The Ultimate Guide to Labeling Machine Manufacturer (2025)
Introduction: Navigating the Global Market for labeling machine manufacturer
In today’s competitive landscape, sourcing reliable labeling machine manufacturers can be a daunting task for international B2B buyers. With the rise of globalization, businesses from regions such as Africa, South America, the Middle East, and Europe (including countries like Turkey and Thailand) face the challenge of selecting the right technology that meets their operational needs while adhering to local regulations and standards. This guide aims to streamline the procurement process by providing a comprehensive overview of labeling machines, including types, applications, and critical considerations for supplier vetting.
Understanding the nuances of labeling technology is essential for optimizing production efficiency and ensuring product compliance. This guide will delve into the various types of labeling machines available on the market, their specific applications across different industries, and the factors that influence cost. Additionally, we will explore best practices for evaluating suppliers, ensuring quality, and negotiating favorable terms.
By equipping B2B buyers with actionable insights and practical strategies, this guide empowers them to make informed purchasing decisions. Whether you are seeking to enhance your packaging line or expand your product offerings, understanding the global landscape of labeling machine manufacturers will enable you to navigate the complexities of this market effectively. Prepare to elevate your sourcing strategy and drive your business forward with confidence.
Understanding labeling machine manufacturer Types and Variations
Type Name | Key Distinguishing Features | Primary B2B Applications | Brief Pros & Cons for Buyers |
---|---|---|---|
Automatic Labeling Machines | High-speed operation, integrated with production lines | Food & Beverage, Pharmaceuticals | Pros: High efficiency, reduced labor costs. Cons: Higher initial investment. |
Semi-Automatic Labeling Machines | Manual loading, automated labeling process | Cosmetics, Small-scale Food Producers | Pros: Lower cost, flexible use. Cons: Slower than fully automatic models. |
Wrap-Around Labeling Machines | Specialized for cylindrical products, adjustable labeling heads | Beverage Bottles, Cosmetic Tubes | Pros: Versatile for various shapes, precise application. Cons: Limited to cylindrical products. |
Front and Back Labeling Machines | Dual-sided labeling capability, customizable for various sizes | Household Products, Electronics | Pros: Efficient for dual labeling, customizable. Cons: Requires more space. |
Labeling Systems with RFID Integration | Advanced technology for tracking and inventory management | Logistics, Pharmaceuticals | Pros: Enhanced tracking, reduces errors. Cons: Higher complexity and cost. |
What Are Automatic Labeling Machines and Their Benefits for B2B Buyers?
Automatic labeling machines are designed for high-speed operations, often integrated into existing production lines. They are ideal for large-scale manufacturing environments, particularly in industries like food and beverage, as well as pharmaceuticals. When considering an automatic labeling machine, B2B buyers should evaluate the machine’s throughput capacity, compatibility with existing systems, and the potential for reduced labor costs. While they offer significant efficiency gains, the initial investment can be substantial, making it essential to assess long-term ROI.
How Do Semi-Automatic Labeling Machines Serve Small to Medium Enterprises?
Semi-automatic labeling machines require manual loading of products but automate the labeling process. This type is particularly suited for small to medium enterprises in sectors like cosmetics and small-scale food production. Buyers should consider their production volume and flexibility needs, as these machines offer a lower cost alternative compared to fully automatic options. However, they may not keep pace with higher production demands, making it crucial to project future growth when investing.
What Are the Unique Features of Wrap-Around Labeling Machines?
Wrap-around labeling machines are specifically designed for cylindrical products, such as beverage bottles and cosmetic tubes. They feature adjustable labeling heads that ensure precise application around the product’s circumference. B2B buyers should assess the versatility of these machines for different product sizes and shapes. While they excel in cylindrical applications, their limitations in labeling non-cylindrical products should be carefully considered, especially for businesses with diverse product lines.
Why Choose Front and Back Labeling Machines for Versatile Applications?
Front and back labeling machines provide the capability to label both sides of a product simultaneously. This feature is especially beneficial for household products and electronics, where dual labeling is often required. Buyers should evaluate the machine’s customization options and space requirements, as these systems can occupy more floor space. While they enhance labeling efficiency, the need for adequate operational space is an important consideration for businesses with limited facilities.
How Do Labeling Systems with RFID Integration Enhance Operational Efficiency?
Labeling systems that incorporate RFID technology are becoming increasingly popular in logistics and pharmaceuticals. These advanced systems not only apply labels but also enable tracking and inventory management. B2B buyers should weigh the benefits of enhanced tracking and error reduction against the complexity and cost of implementation. While RFID integration can significantly improve operational efficiency, it requires a higher level of technical expertise and investment, making it suitable for businesses looking to modernize their supply chain processes.
Related Video: Automatic Labeling Machine – ALTECH
Key Industrial Applications of labeling machine manufacturer
Industry/Sector | Specific Application of Labeling Machine Manufacturer | Value/Benefit for the Business | Key Sourcing Considerations for this Application |
---|---|---|---|
Food and Beverage | Automated labeling for packaging | Increases efficiency and accuracy in production | Compliance with food safety regulations, speed of labeling |
Pharmaceuticals | Serialization and tamper-evident labeling | Enhances product security and traceability | Regulatory compliance, customization options |
Cosmetics and Personal Care | Customizable labels for diverse product lines | Strengthens brand identity and consumer appeal | Material compatibility, eco-friendly options |
Logistics and Warehousing | Barcode labeling for inventory management | Improves inventory tracking and reduces errors | Durability of labels, ease of integration with existing systems |
Electronics | Component labeling for assembly and shipping | Streamlines production and ensures proper assembly | Precision in labeling, adaptability to various surfaces |
How Do Labeling Machines Enhance Efficiency in the Food and Beverage Sector?
