Improve Safety and Efficiency: Your Work Gloves Supplier Guide (2025)
Introduction: Navigating the Global Market for work gloves supplier
In an increasingly interconnected world, sourcing high-quality work gloves can present a daunting challenge for international B2B buyers. Whether you’re operating in the bustling markets of Africa, the dynamic landscapes of South America, the rapidly developing regions of the Middle East, or the established industries of Europe, the need for protective gear that balances comfort and safety is paramount. This guide is designed to simplify the complex process of selecting a reliable work gloves supplier by providing a comprehensive overview of the various types of gloves available, their applications across different industries, and the critical factors to consider when vetting suppliers.
Understanding the nuances of work gloves—from cut-resistant options for manufacturing to heat-resistant gloves for the food industry—can empower you to make informed purchasing decisions. We delve into essential aspects such as cost considerations, compliance with international safety standards, and the importance of supplier certifications. Additionally, this guide offers actionable insights into evaluating supplier reliability, which is crucial for ensuring a consistent supply chain.
By equipping yourself with the knowledge presented in this guide, you can navigate the global market confidently, ensuring that you select a supplier that not only meets your operational needs but also aligns with your quality standards and budget constraints. The journey to finding the right work gloves supplier starts here, enabling you to protect your workforce while enhancing productivity and safety across your operations.
Understanding work gloves supplier Types and Variations
Type Name | Key Distinguishing Features | Primary B2B Applications | Brief Pros & Cons for Buyers |
---|---|---|---|
Leather Work Gloves | Durable, abrasion-resistant, often insulated | Construction, heavy machinery | Pros: Excellent durability; Cons: Higher cost compared to synthetic options. |
Cut-Resistant Gloves | Made from specialized materials like Kevlar or Dyneema | Manufacturing, glass handling | Pros: High protection level; Cons: May reduce dexterity. |
Disposable Gloves | Made from latex, nitrile, or vinyl | Food service, healthcare | Pros: Convenient and hygienic; Cons: Limited durability. |
Thermal Insulated Gloves | Insulated lining for cold environments | Cold storage, outdoor work | Pros: Keeps hands warm; Cons: Can be bulky. |
Chemical-Resistant Gloves | Resistant to hazardous substances | Chemical handling, laboratories | Pros: Protects against chemicals; Cons: Specific to certain chemicals. |
What are Leather Work Gloves and Their B2B Applications?
Leather work gloves are renowned for their durability and resistance to abrasion, making them a staple in industries such as construction and heavy machinery operation. They often provide insulation, which is beneficial for outdoor work in colder climates. When purchasing leather gloves, B2B buyers should consider the specific type of leather used, as this can affect both performance and cost. While they offer excellent protection, the initial investment can be higher compared to synthetic gloves.
How Do Cut-Resistant Gloves Enhance Workplace Safety?
Cut-resistant gloves are designed with specialized materials like Kevlar or Dyneema, providing exceptional protection against cuts and lacerations. They are crucial in manufacturing environments, particularly those involving sharp tools or materials, such as glass handling. B2B buyers should evaluate the cut resistance rating and ensure the gloves meet industry standards. While these gloves offer high protection, they may compromise dexterity, which is a vital factor for tasks requiring precision.
Why Choose Disposable Gloves for Your Business?
Disposable gloves, available in materials like latex, nitrile, or vinyl, are essential in industries such as food service and healthcare. They provide convenience and maintain hygiene, as they can be discarded after a single use. When selecting disposable gloves, buyers should consider the material’s sensitivity to chemicals, potential allergies, and the level of protection needed. While they are cost-effective and easy to use, their limited durability makes them unsuitable for tasks requiring prolonged use.
What Are the Benefits of Thermal Insulated Gloves?
Thermal insulated gloves are designed to protect hands from extreme cold, making them ideal for cold storage facilities and outdoor work environments. These gloves typically feature an insulated lining that retains heat, ensuring comfort during prolonged exposure to low temperatures. B2B buyers should assess the level of insulation and the gloves’ bulkiness, as thicker gloves can hinder dexterity. While they effectively keep hands warm, the trade-off may be reduced tactile sensitivity.
How Do Chemical-Resistant Gloves Protect Workers?
Chemical-resistant gloves are specifically engineered to protect against hazardous substances, making them vital in chemical handling and laboratory settings. They are crafted from materials that resist permeation and degradation from various chemicals. Buyers in B2B contexts should identify the specific chemicals their workforce will encounter and choose gloves designed for those substances. While these gloves offer critical protection, they are often specialized, which can limit their use across different tasks.
Related Video: Work Gloves For Different Jobs: Gloves For Electricians
Key Industrial Applications of work gloves supplier
Industry/Sector | Specific Application of Work Gloves Supplier | Value/Benefit for the Business | Key Sourcing Considerations for this Application |
---|---|---|---|
Construction | Hand protection for workers handling heavy materials and tools | Reduces injury risk, ensuring worker safety and compliance | Material durability, grip quality, and compliance with safety standards |
Manufacturing | Gloves for assembly line workers in automotive and electronics | Enhances productivity while protecting against cuts and abrasions | Custom sizes and ergonomic designs to fit diverse workforce |
Agriculture | Protective gloves for handling chemicals and machinery | Prevents skin exposure to harmful substances and injuries | Chemical resistance, comfort for extended wear, and compliance with agricultural regulations |
Oil and Gas | Gloves for workers in drilling and extraction operations | Ensures safety in hazardous environments while maintaining dexterity | Heat resistance, oil and chemical protection, and ANSI certifications |
Food Processing | Sanitary gloves for food handling and preparation | Maintains hygiene standards, preventing contamination | FDA compliance, material safety for food contact, and comfort for long use |
How Are Work Gloves Used in the Construction Industry?
In the construction sector, work gloves are essential for protecting workers from injuries while handling heavy materials and using various tools. Suppliers provide gloves designed to offer high durability, grip, and protection against cuts and abrasions. For international buyers, sourcing gloves that meet local safety regulations and standards is crucial, particularly in regions like Africa and South America, where construction sites may have unique challenges such as extreme weather conditions.
