The Ultimate Guide to Dining Table Manufacturer (2025)
Introduction: Navigating the Global Market for dining table manufacturer
In the competitive landscape of global trade, sourcing high-quality dining tables can be a daunting challenge for B2B buyers, particularly those operating in diverse markets such as Africa, South America, the Middle East, and Europe. Buyers often face uncertainties regarding supplier reliability, product quality, and compliance with international standards. This guide aims to demystify the process of selecting dining table manufacturers by providing a comprehensive overview of the market landscape, including various types of dining tables, their applications in both commercial and residential settings, and critical supplier vetting strategies.
Understanding the nuances of cost structures and the factors influencing pricing will empower buyers to make informed decisions that align with their business objectives. From selecting the right materials to understanding market trends, this guide addresses key considerations for international buyers looking to enhance their procurement strategies.
By leveraging actionable insights and expert recommendations, B2B buyers will be equipped to navigate the complexities of sourcing dining tables effectively. This guide serves as a valuable resource for those seeking to optimize their purchasing processes, ensuring they partner with reputable manufacturers that meet their specific needs, whether they are based in bustling cities like Nairobi or established markets like Berlin.
Understanding dining table manufacturer Types and Variations
Type Name | Key Distinguishing Features | Primary B2B Applications | Brief Pros & Cons for Buyers |
---|---|---|---|
Solid Wood Dining Tables | Made from hardwoods like oak, maple, or walnut; durable and long-lasting | Restaurants, hotels, and upscale dining | Pros: High durability, classic aesthetic. Cons: Higher price point, heavier for transport. |
Glass Dining Tables | Features a glass tabletop, often with metal or wood bases; modern design | Contemporary restaurants, event venues | Pros: Sleek appearance, easy to clean. Cons: Can be fragile, may require more maintenance. |
Extendable Dining Tables | Tables that can be adjusted in size; typically include additional leafs | Banquet halls, catering services | Pros: Versatile for varying guest numbers. Cons: May have mechanical issues over time. |
Reclaimed Wood Dining Tables | Crafted from recycled wood, offering a rustic look; eco-friendly | Eco-conscious businesses, rustic-themed venues | Pros: Sustainable, unique designs. Cons: Variability in quality, may require sealing. |
Metal Dining Tables | Constructed from steel or aluminum; industrial style; often lightweight | Cafes, outdoor dining, and casual eateries | Pros: Lightweight, weather-resistant. Cons: Can be less comfortable without cushions. |
What Are the Characteristics of Solid Wood Dining Tables?
Solid wood dining tables are renowned for their robustness and timeless appeal. Made from high-quality hardwoods like oak, walnut, or maple, these tables are designed to withstand heavy use, making them ideal for busy restaurants and hotels. When considering a purchase, B2B buyers should evaluate the wood type for durability and aesthetic appeal, as well as the table’s finish to ensure it meets the desired style and maintenance requirements.
How Do Glass Dining Tables Stand Out?
Glass dining tables offer a modern, sophisticated look that can elevate the ambiance of any dining space. Typically featuring a tempered glass top supported by metal or wooden bases, these tables are popular in contemporary restaurants and event venues. Buyers should consider the thickness of the glass and the base’s sturdiness, as well as the ease of cleaning, since glass surfaces can show fingerprints and smudges more readily than other materials.
Why Choose Extendable Dining Tables for B2B Settings?
Extendable dining tables provide exceptional flexibility, allowing businesses to adapt their dining arrangements based on guest volume. These tables usually come with additional leafs or sections that can be added or removed as needed, making them perfect for banquet halls and catering services. Buyers should assess the mechanism for extending the table and ensure it is user-friendly, as well as check the table’s stability when extended to avoid accidents during busy service periods.
What Makes Reclaimed Wood Dining Tables Unique?
Reclaimed wood dining tables are crafted from salvaged wood, offering a rustic charm and sustainability that appeals to eco-conscious businesses. Each table is unique, showcasing the character of the wood, which can be a strong selling point for rustic-themed venues. Buyers should consider the sourcing and treatment of the wood to ensure it meets health and safety standards, as well as its maintenance needs, which may involve regular sealing to protect against wear.
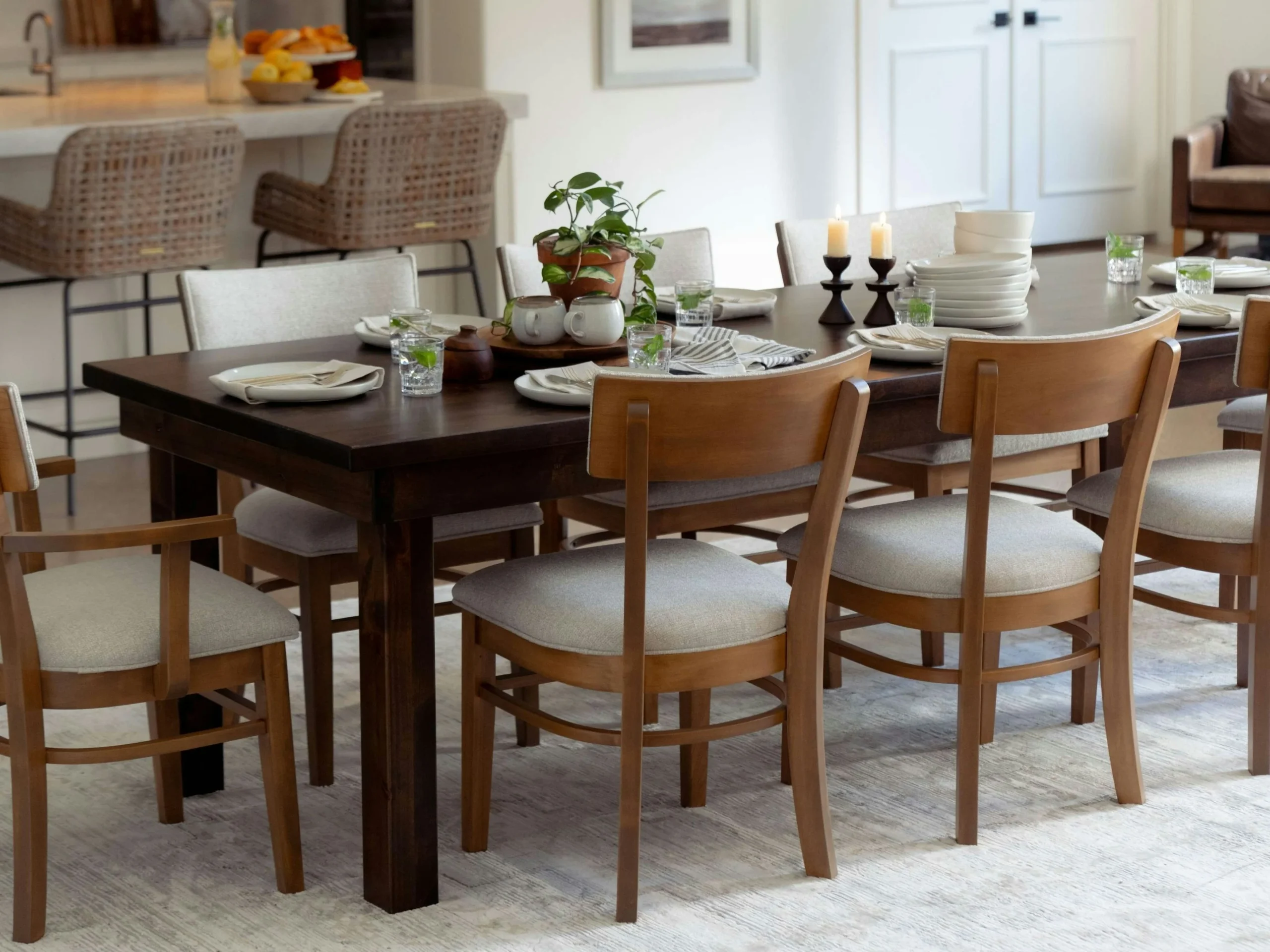
A stock image related to dining table manufacturer.
Why Opt for Metal Dining Tables in Casual Settings?
Metal dining tables are characterized by their industrial aesthetic and lightweight nature, making them suitable for cafes, outdoor dining, and casual eateries. Often made from steel or aluminum, these tables are resistant to weather elements, which is a significant advantage for outdoor settings. Buyers should evaluate the comfort level of metal tables, as they may require additional cushions for prolonged use, and assess the finish to ensure it aligns with their branding and design preferences.
