The Ultimate Guide to Laser Cutting Machines China (2025)
Introduction: Navigating the Global Market for laser cutting machines china
Navigating the complexities of sourcing laser cutting machines from China can be a daunting task for international B2B buyers. With a myriad of suppliers, varying technologies, and fluctuating costs, it’s essential to have a clear roadmap to make informed purchasing decisions. This guide aims to demystify the process by providing an in-depth overview of the different types of laser cutting machines available, their applications across various industries, and the critical factors to consider when vetting suppliers.
Understanding the landscape of laser cutting technology is crucial for businesses in regions like Africa, South America, the Middle East, and Europe, including key markets such as Egypt and Italy. The guide will cover essential topics such as the latest advancements in laser technology, practical applications in manufacturing and design, and comprehensive strategies for assessing supplier credibility. Additionally, we will explore cost considerations, ensuring you can budget effectively while maximizing value.
By equipping you with actionable insights and expert recommendations, this guide empowers B2B buyers to navigate the global market with confidence. Whether you’re looking to enhance production capabilities or explore new applications for laser cutting, our comprehensive resource is designed to streamline your decision-making process and ultimately drive business growth.
Understanding laser cutting machines china Types and Variations
Type Name | Key Distinguishing Features | Primary B2B Applications | Brief Pros & Cons for Buyers |
---|---|---|---|
CO2 Laser Cutting Machines | Utilizes a gas laser, ideal for non-metal materials. | Wood, acrylic, textiles cutting | Pros: Cost-effective, versatile for various materials. Cons: Slower cutting speed for metals. |
Fiber Laser Cutting Machines | Uses fiber optics for high precision and speed, ideal for metals. | Metal fabrication, automotive parts | Pros: High efficiency, minimal maintenance. Cons: Higher initial investment. |
YAG Laser Cutting Machines | Solid-state laser, suitable for both metals and plastics. | Aerospace, electronics industries | Pros: Good for thick materials, long lifespan. Cons: Limited to specific materials. |
Ultrafast Laser Cutting Machines | Delivers extremely short pulse durations, minimizing heat impact. | Medical devices, microelectronics | Pros: High precision, excellent for delicate applications. Cons: Expensive technology. |
Laser Engraving Machines | Combines cutting and engraving capabilities, often CO2-based. | Personalized products, signage | Pros: Multi-functional, ideal for customization. Cons: Slower than dedicated cutting machines. |
What are the characteristics of CO2 Laser Cutting Machines?
CO2 laser cutting machines are characterized by their use of a gas laser that emits a wavelength suitable for cutting a wide range of non-metal materials, including wood, acrylic, and textiles. They are particularly favored for their cost-effectiveness and versatility, making them a popular choice among small to medium-sized enterprises looking to enter the laser cutting market. B2B buyers should consider the type of materials they intend to work with, as these machines may not be optimal for cutting metals.
How do Fiber Laser Cutting Machines stand out?
Fiber laser cutting machines are known for their high precision and speed, making them ideal for metal cutting applications. They utilize fiber optics to deliver a concentrated beam, resulting in clean cuts and reduced operational costs due to their energy efficiency. For businesses in the metal fabrication or automotive industries, investing in fiber laser technology can lead to significant productivity gains. However, buyers must be prepared for a higher upfront investment compared to CO2 machines.
What makes YAG Laser Cutting Machines suitable for specific industries?
YAG (Yttrium Aluminum Garnet) laser cutting machines are solid-state lasers that excel in cutting both metals and plastics. They are particularly well-suited for industries like aerospace and electronics, where precision and the ability to handle thicker materials are crucial. The longevity and reliability of YAG lasers can be appealing to B2B buyers, although they may be limited to specific applications and materials, which should be carefully evaluated before purchase.
Why are Ultrafast Laser Cutting Machines considered advanced?
Ultrafast laser cutting machines utilize extremely short pulse durations, which minimizes heat-affected zones during cutting. This technology is particularly advantageous for applications in the medical device and microelectronics sectors, where precision is paramount. While these machines offer unparalleled accuracy, they come with a higher price tag, making them a consideration for businesses with specialized needs and budgets to match.
How do Laser Engraving Machines add value?
Laser engraving machines provide the dual capability of cutting and engraving, often based on CO2 technology. They are ideal for creating personalized products and signage, making them a popular choice for businesses focused on customization. While they offer multifunctionality, buyers should be aware that these machines may operate slower than dedicated cutting machines, which could impact production timelines in high-volume environments.
Related Video: China coil fed laser blanking machine,Coil fed fiber laser cutting system with automatic stacker
Key Industrial Applications of laser cutting machines china
Industry/Sector | Specific Application of laser cutting machines china | Value/Benefit for the Business | Key Sourcing Considerations for this Application |
---|---|---|---|
Automotive | Precision cutting of metal components | Enhanced accuracy and reduced waste in production | Evaluate machine precision, after-sales support, and availability of spare parts. |
Aerospace | Cutting complex shapes in lightweight materials | Improved performance and fuel efficiency of aircraft | Assess certifications, material compatibility, and technical support. |
Electronics | PCB manufacturing and cutting intricate designs | Higher production speed and lower defect rates | Focus on machine automation capabilities and integration with existing systems. |
Metal Fabrication | Custom metal part production | Flexibility in design and rapid prototyping | Check for customization options and local service availability. |
Furniture Manufacturing | Laser cutting of wood and composite materials | Enhanced design possibilities and aesthetic finishes | Ensure compliance with local regulations and material specifications. |
How Are Laser Cutting Machines Used in the Automotive Sector?
