Maximize Quality: The Ultimate Wood Panel Custom Guide (2025)
Introduction: Navigating the Global Market for wood panel custom
In today’s dynamic global market, sourcing custom wood panels presents a unique set of challenges for international B2B buyers. With varying quality standards, diverse applications, and a multitude of suppliers, navigating this landscape can be daunting. The demand for bespoke wood panel solutions—whether for architectural projects, furniture manufacturing, or interior design—requires a strategic approach to ensure that the products meet specific requirements while adhering to budget constraints.
This comprehensive guide serves as a vital resource for B2B buyers from Africa, South America, the Middle East, and Europe—including countries like Italy and Australia—by offering actionable insights into the intricacies of the wood panel custom market. We delve into the different types of wood panels available, explore their wide-ranging applications, and provide essential tips for vetting suppliers to ensure quality and reliability. Furthermore, we address cost factors and potential pitfalls, equipping buyers with the knowledge needed to make informed purchasing decisions.
By leveraging this guide, international buyers can streamline their procurement processes, minimize risks, and ultimately enhance their competitive edge in their respective industries. Whether you are looking to enhance your product offerings or optimize supply chain management, understanding the global landscape of custom wood panels is crucial for achieving success in today’s interconnected marketplace.
Understanding wood panel custom Types and Variations
Type Name | Key Distinguishing Features | Primary B2B Applications | Brief Pros & Cons for Buyers |
---|---|---|---|
Plywood | Made from layers of wood veneer, strong and stable | Furniture, cabinetry, flooring | Pros: Cost-effective, versatile. Cons: Limited moisture resistance. |
Medium Density Fiberboard (MDF) | Composed of wood fibers and resin, smooth surface | Interior applications, decorative panels | Pros: Excellent for detailed finishes. Cons: Heavier, lower strength. |
Oriented Strand Board (OSB) | Made from strands of wood, engineered for strength | Construction, sheathing, flooring | Pros: High structural integrity. Cons: Can be less aesthetically pleasing. |
Laminated Veneer Lumber (LVL) | Layers of wood bonded with adhesive, strong and stable | Beams, headers, structural applications | Pros: High load-bearing capacity. Cons: More expensive than traditional lumber. |
Particle Board | Compressed wood particles, often covered with veneer | Furniture, shelving, low-cost applications | Pros: Affordable, lightweight. Cons: Susceptible to moisture damage. |
What are the Key Characteristics of Plywood for B2B Buyers?
Plywood is a widely used wood panel type made from thin layers of wood veneer glued together. Its multi-layered structure provides exceptional strength and stability, making it suitable for various applications such as furniture, cabinetry, and flooring. For B2B buyers, it’s crucial to consider the grade of plywood, as higher grades offer better appearance and durability. Additionally, sourcing plywood that meets international standards can ensure compliance with construction regulations in different markets.
How Does Medium Density Fiberboard (MDF) Benefit B2B Applications?
Medium Density Fiberboard (MDF) is manufactured from wood fibers bonded with resin, resulting in a smooth and uniform surface. It is particularly favored for interior applications, including decorative panels and furniture, where a fine finish is essential. B2B buyers should note that while MDF is excellent for detailed designs, it is heavier and less durable than other wood panels. Consideration of weight and application-specific durability is essential when selecting MDF for projects.
What Makes Oriented Strand Board (OSB) a Popular Choice in Construction?
Oriented Strand Board (OSB) is an engineered wood product made from strands of wood that are oriented in specific directions for enhanced strength. This type of wood panel is commonly used in construction for sheathing, flooring, and roof applications. B2B buyers should recognize that while OSB offers high structural integrity, its aesthetic appeal may be lower compared to plywood or MDF. Understanding the intended use and visual requirements is critical when opting for OSB in construction projects.
Why Should B2B Buyers Consider Laminated Veneer Lumber (LVL)?
Laminated Veneer Lumber (LVL) is created by bonding layers of wood veneers with adhesive, resulting in a strong and stable material ideal for structural applications like beams and headers. Its high load-bearing capacity makes it a preferred choice for building construction. For B2B buyers, the higher cost of LVL compared to traditional lumber is an important consideration, but the benefits in terms of strength and stability can justify the investment, especially for large-scale projects.
What are the Advantages and Disadvantages of Particle Board for B2B Use?
Particle Board is made from compressed wood particles, often covered with a veneer layer. It is a cost-effective option for furniture and shelving, appealing to budget-conscious B2B buyers. However, its susceptibility to moisture damage is a significant drawback, making it less suitable for environments with high humidity. Buyers should assess the application context carefully, weighing the affordability of particle board against its potential limitations in durability and performance.
Related Video: Custom Building Wood Fence – Step by Step Privacy Wood Fence
Key Industrial Applications of wood panel custom
Industry/Sector | Specific Application of wood panel custom | Value/Benefit for the Business | Key Sourcing Considerations for this Application |
---|---|---|---|
Furniture Manufacturing | Custom cabinetry and furniture design | Enhanced aesthetics and functional design flexibility | Quality of materials, adherence to design specifications, lead times |
Construction | Interior wall panels and cladding | Improved insulation and soundproofing | Durability, fire resistance, and compliance with local regulations |
Retail and Hospitality | Custom display fixtures and interior decor | Unique branding opportunities and customer engagement | Design customization, material sustainability, and cost-effectiveness |
Automotive | Interior panels and components | Lightweight solutions that enhance fuel efficiency | Precision engineering, material quality, and supplier reliability |
Packaging | Custom wooden crates and pallets | Increased protection for goods and reduced shipping costs | Load capacity, compliance with international shipping standards |
How is Custom Wood Panel Used in Furniture Manufacturing?
In the furniture manufacturing sector, custom wood panels are essential for creating bespoke cabinetry and furniture pieces that meet specific client needs. These panels allow manufacturers to offer unique designs that enhance the aesthetics and functionality of their products. International buyers should consider sourcing high-quality materials that adhere to specific design specifications while also being mindful of lead times to ensure timely production.