Related Video: A Guide To Proper Dining Etiquette And Table Manners
Key Industrial Applications of dining table manufacturer
Industry/Sector | Specific Application of dining table manufacturer | Value/Benefit for the Business | Key Sourcing Considerations for this Application |
---|---|---|---|
Hospitality | Dining tables for hotels and restaurants | Enhances customer experience and increases seating capacity | Durability, design, and customization options to fit brand identity |
Education | Cafeteria dining tables for schools and universities | Supports large group gatherings and promotes social interaction | Safety standards, ease of maintenance, and scalability |
Corporate Offices | Breakroom and conference dining tables | Facilitates employee collaboration and enhances workplace culture | Ergonomics, modular designs, and space optimization |
Event Planning | Rental dining tables for events and functions | Provides flexibility and choice for diverse event settings | Portability, ease of setup, and variety in styles |
Residential Development | Dining tables for residential complexes and apartments | Increases property value and appeals to potential buyers/renters | Aesthetic appeal, material quality, and size options |
How Are Dining Tables Used in the Hospitality Industry?
In the hospitality sector, dining tables are integral to hotels and restaurants, creating an inviting atmosphere for guests. They solve the problem of maximizing space while accommodating varying group sizes. International buyers from regions like Africa and Europe should consider durability, as these tables must withstand heavy use. Customization options are also critical, allowing businesses to align the table’s design with their brand identity, enhancing the overall dining experience.
What Role Do Dining Tables Play in Educational Settings?
In educational institutions, dining tables are essential for cafeterias, providing students a place to gather and socialize. These tables promote community building, addressing the need for social interaction among students. For buyers in South America and the Middle East, it is vital to adhere to safety standards and select materials that are easy to clean and maintain, ensuring longevity and hygiene in high-traffic areas.
How Can Dining Tables Enhance Corporate Office Environments?
Corporate offices utilize dining tables in breakrooms and for meetings, fostering collaboration among employees. These tables solve the issue of creating a comfortable space for informal discussions and meals, ultimately enhancing workplace culture. B2B buyers in Europe should prioritize ergonomic designs and modular options, enabling flexibility in workspace configurations while ensuring comfort for employees.
What Are the Benefits of Dining Tables in Event Planning?
Dining tables are crucial in the event planning industry, where they are often rented for various functions. They provide the flexibility needed to accommodate different event styles, from formal banquets to casual gatherings. Buyers, particularly in Africa, must consider portability and ease of setup when sourcing tables, as these factors significantly impact the efficiency of event execution. Variety in styles and sizes also allows for customization to meet specific event themes.
Why Are Dining Tables Important in Residential Developments?
In residential developments, dining tables are a key feature that can enhance the appeal of properties. They not only increase the functional space within apartments but also contribute to the overall aesthetic value, attracting potential buyers or renters. International buyers should focus on the material quality and aesthetic appeal of dining tables, as these elements play a significant role in the purchasing decision of prospective tenants in competitive markets.
Related Video: Table Top Epoxy on custom table
3 Common User Pain Points for ‘dining table manufacturer’ & Their Solutions
Scenario 1: Quality Concerns with Dining Tables from Manufacturers
The Problem: International B2B buyers often face significant challenges regarding the quality of dining tables sourced from manufacturers. In regions like Africa and South America, where local suppliers may not meet international quality standards, buyers risk investing in subpar products that lead to dissatisfaction among end customers. Issues such as poor craftsmanship, inadequate materials, and lack of durability can severely impact a buyer’s reputation and profitability.
The Solution: To mitigate quality concerns, B2B buyers should establish a robust sourcing strategy. This begins with conducting thorough due diligence on potential dining table manufacturers. Look for suppliers with established certifications, such as ISO 9001, which demonstrates a commitment to quality management. Additionally, request samples before placing large orders to assess the craftsmanship and materials firsthand. Engaging in factory visits, if possible, or utilizing third-party inspection services can further ensure compliance with quality standards. Building a long-term relationship with manufacturers who have a proven track record can also lead to better quality assurance and product consistency.