In the automotive industry, laser cutting machines from China are crucial for precision cutting of metal components such as chassis parts, brackets, and body panels. These machines offer enhanced accuracy, allowing manufacturers to minimize waste and optimize material usage. International buyers should prioritize sourcing machines with high precision and robust after-sales support, as well as ensuring the availability of spare parts for maintenance.
What Are the Applications of Laser Cutting in Aerospace Manufacturing?
Aerospace manufacturers leverage laser cutting machines to create complex shapes in lightweight materials like aluminum and titanium. This technology not only improves the performance of aircraft but also contributes to fuel efficiency by reducing overall weight. Buyers in this sector should consider sourcing machines with specific aerospace certifications and assess their compatibility with the materials they intend to use, along with the availability of technical support.
How Do Electronics Manufacturers Benefit from Laser Cutting Machines?
In the electronics sector, laser cutting machines are employed for the manufacturing of printed circuit boards (PCBs) and cutting intricate designs in various substrates. This technology leads to higher production speeds and lower defect rates, which are critical for maintaining competitive advantage. B2B buyers should focus on machines that offer automation capabilities and seamless integration with existing manufacturing systems to enhance productivity.
What Role Do Laser Cutting Machines Play in Metal Fabrication?
Metal fabrication companies utilize laser cutting machines for custom metal part production, allowing for flexibility in design and rapid prototyping. This capability enables businesses to respond quickly to market demands and produce unique products efficiently. When sourcing these machines, it’s important for buyers to check for customization options and the availability of local service to ensure timely support and maintenance.
How Are Laser Cutting Machines Transforming Furniture Manufacturing?
In the furniture manufacturing industry, laser cutting machines are used to cut wood and composite materials, enabling manufacturers to achieve intricate designs and high-quality finishes. This technology enhances aesthetic appeal while maintaining structural integrity. Buyers should ensure that the machines comply with local regulations and meet the specific material requirements to avoid complications during production.
Related Video: How does the CNC Fiber laser cutting machine work? – Factories
3 Common User Pain Points for ‘laser cutting machines china’ & Their Solutions
Scenario 1: Difficulty in Identifying Quality Suppliers for Laser Cutting Machines from China
The Problem:
Many international B2B buyers, particularly from regions like Africa and South America, face significant challenges when trying to identify trustworthy suppliers of laser cutting machines from China. The sheer volume of manufacturers can be overwhelming, and distinguishing between high-quality suppliers and those offering subpar products is often a daunting task. This challenge is compounded by language barriers, varying quality standards, and concerns about after-sales support. As a result, buyers risk investing in equipment that may not meet their production needs or may fail prematurely, leading to costly downtimes.
The Solution:
To navigate this issue effectively, buyers should engage in thorough due diligence before making a purchasing decision. Start by utilizing reputable online platforms like Alibaba or Global Sources, where you can filter suppliers based on ratings and certifications. Look for suppliers with a proven track record, verified customer reviews, and those who can provide detailed product specifications. Additionally, consider requesting samples of their products to assess quality firsthand. Finally, establishing clear communication with suppliers is essential; use a translator if necessary to ensure all specifications and expectations are clearly understood.
Scenario 2: Understanding the Technical Specifications of Laser Cutting Machines
The Problem:
Another common pain point for B2B buyers is the complexity of technical specifications associated with laser cutting machines. For buyers from Europe or the Middle East, understanding how factors like laser power, cutting speed, and material compatibility affect performance can be particularly challenging. Misunderstandings in this area can lead to purchasing equipment that does not align with production requirements, resulting in inefficient operations and increased costs.
The Solution:
Buyers should prioritize acquiring a strong understanding of the technical specifications relevant to their specific industry needs. Start by consulting with industry experts or technical advisors who can provide insights into the laser cutting technology best suited for your materials and production volumes. Additionally, many manufacturers offer online resources and technical documentation that can be invaluable in making informed decisions. Taking the time to attend trade shows or webinars can also help buyers understand the latest advancements in laser cutting technology and how they can benefit their operations.
Scenario 3: Ensuring Reliable After-Sales Support and Service
The Problem:
International buyers often express concern about the level of after-sales support they will receive after purchasing laser cutting machines from China. This concern is particularly prevalent among businesses in regions like Africa and the Middle East, where access to prompt and effective service can be limited. Buyers worry about potential machine malfunctions or the need for maintenance and whether they will be able to receive timely assistance from their suppliers.
The Solution:
To mitigate these concerns, buyers should specifically inquire about after-sales support during the procurement process. Before finalizing any agreements, ensure that the supplier provides a comprehensive warranty, details on service availability, and the process for obtaining spare parts. Additionally, consider opting for suppliers who have established a local presence or partnerships in your region, as this can significantly improve response times for service and support. Lastly, establishing a clear service level agreement (SLA) that outlines expected response times and support conditions can further safeguard your investment in the laser cutting machinery.
Strategic Material Selection Guide for laser cutting machines china
What Are the Key Materials for Laser Cutting Machines in China?
When selecting materials for laser cutting applications, it’s crucial to understand their properties, advantages, and limitations. This knowledge is particularly valuable for international B2B buyers from regions such as Africa, South America, the Middle East, and Europe. Here, we analyze four common materials used in laser cutting machines manufactured in China.
