The Ultimate Guide to Grinding Machine Manufacturer (2025)
Introduction: Navigating the Global Market for grinding machine manufacturer
In the ever-evolving landscape of global manufacturing, sourcing high-quality grinding machines is a critical challenge for international B2B buyers. Whether you are based in Africa, South America, the Middle East, or Europe, understanding the nuances of selecting the right grinding machine manufacturer can significantly impact your operational efficiency and product quality. This guide delves into the multifaceted world of grinding machine manufacturers, offering insights into various types of machines, their applications, and the intricacies of supplier vetting.
Navigating this global market requires a keen understanding of not only the specifications and performance metrics of different grinding machines but also the cost structures associated with them. Buyers must consider factors such as after-sales support, warranty terms, and maintenance services, which can vary widely across regions and manufacturers. With this comprehensive resource, you will be empowered to make informed purchasing decisions that align with your specific business needs.
By outlining critical considerations and offering actionable strategies, this guide serves as a valuable tool for international B2B buyers. Whether you are looking to enhance your production capabilities in Mexico or seeking reliable suppliers in the UAE, our goal is to equip you with the knowledge to navigate the complexities of the grinding machine market effectively.
Understanding grinding machine manufacturer Types and Variations
Type Name | Key Distinguishing Features | Primary B2B Applications | Brief Pros & Cons for Buyers |
---|---|---|---|
Cylindrical Grinding Machines | Designed for precision grinding of cylindrical parts. | Automotive, aerospace, and manufacturing. | Pros: High accuracy, versatile. Cons: Higher cost, may require skilled operators. |
Surface Grinding Machines | Flat surface grinding capability with various bed sizes. | Tool manufacturing, metalworking, and mold making. | Pros: Excellent surface finish, adaptable. Cons: Limited to flat surfaces, slower for complex shapes. |
Centerless Grinding Machines | Utilizes a grinding wheel and regulating wheel for support. | Production of shafts, rods, and tubes. | Pros: High production rates, minimal setup time. Cons: Limited to specific part shapes, requires precise alignment. |
Tool and Cutter Grinding Machines | Specializes in sharpening and shaping cutting tools. | Tool manufacturing, maintenance workshops. | Pros: Essential for tool longevity, versatile. Cons: Can be complex, requires regular maintenance. |
Internal Grinding Machines | Focuses on grinding the internal surfaces of cylindrical parts. | Automotive, aerospace, and precision engineering. | Pros: High precision for internal diameters, compact design. Cons: More specialized, potentially higher costs. |
What Are Cylindrical Grinding Machines and Their B2B Relevance?
Cylindrical grinding machines are essential for achieving high precision in cylindrical parts, making them crucial in industries such as automotive and aerospace. These machines are capable of grinding both external and internal surfaces of cylindrical workpieces, ensuring tight tolerances and excellent surface finishes. When purchasing, buyers should consider factors like machine size, grinding wheel specifications, and the required level of automation to maximize productivity.
How Do Surface Grinding Machines Enhance Manufacturing Processes?
Surface grinding machines are designed to provide a smooth finish on flat surfaces, which is vital in tool manufacturing and mold making. These machines can accommodate various bed sizes, allowing flexibility for different workpieces. Buyers should assess the machine’s capabilities in terms of surface finish quality and production speed, as well as its compatibility with existing manufacturing processes to ensure seamless integration.
What Advantages Do Centerless Grinding Machines Offer for High-Volume Production?
Centerless grinding machines are favored for their ability to grind parts without the need for a fixed support, resulting in high production rates and minimal setup time. This makes them ideal for producing shafts, rods, and tubes in mass quantities. When considering a centerless grinder, buyers should evaluate the machine’s capacity, the range of part sizes it can handle, and its alignment precision to maintain production efficiency.
Why Are Tool and Cutter Grinding Machines Critical for Tool Maintenance?
Tool and cutter grinding machines are specialized for sharpening and shaping cutting tools, which is essential for maintaining tool longevity and performance. These machines are widely used in manufacturing and maintenance workshops. Buyers must consider the machine’s versatility, ease of use, and maintenance requirements to ensure that it meets the specific needs of their operations.
What Makes Internal Grinding Machines Unique for Precision Engineering?
Internal grinding machines are designed for grinding the internal surfaces of cylindrical parts, making them indispensable in industries that require high precision, such as aerospace and automotive. Their compact design allows for easy integration into production lines. When purchasing, buyers should focus on the machine’s precision capabilities, the range of internal diameters it can accommodate, and the overall cost-effectiveness of the investment.
Related Video: G7 5-Axis Grinding Machine for Aerospace Engine Components
Key Industrial Applications of grinding machine manufacturer
Industry/Sector | Specific Application of Grinding Machine Manufacturer | Value/Benefit for the Business | Key Sourcing Considerations for this Application |
---|---|---|---|
Automotive Manufacturing | Crankshaft and Cylinder Head Grinding | Enhances engine performance and durability | Precision requirements, machine size, and tooling compatibility |
Aerospace | Turbine Blade Grinding | Improves efficiency and reduces fuel consumption | Compliance with aerospace standards, surface finish quality |
Metal Fabrication | Surface Grinding for Flat Parts | Ensures uniformity and reduces finishing time | Material compatibility, machine versatility, and automation options |
Tool and Die Making | Tool Grinding for High-Precision Tools | Increases tool life and reduces downtime | Customization needs, grinding wheel specifications, and delivery times |
Medical Device Manufacturing | Grinding for Implants and Surgical Instruments | Ensures high precision and biocompatibility | Regulatory compliance, material sourcing, and quality assurance |
How Are Grinding Machines Used in Automotive Manufacturing?
In the automotive sector, grinding machines are crucial for processing crankshafts and cylinder heads. These components require high precision to ensure optimal engine performance and durability. Grinding minimizes surface irregularities, enabling better fit and function. International buyers, particularly from regions like Africa and Europe, must consider the machine’s precision capabilities, size, and compatibility with various tooling options to meet their production needs effectively.
