The Ultimate Guide to Brass Fitting Manufacturers (2025)
Introduction: Navigating the Global Market for Brass Fitting Manufacturers
In today’s competitive landscape, international B2B buyers face the critical challenge of sourcing high-quality brass fittings that meet their specific needs. As a versatile material, brass fittings are essential in various applications, from plumbing and HVAC systems to automotive and industrial machinery. This guide serves as a comprehensive resource for buyers from Africa, South America, the Middle East, and Europe, including regions such as Egypt and South Africa, aiming to navigate the complex global market of brass fitting manufacturers.
Covering a wide array of topics, this guide delves into different types of brass fittings, their applications, and key considerations for supplier vetting. It provides actionable insights into pricing structures, material specifications, and quality assurance practices. By equipping buyers with the knowledge to evaluate suppliers effectively, this resource empowers informed purchasing decisions, ensuring that investments in brass fittings yield maximum value and reliability.
For B2B buyers, understanding the nuances of sourcing brass fittings is crucial not only for operational efficiency but also for maintaining competitive advantage in their respective markets. This guide will help you identify reputable manufacturers, comprehend market trends, and ultimately enhance your procurement strategies in the brass fittings sector.
Understanding Brass Fitting Manufacturers Types and Variations
Type Name | Key Distinguishing Features | Primary B2B Applications | Brief Pros & Cons for Buyers |
---|---|---|---|
Standard Brass Fittings | Made from common brass alloys like H59 and H62; good corrosion resistance | Plumbing, HVAC systems | Pros: Affordable, widely available. Cons: Limited strength for high-pressure applications. |
Lead-Free Brass Fittings | Composed of alloys with reduced lead content; compliant with health regulations | Drinking water systems, food processing | Pros: Safe for potable water, environmentally friendly. Cons: Higher cost than standard brass. |
Specialty Brass Fittings | Customized alloys with elements like aluminum or nickel; enhanced durability | Marine applications, high-stress environments | Pros: Superior performance, tailored solutions. Cons: Longer lead times, potentially higher costs. |
Forged Brass Fittings | Created through forging processes; high strength and integrity | Industrial machinery, heavy-duty applications | Pros: Excellent strength, reliable under stress. Cons: More expensive due to manufacturing process. |
Compression Brass Fittings | Designed for easy installation; features compression fittings for secure connections | Residential plumbing, gas lines | Pros: Quick installation, no need for welding. Cons: May require periodic maintenance. |
What Are Standard Brass Fittings and Their B2B Relevance?
Standard brass fittings, typically made from alloys such as H59 and H62, are widely used in plumbing and HVAC systems due to their excellent corrosion resistance and affordability. For B2B buyers, the low cost and availability make these fittings an attractive option for large-scale projects. However, they may not be suitable for high-pressure applications, which is a critical consideration when sourcing materials for demanding environments.
Why Choose Lead-Free Brass Fittings?
Lead-free brass fittings are designed to meet health regulations, making them ideal for applications involving drinking water and food processing. These fittings not only ensure safety but also demonstrate a commitment to environmental responsibility. Although they come at a higher price point compared to standard brass, the long-term benefits of compliance and health safety can outweigh the initial investment, especially for buyers focused on sustainability.
What Are Specialty Brass Fittings and Their Applications?
Specialty brass fittings are tailored to meet specific requirements by incorporating elements such as aluminum or nickel to enhance durability and resistance to harsh conditions. These fittings are often used in marine applications and high-stress environments. B2B buyers should consider the performance benefits and potential customization options, although they may face longer lead times and higher costs due to the specialized manufacturing processes involved.
How Do Forged Brass Fittings Stand Out?
Forged brass fittings are produced through a forging process that enhances their strength and integrity, making them suitable for industrial machinery and heavy-duty applications. For B2B buyers, the reliability of forged fittings under stress is a significant advantage, particularly in demanding environments. However, the manufacturing process can lead to increased costs, which buyers must weigh against the benefits of enhanced durability.
What Are the Benefits of Compression Brass Fittings?
Compression brass fittings are designed for easy installation and secure connections, making them popular in residential plumbing and gas lines. Their ability to facilitate quick installations without welding is a major plus for contractors and builders. However, buyers should be aware that compression fittings may require periodic maintenance to ensure ongoing reliability, which could impact long-term operational costs.
Related Video: Press Fitting Compatibility Guide
Key Industrial Applications of Brass Fitting Manufacturers
Industry/Sector | Specific Application of Brass Fitting Manufacturers | Value/Benefit for the Business | Key Sourcing Considerations for this Application |
---|---|---|---|
Plumbing and Water Supply | Brass fittings for pipes and valves in residential and commercial plumbing systems | Enhanced durability and corrosion resistance, ensuring long-lasting installations | Certifications for quality standards, compatibility with local plumbing codes, and availability of various sizes and types |
HVAC (Heating, Ventilation, and Air Conditioning) | Brass connectors and fittings for HVAC systems and refrigerants | Improved thermal conductivity and reliability in high-pressure applications | Compliance with international HVAC standards, resistance to temperature fluctuations, and supplier reliability |
Automotive Industry | Brass fittings in fuel and brake systems | High strength and resistance to wear, ensuring safety and performance | Compliance with automotive standards, dimensional accuracy, and ability to withstand harsh environments |
Industrial Machinery | Brass fittings in hydraulic and pneumatic systems | Enhanced performance and efficiency in fluid transfer applications | Customization options for specific applications, lead times for production, and bulk purchasing agreements |
Electronics and Electrical | Brass connectors in electrical applications | Excellent conductivity and reliability for electrical connections | RoHS compliance, compatibility with various electrical components, and sourcing from certified manufacturers |
How are Brass Fitting Manufacturers Used in Plumbing and Water Supply?
