The Ultimate Guide to Motion Sensor Light Manufacturer (2025)
Introduction: Navigating the Global Market for motion sensor light manufacturer
In today’s fast-paced business environment, sourcing reliable motion sensor light manufacturers can present a significant challenge for international B2B buyers. With the increasing demand for energy-efficient and smart lighting solutions, navigating the global market requires a comprehensive understanding of various suppliers, product types, and applications. This guide is designed to empower decision-makers from Africa, South America, the Middle East, and Europe—regions that are witnessing rapid growth in smart technology adoption—by providing actionable insights into the sourcing process.
Our exploration covers a wide range of topics essential for informed purchasing decisions. You’ll discover the different types of motion sensor lights available, their applications in residential and commercial settings, and the latest technological advancements driving the industry forward. Additionally, we delve into strategies for vetting suppliers, including evaluating their production capabilities, quality assurance processes, and compliance with international standards.
Cost considerations are also a critical aspect of this guide. We provide strategies for negotiating favorable terms while ensuring product quality, helping you balance budget constraints with the need for high-performance lighting solutions. By the end of this guide, you will be equipped with the knowledge necessary to make strategic purchasing decisions that not only meet your operational needs but also align with the sustainability goals of your organization. Whether you are based in Indonesia, Mexico, or beyond, this resource is tailored to help you navigate the complexities of the global motion sensor light market effectively.
Understanding motion sensor light manufacturer Types and Variations
Type Name | Key Distinguishing Features | Primary B2B Applications | Brief Pros & Cons for Buyers |
---|---|---|---|
Passive Infrared (PIR) | Detects motion through heat signatures; highly energy-efficient | Warehouses, retail spaces, outdoor areas | Pros: Cost-effective, low maintenance. Cons: Limited range in cold environments. |
Ultrasonic | Uses sound waves to detect movement; effective in enclosed spaces | Offices, hotels, security systems | Pros: High sensitivity, good for complex layouts. Cons: Can be affected by ambient noise. |
Dual-Tech | Combines PIR and ultrasonic technologies for enhanced detection | Large facilities, parking lots, airports | Pros: Reduced false alarms, versatile. Cons: Higher initial cost. |
Microwave | Utilizes microwave radar technology; detects motion through walls | Industrial applications, large outdoor areas | Pros: Long detection range, unaffected by temperature. Cons: More expensive, potential interference. |
Solar-Powered | Operates on solar energy; eco-friendly and cost-effective | Remote locations, outdoor lighting | Pros: Low operational costs, sustainable. Cons: Dependent on sunlight, limited in cloudy areas. |
What are the Characteristics of Passive Infrared (PIR) Motion Sensors?
Passive Infrared (PIR) motion sensors are among the most widely used types in the B2B market due to their cost-effectiveness and energy efficiency. They work by detecting the heat emitted from living beings, making them ideal for applications in warehouses, retail spaces, and outdoor areas. When considering PIR sensors, buyers should evaluate their range and sensitivity, particularly in environments subject to extreme temperatures, as these factors can influence performance and reliability.
How Do Ultrasonic Motion Sensors Function and Where Are They Best Suited?
Ultrasonic motion sensors detect movement by emitting sound waves and measuring their reflection. This technology is particularly effective in enclosed spaces such as offices and hotels, where the complexity of layouts can lead to blind spots. When purchasing ultrasonic sensors, B2B buyers should consider the ambient noise levels of their environments, as excessive noise can interfere with the sensor’s ability to detect movement accurately.
What Are the Advantages of Dual-Tech Motion Sensors for Large Facilities?
Dual-tech motion sensors combine the functionalities of both PIR and ultrasonic technologies, offering enhanced detection capabilities. They are particularly suitable for larger facilities, parking lots, and airports, where the risk of false alarms can be a concern. Buyers should weigh the benefits of reduced false alarms against the higher initial costs, ensuring that the investment aligns with their operational needs and security requirements.
Why Choose Microwave Motion Sensors for Industrial Applications?
Microwave motion sensors operate using radar technology, allowing them to detect motion through walls and other obstacles. This makes them particularly useful in industrial applications and large outdoor areas where traditional sensors may struggle. B2B buyers should consider the longer detection range and the sensor’s immunity to temperature variations, but they should also be aware of the higher costs and potential for interference from other electronic devices.
What Are the Benefits of Solar-Powered Motion Sensors for Remote Locations?
Solar-powered motion sensors are an eco-friendly option that operates on renewable energy, making them ideal for remote locations where traditional power sources may be unavailable. They are particularly beneficial for outdoor lighting applications. When purchasing solar-powered sensors, buyers must assess the expected sunlight in their area, as prolonged cloudy conditions can affect functionality. The low operational costs and sustainability make them an attractive option, despite their dependency on environmental conditions.
Related Video: Motion Sensor Light Installation
Key Industrial Applications of motion sensor light manufacturer
Industry/Sector | Specific Application of motion sensor light manufacturer | Value/Benefit for the Business | Key Sourcing Considerations for this Application |
---|---|---|---|
Retail | Automated lighting in store aisles | Enhances customer experience and reduces energy costs | Durability, energy efficiency, and design flexibility |
Warehousing and Logistics | Motion-activated lighting in storage areas | Improves safety and operational efficiency | Compliance with safety standards and brightness levels |
Hospitality | Outdoor lighting for hotel entrances and pathways | Increases security and guest satisfaction | Weather resistance and aesthetic appeal |
Healthcare | Motion-sensor lights in patient rooms | Enhances patient safety and reduces energy usage | Non-intrusive operation and easy installation |
Manufacturing | Lighting in production areas | Boosts productivity and reduces accidents | Robustness and adaptability to different environments |
How Are Motion Sensor Lights Used in Retail Environments?
