The Ultimate Guide to Check Valve Manufacturer (2025)
Introduction: Navigating the Global Market for check valve manufacturer
Navigating the global market for check valve manufacturers can be daunting for B2B buyers, especially when sourcing reliable suppliers that meet quality, compliance, and cost-effectiveness requirements. With various types of check valves—such as swing, ball, and diaphragm valves—each with distinct applications across industries like oil and gas, water treatment, and pharmaceuticals, understanding these nuances is crucial. This guide is designed to equip international B2B buyers, particularly those from Africa, South America, the Middle East, and Europe (including the UK and Colombia), with actionable insights that simplify the purchasing process.
In the following sections, we will explore critical aspects of sourcing check valves, including detailed descriptions of different types, their applications, and the vetting process for suppliers. Additionally, we will provide insights into cost considerations, market trends, and best practices for establishing long-term supplier relationships. By leveraging this comprehensive guide, you will be empowered to make informed purchasing decisions that not only enhance operational efficiency but also ensure compliance with international standards.
Understanding the complexities of the check valve market can ultimately lead to improved project outcomes and reduced risks. Thus, let’s delve into the essentials of navigating this global landscape and uncover strategies that will serve your business’s needs effectively.
Understanding check valve manufacturer Types and Variations
Type Name | Key Distinguishing Features | Primary B2B Applications | Brief Pros & Cons for Buyers |
---|---|---|---|
Swing Check Valve | Utilizes a swinging disc to allow flow in one direction; typically has a low-pressure drop. | Water treatment, HVAC systems | Pros: Low maintenance, cost-effective. Cons: May be less effective in low flow conditions. |
Lift Check Valve | Operates with a vertical disc that lifts to allow flow; suitable for high-pressure applications. | Oil and gas, chemical processing | Pros: Efficient in high-pressure systems. Cons: More complex, higher maintenance costs. |
Ball Check Valve | Features a ball that moves to block flow; offers tight sealing and minimal leakage. | Pump protection, irrigation systems | Pros: Excellent sealing, versatile. Cons: Can be more expensive than other types. |
Dual Plate Check Valve | Contains two plates that open and close rapidly; designed for high flow rates and low pressure drop. | Pipeline systems, power plants | Pros: Compact design, quick response. Cons: Higher initial cost, may require specific installation conditions. |
Spring Check Valve | Uses a spring to hold the valve closed until upstream pressure opens it; effective in preventing backflow. | Fire protection systems, drainage | Pros: Reliable backflow prevention. Cons: Spring wear can lead to failure over time. |
What Are the Key Characteristics of Swing Check Valves?
Swing check valves are designed with a disc that swings open to permit flow and closes when backflow occurs. They are particularly useful in applications where the pressure drop needs to be minimized, such as in water treatment and HVAC systems. B2B buyers should consider the maintenance requirements and installation space, as these valves can be bulkier than others.
How Do Lift Check Valves Operate in High-Pressure Environments?
Lift check valves feature a disc that lifts off its seat when flow is present, allowing for efficient operation in high-pressure applications like oil and gas. These valves are known for their durability and are suitable for heavy industrial use. Buyers should assess the complexity of installation and potential maintenance costs, as they may require more frequent servicing than simpler designs.
What Are the Advantages of Ball Check Valves?
Ball check valves utilize a ball that blocks flow when backpressure is present, providing excellent sealing capabilities. They are versatile and can be used in various applications, including pump protection and irrigation systems. While they offer minimal leakage, buyers should evaluate the cost-effectiveness of this option against its higher price point compared to other valve types.
Why Choose Dual Plate Check Valves for Pipeline Systems?
Dual plate check valves are designed with two plates that open and close quickly, making them ideal for high flow rates and low pressure drops. Their compact design allows for easier installation in tight spaces, particularly in pipeline systems and power plants. However, potential buyers should be aware of the higher initial investment and ensure compatibility with existing systems.
What Are the Considerations for Spring Check Valves?
Spring check valves leverage a spring mechanism to keep the valve closed until upstream pressure forces it open, effectively preventing backflow. They are commonly used in fire protection and drainage systems. Buyers need to consider the longevity of the spring, as wear can lead to valve failure, impacting system reliability. Regular inspections and maintenance are crucial to ensure optimal performance.
Related Video: what is the most common type check valve?How to find a qualified manufacturer for check valve?
Key Industrial Applications of check valve manufacturer
Industry/Sector | Specific Application of Check Valve Manufacturer | Value/Benefit for the Business | Key Sourcing Considerations for this Application |
---|---|---|---|
Oil and Gas | Preventing backflow in pipelines | Ensures safety and efficiency in fluid transport | Material compatibility, pressure ratings, and certifications |
Water Treatment | Controlling flow in treatment plants | Enhances operational efficiency and reduces downtime | Maintenance requirements, size specifications, and installation ease |
Food and Beverage | Maintaining hygiene in processing systems | Ensures product quality and compliance with regulations | FDA compliance, material certifications, and ease of cleaning |
Chemical Manufacturing | Managing corrosive substances in processing | Minimizes leaks and protects equipment integrity | Material specifications, temperature tolerance, and reliability |
HVAC Systems | Regulating flow in heating and cooling systems | Improves energy efficiency and system reliability | Size, pressure ratings, and compatibility with existing systems |
How are Check Valves Applied in Oil and Gas Industries?