Labeling machines in the food and beverage industry automate the process of applying labels on various packaging types, such as bottles, jars, and cartons. This automation not only speeds up production but also ensures that labels are applied accurately, reducing the risk of mislabeling that could lead to compliance issues. For international buyers, especially in regions like Africa and South America, sourcing machines that meet local food safety regulations is crucial. Additionally, the ability to handle different label sizes and types can provide flexibility in a diverse product lineup.
What Role Do Labeling Machines Play in Pharmaceutical Compliance?
In the pharmaceutical sector, labeling machines are critical for applying serialization and tamper-evident labels. These features enhance product security and allow for effective tracking throughout the supply chain, which is essential for regulatory compliance. International buyers from the Middle East and Europe should focus on sourcing machines that can accommodate specific regulatory requirements in their regions, such as the EU Falsified Medicines Directive. Customization options for labels, including QR codes and batch numbers, can also significantly improve traceability.
How Can Cosmetics Companies Benefit from Customizable Labeling Solutions?
Cosmetics and personal care manufacturers often require labeling machines that can produce a variety of labels for different products, including skincare, makeup, and hair care items. These machines allow for high-quality, visually appealing labels that enhance brand identity and attract consumers. Buyers from Europe and South America should consider sourcing machines that offer eco-friendly labeling solutions, as consumer preferences are increasingly leaning towards sustainable products. The ability to adapt labels for seasonal promotions or new product launches can also provide a competitive edge.
In What Ways Do Labeling Machines Improve Logistics and Inventory Management?
In logistics and warehousing, labeling machines are utilized for barcode labeling, which plays a vital role in inventory management. By automating the labeling process, businesses can improve accuracy in tracking inventory levels and reduce human error. International buyers, particularly those in Africa and the Middle East, should ensure that the machines they source can produce durable labels that withstand various environmental conditions. Integration capabilities with existing inventory management systems are also a key consideration to streamline operations.
How Do Labeling Machines Support Electronics Manufacturing?
In the electronics industry, labeling machines are essential for applying labels to components and finished products for assembly and shipping. These machines help ensure that components are correctly identified, which streamlines production processes and reduces assembly errors. Buyers from regions like Turkey and Thailand should look for machines that offer precision labeling to accommodate small and intricate parts. Additionally, versatility in labeling different surfaces and materials can enhance the overall efficiency of the production line.
Related Video: Liquid – Filling, Capping, and Labeling Machine With the Speed of up to 220 Bottles/minute.
3 Common User Pain Points for ‘labeling machine manufacturer’ & Their Solutions
Scenario 1: Inconsistent Labeling Quality Across Production Batches
The Problem: Many international B2B buyers face the challenge of inconsistent labeling quality when sourcing labeling machines. This inconsistency can lead to misbranding, compliance issues, and ultimately damage customer trust. For manufacturers in regions like Africa or South America, where regulatory scrutiny may be increasing, the need for precision in labeling is paramount. Buyers often find themselves grappling with machines that fail to deliver uniform labels due to poor calibration or inadequate material compatibility, causing significant production delays and increased operational costs.
The Solution: To mitigate these issues, buyers should prioritize working with labeling machine manufacturers that offer robust testing and calibration services. Before making a purchase, request samples of labels produced by the machines under consideration. Additionally, inquire about the machine’s compatibility with various labeling materials to ensure that it meets your specific needs. It’s also advisable to implement a routine maintenance schedule and invest in training for operators to understand the nuances of the machine’s operation. This proactive approach will help maintain consistent labeling quality across all production batches.
Scenario 2: Difficulty in Integrating Labeling Machines with Existing Production Lines
The Problem: Integration challenges often arise when businesses attempt to incorporate new labeling machines into their existing production lines. This can result from differences in technology, inadequate communication between machines, or a lack of space. Buyers from regions like the Middle East or Europe may find that their new machines disrupt workflow, causing bottlenecks and inefficiencies that can ripple through the entire production process.
The Solution: To ensure seamless integration, B2B buyers should conduct a thorough analysis of their current production setup before purchasing a labeling machine. Engage with manufacturers that offer customizable solutions that can be tailored to fit your specific production environment. Additionally, invest in consultation services from the manufacturer to assess compatibility and recommend necessary modifications to your production line. This collaboration can streamline installation and reduce downtime, ensuring that the new labeling machine enhances productivity rather than hinders it.
Scenario 3: Limited Technical Support and Maintenance Resources
The Problem: One of the significant pain points for B2B buyers is the lack of adequate technical support and maintenance resources post-purchase. For companies in emerging markets like South America and Africa, access to qualified technicians for repair and maintenance of labeling machines can be scarce. This gap can lead to prolonged downtime during equipment failures, which negatively impacts production schedules and profitability.
The Solution: To address this issue, buyers should prioritize manufacturers that offer comprehensive after-sales support, including training for in-house maintenance staff and easy access to spare parts. When evaluating potential suppliers, ask about their support structure and response times for service requests. Additionally, consider investing in a service contract that includes regular maintenance checks and emergency support. By establishing a robust support network, businesses can significantly reduce the risk of prolonged downtime and ensure that their labeling operations run smoothly and efficiently.