In retail settings, motion sensor lights are deployed in store aisles to activate lighting only when customers are present. This not only creates a welcoming atmosphere but also significantly cuts energy costs by ensuring lights are off when the space is unoccupied. B2B buyers from Africa, South America, and Europe should consider the durability and energy efficiency of these systems, as well as their design flexibility to align with store aesthetics.
What Are the Benefits of Motion Sensor Lighting in Warehousing and Logistics?
In warehouses and logistics centers, motion-activated lights illuminate storage areas only when movement is detected. This application enhances safety by ensuring that dark areas are lit when needed, reducing the risk of accidents. For international buyers, compliance with local safety standards and the required brightness levels for operational efficiency are crucial sourcing considerations when selecting motion sensor lighting solutions.
How Can Hospitality Businesses Enhance Guest Experience with Motion Sensor Lights?
Hotels and resorts utilize motion sensor lights for outdoor pathways and entrances, providing safety and enhancing the guest experience. These lights activate as guests approach, ensuring well-lit areas and deterring potential security threats. B2B buyers in the hospitality sector should prioritize weather-resistant products that maintain aesthetic appeal while providing functionality in various climates.
Why Are Motion Sensor Lights Important in Healthcare Facilities?
In healthcare settings, motion-sensor lights are particularly valuable in patient rooms, where they can illuminate spaces without disturbing patients. These lights activate when staff enter, ensuring safety and comfort while also reducing energy consumption. Buyers in the healthcare sector must focus on non-intrusive operation and ease of installation to meet the specific needs of their facilities.
How Do Motion Sensor Lights Improve Productivity in Manufacturing?
Manufacturing facilities benefit from motion sensor lighting by illuminating production areas only when necessary, which helps reduce energy waste and improve worker safety. This application can lead to increased productivity as employees work in well-lit environments without the distraction of flickering lights. Buyers in this sector should consider the robustness of the lighting solutions and their adaptability to various manufacturing environments, ensuring long-term performance.
Related Video: How to use PIR Motion Sensor with Arduino | Motion sensor light
3 Common User Pain Points for ‘motion sensor light manufacturer’ & Their Solutions
Scenario 1: Inconsistent Product Quality Across Suppliers
The Problem: B2B buyers often face the challenge of inconsistent quality in motion sensor lights from different manufacturers. This inconsistency can lead to project delays, increased costs due to returns and replacements, and potential harm to their business reputation. For instance, a construction company in South America may receive subpar sensors that fail to activate in low-light conditions, leading to safety concerns on job sites. This scenario can erode trust between buyers and suppliers, making it crucial for businesses to find reliable manufacturers.
The Solution: To mitigate quality inconsistency, B2B buyers should prioritize thorough supplier assessments. This includes requesting samples from multiple manufacturers and conducting performance tests under various conditions before making bulk orders. Additionally, establishing a clear quality assurance agreement that outlines specific performance metrics can help ensure that products meet the required standards. Buyers should also consider suppliers with ISO certifications or other quality management systems, as these often indicate a commitment to consistent quality control practices. Building a long-term relationship with a selected manufacturer can further enhance reliability, as manufacturers become more familiar with the buyer’s quality expectations over time.
Scenario 2: Challenges with Installation and Integration
The Problem: Another common pain point is the complexity involved in installing and integrating motion sensor lights into existing infrastructure. B2B buyers in regions like the Middle East may struggle with compatibility issues, particularly if they are working with older buildings or systems. The lack of comprehensive installation guides or support from manufacturers can lead to increased labor costs and project delays, as workers may need additional training or resources to complete the installation correctly.
The Solution: To address installation challenges, buyers should seek manufacturers that offer comprehensive support packages, including detailed installation guides, technical training for staff, and responsive customer service. It is beneficial to inquire whether the manufacturer provides on-site support or remote assistance during the installation phase. Furthermore, investing in smart motion sensor systems that are designed for easy integration with existing infrastructure can reduce compatibility issues. Buyers should also consider leveraging local contractors who have experience with similar installations, as their expertise can streamline the process and minimize potential pitfalls.
Scenario 3: Insufficient After-Sales Support and Warranty Issues
The Problem: Many international B2B buyers report difficulties in obtaining adequate after-sales support and warranty coverage from motion sensor light manufacturers. In Africa, for example, buyers may find themselves without recourse when products malfunction shortly after installation, leading to unforeseen expenses and operational disruptions. This lack of support can be particularly frustrating for businesses that rely on these lights for security and safety purposes.
The Solution: To ensure robust after-sales support, buyers should conduct due diligence before finalizing any agreements with manufacturers. This includes verifying the manufacturer’s warranty policies, understanding the claims process, and assessing the availability of replacement parts. Buyers should prioritize manufacturers who offer extended warranties and clear service level agreements (SLAs) that guarantee timely support and service. Establishing a clear communication line with the manufacturer can facilitate quicker resolutions to issues as they arise. Additionally, buyers might consider joining industry forums or networks that provide insights into reliable suppliers and share experiences regarding after-sales service, helping them make informed decisions.
Strategic Material Selection Guide for motion sensor light manufacturer
When selecting materials for motion sensor lights, manufacturers must consider various factors that influence product performance, cost, and market suitability. Here, we analyze four common materials used in the industry: plastics, aluminum, stainless steel, and glass. Each material presents unique characteristics that can significantly impact the product’s effectiveness and marketability, particularly for international B2B buyers from Africa, South America, the Middle East, and Europe.
What Are the Key Properties of Plastics for Motion Sensor Lights?
Plastics, particularly polycarbonate and ABS, are widely used in motion sensor lights due to their lightweight nature and versatility. They typically have a temperature rating of -40°C to 120°C, making them suitable for various climates. Additionally, they offer good corrosion resistance, which is essential for outdoor applications.
