The Ultimate Guide to Centrifugal Pump Supplier (2025)
Introduction: Navigating the Global Market for centrifugal pump supplier
In today’s interconnected global marketplace, sourcing a reliable centrifugal pump supplier poses significant challenges for international B2B buyers. Whether you’re operating in Africa, South America, the Middle East, or Europe, the stakes are high when it comes to ensuring the efficiency and reliability of your operations. This guide aims to streamline your purchasing process by providing a comprehensive overview of centrifugal pumps, including their various types, applications, and the critical factors to consider when vetting suppliers.
Understanding the different centrifugal pump types—such as single-stage, multi-stage, and submersible pumps—along with their specific applications in industries like agriculture, manufacturing, and water management, is essential for making informed decisions. Additionally, we will delve into key aspects of supplier vetting, including certifications, customer service, and technical support, ensuring you partner with suppliers that meet your operational standards.
Furthermore, this guide will illuminate cost factors associated with centrifugal pumps, enabling you to budget effectively while maximizing your return on investment. By equipping you with actionable insights, we empower you to make well-informed purchasing decisions that can lead to enhanced operational efficiency and long-term success in your industry. Whether you’re based in the bustling markets of Nigeria or the industrial hubs of the UK, our guide will serve as your roadmap to navigating the complexities of global sourcing for centrifugal pumps.
Understanding centrifugal pump supplier Types and Variations
Type Name | Key Distinguishing Features | Primary B2B Applications | Brief Pros & Cons for Buyers |
---|---|---|---|
End Suction Pumps | Simple design, horizontal orientation, single-stage | Water supply, HVAC, irrigation | Pros: Cost-effective, easy maintenance. Cons: Limited efficiency in high-pressure applications. |
Vertical Turbine Pumps | Multi-stage design, submerged operation | Deep well pumping, water treatment | Pros: High efficiency, space-saving. Cons: Complex installation, higher upfront costs. |
Self-Priming Pumps | Capable of removing air and priming itself | Wastewater management, chemical transfer | Pros: Versatile, reliable in varying conditions. Cons: May require more energy, less efficient than standard pumps. |
Magnetic Drive Pumps | No mechanical seal, uses magnets for operation | Chemical processing, pharmaceuticals | Pros: Leak-free operation, suitable for hazardous fluids. Cons: Higher initial investment, limited flow rates. |
Submersible Pumps | Designed to operate underwater, typically electric | Sewage, drainage, dewatering | Pros: Efficient for submerged applications, compact design. Cons: Maintenance can be challenging, may require specialized knowledge. |
What Are the Key Characteristics of End Suction Pumps?
End suction pumps are known for their straightforward design and horizontal orientation, making them a popular choice in various industries. They typically feature a single-stage impeller, which allows them to handle low to moderate flow rates efficiently. B2B buyers should consider their application needs; while these pumps are cost-effective and easy to maintain, they may not perform well under high-pressure conditions, limiting their use in specific scenarios.
How Do Vertical Turbine Pumps Stand Out?
Vertical turbine pumps are designed for multi-stage operation and are often submerged, allowing them to efficiently draw water from deep wells. They are particularly suitable for applications requiring high efficiency and compact installations, such as water treatment and irrigation systems. While they offer excellent performance, potential buyers should be aware of the complexities involved in installation and the higher initial costs associated with these pumps.
What Makes Self-Priming Pumps a Versatile Choice?
Self-priming pumps are engineered to remove air from the system and can efficiently prime themselves, making them ideal for applications where fluid levels may fluctuate, such as in wastewater management or chemical transfer. Their versatility and reliability in various conditions are significant advantages. However, buyers should consider that these pumps may consume more energy and can be less efficient compared to traditional options.
Why Consider Magnetic Drive Pumps?
Magnetic drive pumps are unique in their design, utilizing magnets to eliminate the need for mechanical seals, resulting in a leak-free operation. This feature makes them particularly suitable for handling hazardous fluids in chemical processing and pharmaceutical applications. Although they require a higher initial investment and have limitations in flow rates, their safety and efficiency make them appealing to B2B buyers focused on compliance and reliability.
What Are the Advantages and Disadvantages of Submersible Pumps?
Submersible pumps are specifically designed to operate underwater, making them ideal for sewage, drainage, and dewatering applications. Their compact design is advantageous for tight spaces, and they are generally efficient in submerged operations. However, maintenance can be challenging due to their underwater placement, and buyers may need specialized knowledge to ensure proper servicing.
Related Video: Centrifugal Pump Types
Key Industrial Applications of centrifugal pump supplier
Industry/Sector | Specific Application of centrifugal pump supplier | Value/Benefit for the Business | Key Sourcing Considerations for this Application |
---|---|---|---|
Water Treatment | Pumping and transferring water in treatment facilities | Ensures clean water supply and compliance with health regulations | Energy efficiency, corrosion resistance, and maintenance support |
Oil and Gas | Transporting crude oil and refined products | Enhances operational efficiency and reduces downtime | Material compatibility, pressure ratings, and reliability |
Agriculture and Irrigation | Irrigation systems for crop production | Increases crop yield and optimizes water usage | Flow rate, pump durability, and adaptability to varying conditions |
Chemical Processing | Handling corrosive and hazardous liquids | Improves safety and efficiency in chemical production | Material specifications, safety certifications, and regulatory compliance |
HVAC Systems | Circulating fluids in heating and cooling systems | Enhances energy efficiency and system reliability | Noise levels, energy consumption, and compatibility with existing systems |
How Are Centrifugal Pumps Used in Water Treatment Applications?
Centrifugal pump suppliers play a crucial role in water treatment facilities by ensuring the efficient pumping and transferring of water. These pumps help in the filtration and distribution of clean water, which is vital for public health and safety. For international buyers, particularly in regions like Africa and South America, sourcing pumps that are energy-efficient and resistant to corrosion is essential, given the challenging environments and regulatory requirements. Buyers should also prioritize suppliers that offer comprehensive maintenance support to ensure long-term operational reliability.
What Role Do Centrifugal Pumps Play in the Oil and Gas Sector?
