Maximize Efficiency: The Ultimate Reactor Manufacturer Guide (2025)
Introduction: Navigating the Global Market for reactor manufacturer
In today’s competitive landscape, sourcing a reliable reactor manufacturer can pose significant challenges for international B2B buyers. With the increasing demand for industrial reactors across sectors such as chemicals, pharmaceuticals, and energy, understanding the nuances of the global market is crucial. This guide is designed to empower decision-makers from Africa, South America, the Middle East, and Europe—particularly those in emerging markets like the UAE and Turkey—by offering comprehensive insights into the reactor manufacturing landscape.
Throughout this guide, we will delve into various types of reactors, their specific applications, and the critical factors to consider when selecting a manufacturer. We will also explore the intricacies of supplier vetting, ensuring that buyers can identify reputable manufacturers who meet their unique operational needs. Additionally, we will provide actionable insights into pricing structures, enabling buyers to make informed decisions that align with their budgetary constraints.
By equipping you with essential knowledge about the reactor manufacturing process and market dynamics, this guide aims to facilitate informed purchasing decisions. Whether you are navigating the complexities of international regulations or seeking innovative solutions tailored to your industry, understanding the global market for reactor manufacturers is essential for driving operational efficiency and achieving long-term business success.
Understanding reactor manufacturer Types and Variations
Type Name | Key Distinguishing Features | Primary B2B Applications | Brief Pros & Cons for Buyers |
---|---|---|---|
Continuous Stirred Tank Reactor (CSTR) | Operates continuously, well-mixed, and uniform product quality | Chemical processing, pharmaceuticals | Pros: Efficient for large volumes; Cons: Not ideal for high-viscosity materials. |
Batch Reactor | Processes materials in discrete batches, versatile design | Specialty chemicals, food processing | Pros: Flexibility in production; Cons: Higher labor and downtime costs. |
Plug Flow Reactor (PFR) | Allows for a continuous flow with minimal back-mixing | Petrochemicals, polymer production | Pros: High efficiency for reactions; Cons: Limited to specific reaction conditions. |
Fluidized Bed Reactor | Utilizes a fluidized state for solid particles, enhancing reaction rates | Gasification, catalytic reactions | Pros: Excellent heat and mass transfer; Cons: Complex design and operation. |
Membrane Reactor | Integrates membrane separation with reaction processes | Wastewater treatment, biofuels | Pros: High selectivity and efficiency; Cons: Higher initial investment. |
What are the Characteristics of Continuous Stirred Tank Reactors (CSTR)?
Continuous Stirred Tank Reactors (CSTR) are characterized by their ability to maintain a uniform composition through continuous input and output of reactants and products. This type is particularly suitable for large-scale production in industries such as chemicals and pharmaceuticals. When considering a CSTR, buyers should evaluate factors such as the reactor’s mixing efficiency, residence time, and compatibility with their specific chemical processes. While they offer high productivity, CSTRs may not be the best choice for high-viscosity materials due to potential mixing challenges.
How Do Batch Reactors Offer Flexibility?
Batch Reactors are designed to process materials in discrete batches, making them highly versatile for various applications, including specialty chemicals and food processing. Their key feature is the ability to handle different formulations and adjust operational parameters easily. B2B buyers should consider the flexibility and scalability of batch reactors, as well as the potential for increased labor and downtime costs. While they can be more labor-intensive, the flexibility they offer can lead to better product customization and quality control.
What Makes Plug Flow Reactors (PFR) Efficient?
Plug Flow Reactors (PFR) allow for continuous flow with minimal back-mixing, which is crucial for maintaining concentration gradients during reactions. They are commonly used in industries such as petrochemicals and polymer production, where high efficiency and reaction control are paramount. Buyers interested in PFRs should focus on the specific reaction kinetics and conditions, as these reactors are limited to certain processes. The efficiency they provide can significantly enhance production rates, but they require precise control of flow rates and temperatures.
Why Choose Fluidized Bed Reactors for Catalytic Reactions?
Fluidized Bed Reactors utilize a fluidized state to enhance the interaction between solid particles and gases, making them ideal for gasification and catalytic reactions. This type of reactor is known for its excellent heat and mass transfer capabilities, which can lead to improved reaction rates. For B2B buyers, the complexity of design and operation should be a key consideration. While fluidized bed reactors can optimize performance, they may involve higher operational costs and require skilled personnel for management.
How Do Membrane Reactors Enhance Efficiency?
Membrane Reactors integrate membrane separation with reaction processes, providing high selectivity and efficiency in applications such as wastewater treatment and biofuels. This innovative approach allows for simultaneous reaction and separation, reducing energy costs and improving overall process efficiency. Buyers should weigh the benefits of reduced operational costs against the higher initial investment required for membrane technologies. The long-term gains in efficiency and product purity can make them an attractive option for forward-thinking businesses in competitive markets.
Related Video: Top 3 MOST Popular Nuclear Reactor Types Worldwide
Key Industrial Applications of reactor manufacturer
Industry/Sector | Specific Application of Reactor Manufacturer | Value/Benefit for the Business | Key Sourcing Considerations for this Application |
---|---|---|---|
Chemical Manufacturing | Production of Specialty Chemicals | Enhanced product purity and yield, leading to competitive pricing | Compliance with local and international safety standards |
Pharmaceuticals | Synthesis of Active Pharmaceutical Ingredients (APIs) | Increased efficiency and reduced time-to-market for new drugs | Quality certifications and regulatory compliance |
Oil & Gas | Catalytic Reforming and Hydrocracking Processes | Improved fuel quality and energy efficiency | Equipment durability and resistance to corrosive environments |
Food & Beverage | Fermentation Processes | Consistent product quality and scalability | Hygiene standards and material safety certifications |
Waste Management | Waste Treatment and Recycling | Environmental compliance and cost savings | Technology compatibility and local regulations |
What Are the Key Industrial Applications of Reactor Manufacturers in Chemical Manufacturing?