Pros & Cons: The primary advantage of plastics is their cost-effectiveness and ease of manufacturing, allowing for complex shapes and designs. However, they may not be as durable as metals and can degrade under UV exposure unless treated. For international buyers, it is crucial to ensure compliance with local standards regarding fire safety and environmental impact.
How Does Aluminum Benefit Motion Sensor Light Manufacturing?
Aluminum is another popular choice due to its excellent strength-to-weight ratio and corrosion resistance. It can withstand temperatures ranging from -50°C to 150°C, making it suitable for diverse environments. Aluminum also provides good thermal conductivity, which can enhance the performance of integrated electronic components.
Pros & Cons: The key advantage of aluminum is its durability and aesthetic appeal, making it suitable for high-end applications. However, the manufacturing process can be more complex and costly compared to plastics. International buyers should consider the availability of aluminum in their regions and any associated tariffs or regulations.
Why Choose Stainless Steel for Motion Sensor Lights?
Stainless steel is renowned for its exceptional corrosion resistance and mechanical strength. It can handle extreme temperatures and pressures, making it ideal for harsh environments. With a temperature rating of -200°C to 800°C, stainless steel is versatile for various applications.
Pros & Cons: The primary advantage of stainless steel is its longevity and resistance to rust, which is particularly beneficial in coastal or humid regions. However, it is more expensive and heavier than other materials, which can affect shipping costs and installation. Buyers from regions with stringent material regulations should ensure compliance with standards such as ASTM or DIN.
What Role Does Glass Play in Motion Sensor Light Design?
Glass is often used for the lenses of motion sensor lights due to its clarity and ability to transmit light effectively. Tempered glass can withstand high temperatures and impacts, making it suitable for outdoor lighting applications.
Pros & Cons: The key advantage of glass is its aesthetic quality and durability when properly treated. However, it is more fragile than other materials and can break under stress. International buyers should consider local preferences for design and the potential need for additional protective features.
Summary Table of Material Selection for Motion Sensor Lights
Material | Typical Use Case for motion sensor light manufacturer | Key Advantage | Key Disadvantage/Limitation | Relative Cost (Low/Med/High) |
---|---|---|---|---|
Plastics | Housing and components for indoor/outdoor lights | Cost-effective and versatile | Less durable, UV degradation potential | Low |
Aluminum | Structural components and casings for outdoor lights | Durable, lightweight, and aesthetically pleasing | Higher manufacturing complexity and cost | Medium |
Stainless Steel | Heavy-duty outdoor motion sensor lights | Exceptional corrosion resistance and strength | Expensive and heavier than alternatives | High |
Glass | Lenses for motion sensor lights | Excellent light transmission and aesthetic appeal | Fragile and can break under stress | Medium |
In conclusion, selecting the right material for motion sensor lights is crucial for ensuring product performance, durability, and market competitiveness. International B2B buyers must consider local regulations, material availability, and specific application requirements to make informed purchasing decisions.
In-depth Look: Manufacturing Processes and Quality Assurance for motion sensor light manufacturer
What Are the Key Stages in the Manufacturing Process of Motion Sensor Lights?
Manufacturing motion sensor lights involves several critical stages that ensure quality, functionality, and durability. Understanding these stages is essential for B2B buyers, particularly those from diverse regions such as Africa, South America, the Middle East, and Europe. The primary stages include material preparation, forming, assembly, and finishing.
-
Material Preparation: This initial stage involves selecting high-quality raw materials, including plastics, metals, and electronic components. B2B buyers should ensure suppliers source materials that comply with international standards to guarantee product safety and longevity. Suppliers often conduct material tests to verify the quality of incoming raw materials.
-
Forming: In this stage, raw materials are shaped into components. Techniques such as injection molding for plastic parts and stamping for metal components are common. Buyers should inquire about the forming technologies used by manufacturers, as advanced methods can enhance precision and reduce waste.
-
Assembly: The assembly stage integrates various components, including sensors, circuit boards, and housing. Automated assembly lines are often employed to ensure consistent quality and efficiency. Buyers should consider manufacturers that utilize automated systems, as this can lead to improved accuracy and lower labor costs.
-
Finishing: The final stage involves applying surface treatments, such as painting, coating, or polishing, to enhance aesthetics and durability. Quality finishing processes can significantly affect the product’s marketability. B2B buyers should assess whether manufacturers offer custom finishing options to meet specific branding needs.
How Is Quality Assurance Integrated into the Manufacturing Process?
Quality assurance (QA) is a critical aspect of the manufacturing process, ensuring that motion sensor lights meet industry standards and customer expectations. B2B buyers should be familiar with the international and industry-specific quality standards that manufacturers adhere to.
-
International Standards: Many manufacturers comply with ISO 9001, which focuses on quality management systems. This certification signifies that the manufacturer has established processes to consistently provide products that meet customer and regulatory requirements. Buyers should request proof of ISO certification as part of their supplier evaluation.
-
Industry-Specific Standards: In addition to ISO standards, motion sensor lights may need to comply with certifications such as CE (for European markets) and UL (for North American markets). These certifications ensure that products meet safety and performance criteria. B2B buyers should check the relevant certifications based on their target markets.
What Are the Critical Quality Control Checkpoints in Motion Sensor Light Manufacturing?
Quality control (QC) is integrated throughout the manufacturing process, with specific checkpoints that ensure each stage meets predefined standards.
-
Incoming Quality Control (IQC): This initial checkpoint involves inspecting raw materials upon arrival at the manufacturing facility. Suppliers conduct tests to verify that materials meet specified requirements, including physical and chemical properties. B2B buyers should inquire about the IQC processes of potential suppliers to ensure they prioritize quality from the start.
-
In-Process Quality Control (IPQC): During the manufacturing process, IPQC checks are implemented to monitor the production line. This includes regular inspections and tests at various stages, such as during assembly and before finishing. These checks help identify defects early, reducing waste and ensuring that only high-quality products proceed to the next stage.