In the plumbing and water supply sector, brass fittings are crucial for connecting pipes and valves in both residential and commercial systems. Their corrosion resistance and durability ensure that installations can withstand high pressures and varying temperatures. International buyers, particularly from Africa and South America, should focus on sourcing brass fittings that comply with local plumbing codes and standards, as well as those that offer a variety of sizes and types to meet diverse project requirements.
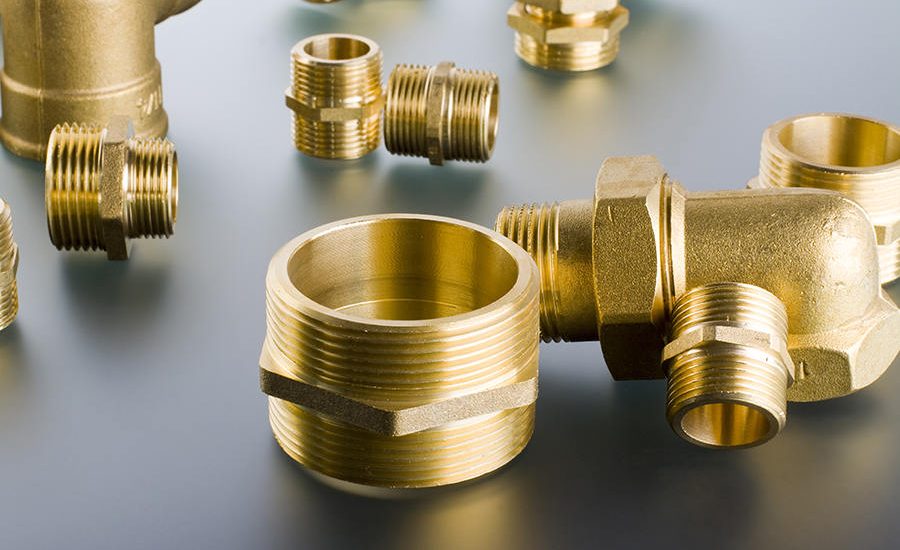
A stock image related to Brass Fitting Manufacturers.
What Role Do Brass Fittings Play in HVAC Systems?
Brass fittings are extensively used in HVAC systems, particularly for connecting refrigerants and ensuring efficient heat exchange. Their superior thermal conductivity and strength make them ideal for high-pressure applications. B2B buyers from the Middle East and Europe should prioritize suppliers that adhere to international HVAC standards and can provide fittings resistant to temperature fluctuations, ensuring reliable performance in diverse climates.
How Are Brass Fittings Essential in the Automotive Industry?
In the automotive sector, brass fittings are employed in fuel and brake systems due to their high strength and wear resistance. These properties are vital for maintaining safety and performance in vehicles. Buyers should ensure that their suppliers meet automotive standards and provide fittings with precise dimensions to guarantee compatibility and reliability under harsh conditions.
Why Are Brass Fittings Important in Industrial Machinery?
Brass fittings play a significant role in hydraulic and pneumatic systems within industrial machinery. They facilitate efficient fluid transfer, contributing to the overall performance and efficiency of machinery. Buyers in this sector should seek manufacturers that offer customization options to fit specific applications, as well as favorable lead times for bulk orders, to streamline their operations.
How Do Brass Connectors Benefit Electronics and Electrical Applications?
In electronics, brass connectors are utilized for their excellent conductivity and reliability. They are essential for creating secure electrical connections that can withstand varying environmental conditions. B2B buyers must ensure that their suppliers comply with RoHS regulations and offer products that are compatible with various electrical components, as this can significantly impact the performance and safety of electronic devices.
Related Video: Fitting allowance for the piping trades
3 Common User Pain Points for ‘Brass Fitting Manufacturers’ & Their Solutions
Scenario 1: Understanding the Quality Variability in Brass Fittings
The Problem:
International B2B buyers often struggle with the variability in quality among brass fittings. This inconsistency can arise from differing manufacturing processes, raw material quality, and supplier practices. Buyers from regions like Africa and South America may find it challenging to assess whether a brass fitting meets their required specifications, leading to potential failures in applications, increased costs, and unsatisfactory project outcomes. This situation can be especially precarious when sourcing from manufacturers with less transparent practices.
The Solution:
To mitigate quality variability, buyers should establish clear specifications based on recognized industry standards, such as ASTM or ISO. When engaging with brass fitting manufacturers, request detailed documentation that includes material certifications, production processes, and quality control measures. Additionally, consider conducting a factory audit or requesting samples for testing before placing bulk orders. This proactive approach not only ensures that the products meet necessary quality standards but also fosters a stronger relationship with the supplier, which can lead to better service and reliability in the long run.
Scenario 2: Navigating Compliance with Regional Standards
The Problem:
Brass fittings often need to comply with specific regional standards and regulations, which can vary significantly between markets, such as those in Europe and the Middle East. Buyers may find it cumbersome to navigate these regulations, leading to delays in product acceptance, additional costs for compliance testing, or even legal issues if the products do not meet local standards. This is particularly critical in industries like plumbing and HVAC, where safety and performance are paramount.