Strategic Material Selection Guide for labeling machine manufacturer
When selecting materials for labeling machines, international B2B buyers must consider various factors that impact performance, durability, and compliance with regional standards. Below is an analysis of several common materials used in labeling machines, focusing on their properties, advantages, disadvantages, and specific considerations for buyers from Africa, South America, the Middle East, and Europe.
What Are the Key Properties of Stainless Steel in Labeling Machines?
Stainless steel is a widely used material in labeling machines due to its excellent corrosion resistance and high strength. It typically withstands temperatures ranging from -200°C to 800°C, making it suitable for various environments. The material’s non-reactive nature ensures that it does not contaminate products, which is crucial in food and pharmaceutical applications.
Pros & Cons:
The durability of stainless steel is one of its most significant advantages, providing a long service life with minimal maintenance. However, its higher cost compared to other materials may be a limitation for budget-conscious buyers. Additionally, manufacturing complexities can arise from the need for specialized tools and processes.
Impact on Application:
Stainless steel is compatible with a wide range of media, including water, oils, and chemicals, making it versatile for different labeling applications. Buyers should consider the specific requirements of their products to ensure compatibility.
Considerations for International Buyers:
Compliance with international standards such as ASTM and DIN is essential. Buyers should also be aware of local regulations regarding food safety and hygiene, particularly in regions with stringent health codes.
How Does Plastic Compare as a Material for Labeling Machines?
Plastics, such as polypropylene and polyethylene, are increasingly popular in the labeling machine industry due to their lightweight nature and cost-effectiveness. These materials typically have temperature ratings between -40°C and 100°C, making them suitable for moderate conditions.
Pros & Cons:
The primary advantage of plastic is its low cost and ease of manufacturing, which allows for rapid production and customization. However, plastics may not offer the same level of durability as metals, leading to potential wear and tear over time. Additionally, their lower resistance to chemicals can limit their use in specific applications.
Impact on Application:
Plastic materials are often used in labeling applications where weight is a concern, such as portable labeling machines. However, buyers must consider the environmental impact and potential recyclability of plastic materials.
Considerations for International Buyers:
Buyers should ensure that the plastics used comply with local environmental regulations and standards. In regions like Europe, there may be stricter guidelines regarding the use of certain plastics, necessitating thorough research.
What Are the Advantages of Aluminum in Labeling Machines?
Aluminum is another common material in labeling machines, known for its lightweight properties and good corrosion resistance. It typically performs well in temperatures ranging from -50°C to 150°C.
Pros & Cons:
The key advantage of aluminum is its balance between strength and weight, making it an ideal choice for machines that require mobility. However, aluminum can be more expensive than plastic and may not be as durable as stainless steel, leading to potential long-term costs.
Impact on Application:
Aluminum is suitable for various labeling applications, particularly in industries that prioritize lightweight machinery, such as logistics and packaging. Its resistance to corrosion allows it to perform well in humid environments.
Considerations for International Buyers:
Buyers should consider the availability of aluminum and its compliance with international standards. In regions like the Middle East, where high temperatures are common, ensuring that aluminum components can withstand local conditions is vital.
How Does Composite Material Enhance Labeling Machine Performance?
Composite materials, which combine different substances to enhance performance, are gaining traction in the labeling machine sector. These materials can be engineered to provide specific properties, such as increased strength or reduced weight.
Pros & Cons:
The primary advantage of composite materials is their versatility, allowing manufacturers to tailor properties to specific applications. However, the complexity of manufacturing and potentially higher costs can be a drawback for some buyers.
Impact on Application:
Composites can be particularly beneficial in specialized labeling applications, such as those requiring high resistance to chemicals or extreme temperatures. Buyers should evaluate the specific needs of their applications when considering composites.
Considerations for International Buyers:
Understanding the manufacturing processes and compliance with international standards is crucial for buyers interested in composite materials. In regions like South America, where resource availability may vary, sourcing can be a challenge.
Summary Table of Material Selection for Labeling Machines
Material | Typical Use Case for labeling machine manufacturer | Key Advantage | Key Disadvantage/Limitation | Relative Cost (Low/Med/High) |
---|---|---|---|---|
Stainless Steel | Food and pharmaceutical labeling machines | Excellent corrosion resistance | Higher cost and manufacturing complexity | High |
Plastic | Portable labeling machines in moderate conditions | Low cost and ease of manufacturing | Limited durability and chemical resistance | Low |
Aluminum | Lightweight labeling machines for logistics | Balance of strength and weight | More expensive than plastic, less durable than stainless steel | Medium |
Composite | Specialized applications requiring tailored properties | Versatility in performance | Higher cost and manufacturing complexity | High |
This strategic material selection guide provides essential insights for international B2B buyers, enabling them to make informed decisions that align with their operational needs and regional standards.
In-depth Look: Manufacturing Processes and Quality Assurance for labeling machine manufacturer
What Are the Key Stages in the Manufacturing Process of Labeling Machines?
The manufacturing process for labeling machines involves several critical stages, ensuring that the final product is reliable and efficient. Understanding these stages can help international B2B buyers make informed decisions when selecting suppliers.