In the oil and gas industry, centrifugal pumps are instrumental in transporting crude oil and refined products through pipelines. Their ability to handle high flow rates while maintaining pressure is critical for operational efficiency and minimizing downtime. Buyers from the Middle East, known for its vast oil reserves, should consider pumps that are specifically designed for high-pressure applications and compatible with various oil types. Additionally, understanding material compatibility is crucial to prevent corrosion and enhance pump longevity.
How Are Centrifugal Pumps Beneficial in Agriculture and Irrigation?
Centrifugal pumps are essential in agriculture, particularly for irrigation systems that optimize water usage and enhance crop yield. By efficiently distributing water to fields, these pumps support sustainable farming practices. International buyers, especially from regions like Europe and Africa, should focus on pumps that can adapt to varying irrigation needs and environmental conditions. Durability and flow rate are key considerations, ensuring that the pumps can withstand harsh agricultural environments.
What Are the Applications of Centrifugal Pumps in Chemical Processing?
In chemical processing, centrifugal pumps are used to handle corrosive and hazardous liquids, making them vital for safety and operational efficiency. These pumps help in the accurate transfer of chemicals, reducing the risk of spills and contamination. Buyers from South America and Europe must ensure that the pumps meet stringent safety certifications and material specifications to comply with local regulations. Additionally, understanding the specific requirements for handling various chemicals is essential for selecting the right pump.
How Do Centrifugal Pumps Enhance HVAC Systems?
Centrifugal pumps are integral to HVAC systems, circulating fluids for heating and cooling. They improve energy efficiency and system reliability, ensuring optimal temperature control in commercial and industrial settings. For B2B buyers in Europe, selecting pumps with low noise levels and high energy efficiency ratings is crucial for compliance with environmental regulations. Compatibility with existing HVAC systems and ease of maintenance should also be key factors in the sourcing process.
Related Video: Centrifugal Pump Basics – How centrifugal pumps work working principle hvacr
3 Common User Pain Points for ‘centrifugal pump supplier’ & Their Solutions
Scenario 1: Inconsistent Pump Performance Across Different Environments
The Problem: B2B buyers often face the challenge of centrifugal pumps underperforming when deployed in varying environmental conditions. For instance, a manufacturing plant in Nigeria may have to deal with high ambient temperatures and fluctuating electricity supply, which can lead to pump inefficiencies. This inconsistency can result in decreased productivity, increased operational costs, and even potential safety hazards if the pumps fail to operate as intended.
The Solution: To ensure optimal performance regardless of environmental conditions, buyers should thoroughly assess the specific requirements of their applications. First, engage with suppliers who offer customizable centrifugal pumps that can be tailored to handle local conditions, such as temperature variations and power supply irregularities. Secondly, utilize pump selection software that factors in local environmental conditions to recommend the most suitable pump model. Finally, consider regular maintenance and performance monitoring to identify and rectify any issues promptly. Establishing a strong relationship with a reputable supplier who can provide ongoing support and advice is crucial for long-term success.
Scenario 2: Difficulty in Sourcing Spare Parts Promptly
The Problem: A common pain point for international B2B buyers is the delayed availability of spare parts for centrifugal pumps, which can lead to prolonged downtime in critical operations. This issue is particularly prevalent in regions like South America or Africa, where supply chains may be less robust. When a pump breaks down, the inability to quickly source the necessary parts can significantly hinder production processes and lead to lost revenue.
The Solution: To mitigate this risk, buyers should prioritize suppliers who maintain a comprehensive inventory of spare parts and can provide rapid shipping options. Establishing contracts with suppliers that include guaranteed lead times for parts delivery can also be beneficial. Additionally, buyers can invest in predictive maintenance technologies that help identify potential pump failures before they occur, allowing for proactive ordering of spare parts. Creating a local network of service providers who can assist with repairs and maintenance can further reduce dependency on distant suppliers and enhance operational resilience.
Scenario 3: Lack of Technical Expertise for Proper Pump Installation
The Problem: Many B2B buyers struggle with the technical complexities involved in the installation and operation of centrifugal pumps. In regions such as the Middle East, where the demand for industrial applications is rising, the lack of trained personnel can result in improper installation, leading to inefficient pump operation and increased wear and tear. This can create a costly cycle of repairs and replacements that could have been avoided.
The Solution: To address this issue, buyers should ensure that their suppliers offer comprehensive training programs for their staff. This includes not only installation training but also guidance on best practices for pump operation and maintenance. Furthermore, consider engaging suppliers who provide installation services or technical support as part of their offerings. Implementing a robust training schedule can empower employees with the necessary skills to manage centrifugal pumps effectively. Additionally, leveraging online resources such as webinars and instructional videos can supplement on-site training and help reinforce knowledge within the team. By investing in education and support, companies can enhance operational efficiency and reduce long-term costs associated with improper pump management.
Strategic Material Selection Guide for centrifugal pump supplier
What are the Common Materials Used in Centrifugal Pumps?
When selecting materials for centrifugal pumps, it’s crucial to understand the properties, advantages, and limitations of each option. This knowledge helps international B2B buyers make informed decisions tailored to their specific applications, especially in diverse markets like Africa, South America, the Middle East, and Europe.
How Does Stainless Steel Perform in Centrifugal Pumps?
Key Properties: Stainless steel is renowned for its excellent corrosion resistance, high strength, and ability to withstand high temperatures and pressures. It typically has a temperature rating of up to 300°C (572°F) and can handle pressures exceeding 20 bar.
Pros & Cons: The durability of stainless steel makes it suitable for various applications, including those involving aggressive chemicals. However, its higher cost compared to other materials can be a drawback for budget-conscious buyers. Manufacturing complexity is moderate, requiring specialized techniques for welding and machining.
Impact on Application: Stainless steel is compatible with a wide range of media, including water, oils, and some acids. Its resistance to corrosion ensures longevity in harsh environments, making it a preferred choice in industries like food processing and pharmaceuticals.
Considerations for International Buyers: Buyers from regions like the UK and Nigeria should ensure compliance with international standards such as ASTM A240 for stainless steel grades. Understanding local regulations regarding material specifications is essential for seamless procurement.
What Role Does Cast Iron Play in Centrifugal Pumps?
Key Properties: Cast iron is known for its excellent wear resistance and ability to absorb vibrations. It typically operates well under moderate temperature and pressure conditions, with a maximum temperature rating of around 200°C (392°F) and pressure ratings up to 10 bar.