In the oil and gas sector, check valves are critical for preventing backflow in pipelines, which can lead to significant safety hazards and operational inefficiencies. By ensuring that fluids flow in one direction, these valves protect equipment from damage and reduce the risk of spills. International buyers, particularly from regions like Africa and the Middle East, should consider sourcing check valves that meet specific material compatibility standards to handle the corrosive nature of oil and gas. Additionally, pressure ratings and certifications are essential to ensure compliance with industry regulations.
What Role do Check Valves Play in Water Treatment Facilities?
Check valves are used extensively in water treatment plants to control the flow of water through various processes. They help maintain the integrity of the system by preventing backflow, which can contaminate treated water. For buyers in South America and Europe, it is crucial to evaluate the maintenance requirements and size specifications of these valves to ensure optimal performance. The ability to withstand varying pressure conditions is also a key consideration, as it directly impacts operational efficiency and reduces downtime.
Why are Check Valves Important in Food and Beverage Processing?
In the food and beverage industry, maintaining hygiene and product quality is paramount. Check valves play a vital role in processing systems by ensuring that fluids do not reverse flow, which could lead to contamination. B2B buyers, particularly from Europe, must prioritize sourcing check valves that comply with FDA regulations and are made from materials that are easy to clean. This attention to compliance and maintenance facilitates smooth operations and upholds the quality standards required in food production.
How do Check Valves Enhance Safety in Chemical Manufacturing?
Check valves in chemical manufacturing are essential for managing the flow of corrosive substances. They prevent leaks that could lead to dangerous spills and equipment damage, thus enhancing workplace safety. Buyers from Africa and South America should focus on sourcing valves that meet specific material specifications and temperature tolerances, as these factors directly influence reliability and longevity. Investing in high-quality check valves can significantly minimize the risk of accidents and protect both personnel and equipment.
What Benefits do Check Valves Provide in HVAC Systems?
In HVAC systems, check valves regulate the flow of air and fluids, contributing to the overall energy efficiency of the system. By preventing backflow, these valves help maintain consistent temperature control and system reliability. For international buyers in Europe and the Middle East, sourcing the right size and pressure-rated check valves is crucial for compatibility with existing systems. Ensuring that the valves can withstand the operational demands of HVAC applications will lead to improved performance and reduced energy costs.
3 Common User Pain Points for ‘check valve manufacturer’ & Their Solutions
Scenario 1: Difficulty Sourcing High-Quality Check Valves
The Problem: Many B2B buyers, particularly those in emerging markets such as Africa and South America, struggle to source high-quality check valves that meet international standards. They often encounter a mix of manufacturers, some of which may offer subpar products that fail to meet necessary specifications. This can lead to operational failures, increased downtime, and financial losses. Buyers may feel overwhelmed by the vast number of options and uncertain about how to verify the quality and reliability of manufacturers.
The Solution: To effectively source high-quality check valves, buyers should begin by conducting thorough research on potential manufacturers. Look for certifications such as ISO 9001, which indicates adherence to quality management standards. Utilize industry forums and trade shows to connect directly with manufacturers and ask for references or case studies demonstrating their product reliability. Additionally, consider engaging third-party quality assurance services to inspect products before shipment. This proactive approach will help ensure that the check valves purchased are durable, reliable, and suitable for your specific applications.
Scenario 2: Inconsistent Technical Specifications and Compatibility Issues
The Problem: Another common pain point is the inconsistency in technical specifications provided by different manufacturers. Buyers often face challenges when trying to ensure that the check valves they order are compatible with existing systems. This can lead to costly mistakes, such as ordering valves that do not fit or function as required, causing project delays and additional expenses.
The Solution: To mitigate compatibility issues, buyers should prioritize clear communication with manufacturers regarding specifications. Before placing an order, create a detailed checklist that includes all necessary parameters such as size, pressure ratings, and materials of construction. Request technical data sheets and product samples to evaluate compatibility with your systems. Engaging a technical consultant can also be beneficial; they can provide expert advice on selecting the right check valves based on your specific application and operational conditions. This collaborative approach will help streamline the procurement process and reduce the likelihood of costly errors.
Scenario 3: Limited After-Sales Support and Warranty Challenges
The Problem: Buyers often find that after-sales support is lacking, which can lead to frustration when issues arise post-purchase. Without adequate support, companies may struggle with installation, maintenance, or troubleshooting of check valves, particularly if they encounter defects or performance issues. This lack of support can hinder operational efficiency and increase the total cost of ownership.
The Solution: When selecting a check valve manufacturer, prioritize those that offer comprehensive after-sales support and robust warranty options. Inquire about the manufacturer’s customer service response times and whether they provide on-site assistance or remote troubleshooting. Additionally, make sure to understand the warranty terms clearly—what is covered, for how long, and under what conditions. Establishing a good relationship with the manufacturer can also facilitate better support; don’t hesitate to communicate your needs and expectations upfront. By choosing a manufacturer that values customer service, buyers can ensure they receive the ongoing support necessary to maintain operational efficiency and minimize downtime.
Strategic Material Selection Guide for check valve manufacturer
What Are the Key Materials Used in Check Valve Manufacturing?
When selecting materials for check valves, manufacturers typically consider factors such as temperature and pressure ratings, corrosion resistance, and compatibility with specific media. Here, we analyze four common materials used in check valve manufacturing: stainless steel, brass, plastic, and cast iron. Each material has distinct properties, advantages, and disadvantages that can significantly impact the performance and suitability of the check valves in various applications.
