The Ultimate Guide to Heat Exchanger Manufacturer (2025)
Introduction: Navigating the Global Market for heat exchanger manufacturer
In today’s global market, sourcing reliable heat exchanger manufacturers presents a significant challenge for international B2B buyers, particularly those operating in diverse regions such as Africa, South America, the Middle East, and Europe. With varying industrial standards, regulatory requirements, and logistical complexities, identifying the right supplier can be daunting. This guide serves as a comprehensive resource, covering essential aspects of heat exchanger procurement, including types, applications, supplier vetting processes, and cost considerations.
By delving into the different types of heat exchangers—such as shell and tube, plate, and air-cooled variants—buyers can better align their needs with the appropriate technology. The guide also addresses critical applications across various industries, from oil and gas to HVAC, ensuring that buyers understand how these systems can optimize their operations.
Furthermore, we provide actionable insights on how to effectively vet potential suppliers, emphasizing the importance of quality certifications, customer reviews, and after-sales support. This information empowers B2B buyers to make informed purchasing decisions, minimizing risks and enhancing operational efficiency.
Ultimately, whether you are a manufacturer in the UAE, a distributor in Indonesia, or an end-user in Brazil, this guide aims to equip you with the knowledge needed to navigate the complexities of the heat exchanger market successfully.
Understanding heat exchanger manufacturer Types and Variations
Type Name | Key Distinguishing Features | Primary B2B Applications | Brief Pros & Cons for Buyers |
---|---|---|---|
Shell and Tube | Composed of a series of tubes, one set carrying the hot fluid and the other the cold fluid. | Oil refineries, chemical processing, power plants | Pros: High efficiency, versatile; Cons: Can be bulky and require more space. |
Plate Heat Exchanger | Consists of thin, corrugated plates stacked together, allowing fluids to flow through alternating channels. | Food processing, HVAC, pharmaceuticals | Pros: Compact size, high heat transfer efficiency; Cons: Limited pressure and temperature ranges. |
Air-Cooled Heat Exchanger | Uses air to cool fluids, often with fans to enhance heat transfer. | Power generation, refrigeration, petrochemical | Pros: No water required, low maintenance; Cons: Performance can be affected by ambient temperature. |
Double-Pipe Heat Exchanger | Simplest design, with one pipe inside another; hot fluid flows through the inner pipe while the cold fluid flows in the annular space. | Small-scale applications, laboratories | Pros: Easy to clean and maintain; Cons: Less efficient compared to other types. |
Spiral Heat Exchanger | Features spiral channels that enhance the mixing of fluids for efficient heat transfer. | Waste heat recovery, chemical industries | Pros: Compact design, effective for viscous fluids; Cons: Higher initial cost, complex design. |
What are the Key Characteristics of Shell and Tube Heat Exchangers?
Shell and tube heat exchangers are widely recognized for their robust construction and high efficiency. They consist of a series of tubes, with one set carrying the hot fluid and the other the cold fluid. This type is particularly suited for industries such as oil refining and chemical processing, where high pressures and temperatures are common. When purchasing, buyers should consider factors such as material compatibility, pressure drop, and maintenance needs, as these can significantly impact operational efficiency.
How Do Plate Heat Exchangers Stand Out?
Plate heat exchangers are characterized by their compact design, consisting of thin, corrugated plates stacked together to create multiple channels for fluid flow. They are ideal for applications in food processing and HVAC systems due to their high heat transfer efficiency and smaller footprint. B2B buyers should evaluate the materials used in construction, as well as the specific temperature and pressure limits, to ensure suitability for their processes.
Why Choose Air-Cooled Heat Exchangers?
Air-cooled heat exchangers utilize ambient air to cool fluids, often employing fans to enhance the cooling process. This design is advantageous in industries such as power generation and petrochemicals, where water scarcity is a concern. Buyers should consider the local climate’s impact on performance, as well as maintenance requirements, since these exchangers can accumulate debris over time, affecting efficiency.
What Are the Benefits of Double-Pipe Heat Exchangers?
Double-pipe heat exchangers feature a straightforward design with one pipe inside another, allowing for effective heat transfer between two fluids. They are most suitable for small-scale applications and laboratories where space is limited. When considering this type, buyers should think about the ease of cleaning and maintenance, but also recognize that their efficiency may not match that of more complex designs.
How Do Spiral Heat Exchangers Enhance Efficiency?
Spiral heat exchangers are designed with spiral channels that facilitate efficient mixing of fluids, making them especially effective for handling viscous fluids in waste heat recovery and chemical processing. They offer a compact design and can handle a wide range of fluid types. B2B buyers should weigh the initial investment against long-term operational savings and the potential for reduced maintenance costs when evaluating this option.
Related Video: HVAC Heat Exchangers Explained The basics working principle how heat exchanger works
Key Industrial Applications of heat exchanger manufacturer
Industry/Sector | Specific Application of heat exchanger manufacturer | Value/Benefit for the Business | Key Sourcing Considerations for this Application |
---|---|---|---|
Oil & Gas | Heat recovery in refining processes | Enhances energy efficiency and reduces costs | Compliance with safety standards and materials suited for high-pressure environments |
Chemical Processing | Heat exchange in reaction vessels | Optimizes reaction conditions and product yield | Corrosion resistance and customization for specific chemicals used |
HVAC Systems | Cooling and heating systems | Improves energy efficiency and comfort levels | Compatibility with existing infrastructure and energy ratings |
Food & Beverage | Pasteurization and cooling processes | Ensures food safety and extends shelf life | Hygiene standards and materials that comply with food safety regulations |
Power Generation | Condensing and cooling in steam cycles | Increases overall efficiency and reduces emissions | Robust design to handle varying temperatures and pressures |
How Are Heat Exchangers Used in the Oil & Gas Industry?
