The Ultimate Guide to Knife Sharpener Manufacturer (2025)
Introduction: Navigating the Global Market for knife sharpener manufacturer
In today’s competitive landscape, sourcing high-quality knife sharpeners can pose significant challenges for international B2B buyers. The knife sharpener manufacturing sector is vast, with diverse options ranging from manual to electric sharpeners, each designed for specific applications in culinary, industrial, and retail settings. Understanding the nuances of these products, alongside effective supplier vetting and cost considerations, is essential for making informed purchasing decisions.
This comprehensive guide serves as an invaluable resource for B2B buyers, particularly those from Africa, South America, the Middle East, and Europe, including key markets like South Africa and Spain. It delves into various types of knife sharpeners, examining their applications across different industries and the technological advancements shaping the market.
Moreover, the guide emphasizes best practices for supplier evaluation, ensuring that buyers can identify reputable manufacturers who meet their quality and compliance standards. It also addresses cost factors, providing insights into pricing strategies that can help businesses optimize their budgets. By equipping buyers with actionable knowledge, this guide empowers them to navigate the global market effectively, ensuring they choose the right knife sharpener solutions that align with their operational needs and quality expectations.
Understanding knife sharpener manufacturer Types and Variations
Type Name | Key Distinguishing Features | Primary B2B Applications | Brief Pros & Cons for Buyers |
---|---|---|---|
Manual Knife Sharpeners | Simple, portable, and often hand-operated tools | Small restaurants, home chefs | Pros: Cost-effective, easy to use. Cons: Requires skill and time. |
Electric Knife Sharpeners | Powered devices that automate the sharpening process | Large food service operations | Pros: Fast and consistent results. Cons: Higher initial investment. |
Professional Knife Sharpeners | Heavy-duty, often used in commercial settings | Culinary schools, butcher shops | Pros: High precision and durability. Cons: Requires training and maintenance. |
Diamond Knife Sharpeners | Utilize diamond-coated surfaces for sharpening | High-end restaurants, catering | Pros: Long-lasting, effective on all blade types. Cons: More expensive than traditional options. |
Specialty Knife Sharpeners | Designed for specific types of knives (e.g., serrated) | Specialty kitchens, knife retailers | Pros: Tailored results for unique knives. Cons: Limited versatility for general use. |
What are the Characteristics of Manual Knife Sharpeners?
Manual knife sharpeners are typically compact and easy to use, making them ideal for small restaurants or home chefs. They often require a bit of skill to achieve the desired sharpness, as users must manually guide the knife through the sharpening mechanism. Buyers should consider the material quality and design, as these factors can affect the longevity and effectiveness of the sharpener.
How Do Electric Knife Sharpeners Benefit Large Operations?
Electric knife sharpeners are designed for efficiency and speed, making them suitable for large food service operations. These devices automate the sharpening process, ensuring consistent results across multiple knives in a short amount of time. While the initial investment is higher, the time saved and the uniformity of the sharpening can justify the cost for businesses that rely on quick service and high-quality kitchen tools.
What Makes Professional Knife Sharpeners Ideal for Commercial Use?
Professional knife sharpeners are built for heavy-duty use and can handle a wide range of knife types, making them essential in culinary schools and butcher shops. These sharpeners offer precision and durability, catering to the demands of professional chefs. However, they often require specialized training to operate effectively, and buyers should factor in maintenance costs when considering these products.
Why Choose Diamond Knife Sharpeners for High-End Restaurants?
Diamond knife sharpeners feature diamond-coated surfaces that provide superior sharpening capabilities. They are effective on various blade types, making them a favorite in high-end restaurants and catering businesses. Although they tend to be more expensive than traditional sharpeners, their longevity and effectiveness can result in cost savings over time, especially for establishments that prioritize quality.
What are the Advantages of Specialty Knife Sharpeners?
Specialty knife sharpeners are designed for specific types of knives, such as serrated or fillet knives, making them a valuable tool for specialty kitchens and knife retailers. These sharpeners provide tailored results that enhance the performance of unique blade types. However, their limited versatility means they may not be suitable for general knife sharpening needs, which is an essential consideration for B2B buyers looking for multifunctional solutions.
Related Video: How to Sharpen Your Knives with the Spyderco Tri-Angle Sharpmaker Knife Sharpener
Key Industrial Applications of knife sharpener manufacturer
Industry/Sector | Specific Application of Knife Sharpener Manufacturer | Value/Benefit for the Business | Key Sourcing Considerations for this Application |
---|---|---|---|
Food Service | Commercial Kitchen Knife Sharpening | Ensures optimal performance and safety of kitchen knives, improving food preparation efficiency. | Quality of sharpening mechanism, durability, and ease of use. |
Manufacturing | Tool and Equipment Maintenance | Extends the lifespan of cutting tools, reducing downtime and maintenance costs. | Compatibility with existing tools, speed of sharpening, and precision. |
Agriculture | Agricultural Equipment Sharpening | Enhances the efficiency of farming tools like sickles and shears, leading to better crop yields. | Ability to handle various tool sizes, portability, and ease of operation. |
Retail | Knife Sharpening Services in Stores | Attracts customers seeking maintenance services, increasing foot traffic and sales. | Training for staff, service speed, and customer satisfaction guarantees. |
Hospitality | Catering Equipment Maintenance | Keeps catering knives and tools sharp, ensuring high-quality service and food presentation. | Customization options, service agreements, and training for staff. |
How is Knife Sharpener Manufacturing Applied in the Food Service Industry?
In the food service industry, knife sharpeners are essential for maintaining the performance of kitchen knives. Regularly sharpened knives not only enhance safety by reducing the risk of accidents but also streamline food preparation processes. Buyers in this sector should prioritize sharpener durability and ease of use, ensuring that staff can quickly and efficiently maintain their tools without excessive downtime.
What Role Does Knife Sharpening Play in Manufacturing?
In manufacturing, knife sharpeners are crucial for maintaining the efficacy of cutting tools used in production lines. Sharp tools reduce the risk of errors and improve the quality of finished products, leading to cost savings and increased productivity. When sourcing sharpeners, businesses should consider compatibility with existing tools, the speed of sharpening, and the precision offered by the equipment to ensure seamless integration into their maintenance routines.
