The Ultimate Guide to Acoustic Panel Supplier (2025)
Introduction: Navigating the Global Market for acoustic panel supplier
In today’s globalized marketplace, sourcing the right acoustic panel supplier can be a daunting task for international B2B buyers, particularly in diverse regions such as Africa, South America, the Middle East, and Europe. The challenge lies not only in identifying suppliers that meet specific acoustic performance standards but also in navigating logistical complexities and understanding regional regulations. This guide aims to demystify the process of sourcing acoustic panels, offering insights into various types of panels, their applications across different industries, and critical considerations for supplier vetting.
Throughout this comprehensive resource, we will cover essential aspects such as the cost implications of different acoustic solutions, the significance of certifications and quality assurance, and tips for establishing effective communication with suppliers. By focusing on actionable insights tailored for buyers in countries like Kenya and the UAE, this guide empowers decision-makers to make informed purchasing choices that align with their organizational needs and budgets.
Whether you are looking to enhance the acoustics of an office space, an educational facility, or a hospitality venue, understanding the nuances of the global acoustic panel market is crucial. With the right knowledge, you can confidently select suppliers that not only provide high-quality products but also offer sustainable solutions that cater to your specific requirements.
Understanding acoustic panel supplier Types and Variations
Type Name | Key Distinguishing Features | Primary B2B Applications | Brief Pros & Cons for Buyers |
---|---|---|---|
Fabric-Wrapped Acoustic Panels | Soft fabric covering for aesthetic appeal | Offices, conference rooms, auditoriums | Pros: Versatile designs; good sound absorption. Cons: May require maintenance. |
Foam Acoustic Panels | Lightweight and easily installed | Home studios, small offices | Pros: Cost-effective; easy to customize. Cons: Less durable; limited aesthetic options. |
Wooden Acoustic Panels | Natural wood finish for a premium look | High-end venues, restaurants | Pros: Attractive appearance; effective sound control. Cons: Higher cost; heavier. |
Metal Acoustic Panels | Durable and modern, often used in industrial spaces | Factories, warehouses | Pros: Long-lasting; easy to clean. Cons: Can be more expensive; less warmth in aesthetics. |
Composite Acoustic Panels | Combination of materials for enhanced performance | Theaters, multipurpose spaces | Pros: Balanced sound absorption and aesthetic flexibility. Cons: May be pricier; requires careful installation. |
What Are Fabric-Wrapped Acoustic Panels and Their B2B Suitability?
Fabric-wrapped acoustic panels are designed with a soft fabric covering that enhances sound absorption while adding an aesthetic touch to interiors. These panels are particularly suitable for environments like offices, conference rooms, and auditoriums where both sound quality and visual appeal are critical. When purchasing, B2B buyers should consider the range of fabric options available, as well as the maintenance requirements, since the fabric can attract dust and stains.
How Do Foam Acoustic Panels Benefit Small Businesses?
Foam acoustic panels are lightweight and easy to install, making them a popular choice for home studios and small offices. Their affordability and customization options allow businesses on a budget to enhance sound quality effectively. However, buyers should be aware that while foam panels are cost-effective, they may not offer the same durability or aesthetic appeal as other options, making them less suitable for high-traffic or high-profile environments.
Why Choose Wooden Acoustic Panels for High-End Applications?
Wooden acoustic panels provide a premium finish that is ideal for high-end venues such as restaurants and theaters. Their natural wood appearance not only contributes to sound control but also elevates the overall design of a space. B2B buyers should consider the initial investment in wooden panels, as they tend to be more expensive. Additionally, the weight of wooden panels may require specific installation considerations.
What Are the Advantages of Metal Acoustic Panels in Industrial Settings?
Metal acoustic panels are known for their durability and modern look, making them suitable for industrial applications like factories and warehouses. These panels are easy to clean and maintain, which is a significant advantage in environments where dust and debris are prevalent. B2B buyers must weigh the higher costs against the long-term benefits of durability and reduced maintenance when considering metal panels for their projects.
How Do Composite Acoustic Panels Provide Versatility for Multipurpose Spaces?
Composite acoustic panels combine different materials to offer enhanced sound absorption and aesthetic flexibility. They are ideal for theaters and multipurpose spaces where both functionality and design matter. When purchasing composite panels, B2B buyers should evaluate the specific performance characteristics required for their environment, as these panels can vary widely in composition and effectiveness. The investment may be higher, but the potential for a balanced acoustic environment makes them worth considering.
Related Video: Acoustic Panels – What & Where
Key Industrial Applications of acoustic panel supplier
Industry/Sector | Specific Application of Acoustic Panel Supplier | Value/Benefit for the Business | Key Sourcing Considerations for this Application |
---|---|---|---|
Education | Classroom Soundproofing | Enhances learning environments by reducing noise distractions. | Durability, ease of installation, and aesthetic appeal. |
Hospitality | Hotel Lobby and Conference Room Design | Creates a welcoming atmosphere while ensuring guest comfort. | Fire safety standards, acoustic performance, and design. |
Healthcare | Hospital Waiting Areas and Treatment Rooms | Improves patient comfort and confidentiality, promoting healing. | Hygiene standards, material safety, and sound absorption. |
Corporate Offices | Open Office Space Acoustic Treatment | Increases productivity by minimizing noise pollution. | Customization options, installation services, and warranties. |
Manufacturing | Production Floor Noise Control | Protects workers from excessive noise, ensuring safety compliance. | Compliance with industry regulations and durability. |
How Are Acoustic Panels Used in Educational Settings?
