Optimize Costs: The Ultimate Guide to Grip Manufacturer (2025)
Introduction: Navigating the Global Market for grip manufacturer
In today’s competitive landscape, sourcing high-quality grips from reliable manufacturers can be a significant challenge for B2B buyers across the globe. Whether you are in the construction, automotive, or sports equipment sectors, understanding the nuances of grip manufacturing is crucial for ensuring safety and performance in your products. This guide offers a comprehensive overview of the grip manufacturing market, covering various types of grips, their applications, and essential factors for supplier vetting.
International B2B buyers, especially those operating in Africa, South America, the Middle East, and Europe, will find actionable insights on navigating supplier landscapes, evaluating costs, and identifying the best materials for their specific needs. With a focus on transparency and informed decision-making, this guide empowers buyers to make strategic choices that enhance their product offerings while minimizing risks associated with sourcing.
From understanding the technical specifications of different grip materials to assessing the reliability of potential suppliers, this resource provides the necessary tools and knowledge to streamline your purchasing process. By addressing common pain points and offering practical solutions, we aim to facilitate better procurement strategies that cater to the diverse needs of the global market. Whether you are a seasoned buyer or new to the industry, this guide is designed to elevate your sourcing efforts and contribute to your business’s success.
Understanding grip manufacturer Types and Variations
Type Name | Key Distinguishing Features | Primary B2B Applications | Brief Pros & Cons for Buyers |
---|---|---|---|
Rubber Grip Manufacturers | Flexible, durable, excellent shock absorption | Sports equipment, tools | Pros: Cost-effective, good grip; Cons: Limited temperature resistance. |
Foam Grip Manufacturers | Lightweight, soft, comfortable to hold | Fitness equipment, bicycles | Pros: Comfortable for extended use; Cons: Less durable than rubber. |
Metal Grip Manufacturers | Sturdy, often used for high-load applications | Industrial tools, machinery | Pros: High durability, long lifespan; Cons: Can be heavy and less ergonomic. |
Plastic Grip Manufacturers | Versatile, can be molded into various shapes and sizes | Consumer electronics, toys | Pros: Lightweight, customizable; Cons: May not provide the best grip. |
Composite Grip Manufacturers | Combines materials for enhanced performance | High-performance sports gear | Pros: Optimized properties, lightweight; Cons: Higher cost compared to single-material grips. |
What are the Key Characteristics of Rubber Grip Manufacturers?
Rubber grip manufacturers specialize in creating grips from rubber compounds, which offer excellent flexibility and durability. These grips are particularly effective in absorbing shock, making them ideal for sports equipment and hand tools. When considering rubber grips, buyers should assess the specific rubber compound used, as variations can affect durability and performance. Additionally, they are often cost-effective, making them a popular choice for mass-produced items.
How Do Foam Grip Manufacturers Stand Out?
Foam grip manufacturers produce grips that are lightweight and soft, providing comfort for users. These grips are commonly used in fitness equipment and bicycles, where prolonged handling is necessary. Buyers should consider the density and thickness of the foam, as these factors influence comfort and durability. While foam grips are comfortable, they may not withstand wear and tear as effectively as rubber or metal options, making them suitable for less demanding applications.
What Makes Metal Grip Manufacturers a Preferred Choice?
Metal grip manufacturers focus on producing grips from robust metals, making them suitable for high-load applications such as industrial tools and machinery. These grips are characterized by their high durability and long lifespan, which is essential for equipment used in challenging environments. However, buyers should be mindful of the weight of metal grips, as they can be heavier and less ergonomic than other options. When selecting metal grips, it’s crucial to evaluate the type of metal used and its resistance to corrosion.
Why Choose Plastic Grip Manufacturers?
Plastic grip manufacturers offer versatility, as plastic can be molded into various shapes and sizes, catering to different ergonomic needs. These grips are commonly found in consumer electronics and toys, providing a lightweight option for users. Buyers should consider the type of plastic used, as some plastics may not provide the best grip or durability. While plastic grips can be cost-effective and customizable, they may lack the tactile feel of rubber or foam grips, which can impact user experience.
What are the Benefits of Composite Grip Manufacturers?
Composite grip manufacturers combine multiple materials to optimize grip performance, making them ideal for high-performance sports gear. These grips leverage the strengths of different materials, resulting in a lightweight and durable option. Buyers should evaluate the specific composite materials used, as the combination can significantly influence performance characteristics. While composite grips often come at a higher cost, their enhanced performance can justify the investment, particularly in competitive sports applications.
Related Video: Heat Pump Thermostat O, B, and C Terminal Variations Explained
Key Industrial Applications of grip manufacturer
Industry/Sector | Specific Application of grip manufacturer | Value/Benefit for the Business | Key Sourcing Considerations for this Application |
---|---|---|---|
Automotive | Steering Wheel Grips | Enhanced driver control and comfort | Material durability, ergonomic design, and safety standards |
Construction | Tool Handles and Safety Grips | Improved safety and efficiency in manual tasks | Grip texture, weather resistance, and compliance with safety regulations |
Medical Equipment | Surgical Instrument Grips | Precision handling and reduced fatigue for healthcare professionals | Sterilization compatibility, ergonomic features, and grip firmness |
Consumer Electronics | Mobile Device Cases with Grip Enhancements | Increased user satisfaction and product usability | Compatibility with device models, aesthetic appeal, and tactile feel |
Sports Equipment | Grip Enhancements for Sports Gear | Enhanced performance and user confidence | Weight considerations, material grip properties, and durability under stress |
How Are Grips Used in the Automotive Industry?
In the automotive sector, grip manufacturers produce steering wheel grips that enhance driver control and comfort. These grips are designed to provide a firm hold, reducing slippage during operation, which is crucial for safety. B2B buyers, particularly from regions like Europe and the Middle East, should consider factors such as material durability and ergonomic design to ensure that the grips meet stringent safety standards and consumer expectations.
What Role Do Grips Play in Construction?