-
Material Preparation
The first step involves sourcing high-quality materials, including metals, plastics, and electronic components. Suppliers often use advanced materials like stainless steel for durability and compliance with hygiene standards. Buyers should prioritize manufacturers that demonstrate their sourcing practices, focusing on sustainability and material certification. -
Forming
This stage encompasses processes such as cutting, molding, and machining. Techniques like CNC (Computer Numerical Control) machining are widely used for precision and consistency. Buyers should inquire about the technology used in forming, as advanced machinery can significantly impact the accuracy and quality of the labeling machines. -
Assembly
Assembly involves integrating various components, including label applicators, sensors, and control systems. Manufacturers often adopt lean manufacturing principles to streamline this process, which reduces waste and enhances efficiency. It is crucial for buyers to understand how manufacturers manage assembly lines and whether they employ skilled labor to ensure quality assembly. -
Finishing
The final stage includes surface treatment, painting, and quality checks. Finishing processes are vital for aesthetics and protection against environmental factors. Buyers should ask about the finishing techniques employed and the types of coatings used, as these can affect the machine’s longevity and maintenance needs.
How Is Quality Assurance Implemented in Labeling Machine Manufacturing?
Quality assurance (QA) is integral to the production of labeling machines, ensuring that every unit meets established standards. B2B buyers should familiarize themselves with international quality standards and specific industry requirements.
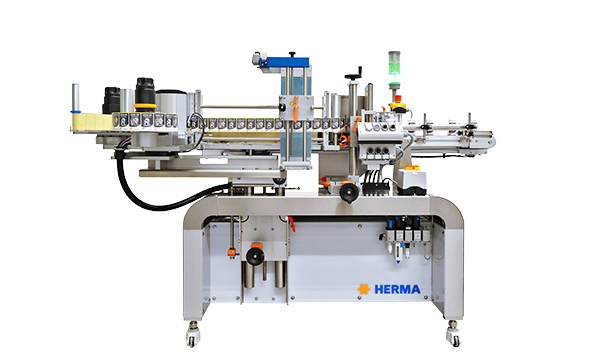
A stock image related to labeling machine manufacturer.
-
International Standards
Adhering to international standards such as ISO 9001 is essential for manufacturers aiming to provide high-quality products. This certification indicates a commitment to quality management systems and continuous improvement. Buyers should look for suppliers who can present valid ISO certifications as part of their quality assurance processes. -
Industry-Specific Standards
Depending on the application of the labeling machines, additional certifications like CE marking (for compliance with European standards) or API standards (for equipment used in the oil and gas industry) may apply. Understanding these standards helps buyers ensure that the machines are suitable for their specific needs and compliant with local regulations. -
Quality Control Checkpoints
Effective quality control (QC) involves several checkpoints throughout the manufacturing process, including:
– Incoming Quality Control (IQC): Inspecting raw materials and components upon arrival to ensure they meet specifications.
– In-Process Quality Control (IPQC): Monitoring the production process to identify any deviations from quality standards in real-time.
– Final Quality Control (FQC): Conducting thorough inspections and tests on the finished products before they are dispatched.
What Common Testing Methods Are Used in Labeling Machine Quality Assurance?
Testing methods play a crucial role in validating the performance and reliability of labeling machines. Understanding these methods can aid buyers in assessing supplier capabilities.
-
Functional Testing
This involves checking the machine’s operational performance, including speed, accuracy, and labeling consistency. Buyers should ensure that manufacturers conduct thorough functional tests and provide detailed reports. -
Durability Testing
Manufacturers often perform stress tests to evaluate how machines withstand extreme conditions, such as temperature variations and humidity. Buyers should inquire about the testing protocols used to assess durability. -
Compliance Testing
This testing ensures that the machines meet specific regulatory requirements. For instance, electrical safety tests and electromagnetic compatibility tests are critical for compliance with international standards. Buyers should request compliance testing documentation to verify adherence to relevant regulations.
How Can B2B Buyers Verify Supplier Quality Control Practices?
Verifying a supplier’s quality control practices is essential for B2B buyers, especially when sourcing from international manufacturers. Here are some actionable steps:
-
Conduct Supplier Audits
Regular audits allow buyers to assess the supplier’s manufacturing processes, quality control measures, and compliance with standards. Audits should be thorough and ideally conducted by independent third parties to ensure objectivity. -
Request Quality Control Reports
Buyers should ask for documentation detailing the QC processes, including inspection and testing reports. These documents provide insights into how the manufacturer upholds quality standards throughout production. -
Utilize Third-Party Inspection Services
Engaging third-party inspection services can provide an unbiased evaluation of the supplier’s quality control practices. These services often include pre-shipment inspections and final product evaluations, which can significantly reduce risk.
What Are the Quality Control and Certification Nuances for International Buyers?
For international B2B buyers, understanding quality control and certification nuances is vital, particularly when sourcing from diverse regions like Africa, South America, the Middle East, and Europe.
-
Regional Certification Requirements
Different regions have varying certification requirements. For example, European buyers often require CE marking, while buyers in the Middle East may need local regulatory compliance. Buyers must be aware of these requirements to avoid legal complications. -
Cultural Considerations in Quality Assurance
Cultural differences can influence quality assurance practices. Buyers should consider local manufacturing practices and how they impact quality control. Establishing clear communication and expectations can help bridge cultural gaps. -
Language Barriers and Documentation
Language differences can complicate the verification of quality control practices. Buyers should ensure that documentation is available in a language they understand, and they may need to involve translators during audits and inspections.
By understanding the manufacturing processes and quality assurance practices of labeling machine manufacturers, international B2B buyers can make more informed decisions, mitigate risks, and ensure they select reliable suppliers.