What Role Do Grinding Machines Play in Aerospace Applications?
Aerospace manufacturers utilize grinding machines to achieve the intricate geometries required for turbine blades. The grinding process enhances efficiency by reducing drag, which is vital for fuel consumption. Buyers from South America and the Middle East should prioritize machines that comply with stringent aerospace standards, ensuring surface finish quality and precision. Additionally, sourcing machines with advanced features for automation can significantly improve productivity in this highly competitive sector.
Why Is Surface Grinding Important in Metal Fabrication?
In metal fabrication, surface grinding is employed to achieve flatness and uniformity in parts that require a smooth finish. This application is essential for reducing finishing time and improving overall product quality. For international B2B buyers, especially in Europe, understanding the material compatibility and versatility of grinding machines is crucial. They should also consider the availability of automation options that can streamline production processes and enhance efficiency.
How Do Grinding Machines Benefit Tool and Die Making?
Grinding machines are indispensable in tool and die making, where high-precision tools are critical for manufacturing processes. By grinding tools to exact specifications, manufacturers can extend tool life and minimize downtime due to tool replacement. Buyers should evaluate the customization capabilities of grinding machines, ensuring they meet specific grinding wheel specifications and delivery timelines to remain competitive in the market.
What Is the Importance of Grinding in Medical Device Manufacturing?
In the medical device sector, grinding machines are utilized to produce implants and surgical instruments with high precision. This precision is vital for ensuring the biocompatibility and functionality of medical devices. Buyers from regions like Africa and the Middle East must focus on sourcing machines that comply with regulatory standards and ensure quality assurance. Understanding the material sourcing process is also essential to maintain the integrity of medical products.
3 Common User Pain Points for ‘grinding machine manufacturer’ & Their Solutions
Scenario 1: Inefficient Production Due to Subpar Machinery
The Problem:
Many B2B buyers in the manufacturing sector face the challenge of outdated or inadequate grinding machines that hinder production efficiency. This can lead to increased operational costs, longer lead times, and compromised product quality. For instance, a buyer sourcing a grinding machine for precision parts may discover that their current equipment is unable to meet the required tolerances, resulting in frequent adjustments and rework. This not only impacts delivery schedules but also strains relationships with clients who expect timely and high-quality outputs.
The Solution:
To overcome this issue, buyers should conduct thorough market research to identify reputable grinding machine manufacturers known for high precision and reliability. It’s crucial to specify the exact requirements, such as material types, tolerances, and production volumes, to ensure the selected machine aligns with operational needs. Engaging with manufacturers directly can provide insights into the latest technologies available, such as CNC grinding, which can significantly enhance productivity. Additionally, requesting demonstrations or trial periods can help buyers assess the machine’s performance before making a substantial investment.
Scenario 2: High Maintenance Costs and Downtime
The Problem:
Another common pain point for B2B buyers is the high cost of maintenance and unexpected downtime associated with grinding machines. For companies in regions like Africa or South America, where parts and technical support may not be readily available, the implications of a machine breakdown can be dire. A buyer may find that the grinding machines they invested in require frequent repairs, leading to increased operational costs and lost production time. This not only affects profitability but can also damage a company’s reputation for reliability.
The Solution:
To mitigate these challenges, buyers should prioritize purchasing machines that come with robust after-sales support and warranty options. It is advisable to look for manufacturers that offer comprehensive maintenance packages, including regular check-ups and training for in-house technicians. Buyers should also consider investing in machines designed for ease of maintenance, which can drastically reduce downtime. Establishing a good relationship with the manufacturer can facilitate quicker access to spare parts and technical assistance, ensuring that any issues are resolved promptly.
Scenario 3: Difficulty in Finding the Right Grinding Machine for Specific Applications
The Problem:
Many international B2B buyers struggle with selecting the right grinding machine that meets specific application needs, such as cylindrical, surface, or tool grinding. This challenge is particularly pronounced in diverse markets like the Middle East and Europe, where varied industrial standards and applications can make it difficult to find a one-size-fits-all solution. For example, a buyer may need a grinding machine capable of processing multiple materials, but their existing options are limited or do not perform well across different substrates.
The Solution:
To address this issue, buyers should engage in detailed consultations with manufacturers to discuss their unique operational requirements. It’s essential to clarify the types of materials being processed and the specific grinding techniques required. Manufacturers often provide tailored solutions or can guide buyers toward modular machines that can be adapted for various applications. Additionally, buyers should consider visiting trade shows or exhibitions to see a range of machines in action and consult with industry experts. This hands-on approach can ensure that they make informed decisions that align with their specific needs, ultimately enhancing their operational capabilities.
Strategic Material Selection Guide for grinding machine manufacturer
What Are the Key Materials Used in Grinding Machine Manufacturing?
When selecting materials for grinding machines, manufacturers must consider various factors that impact performance, durability, and cost. Below are analyses of four common materials used in the grinding machine industry, focusing on their properties, advantages and disadvantages, and specific considerations for international B2B buyers.
How Does Steel Perform as a Material for Grinding Machines?
Key Properties: Steel is known for its high tensile strength and durability, making it suitable for high-pressure applications. It can withstand significant wear and tear, which is essential in grinding operations.
Pros & Cons: The primary advantage of steel is its robustness and ability to handle heavy loads. However, it is susceptible to corrosion if not properly treated, which can lead to increased maintenance costs. Additionally, the manufacturing complexity can vary depending on the type of steel used (e.g., carbon steel vs. stainless steel).
Impact on Application: Steel is compatible with various grinding media, including ceramic and diamond abrasives. Its strength allows for efficient grinding of hard materials, making it a preferred choice in heavy-duty applications.
Considerations for International Buyers: Compliance with international standards such as ASTM and DIN is crucial. Buyers from regions like Africa and the Middle East may need to consider local regulations regarding material sourcing and environmental impact.