The Solution:
Buyers should conduct thorough research on the compliance requirements relevant to their target market before sourcing brass fittings. Engaging with a knowledgeable local partner or consultant can provide insights into regulatory standards and help streamline the compliance process. Furthermore, work with manufacturers that have a proven track record of meeting these standards and can provide the necessary certifications. Including compliance as a criterion in the supplier selection process can significantly reduce the risk of non-compliance and enhance the speed of market entry.
Scenario 3: Addressing Supply Chain Disruptions
The Problem:
Supply chain disruptions are a common concern for B2B buyers, particularly those sourcing brass fittings from international manufacturers. Factors such as political instability, logistical challenges, and unexpected demand fluctuations can lead to delays in delivery, impacting project timelines and operational efficiency. Buyers from regions such as Europe may face additional challenges due to Brexit-related changes or global shipping issues.
The Solution:
To combat supply chain disruptions, it is essential to diversify sourcing strategies. Buyers should consider establishing relationships with multiple suppliers across different geographic regions to ensure a steady supply of brass fittings. Additionally, implementing a just-in-time inventory system can help manage stock levels effectively while minimizing holding costs. Regularly communicating with suppliers about their production capabilities and potential issues can also foster transparency and allow buyers to plan accordingly. By building a resilient supply chain, buyers can better navigate uncertainties and maintain operational continuity.
Strategic Material Selection Guide for Brass Fitting Manufacturers
What Are the Key Materials for Brass Fitting Manufacturers?
When selecting materials for brass fittings, manufacturers often consider a variety of alloys and metals. Here, we analyze four common materials, focusing on their properties, advantages, disadvantages, and implications for international B2B buyers.
1. Brass Alloys (Cu-Zn)
Key Properties:
Brass, primarily composed of copper (Cu) and zinc (Zn), exhibits excellent machinability, corrosion resistance, and good thermal and electrical conductivity. It can handle moderate temperatures and pressures, making it suitable for plumbing and HVAC applications.
Pros & Cons:
Brass fittings are durable and resistant to corrosion, particularly in water and air applications. However, they can be more expensive than other materials like plastic or steel. Manufacturing complexity is moderate, as brass can be easily cast and forged, but requires careful handling to avoid oxidation during production.
Impact on Application:
Brass is highly compatible with water, air, and some gas applications. Its corrosion resistance makes it ideal for plumbing fittings, but it may not be suitable for aggressive chemicals or high-temperature steam.
Considerations for International Buyers:
Buyers from regions like Africa, South America, the Middle East, and Europe should ensure compliance with local standards such as ASTM or DIN. In countries like Egypt and South Africa, the availability of quality brass fittings that meet local regulations is crucial.
2. Copper (Cu)
Key Properties:
Copper fittings are known for their excellent thermal and electrical conductivity, high ductility, and resistance to corrosion. They can withstand high temperatures and pressures, making them ideal for applications in HVAC and refrigeration.
Pros & Cons:
Copper is highly durable and has a long lifespan, but it is more expensive than brass and can be challenging to work with due to its malleability. The manufacturing process can be complex, requiring specialized equipment for shaping and joining.
Impact on Application:
Copper fittings excel in applications involving hot water and steam. However, they may not be suitable for environments with high acidity or alkalinity, as this can lead to corrosion.
Considerations for International Buyers:
International buyers should verify the copper’s purity and compliance with relevant standards. In Europe, for instance, adherence to EN standards is essential for market acceptance.
3. Bronze Alloys
Key Properties:
Bronze, an alloy primarily of copper and tin, offers superior corrosion resistance, especially in marine environments. It has excellent wear resistance and can withstand high pressures.
Pros & Cons:
Bronze fittings are highly durable and resistant to saltwater corrosion, making them ideal for marine applications. However, they are typically more expensive than brass and copper, and their manufacturing process can be more complex due to the need for precise alloying.
Impact on Application:
Bronze is particularly suited for applications in marine and industrial environments where corrosion is a concern. Its compatibility with various fluids makes it versatile, but it may not be suitable for high-temperature applications.
Considerations for International Buyers:
Buyers should be aware of the specific bronze alloy grades and their certifications. In regions like the Middle East, where marine applications are prevalent, ensuring compliance with local maritime standards is vital.
4. Plastic Composites
Key Properties:
Plastic fittings, often made from PVC or CPVC, are lightweight, corrosion-resistant, and easy to install. They can handle a wide range of temperatures and pressures, depending on the type of plastic used.
Pros & Cons:
Plastic fittings are cost-effective and resistant to corrosion, making them suitable for various applications. However, they may not be as durable as metal fittings and can be sensitive to UV exposure and extreme temperatures.
Impact on Application:
Plastic fittings are ideal for water distribution and irrigation systems. However, they should not be used in high-pressure or high-temperature applications due to their lower strength compared to metals.
Considerations for International Buyers:
B2B buyers should check for certifications and compliance with local regulations regarding plastic materials. In Europe, for instance, compliance with REACH regulations is essential for market entry.
Summary Table of Material Selection for Brass Fitting Manufacturers
Material | Typical Use Case for Brass Fitting Manufacturers | Key Advantage | Key Disadvantage/Limitation | Relative Cost (Low/Med/High) |
---|---|---|---|---|
Brass Alloys (Cu-Zn) | Plumbing, HVAC, and general fittings | Excellent corrosion resistance | Higher cost compared to plastics | Medium |
Copper (Cu) | HVAC and refrigeration systems | Superior thermal and electrical conductivity | Expensive and complex to manufacture | High |
Bronze Alloys | Marine and industrial applications | Exceptional corrosion resistance | More expensive and complex | High |
Plastic Composites | Water distribution and irrigation systems | Lightweight and cost-effective | Less durable than metals | Low |
This guide provides a comprehensive overview of material options for brass fitting manufacturers, enabling international buyers to make informed decisions based on their specific needs and regional standards.