In educational institutions, acoustic panels are pivotal for soundproofing classrooms. By minimizing external noise distractions, they enhance the learning environment, allowing students to focus better. International buyers, particularly from regions like Africa and South America, should consider factors such as durability and ease of installation, as schools often require efficient and effective solutions that are budget-friendly yet impactful.
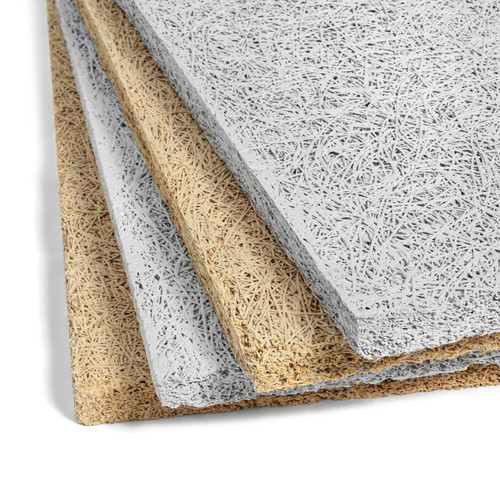
A stock image related to acoustic panel supplier.
What Role Do Acoustic Panels Play in the Hospitality Industry?
In the hospitality sector, acoustic panels are essential for designing hotel lobbies and conference rooms. They contribute to a welcoming atmosphere while ensuring that noise levels remain manageable for guests and attendees. For B2B buyers in the Middle East and Europe, sourcing panels that meet fire safety standards and provide excellent acoustic performance is crucial, especially in high-traffic areas where guest comfort is paramount.
Why Are Acoustic Panels Important in Healthcare Facilities?
Acoustic panels find significant application in healthcare settings, particularly in hospital waiting areas and treatment rooms. They help improve patient comfort by reducing noise levels, which is vital for promoting a healing environment. Buyers from regions like Kenya and the UAE should prioritize hygiene standards and material safety when sourcing these products, ensuring they meet the specific needs of medical facilities.
How Do Acoustic Panels Enhance Corporate Office Environments?
In corporate offices, acoustic treatment of open spaces is essential for increasing productivity by minimizing noise pollution. Acoustic panels can be strategically placed to optimize sound distribution, allowing for a more collaborative atmosphere. B2B buyers in Europe and South America should look for customization options and reliable installation services to ensure the panels fit their specific office layouts and aesthetic preferences.
What Benefits Do Acoustic Panels Provide in Manufacturing Settings?
In manufacturing environments, acoustic panels are critical for noise control on production floors. They help protect workers from excessive noise, thus ensuring safety compliance and enhancing overall workplace comfort. International buyers, especially from Africa and the Middle East, should consider the durability of materials and compliance with industry regulations when sourcing acoustic solutions for their facilities, as these factors directly impact employee health and operational efficiency.
Related Video: Industrial Control Panel Basics
3 Common User Pain Points for ‘acoustic panel supplier’ & Their Solutions
Scenario 1: Insufficient Acoustic Performance for Large Spaces
The Problem: Many B2B buyers, especially those managing large venues such as auditoriums, conference halls, or open-plan offices, often face the challenge of inadequate sound absorption. They invest in acoustic panels, but the performance does not meet expectations, leading to echo and noise issues. This can result in poor communication, decreased productivity, and an unpleasant environment for clients and employees alike. Buyers may feel frustrated, especially after spending significant budgets on what they believed were quality solutions.
The Solution: To address this issue, buyers should conduct a thorough acoustic assessment of the space before purchasing panels. Engaging an acoustic consultant can provide valuable insights into the specific sound issues and the appropriate types of panels needed. When sourcing panels, focus on suppliers that offer customizable solutions tailored to the unique acoustics of large spaces. Look for products with high Noise Reduction Coefficient (NRC) ratings and ensure they are tested in real-world conditions. Additionally, consider a mix of panel types (e.g., wall-mounted, ceiling tiles) to enhance overall sound absorption effectively. Collaborating with the supplier during the installation phase can also ensure optimal placement, maximizing the panels’ effectiveness.
Scenario 2: Limited Design Options Affecting Brand Aesthetics
The Problem: In competitive markets, brand image is crucial, and many B2B buyers struggle to find acoustic panels that align with their design aesthetics. For businesses in sectors like hospitality or retail, the visual appeal of the environment is as important as sound quality. Buyers often feel constrained by the limited color and material options provided by suppliers, leading to a mismatch between functionality and branding.
The Solution: To overcome this challenge, buyers should prioritize suppliers that offer a wide range of customizable designs, colors, and materials. Look for manufacturers that provide the option to print custom designs or patterns on acoustic panels, allowing for brand-specific aesthetics. Another effective approach is to source panels from suppliers who collaborate with designers and architects, ensuring that the products not only perform well acoustically but also enhance the overall interior design. When requesting samples, ask for mock-ups that can demonstrate how the panels will integrate with existing decor, thus enabling informed decisions that harmonize sound management with brand identity.
Scenario 3: Concerns Over Sustainability and Environmental Impact
The Problem: Increasingly, B2B buyers are conscious of sustainability and the environmental impact of their purchasing decisions. Many acoustic panels are made from materials that may not be eco-friendly or recyclable, which can be a significant concern for companies aiming to meet corporate social responsibility goals. Buyers may find it challenging to identify suppliers that align with their values, leading to indecision and potential delays in project timelines.