What Are the Applications of Work Gloves in Manufacturing?
Manufacturing environments, especially in automotive and electronics, require gloves that protect assembly line workers from sharp objects while maintaining dexterity. Work gloves suppliers offer specialized gloves that enhance productivity and minimize injury risks. Buyers should consider factors such as custom sizing and ergonomic designs to accommodate diverse workforce needs in Europe and the Middle East, ensuring comfort during long shifts.
How Do Work Gloves Benefit Agriculture Workers?
In agriculture, gloves are vital for protecting workers from exposure to chemicals and injuries when operating machinery. Suppliers provide gloves that are chemically resistant and designed for comfort during prolonged use. International buyers must ensure that the gloves comply with local agricultural regulations and standards, particularly in regions like South Africa and South America, where diverse crops and chemicals may be used.
What Is the Importance of Work Gloves in the Oil and Gas Industry?
Work gloves in the oil and gas sector are specifically designed to withstand harsh conditions, including exposure to heat, oil, and chemicals. These gloves ensure safety for workers involved in drilling and extraction operations, allowing them to perform tasks with dexterity. Buyers should prioritize sourcing gloves that meet ANSI certifications and provide adequate protection against the specific hazards present in their operational environments.
Why Are Sanitary Gloves Essential in Food Processing?
In food processing, maintaining hygiene is paramount, making sanitary gloves a critical requirement for food handling and preparation. Suppliers offer gloves that comply with FDA regulations to prevent food contamination. International buyers in Europe and the Middle East should focus on sourcing gloves that are safe for food contact and comfortable for extended wear, thereby ensuring compliance with stringent food safety standards.
Related Video: How to Choose the Right Nitrile Gloves
3 Common User Pain Points for ‘work gloves supplier’ & Their Solutions
Scenario 1: Inconsistent Quality of Work Gloves
The Problem: International B2B buyers often face the challenge of inconsistent quality in work gloves supplied by manufacturers. This inconsistency can lead to serious safety risks for workers, especially in high-risk environments such as construction, manufacturing, or chemical handling. A buyer might receive a batch of gloves that do not meet the specified safety standards, leading to increased liability, worker injuries, and potential legal ramifications.
The Solution: To mitigate quality issues, buyers should establish clear quality specifications and conduct thorough supplier evaluations before placing orders. This includes requesting samples from potential suppliers to assess the quality firsthand. Implementing a robust quality assurance process, such as third-party inspections and audits, can further ensure that the gloves meet the required standards. Buyers should also consider building long-term relationships with suppliers who have a proven track record of quality compliance, thus reducing the risk of receiving subpar products.
Scenario 2: Limited Customization Options for Specific Needs
The Problem: Many B2B buyers require customized work gloves tailored to specific tasks or environments, but often encounter suppliers who offer a limited range of options. For instance, a company in South Africa may need gloves that provide both dexterity for precision tasks and cut resistance for safety, but find that their suppliers only offer generic products that do not meet these specific needs.
The Solution: Buyers should actively seek suppliers that specialize in customization. This can involve discussing specific requirements upfront, such as materials, sizes, and safety features, to ensure that the supplier can accommodate these needs. Utilizing technology such as 3D modeling and virtual prototypes can help buyers visualize the final product before production. Additionally, engaging in discussions with suppliers about developing bespoke solutions can foster innovation and result in gloves that are specifically designed for the buyer’s operational challenges.
Scenario 3: Challenges in Sourcing Sustainable Work Gloves
The Problem: With the growing emphasis on sustainability, many international B2B buyers are struggling to find work gloves that align with eco-friendly practices. For example, a buyer from Europe may want to source gloves made from biodegradable materials or those produced under fair labor conditions, but often finds that suppliers do not clearly disclose their sustainability practices.
The Solution: To address this, buyers should prioritize transparency in the sourcing process. This involves asking suppliers for detailed information about their manufacturing processes, sourcing of materials, and labor practices. Certifications such as ISO 14001 (Environmental Management) and Fair Trade can serve as indicators of a supplier’s commitment to sustainability. Establishing a set of sustainability criteria that suppliers must meet can streamline the selection process and help buyers align their procurement practices with corporate social responsibility goals. Additionally, forming partnerships with suppliers dedicated to sustainable practices can enhance brand reputation and appeal to eco-conscious customers.
Strategic Material Selection Guide for work gloves supplier
When selecting materials for work gloves, international B2B buyers must consider various factors that affect performance, durability, and compliance with regional standards. Here, we analyze four common materials used in work gloves, highlighting their properties, advantages, disadvantages, and specific considerations for buyers from Africa, South America, the Middle East, and Europe.
What Are the Key Properties of Leather in Work Gloves?
Leather is a traditional material known for its durability and comfort. It offers excellent abrasion resistance and can withstand a range of temperatures, making it suitable for various applications.
- Key Properties: Leather gloves typically have a temperature rating of up to 200°F (93°C) and are resistant to cuts and punctures.
- Pros: They provide a good grip, are breathable, and conform well to hand shapes over time.
- Cons: Leather can be expensive, requires maintenance to prevent drying and cracking, and may not be suitable for wet conditions unless treated.
- Impact on Application: Leather gloves are ideal for construction, automotive, and heavy-duty tasks, but their performance may decline in wet or oily environments.
- Considerations for Buyers: Buyers should ensure compliance with local regulations regarding leather sourcing and animal welfare standards, especially in regions sensitive to these issues.
How Does Synthetic Rubber Perform in Work Gloves?
Synthetic rubber, often used in coated gloves, provides a balance of flexibility and durability. It is particularly effective in environments where grip and dexterity are crucial.
- Key Properties: Synthetic rubber gloves typically offer good chemical resistance and can withstand temperatures up to 180°F (82°C).