Practical Sourcing Guide: A Step-by-Step Checklist for ‘labeling machine manufacturer’
The following checklist serves as a practical guide for international B2B buyers looking to procure labeling machines. It is designed to streamline the sourcing process and ensure that you make informed decisions when selecting a manufacturer.
Step 1: Define Your Technical Specifications
Establishing clear technical specifications is the foundation of your sourcing process. Determine the type of labeling machine that suits your needs, such as automatic or semi-automatic, and identify the materials and sizes of labels you will be using. This clarity will help you communicate effectively with potential suppliers and ensure they can meet your requirements.
Step 2: Research Market Trends and Innovations
Understanding the latest trends and technological advancements in labeling machines can give you a competitive edge. Explore innovations such as digital printing, eco-friendly materials, and automation features that improve efficiency. This knowledge will not only help you in selecting a machine but also in negotiating better terms with suppliers.
Step 3: Evaluate Potential Suppliers
Before making a commitment, thoroughly vet potential suppliers. Request company profiles, case studies, and references from buyers in similar industries or regions. Look for suppliers with a proven track record, especially those who have experience serving businesses in Africa, South America, the Middle East, and Europe.
- Key considerations:
- Industry Experience: Ensure the supplier has expertise in your specific sector.
- Customer Reviews: Look for feedback regarding product quality and service.
Step 4: Verify Supplier Certifications
It’s essential to confirm that your potential suppliers hold relevant certifications, such as ISO, CE, or other industry-specific standards. These certifications indicate compliance with quality and safety regulations, which is crucial for ensuring that the machines you purchase will perform reliably and meet your operational standards.
Step 5: Request Samples and Demonstrations
Before finalizing any order, request samples or demonstrations of the labeling machines. This step allows you to evaluate the quality of the machines firsthand and assess their performance in real-time. Pay attention to ease of use, speed, and the quality of the labels produced.
Step 6: Negotiate Terms and Conditions
Negotiating favorable terms is vital in the procurement process. Discuss pricing, payment terms, delivery schedules, and warranty conditions. Be clear about your expectations and ensure that both parties understand the terms to avoid misunderstandings later on.
Step 7: Plan for After-Sales Support and Training
After making a purchase, ensuring proper after-sales support and training is critical for maximizing your investment. Verify that the supplier offers comprehensive training for your staff and a reliable support system for troubleshooting and maintenance. This support will ensure the longevity of your labeling machine and optimal operational efficiency.
By following these steps, you can enhance your sourcing strategy for labeling machines, ensuring that you find a manufacturer that meets your specific needs and delivers quality products efficiently.
Comprehensive Cost and Pricing Analysis for labeling machine manufacturer Sourcing
What are the Key Cost Components in Sourcing Labeling Machines?
When evaluating the total cost of sourcing labeling machines, several critical components come into play. Understanding these elements is crucial for international B2B buyers, particularly those from Africa, South America, the Middle East, and Europe.
-
Materials: The cost of raw materials significantly impacts the overall pricing. Common materials include stainless steel, plastics, and electronic components. Buyers should consider the quality and source of these materials, as they can vary widely in price and performance.
-
Labor: Labor costs can differ based on the manufacturer’s location. For instance, suppliers in regions with lower labor costs may offer competitive pricing. However, be cautious of potential trade-offs in quality and expertise.
-
Manufacturing Overhead: This includes indirect costs related to production, such as utilities, rent, and equipment maintenance. Understanding how a manufacturer allocates these costs can help buyers identify potential areas for negotiation.
-
Tooling: Tooling costs are associated with the production of specific parts or customizations. If a buyer requires tailored solutions, these costs can escalate. It’s essential to discuss tooling requirements early in the negotiation process.
-
Quality Control (QC): Implementing stringent QC measures ensures product reliability and compliance with industry standards. Buyers should factor in the costs of quality inspections, testing, and certifications when assessing pricing.
-
Logistics: Transportation and handling costs can vary significantly, especially for international shipments. Factors such as shipping distance, mode of transport, and customs duties must be considered to avoid unexpected expenses.
-
Margin: Manufacturers typically include a profit margin in their pricing. This margin can vary based on market conditions and the manufacturer’s business model.
How Do Price Influencers Affect Labeling Machine Costs?
Several factors can influence the pricing of labeling machines beyond the basic cost components:
-
Volume and Minimum Order Quantity (MOQ): Larger orders often lead to reduced per-unit costs. Buyers should assess their needs carefully to leverage economies of scale.
-
Specifications and Customization: Custom features or unique specifications can increase costs. Buyers should clearly define their requirements to avoid unnecessary expenses.
-
Material Quality and Certifications: Higher-quality materials and certifications (e.g., ISO standards) may incur additional costs but can enhance product longevity and performance.
-
Supplier Factors: The manufacturer’s reputation, experience, and location can significantly impact pricing. Established suppliers with a proven track record might charge more but offer greater reliability.
-
Incoterms: The choice of Incoterms determines the responsibilities of buyers and sellers regarding shipping costs and risks. Understanding these terms can lead to better budgeting and negotiation outcomes.
What Buyer Tips Can Help Optimize Costs?
To navigate the complexities of labeling machine sourcing and optimize costs, international B2B buyers should consider the following strategies:
-
Negotiate Effectively: Engage suppliers in open discussions about pricing. Understanding the cost structure allows for informed negotiations, particularly on volume discounts and customization options.