Pros & Cons: The primary advantage of cast iron is its low cost and ease of manufacturing. However, it is prone to corrosion, especially in wet environments, which can limit its applicability. Additionally, cast iron is heavier, which may complicate installation and transportation.
Impact on Application: Cast iron is suitable for handling water and other non-corrosive fluids, making it ideal for municipal water systems and irrigation. However, its susceptibility to rust necessitates protective coatings in humid conditions.
Considerations for International Buyers: Buyers should be aware of local standards for cast iron, such as DIN 1691, to ensure compatibility and quality. In regions with high humidity, additional protective measures may be necessary to extend the pump’s lifespan.
Why Choose Plastic for Centrifugal Pumps?
Key Properties: Plastic materials, such as polypropylene and PVC, offer excellent chemical resistance and are lightweight. They can typically handle temperatures up to 60°C (140°F) and pressures around 6 bar.
Pros & Cons: The primary advantage of plastic is its resistance to corrosion and low cost. However, its lower strength and temperature ratings can limit its use in high-pressure applications. Manufacturing processes for plastic components are generally simpler than for metals.
Impact on Application: Plastic pumps are ideal for transferring corrosive chemicals in industries like agriculture and wastewater management. However, they may not be suitable for high-temperature or high-pressure applications.
Considerations for International Buyers: Buyers should ensure that the plastic materials comply with local and international standards, such as ASTM D1784. Understanding the specific chemical compatibility of the chosen plastic is crucial for effective application.
What About Bronze in Centrifugal Pumps?
Key Properties: Bronze is known for its excellent corrosion resistance, particularly in marine environments. It can handle temperatures up to 200°C (392°F) and pressures exceeding 10 bar.
Pros & Cons: The key advantage of bronze is its durability and resistance to seawater corrosion, making it ideal for marine applications. However, it is more expensive than cast iron and plastic, which may deter some buyers. Manufacturing processes for bronze can be complex and costly.
Impact on Application: Bronze is particularly suited for applications involving seawater or other corrosive environments, such as in shipbuilding or offshore oil rigs. Its strength and resistance to wear also make it suitable for high-performance pumps.
Considerations for International Buyers: Buyers should consider compliance with standards such as ASTM B584 for bronze alloys. Understanding the specific environmental conditions of the application is essential for selecting the right bronze grade.
Summary Table of Material Selection
Material | Typical Use Case for centrifugal pump supplier | Key Advantage | Key Disadvantage/Limitation | Relative Cost (Low/Med/High) |
---|---|---|---|---|
Stainless Steel | Food processing, pharmaceuticals | Excellent corrosion resistance | Higher cost | High |
Cast Iron | Municipal water systems, irrigation | Low cost, good wear resistance | Prone to corrosion | Low |
Plastic | Agriculture, wastewater management | Chemical resistance, lightweight | Lower strength and temperature rating | Low |
Bronze | Marine applications, offshore oil rigs | Excellent corrosion resistance | Higher cost, complex manufacturing | Medium |
This strategic material selection guide provides international B2B buyers with essential insights into the materials used in centrifugal pumps, enabling them to make informed decisions based on their specific operational needs and regional considerations.
In-depth Look: Manufacturing Processes and Quality Assurance for centrifugal pump supplier
What Are the Key Stages in the Manufacturing Process of Centrifugal Pumps?
The manufacturing process for centrifugal pumps is intricate and requires a series of well-defined stages to ensure efficiency and quality. Understanding these stages is crucial for international B2B buyers, especially those from Africa, South America, the Middle East, and Europe.
1. Material Preparation
The first stage involves selecting the right materials. Most centrifugal pumps are made from various metals like stainless steel, cast iron, or bronze, chosen based on their strength and resistance to corrosion. The material undergoes rigorous testing to ensure it meets the required specifications. Suppliers often use advanced technology such as spectrometers to analyze the chemical composition of the materials before proceeding.
2. Forming Techniques
Once the materials are prepared, they undergo forming processes. This may include casting, machining, or forging.
- Casting is commonly used for pump casings, where molten metal is poured into molds to create the desired shape.
- Machining is essential for creating precise components like impellers and shafts, often involving CNC (Computer Numerical Control) technology for accuracy.
- Forging is used for high-stress components, enhancing the material’s strength through deformation.
Each technique has its advantages, and the choice often depends on the specific pump design and application.
3. Assembly Process
After the individual components are formed, they are assembled. This stage requires skilled labor to ensure that each part fits perfectly, as even minor misalignments can lead to performance issues.
- Sub-assembly of components such as the motor and impeller is common before the final assembly.
- The use of jigs and fixtures can enhance assembly precision.
- Adequate lubrication is applied during assembly to reduce friction and wear.
4. Finishing Touches
The final stage involves finishing processes such as surface treatment, painting, and quality checks. Surface treatments like anodizing or galvanizing protect against corrosion and wear.
- Painting not only provides aesthetic value but also adds an extra layer of protection.
- Final inspections are performed to ensure that the pump meets the specified tolerances and quality standards before packaging.
How Is Quality Assurance Implemented in Centrifugal Pump Manufacturing?
Quality assurance (QA) is critical in the manufacturing of centrifugal pumps, especially for international B2B buyers who prioritize reliability and performance.
International Standards for Quality Assurance
Many manufacturers adhere to international standards such as ISO 9001, which outlines a framework for maintaining quality management systems. Compliance with these standards ensures that the manufacturing processes are efficient and that the products meet customer expectations. Other industry-specific certifications include:
- CE Marking: Indicates compliance with European health, safety, and environmental protection standards.
- API Standards: The American Petroleum Institute sets standards specifically for pumps used in the oil and gas industry.
Buyers should inquire about these certifications when assessing potential suppliers.
What Are the Key QC Checkpoints in Centrifugal Pump Manufacturing?
Quality control (QC) involves various checkpoints throughout the manufacturing process. Key QC checkpoints include:
- Incoming Quality Control (IQC): This initial checkpoint ensures that raw materials and components meet specifications before they are used in production.
- In-Process Quality Control (IPQC): Continuous monitoring during the manufacturing process helps identify any deviations from quality standards. This may include measuring dimensions and conducting performance tests.
- Final Quality Control (FQC): Before a pump is shipped, it undergoes comprehensive testing, including hydraulic performance tests, pressure tests, and noise level checks.