-
Final Quality Control (FQC): At the completion of the manufacturing process, FQC involves comprehensive testing of finished products to ensure they meet all specifications. This may include functional tests, performance evaluations, and visual inspections. B2B buyers should request detailed reports on FQC results to assess the reliability of the final products.
What Common Testing Methods Are Used for Motion Sensor Lights?
Several testing methods are commonly employed to ensure that motion sensor lights function correctly and safely. These methods can vary based on the specific requirements of the product and the markets in which they will be sold.
-
Functional Testing: This involves checking the motion detection capabilities, light output, and response times of the sensors. Manufacturers often simulate real-world conditions to verify that the products perform as expected.
-
Environmental Testing: Motion sensor lights are often subjected to environmental tests to evaluate their performance under different conditions, such as humidity, temperature variations, and exposure to UV light. This ensures that the products can withstand diverse climates, particularly important for buyers in regions with extreme weather.
-
Safety Testing: Ensuring electrical safety is critical for motion sensor lights. Testing for electrical insulation, short circuits, and fire resistance is vital. Buyers should verify that manufacturers conduct safety tests in compliance with relevant standards.
How Can B2B Buyers Verify Supplier Quality Control Practices?
When sourcing motion sensor lights, B2B buyers must take proactive steps to verify the quality control practices of potential suppliers. Here are several strategies:
-
Supplier Audits: Conducting on-site audits allows buyers to assess the manufacturing processes and quality control systems firsthand. This is particularly beneficial for buyers from Africa, South America, the Middle East, and Europe, as it provides insight into the supplier’s operational capabilities.
-
Requesting Quality Reports: Suppliers should provide documentation detailing their quality control processes, including IQC, IPQC, and FQC results. B2B buyers should analyze these reports to ensure that the manufacturer adheres to high-quality standards.
-
Third-Party Inspections: Engaging third-party inspection services can provide an unbiased assessment of the supplier’s quality control practices. This is especially valuable for international buyers who may not have the resources to conduct audits themselves.
What Are the Quality Control Nuances for International B2B Buyers?
Navigating quality control nuances is essential for international B2B buyers, especially those sourcing from different regions. Here are a few considerations:
-
Cultural Differences in Quality Standards: Buyers should be aware that quality perceptions may vary across regions. Understanding the local manufacturing culture and quality expectations can help buyers make informed decisions.
-
Regulatory Compliance: Each region has specific regulations and standards that products must meet. B2B buyers should familiarize themselves with these requirements to avoid potential compliance issues, particularly when importing goods.
-
Language Barriers: Communication can be a challenge when dealing with international suppliers. Buyers should ensure that they have clear channels of communication regarding quality specifications and expectations to mitigate misunderstandings.
In summary, a thorough understanding of the manufacturing processes and quality assurance practices in the motion sensor light industry is crucial for B2B buyers. By focusing on the key stages of manufacturing, relevant quality standards, and effective verification methods, buyers can make informed decisions and establish successful partnerships with manufacturers worldwide.
Practical Sourcing Guide: A Step-by-Step Checklist for ‘motion sensor light manufacturer’
The following guide provides a structured approach for B2B buyers looking to source motion sensor lights from manufacturers, particularly focusing on international markets in Africa, South America, the Middle East, and Europe. This checklist aims to streamline the sourcing process, ensuring that buyers make informed and strategic decisions.
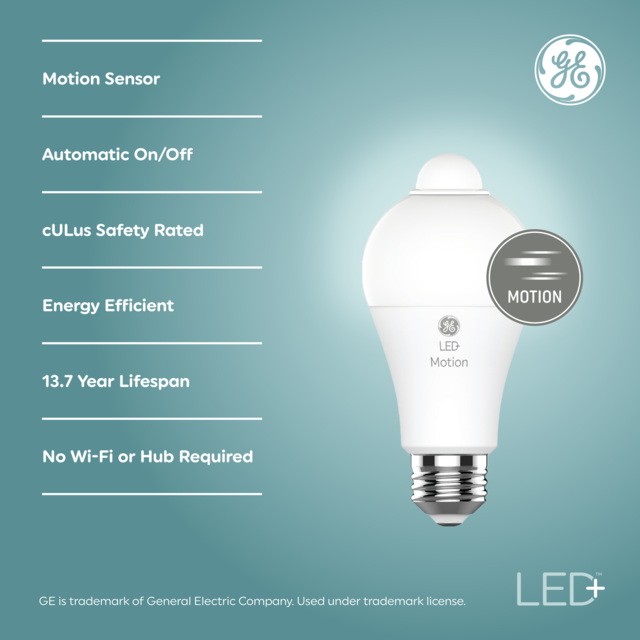
A stock image related to motion sensor light manufacturer.
Step 1: Define Your Technical Specifications
Establishing clear technical specifications is crucial for aligning your requirements with what suppliers can offer. This includes understanding the type of motion sensor technology (PIR, microwave, etc.), power source options (battery, solar, wired), and desired features (dimming capabilities, light color temperature, etc.). A well-defined specification helps minimize misunderstandings and ensures that the products meet your operational needs.
Step 2: Conduct Market Research
Before reaching out to manufacturers, conduct thorough market research to identify potential suppliers. Investigate trends in the motion sensor light industry, review existing customer feedback, and analyze competitors’ products. Utilize industry reports and online forums to gain insights into which manufacturers are reputable and reliable.
Step 3: Evaluate Potential Suppliers
Before committing to a supplier, perform a detailed evaluation. Request company profiles, certifications, and case studies to assess their credibility. It’s beneficial to seek references from buyers in similar industries or regions, which provides a clearer picture of the supplier’s reliability and product quality. Consider using platforms like Alibaba or Global Sources for supplier ratings and reviews.
