The Ultimate Guide to Aluminum Composite Panel Supplier (2025)
Introduction: Navigating the Global Market for aluminum composite panel supplier
Navigating the complexities of sourcing aluminum composite panels can be a daunting task for international B2B buyers, especially those operating in diverse markets such as Africa, South America, the Middle East, and Europe. The challenge often lies in identifying reliable suppliers who not only meet quality standards but also understand regional regulations and market dynamics. This guide serves as a comprehensive resource for those looking to streamline their procurement process for aluminum composite panel suppliers.
We delve into the various types of aluminum composite panels available on the market, their applications in sectors ranging from construction to signage, and critical factors to consider when vetting potential suppliers. Additionally, we explore cost structures and pricing strategies, ensuring that buyers can make informed financial decisions. By providing actionable insights and practical tips, this guide empowers B2B buyers from countries like Brazil and Poland to navigate the global marketplace effectively.
With a focus on enhancing procurement strategies, we aim to equip buyers with the knowledge necessary to foster successful partnerships with reputable suppliers. Whether you are looking for specific product specifications or ways to enhance your supply chain efficiency, this guide will serve as your go-to reference for all things related to aluminum composite panels.
Understanding aluminum composite panel supplier Types and Variations
Type Name | Key Distinguishing Features | Primary B2B Applications | Brief Pros & Cons for Buyers |
---|---|---|---|
Standard Aluminum Composite Panels | Lightweight, durable, and cost-effective. Typically consists of two aluminum sheets enclosing a non-aluminum core. | Facades, interior walls, and signage. | Pros: Affordable, versatile. Cons: Limited insulation properties. |
Fire-Resistant Aluminum Composite Panels | Designed with a fire-retardant core material, enhancing safety in construction. | High-rise buildings, public spaces, and airports. | Pros: Enhanced safety, meets strict building codes. Cons: Higher cost than standard panels. |
High-Performance Aluminum Composite Panels | Superior thermal insulation and soundproofing features. Often includes a thicker core and advanced coatings. | Commercial buildings, hotels, and hospitals. | Pros: Energy-efficient, excellent durability. Cons: Higher investment required. |
Eco-Friendly Aluminum Composite Panels | Made from recycled materials and designed for sustainability. | Green building projects, eco-friendly developments. | Pros: Sustainable choice, potential tax incentives. Cons: Limited availability, may be pricier. |
Custom Aluminum Composite Panels | Tailored designs and sizes to meet specific project requirements. | Architectural projects, branding applications. | Pros: Unique aesthetics, tailored solutions. Cons: Longer lead times, potentially higher costs. |
What are Standard Aluminum Composite Panels and Their B2B Relevance?
Standard aluminum composite panels are the most commonly used type, known for their lightweight and durability. These panels typically consist of two thin layers of aluminum enclosing a non-aluminum core, making them an economical choice for various applications. B2B buyers often leverage these panels for facades, interior walls, and signage due to their versatility and affordability. However, they may not provide adequate insulation, which is a crucial consideration for projects requiring thermal efficiency.
How Do Fire-Resistant Aluminum Composite Panels Enhance Safety?
Fire-resistant aluminum composite panels are specifically engineered with a fire-retardant core, making them essential for high-rise buildings and public spaces. These panels comply with stringent building codes aimed at enhancing safety. B2B buyers in sectors such as construction and architecture prioritize these panels for their superior safety features. However, they come at a higher cost than standard panels, which buyers must weigh against the safety benefits.
Why Choose High-Performance Aluminum Composite Panels?
High-performance aluminum composite panels are designed for applications requiring superior thermal insulation and soundproofing. Featuring a thicker core and advanced coatings, these panels are ideal for commercial buildings, hotels, and hospitals where energy efficiency is a priority. While they offer excellent durability and insulation, the investment required is significantly higher, making them suitable for projects with long-term financial considerations.
What Are the Benefits of Eco-Friendly Aluminum Composite Panels?
Eco-friendly aluminum composite panels are manufactured from recycled materials and are designed with sustainability in mind. They are increasingly popular in green building projects and eco-friendly developments, appealing to B2B buyers looking to enhance their sustainability credentials. While these panels may offer potential tax incentives, their availability can be limited, and they may come at a higher price point.
How Do Custom Aluminum Composite Panels Meet Specific Needs?
Custom aluminum composite panels provide tailored designs and sizes, allowing businesses to meet specific project requirements. These panels are particularly valuable in architectural projects and branding applications where unique aesthetics are critical. While they offer the advantage of customization, buyers should consider longer lead times and potentially higher costs associated with bespoke solutions.
Related Video: Production process of aluminum composite panel
Key Industrial Applications of aluminum composite panel supplier
Industry/Sector | Specific Application of aluminum composite panel supplier | Value/Benefit for the Business | Key Sourcing Considerations for this Application |
---|---|---|---|
Building & Construction | Facade cladding for commercial and residential buildings | Enhances aesthetic appeal, improves insulation, and reduces maintenance costs | Ensure compliance with local building codes and standards |
Transportation | Interior wall panels for buses and trains | Lightweight, durable, and easy to clean, improving passenger comfort | Assess fire safety ratings and durability under varying conditions |
Signage and Advertising | Outdoor and indoor signage | High visibility, weather-resistant, and customizable for branding | Consider color fastness and surface finishes for longevity |
Aerospace | Aircraft interior panels | Lightweight and corrosion-resistant, contributing to fuel efficiency | Verify compliance with aviation safety standards |
Electronics & Appliances | Housing for electronic devices | Provides protection while maintaining lightweight and thermal properties | Look for EMI shielding capabilities and thermal management features |
What are the Key Applications of Aluminum Composite Panels in Building & Construction?
Aluminum composite panels (ACP) serve as a versatile solution in the building and construction industry, particularly for facade cladding. These panels not only enhance the aesthetic appeal of commercial and residential buildings but also provide excellent insulation properties, reducing energy costs. International buyers must ensure that the ACP they source complies with local building codes, particularly in regions with stringent fire safety regulations, such as Europe and the Middle East.