How Does Stainless Steel Perform in Check Valve Applications?
Key Properties:
Stainless steel check valves are known for their excellent corrosion resistance, high strength, and ability to withstand high temperatures and pressures. They typically have a temperature rating of up to 800°F (427°C) and can handle pressures exceeding 3000 psi, depending on the grade.
Pros & Cons:
The primary advantage of stainless steel is its durability and longevity, making it suitable for harsh environments, including chemical processing and oil and gas industries. However, it tends to be more expensive than other materials and may require complex manufacturing processes, which can increase lead times.
Impact on Application:
Stainless steel is compatible with a wide range of media, including water, steam, and various chemicals. This versatility makes it a preferred choice for international buyers needing reliable performance in diverse applications.
Considerations for International Buyers:
When purchasing stainless steel check valves, buyers should ensure compliance with international standards such as ASTM or DIN. Additionally, understanding local regulations regarding corrosion resistance and material certifications is crucial.
What Are the Advantages of Brass in Check Valve Manufacturing?
Key Properties:
Brass check valves offer good corrosion resistance and are suitable for moderate temperature and pressure applications, typically rated up to 250°F (121°C) and 150 psi.
Pros & Cons:
Brass is relatively easy to machine and has a lower cost compared to stainless steel, making it an attractive option for many applications. However, it is less durable than stainless steel and may not perform well in highly corrosive environments, limiting its use in certain industries.
Impact on Application:
Brass is commonly used in plumbing and HVAC applications due to its compatibility with water and air. However, it may not be suitable for aggressive chemicals, which can lead to premature failure.
Considerations for International Buyers:
Buyers should verify that brass check valves meet relevant standards, such as JIS or ASTM, especially when importing from different regions. Understanding the local market’s preferences for materials can also influence purchasing decisions.
How Do Plastic Check Valves Compare in Terms of Performance?
Key Properties:
Plastic check valves, typically made from PVC or CPVC, are lightweight and resistant to corrosion. They are generally rated for temperatures up to 140°F (60°C) and pressures around 150 psi.
Pros & Cons:
The main advantage of plastic check valves is their cost-effectiveness and ease of installation. However, their lower temperature and pressure ratings limit their use in high-stress applications, making them less suitable for industrial uses.
Impact on Application:
Plastic valves are ideal for water treatment and chemical processing applications where corrosive substances are present. However, they may not be appropriate for high-temperature steam applications.
Considerations for International Buyers:
Buyers in regions with varying temperature and pressure requirements should assess whether plastic check valves meet local standards and regulations. Additionally, understanding the environmental impact of plastic materials is increasingly important in many markets.
What Role Does Cast Iron Play in Check Valve Manufacturing?
Key Properties:
Cast iron check valves are known for their strength and durability, with temperature ratings up to 400°F (204°C) and pressure ratings around 200 psi.
Pros & Cons:
The primary advantage of cast iron is its robustness, making it suitable for heavy-duty applications. However, it is prone to corrosion and may require protective coatings, which can increase maintenance costs.
Impact on Application:
Cast iron is commonly used in municipal water systems and industrial applications where durability is essential. However, its weight and susceptibility to corrosion can be drawbacks in certain environments.
Considerations for International Buyers:
Buyers should ensure that cast iron check valves comply with local standards, especially in regions where corrosion resistance is critical. Understanding the implications of weight and transport costs is also important for international shipping.
Summary Table of Material Selection for Check Valve Manufacturers
Material | Typical Use Case for check valve manufacturer | Key Advantage | Key Disadvantage/Limitation | Relative Cost (Low/Med/High) |
---|---|---|---|---|
Stainless Steel | Chemical processing, oil and gas | Excellent corrosion resistance | Higher cost and manufacturing complexity | High |
Brass | Plumbing, HVAC applications | Cost-effective and easy to machine | Less durable in corrosive environments | Medium |
Plastic | Water treatment, chemical processing | Lightweight and cost-effective | Limited temperature and pressure ratings | Low |
Cast Iron | Municipal water systems, heavy-duty applications | Robust and durable | Prone to corrosion and heavy weight | Medium |
This strategic material selection guide provides B2B buyers with essential insights into the properties, advantages, and limitations of various materials used in check valve manufacturing. Understanding these factors can help inform purchasing decisions and ensure compliance with international standards.
In-depth Look: Manufacturing Processes and Quality Assurance for check valve manufacturer
What Are the Typical Manufacturing Processes for Check Valves?
Manufacturing check valves involves several key stages that ensure the final product meets performance and quality standards. Understanding these processes is crucial for international B2B buyers, particularly those in regions like Africa, South America, the Middle East, and Europe.
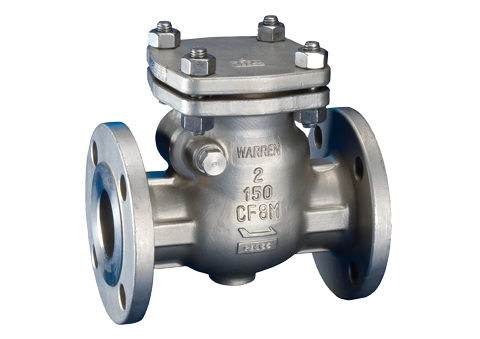
A stock image related to check valve manufacturer.
How Is Material Prepared for Check Valve Manufacturing?
The first stage in the manufacturing process is material preparation. Common materials used for check valves include stainless steel, brass, and PVC.