In the oil and gas sector, heat exchangers are crucial for heat recovery during refining processes. By transferring heat from one fluid to another, they enhance energy efficiency, significantly reducing operational costs. International buyers from regions like the Middle East, where oil extraction is prevalent, must consider sourcing heat exchangers that comply with stringent safety and environmental regulations. Materials must also withstand high pressures and corrosive substances, necessitating a focus on quality and durability.
What Role Do Heat Exchangers Play in Chemical Processing?
Within chemical processing, heat exchangers are employed in reaction vessels to manage temperature control effectively. This optimization leads to improved reaction conditions, ultimately increasing product yield. Buyers in Africa and South America should prioritize suppliers who offer corrosion-resistant materials tailored to their specific chemical applications. Customization options are vital to ensure compatibility with various chemicals and to meet local regulatory standards.
How Are Heat Exchangers Integrated into HVAC Systems?
In HVAC applications, heat exchangers facilitate efficient cooling and heating, crucial for maintaining comfortable indoor environments. They contribute to energy efficiency, which is a significant concern for European buyers focused on sustainability. When sourcing heat exchangers, compatibility with existing systems and compliance with energy efficiency ratings should be key considerations. Additionally, international buyers should assess the supplier’s ability to provide support for installation and maintenance.
Why Are Heat Exchangers Important in Food & Beverage Processing?
In the food and beverage industry, heat exchangers are essential for processes like pasteurization and cooling, ensuring food safety and extending shelf life. Suppliers must meet strict hygiene standards and utilize materials compliant with food safety regulations, which is particularly important for buyers in South America and Africa, where food safety is a growing concern. Understanding local regulations regarding food processing can also guide sourcing decisions.
How Do Heat Exchangers Enhance Power Generation Efficiency?
Heat exchangers are pivotal in power generation, especially in condensing and cooling systems within steam cycles. They enhance overall efficiency and reduce emissions, aligning with global sustainability goals. Buyers in regions like Europe, where there is a strong emphasis on clean energy, should consider the robustness of heat exchangers to handle varying temperatures and pressures. Additionally, sourcing from manufacturers with a proven track record in energy efficiency can provide a competitive edge in the market.
Related Video: Double Pipe Heat Exchanger Basics Explained – industrial engineering
3 Common User Pain Points for ‘heat exchanger manufacturer’ & Their Solutions
Scenario 1: Challenges with Heat Exchanger Sizing and Selection
The Problem:
Many B2B buyers in industries such as oil and gas, pharmaceuticals, and food processing struggle with selecting the appropriate size and type of heat exchanger for their specific applications. Inadequate sizing can lead to inefficient thermal performance, increased operational costs, and potential equipment failure. Buyers often find it difficult to navigate the technical specifications and performance parameters, leading to confusion and uncertainty about their purchase decisions.
The Solution:
To address sizing and selection challenges, B2B buyers should engage in thorough consultation with manufacturers before making a purchase. Start by providing detailed information about your application, including temperature ranges, pressure conditions, and the type of fluids involved. Manufacturers often have engineering teams that can assist with custom calculations and simulations to determine the optimal heat exchanger design. It is also beneficial to request case studies or examples of similar applications to understand how the heat exchanger will perform in real-world scenarios. This collaborative approach ensures that you invest in equipment that meets your operational requirements effectively, minimizing the risk of future inefficiencies.
Scenario 2: High Maintenance Costs and Downtime
The Problem:
International buyers often face challenges with maintenance and operational downtime associated with heat exchangers. Over time, fouling, corrosion, or scaling can lead to significant performance drops, requiring costly repairs and downtime that can disrupt production schedules. This issue is particularly critical in regions where spare parts and maintenance services may not be readily available, complicating timely interventions.
The Solution:
To mitigate maintenance issues, it is crucial to implement a proactive maintenance strategy from the outset. Buyers should inquire about the heat exchanger’s design features that facilitate easier cleaning and maintenance, such as removable bundles or access ports. Additionally, investing in predictive maintenance technologies, such as IoT sensors and monitoring systems, can help track performance metrics and predict potential failures before they occur. Establishing a strong relationship with your manufacturer or supplier can also provide access to technical support and maintenance resources, ensuring your heat exchanger operates at peak efficiency and reducing the total cost of ownership.
Scenario 3: Navigating Compliance and Regulatory Standards
The Problem:
B2B buyers from regions like Africa, South America, the Middle East, and Europe often encounter regulatory hurdles when sourcing heat exchangers. Compliance with local and international standards related to safety, environmental impact, and energy efficiency can be daunting. Failure to meet these requirements can lead to legal repercussions, fines, and operational shutdowns.
The Solution:
To navigate compliance challenges effectively, buyers should prioritize manufacturers that demonstrate a clear understanding of applicable regulations and standards in your region. Request documentation that outlines compliance with standards such as ASME, TEMA, or local environmental regulations. Engaging with manufacturers who provide certifications and have experience in your industry can ease the compliance burden. Additionally, consider conducting a thorough risk assessment and consultation with legal experts to ensure that all aspects of your heat exchanger procurement meet regulatory requirements. By choosing compliant manufacturers, you not only protect your organization from legal risks but also enhance your reputation in the market as a responsible and conscientious buyer.
Strategic Material Selection Guide for heat exchanger manufacturer
When selecting materials for heat exchangers, manufacturers must consider various factors that impact performance, durability, and cost. Below, we analyze four common materials used in heat exchanger manufacturing, focusing on their properties, advantages, disadvantages, and specific considerations for international B2B buyers.