In the chemical manufacturing sector, reactor manufacturers are crucial for producing specialty chemicals. These reactors facilitate controlled reactions, ensuring high purity and optimal yields. For international buyers, particularly from regions like Africa and South America, sourcing reactors that comply with local and international safety standards is vital. Understanding the specific chemical processes and required materials will help buyers select the right reactor technology that aligns with their production goals.
How Do Reactor Manufacturers Support the Pharmaceutical Industry?
In pharmaceuticals, reactor manufacturers play a pivotal role in synthesizing Active Pharmaceutical Ingredients (APIs). These reactors are designed for precision and efficiency, which is essential for meeting strict regulatory standards. Buyers, especially in the Middle East and Europe, must prioritize quality certifications and regulatory compliance when sourcing reactors. This ensures that the manufacturing process can be scaled efficiently while maintaining the integrity of the final product.
What Role Do Reactor Manufacturers Play in the Oil & Gas Sector?
Reactor manufacturers are integral to processes like catalytic reforming and hydrocracking in the oil and gas industry. These reactors enhance fuel quality and energy efficiency, which are critical for reducing operational costs. For B2B buyers in Europe and the UAE, focusing on equipment durability and resistance to corrosive environments is essential, given the harsh conditions in which these reactors operate. Understanding the technological specifications and maintenance needs will ensure optimal performance.
How Are Reactor Manufacturers Used in the Food & Beverage Industry?
In the food and beverage sector, reactor manufacturers are utilized for fermentation processes. These reactors ensure consistent product quality and scalability, which are vital for meeting consumer demand. Buyers from Africa and South America should consider hygiene standards and material safety certifications when sourcing reactors. This attention to safety not only complies with local regulations but also builds consumer trust in the final product.
What Benefits Do Reactor Manufacturers Provide in Waste Management?
Reactor manufacturers are also key players in waste treatment and recycling processes. These reactors help businesses comply with environmental regulations while reducing operational costs. For international buyers, particularly in the Middle East and Europe, understanding technology compatibility and local regulations is crucial when sourcing these reactors. This ensures that waste management solutions are effective and sustainable, aligning with both business goals and environmental responsibilities.
Related Video: Bioreactors | Design, Principle, Parts, Types, Applications, & Limitations | Biotechnology Courses
3 Common User Pain Points for ‘reactor manufacturer’ & Their Solutions
Scenario 1: Navigating Compliance and Regulatory Challenges in Reactor Manufacturing
The Problem:
International B2B buyers often face significant hurdles when it comes to compliance with local and international regulations surrounding reactor manufacturing. For example, buyers from the Middle East may encounter strict safety and environmental regulations that differ from those in Europe or Africa. This discrepancy can lead to misunderstandings about the specifications needed, resulting in delays, increased costs, and potential fines. The fear of non-compliance can also stifle innovation, as buyers may hesitate to invest in new reactor technologies that do not have clear regulatory pathways.
The Solution:
To effectively navigate these compliance challenges, buyers should conduct thorough research on both local and international regulations relevant to their operations. Engaging with local regulatory bodies and industry associations can provide valuable insights into the specific requirements for reactor manufacturing. Additionally, establishing a relationship with a reactor manufacturer that has a strong track record in compliance can be beneficial. Such manufacturers often have dedicated compliance teams that can help buyers understand regulatory requirements, streamline approval processes, and ensure that the reactors meet the necessary standards. Buyers should also consider investing in training for their teams to stay updated on regulatory changes, which can mitigate risks and foster a culture of compliance.
Scenario 2: Managing Supply Chain Disruptions in Reactor Procurement
The Problem:
Supply chain disruptions are a common pain point for B2B buyers in the reactor manufacturing sector, particularly for those located in Africa and South America. Factors such as geopolitical instability, natural disasters, or even pandemics can lead to delays in procurement, impacting production schedules and operational efficiency. For instance, a buyer waiting for reactor components may find that shipping delays lead to idle production lines, resulting in lost revenue and customer dissatisfaction.
The Solution:
To address these supply chain challenges, buyers should diversify their supplier base. Relying on multiple manufacturers across different regions can reduce the risk of disruption from any single source. Additionally, buyers should consider implementing just-in-time inventory strategies to minimize stock shortages while still maintaining the flexibility to respond to demand. Regular communication with suppliers regarding their capacity, lead times, and any potential risks can also help in planning and mitigating disruptions. Furthermore, investing in supply chain management software can provide real-time visibility into inventory levels and supplier performance, enabling proactive decision-making to keep operations running smoothly.
Scenario 3: Difficulty in Customizing Reactor Solutions for Specific Applications
The Problem:
Many B2B buyers struggle with the customization of reactor solutions to meet unique operational requirements. For example, a buyer in Turkey may need a reactor designed for a specific chemical process that is not readily available in standard models. This challenge can lead to a compromise in operational efficiency, as off-the-shelf solutions may not align perfectly with their needs, resulting in suboptimal performance and increased operational costs.
The Solution:
To overcome this customization hurdle, buyers should engage in detailed discussions with potential reactor manufacturers early in the procurement process. Clearly articulating specific requirements, including temperature ranges, pressure conditions, and material compatibility, can help manufacturers propose tailored solutions. Buyers should also seek manufacturers that offer modular reactor designs, as these can be more easily adapted to meet changing process requirements. Additionally, conducting pilot tests or trials with prototypes can provide valuable insights into how the reactor will perform in real-world conditions before making a significant investment. Lastly, establishing long-term partnerships with manufacturers can facilitate ongoing customization and support as operational needs evolve.
Strategic Material Selection Guide for reactor manufacturer
When selecting materials for reactor manufacturing, it is crucial to consider the specific properties and performance requirements of the reactors being produced. The choice of material can significantly influence the durability, efficiency, and safety of the reactor. Below is an analysis of four common materials used in reactor manufacturing, focusing on their properties, advantages, disadvantages, and considerations for international B2B buyers.