How Does Knife Sharpening Benefit the Agriculture Sector?
Agricultural tools, such as sickles and shears, require regular sharpening to perform effectively. A reliable knife sharpener can greatly enhance the efficiency of these tools, contributing to better crop yields and reduced labor time. For international buyers, it’s important to assess the sharpener’s ability to handle various tool sizes and its portability, especially in remote farming locations where access to sharpening services may be limited.
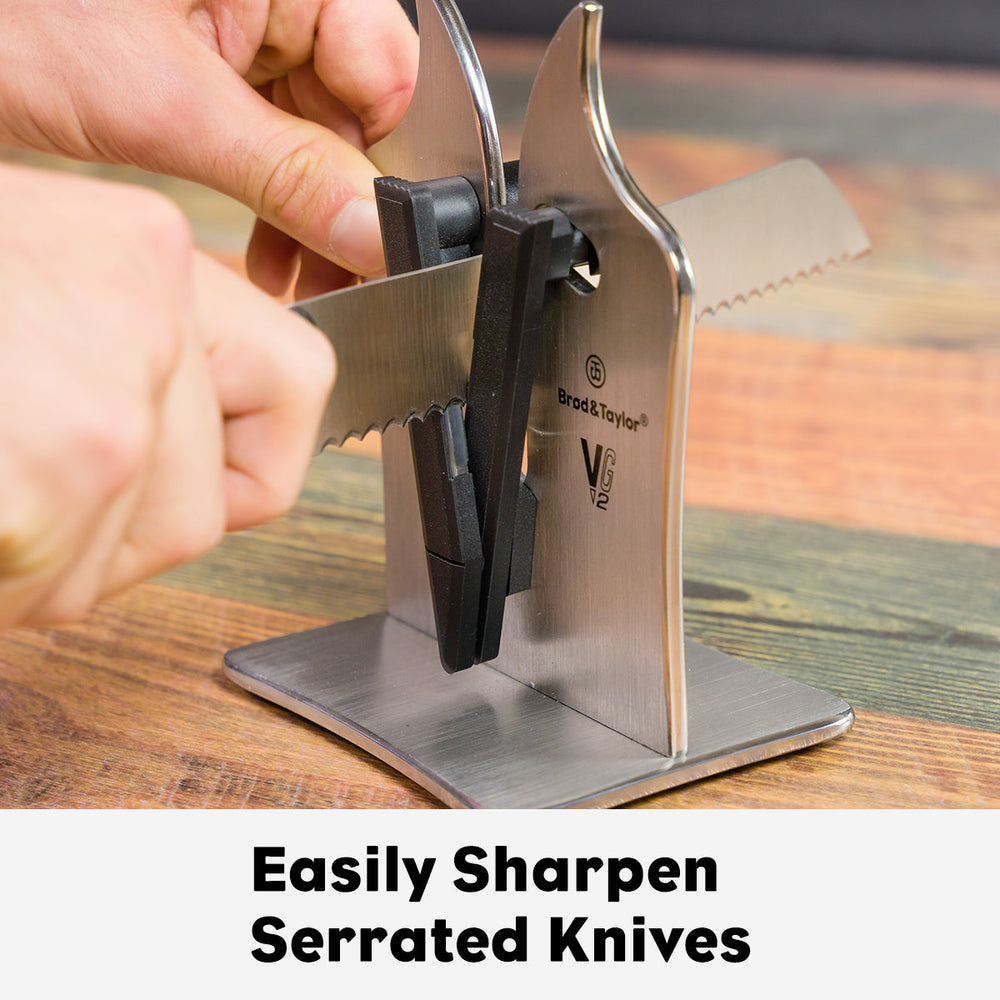
A stock image related to knife sharpener manufacturer.
Why are Knife Sharpeners Important for Retail Businesses?
Retail businesses that offer knife sharpening services can attract a significant customer base seeking maintenance for their kitchen tools. This additional service can increase foot traffic and overall sales. Retailers should consider staff training on the sharpening process, the speed of service, and customer satisfaction guarantees to ensure a positive experience for their clientele.
How Does Knife Sharpening Enhance Hospitality Services?
In the hospitality sector, maintaining sharp catering knives and tools is vital for high-quality service and food presentation. A reliable knife sharpener allows caterers to keep their equipment in optimal condition, ensuring that they can deliver exceptional service consistently. Buyers should look for customization options, service agreements, and training programs for staff to maximize the effectiveness of their sharpening solutions.
Related Video: Work Sharp Knife & Tool Sharpener – Advanced Tips & Techniques
3 Common User Pain Points for ‘knife sharpener manufacturer’ & Their Solutions
Scenario 1: Difficulty in Ensuring Consistent Sharpness Across Product Lines
The Problem: B2B buyers, particularly those in the food service or manufacturing sectors, often face the challenge of ensuring that their knives maintain a consistent level of sharpness. This inconsistency can lead to operational inefficiencies, increased labor costs, and product waste. For instance, a restaurant may find that their kitchen staff is spending too much time sharpening knives, which detracts from their primary responsibilities, leading to slower service and reduced customer satisfaction.
The Solution: To address this issue, buyers should consider investing in high-quality knife sharpeners that offer adjustable sharpening angles and multiple sharpening modes. When sourcing from a knife sharpener manufacturer, look for models that cater to various types of knives used in your industry—such as chef’s knives, serrated knives, and paring knives. It’s crucial to specify your needs clearly during the procurement process, ensuring that the manufacturer understands the volume of use and types of knives. Additionally, implementing a scheduled maintenance program that includes regular sharpening can help maintain blade performance, ultimately improving efficiency and prolonging the lifespan of your knives.
Scenario 2: Navigating the Complexity of Different Sharpening Technologies
The Problem: Many B2B buyers are overwhelmed by the variety of knife sharpening technologies available in the market, such as electric sharpeners, manual sharpeners, and professional-grade systems. This confusion can lead to poor purchasing decisions that may not meet the specific needs of their operations. For example, a buyer may opt for a manual sharpener thinking it’s cost-effective, only to find it unsatisfactory for high-volume usage in a commercial kitchen.