What are the Key Properties of Stainless Steel in Heat Exchanger Applications?
Stainless steel is renowned for its excellent corrosion resistance, high-temperature tolerance, and strength. It typically has a temperature rating of up to 800°C and can withstand high-pressure environments, making it suitable for various applications, including chemical processing and oil and gas industries. The most common grades used are 304 and 316, with 316 offering superior resistance to chlorides.
Pros: Stainless steel is durable, easy to clean, and has a long lifespan, which reduces maintenance costs. It is also widely accepted in international markets, aligning with standards like ASTM and DIN.
Cons: The primary drawback is its cost, which is higher than other materials such as carbon steel. Additionally, its manufacturing process can be complex, particularly for intricate designs.
Impact on Application: Stainless steel is compatible with a wide range of media, including water, oils, and chemicals, making it versatile for various heat exchanger designs.
How Does Copper Perform as a Material for Heat Exchangers?
Copper is favored for its excellent thermal conductivity, which significantly enhances heat transfer efficiency. It can handle temperatures up to 200°C and is also resistant to corrosion, especially in non-oxidizing environments.
Pros: The high thermal efficiency of copper translates to smaller and lighter heat exchangers, which can reduce installation costs. It is also relatively easy to fabricate and weld.
Cons: Copper’s susceptibility to corrosion in certain environments, such as seawater or acidic conditions, limits its use. Additionally, it is more expensive than aluminum, which may deter some buyers.
Impact on Application: Copper is ideal for applications requiring rapid heat transfer, such as refrigeration and HVAC systems, but careful consideration of the operating environment is essential.
What are the Advantages and Disadvantages of Aluminum in Heat Exchanger Design?
Aluminum is lightweight and has good thermal conductivity, making it a popular choice for applications where weight is a critical factor, such as in automotive and aerospace industries. It typically operates effectively at temperatures up to 150°C.
Pros: Aluminum’s low weight can lead to reduced transportation and installation costs. It is also less expensive than stainless steel and copper, offering a cost-effective solution for many applications.
Cons: While aluminum has good corrosion resistance, it is not as robust as stainless steel and may require protective coatings in harsh environments. Its lower temperature tolerance can also limit its use in high-temperature applications.
Impact on Application: Aluminum is suitable for applications involving air-to-air heat exchangers and low-pressure systems but may not be ideal for aggressive chemical environments.
What Role Does Carbon Steel Play in Heat Exchanger Manufacturing?
Carbon steel is a cost-effective option for heat exchangers used in low-pressure and non-corrosive environments. It can handle temperatures up to 400°C, making it suitable for several industrial applications.
Pros: The primary advantage of carbon steel is its low cost compared to other materials, which can significantly reduce initial investment costs. It is also readily available and easy to fabricate.
Cons: Carbon steel is prone to corrosion, especially in humid or aggressive environments, which can lead to a shorter lifespan and higher maintenance costs. It also requires protective coatings or treatments to enhance its durability.
Impact on Application: Carbon steel is best suited for applications involving water or steam, but it may not be appropriate for corrosive media without additional protective measures.
Summary Table of Material Selection for Heat Exchangers
Material | Typical Use Case for heat exchanger manufacturer | Key Advantage | Key Disadvantage/Limitation | Relative Cost (Low/Med/High) |
---|---|---|---|---|
Stainless Steel | Chemical processing, oil and gas | Excellent corrosion resistance | Higher cost and manufacturing complexity | High |
Copper | Refrigeration, HVAC systems | High thermal conductivity | Susceptible to corrosion in certain environments | Med |
Aluminum | Automotive, aerospace applications | Lightweight and cost-effective | Lower temperature tolerance and corrosion resistance | Low |
Carbon Steel | Water and steam applications | Cost-effective | Prone to corrosion without protection | Low |
This strategic material selection guide provides international B2B buyers with a comprehensive overview of materials used in heat exchanger manufacturing, highlighting key properties and considerations that can influence purchasing decisions. Understanding these factors is crucial for optimizing performance and ensuring compliance with industry standards across different regions.
In-depth Look: Manufacturing Processes and Quality Assurance for heat exchanger manufacturer
Manufacturing heat exchangers is a complex process that requires precision and adherence to strict quality control standards. For international B2B buyers, understanding these manufacturing processes and quality assurance protocols is essential when selecting suppliers. This section provides a comprehensive overview of the typical manufacturing stages, key techniques involved, and quality assurance measures that ensure the reliability and efficiency of heat exchangers.
What Are the Main Stages of Heat Exchanger Manufacturing?
The manufacturing of heat exchangers typically involves several key stages: material preparation, forming, assembly, and finishing. Each stage plays a crucial role in ensuring the final product meets the required specifications.
Material Preparation: How Is It Done?
Material preparation is the initial stage where raw materials, such as metals (stainless steel, copper, aluminum), are sourced and processed. This phase includes cutting, shaping, and treating materials to enhance their durability and resistance to corrosion. For B2B buyers, it is vital to verify the quality of raw materials used, as they significantly influence the performance and lifespan of the heat exchangers.
What Forming Techniques Are Commonly Used?
The forming stage involves shaping the prepared materials into the desired configuration. Common techniques include:
-
Welding: A critical process for joining metal parts, ensuring strong and leak-proof connections. Various welding methods, such as TIG (Tungsten Inert Gas) and MIG (Metal Inert Gas), are employed based on material types and thicknesses.