What are the Key Properties of Carbon Steel in Reactor Manufacturing?
Carbon steel is a widely used material in reactor manufacturing due to its strength and versatility. It typically offers good mechanical properties, with a temperature rating up to 400°C (752°F) and pressure ratings that can exceed 20 MPa, depending on the specific grade. Carbon steel is also relatively cost-effective, making it an attractive option for many manufacturers.
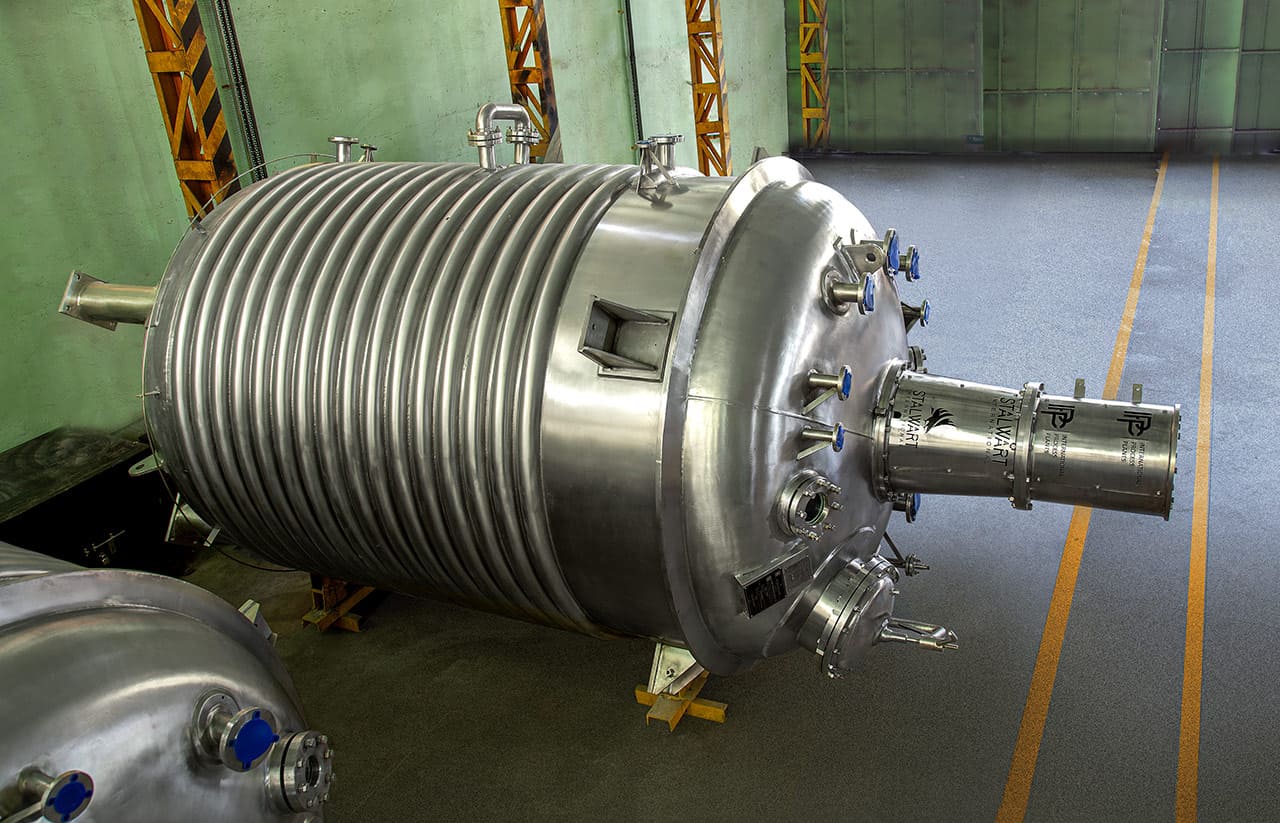
A stock image related to reactor manufacturer.
Pros and Cons:
The primary advantage of carbon steel is its durability and ability to withstand high pressures. However, it has limited corrosion resistance, which can be a significant drawback in reactive environments. This limitation may necessitate additional protective coatings or treatments, increasing manufacturing complexity and costs.
Impact on Application:
Carbon steel is suitable for a range of applications, particularly where the media is not highly corrosive. It is often used in oil and gas, chemical processing, and power generation sectors.
Considerations for International Buyers:
Buyers should ensure compliance with international standards such as ASTM A106 or DIN 17100. In regions like Africa and South America, where corrosion can be a concern due to environmental factors, additional protective measures may be necessary.
How Does Stainless Steel Perform in Reactor Applications?
Stainless steel is another popular choice for reactor manufacturing, particularly in applications involving corrosive media. Its excellent corrosion resistance and ability to maintain structural integrity at high temperatures (up to 800°C or 1472°F) make it a preferred material for many industries.
Pros and Cons:
The key advantage of stainless steel is its resistance to corrosion and oxidation, which extends the lifespan of reactors. However, it is generally more expensive than carbon steel, which can impact overall project budgets. Additionally, the manufacturing process for stainless steel can be more complex, requiring specialized welding techniques.
Impact on Application:
Stainless steel is ideal for reactors handling aggressive chemicals, such as acids and bases, making it suitable for the pharmaceutical and food processing industries.
Considerations for International Buyers:
Buyers should be aware of relevant standards such as ASTM A240 or JIS G4303. In regions like the Middle East, where high temperatures are common, selecting the appropriate grade of stainless steel is essential to ensure performance.
What are the Benefits of Using Alloy Steel in Reactor Manufacturing?
Alloy steel combines various elements to enhance specific properties, making it suitable for high-performance applications. It can withstand higher temperatures and pressures than carbon steel, with ratings often exceeding 600°C (1112°F) and 30 MPa.