The Solution: To effectively navigate this complexity, buyers should conduct thorough research on the different types of sharpeners and their respective benefits. Engaging with knife sharpener manufacturers to request demonstrations or samples can provide valuable hands-on experience. Additionally, consider your specific operational needs—such as the volume of knives sharpened daily and the skill level of the staff using the equipment. When discussing options with manufacturers, ask about the technology used in their sharpeners and how it aligns with your operational requirements. This not only clarifies which products are best suited for your needs but also ensures that you are making a well-informed investment.
Scenario 3: Challenges in Supplier Reliability and After-Sales Support
The Problem: B2B buyers frequently encounter issues with the reliability of knife sharpener suppliers, particularly in terms of timely delivery and quality assurance. A delay in receiving sharpeners can disrupt business operations, especially in sectors like hospitality or food processing where efficiency is critical. Moreover, inadequate after-sales support can leave buyers without essential maintenance and repair services, leading to further downtime.
The Solution: To mitigate these risks, buyers should prioritize partnering with knife sharpener manufacturers known for their strong reputations in reliability and customer support. Before finalizing a purchase, conduct due diligence by reviewing supplier credentials and seeking testimonials from other clients in your industry. Additionally, inquire about their warranty policies and the availability of spare parts, as well as their responsiveness to service requests. Establishing a long-term relationship with a reliable manufacturer can provide peace of mind, ensuring that you receive ongoing support and service, thus minimizing disruptions to your operations.
Strategic Material Selection Guide for knife sharpener manufacturer
What Are the Key Materials for Knife Sharpener Manufacturing?
When selecting materials for knife sharpeners, manufacturers must consider several factors including performance, durability, cost, and compliance with international standards. Below are analyses of four common materials used in knife sharpener manufacturing, focusing on their properties, advantages, disadvantages, and implications for international B2B buyers.
1. Stainless Steel: A Versatile Choice for Knife Sharpeners
Key Properties: Stainless steel is known for its excellent corrosion resistance and durability. It can withstand high temperatures and is often rated for moderate to high pressure, making it suitable for various sharpening applications.
Pros & Cons: The primary advantage of stainless steel is its longevity; it resists rust and stains, ensuring a longer lifespan for the sharpeners. However, it can be more expensive than other materials and may require more complex manufacturing processes due to its hardness.
Impact on Application: Stainless steel sharpeners are compatible with a wide range of knife materials, including carbon steel and ceramic. This versatility is crucial for manufacturers targeting diverse markets.
Considerations for International Buyers: Buyers from regions like Europe and South America should ensure compliance with standards such as ASTM and DIN for stainless steel grades. Additionally, they should consider local preferences for specific grades that offer better performance in humid environments.
2. Diamond Abrasives: The Premium Option for Precision Sharpening
Key Properties: Diamond abrasives are known for their exceptional hardness and ability to maintain a sharp edge. They can handle high temperatures and are resistant to wear, making them ideal for professional-grade sharpeners.
Pros & Cons: The key advantage of diamond abrasives is their effectiveness in sharpening even the hardest materials, resulting in a superior finish. However, they are significantly more expensive and may not be suitable for all consumer markets.
Impact on Application: Diamond sharpeners are particularly effective for high-end knives, including those made from advanced alloys. This makes them a preferred choice for professional chefs and culinary enthusiasts.
Considerations for International Buyers: Buyers should be aware of the varying regulations regarding diamond abrasives in different regions. For instance, compliance with local safety standards in the Middle East and Europe is crucial for market entry.
3. Ceramic: Lightweight and Effective
Key Properties: Ceramic materials are lightweight and offer excellent hardness, allowing for effective sharpening without the risk of rust or corrosion. They can handle moderate pressure and are often rated for high-temperature applications.
Pros & Cons: The main advantage of ceramic sharpeners is their lightweight nature, which makes them easy to handle. However, they can be brittle and prone to chipping if dropped, which may limit their durability.
Impact on Application: Ceramic sharpeners are particularly effective for fine-edge knives and can be used on various materials, making them versatile for different markets.
Considerations for International Buyers: Buyers from Africa and South America should consider the local market’s acceptance of ceramic products, as well as compliance with safety standards. Understanding regional preferences can also guide product design.
4. Aluminum Oxide: A Cost-Effective Alternative
Key Properties: Aluminum oxide is a common abrasive material known for its durability and effectiveness in sharpening. It is resistant to wear and can handle moderate temperatures and pressures.
Pros & Cons: The primary advantage of aluminum oxide is its cost-effectiveness, making it an attractive option for budget-conscious manufacturers. However, it may not provide the same level of performance as diamond or ceramic options.
Impact on Application: Aluminum oxide sharpeners are suitable for general-purpose use and can effectively sharpen a variety of knife types, making them popular among casual users.
Considerations for International Buyers: Buyers in regions like South Africa should be aware of local manufacturing capabilities and standards. Ensuring compliance with relevant regulations can enhance marketability.
Summary Table of Material Selection for Knife Sharpeners
Material | Typical Use Case for knife sharpener manufacturer | Key Advantage | Key Disadvantage/Limitation | Relative Cost (Low/Med/High) |
---|---|---|---|---|
Stainless Steel | General-purpose sharpeners for various knife types | Excellent corrosion resistance | Higher manufacturing complexity | Medium |
Diamond Abrasives | Professional-grade sharpeners for high-end knives | Superior sharpening performance | High cost and limited market appeal | High |
Ceramic | Lightweight sharpeners for fine-edge knives | Easy to handle and rust-resistant | Brittle and prone to chipping | Medium |
Aluminum Oxide | Cost-effective sharpeners for general use | Affordable and durable | Lower performance compared to others | Low |
By understanding the properties and implications of these materials, international B2B buyers can make informed decisions that align with their market needs and compliance requirements.
In-depth Look: Manufacturing Processes and Quality Assurance for knife sharpener manufacturer
What Are the Main Stages of Manufacturing Knife Sharpeners?
The manufacturing process of knife sharpeners involves several crucial stages, each contributing to the final product’s quality and functionality. For B2B buyers, understanding these stages ensures they can select suppliers that adhere to high manufacturing standards.