Scenario 2: Long Lead Times and Delivery Issues
The Problem: Long lead times and delivery issues are prevalent pain points for B2B buyers in the dining table industry, particularly when dealing with overseas manufacturers. Buyers often find themselves in tight timelines for project completion, and delays can disrupt their operations, lead to lost sales, and damage client relationships. In regions such as the Middle East and Europe, where timely delivery is critical, these challenges can be particularly detrimental.
The Solution: To address lead time concerns, buyers should prioritize manufacturers who can demonstrate reliable logistics capabilities and a history of on-time deliveries. Establish clear communication regarding timelines at the outset and include penalties for delays in contracts to safeguard against potential disruptions. Additionally, consider diversifying your supplier base to include local manufacturers who can provide quicker turnaround times. Utilizing technology, such as supply chain management software, can help track orders and forecast potential delays, allowing buyers to make informed decisions proactively.
Scenario 3: Customization Challenges in Dining Table Orders
The Problem: Customization is a key demand among B2B buyers looking for unique dining table designs that align with their brand identity. However, many manufacturers struggle to accommodate specific design requests or provide adequate support during the customization process. This can lead to frustration and misalignment with customer expectations, particularly in competitive markets like Europe and South America.
The Solution: To overcome customization challenges, buyers should clearly articulate their design specifications and expectations from the beginning. Create detailed design briefs that include dimensions, materials, finishes, and any other specific requirements. Collaborate closely with manufacturers during the design phase, utilizing 3D modeling software to visualize the final product before production. Establishing a feedback loop with manufacturers can facilitate adjustments and ensure the final product aligns with the buyer’s vision. Additionally, consider partnering with manufacturers that specialize in custom furniture to leverage their expertise and streamline the process.
Strategic Material Selection Guide for dining table manufacturer
What Are the Key Properties of Common Materials Used in Dining Table Manufacturing?
When selecting materials for dining tables, manufacturers must consider several factors, including durability, cost, and the specific needs of international markets. Here we analyze four common materials: wood, metal, glass, and composite materials.
How Does Wood Perform as a Material for Dining Tables?
Key Properties: Wood is a natural material known for its aesthetic appeal and strength. It has good thermal insulation properties and can withstand moderate pressure. However, it is susceptible to moisture, which can lead to warping or swelling.
Pros & Cons: The advantages of wood include its durability and timeless appeal, making it suitable for both traditional and modern designs. However, wood can be expensive, especially high-quality hardwoods like oak or walnut. Additionally, it requires regular maintenance to prevent damage from moisture and pests.
Impact on Application: Wood is compatible with a variety of finishes and can be easily customized. However, in humid climates, such as parts of Africa or South America, specific treatments may be necessary to enhance moisture resistance.
Considerations for International Buyers: Buyers from regions like Europe may prefer sustainably sourced wood, adhering to standards such as the Forest Stewardship Council (FSC) certification. Compliance with local regulations regarding wood treatment and pest control is also crucial.
What Are the Benefits of Metal in Dining Table Manufacturing?
Key Properties: Metals like steel and aluminum offer high strength-to-weight ratios and excellent durability. They are resistant to corrosion and can withstand high temperatures and pressures.
Pros & Cons: The primary advantage of metal is its longevity and low maintenance requirements. However, metal tables can be heavy and may require complex manufacturing processes, which can increase costs. Additionally, metal can be cold to the touch, which may not be appealing in dining settings.
Impact on Application: Metal tables are ideal for outdoor use and can withstand various weather conditions, making them suitable for regions with extreme climates. They can also be finished in various ways to enhance aesthetics.
Considerations for International Buyers: Buyers should be aware of compliance with standards such as ASTM (American Society for Testing and Materials) for metals. In regions like the Middle East, where high temperatures are common, choosing metals with appropriate coatings for UV resistance is essential.
How Does Glass Fit into the Dining Table Material Selection?
Key Properties: Glass is a versatile material that is aesthetically pleasing and can be tempered for increased strength. It is non-porous, making it resistant to stains and easy to clean.
Pros & Cons: The main advantage of glass tables is their modern look and the ability to visually expand a space. However, glass can be fragile and may chip or shatter under impact. Additionally, it may require more frequent cleaning to maintain its appearance.
Impact on Application: Glass is often used in combination with other materials, such as metal or wood, to create unique designs. It is suitable for indoor use but can be less ideal for outdoor settings unless specifically treated.
Considerations for International Buyers: Buyers should ensure that the glass meets safety standards, such as those set by the European Union (EU) regarding tempered glass. In regions like South America, where glass may be more prone to breakage, additional safety features may be required.
What Role Do Composite Materials Play in Dining Table Manufacturing?
Key Properties: Composite materials, such as MDF (Medium Density Fiberboard) and plywood, combine the benefits of different materials. They are generally lightweight, cost-effective, and can be designed to mimic the appearance of solid wood.
Pros & Cons: The advantages include lower costs and ease of manufacturing, allowing for intricate designs. However, composites may not be as durable as solid wood and can be sensitive to moisture, leading to potential swelling or delamination.
Impact on Application: Composite materials are suitable for a variety of applications, including budget-friendly dining tables. They can be finished with veneers to enhance appearance.
Considerations for International Buyers: Buyers should consider the environmental impact of composite materials and seek products that comply with standards such as CARB (California Air Resources Board) for formaldehyde emissions. This is particularly important in regions like Europe, where environmental regulations are stringent.
Summary Table of Material Selection for Dining Table Manufacturers
Material | Typical Use Case for dining table manufacturer | Key Advantage | Key Disadvantage/Limitation | Relative Cost (Low/Med/High) |
---|---|---|---|---|
Wood | Traditional dining tables with aesthetic appeal | Durable and customizable | Expensive and moisture-sensitive | High |
Metal | Modern and industrial-style tables | Long-lasting and low maintenance | Heavy and may require complex mfg | Medium |
Glass | Contemporary designs and space-enhancing tables | Aesthetic and easy to clean | Fragile and requires frequent cleaning | Medium |
Composite | Budget-friendly and versatile designs | Cost-effective and lightweight | Less durable and moisture-sensitive | Low |
This comprehensive analysis of materials provides international B2B buyers with actionable insights to make informed decisions when sourcing dining tables, ensuring they meet both performance requirements and market preferences.