-
Bending and Stamping: These methods are used to create specific geometries and features in heat exchanger components, enhancing their thermal efficiency.
-
Tube Expansion: In many designs, tubes are expanded to fit securely into the header plates, which is essential for optimal thermal performance.
How Is Assembly Conducted in Heat Exchanger Manufacturing?
Once the individual components are formed, the assembly stage begins. This involves:
-
Component Integration: Assembling various parts, including tubes, plates, and headers, to create the complete heat exchanger unit.
-
Sealing and Insulation: Ensuring that all joints are properly sealed to prevent leakage and that insulation is applied where necessary to minimize heat loss.
Effective assembly is critical for the operational efficiency and reliability of the heat exchanger. B2B buyers should inquire about the assembly processes and the experience of the workforce involved, as these factors directly affect product quality.
What Finishing Processes Are Important for Heat Exchangers?
Finishing processes enhance the aesthetic and functional properties of heat exchangers. These may include:
-
Surface Treatment: Techniques such as anodizing or passivation are used to improve corrosion resistance and surface finish.
-
Testing and Inspection: After assembly, heat exchangers undergo rigorous testing to ensure they meet performance specifications. This includes pressure tests, leak tests, and thermal performance evaluations.
What Quality Assurance Standards Should B2B Buyers Be Aware Of?
Quality assurance (QA) is paramount in manufacturing heat exchangers. Familiarity with international standards and industry-specific certifications helps B2B buyers assess supplier reliability.
Which International Standards Are Relevant?
-
ISO 9001: This standard outlines the requirements for a quality management system (QMS). Suppliers certified under ISO 9001 demonstrate a commitment to quality processes and customer satisfaction.
-
CE Marking: Essential for products sold in Europe, CE marking indicates compliance with safety, health, and environmental protection standards.
-
API Standards: For heat exchangers used in the oil and gas industry, adherence to American Petroleum Institute (API) standards is critical for ensuring operational safety and reliability.
What Are the Key QC Checkpoints in the Manufacturing Process?
Quality control (QC) checkpoints throughout the manufacturing process help ensure that each heat exchanger meets the required specifications. Key checkpoints include:
-
Incoming Quality Control (IQC): This initial inspection phase involves verifying the quality of raw materials and components before they enter the production line.
-
In-Process Quality Control (IPQC): During manufacturing, IPQC checks are performed to monitor processes and identify any deviations from quality standards. This includes regular inspections of welding quality and dimensional accuracy.
-
Final Quality Control (FQC): At this stage, the completed heat exchanger undergoes extensive testing to ensure it meets all specifications and standards. FQC may involve performance testing under simulated operational conditions.
How Can B2B Buyers Verify Supplier Quality Control?
For international B2B buyers, verifying the QC processes of potential suppliers is crucial for ensuring product reliability. Here are actionable steps to consider:
-
Conduct Audits: Request on-site audits of the manufacturing facilities to assess their adherence to quality standards and processes. This allows buyers to gain firsthand insight into the supplier’s operations.
-
Review Quality Reports: Suppliers should provide detailed quality control reports, including results from various testing phases. Analyzing these reports helps buyers understand the supplier’s commitment to quality.
-
Engage Third-Party Inspectors: Consider hiring third-party inspection services to conduct independent evaluations of the manufacturing process and finished products. This adds an extra layer of assurance regarding quality compliance.
What Are the QC and Certification Nuances for International Buyers?
For B2B buyers in regions like Africa, South America, the Middle East, and Europe, understanding the nuances of QC and certification is vital. Different markets may have varying standards and expectations, which can impact procurement strategies. Buyers should:
-
Understand Regional Standards: Familiarize themselves with local regulations and standards that may differ from international norms. For example, certain countries may have additional certifications or compliance requirements.
-
Establish Clear Communication: Maintain open lines of communication with suppliers to ensure that all quality expectations are understood and met. This reduces the risk of misunderstandings and ensures that products are delivered as specified.
-
Leverage Trade Networks: Utilize trade associations and networks to gather insights about reputable suppliers and their quality assurance practices. Networking with industry peers can provide valuable recommendations and feedback.
By comprehensively understanding the manufacturing processes and quality assurance measures for heat exchangers, international B2B buyers can make informed decisions that ensure they partner with reliable suppliers capable of delivering high-quality products.
Practical Sourcing Guide: A Step-by-Step Checklist for ‘heat exchanger manufacturer’
Introduction
Sourcing a heat exchanger manufacturer requires careful consideration and strategic planning. This guide provides a comprehensive checklist for international B2B buyers, particularly from Africa, South America, the Middle East, and Europe, to ensure you choose the right supplier that meets your technical, quality, and service expectations.
Step 1: Define Your Technical Specifications
Before starting your search for a heat exchanger manufacturer, clearly outline your technical requirements. This includes the type of heat exchanger needed (e.g., shell and tube, plate, air-cooled), materials, size, and capacity. Precise specifications not only help in narrowing down potential suppliers but also facilitate accurate quotes and ensure that the products meet your operational needs.
Step 2: Conduct Market Research on Suppliers
Invest time in researching potential suppliers in the heat exchanger manufacturing space. Look for manufacturers with a proven track record in your industry and geographical region. Key aspects to consider include:
– Industry experience: Suppliers with extensive experience in similar applications are more likely to understand your needs.
– Customer reviews and testimonials: These provide insights into the reliability and quality of the supplier’s products and services.
Step 3: Evaluate Supplier Certifications
It is vital to verify that potential suppliers hold relevant certifications, such as ISO 9001 for quality management or ASME certification for specific heat exchanger designs. Certifications indicate that the manufacturer adheres to industry standards and practices, which is crucial for ensuring the safety and efficiency of the products you will be using.