Step 4: Verify Supplier Certifications
Confirm that potential suppliers hold relevant certifications that demonstrate compliance with international standards. Look for certifications such as ISO 9001 for quality management and CE marking for European markets. These certifications not only ensure product quality but also facilitate smoother customs clearance and regulatory compliance.
Step 5: Request Samples for Testing
Once you have narrowed down potential suppliers, request product samples. Testing samples allows you to evaluate the performance, durability, and overall quality of the motion sensor lights. Pay attention to factors such as ease of installation, sensitivity of the sensors, and energy efficiency. This step is essential to verify that the products align with your specifications before placing a bulk order.
Step 6: Negotiate Terms and Conditions
Engage in negotiations to establish favorable terms and conditions, including pricing, payment terms, delivery schedules, and warranty policies. Clear communication during this phase can prevent misunderstandings later. Ensure that all agreements are documented to protect both parties and facilitate smoother transactions.
Step 7: Plan for Logistics and Distribution
Finally, develop a logistics plan that accounts for shipping methods, import duties, and distribution channels. Consider local regulations regarding electrical products in your region to ensure compliance. Collaborating with a logistics partner familiar with international shipping can streamline this process, minimizing delays and additional costs.
By following this checklist, B2B buyers can enhance their sourcing strategy for motion sensor lights, ensuring they select a manufacturer that meets their quality, compliance, and logistical needs.
Comprehensive Cost and Pricing Analysis for motion sensor light manufacturer Sourcing
What Are the Key Cost Components for Motion Sensor Light Manufacturing?
When sourcing motion sensor lights, understanding the cost structure is crucial for international B2B buyers. The primary cost components include:
-
Materials: The quality and type of materials used, such as plastics, metals, and electronic components, significantly impact the overall cost. Sourcing high-quality materials can enhance product durability and performance but may increase initial costs.
-
Labor: Labor costs vary by region and can affect the pricing structure. In countries with lower labor costs, manufacturing expenses can be significantly reduced, making them attractive for bulk orders.
-
Manufacturing Overhead: This includes costs associated with factory operations, utilities, and equipment maintenance. Efficient manufacturing processes can minimize overhead, allowing manufacturers to offer competitive pricing.
-
Tooling: Initial tooling costs for custom designs can be substantial. However, once the tooling is set up, the per-unit cost can decrease, making it cost-effective for larger orders.
-
Quality Control (QC): Implementing rigorous QC processes ensures product reliability and compliance with international standards. While this adds to upfront costs, it can save buyers from costly recalls and reputational damage.
-
Logistics: Shipping and handling costs can vary widely based on the shipping method, distance, and Incoterms. Buyers should factor in these costs when calculating the total expenditure.
-
Margin: Manufacturers typically include a profit margin in their pricing. Understanding the average margins within the industry can help buyers negotiate better terms.
How Do Price Influencers Affect Motion Sensor Light Sourcing?
Several factors influence the pricing of motion sensor lights, including:
-
Volume/MOQ: Minimum order quantities (MOQ) can significantly affect pricing. Ordering in bulk often leads to discounts, making it essential for buyers to assess their needs and negotiate effectively.
-
Specifications and Customization: Customized products may incur additional costs for design and tooling. Buyers should clearly define their requirements to avoid unexpected expenses.
-
Materials and Quality Certifications: The choice of materials and the existence of quality certifications (like ISO or CE) can elevate costs. Buyers should evaluate whether these certifications are necessary for their markets.
-
Supplier Factors: The reputation and reliability of the supplier can influence pricing. Established manufacturers may charge more but offer better quality assurance and service.
-
Incoterms: Understanding international shipping terms (e.g., FOB, CIF) is critical for calculating total costs. Different Incoterms can shift responsibility for shipping costs and risks between buyers and sellers.
What Are the Best Negotiation Tips for International B2B Buyers?
To optimize sourcing costs, international buyers should consider the following strategies:
-
Research Market Prices: Conduct thorough market research to understand the average prices for motion sensor lights. This knowledge empowers buyers during negotiations.
-
Leverage Volume Discounts: If possible, consolidate orders to meet MOQs and secure better pricing. Suppliers are often willing to negotiate on bulk orders.
-
Assess Total Cost of Ownership (TCO): Evaluate the long-term costs associated with the product, including maintenance and potential energy savings. A higher upfront cost may result in lower TCO, making it a worthwhile investment.
-
Build Relationships with Suppliers: Establishing a strong relationship with suppliers can lead to better pricing and preferential treatment in future dealings.
-
Be Aware of Pricing Nuances: Different regions may have varying pricing strategies. For example, suppliers in Africa or South America might have different pricing structures compared to those in Europe or the Middle East due to local economic factors.
Disclaimer on Indicative Prices
Pricing for motion sensor lights can fluctuate based on market conditions, supplier negotiations, and changing material costs. Therefore, the prices discussed in this analysis should be considered indicative. Buyers are encouraged to obtain multiple quotes and conduct due diligence before finalizing any agreements.
Alternatives Analysis: Comparing motion sensor light manufacturer With Other Solutions
Understanding the Importance of Alternative Solutions in Motion Sensor Technology
When considering the implementation of motion sensor lights, it’s essential for B2B buyers to evaluate various alternatives that fulfill similar objectives. By analyzing different technologies and solutions, businesses can make informed decisions that align with their operational needs, budget constraints, and long-term goals. This section explores how traditional motion sensor lights compare to other viable solutions, providing valuable insights for international buyers from diverse regions such as Africa, South America, the Middle East, and Europe.