In-depth Look: Manufacturing Processes and Quality Assurance for dining table manufacturer
What Are the Main Stages of the Dining Table Manufacturing Process?
The manufacturing process for dining tables involves several critical stages that ensure the final product meets both aesthetic and functional standards. Understanding these stages is vital for international B2B buyers looking to make informed purchasing decisions.
1. Material Preparation: How Are Raw Materials Selected and Processed?
The first step in the manufacturing process is the selection and preparation of raw materials. Common materials for dining tables include hardwoods (like oak, walnut, and maple), softwoods (like pine), and engineered wood products (like MDF or particleboard).
- Material Sourcing: Buyers should ensure suppliers source wood from sustainably managed forests, as this not only complies with environmental regulations but also appeals to eco-conscious consumers.
- Drying Process: Once sourced, wood undergoes a drying process to reduce moisture content, preventing warping and splitting during production. This can be done through air drying or kiln drying.
2. Forming: What Techniques Are Used to Shape Dining Tables?
Once the materials are prepared, the next stage is forming, which involves cutting and shaping the wood into the desired design.
- Cutting: Advanced saws, such as CNC machines, are often used for precision cutting, allowing for intricate designs and reducing waste.
- Shaping and Joining: Techniques like dovetail joints, mortise and tenon joints, and biscuit joints are employed to ensure durability. Buyers should inquire about the specific joinery techniques used, as these impact the table’s longevity and stability.
3. Assembly: How Are Components Brought Together?
After forming, the assembly stage involves putting together the various parts of the dining table.
- Dry Fitting: Prior to glue application, components are dry-fitted to ensure proper alignment and fit.
- Adhesives and Fasteners: High-quality adhesives are used, often complemented by mechanical fasteners for added strength. The choice of adhesive can affect the final product’s durability, so buyers should ask about the types used.
4. Finishing: What Are the Final Touches Applied to Dining Tables?
The finishing stage enhances the appearance of the dining table while providing protection against wear and tear.
- Sanding: The surface is meticulously sanded to achieve a smooth finish.
- Staining and Sealing: Various stains can be applied to enhance the wood’s natural beauty, followed by a sealing process to protect against moisture and scratches. Buyers should consider the environmental impact of finishes and ask about VOC (volatile organic compounds) levels.
What Quality Assurance Standards Should B2B Buyers Look For?
Quality assurance is a critical component of the dining table manufacturing process, ensuring that products meet international standards and buyer expectations.
International Standards: Which Certifications Are Relevant?
For B2B buyers, understanding the relevant certifications can provide assurance of quality and safety.
- ISO 9001: This international standard specifies requirements for a quality management system (QMS) and is crucial for manufacturers to demonstrate consistent quality.
- CE Marking: In Europe, CE marking indicates compliance with health, safety, and environmental protection standards.
- FSC Certification: Buyers should look for suppliers with Forest Stewardship Council (FSC) certification, ensuring that wood is sourced sustainably.
What Are the Key Quality Control Checkpoints in Dining Table Manufacturing?
Quality control (QC) is essential to ensure that every dining table produced meets the required specifications and standards.
1. Incoming Quality Control (IQC): How Are Raw Materials Assessed?
IQC involves inspecting raw materials upon arrival to ensure they meet specified quality standards.
- Visual Inspection: Materials are checked for defects such as warping or discoloration.
- Moisture Content Testing: The moisture levels of the wood are tested to prevent future issues in production.
2. In-Process Quality Control (IPQC): How Is Quality Maintained During Production?
During the manufacturing process, IPQC ensures that quality is maintained at each stage.
- Regular Inspections: Operators conduct regular checks for dimensional accuracy and joinery integrity.
- Testing Adhesives: The effectiveness of adhesives is often tested to ensure strong bonds.
3. Final Quality Control (FQC): What Happens Before Shipping?
FQC is the last line of defense before the dining tables are shipped to buyers.
- Comprehensive Inspection: Each table undergoes a thorough inspection for finish quality, structural integrity, and overall aesthetics.
- Load Testing: Some manufacturers perform load testing to ensure the table can withstand typical usage.
How Can B2B Buyers Verify Supplier Quality Control Measures?
For international B2B buyers, verifying a supplier’s quality control measures is crucial for ensuring product reliability.
1. Audits: What Should Buyers Expect During a Supplier Audit?
Buyers can conduct audits to assess the supplier’s manufacturing processes and quality control systems.
- On-site Visits: Visiting the manufacturing facility allows buyers to observe production processes and QC measures firsthand.
- Documentation Review: Buyers should request to see quality control documentation, including inspection records and compliance certifications.
2. Reports: How Can Quality Reports Provide Assurance?
Suppliers should provide detailed reports on their quality control processes.
- Quality Control Plans: Requesting a copy of the supplier’s quality control plan can offer insights into their procedures and standards.
- Testing Results: Buyers should ask for documentation of testing results to verify compliance with standards.
3. Third-party Inspections: Why Are They Important?
Engaging third-party inspectors can provide an unbiased assessment of the supplier’s quality control.
- Independent Verification: Third-party inspections can validate the quality of materials and finished products.
- International Compliance: Inspectors can ensure that products meet both local and international standards, which is particularly important for buyers from diverse regions such as Africa, South America, the Middle East, and Europe.
Conclusion: What Should International B2B Buyers Prioritize?
For B2B buyers, particularly those from Africa, South America, the Middle East, and Europe, understanding the intricacies of the dining table manufacturing process and quality assurance practices is essential. By focusing on material selection, manufacturing techniques, and rigorous quality control standards, buyers can make informed decisions that lead to successful partnerships and high-quality products. Prioritizing certifications, conducting thorough audits, and considering third-party inspections can significantly enhance the buyer’s confidence in their supplier’s capabilities.
Practical Sourcing Guide: A Step-by-Step Checklist for ‘dining table manufacturer’
To ensure a successful procurement process for dining tables, international B2B buyers should follow a structured sourcing guide. This checklist is designed to help you navigate the complexities of selecting the right dining table manufacturer, particularly for businesses located in Africa, South America, the Middle East, and Europe.