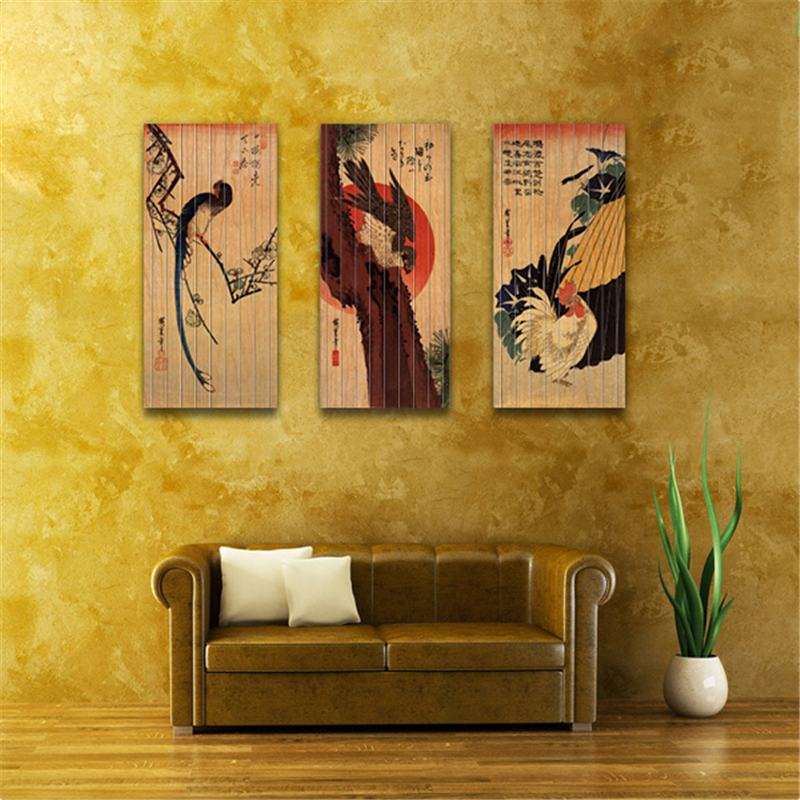
A stock image related to wood panel custom.
What Role Does Custom Wood Panel Play in Construction?
Custom wood panels are widely used in the construction industry for applications like interior wall panels and cladding. They provide not only aesthetic appeal but also improved insulation and soundproofing, which are critical in residential and commercial buildings. Buyers from regions such as Africa and the Middle East should prioritize durability and fire resistance, ensuring that the materials comply with local building regulations and standards.
Why is Custom Wood Panel Important in Retail and Hospitality?
In retail and hospitality, custom wood panels are vital for creating display fixtures and interior decor that reflect brand identity. These tailored solutions offer unique branding opportunities that can significantly enhance customer engagement. B2B buyers in Europe, particularly in Italy, should focus on design customization and material sustainability to meet consumer preferences for environmentally friendly products while also considering cost-effectiveness.
How is Custom Wood Panel Utilized in the Automotive Industry?
The automotive industry benefits from custom wood panels for interior applications, including dashboards and trim components. These lightweight solutions not only improve vehicle aesthetics but also contribute to fuel efficiency by reducing overall vehicle weight. Buyers in this sector must emphasize precision engineering and high material quality, as well as the reliability of suppliers to ensure that components meet rigorous safety and performance standards.
What are the Advantages of Custom Wood Panel in Packaging?
Custom wooden crates and pallets made from wood panels are increasingly popular in the packaging industry due to their ability to provide increased protection for goods during transport. They can also reduce shipping costs by being lightweight yet sturdy. International buyers need to consider load capacity and ensure compliance with international shipping standards, particularly for those sourcing from regions like South America and Africa, where logistics can pose challenges.
Related Video: KUKA Robot Acts as a Multifunctional Assistant in the Wood Industry
3 Common User Pain Points for ‘wood panel custom’ & Their Solutions
Scenario 1: Inconsistent Quality of Custom Wood Panels
The Problem: One of the most pressing challenges for international B2B buyers is the inconsistency in the quality of custom wood panels. This issue often arises when sourcing from different suppliers or regions, leading to variations in thickness, color, grain pattern, and durability. Such discrepancies can result in costly project delays, increased waste, and ultimately, dissatisfaction from clients who expect a uniform product. Buyers may also struggle with the lack of standardized quality control processes across suppliers, making it difficult to ensure that the panels meet their specific requirements.
The Solution: To mitigate quality inconsistencies, buyers should establish clear specifications and standards that detail the exact requirements for the wood panels. This includes guidelines on dimensions, tolerances, finishes, and types of wood. Engaging in a thorough vetting process for suppliers is crucial; consider conducting factory audits or requesting samples before placing larger orders. Additionally, building a strong relationship with a few key suppliers can foster better communication regarding quality expectations and lead to more consistent product outcomes. Utilizing technology such as digital quality assurance platforms can also help monitor product quality throughout the manufacturing process.
Scenario 2: Long Lead Times and Delays in Delivery
The Problem: For businesses in Africa, South America, the Middle East, and Europe, long lead times and unexpected delays in the delivery of custom wood panels can significantly disrupt project timelines. Factors such as shipping logistics, customs clearance, and production schedules can all contribute to these delays. This situation creates a ripple effect, impacting project planning, resource allocation, and client satisfaction.
The Solution: To address lead time issues, it’s essential for buyers to communicate their project timelines clearly with suppliers from the outset. Implementing a buffer in the project schedule can also help accommodate potential delays. Additionally, consider diversifying your supplier base to include local manufacturers who can provide quicker turnaround times. Leveraging advanced logistics solutions, such as tracking technologies and inventory management systems, can enhance visibility and predictability in the supply chain. Finally, establishing strong relationships with freight forwarders can streamline the shipping process and facilitate faster customs clearance.
