The Ultimate Guide to Garden Furniture Manufacturer (2025)
Introduction: Navigating the Global Market for garden furniture manufacturer
As the demand for outdoor living spaces continues to rise, sourcing high-quality garden furniture has become a crucial challenge for international B2B buyers. Whether you are looking for durable patio sets, elegant loungers, or multifunctional outdoor dining furniture, understanding the global market landscape is essential. This guide delves into the various types of garden furniture available, their applications in diverse environments, and the importance of vetting suppliers to ensure quality and sustainability.
In the face of rising competition and evolving consumer preferences, buyers from regions such as Africa, South America, the Middle East, and Europe—including key markets like Spain and South Africa—must make informed purchasing decisions. This guide equips you with actionable insights on pricing strategies, material options, and supplier reliability, enabling you to navigate the complexities of global sourcing effectively.
By addressing common pitfalls and providing expert advice on what to look for in a garden furniture manufacturer, this resource aims to empower you to make confident, strategic decisions that align with your business goals. With the right knowledge, you can enhance your product offerings and meet the growing demand for stylish, functional, and sustainable outdoor solutions.
Understanding garden furniture manufacturer Types and Variations
Type Name | Key Distinguishing Features | Primary B2B Applications | Brief Pros & Cons for Buyers |
---|---|---|---|
Metal Garden Furniture | Durable, weather-resistant, often powder-coated | Hotels, restaurants, outdoor cafes | Pros: Long-lasting, low maintenance. Cons: Can be heavy and less comfortable without cushions. |
Wooden Garden Furniture | Natural aesthetics, variety of wood types | Landscaping projects, resorts | Pros: Classic look, eco-friendly options. Cons: Requires regular maintenance to prevent weather damage. |
Plastic Garden Furniture | Lightweight, affordable, versatile designs | Event rentals, temporary setups | Pros: Easy to transport, low cost. Cons: Less durable, may fade over time. |
Rattan/Wicker Garden Furniture | Stylish, often lightweight, suitable for cushions | Luxury hotels, private gardens | Pros: Comfortable, elegant appearance. Cons: Can be less durable if not treated properly. |
Concrete Garden Furniture | Extremely durable, can be molded into various shapes | Public parks, commercial spaces | Pros: Very sturdy, low maintenance. Cons: Heavy, limited portability. |
What Are the Key Characteristics of Metal Garden Furniture?
Metal garden furniture, typically made from aluminum or steel, is known for its durability and resistance to weather conditions. It is often coated with powder for added protection against rust and corrosion, making it ideal for outdoor commercial settings like hotels and restaurants. When purchasing, B2B buyers should consider weight, as heavier pieces may provide stability but can be challenging to move. Additionally, assessing comfort through the availability of cushions is crucial for guest satisfaction.
How Does Wooden Garden Furniture Stand Out?
Wooden garden furniture is celebrated for its natural beauty and variety, often crafted from hardwoods like teak or softer woods like pine. It is suitable for landscaping projects and resorts where aesthetics are paramount. Buyers should weigh the ecological benefits of sustainably sourced wood against the need for regular maintenance, such as sealing and staining, to protect against the elements. The choice of wood type can significantly affect longevity and overall cost.
Why Choose Plastic Garden Furniture for B2B Needs?
Plastic garden furniture is a popular choice for its lightweight and cost-effective nature, making it ideal for event rentals and temporary setups. It comes in a variety of colors and styles, offering versatility for different branding needs. While it is easy to transport and maintain, buyers should be cautious of its durability, as cheaper plastic can fade and become brittle over time. Ensuring quality through reputable manufacturers is key to maximizing value.
What Are the Benefits of Rattan/Wicker Garden Furniture?
Rattan or wicker garden furniture combines style with comfort, often featuring plush cushions that enhance the outdoor experience. It is commonly used in luxury hotels and private gardens, appealing to buyers looking for an elegant aesthetic. However, B2B buyers must consider the durability of the materials used; synthetic rattan is generally more weather-resistant than natural fibers. Understanding the treatment processes can help ensure longevity.
How Does Concrete Garden Furniture Compare?
Concrete garden furniture is unmatched in durability, often found in public parks and commercial spaces where heavy use is expected. Its ability to withstand harsh weather conditions makes it a long-term investment. However, buyers should note that concrete pieces can be quite heavy, limiting portability and flexibility in arrangements. The unique designs available can also serve as a focal point in outdoor settings, enhancing the overall ambiance.
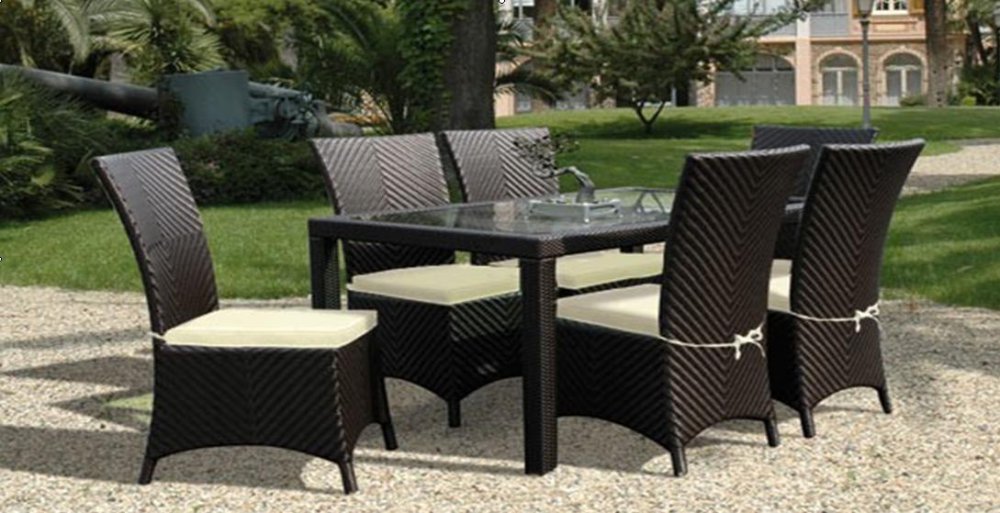
A stock image related to garden furniture manufacturer.