The Solution: To tackle this pain point, buyers should actively seek suppliers that prioritize sustainability in their manufacturing processes. This includes sourcing materials that are recycled, recyclable, or made from sustainable resources. When evaluating potential suppliers, request detailed information about their sustainability practices, certifications, and product lifecycle assessments. Consider establishing partnerships with manufacturers who can provide documentation of their eco-friendly initiatives and demonstrate their commitment to reducing environmental footprints. Additionally, exploring local suppliers can minimize transportation emissions and support local economies, making a positive impact while fulfilling acoustic needs.
Strategic Material Selection Guide for acoustic panel supplier
What Are the Key Properties of Common Acoustic Panel Materials?
When selecting materials for acoustic panels, understanding their properties is essential for ensuring optimal performance. Here, we analyze four common materials used in acoustic panels: fiberglass, foam, wood, and metal. Each material has unique characteristics that influence their suitability for various applications.
How Does Fiberglass Perform in Acoustic Applications?
Fiberglass is widely recognized for its sound absorption capabilities, making it a popular choice for acoustic panels. It has a high temperature rating, allowing it to withstand various environmental conditions without degrading. Additionally, fiberglass is resistant to moisture and mold, which is crucial in humid climates often found in regions like Africa and the Middle East.
Pros: Fiberglass panels are durable and lightweight, making them easy to install. They offer excellent sound absorption and can be manufactured in various densities and thicknesses to suit specific needs.
Cons: The primary drawback of fiberglass is its cost, which can be higher than other materials. Moreover, installation requires careful handling to avoid skin irritation, necessitating safety measures.
Impact on Application: Fiberglass is compatible with various media, including music studios, offices, and auditoriums, where sound clarity is paramount.
Considerations for International Buyers: Compliance with standards such as ASTM E795 for sound absorption is crucial. Buyers from regions like Europe may prefer panels that meet EU regulations regarding safety and environmental impact.
What Advantages Does Foam Offer for Acoustic Panels?
Foam is another popular material for acoustic panels, known for its lightweight and versatile nature. It is available in various shapes and densities, allowing for tailored sound absorption.
Pros: Foam panels are typically more affordable than fiberglass, making them an attractive option for budget-conscious buyers. Their lightweight nature simplifies installation, and they can be easily cut to fit specific applications.
Cons: While foam offers good sound absorption, its durability can be a concern, especially in high-traffic areas. Foam panels may also be less effective in extreme temperatures, which could limit their use in certain climates.
Impact on Application: Foam is widely used in recording studios, home theaters, and conference rooms where sound quality is essential.
Considerations for International Buyers: Buyers should look for foam that complies with fire safety standards, particularly in regions like the UAE where regulations are stringent. Understanding local preferences for aesthetics can also guide material selection.
How Does Wood Contribute to Acoustic Performance?
Wood is often chosen for its aesthetic appeal and natural sound absorption qualities. It can effectively reduce echo and improve sound quality in various environments.
Pros: Wood panels are not only visually appealing but also provide excellent acoustical performance. They are durable and can be treated or finished to enhance their longevity.
Cons: The main limitation of wood is its higher cost compared to synthetic materials. Additionally, wood requires careful sourcing to ensure sustainability, which may complicate procurement for international buyers.
Impact on Application: Wood is ideal for concert halls, theaters, and high-end office spaces where aesthetics and acoustics are prioritized.
Considerations for International Buyers: Buyers should ensure that wood panels comply with local environmental regulations and standards such as FSC certification. This is particularly important in regions like Europe, where sustainability is a significant concern.
What Role Does Metal Play in Acoustic Panel Solutions?
Metal panels are less common but can be effective in specific applications, particularly in industrial settings. They offer unique acoustic properties and durability.
Pros: Metal panels are highly durable and resistant to corrosion, making them suitable for harsh environments. They can also be designed to reflect sound, which can be beneficial in certain applications.
Cons: Metal can be more expensive than other materials, and its sound absorption capabilities may not be as effective as softer materials. Additionally, installation can be more complex due to weight.
Impact on Application: Metal panels are often used in factories, warehouses, and commercial spaces where durability is essential.
Considerations for International Buyers: Compliance with standards such as DIN 4102 for fire safety is crucial, especially in regions with stringent regulations like Europe.
Summary Table of Material Selection for Acoustic Panels
Material | Typical Use Case for acoustic panel supplier | Key Advantage | Key Disadvantage/Limitation | Relative Cost (Low/Med/High) |
---|---|---|---|---|
Fiberglass | Music studios, auditoriums | Excellent sound absorption | Higher cost, requires careful handling | High |
Foam | Home theaters, conference rooms | Affordable and lightweight | Less durable, temperature sensitivity | Low |
Wood | Concert halls, high-end offices | Aesthetic appeal and durability | Higher cost, sourcing complexity | High |
Metal | Industrial settings, warehouses | Highly durable, corrosion-resistant | Expensive, complex installation | Med |
This comprehensive analysis of materials provides international B2B buyers with actionable insights to make informed decisions when sourcing acoustic panels. Understanding the properties, advantages, and limitations of each material is crucial for selecting the right solution for specific applications.
In-depth Look: Manufacturing Processes and Quality Assurance for acoustic panel supplier
What Are the Main Stages of Acoustic Panel Manufacturing?
The manufacturing process of acoustic panels involves several key stages that ensure the final product meets both performance and aesthetic standards. Understanding these stages is crucial for B2B buyers to ensure they are sourcing high-quality products.