How Does Steel Perform in Laser Cutting Applications?
Key Properties:
Steel is known for its strength and durability. It typically has a high melting point (around 1370°C) and excellent corrosion resistance, especially when treated or alloyed.
Pros & Cons:
Steel is highly durable and suitable for heavy-duty applications. However, it can be more challenging to cut due to its density, requiring higher power lasers. The cost of high-quality steel can be significant, affecting overall project budgets.
Impact on Application:
Steel is ideal for structural components and industrial applications. Its compatibility with various coatings and finishes makes it versatile for different end products.
Considerations for International Buyers:
Buyers should ensure compliance with local standards such as ASTM or DIN for steel grades. In regions like Europe and the Middle East, specific certifications may be required for construction materials.
What Are the Advantages of Using Aluminum in Laser Cutting?
Key Properties:
Aluminum is lightweight and has a melting point of approximately 660°C. It offers good corrosion resistance and is easily machinable.
Pros & Cons:
The primary advantage of aluminum is its lightweight nature, making it suitable for applications where weight is a concern. However, it can be more expensive than steel, and its lower melting point may lead to warping during cutting.
Impact on Application:
Aluminum is commonly used in aerospace and automotive industries due to its strength-to-weight ratio. It is also ideal for decorative applications due to its ability to be anodized.
Considerations for International Buyers:
Buyers should consider the specific aluminum grades that comply with international standards. In regions like Africa and South America, sourcing high-quality aluminum can be a challenge due to availability.
Why Choose Plastics for Laser Cutting?
Key Properties:
Plastics like acrylic and polycarbonate have lower melting points (around 100-160°C) and are resistant to corrosion and chemicals.
Pros & Cons:
Plastics are cost-effective and easy to cut, making them ideal for prototypes and signage. However, they may not be suitable for high-strength applications and can be less durable than metals.
Impact on Application:
Plastics are widely used in consumer products, signage, and packaging. Their versatility allows for intricate designs and custom shapes.
Considerations for International Buyers:
Buyers should ensure that the plastics used meet local environmental regulations, especially in Europe, where restrictions on certain materials may apply.
How Does Wood Fare in Laser Cutting Applications?
Key Properties:
Wood is a natural material with variable density and melting points depending on the type. It generally has good machinability and is biodegradable.
Pros & Cons:
Wood is widely available and cost-effective, making it suitable for a variety of applications. However, its variability can lead to inconsistent cutting results, and it may require additional treatments for durability.
Impact on Application:
Wood is commonly used for furniture, crafts, and decorative items. Its aesthetic appeal makes it a popular choice for custom projects.
Considerations for International Buyers:
Buyers should be aware of local regulations regarding the sourcing of wood, particularly in terms of sustainability and certification (e.g., FSC certification in Europe).
Summary Table of Material Selection for Laser Cutting Machines
Material | Typical Use Case for laser cutting machines china | Key Advantage | Key Disadvantage/Limitation | Relative Cost (Low/Med/High) |
---|---|---|---|---|
Steel | Structural components, industrial applications | High durability and strength | Difficult to cut, higher power needed | High |
Aluminum | Aerospace, automotive, decorative applications | Lightweight, good corrosion resistance | Expensive, may warp during cutting | Medium |
Plastics | Prototypes, signage, packaging | Cost-effective, easy to cut | Less durable, not for high-strength use | Low |
Wood | Furniture, crafts, decorative items | Aesthetic appeal, widely available | Variable quality, inconsistent results | Low |
This strategic material selection guide provides international B2B buyers with essential insights to make informed decisions regarding laser cutting applications. Understanding the properties, advantages, and limitations of each material will aid in selecting the best option for specific projects.
In-depth Look: Manufacturing Processes and Quality Assurance for laser cutting machines china
What Are the Main Stages in the Manufacturing Process of Laser Cutting Machines from China?
The manufacturing of laser cutting machines involves several critical stages that ensure high-quality output and efficiency. Understanding these stages is vital for international B2B buyers, especially those from Africa, South America, the Middle East, and Europe.
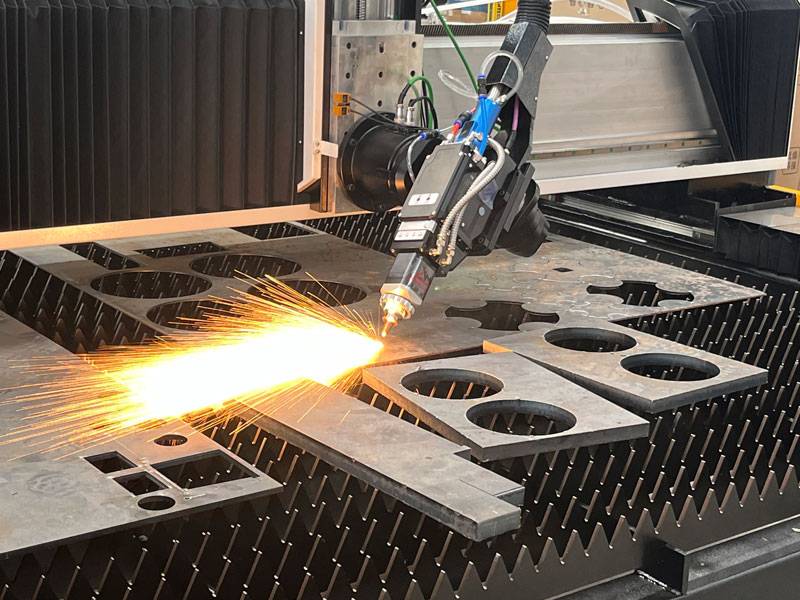
A stock image related to laser cutting machines china.