Related Video: Wooden Furniture Mass Production Factory. Wood Couch Manufacturing Process.
Key Industrial Applications of garden furniture manufacturer
Industry/Sector | Specific Application of garden furniture manufacturer | Value/Benefit for the Business | Key Sourcing Considerations for this Application |
---|---|---|---|
Hospitality | Outdoor seating for restaurants and cafes | Enhances customer experience and expands seating capacity | Durability, weather resistance, and aesthetic appeal |
Real Estate Development | Furnishing for residential complexes and parks | Increases property value and attracts tenants | Customization options, compliance with local regulations |
Events and Catering | Temporary outdoor furniture for events | Provides flexibility and enhances event ambiance | Portability, ease of setup, and rental options |
Retail | Display furniture for garden centers and home stores | Attracts customers and showcases products effectively | Design versatility, branding opportunities, and durability |
Public Spaces | Installation in parks and recreational areas | Promotes community engagement and enhances public spaces | Safety standards, maintenance requirements, and sustainability |
How is Garden Furniture Used in the Hospitality Sector?
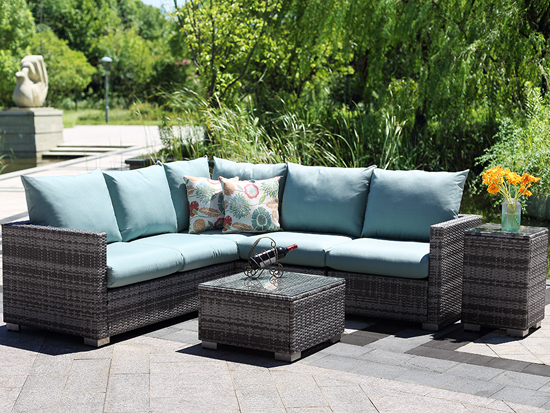
A stock image related to garden furniture manufacturer.
In the hospitality industry, garden furniture manufacturers provide essential outdoor seating solutions for restaurants and cafes. This furniture not only enhances the aesthetic appeal of outdoor dining areas but also expands the seating capacity, allowing businesses to accommodate more customers during peak hours. For international B2B buyers, especially from regions like South Africa and Spain, sourcing furniture that is both durable and weather-resistant is critical. These buyers must consider local climate conditions to ensure the longevity of their investments.
What Role Does Garden Furniture Play in Real Estate Development?
In real estate development, garden furniture is utilized to furnish residential complexes and public parks. By integrating stylish and functional outdoor furniture, developers can significantly increase property value and attract potential tenants. International buyers in Europe and the Middle East should focus on customization options that align with the architectural style of their developments. Additionally, compliance with local regulations regarding safety and environmental standards is essential when sourcing these products.
How is Garden Furniture Applied in Events and Catering?
Garden furniture manufacturers supply temporary outdoor furniture for events, such as weddings and corporate gatherings. This furniture provides flexibility in layout and enhances the overall ambiance of the event, making it a crucial element for catering businesses. For B2B buyers, especially in South America and Africa, considerations like portability and ease of setup are vital. Furthermore, having rental options can significantly benefit event planners looking to manage costs effectively.
Why is Garden Furniture Important for Retail Spaces?
In the retail sector, garden furniture is used as display furniture in garden centers and home improvement stores. This application attracts customers and effectively showcases products, contributing to increased sales. B2B buyers in Europe should prioritize design versatility and durability when sourcing display furniture. Additionally, opportunities for branding through customized designs can enhance marketing efforts and customer engagement.
How Does Garden Furniture Benefit Public Spaces?
Garden furniture plays a significant role in public spaces, such as parks and recreational areas. By installing comfortable and aesthetically pleasing furniture, municipalities can promote community engagement and enhance the usability of these spaces. International buyers from the Middle East and Africa should pay attention to safety standards and maintenance requirements when sourcing public space furniture. Sustainability is also a growing consideration, as eco-friendly materials are increasingly favored in public installations.
Related Video: Farm tools and their uses
3 Common User Pain Points for ‘garden furniture manufacturer’ & Their Solutions
Scenario 1: Managing Supply Chain Disruptions in Garden Furniture Procurement
The Problem: International B2B buyers often face significant challenges related to supply chain disruptions when sourcing garden furniture. Factors such as political instability, shipping delays, and fluctuating tariffs can lead to unpredictable delivery timelines and increased costs. For buyers in regions like Africa or South America, these disruptions can hinder their ability to meet customer demands, ultimately affecting sales and reputation.
The Solution: To mitigate supply chain issues, buyers should establish relationships with multiple garden furniture manufacturers across different geographic locations. This diversification allows for flexibility in sourcing materials and products, ensuring that if one supplier faces disruptions, alternatives are readily available. Additionally, employing a robust logistics partner can streamline shipping processes and provide real-time tracking, giving buyers better visibility and control over their orders. It is also beneficial to negotiate clear terms regarding delivery times and contingencies in contracts to protect against unforeseen delays.