-
Focus on Total Cost of Ownership (TCO): Consider not just the initial purchase price but also maintenance, operation, and potential downtime costs. A lower upfront price may lead to higher TCO if the machine is less reliable.
-
Be Aware of Pricing Nuances: Different regions may have varying pricing norms. For example, buyers in Europe may face stricter regulations that impact costs compared to those in Africa or South America.
-
Conduct Market Research: Stay informed about market trends and competitor pricing to ensure you are getting a fair deal.
-
Request Multiple Quotes: Comparing quotes from different manufacturers can provide insights into standard pricing and help identify the best value for your investment.
Disclaimer for Indicative Prices
It is essential to note that prices can fluctuate based on market conditions, supplier negotiations, and specific project requirements. Therefore, always seek updated quotations tailored to your specific needs before making procurement decisions.
Alternatives Analysis: Comparing labeling machine manufacturer With Other Solutions
In today’s competitive market, international B2B buyers must carefully evaluate their options when considering labeling solutions. While traditional labeling machine manufacturers offer a range of products designed to meet various needs, there are alternative technologies and methods that can also achieve labeling goals. This section compares labeling machine manufacturers against two viable alternatives: manual labeling and digital printing technology.
Comparison Aspect | Labeling Machine Manufacturer | Manual Labeling | Digital Printing Technology |
---|---|---|---|
Performance | High-speed and consistent | Varies by labor skill | High-quality, customizable |
Cost | High initial investment | Low initial investment | Moderate initial investment |
Ease of Implementation | Requires training and setup | Simple and intuitive | Requires design software and setup |
Maintenance | Regular maintenance needed | Minimal maintenance | Regular software updates needed |
Best Use Case | High-volume production | Low-volume, artisanal | Short runs with customization |
What Are the Advantages and Disadvantages of Manual Labeling?
Manual labeling involves using adhesive labels that workers apply by hand. This approach is often favored by small businesses or startups that do not have high production volumes.
Pros:
– Cost-effective: The initial investment is minimal, making it an attractive option for businesses with tight budgets.
– Flexibility: Manual labeling allows for quick changes in labeling designs without needing new machinery.
Cons:
– Inconsistent Quality: The quality of the labeling can vary significantly based on the skill and speed of the labor force.
– Time-consuming: For larger production runs, manual labeling can be inefficient and slow, leading to potential bottlenecks.
How Does Digital Printing Technology Compare?
Digital printing technology allows businesses to print labels on demand, often utilizing high-resolution printers that can produce intricate designs. This method is particularly beneficial for brands requiring customized labels in shorter runs.
Pros:
– Customization: Digital printing enables personalized labels without the need for extensive setup, ideal for limited editions or promotional campaigns.
– High-quality output: This technology can produce vibrant colors and detailed graphics, enhancing product appeal.
Cons:
– Initial Setup Costs: While not as high as labeling machines, the costs associated with software and printers can be significant.
– Speed Limitations: Digital printing may not be as fast as traditional labeling machines for high-volume production, which can limit its use in some manufacturing settings.
How Can B2B Buyers Choose the Right Labeling Solution?
When selecting the appropriate labeling solution, international B2B buyers should assess their specific requirements, including production volume, budget constraints, and the level of customization needed. For high-volume production, a labeling machine manufacturer may be the most suitable choice due to its efficiency and consistency. Conversely, businesses with lower output or those needing frequent label changes may benefit from manual labeling or digital printing technology. Evaluating each option’s performance, cost, and maintenance will help ensure that buyers make informed decisions that align with their operational goals.
Essential Technical Properties and Trade Terminology for labeling machine manufacturer
When exploring the purchase of labeling machines, it’s crucial for international B2B buyers to understand the essential technical properties and trade terminology associated with these products. This knowledge not only aids in making informed decisions but also enhances negotiation processes and overall procurement efficiency.
What Are the Key Technical Properties of Labeling Machines?
1. Material Grade: Why Is It Important?
The material grade of a labeling machine refers to the quality of the components used in its construction. Common materials include stainless steel, aluminum, and high-grade plastics. A higher material grade typically indicates better durability and resistance to corrosion, making it essential for industries such as food and pharmaceuticals where hygiene is paramount. Buyers should assess whether the material grade aligns with their operational environment and product requirements to ensure longevity and compliance with industry standards.
2. Tolerance: How Does It Affect Labeling Accuracy?
Tolerance defines the permissible limit of variation in a machine’s dimensions and performance specifications. In labeling machines, tighter tolerances ensure that labels are applied accurately and consistently, which is critical in maintaining brand integrity and product compliance. Buyers should inquire about the tolerances offered by manufacturers to ensure they meet their specific labeling needs, particularly in high-speed or high-volume production scenarios.
3. Speed: What Is the Optimal Rate for Your Production Line?
The speed of a labeling machine, often measured in labels per minute (LPM), is a vital specification for businesses with high throughput requirements. A machine that operates too slowly can bottleneck production, leading to inefficiencies and increased operational costs. Buyers should evaluate their production capacity and choose a labeling machine that can meet or exceed their operational demands without sacrificing quality.
4. Applicator Type: Which Is Best for Your Products?
Labeling machines may feature various applicator types, such as wipe-on, blow-on, or tamp-blow systems, each suited for different packaging formats and environments. Understanding which applicator type best fits your product line can significantly impact efficiency and labeling accuracy. Buyers should consider the nature of their products, including shape and surface material, when selecting an applicator type.