-
Material Preparation
– The first step involves sourcing high-quality raw materials, typically steel or ceramic, which are essential for the sharpener’s effectiveness. Suppliers should provide documentation on the material grades used, as different grades can affect durability and performance.
– Pre-treatment processes such as annealing or hardening may be conducted to enhance the material’s properties. B2B buyers should inquire about the materials’ certifications, ensuring they meet international standards. -
Forming
– This stage includes cutting, shaping, and forming the raw materials into the required components. Techniques such as die casting, forging, or CNC machining are commonly employed.
– Precision in this stage is vital. Suppliers should utilize advanced machinery and technology to ensure consistent dimensions and tolerances. Buyers may request samples or prototypes to assess the accuracy of the forming process. -
Assembly
– Once the components are formed, they are assembled into the final product. This may include joining different materials or adding features such as ergonomic grips.
– Automated assembly lines or manual assembly techniques may be used, depending on the complexity of the product. B2B buyers should verify the assembly methods used, as they can impact the product’s overall quality and reliability. -
Finishing
– The finishing stage involves surface treatment processes such as polishing, coating, or painting, which enhance both aesthetics and functionality. For instance, coatings can improve corrosion resistance.
– Quality assurance in finishing is critical. Buyers should look for suppliers that conduct thorough inspections and tests on finished products to ensure they meet specified standards.
How Is Quality Assurance Implemented in Knife Sharpener Manufacturing?
Quality assurance (QA) is integral to the manufacturing process, ensuring that products meet or exceed customer expectations. For international B2B buyers, understanding the QA measures in place is essential for establishing trust with suppliers.
-
What International Standards Should B2B Buyers Consider?
– Suppliers should comply with international quality management standards such as ISO 9001, which outlines criteria for a quality management system. Compliance with ISO standards signifies that the manufacturer has robust quality control processes.
– Industry-specific certifications, such as CE marking for products sold in Europe or API standards for certain industrial applications, may also be relevant. B2B buyers should request documentation of these certifications to ensure compliance. -
What Are the Key Quality Control Checkpoints?
– Quality control (QC) involves several checkpoints throughout the manufacturing process:- Incoming Quality Control (IQC): This involves inspecting raw materials upon arrival to ensure they meet specified standards.
- In-Process Quality Control (IPQC): Continuous monitoring during production helps identify defects early.
- Final Quality Control (FQC): A comprehensive inspection of finished products before shipment ensures they meet quality specifications.
-
What Common Testing Methods Are Used?
– Various testing methods may be employed to assess the performance and durability of knife sharpeners, including:- Sharpness Tests: Evaluating the effectiveness of the sharpener.
- Durability Tests: Assessing the wear and tear of materials over time.
- Safety Tests: Ensuring that products meet safety standards to protect end-users.
How Can B2B Buyers Verify Supplier Quality Control Processes?
For international B2B buyers, ensuring that a supplier maintains rigorous quality control standards is paramount. Here are actionable steps to verify QC processes:
-
Request Audits and Reports
– Buyers should request copies of recent quality audits and inspection reports from suppliers. These documents provide insights into the supplier’s compliance with quality standards and their track record in maintaining product quality. -
Conduct On-Site Visits
– Whenever feasible, B2B buyers should conduct on-site visits to the manufacturing facility. This allows them to observe the manufacturing processes, quality control measures, and overall working conditions. It also helps build a relationship with the supplier. -
Engage Third-Party Inspection Services
– Utilizing third-party inspection services can provide an unbiased assessment of the supplier’s quality control processes. These services can perform inspections at various manufacturing stages and offer detailed reports on compliance with industry standards. -
Understand Quality Control Nuances for International Transactions
– Different regions may have varying quality standards and regulations. For example, European markets often require CE marking, while buyers from Africa and South America may have different local certifications. Understanding these nuances helps buyers ensure compliance and avoid potential issues.
What Are the Common Challenges in Quality Assurance for Knife Sharpeners?
International B2B buyers face several challenges when it comes to quality assurance in knife sharpener manufacturing:
-
Supply Chain Variability
– Variations in raw material quality can affect the final product. Buyers should work closely with suppliers to establish quality benchmarks for materials. -
Cultural Differences in Quality Standards
– Different countries may have varying perceptions of quality. B2B buyers should communicate clearly with suppliers about their expectations and requirements to ensure alignment. -
Regulatory Compliance
– Navigating the regulatory landscape can be complex, especially for products intended for multiple markets. Buyers should be proactive in understanding the regulatory requirements in their target markets.
By focusing on these manufacturing processes and quality assurance measures, international B2B buyers can make informed decisions when selecting knife sharpener manufacturers. This diligence not only enhances product reliability but also fosters long-term partnerships built on trust and quality.
Practical Sourcing Guide: A Step-by-Step Checklist for ‘knife sharpener manufacturer’
To effectively source a knife sharpener manufacturer, international B2B buyers must follow a structured approach. This guide provides a practical checklist to ensure you make informed decisions when selecting a supplier. Each step addresses critical aspects of the sourcing process, tailored to meet the needs of buyers from diverse regions, including Africa, South America, the Middle East, and Europe.
Step 1: Define Your Technical Specifications
Clearly outlining your technical requirements is essential to finding the right manufacturer. Specify the type of knife sharpeners you need, including dimensions, materials, and any special features. This clarity helps in communicating your needs effectively and ensures that potential suppliers can meet your expectations.
- Consider the end-user requirements: Are you targeting professional chefs or home cooks? This distinction will influence the design and functionality needed.
Step 2: Conduct Market Research
Before approaching manufacturers, conduct thorough market research to understand the landscape. Identify leading manufacturers and analyze their product offerings, pricing, and market reputation.
- Utilize trade shows and online platforms: Attend relevant trade exhibitions or explore online B2B marketplaces to gather insights and connect with potential suppliers.
Step 3: Evaluate Potential Suppliers
Before committing to a supplier, it’s crucial to vet them thoroughly. Request company profiles, case studies, and references from buyers in a similar industry or region. This step ensures that the manufacturer has a proven track record and can meet your quality standards.