Comparative Analysis of Motion Sensor Light Solutions
Comparison Aspect | Motion Sensor Light Manufacturer | Smart Lighting Systems | Manual Lighting Controls |
---|---|---|---|
Performance | Highly effective in detecting motion; quick response times | Offers programmable features; can adjust to environmental conditions | Dependent on user interaction; slower to respond |
Cost | Moderate initial investment; potential for long-term savings | Higher upfront cost; ongoing software subscriptions may apply | Low initial cost; no long-term savings on energy |
Ease of Implementation | Requires professional installation; integration with existing systems | Complex installation; may need specialized expertise | Simple installation; easily adaptable to existing setups |
Maintenance | Requires occasional sensor cleaning and battery replacements | Regular software updates; hardware may need upgrades | Minimal maintenance; relies on user management |
Best Use Case | Ideal for security and outdoor lighting | Best for smart homes and energy-efficient environments | Suitable for low-traffic areas or temporary setups |
What Are the Advantages and Disadvantages of Smart Lighting Systems?
Smart lighting systems offer advanced features such as programmable settings, remote control, and integration with other smart devices. These systems can adjust based on occupancy and ambient light, providing energy efficiency and enhanced user experience. However, the higher upfront costs and the need for ongoing software subscriptions can be a barrier for some businesses. Additionally, installation complexity may require specialized technicians, which could lead to increased labor costs.
How Do Manual Lighting Controls Compare?
Manual lighting controls represent the simplest form of lighting management, relying on user intervention to turn lights on and off. This solution is cost-effective with minimal initial investment and low maintenance. However, it lacks the efficiency and responsiveness of automated systems. Manual controls are best suited for environments with infrequent use or where budget constraints limit investment in more advanced technologies.
Conclusion: How to Choose the Right Lighting Solution for Your Business
In selecting the appropriate lighting solution, B2B buyers should consider their specific operational needs, budget, and the environment in which the technology will be implemented. Motion sensor lights are particularly effective for security and outdoor applications, while smart lighting systems excel in energy efficiency and adaptability. On the other hand, manual controls may serve well in low-traffic areas where cost is a significant concern. Ultimately, understanding the strengths and weaknesses of each option will empower buyers to make strategic decisions that enhance their operational efficiency and cost-effectiveness.
Essential Technical Properties and Trade Terminology for motion sensor light manufacturer
What Are the Essential Technical Properties of Motion Sensor Lights?
When considering the procurement of motion sensor lights, understanding their technical properties is crucial for making informed purchasing decisions. Here are some essential specifications that every B2B buyer should be aware of:
1. Material Grade and Durability
The material used in motion sensor lights can significantly affect their longevity and performance. Common materials include high-grade plastics, aluminum, and tempered glass. Each material offers different levels of resistance to environmental factors such as heat, moisture, and impact. For instance, aluminum fixtures are generally more durable and resistant to corrosion, making them suitable for outdoor use. Ensuring that the lights meet specific material standards can prevent premature failures and reduce replacement costs.
2. Power Consumption and Efficiency
Efficiency ratings, often measured in lumens per watt, indicate how much light is produced relative to the energy consumed. Motion sensor lights with higher efficiency ratings save energy and lower operating costs, which is particularly appealing for businesses looking to reduce their carbon footprint. Understanding the power consumption also aids in compliance with local energy regulations and standards, which can vary significantly across regions like Europe and Africa.
3. Detection Range and Angle
The detection range and angle of motion sensors are critical for ensuring optimal coverage in the intended area. Typically, the range can vary from a few meters up to 20 meters, and the angle may range from 90 to 360 degrees. Buyers should assess the specific needs of their installation environment—such as parking lots or indoor facilities—to select sensors that provide adequate coverage without leaving blind spots.
4. IP Rating (Ingress Protection)
The IP rating indicates how well a light fixture is protected against dust and water ingress. For instance, an IP65 rating means that the light is completely dust-tight and can withstand water jets from any direction. This specification is particularly important for outdoor applications or in environments where exposure to moisture is expected, such as in humid climates in South America or coastal areas in Europe.
5. Operating Temperature Range
Different regions experience varying climatic conditions, which can impact the performance of motion sensor lights. Manufacturers typically specify an operating temperature range, which indicates the extreme conditions under which the lights can function effectively. Understanding this range is crucial, especially for buyers in regions with extreme temperatures, to avoid functionality issues.
What Are Common Trade Terms in the Motion Sensor Light Manufacturing Industry?
Familiarizing yourself with industry jargon can facilitate smoother negotiations and transactions. Here are some common terms that B2B buyers should understand:
1. OEM (Original Equipment Manufacturer)
An OEM refers to a company that produces parts or equipment that may be marketed by another manufacturer. In the context of motion sensor lights, buyers may choose to work with an OEM for custom designs or specific features that align with their branding. Understanding OEM relationships can lead to more tailored solutions.
2. MOQ (Minimum Order Quantity)
MOQ is the smallest number of units that a supplier is willing to sell. Knowing the MOQ is vital for budgeting and inventory management. Buyers should negotiate MOQs to ensure they align with their purchasing capabilities while still meeting supplier requirements.
3. RFQ (Request for Quotation)
An RFQ is a document sent to suppliers requesting pricing and terms for specific products. It is a crucial step in the procurement process that allows buyers to compare offers from different manufacturers. Providing detailed specifications in an RFQ can lead to more accurate quotes and better decision-making.
4. Incoterms (International Commercial Terms)
Incoterms are a set of international rules that define the responsibilities of sellers and buyers in international transactions. Understanding these terms is critical for clarifying shipping costs, risks, and responsibilities, which can vary significantly between regions like Europe and Africa.
5. Lead Time
Lead time refers to the amount of time it takes from placing an order until it is received. Knowing the lead time is essential for planning and can impact inventory levels and project timelines. Buyers should communicate their expectations clearly to manufacturers to avoid delays.
Conclusion
Understanding the essential technical properties and trade terminology in the motion sensor light manufacturing industry is vital for B2B buyers. By familiarizing themselves with these specifications and terms, international buyers from Africa, South America, the Middle East, and Europe can make more informed purchasing decisions, ensuring they acquire products that meet their operational needs and comply with local regulations.
