Optimize Your Purchase: Choosing a Sound System Manufacturer (2025)
Introduction: Navigating the Global Market for sound system manufacturer
In the rapidly evolving landscape of audio technology, international B2B buyers face the critical challenge of sourcing high-quality sound systems that meet diverse needs across various industries. Whether you are looking for commercial sound systems for large venues in the UAE or high-fidelity audio solutions for corporate environments in Europe, understanding the global market for sound system manufacturers is essential. This guide serves as a comprehensive resource, covering an array of topics including the types of sound systems available, their applications in different sectors, supplier vetting processes, and cost considerations.
By delving into this guide, B2B buyers from Africa, South America, the Middle East, and Europe will gain actionable insights that empower informed purchasing decisions. You’ll learn how to navigate the complexities of the market, identify reputable suppliers, and evaluate products based on your specific requirements. Furthermore, this guide aims to equip you with the knowledge necessary to negotiate effectively and ensure that your investment aligns with your business goals and customer expectations.
As the demand for superior audio experiences continues to rise, being well-informed about the options available can give your business a competitive edge. Embrace the opportunity to enhance your audio offerings and foster lasting relationships with sound system manufacturers worldwide.
Understanding sound system manufacturer Types and Variations
Type Name | Key Distinguishing Features | Primary B2B Applications | Brief Pros & Cons for Buyers |
---|---|---|---|
Professional Audio Systems | High power output, multi-channel capabilities | Concerts, events, large venues | Pros: Superior sound quality, robust build. Cons: Higher cost, complex setup. |
Commercial Sound Systems | Designed for public address and background music | Retail, hospitality, corporate events | Pros: Versatile, easy to install. Cons: May lack high fidelity for music-focused environments. |
Home Theater Systems | Integrated systems for immersive audio-visual experience | Residential entertainment, small venues | Pros: Great sound quality, user-friendly. Cons: Limited scalability for larger events. |
Portable PA Systems | Lightweight, battery-operated, and easy to transport | Outdoor events, small gatherings | Pros: Mobility, ease of use. Cons: Limited sound projection compared to larger systems. |
Custom Sound Solutions | Tailored systems designed for specific environments | Houses of worship, corporate offices | Pros: Optimized for unique spaces, high adaptability. Cons: Longer lead times, potential higher costs. |
What are the Characteristics of Professional Audio Systems?
Professional audio systems are characterized by their high power output and multi-channel capabilities, making them ideal for concerts and large events. These systems often include high-quality microphones, mixers, and speakers designed to deliver superior sound quality. For B2B buyers, the investment in professional audio systems is justified by their ability to handle demanding audio environments and deliver consistent performance, although they come with a higher price tag and require skilled personnel for setup.
How Do Commercial Sound Systems Function in Business Settings?
Commercial sound systems are designed for public address and background music, making them versatile for various business applications, including retail and hospitality environments. They typically feature easy installation and user-friendly operation, allowing businesses to create an inviting atmosphere for customers. While these systems are generally cost-effective and adaptable, they may not provide the high fidelity needed for music-centric settings, which is a consideration for buyers focused on audio quality.
What Makes Home Theater Systems Suitable for Smaller Venues?
Home theater systems offer an integrated audio-visual experience, making them popular for residential entertainment and small venues. These systems are designed to provide excellent sound quality while being user-friendly, often featuring simple remote controls and wireless connectivity. B2B buyers should consider these systems for smaller events or residential applications, though they may not scale well for larger gatherings, which limits their versatility.
Why Choose Portable PA Systems for Events?
Portable PA systems are lightweight and often battery-operated, making them easy to transport for outdoor events and small gatherings. Their design prioritizes mobility and ease of use, allowing businesses to set up audio quickly and efficiently. However, while they are convenient, buyers should be aware that portable systems may have limitations in sound projection compared to larger, more powerful setups, which could affect performance in larger spaces.
How Do Custom Sound Solutions Benefit Unique Environments?
Custom sound solutions are tailored to meet the specific needs of unique environments, such as houses of worship or corporate offices. These systems are optimized for the acoustics of their designated spaces, providing superior audio performance and adaptability. However, B2B buyers should consider the longer lead times and potentially higher costs associated with these solutions, as well as the need for professional consultation to ensure the system meets their specific requirements.
Related Video: The Genius Behind Bach’s Goldberg Variations: CANONS
Key Industrial Applications of sound system manufacturer
Industry/Sector | Specific Application of sound system manufacturer | Value/Benefit for the Business | Key Sourcing Considerations for this Application |
---|---|---|---|
Entertainment | Live Event Sound Systems | Enhances audience experience through high-quality audio, crucial for concerts and festivals. | Compatibility with existing equipment, scalability, and reliability under demanding conditions. |
Corporate | Conference Room Audio Solutions | Facilitates effective communication and collaboration in meetings, improving productivity. | Integration with video conferencing tools, ease of use, and support for multiple audio sources. |
Hospitality | Background Music Systems for Hotels and Restaurants | Creates an inviting atmosphere, boosting customer satisfaction and retention. | Sound quality, system flexibility, and ability to customize playlists for different times of day. |
Education | Classroom Audio Systems | Ensures clear audio delivery for lectures, enhancing learning outcomes for students. | Durability, ease of installation, and compatibility with various teaching aids and technologies. |
Retail | In-Store Sound Systems | Engages customers with music and announcements, driving sales and enhancing the shopping experience. | Sound coverage, system size, and ability to integrate with retail management systems. |
How Are Sound Systems Used in the Entertainment Industry?