- Look for certifications: Check if the supplier has relevant industry certifications, such as ISO, which indicates adherence to quality management standards.
Step 4: Verify Supplier Certifications
Certifications are vital indicators of a manufacturer’s credibility and quality standards. Verify that the supplier holds necessary certifications relevant to your market, such as safety and environmental standards.
- Ask for documentation: Request copies of certifications and ensure they are up-to-date. This verification protects your business from potential compliance issues.
Step 5: Request Samples
Before placing a bulk order, always request product samples. This allows you to assess the quality, functionality, and durability of the knife sharpeners firsthand.
- Evaluate based on your specifications: Test the samples against your defined criteria to ensure they meet your expectations.
Step 6: Negotiate Terms and Conditions
Once you’ve identified a suitable manufacturer, engage in negotiations regarding pricing, payment terms, and delivery schedules. Clear communication at this stage is crucial to avoid misunderstandings later on.
- Consider long-term partnerships: Discuss potential for future orders and any flexibility in pricing for bulk purchases, which can enhance your supplier relationship.
Step 7: Establish a Communication Plan
Effective communication is key to a successful sourcing relationship. Establish a clear communication plan with your supplier that includes regular updates, points of contact, and preferred communication channels.
- Set expectations for response times: Clarify how quickly you expect responses to inquiries or issues that may arise during the production process.
By following this checklist, B2B buyers can navigate the complexities of sourcing a knife sharpener manufacturer with confidence, ensuring they select a reliable partner that meets their needs.
Comprehensive Cost and Pricing Analysis for knife sharpener manufacturer Sourcing
What Are the Key Cost Components for Knife Sharpener Manufacturing?
When considering the sourcing of knife sharpeners, understanding the cost structure is crucial for international B2B buyers. The primary cost components in knife sharpener manufacturing include:
-
Materials: The type of materials used significantly affects the overall cost. High-grade steel, ceramic, or diamond abrasives can increase expenses, but they also enhance product durability and performance. Buyers should assess the material specifications required for their market.
-
Labor: Labor costs can vary widely based on the manufacturing location. Regions with lower labor costs, such as parts of Africa and South America, can offer significant savings. However, ensure that labor quality meets international standards.
-
Manufacturing Overhead: This encompasses all indirect costs associated with production, such as utilities, rent, and administrative expenses. These costs can fluctuate based on the efficiency of the production process and the location of the manufacturer.
-
Tooling: The initial investment in machinery and tools is essential for production. Custom designs may require specialized tooling, which can lead to higher upfront costs. Buyers should inquire about these costs during the negotiation phase.
-
Quality Control (QC): Implementing a robust QC process ensures that the knife sharpeners meet specific quality standards. While this adds to the cost, it is critical for reducing returns and enhancing customer satisfaction.
-
Logistics: Transportation costs can significantly impact the total cost, particularly for international shipments. Factors such as distance, shipping method, and tariffs should be factored into the overall pricing analysis.
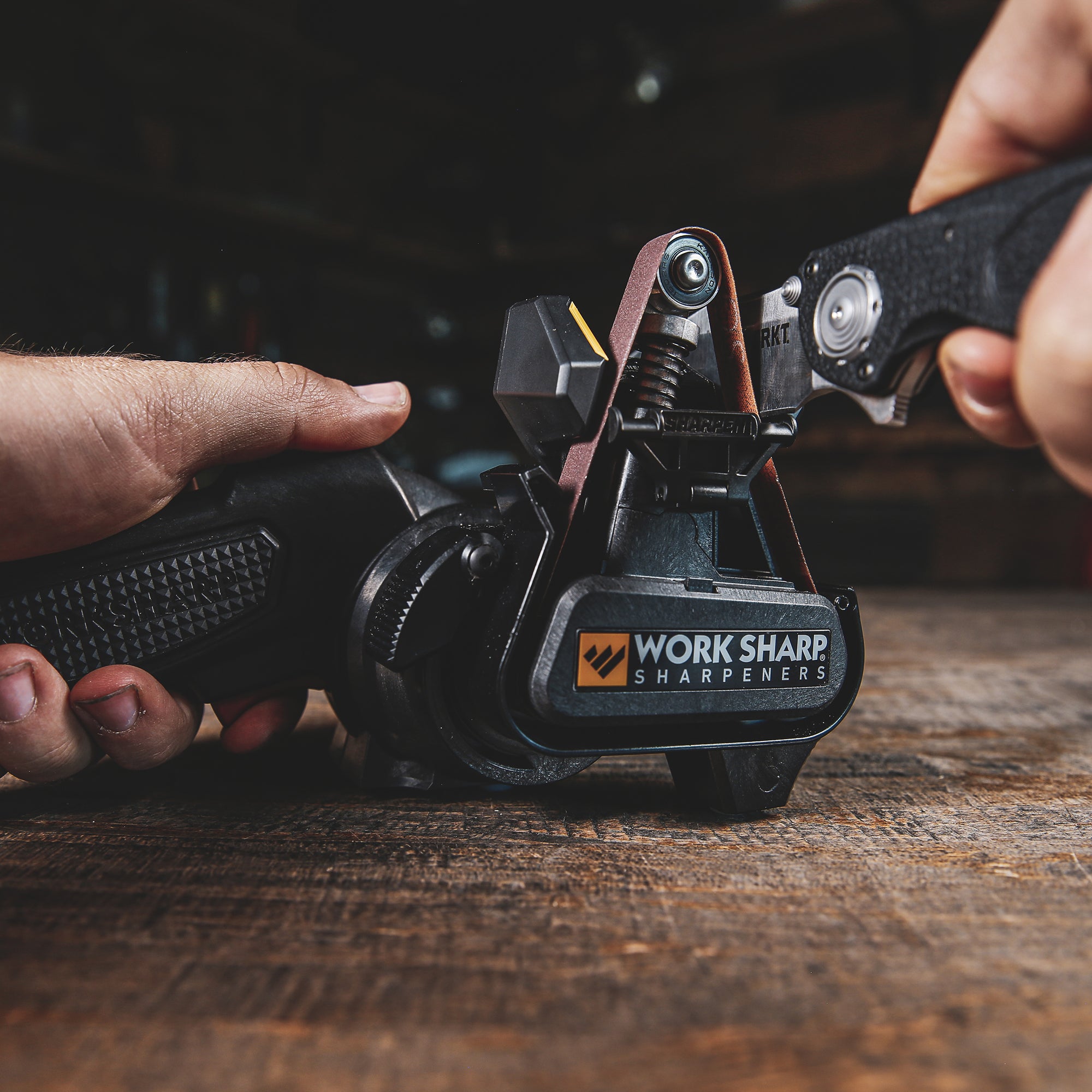
A stock image related to knife sharpener manufacturer.