In construction, grips are vital for tool handles and safety grips, which significantly improve safety and efficiency in manual tasks. A well-designed grip can prevent accidents by ensuring that tools are securely held, even in adverse weather conditions. International buyers from Africa and South America should prioritize sourcing grips that offer weather resistance and a textured surface for better handling, as well as compliance with local safety regulations.
Why Are Grips Important in Medical Equipment?
Grip manufacturers also cater to the medical equipment industry, where surgical instrument grips are essential for precision handling and reducing fatigue among healthcare professionals. These grips must be designed for sterilization compatibility and ergonomic comfort, ensuring that they can withstand rigorous cleaning processes while providing a secure hold. Buyers in this sector must emphasize grip firmness and ergonomic features to enhance surgical outcomes and practitioner comfort.
How Do Grips Enhance Consumer Electronics?
In the consumer electronics sector, grip manufacturers produce mobile device cases that feature grip enhancements. These grips not only improve usability but also increase user satisfaction by preventing accidental drops. B2B buyers should focus on sourcing cases that are compatible with various device models, while also considering the aesthetic appeal and tactile feel of the grips, as these factors influence consumer purchasing decisions.
What Benefits Do Grips Provide in Sports Equipment?
Finally, in the sports equipment industry, grips are crucial for enhancing performance and user confidence. Whether for rackets, bats, or other sporting goods, the right grip can significantly affect a player’s ability to perform. Buyers should consider weight, material grip properties, and durability under stress when sourcing these products, ensuring that they meet the demands of competitive sports while providing comfort and control.
Related Video: Types Of Flowmeters And Their Industrial Applications.
3 Common User Pain Points for ‘grip manufacturer’ & Their Solutions
Scenario 1: Understanding Material Specifications for Optimal Performance
The Problem: B2B buyers often struggle with selecting the right materials for grips, particularly when they are unfamiliar with the technical specifications. This can lead to choosing materials that either don’t provide the necessary durability or comfort, ultimately affecting the end-user experience. For instance, a construction firm sourcing grips for power tools may find that the rubber material is too soft, resulting in rapid wear and tear, while a sporting goods company might select a material that provides insufficient grip in wet conditions. This not only impacts product quality but can also lead to customer dissatisfaction and increased return rates.
The Solution: To overcome this challenge, buyers should conduct thorough research into the different materials available for grips, such as thermoplastic elastomers (TPE), polyvinyl chloride (PVC), or silicone. Engaging with grip manufacturers who provide detailed technical data sheets can be invaluable. These sheets typically include information on hardness, tensile strength, and weather resistance. Furthermore, consider requesting samples to test the grips in real-world conditions before finalizing an order. This hands-on approach allows you to evaluate how well the material performs under specific conditions, ensuring you make an informed choice that aligns with your product’s requirements.
Scenario 2: Navigating Customization Options for Diverse Applications
The Problem: Many B2B buyers are unaware of the extent of customization options available when sourcing grips from manufacturers. This can lead to a generic solution that does not meet the specific needs of their applications. For example, an automotive parts supplier may require grips that accommodate varying hand sizes for different models, but without realizing that custom ergonomic designs are possible, they may end up with a one-size-fits-all solution that fails to enhance user experience.
The Solution: Buyers should engage in open discussions with grip manufacturers about their specific application needs. It’s crucial to detail the user demographics and the intended use of the grips to explore customization options effectively. Manufacturers often offer tailored designs, colors, and textures that can significantly improve functionality and user satisfaction. Additionally, leveraging 3D modeling or prototype services can help visualize the grip design before production, allowing for adjustments based on feedback from potential users. This proactive approach can lead to a product that not only meets but exceeds user expectations, ultimately driving sales and customer loyalty.
Scenario 3: Overcoming Supply Chain Challenges in Grip Manufacturing
The Problem: International B2B buyers often face significant supply chain disruptions, particularly when dealing with manufacturers located overseas. Issues such as shipping delays, customs regulations, and fluctuating costs can lead to unpredictable lead times, impacting production schedules and the ability to meet market demands. For instance, a South American retailer sourcing grips from a European manufacturer may experience unexpected delays due to changes in trade policies, resulting in stock shortages and lost sales opportunities.
The Solution: To mitigate supply chain risks, B2B buyers should diversify their supplier base by exploring local manufacturers or those with established logistics networks in their region. Building relationships with multiple grip manufacturers can provide alternatives in case of disruptions. Additionally, utilizing technology for better supply chain visibility, such as inventory management systems and order tracking platforms, can enhance transparency and responsiveness. Establishing clear communication with suppliers regarding lead times and potential risks can also help manage expectations and prepare for contingencies. This strategic approach not only ensures a more reliable supply chain but also enhances the buyer’s ability to respond quickly to market changes.
Strategic Material Selection Guide for grip manufacturer
When selecting materials for grips, manufacturers must consider several factors that influence the performance, durability, and suitability of their products. Below, we analyze four common materials used in grip manufacturing, focusing on their properties, advantages, disadvantages, and specific considerations for international B2B buyers.
What Are the Key Properties of Rubber in Grip Manufacturing?
Rubber is one of the most widely used materials for grips due to its excellent elasticity and resilience. It can withstand a wide range of temperatures and offers good abrasion resistance. Rubber grips perform well under pressure and provide a non-slip surface, making them ideal for various applications, including tools and sporting equipment.
Pros and Cons: The primary advantage of rubber is its durability and comfort, as it provides a soft touch. However, it can degrade over time when exposed to UV light and certain chemicals, which may limit its lifespan in outdoor applications. Additionally, while rubber is generally cost-effective, the manufacturing process can be complex, especially if specialized formulations are required.
Impact on Application: Rubber grips are compatible with a variety of media, including oils and solvents, but caution should be exercised with strong acids and bases.
Considerations for International Buyers: Buyers from regions such as Africa and South America should ensure that the rubber meets local compliance standards, such as ASTM or ISO certifications, to guarantee quality and safety.
How Does Polypropylene Enhance Grip Performance?
Polypropylene (PP) is another popular choice for grip manufacturing, known for its lightweight and chemical resistance. It is often used in applications where moisture is a concern, as it does not absorb water, making it ideal for marine or outdoor products.