Scenario 3: Difficulty in Customization and Design Flexibility
The Problem: B2B buyers often find themselves frustrated by the limitations in customization options for wood panels. Many suppliers may offer standard sizes and designs that do not meet the unique needs of a project, particularly in niche markets or specialized industries. This lack of flexibility can hinder creativity and innovation in design, ultimately affecting the buyer’s ability to deliver tailored solutions to their clients.
The Solution: To overcome the challenges of customization, buyers should prioritize suppliers that specialize in bespoke wood panel solutions. When negotiating with suppliers, clearly outline your specific design needs and ask about their capabilities in terms of customization. Utilizing CAD (Computer-Aided Design) software can facilitate better communication of design ideas and specifications, making it easier for suppliers to understand and execute on your vision. Furthermore, consider collaborating with suppliers that offer prototyping services, allowing you to test and refine designs before full-scale production. Engaging in continuous dialogue with your suppliers about emerging trends and technologies can also inspire innovative solutions tailored to your projects.
Strategic Material Selection Guide for wood panel custom
When selecting materials for custom wood panels, international B2B buyers must consider various factors that influence product performance, cost, and suitability for specific applications. Below, we analyze four common materials used in wood panel customization, highlighting their properties, advantages, disadvantages, and specific considerations for buyers in Africa, South America, the Middle East, and Europe.
What Are the Key Properties of Plywood for Custom Wood Panels?
Plywood is a versatile engineered wood product made from thin layers of wood veneer glued together. It boasts excellent strength-to-weight ratios and is resistant to warping and cracking under varying temperatures and humidity levels. Plywood typically has a temperature rating of up to 60°C (140°F) and is suitable for both interior and exterior applications.
Pros & Cons: The primary advantages of plywood include its durability, cost-effectiveness, and ease of manufacturing. However, it can be susceptible to water damage if not properly treated, and its aesthetic appeal may not match that of solid wood.
Impact on Application: Plywood is compatible with various media, making it suitable for furniture, cabinetry, and flooring. Buyers should ensure compliance with local standards, such as ASTM for the U.S. market or EN standards in Europe.
How Does Medium Density Fiberboard (MDF) Compare for Custom Wood Panels?
Medium Density Fiberboard (MDF) is made from wood fibers bonded with resin under heat and pressure. It offers a smooth surface ideal for painting and veneering, with a density that provides excellent sound insulation.
Pros & Cons: MDF is relatively inexpensive and easy to work with, making it a popular choice for intricate designs. However, it is less durable than plywood and can be prone to swelling when exposed to moisture.
Impact on Application: MDF is commonly used in decorative applications such as moldings and cabinetry. Buyers should be aware of formaldehyde emissions and ensure compliance with regulations such as CARB in California or E1 standards in Europe.
What Are the Advantages of Oriented Strand Board (OSB) for Custom Wood Panels?
Oriented Strand Board (OSB) is an engineered wood product made from strands of wood arranged in layers and bonded with adhesive. OSB is recognized for its structural strength and is often used in construction applications.
Pros & Cons: OSB is cost-effective and offers good load-bearing capacity. However, its appearance is less refined than plywood or MDF, which may limit its use in visible applications.
Impact on Application: OSB is suitable for wall sheathing and flooring but may not be ideal for high-end furniture. Buyers should check for compliance with local building codes and standards, particularly in regions prone to humidity.
Why Is Solid Wood a Preferred Choice for Custom Wood Panels in Certain Applications?
Solid wood panels are made from natural timber and are prized for their aesthetic appeal and durability. They offer excellent temperature and pressure resistance, making them suitable for high-quality furniture and cabinetry.
Pros & Cons: The main advantage of solid wood is its natural beauty and long lifespan. However, it is often the most expensive option and can be challenging to source sustainably.
Impact on Application: Solid wood is ideal for high-end applications where aesthetics are paramount. Buyers should consider sustainability certifications such as FSC to ensure responsible sourcing.
Material | Typical Use Case for wood panel custom | Key Advantage | Key Disadvantage/Limitation | Relative Cost (Low/Med/High) |
---|---|---|---|---|
Plywood | Furniture, cabinetry, flooring | Excellent strength-to-weight ratio | Susceptible to water damage | Medium |
Medium Density Fiberboard (MDF) | Decorative moldings, cabinetry | Smooth surface ideal for painting | Prone to swelling in moisture | Low |
Oriented Strand Board (OSB) | Wall sheathing, flooring | Cost-effective with good load-bearing | Less refined appearance | Low |
Solid Wood | High-end furniture, cabinetry | Natural beauty and durability | Expensive and sourcing challenges | High |
In conclusion, the choice of material for custom wood panels significantly impacts performance, cost, and application suitability. International B2B buyers should carefully evaluate these factors, ensuring compliance with local standards and regulations to make informed purchasing decisions.
In-depth Look: Manufacturing Processes and Quality Assurance for wood panel custom
What Are the Key Stages in the Manufacturing Process of Custom Wood Panels?
The manufacturing process for custom wood panels involves several critical stages that ensure the final product meets both aesthetic and functional requirements. Understanding these stages is essential for international B2B buyers looking to source high-quality wood panels.
-
Material Preparation: The first stage involves selecting and preparing the raw materials. High-quality timber is sourced, often from sustainable forests, to minimize environmental impact. This stage includes cutting logs into manageable sizes, debarking, and drying the wood to a specific moisture content to prevent warping and splitting later in the process. Buyers should inquire about the wood species and sourcing practices to ensure they align with their standards.
-
Forming: Once the materials are prepared, the next step is forming. This involves shaping the wood into panels using techniques such as laminating, pressing, or veneering. Depending on the desired characteristics of the final product, different adhesives and treatments may be applied. Buyers should assess the technology used in this stage, as advanced techniques can enhance durability and finish quality.
-
Assembly: After forming, the panels are assembled. This could involve joining multiple layers of wood or integrating additional materials such as particleboard or MDF (Medium Density Fiberboard). The assembly method significantly impacts the structural integrity of the panels. Buyers should look for suppliers that employ precision machinery to ensure consistent assembly quality.