Scenario 2: Ensuring Quality and Durability of Garden Furniture Products
The Problem: Quality assurance is a pressing concern for B2B buyers in the garden furniture sector. Many manufacturers may offer appealing designs at competitive prices, but the durability of materials and construction is often compromised. This is particularly problematic for buyers in regions with extreme weather conditions, where furniture must withstand sun, rain, and humidity without deteriorating quickly.
The Solution: Buyers should prioritize sourcing from manufacturers who provide detailed information about the materials used in their products, along with warranties or guarantees that reflect their durability. Conducting factory visits or requesting samples can provide firsthand insight into the quality of craftsmanship. Implementing a quality control checklist that includes criteria such as material specifications, weather resistance, and safety standards can help in making informed purchasing decisions. Additionally, consider utilizing third-party inspection services to verify product quality before shipment.
Scenario 3: Navigating Cultural Preferences and Trends in Garden Furniture Design
The Problem: B2B buyers must often navigate diverse cultural preferences and trends in garden furniture design, which can vary significantly across regions such as Europe, the Middle East, and Africa. Misalignment between product offerings and local consumer preferences can lead to poor sales performance and excess inventory, impacting profitability.
The Solution: To address this issue, buyers should conduct thorough market research to understand local tastes and trends in garden furniture. Collaborating with local designers or consultants can provide valuable insights into consumer preferences and help tailor product selections accordingly. Attending international trade shows and exhibitions can also expose buyers to emerging trends and innovative designs that resonate with their target market. Additionally, leveraging social media and customer feedback can guide product development and marketing strategies, ensuring alignment with regional expectations. Engaging in direct conversations with manufacturers about customization options can facilitate the creation of products that cater specifically to local demands.
Strategic Material Selection Guide for garden furniture manufacturer
When selecting materials for garden furniture manufacturing, it is crucial for international B2B buyers to consider various factors that influence product performance, durability, and compliance with regional standards. This section analyzes four common materials used in garden furniture: wood, metal, plastic, and composite materials, highlighting their properties, advantages, disadvantages, and specific considerations for buyers from Africa, South America, the Middle East, and Europe.
What Are the Key Properties of Wood for Garden Furniture?
Wood is a traditional choice for garden furniture, valued for its aesthetic appeal and natural feel. Key properties include its strength and thermal insulation, which makes it comfortable to use in varying temperatures. However, wood is susceptible to moisture, pests, and UV damage, which can affect its longevity.
Pros & Cons:
– Pros: Wood offers excellent durability and can be refinished or restored, enhancing its lifespan. It is also relatively easy to work with during manufacturing.
– Cons: The cost of high-quality hardwood can be significant, and maintenance is required to prevent rot and degradation. Additionally, wood may not be suitable for all climates, particularly humid or very dry regions.
Impact on Application: Wood is compatible with various finishes, allowing customization for aesthetic preferences. However, it may require treatments to enhance its resistance to environmental factors.
Considerations for International Buyers: Buyers should ensure compliance with local regulations regarding sustainable sourcing and treatment of wood. Standards such as FSC certification are increasingly valued in markets like Europe and North America.
How Does Metal Perform as a Material for Garden Furniture?
Metal, particularly aluminum and steel, is increasingly popular for garden furniture due to its strength and modern aesthetic. Key properties include high corrosion resistance (especially for aluminum) and the ability to withstand heavy loads.
Pros & Cons:
– Pros: Metal furniture is durable and often requires minimal maintenance. Aluminum is lightweight, making it easy to move, while steel provides sturdiness.
– Cons: Metal can become hot in direct sunlight, making it uncomfortable to use without cushions. Additionally, steel may rust if not properly coated or treated.
Impact on Application: Metal furniture is suitable for various outdoor settings, but compatibility with specific environments (e.g., coastal areas) should be considered due to potential corrosion.
Considerations for International Buyers: Compliance with standards like ASTM or EN for corrosion resistance is crucial. Buyers should also consider local preferences for design and finish.
What Are the Advantages of Using Plastic in Garden Furniture?
Plastic materials, particularly high-density polyethylene (HDPE), are gaining traction in the garden furniture market. They are known for their weather resistance and low maintenance requirements.
Pros & Cons:
– Pros: Plastic is lightweight, affordable, and resistant to fading and moisture. It is also easy to clean and can be produced in various colors.
– Cons: While durable, plastic may not have the same aesthetic appeal as wood or metal. It can also warp under extreme temperatures.
Impact on Application: Plastic is suitable for casual outdoor settings and is often used in family-oriented designs. However, its longevity can be affected by exposure to harsh weather conditions.
Considerations for International Buyers: Buyers should look for compliance with environmental standards, especially regarding recyclability and the use of recycled materials. Preferences may vary by region, with some markets favoring eco-friendly options.
Why Are Composite Materials Important for Garden Furniture?
Composite materials, which combine wood fibers and plastic, offer a unique blend of properties. They are designed to provide the aesthetic of wood with the durability of plastic.
Pros & Cons:
– Pros: Composites are resistant to moisture, insects, and fading. They require minimal maintenance and do not splinter, making them safe for families.
– Cons: The initial cost can be higher than traditional materials, and not all composites are created equal in terms of durability.
Impact on Application: Composites are ideal for high-traffic areas and can withstand various weather conditions, making them suitable for diverse climates.
Considerations for International Buyers: Buyers should verify the manufacturer’s claims regarding durability and environmental impact. Compliance with standards such as ASTM for performance testing is essential.