1. Material Preparation
The first step in the manufacturing process is material preparation. This includes the selection of high-quality raw materials, such as steel and aluminum, which are essential for the structural integrity of the machines. Suppliers often conduct thorough inspections to ensure that the materials meet specified standards.
In addition, cutting-edge technologies like computer-aided design (CAD) are employed to create precise specifications for the components. This preparation phase sets the foundation for the subsequent stages and significantly impacts the overall performance of the laser cutting machines.
2. Forming and Machining
Once the materials are prepared, the next stage is forming and machining. This involves processes such as bending, cutting, and milling to shape the components according to the design specifications. Advanced CNC (Computer Numerical Control) machines are commonly used for their precision and efficiency.
The forming techniques may vary based on the complexity of the design and the type of materials used. For example, sheet metal is often formed using laser cutting technology, which not only provides accuracy but also reduces waste.
3. Assembly
The assembly stage is where all the machined parts are brought together. This is a crucial step that requires skilled technicians to ensure that the components fit together correctly. Quality assurance checks are often implemented throughout the assembly process to catch any potential issues early.
Many manufacturers adopt modular assembly techniques, allowing for easier troubleshooting and maintenance. This approach also facilitates customization, enabling buyers to request specific features or adjustments based on their operational needs.
4. Finishing Processes
After assembly, the machines undergo various finishing processes, including painting, coating, and surface treatments. These processes not only enhance the aesthetic appeal of the machines but also provide protective layers that improve durability and resistance to corrosion.
Final inspections are conducted during this stage to ensure that the machines meet quality standards before they are packaged and shipped.
How Is Quality Assurance Implemented in the Manufacturing of Laser Cutting Machines?
Quality assurance (QA) is a critical aspect of the manufacturing process for laser cutting machines. It ensures that the final products meet international standards and customer expectations.
International Standards for Quality Assurance
For international B2B buyers, understanding the relevant quality standards is crucial. Many manufacturers in China adhere to ISO 9001, which focuses on quality management systems. Compliance with this standard indicates that the manufacturer consistently provides products that meet customer and regulatory requirements.
In addition to ISO standards, industry-specific certifications such as CE (Conformité Européenne) for European markets and API (American Petroleum Institute) standards for the oil and gas sector may also be applicable. These certifications provide assurance regarding the safety and reliability of the machines.
What Are the Key Quality Control Checkpoints?
Quality control (QC) involves multiple checkpoints throughout the manufacturing process:
-
Incoming Quality Control (IQC): This is the first line of defense, where raw materials are inspected upon arrival. IQC ensures that the materials meet specified quality standards before they enter the production process.
-
In-Process Quality Control (IPQC): During the manufacturing stages, regular inspections are conducted to monitor the quality of components as they are being formed and assembled. This helps to identify and rectify any defects early in the process.
-
Final Quality Control (FQC): Once the machines are fully assembled and finished, a thorough final inspection is conducted. This includes functional testing and performance evaluations to ensure that the machines operate as intended.
How Can B2B Buyers Verify Supplier Quality Control?
For international buyers, especially from regions like Africa and South America where supply chain risks may be higher, verifying supplier quality control is essential. Here are several strategies to consider:
Conduct Supplier Audits
Performing audits is one of the most effective ways to assess a supplier’s quality control processes. An on-site audit allows buyers to observe the manufacturing environment, evaluate the quality management systems in place, and assess compliance with international standards.
Request Quality Reports
Buyers should request quality control reports from suppliers. These reports should detail the results of IQC, IPQC, and FQC, including any corrective actions taken for non-conformities. Analyzing these reports can provide insights into the supplier’s commitment to quality.
Utilize Third-Party Inspection Services
Engaging third-party inspection services can provide an unbiased evaluation of the manufacturing processes and quality assurance measures implemented by suppliers. These services can conduct random inspections and provide detailed reports that buyers can use to make informed decisions.
What Are the Quality Control Nuances for International Buyers?
Understanding the nuances of quality control is vital for international B2B buyers. Different regions may have varying standards and expectations regarding quality. Here are some considerations:
-
Regulatory Compliance: Buyers must be aware of the regulatory requirements in their respective countries. For instance, European buyers may prioritize CE certification, while Middle Eastern buyers may focus on local compliance standards.
-
Cultural Differences: Different cultures may have varying approaches to quality and business practices. Establishing clear communication and expectations can help bridge these gaps.
-
Post-Purchase Support: Quality assurance doesn’t end with the purchase. Buyers should inquire about warranty periods, maintenance support, and availability of spare parts to ensure long-term satisfaction with their laser cutting machines.
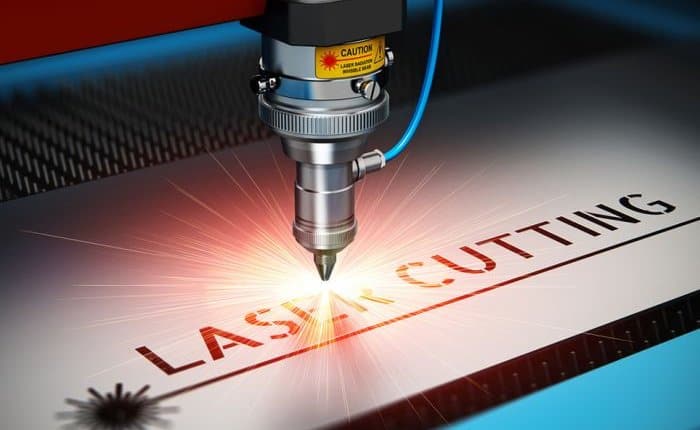
A stock image related to laser cutting machines china.