-
Finishing: The final manufacturing stage is finishing, which includes sanding, coating, and applying stains or varnishes. The choice of finish can greatly affect both the aesthetic appeal and the durability of the panels. B2B buyers should request samples of different finishes to evaluate their suitability for specific applications.
What Quality Assurance Measures Are Essential in Custom Wood Panel Manufacturing?
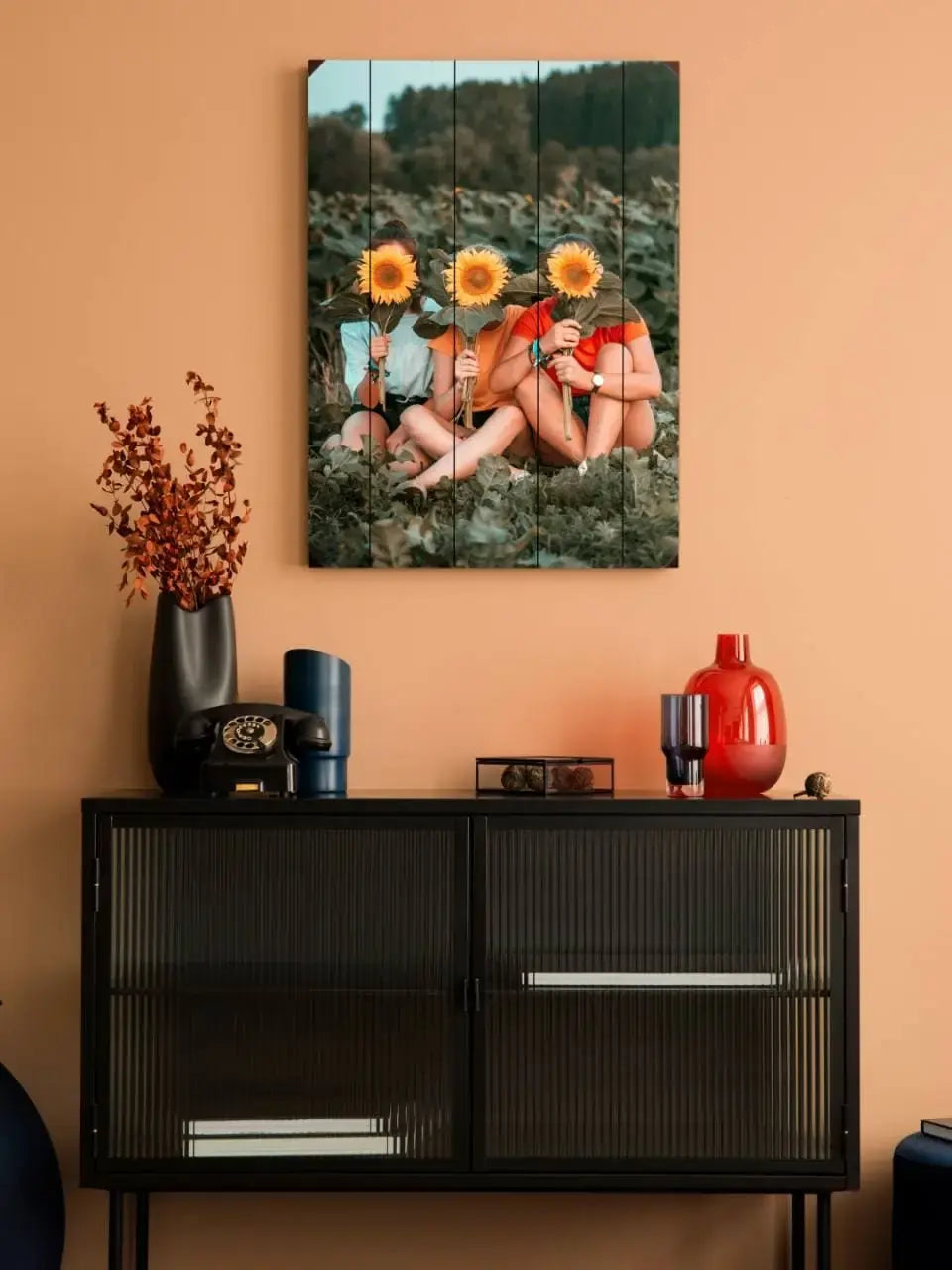
A stock image related to wood panel custom.
Quality assurance (QA) in the manufacturing of custom wood panels is vital for ensuring that the final product meets international standards and customer expectations. Here are key QA measures that B2B buyers should consider:
-
International Standards Compliance: Many wood panel manufacturers adhere to international quality standards, such as ISO 9001, which provides a framework for consistent quality management systems. Buyers should verify that their suppliers are certified and maintain these standards throughout their operations.
-
Industry-Specific Certifications: Depending on the market, there may be additional certifications that are relevant. For instance, CE marking is crucial for products sold in the European market, indicating compliance with safety and environmental regulations. In North America, the APA (American Plywood Association) certification may be important. Buyers should ask about these certifications to ensure compliance.
-
Quality Control Checkpoints: Effective quality control involves multiple checkpoints throughout the manufacturing process:
– Incoming Quality Control (IQC): This stage involves inspecting raw materials upon arrival to ensure they meet predefined specifications.
– In-Process Quality Control (IPQC): During manufacturing, continuous monitoring is conducted to catch any deviations from quality standards early.
– Final Quality Control (FQC): After production, finished panels undergo rigorous testing for dimensional accuracy, appearance, and strength. -
Common Testing Methods: Testing methods can include moisture content analysis, strength testing (such as bending and tensile strength), and surface finish evaluation. B2B buyers should request detailed testing reports to verify that the products meet their specific requirements.
How Can B2B Buyers Verify Supplier Quality Control Practices?
To ensure that suppliers maintain high standards of quality control, B2B buyers should adopt several verification strategies:
-
Supplier Audits: Conducting regular audits of potential suppliers is one of the most effective ways to assess their manufacturing practices and quality control processes. These audits can be performed by the buyer or by hiring third-party inspection agencies.