Step 1: Define Your Technical Specifications
Before reaching out to suppliers, it’s essential to clearly outline your requirements. This includes dimensions, materials (such as wood types or metal finishes), and any design specifics. Having a detailed specification not only streamlines communication but also helps in assessing supplier capabilities effectively.
- Material Preferences: Specify if you require sustainable materials or specific finishes.
- Size Requirements: Include standard sizes or custom dimensions needed for your market.
Step 2: Conduct Market Research for Potential Suppliers
Identify potential manufacturers who specialize in dining tables. Utilize online platforms, trade shows, and industry directories to gather a list of candidates. This step is vital as it sets the foundation for your supplier shortlist.
- Geographic Focus: Consider suppliers in regions known for quality craftsmanship, such as Europe or South America.
- Reputation Checks: Look for reviews or testimonials from previous clients to gauge reliability.
Step 3: Evaluate Potential Suppliers
Once you have a shortlist, evaluate each supplier based on their production capabilities and past performance. Request detailed company profiles, product samples, and references from clients in similar markets.
- Production Capacity: Ensure they can meet your order volumes and timelines.
- Quality Control Practices: Inquire about their quality assurance processes to ensure product consistency.
Step 4: Verify Supplier Certifications and Compliance
Ensure that your chosen manufacturers comply with international standards and certifications relevant to furniture production. This step is crucial for ensuring product safety and quality.
- Certification Types: Look for ISO certifications, FSC (Forest Stewardship Council) for sustainable sourcing, or other relevant local standards.
- Compliance with Regulations: Ensure they adhere to import/export regulations in your country.
Step 5: Request Quotes and Compare Pricing
Contact selected suppliers to request quotes based on your specifications. This will not only help you understand the market price but also give you insight into each supplier’s pricing structure and flexibility.
- Cost Breakdown: Ask for detailed pricing, including shipping and handling charges.
- Negotiation Opportunities: Identify areas where you can negotiate better terms or bulk discounts.
Step 6: Conduct Factory Visits or Virtual Tours
If feasible, arrange factory visits to assess the manufacturing process firsthand. If not, request virtual tours to observe production practices and facilities. This step builds trust and provides deeper insight into the supplier’s operations.
- Production Environment: Evaluate the cleanliness and organization of the factory.
- Employee Practices: Observe workforce conditions and training programs, which can affect product quality.
Step 7: Finalize Agreements and Establish Communication Channels
Once you’ve selected a supplier, finalize your agreements detailing terms, delivery schedules, and payment methods. Establish clear communication channels to facilitate ongoing discussions and issue resolution.
- Contract Clarity: Ensure all terms are clearly outlined to avoid misunderstandings.
- Regular Updates: Set expectations for regular updates on production and shipping timelines.
Following this structured sourcing checklist will empower B2B buyers to make informed decisions when procuring dining tables, ultimately enhancing the efficiency and effectiveness of the sourcing process.
Comprehensive Cost and Pricing Analysis for dining table manufacturer Sourcing
What Are the Key Cost Components in Dining Table Manufacturing?
When sourcing dining tables, understanding the cost structure is crucial for international B2B buyers. The primary components influencing the cost include:
-
Materials: The type of wood, metal, or composite used significantly impacts pricing. High-quality hardwoods like oak or walnut are more expensive than softer woods or engineered materials.
-
Labor: Labor costs vary by region and can be influenced by local wage standards and skill levels. Countries with lower labor costs may offer cheaper products but potentially at the expense of craftsmanship.
-
Manufacturing Overhead: This encompasses utilities, rent, and administrative costs associated with running a factory. Efficient manufacturing processes can reduce these overheads, allowing for more competitive pricing.
-
Tooling: Custom tooling for specific designs can increase initial costs. However, if a manufacturer specializes in certain styles, the amortization of these costs over large production runs can lead to better pricing.
-
Quality Control (QC): Implementing stringent QC processes ensures product reliability but may increase costs. Certifications (e.g., ISO, FSC) can also add to expenses but may be necessary for certain markets.
-
Logistics: Shipping costs can vary widely based on distance, shipping method, and weight. Buyers should consider the total logistics cost, including customs duties and tariffs.
-
Margin: Manufacturers will typically add a profit margin to cover their costs and generate revenue. This margin can vary significantly based on market conditions and competition.
How Do Price Influencers Affect Dining Table Sourcing?
Several factors can influence the final price of dining tables:
-
Volume and Minimum Order Quantity (MOQ): Higher volumes often lead to discounts, as manufacturers can spread costs over more units. Understanding the MOQ is essential for budget planning.
-
Specifications and Customization: Customized designs and specifications will generally incur additional costs. Buyers should clearly define their needs to avoid unexpected charges.
-
Materials and Quality: The choice of materials directly impacts the price. Buyers should weigh the benefits of higher-quality materials against their budget constraints.
-
Supplier Factors: The reputation and reliability of the supplier can affect pricing. Established manufacturers may charge a premium for their track record of quality and service.
-
Incoterms: Understanding Incoterms (International Commercial Terms) is critical for clarifying responsibilities in shipping and delivery. Different terms can affect the total cost of ownership.
What Negotiation Strategies Can International B2B Buyers Use?
B2B buyers from Africa, South America, the Middle East, and Europe should consider the following strategies:
-
Leverage Volume Discounts: If possible, consolidate orders across multiple products to negotiate better pricing.
-
Clarify Total Cost of Ownership: Go beyond the initial price to consider shipping, duties, and potential tariffs. A lower upfront cost may not always equate to savings.
-
Build Long-Term Relationships: Establishing a rapport with suppliers can lead to better pricing and terms. Consistent orders may encourage suppliers to provide favorable rates.
-
Research and Benchmarking: Conduct market research to understand typical pricing for similar products. This knowledge can strengthen your negotiating position.
What Should Buyers Be Aware of Regarding Indicative Prices?
Buyers should approach indicative prices with caution, as they can fluctuate based on various factors, including market demand, raw material availability, and geopolitical events. Always request detailed quotes and consider multiple suppliers to ensure competitive pricing. Additionally, be prepared for price adjustments based on changing specifications or unforeseen costs in manufacturing or logistics.