Pros and Cons:
The main advantage of alloy steel is its superior strength and toughness, which allows for the construction of more robust reactors. However, the cost of alloy steel is generally higher, and its manufacturing process can be more intricate due to the need for precise control of alloying elements.
Impact on Application:
Alloy steel is particularly effective in high-pressure applications, such as in petrochemical reactors or power plants, where safety and reliability are paramount.
Considerations for International Buyers:
Compliance with standards like ASTM A387 is critical. Buyers from Europe and the Middle East should also consider local regulations regarding material certification and quality assurance.
How Does Glass-Lined Steel Compare in Reactor Manufacturing?
Glass-lined steel combines the strength of steel with the corrosion resistance of glass, making it an excellent choice for reactors handling corrosive substances. The glass lining can typically withstand temperatures up to 200°C (392°F).
Pros and Cons:
The primary advantage of glass-lined steel is its outstanding resistance to corrosion and chemical attack, making it suitable for various applications. However, it is more fragile than other materials, which can lead to challenges during handling and installation.
Impact on Application:
Glass-lined reactors are commonly used in the chemical and pharmaceutical industries, where purity and chemical resistance are critical.
Considerations for International Buyers:
Buyers should ensure compliance with standards such as ASTM A193. In regions like Africa and South America, where transportation and handling can be challenging, the fragility of glass-lined steel should be taken into account.
Summary Table of Material Selection for Reactor Manufacturing
Material | Typical Use Case for reactor manufacturer | Key Advantage | Key Disadvantage/Limitation | Relative Cost (Low/Med/High) |
---|---|---|---|---|
Carbon Steel | Oil and gas, chemical processing | High durability and strength | Limited corrosion resistance | Medium |
Stainless Steel | Pharmaceutical, food processing | Excellent corrosion resistance | Higher cost and manufacturing complexity | High |
Alloy Steel | Petrochemical reactors, power plants | Superior strength and toughness | Higher cost and complex manufacturing | High |
Glass-Lined Steel | Chemical and pharmaceutical industries | Outstanding corrosion resistance | Fragile and handling challenges | Medium |
This strategic material selection guide provides essential insights for international B2B buyers, helping them make informed decisions that align with their operational requirements and regional standards.
In-depth Look: Manufacturing Processes and Quality Assurance for reactor manufacturer
What Are the Key Stages in the Manufacturing Process of Reactors?
The manufacturing process for reactors is intricate, involving several critical stages that ensure the final product meets the necessary performance and safety standards. Understanding these stages can help B2B buyers in Africa, South America, the Middle East, and Europe make informed purchasing decisions.
1. Material Preparation
The first stage in reactor manufacturing is material preparation. This involves selecting high-quality raw materials that meet specific industry standards. Common materials used in reactor construction include carbon steel, stainless steel, and exotic alloys. Suppliers should provide certifications for these materials, confirming they comply with relevant standards such as ASTM or ASME.
2. Forming Techniques
Once the materials are prepared, the next step is forming. This can include processes such as:
- Welding: Critical for joining components, welding techniques like TIG and MIG are commonly used in reactor manufacturing. The choice of welding technique can significantly affect the reactor’s integrity.
- Casting: For complex shapes, casting may be employed. This requires precise control over the cooling process to avoid defects.
- Machining: Components may undergo machining to achieve tight tolerances necessary for operational efficiency.
Buyers should inquire about the forming techniques used and the qualifications of the personnel performing these tasks, as skilled labor is essential for maintaining quality.
3. Assembly Process
After forming, the assembly phase begins. This stage is crucial as it involves the integration of various components into the reactor system. Key considerations during assembly include:
- Alignment and Fit: Proper alignment is essential to ensure that the reactor operates efficiently and safely.
- Sealing: Effective sealing techniques must be employed to prevent leaks and ensure safety during operation.
Buyers should assess how the manufacturer verifies the integrity of assemblies, particularly through the use of jigs and fixtures that maintain precision.
4. Finishing Touches
The final stage of manufacturing involves finishing processes, which can include surface treatment, coating, and inspection. Surface treatments such as passivation can enhance corrosion resistance, while coatings may provide additional protection against environmental factors.
How is Quality Assurance Implemented in Reactor Manufacturing?
Quality assurance (QA) is paramount in reactor manufacturing to ensure safety, reliability, and compliance with international regulations. B2B buyers must understand the QA processes employed by potential suppliers.
1. What International and Industry-Specific Standards Should Buyers Consider?
Reactor manufacturers typically adhere to several international standards, including:
- ISO 9001: This standard emphasizes a quality management system that enhances customer satisfaction through effective processes.
- CE Marking: Particularly relevant in Europe, CE marking indicates compliance with health, safety, and environmental protection standards.
- API Standards: For oil and gas applications, API standards ensure that the reactors meet the necessary operational requirements.
Buyers should verify that the supplier’s certifications are current and applicable to their specific needs.
2. What Are the Key Quality Control Checkpoints?
Quality control (QC) is integrated at various checkpoints throughout the manufacturing process:
- Incoming Quality Control (IQC): This initial checkpoint ensures that all incoming materials meet specified quality standards before they are used in production.
- In-Process Quality Control (IPQC): During manufacturing, continuous monitoring is essential to identify and rectify any deviations from quality standards.
- Final Quality Control (FQC): After assembly, a comprehensive inspection is performed to ensure that the finished reactor meets all specifications and safety standards.
Buyers should request detailed QC reports that outline the procedures followed at each checkpoint.
3. What Common Testing Methods Are Employed?
To ensure that reactors operate safely and efficiently, several testing methods are commonly used, including:
- Hydrostatic Testing: This method checks for leaks and ensures that the reactor can withstand operating pressures.
- Non-Destructive Testing (NDT): Techniques such as ultrasonic testing and radiographic testing help identify internal flaws without damaging the reactor.
- Performance Testing: This evaluates the reactor’s operational capabilities under real-world conditions.
Understanding these testing methods allows buyers to gauge the thoroughness of a manufacturer’s quality assurance process.