Pros and Cons: Polypropylene grips are easy to mold and can be produced in various colors and textures, enhancing aesthetic appeal. However, they may not provide the same level of grip as rubber, particularly in wet conditions. While the cost of polypropylene is generally low, its mechanical properties can be less robust compared to other materials.
Impact on Application: PP is suitable for applications where exposure to chemicals or moisture is prevalent, but it may not perform well in high-temperature environments.
Considerations for International Buyers: Buyers in Europe, particularly Germany, should be aware of the REACH regulations concerning chemical safety, ensuring that the polypropylene used is compliant with EU standards.
What Are the Benefits of Using Foam in Grip Manufacturing?
Foam materials, particularly EVA (ethylene-vinyl acetate) foam, are increasingly popular for grips due to their lightweight and cushioning properties. They provide excellent shock absorption, making them suitable for sports equipment and tools that require extended use.
Pros and Cons: The main advantage of foam grips is their comfort and ability to reduce fatigue during prolonged use. However, they can compress over time, leading to a loss of grip quality. The cost of foam can vary, but it is generally considered medium-range.
Impact on Application: Foam grips are ideal for applications where user comfort is paramount, but they may not be suitable for heavy-duty applications due to their lower durability compared to rubber or thermoplastics.
Considerations for International Buyers: Buyers from the Middle East should consider the heat resistance of foam materials, as extreme temperatures can affect performance.
Why Choose Thermoplastic Elastomers (TPE) for Grips?
Thermoplastic elastomers (TPE) combine the properties of rubber and plastic, offering flexibility, durability, and ease of processing. TPE grips can be engineered to meet specific performance requirements, making them versatile for various applications.
Pros and Cons: TPE grips provide excellent grip and comfort while being resistant to UV light and weathering, making them suitable for outdoor use. However, they can be more expensive than traditional rubber, and their manufacturing process may require specialized equipment.
Impact on Application: TPE is compatible with a wide range of chemicals and offers good temperature resistance, making it suitable for diverse applications.
Considerations for International Buyers: Buyers in South America should ensure that TPE materials comply with local and international standards, as well as verify the manufacturer’s certifications.
Summary Table of Material Selection for Grip Manufacturing
Material | Typical Use Case for grip manufacturer | Key Advantage | Key Disadvantage/Limitation | Relative Cost (Low/Med/High) |
---|---|---|---|---|
Rubber | Hand tools, sporting equipment | Excellent durability and comfort | Degrades under UV exposure | Medium |
Polypropylene | Marine applications, outdoor products | Lightweight and moisture-resistant | Lower grip performance in wet conditions | Low |
Foam (EVA) | Sports equipment, ergonomic tools | Shock absorption and comfort | Compresses over time | Medium |
Thermoplastic Elastomers (TPE) | Versatile applications, outdoor tools | Flexibility and weather resistance | Higher cost and manufacturing complexity | High |
This guide provides a comprehensive overview of material options for grip manufacturers, enabling international B2B buyers to make informed decisions tailored to their specific needs and regional compliance requirements.
In-depth Look: Manufacturing Processes and Quality Assurance for grip manufacturer
What Are the Main Stages of Manufacturing for Grip Manufacturers?
The manufacturing process for grips, commonly used in various industries such as automotive, sports, and consumer goods, typically involves several key stages: material preparation, forming, assembly, and finishing. Understanding these stages is crucial for international B2B buyers looking to source high-quality grips.
1. Material Preparation: What Materials Are Commonly Used for Grips?
The first step in the manufacturing process is material preparation. Grip manufacturers often use materials like rubber, silicone, thermoplastics, and foam. Each material has unique properties that influence the grip’s durability, texture, and performance.
- Rubber: Known for its elasticity and resistance to wear, rubber is a popular choice for grips that require high durability.
- Silicone: This material is favored for its temperature resistance and flexibility, making it ideal for grips that must withstand extreme conditions.
- Thermoplastics: These materials can be molded into complex shapes and are often used for injection-molded grips.
- Foam: Lightweight and comfortable, foam grips are commonly found in consumer products like sports equipment and handheld devices.
2. Forming: How Are Grips Shaped and Molded?
After material preparation, the next stage is forming, which shapes the materials into the desired grip design. Common techniques include:
- Injection Molding: This process involves injecting molten material into a mold. It’s efficient for producing large quantities of identical grips and allows for intricate designs.
- Compression Molding: Used for rubber and foam grips, this method compresses material into a mold under heat and pressure, ensuring uniformity and strength.
- Extrusion: This technique forces material through a die to create long shapes, which can then be cut to size for grips.
Each technique has its advantages, and the choice depends on factors such as production volume, design complexity, and material properties.
3. Assembly: What Assembly Techniques Are Used for Multi-Part Grips?
In cases where grips consist of multiple components, the assembly stage becomes critical. Common assembly techniques include:
- Adhesive Bonding: This method involves using adhesives to bond different grip materials together, ensuring a strong and durable final product.
- Mechanical Fastening: Screws, rivets, or other fasteners may be used to assemble multi-part grips, particularly in applications requiring easy disassembly or maintenance.
- Heat Sealing: This technique applies heat to join two surfaces, commonly used in foam or rubber grips.
4. Finishing: How Is the Final Product Prepared for Market?
The finishing stage enhances the grip’s aesthetics and performance. Processes include:
- Surface Treatment: Techniques like sanding, polishing, or coating can improve texture, grip, and appearance.
- Printing and Branding: Many manufacturers apply logos or branding through techniques like pad printing or screen printing, adding value and brand recognition.
- Quality Control Checks: Before products are packaged, they undergo final quality checks to ensure they meet specifications.
What Quality Assurance Measures Should B2B Buyers Consider?
Quality assurance (QA) is a critical aspect of the manufacturing process, ensuring that grips meet international standards and specific customer requirements. For B2B buyers, understanding these measures can significantly impact purchasing decisions.