In the entertainment sector, sound system manufacturers provide live event sound solutions that are integral for concerts, festivals, and performances. These systems are designed to deliver high-quality audio that enhances the audience’s experience. Key considerations for international buyers include the compatibility of sound systems with existing equipment and their ability to scale for different event sizes, particularly in vibrant markets across Africa and South America, where live events are gaining popularity.
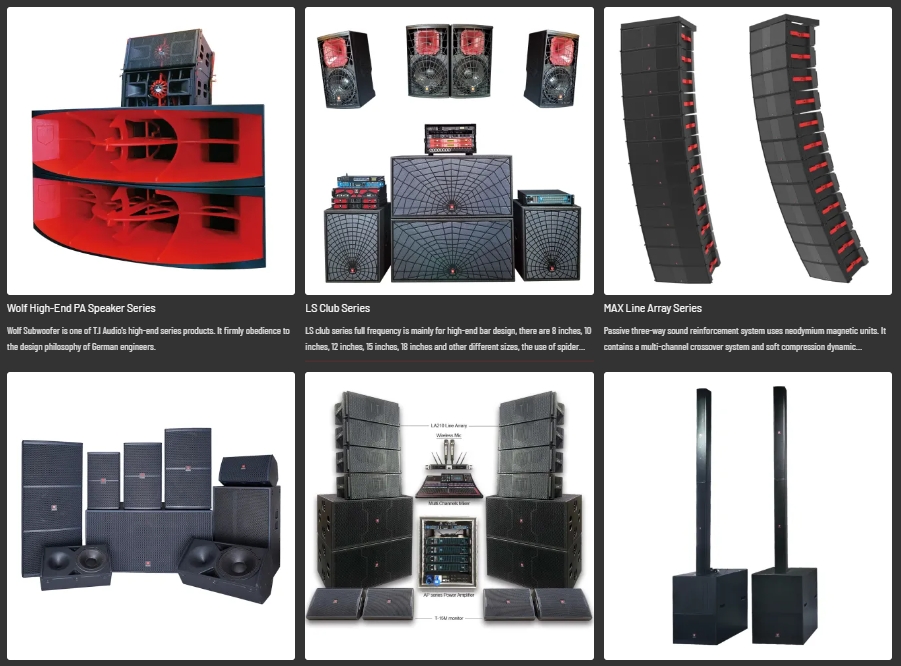
A stock image related to sound system manufacturer.
What Are the Benefits of Audio Solutions in Corporate Settings?
In corporate environments, sound systems are vital for conference rooms, facilitating clear communication during meetings. High-quality audio systems can significantly improve productivity by ensuring all participants can hear and be heard, regardless of the room size. Buyers from the Middle East and Europe should prioritize systems that integrate seamlessly with video conferencing tools, offer user-friendly interfaces, and support multiple audio sources to cater to diverse corporate needs.
How Do Sound Systems Enhance the Hospitality Experience?
In the hospitality industry, sound systems are essential for creating a pleasant ambiance in hotels and restaurants. Background music systems not only enhance the atmosphere but also contribute to customer satisfaction and retention. For B2B buyers, especially in Europe and the UAE, sourcing systems that provide excellent sound quality, flexibility for playlist customization, and durability to withstand various environments is crucial.
Why Are Audio Solutions Important in Educational Institutions?
Educational institutions benefit from classroom audio systems that ensure clear audio delivery during lectures. These systems enhance learning outcomes by making it easier for students to engage with the material presented. Buyers in Africa and South America should focus on durability and ease of installation, as well as compatibility with various teaching aids, to ensure a smooth learning environment.
How Do Retail Sound Systems Impact Customer Experience?
In retail settings, sound systems play a critical role in engaging customers through music and announcements, which can drive sales and enhance the shopping experience. International buyers should consider sound coverage, system size, and the ability to integrate with retail management systems when selecting audio solutions. This is particularly important in diverse markets where customer engagement strategies vary significantly.
Related Video: FANUC Industrial Robots | AUDI Case Study
3 Common User Pain Points for ‘sound system manufacturer’ & Their Solutions
Scenario 1: Inconsistent Sound Quality Across Events
The Problem: For B2B buyers in the event management or hospitality sectors, ensuring consistent sound quality across different venues can be a significant challenge. Factors such as varying acoustics, equipment compatibility, and environmental noise can lead to disappointing audio experiences. This inconsistency can tarnish brand reputation and affect customer satisfaction, making it crucial for buyers to source reliable sound systems that adapt to diverse settings.
The Solution: To tackle this issue, buyers should invest in sound systems that offer advanced adaptive sound technology. When selecting a sound system manufacturer, prioritize those that provide comprehensive consultation services and customized solutions based on venue specifications. Conduct thorough site assessments before purchasing equipment. This approach ensures the selected systems can be calibrated to the venue’s unique acoustics. Additionally, consider manufacturers that offer modular systems, which allow for easy adjustments and upgrades as needed. Implementing a robust training program for staff on how to operate and fine-tune the sound system can also enhance audio consistency across events.
Scenario 2: Complex Integration with Existing Equipment
The Problem: Many B2B buyers face difficulties integrating new sound systems with their existing audiovisual setups. This issue often arises in educational institutions, corporate environments, or entertainment venues where legacy systems are in place. Compatibility issues can lead to significant downtime, disrupt events, and require unexpected expenses for additional adapters or converters.