In-depth Look: Manufacturing Processes and Quality Assurance for Brass Fitting Manufacturers
What Are the Main Stages in the Manufacturing Process of Brass Fittings?
Brass fittings are essential components in various industries, including plumbing, HVAC, and automotive. Understanding the manufacturing process can help B2B buyers make informed decisions. The production of brass fittings typically involves several key stages: material preparation, forming, assembly, and finishing.
How Is Material Prepared for Brass Fitting Production?
The first step in manufacturing brass fittings is material preparation. Brass alloys, primarily composed of copper and zinc, are selected based on the desired specifications. The alloy is usually in the form of rods, bars, or sheets, and the specific grade of brass (e.g., H59, H62) is chosen according to the application requirements.
Once the material is selected, it undergoes processes like annealing to enhance its ductility and reduce hardness, making it easier to form. This stage is crucial, as it directly impacts the quality and performance of the final product.
What Techniques Are Used in Forming Brass Fittings?
Forming is a critical phase where the prepared material is shaped into the desired fitting form. Common techniques include:
- Machining: This method uses cutting tools to remove excess material, achieving precise dimensions. CNC (Computer Numerical Control) machines are often employed for high accuracy and repeatability.
- Forging: This involves shaping the brass using compressive forces, which improves the material’s strength and fatigue resistance.
- Die Casting: In this technique, molten brass is poured into molds to create complex shapes. It is particularly useful for high-volume production.
The choice of forming technique depends on factors such as the complexity of the fitting, production volume, and material properties.
How Are Brass Fittings Assembled?
Once individual components are formed, they are assembled into the final product. This may involve soldering, brazing, or mechanical fastening, depending on the design and intended application. The assembly process is closely monitored to ensure that all parts fit together correctly and that the connections are secure.
What Are the Finishing Processes for Brass Fittings?
The finishing stage enhances both the aesthetic and functional properties of brass fittings. Common finishing processes include:
- Surface Treatment: Techniques like plating, polishing, or applying protective coatings are used to improve corrosion resistance and appearance.
- Heat Treatment: This process can further enhance mechanical properties and relieve internal stresses within the material.
- Quality Checks: Before final packaging, fittings undergo rigorous inspection to ensure they meet specified standards.
What International Standards and Quality Control Practices Are Relevant for Brass Fittings?
Quality assurance is a vital aspect of brass fitting manufacturing, ensuring that products meet international standards and customer specifications. Key standards include:
- ISO 9001: This standard outlines the requirements for a quality management system, focusing on consistent product quality and customer satisfaction.
- CE Marking: Particularly relevant in Europe, this indicates that products meet EU safety, health, and environmental protection standards.
- API Standards: For fittings used in the oil and gas industry, adherence to American Petroleum Institute standards is critical.
What Are the Key Quality Control Checkpoints in Brass Fitting Manufacturing?
Quality control (QC) in brass fitting manufacturing involves several checkpoints throughout the production process:
- Incoming Quality Control (IQC): This phase involves inspecting raw materials for compliance with specifications before they are processed.
- In-Process Quality Control (IPQC): Continuous monitoring during production helps identify defects early, minimizing waste and rework.
- Final Quality Control (FQC): Before shipping, the final products are thoroughly inspected and tested to ensure they meet quality standards.
Common testing methods include:
- Dimensional Inspection: Ensures that fittings meet precise specifications.
- Pressure Testing: Assesses the integrity and leak-proof nature of fittings.
- Corrosion Resistance Testing: Evaluates the material’s ability to withstand environmental factors.
How Can B2B Buyers Verify Supplier Quality Control Practices?
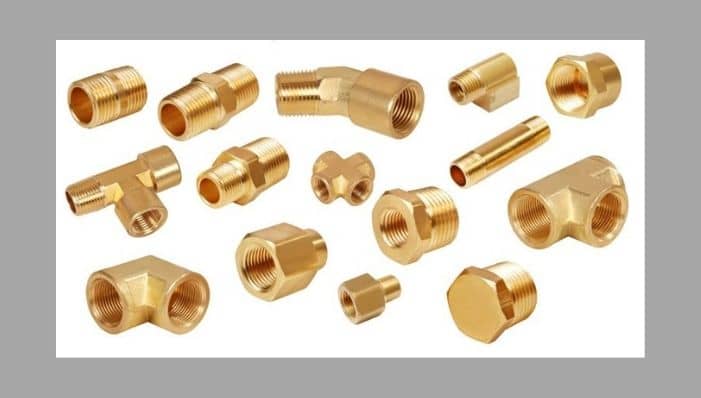
A stock image related to Brass Fitting Manufacturers.
International B2B buyers, especially those from regions such as Africa, South America, the Middle East, and Europe, should consider several methods to verify a supplier’s quality control practices:
- Supplier Audits: Conducting on-site audits helps buyers assess the manufacturing processes and QC protocols directly.
- Quality Assurance Reports: Requesting detailed QC reports, including testing results and inspection records, can provide insights into the supplier’s commitment to quality.
- Third-Party Inspections: Engaging independent inspection agencies can offer an objective assessment of the supplier’s quality control measures.
What Are the QC and Certification Nuances for International B2B Buyers?