- Pros: They are lightweight, flexible, and provide a secure grip in both dry and wet conditions.
- Cons: While durable, synthetic rubber may not offer the same level of puncture resistance as leather and can degrade under UV exposure.
- Impact on Application: These gloves are suitable for tasks in chemical handling, manufacturing, and food processing, where grip and dexterity are essential.
- Considerations for Buyers: Ensure that the gloves meet ASTM or EN standards for chemical resistance, particularly for industries with strict compliance requirements.
What Are the Advantages of Kevlar in Work Gloves?
Kevlar is a high-performance material known for its exceptional cut resistance. It is often blended with other materials to enhance overall glove performance.
- Key Properties: Kevlar gloves can resist cuts and abrasions while maintaining flexibility, with a cut resistance rating of up to Level 5.
- Pros: They are lightweight, comfortable, and provide excellent dexterity, making them suitable for precision tasks.
- Cons: Kevlar gloves can be more expensive and may not provide adequate thermal protection.
- Impact on Application: Ideal for glass handling, metal stamping, and other applications where cut hazards are present.
- Considerations for Buyers: Buyers should verify compliance with cut resistance standards, such as ANSI/ISEA 105, and consider the specific cut hazards in their industry.
How Does Cotton Impact Work Gloves Performance?
Cotton is often used in lighter-duty gloves and is valued for its comfort and breathability. It is typically used as a liner or for general-purpose gloves.
- Key Properties: Cotton gloves are breathable and can absorb moisture, making them comfortable for prolonged wear.
- Pros: They are inexpensive, lightweight, and provide basic protection against dirt and minor abrasions.
- Cons: Cotton gloves offer limited protection against cuts, punctures, and chemicals, making them unsuitable for heavy-duty applications.
- Impact on Application: Best suited for light assembly work, gardening, and general maintenance tasks.
- Considerations for Buyers: Ensure that cotton gloves meet local labor standards for safety and comfort, especially in regions with high temperatures.
Summary Table of Material Selection for Work Gloves
Material | Typical Use Case for work gloves supplier | Key Advantage | Key Disadvantage/Limitation | Relative Cost (Low/Med/High) |
---|---|---|---|---|
Leather | Construction, automotive | Excellent durability and comfort | Expensive, requires maintenance | High |
Synthetic Rubber | Chemical handling, food processing | Good grip and flexibility | Less puncture resistance | Medium |
Kevlar | Glass handling, metal stamping | High cut resistance | More expensive, limited thermal protection | High |
Cotton | Light assembly, gardening | Comfortable and breathable | Limited protection against hazards | Low |
This strategic material selection guide provides B2B buyers with essential insights into the properties, advantages, and limitations of various glove materials, enabling informed purchasing decisions that align with their specific operational needs and compliance requirements.
In-depth Look: Manufacturing Processes and Quality Assurance for work gloves supplier
What Are the Key Stages in the Manufacturing Process of Work Gloves?
The manufacturing process for work gloves involves several critical stages, each essential for ensuring the final product meets industry standards and buyer expectations. The primary stages include:
-
Material Preparation: The first step involves sourcing high-quality raw materials such as leather, synthetic fibers, and rubber. For B2B buyers, understanding the material selection is crucial, as it directly impacts durability and performance. Suppliers should provide material specifications, including thickness, tensile strength, and abrasion resistance.
-
Forming: In this stage, the prepared materials are cut and shaped into glove patterns. This is typically achieved through die-cutting or automated cutting machines that ensure precision. Buyers should inquire about the technology used, as advanced machinery can enhance consistency and reduce waste.
-
Assembly: After forming, the pieces are stitched together. This process may involve various techniques such as single or double stitching, depending on the glove’s intended use. For instance, gloves designed for heavy-duty tasks may require reinforced stitching. Buyers should verify the stitching techniques employed by suppliers to ensure the gloves can withstand rigorous use.
-
Finishing: The final stage involves applying any additional treatments or coatings, such as water-resistant finishes or grip enhancements. This is where the gloves are also inspected for any defects before packaging. B2B buyers should ensure that the finishing processes align with their requirements, particularly for specialized applications.
How Is Quality Assurance Implemented in Work Gloves Manufacturing?
Quality assurance (QA) is integral to the work gloves manufacturing process, ensuring that products meet both international standards and specific buyer requirements. Key components of QA include:
-
International Standards Compliance: For B2B buyers, it is essential to ensure that suppliers comply with recognized international standards such as ISO 9001, which focuses on quality management systems. Additionally, industry-specific standards like CE marking (for European markets) or API (American Petroleum Institute) certifications for gloves used in oil and gas can be critical. Buyers should request documentation proving compliance with these standards.
-
Quality Control Checkpoints: Quality control (QC) is typically organized at various checkpoints throughout the manufacturing process:
– Incoming Quality Control (IQC): This involves inspecting raw materials upon arrival to ensure they meet specifications.
– In-Process Quality Control (IPQC): During the manufacturing stages, random samples are tested to catch any defects early.
– Final Quality Control (FQC): Before packaging, a thorough inspection of the finished gloves is conducted. This includes checking for visual defects, stitching integrity, and compliance with specifications. -
Common Testing Methods: Various testing methods are employed to ensure gloves meet performance requirements, including:
– Abrasion Resistance Tests: To determine how well the gloves hold up against wear and tear.
– Cut Resistance Tests: Particularly important for gloves used in industries like construction or manufacturing.
– Chemical Resistance Tests: For gloves intended for use in environments where exposure to hazardous substances is a concern.
How Can B2B Buyers Verify Supplier Quality Control Processes?
B2B buyers need to employ a strategic approach to verify the quality control processes of potential suppliers. Here are actionable steps to consider:
-
Supplier Audits: Conducting on-site audits allows buyers to assess the manufacturing environment, machinery, and quality control processes directly. This provides insights into the supplier’s commitment to quality and adherence to standards.