The Solution: To ensure seamless integration, buyers should look for sound system manufacturers that prioritize compatibility and provide comprehensive technical support. Before making a purchase, buyers should engage in detailed discussions with manufacturers about existing systems and specific requirements. Request demonstrations to see how new systems can interface with older equipment. Manufacturers that offer custom integration services can simplify this process, ensuring that all components work together smoothly. Consider investing in systems that support common protocols, such as Dante or AVB, which facilitate better connectivity and reduce integration headaches.
Scenario 3: Limited Support and Training for System Usage
The Problem: After investing in high-quality sound systems, B2B buyers often encounter issues due to insufficient training and support for their teams. This lack of knowledge can lead to improper usage, suboptimal sound quality, and increased maintenance costs. Buyers from sectors such as corporate, education, or live events may find themselves struggling to leverage their sound systems effectively, ultimately impacting their overall productivity and service quality.
The Solution: To overcome this challenge, buyers should prioritize manufacturers that offer extensive training programs and ongoing support services. When negotiating contracts, inquire about included training sessions for staff and technicians, ensuring they are well-equipped to operate and troubleshoot the equipment. Consider manufacturers that provide online resources, such as tutorials and user forums, to assist users beyond initial training. Additionally, establishing a relationship with the manufacturer for regular maintenance checks can help identify potential issues early and ensure systems perform at their best. Investing in sound systems with user-friendly interfaces and remote monitoring capabilities can further simplify operation and maintenance, ultimately enhancing overall user experience.
Strategic Material Selection Guide for sound system manufacturer
When selecting materials for sound system manufacturing, it’s essential to consider their properties, advantages, disadvantages, and the specific needs of international B2B buyers. Below is an analysis of four common materials used in sound system manufacturing, focusing on their relevance to product performance, manufacturing complexity, and market considerations for buyers from Africa, South America, the Middle East, and Europe.
What Are the Key Properties of Wood in Sound System Manufacturing?

A stock image related to sound system manufacturer.
Wood is a traditional material often used in speaker cabinets and enclosures. Its acoustic properties are highly valued, as it can enhance sound quality by providing a warm, rich tone.
- Key Properties: Wood has excellent sound absorption qualities and can be treated for moisture resistance, which is crucial for maintaining sound integrity in varying climates.
- Pros & Cons: While wood is aesthetically pleasing and offers good acoustic performance, it can be susceptible to warping and requires careful handling during manufacturing. The cost can vary significantly based on the type of wood used.
- Impact on Application: Wood is particularly suitable for high-end audio systems where sound quality is paramount. However, it may not be the best choice for portable systems due to weight considerations.
- Considerations for International Buyers: Buyers should ensure compliance with local environmental regulations regarding wood sourcing. Standards such as FSC certification may be important in regions like Europe.
How Does Plastic Compare as a Material for Sound Systems?
Plastic is increasingly used in sound system components, especially for casings and connectors, due to its versatility and cost-effectiveness.
- Key Properties: Plastics are lightweight, corrosion-resistant, and can be molded into complex shapes. They can also be treated to enhance UV resistance.
- Pros & Cons: The main advantage of plastic is its low cost and ease of manufacturing. However, it may not provide the same acoustic performance as wood or metal, leading to potential compromises in sound quality.
- Impact on Application: Plastic is ideal for budget-friendly sound systems and portable devices, where weight and cost are critical factors.
- Considerations for International Buyers: Compliance with safety standards such as RoHS (Restriction of Hazardous Substances) is essential, particularly in Europe and the Middle East.
What Are the Benefits of Using Metal in Sound System Components?
Metals, particularly aluminum and steel, are often used in sound system manufacturing for structural components and heat sinks.
- Key Properties: Metals offer high durability, excellent thermal conductivity, and resistance to corrosion, especially when treated with protective coatings.
- Pros & Cons: While metals provide robustness and longevity, they can be heavier and more expensive than other materials. Manufacturing processes for metal components can also be more complex.
- Impact on Application: Metal is suitable for professional audio equipment that requires durability and reliability under demanding conditions.
- Considerations for International Buyers: Buyers should consider the compatibility of metal components with local regulations, such as those governing electromagnetic interference (EMI) in the Middle East and Europe.
Why Is Composite Material Gaining Popularity in Sound Systems?
Composite materials, often a combination of wood, plastics, and metals, are becoming popular in sound system manufacturing due to their tailored properties.
- Key Properties: Composites can be engineered for specific acoustic properties, weight, and durability, making them versatile for various applications.
- Pros & Cons: The primary advantage is the ability to optimize performance characteristics while minimizing weight. However, they can be more expensive and complex to manufacture.
- Impact on Application: Composites are ideal for high-performance audio systems where both sound quality and durability are critical.
- Considerations for International Buyers: Buyers should be aware of the specific manufacturing standards and certifications required for composites in their regions, such as ASTM standards in the USA and DIN standards in Europe.