Navigating Market Dynamics and Sourcing Trends in the motion sensor light manufacturer Sector
What Are the Key Market Dynamics Driving the Motion Sensor Light Manufacturing Sector?
The motion sensor light manufacturing sector is experiencing robust growth driven by several global factors. One of the primary drivers is the increasing demand for energy-efficient lighting solutions, particularly in urban areas where smart city initiatives are gaining momentum. Countries in Africa, South America, the Middle East, and Europe are investing heavily in infrastructure that prioritizes sustainable energy practices, making motion sensor lighting an attractive option.
Another emerging trend is the integration of advanced technologies such as Internet of Things (IoT) capabilities and artificial intelligence in lighting systems. This trend facilitates enhanced user control and energy management, aligning with the preferences of modern consumers and businesses. For international B2B buyers, particularly those in emerging markets like Indonesia and Mexico, sourcing manufacturers that can provide smart, connected solutions will be crucial.
Furthermore, fluctuations in raw material costs and supply chain disruptions—exacerbated by geopolitical tensions and global health crises—are influencing market dynamics. B2B buyers must remain agile, leveraging local suppliers where possible and establishing strong relationships with manufacturers to mitigate risks associated with sourcing.
How Important Is Sustainability and Ethical Sourcing in the Motion Sensor Light Industry?
Sustainability and ethical sourcing are increasingly pivotal in the motion sensor light manufacturing sector. The environmental impact of lighting products, particularly in terms of energy consumption and waste generation, has prompted buyers to prioritize sustainable solutions. Manufacturers who utilize eco-friendly materials and processes not only reduce their carbon footprint but also appeal to a growing base of environmentally-conscious customers.
The importance of ethical supply chains cannot be overstated. B2B buyers are increasingly scrutinizing their suppliers’ practices, looking for certifications such as ISO 14001 for environmental management and other ‘green’ certifications that validate sustainable practices. This trend is especially relevant for buyers in regions like Europe, where regulatory frameworks around sustainability are becoming stricter.
Moreover, incorporating recycled materials in motion sensor lighting products can significantly enhance a company’s brand reputation. B2B buyers should seek suppliers who are committed to sustainability, as this can lead to long-term cost savings and a competitive edge in the marketplace.
What Is the Historical Context of Motion Sensor Lighting Technology?
The evolution of motion sensor lighting technology can be traced back to the mid-20th century when the first passive infrared (PIR) sensors were developed. Initially used in security applications, these sensors have evolved significantly, driven by advancements in technology and increased consumer awareness of energy efficiency. Over the last two decades, the integration of smart technologies and wireless capabilities has transformed motion sensor lights from simple security devices to sophisticated energy management tools.
This historical context is crucial for B2B buyers as it highlights the rapid pace of innovation in this sector. Understanding the trajectory of motion sensor lighting technology can inform purchasing decisions, guiding buyers toward manufacturers that are not only established but also at the forefront of technological advancements. As the market continues to evolve, staying informed about historical trends will help buyers anticipate future developments and adapt their sourcing strategies accordingly.
Frequently Asked Questions (FAQs) for B2B Buyers of motion sensor light manufacturer
-
How do I choose the right motion sensor light manufacturer for my business needs?
Choosing the right manufacturer involves evaluating their industry experience, product range, and compliance with international standards. Look for manufacturers that specialize in motion sensor lights and have a strong portfolio of successful projects. It’s also crucial to assess their ability to customize products according to your specific requirements. Engaging with their previous clients can provide insights into their reliability and quality. -
What are the common features to consider in motion sensor lights?
When sourcing motion sensor lights, consider features such as detection range, sensitivity settings, power consumption, and durability. Additionally, look for options that include adjustable timing settings, energy-efficient designs, and weatherproof ratings. These features can enhance the functionality and longevity of the lights, making them suitable for various applications, from residential to commercial use. -
What is the typical minimum order quantity (MOQ) for motion sensor lights?
MOQs can vary significantly among manufacturers, typically ranging from 100 to 1,000 units. Factors influencing MOQ include the manufacturer’s production capacity, the complexity of the product, and the customization options you require. It’s advisable to discuss your specific needs with the manufacturer to negotiate a suitable MOQ that aligns with your budget and inventory management strategy. -
How do I ensure quality assurance when sourcing motion sensor lights?
To ensure quality assurance, request detailed product specifications and certifications from the manufacturer. It’s beneficial to ask about their quality control processes and whether they conduct third-party testing. Additionally, consider arranging a factory visit or requesting samples before placing a bulk order. This helps verify the product quality and adherence to your standards. -
What payment terms should I expect from motion sensor light manufacturers?
Payment terms can vary widely but generally include options such as upfront deposits (typically 30%-50%) and balance payments upon delivery. Some manufacturers may offer credit terms for established clients. It’s essential to clarify these terms upfront and consider using secure payment methods, such as letters of credit or escrow services, to mitigate risks associated with international transactions. -
How can I effectively communicate my customization requirements to a manufacturer?
Effective communication of your customization requirements involves providing detailed specifications, including design, functionality, and any specific industry standards you need to meet. Utilize sketches, prototypes, or reference products to convey your vision clearly. Regular updates and feedback throughout the design process can help ensure the final product aligns with your expectations. -
What logistics considerations should I keep in mind when importing motion sensor lights?
Logistics considerations include shipping methods, costs, customs duties, and delivery timelines. Choose a reliable freight forwarder experienced in handling electronic goods to navigate these complexities. Be aware of the import regulations specific to your country, as they can affect delivery times and costs. Planning for potential delays and ensuring adequate insurance coverage for your shipments is also advisable. -
How do I verify the credibility of a motion sensor light manufacturer?
