Good for blending and emulsifying | Effective for cell disruption and emulsification |
Cost | Moderate to High | Lower Initial Cost | Moderate to High |
Ease of Implementation | Requires specialized setup and training | Relatively easy to set up and operate | Requires technical expertise |
Maintenance | Regular maintenance required | Low maintenance needs | Moderate maintenance needs |
Best Use Case | Pharmaceutical, food & beverage | Cosmetics, food products | Biotechnology, pharmaceuticals |
What Are the Advantages and Disadvantages of a High-Shear Mixer?
High-shear mixers are an alternative often used in various industries for blending and emulsifying ingredients. One of the main advantages is their lower initial cost compared to traditional homogenizers, making them accessible for small to medium-sized enterprises. They are relatively easy to set up and operate, reducing training time for staff. However, while they perform well for many applications, they may not achieve the same level of emulsification or particle size reduction as homogenizers, which can be critical in industries such as pharmaceuticals or food processing where product quality is paramount.
How Does an Ultrasonic Processor Compare to a Homogenizer Manufacturer?
Ultrasonic processors utilize high-frequency sound waves to create intense pressure changes, leading to cavitation bubbles that break down materials. This method is particularly effective for applications requiring cell disruption, such as in biotechnology or pharmaceuticals. While they provide excellent performance for specific applications, the initial investment can be on par with or even exceed that of traditional homogenizers. Furthermore, ultrasonic processors often require a higher level of technical expertise for operation and maintenance, which may not be feasible for all businesses. Despite these drawbacks, their effectiveness in certain applications can make them a worthwhile consideration for specialized industries.
How Can B2B Buyers Choose the Right Solution for Their Needs?
When evaluating homogenizer manufacturers against alternative solutions, B2B buyers should consider several factors, including the specific application, budget constraints, and operational capabilities. Understanding the performance requirements of the product is critical; for instance, if ultra-fine emulsification is necessary, a traditional homogenizer may be indispensable. Conversely, for businesses focused on cost efficiency and ease of use, high-shear mixers could be more appropriate. Additionally, the level of technical expertise available within the organization can influence the choice of equipment. By aligning the chosen solution with operational goals and resource availability, buyers can make strategic decisions that enhance productivity and product quality.
Essential Technical Properties and Trade Terminology for homogenizer manufacturer
What Are the Critical Technical Properties of Homogenizers?
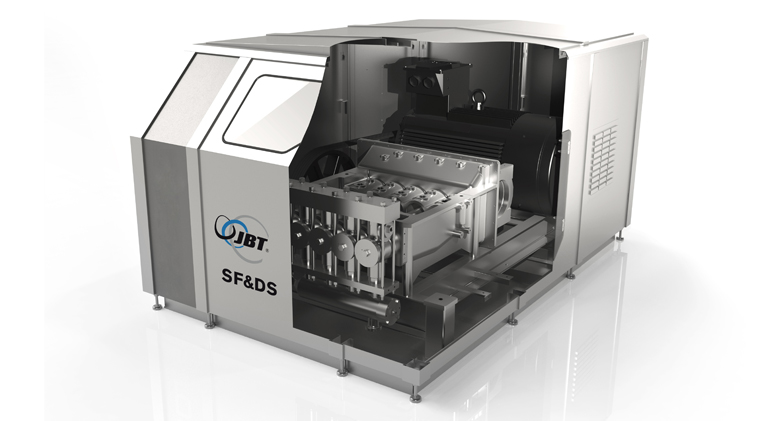
A stock image related to homogenizer manufacturer.
When sourcing homogenizers, understanding their technical specifications is crucial for making informed purchasing decisions. Below are some of the essential properties that international B2B buyers should consider:
1. Material Grade
Homogenizers are typically constructed from stainless steel or other corrosion-resistant materials. The grade of material affects durability, hygiene, and suitability for various applications. For instance, 316 stainless steel is preferred in food and pharmaceutical industries due to its resistance to corrosion and ability to withstand high-pressure environments. Selecting the appropriate material grade ensures longevity and compliance with industry standards.