Summary Table of Material Selection for Sound System Manufacturing
Material | Typical Use Case for Sound System Manufacturer | Key Advantage | Key Disadvantage/Limitation | Relative Cost (Low/Med/High) |
---|---|---|---|---|
Wood | Speaker cabinets and enclosures | Excellent acoustic properties | Susceptible to warping | Medium |
Plastic | Casings and connectors | Lightweight and cost-effective | May compromise sound quality | Low |
Metal | Structural components and heat sinks | High durability and thermal conductivity | Heavier and more expensive | High |
Composite | High-performance audio systems | Optimized performance characteristics | More complex to manufacture | High |
This guide provides a comprehensive overview of the materials relevant to sound system manufacturing, offering actionable insights for international B2B buyers to make informed decisions based on their specific needs and regional considerations.
In-depth Look: Manufacturing Processes and Quality Assurance for sound system manufacturer
What Are the Main Stages in the Manufacturing Process of Sound Systems?
The manufacturing process for sound systems is a complex sequence of stages that ensures the delivery of high-quality audio products. Here are the primary stages involved:
-
Material Preparation: This initial stage involves sourcing raw materials such as metals, plastics, and electronic components. Suppliers are often evaluated based on quality certifications and reliability. For B2B buyers, it’s crucial to understand the material sourcing practices of manufacturers, especially regarding sustainability and compliance with international standards.
-
Forming: In this stage, raw materials are shaped into components. Techniques such as injection molding, die-casting, and CNC machining are commonly used. The choice of method can affect both the cost and quality of the final product. Buyers should inquire about the forming techniques used and their implications on durability and acoustic performance.
-
Assembly: This phase involves the integration of various components into a cohesive unit. Automated assembly lines are often employed to enhance efficiency, but skilled labor is also essential for complex tasks, especially in high-end sound systems. B2B buyers should assess the assembly process for flexibility and the ability to accommodate customizations.
-
Finishing: The final manufacturing stage includes surface treatment, painting, and the application of branding. This is crucial for aesthetic appeal and product differentiation in competitive markets. Buyers should consider how the finishing processes align with their branding needs and whether they can influence design choices.
How Is Quality Assurance Implemented in Sound System Manufacturing?
Quality assurance (QA) is critical in the sound system manufacturing process to ensure that products meet industry standards and customer expectations. Here’s how QA is typically structured:
-
International Standards and Certifications: Many manufacturers adhere to ISO 9001, which sets criteria for quality management systems. This certification demonstrates a commitment to quality and continuous improvement. Additionally, industry-specific certifications such as CE (Conformité Européenne) for European markets and API (American Petroleum Institute) for certain components are vital. B2B buyers should verify these certifications as part of supplier assessments.
-
Quality Control Checkpoints: The manufacturing process includes several quality control (QC) checkpoints:
– Incoming Quality Control (IQC): This involves inspecting raw materials and components upon receipt to ensure they meet specified standards.
– In-Process Quality Control (IPQC): Throughout the manufacturing process, various tests are conducted to catch defects early. This includes monitoring assembly processes and conducting functional tests.
– Final Quality Control (FQC): Before products leave the factory, a comprehensive inspection is conducted to ensure they meet all quality standards. This often includes acoustic testing, durability assessments, and aesthetic evaluations. -
Common Testing Methods: Various testing methods are employed to verify product performance, including:
– Acoustic Testing: Measuring frequency response, distortion levels, and sound pressure levels to ensure optimal audio quality.
– Durability Testing: Subjecting products to stress tests to evaluate their lifespan under typical usage conditions.
– Electrical Testing: Ensuring that electronic components function correctly and safely.
How Can B2B Buyers Verify Supplier Quality Control?
For international B2B buyers, particularly those from Africa, South America, the Middle East, and Europe, verifying a supplier’s quality control practices is essential. Here are some actionable steps:
-
Conduct Supplier Audits: Regular audits of suppliers can provide insights into their manufacturing processes and quality control measures. Buyers should establish a framework for conducting these audits, focusing on compliance with international standards and internal quality policies.
-
Request Quality Reports: Suppliers should be able to provide detailed quality reports, including results from IQC, IPQC, and FQC stages. These reports should outline testing procedures, outcomes, and any corrective actions taken.
-
Third-Party Inspections: Engaging third-party inspection agencies can enhance the credibility of quality assessments. These agencies can conduct independent evaluations of the manufacturing process and final products, providing unbiased insights into quality compliance.
What Are the Quality Control Nuances for International Buyers?
B2B buyers must navigate various quality control nuances when sourcing sound systems internationally:
-
Understanding Regional Standards: Different regions may have specific quality standards that manufacturers must comply with. For instance, products sold in Europe must meet CE marking requirements, while products in the UAE may need to adhere to ESMA regulations. Buyers should ensure that suppliers are familiar with these standards.
-
Cultural Considerations: Communication and expectations regarding quality can vary significantly across cultures. Buyers should be aware of these differences and engage in clear, open dialogue with suppliers to set mutual quality expectations.
-
Supply Chain Transparency: Buyers should seek suppliers who prioritize transparency in their supply chains. This includes disclosing sourcing practices, manufacturing processes, and any potential quality issues. Enhanced transparency fosters trust and ensures that buyers can make informed decisions.
Conclusion
In summary, understanding the manufacturing processes and quality assurance practices of sound system manufacturers is vital for international B2B buyers. By focusing on material preparation, forming, assembly, and finishing stages, as well as implementing robust quality control measures, manufacturers can deliver products that meet the high standards expected in today’s global market. Buyers should take proactive steps to verify supplier practices, ensuring that they align with their quality expectations and regional compliance requirements.