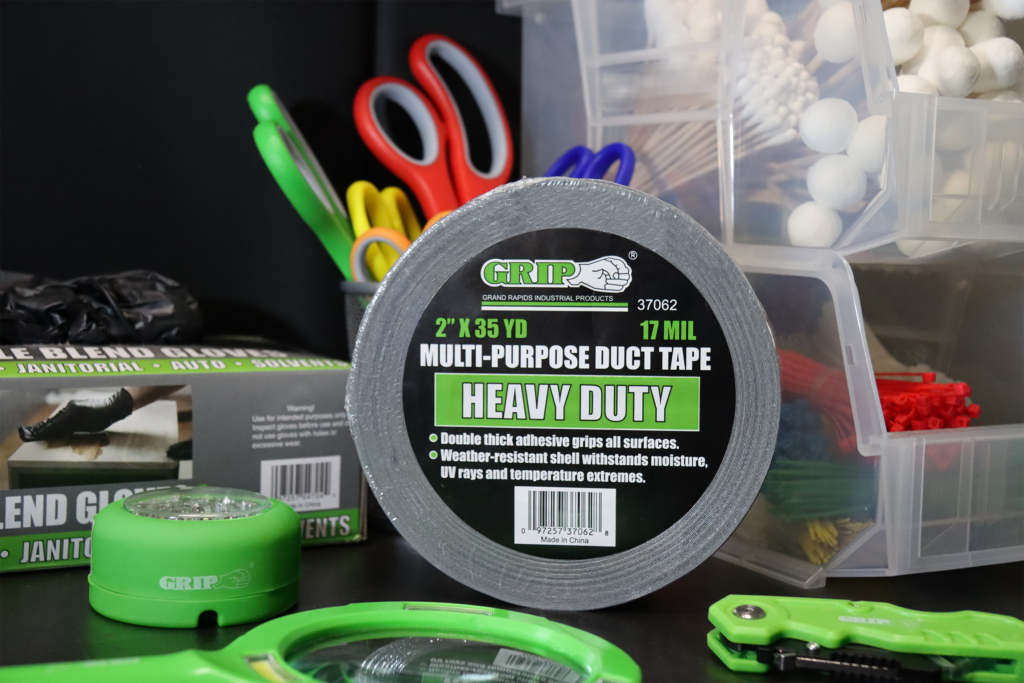
A stock image related to grip manufacturer.
1. What Are the Relevant International Standards for Grip Manufacturing?
International standards like ISO 9001 are vital for ensuring consistent quality management systems. Compliance with ISO 9001 indicates that a manufacturer has established processes for quality control, continuous improvement, and customer satisfaction.
In addition to ISO standards, industry-specific certifications such as CE marking (for European markets) and API certification (for oil and gas applications) may be relevant. These certifications assure buyers that products meet specific safety and performance criteria.
2. What Quality Control Checkpoints Are Common in Grip Manufacturing?
Quality control checkpoints throughout the manufacturing process ensure that products meet quality standards. Key checkpoints include:
- Incoming Quality Control (IQC): This step involves inspecting raw materials upon arrival to ensure they meet specifications.
- In-Process Quality Control (IPQC): During production, periodic checks are conducted to monitor quality and identify any deviations from standards.
- Final Quality Control (FQC): Before shipping, products undergo final inspections to ensure they meet all quality requirements and specifications.
3. What Testing Methods Are Used to Ensure Grip Quality?
Common testing methods for grips include:
- Durability Testing: Evaluates how well grips withstand wear and tear under normal usage conditions.
- Grip Strength Testing: Assesses the effectiveness of the grip in real-world applications, ensuring it provides adequate traction and comfort.
- Environmental Testing: Simulates various environmental conditions (temperature, humidity) to ensure product performance under different circumstances.
How Can B2B Buyers Verify Supplier Quality Control?
For international B2B buyers, verifying the quality control practices of potential suppliers is crucial for ensuring product reliability and performance.
1. What Steps Can Buyers Take to Audit Suppliers?
- Supplier Audits: Conducting on-site audits can provide insights into a manufacturer’s quality control processes and compliance with international standards.
- Requesting Quality Reports: Suppliers should provide documentation of their quality control processes, including inspection results and compliance certifications.
- Third-Party Inspections: Hiring third-party inspection agencies can offer impartial assessments of the manufacturer’s quality control practices.
2. What Nuances Should International Buyers Consider?
B2B buyers from different regions should be aware of specific nuances related to quality assurance:
- Regulatory Compliance: Different regions may have unique regulations regarding product safety and quality. Buyers should ensure that suppliers comply with the relevant local laws and standards.
- Cultural Differences: Understanding cultural attitudes toward quality and business practices can help in establishing effective communication and expectations with suppliers.
By thoroughly understanding the manufacturing processes and quality assurance measures, international B2B buyers can make informed decisions when sourcing grips, ensuring they select reliable suppliers that meet their quality and performance needs.
Practical Sourcing Guide: A Step-by-Step Checklist for ‘grip manufacturer’
Introduction
When sourcing grips for manufacturing, international B2B buyers must navigate various factors to ensure they select the right supplier. This checklist is designed to streamline the procurement process, helping you make informed decisions tailored to your specific needs. By following these steps, you can optimize your sourcing strategy and minimize potential risks.
Step 1: Define Your Technical Specifications
Clearly outlining your technical specifications is essential for effective sourcing. This includes understanding the materials, dimensions, and performance requirements of the grips you need. By providing detailed specifications, you enable suppliers to offer accurate quotes and avoid miscommunication.
- Consider factors such as:
- Material durability and weight.
- Grip texture and ergonomics for end-users.
- Compliance with industry standards and regulations.
Step 2: Conduct Market Research for Grip Manufacturers
Before approaching suppliers, conduct thorough market research to identify potential manufacturers. Look for companies that specialize in the production of grips relevant to your industry. This step helps you understand the competitive landscape and gauge the availability of quality suppliers.
- Use resources like:
- Industry reports and trade publications.
- Online marketplaces and supplier directories.
- Trade shows and industry events to meet potential partners.
Step 3: Evaluate Potential Suppliers Thoroughly
Before making any commitments, evaluate potential suppliers comprehensively. Request detailed company profiles, case studies, and references from clients in similar sectors. This evaluation is crucial to ensure the supplier can meet your quality and delivery expectations.