By understanding these key components and strategies, international B2B buyers can make informed decisions when sourcing dining tables, ensuring they achieve the best value for their investments.
Alternatives Analysis: Comparing dining table manufacturer With Other Solutions
When considering dining table solutions, international B2B buyers have a variety of options beyond traditional dining table manufacturers. Understanding these alternatives can help businesses make informed purchasing decisions that align with their specific needs and contexts, particularly in diverse markets such as Africa, South America, the Middle East, and Europe.
Comparison Aspect | Dining Table Manufacturer | Modular Furniture Solutions | Digital Dining Solutions |
---|---|---|---|
Performance | High durability and aesthetic appeal | Versatile and customizable | Innovative but requires tech-savvy users |
Cost | Medium to high, depending on materials | Variable, often lower upfront costs | Potentially higher due to technology integration |
Ease of Implementation | Straightforward, with installation required | Easy to assemble, depending on design | Requires setup and user training |
Maintenance | Regular care needed to maintain appearance | Minimal, depending on materials | Regular software updates and tech support |
Best Use Case | Formal dining settings, restaurants | Flexible spaces, event venues | Modern dining experiences, tech-oriented establishments |
What are Modular Furniture Solutions and Their Advantages?
Modular furniture solutions provide flexibility and adaptability for various dining environments. These products often come in pre-designed units that can be rearranged or reconfigured to suit different occasions. The primary advantage of modular furniture is its cost-effectiveness, as it typically incurs lower upfront costs compared to bespoke dining tables. Additionally, they are often easier to assemble and disassemble, making them ideal for businesses that require frequent layout changes, such as event venues or co-working spaces. However, while they offer versatility, the aesthetic appeal may not match that of custom-manufactured tables, which can affect brand image in more formal dining settings.
How Do Digital Dining Solutions Transform Dining Experiences?
Digital dining solutions leverage technology to enhance the dining experience through features like ordering via tablets, integrating payment systems, and providing interactive menus. This modern approach is particularly beneficial for tech-savvy establishments looking to attract a younger clientele. However, the integration of such technology can result in higher initial investments and ongoing costs for software updates and technical support. Businesses must also consider the learning curve for staff and customers alike, which can impact the overall dining experience. While these solutions can create a more engaging atmosphere, they may not suit traditional dining establishments focused on a classic dining experience.
Conclusion: How to Choose the Right Dining Table Solution?
When deciding between a dining table manufacturer and alternative solutions, B2B buyers must consider their specific operational needs and customer demographics. Assessing factors such as cost, ease of implementation, and maintenance requirements will guide businesses toward the most suitable option. For instance, if flexibility and cost are paramount, modular furniture might be the best choice. Conversely, if creating a high-end, aesthetically pleasing environment is essential, investing in a traditional dining table manufacturer would be advisable. Ultimately, aligning the selected solution with the business’s long-term strategy will ensure a successful investment in dining infrastructure.
Essential Technical Properties and Trade Terminology for dining table manufacturer
What Are the Essential Technical Properties for Dining Table Manufacturing?
When sourcing dining tables, understanding the technical specifications is crucial for making informed purchasing decisions. Here are some critical properties that B2B buyers should consider:
1. Material Grade
The material used in dining table production significantly impacts durability, aesthetics, and price. Common materials include solid wood, engineered wood, metal, and glass. For instance, solid hardwood (like oak or maple) offers longevity and can withstand heavy use, making it ideal for commercial settings. Buyers should request information on the material grade to ensure it meets their quality standards.
2. Tolerance Levels
Tolerance refers to the allowable deviation in dimensions during manufacturing. For dining tables, this might include the thickness of the tabletop or the height of the legs. Tight tolerances (e.g., ±0.5 mm) ensure that all components fit together seamlessly, which is essential for aesthetic appeal and structural integrity. High tolerance levels are particularly important for modular tables that may need to be assembled on-site.
3. Finish and Coating
The finish applied to a dining table can enhance its durability and resistance to stains, scratches, and moisture. Common finishes include varnishes, lacquers, and oil-based coatings. B2B buyers should inquire about the type of finish used, as this can affect maintenance requirements and the longevity of the product, especially in high-traffic environments.
4. Weight Capacity
Understanding the weight capacity of a dining table is crucial, particularly for commercial use in restaurants or event spaces. Manufacturers should provide specifications detailing the maximum load the table can support without compromising stability. This ensures that the table can handle various dining scenarios, from casual meals to formal events.
5. Sustainability Certifications
With a growing emphasis on sustainability, many buyers are interested in the environmental impact of their purchases. Look for certifications like FSC (Forest Stewardship Council) or Greenguard, which indicate responsible sourcing and low chemical emissions. These certifications not only enhance brand reputation but also appeal to eco-conscious consumers.
What Trade Terms Should B2B Buyers Understand in Dining Table Manufacturing?
Familiarity with industry jargon can streamline communication and negotiations with suppliers. Here are some common terms that international buyers should know:
1. OEM (Original Equipment Manufacturer)
An OEM is a company that manufactures products based on the designs and specifications provided by another company. In the context of dining tables, this could mean a manufacturer that produces custom designs for a retailer. Understanding OEM relationships can help buyers identify potential suppliers who can offer bespoke solutions.
2. MOQ (Minimum Order Quantity)
MOQ refers to the smallest quantity of a product that a supplier is willing to sell. This is particularly important for B2B buyers, as MOQs can affect inventory levels and capital investment. Buyers should negotiate MOQs to align with their purchasing needs without overcommitting to inventory.
3. RFQ (Request for Quotation)
An RFQ is a document sent to suppliers requesting pricing and terms for specific products. For dining table manufacturers, an RFQ should include details such as material specifications, dimensions, and quantities. A well-prepared RFQ can lead to competitive pricing and favorable terms.
4. Incoterms (International Commercial Terms)
Incoterms define the responsibilities of buyers and sellers in international trade. They clarify who is responsible for shipping, insurance, and tariffs. Understanding these terms is essential for B2B buyers to avoid unexpected costs and ensure smooth transactions.
5. Lead Time
Lead time refers to the time taken from placing an order to receiving the product. For dining table manufacturers, lead times can vary based on production schedules and material availability. Buyers should factor in lead times when planning inventory replenishment to avoid stockouts.
