The Ultimate Guide to Kitchen Appliances China (2025)
Introduction: Navigating the Global Market for kitchen appliances china
Navigating the complexities of sourcing kitchen appliances from China can be daunting for international B2B buyers, especially those from emerging markets in Africa, South America, the Middle East, and Europe. With a myriad of suppliers and a vast array of products available, identifying reliable manufacturers while ensuring compliance with local regulations poses a significant challenge. This guide on kitchen appliances from China aims to simplify that journey, offering insights into various types of kitchen appliances, their applications, and the essential steps for effective supplier vetting.
Buyers will find a comprehensive overview of the kitchen appliance market, including trends in energy efficiency, innovative technology, and design aesthetics that appeal to diverse consumer preferences. Additionally, this guide covers critical aspects such as cost considerations, shipping logistics, and quality assurance practices, equipping buyers with the knowledge needed to make informed purchasing decisions.
By understanding the landscape of kitchen appliances in China, international B2B buyers can mitigate risks associated with sourcing and capitalize on opportunities to enhance their product offerings. This resource empowers businesses in regions like Nigeria and the UAE to confidently navigate the global marketplace, ultimately driving growth and competitiveness in their local markets.
Understanding kitchen appliances china Types and Variations
Type Name | Key Distinguishing Features | Primary B2B Applications | Brief Pros & Cons for Buyers |
---|---|---|---|
Refrigerators | Energy-efficient, varying sizes, smart technology options | Grocery stores, restaurants, hotels | Pros: Energy savings, advanced features. Cons: Higher upfront cost. |
Ovens and Ranges | Convection options, gas/electric variations, multi-function | Catering services, bakeries, restaurants | Pros: Versatility, high cooking efficiency. Cons: Requires skilled operation. |
Dishwashers | Multiple wash cycles, energy-efficient models, compact sizes | Restaurants, hotels, food services | Pros: Saves labor, improves sanitation. Cons: Initial investment can be high. |
Food Processors | Various attachments, high capacity, automation features | Food manufacturing, catering services | Pros: Reduces prep time, versatile. Cons: Maintenance can be complex. |
Coffee Machines | Commercial-grade, programmable settings, large capacity | Cafes, restaurants, hotels | Pros: Consistent quality, high demand. Cons: Requires regular maintenance. |
What Are the Key Characteristics of Refrigerators for B2B Buyers?
Refrigerators designed for commercial use come in various sizes and configurations, including upright and chest models. They often feature advanced energy-efficient technologies and smart capabilities that allow for temperature monitoring and alerts. For B2B buyers, considering the energy consumption and storage capacity is crucial, especially in sectors like grocery stores and hotels where refrigeration is essential for inventory management. Additionally, compatibility with existing kitchen layouts and the availability of warranty services are significant factors in the purchasing decision.
How Do Ovens and Ranges Serve the Needs of B2B Buyers?
Ovens and ranges are vital in commercial kitchens, offering options such as convection cooking, gas, and electric models. They often come equipped with multiple burners and oven compartments, allowing for simultaneous cooking of various dishes. B2B buyers in the catering and restaurant sectors should evaluate the cooking efficiency and versatility of these appliances, particularly in high-volume environments. Furthermore, the need for skilled personnel to operate advanced cooking technologies can influence purchasing decisions, making training and support essential considerations.
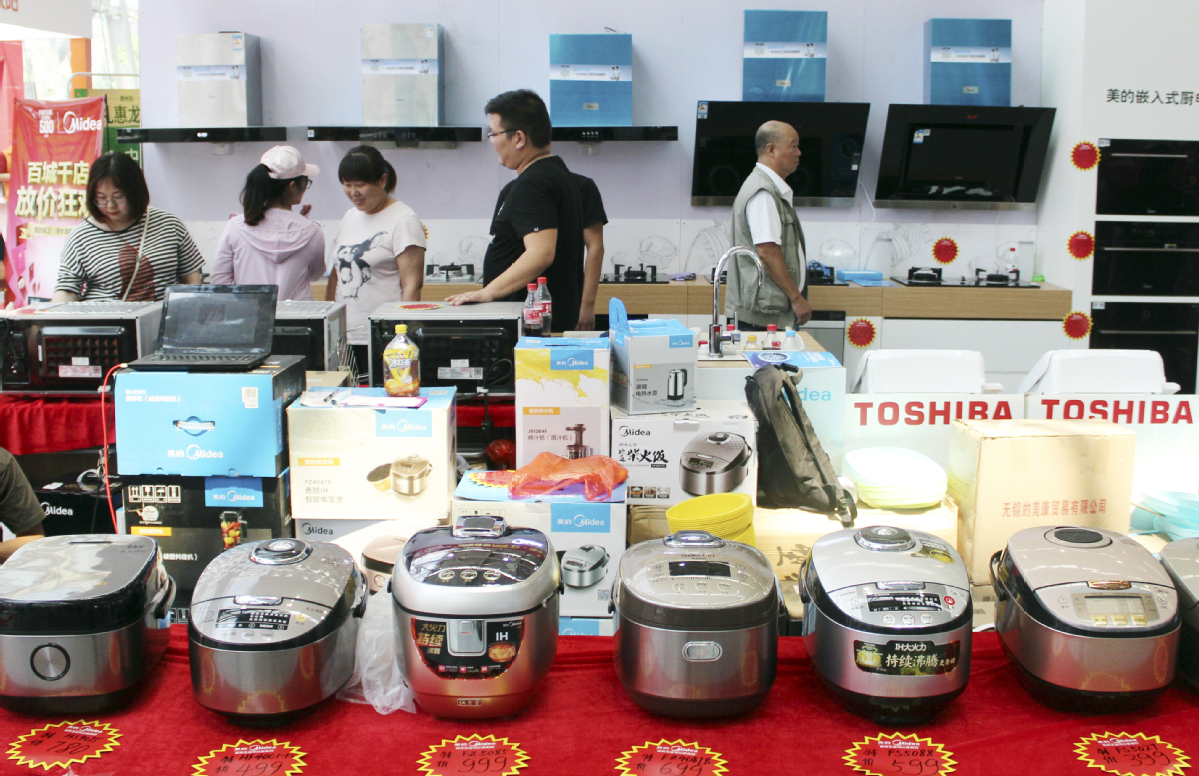
A stock image related to kitchen appliances china.