-
Request Quality Reports: Buyers should ask suppliers for detailed quality assurance reports, including results from IQC, IPQC, and FQC stages. These documents should outline any issues encountered and corrective actions taken.
-
Third-Party Inspections: Engaging independent third-party inspection services can provide an unbiased assessment of the supplier’s quality control processes. These inspections often include comprehensive testing and reporting, ensuring that the gloves meet the required specifications.
What Are the Quality Control Nuances for International B2B Buyers?
For international buyers, particularly those from Africa, South America, the Middle East, and Europe, there are specific nuances to consider:
-
Understanding Regional Standards: Different regions may have varying requirements for safety and quality standards. For example, European buyers may prioritize CE marking, while buyers in South America may need to comply with local regulations. Buyers should familiarize themselves with these requirements to avoid compliance issues.
-
Communication and Documentation: Clear communication with suppliers regarding quality expectations is vital. B2B buyers should ensure that all agreements are documented, including quality specifications and compliance requirements. This clarity helps prevent misunderstandings and ensures accountability.
-
Cultural Considerations: Understanding cultural differences in business practices can impact negotiations and quality expectations. For instance, suppliers in certain regions may have different approaches to quality control and customer service. Building strong relationships and trust can enhance cooperation and quality outcomes.
Conclusion
Understanding the manufacturing processes and quality assurance practices of work gloves suppliers is essential for B2B buyers. By focusing on material preparation, forming, assembly, and finishing stages, buyers can make informed decisions. Moreover, verifying compliance with international standards, implementing rigorous quality control measures, and conducting thorough supplier evaluations will ensure that the gloves meet the necessary performance and safety requirements. In a competitive global market, these insights will empower buyers to select the best suppliers for their needs.
Practical Sourcing Guide: A Step-by-Step Checklist for ‘work gloves supplier’
Introduction: Why a Sourcing Checklist is Essential for Work Gloves
Sourcing work gloves from reliable suppliers is a critical process that requires careful consideration. This checklist is designed to guide international B2B buyers, particularly from Africa, South America, the Middle East, and Europe, through the essential steps of finding the right work gloves supplier. By following these steps, you can ensure quality, compliance, and optimal pricing, leading to a successful procurement process.
Step 1: Define Your Technical Specifications
Before beginning your search, clearly outline the specifications for the work gloves you need. Consider factors such as material, size, durability, and intended use (e.g., industrial, medical, or agricultural). This step is vital as it helps you communicate effectively with suppliers and ensures that you receive products that meet your operational requirements.
- Material Considerations: Determine if you need leather, synthetic, or cotton gloves based on the job requirements.
- Safety Standards: Identify any relevant safety certifications (e.g., EN 388 for cut resistance) that the gloves must comply with.
Step 2: Research Potential Suppliers
Conduct thorough research to identify potential suppliers who specialize in work gloves. Utilize online platforms, trade shows, and industry contacts to compile a list of candidates. This step is crucial because a well-researched supplier is more likely to meet your quality and service expectations.
- Use B2B Marketplaces: Websites like Alibaba, Global Sources, or industry-specific directories can help find reputable suppliers.
- Check Reviews and Ratings: Look for supplier reviews and ratings from previous buyers to gauge their reliability.
Step 3: Evaluate Supplier Certifications
Verify the certifications and compliance of potential suppliers. This is essential to ensure that the gloves meet industry standards and regulations, which can vary by region. Confirming certifications can protect your company from liability and ensure product safety.
- Common Certifications: Look for ISO 9001 (Quality Management), CE marking for European markets, and any local safety compliance standards.
- Request Documentation: Ask suppliers to provide copies of their certifications for verification.
Step 4: Request Samples for Testing
Before placing a bulk order, request samples of the gloves to assess quality and suitability. Testing samples can save you from costly mistakes and ensure the gloves meet your specifications in real-world applications.
- Conduct Fit Tests: Check the comfort, fit, and usability of the gloves during actual work conditions.
- Evaluate Durability: Perform basic durability tests to see if they withstand the intended use.
Step 5: Negotiate Pricing and Terms
Once you have evaluated the suppliers and their products, enter into negotiations. Discuss pricing, payment terms, and delivery schedules. This step is important to ensure you are getting the best value for your investment while maintaining quality.
- Bulk Order Discounts: Inquire about discounts for larger orders, which can significantly reduce costs.
- Payment Terms: Establish clear payment terms to avoid misunderstandings later.
Step 6: Establish a Clear Contract
Finalizing a contract with your chosen supplier is a crucial step. The contract should outline all terms, including product specifications, pricing, delivery timelines, and penalties for non-compliance. A well-defined contract protects both parties and helps mitigate risks.
- Include Quality Assurance Clauses: Specify the quality standards and what recourse you have if they are not met.
- Delivery Schedules: Clearly state the expected delivery dates and any penalties for delays.
Step 7: Monitor Supplier Performance
After initiating the relationship, continuously monitor supplier performance. Regular assessments can help ensure that the supplier meets your ongoing needs and maintains the quality of the products supplied.
- Set Key Performance Indicators (KPIs): Establish KPIs to evaluate delivery times, product quality, and responsiveness.
- Feedback Loops: Create channels for feedback to address any issues promptly, fostering a cooperative relationship.
By following this practical sourcing checklist, B2B buyers can navigate the complexities of procuring work gloves and establish fruitful partnerships with suppliers that contribute to their business success.
Comprehensive Cost and Pricing Analysis for work gloves supplier Sourcing
What Are the Key Cost Components in Work Gloves Supplier Pricing?
When sourcing work gloves, understanding the cost structure is crucial for international B2B buyers. The primary cost components involved in the pricing of work gloves include:
-
Materials: The choice of materials significantly impacts costs. Common materials include leather, synthetic fabrics, cotton, and rubber. High-quality materials typically increase the price but can also enhance durability and safety.
-
Labor: Labor costs vary by region and are influenced by local wage standards. In countries with higher labor costs, such as those in Europe, the overall price of gloves may be elevated compared to regions with lower wages, such as parts of Africa and South America.