-
Material Selection: The choice of material depends on the intended application of the check valve. For instance, stainless steel is preferred for high-pressure applications due to its corrosion resistance.
-
Cutting and Sizing: Raw materials are cut to specified dimensions using advanced cutting technologies, such as laser cutting or water jet cutting. This precision ensures that each component fits seamlessly during assembly.
-
Surface Treatment: Materials often undergo surface treatments, like sandblasting or polishing, to enhance their durability and resistance to wear.
What Are the Key Forming Techniques Used in Check Valve Manufacturing?
The forming stage is critical as it shapes the valve components. Various techniques are employed, depending on the complexity and design of the check valve.
-
Casting: For complex shapes, casting is commonly used. Molten metal is poured into a mold to create components like valve bodies.
-
Machining: CNC (Computer Numerical Control) machining is employed to achieve precise dimensions and tolerances. This technique is vital for components like seats and discs, which require a high degree of accuracy.
-
Forging: For high-strength applications, forging may be used. This process involves shaping the metal while it is heated, resulting in enhanced structural integrity.
How Is Assembly Conducted in Check Valve Manufacturing?
Assembly is where individual components come together to form the finished product.
-
Component Verification: Before assembly, each component is inspected for defects and conformity to specifications.
-
Joining Techniques: Various joining methods, such as welding, threading, or the use of adhesive, are used depending on the material and design requirements.
-
Final Assembly: The components are assembled in a clean environment to prevent contamination. Each valve is fitted with seals and gaskets to ensure leak-proof operation.
What Finishing Processes Are Involved in Check Valve Manufacturing?
Finishing processes enhance the valve’s performance and aesthetic appeal.
-
Coating: Many manufacturers apply protective coatings to prevent corrosion and wear. Common coatings include epoxy and Teflon.
-
Final Inspection: A comprehensive inspection is performed post-finishing to ensure that the valve meets all specifications and is free from defects.
-
Packaging: Finished check valves are packaged in a manner that prevents damage during transit. Proper labeling is crucial for easy identification.
How Is Quality Assurance Implemented in Check Valve Manufacturing?
Quality assurance is a vital aspect of manufacturing check valves, ensuring that each product meets international standards and customer expectations.
Which International Standards Should B2B Buyers Consider?
B2B buyers should be aware of the various international standards that govern check valve manufacturing.
-
ISO 9001: This standard outlines the requirements for a quality management system (QMS). Manufacturers with ISO 9001 certification demonstrate a commitment to consistent quality and continuous improvement.
-
CE Marking: For products sold within the European Union, CE marking indicates compliance with health, safety, and environmental protection standards.
-
API Standards: The American Petroleum Institute (API) sets standards specifically for valves used in the oil and gas industry, ensuring reliability under extreme conditions.
What Are the Key Quality Control Checkpoints in Manufacturing?
Quality control (QC) involves several checkpoints throughout the manufacturing process:
-
Incoming Quality Control (IQC): This initial inspection assesses raw materials and components upon arrival to ensure they meet specifications.
-
In-Process Quality Control (IPQC): Throughout manufacturing, operators conduct checks to monitor compliance with quality standards. This includes dimensional checks and functional tests.
-
Final Quality Control (FQC): Before packaging, a final inspection is conducted, which may include pressure tests, leak tests, and functional assessments to ensure the valve operates correctly.
What Common Testing Methods Are Used for Check Valves?
Testing methods are crucial for verifying the performance and safety of check valves.
-
Hydrostatic Testing: This method involves filling the valve with water and pressurizing it to check for leaks and structural integrity.
-
Functional Testing: This assesses the valve’s operational performance under simulated conditions to ensure it opens and closes correctly.
-
Non-Destructive Testing (NDT): Techniques like ultrasonic testing and magnetic particle testing are used to detect internal flaws without damaging the valve.
How Can B2B Buyers Verify a Supplier’s Quality Control?
For international B2B buyers, verifying a supplier’s quality control processes is essential for ensuring product reliability.
-
Audits: Conducting on-site audits of the manufacturer can provide insights into their quality control processes and adherence to international standards.
-
Quality Reports: Requesting detailed quality reports and certifications can help assess the supplier’s commitment to quality assurance.
-
Third-Party Inspections: Engaging third-party inspection services can provide an unbiased evaluation of the supplier’s manufacturing and quality control practices.
What Are the QC and Certification Nuances for International B2B Buyers?
International B2B buyers, especially from diverse regions like Africa, South America, the Middle East, and Europe, should be aware of specific nuances related to quality control and certification.
-
Regional Standards: Different regions may have unique certification requirements. Buyers should familiarize themselves with local regulations and standards applicable to their markets.
-
Documentation: Proper documentation is crucial for customs clearance and compliance with regional regulations. Ensure that all certificates and reports are available and accurate.
-
Cultural Sensitivity: Understanding cultural differences in business practices can enhance communication and foster stronger supplier relationships.
By comprehensively understanding the manufacturing processes and quality assurance measures in the check valve industry, international B2B buyers can make informed decisions, ensuring they source reliable and high-quality products that meet their specific needs.