What Common Testing Methods Are Used to Ensure Pump Quality?
Ensuring the quality of centrifugal pumps involves various testing methods that assess their performance and reliability. Some common testing methods include:
- Hydraulic Testing: This evaluates the pump’s performance under operating conditions, checking for flow rate and pressure.
- Vibration Analysis: This method identifies potential mechanical issues by measuring vibrations during operation.
- Non-Destructive Testing (NDT): Techniques such as ultrasonic testing or X-ray inspection help detect internal flaws without damaging the components.
How Can B2B Buyers Verify Supplier Quality Control?
International B2B buyers should actively verify the quality control processes of their suppliers to ensure reliability. Here are some actionable steps:
Conduct Supplier Audits
Regular audits of potential suppliers can provide insights into their manufacturing processes and quality assurance measures. Buyers should assess:
- Compliance with international standards.
- Maintenance of equipment and machinery.
- Employee training programs.
Request Quality Assurance Reports
Suppliers should provide detailed QA reports that outline their testing procedures, results, and compliance with standards. This documentation is essential for verifying the quality and reliability of the products.
Engage Third-Party Inspection Services
Utilizing third-party inspection services can further enhance the assurance of product quality. Independent inspectors can verify that the manufacturing processes adhere to specified standards and provide unbiased reports.
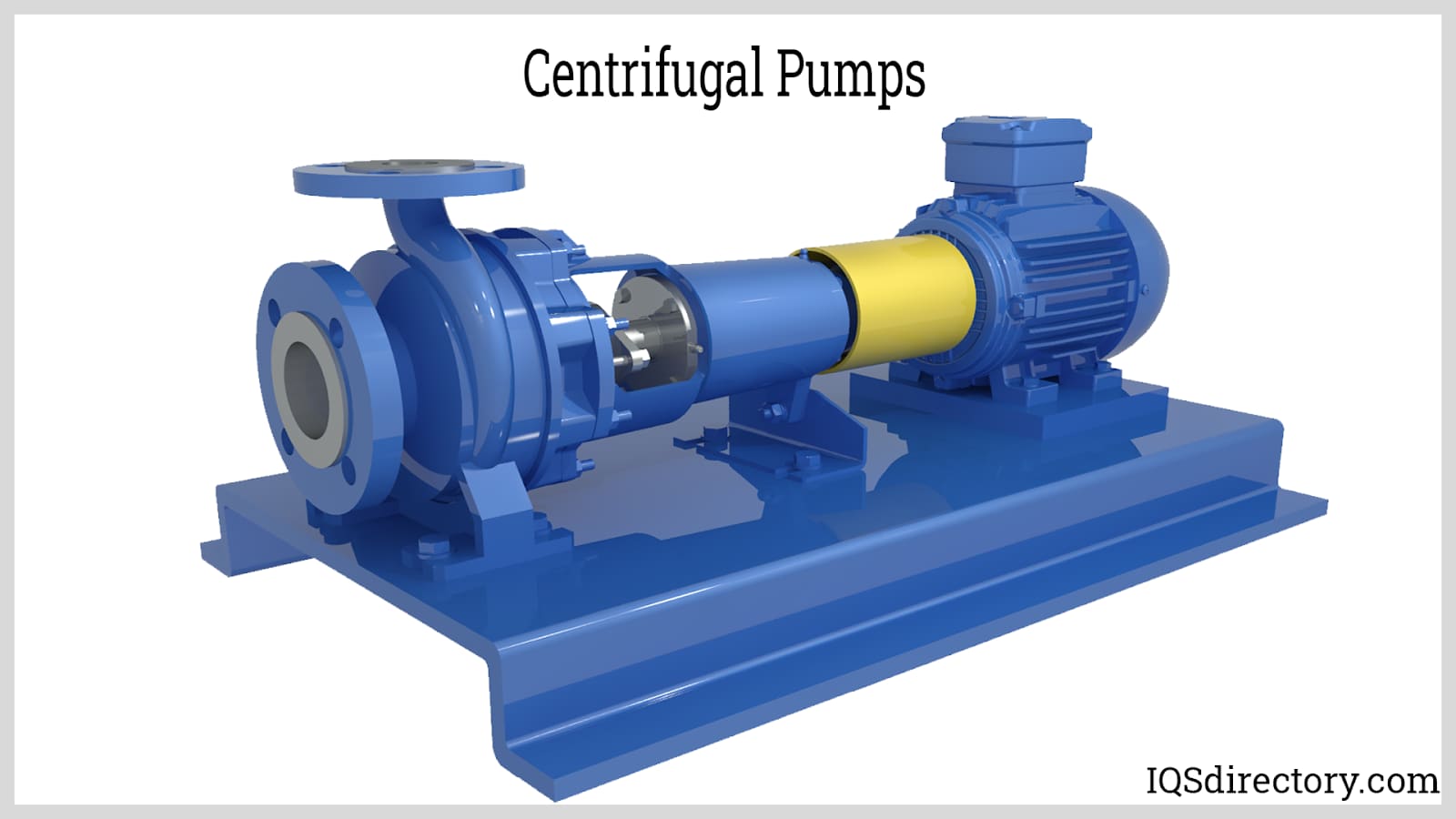
A stock image related to centrifugal pump supplier.
What Are the Quality Control Nuances for International Buyers?
For international buyers, particularly from diverse regions like Africa, South America, the Middle East, and Europe, understanding regional compliance requirements is vital.
- Cultural Differences: Buyers should be aware that quality expectations may vary by region. For instance, European standards may be more stringent than those in other regions.
- Logistical Challenges: International shipments can pose risks such as damage during transport. Ensuring that suppliers have robust packaging and handling protocols is crucial.
- Regulatory Compliance: Buyers should ensure that suppliers comply with local regulations and standards, which may impact the acceptability of products in their markets.
By carefully considering these manufacturing processes and quality assurance measures, B2B buyers can make informed decisions, ensuring that they partner with reliable centrifugal pump suppliers who meet their operational needs.
Practical Sourcing Guide: A Step-by-Step Checklist for ‘centrifugal pump supplier’
In the competitive landscape of international B2B procurement, sourcing a reliable centrifugal pump supplier is critical for ensuring operational efficiency and product quality. This checklist serves as a practical guide to help buyers from regions such as Africa, South America, the Middle East, and Europe navigate the complexities of the sourcing process effectively.