By understanding the manufacturing processes and quality assurance measures involved in the production of laser cutting machines from China, international B2B buyers can make informed decisions that align with their operational needs and quality expectations.
Practical Sourcing Guide: A Step-by-Step Checklist for ‘laser cutting machines china’
This practical sourcing guide is designed to assist international B2B buyers in navigating the procurement process for laser cutting machines from China. By following this step-by-step checklist, you can ensure that you make informed decisions that align with your business needs and budget.
Step 1: Define Your Technical Specifications
Establishing clear technical specifications is crucial for identifying the right laser cutting machine for your operations. Determine the materials you plan to cut, the thickness of these materials, and the desired cutting speed and precision. This information will help you communicate effectively with potential suppliers and avoid misunderstandings.
- Materials: Common materials include metal, wood, and acrylic. Each may require different laser types (e.g., CO2 or fiber lasers).
- Thickness and Speed: Define the maximum material thickness and the production speed you need to maintain efficiency.
Step 2: Research Potential Suppliers
Conduct thorough research on suppliers who specialize in laser cutting machines in China. Utilize online platforms, industry directories, and trade shows to gather a list of potential candidates. It’s essential to assess their market presence and reputation.
- Online Platforms: Websites like Alibaba and Made-in-China can provide extensive supplier listings.
- Trade Shows: Attend industry-specific trade shows to meet suppliers in person and view their machines.
Step 3: Evaluate Supplier Certifications and Standards
Before proceeding with any supplier, verify their certifications and compliance with international standards. Look for ISO certifications and other relevant quality assurance measures to ensure that the machines meet safety and performance standards.
- ISO Certifications: These indicate adherence to quality management and operational standards.
- Compliance: Check if they comply with local regulations in your country regarding machinery imports.
Step 4: Request Detailed Quotations
Once you have shortlisted potential suppliers, request detailed quotations that include pricing, payment terms, and lead times. A comprehensive quote will help you compare options effectively and identify any hidden costs.
- Cost Breakdown: Ensure that the quote includes all costs, such as shipping, customs duties, and installation.
- Payment Terms: Understand the payment structure, including deposits and payment milestones.
Step 5: Assess After-Sales Support and Warranty
Evaluate the after-sales support offered by the supplier, including warranty terms and maintenance services. Strong after-sales support can be crucial for minimizing downtime and ensuring operational efficiency.
- Warranty: A good warranty period should cover defects and malfunctions.
- Support Services: Check if they offer technical support, training, and spare parts availability.
Step 6: Conduct a Factory Visit (If Possible)
If feasible, arrange a factory visit to inspect the manufacturing processes and quality control measures in place. This step provides firsthand insight into the supplier’s capabilities and helps build trust.
- Inspection: Look for advanced manufacturing techniques and quality checks during production.
- Engagement: Engage with the technical team to discuss machine operation and maintenance protocols.
Step 7: Finalize the Contract
After selecting a supplier, ensure that all terms are clearly outlined in a contract. This should include delivery timelines, payment schedules, and any contingencies for potential issues.
- Clarity: The contract should be unambiguous to avoid disputes later.
- Legal Review: Consider having the contract reviewed by a legal professional to safeguard your interests.
By following this checklist, B2B buyers can streamline their sourcing process for laser cutting machines from China, ensuring they make informed and strategic purchasing decisions.
Comprehensive Cost and Pricing Analysis for laser cutting machines china Sourcing
Understanding the cost structure and pricing of laser cutting machines sourced from China is vital for international B2B buyers, especially those from regions like Africa, South America, the Middle East, and Europe. This analysis will explore the key components that influence costs, the factors affecting pricing, and actionable tips for buyers to optimize their sourcing strategy.
What Are the Main Cost Components of Laser Cutting Machines from China?
-
Materials: The cost of raw materials, such as metals and optical components, plays a significant role in the overall pricing of laser cutting machines. Fluctuations in commodity prices can directly impact manufacturing costs. Buyers should consider sourcing materials in bulk to negotiate better rates.
-
Labor: Labor costs in China are generally lower than in many Western countries, but they can vary significantly by region and skill level. Understanding the local labor market can help buyers gauge the potential impact on pricing.
-
Manufacturing Overhead: This includes utilities, rent, and other operational costs incurred during production. Efficient manufacturers often pass on lower overhead costs to buyers, making it essential to evaluate supplier facilities.
-
Tooling: Specialized tooling required for the production of laser cutting machines can be expensive. Buyers should inquire about tooling costs, especially for customized machines, as these can significantly affect the final price.
-
Quality Control (QC): Implementing a robust QC process ensures that the machines meet international standards. However, stringent QC measures can also increase production costs. Buyers should weigh the benefits of quality assurance against price.
-
Logistics: Shipping costs, including freight, insurance, and customs duties, are critical components of total cost. Buyers should consider logistics when calculating the total cost of ownership and explore various shipping options to minimize expenses.