-
Reviewing Quality Assurance Reports: Buyers should request access to quality assurance reports, including testing results and compliance certifications. This documentation provides insights into the supplier’s quality management practices.
-
Third-Party Inspections: Engaging third-party inspection services can offer an unbiased evaluation of the supplier’s production processes and quality control measures. This is particularly valuable for international transactions, where buyers may not have the means to conduct on-site inspections.
-
Understanding QC and Certification Nuances: For international buyers, particularly those from Africa, South America, the Middle East, and Europe, it’s important to understand how different regions interpret and implement quality standards. Some countries may have specific local regulations that impact product quality. Buyers should familiarize themselves with these nuances to ensure compliance and mitigate risks.
What Are the Challenges and Considerations for International B2B Buyers in Quality Assurance?
International B2B buyers face unique challenges when it comes to quality assurance in the custom wood panel industry:
-
Cultural and Regulatory Differences: Different countries have varying regulations regarding wood sourcing, manufacturing practices, and quality standards. B2B buyers must conduct thorough research to understand these differences to avoid compliance issues.
-
Supply Chain Transparency: Ensuring transparency in the supply chain can be challenging, especially with multiple intermediaries involved. Buyers should seek suppliers that provide complete visibility into their sourcing and manufacturing processes.
-
Language Barriers and Communication: Effective communication is crucial in quality assurance. Language barriers can lead to misunderstandings regarding specifications and quality requirements. Buyers should establish clear communication channels and consider using professional translators if necessary.
-
Logistics and Shipping Considerations: Quality can be compromised during shipping and handling. Buyers should work with suppliers that prioritize packaging and logistics to protect the integrity of the wood panels during transit.
By understanding these manufacturing processes and quality assurance practices, international B2B buyers can make informed decisions when sourcing custom wood panels, ensuring they receive high-quality products that meet their needs and standards.
Practical Sourcing Guide: A Step-by-Step Checklist for ‘wood panel custom’
This practical sourcing guide is designed to help international B2B buyers effectively procure custom wood panels. Whether you are based in Africa, South America, the Middle East, or Europe, following these steps will streamline your sourcing process and help you make informed decisions.
Step 1: Define Your Technical Specifications
Clearly outlining your technical requirements is the foundation of a successful sourcing process. This includes dimensions, material types, finishes, and any specific industry standards you must adhere to. Providing precise specifications helps suppliers understand your needs and reduces the likelihood of misunderstandings or errors during production.
Step 2: Research Potential Suppliers
Conduct thorough research to identify reputable suppliers who specialize in custom wood panels. Utilize online marketplaces, industry directories, and trade shows to gather a list of potential candidates. Pay attention to their experience in your specific market and their track record for quality and reliability.
Step 3: Evaluate Supplier Credentials
Before moving forward, it is essential to verify the credentials of potential suppliers. Request documentation such as ISO certifications, sustainability practices, and compliance with local regulations. This step ensures that you are partnering with a supplier that meets industry standards and maintains ethical production practices.
Step 4: Request Samples and Prototypes
Once you have shortlisted suppliers, request samples or prototypes of their wood panels. This is crucial for assessing the quality, aesthetics, and craftsmanship of the products. Evaluate the samples against your specifications to ensure they meet your expectations before placing a larger order.
Step 5: Negotiate Terms and Pricing
Engage in discussions regarding pricing, payment terms, and delivery schedules with your chosen supplier. Ensure that all terms are clear and documented to avoid potential disputes later. Consider factors such as bulk order discounts, payment methods, and lead times to find the best deal.
Step 6: Establish Communication Protocols
Effective communication is key to a successful partnership. Establish clear lines of communication, including preferred contact methods and response times. Regular updates on production status and any potential issues will help build trust and ensure that your project stays on track.
Step 7: Plan for Quality Control and Inspection
Implement a quality control plan that includes inspection of the wood panels upon delivery. Define the criteria for acceptance and determine how discrepancies will be handled. This proactive approach helps mitigate risks associated with quality issues and ensures that you receive products that meet your specifications.
By following this step-by-step checklist, you can navigate the complexities of sourcing custom wood panels with confidence, ensuring that you secure high-quality materials that meet your business needs.
Comprehensive Cost and Pricing Analysis for wood panel custom Sourcing
What Are the Key Cost Components in Custom Wood Panel Sourcing?
When sourcing custom wood panels, understanding the various cost components is essential for accurate budgeting and pricing strategies. The primary cost components include:
-
Materials: The choice of wood species (e.g., oak, pine, MDF) significantly impacts material costs. High-quality, sustainably sourced wood may come at a premium but can enhance product longevity and appeal.
-
Labor: Labor costs vary by region and depend on the complexity of the manufacturing process. Skilled labor for intricate designs may increase costs, while automated processes can reduce them.
-
Manufacturing Overhead: This includes expenses related to facility operations, utilities, and equipment maintenance. Efficient manufacturing practices can help minimize these overhead costs.
-
Tooling: Custom designs often require specialized tooling and molds, contributing to initial setup costs. However, these costs can be amortized over larger production runs.
-
Quality Control (QC): Ensuring product quality through rigorous QC processes adds to the overall cost but is critical for maintaining standards and meeting buyer specifications.
-
Logistics: Transportation and shipping costs are influenced by the distance between the supplier and the buyer, as well as the chosen shipping methods. International shipping can involve additional tariffs and customs duties.
-
Margin: Suppliers typically add a markup to cover their costs and ensure profitability. Understanding the markup percentage can aid in evaluating supplier pricing.
How Do Price Influencers Affect Custom Wood Panel Sourcing?
Several factors can influence the pricing of custom wood panels. Key influencers include:
-
Volume and Minimum Order Quantity (MOQ): Larger orders often result in lower unit prices due to economies of scale. However, buyers must consider their storage capabilities and cash flow when committing to high MOQs.