What Advantages Do Dishwashers Offer to Commercial Buyers?
Commercial dishwashers are designed to handle large volumes of dishware efficiently, providing multiple wash cycles and energy-saving features. They are essential for maintaining hygiene standards in restaurants and hotels. When selecting a dishwasher, B2B buyers should consider the machine’s capacity, speed of operation, and water consumption. While the initial investment might be significant, the long-term savings in labor and improved sanitation make them a valuable asset in any food service operation.
What Should B2B Buyers Know About Food Processors?
Food processors are indispensable in food preparation, offering various attachments for chopping, slicing, and blending. Their capacity to handle large quantities of ingredients makes them ideal for food manufacturing and catering services. B2B buyers should assess the durability and power of the motor, as well as the ease of cleaning and maintenance. While food processors can significantly reduce prep time, buyers must also consider the potential complexity of repairs and the availability of replacement parts when making purchasing decisions.
How Do Coffee Machines Cater to Commercial Needs?
Commercial coffee machines are designed to meet the high demand of cafes and restaurants, offering programmable settings and large capacities. They ensure consistent quality and flavor, which is crucial for customer satisfaction. B2B buyers should focus on the machine’s brewing speed, maintenance requirements, and the availability of service support. Although these machines can be costly, the potential for increased customer traffic and sales makes them a worthwhile investment in the competitive food and beverage industry.
Related Video: 40 Chinese Kitchen Gadgets 2022 & Home appliances/Smart Gadgets | Available on Amazon part 6
Key Industrial Applications of kitchen appliances china
Industry/Sector | Specific Application of Kitchen Appliances China | Value/Benefit for the Business | Key Sourcing Considerations for this Application |
---|---|---|---|
Hospitality | Commercial kitchen equipment for restaurants | Enhanced operational efficiency and food quality | Compliance with local safety regulations and energy standards |
Food Processing | Industrial food processors and mixers | Increased production capacity and consistency | Durability and ease of maintenance |
Retail & Grocery | Refrigeration units for supermarkets | Improved product shelf-life and customer satisfaction | Energy efficiency and reliability during peak hours |
Catering Services | Portable cooking appliances for events | Flexibility and speed in food preparation | Compact design and ease of transport |
Healthcare Facilities | Specialized kitchen appliances for dietary needs | Nutritional compliance and patient satisfaction | Hygiene standards and specialized functionality |
How are Kitchen Appliances from China Used in the Hospitality Sector?
In the hospitality industry, commercial kitchen equipment sourced from China plays a pivotal role in enhancing operational efficiency within restaurants and hotels. These appliances, such as industrial ovens and dishwashers, streamline food preparation and service processes, ensuring high-quality meals are served promptly. International buyers, especially from regions like Africa and the Middle East, must prioritize compliance with local safety regulations and energy standards to ensure smooth operations and customer satisfaction.
What Role Do Kitchen Appliances Play in Food Processing?
In food processing, industrial kitchen appliances, including food processors and mixers, are essential for increasing production capacity and maintaining product consistency. These appliances help manufacturers automate their processes, reducing labor costs while enhancing output quality. For buyers in South America and Europe, sourcing durable equipment that is easy to maintain is crucial to minimize downtime and maximize productivity.
How Do Refrigeration Units Benefit Retail and Grocery Stores?
Refrigeration units sourced from China are vital for supermarkets and grocery stores, significantly improving the shelf life of perishable goods. These appliances help maintain optimal temperatures, ensuring food safety and enhancing customer satisfaction. International B2B buyers should consider energy efficiency and reliability, particularly during peak shopping hours, to ensure their refrigeration solutions meet both operational and sustainability goals.
Why Are Portable Cooking Appliances Important for Catering Services?
Catering services benefit greatly from portable cooking appliances, enabling flexibility and speed in food preparation at various events. These appliances allow caterers to efficiently serve large groups without compromising on quality. Buyers looking to source these appliances must focus on compact designs that are easy to transport, ensuring they can meet diverse client needs while maintaining high service standards.
How Are Specialized Kitchen Appliances Used in Healthcare Facilities?
In healthcare facilities, specialized kitchen appliances address dietary needs, ensuring compliance with nutritional standards for patients. Equipment such as steamers and food blenders help prepare tailored meals that cater to specific health requirements. For international buyers, especially from regions like Africa and the Middle East, adherence to hygiene standards and functionality is paramount, as it directly impacts patient satisfaction and health outcomes.