Practical Sourcing Guide: A Step-by-Step Checklist for ‘sound system manufacturer’
In the competitive landscape of sound system manufacturing, international B2B buyers must approach sourcing with a well-structured plan. This guide provides a practical checklist to help you navigate the procurement process effectively, ensuring you select the best sound system manufacturer that meets your specific requirements.
Step 1: Define Your Technical Specifications
Start by outlining the technical requirements for your sound system. This includes parameters like audio quality, power output, connectivity options (Bluetooth, Wi-Fi, etc.), and compatibility with existing systems. Clearly defined specifications help in identifying manufacturers that can meet your needs and avoid misunderstandings later in the procurement process.
Step 2: Research Potential Manufacturers
Conduct thorough research to compile a list of potential sound system manufacturers. Look for companies with a strong reputation, verified customer reviews, and a history of delivering high-quality products. Utilize platforms like LinkedIn, industry forums, and trade shows to gather insights and recommendations.
- Tip: Pay attention to manufacturers that specialize in your specific application, whether it be live sound, home audio, or commercial installations.
Step 3: Evaluate Supplier Certifications
Ensure that the manufacturers you’re considering hold relevant industry certifications. Certifications such as ISO 9001 for quality management or specific safety certifications demonstrate a commitment to quality and compliance with international standards.
- Why it matters: Certifications can be crucial for ensuring product safety, reliability, and performance consistency, especially in regions with stringent regulations.
Step 4: Request Product Samples
Before finalizing any contracts, request product samples from shortlisted manufacturers. Testing these samples allows you to assess the audio quality, build quality, and overall performance of the sound systems.
- What to look for: Pay attention to sound clarity, bass response, and usability features like control interfaces and connectivity options.
Step 5: Analyze Pricing and Payment Terms
Once you have a clear understanding of your options, compare pricing structures and payment terms among different manufacturers. Look for transparency in pricing and ensure that there are no hidden fees.
- Consider: Discuss bulk order discounts or payment plans that might be beneficial for your business, especially if you plan to make large purchases.
Step 6: Check After-Sales Support and Warranty
Evaluate the after-sales support offered by the manufacturers. A good warranty and support policy can save you significant costs in case of product defects or issues after purchase.
- Key questions: Inquire about the warranty duration, the process for claims, and whether technical support is available post-purchase.
Step 7: Negotiate Contracts Carefully
Once you’ve selected a manufacturer, negotiate the contract details with care. Ensure that all terms, including delivery timelines, payment schedules, and quality assurance measures, are clearly articulated and agreed upon.
- Final tip: Consider consulting with a legal expert to review contracts, ensuring that your interests are protected.
By following these steps, you can streamline your procurement process and establish a strong partnership with a reliable sound system manufacturer, ultimately leading to successful project outcomes.
Comprehensive Cost and Pricing Analysis for sound system manufacturer Sourcing
What Are the Key Cost Components in Sound System Manufacturing?
When sourcing sound systems, understanding the cost structure is vital for international B2B buyers. The primary cost components include:
-
Materials: The quality and type of components, such as speakers, amplifiers, and enclosures, significantly affect pricing. High-quality materials lead to better sound fidelity but also increase costs.
-
Labor: Labor costs can vary widely based on the region. In countries with higher labor costs, such as those in Europe, the overall cost of production may be higher than in regions like South America or Africa, where labor might be less expensive.
-
Manufacturing Overhead: This includes costs related to factory operations, utilities, and maintenance. Efficient manufacturing processes can help minimize these expenses.
-
Tooling: Initial setup costs for specialized equipment and molds for custom designs can be substantial. Buyers should inquire about these costs, especially for bespoke sound system designs.
-
Quality Control (QC): Ensuring product quality is crucial and incurs costs. Robust QC processes can prevent defects, which may save money in the long term by reducing returns and warranty claims.
-
Logistics: Shipping costs can significantly impact total expenditure, particularly for international shipments. Factors such as distance, transport mode, and customs fees play a role.
-
Margin: Manufacturers typically include a profit margin that reflects their business strategy and market positioning. Understanding this margin can help buyers gauge the pricing structure.
How Do Price Influencers Affect Sound System Costs?
Several factors influence pricing in the sound system manufacturing sector:
-
Volume/MOQ (Minimum Order Quantity): Ordering in bulk often leads to discounts. Manufacturers may have different pricing tiers based on the quantity ordered, so negotiating for larger volumes can yield better rates.
-
Specifications and Customization: Custom designs or specifications can lead to higher costs. Buyers should clearly define their needs to avoid unexpected expenses.
-
Materials: The choice of materials significantly affects the final price. Buyers should balance between cost and quality, especially when sourcing materials that meet regional preferences or standards.
-
Quality and Certifications: Products that meet specific quality standards or certifications (e.g., ISO, CE) may come at a premium. Buyers should assess whether these certifications are necessary for their market.
-
Supplier Factors: The reputation and reliability of suppliers can influence pricing. Established manufacturers may charge more due to their proven track record, while newer suppliers might offer competitive rates to gain market share.
-
Incoterms: The terms of shipping and delivery can impact costs significantly. Understanding Incoterms is essential for managing logistics and ensuring that all potential costs are accounted for.
What Are the Best Buyer Tips for Negotiating Sound System Prices?