-
Margin: Suppliers typically add a profit margin to their manufacturing costs. Understanding the margin expectations of Chinese manufacturers can aid in negotiation strategies.
What Influences the Pricing of Laser Cutting Machines?
-
Volume/MOQ (Minimum Order Quantity): Larger orders often attract discounts. Buyers should assess their needs and consider consolidating orders with other buyers to meet MOQ requirements.
-
Specifications and Customization: Custom features or specific technical requirements can lead to increased costs. Buyers should clearly define their needs to avoid unnecessary expenses.
-
Material Quality and Certifications: Higher quality materials and compliance with international certifications (e.g., CE, ISO) can increase costs but are essential for reliability and safety. Buyers should prioritize suppliers who can provide certification documentation.
-
Supplier Factors: The reputation and experience of the supplier can influence pricing. Established suppliers with a track record of quality may charge a premium but can offer peace of mind regarding reliability.
-
Incoterms: The terms of sale can significantly affect costs. Understanding Incoterms (e.g., FOB, CIF) helps buyers calculate logistics and delivery expenses accurately.
How Can Buyers Negotiate and Optimize Costs?
-
Negotiation Tactics: Engage in open discussions with suppliers about pricing flexibility. Many suppliers are willing to negotiate, especially for larger orders or long-term partnerships.
-
Focus on Total Cost of Ownership (TCO): Consider not only the initial purchase price but also maintenance, operational costs, and potential downtime. A lower upfront cost may not always result in the best value.
-
Understand Pricing Nuances: Be aware that prices can vary based on market demand, exchange rates, and seasonal factors. Keeping abreast of these elements can help in making informed purchasing decisions.
-
Leverage Regional Insights: Buyers from specific regions like Egypt, Italy, or Brazil should understand local market conditions that may affect pricing and supplier availability. Engaging with local trade representatives can provide valuable insights.
Conclusion and Disclaimer
While the prices for laser cutting machines sourced from China can vary widely based on the factors discussed, buyers should conduct thorough research and engage in strategic negotiations to achieve the best possible value. It is important to note that prices mentioned in this analysis are indicative and can fluctuate based on market conditions. Always consult directly with suppliers for the most accurate and current pricing information.
Alternatives Analysis: Comparing laser cutting machines china With Other Solutions
When evaluating options for precision cutting in manufacturing, understanding the alternatives to “laser cutting machines from China” is essential for making informed decisions. This section will compare laser cutting technology with alternative methods such as plasma cutting and waterjet cutting. Each method has distinct advantages and drawbacks, which can significantly impact operational efficiency and cost-effectiveness for international B2B buyers.
Comparison Aspect | Laser Cutting Machines China | Plasma Cutting | Waterjet Cutting |
---|---|---|---|
Performance | High precision, clean cuts | Good for thicker materials, less precision | Versatile with various materials, smooth edges |
Cost | Moderate initial investment, low operating costs | Lower initial cost, higher operating costs | Higher initial investment, moderate operating costs |
Ease of Implementation | Requires skilled technicians | Easier to set up and use | Complex setup, requires specialized training |
Maintenance | Low maintenance, regular checks needed | Moderate maintenance needs | High maintenance due to water filtration systems |
Best Use Case | Thin to medium materials, intricate designs | Thicker metals and industrial applications | Materials like glass, stone, and metals needing no heat-affected zone |
What Are the Advantages and Disadvantages of Plasma Cutting as an Alternative?
Plasma cutting is a viable alternative to laser cutting machines, especially for thicker materials. It operates by sending a gas through a nozzle at high speed and electrically ionizing it to create a plasma arc. This method allows for faster cutting speeds and can handle materials up to several inches thick. However, it lacks the precision of laser cutting, resulting in rougher edges and a wider kerf. Plasma cutting is ideal for heavy industrial applications where speed is a priority, but it may not be suitable for intricate designs or thinner materials where a clean cut is essential.
How Does Waterjet Cutting Compare to Laser Cutting Machines?
Waterjet cutting utilizes high-pressure water mixed with abrasive materials to cut through various substances. This method is exceptionally versatile, capable of handling metals, glass, ceramics, and even composites. One significant advantage of waterjet cutting is that it does not introduce heat into the material, preventing warping or thermal distortion. However, it requires a more complex setup and ongoing maintenance due to the need for water filtration systems. Waterjet cutting is best for applications where the integrity of the material is paramount, such as in aerospace or art installations, but it tends to have a higher initial investment.
How Can B2B Buyers Choose the Right Solution for Their Needs?
Choosing the right cutting technology involves assessing several factors, including material type, production volume, and required precision. Buyers from regions such as Africa, South America, the Middle East, and Europe should consider their specific applications and budget constraints. Laser cutting machines from China offer a balance of precision and cost-effectiveness for thinner materials, while plasma cutting may be better suited for heavy industrial tasks. Waterjet cutting, while more expensive, is advantageous for materials sensitive to heat. Ultimately, the best choice will depend on the specific operational needs and long-term goals of the business, ensuring that the selected technology aligns with both current demands and future growth.
Essential Technical Properties and Trade Terminology for laser cutting machines china
What Are the Essential Technical Properties of Laser Cutting Machines?
When considering the purchase of laser cutting machines from China, understanding their technical specifications is crucial for making informed decisions. Here are some key properties to evaluate:
1. Material Grade Compatibility
Laser cutting machines can process various materials, including metals (steel, aluminum), plastics, and wood. The material grade determines the machine’s effectiveness and the quality of the cut. For instance, higher-grade materials may require more powerful lasers and advanced cooling systems. Buyers must ensure that the machine can handle the specific grades they intend to use, which impacts production efficiency and cost.