-
Specifications and Customization: Custom designs typically incur higher costs due to the additional time and resources required. Clear communication of specifications is vital to avoid costly revisions.
-
Material Quality and Certifications: Products that meet specific quality standards or certifications (such as FSC certification) can command higher prices. Buyers should weigh the benefits of certified materials against budget constraints.
-
Supplier Factors: The reputation, reliability, and location of suppliers can impact pricing. Established suppliers may charge more, but they often provide better quality assurance and support.
-
Incoterms: The choice of Incoterms affects shipping costs and responsibilities. Understanding terms like FOB (Free On Board) or CIF (Cost Insurance and Freight) is crucial for accurate total cost assessments.
What Are the Best Tips for Negotiating Prices in Custom Wood Panel Sourcing?
To effectively negotiate prices and ensure cost efficiency, consider the following strategies:
-
Research and Compare: Conduct thorough market research to understand prevailing prices and identify potential suppliers. This knowledge can empower you during negotiations.
-
Focus on Total Cost of Ownership (TCO): Evaluate the long-term costs associated with a supplier beyond the initial purchase price. Consider factors like durability, maintenance, and potential waste.
-
Build Relationships: Developing a strong relationship with suppliers can lead to better pricing and terms. Trust can facilitate negotiations and encourage suppliers to offer discounts or favorable terms.
-
Leverage Volume Discounts: If possible, consolidate orders to meet MOQs and secure lower pricing. Discuss potential long-term contracts with suppliers for consistent pricing.
-
Be Flexible: Flexibility in specifications or delivery timelines can provide leverage in negotiations. Suppliers may be more willing to adjust prices if they can optimize production schedules.
Conclusion: Understanding Costs and Pricing for Informed Decisions
International B2B buyers, particularly from Africa, South America, the Middle East, and Europe, should approach custom wood panel sourcing with a comprehensive understanding of cost structures and pricing influencers. By leveraging insights into costs, negotiation strategies, and total cost evaluations, buyers can make informed decisions that align with their business goals.
Disclaimer: Prices and costs mentioned in this analysis are indicative and subject to change based on market conditions and supplier negotiations. Always consult with suppliers for the most accurate and current pricing.
Alternatives Analysis: Comparing wood panel custom With Other Solutions
Exploring Alternatives to Custom Wood Panels in B2B Applications
When considering custom wood panels for B2B applications, it’s essential to evaluate alternative solutions that may offer similar benefits while addressing specific business needs. This analysis will compare custom wood panels with two viable alternatives: MDF (Medium Density Fiberboard) and Plywood. Understanding the strengths and weaknesses of each option can help international buyers make informed decisions.
Comparison Table of Custom Wood Panels and Alternatives
Comparison Aspect | Wood Panel Custom | MDF (Medium Density Fiberboard) | Plywood |
---|---|---|---|
Performance | High durability and aesthetic appeal | Good durability, smooth surface | Strong, versatile, lightweight |
Cost | Higher initial investment | Generally lower cost | Moderate cost |
Ease of Implementation | Requires skilled labor for installation | Easy to cut and shape | Moderate complexity in installation |
Maintenance | Low maintenance if treated | Low maintenance, but susceptible to water | Moderate maintenance, can warp with moisture |
Best Use Case | High-end applications, bespoke designs | Budget-friendly furniture, cabinetry | Structural applications, outdoor use |
What are the Pros and Cons of Using MDF as an Alternative?
MDF is a popular alternative due to its affordability and ease of use. It is made from wood fibers bonded with adhesives, making it dense and smooth, ideal for detailed finishes. The cost-effectiveness of MDF makes it attractive for bulk orders, particularly for budget-conscious projects in regions like Africa and South America. However, MDF is less durable than custom wood panels and can be susceptible to moisture damage, making it less suitable for high-humidity environments. Additionally, it may lack the aesthetic appeal that custom wood panels offer, limiting its use in high-end applications.
How Does Plywood Compare to Custom Wood Panels?
Plywood is another viable alternative, known for its strength and versatility. Made from layers of wood veneer glued together, plywood is often lighter than solid wood and can provide significant structural integrity. Its moderate cost makes it suitable for a range of applications, including construction and furniture. However, while plywood is more durable than MDF, it may not match the aesthetic quality of custom wood panels. Furthermore, if not properly treated, plywood can warp or degrade in moist conditions, which is a crucial consideration for buyers in humid climates.
How Can B2B Buyers Choose the Right Solution for Their Needs?
When selecting between custom wood panels and their alternatives, B2B buyers should carefully consider their specific project requirements. Factors such as budget constraints, desired aesthetic, and environmental conditions play a critical role in this decision. For projects demanding bespoke designs and high-end finishes, custom wood panels may be the best choice despite the higher cost. Conversely, for more budget-sensitive applications or where moisture resistance is a concern, MDF or plywood may be preferable. Engaging with suppliers who understand regional differences in material performance can also enhance decision-making and lead to better long-term outcomes.
Essential Technical Properties and Trade Terminology for wood panel custom
Understanding the essential technical properties and terminology in the custom wood panel industry is crucial for B2B buyers. This knowledge not only aids in making informed purchasing decisions but also enhances communication with suppliers and manufacturers. Below are some key properties and terms that every international buyer should be familiar with.
What Are the Key Technical Properties of Custom Wood Panels?
1. Material Grade: How Does It Affect Quality?
Material grade refers to the quality classification of the wood used in the panels. Common grades include A, B, C, and D, with A being the highest quality. Higher-grade materials typically offer better durability, appearance, and resistance to defects. For B2B buyers, selecting the appropriate material grade is essential to ensure the longevity and performance of the final product, especially in demanding applications.
2. Tolerance: Why Is Precision Important?
Tolerance defines the allowable deviation in dimensions, such as thickness, width, and length, of wood panels. Tight tolerances are critical for applications where precision is paramount, such as in cabinetry or furniture manufacturing. Understanding tolerance levels helps buyers ensure that the panels will fit seamlessly into their production processes, reducing waste and increasing efficiency.