Navigating the QC landscape can be complex for international B2B buyers. It is essential to understand the local and international certification requirements that may affect product acceptance in various markets. For instance:
- Regional Standards Compliance: Buyers should ensure that products comply with local regulations, which can vary significantly between Africa, South America, the Middle East, and Europe.
- Certification Validity: Verify that certifications are up-to-date and recognized in the buyer’s region to avoid issues with product acceptance.
By understanding these nuances, B2B buyers can effectively assess potential suppliers and ensure that they are sourcing high-quality brass fittings that meet their specific needs.
Practical Sourcing Guide: A Step-by-Step Checklist for ‘Brass Fitting Manufacturers’
The following is a step-by-step checklist for international B2B buyers looking to procure brass fittings from manufacturers. This guide aims to streamline your sourcing process, ensuring you make informed decisions that align with your business needs.
Step 1: Define Your Technical Specifications
Clearly outline the technical requirements for the brass fittings you need. This includes dimensions, pressure ratings, and corrosion resistance standards. Providing detailed specifications helps potential suppliers understand your needs and allows for accurate quotations.
- Considerations: Identify the specific applications for your fittings, such as plumbing, HVAC, or automotive. Different applications may require different material compositions or certifications.
Step 2: Conduct Market Research
Invest time in understanding the brass fitting market landscape, especially if you’re sourcing from regions like Africa or South America. Analyze trends, pricing, and the reputation of various manufacturers.
- Where to Look: Utilize industry reports, trade shows, and online platforms like Alibaba or Global Sources to gather insights about potential suppliers.
Step 3: Evaluate Potential Suppliers
Before committing to a supplier, conduct thorough evaluations. Request detailed company profiles, product catalogs, and case studies to assess their capabilities and experience.
- What to Ask For:
- References from current or past clients in your industry.
- Certifications, such as ISO 9001, to ensure quality management practices.
Step 4: Verify Supplier Certifications
Ensure that your selected suppliers hold relevant certifications that meet international quality standards. This is crucial for ensuring product quality and compliance with regional regulations.
- Key Certifications to Look For:
- ISO 9001 for quality management.
- ASTM or ANSI standards relevant to brass fittings.
Step 5: Request Samples for Testing
Before placing a large order, request samples of the fittings to test for quality and compatibility with your applications. This is a critical step to avoid costly mistakes down the line.
- Testing Focus Areas:
- Check for durability, resistance to corrosion, and the accuracy of dimensions.
- Assess the finish quality and any specific coatings required for your applications.
Step 6: Negotiate Terms and Conditions
Once you’ve selected a supplier, engage in negotiations regarding pricing, payment terms, lead times, and warranty policies. Clear agreements help to avoid misunderstandings later.
- Negotiation Tips:
- Be transparent about your budget and expectations.
- Discuss bulk order discounts or long-term partnership opportunities.
Step 7: Establish a Communication Plan
Set up a clear communication strategy with your chosen supplier. Effective communication is vital to ensure timely updates, address any issues, and maintain a good working relationship.
- Communication Channels:
- Decide on preferred methods (email, phone, video calls) and frequency of updates.
- Assign a dedicated point of contact on both sides for consistency.
By following these steps, international B2B buyers can enhance their sourcing process for brass fittings, ensuring they select the right manufacturers that meet their specific needs and standards.
Comprehensive Cost and Pricing Analysis for Brass Fitting Manufacturers Sourcing
What Are the Key Cost Components in Brass Fitting Manufacturing?
When sourcing brass fittings, international B2B buyers must understand the various cost components that contribute to the final pricing. Key components include:
-
Materials: The primary cost driver is the raw materials used, predominantly brass alloys which consist of copper and zinc. The price of copper, in particular, can fluctuate significantly based on global market trends, impacting the overall cost of brass fittings.
-
Labor: Labor costs vary depending on the region where manufacturing occurs. Countries with higher wage standards, such as those in Europe, will typically see increased labor costs compared to regions in Africa or South America, where labor may be less expensive.
-
Manufacturing Overhead: This includes expenses related to factory operations, utilities, and other indirect costs. Efficient manufacturing processes can help minimize these overheads, potentially lowering the final price.
-
Tooling: The initial investment in tooling and machinery can be substantial, especially for custom fittings. Buyers should consider whether they are sourcing standard fittings or custom solutions, as the latter may require specialized tooling that increases costs.
-
Quality Control (QC): Ensuring that brass fittings meet international quality standards incurs additional costs. This is particularly relevant for buyers in regulated industries or those requiring specific certifications, which can drive up the price.
-
Logistics: Transportation costs, including shipping and handling, also play a critical role. The choice of Incoterms (International Commercial Terms) will affect who bears these costs, influencing the overall pricing structure.
-
Margin: Manufacturers typically add a profit margin to cover risks and ensure sustainability. This margin can vary widely based on the manufacturer’s position in the market and their operational efficiencies.
How Do Price Influencers Affect Brass Fitting Costs?
Several factors can influence the pricing of brass fittings:
-
Volume/MOQ: Bulk orders often lead to reduced per-unit costs. Buyers should negotiate minimum order quantities (MOQs) to benefit from economies of scale.
-
Specifications and Customization: Custom fittings or those with specific technical requirements usually come at a premium. Buyers should clearly communicate their needs to get accurate quotes.
-
Material Quality and Certifications: Higher quality materials or those that meet specific industry certifications (like ISO or ASTM) can command higher prices. Buyers must balance quality requirements against budget constraints.
-
Supplier Factors: The reputation and reliability of suppliers can affect pricing. Established suppliers may charge more due to their proven track record and reliability.