By grasping these technical properties and trade terms, B2B buyers can navigate the dining table manufacturing landscape more effectively, ensuring they make informed decisions that align with their business needs.
Navigating Market Dynamics and Sourcing Trends in the dining table manufacturer Sector
What Are the Current Market Dynamics and Sourcing Trends in the Dining Table Manufacturing Sector?
The dining table manufacturing sector is influenced by various global drivers that shape market dynamics for international B2B buyers, particularly from Africa, South America, the Middle East, and Europe. One significant trend is the increasing demand for multifunctional furniture, as urbanization and smaller living spaces push consumers toward products that maximize utility. Additionally, advancements in B2B technology, such as augmented reality (AR) for virtual showrooms and AI-driven supply chain management, are transforming how manufacturers engage with buyers. For instance, companies can now offer virtual tours of their manufacturing facilities, allowing buyers to inspect quality and processes remotely.
Moreover, sustainability has emerged as a critical factor in sourcing decisions. Buyers are increasingly prioritizing manufacturers that utilize renewable materials and eco-friendly production methods. In regions like Europe and parts of Africa, regulatory frameworks are also tightening around sustainable practices, compelling manufacturers to adopt greener technologies and materials. In South America and the Middle East, the growth of e-commerce platforms facilitates easier access to international suppliers, fostering competition and pushing manufacturers to innovate.
Finally, the ongoing global disruptions, such as the COVID-19 pandemic, have highlighted the need for resilience in supply chains. Buyers are now more inclined to diversify their sourcing strategies, seeking suppliers that can ensure reliability and flexibility in delivery schedules.
How Does Sustainability Influence B2B Sourcing Decisions in the Dining Table Sector?
Sustainability is not just a buzzword; it has become a cornerstone of sourcing strategies in the dining table manufacturing sector. The environmental impact of production processes is under scrutiny, prompting B2B buyers to seek suppliers committed to minimizing their carbon footprint. This includes using sustainably sourced wood, which reduces deforestation and promotes biodiversity.
Ethical supply chains are also gaining importance, as buyers want to ensure that the materials used in manufacturing dining tables are sourced responsibly. Certifications such as Forest Stewardship Council (FSC) and Global Organic Textile Standard (GOTS) are increasingly requested by buyers as proof of sustainable practices. These certifications assure buyers that the materials are not only eco-friendly but also produced under fair labor conditions.
Moreover, there is a growing trend towards using recycled and upcycled materials in furniture design, offering a unique selling proposition for manufacturers. This approach not only appeals to environmentally conscious consumers but also aligns with the circular economy principles that many buyers now advocate.
How Has the Dining Table Manufacturing Sector Evolved Over Time?
The evolution of the dining table manufacturing sector reflects broader societal changes and technological advancements. Historically, dining tables were handcrafted, emphasizing artisanal skills and local materials. However, the industrial revolution introduced mass production techniques, allowing for greater accessibility and affordability.
In recent decades, globalization has transformed the sector, enabling manufacturers to source materials and labor from around the world. This shift has led to a variety of designs and styles, catering to diverse consumer preferences across different regions. The rise of e-commerce has further accelerated this evolution, with buyers now able to explore a wide range of products and suppliers online.
Today, the focus is shifting towards combining traditional craftsmanship with modern technology, resulting in innovative designs that appeal to contemporary consumers. The integration of smart technology into furniture, such as built-in charging ports and adjustable features, is paving the way for the future of dining table manufacturing, aligning with the needs of tech-savvy buyers.
Frequently Asked Questions (FAQs) for B2B Buyers of dining table manufacturer
-
How do I choose the right dining table manufacturer for my business?
When selecting a dining table manufacturer, consider factors such as production capacity, quality assurance processes, and experience in the industry. Look for manufacturers with a strong portfolio and positive reviews from previous clients. Additionally, assess their ability to meet your specific needs, such as design customization, material preferences, and adherence to international standards. Engaging in direct communication can also provide insights into their responsiveness and willingness to collaborate on projects. -
What are the common payment terms offered by dining table manufacturers?
Payment terms can vary significantly among manufacturers, but common practices include a deposit (typically 30-50%) upfront, followed by the balance upon completion or delivery of the order. Some manufacturers may offer net 30 or net 60 terms, allowing you to pay within 30 or 60 days after receipt of goods. Always clarify terms before placing an order to avoid misunderstandings, and consider using letters of credit for larger transactions to mitigate risk. -
What is the typical minimum order quantity (MOQ) for dining tables?
The MOQ for dining tables can range from 50 to 500 units, depending on the manufacturer and the complexity of the design. Custom designs may require higher MOQs due to the specific setup costs involved. It’s advisable to discuss your expected volume and negotiate MOQs that align with your business needs while ensuring that the manufacturer can accommodate your orders without compromising quality. -
How can I ensure the quality of dining tables from a manufacturer?
To ensure quality, request samples of the dining tables before placing a bulk order. This allows you to assess the craftsmanship, materials, and finish. Additionally, inquire about the manufacturer’s quality assurance processes, such as inspections during production and final checks before shipping. Consider visiting the factory if feasible, or hire a third-party inspection service to verify quality standards before shipment. -
What customization options are typically available for dining tables?
Many manufacturers offer various customization options, including size, shape, material, color, and design features. You can specify your requirements for dimensions, finishes, and style to match your brand identity. Some manufacturers may even provide design services to help you create unique pieces. Be sure to discuss your customization needs early in the process to ensure they can accommodate your requests. -
What logistics considerations should I keep in mind when sourcing dining tables internationally?
When sourcing dining tables from international manufacturers, consider shipping costs, delivery times, and customs regulations. Work with a reliable logistics partner who understands the complexities of international shipping, including duties and taxes. Ensure that the manufacturer is experienced in exporting goods and can provide proper documentation for customs clearance. It’s also wise to discuss packaging methods to minimize damage during transit. -
How do I vet potential dining table suppliers?
To vet potential suppliers, conduct thorough research, including checking their business credentials, certifications, and client testimonials. Request references from previous clients to gauge reliability and service quality. Additionally, consider visiting their manufacturing facility to assess their production capabilities and quality control measures. Engaging in direct discussions can also help you gauge their professionalism and willingness to meet your business requirements. -
What are the key trends in dining table design I should consider for my market?