What Role Does Cast Iron Play in Grinding Machine Manufacturing?
Key Properties: Cast iron is characterized by its excellent wear resistance and vibration-damping properties. It can handle high temperatures without deforming, which is beneficial in grinding applications.
Pros & Cons: The main advantage of cast iron is its ability to absorb vibrations, leading to smoother operation and extended tool life. However, it is brittle and can crack under excessive stress, limiting its use in certain applications. Additionally, it is generally more expensive than steel.
Impact on Application: Cast iron is particularly effective for grinding softer materials and is often used in the manufacturing of machine bases and frames due to its stability.
Considerations for International Buyers: Buyers should ensure that the cast iron meets specific standards for hardness and tensile strength, especially in regions like Europe where strict quality controls are in place.
Why Is Aluminum a Popular Choice in Grinding Machines?
Key Properties: Aluminum is lightweight yet strong, making it an excellent choice for applications requiring mobility. It also has good thermal conductivity, which helps dissipate heat during grinding.
Pros & Cons: The lightweight nature of aluminum allows for easier handling and reduced energy costs in operation. However, it is less durable than steel or cast iron and can wear out more quickly, leading to higher replacement costs over time.
Impact on Application: Aluminum is suitable for grinding softer materials and is often used in the manufacturing of components that require precision and lower weight.
Considerations for International Buyers: Buyers should be aware of the alloy specifications, as different aluminum grades have varying properties. Compliance with standards like JIS is essential for ensuring quality.
What Are the Advantages of Composite Materials in Grinding Machines?
Key Properties: Composite materials combine different substances to enhance performance characteristics such as strength, weight, and resistance to wear.
Pros & Cons: The primary advantage of composites is their tailored properties, allowing manufacturers to optimize performance for specific applications. However, they can be more expensive to produce and may require specialized manufacturing processes.
Impact on Application: Composites are increasingly used in advanced grinding machines where weight reduction and enhanced performance are critical, such as in aerospace and automotive industries.
Considerations for International Buyers: Buyers must consider the availability of composite materials in their region and ensure compliance with relevant standards, as these materials can vary significantly in quality.
Summary Table of Material Selection for Grinding Machines
Material | Typical Use Case for grinding machine manufacturer | Key Advantage | Key Disadvantage/Limitation | Relative Cost (Low/Med/High) |
---|---|---|---|---|
Steel | Heavy-duty grinding applications | High tensile strength | Susceptible to corrosion | Medium |
Cast Iron | Machine bases and frames | Excellent vibration damping | Brittle and can crack | High |
Aluminum | Precision components for lighter applications | Lightweight and good thermal conductivity | Less durable than steel | Medium |
Composite | Advanced applications in aerospace and automotive | Tailored properties for specific needs | Higher production costs | High |
This strategic material selection guide provides valuable insights for international B2B buyers, enabling them to make informed decisions based on performance, cost, and compliance with industry standards.
In-depth Look: Manufacturing Processes and Quality Assurance for grinding machine manufacturer
What Are the Main Stages of Manufacturing Grinding Machines?
When evaluating grinding machine manufacturers, understanding their manufacturing processes is crucial. The typical stages involved in the manufacturing of grinding machines include:
-
Material Preparation: The process begins with the selection of high-quality raw materials, often steel or specialized alloys. Manufacturers must ensure that the material has the necessary properties, such as hardness and wear resistance, which are essential for grinding applications. Advanced techniques like chemical composition analysis and mechanical property testing are employed to verify material quality.
-
Forming: In this stage, the raw materials are shaped into components using various techniques. Common methods include casting, forging, and machining. For instance, precision machining is critical for components like spindles and tables to ensure that they meet strict tolerances. This phase may involve CNC (Computer Numerical Control) machines, which enhance accuracy and efficiency.
-
Assembly: Once the components are formed, they are assembled into the final grinding machine. This process often requires skilled labor to ensure that parts fit together precisely. Manufacturers may use jigs and fixtures to maintain alignment during assembly, minimizing the risk of defects.
-
Finishing: The final stage involves surface treatments such as grinding, polishing, and coating to enhance durability and performance. Techniques like heat treatment may also be applied to improve the hardness of critical components. The finishing process is vital for ensuring that the machine performs optimally and has a long service life.
How Do Grinding Machine Manufacturers Ensure Quality Control?
Quality assurance is a fundamental aspect of the grinding machine manufacturing process. To maintain high standards, manufacturers often adhere to various international and industry-specific standards, including:
-
ISO 9001: This widely recognized standard focuses on quality management systems. Compliance with ISO 9001 ensures that manufacturers consistently meet customer and regulatory requirements.
-
CE Marking: For European buyers, CE marking signifies that the product meets EU safety, health, and environmental protection standards. This is particularly important for machines sold in European markets.
-
API Standards: For manufacturers serving the oil and gas industry, compliance with American Petroleum Institute (API) standards is crucial. These standards ensure that machines can operate safely and efficiently in demanding environments.
What Are the Key Quality Control Checkpoints in Grinding Machine Manufacturing?
Quality control (QC) involves several checkpoints throughout the manufacturing process:
-
Incoming Quality Control (IQC): This initial checkpoint verifies the quality of raw materials before production begins. Materials are inspected for compliance with specified standards, and any non-conforming materials are rejected.
-
In-Process Quality Control (IPQC): Throughout the manufacturing process, various inspections are performed to ensure that components are being produced according to specifications. Techniques such as statistical process control (SPC) may be employed to monitor production quality in real-time.
-
Final Quality Control (FQC): After assembly, the complete grinding machine undergoes rigorous testing and inspection. This includes functional tests, performance evaluations, and safety assessments. Manufacturers may also use automated testing equipment to ensure precision and accuracy.
What Testing Methods Are Commonly Used in Grinding Machine Manufacturing?