Step 4: Request and Analyze Quotes
Once you have identified a shortlist of potential suppliers, request detailed quotes from each. Ensure that the quotes include all pertinent information, such as pricing, lead times, warranty details, and payment terms. Analyzing these quotes allows you to compare not just costs but also value, which can significantly affect your overall project budget.
Step 5: Visit Manufacturing Facilities If Possible
If feasible, plan a visit to the manufacturing facilities of your top supplier candidates. This visit will provide you with firsthand insight into their production processes, quality control measures, and operational capabilities. Look for:
– Cleanliness and organization: A well-maintained facility often reflects a commitment to quality.
– Technology and equipment: Modern machinery can indicate the manufacturer’s ability to meet high standards and adapt to new technologies.
Step 6: Assess After-Sales Support and Service
After-sales support is critical for maintaining operational efficiency. Inquire about the support services offered by the manufacturer, including installation assistance, maintenance, and spare parts availability. Strong after-sales service can help resolve issues quickly and minimize downtime, which is essential for your operations.
Step 7: Negotiate Terms and Finalize the Contract
Once you have selected a supplier, engage in negotiations to finalize the terms of the contract. This should cover payment terms, delivery schedules, warranties, and liability clauses. A well-structured contract protects both parties and ensures clarity in expectations, which is vital for a successful long-term partnership.
By following this checklist, B2B buyers can effectively navigate the complex landscape of sourcing heat exchangers, ensuring they partner with a manufacturer that aligns with their technical requirements and business goals.
Comprehensive Cost and Pricing Analysis for heat exchanger manufacturer Sourcing
What Are the Key Cost Components in Heat Exchanger Manufacturing?
Understanding the cost structure of heat exchanger manufacturing is crucial for international B2B buyers. The primary cost components include:
-
Materials: This is typically the largest portion of the total cost. Common materials include stainless steel, copper, and aluminum, which vary in price based on global market conditions and availability.
-
Labor: Labor costs can fluctuate significantly based on the region. In countries with higher labor costs, such as in Western Europe, these expenses can be substantial, while in regions like South America or parts of Africa, labor may be more cost-effective.
-
Manufacturing Overhead: This includes costs related to facilities, utilities, and equipment maintenance. Efficient production processes can help mitigate overhead costs.
-
Tooling: The cost of tooling and molds is essential for custom designs. Buyers should consider the impact of tooling costs on the overall pricing, especially for specialized heat exchangers.
-
Quality Control (QC): QC processes ensure that products meet required standards, which can add to the cost. Certifications like ISO can increase both production costs and marketability.
-
Logistics: Shipping and handling costs can vary based on the distance and mode of transport. These costs can significantly affect the total price, especially for international buyers.
-
Margin: Manufacturers typically add a profit margin, which can vary based on the competitive landscape and market demand.
How Do Price Influencers Affect Heat Exchanger Costs?
Several factors can influence the pricing of heat exchangers:
-
Volume and Minimum Order Quantity (MOQ): Larger orders often lead to lower per-unit costs due to economies of scale. Buyers should negotiate MOQs that suit their needs.
-
Specifications and Customization: Customized heat exchangers can increase costs due to the need for specialized materials and manufacturing processes. Clear specifications can help manufacturers provide accurate quotes.
-
Materials: The choice of materials directly impacts pricing. For instance, high-grade materials may be more expensive but can lead to longer lifespan and better performance.
-
Quality and Certifications: Products that meet international standards or have certifications may carry a premium price. However, these can be critical for compliance and reliability.
-
Supplier Factors: The reputation and reliability of the supplier can influence pricing. Established suppliers with a track record may charge higher prices but offer better service and quality assurance.
-
Incoterms: Understanding Incoterms is vital for international shipping. Terms like FOB (Free on Board) or CIF (Cost, Insurance, and Freight) can affect the total landed cost and should be clearly defined in contracts.
What Tips Can Buyers Use to Negotiate Better Pricing?
For international B2B buyers, particularly from Africa, South America, the Middle East, and Europe, effective negotiation strategies can lead to significant cost savings:
-
Conduct a Total Cost of Ownership (TCO) Analysis: Consider all costs associated with the heat exchanger, including maintenance and operational costs, not just the purchase price.
-
Leverage Volume Discounts: If feasible, consolidate orders to reach higher volumes that qualify for discounts.
-
Request Multiple Quotes: Comparing quotes from different manufacturers can provide leverage in negotiations and help identify competitive pricing.
-
Be Clear About Specifications: Providing detailed specifications can reduce misunderstandings and lead to more accurate pricing.
-
Build Relationships with Suppliers: Establishing a good rapport with suppliers can lead to better pricing and terms in the long run.
-
Understand Local Market Conditions: Being aware of the economic conditions and supply chain challenges in the supplier’s region can provide insights that enhance negotiation strategies.
Conclusion
While indicative prices can vary widely based on numerous factors, understanding the intricate cost structure and price influencers in heat exchanger manufacturing can empower international B2B buyers to make informed purchasing decisions. By employing strategic negotiation techniques and being mindful of total costs, buyers can optimize their sourcing outcomes.