How are Aluminum Composite Panels Used in Transportation?
In the transportation sector, aluminum composite panels are widely used for interior wall applications in buses and trains. Their lightweight nature contributes to improved fuel efficiency, while their durability ensures they withstand the rigors of daily use. Additionally, these panels are easy to clean, enhancing passenger comfort. Buyers should prioritize sourcing panels that meet fire safety ratings and can endure varying environmental conditions, especially in regions with extreme weather like Africa and South America.
What Role Do Aluminum Composite Panels Play in Signage and Advertising?
For signage and advertising, aluminum composite panels are favored for their high visibility and weather resistance. They can be customized with vibrant colors and graphics, making them ideal for both indoor and outdoor applications. When sourcing these panels, businesses should consider the longevity of the surface finishes and color fastness to ensure that their branding remains impactful over time. This is particularly important for international buyers in regions with high UV exposure, such as Africa and South America.
How are Aluminum Composite Panels Beneficial in the Aerospace Industry?
In the aerospace industry, aluminum composite panels are essential for aircraft interiors, where their lightweight and corrosion-resistant properties contribute to fuel efficiency. These panels help reduce the overall weight of the aircraft, which is crucial for performance. Buyers must verify that the materials sourced comply with aviation safety standards, ensuring reliability and safety in critical applications.
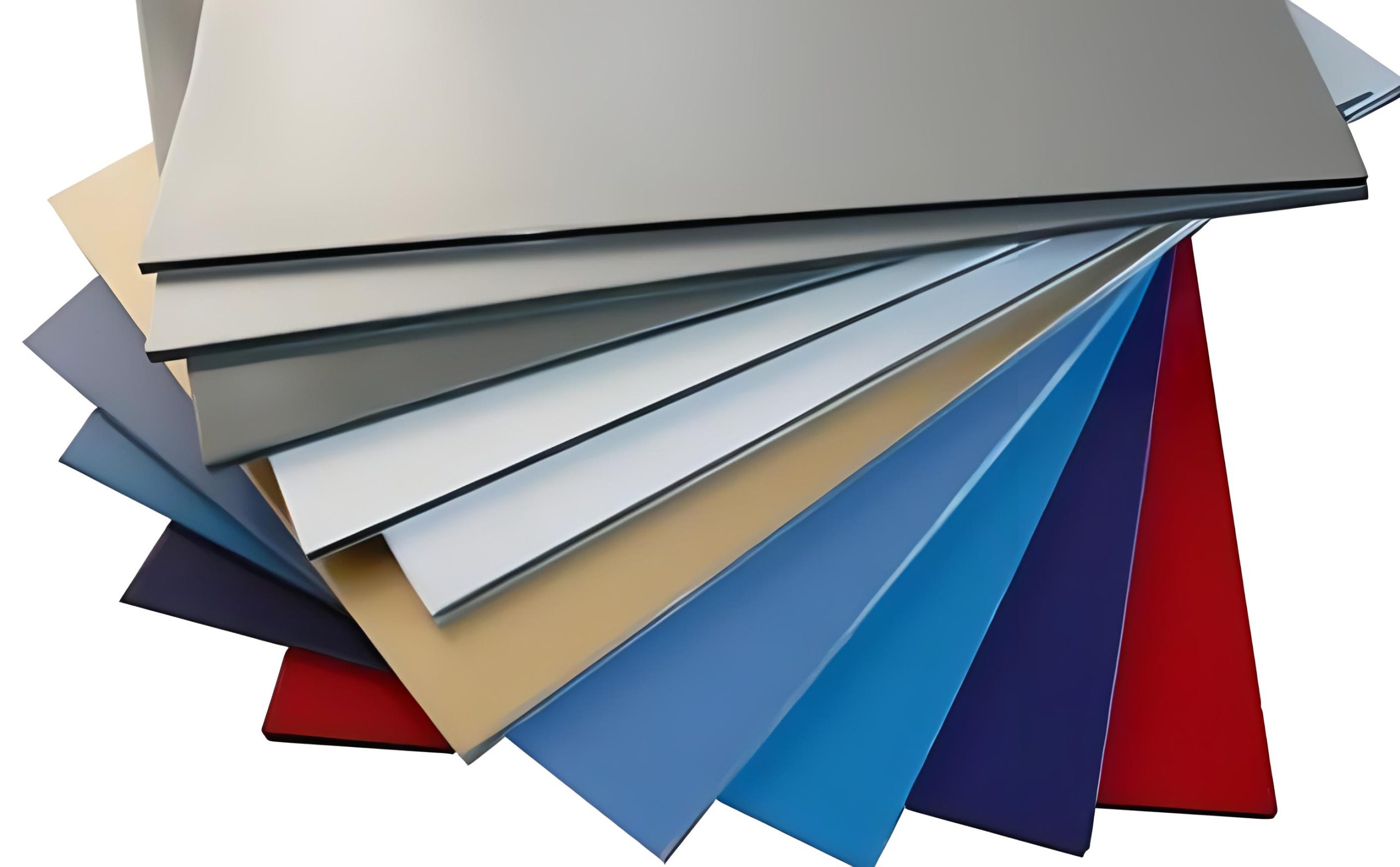
A stock image related to aluminum composite panel supplier.
What are the Advantages of Aluminum Composite Panels in Electronics & Appliances?
Aluminum composite panels are also utilized in the housing of electronic devices, providing protection while maintaining lightweight and thermal properties. This is vital in enhancing the performance and longevity of electronic products. When sourcing for this application, businesses should look for features such as electromagnetic interference (EMI) shielding and effective thermal management capabilities, which are essential for international buyers in technology-driven markets across Europe and South America.
Related Video: aluminum composite panel installation toturial
3 Common User Pain Points for ‘aluminum composite panel supplier’ & Their Solutions
Scenario 1: Difficulty in Finding Reliable Suppliers
The Problem: B2B buyers, especially in emerging markets like Africa and South America, often struggle to identify reliable aluminum composite panel suppliers. These regions may have limited access to international markets, and buyers frequently face challenges related to the quality of products, shipping reliability, and after-sales service. This can lead to delays in project timelines, increased costs, and potential reputational damage for companies that rely on these materials for construction or manufacturing.