- Margin: Manufacturers typically apply a margin to cover their costs and generate profit. Understanding the average margin in the knife sharpener industry can aid buyers in assessing fair pricing.
How Do Price Influencers Affect Knife Sharpener Sourcing?
Several factors can influence the pricing of knife sharpeners:
-
Volume/MOQ (Minimum Order Quantity): Bulk purchases often yield discounts. Buyers should negotiate MOQs that align with their market demands to optimize costs.
-
Specifications and Customization: Custom designs or specific features can increase production costs. Buyers must clarify their requirements upfront to avoid unexpected price hikes.
-
Materials and Quality Certifications: Sourcing materials with specific certifications (e.g., ISO, CE) may raise costs but can also assure quality and compliance in international markets.
-
Supplier Factors: The reputation and reliability of the supplier can influence pricing. Established manufacturers with a track record of quality may charge a premium but offer better service and assurance.
-
Incoterms: Understanding Incoterms (International Commercial Terms) is essential for determining who bears the cost of shipping, insurance, and tariffs. This knowledge can lead to better negotiation outcomes.
What Are the Best Practices for Negotiating Knife Sharpener Prices?
For international B2B buyers, especially from regions like Africa, South America, the Middle East, and Europe, effective negotiation strategies can lead to substantial savings:
-
Conduct Thorough Market Research: Understanding the market rates for knife sharpeners in your region will provide leverage during negotiations.
-
Evaluate Total Cost of Ownership (TCO): Consider not just the purchase price but also long-term factors like maintenance, durability, and resale value. This approach can justify a higher initial cost if it leads to lower TCO.
-
Leverage Relationships: Building strong relationships with suppliers can lead to better terms and pricing. Trust can facilitate negotiations and encourage suppliers to offer discounts.
-
Be Clear About Expectations: Clearly outline your quality and service expectations to avoid misunderstandings that could lead to additional costs.
-
Consider Payment Terms: Flexible payment terms may help mitigate upfront costs. Discussing options such as staggered payments or credit terms can enhance cash flow.
Disclaimer on Indicative Prices
Prices for knife sharpeners can vary widely based on the factors discussed. Buyers should conduct due diligence and obtain multiple quotes to ensure they are receiving a competitive offer tailored to their specific needs.
Alternatives Analysis: Comparing knife sharpener manufacturer With Other Solutions
Understanding Alternatives for Knife Sharpening Solutions
In the competitive landscape of B2B knife sharpening, it’s essential to evaluate not just the traditional knife sharpener manufacturers but also alternative technologies and methods that can provide similar results. This comparison will help international buyers, particularly those from Africa, South America, the Middle East, and Europe, make informed decisions based on performance, cost, and other critical factors.
Comparison Table of Knife Sharpening Solutions
Comparison Aspect | Knife Sharpener Manufacturer | Electric Knife Sharpener | Manual Sharpening Stone |
---|---|---|---|
Performance | High precision and consistency | Quick and efficient sharpening | Variable results based on skill |
Cost | Moderate to high initial investment | Moderate upfront cost, higher long-term costs | Low cost, but requires skill investment |
Ease of Implementation | Requires setup and training | Plug-and-play with minimal training | Requires practice and technique |
Maintenance | Regular maintenance needed | Low maintenance, easy to clean | Requires care to maintain surface |
Best Use Case | Commercial kitchens, high-volume operations | Home use, occasional sharpening | Culinary enthusiasts, budget-conscious users |
Detailed Breakdown of Alternatives
What Are Electric Knife Sharpeners and Their Benefits?
Electric knife sharpeners offer a quick and efficient solution for sharpening blades. They typically feature built-in guides that ensure consistent angles, making them user-friendly for individuals with less sharpening experience. However, while they provide speed, they can sometimes remove more material than necessary, leading to a shorter blade lifespan. This method is ideal for domestic environments where convenience is key, but for businesses that rely on high-quality blades, it may not be the most sustainable choice.
How Do Manual Sharpening Stones Compare?
Manual sharpening stones are a traditional method that requires skill and practice. They can achieve excellent results when used correctly, making them favored by culinary enthusiasts and professional chefs who appreciate the craftsmanship of knife maintenance. The cost of sharpening stones is relatively low, but the need for practice and technique can be a barrier for some users. This method is best suited for individuals who are willing to invest time in learning the art of knife sharpening, making it less practical for high-volume commercial operations.
Conclusion: Choosing the Right Knife Sharpening Solution
When selecting the most suitable knife sharpening solution, B2B buyers should consider their specific operational needs, budget constraints, and the skill levels of their staff. Knife sharpener manufacturers provide high-quality, consistent results ideal for commercial environments, while electric sharpeners offer speed and convenience for home use. On the other hand, manual sharpening stones cater to those who value craftsmanship and are willing to invest time in skill development. Ultimately, the right choice will depend on the buyer’s priorities—whether that’s cost efficiency, ease of use, or performance quality.
Essential Technical Properties and Trade Terminology for knife sharpener manufacturer
What Are the Essential Technical Properties of Knife Sharpeners?
When sourcing knife sharpeners, understanding the technical properties is crucial for international B2B buyers. Here are some key specifications to consider:
1. Material Grade
The material used in knife sharpeners significantly impacts their durability and effectiveness. Common materials include high-carbon steel, ceramic, and diamond abrasives. High-carbon steel offers excellent edge retention and is often used for professional-grade sharpeners. Ceramic is lightweight and provides a finer edge, while diamond abrasives are the most aggressive and suitable for restoring heavily dulled blades. Selecting the appropriate material grade ensures that the sharpener meets the specific needs of your market.