Material Preparation
The first step in the manufacturing process is material preparation. Acoustic panels can be made from various materials, including fiberglass, foam, wood, and recycled materials. Each material has its own acoustic properties, so selecting the right one is essential for the intended application. For instance, fiberglass panels are known for their superior sound absorption, while wood panels offer a more aesthetic appeal.
During this stage, materials are sourced from reputable suppliers, and quality checks are performed to ensure they meet specific standards. Buyers should inquire about the sourcing process to understand how materials are vetted for quality.
Forming Techniques
Once the materials are prepared, they undergo forming techniques to create the desired shape and size. Common forming methods include cutting, molding, and pressing. For example, foam panels are often cut to size using CNC machines, which provide precision and consistency. In contrast, fiberglass panels may be molded into specific shapes to enhance their acoustic properties.
Buyers should evaluate the technology and machinery used in the forming process, as advanced techniques can lead to more consistent quality and better performance.
Assembly Process
After forming, the next stage is assembly. This involves attaching the finished panels to a backing material or frame, which may include additional acoustic treatments. Quality assembly is vital to ensure that the panels maintain their structural integrity and performance over time.
B2B buyers should ask potential suppliers about their assembly methods and whether they employ automated processes, as automation can enhance consistency and reduce human error.
Finishing Techniques
The final stage of manufacturing is finishing, which may include painting, laminating, or coating the panels to enhance their durability and aesthetic appeal. Finishing techniques not only improve the visual aspects of the panels but also contribute to their acoustic performance.
It’s advisable for buyers to request samples of finished products to assess the quality of finishing. A well-finished acoustic panel will not only look good but also perform effectively in sound absorption.
How Is Quality Assurance Implemented in Acoustic Panel Manufacturing?
Quality assurance (QA) is a critical component of the manufacturing process, ensuring that each batch of acoustic panels meets international and industry-specific standards. For B2B buyers, understanding the QA measures in place can provide confidence in the products being sourced.
What Are the Relevant International Standards for Acoustic Panels?
International standards play a significant role in the quality assurance of acoustic panels. The ISO 9001 standard is a widely recognized framework that outlines the requirements for a quality management system. Suppliers adhering to ISO 9001 demonstrate a commitment to quality and continuous improvement.
In addition to ISO certifications, industry-specific standards such as CE marking in Europe and API standards can be relevant. CE marking indicates that the product meets European health and safety requirements, while API standards are crucial for panels used in specific industrial applications.
What Are the Key Quality Control Checkpoints?
Quality control (QC) checkpoints are essential for maintaining product quality throughout the manufacturing process. These checkpoints typically include:
- Incoming Quality Control (IQC): This involves inspecting raw materials upon arrival to ensure they meet specified standards before processing begins.
- In-Process Quality Control (IPQC): During manufacturing, periodic inspections are conducted to monitor processes and ensure they are within acceptable limits.
- Final Quality Control (FQC): Before shipment, finished products undergo a final inspection to verify compliance with quality standards.
B2B buyers should inquire about the specific QC checkpoints employed by suppliers and request documentation demonstrating compliance with these processes.
What Common Testing Methods Are Used for Acoustic Panels?
Testing methods for acoustic panels are vital for verifying their performance characteristics. Common testing methods include:
- Sound Absorption Tests: These tests measure how well the panels absorb sound at different frequencies, providing insight into their acoustic effectiveness.
- Fire Resistance Tests: Given the importance of safety, acoustic panels should undergo fire resistance testing to comply with building regulations.
- Durability Tests: Assessing the panels’ resistance to wear and tear ensures they maintain performance over time.
Buyers should request test reports and certifications from suppliers to confirm that their panels have passed these essential tests.
How Can B2B Buyers Verify Supplier Quality Control?
Verifying the quality control processes of an acoustic panel supplier is crucial for mitigating risks in procurement. Here are several strategies B2B buyers can employ:
Conducting Supplier Audits
One of the most effective ways to assess a supplier’s quality assurance practices is through audits. Buyers can perform on-site audits to evaluate the manufacturing processes, QC checkpoints, and adherence to international standards. This not only builds trust but also allows buyers to identify potential issues early on.
Requesting Quality Assurance Reports
B2B buyers should ask suppliers for detailed quality assurance reports that outline their QC processes, testing results, and compliance with international standards. These documents can provide valuable insights into the supplier’s commitment to quality.
Engaging Third-Party Inspection Services
Another option is to engage third-party inspection services to conduct independent evaluations of the supplier’s manufacturing processes and quality controls. This adds an additional layer of assurance, especially for international buyers who may be unable to conduct on-site inspections.
What Are the QC and Certification Nuances for International Buyers?
For international B2B buyers, understanding the nuances of quality control and certifications can be particularly challenging due to varying regulations across regions. Buyers from Africa, South America, the Middle East, and Europe should consider the following:
- Local Regulations: Familiarize yourself with the acoustic panel regulations specific to your region. For instance, EU buyers must ensure compliance with CE marking, while Middle Eastern buyers may need to adhere to local building codes.
- Cultural Expectations: Different regions may have varying expectations regarding quality and performance. Engaging local partners or consultants can help navigate these cultural differences effectively.
- Language Barriers: Ensure that all documentation and communication with suppliers are clear and accessible. This might involve requesting materials in multiple languages to facilitate understanding.
By thoroughly understanding the manufacturing processes and quality assurance measures of acoustic panel suppliers, B2B buyers can make informed decisions that align with their business needs and regulatory requirements.
Practical Sourcing Guide: A Step-by-Step Checklist for ‘acoustic panel supplier’
This practical sourcing guide is designed to assist international B2B buyers, particularly from Africa, South America, the Middle East, and Europe, in effectively procuring acoustic panels. The steps outlined below will streamline your sourcing process, ensuring that you find a reliable supplier that meets your specific needs.