Summary Table of Material Selection for Garden Furniture
Material | Typical Use Case for Garden Furniture Manufacturer | Key Advantage | Key Disadvantage/Limitation | Relative Cost (Low/Med/High) |
---|---|---|---|---|
Wood | Traditional outdoor furniture, benches, tables | Aesthetic appeal and durability | Susceptible to moisture and pests | Medium |
Metal | Modern chairs, tables, and loungers | High strength and corrosion resistance | Can get hot in direct sunlight | Medium to High |
Plastic | Casual outdoor settings, family furniture | Lightweight and low maintenance | May lack aesthetic appeal | Low |
Composite | High-traffic outdoor areas, durable furniture | Weather resistant and safe for families | Higher initial cost | Medium to High |
This guide provides insights into material selection for garden furniture manufacturing, helping international B2B buyers make informed decisions based on performance, cost, and compliance with regional standards.
In-depth Look: Manufacturing Processes and Quality Assurance for garden furniture manufacturer
What Are the Key Stages in the Manufacturing Process of Garden Furniture?
The manufacturing process for garden furniture involves several critical stages that ensure the final product meets the expectations of durability, aesthetics, and functionality. The main stages include material preparation, forming, assembly, and finishing.
Material Preparation
The first step in manufacturing garden furniture is selecting and preparing the raw materials. Common materials include wood, metal, and synthetic plastics. For wooden furniture, sourcing sustainably harvested timber is essential, not only for environmental compliance but also for ensuring product longevity. This stage often involves cutting, drying, and treating wood to prevent rot and insect damage.
For metal furniture, the materials may undergo processes like galvanization or powder coating to enhance corrosion resistance. Synthetic materials, such as high-density polyethylene (HDPE), are often used for their weather-resistant properties, especially in regions with extreme weather conditions.
How Is Garden Furniture Formed?
Forming is the next critical stage where raw materials are shaped into their final form. For wood, this may involve techniques such as bending, molding, or joining pieces through methods like mortise and tenon or doweling. Metal furniture might require welding, bending, and machining processes, while synthetic materials can be molded or extruded.
Innovative techniques such as CNC machining are increasingly used to enhance precision in forming, ensuring that parts fit together seamlessly. This is particularly beneficial for large orders where uniformity is crucial for bulk buyers.
What Does the Assembly Process Entail?
Once the individual components are formed, the assembly stage begins. This process can be manual or automated, depending on the scale of production. For manual assembly, skilled labor is often required to ensure that joints are secure and that the furniture is structurally sound. Automated assembly lines might utilize robotic arms for repetitive tasks, increasing efficiency and reducing labor costs.
Quality checks during assembly are vital to ensure that all components fit together correctly, and any defects are identified before moving to the next stage.
How Is Finishing Applied to Garden Furniture?
The finishing stage is crucial for enhancing the aesthetic appeal and durability of garden furniture. This can include sanding, staining, painting, or applying protective coatings. For wooden furniture, finishes such as polyurethane or varnish provide a barrier against moisture and UV rays, which is particularly important for outdoor use.
Metal finishes often involve powder coating or painting to prevent rust and enhance visual appeal. In addition, UV-resistant treatments are applied to synthetic materials to prevent fading over time.
What Are the Quality Assurance Standards for Garden Furniture Manufacturing?
Quality assurance (QA) is essential in maintaining high standards throughout the manufacturing process. International standards, such as ISO 9001, provide a framework for quality management systems. This standard ensures that manufacturers consistently meet customer requirements and enhance satisfaction.
Which Industry-Specific Certifications Should B2B Buyers Look For?
In addition to ISO certifications, specific industry standards may apply, such as CE marking for products sold in Europe, which indicates compliance with health, safety, and environmental protection standards. For outdoor furniture, adherence to standards like the American National Standards Institute (ANSI) or the American Society for Testing and Materials (ASTM) can also be crucial, especially in regions like North America.
What Are the Key Quality Control Checkpoints?
Quality control (QC) involves several checkpoints throughout the manufacturing process:
- Incoming Quality Control (IQC): This initial stage checks raw materials for compliance with specifications before they enter the production line.
-
In-Process Quality Control (IPQC): This involves monitoring the manufacturing process to catch defects early. Regular inspections during forming, assembly, and finishing ensure that any issues are identified and addressed promptly.
-
Final Quality Control (FQC): Before products leave the factory, a thorough inspection ensures that they meet all quality standards and specifications.
How Can B2B Buyers Verify Supplier Quality Control?
For international B2B buyers, particularly from regions like Africa, South America, the Middle East, and Europe, verifying supplier quality control is crucial for ensuring product reliability. Here are actionable steps to consider:
-
Conduct Audits: Regular audits of the manufacturing facility can provide insight into the supplier’s quality management practices. Buyers can request to review the results of past audits or arrange for third-party audits if necessary.
-
Review Quality Reports: Suppliers should provide detailed quality reports that outline the results of IQC, IPQC, and FQC processes. These documents should detail any corrective actions taken in response to identified defects.
-
Request Third-Party Inspections: Engaging third-party inspection services can provide an unbiased assessment of the supplier’s quality control processes and the final product quality.
-
Understand Certification Nuances: Buyers should familiarize themselves with relevant certifications and standards applicable in their region. This is particularly important for compliance with local regulations, which may differ significantly from international standards.
-
Evaluate Supplier Communication: Effective communication regarding quality control processes is vital. Suppliers should be transparent about their QC measures and willing to provide documentation upon request.