How Can B2B Buyers Verify Supplier Quality Control?
Verifying a supplier’s quality control processes is essential for international B2B buyers. Here are several actionable steps:
1. Conduct Supplier Audits
Regular audits are an effective way to assess a supplier’s compliance with quality standards. Buyers can conduct these audits themselves or hire third-party inspection services to ensure impartiality.
2. Request Quality Control Documentation
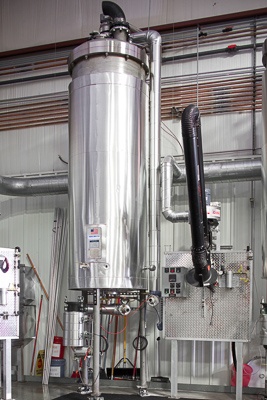
A stock image related to reactor manufacturer.
Buyers should ask for detailed quality control documentation, including inspection reports, test results, and certifications. This information provides insights into the supplier’s commitment to maintaining quality standards.
3. Engage Third-Party Inspection Services
Utilizing third-party inspection services can provide an additional layer of assurance. These services can verify that the manufacturing processes and quality controls are in line with industry standards.
What Are the Quality Control Nuances for International B2B Buyers?
B2B buyers from regions like Africa, South America, the Middle East, and Europe face unique challenges when dealing with international suppliers. Understanding these nuances is crucial:
- Regulatory Compliance: Each region has specific regulatory requirements. Buyers must ensure that the reactors comply with local regulations, which may differ from the manufacturer’s country.
- Cultural Differences: Different cultures may approach quality assurance and customer service differently. Buyers should be aware of these differences and establish clear communication channels.
- Supply Chain Considerations: Logistics and transportation can affect product quality. Buyers should discuss how suppliers handle shipping and ensure proper packaging to prevent damage.
By considering these factors, international B2B buyers can better navigate the complexities of sourcing reactors and ensure they partner with manufacturers committed to quality and safety.
Practical Sourcing Guide: A Step-by-Step Checklist for ‘reactor manufacturer’
This guide serves as a comprehensive checklist for international B2B buyers looking to procure reactor manufacturing services. By following these actionable steps, you can streamline your sourcing process and ensure you partner with the right manufacturer to meet your specific needs.
Step 1: Define Your Technical Specifications
Before initiating your search for a reactor manufacturer, it’s critical to clearly outline your technical specifications. This includes understanding the type of reactor you need (e.g., batch, continuous, or semi-batch), materials required, capacity, and any compliance standards relevant to your industry. Precise specifications will facilitate more accurate quotes and help in assessing supplier capabilities.
Step 2: Conduct Market Research
Understanding the market landscape is essential for informed decision-making. Research potential suppliers in your target regions, focusing on their reputation, market presence, and areas of expertise. Utilize online directories, industry reports, and trade associations to gather insights and identify leading manufacturers.
Step 3: Evaluate Potential Suppliers
Before committing, it’s crucial to vet suppliers thoroughly. Request company profiles, case studies, and references from buyers in a similar industry or region. Look for:
– Experience: Check how long the manufacturer has been in business and their specialization in reactor manufacturing.
– Client Portfolio: Analyze their past projects to ensure they have experience with similar reactors and industries.
Step 4: Verify Supplier Certifications and Compliance
Ensure that potential suppliers possess the necessary certifications that demonstrate adherence to international safety and quality standards, such as ISO certifications. This step is vital not only for regulatory compliance but also for ensuring product reliability and safety. Confirm that they have certifications relevant to your region and industry.
Step 5: Request Detailed Quotes
Once you’ve shortlisted potential suppliers, request detailed quotes that include pricing, delivery timelines, and warranty terms. A comprehensive quote allows for easier comparison between suppliers. Pay attention to:
– Cost Breakdown: Ensure the quote includes a breakdown of costs for materials, labor, and any additional services.
– Lead Times: Understand the expected delivery times and any penalties for delays.
Step 6: Assess After-Sales Support and Service
Evaluate the after-sales support each manufacturer offers. Strong after-sales service can significantly impact your operational efficiency. Consider:
– Technical Support: Availability of technical assistance and troubleshooting resources.
– Maintenance Services: Inquire if they offer maintenance packages or training for your staff.
Step 7: Negotiate Terms and Finalize Agreements
Once you’ve selected a manufacturer, enter into negotiations to finalize the terms of the agreement. Ensure that all aspects, including payment terms, delivery schedules, and warranty conditions, are clearly articulated in the contract. This step is crucial to mitigate any potential disputes in the future.
By following this checklist, B2B buyers can navigate the complexities of sourcing reactor manufacturers effectively, ensuring they make informed decisions that align with their operational requirements and business objectives.
Comprehensive Cost and Pricing Analysis for reactor manufacturer Sourcing
What are the Key Cost Components in Reactor Manufacturing?
When sourcing from reactor manufacturers, understanding the cost structure is paramount. The primary cost components include:
-
Materials: The choice of raw materials significantly affects costs. High-grade alloys or specialized composites may be necessary for certain applications, leading to higher material costs. Buyers should evaluate the suppliers’ material sourcing strategies to identify potential cost savings.
-
Labor: Labor costs can vary widely based on geographic location and skill level. Regions with lower labor costs may offer competitive pricing, but it’s essential to assess the skill and expertise of the workforce to ensure quality output.
-
Manufacturing Overhead: This includes expenses related to utilities, facility maintenance, and administrative costs. Efficient manufacturing processes can help reduce overhead, which in turn can lower overall pricing.
-
Tooling: Custom tooling can be a significant upfront expense, especially for specialized reactors. Buyers should consider whether the supplier has existing tooling that can accommodate their needs to minimize costs.
-
Quality Control (QC): Ensuring that reactors meet stringent quality standards incurs additional costs. However, investing in robust QC processes can prevent costly recalls and enhance product reliability.