5. Power Requirements: What Should You Consider?
Labeling machines can be powered through various means, including electric, pneumatic, or hydraulic systems. Each type has its advantages and operational requirements. Buyers should assess their facility’s existing infrastructure to determine which power source aligns with their operational capabilities, as this can affect installation costs and machine performance.
Which Trade Terms Should B2B Buyers Know?
1. What Is OEM (Original Equipment Manufacturer)?
An OEM refers to a company that produces parts or equipment that may be marketed by another manufacturer. In the context of labeling machines, understanding OEM relationships can help buyers identify quality standards and potential customization options. Buyers should inquire about the OEM status of the labeling machine manufacturer to ensure reliability and quality.
2. What Does MOQ (Minimum Order Quantity) Mean?
MOQ is the smallest quantity of a product that a supplier is willing to sell. Understanding MOQ is critical for B2B buyers, as it can affect inventory management and cash flow. Buyers should negotiate MOQs that align with their operational needs to avoid overstocking or stockouts.
3. What Is an RFQ (Request for Quotation)?
An RFQ is a document used by buyers to solicit price quotes from suppliers. It should include detailed specifications of the labeling machine required. This process allows buyers to compare offers comprehensively and negotiate better terms. Crafting a precise RFQ is essential for obtaining accurate quotations.
4. What Are Incoterms and Why Are They Important?
Incoterms are international commercial terms that define the responsibilities of buyers and sellers in international transactions. They cover aspects such as shipping, insurance, and risk management. Understanding these terms helps buyers clarify shipping costs and liabilities, which is vital for accurate budgeting and risk assessment.
By familiarizing themselves with these technical properties and trade terminologies, international B2B buyers can make more informed decisions when purchasing labeling machines, ensuring that they select equipment that meets their operational needs and aligns with their business objectives.
Navigating Market Dynamics and Sourcing Trends in the labeling machine manufacturer Sector
What Are the Key Market Drivers and Trends in the Labeling Machine Sector?
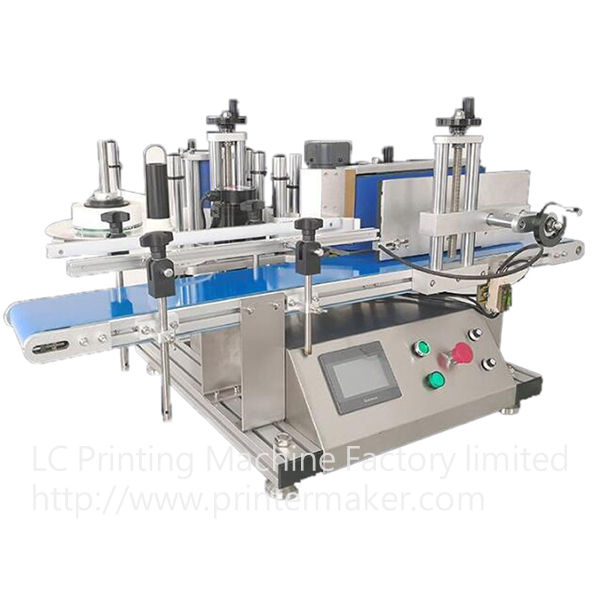
A stock image related to labeling machine manufacturer.
The labeling machine manufacturing sector is experiencing significant evolution driven by several global factors. The surge in e-commerce and the demand for automated solutions are reshaping the landscape, making efficiency and precision paramount for international buyers. This trend is particularly evident in Africa and South America, where manufacturers are increasingly adopting advanced technologies, such as AI and IoT, to enhance productivity. Moreover, the Middle East and European markets are witnessing a push towards smart labeling systems that integrate with existing production lines, catering to the need for real-time data analytics.
Emerging trends include the customization of labeling solutions tailored to diverse industries, from food and beverage to pharmaceuticals. As regulations become more stringent, manufacturers are also focusing on compliance and traceability features in their labeling machines. For B2B buyers, understanding these dynamics is crucial; sourcing from manufacturers who prioritize innovation and adaptability can provide a competitive edge in rapidly changing markets.
How Does Sustainability Impact Sourcing Decisions in the Labeling Machine Sector?
The growing emphasis on sustainability and ethical sourcing is reshaping procurement strategies within the labeling machine sector. Environmental concerns are prompting manufacturers to adopt eco-friendly practices, including the use of biodegradable materials and energy-efficient production processes. Buyers from regions like Europe and the Middle East are increasingly prioritizing suppliers who demonstrate a commitment to sustainability, as this not only enhances brand reputation but also aligns with regulatory requirements.
Ethical supply chains are becoming a focal point, with transparency in sourcing and production processes gaining importance. Certifications such as ISO 14001 (Environmental Management) and FSC (Forest Stewardship Council) are critical for buyers seeking to verify the sustainability of their suppliers. Furthermore, the demand for ‘green’ labeling materials is on the rise, pushing manufacturers to innovate and offer solutions that minimize environmental impact. For international B2B buyers, aligning sourcing decisions with sustainability goals can lead to more responsible business practices and increased customer loyalty.
How Has the Labeling Machine Manufacturing Sector Evolved Over Time?
The labeling machine manufacturing sector has undergone significant transformation over the decades, evolving from manual processes to highly automated systems. Initially, labeling was a labor-intensive task, but the advent of advanced technologies in the late 20th century marked a turning point. The introduction of computerized labeling systems improved accuracy and efficiency, setting the stage for the modern era of automated solutions.