What Testing Methods Are Commonly Used in Garden Furniture Manufacturing?
Testing methods play a crucial role in ensuring the durability and safety of garden furniture. Common testing methods include:
- Load Testing: Assessing the weight-bearing capacity of chairs, tables, and other furniture pieces to ensure they can withstand regular use.
-
Weather Resistance Testing: Simulating environmental conditions, such as UV exposure and moisture, to evaluate how materials will perform over time.
-
Safety Testing: Ensuring that products meet safety standards to prevent injuries during use, particularly for children’s outdoor furniture.
By understanding the manufacturing processes and quality assurance practices involved in garden furniture production, B2B buyers can make informed decisions and select reliable suppliers that meet their quality expectations. This knowledge is essential for establishing successful long-term partnerships in a competitive international market.
Practical Sourcing Guide: A Step-by-Step Checklist for ‘garden furniture manufacturer’
This guide aims to equip international B2B buyers, especially from Africa, South America, the Middle East, and Europe, with a comprehensive checklist for sourcing garden furniture manufacturers. Understanding the nuances of procurement in this sector is crucial for making informed decisions that align with your business needs and market standards.
Step 1: Define Your Technical Specifications
Establishing clear technical specifications is essential to ensure the garden furniture meets your market demands. Consider factors such as materials, dimensions, and design aesthetics that are popular in your region. Be specific about weather resistance, durability, and safety standards that the products must comply with, as these can significantly affect customer satisfaction.
Step 2: Research Potential Suppliers
Conduct thorough research to identify potential suppliers who specialize in garden furniture manufacturing. Utilize online platforms, trade directories, and industry networks to create a list of viable candidates. Focus on suppliers with a strong reputation and positive reviews from other B2B buyers, especially in your target market regions.
Step 3: Evaluate Supplier Certifications
Verify that your shortlisted suppliers hold necessary certifications that validate their compliance with international quality and safety standards. Look for certifications such as ISO 9001 for quality management and FSC for sustainable sourcing of materials. Certifications not only enhance supplier credibility but also ensure that the products you receive are of high quality and environmentally friendly.
Step 4: Request Samples for Quality Assessment
Before placing a bulk order, request samples of the garden furniture to assess the quality and craftsmanship. This step allows you to evaluate materials, finishes, and overall design firsthand. Pay close attention to details such as stitching, paint quality, and sturdiness, as these elements can greatly influence customer perceptions and satisfaction.
Step 5: Negotiate Terms and Pricing
Once you have selected a few potential suppliers, initiate negotiations regarding terms and pricing. Discuss bulk order discounts, payment terms, and delivery timelines. Ensure that you clarify any potential hidden costs, such as shipping fees or taxes, to avoid surprises later in the procurement process.
Step 6: Establish Communication Protocols
Effective communication is key to successful sourcing. Set clear expectations regarding response times, updates on production status, and handling any issues that may arise. Consider using project management tools or regular check-ins to ensure a smooth flow of information throughout the procurement process.
Step 7: Finalize Contracts and Place Orders
After agreeing on terms, finalize contracts that outline all aspects of the deal, including product specifications, delivery schedules, and penalties for non-compliance. Ensure both parties sign the agreement to protect your business interests. Once everything is in place, proceed to place your order with confidence, knowing that you have conducted thorough due diligence.
By following this step-by-step checklist, B2B buyers can effectively navigate the complexities of sourcing garden furniture manufacturers, ensuring they partner with reliable suppliers that meet their specific needs.
Comprehensive Cost and Pricing Analysis for garden furniture manufacturer Sourcing
What Are the Key Cost Components in Garden Furniture Manufacturing?
When sourcing garden furniture, understanding the cost structure is essential for international B2B buyers. The primary cost components include:
-
Materials: The choice of materials significantly impacts the overall cost. Common materials include wood, metal, wicker, and plastic. Sustainable options may have a higher initial price but could reduce long-term costs through durability and lower maintenance.
-
Labor: Labor costs vary widely by region. In countries with higher wages, such as those in Europe, labor costs can represent a substantial portion of total manufacturing expenses. Conversely, manufacturers in regions like South Africa or South America may offer lower labor costs but could also present challenges related to skills and workforce stability.
-
Manufacturing Overhead: This includes utilities, rent, and equipment depreciation. A manufacturer with advanced technology may have higher upfront costs but can achieve efficiency that lowers the per-unit cost over time.
-
Tooling: The investment in molds and specialized tools can be significant, especially for custom designs. This cost is often amortized over larger production runs, making it crucial for buyers to consider order volume.
-
Quality Control (QC): Implementing robust QC processes ensures product reliability but adds to costs. Buyers should evaluate how manufacturers manage QC, as this can affect both price and long-term satisfaction with the products.
-
Logistics: Shipping and handling costs can vary greatly depending on the origin and destination of the goods. It is essential for buyers to factor in these costs when evaluating suppliers.
-
Margin: Manufacturers typically include a profit margin that varies based on market conditions and competition. Understanding typical margins in the target market can help buyers negotiate better deals.
How Do Price Influencers Affect Sourcing Decisions?
Several factors influence pricing in garden furniture manufacturing:
-
Volume/MOQ: Manufacturers often have minimum order quantities (MOQs). Buying in bulk can lead to significant discounts, so it’s beneficial for buyers to assess their needs carefully.
-
Specifications and Customization: Custom designs or specific material requirements can increase costs. Buyers should weigh the benefits of customization against the price increase it incurs.