Testing methods play a critical role in ensuring that grinding machines meet performance and safety standards. Common testing techniques include:
-
Dimensional Inspection: This method involves measuring components to ensure they meet specified dimensions and tolerances. Tools such as calipers, micrometers, and coordinate measuring machines (CMM) are commonly used.
-
Functional Testing: This testing evaluates the machine’s operational capabilities. It includes running the machine under various load conditions to assess performance and reliability.
-
Non-Destructive Testing (NDT): Techniques such as ultrasonic testing, magnetic particle inspection, and dye penetrant testing are used to detect internal defects without damaging the components.
How Can B2B Buyers Verify Supplier Quality Control?
For international B2B buyers, particularly from regions like Africa, South America, the Middle East, and Europe, verifying a supplier’s quality control measures is essential. Here are actionable steps buyers can take:
-
Conduct Supplier Audits: Regular audits of manufacturing facilities can provide insights into a supplier’s quality control processes. Buyers should look for adherence to relevant standards and the presence of quality management systems.
-
Request Quality Assurance Documentation: Suppliers should provide detailed documentation, including quality manuals, inspection reports, and certificates of compliance. This information helps buyers assess the supplier’s commitment to quality.
-
Engage Third-Party Inspection Services: Utilizing independent inspection agencies can provide an unbiased evaluation of the manufacturing processes and quality control measures. These agencies can conduct inspections at various stages of production.
What Are the Quality Control Nuances for International B2B Buyers?
Understanding the nuances of quality control in different regions is vital for international B2B buyers. Buyers should consider:
-
Cultural Differences: Attitudes towards quality and standards may vary across cultures. Buyers should be aware of these differences when negotiating and assessing supplier capabilities.
-
Regulatory Compliance: Each region may have specific regulations and compliance requirements that suppliers must meet. Buyers should ensure that their suppliers are knowledgeable about local regulations.
-
Communication and Language Barriers: Effective communication is key to successful partnerships. Buyers should establish clear lines of communication and consider language differences that may impact quality assurance discussions.
By understanding the manufacturing processes and quality assurance practices of grinding machine manufacturers, B2B buyers can make informed decisions that align with their operational needs and quality standards.
Practical Sourcing Guide: A Step-by-Step Checklist for ‘grinding machine manufacturer’
In the dynamic landscape of international B2B procurement, sourcing a reliable grinding machine manufacturer is crucial for operational efficiency and product quality. This practical checklist will guide you through the essential steps to ensure a successful procurement process, particularly tailored for buyers from Africa, South America, the Middle East, and Europe.
Step 1: Define Your Technical Specifications
Clearly articulating your technical requirements is the foundation of a successful procurement process. Determine the type of grinding machine you need, such as cylindrical, surface, or tool grinders, and specify any unique features or capacities required for your operations. This clarity will enable suppliers to provide accurate quotes and relevant options.
Step 2: Conduct Market Research for Suppliers
Research potential suppliers in your target regions, focusing on manufacturers with a solid reputation and experience in your industry. Utilize online platforms, trade directories, and industry-specific forums to gather a list of manufacturers. Pay attention to their market presence and customer reviews, which can provide insight into their reliability and service quality.
Step 3: Evaluate Potential Suppliers
Before making a commitment, it is essential to thoroughly vet potential suppliers. Request detailed company profiles, including their history, production capabilities, and case studies relevant to your industry. Look for testimonials or references from businesses similar to yours to gauge their reliability and product performance.
- Key Considerations:
- Check the supplier’s experience with international shipping and compliance with local regulations.
- Assess their customer service responsiveness during the inquiry stage.
Step 4: Verify Supplier Certifications and Compliance
Ensure that the suppliers you are considering possess the necessary certifications and comply with international quality standards such as ISO 9001. These certifications are critical indicators of a manufacturer’s commitment to quality and safety. Non-compliance can lead to costly delays and operational disruptions.
Step 5: Request Samples or Demonstrations
Before finalizing your order, ask for samples or arrange for a demonstration of the grinding machine. This step allows you to assess the machine’s performance and suitability for your specific applications. It also provides an opportunity to evaluate the manufacturer’s customer service and support during the process.
Step 6: Negotiate Terms and Conditions
Once you have selected a potential supplier, negotiate the terms of purchase, including pricing, payment terms, delivery schedules, and warranty conditions. Clear agreements can prevent misunderstandings and ensure that both parties have aligned expectations. Pay particular attention to after-sales support and maintenance services offered.
Step 7: Establish a Communication Plan
Effective communication is key to a successful procurement process. Establish a clear line of communication with your chosen supplier to facilitate updates on production status, shipping schedules, and any potential issues that may arise. Regular check-ins can help maintain a strong partnership and ensure that your needs are met throughout the procurement process.
By following these steps, you can enhance your sourcing strategy and secure a reliable grinding machine manufacturer that meets your operational needs and standards.
Comprehensive Cost and Pricing Analysis for grinding machine manufacturer Sourcing
What Are the Key Cost Components in Grinding Machine Manufacturing?
When considering the sourcing of grinding machines, international B2B buyers must be aware of several critical cost components that contribute to the overall pricing. These include:
-
Materials: The type and quality of materials used in manufacturing grinding machines significantly impact costs. High-grade steel and other durable materials often lead to better performance and longevity, albeit at a higher initial price.
-
Labor: Labor costs vary widely by region. In countries with lower wages, such as some regions in Africa and South America, the labor cost may be less, but this can also affect the skill level and quality of workmanship.
-
Manufacturing Overhead: This encompasses the costs associated with running the manufacturing facility, including utilities, rent, and administrative expenses. Efficient operations can lead to lower overhead costs, which can be beneficial for buyers seeking competitive pricing.
-
Tooling: Specialized tooling and fixtures necessary for the production of grinding machines can be a significant expense. Buyers should inquire about these costs, especially if they require customized machines.
-
Quality Control (QC): Rigorous QC processes ensure that the machines meet industry standards and performance specifications. While these processes add to costs, they are essential for ensuring reliability and safety.