2. Tolerance Levels
Tolerance refers to the allowable variation in a manufactured component’s dimensions. For homogenizers, tight tolerance levels are critical to achieving consistent particle size reduction and product uniformity. A tolerance of ±0.1 mm is often standard, especially for applications requiring precise emulsification. Understanding tolerance levels helps buyers gauge the precision of the equipment and its capacity to meet specific processing needs.
3. Flow Rate
The flow rate of a homogenizer indicates the volume of product that can be processed per hour. It is essential for determining how well the equipment can meet production demands. For instance, a homogenizer with a flow rate of 500 liters per hour is suitable for medium-sized operations. Buyers should assess their production scale and select a homogenizer that aligns with their throughput requirements to avoid bottlenecks.
4. Pressure Rating
Pressure rating signifies the maximum pressure the homogenizer can handle during operation. Common ratings range from 10,000 to 30,000 psi, depending on the application. High-pressure homogenizers are essential for achieving finer emulsions and dispersions. Understanding pressure ratings ensures that the chosen equipment can effectively process the intended materials without risk of failure.
5. Energy Efficiency
In today’s competitive market, energy efficiency is a significant consideration. Homogenizers with advanced motor designs or variable frequency drives can reduce energy consumption and operational costs. Buyers should inquire about the energy ratings of potential equipment to optimize operational efficiency and minimize environmental impact.
What Are Common Trade Terms in the Homogenizer Manufacturing Industry?
Understanding industry jargon is equally important for effective communication and negotiation in the B2B landscape. Here are some common terms related to homogenizer manufacturing:
1. OEM (Original Equipment Manufacturer)
An OEM is a company that produces components or equipment that are sold under another company’s brand name. For buyers, working with an OEM can ensure high-quality products tailored to specific needs. Understanding OEM relationships can aid in establishing trust and reliability in supply chains.
2. MOQ (Minimum Order Quantity)
MOQ refers to the smallest quantity of goods a supplier is willing to sell. In the homogenizer market, MOQs can impact purchasing decisions, especially for smaller manufacturers. Buyers should negotiate MOQs to align with their production requirements while ensuring they receive favorable pricing.
3. RFQ (Request for Quotation)
An RFQ is a document sent to suppliers to request pricing and terms for specific products. Crafting a clear RFQ for homogenizers can help streamline the sourcing process and facilitate comparisons between different manufacturers. Including detailed specifications and quantities in an RFQ can yield more accurate and competitive quotes.
4. Incoterms
Incoterms (International Commercial Terms) define the responsibilities of buyers and sellers in international shipping. Terms like FOB (Free on Board) and CIF (Cost, Insurance, and Freight) dictate who is responsible for shipping costs and risks. Familiarity with Incoterms helps buyers navigate logistics and avoid misunderstandings in international transactions.
5. Lead Time
Lead time refers to the period between placing an order and receiving the product. In the context of homogenizers, understanding lead times is essential for planning production schedules. Buyers should discuss lead times with suppliers to ensure timely delivery that aligns with their operational needs.
By familiarizing themselves with these technical properties and trade terms, international B2B buyers can make informed decisions when sourcing homogenizers, ultimately enhancing their operational efficiency and product quality.
Navigating Market Dynamics and Sourcing Trends in the homogenizer manufacturer Sector
What Are the Key Market Trends Influencing the Homogenizer Manufacturer Sector?
The global homogenizer market is witnessing significant growth, driven by the increasing demand for processed food and beverage products, as well as advancements in pharmaceutical and cosmetic applications. Emerging economies in Africa, South America, the Middle East, and Europe are particularly influencing these trends. For instance, the rise of urbanization and changing consumer preferences in countries like Nigeria and Mexico are propelling the need for high-quality homogenized products. B2B buyers in these regions should pay close attention to technological advancements such as the integration of IoT (Internet of Things) in homogenizers, which enhances process monitoring and product consistency.