Related Video: Industrial Control Panel Basics
3 Common User Pain Points for ‘kitchen appliances china’ & Their Solutions
Scenario 1: Navigating Quality Assurance in Kitchen Appliances from China
The Problem: International B2B buyers often face the challenge of ensuring the quality and reliability of kitchen appliances sourced from China. With the vast number of manufacturers, varying quality standards, and the risk of counterfeit products, buyers may find themselves uncertain about the durability and performance of the appliances they intend to purchase. This concern is heightened in regions like Africa and South America, where local market expectations may differ significantly from those in China.
The Solution: To mitigate quality concerns, B2B buyers should implement a multi-step sourcing strategy. First, it is crucial to conduct thorough research on potential suppliers, focusing on their certifications, past client reviews, and production capabilities. Engaging with third-party quality assurance companies can help in assessing the manufacturing processes and product standards before placing large orders. Additionally, buyers should consider visiting factories or participating in trade shows in China to establish personal relationships with manufacturers. This direct interaction not only builds trust but also allows for more tailored specifications and quality controls to be integrated into the manufacturing process.
Scenario 2: Managing Logistics and Supply Chain Challenges
The Problem: B2B buyers often encounter logistical hurdles when importing kitchen appliances from China, including shipping delays, high freight costs, and unpredictable customs regulations. These challenges can lead to increased operational costs and inventory shortages, ultimately affecting customer satisfaction and business reputation. Buyers in the Middle East and Europe might face specific regional logistics issues that complicate timely deliveries.
The Solution: To streamline logistics, buyers should engage with reputable freight forwarders who specialize in international shipping and understand the intricacies of customs regulations in their specific regions. Establishing a clear communication channel with suppliers regarding production timelines can also help in aligning shipping schedules. Utilizing technology, such as supply chain management software, enables real-time tracking of shipments, providing visibility into potential delays. Furthermore, considering alternative shipping methods, such as sea freight for bulk orders or air freight for urgent needs, can offer flexibility and cost-effectiveness in managing supply chain logistics.
Scenario 3: Overcoming Cultural and Communication Barriers
The Problem: Cultural differences and language barriers can complicate negotiations and communications between international buyers and Chinese manufacturers. Misunderstandings regarding product specifications, payment terms, and delivery schedules can lead to frustration and potentially costly errors. Buyers from diverse regions, such as Africa and Europe, might experience varying levels of familiarity with Chinese business practices, which can exacerbate these challenges.
The Solution: To bridge cultural gaps, B2B buyers should invest in hiring bilingual staff or work with local intermediaries who have experience in Chinese business culture. Providing clear, written specifications and using visual aids can enhance understanding and reduce the risk of miscommunication. Additionally, setting up regular check-ins and updates with suppliers can foster a collaborative relationship, ensuring both parties are aligned on expectations. Participating in cross-cultural training programs can also equip buyers with the skills necessary to navigate negotiations effectively, ultimately leading to more successful partnerships with Chinese manufacturers.
Strategic Material Selection Guide for kitchen appliances china
When selecting materials for kitchen appliances manufactured in China, international B2B buyers must consider the unique properties and implications of various materials. This section analyzes four common materials used in kitchen appliances, providing insights into their performance, advantages, limitations, and considerations for buyers from diverse regions, including Africa, South America, the Middle East, and Europe.
What Are the Key Properties of Stainless Steel in Kitchen Appliances?
Stainless steel is a popular choice for kitchen appliances due to its excellent corrosion resistance, high-temperature tolerance, and aesthetic appeal. It typically withstands temperatures up to 800°C and is resistant to rust and staining, making it ideal for environments that experience moisture and heat.
Pros: Stainless steel is highly durable, easy to clean, and has a modern look that appeals to consumers. It is also recyclable, contributing to sustainability efforts.
Cons: The main drawback is its relatively high cost compared to other materials. Additionally, it can be prone to scratching and may require regular maintenance to keep it looking pristine.
Impact on Application: Stainless steel is compatible with various media, including water and food products, making it suitable for refrigerators, ovens, and dishwashers.
Considerations for Buyers: Compliance with international standards such as ASTM and DIN is essential. Buyers should also be aware of local preferences for finishes and grades of stainless steel, as these can vary by region.
How Does Plastic Compare as a Material for Kitchen Appliances?
Plastic is often used in kitchen appliances for components such as handles, knobs, and internal parts. It is lightweight and can be molded into various shapes, offering design flexibility.
Pros: Plastic is generally low-cost and provides excellent insulation properties. It is also resistant to corrosion and can be produced in a variety of colors and finishes.
Cons: The main limitation is its lower durability compared to metals; it can warp or degrade over time, especially when exposed to high temperatures.
Impact on Application: Plastic is suitable for non-load-bearing applications and is often used in appliances that do not require high structural integrity.
Considerations for Buyers: Buyers should ensure that the plastic used meets safety standards, particularly regarding food contact. Compliance with regulations such as REACH in Europe is also crucial.
What Are the Advantages of Glass in Kitchen Appliances?
Glass is increasingly used in kitchen appliances, especially for oven doors, cooktops, and storage containers. It offers a sleek appearance and is non-reactive, making it safe for food storage.
Pros: Glass is aesthetically pleasing, easy to clean, and resistant to staining. It can also withstand high temperatures, making it suitable for cooking applications.
Cons: The primary disadvantage is its fragility; glass can break or shatter if not handled properly. Additionally, it can be heavier than other materials, which may affect the overall weight of the appliance.