- Key considerations include:
- Supplier experience in manufacturing grips.
- Production capabilities and technology used.
- Customer reviews and testimonials.
Step 4: Verify Supplier Certifications and Compliance
It is vital to verify that your chosen suppliers hold relevant certifications and comply with international standards. Certifications such as ISO 9001 can indicate a commitment to quality management systems, while other certifications may demonstrate compliance with safety and environmental regulations.
- Look for:
- Evidence of quality control processes.
- Compliance with regional regulations, especially if sourcing from international suppliers.
Step 5: Request Samples and Conduct Testing
Once you’ve narrowed down your options, request samples of the grips you are interested in. Testing these samples will allow you to assess their quality, performance, and suitability for your specific application. This step is crucial to avoid costly mistakes later in the production process.
- Testing should include:
- Physical durability tests.
- Ergonomic assessments for user comfort.
- Performance evaluations under operational conditions.
Step 6: Negotiate Terms and Conditions
After selecting a supplier, engage in negotiations regarding pricing, lead times, payment terms, and delivery conditions. Clear communication during this phase can help establish a strong working relationship and ensure both parties are aligned.
- Focus on:
- Flexibility in order quantities.
- Transparency in pricing structures.
- Defined timelines for production and delivery.
Step 7: Establish a Communication Plan
Finally, create a robust communication plan with your supplier. Regular updates and open lines of communication can help address any issues promptly and keep the project on track. This proactive approach is vital for maintaining a smooth working relationship.
- Consider:
- Setting regular check-in meetings.
- Utilizing project management tools for transparency.
- Establishing a point of contact for immediate concerns.
By following this sourcing checklist, you can confidently navigate the complexities of procuring grips from manufacturers, ensuring you make well-informed decisions that align with your business objectives.
Comprehensive Cost and Pricing Analysis for grip manufacturer Sourcing
What Are the Key Cost Components in Grip Manufacturing?
When sourcing grips from manufacturers, understanding the breakdown of costs is essential for international B2B buyers. The primary cost components include:
-
Materials: The choice of raw materials significantly impacts the overall cost. For grips, materials such as rubber, foam, and plastics are commonly used. Higher-quality materials may lead to increased durability and performance, but will also raise costs.
-
Labor: Labor costs vary by region and skill level. In countries with lower labor costs, such as some regions in Africa and South America, you may find cheaper pricing. However, consider the trade-off in terms of quality and expertise.
-
Manufacturing Overhead: This encompasses all indirect costs associated with production, including utilities, rent, and equipment maintenance. Manufacturers with efficient overhead management often pass savings on to buyers.
-
Tooling: Initial tooling costs can be substantial, especially for custom designs. Understanding these costs upfront is crucial, particularly if you require specialized grips.
-
Quality Control (QC): Investing in quality control can prevent costly returns and ensure product consistency. A robust QC process may add to the initial cost but can lead to savings in the long run.
-
Logistics: Shipping and handling costs vary depending on the shipping method and distance. International buyers should factor in potential tariffs and import duties, especially when sourcing from Europe or Asia.
-
Margin: Manufacturers typically add a profit margin to their costs. This can vary widely, depending on the manufacturer’s pricing strategy and market competition.
How Do Price Influencers Impact Grip Manufacturing Costs?
Several factors influence the pricing of grips, making it essential to understand these variables when negotiating:
-
Volume and Minimum Order Quantity (MOQ): Larger orders typically lead to reduced costs per unit due to economies of scale. Discussing volume discounts with manufacturers can yield significant savings.
-
Specifications and Customization: Custom designs may incur additional costs for tooling and materials. Ensure you clearly communicate your requirements to avoid unexpected charges.
-
Materials: The selection of materials can greatly affect pricing. High-performance materials may increase costs but can enhance product longevity and user satisfaction.
-
Quality and Certifications: Grips that meet specific industry standards or certifications may carry a premium price. Verify whether these certifications are necessary for your market to avoid unnecessary costs.
-
Supplier Factors: Building a relationship with suppliers can lead to better pricing and flexibility. Consider engaging with suppliers who understand your regional market dynamics.
-
Incoterms: Understanding Incoterms (International Commercial Terms) is vital for clarifying responsibilities and costs associated with shipping and delivery. This can significantly impact the total cost of ownership.
What Are Effective Buyer Tips for Negotiating Grip Manufacturing Prices?
International B2B buyers should adopt strategic approaches to ensure cost-efficiency and favorable pricing:
-
Negotiate Wisely: Leverage your understanding of the cost components and price influencers during negotiations. Being well-informed can lead to better terms and pricing.
-
Consider Total Cost of Ownership (TCO): Evaluate not just the purchase price but also logistics, quality, and potential warranty costs. A lower upfront price may lead to higher long-term costs if quality is compromised.
-
Research Pricing Nuances: Familiarize yourself with regional pricing trends. For example, European manufacturers may have different pricing structures compared to those in Africa or South America due to labor and material costs.
-
Be Cautious with Indicative Prices: Always request detailed quotations rather than relying on indicative prices. Ensure that all components are included to avoid surprises later in the procurement process.
Conclusion
By understanding the cost structure and pricing dynamics in grip manufacturing, international B2B buyers can make informed sourcing decisions. Employing strategic negotiation techniques and considering the total cost of ownership will enhance your purchasing power and ensure you receive quality products at competitive prices.
Alternatives Analysis: Comparing grip manufacturer With Other Solutions
In the dynamic landscape of grip solutions, international B2B buyers often face the challenge of selecting the most suitable option for their needs. With numerous alternatives available, understanding how each solution compares to traditional grip manufacturers is essential. This analysis will delve into two viable alternatives, enabling informed decision-making for businesses across Africa, South America, the Middle East, and Europe.