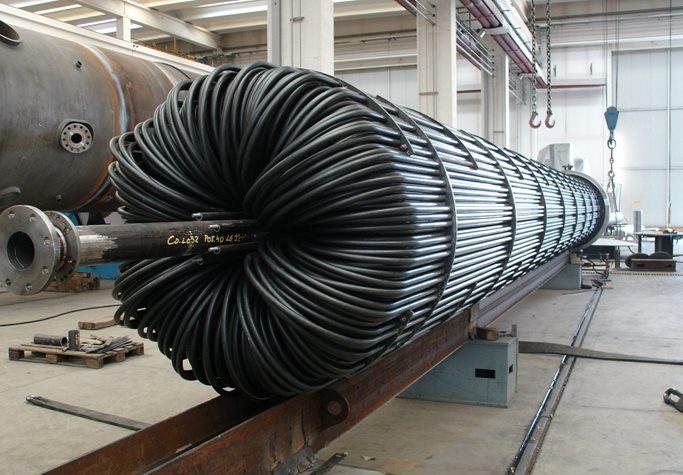
A stock image related to heat exchanger manufacturer.
Alternatives Analysis: Comparing heat exchanger manufacturer With Other Solutions
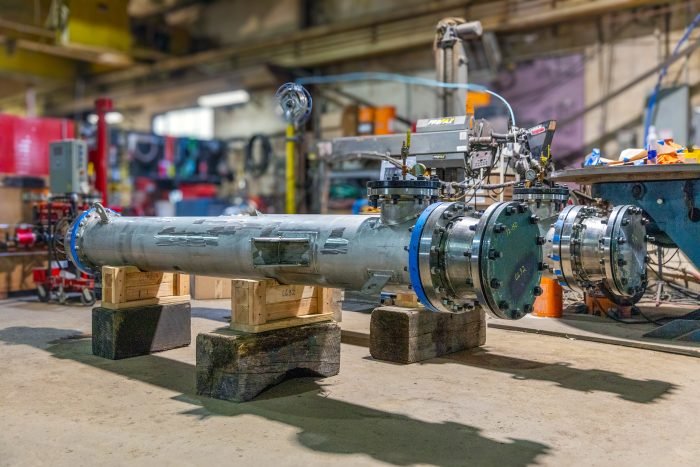
A stock image related to heat exchanger manufacturer.
In the realm of thermal management and fluid dynamics, international B2B buyers often seek efficient solutions for heat transfer applications. While heat exchangers manufactured by established companies offer numerous advantages, it’s essential to consider viable alternatives that may better suit specific operational needs or budget constraints. This analysis will compare heat exchanger manufacturers with other solutions, such as heat pump systems and thermal storage tanks.
Comparison Table of Heat Exchanger Solutions
Comparison Aspect | Heat Exchanger Manufacturer | Heat Pump Systems | Thermal Storage Tanks |
---|---|---|---|
Performance | High efficiency in heat transfer; suitable for various fluids | Moderate efficiency; dependent on ambient conditions | Excellent for load shifting; can improve overall system efficiency |
Cost | Higher upfront costs; long-term savings through efficiency | Moderate initial investment; potential rebates available | Lower initial costs; ongoing operational costs can add up |
Ease of Implementation | Complex installation requiring specialized knowledge | Relatively straightforward installation; often requires HVAC expertise | Simple installation; minimal technical knowledge needed |
Maintenance | Requires regular maintenance; professional servicing recommended | Low maintenance; periodic checks suffice | Minimal maintenance; occasional inspections needed |
Best Use Case | Ideal for industrial applications needing consistent heat exchange | Suitable for residential or commercial heating and cooling | Best for energy storage and peak demand management |
What are the Advantages and Disadvantages of Heat Pump Systems?
Heat pump systems are increasingly popular due to their versatility in providing both heating and cooling. They work by transferring heat from one place to another, making them energy-efficient in moderate climates. The primary advantage is their ability to reduce energy costs significantly, especially with government incentives available in many regions. However, their efficiency can be compromised in extreme temperatures, requiring supplementary heating systems, which may increase overall costs.
How Do Thermal Storage Tanks Compare?
Thermal storage tanks are a cost-effective solution for managing energy loads, particularly in industrial settings where energy demand fluctuates. They store thermal energy for use during peak demand times, which can lead to significant cost savings on energy bills. The low installation complexity is a plus, as businesses can often implement these systems without extensive training. However, the ongoing operational costs can accumulate, especially if the energy source for heating the stored fluid is expensive.
Conclusion: How Can B2B Buyers Choose the Right Solution?
When selecting between a heat exchanger manufacturer and alternative solutions like heat pump systems or thermal storage tanks, international B2B buyers should consider several factors. These include the specific application requirements, budget constraints, and long-term operational efficiency. By evaluating performance metrics, installation complexities, and maintenance needs, buyers can align their choice with their operational goals. Ultimately, the right solution will depend on the unique demands of the business environment and the desired balance between initial investment and long-term savings.
Essential Technical Properties and Trade Terminology for heat exchanger manufacturer
What Are the Key Technical Properties of Heat Exchangers?
When sourcing heat exchangers, understanding their technical specifications is crucial for making informed purchasing decisions. Here are some essential properties to consider:
1. Material Grade
The material used in heat exchangers significantly influences their performance and durability. Common materials include stainless steel, copper, and aluminum. Each material has unique properties, such as corrosion resistance and thermal conductivity. For example, stainless steel is favored for its high resistance to corrosion, making it ideal for industries like oil and gas, while copper is known for its superior thermal conductivity.
2. Design Pressure and Temperature Ratings
These ratings determine the maximum pressure and temperature at which the heat exchanger can operate safely. They are critical for ensuring the equipment can withstand the operational conditions without risk of failure. Buyers should ensure the specifications match their application’s requirements to prevent costly downtime or equipment failure.