-
Logistics: Transportation costs can vary based on distance and the mode of transport. Understanding the logistics involved in shipping reactors, especially across international borders, is crucial for accurate cost estimation.
-
Margin: Supplier profit margins can fluctuate based on market conditions, competition, and demand. Engaging in discussions about margin expectations can yield more favorable pricing.
How Do Price Influencers Impact Reactor Sourcing?
Several factors influence the pricing of reactors, and understanding these can lead to more strategic purchasing decisions:
-
Volume and Minimum Order Quantity (MOQ): Larger orders often lead to discounts. Buyers should assess their needs and negotiate MOQs that align with their project timelines while taking advantage of bulk pricing.
-
Specifications and Customization: Customization requirements can significantly impact costs. Standardized products may be less expensive, so buyers should evaluate whether customization is necessary for their applications.
-
Material Quality and Certifications: Higher quality materials often come with a premium price tag. Additionally, certifications (e.g., ISO, ASME) can influence costs, as manufacturers may charge more for products that meet stringent standards.
-
Supplier Factors: The supplier’s reputation, financial stability, and production capabilities can affect pricing. A well-established supplier with proven reliability may command higher prices but could offer lower risk.
-
Incoterms: The terms of shipment (Incoterms) play a critical role in determining the final cost. Understanding the implications of terms like FOB (Free on Board) or CIF (Cost, Insurance, and Freight) is essential for accurate cost estimation.
What Buyer Tips Can Help Improve Cost-Efficiency?
For international B2B buyers, especially those from Africa, South America, the Middle East, and Europe, the following strategies can enhance cost efficiency:
-
Negotiate Effectively: Strong negotiation skills can lead to better pricing and terms. Prepare by understanding the supplier’s cost structure and be ready to discuss volume commitments or payment terms that may influence pricing.
-
Evaluate Total Cost of Ownership (TCO): Beyond the initial purchase price, consider the TCO, which includes installation, maintenance, and operational costs. A higher upfront investment in quality reactors can lead to lower long-term costs.
-
Understand Pricing Nuances: Pricing structures can differ significantly across regions. Familiarize yourself with local market conditions, tariffs, and trade agreements that may impact costs when sourcing from international suppliers.
-
Build Strong Relationships: Establishing long-term relationships with suppliers can lead to better pricing, priority service, and insights into market trends that can benefit your purchasing strategy.
Disclaimer on Indicative Prices
Prices for reactor manufacturing can fluctuate based on numerous variables, including market conditions and specific buyer requirements. It is advisable for buyers to conduct thorough market research and obtain multiple quotes to ensure competitive pricing.
Alternatives Analysis: Comparing reactor manufacturer With Other Solutions
Introduction to Alternative Solutions for Reactor Manufacturers
When considering reactor manufacturers, it’s essential to evaluate alternative solutions that may meet your operational needs more effectively or economically. Various technologies and methods can achieve similar outcomes, ranging from traditional reactors to newer innovations. This analysis focuses on comparing reactor manufacturers with two viable alternatives: modular reactors and advanced catalytic processes.
Comparison Table of Reactor Manufacturer and Alternatives
Comparison Aspect | Reactor Manufacturer | Modular Reactors | Advanced Catalytic Processes |
---|---|---|---|
Performance | High efficiency, tailored designs | Scalable, consistent output | High selectivity, lower energy use |
Cost | High initial investment | Moderate cost, flexible scaling | Lower operating costs, but high R&D expenses |
Ease of Implementation | Complex setup, long lead times | Quick deployment, easier permits | Requires specialized knowledge |
Maintenance | Regular inspections needed | Lower frequency, modular upkeep | High due to catalyst regeneration |
Best Use Case | Large-scale production, custom solutions | Small to mid-scale operations | Specialty chemicals, fine chemicals |
What Are the Advantages and Disadvantages of Modular Reactors?
Modular reactors present a compelling alternative to traditional reactor manufacturers, particularly for businesses looking for scalability. They can be deployed quickly and require less regulatory hassle compared to larger reactors, making them suitable for emerging markets in Africa and South America. However, while they offer lower initial costs, the long-term expenses may vary based on operational efficiency and output consistency. They are best for companies needing to adapt production capacity without major overhauls.
How Do Advanced Catalytic Processes Compare?
Advanced catalytic processes are another alternative, focusing on reaction efficiency and selectivity. They are particularly advantageous for producing specialty and fine chemicals where precision is critical. These processes can significantly lower energy consumption and waste generation, appealing to environmentally conscious businesses. However, they often require substantial R&D investment and specialized knowledge, making them less accessible for some companies. Their best use case lies in industries where niche products are prioritized over mass production.
Conclusion: How to Choose the Right Solution for Your Needs?
Choosing the right solution between a reactor manufacturer and its alternatives hinges on your specific operational requirements, budget constraints, and long-term goals. For businesses in Africa, South America, the Middle East, and Europe, understanding the nuances of performance, cost, and maintenance can guide informed decisions. Evaluate each option’s advantages and disadvantages in relation to your production scale, regulatory environment, and technical capabilities. By aligning your choice with your strategic objectives, you can ensure optimal operational efficiency and profitability.
Essential Technical Properties and Trade Terminology for reactor manufacturer
What Are the Key Technical Properties of Reactors for International Buyers?
When sourcing reactors, understanding their technical properties is essential for making informed purchasing decisions. Here are some critical specifications that buyers should consider:
1. Material Grade
The material grade of a reactor influences its durability, corrosion resistance, and overall performance. Common materials include stainless steel, carbon steel, and various alloys, each suited for specific chemical processes. For instance, reactors handling corrosive substances may require higher-grade materials to ensure longevity and safety. Buyers should assess the material grade based on the specific application and environmental conditions to avoid premature failure.