-
Manufacturing Overhead: This encompasses expenses related to production facilities, utilities, and equipment maintenance. Suppliers in regions with efficient production practices may offer lower overhead costs, thus impacting pricing favorably.
-
Tooling: Costs associated with molds and machines necessary for manufacturing specific glove types can be substantial, especially for custom designs. These costs are often amortized over larger production runs.
-
Quality Control (QC): Implementing rigorous QC processes ensures product reliability and compliance with safety standards. While this adds to the cost, it is essential for avoiding costly recalls and maintaining brand reputation.
-
Logistics: Transportation and shipping costs can vary significantly based on the distance from the supplier and the chosen Incoterms. Buyers must factor in these expenses when calculating the total cost.
-
Margin: Supplier profit margins can differ based on market demand and competition. Understanding these margins can provide insights into pricing flexibility during negotiations.
How Do Price Influencers Affect Work Gloves Sourcing?
Several factors can influence the final price of work gloves:
-
Volume/MOQ: Larger orders typically result in lower per-unit costs due to economies of scale. Buyers should evaluate their needs to determine the most cost-effective order size.
-
Specifications and Customization: Custom features such as branding, special materials, or specific safety certifications can increase costs. Buyers should weigh the benefits of customization against additional expenses.
-
Quality and Certifications: Gloves that meet higher safety standards or certifications, such as ISO or ANSI, usually come at a premium. However, these certifications can enhance buyer confidence and reduce liability risks.
-
Supplier Factors: The reputation and reliability of the supplier can affect pricing. Established suppliers may charge more due to their proven track record, while newer suppliers might offer competitive rates to build their customer base.
-
Incoterms: The chosen shipping terms can greatly influence total costs. Buyers should understand the implications of terms like FOB (Free on Board) or CIF (Cost, Insurance, and Freight) to make informed decisions about shipping responsibilities and costs.
What Are the Best Practices for Negotiating Work Gloves Prices?
For B2B buyers, particularly those in Africa, South America, the Middle East, and Europe, effective negotiation can lead to significant savings:
-
Conduct Thorough Market Research: Understanding the market rates for work gloves will provide a solid foundation for negotiations. Compare offers from multiple suppliers to gauge competitive pricing.
-
Leverage Total Cost of Ownership (TCO): Instead of focusing solely on the initial purchase price, consider the TCO, which includes maintenance, replacement, and disposal costs. This approach can justify a higher upfront cost if the gloves are more durable or efficient.
-
Build Long-term Relationships: Establishing a good rapport with suppliers can lead to better pricing and service. Long-term partnerships often result in preferential pricing and terms.
-
Be Clear on Specifications: Clearly communicating your requirements can reduce misunderstandings and help suppliers provide accurate quotes. This clarity can also prevent costly modifications later in the supply chain.
-
Utilize Payment Terms: Negotiating favorable payment terms can help manage cash flow and reduce financial strain, especially for larger orders.
Conclusion
Sourcing work gloves requires a comprehensive understanding of cost structures and pricing influencers. By leveraging effective negotiation strategies and considering the total cost of ownership, international B2B buyers can secure favorable terms and high-quality products. Always remember to approach suppliers with a clear understanding of your needs and market conditions to maximize value.
Alternatives Analysis: Comparing work gloves supplier With Other Solutions
In the competitive landscape of industrial safety gear, particularly work gloves, it is essential for B2B buyers to explore various alternatives that can provide similar protective benefits. While traditional work gloves suppliers offer a reliable solution, several alternatives exist that can cater to specific needs and preferences. This section will analyze these alternatives in detail, helping international B2B buyers from regions such as Africa, South America, the Middle East, and Europe make informed decisions.
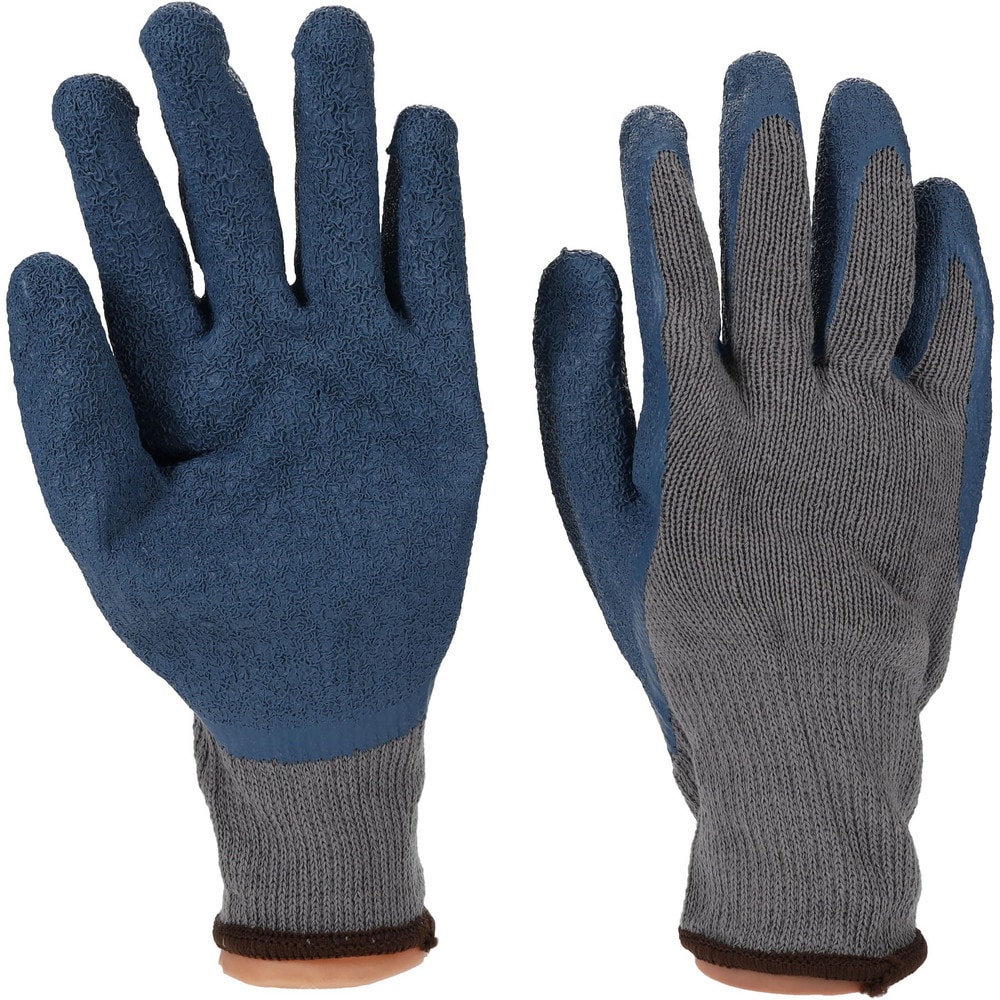
A stock image related to work gloves supplier.