3. Tolerance and Dimensional Specifications
Tolerance refers to the permissible limit of variation in a physical dimension. Accurate tolerances are essential for ensuring proper fit and function within a system. For heat exchangers, precise dimensions ensure optimal heat transfer efficiency. Buyers should verify that manufacturers can meet the required tolerances to avoid installation issues.
4. Heat Transfer Efficiency
This property indicates how effectively a heat exchanger transfers heat between two fluids. It is usually quantified using the Overall Heat Transfer Coefficient (U-value). A higher U-value indicates better performance, leading to reduced energy costs and improved system efficiency. Buyers should inquire about the U-value during the selection process to ensure optimal performance.
5. Surface Area
The surface area available for heat exchange directly impacts the efficiency of the unit. Larger surface areas typically allow for better heat transfer, making it a vital specification to consider. When negotiating, ask manufacturers about the surface area specifications to ensure the heat exchanger meets operational demands.
What Are Common Trade Terms in the Heat Exchanger Industry?
Understanding industry jargon is essential for effective communication with manufacturers and suppliers. Here are some common terms you should know:
1. OEM (Original Equipment Manufacturer)
An OEM is a company that produces parts or equipment that may be marketed by another manufacturer. In the context of heat exchangers, knowing if a supplier is an OEM can help buyers assess quality and reliability, as OEMs often adhere to strict manufacturing standards.
2. MOQ (Minimum Order Quantity)
MOQ refers to the smallest number of units that a supplier is willing to sell. Understanding MOQ is vital for budgeting and inventory management. Buyers should negotiate MOQs based on their projected needs to avoid excess inventory or understocking.
3. RFQ (Request for Quotation)
An RFQ is a document sent to suppliers to solicit price quotes for specific products or services. It typically includes detailed specifications and quantities. Submitting an RFQ helps buyers compare prices and terms from different suppliers, ensuring they get the best deal.
4. Incoterms (International Commercial Terms)
These are standardized terms used in international trade to define the responsibilities of buyers and sellers. Familiarity with Incoterms helps in understanding shipping costs, insurance, and risk during transit. Knowing these terms can prevent misunderstandings and additional costs during the procurement process.
5. Lead Time
Lead time is the amount of time it takes from placing an order to receiving the product. This metric is crucial for project planning, especially in industries with tight deadlines. Buyers should discuss lead times upfront to align their procurement schedules with operational needs.
In summary, understanding both the technical properties and trade terminology related to heat exchangers will empower international B2B buyers to make informed decisions that align with their operational requirements and budget constraints.
Navigating Market Dynamics and Sourcing Trends in the heat exchanger manufacturer Sector
What Are the Current Market Dynamics and Key Trends in the Heat Exchanger Manufacturing Sector?
The heat exchanger manufacturing sector is witnessing transformative shifts driven by globalization, technological advancements, and increasing demand for energy-efficient solutions. Key market drivers include the rising need for sustainable energy systems, particularly in developing regions like Africa and South America, where infrastructure development is crucial. International B2B buyers should be aware that the adoption of smart manufacturing technologies, such as the Internet of Things (IoT) and artificial intelligence (AI), is enhancing operational efficiency and optimizing supply chains.
Emerging trends in sourcing practices reveal a focus on digital platforms for procurement, allowing buyers to access a broader range of suppliers and streamline their sourcing processes. Additionally, the emphasis on customization and modular designs is gaining traction, as businesses seek tailored solutions to meet specific operational requirements. Buyers from Europe and the Middle East are particularly keen on suppliers who can provide flexible solutions that align with local regulations and environmental standards.
Moreover, the market is seeing a shift towards local sourcing as companies aim to mitigate risks associated with global supply chain disruptions. International buyers should consider forming partnerships with local manufacturers in target regions to enhance supply chain resilience while also supporting regional economies.
How Is Sustainability Shaping Sourcing Practices in the Heat Exchanger Sector?
Sustainability has become a critical consideration for B2B buyers in the heat exchanger manufacturing sector. The environmental impact of production processes and the lifecycle of heat exchangers is under scrutiny. Buyers are increasingly prioritizing suppliers who demonstrate a commitment to reducing carbon footprints and utilizing eco-friendly materials in their manufacturing processes.
Ethical sourcing is also gaining importance as companies strive to ensure that their supply chains are not only efficient but also socially responsible. This includes verifying that materials are sourced from suppliers who adhere to fair labor practices and environmental stewardship. Certifications like ISO 14001 (Environmental Management) and LEED (Leadership in Energy and Environmental Design) are becoming essential for buyers seeking to validate the sustainability credentials of their suppliers.
Incorporating ‘green’ materials, such as recycled metals and eco-friendly coatings, can significantly reduce the environmental impact of heat exchangers. Buyers should actively seek out manufacturers who can provide documentation of sustainable practices and materials, ensuring that their procurement decisions align with corporate social responsibility (CSR) goals.
What Is the Historical Context of Heat Exchanger Manufacturing?
The heat exchanger manufacturing sector has evolved significantly since its inception in the early 20th century. Initially, heat exchangers were rudimentary devices primarily used in steam engines and industrial processes. However, as technological advancements emerged, the designs became more sophisticated, catering to various industries, including HVAC, power generation, and chemical processing.
The late 20th century marked a pivotal shift toward energy efficiency and environmental considerations, leading to the development of compact and high-performance heat exchangers. This evolution has been propelled by the growing demand for sustainable energy solutions, particularly in regions facing energy crises or industrial growth.
Understanding the historical context of heat exchangers is crucial for international B2B buyers, as it highlights the innovations and regulatory changes that have shaped current manufacturing practices. This knowledge can inform sourcing strategies, enabling buyers to align their procurement processes with industry best practices and future trends.