As industries expanded and global trade increased, the demand for versatile and reliable labeling machines grew. Today, manufacturers are not only focused on enhancing operational efficiency but also on integrating sustainability into their business models. This evolution reflects broader trends in global manufacturing, where innovation, sustainability, and compliance are intertwined, creating a robust framework for future developments in the labeling machine sector. For B2B buyers, understanding this evolution is key to making informed sourcing decisions that align with current market demands and future trends.
Frequently Asked Questions (FAQs) for B2B Buyers of labeling machine manufacturer
-
How do I select the right labeling machine for my business needs?
Choosing the right labeling machine involves assessing your production requirements, including the type of products being labeled, the volume of production, and specific labeling needs (e.g., size, shape, and material of labels). Additionally, consider the machine’s speed, accuracy, and compatibility with your existing production line. Engaging with manufacturers to discuss your specific needs and requesting samples can also aid in making an informed decision. -
What are the common types of labeling machines available for B2B buyers?
B2B buyers can choose from several types of labeling machines, including semi-automatic, fully automatic, and manual machines. Each type serves different production capacities and labeling complexities. For instance, semi-automatic machines are ideal for lower volume production, while fully automatic machines are suited for high-speed operations. It’s essential to evaluate your production scale and label requirements when selecting the machine type. -
What customization options are available for labeling machines?
Most labeling machine manufacturers offer a range of customization options to meet specific business needs. Customizations may include label size, printing technology (thermal transfer, inkjet, etc.), and machine features (such as coding and marking). Discussing your unique requirements with manufacturers can lead to tailored solutions that enhance operational efficiency and meet regulatory compliance. -
What is the minimum order quantity (MOQ) for labeling machines?
Minimum order quantities can vary significantly between manufacturers. Some may have a MOQ of one unit for standard models, while others might require larger orders for customized machines. When sourcing from international suppliers, it is crucial to clarify MOQ during negotiations to avoid unexpected costs and to ensure that your order aligns with your production needs. -
What payment terms should I expect when purchasing a labeling machine internationally?
Payment terms can differ by manufacturer and region. Common arrangements include upfront payments, partial payments with balance upon delivery, or payment against documents. It is advisable to negotiate favorable terms that align with your cash flow and risk management strategies. Additionally, consider using secure payment methods and trade finance options to mitigate financial risks. -
How can I ensure quality assurance (QA) when sourcing labeling machines?
To ensure quality assurance, request certifications and compliance documentation from manufacturers, such as ISO certifications or CE marking. Conducting factory audits and requesting samples for testing can further validate the quality of the machines. Establishing a reliable relationship with suppliers and maintaining clear communication about quality expectations will also enhance the QA process. -
What are the logistics considerations for importing labeling machines?
Logistics play a critical role in the international procurement of labeling machines. Buyers should consider shipping methods, customs regulations, and potential tariffs when planning their imports. Engaging a freight forwarder can streamline the shipping process and help navigate complex customs requirements. Additionally, understanding the lead times for manufacturing and shipping can help manage expectations and production schedules. -
How do I vet potential labeling machine manufacturers before making a purchase?
Vetting manufacturers involves researching their industry reputation, reviewing client testimonials, and assessing their experience in producing labeling machines. Requesting references from previous clients can provide insights into their reliability and service quality. Additionally, consider visiting their facilities if possible, or attending industry trade shows to evaluate their products firsthand and engage in direct discussions about your requirements.
Important Disclaimer & Terms of Use
⚠️ Important Disclaimer
The information provided in this guide, including content regarding manufacturers, technical specifications, and market analysis, is for informational and educational purposes only. It does not constitute professional procurement advice, financial advice, or legal advice.
While we have made every effort to ensure the accuracy and timeliness of the information, we are not responsible for any errors, omissions, or outdated information. Market conditions, company details, and technical standards are subject to change.
B2B buyers must conduct their own independent and thorough due diligence before making any purchasing decisions. This includes contacting suppliers directly, verifying certifications, requesting samples, and seeking professional consultation. The risk of relying on any information in this guide is borne solely by the reader.
Strategic Sourcing Conclusion and Outlook for labeling machine manufacturer
As the global market for labeling machines continues to evolve, international B2B buyers must adopt a strategic sourcing approach to remain competitive. Understanding the unique needs and regulatory requirements of your specific region—whether in Africa, South America, the Middle East, or Europe—can significantly enhance your procurement strategy. Prioritizing suppliers that offer innovative, customizable solutions and robust support services will ensure that your labeling operations not only comply with local standards but also drive efficiency and cost-effectiveness.
Why is Strategic Sourcing Essential for Your Labeling Needs?
The value of strategic sourcing lies in its ability to align your business objectives with the capabilities of your suppliers. By fostering strong partnerships with manufacturers, you can leverage their expertise in technology advancements, ensuring that your labeling processes are optimized for performance and sustainability.
What Should International Buyers Focus On Moving Forward?
Looking ahead, it is crucial for B2B buyers to stay abreast of emerging trends in automation and sustainability within the labeling industry. Investing in cutting-edge technology will not only improve operational efficiency but also position your business as a leader in sustainable practices.
Take action today by evaluating your current suppliers and exploring new partnerships that align with your strategic goals. Embrace the future of labeling technology and unlock the full potential of your operations.