Comparison Table of Work Gloves Supplier and Alternatives
Comparison Aspect | Work Gloves Supplier | Alternative 1: Smart Safety Gloves | Alternative 2: Protective Hand Creams |
---|---|---|---|
Performance | High durability, cut-resistant, varied materials | Integrated sensors for temperature and impact detection | Provides a barrier against abrasions and minor cuts |
Cost | Moderate to high, depending on material and brand | Higher initial investment due to technology | Low to moderate, depending on product quality |
Ease of Implementation | Requires training on proper usage | May require training for tech integration | Simple application, no special training needed |
Maintenance | Regular inspection and cleaning required | Software updates and battery management | Reapplication needed periodically |
Best Use Case | Heavy-duty industries, construction, manufacturing | High-tech environments, warehouses, and logistics | Light-duty tasks, environments with limited exposure to hazards |
What Are Smart Safety Gloves and Their Advantages?
Smart safety gloves represent an innovative alternative to traditional work gloves. These gloves are embedded with sensors that can monitor environmental conditions, such as temperature and impact levels, offering real-time feedback to the user.
Pros:
– Enhanced safety through real-time monitoring.
– Improved productivity with data-driven insights.
– Ideal for industries requiring high-tech solutions.
Cons:
– Higher upfront costs compared to standard gloves.
– Require regular maintenance and software updates.
– May necessitate training for employees to effectively use the technology.
How Can Protective Hand Creams Be Effective?
Protective hand creams offer a unique solution for workers in less hazardous environments. They form a protective barrier on the skin, reducing the risk of abrasions and minor cuts while providing moisture and comfort.
Pros:
– Cost-effective and easy to apply.
– Suitable for light-duty tasks where traditional gloves may be cumbersome.
– Can be used in conjunction with other protective gear.
Cons:
– Limited protection against severe hazards (e.g., heavy machinery).
– Requires frequent reapplication, especially in wet conditions.
– May not be suitable for environments with chemical exposure.
Conclusion: How to Choose the Right Solution for Your Needs?
Selecting the right protective solution depends on several factors, including the specific hazards present in your work environment, budget constraints, and the level of technological integration desired. For heavy-duty applications, traditional work gloves from a reputable supplier may remain the best option. Conversely, for tech-driven workplaces, smart safety gloves can provide advanced safety features that enhance overall workplace safety. In scenarios with minimal hazards, protective hand creams can be a practical and cost-effective alternative. Ultimately, understanding the unique requirements of your business will guide you in making the most effective choice for your workforce.
Essential Technical Properties and Trade Terminology for work gloves supplier
What Are the Key Technical Properties of Work Gloves for B2B Buyers?
When sourcing work gloves, understanding their technical specifications is crucial for ensuring safety, compliance, and performance. Here are some critical properties to consider:
1. Material Grade: What Should Buyers Look For?
The material grade determines the gloves’ durability and protection level. Common materials include leather, nitrile, latex, and Kevlar. Each material offers unique benefits; for instance, leather provides excellent abrasion resistance, while nitrile is favored for its chemical resistance. Buyers should assess the specific needs of their workforce and choose materials that align with industry standards for safety.
2. Cut Resistance: How Is It Measured?
Cut resistance is essential for gloves used in industries such as construction and manufacturing. This property is typically measured using the EN388 standard, which rates gloves on a scale from A (lowest) to F (highest). A higher cut-resistance rating indicates better protection against sharp objects. Buyers should prioritize cut resistance ratings based on the specific risks associated with their operations.
3. Grip Level: Why Is It Important?
The grip level of work gloves affects how effectively employees can handle tools and materials. This property is often defined by the surface texture and material used. Gloves with enhanced grip features, such as textured palms or rubberized coatings, reduce the likelihood of dropping items and improve overall safety. Understanding the grip requirements for specific tasks can significantly impact productivity.
4. Comfort and Fit: What Should Be Considered?
Comfort and fit are vital for ensuring that workers wear their gloves consistently. Ill-fitting gloves can lead to distractions and reduce safety. Look for gloves with ergonomic designs and adjustable features that cater to various hand sizes. The breathability of the material also plays a role in comfort, particularly in hot working environments.
5. Chemical Resistance: How to Assess It?
For industries handling hazardous materials, chemical resistance is a non-negotiable property. Gloves should be tested against specific chemicals to determine their effectiveness. Buyers should request data sheets that outline the gloves’ resistance to various substances, ensuring compliance with safety regulations.
6. Thermal Resistance: When Is It Necessary?
Thermal resistance is critical in environments where workers are exposed to extreme temperatures. This property indicates how well the gloves can insulate against heat or cold. Gloves with a high thermal resistance rating are essential for industries like metalworking or cold storage, where temperature extremes can pose serious risks.
What Are the Common Trade Terms in the Work Gloves Industry?