-
Logistics: Shipping and handling costs can vary based on the machine’s size and weight, as well as the distance to the buyer’s location. Understanding logistics costs is crucial, especially for international transactions.
-
Margin: Manufacturers typically include a profit margin in their pricing, which can vary based on market conditions, competition, and the perceived value of their machines.
How Do Price Influencers Affect Grinding Machine Costs?
Several factors can influence the final pricing of grinding machines:
-
Volume and Minimum Order Quantity (MOQ): Ordering in bulk often leads to discounts. Buyers should assess their needs and negotiate MOQs that can yield cost savings.
-
Specifications and Customization: Customized machines tailored to specific applications usually come at a premium. Buyers should clearly define their specifications to avoid unexpected costs.
-
Materials and Quality Certifications: Machines built with premium materials and certified for quality (such as ISO certifications) may carry higher prices. Buyers need to evaluate the long-term benefits against the initial costs.
-
Supplier Factors: The reputation and reliability of the supplier can impact pricing. Established manufacturers with a proven track record may charge more but offer better service and support.
-
Incoterms: Understanding Incoterms (International Commercial Terms) is vital for international buyers. These terms dictate responsibilities for shipping, insurance, and tariffs, which can significantly affect the total cost.
What Are Some Effective Buyer Tips for Negotiating Grinding Machine Prices?
B2B buyers should employ strategic approaches when negotiating prices for grinding machines:
-
Negotiation Skills: Effective negotiation can lead to favorable pricing. Prepare by understanding the supplier’s cost structure and market conditions.
-
Cost-Efficiency Considerations: Evaluate the Total Cost of Ownership (TCO) rather than just the upfront price. Consider maintenance, operational efficiency, and potential downtime costs.
-
Pricing Nuances for International Buyers: Be aware of exchange rates, tariffs, and local regulations that can impact the final cost. Engaging with local experts can provide insights into these factors.
-
Long-Term Relationships: Building a long-term relationship with suppliers can lead to better pricing and service. Loyal customers often receive favorable terms and priority support.
Disclaimer on Indicative Prices
Prices for grinding machines can vary widely based on the aforementioned factors. It is essential for buyers to conduct thorough market research and obtain multiple quotes to ensure they are making informed purchasing decisions. Always request detailed pricing breakdowns to better understand the costs involved.
Alternatives Analysis: Comparing grinding machine manufacturer With Other Solutions
Understanding Alternatives to Grinding Machine Manufacturers
In the landscape of industrial manufacturing, particularly in sectors requiring precision machining, the choice of equipment is critical. While grinding machines are a staple for achieving fine finishes and tight tolerances, there are alternative solutions that may serve the same purpose depending on specific operational needs. This analysis will compare the traditional grinding machine manufacturer with two viable alternatives: CNC Machining and Honing Machines.
Comparison Table
Comparison Aspect | Grinding Machine Manufacturer | CNC Machining | Honing Machines |
---|---|---|---|
Performance | High precision, suited for hard materials | Extremely versatile, high speed, and precision | Excellent for achieving tight tolerances and surface finishes |
Cost | Moderate to high initial investment | Higher initial investment but cost-effective for large runs | Moderate cost with less investment than CNC but more than grinding |
Ease of Implementation | Requires skilled operators and setup | Requires programming skills, setup time can vary | Generally easier to set up and operate |
Maintenance | Regular maintenance needed for optimal performance | Requires specialized knowledge for maintenance | Less frequent maintenance, easier to service |
Best Use Case | Ideal for high precision parts in automotive and aerospace | Best for complex geometries and high-volume production | Best for finishing operations and improving surface quality |
Detailed Breakdown of Alternatives
How Does CNC Machining Compare to Grinding Machines?
CNC (Computer Numerical Control) machining represents a significant technological advancement in manufacturing. This method uses computer-controlled machinery to create precise parts from a variety of materials. One of the key advantages of CNC machining is its versatility; it can be programmed to produce complex geometries with high precision. However, the initial investment can be higher than traditional grinding machines. CNC machining is particularly effective for large-scale production runs, where the setup time can be amortized over many parts, making it cost-effective in the long run. On the downside, it requires skilled operators who understand programming and machine operation, which could be a barrier for some manufacturers.
What Are the Benefits of Honing Machines as an Alternative?
Honing machines are designed specifically for finishing and achieving high tolerances on cylindrical parts. They excel at improving surface finishes and dimensional accuracy, making them suitable for applications in the automotive and aerospace industries. The ease of operation is a notable advantage, as honing machines generally require less skill than CNC or grinding machines. Maintenance is also less frequent, which can reduce downtime. However, honing is primarily a finishing process and may not be suitable for all applications where substantial material removal is required. It is best used as a secondary operation after other machining processes.
How Can B2B Buyers Choose the Right Solution?
When selecting between grinding machines and their alternatives, B2B buyers must consider several factors tailored to their specific needs. Assess the types of materials being processed, the required tolerances, and the complexity of the parts. Additionally, evaluate the total cost of ownership, including initial investment, maintenance, and operational costs. Understanding the production volume and the skill level of available personnel can also influence the decision. By carefully analyzing these aspects, businesses can select the most appropriate solution that aligns with their operational goals and budget constraints. This approach ensures that the investment in machinery translates into enhanced productivity and profitability.
Essential Technical Properties and Trade Terminology for grinding machine manufacturer
What Are the Key Technical Properties of Grinding Machines?