Step 1: Define Your Technical Specifications
Before reaching out to suppliers, it’s essential to have a clear understanding of your technical requirements. This includes determining the type of centrifugal pump needed (e.g., single-stage, multi-stage), the capacity, materials, and any specific features such as energy efficiency or corrosion resistance.
- Why it matters: Clear specifications help streamline the selection process and ensure that suppliers can meet your unique operational needs.
Step 2: Research Potential Suppliers
Conduct thorough research to identify potential suppliers in the centrifugal pump market. Utilize online directories, industry associations, and trade shows to compile a list of manufacturers and distributors.
- What to look for: Focus on suppliers with a proven track record in your industry and positive customer feedback. Pay attention to their market presence, production capabilities, and specialization in centrifugal pumps.
Step 3: Evaluate Supplier Certifications and Compliance
Verify that the suppliers you are considering hold relevant certifications, such as ISO 9001 for quality management or CE marking for European standards.
- Importance: Certifications indicate a commitment to quality and compliance with international standards, which is crucial for ensuring safety and reliability in your operations.
Step 4: Request Quotes and Compare Pricing
Once you have shortlisted potential suppliers, request detailed quotes that include pricing, delivery timelines, and payment terms.
- Comparison criteria: Look beyond just the price; consider the total cost of ownership, including shipping, installation, and maintenance services. This will provide a more accurate picture of the supplier’s value proposition.
Step 5: Assess Supplier Reputation and Reliability
Investigate the reputation of potential suppliers by checking online reviews, seeking references, and reviewing case studies.
- Key indicators: Look for suppliers with a strong history of reliability, timely delivery, and excellent customer service. This will help you gauge their ability to meet your needs consistently.
Step 6: Conduct Factory Visits or Virtual Tours
If feasible, arrange factory visits or virtual tours to observe the manufacturing process and quality control measures firsthand.
- Why this is critical: Direct observation allows you to assess the supplier’s production capabilities and quality assurance processes, ensuring they align with your expectations.
Step 7: Negotiate Terms and Finalize Contracts
Once you have selected a supplier, enter negotiations to establish clear terms regarding pricing, delivery schedules, and after-sales support.
- Contract essentials: Ensure that the contract includes warranties, service agreements, and penalties for non-compliance. Clear terms protect your interests and facilitate smooth transactions.
By following this checklist, international B2B buyers can effectively navigate the sourcing process for centrifugal pumps, ensuring they partner with suppliers that align with their operational needs and business goals.
Comprehensive Cost and Pricing Analysis for centrifugal pump supplier Sourcing
Understanding the cost structure and pricing dynamics of centrifugal pump suppliers is crucial for international B2B buyers, particularly those operating in Africa, South America, the Middle East, and Europe. This analysis will cover the various cost components involved in manufacturing centrifugal pumps, the factors influencing pricing, and practical tips for buyers to optimize their sourcing strategies.
What Are the Key Cost Components of Centrifugal Pumps?
When sourcing centrifugal pumps, buyers should be aware of the following cost components:
-
Materials: The type of materials used significantly impacts the overall cost. Common materials include cast iron, stainless steel, and thermoplastics. Higher-grade materials may offer better corrosion resistance or durability but will increase costs.
-
Labor: Labor costs can vary based on the region and the skill level required for production. Countries with lower labor costs may offer more competitive pricing, but this can sometimes come at the expense of quality.
-
Manufacturing Overhead: This includes expenses related to factory operations, such as utilities, maintenance, and management. Efficient manufacturing processes can help minimize these overhead costs.
-
Tooling: The initial investment in specialized tools and molds can be substantial, particularly for custom designs. Buyers should consider whether these costs are amortized over large production runs.
-
Quality Control (QC): Implementing rigorous QC processes ensures that the pumps meet industry standards and certifications. While this may add to the cost, it can prevent costly returns and replacements.
-
Logistics: Transportation and warehousing costs can significantly affect the final price, especially for international shipping. Factors like distance, mode of transport, and customs duties should be factored in.
-
Margin: Suppliers typically add a profit margin to cover their costs and risks. Understanding the supplier’s cost structure can aid in negotiation.
How Do Pricing Influencers Affect Centrifugal Pump Costs?
Several factors can influence the pricing of centrifugal pumps, including:
-
Volume/MOQ: The minimum order quantity (MOQ) plays a significant role in pricing. Bulk orders often lead to discounts, whereas smaller orders may incur higher per-unit costs.
-
Specifications and Customization: Custom pumps designed to meet specific requirements can be more expensive due to the added complexity in design and manufacturing. Standardized models usually offer better pricing.
-
Quality and Certifications: Pumps that comply with international quality standards and certifications (e.g., ISO, API) may command higher prices but provide assurance of reliability and performance.
-
Supplier Factors: The reputation and experience of the supplier can influence pricing. Established suppliers with a track record of quality may charge a premium but could reduce risks associated with sourcing.
-
Incoterms: The chosen Incoterms (International Commercial Terms) affect the responsibility for shipping, insurance, and tariffs, impacting the overall cost structure. Understanding these terms can help buyers assess the total landed cost.
What Are the Best Negotiation Tips for International B2B Buyers?
To effectively negotiate pricing and optimize costs when sourcing centrifugal pumps, consider the following tips:
-
Research Market Prices: Conduct thorough market research to understand the typical pricing for the pumps you are interested in. This knowledge will empower you during negotiations.
-
Evaluate Total Cost of Ownership (TCO): Focus not just on the purchase price but also on factors like maintenance, energy consumption, and lifespan. A higher initial cost may result in lower TCO over time.
-
Leverage Volume Discounts: If you plan to make multiple purchases, negotiate for better pricing based on volume commitments.
-
Request Detailed Quotes: Ask suppliers for a breakdown of costs. This transparency can reveal areas where you might negotiate reductions.
-
Consider Local Suppliers: For buyers in regions like Africa or South America, sourcing from local suppliers can reduce logistics costs and lead times, offering a competitive edge.
-
Build Long-term Relationships: Establishing a reliable partnership with suppliers can lead to better pricing and service terms in the long run.