Familiarizing yourself with industry jargon can streamline communication with suppliers and enhance procurement efficiency. Here are some essential terms:
1. OEM (Original Equipment Manufacturer): What Does It Mean?
OEM refers to companies that produce parts or products that are marketed under another company’s brand. In the context of work gloves, buyers may work with OEMs to customize gloves according to their specifications, ensuring that the products meet their unique needs.
2. MOQ (Minimum Order Quantity): Why Is It Relevant?
MOQ is the smallest quantity of a product that a supplier is willing to sell. Understanding MOQ is crucial for budget planning and inventory management. Buyers should negotiate MOQs based on their purchasing capabilities and anticipated usage to avoid excess inventory.
3. RFQ (Request for Quotation): How to Utilize It?
An RFQ is a document sent to suppliers requesting pricing information on specific products. In the work gloves sector, issuing an RFQ helps buyers gather competitive quotes and ensures they are getting the best value. It’s an essential step in the procurement process.
4. Incoterms: How Do They Affect Shipping?
Incoterms (International Commercial Terms) are standardized trade terms that define the responsibilities of buyers and sellers in international transactions. Understanding these terms is crucial for managing shipping costs and liabilities. Common Incoterms include FOB (Free on Board) and CIF (Cost, Insurance, and Freight), which dictate who is responsible for shipping and insurance at various stages of the delivery process.
5. Compliance Standards: What Should Buyers Know?
Compliance standards refer to the safety regulations that products must meet in specific industries. For work gloves, this may include certifications like ANSI/ISEA and EN standards. Buyers must ensure that their selected gloves comply with relevant safety regulations to protect workers and minimize legal risks.
By understanding these technical properties and trade terms, international B2B buyers can make informed decisions, ensuring they procure the right work gloves for their operational needs.
Navigating Market Dynamics and Sourcing Trends in the work gloves supplier Sector
What Are the Current Market Dynamics and Sourcing Trends in the Work Gloves Supplier Sector?
The work gloves supplier sector is currently experiencing significant shifts influenced by various global drivers. The ongoing expansion of industries such as construction, manufacturing, and agriculture is pushing demand for high-quality protective gear, including work gloves. Furthermore, the rise of automation and robotics in these sectors is creating a need for specialized gloves that offer enhanced dexterity and protection. For international B2B buyers, particularly from Africa, South America, the Middle East, and Europe, understanding these trends is crucial for effective sourcing.
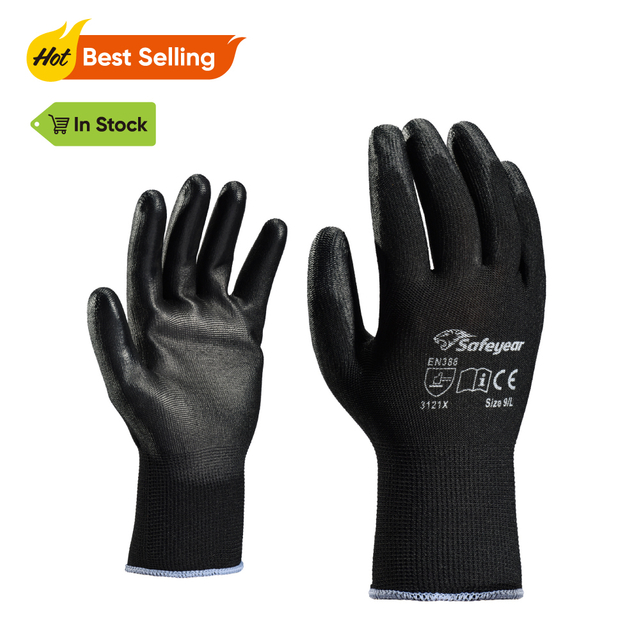
A stock image related to work gloves supplier.
Emerging technologies are also shaping the market dynamics. Smart gloves integrated with sensors are gaining traction, offering users real-time data on their hand movements, which can improve productivity and safety. Additionally, the rise of e-commerce platforms is transforming how buyers procure work gloves, providing access to a wider range of suppliers and products. B2B buyers should leverage these platforms to compare prices, quality, and certifications, ensuring they make informed purchasing decisions.
Another notable trend is the growing focus on customizability in work gloves. Suppliers are increasingly offering tailored solutions to meet specific industry needs, which can significantly enhance user satisfaction and safety. Buyers should engage with suppliers who can provide bespoke solutions to ensure the gloves meet their operational requirements.
How Is Sustainability Impacting the Work Gloves Supplier Market?
Sustainability has become a pivotal consideration for B2B buyers in the work gloves supplier sector. The environmental impact of manufacturing processes, particularly in terms of waste and carbon emissions, is under scrutiny. Suppliers are increasingly adopting eco-friendly practices, such as using recycled materials and minimizing water usage during production. For international buyers, sourcing from suppliers with sustainable practices not only aligns with corporate social responsibility goals but can also enhance brand reputation.
Ethical sourcing is another critical aspect. Buyers are urged to ensure that their suppliers adhere to fair labor practices and provide safe working conditions. Certifications such as Fair Trade and Global Organic Textile Standard (GOTS) are becoming essential indicators of a supplier’s commitment to ethical sourcing. By prioritizing suppliers with these certifications, buyers can contribute to a more sustainable and ethical supply chain.
Moreover, the demand for ‘green’ materials, such as organic cotton and biodegradable synthetic fibers, is on the rise. B2B buyers should seek suppliers that offer these materials to meet the growing consumer demand for environmentally friendly products. This trend not only helps in reducing the environmental footprint but also caters to a demographic that is increasingly conscious of sustainability.
What Is the Brief Evolution of the Work Gloves Supplier Sector?
The work gloves supplier sector has evolved significantly over the decades. Initially, gloves were simple protective coverings made from leather or fabric, primarily designed for manual labor. However, with the advancement of technology and a deeper understanding of workplace safety, the industry has expanded to include a variety of materials and designs.