The Solution: To overcome this challenge, B2B buyers should invest time in conducting thorough research on potential suppliers. This includes checking for certifications that validate quality, such as ISO 9001, and seeking suppliers with a proven track record in international shipping. Engaging in forums or industry-specific groups can provide insights into supplier reputations. Additionally, requesting samples before making a bulk order can help assess product quality firsthand. Establishing clear communication channels with suppliers and asking about their logistics capabilities can further ensure that the selected supplier can meet delivery timelines.
Scenario 2: Navigating Product Specifications and Compliance
The Problem: Another common issue faced by B2B buyers is understanding the various specifications and compliance requirements associated with aluminum composite panels. Different regions have unique building codes and safety regulations, which can vary significantly between Europe, the Middle East, and South America. Without adequate knowledge, buyers risk purchasing panels that do not meet local regulations, leading to costly project delays and potential legal issues.
The Solution: To navigate these complexities, buyers should engage with local experts or consultants who specialize in construction materials and compliance. Additionally, suppliers should provide detailed product datasheets that outline compliance with regional standards. Buyers are encouraged to ask suppliers about their products’ fire ratings, thermal insulation properties, and environmental certifications. Utilizing a checklist based on local regulations can streamline the procurement process, ensuring that all necessary standards are met before making a purchase.
Scenario 3: Cost Control and Budget Overruns
The Problem: Cost management is a critical concern for B2B buyers when sourcing aluminum composite panels. Unexpected price fluctuations due to market demand, raw material costs, or currency exchange rates can lead to budget overruns, which is particularly challenging in projects with tight financial constraints. This can create tension between project managers and finance departments, affecting overall project feasibility.
The Solution: To effectively manage costs, buyers should consider establishing long-term contracts with suppliers that include price guarantees or fixed pricing over a specified period. This can help mitigate the impact of sudden market changes. Furthermore, buyers should conduct market research to understand pricing trends and negotiate based on bulk purchasing power. Engaging multiple suppliers for quotes can also provide leverage in negotiations. Implementing a contingency budget within the overall project budget can provide a buffer against unforeseen costs, ensuring that projects remain financially viable even when unexpected challenges arise.
Strategic Material Selection Guide for aluminum composite panel supplier
What Are the Key Materials for Aluminum Composite Panels?
When selecting materials for aluminum composite panels (ACPs), international B2B buyers should consider several common materials that significantly influence performance, durability, and cost. Below, we analyze four prevalent materials used in ACP production: Aluminum, Polyethylene, Fire-Retardant Core, and Mineral Core. Each material has unique properties, advantages, and limitations that can affect the final product’s suitability for specific applications.
How Does Aluminum Impact Performance in ACPs?
Aluminum is the primary material used in ACPs, known for its lightweight and corrosion-resistant properties. It typically has a temperature rating of up to 600°F (315°C) and can withstand significant pressure without deforming.
Pros:
– Durability: Aluminum is highly resistant to corrosion and weathering, making it suitable for outdoor applications.
– Malleability: It can be easily shaped and formed during manufacturing, allowing for versatile design options.
Cons:
– Cost: While generally affordable, high-quality aluminum can be more expensive than other materials.
– Thermal Conductivity: Aluminum can conduct heat, which may necessitate additional insulation in certain applications.
Impact on Application: Aluminum’s compatibility with various coatings and finishes makes it ideal for aesthetic applications in architecture and signage.
Considerations for International Buyers: Compliance with standards such as ASTM and DIN is crucial. Buyers should also consider local sourcing to mitigate costs associated with import duties.
What Role Does Polyethylene Play in ACPs?
Polyethylene (PE) is often used as the core material in ACPs. It is lightweight and offers good insulation properties, making it a popular choice for interior applications.
Pros:
– Cost-Effective: PE is generally less expensive than other core materials.
– Lightweight: This property aids in reducing transportation costs and simplifies installation.
Cons:
– Flammability: PE is less fire-resistant compared to other core materials, which may limit its use in certain applications.
– Lower Durability: It may not withstand harsh environmental conditions as effectively as other materials.
Impact on Application: PE is suitable for indoor signage and decorative panels but may not meet fire safety standards in some regions.
Considerations for International Buyers: Buyers should ensure that PE panels comply with local fire safety regulations, especially in regions with strict building codes.
Why Choose Fire-Retardant Core for ACPs?
Fire-retardant core materials are designed to enhance the fire resistance of ACPs, making them suitable for high-risk applications.
Pros:
– Enhanced Safety: These materials significantly reduce the risk of fire spread, making them ideal for commercial and public buildings.
– Compliance: Often meets stringent international fire safety standards.
Cons:
– Higher Cost: Fire-retardant cores typically come at a premium compared to standard cores.
– Manufacturing Complexity: The production process may be more complex, affecting lead times.
Impact on Application: Suitable for high-rise buildings, schools, and hospitals where fire safety is paramount.
Considerations for International Buyers: Buyers should verify compliance with local fire safety codes, such as those outlined by NFPA or local authorities.
What Advantages Do Mineral Core Materials Offer?
Mineral core materials provide excellent fire resistance and durability, making them a robust choice for ACPs.
Pros:
– Superior Fire Resistance: Mineral cores can withstand high temperatures and do not contribute to fire spread.
– Durability: They are resistant to impact and weathering, suitable for various climates.
Cons:
– Weight: Mineral cores are heavier than other options, which can increase transportation and installation costs.
– Higher Cost: The production process and raw materials can make them more expensive.
Impact on Application: Ideal for applications requiring high fire safety standards, such as airports and public buildings.
Considerations for International Buyers: Ensure compliance with local building codes and standards, as regulations vary significantly across regions.