Conclusion
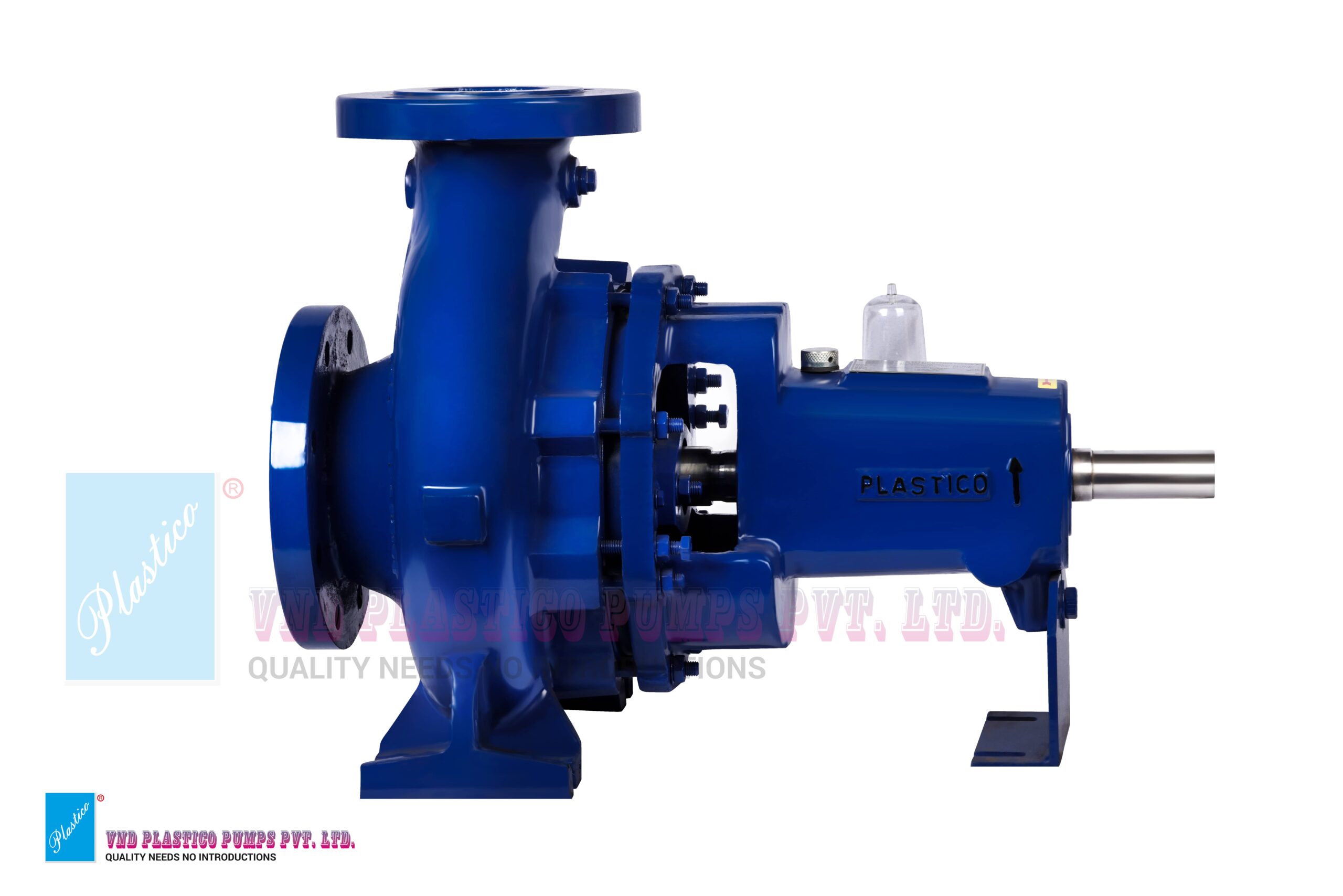
A stock image related to centrifugal pump supplier.
In conclusion, understanding the cost structure and pricing influences of centrifugal pump suppliers is essential for making informed purchasing decisions. By focusing on key cost components, leveraging negotiation strategies, and evaluating the total cost of ownership, international B2B buyers can optimize their sourcing efforts and achieve better value from their suppliers.
Alternatives Analysis: Comparing centrifugal pump supplier With Other Solutions
When evaluating options for fluid transfer solutions, B2B buyers must consider various alternatives to centrifugal pump suppliers. Understanding the strengths and weaknesses of each option can help inform a strategic decision that aligns with business goals, operational efficiency, and budget constraints.
Comparison Aspect | Centrifugal Pump Supplier | Positive Displacement Pump | Peristaltic Pump |
---|---|---|---|
Performance | High flow rates, best for low-viscosity fluids | Better for high-viscosity fluids, consistent flow | Excellent for shear-sensitive fluids, precise dosing |
Cost | Moderate initial investment, variable operating costs | Higher initial cost, lower maintenance costs | Initial cost can vary widely, economical for small-scale |
Ease of Implementation | Generally straightforward installation | More complex setup, requires skilled labor | Simple installation, minimal training required |
Maintenance | Requires regular maintenance, can lead to downtime | Less frequent maintenance, robust design | Low maintenance, hose replacement needed periodically |
Best Use Case | Water treatment, HVAC systems | Chemical processing, food industry | Laboratory applications, medical devices |
What are the Pros and Cons of Positive Displacement Pumps?
Positive displacement pumps are particularly effective for applications that require moving high-viscosity fluids or achieving consistent flow rates regardless of pressure changes. Their robust design can handle a wide range of fluids, making them suitable for industries such as chemical processing and food production. However, they often come with a higher initial investment and more complex installation requirements, which can deter some buyers. Additionally, if not managed properly, these pumps can generate high pressures that might lead to system failures.
How Do Peristaltic Pumps Compare?
Peristaltic pumps excel in applications where precision dosing is crucial, such as in laboratory or medical environments. They operate by compressing a flexible tube, making them ideal for shear-sensitive fluids. Their simple design allows for easy installation and low maintenance, as the only wear part is the hose, which can be replaced without requiring extensive downtime. However, they may not be as efficient for high flow rates as centrifugal pumps and can have variable performance depending on the hose condition.
Conclusion: How Can B2B Buyers Choose the Right Fluid Transfer Solution?