-
Incoterms: The chosen Incoterms can significantly influence the total landed cost of goods. Understanding these terms helps buyers navigate responsibilities for shipping, insurance, and duties, which can add to the overall cost.
What Are the Best Negotiation Strategies for International Buyers?
For B2B buyers from regions such as Africa, South America, the Middle East, and Europe, effective negotiation can yield significant cost savings:
-
Research Market Prices: Understanding the market rates for brass fittings helps buyers negotiate better deals. Buyers should gather multiple quotes to benchmark prices.
-
Leverage Long-Term Relationships: Establishing long-term partnerships with suppliers can lead to better pricing and terms over time. Consistent orders may encourage suppliers to offer discounts.
-
Consider Total Cost of Ownership (TCO): Evaluate not just the purchase price but also the total cost over the product’s life cycle, including maintenance, logistics, and potential downtime costs.
-
Be Flexible with Specifications: If possible, adjusting specifications to align with standard offerings can help reduce costs associated with custom manufacturing.
-
Timing of Orders: Placing orders during off-peak times may allow buyers to benefit from lower rates and better availability.
Disclaimer on Indicative Prices
While this analysis provides insights into the cost structure and pricing nuances for brass fittings, prices can vary significantly based on location, supplier, and market conditions. Buyers should conduct thorough due diligence to obtain accurate and current pricing information tailored to their specific needs.
Alternatives Analysis: Comparing Brass Fitting Manufacturers With Other Solutions
Understanding Alternative Solutions to Brass Fitting Manufacturers
When sourcing fittings for industrial applications, B2B buyers must consider various alternatives to brass fitting manufacturers. The choice of fittings can significantly impact performance, cost, and overall project success. In this analysis, we will compare brass fittings against two viable alternatives: stainless steel fittings and plastic fittings.
Comparison Table of Brass Fittings vs. Alternatives
Comparison Aspect | Brass Fitting Manufacturers | Stainless Steel Fittings | Plastic Fittings |
---|---|---|---|
Performance | Excellent corrosion resistance, good strength | High durability, excellent corrosion resistance | Moderate strength, limited temperature resistance |
Cost | Generally higher cost | Higher upfront cost | Lower initial cost |
Ease of Implementation | Moderate complexity in installation | Moderate to high complexity due to weight | Easy to install, lightweight |
Maintenance | Low maintenance, but can tarnish | Low maintenance, resistant to tarnishing | Requires regular checks for wear |
Best Use Case | Plumbing, HVAC, and high-pressure applications | Food and beverage, chemical processing | Low-pressure applications, irrigation systems |
Detailed Breakdown of Alternatives
1. Stainless Steel Fittings
Stainless steel fittings are renowned for their exceptional durability and resistance to corrosion, making them suitable for high-demand environments such as food and beverage processing, as well as chemical handling. They maintain structural integrity under extreme temperatures, which is crucial for industries that deal with thermal processing. However, the initial investment is higher compared to brass fittings, and their weight can complicate installation. Additionally, while stainless steel fittings require low maintenance, they are susceptible to pitting in chloride-rich environments.
2. Plastic Fittings
Plastic fittings present a cost-effective alternative, particularly for low-pressure applications such as irrigation systems and non-potable water supply. They are lightweight and easy to handle, which simplifies installation and reduces labor costs. Plastic fittings are resistant to corrosion and do not tarnish, but they may not withstand high temperatures or pressure, making them unsuitable for applications that require robust materials. Regular maintenance is necessary to check for wear and potential degradation due to UV exposure or chemical reactions.
Conclusion: Choosing the Right Solution for Your Needs
When deciding between brass fittings and alternative solutions like stainless steel or plastic fittings, B2B buyers should evaluate their specific application requirements. Factors such as environmental conditions, budget constraints, and installation complexity play critical roles in the decision-making process. Brass fittings may offer superior performance for high-pressure applications, while stainless steel is ideal for food processing environments. Conversely, plastic fittings can provide a budget-friendly option for less demanding applications. By thoroughly assessing these factors, buyers can select the most suitable fitting solution to meet their operational needs.
Essential Technical Properties and Trade Terminology for Brass Fitting Manufacturers
What Are the Essential Technical Properties of Brass Fittings?
When sourcing brass fittings, international B2B buyers must be familiar with key technical properties that ensure product quality and compatibility with their applications. Here are critical specifications to consider:
-
Material Grade
Brass fittings are classified into different grades based on their copper and zinc content. Common grades include H59, H62, and H65, where the number indicates the percentage of copper. Understanding the material grade is crucial as it impacts corrosion resistance, strength, and machinability, affecting the performance of fittings in various environments. -
Tolerance
Tolerance refers to the permissible limit of variation in a fitting’s dimensions. For brass fittings, precise tolerances ensure proper fit and function, especially in plumbing and HVAC applications. Buyers should specify tolerance levels to avoid issues during installation and ensure system integrity. -
Pressure Rating
The pressure rating indicates the maximum pressure that a brass fitting can withstand without failure. This specification is vital for applications involving fluid transport, as exceeding the pressure rating could lead to leaks or catastrophic failures. Buyers must assess their operational pressures to select appropriately rated fittings. -
Temperature Resistance
Brass fittings must be able to withstand varying temperatures, especially in industrial applications. The temperature resistance is essential for ensuring that fittings maintain integrity and performance under thermal stress. Buyers should evaluate the operating temperature ranges of their systems when selecting fittings. -
Corrosion Resistance
The corrosion resistance of brass fittings is determined by their alloy composition. Certain grades offer enhanced resistance to specific environments, such as marine or chemical applications. Understanding corrosion resistance helps buyers choose fittings that will last longer and reduce maintenance costs. -
Surface Finish
The surface finish of brass fittings can affect both aesthetics and functionality. Options include polished, brushed, or coated finishes, which can enhance corrosion resistance and reduce friction in applications. Buyers should consider the appropriate finish based on the application’s environmental conditions.