Step 1: Define Your Technical Specifications
Before reaching out to suppliers, clearly outline the technical specifications of the acoustic panels you require. Consider factors such as material type, sound absorption ratings, fire resistance, and aesthetic preferences. This clarity will help you communicate effectively with potential suppliers and ensure that they can meet your requirements.
Step 2: Research Potential Suppliers
Conduct thorough research to identify potential suppliers who specialize in acoustic panels. Utilize online directories, industry forums, and trade shows to compile a list. Pay attention to suppliers that have experience in your region, as they may better understand local regulations and market demands.
Step 3: Evaluate Supplier Certifications
Ensure that the suppliers you are considering hold relevant certifications. These may include ISO certifications, environmental compliance (such as LEED), and safety standards. Certifications not only demonstrate a commitment to quality but also help mitigate risks associated with sourcing from unverified suppliers.
Step 4: Request Samples for Assessment
Before making a final decision, request samples of the acoustic panels. This allows you to assess the quality, design, and suitability for your intended application. Pay attention to factors such as texture, color options, and overall construction quality. Evaluating samples can prevent costly mistakes later in the procurement process.
Step 5: Check References and Reviews
Ask potential suppliers for references from past clients, particularly those in similar industries or regions. Contact these references to inquire about their experiences, including delivery timelines, product quality, and customer service. Additionally, look for online reviews and testimonials to gain insights into the supplier’s reputation.
Step 6: Negotiate Terms and Pricing
Once you have narrowed down your list of suppliers, engage in negotiations regarding pricing, payment terms, and delivery schedules. Be clear about your expectations and any bulk order discounts. Establishing favorable terms can lead to a long-term partnership that benefits both parties.
Step 7: Finalize Contracts and Agreements
After agreeing on terms, ensure that all contractual details are clearly documented. This includes specifications, pricing, timelines, and any warranties or guarantees. Having a solid contract protects both you and the supplier, reducing the likelihood of disputes in the future.
By following these steps, you can enhance your sourcing process for acoustic panels, ensuring that you select a supplier that aligns with your business needs and quality standards.
Comprehensive Cost and Pricing Analysis for acoustic panel supplier Sourcing
What Are the Key Components of Acoustic Panel Supplier Costs?
When evaluating acoustic panel suppliers, understanding the cost structure is vital. The main components influencing the cost include materials, labor, manufacturing overhead, tooling, quality control (QC), logistics, and profit margins.
- Materials: The choice of materials significantly impacts the price of acoustic panels. High-density fiberglass, foam, or wood can lead to varying costs, with more durable and effective options typically priced higher.
- Labor: Labor costs can fluctuate based on the region of production. Countries with lower labor costs may offer more competitive pricing but may also affect quality and lead times.
- Manufacturing Overhead: This includes utilities, rent, and other fixed costs associated with running a production facility. Efficient manufacturing processes can help lower these costs.
- Tooling: Custom tooling for specific panel designs can entail significant upfront costs. Consider if your project requires unique tooling to avoid unexpected expenses.
- Quality Control: Rigorous QC processes ensure the final product meets specifications and standards. While quality control adds to costs, it can prevent more significant losses down the line due to defects.
- Logistics: Shipping and handling costs must be factored in, particularly for international transactions. Freight costs can vary based on distance, mode of transport, and any tariffs or duties.
- Margin: Suppliers will add a profit margin to their costs. Understanding typical margins in the industry can help in negotiating prices.
How Do Pricing Influencers Impact Acoustic Panel Supplier Costs?
Several factors influence the final pricing of acoustic panels beyond the basic cost structure. International B2B buyers should pay attention to these elements:
- Volume/MOQ: Bulk orders often lead to lower per-unit costs. Suppliers may have Minimum Order Quantities (MOQs) that can affect pricing and should be discussed during negotiations.
- Specifications and Customization: Customized panels tailored to specific acoustic requirements or designs usually come at a premium. Clearly defining your needs can help suppliers provide more accurate quotes.
- Materials and Quality Certifications: Panels that meet specific industry standards or certifications (e.g., fire resistance, sound absorption ratings) may incur higher costs. Buyers should assess the necessity of these certifications based on their projects.
- Supplier Factors: The supplier’s location, reputation, and production capacity can influence pricing. Established suppliers may charge more due to perceived reliability and quality.
- Incoterms: Understanding Incoterms (International Commercial Terms) is crucial as they dictate who bears the cost and risk at various stages of the shipping process. This knowledge can help buyers accurately calculate total landed costs.
What Tips Can Help International B2B Buyers Optimize Acoustic Panel Sourcing Costs?
To secure the best value when sourcing acoustic panels, international buyers, especially from regions like Africa, South America, the Middle East, and Europe, should consider the following strategies:
- Negotiation: Always approach negotiations with a clear understanding of your budget and the market rates. Leverage quotes from multiple suppliers to strengthen your position.
- Cost-Efficiency: Consider the Total Cost of Ownership (TCO), which includes not just the purchase price but also installation, maintenance, and potential energy savings from improved acoustics. This comprehensive view can justify higher initial costs for superior products.
- Understanding Pricing Nuances: Prices can vary significantly based on geographical location and market conditions. For instance, suppliers in Europe may have different pricing structures compared to those in the Middle East or Africa due to varying operational costs and market demand.
- Local Partnerships: Establishing relationships with local distributors can reduce shipping costs and tariffs, making sourcing more economical.