Practical Sourcing Guide: A Step-by-Step Checklist for ‘check valve manufacturer’
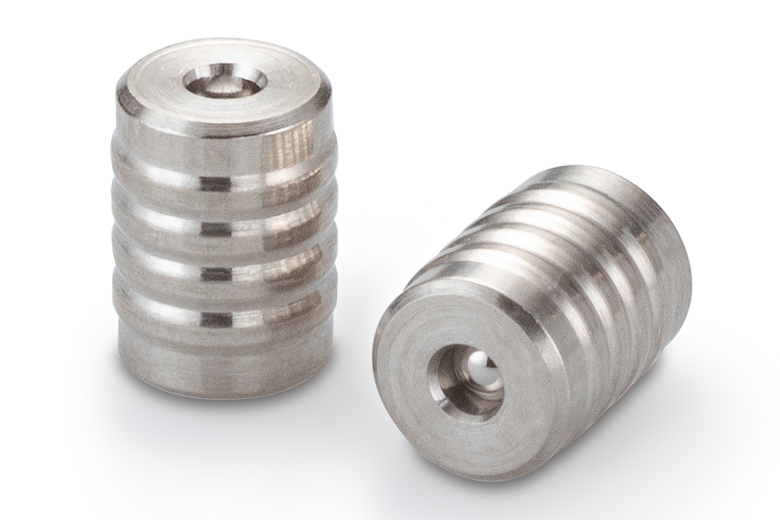
A stock image related to check valve manufacturer.
The purpose of this guide is to provide international B2B buyers with a comprehensive checklist for sourcing check valve manufacturers effectively. This structured approach will help ensure that buyers make informed decisions, minimize risks, and secure high-quality products that meet their operational needs.
Step 1: Define Your Technical Specifications
Establishing clear technical specifications is essential before approaching manufacturers. This includes understanding the required materials, pressure ratings, sizes, and any specific industry standards that the check valves must meet. By detailing these requirements, you can filter potential suppliers who can actually fulfill your needs.
Step 2: Research Potential Manufacturers
Conduct thorough research to identify manufacturers with a solid reputation in the check valve industry. Look for companies that have been in business for several years and specialize in the type of check valves you need. Utilize online resources, industry directories, and trade associations to compile a list of potential suppliers.
Step 3: Evaluate Supplier Certifications and Compliance
✅ Verify Supplier Certifications
It is crucial to ensure that the manufacturers possess relevant certifications such as ISO 9001, which indicates a commitment to quality management systems. Additionally, check for compliance with regional standards, such as the American Petroleum Institute (API) standards for oil and gas applications, to guarantee the product’s reliability and safety.
Step 4: Request Samples and Conduct Quality Checks
Before making a bulk purchase, request samples of the check valves. This step allows you to assess the quality and performance firsthand. Ensure that the samples meet your specifications and perform adequately under expected operational conditions. Conducting these quality checks can prevent costly mistakes later on.
Step 5: Inquire About Lead Times and Production Capacity
Understanding the manufacturer’s lead times and production capacity is vital for planning your procurement process. Ask about their average turnaround time for orders and their ability to handle large or urgent requests. Reliable suppliers should be transparent about their capabilities and any potential delays.
Step 6: Review Pricing and Payment Terms
Compare pricing from different manufacturers while ensuring that you are not compromising on quality. Discuss payment terms, including deposit requirements and payment methods. Transparent pricing structures and flexible payment options can significantly impact your cash flow and overall project budget.
Step 7: Assess After-Sales Support and Warranty Policies
Finally, evaluate the after-sales support offered by the manufacturer. This includes warranty policies, technical support, and availability of spare parts. A manufacturer that provides robust after-sales service can help you address issues quickly and efficiently, ensuring minimal disruption to your operations.
By following this checklist, B2B buyers can navigate the complexities of sourcing check valve manufacturers, making informed decisions that align with their specific needs and business objectives.
Comprehensive Cost and Pricing Analysis for check valve manufacturer Sourcing
What Are the Key Cost Components in Check Valve Manufacturing?
When sourcing check valves, understanding the cost structure is essential for making informed purchasing decisions. The primary components influencing the cost include:
-
Materials: The choice of materials significantly impacts the pricing of check valves. Common materials include stainless steel, brass, and PVC. Higher quality materials generally lead to increased durability and performance but also raise costs.
-
Labor: Labor costs can vary based on the region and the complexity of the manufacturing process. Skilled labor in regions like Europe may be more expensive compared to emerging markets in Africa or South America.
-
Manufacturing Overhead: This includes costs related to utilities, equipment maintenance, and facility expenses. Efficient production processes can help minimize these overheads, affecting the final price.
-
Tooling: The cost of tooling is often a significant upfront investment, especially for custom check valve designs. Buyers should factor in these costs when evaluating overall pricing.
-
Quality Control (QC): Ensuring product quality through rigorous QC processes adds to the cost but is crucial for compliance with international standards. Buyers must balance the cost of QC with the risk of purchasing substandard products.
-
Logistics: Shipping and handling can substantially influence the total cost, particularly for international buyers. Understanding Incoterms can help buyers manage these logistics costs effectively.
-
Margin: Manufacturers typically include a profit margin in their pricing. This margin can vary widely depending on the supplier’s market positioning and the competitive landscape.
How Do Price Influencers Impact Check Valve Sourcing?
Several factors can influence the pricing of check valves, which buyers should consider when negotiating and sourcing:
-
Volume and Minimum Order Quantity (MOQ): Larger orders often lead to discounts due to economies of scale. Buyers should aim to consolidate orders to meet MOQ requirements for better pricing.
-
Specifications and Customization: Custom designs and specific technical requirements can increase costs. Buyers should clearly define specifications to avoid unexpected surcharges.