Summary Table of Material Selection for Aluminum Composite Panels
Material | Typical Use Case for Aluminum Composite Panel Supplier | Key Advantage | Key Disadvantage/Limitation | Relative Cost (Low/Med/High) |
---|---|---|---|---|
Aluminum | Architectural facades, signage, and decorative panels | Lightweight and corrosion-resistant | Higher thermal conductivity | Medium |
Polyethylene | Indoor signage and decorative panels | Cost-effective and lightweight | Lower fire resistance | Low |
Fire-Retardant Core | High-rise buildings, schools, hospitals | Enhanced fire safety | Higher cost and manufacturing complexity | High |
Mineral Core | Airports and public buildings | Superior fire resistance | Increased weight and cost | High |
This guide provides a comprehensive overview of the materials used in aluminum composite panels, helping international B2B buyers make informed decisions based on their specific needs and regional compliance requirements.
In-depth Look: Manufacturing Processes and Quality Assurance for aluminum composite panel supplier
What Are the Typical Manufacturing Processes for Aluminum Composite Panels?
Understanding the manufacturing processes of aluminum composite panels is essential for international B2B buyers. This knowledge not only aids in selecting the right supplier but also ensures that the product meets specific quality and durability standards. The manufacturing process generally involves several key stages: material preparation, forming, assembly, and finishing.
What Is Involved in Material Preparation for Aluminum Composite Panels?
The first step in the manufacturing process is material preparation. This involves sourcing high-quality aluminum sheets and a core material, typically made of polyethylene or mineral-filled materials, which provides insulation and fire resistance.
- Aluminum Sheets: Buyers should look for suppliers who use aluminum that conforms to international standards, such as ASTM B209 or EN 573. This ensures that the material has the necessary strength and durability for construction applications.
- Core Material: Depending on the intended use of the panels, the core material should comply with fire safety regulations, especially in regions with stringent building codes.
How Are Aluminum Composite Panels Formed?
Once the materials are prepared, the next step is forming. This stage involves cutting the aluminum sheets and core material to size and bonding them together.
- Bonding Techniques: The most common bonding methods include adhesive bonding and co-extrusion. Buyers should inquire about the adhesive types used, as some adhesives provide better durability and weather resistance than others.
- Cutting and Shaping: Advanced CNC machines are often used for precision cutting, ensuring that the panels meet exact specifications. This technology minimizes waste and enhances the consistency of the product.
What Does the Assembly Process Entail?
After forming, the panels move to the assembly stage. This involves joining multiple panels or integrating additional features, such as insulation or decorative finishes.
- Joining Techniques: Look for suppliers that employ reliable joining techniques, such as rivets or welding, which can significantly affect the panel’s structural integrity.
- Custom Options: Many suppliers offer customization options, including different colors, finishes, and textures. Buyers should ensure that these options meet their specific project requirements.
How Is the Finishing Process Conducted?
The final stage in the manufacturing process is finishing, which enhances the panels’ aesthetics and protects them from environmental factors.
- Surface Treatments: Common treatments include anodizing, painting, or applying protective films. Buyers should request information on the durability of these finishes, especially in relation to local climate conditions.
- Quality Control: A reputable supplier will conduct quality checks during the finishing process to ensure that the panels meet aesthetic and functional standards.
What Quality Assurance Standards Should B2B Buyers Consider?
Quality assurance is crucial in the production of aluminum composite panels. International buyers should be familiar with various quality standards and checkpoints that suppliers must adhere to.
What International Standards Apply to Aluminum Composite Panels?
International standards such as ISO 9001 ensure that manufacturers implement a quality management system focused on customer satisfaction and continuous improvement.
- ISO 9001 Certification: This certification indicates that the supplier has met rigorous quality management criteria, which can help mitigate risks associated with product defects.
- CE Marking: For buyers in Europe, CE marking signifies that the product meets EU safety, health, and environmental requirements, ensuring compliance for market entry.
What Are the Industry-Specific Standards for Quality Control?
In addition to general quality standards, specific industry standards may apply, such as:
- API Standards: For panels used in the oil and gas industry, compliance with American Petroleum Institute (API) standards is essential.
- Fire Safety Standards: Depending on the application, panels may need to meet fire safety regulations like EN 13501-1 in Europe or ASTM E84 in the U.S.
How Are Quality Control Checkpoints Implemented?
Quality control checkpoints are critical in ensuring that the manufacturing process meets required standards.
- Incoming Quality Control (IQC): This checkpoint evaluates raw materials upon arrival to confirm they meet specified standards.
- In-Process Quality Control (IPQC): Continuous monitoring during the manufacturing process helps identify defects early, minimizing waste and ensuring consistency.
- Final Quality Control (FQC): This final inspection checks the completed panels for adherence to specifications and quality standards before shipment.
How Can B2B Buyers Verify Supplier Quality Control?
Verification of a supplier’s quality control processes is essential for B2B buyers, especially in international transactions.
What Methods Can Buyers Use to Verify Quality Control?
- Supplier Audits: Conducting regular audits of potential suppliers can help buyers assess their quality management practices and compliance with international standards.
- Requesting Quality Reports: Buyers should ask for quality control documentation, including test reports and certifications, to verify compliance with relevant standards.
- Third-Party Inspections: Engaging third-party inspection services can provide an unbiased evaluation of the supplier’s quality control processes and product quality.
What Are the Quality Control Nuances for International B2B Buyers?
For international buyers, particularly from regions such as Africa, South America, the Middle East, and Europe, understanding the nuances of quality control can be complex.
- Regional Regulations: Buyers must be aware of local regulations that may affect product acceptance and compliance. For instance, South American countries may have specific import regulations that differ from those in Europe.
- Communication Barriers: Language and cultural differences can pose challenges in understanding quality standards and supplier capabilities. It is advisable to work with local intermediaries or representatives who can facilitate effective communication.
By understanding these manufacturing processes and quality assurance practices, international B2B buyers can make informed decisions when selecting aluminum composite panel suppliers, ensuring that they receive high-quality products that meet their specific needs.
Practical Sourcing Guide: A Step-by-Step Checklist for ‘aluminum composite panel supplier’
In the competitive landscape of aluminum composite panel procurement, having a structured approach is essential for international B2B buyers. This checklist serves as a practical guide to help you navigate the sourcing process effectively, ensuring that you select a reliable supplier that meets your specific needs.