-
Material Selection: High-quality or specialty materials may raise the price but can also enhance the product’s appeal and longevity. Buyers must balance cost with quality to ensure they meet their market’s expectations.
-
Quality Certifications: Products that meet international standards or certifications may command higher prices. However, these certifications can enhance marketability and consumer trust.
-
Supplier Factors: Reliability, reputation, and production capacity of the supplier can influence pricing. It’s essential for buyers to conduct thorough due diligence to ensure they partner with reputable manufacturers.
-
Incoterms: Understanding Incoterms (International Commercial Terms) is vital as they determine who bears shipping costs and risks. This knowledge can significantly impact the total landed cost of the furniture.
What Are Some Buyer Tips for Negotiating Prices?
For international B2B buyers, particularly from diverse regions such as Africa, South America, the Middle East, and Europe, effective negotiation and sourcing strategies are critical:
- Negotiate Based on Total Cost of Ownership (TCO): Rather than focusing solely on the purchase price, consider the TCO, which includes shipping, maintenance, and potential resale value. This holistic view can lead to more informed purchasing decisions.
-
Leverage Volume Discounts: If possible, consolidate orders to reach higher volumes. This strategy can unlock better pricing and terms from suppliers.
-
Clarify Payment Terms: Flexible payment options can ease cash flow constraints. Buyers should negotiate terms that work best for their financial situation.
-
Be Aware of Pricing Nuances: Different regions may have varying pricing structures due to local economic conditions, tariffs, and trade agreements. Understanding these nuances can give buyers an edge in negotiations.
-
Request Samples: Before committing to a large order, request samples to evaluate quality. This practice minimizes the risk of costly mistakes and ensures that the product meets expectations.
Disclaimer on Indicative Prices
Prices in the garden furniture manufacturing industry are subject to change based on market conditions, material availability, and economic factors. Buyers should always seek updated quotes and consider fluctuations in currency exchange rates when dealing with international suppliers.
Alternatives Analysis: Comparing garden furniture manufacturer With Other Solutions
When considering garden furniture for international markets, it’s essential for B2B buyers to explore various alternatives to traditional garden furniture manufacturers. This analysis will provide insights into comparable solutions that cater to different business needs, focusing on performance, cost, and practicality.
Comparison Aspect | Garden Furniture Manufacturer | Alternative 1: DIY Solutions | Alternative 2: Modular Furniture Systems |
---|---|---|---|
Performance | High-quality materials and craftsmanship. | Varies based on materials used. | Customizable and adaptable to various spaces. |
Cost | Generally higher due to quality and craftsmanship. | Low cost if materials are sourced cheaply. | Moderate cost; investment in quality may be higher. |
Ease of Implementation | Requires professional installation and setup. | Requires skills and tools; can be time-consuming. | Quick assembly with minimal tools required. |
Maintenance | Regular maintenance required to ensure longevity. | Varies based on materials; may require more upkeep. | Generally low maintenance, depending on materials. |
Best Use Case | Ideal for high-end residential or commercial spaces. | Suitable for budget-conscious consumers or temporary setups. | Great for flexible spaces needing frequent redesign. |
What are the Pros and Cons of DIY Solutions for Garden Furniture?
DIY solutions can offer significant cost savings for businesses, especially those operating on a tight budget. By sourcing materials locally, buyers can create unique furniture that reflects their brand’s aesthetic. However, the quality of the final product can vary greatly depending on the skill level of the builders and the materials chosen. Additionally, the time investment may be substantial, which could be a drawback for businesses needing immediate solutions.
How Do Modular Furniture Systems Compare to Traditional Manufacturers?
Modular furniture systems present an appealing alternative due to their flexibility and ease of assembly. These systems allow businesses to adapt their outdoor spaces quickly, accommodating changing needs or seasonal demands. While the initial investment might be moderate, the longevity and adaptability can provide excellent value over time. However, some modular options may not offer the same level of craftsmanship and durability found in traditional garden furniture manufacturing, potentially leading to higher replacement rates in the long run.
Conclusion: How Can B2B Buyers Choose the Right Solution for Their Needs?
When selecting the right garden furniture solution, B2B buyers should carefully evaluate their specific needs, including budget, space requirements, and desired aesthetics. While traditional manufacturers may provide high-quality, durable options ideal for upscale environments, alternatives like DIY solutions and modular systems offer flexibility and cost savings that can be advantageous for different market segments. Ultimately, the decision should align with the overall business strategy, ensuring that the chosen solution meets both current and future demands effectively.
Essential Technical Properties and Trade Terminology for garden furniture manufacturer
What Are the Essential Technical Properties for Garden Furniture Manufacturing?
When sourcing garden furniture, international B2B buyers should be aware of several key technical properties that influence product quality, durability, and suitability for various climates. Understanding these specifications can help make informed purchasing decisions.
1. Material Grade: Why Does It Matter?
The material grade of garden furniture significantly impacts its durability and aesthetic appeal. Common materials include teak, aluminum, and synthetic wicker. For instance, teak is known for its resistance to moisture and insects, making it ideal for outdoor use in humid climates such as those in South Africa. Aluminum, on the other hand, is lightweight and resistant to rust, which is beneficial for regions with high precipitation like parts of Europe. Selecting the right material is crucial for ensuring longevity and reducing replacement costs.
2. Tolerance Levels: What Should Buyers Know?
Tolerance levels refer to the permissible limits of variation in dimensions and physical properties during manufacturing. For example, a tolerance of ±2mm on a table’s height ensures that all units meet customer expectations. Tight tolerances are essential for maintaining consistent quality, especially in furniture that needs to fit specific spaces. Understanding these specifications helps buyers assess the reliability of a manufacturer’s production process.