Impact on Application: Glass is ideal for applications where visibility is important, such as oven doors, allowing users to monitor cooking without opening the door.
Considerations for Buyers: Buyers should verify that the glass used is tempered or otherwise treated for safety. Compliance with international safety standards is essential, especially in regions with strict regulations.
How Does Aluminum Perform in Kitchen Appliances?
Aluminum is another common material used in kitchen appliances, particularly for components like heat exchangers and cookware. It has excellent thermal conductivity and is lightweight.
Pros: Aluminum is cost-effective and offers good resistance to corrosion when anodized. It is also lightweight, which can reduce shipping costs.
Cons: It can be less durable than stainless steel and may warp under high heat unless properly treated.
Impact on Application: Aluminum is suitable for applications requiring good thermal management, such as cookware and heating elements.
Considerations for Buyers: Buyers should ensure that aluminum products comply with local regulations regarding food safety and recycling. The anodization process should also meet industry standards to enhance durability.
Summary Table of Material Selection for Kitchen Appliances
Material | Typical Use Case for kitchen appliances china | Key Advantage | Key Disadvantage/Limitation | Relative Cost (Low/Med/High) |
---|---|---|---|---|
Stainless Steel | Ovens, refrigerators, dishwashers | Corrosion resistance, durability | High cost, prone to scratching | High |
Plastic | Handles, knobs, internal components | Lightweight, low-cost | Lower durability, can warp | Low |
Glass | Oven doors, cooktops, storage containers | Aesthetic appeal, easy to clean | Fragile, heavier than alternatives | Medium |
Aluminum | Cookware, heat exchangers | Lightweight, good thermal conductivity | Less durable, may warp under heat | Medium |
This strategic material selection guide provides international B2B buyers with critical insights into material properties, advantages, and limitations, facilitating informed purchasing decisions for kitchen appliances sourced from China.
In-depth Look: Manufacturing Processes and Quality Assurance for kitchen appliances china
What Are the Main Stages of Manufacturing Kitchen Appliances in China?
The manufacturing of kitchen appliances in China involves several critical stages, each requiring specific techniques and attention to detail. Understanding these stages is essential for B2B buyers to ensure that they select reliable suppliers.
Material Preparation: What Goes Into Kitchen Appliance Manufacturing?
The first stage in the manufacturing process involves the careful selection and preparation of raw materials. Common materials used include stainless steel, plastic, and various alloys. Suppliers typically source these materials from both domestic and international markets. During this stage, materials are inspected for quality to ensure they meet industry standards.
Key techniques in this phase include:
- Material Testing: Conducting tensile strength and corrosion resistance tests to ensure durability.
- Cutting and Shaping: Using CNC machines for precision cutting, which reduces waste and enhances product accuracy.
How Are Kitchen Appliances Formed?
Once materials are prepared, they undergo forming processes that shape them into usable components. This can include processes such as:
- Stamping: Used for metal parts, where sheets of metal are cut and formed into specific shapes.
- Injection Molding: Predominantly used for plastic components, this process involves injecting molten plastic into molds to create the desired shapes.
These techniques are crucial for achieving uniformity and consistency in production, which are vital for maintaining high standards of quality.
What Happens During Assembly of Kitchen Appliances?
After forming, the components are assembled. This stage often involves both manual and automated processes. Key assembly techniques include:
- Automated Assembly Lines: These lines use robotics to enhance speed and precision, minimizing human error.
- Manual Assembly: While more labor-intensive, this method allows for careful inspection and adjustment of components.
Quality checks during assembly include visual inspections and functional tests to ensure that each appliance operates correctly before moving on to the finishing stage.
How Are Kitchen Appliances Finished?
Finishing processes enhance the aesthetic and functional aspects of kitchen appliances. This can involve several techniques:
- Surface Treatment: Such as polishing, painting, or powder coating, which protects against corrosion and improves appearance.
- Final Assembly: This includes adding any additional features, such as knobs, displays, or wiring.
Quality assurance in this stage is critical, as it directly impacts the product’s marketability.
What Quality Assurance Standards Apply to Kitchen Appliances?
Quality assurance is vital in ensuring that kitchen appliances meet both safety and performance standards. International standards such as ISO 9001 are commonly referenced, ensuring that manufacturers adhere to a quality management system. Additionally, industry-specific certifications like CE (for Europe) and UL (for North America) are essential for compliance in various markets.
How Are Quality Control Checkpoints Implemented?
Quality control (QC) is integrated throughout the manufacturing process, with several key checkpoints established:
- Incoming Quality Control (IQC): This initial stage checks raw materials for compliance with specifications before they enter production.
- In-Process Quality Control (IPQC): Conducted during the manufacturing process, this involves regular checks at various stages to ensure that quality is maintained.
- Final Quality Control (FQC): At this stage, finished products undergo rigorous testing to confirm they meet all functional and safety standards.
Common testing methods include:
- Performance Testing: Ensuring that appliances operate as intended under normal conditions.
- Safety Testing: Identifying any potential hazards associated with the appliance’s use.
How Can B2B Buyers Verify Supplier Quality Control?
For international B2B buyers, especially those from regions like Africa, South America, the Middle East, and Europe, verifying a supplier’s quality control practices is crucial to mitigate risks. Here are several actionable steps:
What Auditing Practices Should Buyers Use?
Conducting audits is one of the most effective ways to assess a supplier’s quality control processes. Buyers can:
- Perform On-site Audits: Visiting the manufacturing facility allows buyers to observe processes firsthand and ask questions about quality practices.