Which Trade Terminology Should B2B Buyers Understand for Brass Fittings?
Familiarity with industry-specific terms can streamline procurement processes and enhance communication between buyers and suppliers. Here are essential trade terms for brass fitting manufacturers:
-
OEM (Original Equipment Manufacturer)
OEM refers to companies that produce parts or equipment that may be marketed by another manufacturer. For B2B buyers, understanding OEM relationships is crucial as it affects product specifications and compatibility with existing systems. -
MOQ (Minimum Order Quantity)
MOQ is the smallest quantity of a product that a supplier is willing to sell. This term is vital for buyers, especially small businesses, as it impacts inventory costs and cash flow. Understanding MOQ helps buyers negotiate better terms or seek alternative suppliers. -
RFQ (Request for Quotation)
An RFQ is a document sent to suppliers requesting pricing and terms for specific products. For buyers, issuing an RFQ is a critical step in obtaining competitive pricing and ensuring that all specifications are met. A well-defined RFQ can lead to better supplier relationships and cost savings. -
Incoterms (International Commercial Terms)
Incoterms are predefined commercial terms published by the International Chamber of Commerce (ICC) that clarify the responsibilities of buyers and sellers in international transactions. Familiarity with these terms helps buyers understand shipping responsibilities, risk transfer, and cost management. -
Lead Time
Lead time refers to the period from placing an order to its delivery. This term is essential for buyers to manage project timelines effectively. Understanding lead times can help buyers plan their inventory and production schedules, ensuring timely project completion. -
Certification Standards
Certification standards, such as ASTM or ISO, ensure that products meet specific quality and safety criteria. Buyers should be aware of the relevant certifications for brass fittings to ensure compliance with industry regulations and standards, which can mitigate risks associated with product failures.
By grasping these technical properties and trade terms, B2B buyers can make informed decisions, ensuring they select the right brass fittings for their applications while fostering effective supplier relationships.
Navigating Market Dynamics and Sourcing Trends in the Brass Fitting Manufacturers Sector
What Are the Key Trends Influencing the Brass Fitting Manufacturers Market?
The brass fitting manufacturers market is currently experiencing significant growth driven by various global factors. The increasing demand for plumbing and HVAC systems, particularly in developing regions such as Africa and South America, is a primary driver. The urbanization of these regions, alongside infrastructural development projects, has led to heightened demand for durable and reliable fittings. Additionally, the Middle East is witnessing a surge in construction activities, further boosting the market for brass fittings.
Emerging B2B technologies, such as digital procurement platforms and advanced manufacturing techniques like 3D printing, are reshaping the sourcing landscape. These technologies enable buyers to streamline their procurement processes, enhance inventory management, and reduce lead times. Furthermore, the adoption of IoT (Internet of Things) in manufacturing is leading to smarter production processes, increasing efficiency and reducing waste, which is crucial for international buyers seeking sustainable solutions.
Another noteworthy trend is the shift towards customization. As buyers from Europe, particularly in countries like Germany and France, demand specific requirements for their projects, manufacturers are increasingly offering tailored solutions to meet these needs. This trend not only improves customer satisfaction but also fosters long-term partnerships between suppliers and buyers.
How Is Sustainability Shaping Sourcing Decisions in the Brass Fitting Sector?
Sustainability is becoming a critical consideration for B2B buyers in the brass fitting sector. The environmental impact of manufacturing processes, particularly concerning resource extraction and waste management, is under scrutiny. International buyers are increasingly seeking suppliers who prioritize sustainable practices, such as using recycled materials and adopting energy-efficient manufacturing processes.
Ethical sourcing is another crucial aspect of sustainability. Buyers are demanding transparency in the supply chain, ensuring that materials are sourced responsibly without harming the environment or exploiting labor. Certifications such as ISO 14001 for environmental management and Fair Trade for ethical labor practices are becoming essential for suppliers aiming to attract international clients.
Moreover, the trend towards “green” certifications is gaining momentum. Manufacturers that can demonstrate their commitment to sustainability through recognized certifications can differentiate themselves in a competitive market. For instance, using eco-friendly brass alloys that reduce the carbon footprint during production not only aligns with global sustainability goals but also appeals to environmentally-conscious buyers.
What Historical Developments Have Influenced Brass Fitting Manufacturing?
The evolution of brass fitting manufacturing can be traced back to the industrial revolution, which marked the beginning of mass production techniques. Initially, brass fittings were handcrafted, but advancements in metallurgy and the introduction of machinery transformed the manufacturing landscape. The combination of copper and zinc to create brass offered advantages such as enhanced corrosion resistance and improved mechanical properties, making it a preferred choice for various applications.
As industries expanded, the demand for standardized fittings grew, leading to the establishment of specifications and regulations governing brass fitting production. This standardization not only improved quality but also facilitated international trade, allowing manufacturers from Europe and the Americas to enter emerging markets in Africa and the Middle East.