-
Material Quality and Certifications: Higher quality materials and certifications (such as ISO, API) often demand a premium. Buyers should assess whether the added quality aligns with their application needs.
-
Supplier Factors: The reputation and reliability of the supplier can influence pricing. Established suppliers may charge more due to their track record but could offer better assurance of quality and delivery.
-
Incoterms: Understanding the agreed terms of delivery can impact the total cost. Different Incoterms (like FOB, CIF) allocate responsibilities for shipping and risk, affecting the final price.
What Are the Best Negotiation Tips for International B2B Buyers?
International B2B buyers, particularly from regions like Africa, South America, the Middle East, and Europe, should consider the following strategies to optimize their sourcing process:
-
Negotiate Pricing Based on Total Cost of Ownership (TCO): Instead of focusing solely on the upfront price, consider the long-term costs associated with maintenance, durability, and efficiency of the check valves. A slightly higher initial cost may lead to savings over time.
-
Build Relationships with Suppliers: Establishing a strong relationship with suppliers can lead to better pricing and service. Long-term partnerships may provide additional negotiating power.
-
Conduct Market Research: Understanding market trends and competitor pricing can empower buyers during negotiations. Being informed allows buyers to challenge unreasonable quotes effectively.
-
Leverage Regional Differences: Buyers from Europe may find more competitive pricing when sourcing from manufacturers in Africa or South America. Understanding these dynamics can lead to significant savings.
What Should Buyers Keep in Mind Regarding Pricing Nuances?
Buyers must be cautious about indicative pricing provided by manufacturers. Prices can fluctuate due to market conditions, exchange rates, and material availability. Always request detailed quotes that outline all cost components to avoid surprises later. Additionally, keep in mind that international transactions may involve tariffs and duties, which should be factored into the overall budget.
By understanding these elements, international B2B buyers can enhance their sourcing strategy for check valves, ensuring they secure quality products at competitive prices.
Alternatives Analysis: Comparing check valve manufacturer With Other Solutions
When evaluating the best solutions for fluid control systems, international B2B buyers, particularly from regions such as Africa, South America, the Middle East, and Europe, should consider various alternatives to traditional check valves. Each option has its unique set of advantages and disadvantages that can impact operational efficiency, costs, and maintenance requirements.
Comparison Table of Check Valve Manufacturer with Alternative Solutions
Comparison Aspect | Check Valve Manufacturer | Alternative 1: Ball Valve | Alternative 2: Butterfly Valve |
---|---|---|---|
Performance | High reliability, prevents backflow effectively | Excellent flow control, can handle high pressures | Suitable for large flow rates, quick operation |
Cost | Moderate to high initial cost, durability adds long-term value | Generally lower initial cost | Lower initial cost, economical for large installations |
Ease of Implementation | Requires specific installation techniques | Easy installation, flexible configurations | Simple installation, lightweight |
Maintenance | Low maintenance, but requires periodic checks | Moderate maintenance, can wear over time | Low maintenance, but seals may need replacement |
Best Use Case | Ideal for critical applications where backflow must be prevented | Best for on/off applications and flow regulation | Suitable for large pipelines and quick shut-off applications |
What are the Advantages and Disadvantages of Using Ball Valves as an Alternative?
Ball valves are widely recognized for their ability to provide excellent flow control with minimal pressure drop. They are particularly advantageous in applications requiring quick shut-off capabilities. Their design allows for a tight seal, making them suitable for high-pressure systems. However, ball valves may not be the best choice for applications requiring precise flow regulation, and their moving parts can wear over time, necessitating more frequent maintenance compared to check valves.
How Do Butterfly Valves Compare to Check Valves?
Butterfly valves stand out for their lightweight design and low cost, making them an economical choice for large installations. They are capable of handling substantial flow rates and can be operated quickly, which is beneficial for processes requiring rapid shut-off. Nonetheless, butterfly valves may not provide the same level of backflow prevention as check valves, and their sealing mechanisms can be less durable, which may lead to maintenance concerns over time.
Conclusion: How Can B2B Buyers Choose the Right Solution for Their Needs?
When selecting between a check valve manufacturer and alternative solutions like ball or butterfly valves, B2B buyers must consider several factors, including the specific application requirements, budget constraints, and maintenance capabilities. For critical applications where backflow must be avoided, check valves are often the preferred choice due to their reliability. Conversely, for projects with budget limitations or where rapid shut-off is essential, ball or butterfly valves may offer a more cost-effective solution. Understanding the operational context and long-term maintenance implications will empower buyers to make informed decisions that align with their business objectives.
Essential Technical Properties and Trade Terminology for check valve manufacturer
What Are the Essential Technical Properties of Check Valves?
When sourcing check valves, understanding their technical specifications is crucial for ensuring operational efficiency and compliance with industry standards. Here are several key properties to consider:
What Material Grades Should You Look for in Check Valves?
Material Grade: The materials used in check valve manufacturing significantly affect durability and corrosion resistance. Common materials include stainless steel, brass, and PVC. Stainless steel, for example, is ideal for high-pressure applications and environments with corrosive substances, while PVC is suitable for lower pressure and non-corrosive environments. Selecting the right material can prevent premature failure and reduce maintenance costs.
How Does Tolerance Impact Check Valve Performance?
Tolerance: This refers to the permissible limit of variation in a physical dimension. For check valves, tight tolerances are essential for ensuring a proper fit and function. High tolerance levels can minimize leakage and improve the valve’s sealing capabilities, which is vital in preventing backflow in piping systems. A failure to maintain proper tolerances can lead to inefficiencies and increased operational costs.