Step 1: Define Your Technical Specifications
Before reaching out to potential suppliers, clearly outline your technical requirements for aluminum composite panels. Consider factors such as panel thickness, size, color, fire resistance ratings, and insulation properties. This step is crucial as it sets the foundation for your procurement process and helps suppliers understand your needs.
Step 2: Conduct Market Research on Suppliers
Investigate potential suppliers by researching their reputation within the industry. Look for reviews, testimonials, and case studies that showcase their experience and reliability. Utilize platforms like LinkedIn and industry-specific forums to gather insights from other buyers, which can help you identify reputable suppliers.
Step 3: Verify Supplier Certifications
Ensure that the suppliers you consider hold relevant certifications and comply with international standards, such as ISO 9001 for quality management and ASTM standards for materials. Certifications not only demonstrate a supplier’s commitment to quality but also ensure that their products meet safety and regulatory requirements.
Step 4: Request Samples for Evaluation
Before making any commitments, ask for samples of the aluminum composite panels. Evaluating samples allows you to assess the quality, finish, and durability of the materials firsthand. Pay attention to the panel’s weight, surface finish, and any customizations you might require.
Step 5: Evaluate Supplier Production Capabilities
Assess the supplier’s production capabilities to ensure they can meet your order volume and delivery timelines. Inquire about their manufacturing processes, technology used, and lead times for production. This information is vital for avoiding potential delays in your project.
Step 6: Discuss Pricing and Payment Terms
Engage in transparent discussions regarding pricing structures and payment terms. Request detailed quotes that break down costs, including shipping and any additional fees. Understanding payment terms, such as deposits or credit options, can significantly impact your cash flow and project budgeting.
Step 7: Assess After-Sales Support and Warranty
Finally, inquire about the after-sales support the supplier offers, including warranty policies and customer service. A strong warranty can protect your investment, while responsive customer service ensures that any issues that arise post-purchase are handled efficiently. This step is crucial for long-term satisfaction and reliability in your sourcing relationship.
By following these steps, international B2B buyers can strategically approach the procurement of aluminum composite panels, ensuring they partner with reliable suppliers that meet their specific requirements.
Comprehensive Cost and Pricing Analysis for aluminum composite panel supplier Sourcing
When sourcing aluminum composite panels (ACP), understanding the comprehensive cost structure and pricing dynamics is essential for international B2B buyers. The following insights will help you navigate this complex landscape, particularly if you’re buying from regions like Africa, South America, the Middle East, and Europe.
What Are the Key Cost Components in Aluminum Composite Panel Sourcing?
The total cost of aluminum composite panels involves several critical components:
-
Materials: The primary costs arise from the aluminum and core materials used in ACP production. Prices can fluctuate based on global aluminum market trends, which are influenced by supply chain disruptions, tariffs, and geopolitical factors.
-
Labor: Labor costs vary significantly by region. In countries with higher labor costs, such as those in Western Europe, the overall price may be higher compared to suppliers in Eastern Europe or South America.
-
Manufacturing Overhead: This includes costs associated with running the manufacturing facility, such as utilities, maintenance, and equipment depreciation. Efficient production processes can mitigate overhead costs.
-
Tooling: Tooling costs are incurred for custom molds and machinery needed for specific panel designs. Customization typically increases tooling expenses, which should be factored into the pricing.
-
Quality Control (QC): Investing in rigorous QC processes ensures that the panels meet international standards and specifications. While this may raise upfront costs, it reduces the risk of defects and returns, ultimately saving money in the long run.
-
Logistics: Transportation costs can vary significantly based on distance, shipping methods, and Incoterms. Buyers should consider both domestic and international shipping costs when evaluating suppliers.
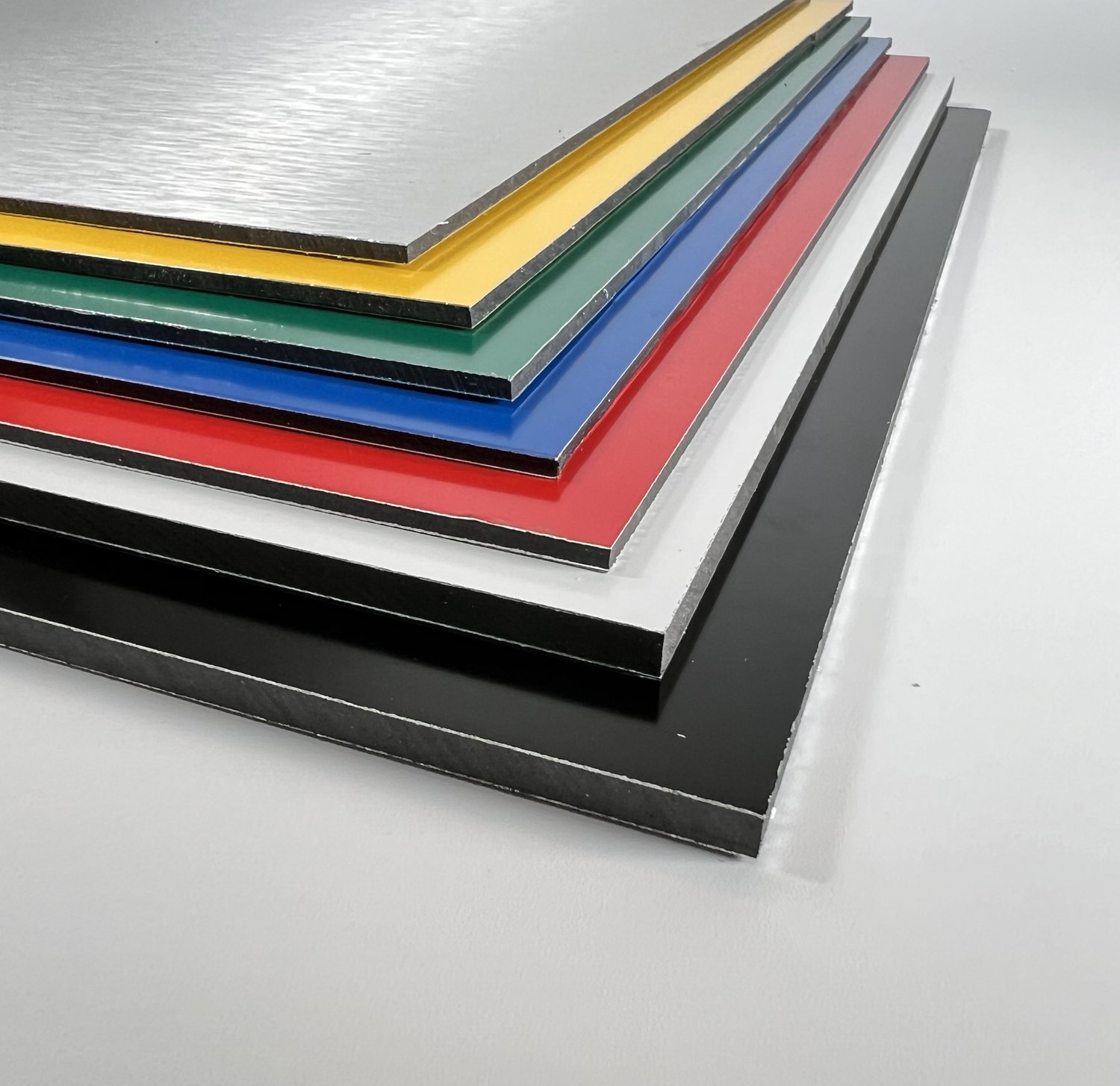
A stock image related to aluminum composite panel supplier.