2. Tolerance Levels
Tolerance refers to the permissible limit or limits of variation in a physical dimension. For knife sharpeners, tolerances are essential for ensuring consistent performance and safety. Tight tolerances (e.g., ±0.01 mm) are critical in precision sharpeners where exact angles are necessary for optimal blade maintenance. Understanding tolerance specifications helps buyers assess quality and reliability, ensuring that the products meet international standards.
3. Grit Size
Grit size indicates the coarseness or fineness of the abrasive material used in the sharpener. It’s measured in numbers—lower numbers (e.g., 200) indicate coarser grits suitable for reshaping edges, while higher numbers (e.g., 2000) are finer and used for polishing. Selecting the right grit size is vital for achieving the desired sharpness and finish, catering to different user preferences and knife types.
4. Ergonomics
Ergonomics involves the design and usability of the sharpener, including handle comfort and ease of operation. A well-designed sharpener reduces user fatigue and enhances safety during use. This is especially important in B2B markets where end-user satisfaction can influence repeat purchases. Consideration of ergonomic design can be a strong selling point in competitive markets.
5. Weight and Portability
The weight of a knife sharpener can affect its usability and portability. Lighter models are often preferred for home use, while heavier, more robust designs may be favored in commercial settings where stability is paramount. Understanding the balance between weight and functionality is crucial for targeting specific buyer segments.
What Are Common Trade Terms in the Knife Sharpener Industry?
Navigating the knife sharpener market involves familiarity with industry-specific terminology. Here are essential trade terms that B2B buyers should know:
1. OEM (Original Equipment Manufacturer)
An OEM is a company that manufactures products that are sold under another company’s brand name. In the knife sharpener industry, buyers may seek OEM partnerships to create custom-branded products. Understanding OEM relationships can help buyers leverage existing manufacturing capabilities for unique product offerings.
2. MOQ (Minimum Order Quantity)
MOQ refers to the smallest quantity of product that a supplier is willing to sell. For knife sharpeners, MOQs can vary widely, affecting inventory management and cost considerations. Knowing the MOQ helps buyers plan their purchasing strategies and ensures that they meet supplier requirements.
3. RFQ (Request for Quotation)
An RFQ is a document sent to suppliers requesting pricing and terms for specific products. When sourcing knife sharpeners, submitting an RFQ helps buyers compare offers and negotiate better terms. It’s an essential step in the procurement process, ensuring transparency and competitiveness.
4. Incoterms (International Commercial Terms)
Incoterms are predefined commercial terms that define the responsibilities of buyers and sellers in international transactions. They dictate aspects such as shipping costs, insurance, and liability. Familiarity with Incoterms is crucial for B2B buyers, particularly those importing knife sharpeners from different regions, as they can significantly affect overall costs and risk management.
5. Lead Time
Lead time refers to the duration between placing an order and receiving the product. In the knife sharpener market, understanding lead times is vital for inventory planning and customer satisfaction. Buyers should communicate clearly with suppliers to set realistic expectations regarding delivery times.
By grasping these essential technical properties and industry terminology, international B2B buyers can make informed decisions when sourcing knife sharpeners, ultimately enhancing their purchasing strategies and market competitiveness.
Navigating Market Dynamics and Sourcing Trends in the knife sharpener manufacturer Sector
What Are the Current Market Dynamics and Key Trends in the Knife Sharpener Manufacturing Sector?
The knife sharpener manufacturing sector is experiencing notable growth driven by several global trends. One of the primary factors is the increasing demand for quality kitchen tools, especially among culinary professionals and home cooks alike. This surge is influenced by the rise in gourmet cooking and food preparation, particularly in regions such as Europe and North America, where culinary arts are deeply appreciated. Additionally, the growing popularity of outdoor activities, such as camping and hunting, has led to an uptick in the demand for portable knife sharpeners.
In terms of technology, B2B buyers are increasingly gravitating towards smart and electric knife sharpeners that offer automated sharpening processes. The integration of artificial intelligence in sharpening tools is also gaining traction, allowing for precision and consistency that manual sharpening cannot provide. For international buyers, especially from Africa and South America, the emergence of e-commerce platforms facilitates easier access to a broader range of products and suppliers, making it essential to stay updated on the latest offerings and innovations.
Furthermore, the market is witnessing a shift towards customization, where manufacturers are offering tailored solutions to meet specific client needs. This trend is particularly beneficial for buyers looking to differentiate their offerings in competitive markets. Understanding these dynamics will empower B2B buyers to make informed sourcing decisions and foster long-term supplier relationships.
How Does Sustainability Influence Sourcing in the Knife Sharpener Sector?
Sustainability has become a critical concern for manufacturers and buyers alike in the knife sharpener industry. The environmental impact of production processes, from material extraction to manufacturing waste, is under scrutiny. B2B buyers are increasingly prioritizing suppliers who demonstrate a commitment to reducing their carbon footprint and promoting responsible sourcing practices.
Ethical supply chains are essential in this context. Manufacturers are now focusing on sourcing materials that are not only high-quality but also sustainably harvested. For instance, the use of recycled metals and environmentally friendly plastics in knife sharpener production is on the rise. Buyers should look for certifications such as ISO 14001, which indicates that a company adheres to environmental management standards, and other green certifications that affirm a manufacturer’s commitment to sustainable practices.
Moreover, promoting transparency within the supply chain enhances trust and builds long-lasting partnerships. B2B buyers can leverage this growing emphasis on sustainability as a competitive advantage, aligning their purchasing decisions with the values of their customers and stakeholders.
How Has the Knife Sharpener Manufacturing Sector Evolved Over Time?
The evolution of the knife sharpener manufacturing sector can be traced back to its humble beginnings, where manual sharpening stones dominated the market. Over the years, technological advancements have transformed the industry significantly. The introduction of electric sharpeners in the late 20th century marked a turning point, allowing for faster and more efficient sharpening processes.
In recent decades, the focus has shifted towards innovation and user-friendly designs, catering to both professional chefs and everyday consumers. The rise of e-commerce has further influenced the sector, enabling manufacturers to reach global markets and diversify their product offerings. As a result, the knife sharpener sector continues to adapt to changing consumer preferences and technological advancements, positioning itself for future growth in the global marketplace.