When evaluating grinding machines, international B2B buyers should focus on several critical specifications that impact performance, efficiency, and longevity. Here are some essential technical properties to consider:
-
Material Grade
The material grade of the grinding machine components, such as the grinding wheel and frame, is crucial for durability and performance. High-grade materials like hardened steel or high-carbon steel can withstand wear and tear, leading to longer machine life and reduced maintenance costs. For buyers from Africa and South America, where environmental conditions may vary, selecting machines made from robust materials is particularly important. -
Tolerance Levels
Tolerance refers to the permissible limit of variation in a physical dimension. Grinding machines typically operate within very tight tolerances (often within ±0.01 mm). Understanding these tolerances is essential for manufacturers in sectors such as automotive or aerospace, where precision is critical. Buyers should ensure that the grinding machine specifications align with their production needs. -
Power and RPM (Revolutions Per Minute)
The power rating and RPM of a grinding machine determine its efficiency and capacity to handle different materials. Higher RPM can lead to faster processing times but may require better cooling systems to prevent overheating. Buyers should assess the power requirements based on their production volume and material hardness. -
Grinding Wheel Composition
The composition of the grinding wheel, including the type of abrasive material (e.g., aluminum oxide, silicon carbide), directly affects the grinding process’s efficiency and finish quality. Different applications may require specific wheel compositions, so buyers should ensure compatibility with their intended use. -
Cooling Systems
Effective cooling systems are essential for maintaining optimal operational temperatures during grinding. Machines equipped with advanced cooling mechanisms can significantly reduce thermal distortion, enhancing precision. Buyers should consider whether a machine’s cooling system meets their operational needs, especially in high-volume production environments. -
Automation Features
Modern grinding machines often come with automation features such as CNC (Computer Numerical Control) capabilities. These features can enhance productivity and reduce labor costs. Buyers should evaluate the level of automation they require based on their production scale and operational efficiency goals.
What Are Common Trade Terms in the Grinding Machine Industry?
Understanding industry jargon is vital for effective communication and negotiation in the grinding machine market. Here are several essential terms that B2B buyers should familiarize themselves with:
-
OEM (Original Equipment Manufacturer)
An OEM is a company that produces parts or equipment that may be marketed by another manufacturer. When sourcing grinding machines, understanding if a supplier is an OEM can assure buyers of the quality and reliability of the machinery, as OEMs typically adhere to stringent production standards. -
MOQ (Minimum Order Quantity)
MOQ refers to the smallest quantity of goods that a supplier is willing to sell. For grinding machines, this can affect procurement strategies, especially for smaller manufacturers. Buyers should negotiate MOQs to ensure they can manage inventory efficiently without overcommitting resources. -
RFQ (Request for Quotation)
An RFQ is a document that a buyer sends to suppliers to request pricing and terms for specific products. Including detailed specifications in the RFQ can help ensure that the quotes received are accurate and relevant to the buyer’s needs. -
Incoterms (International Commercial Terms)
Incoterms are a series of pre-defined commercial terms published by the International Chamber of Commerce (ICC). These terms clarify the responsibilities of buyers and sellers in international transactions, including shipping costs, insurance, and risk management. Familiarity with Incoterms is crucial for buyers from different regions, as it helps avoid misunderstandings during the purchasing process. -
Lead Time
Lead time is the period from placing an order to receiving the product. Understanding lead times is critical for production planning, especially in industries where time-to-market is essential. Buyers should inquire about lead times when negotiating contracts to ensure they align with their project timelines. -
Warranty and Service Agreement
A warranty is a guarantee provided by the manufacturer regarding the machine’s performance and durability over a specified period. A service agreement outlines the terms of ongoing maintenance and support. Buyers should carefully review these documents to ensure they receive adequate protection and support for their investment.
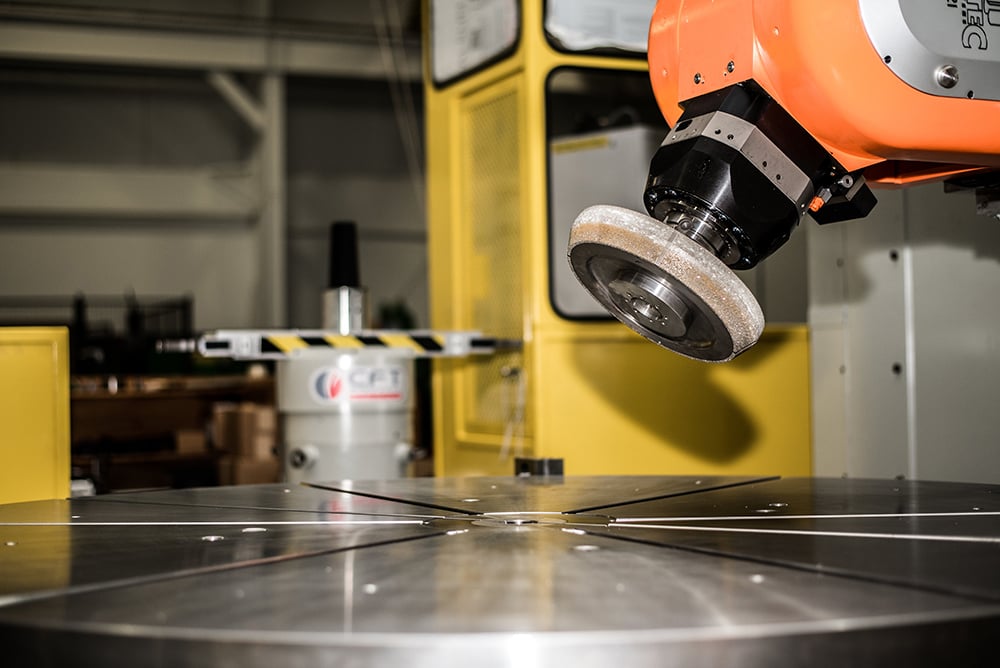
A stock image related to grinding machine manufacturer.
By understanding these technical properties and trade terms, B2B buyers can make informed decisions when sourcing grinding machines, ensuring they choose equipment that aligns with their operational needs and market demands.
Navigating Market Dynamics and Sourcing Trends in the grinding machine manufacturer Sector
What Are the Current Market Dynamics in the Grinding Machine Manufacturing Sector?