- Stay Informed on Market Trends: Keeping abreast of market trends, material innovations, and economic factors can help buyers anticipate changes in pricing and make informed decisions.
Conclusion
Navigating the complexities of sourcing acoustic panels requires a thorough understanding of cost components, pricing influencers, and strategic negotiation techniques. By implementing these insights, B2B buyers can optimize their sourcing strategies and secure quality products that meet their specific needs while maintaining cost-effectiveness. Keep in mind that prices can fluctuate based on market conditions and regional factors, so always verify current pricing with suppliers.
Alternatives Analysis: Comparing acoustic panel supplier With Other Solutions
Understanding Alternatives to Acoustic Panel Suppliers
In today’s competitive business environment, international B2B buyers must consider multiple solutions to optimize their workspace acoustics. While acoustic panels are a popular choice for noise reduction and sound management, alternative methods may offer unique advantages depending on specific project needs, budget constraints, and implementation timelines. This analysis provides a comparative overview of acoustic panels against two viable alternatives: soundproofing materials and acoustic ceiling tiles.
Comparison Table of Acoustic Solutions
Comparison Aspect | Acoustic Panel Supplier | Soundproofing Materials | Acoustic Ceiling Tiles |
---|---|---|---|
Performance | Excellent at absorbing sound frequencies, reducing echoes effectively. | Superior sound isolation, particularly for high decibel levels. | Good for general sound absorption and reducing noise in open spaces. |
Cost | Moderate to high, depending on material and design. | Generally higher upfront costs due to specialized materials. | Moderate; typically more affordable than acoustic panels. |
Ease of Implementation | Easy to install with adhesive or mounting hardware; requires minimal tools. | Often requires professional installation, especially for dense materials. | Relatively simple to install, similar to standard ceiling tiles. |
Maintenance | Low maintenance; occasional cleaning may be needed. | Low maintenance; durable and resistant to wear. | Requires periodic cleaning; may need replacement if damaged. |
Best Use Case | Ideal for offices, studios, and home theaters where sound quality is paramount. | Best for industrial settings or environments with high noise levels, such as manufacturing plants. | Suitable for commercial spaces and schools to manage ambient noise levels. |
What Are the Benefits and Drawbacks of Soundproofing Materials?
Soundproofing materials, such as mass-loaded vinyl or specialized insulation, offer excellent sound isolation capabilities. They are particularly effective in environments where noise pollution is a significant concern, such as factories or urban settings with high traffic noise. However, the installation process can be complex, often requiring professional expertise, which can lead to higher costs. Additionally, soundproofing materials may not provide the aesthetic benefits that acoustic panels do, making them less desirable for public-facing spaces.
How Do Acoustic Ceiling Tiles Compare?
Acoustic ceiling tiles are another viable alternative, designed to absorb sound and reduce overall noise levels in a space. They are often used in commercial settings like offices and schools due to their cost-effectiveness and ease of installation. While they perform well in managing sound, they may not offer the same level of acoustic absorption as dedicated acoustic panels, particularly in environments requiring high sound quality. Maintenance is generally straightforward, but tiles can become stained or damaged over time, necessitating replacement.
Conclusion: How to Choose the Right Acoustic Solution for Your Needs
When selecting the most appropriate acoustic solution, B2B buyers should evaluate their specific operational requirements, budget constraints, and aesthetic preferences. Acoustic panels are ideal for environments that prioritize sound quality, such as recording studios or conference rooms. In contrast, soundproofing materials are better suited for high-noise environments, while acoustic ceiling tiles offer a balance of affordability and performance in typical commercial settings. By considering these factors, businesses can make informed decisions that enhance their acoustic environments while aligning with their overall operational goals.
Essential Technical Properties and Trade Terminology for acoustic panel supplier
What Are the Key Technical Properties of Acoustic Panels for B2B Buyers?
Understanding the technical specifications of acoustic panels is crucial for making informed purchasing decisions. Here are some essential properties that buyers should consider:
1. Material Grade
The grade of material used in acoustic panels significantly affects their sound absorption capabilities and durability. Common materials include fiberglass, foam, and wood. High-grade materials not only provide better acoustic performance but also enhance the longevity of the panels. For B2B buyers, selecting the right material grade ensures that the panels meet specific soundproofing requirements while fitting within budget constraints.
2. Sound Absorption Coefficient (SAC)
The Sound Absorption Coefficient quantifies how well a material absorbs sound at different frequencies, typically ranging from 0 (no absorption) to 1 (total absorption). Panels with a higher SAC are preferable for environments needing significant noise reduction, such as open offices or conference rooms. Buyers should request SAC ratings to ensure that the selected panels will effectively mitigate noise in their intended space.
3. Thickness
The thickness of acoustic panels directly influences their sound absorption capabilities. Thicker panels generally absorb lower frequencies better than thinner ones. When sourcing panels, it’s essential for buyers to consider the acoustic needs of their specific environment, as this will dictate the appropriate thickness required for optimal performance.
4. Fire Rating
Fire safety is a critical concern, especially in commercial spaces. Acoustic panels come with various fire ratings, often classified by standards such as ASTM E84 or EN 13501. B2B buyers must ensure that the panels meet local fire safety regulations, as this not only protects occupants but also complies with insurance requirements.
5. Tolerance Levels
Tolerance refers to the allowable variation in dimensions and performance specifications of the panels. Precise tolerances ensure that panels fit seamlessly within existing structures and perform consistently. For buyers, understanding tolerance levels is vital to avoid installation issues and ensure the desired acoustic performance is achieved.