2. Tolerance Levels
Tolerance refers to the acceptable variation in dimensions and specifications of reactor components. High tolerance levels ensure that parts fit together correctly, which is vital for maintaining pressure and preventing leaks. In industries such as pharmaceuticals or food processing, where precision is crucial, specifying tighter tolerances may be necessary. Understanding tolerance requirements helps buyers prevent costly adjustments and ensure operational efficiency.
3. Pressure Ratings
Pressure ratings indicate the maximum pressure a reactor can safely withstand. This property is critical for applications involving high-pressure processes, such as petrochemical production. Buyers must align the pressure rating with the intended use to avoid safety hazards and equipment failures. A reactor with an insufficient pressure rating can lead to catastrophic failures, which is why this specification should never be overlooked.
4. Temperature Resistance
Temperature resistance defines the reactor’s ability to operate under various thermal conditions. Different processes may require reactors to withstand extreme temperatures, and selecting the right equipment is crucial for safety and efficiency. Buyers should consult technical data sheets to ensure that the reactor can handle the thermal demands of their specific application, particularly in industries like oil and gas.
5. Volume Capacity
Volume capacity refers to the maximum amount of material a reactor can hold. This property influences production efficiency and should be chosen based on the scale of operations. For international buyers, understanding the volume capacity is essential for matching the reactor’s capabilities with production needs, especially when scaling up processes in emerging markets.
What Are Common Trade Terms in the Reactor Manufacturing Industry?
Familiarity with trade terminology can streamline negotiations and facilitate smoother transactions. Here are several essential terms every international B2B buyer should know:
1. OEM (Original Equipment Manufacturer)
An OEM is a company that produces parts or equipment that may be marketed by another manufacturer. In the context of reactors, buyers may deal with OEMs that provide specialized components or complete systems. Understanding the role of OEMs helps buyers navigate sourcing options and ensure they are procuring quality products from reputable manufacturers.
2. MOQ (Minimum Order Quantity)
MOQ refers to the smallest quantity of a product that a supplier is willing to sell. Knowing the MOQ is vital for budget planning and inventory management. For international buyers, especially in regions like Africa and South America, negotiating MOQs can be crucial to avoid excess inventory while ensuring adequate supply for production needs.
3. RFQ (Request for Quotation)
An RFQ is a document that solicits price quotes from suppliers. It typically includes detailed specifications, quantities, and terms of delivery. By issuing an RFQ, buyers can compare offers from multiple manufacturers, ensuring they receive competitive pricing and favorable terms. This process is particularly useful for buyers in the Middle East and Europe looking to make informed purchasing decisions.
4. Incoterms (International Commercial Terms)
Incoterms are a set of predefined international trade terms that clarify the responsibilities of buyers and sellers regarding shipping, insurance, and tariffs. Familiarity with these terms helps buyers understand their obligations and risks involved in international shipping. For instance, terms like FOB (Free on Board) and CIF (Cost, Insurance, and Freight) can significantly impact overall costs.
5. Lead Time
Lead time refers to the time taken from placing an order to receiving the product. Understanding lead times is crucial for supply chain management, particularly in industries with tight production schedules. International buyers must communicate their lead time expectations clearly to suppliers to avoid disruptions in their operations.
By grasping these technical properties and trade terminologies, international B2B buyers can enhance their procurement processes, ensuring they select the right reactors for their specific needs while navigating the complexities of global trade.
Navigating Market Dynamics and Sourcing Trends in the reactor manufacturer Sector
What Are the Current Market Dynamics and Key Trends in the Reactor Manufacturer Sector?
The reactor manufacturer sector is experiencing significant transformations driven by various global factors. The demand for reactors is primarily propelled by the increasing need for energy-efficient solutions, particularly in emerging markets across Africa, South America, the Middle East, and Europe. As countries strive for energy independence and sustainability, there is a growing emphasis on advanced manufacturing technologies, such as automation and digitalization, which enhance production efficiency and reduce costs.
Key trends include the integration of Industry 4.0 technologies, which facilitate real-time monitoring and predictive maintenance. This shift is particularly relevant for international B2B buyers looking to optimize their supply chains and improve operational efficiency. Additionally, the rise of modular reactor designs is gaining traction, offering flexibility and scalability, appealing to buyers in regions with varying energy demands.
Furthermore, geopolitical factors and trade agreements impact sourcing strategies. Buyers from the Middle East and Africa must navigate regional regulations and local market conditions, which can influence the availability and pricing of raw materials. Understanding these dynamics is crucial for making informed purchasing decisions and fostering long-term partnerships with suppliers.
How Is Sustainability and Ethical Sourcing Shaping the Reactor Manufacturer Sector?
Sustainability has become a cornerstone in the reactor manufacturing industry, with an increasing focus on minimizing environmental impact. B2B buyers are now prioritizing suppliers who demonstrate a commitment to sustainable practices, including the use of renewable materials and energy-efficient manufacturing processes. This trend is particularly evident in Europe, where regulatory frameworks are stringent regarding emissions and waste management.
Ethical sourcing is equally vital, as buyers seek transparency in their supply chains. Ensuring that materials are sourced responsibly and ethically not only enhances brand reputation but also aligns with consumer expectations in various markets. Certifications such as ISO 14001 for environmental management and LEED for sustainable building practices are becoming essential for suppliers to establish credibility and attract international buyers.
Incorporating green materials and technologies into reactor manufacturing processes can significantly reduce the carbon footprint of operations. Buyers should engage with manufacturers who are actively pursuing certifications and are willing to share their sustainability initiatives. This approach not only fosters trust but also ensures compliance with increasingly stringent regulations worldwide.
What Is the Brief Evolution of the Reactor Manufacturer Sector?
The reactor manufacturer sector has evolved significantly over the past few decades, driven by technological advancements and changing market demands. Initially focused on traditional methods and designs, the industry has shifted towards innovation and efficiency. The introduction of computer-aided design (CAD) and simulation software has revolutionized the design process, allowing for more complex and efficient reactor systems.