Additionally, the shift towards automation and smart manufacturing is transforming sourcing strategies. Buyers should consider suppliers that offer not only equipment but also digital solutions that streamline operations. This convergence of technology and equipment is expected to improve efficiency, reduce waste, and enhance product quality, making it essential for international buyers to evaluate potential partners based on their technological capabilities.
How Important Is Sustainability and Ethical Sourcing in the Homogenizer Sector?
As global awareness of environmental issues increases, sustainability is becoming a pivotal factor in the sourcing decisions of B2B buyers. The homogenizer manufacturing sector is no exception, with a growing emphasis on reducing the environmental impact of production processes. Buyers should prioritize suppliers that utilize ‘green’ materials and have certifications such as ISO 14001, which demonstrates a commitment to effective environmental management systems.
Ethical sourcing practices are also gaining traction, particularly in regions where social responsibility is closely tied to brand reputation. Buyers should investigate the supply chains of potential vendors to ensure they adhere to fair labor practices and sustainable sourcing. This not only aligns with global trends but can also enhance brand loyalty among environmentally-conscious consumers. By selecting suppliers who prioritize sustainability, B2B buyers can contribute to a more responsible industry while also meeting the growing demand for eco-friendly products.
How Has the Homogenizer Industry Evolved Over Time?
The homogenizer industry has evolved significantly over the past few decades, transitioning from simple mechanical devices to sophisticated machines equipped with advanced technology. Initially used primarily in the dairy sector, homogenizers now find applications across various industries, including food and beverage, pharmaceuticals, and cosmetics. This diversification has been fueled by advancements in technology, which have enhanced the efficiency and precision of homogenization processes.
With the growing demand for high-quality emulsions and consistent product texture, manufacturers have had to innovate continuously. As a result, today’s homogenizers are not only more efficient but also increasingly capable of producing a wider range of products. This evolution highlights the importance for B2B buyers to remain informed about the latest innovations and technologies to make strategic sourcing decisions that align with their operational needs.
Frequently Asked Questions (FAQs) for B2B Buyers of homogenizer manufacturer
-
How do I choose the right homogenizer manufacturer for my business needs?
Choosing the right homogenizer manufacturer involves assessing several key factors. First, evaluate the manufacturer’s experience and expertise in your specific industry, as this can significantly impact the quality of the equipment. Next, consider their production capacity and lead times to ensure they can meet your demands. Additionally, request references or case studies from similar businesses to gauge their reliability. Finally, review their customer service and support options, as ongoing assistance is crucial for equipment maintenance and troubleshooting. -
What are the essential features to look for in a homogenizer?
When sourcing a homogenizer, prioritize features that align with your production needs. Consider the type of materials you will be processing, as different homogenizers are designed for specific applications (e.g., food, pharmaceuticals, or cosmetics). Look for adjustable pressure settings, ease of cleaning, and energy efficiency. Additionally, ensure the homogenizer offers consistent particle size reduction, as this can affect product quality. Lastly, check if the manufacturer provides customization options to tailor the machine to your specifications. -
What are the minimum order quantities (MOQs) for homogenizers?
Minimum order quantities (MOQs) can vary significantly among homogenizer manufacturers, often depending on the type and complexity of the equipment. For standard models, MOQs may range from one unit to several dozen, while custom-designed homogenizers may require higher volumes to justify production costs. It’s crucial to discuss MOQs with potential suppliers upfront to ensure they align with your purchasing capabilities. Additionally, inquire about the possibility of sample units or trial runs if you’re uncertain about committing to larger orders. -
How can I vet a homogenizer manufacturer for quality assurance?
To vet a homogenizer manufacturer, start by reviewing their certifications and compliance with international quality standards, such as ISO 9001. Request documentation of their quality control processes, including testing procedures and equipment used during production. Consider visiting their facility if possible, or request a virtual tour to observe their operations firsthand. Additionally, seek customer testimonials or reviews to understand their reputation in the industry. Lastly, inquire about after-sales support and warranty policies, as these can be indicators of their commitment to quality. -
What payment terms should I expect when purchasing homogenizers internationally?