3. Finish Quality: How It Affects Maintenance
The finish quality of garden furniture affects both appearance and maintenance requirements. Common finishes include powder coating and varnishing. A high-quality powder coat provides UV protection and scratch resistance, which is particularly important in sunny climates like those found in the Middle East. Buyers should inquire about the types of finishes used and their expected lifespan to gauge maintenance needs.
4. Weight Capacity: Why Is It Critical?
Weight capacity indicates how much weight a piece of furniture can safely support. This is particularly important for items like chairs and tables that will accommodate various users. For instance, a dining table designed for outdoor use should have a higher weight capacity to withstand heavy usage during gatherings. Ensuring the furniture meets appropriate weight standards can prevent accidents and enhance customer satisfaction.
What Are Common Trade Terminology and Jargon in Garden Furniture Manufacturing?
Navigating the world of garden furniture manufacturing involves understanding specific trade terms that can influence purchasing decisions. Here are some essential terms that buyers should familiarize themselves with:
1. OEM (Original Equipment Manufacturer): What Does It Mean?
OEM refers to a company that produces parts or equipment that may be marketed by another manufacturer. In the garden furniture industry, an OEM might produce furniture components that are branded by another company. Understanding OEM relationships can help buyers identify potential partners and evaluate product authenticity.
2. MOQ (Minimum Order Quantity): How Is It Relevant?
MOQ is the smallest quantity of a product that a supplier is willing to sell. In the garden furniture sector, MOQs can vary significantly based on the manufacturer and the product type. Knowing the MOQ helps buyers assess whether they can meet the supplier’s requirements, which can impact overall purchasing costs and inventory management.
3. RFQ (Request for Quotation): Why Is It Important?
An RFQ is a document that a buyer submits to suppliers to solicit pricing and terms for specific goods or services. For garden furniture, an RFQ allows buyers to compare quotes from various manufacturers, ensuring they get competitive pricing and favorable terms. This process is vital for budgeting and financial planning.
4. Incoterms: What Are They and Why Do They Matter?
Incoterms (International Commercial Terms) are standardized terms that define the responsibilities of buyers and sellers in international transactions. For garden furniture, understanding Incoterms like FOB (Free On Board) or CIF (Cost, Insurance, and Freight) is crucial for determining shipping costs and responsibilities. This knowledge helps buyers negotiate better shipping agreements and avoid unexpected charges.
By familiarizing themselves with these technical properties and trade terms, international B2B buyers can enhance their purchasing strategies, ensuring they select the best garden furniture for their needs while navigating the complexities of global trade.
Navigating Market Dynamics and Sourcing Trends in the garden furniture manufacturer Sector
What Are the Current Market Dynamics and Sourcing Trends in the Garden Furniture Manufacturing Sector?
The garden furniture manufacturing sector is witnessing significant transformation driven by various global factors. The increasing demand for outdoor living spaces, particularly in urban areas, is a primary market driver. As more consumers seek to enhance their outdoor environments, B2B buyers are presented with a growing array of innovative designs and multifunctional products. Additionally, the rise of e-commerce platforms has streamlined sourcing processes, allowing international buyers from regions like Africa, South America, the Middle East, and Europe (notably Spain and South Africa) to access a broader range of suppliers.
Emerging technologies such as augmented reality (AR) and virtual reality (VR) are reshaping how buyers interact with products before purchase. These technologies enable buyers to visualize furniture in their intended environments, fostering informed decision-making. Moreover, the integration of smart technologies into garden furniture—like solar-powered lighting and Bluetooth speakers—has become increasingly popular, appealing to a tech-savvy consumer base.
The market is also adapting to shifts in consumer preferences towards customizable and sustainable products. Buyers are now looking for suppliers who can offer personalized solutions that cater to specific aesthetic and functional requirements, further solidifying the need for flexibility in manufacturing processes.
How Is Sustainability Shaping the Garden Furniture Manufacturing Sector?
Sustainability is no longer a niche consideration; it is central to the garden furniture manufacturing sector’s future. As environmental awareness grows, international B2B buyers are increasingly prioritizing suppliers with ethical sourcing practices and sustainable materials. The use of reclaimed wood, recycled plastics, and eco-friendly finishes is becoming a standard expectation rather than an exception.
The importance of ethical supply chains cannot be overstated. Buyers are now demanding transparency in sourcing, as they recognize the environmental and social implications of their purchasing decisions. Certifications such as FSC (Forest Stewardship Council) and Greenguard are becoming essential criteria for supplier selection, ensuring that products meet high environmental standards.
Additionally, the concept of circular economy is gaining traction, where manufacturers design products for longevity and recyclability. This shift not only addresses environmental concerns but also appeals to consumers who are willing to invest in sustainable products, thus enhancing brand loyalty.
What Is the Evolution of the Garden Furniture Manufacturing Sector and Its Significance for B2B Buyers?
The garden furniture manufacturing sector has evolved significantly over the decades, transitioning from traditional craftsmanship to modern manufacturing techniques. Initially, garden furniture was predominantly made from wood, focusing on durability and aesthetic appeal. However, the late 20th century saw the introduction of new materials like aluminum and synthetic wicker, driven by the need for lightweight, weather-resistant options.
This evolution reflects broader trends in consumer behavior, particularly the growing emphasis on outdoor lifestyles and the desire for low-maintenance solutions. For B2B buyers, understanding this historical context is crucial, as it informs current market offerings and future innovations. Buyers can leverage this knowledge to anticipate trends and make strategic sourcing decisions that align with consumer demands.