Why Is Pressure Rating Important for Check Valves?
Pressure Rating: This specification indicates the maximum pressure the valve can withstand without failure. It’s crucial for selecting a check valve that meets the demands of your specific application, whether in plumbing, industrial, or oil and gas sectors. Using a valve with a pressure rating below your system’s requirements can lead to catastrophic failures, resulting in costly downtime and repairs.
What Role Does Size and Connection Type Play in Valve Selection?
Size and Connection Type: Check valves come in various sizes, and selecting the correct size ensures optimal flow rates and pressure drops. Additionally, connection types (such as threaded, flanged, or welded) must match your existing piping system to ensure compatibility. Proper sizing and connection will not only enhance the valve’s performance but also simplify installation.
How Do Certifications and Compliance Standards Affect Your Choice?
Certifications and Compliance Standards: Various industries have specific standards (like ANSI, API, or ISO) that check valves must meet. Understanding these certifications is critical for B2B buyers, as they often dictate the valve’s quality and reliability. Purchasing compliant products can mitigate risks associated with regulatory penalties and enhance the overall safety of your operations.
What Are Common Trade Terms Used in the Check Valve Industry?
Understanding industry jargon is essential for effective communication and negotiation with suppliers. Here are several common terms:
What Does OEM Mean in the Check Valve Market?
OEM (Original Equipment Manufacturer): This term refers to a company that produces parts and equipment that may be marketed by another manufacturer. In the check valve industry, OEMs often provide customized solutions tailored to specific applications. Buyers should consider OEM relationships when seeking specialized products, as these manufacturers can offer superior quality and support.
Why Is MOQ Important When Sourcing Check Valves?
MOQ (Minimum Order Quantity): This refers to the smallest quantity of a product that a supplier is willing to sell. Understanding MOQ is vital for B2B buyers to manage inventory costs effectively. When negotiating with suppliers, knowing the MOQ can also help in assessing the feasibility of large-scale projects.
What Is an RFQ and How Do You Use It?
RFQ (Request for Quotation): This is a document used by buyers to invite suppliers to bid on providing goods or services. An RFQ typically includes detailed specifications and requirements for the check valves needed. Crafting a clear and comprehensive RFQ can lead to more accurate quotes and better supplier relationships.
How Do Incoterms Affect International Trade of Check Valves?
Incoterms (International Commercial Terms): These are standardized terms used in international trade to clarify the responsibilities of buyers and sellers. Understanding Incoterms is crucial for international B2B transactions, as they define who pays for shipping, insurance, and tariffs. Familiarity with these terms can help avoid disputes and ensure smooth logistics.
By grasping these technical properties and industry terms, international B2B buyers can make informed decisions when sourcing check valves, ultimately leading to enhanced operational performance and cost efficiency.
Navigating Market Dynamics and Sourcing Trends in the check valve manufacturer Sector
What Are the Current Market Dynamics and Key Trends in the Check Valve Manufacturing Sector?
The check valve manufacturing sector is experiencing significant growth driven by various global factors. Increased demand for automation and efficiency in industrial processes is pushing manufacturers to innovate and enhance product reliability. Emerging markets in Africa and South America are particularly notable, as these regions invest in infrastructure and industrial development, creating a robust demand for high-quality check valves. In Europe and the Middle East, stringent regulations concerning safety and environmental standards are prompting companies to adopt advanced technologies, including IoT and AI, in their sourcing and manufacturing processes.
International B2B buyers should also be aware of the rising trend towards digital procurement solutions. Platforms that facilitate direct connections between manufacturers and buyers are becoming more popular, allowing for greater transparency and efficiency in sourcing. Additionally, manufacturers are increasingly focusing on customization to meet specific industry requirements, thus providing buyers with tailored solutions that enhance operational efficiency.
How Is Sustainability Influencing B2B Sourcing Trends in the Check Valve Sector?
Sustainability is becoming a critical factor in the sourcing strategies of international B2B buyers, particularly in the check valve manufacturing sector. Companies are under growing pressure to minimize their environmental impact, which is leading to a shift towards sustainable practices. This includes sourcing materials that are not only durable but also environmentally friendly. Buyers should prioritize manufacturers that utilize ‘green’ certifications and eco-friendly materials, as these are increasingly becoming a benchmark for quality and reliability in the industry.
Furthermore, ethical sourcing is gaining traction, with buyers seeking out suppliers who adhere to fair labor practices and responsible sourcing standards. This trend is not only beneficial for the planet but also enhances brand reputation, which is crucial for businesses operating in competitive markets. B2B buyers should ensure that their supply chains are transparent and that their partners are committed to sustainability initiatives, as this can significantly influence purchasing decisions.
What Is the Evolution of the Check Valve Manufacturing Sector?
The check valve manufacturing sector has evolved significantly over the past few decades. Initially focused on basic functionality, the industry has transformed in response to technological advancements and changing market demands. Early check valves were primarily mechanical devices designed for basic flow control. However, the introduction of advanced materials and manufacturing techniques has led to the development of highly specialized valves capable of withstanding extreme conditions and providing enhanced performance.
In recent years, the integration of digital technologies has further revolutionized the sector. Smart check valves equipped with sensors and IoT capabilities are now available, offering real-time monitoring and data analysis. This evolution not only improves operational efficiency but also enables predictive maintenance, reducing downtime and costs for businesses. For international B2B buyers, understanding this evolution is crucial for making informed sourcing decisions that align with both current market trends and future innovations.