Comparison Table of Grip Solutions
Comparison Aspect | Grip Manufacturer | Alternative 1: Adhesive Grips | Alternative 2: Ergonomic Handles |
---|---|---|---|
Performance | High durability and reliability in various environments. | Good for temporary applications, but may wear out quickly. | Provides excellent comfort and support for prolonged use. |
Cost | Moderate initial investment; often more economical long-term due to durability. | Low initial cost; may incur additional costs for replacements. | Higher upfront cost due to ergonomic design features. |
Ease of Implementation | Requires professional installation for optimal performance. | Easy to apply; no specialized skills needed. | Installation may require some skill but is generally straightforward. |
Maintenance | Low maintenance; occasional inspections recommended. | Requires frequent reapplication, especially in high-use areas. | Minimal maintenance; durable designs often resist wear. |
Best Use Case | Ideal for industrial applications needing high durability. | Suitable for temporary or less demanding applications. | Best for ergonomic needs in consumer products or tools. |
What Are the Advantages and Disadvantages of Adhesive Grips?
Adhesive grips offer a quick and cost-effective solution for temporary needs. They are particularly beneficial for short-term projects or prototypes where high durability is not a priority. However, their performance can diminish over time, especially in high-traffic areas, leading to increased replacement costs. Additionally, they may not provide the same level of grip or stability as traditional grip solutions.
How Do Ergonomic Handles Enhance User Experience?
Ergonomic handles focus on user comfort and efficiency, making them ideal for tools and consumer products where prolonged use is expected. These grips are designed to reduce strain and fatigue, enhancing overall user experience. While they tend to have a higher initial cost, the benefits of improved usability and potentially reduced health-related issues can outweigh the upfront investment. However, they may require careful installation and are less suited for high-durability applications compared to traditional grip manufacturers.
Conclusion: How to Choose the Right Grip Solution for Your Business?
When selecting a grip solution, B2B buyers should carefully assess their specific requirements and constraints. Factors such as performance needs, budget considerations, and the intended application will guide the choice between grip manufacturers and alternative solutions. For industries requiring long-lasting durability, traditional grip manufacturers remain the top choice. However, for projects with budget constraints or temporary needs, adhesive grips may suffice. Ergonomic handles, while more expensive, are ideal for enhancing user experience in consumer-focused applications. Ultimately, understanding these alternatives ensures that businesses can make informed decisions that align with their operational goals and customer satisfaction.
Essential Technical Properties and Trade Terminology for grip manufacturer
What Are the Key Technical Properties for Grip Manufacturers?
When sourcing grips, understanding the essential technical properties is crucial for ensuring product quality and performance. Here are several key specifications that international B2B buyers should consider:
-
Material Grade
– The type of material used in grip manufacturing significantly affects durability, flexibility, and comfort. Common materials include rubber, silicone, and thermoplastic elastomers (TPE). Each material has distinct properties, such as weather resistance or softness, which cater to specific applications. For instance, rubber grips are often preferred for their high friction and durability. -
Tolerance
– Tolerance refers to the permissible limits of variation in a physical dimension. It is vital in ensuring that grips fit properly on tools or equipment. For B2B buyers, understanding tolerance levels helps prevent issues such as misalignment or excessive wear, which can lead to product failure and increased costs. -
Surface Texture
– The texture of the grip can enhance user experience by providing better traction and control. Different surface finishes, such as smooth, textured, or patterned, can be tailored to meet specific ergonomic needs. Buyers should assess the end-user’s requirements to select the appropriate surface texture that enhances grip performance. -
Hardness (Durometer)
– Measured on a durometer scale, hardness indicates how firm or soft the grip material is. Softer materials (low durometer) often provide better shock absorption and comfort, while harder materials (high durometer) offer increased durability. Understanding hardness is essential for buyers to ensure that the grip meets the end-user’s ergonomic needs without compromising performance. -
Resistance Properties
– Grips may need to withstand various environmental factors, such as chemicals, UV exposure, or extreme temperatures. Resistance properties indicate how well a grip can endure these conditions without degrading. Buyers should consider the specific applications and environments in which the grips will be used to ensure longevity and reliability.
What Are Common Trade Terms in Grip Manufacturing?
Familiarity with industry jargon is essential for effective communication and negotiation in B2B transactions. Here are some common terms that buyers should know:
-
OEM (Original Equipment Manufacturer)
– This term refers to a company that produces parts or equipment that may be marketed by another manufacturer. Understanding OEM relationships is crucial for buyers looking for quality assurance and compatibility in their sourced grips. -
MOQ (Minimum Order Quantity)
– MOQ is the smallest number of units that a supplier is willing to sell. This term is important for buyers to understand their purchasing limits and to plan inventory accordingly. Negotiating MOQ can lead to cost savings and better inventory management. -
RFQ (Request for Quotation)
– An RFQ is a document sent to suppliers asking for a price quote on specific products. It typically includes details about the desired specifications, quantities, and delivery timelines. Buyers should prepare clear RFQs to ensure accurate and competitive pricing from manufacturers. -
Incoterms (International Commercial Terms)
– These are a series of pre-defined commercial terms published by the International Chamber of Commerce (ICC) relating to international commercial law. Understanding Incoterms is vital for buyers to clarify responsibilities regarding shipping, insurance, and tariffs, ultimately impacting the total landed cost of the goods. -
Lead Time
– Lead time refers to the amount of time it takes from placing an order to receiving the goods. This is crucial for buyers to manage their supply chain effectively and ensure that production schedules are met without delays.
By understanding these technical properties and trade terms, international B2B buyers can make informed decisions, ensuring they source high-quality grips that meet their specific needs while navigating the complexities of global trade.
Navigating Market Dynamics and Sourcing Trends in the grip manufacturer Sector
What are the Key Market Dynamics and Trends Affecting the Grip Manufacturer Sector?
The grip manufacturer sector is experiencing robust growth, driven by various global factors. The increasing demand for ergonomic tools and equipment across industries such as automotive, construction, and sports is a significant driver. Enhanced consumer awareness regarding safety and efficiency is pushing manufacturers to innovate, integrating smart technologies such as IoT and AI into their products. For international B2B buyers, particularly those from Africa, South America, the Middle East, and Europe, understanding these trends is crucial for sourcing decisions.