When selecting a fluid transfer solution, B2B buyers should evaluate their specific operational needs, budget, and maintenance capabilities. Centrifugal pumps are suitable for high flow applications with low-viscosity fluids, while positive displacement pumps offer reliability in high-viscosity contexts. Peristaltic pumps shine in precision applications, albeit with some limitations in flow rate. By assessing the unique requirements of their operations and considering the pros and cons of each alternative, buyers can make informed decisions that enhance efficiency and productivity in their processes.
Essential Technical Properties and Trade Terminology for centrifugal pump supplier
What Are the Essential Technical Properties of Centrifugal Pumps?
Understanding the technical properties of centrifugal pumps is crucial for international B2B buyers. These specifications not only influence the performance and reliability of the pumps but also impact long-term operational costs.
1. Material Grade: Why Does It Matter?
The material grade of a centrifugal pump determines its resistance to corrosion, wear, and temperature fluctuations. Common materials include stainless steel, cast iron, and various plastics. For instance, stainless steel is preferred in chemical applications due to its resistance to aggressive substances. Selecting the right material can minimize maintenance costs and enhance the pump’s lifespan, making it a vital consideration for buyers in industries such as oil and gas, agriculture, and water treatment.
2. Tolerance: What Role Does It Play?
Tolerance refers to the permissible limit or limits of variation in a physical dimension. In centrifugal pumps, tight tolerances are essential for ensuring efficient operation and reducing the risk of mechanical failure. For example, a tolerance of ±0.01 mm in the impeller shaft can significantly affect pump efficiency. Buyers should prioritize suppliers who adhere to stringent tolerance standards to ensure optimal performance and reliability.
3. Flow Rate: How Is It Calculated?
Flow rate, measured in cubic meters per hour (m³/h), indicates the volume of fluid a pump can move in a given time. This specification is critical for selecting a pump that meets the specific needs of an application. Understanding the required flow rate helps buyers avoid oversizing or undersizing the pump, which can lead to inefficiencies or operational issues.
4. Efficiency: Why Is It Important?
Pump efficiency, usually expressed as a percentage, measures how effectively a pump converts input power into hydraulic energy. Higher efficiency means lower operational costs and less energy consumption, which is particularly important for businesses looking to reduce their carbon footprint. Buyers should seek centrifugal pumps with high-efficiency ratings to ensure cost-effectiveness in the long run.
5. Net Positive Suction Head (NPSH): What Should You Know?
NPSH is the minimum pressure required at the pump suction to avoid cavitation, which can cause significant damage. Understanding the NPSH available in a system versus the NPSH required by the pump is essential for preventing operational issues. B2B buyers should consider this property when evaluating pump installations, especially in regions with variable atmospheric pressures.
What Are Common Trade Terminology and Jargon in the Centrifugal Pump Industry?
Understanding industry terminology is equally crucial for effective communication and negotiation with suppliers. Here are some key terms to know:
1. OEM (Original Equipment Manufacturer): What Does It Mean?
OEM refers to companies that produce parts or equipment that may be marketed by another manufacturer. In the context of centrifugal pumps, an OEM may design and manufacture pumps that are then branded and sold by larger companies. Buyers should be aware of OEM relationships to ensure they are sourcing quality products.
2. MOQ (Minimum Order Quantity): Why Is It Significant?
MOQ denotes the smallest quantity of a product that a supplier is willing to sell. Understanding MOQ is vital for buyers as it affects inventory management and initial investment. Suppliers with low MOQs can be advantageous for smaller businesses or those testing new products.
3. RFQ (Request for Quotation): How Should You Use It?
An RFQ is a document sent to suppliers requesting pricing and terms for specific products. For buyers, submitting RFQs can lead to competitive pricing and better negotiation terms. It’s essential to detail all required specifications in an RFQ to ensure accurate quotes.
4. Incoterms (International Commercial Terms): Why Are They Important?
Incoterms are internationally recognized rules that define the responsibilities of buyers and sellers in international transactions. Understanding Incoterms helps buyers clarify shipping, insurance, and liability issues, which are critical when sourcing pumps from overseas suppliers.
5. Lead Time: How Does It Impact Your Purchase?
Lead time is the duration between placing an order and receiving the product. For B2B buyers, understanding lead times is crucial for project planning and ensuring timely operations. Suppliers with shorter lead times can provide a competitive advantage in industries where time is critical.
By familiarizing yourself with these technical properties and trade terminologies, you can make more informed purchasing decisions, ultimately leading to better outcomes for your business.
Navigating Market Dynamics and Sourcing Trends in the centrifugal pump supplier Sector
What Are the Current Market Dynamics and Key Trends in the Centrifugal Pump Supplier Sector?
The centrifugal pump supplier sector is experiencing significant transformation driven by global industrialization and the increasing demand for efficient fluid handling solutions. Key market drivers include the rise of emerging economies in Africa and South America, where infrastructure development is accelerating. Additionally, the demand for sustainable and energy-efficient solutions is reshaping the market landscape, with B2B buyers increasingly prioritizing suppliers that can demonstrate innovation in energy conservation and operational efficiency.
Emerging technologies such as IoT and AI are revolutionizing the way centrifugal pumps are monitored and maintained. Smart pumps equipped with sensors can provide real-time data on performance, enabling predictive maintenance that reduces downtime and operational costs. This technological shift is particularly relevant for international buyers seeking to enhance their operational efficiencies while minimizing risks associated with equipment failure.
Furthermore, the market is witnessing a trend towards customization, as buyers look for tailored solutions that meet specific operational needs. This demand for bespoke solutions is prompting suppliers to invest in advanced manufacturing processes, including 3D printing and modular design, to better serve diverse markets, especially in regions like the Middle East and Europe.
How Is Sustainability and Ethical Sourcing Shaping the Centrifugal Pump Supplier Industry?
The centrifugal pump supplier sector is increasingly aligning itself with sustainability goals, reflecting a broader global commitment to environmental stewardship. The environmental impact of manufacturing processes is under scrutiny, with buyers demanding transparency regarding the sourcing of materials and the sustainability of production methods. Ethical sourcing is becoming a critical criterion for B2B buyers, particularly in regions where regulatory frameworks are evolving to enforce stricter environmental standards.