Current trends in dining table design include sustainable materials, multifunctional furniture, and minimalist aesthetics. For markets in Africa, South America, the Middle East, and Europe, consider local cultural influences and preferences in style and functionality. Additionally, focus on incorporating elements that appeal to modern consumers, such as eco-friendly practices and customizable features. Staying informed about design trends can help you select products that resonate with your target audience.
Important Disclaimer & Terms of Use
⚠️ Important Disclaimer
The information provided in this guide, including content regarding manufacturers, technical specifications, and market analysis, is for informational and educational purposes only. It does not constitute professional procurement advice, financial advice, or legal advice.
While we have made every effort to ensure the accuracy and timeliness of the information, we are not responsible for any errors, omissions, or outdated information. Market conditions, company details, and technical standards are subject to change.
B2B buyers must conduct their own independent and thorough due diligence before making any purchasing decisions. This includes contacting suppliers directly, verifying certifications, requesting samples, and seeking professional consultation. The risk of relying on any information in this guide is borne solely by the reader.
Strategic Sourcing Conclusion and Outlook for dining table manufacturer
In the evolving landscape of dining table manufacturing, strategic sourcing emerges as a pivotal factor for international B2B buyers seeking to optimize their procurement processes. By understanding and leveraging supplier capabilities, buyers can ensure access to high-quality products that meet specific market demands, particularly in regions like Africa, South America, the Middle East, and Europe.
Focusing on long-term partnerships with manufacturers enhances not only cost-efficiency but also innovation in product design and sustainability practices. Buyers should prioritize suppliers who demonstrate a commitment to ethical sourcing and environmental responsibility, aligning with the growing consumer demand for sustainable products.
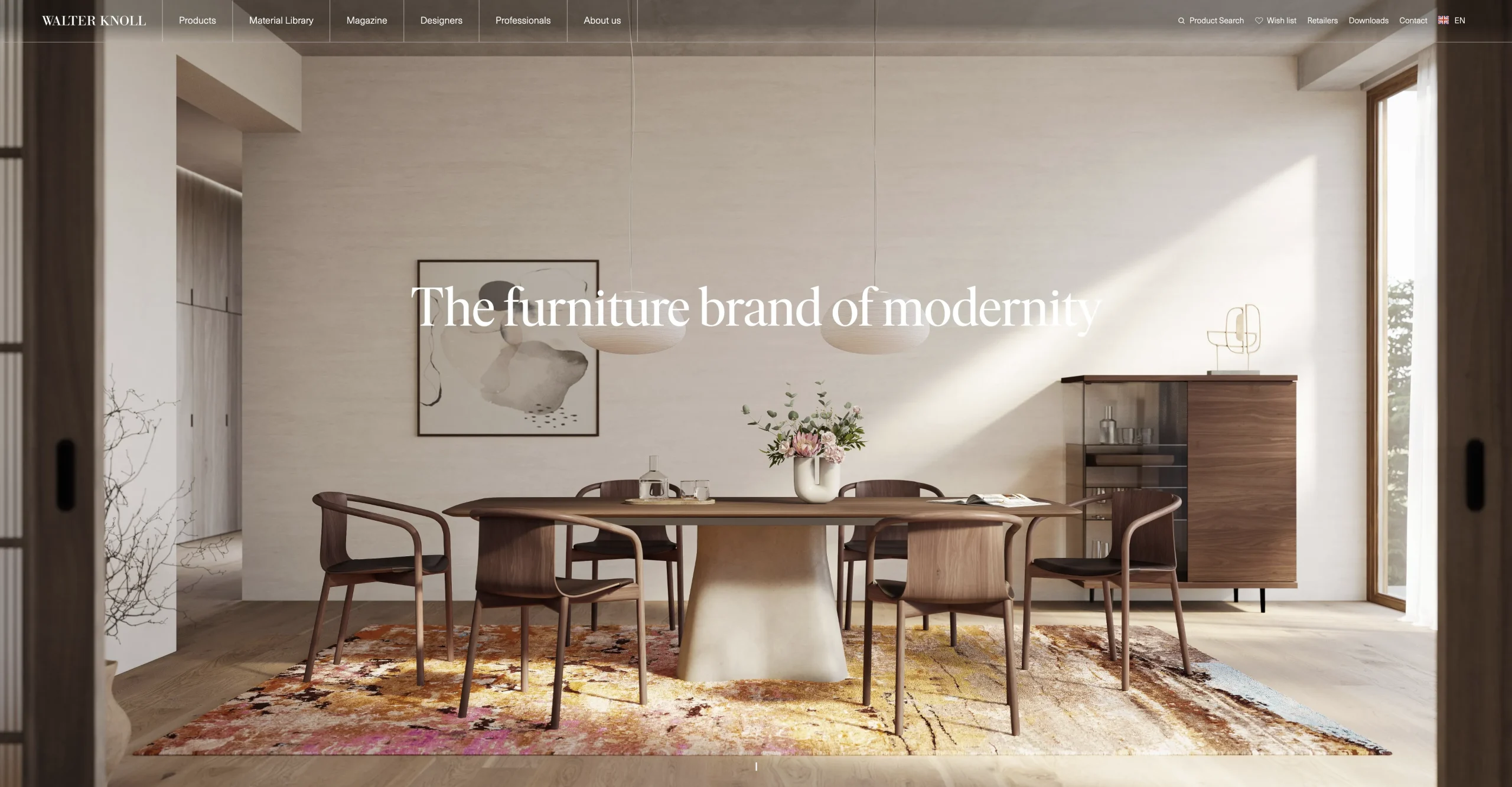
A stock image related to dining table manufacturer.
As the market continues to adapt to changing consumer preferences and economic challenges, staying informed and agile will be crucial. Engaging in strategic sourcing practices will empower buyers to navigate these complexities effectively.
Looking ahead, we encourage international B2B buyers to actively explore partnerships with reputable dining table manufacturers, fostering collaboration that drives mutual growth and success. Your proactive approach in sourcing can significantly impact your competitive advantage in the marketplace.