- Margin: Suppliers typically add a profit margin to cover their operational costs and ensure profitability. This margin can vary widely based on market competition and the supplier’s positioning.
What Influences Pricing in Aluminum Composite Panel Supply?
Several factors can influence the pricing of aluminum composite panels:
-
Volume and Minimum Order Quantity (MOQ): Suppliers often provide better pricing for larger orders. Understanding the MOQ can help you negotiate better terms.
-
Specifications and Customization: Custom specifications can significantly increase costs due to the additional tooling and labor involved. Standard products generally have a lower price point.
-
Materials Quality and Certifications: High-quality materials and adherence to international certifications (e.g., ISO, ASTM) can increase costs but also ensure better durability and performance.
-
Supplier Factors: Established suppliers with a good reputation may charge a premium for their products. However, this could translate into better service and support.
-
Incoterms: The choice of Incoterms can greatly impact overall costs. Terms like CIF (Cost, Insurance, and Freight) will include shipping and insurance in the price, while FOB (Free on Board) may require additional logistics costs to be accounted for by the buyer.
What Are the Best Buyer Tips for Cost-Efficiency?
For international B2B buyers, particularly from Africa, South America, the Middle East, and Europe, consider the following strategies to enhance cost-efficiency:
-
Negotiate Terms: Always negotiate pricing and payment terms. Leverage your buying power, especially if you are placing a large order or establishing a long-term partnership.
-
Assess Total Cost of Ownership (TCO): When evaluating suppliers, consider not just the initial purchase price but also the lifetime costs associated with maintenance, installation, and potential replacements.
-
Understand Pricing Nuances: Be aware that regional economic conditions, currency fluctuations, and local trade policies can affect pricing. Engage with suppliers who are transparent about how these factors influence their pricing.
-
Explore Local Suppliers: Depending on your location, sourcing from local suppliers can reduce shipping costs and lead times, making it easier to manage your supply chain.
Conclusion
Navigating the complexities of sourcing aluminum composite panels requires a deep understanding of cost structures and pricing influencers. By leveraging this knowledge, B2B buyers can make informed decisions that enhance their procurement strategies and optimize their overall costs. Always remember to ask for indicative pricing from multiple suppliers to compare and find the best deal tailored to your specific needs.
Alternatives Analysis: Comparing aluminum composite panel supplier With Other Solutions
In the competitive landscape of building materials, international B2B buyers must evaluate various options to find the most suitable solution for their projects. Aluminum composite panels (ACP) are widely recognized for their durability and aesthetic appeal. However, buyers should also consider alternative materials and technologies that may offer different benefits. This analysis provides a comparative look at aluminum composite panel suppliers alongside other viable alternatives, such as fiber-reinforced plastic (FRP) panels and traditional metal cladding.
Comparison Table of Aluminum Composite Panels and Alternatives
Comparison Aspect | Aluminum Composite Panel Supplier | Fiber-Reinforced Plastic (FRP) Panels | Traditional Metal Cladding |
---|---|---|---|
Performance | High durability, weather-resistant | Excellent impact resistance, lightweight | Strong, durable, good fire resistance |
Cost | Moderate to high | Generally lower than ACP | Varies widely, often moderate |
Ease of Implementation | Requires specialized installation | Easier to install, can be DIY | Can be complex, requires skilled labor |
Maintenance | Low maintenance, easy to clean | Low maintenance, resistant to corrosion | Moderate; requires regular inspections |
Best Use Case | Architectural facades, signage | Industrial applications, interiors | Commercial buildings, industrial facilities |
What are the Benefits and Drawbacks of Fiber-Reinforced Plastic (FRP) Panels?
Fiber-reinforced plastic (FRP) panels are a lightweight alternative that excels in applications requiring high impact resistance. Their flexibility allows for easier installation, which can often be performed without specialized labor, making them appealing for quick turnarounds. However, while FRP panels are generally less expensive, they may not match the aesthetic appeal of aluminum composites, which can limit their use in high-end architectural projects. Additionally, FRP may have lower fire resistance compared to metal options, which is a critical factor in certain applications.
How Does Traditional Metal Cladding Compare to Aluminum Composite Panels?
Traditional metal cladding, such as steel or zinc, offers strong durability and excellent fire resistance, making it suitable for industrial and commercial buildings. It can also provide a classic look that some clients prefer. However, the installation process can be complex, requiring skilled labor and more time compared to aluminum composites. Furthermore, traditional cladding may require more maintenance over time, particularly in corrosive environments. While the initial cost can vary, the long-term investment must be considered in the context of maintenance and replacement.