2. Cutting Thickness and Tolerance
Cutting thickness refers to the maximum material thickness that a laser cutting machine can effectively cut. Tolerance, on the other hand, is the precision with which the machine can perform cuts. Tighter tolerances are essential for applications requiring high precision, such as aerospace or medical device manufacturing. Understanding these specifications helps buyers match their production needs with the capabilities of the machine, ensuring quality and minimizing waste.
3. Laser Power
Measured in watts, the laser power directly influences cutting speed and material thickness capabilities. Higher wattage allows for faster cutting and the ability to process thicker materials. For B2B buyers, selecting the appropriate laser power is crucial, as it affects productivity and operational costs. Evaluating the power needs based on intended applications will help in selecting a machine that aligns with business goals.
4. Beam Quality (M² Factor)
The beam quality indicates how well the laser can focus its energy. A lower M² factor signifies a better beam quality, which results in finer cuts and higher precision. For industries that require intricate designs or detailed work, investing in a machine with superior beam quality can lead to enhanced outcomes and reduced post-processing work.
5. Speed and Acceleration
Cutting speed is the rate at which a laser cutting machine can move and cut through material. Acceleration refers to how quickly the machine can reach its maximum speed. Faster machines can significantly enhance productivity, particularly in high-volume production settings. Buyers should consider their production needs and evaluate how speed and acceleration will affect their operational efficiency.
What Trade Terminology Should B2B Buyers Know When Purchasing Laser Cutting Machines?
Understanding the trade terminology associated with laser cutting machines is essential for navigating the procurement process. Here are some common terms that buyers should be familiar with:
1. OEM (Original Equipment Manufacturer)
An OEM is a company that produces parts or equipment that may be marketed by another manufacturer. In the context of laser cutting machines, buyers should ensure they are sourcing from reputable OEMs to guarantee quality and reliability of the machines.
2. MOQ (Minimum Order Quantity)
MOQ refers to the smallest number of units a supplier is willing to sell. Understanding MOQ is vital for budget planning and inventory management. Buyers should assess their production needs to determine if the MOQ aligns with their operational requirements.
3. RFQ (Request for Quotation)
An RFQ is a document sent to suppliers to request pricing and terms for specific products or services. For B2B buyers, submitting an RFQ is an effective way to gather information from multiple suppliers and negotiate the best deals.
4. Incoterms (International Commercial Terms)
Incoterms are a set of international rules that define the responsibilities of buyers and sellers in shipping goods. Familiarity with Incoterms helps buyers understand shipping costs, risks, and delivery responsibilities, which is crucial when importing equipment from countries like China.
5. Lead Time
Lead time refers to the time taken from placing an order to receiving the goods. Understanding lead times is essential for planning production schedules and ensuring timely delivery of materials and equipment.
6. Warranty and After-Sales Support
This term encompasses the guarantees provided by the manufacturer regarding the machine’s performance and the support available after purchase. Buyers should inquire about warranty periods and the nature of after-sales support to ensure they have recourse in case of issues post-purchase.
By understanding these technical properties and trade terminologies, international B2B buyers can make informed decisions and optimize their procurement processes for laser cutting machines from China.
Navigating Market Dynamics and Sourcing Trends in the laser cutting machines china Sector
What Are the Current Market Dynamics in the Laser Cutting Machines Sector in China?
The laser cutting machines market in China is witnessing significant growth, driven by several global factors. Increased demand for precision manufacturing across various sectors such as automotive, aerospace, and electronics is propelling the adoption of laser cutting technology. Furthermore, the rise of Industry 4.0 and the integration of smart manufacturing technologies are reshaping how businesses approach sourcing, leading to a heightened focus on automation and efficiency. For international B2B buyers from regions like Africa, South America, the Middle East, and Europe, understanding these dynamics is crucial for making informed purchasing decisions.
Emerging trends include the increasing utilization of fiber laser technology, which offers advantages such as higher cutting speeds and lower operational costs compared to traditional CO2 lasers. As companies aim to optimize their supply chains, there is a noticeable shift towards sourcing from manufacturers that can provide not only high-quality machines but also robust after-sales support. Buyers should also pay attention to manufacturers that invest in R&D to stay ahead of technological advancements, ensuring they have access to the latest innovations in laser cutting solutions.
How Is Sustainability Influencing Sourcing Decisions for Laser Cutting Machines?
Sustainability is becoming a critical consideration in the sourcing of laser cutting machines. As environmental regulations tighten globally, businesses are increasingly aware of their ecological footprint and the importance of ethical supply chains. For B2B buyers, this translates into a demand for suppliers who prioritize sustainable practices, such as using energy-efficient machines and sourcing raw materials responsibly.
In addition, buyers should seek manufacturers that possess certifications like ISO 14001, which demonstrates a commitment to environmental management. These certifications not only enhance the credibility of suppliers but also align with the growing trend of corporate social responsibility among businesses worldwide. Integrating ‘green’ materials and practices into the production of laser cutting machines not only minimizes environmental impact but also caters to a market increasingly driven by sustainability-conscious consumers.
What Is the Evolution of Laser Cutting Technology and Its Impact on B2B Buyers?