In recent decades, the rise of globalization has further influenced the sector, as manufacturers increasingly seek to establish production facilities in regions with lower labor costs. This shift has enabled them to meet the growing demand in local markets while maintaining competitive pricing. Today, the brass fitting industry continues to innovate, focusing on sustainability and technological advancements to meet the challenges of a dynamic global market.
Frequently Asked Questions (FAQs) for B2B Buyers of Brass Fitting Manufacturers
-
How do I choose the right brass fitting manufacturer for my business needs?
Selecting the right brass fitting manufacturer involves evaluating several factors. Start by assessing their industry experience and expertise in producing the specific type of brass fittings you require. Check their certifications and compliance with international quality standards, such as ISO or ASTM. Additionally, consider their production capacity, lead times, and customization options. It is also beneficial to read customer reviews and request samples to evaluate product quality before making a decision. -
What are the key quality assurance practices to look for in brass fitting manufacturers?
Quality assurance is crucial when sourcing brass fittings. Look for manufacturers that implement rigorous quality control measures, such as in-process inspections and final product testing. They should have documented quality management systems in place, ideally certified to ISO 9001 standards. Additionally, inquire about their material sourcing, testing methods, and any warranties or guarantees they offer on their products to ensure durability and reliability. -
What customization options are typically available with brass fittings?
Most brass fitting manufacturers offer a range of customization options to meet specific project requirements. Common customizations include size, shape, and threading types, as well as surface treatments like plating or polishing. You can also request specific alloy compositions or additional features like integrated seals or valves. To ensure your needs are met, provide detailed specifications and consider discussing your project with the manufacturer’s engineering team. -
What is the minimum order quantity (MOQ) for brass fittings from manufacturers?
Minimum order quantities (MOQs) for brass fittings can vary significantly among manufacturers. While some may accept small orders of a few hundred units, others may require orders in the thousands to justify production costs. It’s essential to clarify the MOQ during initial discussions and consider negotiating based on your needs. Additionally, some manufacturers may offer flexibility for first-time buyers or for long-term partnerships. -
What payment terms should I expect when sourcing brass fittings internationally?
Payment terms can differ widely based on the manufacturer’s policies and your negotiation skills. Common terms include a deposit (often 30-50%) upfront, with the balance due before shipment or upon delivery. Some manufacturers may offer credit terms for established customers. It’s important to discuss payment options early in the negotiation process and consider using secure payment methods, such as letters of credit or escrow services, especially for larger transactions. -
How can I effectively vet potential brass fitting suppliers?
Vetting potential suppliers is crucial for ensuring a reliable partnership. Start by checking their business credentials, including registration, licenses, and certifications. Look for customer reviews and testimonials, and request references from previous clients. Conduct site visits if possible to inspect their manufacturing processes and facilities. Additionally, assess their communication responsiveness and willingness to collaborate, as these factors can greatly affect your overall experience. -
What are the logistics considerations when importing brass fittings?
When importing brass fittings, logistics play a vital role in the overall supply chain. Consider the shipping methods available, including air freight for speed or sea freight for cost-effectiveness. Be aware of customs regulations and import duties specific to your country, as these can impact overall costs. Collaborating with a freight forwarder can streamline the process, ensuring proper documentation and compliance with import laws. -
What are the common applications of brass fittings in various industries?
Brass fittings are widely used across several industries due to their durability and corrosion resistance. Common applications include plumbing systems, HVAC systems, and automotive parts. They are also prevalent in electrical components and decorative hardware due to their aesthetic appeal. Understanding the specific applications of brass fittings relevant to your industry can help you communicate your needs more effectively to manufacturers.
Important Disclaimer & Terms of Use
⚠️ Important Disclaimer
The information provided in this guide, including content regarding manufacturers, technical specifications, and market analysis, is for informational and educational purposes only. It does not constitute professional procurement advice, financial advice, or legal advice.
While we have made every effort to ensure the accuracy and timeliness of the information, we are not responsible for any errors, omissions, or outdated information. Market conditions, company details, and technical standards are subject to change.
B2B buyers must conduct their own independent and thorough due diligence before making any purchasing decisions. This includes contacting suppliers directly, verifying certifications, requesting samples, and seeking professional consultation. The risk of relying on any information in this guide is borne solely by the reader.
Strategic Sourcing Conclusion and Outlook for Brass Fitting Manufacturers
What Are the Key Takeaways for International B2B Buyers in Brass Fittings?
In the dynamic landscape of brass fitting manufacturing, strategic sourcing emerges as a crucial approach for international buyers. Understanding the differences between various brass alloys, such as H59 and H62, is essential for selecting the right materials that meet specific project requirements. Buyers must prioritize suppliers who demonstrate transparency in their sourcing practices and offer high-quality products that comply with international standards.
How Can Strategic Sourcing Enhance Your Supply Chain?
By leveraging strategic sourcing, businesses can optimize their supply chains, reduce costs, and improve product quality. Engaging with manufacturers who utilize advanced production techniques and sustainable practices can yield long-term benefits, including reliability and enhanced performance of brass fittings. This is particularly relevant for buyers in regions like Africa and South America, where local suppliers may offer competitive pricing but vary in quality.
What Does the Future Hold for Brass Fitting Manufacturers?
As global demand for brass fittings continues to rise, driven by infrastructure developments and industrial growth, international buyers should remain proactive. Emphasizing partnerships with manufacturers that prioritize innovation and quality will be key to staying ahead. By investing in strategic sourcing now, businesses can position themselves to capitalize on emerging opportunities, ensuring they meet the growing needs of their markets effectively. Engage with trusted suppliers today to secure a competitive edge in the brass fittings sector.