Emerging sourcing trends reflect a shift towards digital platforms that facilitate better supplier-buyer relationships. Platforms that offer real-time data analytics and supply chain visibility are gaining traction. This allows buyers to make informed decisions based on comprehensive insights into supplier performance, cost management, and inventory levels. Notably, European buyers are increasingly favoring suppliers that can demonstrate technological advancements and quick adaptability to market changes.
Additionally, sustainability is becoming a cornerstone of sourcing decisions. Buyers are now prioritizing suppliers that adhere to eco-friendly practices and utilize sustainable materials. This trend is evident in regions like Europe, where stringent regulations are fostering a more conscious approach to manufacturing.
How is Sustainability Shaping the Grip Manufacturer Sector?
Sustainability is no longer just a buzzword; it is a fundamental aspect of modern manufacturing, including the grip manufacturer sector. The environmental impact of production processes has led to increased scrutiny from consumers and regulatory bodies alike. B2B buyers are now looking for manufacturers who not only comply with environmental regulations but actively seek to minimize their carbon footprint.
Ethical sourcing is also gaining importance, with buyers favoring suppliers who maintain transparent supply chains and prioritize fair labor practices. This approach not only enhances brand reputation but also fosters loyalty among environmentally-conscious consumers. Certifications such as ISO 14001 (Environmental Management) and Fair Trade are becoming essential credentials that buyers seek in their suppliers.
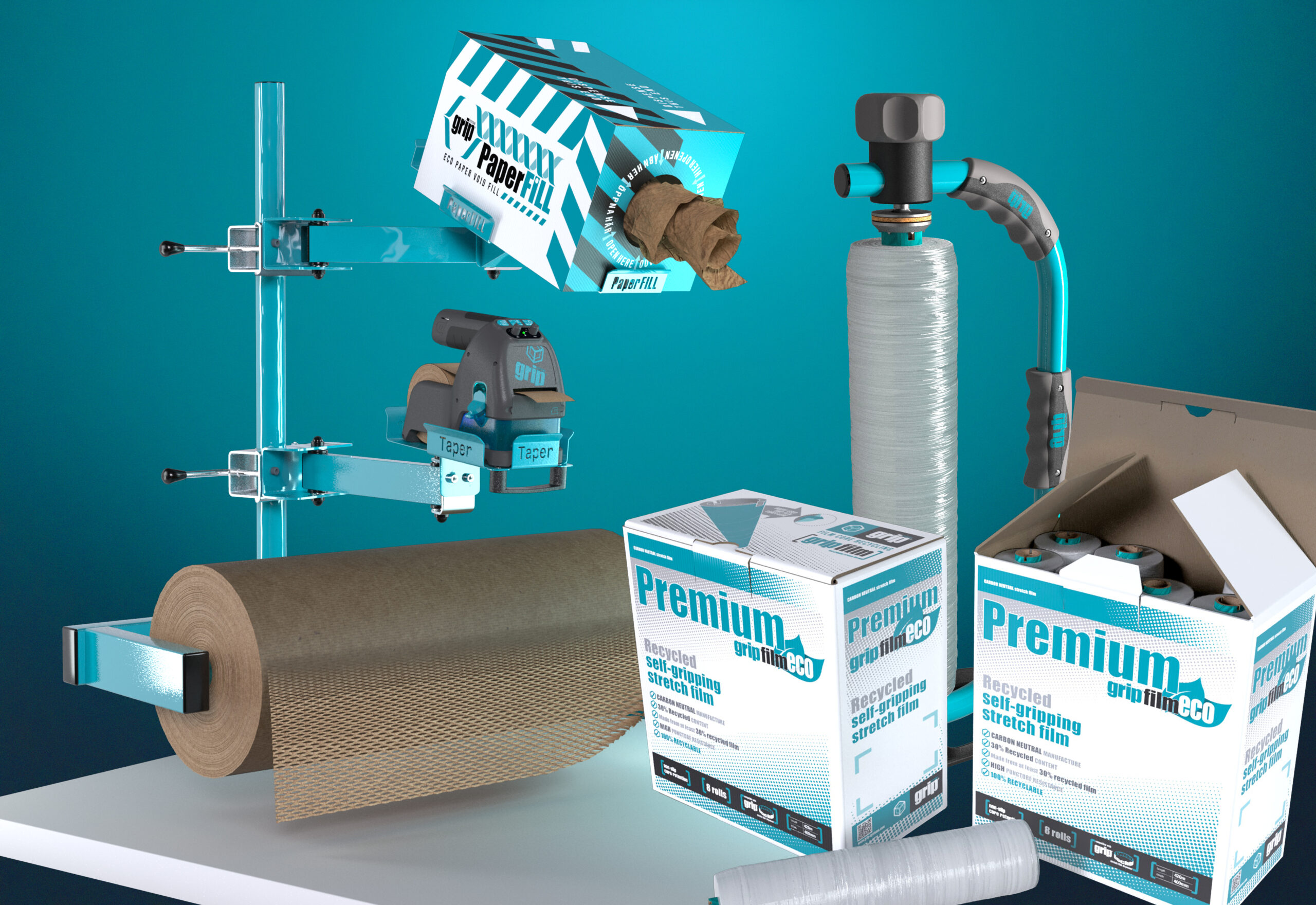
A stock image related to grip manufacturer.
To align with these trends, grip manufacturers are investing in ‘green’ materials, such as biodegradable plastics and recycled composites, which appeal to eco-conscious buyers. Furthermore, the adoption of circular economy principles, focusing on reducing waste and promoting reuse, is reshaping sourcing strategies. International buyers are encouraged to conduct thorough due diligence on suppliers’ sustainability practices to ensure alignment with their own corporate social responsibility goals.
What is the Evolution of the Grip Manufacturer Sector?
The grip manufacturer sector has evolved significantly over the past few decades. Initially dominated by traditional manufacturing processes, the industry has embraced technological advancements, leading to enhanced production efficiency and product quality. The advent of automation and precision engineering has allowed manufacturers to produce grips that meet specific user requirements, enhancing functionality and comfort.