Conclusion
Understanding the current market dynamics, sustainability trends, and the historical evolution of the knife sharpener manufacturing sector equips international B2B buyers with the insights necessary to navigate this industry effectively. By staying informed and aligning sourcing strategies with emerging trends, buyers can enhance their competitive edge and foster sustainable growth in their businesses.
Frequently Asked Questions (FAQs) for B2B Buyers of knife sharpener manufacturer
-
How do I choose the right knife sharpener manufacturer for my business needs?
Choosing the right knife sharpener manufacturer involves assessing their product quality, production capacity, and reliability. Start by researching manufacturers that specialize in the type of sharpeners you need, whether for commercial kitchens or personal use. Request samples to evaluate the sharpness, durability, and overall design. Additionally, consider the manufacturer’s experience in international trade, especially if you’re importing from regions like Europe, Africa, or South America. Engage in conversations about their production timelines, certifications, and after-sales support to ensure they align with your business requirements. -
What are the key factors to consider when vetting a knife sharpener supplier?
When vetting a knife sharpener supplier, key factors to consider include their industry reputation, production capabilities, and compliance with international quality standards. Look for reviews and testimonials from other B2B buyers to gauge reliability. Verify their certifications, such as ISO or CE, which indicate adherence to quality and safety regulations. Additionally, assess their responsiveness to inquiries and their willingness to provide customization options. This due diligence will help mitigate risks associated with supplier reliability and product quality. -
What is the typical minimum order quantity (MOQ) for knife sharpeners?
The minimum order quantity (MOQ) for knife sharpeners can vary significantly based on the manufacturer and the type of products. Generally, MOQs can range from 50 to 500 units. Some manufacturers may offer lower MOQs for standard models but may require higher quantities for customized or specialized sharpeners. It’s essential to discuss MOQs upfront to ensure they align with your business needs and budget. Additionally, consider the potential for bulk discounts, which can provide cost savings as your order volume increases. -
What customization options are available for knife sharpeners?
Many knife sharpener manufacturers offer customization options to cater to specific business needs. These can include alterations in design, color, branding (such as logo placement), and even functionality (like electric versus manual). Discuss your requirements with the manufacturer to explore possibilities that fit your target market. Keep in mind that customization may affect the MOQ and lead times, so plan accordingly to meet your product launch timelines. -
What payment terms should I expect when sourcing knife sharpeners internationally?
Payment terms when sourcing knife sharpeners can vary widely depending on the supplier and the relationship established. Common terms include advance payment (often 30-50% deposit), net 30/60/90 days, or letter of credit (LC) for larger transactions. Always clarify payment terms before finalizing the order to avoid misunderstandings. Additionally, consider the implications of currency exchange rates and transaction fees, especially when dealing with manufacturers in different regions such as Africa or South America. -
How can I ensure quality assurance for knife sharpeners sourced from manufacturers?
To ensure quality assurance when sourcing knife sharpeners, establish clear quality standards with your supplier before production begins. Request detailed product specifications and conduct regular inspections during the manufacturing process. Consider third-party quality control inspections, especially for larger orders, to verify compliance with your standards. Additionally, request samples before the final shipment to assess quality firsthand. Building a strong relationship with your supplier can also facilitate better communication about quality expectations. -
What logistics considerations should I keep in mind when importing knife sharpeners?
When importing knife sharpeners, logistics considerations are crucial to ensure timely delivery and cost-effectiveness. Evaluate shipping options, including air freight for faster delivery or sea freight for cost savings on larger shipments. Understand the customs regulations and import duties specific to your country, as they can impact total costs. Partnering with a reliable freight forwarder can simplify the process and help navigate paperwork. Lastly, establish clear communication with your supplier regarding shipping timelines and tracking. -
How do I handle after-sales support and warranty issues for knife sharpeners?
After-sales support and warranty issues are vital for maintaining customer satisfaction. Ensure that the manufacturer provides a clear warranty policy covering defects and performance issues. Establish a process for handling returns or replacements, and communicate this to your customers. Discuss the manufacturer’s capability for providing ongoing support, such as spare parts availability and maintenance guidance. A strong after-sales support system can differentiate your business and foster long-term customer loyalty.
Important Disclaimer & Terms of Use
⚠️ Important Disclaimer
The information provided in this guide, including content regarding manufacturers, technical specifications, and market analysis, is for informational and educational purposes only. It does not constitute professional procurement advice, financial advice, or legal advice.
While we have made every effort to ensure the accuracy and timeliness of the information, we are not responsible for any errors, omissions, or outdated information. Market conditions, company details, and technical standards are subject to change.
B2B buyers must conduct their own independent and thorough due diligence before making any purchasing decisions. This includes contacting suppliers directly, verifying certifications, requesting samples, and seeking professional consultation. The risk of relying on any information in this guide is borne solely by the reader.
Strategic Sourcing Conclusion and Outlook for knife sharpener manufacturer
What Are the Key Takeaways for International B2B Buyers in Knife Sharpening Solutions?
In conclusion, strategic sourcing for knife sharpener manufacturers presents a significant opportunity for B2B buyers across Africa, South America, the Middle East, and Europe. By focusing on quality, supplier reliability, and innovative technology, businesses can enhance their operational efficiency and customer satisfaction. Understanding regional market dynamics and consumer preferences allows buyers to make informed decisions that align with their specific needs.
How Can Buyers Leverage Strategic Sourcing to Enhance Their Business?
Implementing a strategic sourcing approach not only mitigates risks but also fosters long-term partnerships with manufacturers who share a commitment to quality and sustainability. As global demand for high-quality knife sharpeners continues to rise, the importance of sourcing from reputable manufacturers becomes even more critical.
What’s Next for International Buyers in the Knife Sharpener Market?
As we look to the future, international B2B buyers are encouraged to actively engage with suppliers and explore innovative solutions that can elevate their product offerings. By prioritizing strategic sourcing, companies can position themselves to adapt to evolving market trends and consumer needs. Take the next step in your sourcing journey by reaching out to potential partners and exploring the vast opportunities within the knife sharpener industry.