3. Moisture Content: How Does It Influence Performance?
Moisture content indicates the amount of water present in the wood. It is a critical property because wood can expand or contract with changes in humidity, affecting stability and durability. For buyers, specifying the desired moisture content is vital to prevent warping or cracking, particularly in regions with extreme weather conditions.
4. Density: What Role Does It Play in Strength?
Density measures the mass of the wood per unit volume and is an indicator of strength and durability. Higher density generally means the panel is stronger and more resistant to wear and tear. Buyers should consider density when evaluating panels for load-bearing applications or high-traffic environments, ensuring that the chosen products meet their specific performance requirements.
5. Surface Finish: How Does It Affect Aesthetics and Functionality?
Surface finish refers to the treatment applied to the wood panel’s surface, which can enhance appearance and protect against moisture, scratches, and stains. Common finishes include varnish, lacquer, and oil. Buyers must consider the intended use of the panels when selecting a finish, as it can significantly impact both aesthetic appeal and functional longevity.
What Are Common Trade Terms in the Custom Wood Panel Industry?
1. OEM (Original Equipment Manufacturer): What Does It Mean?
OEM refers to a company that produces parts or equipment that may be marketed by another manufacturer. In the context of custom wood panels, understanding OEM relationships can help buyers identify reliable suppliers who can deliver specialized products tailored to specific needs.
2. MOQ (Minimum Order Quantity): Why Is It Important for Buyers?
MOQ indicates the smallest quantity a supplier is willing to sell. Knowing the MOQ is essential for B2B buyers to manage inventory and cash flow effectively. Buyers should negotiate MOQs that align with their production needs to avoid excess inventory costs.
3. RFQ (Request for Quotation): How to Use It Effectively?
An RFQ is a document sent to suppliers requesting pricing and terms for specific products. Crafting a detailed RFQ can help buyers receive accurate quotes, ensuring they get the best value for their investments. Including specifications like material grade, dimensions, and finishes in the RFQ is crucial for obtaining relevant responses.
4. Incoterms (International Commercial Terms): What Should Buyers Know?
Incoterms are internationally recognized terms that define the responsibilities of buyers and sellers in international transactions. Familiarity with these terms, such as FOB (Free on Board) and CIF (Cost, Insurance, and Freight), is vital for buyers to understand shipping costs, risks, and responsibilities, ultimately aiding in smoother transactions.
5. Lead Time: Why Is It Critical in Supply Chain Management?
Lead time refers to the time taken from placing an order to delivery. Understanding lead times is essential for effective project planning and inventory management. Buyers should communicate their timelines clearly to suppliers to ensure timely delivery of custom wood panels.
By grasping these essential properties and terminologies, international B2B buyers can navigate the custom wood panel industry more effectively, making informed decisions that contribute to their business success.
Navigating Market Dynamics and Sourcing Trends in the wood panel custom Sector
What Are the Key Market Dynamics and Sourcing Trends in the Wood Panel Custom Sector?
The wood panel custom sector is experiencing significant transformation driven by global market dynamics and technological advancements. As international B2B buyers, particularly those from Africa, South America, the Middle East, and Europe, navigate these changes, understanding current trends is crucial.
Global Drivers Shaping the Market
The increasing demand for sustainable building materials is reshaping the wood panel industry. Buyers are increasingly seeking products that not only meet aesthetic and functional requirements but also align with sustainability goals. Additionally, the global rise in construction and renovation projects, particularly in emerging economies, continues to spur demand for custom wood panels. This is complemented by an uptick in digital transformation within the sector, where B2B e-commerce platforms are streamlining sourcing processes, making it easier for buyers to find suppliers worldwide.
Emerging B2B Tech Trends
Technological innovations such as 3D modeling and virtual reality are becoming prominent in the design and customization of wood panels. These technologies enable buyers to visualize and customize products before making a purchase, enhancing the overall customer experience. Furthermore, data analytics is increasingly being utilized to forecast demand and optimize inventory management, helping buyers make informed decisions and reduce excess stock.
Market Dynamics for International Buyers
For B2B buyers, understanding regional market dynamics is essential. In Africa and South America, where local timber resources are abundant, there is a growing trend towards using indigenous materials, which can reduce costs and improve supply chain resilience. Meanwhile, in Europe, stringent regulations regarding sustainable sourcing are prompting buyers to seek suppliers with certified sustainable practices. Buyers must stay informed about these regional trends to leverage opportunities effectively.
How Is Sustainability and Ethical Sourcing Impacting the Wood Panel Custom Sector?
Sustainability has become a cornerstone of procurement strategies in the wood panel custom sector. The environmental impact of deforestation and unsustainable forestry practices has raised awareness among B2B buyers, pushing them toward ethical sourcing practices.
Importance of Ethical Supply Chains
The significance of ethical supply chains cannot be overstated. International buyers are increasingly scrutinizing their suppliers’ practices, seeking those who adhere to responsible sourcing guidelines. This includes verifying that wood products originate from sustainably managed forests and that suppliers comply with regulations such as the EU Timber Regulation (EUTR). By prioritizing ethical sourcing, buyers not only contribute to environmental conservation but also enhance their brand reputation, appealing to a growing market segment that values sustainability.
‘Green’ Certifications and Materials
To facilitate informed sourcing decisions, various ‘green’ certifications are available, such as the Forest Stewardship Council (FSC) and the Programme for the Endorsement of Forest Certification (PEFC). These certifications assure buyers that their wood panel products are sourced sustainably. Additionally, the use of reclaimed wood and alternative materials, such as bamboo and engineered wood products, is gaining traction. Buyers should actively seek suppliers who offer certified products or innovative materials to meet both their project requirements and sustainability goals.
How Has the Wood Panel Custom Sector Evolved Over Time?
The wood panel custom sector has evolved significantly over the decades, transitioning from traditional craftsmanship to a more technology-driven industry. Initially, wood panels were primarily produced using manual techniques, with customization limited to basic dimensions and finishes. However, as the construction industry has advanced, so too has the demand for more complex and tailored solutions.