For international B2B buyers, particularly from regions like Africa, South America, the Middle East, and Europe, here are actionable tips to optimize costs:
-
Negotiate Terms: Always negotiate pricing, payment terms, and delivery timelines. Suppliers often have room for flexibility, especially for larger orders.
-
Focus on Cost-Efficiency: Calculate the Total Cost of Ownership (TCO), which includes not just the purchase price but also logistics, maintenance, and eventual disposal costs. This comprehensive view can help in making informed purchasing decisions.
-
Understand Pricing Nuances: Be aware of regional pricing differences. For instance, certain suppliers might offer better deals for specific markets due to local competition or production costs.
-
Leverage Relationships: Building strong relationships with suppliers can lead to better pricing and terms. Regular communication can also foster trust, which may yield benefits in negotiations.
-
Research and Compare: Always compare multiple suppliers. Different manufacturers might offer varying price points based on their operational efficiencies and material costs.
Disclaimer on Pricing
Prices mentioned are indicative and can vary based on market conditions, supply chain fluctuations, and specific buyer requirements. It is advisable to obtain detailed quotes from multiple suppliers to ensure the best deal.
Alternatives Analysis: Comparing sound system manufacturer With Other Solutions
When exploring sound system solutions, it’s essential for B2B buyers to consider various alternatives to traditional sound system manufacturers. These alternatives can offer unique advantages depending on the specific needs of businesses, such as budget constraints, installation complexity, and desired sound quality. Below, we compare sound system manufacturers with two viable alternatives: digital streaming solutions and portable audio systems.
Comparison Aspect | Sound System Manufacturer | Digital Streaming Solutions | Portable Audio Systems |
---|---|---|---|
Performance | High-quality sound output | Variable, depends on internet and hardware | Moderate, designed for mobility |
Cost | Typically high initial investment | Subscription-based, often lower upfront costs | Varies widely, generally affordable |
Ease of Implementation | Requires professional installation | Easy setup, often plug-and-play | Very easy, usually battery-operated |
Maintenance | Regular maintenance needed | Minimal, mostly software updates | Low, typically requires battery replacements |
Best Use Case | Permanent installations in venues or large spaces | Flexible, ideal for remote work or small gatherings | On-the-go audio needs, outdoor events |
What Are the Advantages and Disadvantages of Digital Streaming Solutions?
Digital streaming solutions, such as platforms like Spotify or Apple Music, allow businesses to play high-quality audio without the need for extensive hardware. These systems are often cloud-based, meaning they can be accessed from various devices, making them highly versatile. The primary advantage is the low initial investment, as many services operate on a subscription model. However, performance can vary based on internet connection quality, and reliance on third-party services may be a drawback for companies seeking complete control over their audio output.
How Do Portable Audio Systems Compare to Traditional Sound Systems?
Portable audio systems, including Bluetooth speakers and compact soundbars, provide an excellent alternative for businesses that require mobility. These systems are easy to set up and operate, making them ideal for events, conferences, or outdoor gatherings. While they typically offer moderate sound quality compared to traditional systems, their affordability and convenience make them appealing for temporary setups. The downside is that they may lack the robust sound output needed for larger venues, and battery life can be a limiting factor for extended use.
How Can B2B Buyers Choose the Right Sound Solution?
When selecting the right sound solution, B2B buyers should assess their specific requirements, including the size of the space, intended use, and budget constraints. Sound system manufacturers excel in delivering high-quality, permanent installations suited for large venues, while digital streaming solutions offer flexibility and cost-effectiveness for smaller settings. Portable audio systems serve well in scenarios requiring mobility and ease of use. By weighing these factors against their unique business needs, buyers can make informed decisions that enhance their audio experience while optimizing their investments.
Essential Technical Properties and Trade Terminology for sound system manufacturer
What Are the Essential Technical Properties for Sound System Manufacturers?
When sourcing sound systems, international B2B buyers must understand key technical properties that influence performance, durability, and overall value. Here are some critical specifications to consider:
1. Material Grade: What Should You Look For?
Material grade refers to the quality and type of materials used in the construction of sound systems. Common materials include high-grade plastics, metals, and composites. For instance, aluminum is often preferred for its lightweight and durability, while high-density MDF (medium-density fiberboard) is utilized in speaker enclosures for superior acoustic properties. Selecting the right material is crucial, as it directly affects sound quality, longevity, and aesthetic appeal.
2. Frequency Response: How Does It Impact Sound Quality?
Frequency response measures the range of sound frequencies a speaker can reproduce, typically expressed in Hertz (Hz). A standard range for quality speakers is between 20 Hz to 20 kHz, covering the entire audible spectrum. Understanding this specification helps buyers assess how well a sound system will perform across different audio types, from deep bass to crisp treble.
3. Power Handling: What Is Its Significance?
Power handling indicates the maximum amount of power (measured in watts) a sound system can handle without distortion or damage. This specification is critical for B2B buyers, as it informs them about the system’s capability to deliver sound at high volumes without compromising quality. Adequate power handling ensures that the system can meet the demands of various environments, from intimate gatherings to large events.
4. Sensitivity: Why Is It Important?
Sensitivity measures how effectively a speaker converts power into sound, typically expressed in decibels (dB). A higher sensitivity rating means the speaker requires less power to produce the same volume as a lower-rated speaker. This is particularly important for energy efficiency and can significantly impact overall system performance, especially in commercial applications where power consumption is a concern.