Frequently Asked Questions (FAQs) for B2B Buyers of check valve manufacturer
-
How do I ensure the quality of check valves when sourcing from manufacturers?
To ensure the quality of check valves, first establish a clear set of specifications based on industry standards. Request certifications such as ISO 9001 or API 6D from potential manufacturers. Conduct on-site inspections or third-party quality audits to verify manufacturing processes and materials used. Additionally, ask for product samples and conduct performance tests to evaluate durability and functionality before placing bulk orders. -
What are the critical factors to consider when selecting a check valve manufacturer?
When selecting a check valve manufacturer, consider their reputation, experience, and specialization in your industry. Evaluate their production capabilities, technology, and compliance with international standards. It’s also essential to assess their customer service and support during the procurement process. Lastly, inquire about their ability to provide customization options that meet your specific project needs. -
What is the typical minimum order quantity (MOQ) for check valves?
The minimum order quantity for check valves can vary significantly based on the manufacturer and valve specifications. Typically, MOQs can range from 50 to 500 units for standard models. However, for specialized or custom valves, MOQs may be higher. Always discuss your requirements with the manufacturer to negotiate MOQs that align with your project needs and budget. -
How can I customize check valves to meet specific project requirements?
Customizing check valves involves working closely with the manufacturer to specify your design needs, including size, material, pressure ratings, and end connections. Provide detailed drawings or specifications, and inquire about the manufacturer’s capabilities for custom tooling or modifications. Discuss lead times and costs associated with customization, ensuring that they align with your project timeline and budget.
-
What payment terms should I expect when sourcing check valves internationally?
Payment terms for international purchases of check valves can vary. Common practices include a 30% deposit upon order confirmation, with the remaining 70% due before shipment. Some manufacturers may offer letters of credit or payment through platforms like PayPal for smaller orders. Always clarify payment terms upfront and ensure that they are documented in your purchase agreement to avoid misunderstandings. -
How do I navigate logistics and shipping when sourcing check valves from overseas?
To navigate logistics, work with your manufacturer to determine the best shipping methods based on cost, urgency, and destination. Consider using freight forwarders who can handle customs clearance and provide insights into local regulations. Always factor in lead times for production and shipping to ensure timely delivery. Additionally, communicate with your supplier about packaging and handling procedures to prevent damage during transit. -
What quality assurance practices should be in place when sourcing check valves?
Quality assurance practices should include regular inspections during the manufacturing process, along with final product testing before shipment. Request detailed inspection reports and certifications for materials used. It’s advisable to implement a quality control plan that includes incoming inspection upon receipt of goods. Establishing a clear return policy for defective products can also safeguard your investment. -
How can I verify the credibility of a check valve manufacturer before making a purchase?
To verify the credibility of a check valve manufacturer, conduct thorough research by checking online reviews and testimonials from previous clients. Request references and case studies relevant to your industry. It’s beneficial to visit their facility if possible, or arrange for a virtual tour. Additionally, assess their certifications, compliance with safety standards, and participation in industry organizations to ensure their reliability and professionalism.
Important Disclaimer & Terms of Use
⚠️ Important Disclaimer
The information provided in this guide, including content regarding manufacturers, technical specifications, and market analysis, is for informational and educational purposes only. It does not constitute professional procurement advice, financial advice, or legal advice.
While we have made every effort to ensure the accuracy and timeliness of the information, we are not responsible for any errors, omissions, or outdated information. Market conditions, company details, and technical standards are subject to change.
B2B buyers must conduct their own independent and thorough due diligence before making any purchasing decisions. This includes contacting suppliers directly, verifying certifications, requesting samples, and seeking professional consultation. The risk of relying on any information in this guide is borne solely by the reader.
Strategic Sourcing Conclusion and Outlook for check valve manufacturer
What Are the Key Takeaways for B2B Buyers in Strategic Sourcing of Check Valves?
In the evolving landscape of industrial manufacturing, strategic sourcing of check valves has emerged as a critical component for international B2B buyers. By understanding supplier capabilities, product specifications, and the importance of compliance with local and international standards, companies can significantly enhance their operational efficiency and reduce costs. Engaging with manufacturers who prioritize innovation and sustainability will not only ensure high-quality products but also foster long-term partnerships that can adapt to market changes.
How Can International Buyers Benefit from Strategic Sourcing?
For buyers in Africa, South America, the Middle East, and Europe, the strategic sourcing process is an opportunity to leverage global supply chains effectively. It allows for the identification of competitive pricing, reliability in delivery, and superior technical support. By establishing strong relationships with reputable manufacturers, businesses can mitigate risks associated with supply disruptions and ensure continuity in their operations.
What Is the Future Outlook for Check Valve Sourcing?
Looking ahead, it is essential for B2B buyers to remain proactive in their sourcing strategies. The increasing demand for advanced materials and technologies in check valves will shape the future of procurement in this sector. Buyers are encouraged to stay informed about industry trends and innovations, and to engage in continuous dialogue with suppliers. This forward-thinking approach will not only enhance procurement outcomes but also position companies for success in an increasingly competitive market.
In conclusion, embracing strategic sourcing in the check valve manufacturing sector is not just a necessity; it is a pathway to sustained growth and operational excellence. International B2B buyers should take actionable steps now to explore new partnerships and invest in their sourcing strategies to thrive in the future.