- Request Audit Reports: Suppliers should provide documentation of past audits, including any corrective actions taken.
How Do Third-Party Inspections Work?
Engaging third-party inspection services can provide an unbiased assessment of a supplier’s quality control processes. These services typically offer:
- Pre-shipment Inspections: Evaluating the final products before they are shipped to ensure they meet specified standards.
- Random Sampling: Inspecting a random selection of products to verify that the entire batch adheres to quality requirements.
What Are the Nuances of Quality Control for International B2B Buyers?
International buyers must also be aware of the nuances in quality control that may differ by region:
- Certification Requirements: Different markets have unique certification requirements. For instance, appliances exported to Europe must comply with CE standards, while those going to the U.S. may need UL certification.
- Cultural Differences: Approaches to quality assurance can vary significantly between cultures, affecting how inspections and quality checks are conducted.
Understanding these nuances helps buyers make informed decisions and choose suppliers that align with their quality standards.
Conclusion: Maximizing Quality Assurance in Kitchen Appliance Manufacturing
In summary, the manufacturing processes and quality assurance practices for kitchen appliances in China are complex and multifaceted. By understanding each stage of production, from material preparation to final quality checks, B2B buyers can better assess potential suppliers. Implementing thorough verification processes, including audits and third-party inspections, will further ensure that the products meet the necessary international standards, ultimately leading to successful business relationships and satisfied customers.
Practical Sourcing Guide: A Step-by-Step Checklist for ‘kitchen appliances china’
The following practical sourcing guide provides a comprehensive checklist for international B2B buyers seeking to procure kitchen appliances from China. This guide aims to streamline your sourcing process and ensure you make informed decisions.
Step 1: Define Your Technical Specifications
Establishing clear technical specifications is vital for successful procurement. Determine the type of kitchen appliances you need, such as blenders, microwaves, or refrigerators, and outline their features, dimensions, and performance standards. This clarity helps in communicating effectively with suppliers and ensures you receive products that meet your requirements.
Step 2: Conduct Market Research
Understanding the current market landscape is essential. Research trends in kitchen appliances, including popular brands, emerging technologies, and pricing structures. Utilize online resources, trade reports, and industry publications to gather insights on what competitors are offering and what consumers in your target market are looking for.
Step 3: Evaluate Potential Suppliers
Thoroughly vet potential suppliers to mitigate risks. Start by requesting company profiles, product catalogs, and case studies. Look for suppliers with a proven track record in your industry, and ask for references from businesses similar to yours. Assess their reputation through online reviews and industry ratings.
- Check for trade certifications: Ensure that suppliers have relevant certifications, such as ISO 9001, which indicates quality management systems.
- Verify production capabilities: Inquire about their manufacturing processes, capacity, and technology used to meet your volume needs.
Step 4: Request Samples
Before making a bulk order, request samples of the products. This step allows you to evaluate the quality, design, and functionality of the kitchen appliances firsthand. Ensure that the samples meet your defined specifications and are compliant with safety standards applicable in your region.
Step 5: Negotiate Terms and Pricing
Effective negotiation can lead to better pricing and terms. Discuss payment options, lead times, and shipping arrangements. It’s essential to be clear about your expectations regarding minimum order quantities and delivery schedules. Compare offers from multiple suppliers to ensure competitive pricing.
Step 6: Understand Import Regulations
Familiarize yourself with import regulations and tariffs. Each country has specific rules regarding the importation of kitchen appliances, including safety standards and certifications. Consult local regulatory bodies or logistics experts to ensure compliance and avoid unexpected fees or delays.
Step 7: Establish a Quality Control Process
Implementing a quality control process is crucial for ensuring product standards. Define quality benchmarks and establish procedures for inspecting products upon arrival. Consider hiring third-party inspection services in China to verify that the appliances meet your specifications before shipment.
By following this checklist, international B2B buyers can navigate the complexities of sourcing kitchen appliances from China with greater confidence, ensuring they find reliable suppliers and high-quality products tailored to their needs.
Comprehensive Cost and Pricing Analysis for kitchen appliances china Sourcing
When sourcing kitchen appliances from China, understanding the comprehensive cost structure and pricing analysis is crucial for international B2B buyers. This analysis helps in making informed decisions that can significantly impact profitability and operational efficiency.
What Are the Key Cost Components in Kitchen Appliance Sourcing?
-
Materials: The choice of materials greatly influences the overall cost. High-quality stainless steel or eco-friendly materials may increase initial expenses but can lead to better durability and customer satisfaction.
-
Labor: Labor costs in China can vary depending on the region and the complexity of the manufacturing process. Skilled labor may command higher wages, impacting the final price of kitchen appliances.
-
Manufacturing Overhead: This includes factory costs such as utilities, equipment depreciation, and administrative expenses. Buyers should inquire about how these costs are factored into the pricing.
-
Tooling: Custom tooling for specific designs or functions can be a significant upfront investment. Understanding tooling costs is essential for buyers looking for unique or specialized products.
-
Quality Control (QC): Implementing rigorous QC processes ensures product reliability but may add to the cost. Buyers should weigh the benefits of higher QC standards against potential price increases.
-
Logistics: Shipping and logistics costs can fluctuate based on distance, volume, and chosen transportation methods. International buyers need to account for these expenses in their total cost analysis.
-
Margin: Suppliers typically add a profit margin to the manufacturing cost, which can vary widely based on market conditions, competition, and the supplier’s positioning.