How Can B2B Buyers Choose the Right Solution for Their Needs?
When selecting a building material, B2B buyers should assess their specific project requirements, including budget constraints, aesthetic preferences, and functional needs. Aluminum composite panels offer a balance of durability and design flexibility, making them ideal for architectural projects. In contrast, FRP panels may be better suited for industrial applications where impact resistance is paramount, while traditional metal cladding can provide a robust solution for commercial settings. Evaluating these alternatives based on performance, cost, implementation ease, and maintenance will enable buyers to make informed decisions that align with their project goals. By considering the unique attributes of each option, businesses can ensure they select the most appropriate solution for their construction needs.
Essential Technical Properties and Trade Terminology for aluminum composite panel supplier
What Are the Key Technical Properties of Aluminum Composite Panels?
When evaluating aluminum composite panels (ACP) for your projects, understanding their technical properties is essential. Here are some critical specifications that influence the performance, durability, and application of these materials:
-
Material Grade
– Definition: This refers to the alloy of aluminum used in the panels, commonly 3003 or 5005 grades.
– B2B Importance: Different grades offer varying levels of strength, corrosion resistance, and weight. Choosing the right grade is crucial for ensuring that the panels meet structural and aesthetic requirements for your specific application. -
Panel Thickness
– Definition: The overall thickness of the ACP, typically ranging from 3mm to 6mm.
– B2B Importance: Thickness affects the panel’s rigidity and insulation properties. For instance, thicker panels provide better thermal insulation and durability, making them ideal for external cladding in regions with extreme weather conditions. -
Fire Rating
– Definition: This indicates how well the material resists fire and how long it can withstand flames before igniting.
– B2B Importance: Compliance with local building codes regarding fire safety is critical. Panels with a higher fire rating (like A2 or B1) are often required for commercial buildings, ensuring safety and insurance compliance. -
Surface Finish
– Definition: The finish applied to the surface of the panels, such as PVDF (polyvinylidene fluoride) or PE (polyethylene).
– B2B Importance: The choice of surface finish affects both aesthetics and longevity. PVDF coatings offer superior UV resistance and color retention, making them suitable for outdoor applications where exposure to sunlight is prevalent. -
Tolerance Levels
– Definition: This refers to the allowable deviation from specified dimensions.
– B2B Importance: Tolerance levels ensure that the panels fit correctly during installation. High precision in manufacturing leads to fewer complications on-site, reducing labor costs and time delays.
What Are Common Trade Terms in the Aluminum Composite Panel Industry?
Understanding industry jargon can streamline communication and negotiations with suppliers. Here are some common terms you should know:
-
OEM (Original Equipment Manufacturer)
– Definition: A company that produces parts or equipment that may be marketed by another manufacturer.
– Relevance: Knowing whether a supplier is an OEM can help assess the quality and reliability of the panels, as OEMs typically adhere to higher manufacturing standards. -
MOQ (Minimum Order Quantity)
– Definition: The smallest number of units a supplier is willing to sell.
– Relevance: Understanding MOQ is crucial for budget planning and inventory management. If the MOQ is higher than your immediate needs, it may lead to excess inventory costs. -
RFQ (Request for Quotation)
– Definition: A document sent to suppliers requesting price and terms for a specific quantity of products.
– Relevance: Sending an RFQ helps you gather competitive pricing and terms from multiple suppliers, enabling better negotiation outcomes. -
Incoterms (International Commercial Terms)
– Definition: A set of predefined international trade terms published by the International Chamber of Commerce (ICC) that clarifies the responsibilities of buyers and sellers.
– Relevance: Familiarity with Incoterms is essential for understanding shipping costs, risks, and responsibilities. Common terms include FOB (Free on Board) and CIF (Cost, Insurance, and Freight), which dictate who bears the costs and risks during transit. -
Lead Time
– Definition: The time taken from placing an order to the delivery of the product.
– Relevance: Knowing the lead time is vital for project planning and scheduling. Suppliers with shorter lead times can help you meet tight deadlines.
By understanding these technical properties and trade terms, B2B buyers can make informed decisions when sourcing aluminum composite panels, ensuring that they choose the right products for their projects while optimizing costs and timelines.
Navigating Market Dynamics and Sourcing Trends in the aluminum composite panel supplier Sector
What Are the Current Market Dynamics and Key Trends in the Aluminum Composite Panel Supplier Sector?
The aluminum composite panel (ACP) market is experiencing significant growth, driven by the rising demand for lightweight and durable materials in construction and interior applications. Global urbanization, particularly in Africa and South America, is pushing the need for modern building solutions, while stringent building codes in Europe and the Middle East are emphasizing the importance of safety and sustainability. This shift is leading to increased interest in aluminum composite panels, which offer excellent thermal insulation, fire resistance, and aesthetic versatility.
Emerging technologies such as digital supply chain management and automation are reshaping sourcing trends in the B2B space. Suppliers are adopting advanced analytics and AI-driven insights to optimize inventory management and streamline procurement processes. International buyers, especially from Brazil and Poland, should look for suppliers that leverage these technologies to improve operational efficiency and reduce lead times. Additionally, the trend towards customization is gaining traction, with buyers seeking personalized designs that meet specific architectural needs.
How Is Sustainability Impacting the Sourcing Decisions of Aluminum Composite Panels?
Sustainability is no longer just a buzzword; it has become a critical factor in sourcing decisions for B2B buyers in the aluminum composite panel sector. The environmental impact of production processes, waste management, and product lifecycle are all under scrutiny. Buyers from regions like Africa and the Middle East are increasingly prioritizing suppliers that adhere to sustainable practices, such as using recycled materials and energy-efficient manufacturing methods.
Ethical sourcing is another vital consideration. Buyers should seek suppliers with certifications like ISO 14001, which indicates a commitment to environmental management, and LEED (Leadership in Energy and Environmental Design), which recognizes sustainable building practices. By choosing suppliers that prioritize sustainability, international buyers not only enhance their brand reputation but also contribute to a more sustainable future for the construction industry.