The evolution of laser cutting technology has been marked by significant advancements since its inception in the 1960s. Initially used primarily in industrial applications, laser cutting has evolved to encompass a wide array of materials and applications, making it a versatile choice for manufacturers. The introduction of fiber lasers in the early 2000s revolutionized the industry, offering enhanced efficiency and precision, which has become crucial for modern manufacturing processes.
For international B2B buyers, understanding this evolution is essential, as it highlights the importance of investing in advanced technology that meets current market demands. The transition from traditional cutting methods to laser solutions not only improves operational efficiency but also reduces waste, aligning with sustainability goals. Buyers should consider suppliers who have adapted to these changes and are committed to ongoing innovation, ensuring they remain competitive in a rapidly evolving marketplace.
Frequently Asked Questions (FAQs) for B2B Buyers of laser cutting machines china
-
How do I choose the right laser cutting machine from China?
Choosing the right laser cutting machine involves assessing your specific needs, such as the materials you plan to cut, the thickness of those materials, and the desired precision. Research different manufacturers and their product offerings, paying attention to specifications like laser power, cutting speed, and bed size. Consider seeking out suppliers with experience in your industry and reading reviews from other B2B buyers. It’s also beneficial to request samples or demonstrations to gauge performance before making a decision. -
What are the key features to look for in a laser cutting machine?
Important features to consider include laser type (CO2 or fiber), cutting speed, precision, maximum material thickness, and automation capabilities. Additionally, look for machines with user-friendly software, compatibility with various materials, and robust safety features. Warranty terms and after-sales support are also crucial, as they can significantly impact your operational efficiency and maintenance costs in the long run. -
How can I verify the credibility of a Chinese laser cutting machine supplier?
To verify a supplier’s credibility, conduct thorough due diligence. Check their business licenses, certifications (like ISO), and industry reputation through platforms such as Alibaba or Global Sources. Request references from previous clients and inspect their manufacturing facilities if possible. Engaging a third-party inspection service can also provide insights into the supplier’s reliability and product quality. -
What is the minimum order quantity (MOQ) for laser cutting machines from China?
The MOQ for laser cutting machines can vary significantly among suppliers. Typically, manufacturers may set an MOQ of 1 to 5 units for standard machines, while custom configurations may require higher quantities. It’s advisable to communicate your needs directly with suppliers to understand their MOQ policies and negotiate terms that align with your purchasing capabilities. -
What payment terms are commonly accepted when buying laser cutting machines from China?
Payment terms can differ by supplier, but common options include a 30% deposit upfront and the remaining 70% before shipment. Some suppliers may accept letters of credit or payment through escrow services for added security. Always clarify payment terms in your contract to avoid misunderstandings and ensure a smooth transaction process. -
How do I handle logistics and shipping for my laser cutting machine purchase?
When arranging logistics, consider the shipping method (air or sea), as this will impact delivery time and cost. Collaborate with your supplier to determine the best shipping option based on your location. It’s also essential to be aware of import duties and taxes in your country, which can affect overall costs. Engaging a freight forwarder can streamline the process and help manage customs clearance. -
What quality assurance processes should I expect from a laser cutting machine supplier?
Reputable suppliers should implement stringent quality assurance processes, including pre-production samples, in-process inspections, and final quality checks before shipment. Request detailed documentation of these processes, including test reports and certifications. Establishing clear quality standards in your contract can help ensure that the equipment meets your specifications and performance expectations. -
Can I customize a laser cutting machine to meet my specific needs?
Yes, many Chinese manufacturers offer customization options for laser cutting machines. You can request modifications based on your specific production requirements, such as bed size, laser power, and additional features. Discuss your needs with the supplier early in the negotiation process to ensure they can accommodate your requests and to understand any implications for cost and lead time.
Important Disclaimer & Terms of Use
⚠️ Important Disclaimer
The information provided in this guide, including content regarding manufacturers, technical specifications, and market analysis, is for informational and educational purposes only. It does not constitute professional procurement advice, financial advice, or legal advice.
While we have made every effort to ensure the accuracy and timeliness of the information, we are not responsible for any errors, omissions, or outdated information. Market conditions, company details, and technical standards are subject to change.
B2B buyers must conduct their own independent and thorough due diligence before making any purchasing decisions. This includes contacting suppliers directly, verifying certifications, requesting samples, and seeking professional consultation. The risk of relying on any information in this guide is borne solely by the reader.
Strategic Sourcing Conclusion and Outlook for laser cutting machines china
As the global demand for precision and efficiency in manufacturing continues to rise, the strategic sourcing of laser cutting machines from China presents an invaluable opportunity for international B2B buyers. By understanding the key factors such as technological advancements, cost-efficiency, and supplier reliability, buyers can make informed decisions that drive competitive advantage in their respective markets.
Investing in high-quality laser cutting technology not only enhances production capabilities but also reduces waste and operational costs, particularly for industries such as automotive, aerospace, and textiles. For buyers in Africa, South America, the Middle East, and Europe, leveraging China’s extensive manufacturing base can lead to significant savings and access to the latest innovations.
Looking ahead, it is crucial for businesses to build strong relationships with Chinese suppliers, ensuring transparency and alignment on quality standards. As you evaluate potential suppliers, consider their track record, customer service, and the adaptability of their technology to meet your specific needs.
Take the next step in transforming your manufacturing processes by actively seeking partnerships with reputable Chinese manufacturers. Embrace the future of laser cutting technology to enhance your operational efficiency and market responsiveness.