To verify a manufacturer’s credibility, check their business licenses, certifications, and industry affiliations. Request references from previous clients and review case studies or testimonials to gauge their reputation. Online platforms like LinkedIn can also provide insights into the manufacturer’s background and credibility. Conducting thorough due diligence can help prevent potential issues during your sourcing process.
Important Disclaimer & Terms of Use
⚠️ Important Disclaimer
The information provided in this guide, including content regarding manufacturers, technical specifications, and market analysis, is for informational and educational purposes only. It does not constitute professional procurement advice, financial advice, or legal advice.
While we have made every effort to ensure the accuracy and timeliness of the information, we are not responsible for any errors, omissions, or outdated information. Market conditions, company details, and technical standards are subject to change.
B2B buyers must conduct their own independent and thorough due diligence before making any purchasing decisions. This includes contacting suppliers directly, verifying certifications, requesting samples, and seeking professional consultation. The risk of relying on any information in this guide is borne solely by the reader.
Strategic Sourcing Conclusion and Outlook for motion sensor light manufacturer
In navigating the complex landscape of motion sensor light manufacturing, international B2B buyers must prioritize strategic sourcing as a pivotal component of their procurement strategy. Engaging with reputable manufacturers not only ensures high-quality products but also fosters long-term partnerships that can yield competitive pricing and innovation. By leveraging data analytics and understanding market trends, companies can identify reliable suppliers that align with their sustainability goals and regulatory requirements.
What are the key benefits of strategic sourcing in motion sensor light manufacturing? Buyers can expect enhanced supply chain resilience, improved cost management, and the opportunity to tap into emerging technologies that drive efficiency. As regions like Africa, South America, the Middle East, and Europe continue to embrace energy-efficient solutions, the demand for advanced motion sensor lighting will only grow.
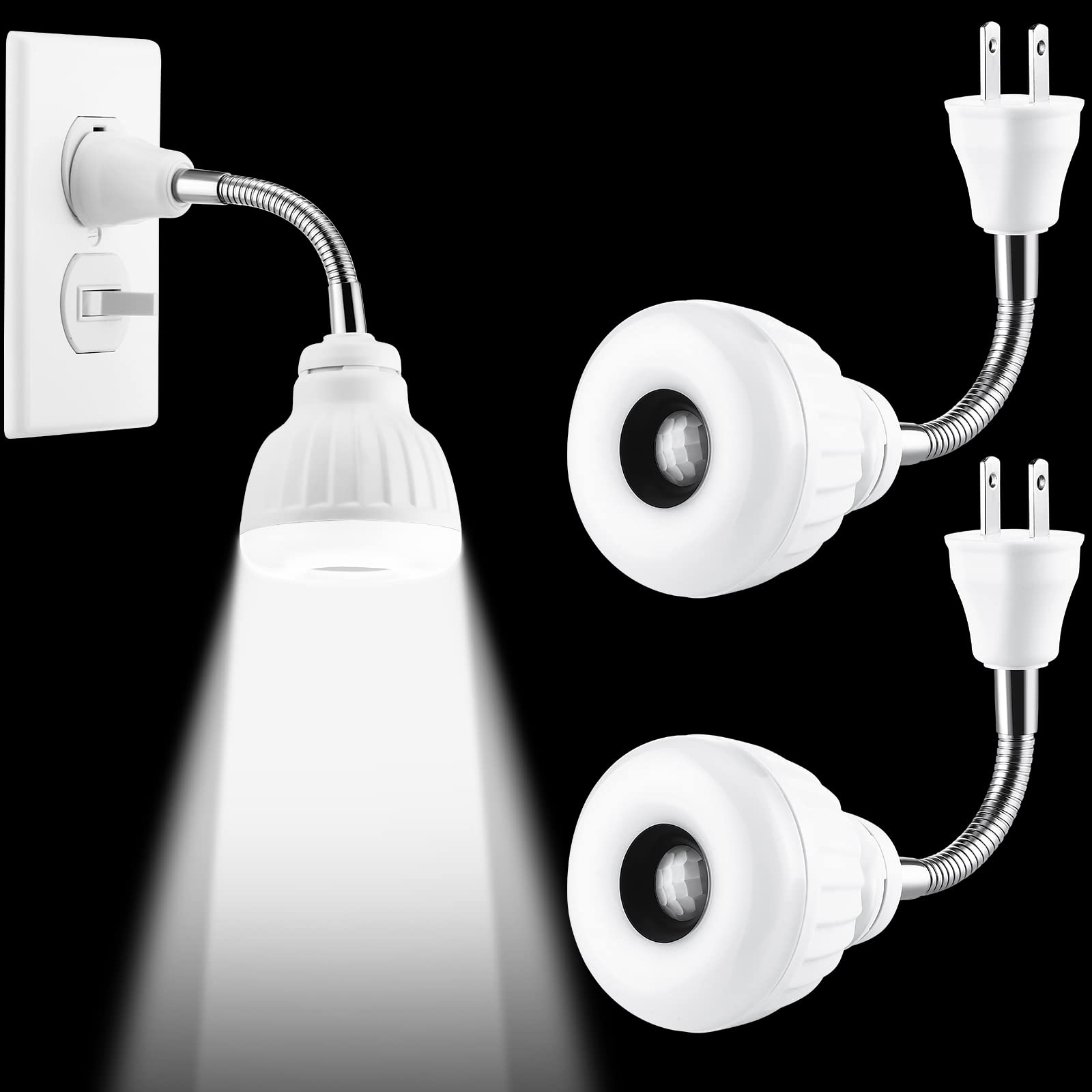
A stock image related to motion sensor light manufacturer.
As you contemplate your sourcing strategies, consider the evolving market dynamics and the importance of aligning with manufacturers who share your vision for innovation and sustainability. Now is the time to take action—explore partnerships that will not only meet your immediate needs but also position your business at the forefront of the motion sensor lighting revolution.