In the late 20th century, the introduction of synthetic materials revolutionized glove manufacturing, allowing for enhanced durability and protection. The 21st century has seen the rise of advanced technologies, such as breathable fabrics and smart gloves, which have further transformed the market. This evolution reflects the sector’s responsiveness to the changing needs of industries and the growing emphasis on safety and efficiency in the workplace.
For international B2B buyers, understanding this historical context is essential. It highlights the importance of sourcing from suppliers who are not only aware of current trends but also possess the capability to innovate and adapt to future demands.
Frequently Asked Questions (FAQs) for B2B Buyers of work gloves supplier
-
How do I choose the right work gloves supplier for my business needs?
Selecting the right work gloves supplier involves assessing several key factors. Start by identifying your specific requirements, such as glove type, material, and safety standards. Research potential suppliers by checking their industry reputation, certifications, and customer reviews. Engage in direct communication to gauge their responsiveness and willingness to customize products according to your needs. Finally, consider their production capacity and logistics capabilities to ensure they can meet your order volume and delivery timelines. -
What are the benefits of customizing work gloves for my company?
Customizing work gloves offers significant advantages, including enhanced brand recognition and employee comfort. Tailored gloves can meet specific safety standards required in your industry, ensuring compliance and reducing liability. Customization options, such as color, material, and size, allow you to create a product that fits your workforce’s unique needs. This not only improves worker safety and productivity but also fosters a sense of belonging and pride among employees. -
What minimum order quantities (MOQs) should I expect from work gloves suppliers?
Minimum order quantities (MOQs) can vary significantly among suppliers, typically ranging from 100 to several thousand pairs. Factors influencing MOQs include the supplier’s production capabilities, the complexity of customization, and the type of glove required. When sourcing, discuss your specific needs with potential suppliers to find flexibility in MOQs, especially if you are a smaller business or looking to test new products without committing to large volumes. -
How can I verify the quality of work gloves from a supplier?
To verify the quality of work gloves, request samples before placing a bulk order. Assess the materials used, stitching, and overall craftsmanship. Check for compliance with relevant safety standards, such as ANSI or EN certifications. Furthermore, inquire about the supplier’s quality assurance processes, including testing methods and inspection protocols. Building a relationship with suppliers who are transparent about their quality control practices is essential for ensuring product reliability. -
What payment terms are standard when working with international suppliers?
Payment terms for international suppliers can vary widely, but common practices include letters of credit, advance payments, and net payment terms (e.g., net 30 or net 60 days). It’s crucial to negotiate terms that align with your cash flow while also providing security for the supplier. Establishing clear agreements in writing can help mitigate disputes and ensure timely fulfillment of orders. Always consider using escrow services for larger transactions to safeguard your investment. -
What logistics considerations should I keep in mind when sourcing work gloves internationally?
When sourcing work gloves internationally, consider shipping methods, lead times, and customs regulations in your country. Evaluate whether the supplier can handle logistics or if you need a third-party logistics provider. Understand the Incoterms (International Commercial Terms) that will dictate the responsibilities of both parties regarding shipping costs, insurance, and risk. Additionally, factor in potential delays due to customs clearance and ensure compliance with any import regulations. -
How do I handle communication barriers with overseas suppliers?
Effective communication with overseas suppliers is crucial for a successful partnership. To overcome language barriers, consider using professional translation services or tools. Clearly articulate your requirements, expectations, and any concerns in simple language. Regular updates through emails, video calls, or messaging apps can help maintain transparency. Establishing a contact person at both ends can also streamline communication and improve response times. -
What certifications should I look for in a work gloves supplier?
When vetting work gloves suppliers, look for industry-specific certifications that demonstrate compliance with safety and quality standards. Common certifications include ISO 9001 for quality management systems, ANSI/ISEA for safety gloves, and CE marking for compliance with European health and safety regulations. These certifications indicate that the supplier adheres to rigorous manufacturing processes and product testing, which is essential for ensuring the safety and reliability of the gloves you source.
Important Disclaimer & Terms of Use
⚠️ Important Disclaimer
The information provided in this guide, including content regarding manufacturers, technical specifications, and market analysis, is for informational and educational purposes only. It does not constitute professional procurement advice, financial advice, or legal advice.
While we have made every effort to ensure the accuracy and timeliness of the information, we are not responsible for any errors, omissions, or outdated information. Market conditions, company details, and technical standards are subject to change.
B2B buyers must conduct their own independent and thorough due diligence before making any purchasing decisions. This includes contacting suppliers directly, verifying certifications, requesting samples, and seeking professional consultation. The risk of relying on any information in this guide is borne solely by the reader.
Strategic Sourcing Conclusion and Outlook for work gloves supplier
What Are the Key Takeaways for Strategic Sourcing of Work Gloves?
In summary, international B2B buyers, particularly from Africa, South America, the Middle East, and Europe, should prioritize strategic sourcing when selecting work gloves suppliers. Understanding the diverse range of materials, safety standards, and customization options available is crucial. Buyers must conduct thorough market research to identify suppliers who not only meet quality and compliance standards but also offer competitive pricing and flexible order quantities.
How Can Strategic Sourcing Enhance Your Supply Chain?
Strategic sourcing offers significant advantages such as improved supplier relationships, cost savings, and access to innovative products. By leveraging data analytics and supplier performance metrics, businesses can make informed decisions that enhance their supply chain resilience. This approach is especially vital in a global market, where fluctuating demands and regulations can impact supply stability.
What Is the Future of Work Gloves Supply in Global Markets?
Looking ahead, the demand for high-quality, durable work gloves will continue to rise across various industries. As sustainability becomes a focal point, suppliers who adopt eco-friendly practices will gain a competitive edge. International buyers should stay proactive in exploring new partnerships and technologies that align with their operational goals.
Call to Action for International Buyers
Engage with suppliers who demonstrate a commitment to quality and innovation. Initiate discussions with potential partners to explore how they can meet your specific needs while aligning with your strategic sourcing goals. By doing so, you will not only enhance workplace safety but also position your business for long-term success in a competitive landscape.