How Do Price Influencers Impact Kitchen Appliance Costs?
-
Volume/MOQ: Minimum Order Quantities (MOQ) can significantly affect pricing. Larger orders often result in lower per-unit costs, making volume negotiations a key strategy for cost savings.
-
Specifications and Customization: Unique specifications or customized features can increase costs. Buyers should clearly communicate their needs to avoid unexpected price hikes.
-
Materials and Quality Certifications: Sourcing appliances with specific certifications (like CE or ISO) may lead to higher costs but can enhance marketability and compliance in certain regions.
-
Supplier Factors: The reputation and reliability of suppliers play a crucial role. Established suppliers may charge higher prices due to their experience and quality assurance processes.
-
Incoterms: The choice of Incoterms can impact the total cost. Different terms dictate who is responsible for shipping, insurance, and customs, affecting the overall pricing structure.
What Are Some Effective Buyer Tips for Negotiation and Cost Efficiency?
-
Negotiate Wisely: Leverage your purchasing volume to negotiate better pricing terms. Building a long-term relationship with suppliers can also yield discounts and favorable conditions.
-
Consider Total Cost of Ownership (TCO): Evaluate not just the purchase price but also maintenance, operational costs, and lifespan when assessing appliances. This approach helps in identifying the best value for investment.
-
Understand Pricing Nuances: International buyers should be aware of currency fluctuations and their effects on pricing. It’s advisable to lock in prices when favorable rates are available.
-
Stay Informed About Market Trends: Regularly monitor market conditions and supplier performance to adapt purchasing strategies accordingly. This can include staying updated on new materials or technologies that could influence pricing.
-
Request Detailed Quotations: Ensure that quotes include a breakdown of all costs involved, from materials to logistics. This transparency allows for better comparison between suppliers and aids in negotiation.
Conclusion
Navigating the complexities of cost and pricing analysis for kitchen appliances sourced from China requires diligence and strategic planning. By understanding the key cost components, price influencers, and employing effective negotiation tactics, international B2B buyers can optimize their procurement processes and enhance their market competitiveness. Always remember to seek indicative prices and adjust your budget accordingly, as prices can vary based on market conditions and specific requirements.
Alternatives Analysis: Comparing kitchen appliances china With Other Solutions
Understanding Alternatives to Kitchen Appliances from China
In the competitive landscape of kitchen appliances, international B2B buyers must consider various alternatives to those sourced from China. Each option brings its own set of advantages and challenges, influencing factors such as performance, cost, ease of implementation, and maintenance. This section provides a comparative analysis to aid buyers in making informed decisions tailored to their specific needs.
Comparison Table of Kitchen Appliances
Comparison Aspect | Kitchen Appliances China | Alternative 1: European Appliances | Alternative 2: Local Manufacturers |
---|---|---|---|
Performance | High quality, diverse range | Excellent build quality, energy-efficient | Variable quality, often budget-friendly |
Cost | Generally lower prices | Higher price points | Competitive pricing, depending on region |
Ease of Implementation | Standardized processes | Comprehensive installation support | Varies, often requiring local knowledge |
Maintenance | Availability of parts can be inconsistent | Strong support network, easy access to parts | Local service may be limited but often faster |
Best Use Case | High-volume commercial use | Upscale kitchens, energy-conscious buyers | Small businesses, budget-sensitive buyers |
In-Depth Analysis of Alternatives
What Are the Advantages of European Appliances?
European kitchen appliances are renowned for their superior build quality and energy efficiency. Brands from countries like Germany and Italy emphasize innovation and sustainability, making them ideal for upscale kitchens where performance is paramount. However, the higher price point can be a barrier for some buyers, particularly in emerging markets. Additionally, while installation support is robust, the initial investment might not align with all business models, especially for smaller enterprises.
How Do Local Manufacturers Compare?
Local kitchen appliance manufacturers can offer competitive pricing and cater to specific regional needs, making them appealing to budget-sensitive buyers. They often provide quicker service and support since they are familiar with local market conditions. However, the quality can vary significantly, and buyers may encounter challenges in sourcing parts and warranty service. Local manufacturers are well-suited for small businesses that prioritize affordability and immediate support over long-term durability.
Conclusion: How to Choose the Right Kitchen Appliance Solution
When deciding between kitchen appliances from China, European brands, or local manufacturers, B2B buyers should assess their specific operational needs, budget constraints, and long-term business goals. Consider performance requirements and the total cost of ownership, including maintenance and support. By carefully evaluating these alternatives, international buyers can find the most suitable solution that aligns with their strategic objectives and market demands.
Essential Technical Properties and Trade Terminology for kitchen appliances china
What Are the Essential Technical Properties of Kitchen Appliances from China?