Frequently Asked Questions (FAQs) for B2B Buyers of heat exchanger manufacturer
-
1. How do I select the right heat exchanger for my industry?
Choosing the right heat exchanger involves assessing your specific application requirements, including temperature and pressure ranges, fluid types, and desired efficiency. Start by understanding the thermal load and the space available for installation. Consult with manufacturers to evaluate different types, such as shell-and-tube, plate, or air-cooled heat exchangers, based on your operational needs. Additionally, consider energy efficiency ratings and maintenance requirements to ensure long-term performance and cost-effectiveness. -
2. What are the key factors to consider when vetting a heat exchanger manufacturer?
When vetting a heat exchanger manufacturer, assess their industry experience, certifications, and reputation. Check for compliance with international standards such as ISO and ASME. Request references from previous clients and review case studies that demonstrate their capabilities. Additionally, evaluate their production capacity, technology used, and after-sales support to ensure they can meet your demands and provide timely assistance when needed. -
3. What is the minimum order quantity (MOQ) for heat exchangers from international manufacturers?
Minimum order quantities (MOQ) can vary significantly among manufacturers, typically ranging from one unit to several dozen, depending on the product type and customization level. For standard models, many manufacturers may have lower MOQs, while custom-designed heat exchangers often require larger orders. It’s crucial to communicate your needs clearly and inquire about flexibility in MOQs to find a suitable supplier that aligns with your project requirements. -
4. How can I customize my heat exchanger for specific applications?
Customization options for heat exchangers include size, material, design configuration, and connection types. To initiate customization, provide detailed specifications of your application, including operating conditions and performance goals. Collaborate closely with the manufacturer’s engineering team to explore design alternatives and material choices that enhance efficiency and durability. Ensure to review prototypes or simulations before finalizing the design to confirm it meets your operational needs. -
5. What payment terms should I expect when purchasing heat exchangers internationally?
Payment terms can vary widely based on the manufacturer and the buyer’s creditworthiness. Common terms include upfront payments, partial payments upon order confirmation, and balance due upon delivery. For larger orders, manufacturers may offer financing options or extended payment terms. Always clarify payment methods (e.g., wire transfer, letter of credit) and ensure all terms are documented in the purchase agreement to avoid misunderstandings. -
6. How do I ensure quality assurance when sourcing heat exchangers?
To ensure quality assurance, request detailed documentation on the manufacturing process, including quality control procedures and certifications. Ask for a sample or prototype before placing a large order to evaluate performance. Consider third-party inspections or audits, especially for critical applications. Establish clear acceptance criteria in your contract and maintain open communication with the manufacturer throughout the production process to address any concerns promptly. -
7. What logistics considerations should I keep in mind when importing heat exchangers?
Logistics considerations for importing heat exchangers include shipping methods, customs regulations, and potential tariffs. Evaluate the most cost-effective shipping options, balancing speed and expense. Collaborate with logistics providers familiar with international shipping to ensure compliance with import regulations. Additionally, factor in lead times for production and shipping to avoid delays in project timelines, and consider insurance coverage for high-value shipments. -
8. How can I evaluate the technical support offered by a heat exchanger manufacturer?
Evaluating technical support from a heat exchanger manufacturer involves assessing their responsiveness, expertise, and availability. Inquire about the support channels they offer, such as phone, email, or live chat, and their typical response times. Review the availability of technical documentation, training resources, and troubleshooting assistance. It can also be beneficial to read reviews from other clients regarding their experiences with the manufacturer’s customer service to gauge overall satisfaction.
Important Disclaimer & Terms of Use
⚠️ Important Disclaimer
The information provided in this guide, including content regarding manufacturers, technical specifications, and market analysis, is for informational and educational purposes only. It does not constitute professional procurement advice, financial advice, or legal advice.
While we have made every effort to ensure the accuracy and timeliness of the information, we are not responsible for any errors, omissions, or outdated information. Market conditions, company details, and technical standards are subject to change.
B2B buyers must conduct their own independent and thorough due diligence before making any purchasing decisions. This includes contacting suppliers directly, verifying certifications, requesting samples, and seeking professional consultation. The risk of relying on any information in this guide is borne solely by the reader.
Strategic Sourcing Conclusion and Outlook for heat exchanger manufacturer
In today’s competitive landscape, international B2B buyers must prioritize strategic sourcing to enhance their procurement processes, particularly when it comes to heat exchangers. By carefully evaluating suppliers based on quality, cost, and delivery capabilities, businesses can secure the most advantageous partnerships. Buyers should also consider the importance of supplier diversity and the role it plays in fostering innovation and sustainability.
What Are the Key Takeaways for Strategic Sourcing in Heat Exchangers?
Understanding the specific needs of your industry—whether it’s energy, manufacturing, or HVAC—will guide you in selecting the right heat exchanger manufacturer. By leveraging technology and data analytics, businesses can make informed decisions that drive efficiency and cost-effectiveness. Additionally, establishing long-term relationships with manufacturers can lead to improved service levels and customization options.
How Can International Buyers Prepare for Future Trends?
As we look ahead, the global demand for energy-efficient and environmentally-friendly heat exchangers will continue to rise. Buyers from Africa, South America, the Middle East, and Europe should stay informed about regulatory changes and technological advancements that may impact their sourcing strategies. Engaging with suppliers who are committed to innovation will be crucial for maintaining competitive advantage.
In conclusion, embracing a strategic sourcing approach will empower international B2B buyers to navigate the complexities of the heat exchanger market effectively. Take action today by assessing your sourcing strategies to align with future trends and ensure your business remains at the forefront of industry advancements.