Sustainability certifications, such as ISO 14001, are gaining importance, as they indicate a supplier’s commitment to reducing their environmental footprint. Additionally, the use of ‘green’ materials—such as recyclable components and low-impact manufacturing processes—has become a key differentiator in supplier selection. B2B buyers are encouraged to engage with suppliers who prioritize ethical sourcing, as this not only enhances corporate responsibility but can also lead to long-term cost savings through energy efficiency and reduced waste.
In conclusion, sustainability and ethical sourcing are not just trends; they are essential factors that influence purchasing decisions in the centrifugal pump supplier sector. Buyers who align with suppliers that share these values are likely to benefit from enhanced brand reputation and customer loyalty.
What Is the Historical Context of the Centrifugal Pump Supplier Sector?
The centrifugal pump industry has evolved significantly since its inception in the late 19th century, initially driven by agricultural and industrial needs. Early designs focused primarily on mechanical efficiency, but as industries grew and technology advanced, the focus shifted toward reliability and versatility.
The introduction of electric motors in the mid-20th century transformed the sector, allowing for more compact designs and greater operational flexibility. Over the last few decades, the industry has embraced digital transformation, with advancements in automation and data analytics leading to smarter, more efficient pumping solutions. This evolution has set the stage for the current focus on sustainability and ethical sourcing, reflecting the industry’s response to modern environmental challenges and the expectations of B2B buyers worldwide.
In summary, understanding these historical trends provides valuable context for international buyers as they navigate the complexities of the centrifugal pump supplier market today.
Frequently Asked Questions (FAQs) for B2B Buyers of centrifugal pump supplier
-
How do I choose the right centrifugal pump supplier for my business?
When selecting a centrifugal pump supplier, consider their industry experience, product range, and customer reviews. Evaluate their ability to provide technical support and after-sales service. It’s also essential to confirm their compliance with international standards and certifications, particularly if you are sourcing from different regions. Request case studies or references to gauge their reliability and performance in similar applications to yours. -
What are the key specifications I should look for in centrifugal pumps?
Key specifications include flow rate, head pressure, efficiency, and the materials used in construction. Assess the pump’s compatibility with the fluids you’ll be handling, including temperature and viscosity. Additionally, consider the pump’s energy consumption, maintenance requirements, and whether it can accommodate future scalability needs as your operations grow. -
What are common payment terms when sourcing centrifugal pumps internationally?
Payment terms can vary widely by supplier and region. Common options include advance payment, letters of credit, and net payment terms (e.g., net 30 or net 60 days). Ensure you negotiate terms that provide a balance of risk and convenience, particularly if you’re dealing with suppliers from different countries. It’s advisable to consult with a trade finance expert to secure favorable conditions.
-
What should I know about the minimum order quantity (MOQ) for centrifugal pumps?
Minimum order quantities can significantly impact your purchasing strategy. Suppliers often set MOQs based on production costs and inventory levels. If you require smaller quantities, inquire about flexibility in MOQs or whether they offer a range of products that could meet your needs. Building a long-term relationship with suppliers may also enable negotiations for lower MOQs over time. -
How can I ensure the quality of centrifugal pumps from my supplier?
To ensure quality, request documentation of certifications and compliance with international standards like ISO or API. Conduct factory audits if possible, or utilize third-party inspection services to verify product quality before shipment. Additionally, assess the supplier’s warranty and return policy to safeguard your investment in case of defects or performance issues. -
What logistics considerations should I keep in mind when importing centrifugal pumps?
Logistics can be complex when importing equipment like centrifugal pumps. Consider shipping methods, customs regulations, and potential tariffs that may apply. Work closely with a freight forwarder who understands the nuances of international shipping and can provide guidance on the best practices for transporting heavy machinery. Ensure that you have the necessary documentation ready to avoid delays at customs. -
Can centrifugal pumps be customized to meet specific operational needs?
Yes, many suppliers offer customization options for centrifugal pumps to accommodate specific applications. Customizations may include adjustments in size, materials, and performance specifications. When discussing customization, clearly outline your operational requirements and any constraints. This dialogue can also lead to recommendations on the most suitable pump models tailored to your needs. -
What are the best practices for vetting a centrifugal pump supplier?
When vetting suppliers, conduct thorough research to evaluate their reputation, financial stability, and client feedback. Utilize online resources, industry networks, and trade associations for insights. Request samples or trial units to assess product performance and quality firsthand. Establishing clear communication and understanding their customer support capabilities will also help ensure a good partnership moving forward.
Important Disclaimer & Terms of Use
⚠️ Important Disclaimer
The information provided in this guide, including content regarding manufacturers, technical specifications, and market analysis, is for informational and educational purposes only. It does not constitute professional procurement advice, financial advice, or legal advice.
While we have made every effort to ensure the accuracy and timeliness of the information, we are not responsible for any errors, omissions, or outdated information. Market conditions, company details, and technical standards are subject to change.
B2B buyers must conduct their own independent and thorough due diligence before making any purchasing decisions. This includes contacting suppliers directly, verifying certifications, requesting samples, and seeking professional consultation. The risk of relying on any information in this guide is borne solely by the reader.
Strategic Sourcing Conclusion and Outlook for centrifugal pump supplier
What Are the Key Takeaways for Strategic Sourcing of Centrifugal Pumps?
In conclusion, strategic sourcing is paramount for international B2B buyers seeking reliable centrifugal pump suppliers. Establishing strong relationships with manufacturers not only ensures access to high-quality products but also supports long-term operational efficiency. Buyers from regions such as Africa, South America, the Middle East, and Europe should focus on suppliers that offer robust after-sales support, compliance with local regulations, and adaptability to specific industry needs.
How Can Buyers Prepare for Future Sourcing Opportunities?
As the market for centrifugal pumps continues to evolve, driven by technological advancements and increasing sustainability concerns, buyers must stay informed. Engaging with suppliers who prioritize innovation and eco-friendly practices will be crucial. Furthermore, leveraging digital tools for supplier evaluations and performance tracking can enhance decision-making processes.
What Is the Next Step for International Buyers?
As you consider your sourcing strategy, take proactive steps to evaluate potential suppliers thoroughly. Conduct market research, attend industry trade shows, and initiate discussions with suppliers to gauge their capabilities. By doing so, you position your business to benefit from the best available options in the centrifugal pump market, ensuring both immediate and long-term success. Embrace the future of sourcing with confidence and commitment to quality.