When sourcing kitchen appliances from China, understanding the key technical properties is vital for ensuring quality and compatibility with market standards. Below are some critical specifications that international B2B buyers should consider:
-
Material Grade
– Kitchen appliances are typically made from stainless steel, plastic, or glass. The material grade, often indicated by standards like ASTM or ISO, determines durability, corrosion resistance, and safety for food contact. High-grade materials can lead to longer-lasting appliances, which is crucial for maintaining customer satisfaction and minimizing returns. -
Energy Efficiency Rating
– Energy efficiency is an essential property, especially in markets with strict energy regulations. Appliances are often rated using labels like Energy Star or similar local certifications. An efficient appliance not only reduces operational costs for end-users but also aligns with global sustainability goals, making it an attractive feature for buyers. -
Tolerance Levels
– Tolerance refers to the allowable deviation in dimensions during manufacturing. In kitchen appliances, precise tolerances ensure proper fit and function, which is critical for components like hinges, seals, and electrical connections. Understanding tolerance specifications helps buyers mitigate risks associated with assembly and performance failures. -
Safety Certifications
– Compliance with safety standards such as CE, UL, or RoHS is crucial for kitchen appliances. These certifications indicate that the products meet specific safety and environmental guidelines. For B2B buyers, ensuring that appliances are certified can prevent legal issues and enhance marketability. -
Capacity and Size Specifications
– Dimensions and capacity metrics are vital for appliances like ovens, refrigerators, and dishwashers. Buyers must ensure that the products fit the intended spaces in commercial kitchens or residential settings. Accurately understanding these specifications can lead to better inventory management and customer satisfaction.
What Common Trade Terminology Should Buyers Know When Sourcing Kitchen Appliances?
Familiarity with industry jargon can streamline communication and negotiation processes for B2B buyers. Below are some common terms relevant to sourcing kitchen appliances from China:
-
OEM (Original Equipment Manufacturer)
– An OEM is a company that produces parts or equipment that may be marketed by another manufacturer. For buyers, working with OEMs can lead to customized products tailored to specific market needs, enhancing brand identity and customer loyalty. -
MOQ (Minimum Order Quantity)
– MOQ refers to the smallest quantity of a product that a supplier is willing to sell. Understanding MOQ is crucial for budgeting and inventory planning. Buyers should negotiate MOQs that align with their sales forecasts to minimize excess inventory costs. -
RFQ (Request for Quotation)
– An RFQ is a document sent to suppliers to request pricing and terms for specific products. It is an essential step in the procurement process, helping buyers compare offers and make informed purchasing decisions. -
Incoterms (International Commercial Terms)
– Incoterms define the responsibilities of buyers and sellers in international transactions, including shipping costs, risk, and insurance. Familiarity with these terms helps buyers understand their obligations and negotiate better shipping arrangements. -
Lead Time
– Lead time refers to the time taken from placing an order to delivery. Understanding lead times is essential for managing supply chain operations and ensuring that products are available when needed, particularly in seasonal markets. -
Warranty and After-Sales Support
– Warranty terms specify the duration and conditions under which a product can be repaired or replaced. Knowledge of warranty policies and after-sales support options can significantly influence buyer confidence and long-term relationships with suppliers.
By grasping these technical properties and trade terms, international B2B buyers can make informed decisions when sourcing kitchen appliances from China, ultimately enhancing their procurement strategies and market competitiveness.
Navigating Market Dynamics and Sourcing Trends in the kitchen appliances china Sector
What Are the Current Market Dynamics and Key Trends in the Kitchen Appliances Sector from China?
The kitchen appliances sector in China is witnessing rapid evolution, driven by both domestic demand and international market dynamics. A key global driver is the increasing consumer preference for smart home technologies, which has pushed manufacturers to innovate. Smart kitchen appliances that offer connectivity features, energy efficiency, and user-friendly interfaces are gaining traction. Additionally, the rise of e-commerce has transformed sourcing strategies, allowing international buyers from Africa, South America, the Middle East, and Europe to access a broader range of products with ease.
Another significant trend is the focus on energy-efficient appliances, spurred by growing environmental awareness and regulations. Countries are increasingly prioritizing products that comply with energy standards, presenting opportunities for B2B buyers to source sustainable and efficient kitchen appliances. The demand for customization is also on the rise, with buyers seeking tailored solutions that cater to local tastes and preferences. This trend is particularly relevant for buyers in diverse markets such as Nigeria and the UAE, where cultural influences shape kitchen design and appliance selection.
How Is Sustainability Influencing B2B Sourcing Decisions in Kitchen Appliances?
Sustainability has become a pivotal consideration for B2B buyers in the kitchen appliances sector. The environmental impact of manufacturing processes and product lifecycle is under scrutiny, leading to a demand for ethical sourcing practices. Buyers are increasingly evaluating suppliers based on their commitment to sustainability, which includes responsible sourcing of materials and adherence to environmental regulations.
Certifications such as Energy Star and ISO 14001 are becoming essential benchmarks for buyers seeking to ensure their suppliers meet environmental standards. Moreover, the use of recyclable materials and eco-friendly manufacturing processes is gaining importance. This shift not only helps in reducing the carbon footprint but also appeals to consumers who are increasingly choosing brands that align with their values. For international buyers, particularly those in emerging markets, understanding these sustainability trends can provide a competitive edge in sourcing kitchen appliances that resonate with environmentally conscious consumers.
How Has the Kitchen Appliances Market Evolved Over Time?
The evolution of the kitchen appliances market in China can be traced back several decades, from traditional cooking methods to the integration of modern technologies. Initially dominated by basic appliances, the market has expanded significantly due to urbanization and rising disposable incomes. The late 1990s and early 2000s marked a turning point as global brands entered the Chinese market, introducing advanced technologies and premium products.
As consumer preferences evolved, so did the focus on design and functionality. The introduction of smart technologies in recent years has further revolutionized the sector, making appliances more intuitive and integrated into the digital lifestyle. This historical context is crucial for B2B buyers to understand current trends and anticipate future developments in the kitchen appliances sector, particularly when sourcing from China.