What Is the Historical Context of the Aluminum Composite Panel Industry?
The aluminum composite panel industry has evolved significantly since its inception in the late 20th century. Initially used primarily for signage and interior applications, ACPs have transitioned into a preferred material for façade systems and exterior cladding due to their lightweight nature and design flexibility. The introduction of stringent fire safety regulations in the early 2000s further propelled advancements in ACP technology, leading to the development of fire-resistant composites.
As the industry matures, the focus is shifting towards innovation and sustainability, with suppliers investing in research and development to create new products that meet the evolving needs of architects and builders. This historical perspective is crucial for international B2B buyers, as it highlights the industry’s responsiveness to market demands and the importance of aligning with suppliers that are committed to ongoing innovation and ethical practices.
Frequently Asked Questions (FAQs) for B2B Buyers of aluminum composite panel supplier
-
How do I ensure the quality of aluminum composite panels before purchasing?
To ensure the quality of aluminum composite panels, request samples from potential suppliers. Evaluate these samples for thickness, surface finish, and color consistency. Additionally, inquire about certifications such as ISO 9001 for quality management systems. It’s also beneficial to check for compliance with international standards like ASTM or EN, which indicate that the panels meet specific performance criteria. Engaging in third-party testing can further validate quality claims. -
What are the best practices for sourcing aluminum composite panels internationally?
When sourcing aluminum composite panels internationally, start by conducting thorough market research to identify reputable suppliers. Utilize platforms like Alibaba, Global Sources, or industry-specific trade shows to connect with manufacturers. Verify supplier credentials through references, certifications, and audits. It’s essential to understand import regulations and tariffs in your country to avoid unexpected costs. Building a relationship with suppliers through regular communication can also facilitate smoother transactions. -
What customization options are available for aluminum composite panels?
Most suppliers offer a range of customization options for aluminum composite panels, including size, color, and surface finish. Depending on the manufacturer, you may also have options for specific coatings or fire-resistant materials. Discuss your project requirements with potential suppliers to understand their capabilities and limitations. Ensure that any customizations align with your project timelines and budget constraints. -
What is the minimum order quantity (MOQ) for aluminum composite panels?
The minimum order quantity (MOQ) for aluminum composite panels varies by supplier and can range from a few hundred to several thousand square meters. Smaller suppliers may have lower MOQs, while larger manufacturers often require higher quantities to justify production costs. When negotiating, clarify your project needs and explore the possibility of bulk purchasing discounts or consolidating orders with other products to meet MOQ requirements. -
What payment terms should I expect from aluminum composite panel suppliers?
Payment terms for aluminum composite panels typically vary between suppliers. Common terms include a 30% upfront deposit with the balance due before shipment, or a letter of credit. Always clarify payment terms in advance to avoid misunderstandings. It’s advisable to use secure payment methods such as PayPal or escrow services for international transactions to protect against fraud. -
How can I vet suppliers of aluminum composite panels effectively?
To effectively vet suppliers, start by checking their business licenses and certifications. Look for online reviews and testimonials from previous clients. Conduct interviews or meetings to assess their responsiveness and willingness to collaborate. Request references from past clients, particularly those in your region, to understand their reliability and service quality. If possible, visit the supplier’s facility to evaluate their production capabilities firsthand. -
What logistics considerations should I keep in mind when importing aluminum composite panels?
Logistics is crucial when importing aluminum composite panels. Assess shipping methods, costs, and delivery times to ensure they align with your project deadlines. Understand the customs clearance process in your country, including any tariffs or duties that may apply. It’s advisable to work with a freight forwarder who can assist with logistics, documentation, and compliance to ensure a smooth import process. -
How do I handle quality assurance for imported aluminum composite panels?
To handle quality assurance for imported aluminum composite panels, establish clear quality criteria before placing an order. Conduct inspections upon arrival to check for defects or discrepancies against the specifications. Consider hiring third-party inspection services to provide an unbiased assessment of the shipment. Document any issues and communicate them promptly with the supplier for resolution, which may include replacements or refunds, depending on your agreement.
Important Disclaimer & Terms of Use
⚠️ Important Disclaimer
The information provided in this guide, including content regarding manufacturers, technical specifications, and market analysis, is for informational and educational purposes only. It does not constitute professional procurement advice, financial advice, or legal advice.
While we have made every effort to ensure the accuracy and timeliness of the information, we are not responsible for any errors, omissions, or outdated information. Market conditions, company details, and technical standards are subject to change.
B2B buyers must conduct their own independent and thorough due diligence before making any purchasing decisions. This includes contacting suppliers directly, verifying certifications, requesting samples, and seeking professional consultation. The risk of relying on any information in this guide is borne solely by the reader.
Strategic Sourcing Conclusion and Outlook for aluminum composite panel supplier
What Are the Key Takeaways for International B2B Buyers of Aluminum Composite Panels?
In conclusion, strategic sourcing of aluminum composite panels offers significant advantages for international B2B buyers, particularly those operating in Africa, South America, the Middle East, and Europe. By carefully evaluating suppliers based on factors such as quality, sustainability, and technological innovation, buyers can ensure that they are making informed decisions that align with their operational goals and market demands.
How Can Strategic Sourcing Enhance Your Competitive Edge?
The process of strategic sourcing not only reduces costs but also enhances product quality and supplier relationships. As the demand for sustainable building materials grows, prioritizing suppliers who adhere to environmentally friendly practices can further position your business as a leader in the industry. This is especially relevant in markets like Brazil and Poland, where sustainability is becoming a critical factor in construction projects.
What Is the Future Outlook for Aluminum Composite Panels?
Looking ahead, the aluminum composite panel market is poised for growth, driven by advancements in manufacturing techniques and increased applications across various sectors. International B2B buyers are encouraged to stay proactive, engage in market research, and build partnerships with innovative suppliers. Embrace the future of construction materials by leveraging strategic sourcing to enhance your supply chain and meet evolving customer expectations. Your next step could redefine your competitive landscape—make it count.