What Are Common Trade Terms Used in the Acoustic Panel Industry?
Familiarizing yourself with industry terminology can enhance communication with suppliers and streamline the purchasing process. Here are some common terms to know:
1. OEM (Original Equipment Manufacturer)
An OEM is a company that produces parts or equipment that may be marketed by another manufacturer. In the context of acoustic panels, working with an OEM can allow buyers to customize products according to their specifications, which is particularly beneficial for large projects needing bespoke solutions.
2. MOQ (Minimum Order Quantity)
MOQ refers to the smallest quantity of a product that a supplier is willing to sell. Understanding MOQ is crucial for buyers, as it can affect budgeting and inventory management. Buyers should negotiate MOQs to align with their project needs without incurring unnecessary costs.
3. RFQ (Request for Quotation)
An RFQ is a document sent to suppliers requesting a quote for specific products or services. This is a standard practice in B2B transactions, allowing buyers to compare prices, terms, and conditions across multiple suppliers. A well-prepared RFQ can streamline the procurement process and ensure competitive pricing.
4. Incoterms (International Commercial Terms)
Incoterms are a set of predefined international trade terms that clarify the responsibilities of buyers and sellers regarding shipping, insurance, and tariffs. Familiarity with Incoterms can help buyers understand their obligations and rights in international transactions, reducing potential disputes and enhancing clarity in contracts.
5. Lead Time
Lead time refers to the time taken from placing an order to delivery. For B2B buyers, understanding lead times is essential for project planning and inventory management. Buyers should inquire about lead times during negotiations to ensure that they can meet their project deadlines without delays.
By grasping these technical properties and trade terms, international B2B buyers can navigate the acoustic panel market more effectively, ensuring that they make informed decisions that align with their operational needs and budget constraints.
Navigating Market Dynamics and Sourcing Trends in the acoustic panel supplier Sector
What Are the Current Market Dynamics and Key Trends in the Acoustic Panel Supplier Sector?
The acoustic panel supplier sector is experiencing significant transformation driven by global demand for improved sound environments in commercial, industrial, and residential spaces. Increasing urbanization, particularly in Africa, South America, and the Middle East, is boosting the need for effective noise control solutions. The rise of hybrid work models post-pandemic has further accelerated the demand for acoustic panels, as businesses seek to enhance workplace acoustics to support employee productivity.
Technological advancements are also shaping sourcing trends. The integration of smart technologies into acoustic panel manufacturing—such as sound-absorbing materials with embedded sensors—allows for real-time monitoring of sound levels and performance. Furthermore, the adoption of digital procurement platforms is streamlining the sourcing process for international buyers. These platforms facilitate access to a broader range of suppliers, allowing B2B buyers from regions like Europe and the Middle East to compare products and prices easily.
Additionally, there is a growing trend toward customization in acoustic solutions. Suppliers are increasingly offering tailored products that meet specific aesthetic and functional requirements of diverse markets. This trend provides an opportunity for buyers to collaborate closely with suppliers to create bespoke solutions that cater to their unique needs.
How Is Sustainability and Ethical Sourcing Impacting the Acoustic Panel Supplier Sector?
Sustainability is becoming a cornerstone of purchasing decisions in the acoustic panel sector. B2B buyers are increasingly aware of the environmental impact of their sourcing choices, prompting suppliers to adopt more sustainable practices. Acoustic panels made from recycled materials or sustainably sourced wood are gaining traction, as they help reduce the overall carbon footprint of construction and renovation projects.
Moreover, ethical sourcing is critical in establishing a responsible supply chain. Buyers are encouraged to seek suppliers who adhere to fair labor practices and environmental regulations. Certifications such as FSC (Forest Stewardship Council) for wood products and GREENGUARD for low chemical emissions provide assurance that the materials used are both environmentally friendly and socially responsible. This focus on sustainability not only enhances brand reputation but also aligns with the growing consumer demand for eco-friendly products.
Investing in suppliers that prioritize sustainability can lead to long-term cost savings through energy efficiency and waste reduction, making it an essential consideration for international buyers in regions like Africa and South America, where environmental regulations are evolving.
How Has the Acoustic Panel Supplier Sector Evolved Over Time?
The acoustic panel supplier sector has evolved significantly over the decades, transitioning from basic soundproofing solutions to sophisticated acoustic treatments that enhance sound quality and aesthetics. Initially focused on industrial applications, the market has expanded to encompass various sectors, including education, healthcare, and hospitality.
In recent years, the proliferation of design-oriented acoustic solutions has transformed the perception of acoustic panels from purely functional products to essential elements of interior design. This evolution reflects a broader trend in B2B markets where aesthetics and functionality are increasingly intertwined, prompting suppliers to innovate continually.
As international buyers navigate this dynamic market, understanding these trends and historical shifts will be crucial in making informed sourcing decisions that align with their business objectives and sustainability goals.
Frequently Asked Questions (FAQs) for B2B Buyers of acoustic panel supplier
-
How do I choose the right acoustic panel supplier for my business needs?
Selecting the right acoustic panel supplier requires a clear understanding of your specific needs, including the type of space you’re acoustically treating and your budget. Research potential suppliers by examining their product range, certifications, and customer reviews. It’s also beneficial to request samples to evaluate quality and performance. Engaging in direct communication with suppliers can provide insights into their responsiveness and willingness to customize products to meet your requirements. -
What are the key factors to consider when sourcing acoustic panels internationally?