The introduction of machinery and automated processes in the late 20th century revolutionized production capabilities, enabling faster turnaround times and greater precision. Today, the combination of advanced manufacturing technologies and digital design tools allows for unprecedented levels of customization and personalization. This evolution not only meets the diverse needs of international B2B buyers but also sets the stage for future innovations in the wood panel custom sector. Understanding this historical context can provide valuable insights for buyers looking to leverage the latest advancements in their sourcing strategies.
Frequently Asked Questions (FAQs) for B2B Buyers of wood panel custom
-
How do I solve issues with wood panel customization for my specific needs?
To address customization challenges, clearly define your requirements before engaging with suppliers. Provide detailed specifications, including dimensions, materials, finishes, and intended use. Open communication is vital—request samples to evaluate quality and craftsmanship. Establish a collaborative relationship with suppliers, as many are willing to accommodate adjustments based on your feedback. Additionally, consider using CAD drawings or prototypes to visualize your needs better, ensuring that the final product aligns with your expectations. -
What is the best type of wood panel for sustainable building projects?
For sustainable building projects, consider using bamboo, reclaimed wood, or certified products from sustainably managed forests. Bamboo grows rapidly and has a lower environmental impact, while reclaimed wood reduces waste and gives character to new constructions. Look for certifications such as FSC (Forest Stewardship Council) or PEFC (Programme for the Endorsement of Forest Certification) to ensure that the wood panels meet sustainability criteria. Collaborate with suppliers who prioritize eco-friendly practices to enhance your project’s sustainability profile. -
How can I ensure the quality of wood panels before making a purchase?
To ensure quality, first, conduct thorough research on potential suppliers. Look for reviews, certifications, and industry reputation. Request product samples to assess the material’s durability, finish, and overall craftsmanship. Implement quality assurance protocols, such as on-site inspections during production or third-party quality checks before shipment. Establish clear quality metrics with suppliers and communicate your expectations upfront to prevent misunderstandings. -
What are the typical minimum order quantities (MOQs) for custom wood panels?
Minimum order quantities for custom wood panels can vary significantly based on the supplier and the complexity of the customization. Generally, MOQs may range from 50 to 500 units. For smaller businesses or those testing a new market, some suppliers may offer lower MOQs, but expect higher per-unit costs. Always clarify MOQs during initial discussions to align expectations and explore options for batch ordering to meet your needs efficiently. -
What payment terms should I expect when sourcing wood panels internationally?
Payment terms for international wood panel purchases typically include options such as advance payments, letters of credit, or payment upon delivery. It’s common for suppliers to require a deposit (20-30%) upfront to initiate production, with the balance due before shipment. Negotiate terms that suit your cash flow while ensuring security for both parties. Consider using escrow services for large transactions to protect your investment until the goods are received and inspected. -
How do I vet suppliers for custom wood panels in international markets?
Vetting suppliers requires a multi-faceted approach. Start by checking their credentials, including business licenses and certifications relevant to your industry. Look for testimonials or case studies from previous clients, particularly those in your region. Utilize platforms like Alibaba or Global Sources, where verified suppliers are listed. Additionally, consider conducting factory visits or utilizing third-party inspection services to assess manufacturing capabilities and quality control processes. -
What logistics considerations should I keep in mind when importing wood panels?
When importing wood panels, logistics considerations include shipping methods, customs regulations, and delivery timelines. Choose between air freight for speed or ocean freight for cost-effectiveness. Ensure compliance with international shipping regulations, including phytosanitary certificates if required. Work with a freight forwarder who understands the specific requirements for wood products in your target market to streamline customs clearance and minimize delays. -
How can I manage the risk of supply chain disruptions in wood panel sourcing?
To manage supply chain risks, diversify your supplier base across different regions to mitigate the impact of localized disruptions. Establish strong relationships with multiple suppliers to ensure alternative options are available. Maintain a buffer stock of critical materials to weather short-term shortages. Regularly assess your supply chain for vulnerabilities, and stay informed about geopolitical events or economic changes that could affect your suppliers.
Important Disclaimer & Terms of Use
⚠️ Important Disclaimer
The information provided in this guide, including content regarding manufacturers, technical specifications, and market analysis, is for informational and educational purposes only. It does not constitute professional procurement advice, financial advice, or legal advice.
While we have made every effort to ensure the accuracy and timeliness of the information, we are not responsible for any errors, omissions, or outdated information. Market conditions, company details, and technical standards are subject to change.
B2B buyers must conduct their own independent and thorough due diligence before making any purchasing decisions. This includes contacting suppliers directly, verifying certifications, requesting samples, and seeking professional consultation. The risk of relying on any information in this guide is borne solely by the reader.
Strategic Sourcing Conclusion and Outlook for wood panel custom
In the ever-evolving landscape of the wood panel custom industry, strategic sourcing emerges as a pivotal element for international B2B buyers seeking to optimize their supply chains. By leveraging global networks, buyers from Africa, South America, the Middle East, and Europe can access a diverse range of materials and innovations that enhance product quality and sustainability.
What Are the Key Benefits of Strategic Sourcing for Wood Panels?
Strategic sourcing not only reduces costs but also fosters long-term partnerships with suppliers who align with your business values and quality standards. This approach allows companies to adapt swiftly to market changes, ensuring they remain competitive in a fast-paced environment.
How Can International Buyers Prepare for Future Trends in Wood Panels?
Looking ahead, international buyers should stay informed about emerging trends such as eco-friendly materials and advanced manufacturing techniques. Engaging in continuous market analysis and establishing flexible sourcing strategies will enable businesses to respond effectively to consumer demands and regulatory changes.
In conclusion, the wood panel custom market offers immense opportunities for growth and innovation. By committing to strategic sourcing practices, international B2B buyers can position themselves at the forefront of the industry, ready to embrace future challenges and opportunities. It’s time to take action—evaluate your sourcing strategies today and unlock the potential for success in the global market.