In summary, navigating the kitchen appliances market in China requires an understanding of current dynamics, sustainability practices, and historical evolution. By leveraging these insights, international B2B buyers can make informed decisions that align with market trends and consumer preferences.
Frequently Asked Questions (FAQs) for B2B Buyers of kitchen appliances china
-
How can I effectively source kitchen appliances from China for my business?
To effectively source kitchen appliances from China, start by identifying reliable suppliers through platforms like Alibaba or Global Sources. Verify their credentials, check reviews, and request samples to assess quality. Establish clear communication regarding your specifications, quality expectations, and lead times. Consider visiting trade shows in China to meet suppliers face-to-face and build relationships. Additionally, engage with local trade associations for insights into the market and potential partners. -
What are the key factors to consider when vetting suppliers of kitchen appliances in China?
When vetting suppliers, focus on their production capacity, quality certifications (like ISO 9001), and compliance with international standards. Request references from other clients and evaluate their response times and customer service. It’s also crucial to assess their financial stability and ability to handle your order volume. Conducting a factory audit, if feasible, can provide insights into their operational capabilities and manufacturing processes. -
What is the typical minimum order quantity (MOQ) for kitchen appliances sourced from China?
The MOQ for kitchen appliances can vary significantly depending on the supplier and product type. Generally, it ranges from 50 to 1,000 units. Larger manufacturers may offer lower MOQs for popular items, while specialized or custom products may require higher quantities. Always negotiate the MOQ based on your business needs, and consider consolidating orders to meet MOQ requirements without overextending your inventory. -
What payment terms should I expect when sourcing kitchen appliances from China?
Payment terms often include options like T/T (telegraphic transfer), L/C (letter of credit), or PayPal. Many suppliers may request a 30% deposit upfront and the remaining 70% before shipping. Be cautious of suppliers that ask for full payment in advance. It’s advisable to use secure payment methods and consider escrow services for larger transactions to protect your investment until the goods are received and verified. -
How can I ensure quality assurance for kitchen appliances sourced from China?
To ensure quality assurance, establish clear specifications and standards with your supplier before production begins. Implement a quality control process, which may include pre-production samples and in-line inspections. Hiring third-party inspection services can further verify that the appliances meet your requirements before shipment. Consider building a relationship with a local quality assurance firm that understands the Chinese manufacturing landscape. -
What logistics considerations should I keep in mind when importing kitchen appliances from China?
Logistics involve selecting a reliable freight forwarder who understands international shipping regulations and can handle customs clearance. Be aware of shipping costs, which can significantly impact your overall budget. Depending on your location, choose between air freight for speed or sea freight for cost-effectiveness. Ensure that your supplier provides all necessary documentation for smooth customs processing and consider insurance to protect against potential shipping damages. -
How can I customize kitchen appliances according to my market needs?
Customization options can vary by supplier, but many manufacturers in China are open to tailoring products to meet specific market demands. Discuss your requirements upfront, including design, features, and branding. Be prepared to provide prototypes or detailed specifications. Some suppliers may require a higher MOQ for customized products, so factor this into your planning. Collaborating closely with the supplier during the design process can help ensure the final product aligns with your expectations. -
What are the common challenges B2B buyers face when sourcing kitchen appliances from China, and how can I overcome them?
Common challenges include communication barriers, quality discrepancies, and delays in shipping. To overcome these issues, maintain regular communication with your supplier and use clear, concise language. Utilize technology like video calls for real-time discussions. Implement a robust quality control plan to address potential discrepancies early. Lastly, build a buffer into your timeline to account for unexpected delays in production or logistics, ensuring your supply chain remains resilient.
Important Disclaimer & Terms of Use
⚠️ Important Disclaimer
The information provided in this guide, including content regarding manufacturers, technical specifications, and market analysis, is for informational and educational purposes only. It does not constitute professional procurement advice, financial advice, or legal advice.
While we have made every effort to ensure the accuracy and timeliness of the information, we are not responsible for any errors, omissions, or outdated information. Market conditions, company details, and technical standards are subject to change.
B2B buyers must conduct their own independent and thorough due diligence before making any purchasing decisions. This includes contacting suppliers directly, verifying certifications, requesting samples, and seeking professional consultation. The risk of relying on any information in this guide is borne solely by the reader.
Strategic Sourcing Conclusion and Outlook for kitchen appliances china
What Are the Key Takeaways for B2B Buyers in Kitchen Appliances from China?
Strategic sourcing in the kitchen appliances sector from China presents an array of opportunities for international B2B buyers, particularly those from Africa, South America, the Middle East, and Europe. By leveraging China’s extensive manufacturing capabilities, businesses can access a diverse range of products that combine quality with competitive pricing. Key takeaways include the importance of establishing strong supplier relationships, understanding local regulations, and conducting thorough due diligence to mitigate risks associated with international trade.
How Can Strategic Sourcing Enhance Your Business?
Investing time in strategic sourcing not only helps in securing the best products but also fosters long-term partnerships that can lead to innovation and improved supply chain efficiencies. By focusing on sustainability and compliance, buyers can enhance their brand reputation and align with global trends towards eco-friendly practices.
What Should B2B Buyers Do Next?
Looking ahead, international B2B buyers are encouraged to actively engage with Chinese manufacturers, utilizing platforms that facilitate communication and transparency. This proactive approach will ensure that businesses can adapt to market changes and consumer demands swiftly. By embracing these strategies, buyers can position themselves for success in the ever-evolving kitchen appliances market.