The grinding machine manufacturing sector is witnessing significant shifts driven by technological advancements, increasing demand for precision engineering, and the push for automation. Global drivers such as Industry 4.0 and the Internet of Things (IoT) are influencing sourcing trends, allowing manufacturers to integrate smart technologies into grinding machines. This integration enhances operational efficiency, reduces downtime, and improves product quality, making it a compelling proposition for international B2B buyers, especially in regions like Africa, South America, the Middle East, and Europe.
Emerging trends include the adoption of CNC (Computer Numerical Control) machines, which offer higher precision and reduced labor costs. Additionally, there is a growing trend toward modular and adaptable machinery that can be customized to meet specific production needs, thereby enhancing flexibility. As buyers from diverse markets seek to optimize production processes, understanding these dynamics becomes crucial for making informed purchasing decisions.
Moreover, the global market is increasingly influenced by the demand for sustainable practices. B2B buyers are now more inclined to partner with manufacturers who prioritize eco-friendly technologies and materials in their grinding machines. This shift not only meets regulatory requirements but also aligns with the corporate social responsibility goals of many organizations.
How Is Sustainability Shaping the Grinding Machine Manufacturing Sector?
Sustainability is becoming a pivotal factor in the grinding machine manufacturing industry. The environmental impact of manufacturing processes and the lifecycle of machines are under scrutiny. B2B buyers are increasingly aware of the need for ethical sourcing and the importance of minimizing waste and energy consumption in production. This consciousness is prompting manufacturers to innovate in terms of design and materials.
Buyers should look for manufacturers that hold certifications such as ISO 14001, which indicates effective environmental management systems. Additionally, the use of ‘green’ materials—those that are recyclable or have a reduced environmental footprint—can enhance the sustainability profile of grinding machines. This not only helps in reducing operational costs but also resonates with the growing consumer demand for environmentally responsible products.
Moreover, ethical supply chains are becoming essential. Companies that prioritize transparency in their sourcing processes and ensure fair labor practices are gaining favor among international B2B buyers. This trend is particularly significant in markets like the Middle East and Africa, where consumers are increasingly advocating for ethical business practices.
What Is the Evolution of Grinding Machine Manufacturing?
The grinding machine manufacturing sector has evolved dramatically over the decades. Initially, grinding machines were simple, manually operated tools primarily used in workshops. However, advancements in technology during the late 20th century led to the introduction of CNC machines, revolutionizing the industry. These machines allowed for higher precision and efficiency, making them indispensable in sectors such as automotive and aerospace.
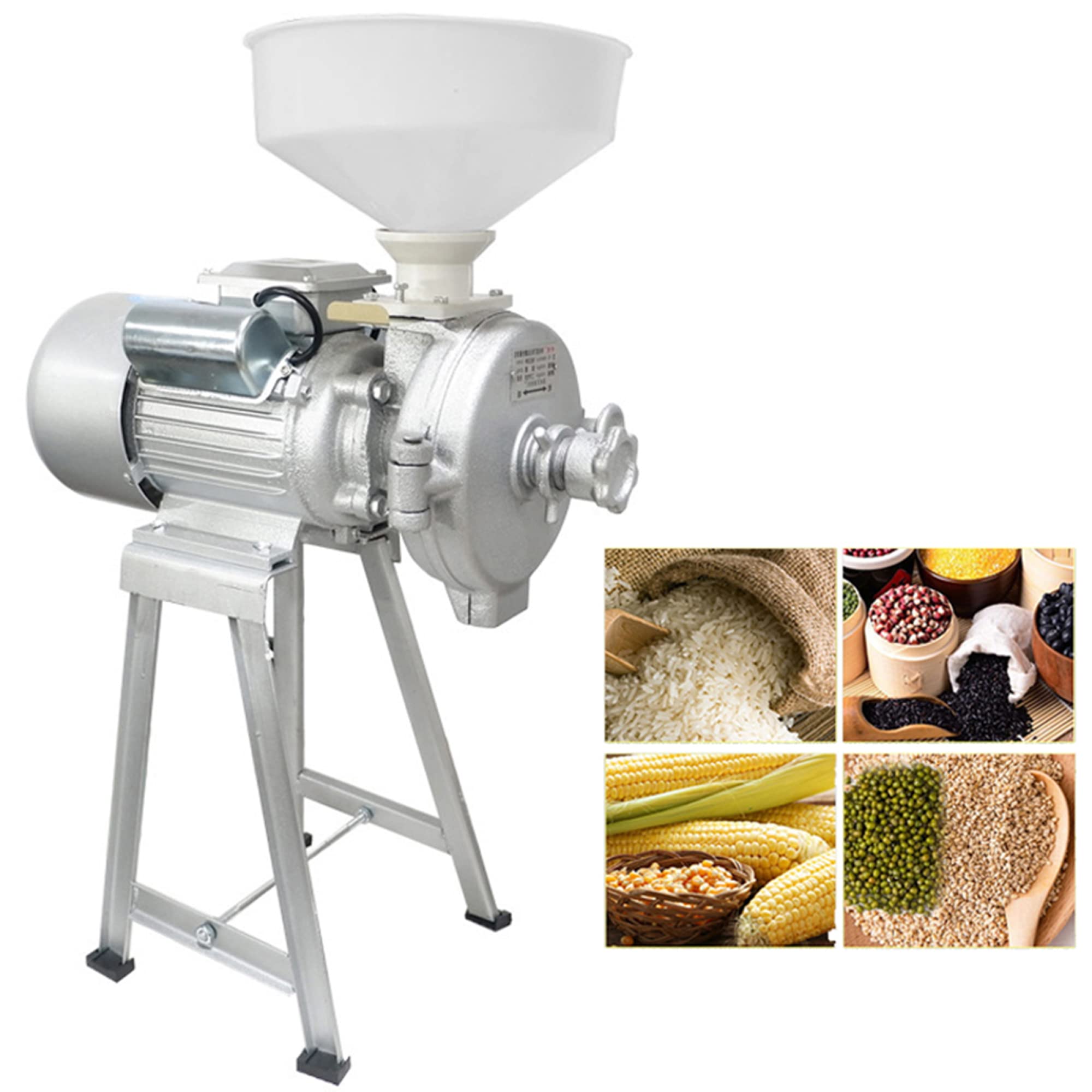
A stock image related to grinding machine manufacturer.