In recent years, the emphasis on sustainability and regulatory compliance has further transformed the landscape. Manufacturers are increasingly adopting environmentally friendly practices and materials, responding to the global call for more responsible industrial operations. This evolution presents a unique opportunity for international B2B buyers to align with forward-thinking suppliers that prioritize both innovation and sustainability in their offerings.
By understanding these historical shifts, buyers can better navigate the current market and leverage opportunities for collaboration with manufacturers that are well-positioned for future growth.
Frequently Asked Questions (FAQs) for B2B Buyers of reactor manufacturer
-
How do I choose the right reactor manufacturer for my business needs?
Choosing the right reactor manufacturer involves assessing several key factors. Start by identifying your specific requirements, such as reactor type, capacity, and intended applications. Research potential manufacturers based on their experience, certifications, and technological capabilities. Request case studies or client testimonials to gauge their reliability and quality. Additionally, consider suppliers who offer customization options to meet your unique operational needs. Engaging in discussions about your project scope can also help in determining their understanding of your industry challenges. -
What is the best reactor design for chemical processing applications?
The best reactor design for chemical processing largely depends on the specific reactions and processes involved. Common designs include batch reactors for small-scale production and continuous reactors for larger, ongoing processes. For exothermic reactions, a well-designed heat exchanger is crucial to manage temperature. Additionally, consider factors like mixing efficiency, residence time, and material compatibility. Consulting with a manufacturer who can provide expertise in reactor design tailored to your application will ensure optimal performance and safety. -
What are the minimum order quantities (MOQ) for reactors from manufacturers?
Minimum order quantities (MOQ) can vary significantly among reactor manufacturers. Typically, MOQs are influenced by the complexity of the reactor design, production costs, and the manufacturer’s operational capabilities. Smaller manufacturers may offer lower MOQs, while larger firms might require higher quantities to justify production runs. It’s essential to discuss your needs directly with potential suppliers to negotiate terms that align with your business volume and budget constraints, especially if you’re looking to pilot a new process. -
How can I ensure quality assurance (QA) in reactor manufacturing?
To ensure quality assurance in reactor manufacturing, start by selecting a manufacturer with robust QA processes in place. Request information about their quality certifications, such as ISO 9001, and inquire about their testing protocols for materials and finished products. Regular audits and inspections during the manufacturing process can also help maintain quality standards. Establish a clear communication channel with the manufacturer for ongoing updates and feedback, and consider third-party inspections if necessary to verify compliance with industry standards. -
What payment terms are typically offered by reactor manufacturers?
Payment terms can vary widely among reactor manufacturers, often depending on the company’s policies and the scale of the order. Common terms include a deposit upfront (typically 30-50%), with the balance due upon completion or prior to shipping. Some manufacturers may offer financing options or installment payments for larger orders. It’s crucial to clarify payment terms early in negotiations to ensure alignment with your financial planning and to avoid any misunderstandings later in the procurement process. -
What logistics considerations should I keep in mind when importing reactors?
When importing reactors, consider logistics factors such as shipping methods, customs regulations, and delivery timelines. Collaborate with your manufacturer to understand the best shipping options based on your location and urgency. Ensure compliance with local import regulations in your country, which can vary significantly across regions like Africa, South America, and Europe. Additionally, factor in potential tariffs and duties that may apply. Engaging a logistics partner with experience in industrial equipment can streamline the process and mitigate risks. -
How do I vet potential reactor suppliers to ensure reliability?
Vetting potential reactor suppliers involves a multi-faceted approach. Begin by checking their industry reputation through reviews and testimonials from previous clients. Request references and conduct interviews with existing customers to gather insights into their experiences. Assess the supplier’s financial stability, production capacity, and adherence to international standards. Additionally, visiting their facility, if possible, can provide firsthand insight into their operations and quality control practices, fostering confidence in your selection. -
What customization options are available for industrial reactors?
Customization options for industrial reactors are often extensive, catering to specific operational requirements. Common customizations include size adjustments, material selection (such as stainless steel or glass-lined), and modifications to enhance safety features, such as pressure relief valves. Some manufacturers also offer integration of advanced control systems for better process management. Engaging in detailed discussions with your chosen supplier about your specific needs will help identify the best customization options to optimize reactor performance for your applications.
Important Disclaimer & Terms of Use
⚠️ Important Disclaimer
The information provided in this guide, including content regarding manufacturers, technical specifications, and market analysis, is for informational and educational purposes only. It does not constitute professional procurement advice, financial advice, or legal advice.
While we have made every effort to ensure the accuracy and timeliness of the information, we are not responsible for any errors, omissions, or outdated information. Market conditions, company details, and technical standards are subject to change.
B2B buyers must conduct their own independent and thorough due diligence before making any purchasing decisions. This includes contacting suppliers directly, verifying certifications, requesting samples, and seeking professional consultation. The risk of relying on any information in this guide is borne solely by the reader.
Strategic Sourcing Conclusion and Outlook for reactor manufacturer
As international B2B buyers in the reactor manufacturing sector, understanding the nuances of strategic sourcing is crucial for optimizing procurement processes. The key takeaways from this guide emphasize the importance of evaluating suppliers based on quality, reliability, and technological innovation. Buyers should prioritize partnerships that not only meet immediate needs but also align with long-term sustainability goals.
What are the benefits of strategic sourcing for reactor manufacturers? Engaging in strategic sourcing can lead to significant cost savings, improved supply chain resilience, and access to cutting-edge technologies. By leveraging local suppliers in regions like Africa, South America, the Middle East, and Europe, businesses can enhance their operational efficiency while fostering regional economic growth.
Looking ahead, the landscape of reactor manufacturing is poised for transformation driven by advancements in technology and evolving regulatory frameworks. B2B buyers must remain agile, continuously assessing market trends and supplier capabilities. Embrace a proactive approach to sourcing by building strong relationships with manufacturers and exploring innovative solutions that cater to your specific operational needs. By doing so, you position your organization not just to survive but to thrive in a competitive global market.