In conclusion, navigating the complexities of the garden furniture manufacturing sector requires B2B buyers to stay informed about market dynamics, prioritize sustainability, and recognize the historical context that shapes current offerings. By doing so, they can make strategic, informed decisions that not only meet their immediate needs but also contribute to long-term sustainability goals.
Frequently Asked Questions (FAQs) for B2B Buyers of garden furniture manufacturer
-
How do I choose the right garden furniture manufacturer for my business needs?
When selecting a garden furniture manufacturer, assess their product quality, design variety, and materials used. Look for manufacturers with a strong portfolio and positive client testimonials. Consider their production capacity to meet your demand and their ability to customize products to fit your brand’s aesthetic. Additionally, verify their compliance with international standards and regulations to ensure quality and safety. -
What are the common materials used in garden furniture production?
Garden furniture is typically made from materials such as aluminum, teak, wicker, and plastic. Aluminum is lightweight and rust-resistant, making it ideal for outdoor use. Teak is highly durable and weather-resistant, while wicker offers a classic look with comfort. Plastic can be cost-effective and comes in various designs. Evaluate the material’s durability, maintenance requirements, and aesthetic appeal based on your target market’s preferences. -
What minimum order quantities (MOQs) should I expect from garden furniture manufacturers?
MOQs vary significantly among manufacturers, often influenced by production capabilities and material costs. Generally, expect MOQs to range from 50 to 500 units per design. Discuss your specific needs with potential suppliers, as many are willing to negotiate MOQs for first-time orders or long-term partnerships. Understanding your sales forecasts can help you negotiate favorable terms. -
How can I ensure the quality of garden furniture products?
To ensure product quality, conduct thorough supplier vetting by requesting samples and reviewing past client feedback. Establish clear quality assurance protocols that include inspections at various production stages. Discuss certifications that validate adherence to international standards, and consider visiting the manufacturing site if possible. Implementing regular audits can also enhance quality control. -
What payment terms are typically offered by garden furniture manufacturers?
Payment terms can vary widely based on the manufacturer and the buyer’s relationship. Common terms include a 30% deposit upfront with the balance due before shipping or upon delivery. Some suppliers might offer letters of credit or payment through escrow services for larger orders. Always clarify terms and negotiate to secure conditions that protect your financial interests while maintaining a good relationship with the supplier. -
What customization options are available for garden furniture?
Most garden furniture manufacturers offer a range of customization options, including color, material, size, and design modifications. Discuss your specific needs early in the negotiation process to determine the feasibility of your requests. Some manufacturers may also provide branding options, such as logo placement, which can enhance your product’s marketability. -
How do I handle logistics when importing garden furniture?
Logistics for importing garden furniture involves coordinating shipping methods, customs clearance, and warehousing. Work closely with the manufacturer to understand their shipping practices and timelines. Choose reliable freight forwarders experienced in handling bulky items to ensure safe transport. Familiarize yourself with customs regulations in your country to avoid delays and additional costs. -
What are the best practices for establishing a long-term relationship with a garden furniture supplier?
To foster a successful long-term relationship with your garden furniture supplier, maintain open communication and regularly provide feedback on product quality and service. Establish clear expectations regarding delivery times, quality standards, and payment terms. Participate in joint planning for future orders to align your business goals. Building trust through consistency and reliability will encourage the supplier to prioritize your needs.
Important Disclaimer & Terms of Use
⚠️ Important Disclaimer
The information provided in this guide, including content regarding manufacturers, technical specifications, and market analysis, is for informational and educational purposes only. It does not constitute professional procurement advice, financial advice, or legal advice.
While we have made every effort to ensure the accuracy and timeliness of the information, we are not responsible for any errors, omissions, or outdated information. Market conditions, company details, and technical standards are subject to change.
B2B buyers must conduct their own independent and thorough due diligence before making any purchasing decisions. This includes contacting suppliers directly, verifying certifications, requesting samples, and seeking professional consultation. The risk of relying on any information in this guide is borne solely by the reader.
Strategic Sourcing Conclusion and Outlook for garden furniture manufacturer
What Are the Key Takeaways for Strategic Sourcing in Garden Furniture?
In conclusion, the strategic sourcing of garden furniture offers significant opportunities for international B2B buyers, especially those from Africa, South America, the Middle East, and Europe. Key takeaways include the importance of understanding regional market trends, consumer preferences, and sustainability practices. By leveraging these insights, businesses can make informed decisions that enhance their supply chain efficiency and product offerings.
How Can Strategic Sourcing Enhance Your Competitive Edge?
Investing in strategic sourcing not only optimizes costs but also fosters relationships with reliable manufacturers who prioritize quality and innovation. This approach is crucial for navigating the complexities of international trade and ensuring compliance with varying regulations across different markets. Buyers should focus on establishing partnerships with manufacturers who share their commitment to sustainability, as this is increasingly becoming a key differentiator in the market.
What’s Next for International B2B Buyers in the Garden Furniture Sector?
As we look ahead, the garden furniture industry is poised for growth, driven by rising demand for outdoor living spaces. Buyers are encouraged to remain proactive in their sourcing strategies, exploring new suppliers and innovations that cater to evolving consumer needs. By staying ahead of market trends and embracing sustainable practices, businesses can not only enhance their product offerings but also contribute positively to the global environment. Take the next step in your strategic sourcing journey—connect with trusted manufacturers today to capitalize on these emerging opportunities.