The turn of the 21st century brought about further innovations, including the integration of automation and smart technologies. Today, grinding machines are equipped with sensors and IoT capabilities, enabling real-time monitoring and data collection. This evolution reflects the industry’s response to the increasing demand for higher productivity and precision, positioning it as a crucial player in modern manufacturing ecosystems.
Understanding this historical context helps international B2B buyers appreciate the technological advancements and current trends in the grinding machine sector, enabling better decision-making and strategic sourcing in their procurement processes.
Frequently Asked Questions (FAQs) for B2B Buyers of grinding machine manufacturer
-
How do I ensure the quality of grinding machines from manufacturers?
To ensure quality when sourcing grinding machines, start by conducting thorough research on potential manufacturers. Look for certifications such as ISO 9001, which indicates adherence to quality management standards. Request samples or visit manufacturing facilities if possible. Additionally, engage in discussions with current customers or read reviews to gauge reliability. Inspecting the machines upon delivery for defects or inconsistencies can also help ensure that you receive a high-quality product. -
What is the best grinding machine for industrial applications?
The best grinding machine for industrial applications largely depends on your specific needs, including the type of material being processed and the desired finish. For high-volume production, CNC cylindrical grinders are recommended for their precision and efficiency. If you need versatility, consider surface grinders that can handle various shapes and sizes. Always evaluate the machine’s specifications, such as power, speed, and available attachments, to ensure it meets your operational requirements. -
How can I vet grinding machine suppliers effectively?
Vetting suppliers involves several steps: first, check their reputation within the industry by seeking referrals or reading online reviews. Verify their certifications and compliance with international standards. Assess their financial stability to ensure they can fulfill large orders. Additionally, consider their experience in shipping to your region, as local regulations and logistics can impact delivery. Finally, establish clear communication to gauge their responsiveness and willingness to address your concerns. -
What are the typical minimum order quantities (MOQs) for grinding machines?
Minimum order quantities (MOQs) for grinding machines can vary significantly by manufacturer and machine type. Generally, MOQs range from one machine for specialized models to multiple units for standard models. It’s crucial to discuss MOQs upfront to avoid misunderstandings. If you require a smaller quantity, some manufacturers may offer flexibility, especially if you are willing to pay a premium. Always clarify any potential additional costs associated with lower MOQs. -
What payment terms should I expect when purchasing grinding machines internationally?
Payment terms can differ based on the manufacturer and the nature of the transaction. Common terms include a deposit upon order placement, followed by the balance before shipment or upon delivery. It’s advisable to consider secure payment methods like letters of credit or escrow services, particularly for large transactions. Always negotiate terms that protect your interests, especially in international dealings where risks can be higher. -
How do I handle logistics when importing grinding machines?
Handling logistics for importing grinding machines involves several critical steps. First, select a reliable freight forwarder experienced in handling heavy machinery. Ensure all shipping documents, including invoices and customs declarations, are accurately prepared to avoid delays. Understand the shipping regulations and tariffs in your country, as these can significantly affect costs and delivery times. Finally, arrange for local transportation upon arrival to ensure a smooth transition to your facility. -
Can grinding machines be customized for specific applications?
Yes, many manufacturers offer customization options for grinding machines to better suit specific applications. Customizations may include modifications to machine size, grinding wheels, or control systems. When discussing your needs with a manufacturer, provide detailed specifications and examples of your application requirements. This will help them understand your needs and offer solutions that enhance machine performance and efficiency. -
What quality assurance measures should I expect from grinding machine manufacturers?
Reputable grinding machine manufacturers typically implement stringent quality assurance (QA) measures throughout their production process. Look for manufacturers who conduct regular inspections and testing of their machines at various stages of production. They should provide documentation of quality checks, including performance tests and compliance certifications. Additionally, inquire about their warranty policies, as a robust warranty can be an indicator of confidence in their product quality.
Important Disclaimer & Terms of Use
⚠️ Important Disclaimer
The information provided in this guide, including content regarding manufacturers, technical specifications, and market analysis, is for informational and educational purposes only. It does not constitute professional procurement advice, financial advice, or legal advice.
While we have made every effort to ensure the accuracy and timeliness of the information, we are not responsible for any errors, omissions, or outdated information. Market conditions, company details, and technical standards are subject to change.
B2B buyers must conduct their own independent and thorough due diligence before making any purchasing decisions. This includes contacting suppliers directly, verifying certifications, requesting samples, and seeking professional consultation. The risk of relying on any information in this guide is borne solely by the reader.
Strategic Sourcing Conclusion and Outlook for grinding machine manufacturer
In the rapidly evolving landscape of grinding machine manufacturing, strategic sourcing emerges as a critical factor for international B2B buyers. By aligning with reputable manufacturers, buyers can ensure they receive high-quality, precision-engineered machinery tailored to their specific needs. Emphasizing supplier relationships, understanding regional market dynamics, and leveraging technological advancements are essential for optimizing procurement processes.
For buyers in Africa, South America, the Middle East, and Europe, it is vital to prioritize transparency and sustainability in sourcing practices. Engaging with suppliers who adhere to these principles not only fosters trust but also enhances brand reputation and customer loyalty. Additionally, investing in training and support from suppliers can significantly improve operational efficiency and reduce downtime.
Looking forward, the grinding machine industry is poised for innovation. As manufacturers adopt Industry 4.0 technologies, including automation and data analytics, buyers must remain agile and open to adapting their sourcing strategies. Embrace these changes and position your business for success by leveraging strategic sourcing to unlock new opportunities in the global market.