Historically, grip manufacturing focused primarily on materials such as rubber and plastic. However, as industries have evolved, so too have the materials and technologies used in grip production. The integration of advanced materials, such as thermoplastic elastomers and composites, reflects a growing demand for durability and performance.
This evolution not only caters to the needs of diverse industries but also aligns with the increasing demand for customization and personalized solutions in the B2B landscape. Understanding this history is vital for international buyers, as it provides insight into the capabilities and innovations that modern grip manufacturers can offer. By leveraging this knowledge, buyers can make more informed sourcing decisions that align with their operational needs and market demands.
Frequently Asked Questions (FAQs) for B2B Buyers of grip manufacturer
-
How do I evaluate the quality of grips from a manufacturer?
To assess the quality of grips from a manufacturer, begin with samples. Request a variety of grips to analyze the materials, durability, and finish. Check for certifications that indicate compliance with industry standards. Customer reviews and case studies can provide insights into the manufacturer’s reliability and product performance. Additionally, inquire about their quality assurance processes, including testing methods and defect rates. Establishing a direct line of communication with the manufacturer can also clarify their commitment to quality. -
What are the most important factors when choosing a grip manufacturer?
When selecting a grip manufacturer, consider their experience in the industry, production capacity, and technical expertise. Evaluate their ability to customize products based on your specific requirements, including material selection and design features. Assess their communication efficiency and responsiveness, as these factors can significantly affect your business relationship. Lastly, look for a manufacturer that has established logistics and supply chain capabilities to ensure timely delivery and consistent quality. -
How can I ensure my grip specifications are met during production?
To ensure your grip specifications are met, start with a detailed design brief that outlines all technical specifications, materials, and performance criteria. Collaborate closely with the manufacturer during the prototype phase to refine the design. Implement a regular review process throughout production, including on-site visits if possible, to monitor progress and address issues promptly. Establish clear communication channels and set milestones to ensure both parties are aligned at every stage of the production process. -
What is the minimum order quantity (MOQ) for grips from manufacturers?
The minimum order quantity (MOQ) for grips can vary significantly between manufacturers, often influenced by the type of grip and production methods. Generally, MOQs can range from 100 to several thousand units. When negotiating with a manufacturer, express your needs and inquire about their flexibility regarding MOQs, particularly for first-time orders or custom designs. Some manufacturers may offer lower MOQs for certain products or during promotional periods, so it’s worth exploring these options. -
What payment terms should I expect from a grip manufacturer?
Payment terms vary among grip manufacturers, but typical arrangements include a deposit upfront (usually 30-50%) followed by the balance upon delivery or before shipment. Some manufacturers may offer credit terms for established buyers. It’s essential to clarify payment options during negotiations, including any potential discounts for early payments or bulk orders. Additionally, consider using secure payment methods or escrow services to protect your investment, especially when dealing with new suppliers. -
How do I navigate logistics and shipping when sourcing grips internationally?
Navigating logistics and shipping for international sourcing requires a clear understanding of incoterms, which define the responsibilities of buyers and sellers in the shipping process. Discuss shipping options with your manufacturer, including freight costs, delivery timelines, and customs clearance processes. Partnering with a reliable freight forwarder can simplify logistics, providing expertise in handling international shipments and ensuring compliance with local regulations. Keep track of shipping schedules and maintain communication with your manufacturer to anticipate any potential delays. -
What quality assurance practices should a reputable grip manufacturer follow?
A reputable grip manufacturer should implement comprehensive quality assurance practices, including regular inspections at various production stages, from raw material sourcing to final product testing. They should adhere to industry standards and certifications relevant to grip manufacturing, such as ISO certifications. Additionally, they should maintain transparent documentation of quality control processes and testing results. Engaging in third-party quality audits can further validate their commitment to delivering high-quality products. -
How can I customize grips to meet my specific needs?
To customize grips effectively, begin by identifying your specific requirements, such as material, texture, shape, and size. Discuss these needs with your manufacturer to explore available options. Many manufacturers offer design services and can assist in creating prototypes based on your specifications. Be clear about your desired outcomes and any performance metrics that must be met. Regular feedback during the prototyping phase will ensure the final product aligns with your expectations and market needs.
Important Disclaimer & Terms of Use
⚠️ Important Disclaimer
The information provided in this guide, including content regarding manufacturers, technical specifications, and market analysis, is for informational and educational purposes only. It does not constitute professional procurement advice, financial advice, or legal advice.
While we have made every effort to ensure the accuracy and timeliness of the information, we are not responsible for any errors, omissions, or outdated information. Market conditions, company details, and technical standards are subject to change.
B2B buyers must conduct their own independent and thorough due diligence before making any purchasing decisions. This includes contacting suppliers directly, verifying certifications, requesting samples, and seeking professional consultation. The risk of relying on any information in this guide is borne solely by the reader.
Strategic Sourcing Conclusion and Outlook for grip manufacturer
What Are the Key Takeaways for International B2B Buyers in Grip Manufacturing?
In conclusion, the strategic sourcing of grips is vital for international B2B buyers, particularly those operating in Africa, South America, the Middle East, and Europe. Key insights include the importance of evaluating suppliers not just on price but on factors such as quality, compliance with international standards, and sustainability practices. Establishing strong relationships with manufacturers can lead to better negotiation power and more favorable terms, ultimately enhancing supply chain efficiency.
How Does Strategic Sourcing Enhance Competitive Advantage?
Strategic sourcing enables companies to optimize procurement processes, reduce costs, and improve product quality. By focusing on long-term partnerships rather than transactional relationships, businesses can ensure a steady supply of high-quality grips that meet their specific needs. This approach not only mitigates risks associated with supply chain disruptions but also fosters innovation through collaboration with manufacturers.
What Should Buyers Do Next?
As you consider your grip sourcing strategies, take proactive steps to engage with potential suppliers, conduct thorough market research, and participate in industry events. This will not only help you identify the best partners but also keep you informed of emerging trends and technologies in the grip manufacturing sector. Embrace the opportunity to enhance your procurement strategies and drive your business forward by making informed sourcing decisions today.