5. Impedance: How Does It Affect System Compatibility?
Impedance, measured in ohms, refers to the resistance a speaker presents to the amplifier. Common values are 4, 6, or 8 ohms. Understanding impedance is essential for ensuring compatibility between the speakers and amplifiers in a sound system. Incorrect impedance can lead to suboptimal performance or damage to the equipment.
Which Trade Terminology Should You Know as a B2B Buyer?
Familiarizing yourself with industry-specific terminology is essential for effective communication and negotiation in the sound system market. Here are key terms every buyer should know:
1. OEM (Original Equipment Manufacturer): What Does It Mean?
An OEM is a company that produces parts or equipment that may be marketed by another manufacturer. For buyers, understanding OEM relationships can provide insights into the quality and reliability of components within sound systems.
2. MOQ (Minimum Order Quantity): How Does It Affect Your Orders?
MOQ refers to the smallest quantity of goods a supplier is willing to sell. Understanding MOQ is crucial for B2B buyers, as it can affect inventory management and overall cost. Negotiate MOQs that align with your purchasing capacity to avoid excess stock.
3. RFQ (Request for Quotation): Why Is It Necessary?
An RFQ is a standard business process wherein a company invites suppliers to submit price quotes for specific products. Utilizing RFQs allows buyers to compare offers and select suppliers based on price, quality, and delivery terms, ensuring the best value.
4. Incoterms: What Are They and Why Do They Matter?
Incoterms (International Commercial Terms) are a set of rules that define the responsibilities of buyers and sellers in international transactions. Familiarity with Incoterms helps buyers understand shipping costs, risks, and obligations, allowing for better planning and budgeting.
5. Lead Time: How Can It Impact Your Supply Chain?
Lead time refers to the time it takes from placing an order to receiving the product. Understanding lead times is crucial for effective inventory management and ensuring that sound systems are available when needed, particularly in fast-paced markets.
By grasping these technical properties and trade terms, B2B buyers can make more informed decisions, leading to successful partnerships and optimized purchasing strategies in the sound system market.
Navigating Market Dynamics and Sourcing Trends in the sound system manufacturer Sector
What Are the Current Market Dynamics and Sourcing Trends in the Sound System Manufacturing Sector?
The global sound system manufacturing market is witnessing robust growth, driven by the increasing demand for high-quality audio experiences across various sectors, including entertainment, education, and corporate environments. Emerging technologies such as Bluetooth, smart connectivity, and immersive audio solutions are shaping the landscape. For international B2B buyers, particularly from Africa, South America, the Middle East, and Europe, understanding these dynamics is crucial for making informed sourcing decisions.
Recent trends indicate a shift towards integrated sound systems that offer multi-functional capabilities, such as voice control and connectivity with smart home devices. This trend is particularly evident in the Middle East and Europe, where consumers are increasingly seeking advanced audio solutions that blend aesthetics with high performance. Additionally, as businesses seek to enhance user experiences, there is a growing emphasis on customized sound solutions tailored to specific environments, from retail spaces to large event venues.
Another noteworthy development is the rise of direct-to-consumer (DTC) models. Manufacturers are increasingly engaging with end-users through online platforms, thereby reducing reliance on traditional distribution channels. This shift not only allows for better customer engagement but also provides valuable insights into market preferences, enabling companies to refine their offerings. For B2B buyers, this presents opportunities to negotiate better terms and access innovative products directly from manufacturers.
How Important Is Sustainability and Ethical Sourcing in the Sound System Manufacturing Sector?
Sustainability and ethical sourcing are becoming paramount in the sound system manufacturing sector, reflecting the growing awareness of environmental impact among consumers and businesses alike. The production of sound systems often involves materials and processes that can be detrimental to the environment, making it essential for manufacturers to adopt greener practices.
International buyers are increasingly prioritizing suppliers that demonstrate a commitment to sustainability. This includes the use of recycled materials, energy-efficient manufacturing processes, and environmentally friendly packaging. Certifications such as ISO 14001 (Environmental Management) and the Forest Stewardship Council (FSC) for wood products are becoming critical criteria for sourcing decisions.
Moreover, ethical sourcing practices, which ensure fair labor conditions and responsible sourcing of raw materials, are gaining traction. Buyers from regions like Africa and South America are particularly keen on establishing partnerships with manufacturers who uphold social responsibility, as this aligns with their own corporate values and consumer expectations. By choosing suppliers with robust sustainability credentials, B2B buyers can not only enhance their brand reputation but also contribute positively to the global effort towards environmental stewardship.
What Is the Evolution of the Sound System Manufacturing Sector?
The sound system manufacturing sector has undergone significant transformations over the decades, evolving from basic audio equipment to sophisticated, technology-driven solutions. Initially, sound systems were primarily used in public address applications and home audio setups. The introduction of stereo sound in the mid-20th century marked a pivotal point, leading to a surge in consumer interest and demand.
The late 20th century saw the rise of digital technology, which revolutionized sound systems with the advent of digital signal processing (DSP) and compact disc technology. This era also witnessed the birth of portable audio devices, making high-quality sound accessible to a broader audience.
In the 21st century, the integration of wireless technology and smart capabilities has further transformed the landscape. Today, manufacturers are focusing on creating immersive audio experiences that cater to diverse consumer needs. As the sector continues to innovate, international B2B buyers must stay abreast of these developments to capitalize on emerging opportunities and maintain a competitive edge in their respective markets.