When sourcing acoustic panels from international suppliers, consider factors such as material quality, acoustic performance ratings, and compliance with local regulations. Evaluate the supplier’s reputation in the market and their ability to provide after-sales support. Logistics and shipping times are crucial; ensure the supplier has reliable shipping methods to your region. Lastly, assess the total cost, including duties and taxes, to avoid unexpected expenses upon arrival. -
What customization options are available for acoustic panels?
Many suppliers offer customization options to cater to specific aesthetic and acoustic requirements. Customizations can include panel size, thickness, fabric types, and color choices. Some suppliers may also provide bespoke solutions tailored to unique architectural designs or specific sound absorption needs. Always communicate your requirements clearly and request a portfolio of past custom projects to gauge the supplier’s capability. -
What is the minimum order quantity (MOQ) for acoustic panels?
Minimum order quantities can vary significantly among suppliers. Some may have a low MOQ, ideal for small businesses or projects, while others may require larger orders to maintain competitive pricing. When sourcing, inquire about MOQs upfront and discuss potential flexibility, especially if you are considering a long-term partnership. This can help you manage inventory better and align with your project timelines. -
What payment terms should I expect when ordering acoustic panels?
Payment terms can differ based on the supplier’s policies and your negotiation skills. Common terms include upfront payments, 30- or 60-day payment periods post-delivery, or a combination of both. For international transactions, consider using secure payment methods such as letters of credit or escrow services to mitigate risks. Always clarify payment terms in the contract to avoid any misunderstandings later. -
How do I ensure quality assurance when sourcing acoustic panels?
To ensure quality assurance, request detailed product specifications and certifications from the supplier. Many reputable manufacturers provide third-party testing results that confirm their panels meet industry standards for sound absorption and fire safety. Additionally, consider establishing a quality control process where you can inspect samples before bulk orders. This proactive approach helps mitigate risks associated with product defects.
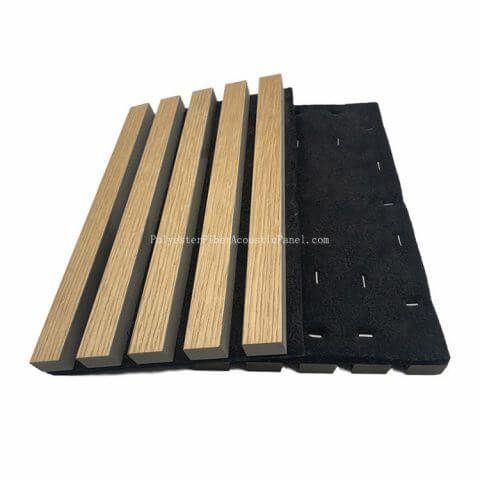
A stock image related to acoustic panel supplier.
-
What logistics considerations should I be aware of when importing acoustic panels?
When importing acoustic panels, logistics considerations include shipping methods, lead times, and customs clearance processes. Ensure the supplier has experience with international shipping and can provide necessary documentation for customs. Additionally, factor in potential delays due to port congestion or regulatory inspections. Collaborating with a reliable freight forwarder can help streamline the logistics process and ensure timely delivery. -
How can I assess the reputation of an acoustic panel supplier?
Assessing a supplier’s reputation involves researching their history, customer testimonials, and case studies. Utilize platforms like LinkedIn, industry forums, and trade shows to gather insights from other businesses that have worked with them. Additionally, consider reaching out to previous clients for direct feedback regarding their experiences. A supplier with a strong reputation typically demonstrates reliability, quality products, and excellent customer service, which are essential for long-term partnerships.
Important Disclaimer & Terms of Use
⚠️ Important Disclaimer
The information provided in this guide, including content regarding manufacturers, technical specifications, and market analysis, is for informational and educational purposes only. It does not constitute professional procurement advice, financial advice, or legal advice.
While we have made every effort to ensure the accuracy and timeliness of the information, we are not responsible for any errors, omissions, or outdated information. Market conditions, company details, and technical standards are subject to change.
B2B buyers must conduct their own independent and thorough due diligence before making any purchasing decisions. This includes contacting suppliers directly, verifying certifications, requesting samples, and seeking professional consultation. The risk of relying on any information in this guide is borne solely by the reader.
Strategic Sourcing Conclusion and Outlook for acoustic panel supplier
What Are the Key Takeaways for B2B Buyers in Acoustic Panel Sourcing?
In conclusion, strategic sourcing of acoustic panels offers significant advantages for international B2B buyers across diverse regions such as Africa, South America, the Middle East, and Europe. By prioritizing quality, supplier reliability, and cost-effectiveness, businesses can enhance their acoustic solutions while optimizing their budgets. Engaging with suppliers who understand local market dynamics and can provide tailored solutions is crucial for successful implementation.
How Can Strategic Sourcing Impact Your Business Growth?
The value of strategic sourcing extends beyond immediate cost savings; it fosters long-term partnerships that can lead to innovation and enhanced product offerings. Buyers are encouraged to leverage data-driven insights and market trends to inform their procurement strategies. This approach not only mitigates risks but also positions businesses for future growth in an increasingly competitive landscape.
What Should International B2B Buyers Do Next?
As you navigate the sourcing landscape for acoustic panels, consider establishing a robust evaluation framework that includes supplier audits and performance metrics. By doing so, you can ensure that your chosen partners align with your strategic goals. Looking ahead, the demand for high-quality acoustic solutions is expected to grow, making now the ideal time to refine your sourcing strategies. Take action today to secure partnerships that will drive your business forward in a dynamic market.