Payment terms for international purchases of homogenizers can vary widely. Common options include advance payment, partial payments, or payment upon delivery. Many manufacturers may request a deposit (typically 30-50%) to initiate production, with the balance due before shipping. It’s advisable to negotiate terms that provide you with a sense of security, such as escrow services or letters of credit, especially when dealing with new suppliers. Always clarify payment methods accepted and any additional costs, such as taxes or tariffs, to avoid surprises. -
How do logistics and shipping impact the procurement of homogenizers?
Logistics and shipping play a crucial role in the procurement of homogenizers, especially when sourcing from international manufacturers. Consider factors like shipping timelines, costs, and customs clearance processes. Work with suppliers who have experience in exporting machinery to your region, as they can navigate potential challenges more effectively. Additionally, discuss the terms of delivery (e.g., FOB, CIF) to understand who is responsible for various shipping costs. Lastly, ensure your chosen logistics partner can handle the transportation of heavy machinery safely and efficiently. -
What are the common challenges faced when sourcing homogenizers from Africa, South America, or the Middle East?
Sourcing homogenizers from regions like Africa, South America, or the Middle East can present unique challenges. These may include fluctuating currency rates, varying regulatory standards, and potential communication barriers with manufacturers. Additionally, infrastructure issues, such as unreliable shipping routes or delays in customs, can affect delivery times. To mitigate these challenges, conduct thorough research on the local market and regulatory environment. Establish strong communication channels with suppliers and consider working with local agents who understand the regional landscape. -
How important is after-sales support when choosing a homogenizer manufacturer?
After-sales support is critical when selecting a homogenizer manufacturer, as it ensures that you have access to assistance for installation, maintenance, and repairs. A manufacturer that provides robust support can help minimize downtime and keep your operations running smoothly. Inquire about their customer service availability, warranty terms, and whether they offer training for your staff on using the equipment. Additionally, check if they have a network of local technicians or service centers, which can significantly reduce response times for any issues that may arise.
Important Disclaimer & Terms of Use
⚠️ Important Disclaimer
The information provided in this guide, including content regarding manufacturers, technical specifications, and market analysis, is for informational and educational purposes only. It does not constitute professional procurement advice, financial advice, or legal advice.
While we have made every effort to ensure the accuracy and timeliness of the information, we are not responsible for any errors, omissions, or outdated information. Market conditions, company details, and technical standards are subject to change.
B2B buyers must conduct their own independent and thorough due diligence before making any purchasing decisions. This includes contacting suppliers directly, verifying certifications, requesting samples, and seeking professional consultation. The risk of relying on any information in this guide is borne solely by the reader.
Strategic Sourcing Conclusion and Outlook for homogenizer manufacturer
In today’s competitive landscape, strategic sourcing for homogenizers plays a critical role in optimizing operational efficiency and enhancing product quality. International B2B buyers, particularly from regions like Africa, South America, the Middle East, and Europe, must prioritize sourcing strategies that align with their specific market needs and regulatory requirements. Understanding local supplier capabilities and leveraging global partnerships can significantly reduce costs while ensuring access to advanced technology and innovation.
What are the key benefits of strategic sourcing for homogenizers? By adopting a comprehensive sourcing approach, businesses can achieve better price negotiations, enhance supply chain resilience, and gain insights into emerging trends within the homogenization sector. This not only fosters long-term relationships with suppliers but also positions companies to respond effectively to market fluctuations.
As we look to the future, the demand for high-performance homogenizers will continue to grow, driven by advancements in food and beverage, pharmaceuticals, and cosmetics industries. International buyers should remain proactive, exploring new supplier relationships and evaluating their sourcing strategies. Embracing digital tools for supplier management and market intelligence will empower companies to navigate the evolving landscape successfully. Engage with potential suppliers today to secure a competitive advantage and drive sustainable growth in your operations.