Frequently Asked Questions (FAQs) for B2B Buyers of sound system manufacturer
-
How do I choose the right sound system manufacturer for my business needs?
Selecting the appropriate sound system manufacturer involves evaluating their product range, quality certifications, and industry reputation. Consider manufacturers who specialize in your specific market requirements, such as commercial audio systems or portable solutions. Request samples to assess sound quality and reliability. Additionally, check for customer testimonials and case studies to understand their experience with similar businesses. Networking through industry events can also provide valuable insights into potential partners. -
What are the key factors to consider when sourcing sound systems internationally?
When sourcing sound systems from international manufacturers, consider factors such as compliance with local regulations, shipping logistics, and import duties. It’s crucial to verify the manufacturer’s certifications, such as ISO standards, which ensure quality and safety. Evaluate their production capacity to meet your order volume and timelines. Additionally, assess their ability to provide after-sales support and warranty services, as these can significantly impact your business operations. -
What customization options are typically available from sound system manufacturers?
Most sound system manufacturers offer customization options to meet specific client requirements. This may include modifications in design, color, branding, and technical specifications like power output and connectivity features. Discuss your needs upfront to ensure the manufacturer can accommodate your requests. Some manufacturers may also provide bespoke solutions for unique projects, such as integrating advanced technology or unique audio features, so inquire about their capabilities. -
What is the minimum order quantity (MOQ) when sourcing sound systems?
Minimum order quantities (MOQs) vary widely among sound system manufacturers, often influenced by factors such as product type and customization level. Typically, MOQs can range from a few units for standard products to larger quantities for custom designs. It’s advisable to clarify MOQs during initial discussions to avoid misunderstandings later. Some manufacturers may offer flexibility for first-time buyers or smaller businesses, so negotiating terms can be beneficial. -
How can I ensure quality assurance when purchasing sound systems?
To ensure quality assurance when sourcing sound systems, request detailed information about the manufacturer’s quality control processes. Inquire about their testing methods and certifications, such as CE or UL, which indicate compliance with international safety standards. Additionally, consider conducting factory audits or hiring third-party inspection services to evaluate production practices. Establishing clear quality expectations in your purchase agreement can also help mitigate risks associated with product defects. -
What are the common payment terms for international sound system purchases?
Payment terms for international purchases typically vary by manufacturer and can include options such as advance payment, letter of credit, or payment upon delivery. Many suppliers prefer a deposit upfront (usually 30% to 50%) with the balance due before shipment. It’s crucial to negotiate terms that align with your cash flow and risk management strategies. Always ensure that payment methods are secure and that you receive clear invoices detailing the transaction.
- What logistics considerations should I keep in mind when importing sound systems?
When importing sound systems, logistics considerations include shipping methods, customs clearance, and delivery timelines. Choose between air freight for faster delivery or sea freight for cost-effectiveness, depending on your urgency and budget. Understand the customs regulations in your country to prepare necessary documentation, such as invoices and packing lists. Working with an experienced freight forwarder can streamline the process and help navigate any potential challenges.
- How do I handle potential disputes with sound system manufacturers?
Handling disputes with manufacturers requires clear communication and documentation. Always maintain records of contracts, correspondence, and transaction details. If a dispute arises, attempt to resolve the issue directly with the manufacturer first, as many are willing to negotiate. If necessary, involve a third-party mediator or legal counsel to facilitate discussions. Additionally, consider including dispute resolution clauses in your contracts, specifying arbitration or mediation procedures to manage conflicts effectively.
Important Disclaimer & Terms of Use
⚠️ Important Disclaimer
The information provided in this guide, including content regarding manufacturers, technical specifications, and market analysis, is for informational and educational purposes only. It does not constitute professional procurement advice, financial advice, or legal advice.
While we have made every effort to ensure the accuracy and timeliness of the information, we are not responsible for any errors, omissions, or outdated information. Market conditions, company details, and technical standards are subject to change.
B2B buyers must conduct their own independent and thorough due diligence before making any purchasing decisions. This includes contacting suppliers directly, verifying certifications, requesting samples, and seeking professional consultation. The risk of relying on any information in this guide is borne solely by the reader.
Strategic Sourcing Conclusion and Outlook for sound system manufacturer
In the evolving landscape of the sound system manufacturing sector, international B2B buyers, particularly from Africa, South America, the Middle East, and Europe, stand to gain significantly from strategic sourcing practices. By leveraging a comprehensive understanding of market dynamics, suppliers can optimize their procurement processes, ensuring they acquire high-quality sound systems that meet diverse regional needs.
How Can Strategic Sourcing Enhance Your Sound System Purchases?
Strategic sourcing not only helps in identifying reliable suppliers but also fosters long-term partnerships that can lead to better pricing, improved quality, and consistent supply chains. Buyers should focus on evaluating suppliers based on their technological capabilities, customer service, and responsiveness to market trends. This strategic approach enables companies to stay ahead of competition while maximizing value for their investments.
What Are the Future Trends in Sound System Manufacturing?
Looking ahead, the integration of advanced technologies such as AI and IoT in sound systems presents new opportunities. These innovations promise enhanced user experiences and greater customization options, which are increasingly becoming essential in the global market.
As you navigate the complexities of sound system procurement, consider adopting these strategic sourcing principles to enhance your purchasing decisions. Embrace the future of sound technology and make informed choices that will elevate your business offerings.