The Ultimate Guide to Plastic Chair Manufacturer (2025)
Introduction: Navigating the Global Market for plastic chair manufacturer
As global demand for versatile and sustainable seating solutions rises, the challenge of sourcing high-quality plastic chairs becomes paramount for international B2B buyers. Whether you are seeking durable outdoor chairs for a café in Colombia or ergonomic office chairs for a startup in France, understanding the nuances of the plastic chair manufacturing industry is crucial. This guide provides comprehensive insights into the various types of plastic chairs available, their applications across diverse sectors, and effective supplier vetting techniques to ensure quality and compliance.
Navigating the complexities of pricing, material sourcing, and regulatory standards can be overwhelming, especially for buyers from regions like Africa, South America, the Middle East, and Europe. With the ever-increasing focus on sustainability, it is essential to consider factors such as eco-friendly materials and manufacturing processes. This guide empowers B2B buyers by offering actionable strategies and expert insights that facilitate informed purchasing decisions.
From understanding the lifecycle of plastic materials to evaluating the cost implications of sourcing, our guide serves as a vital resource for businesses aiming to optimize their procurement processes. By arming yourself with knowledge about the latest trends and best practices in the plastic chair market, you can confidently navigate this global landscape and make choices that align with your business goals and sustainability commitments.
Understanding plastic chair manufacturer Types and Variations
Type Name | Key Distinguishing Features | Primary B2B Applications | Brief Pros & Cons for Buyers |
---|---|---|---|
Injection-Molded Chairs | High precision, diverse designs, and color options | Office furniture, event seating | Pros: Cost-effective, durable. Cons: Limited customization. |
Blow-Molded Chairs | Lightweight, stackable, and weather-resistant | Outdoor events, public seating | Pros: Easy to transport, versatile. Cons: Less aesthetic appeal. |
Rattan-Style Plastic Chairs | Mimics natural rattan, offers a vintage look | Cafés, restaurants, and lounges | Pros: Stylish, comfortable. Cons: Higher price point. |
Recycled Plastic Chairs | Made from post-consumer waste, eco-friendly | Sustainable projects, schools | Pros: Environmentally friendly, durable. Cons: Limited color options. |
Folding Plastic Chairs | Compact, easy to store, and transport | Trade shows, temporary setups | Pros: Space-saving, lightweight. Cons: May lack stability. |
What Are Injection-Molded Chairs and Their B2B Suitability?
Injection-molded chairs are crafted through a process that allows for high precision and a wide range of design options. These chairs are typically made from polypropylene or other durable plastics, making them suitable for various applications, including office furniture and event seating. When purchasing, buyers should consider the chair’s durability and the manufacturer‘s ability to deliver consistent quality.
How Do Blow-Molded Chairs Stand Out in the Market?
Blow-molded chairs are characterized by their lightweight nature and stackable design, making them ideal for outdoor events and public seating areas. These chairs are often made from high-density polyethylene (HDPE), which is resistant to moisture and UV rays. B2B buyers should focus on the chair’s weight capacity and stackability when making a decision, especially for venues that require frequent setup changes.
What Makes Rattan-Style Plastic Chairs a Popular Choice?
Rattan-style plastic chairs offer the aesthetic appeal of natural rattan while providing the durability of plastic. They are commonly used in cafés, restaurants, and lounges where design matters. Buyers should weigh the cost against the style and comfort offered by these chairs, as they often come at a higher price point compared to standard plastic options.
Why Choose Recycled Plastic Chairs for Sustainable Projects?
Recycled plastic chairs are manufactured using post-consumer waste, making them an eco-friendly option for businesses committed to sustainability. These chairs are durable and suitable for schools and sustainable projects. Buyers should consider the availability of colors and styles, as options may be limited compared to traditional plastic chairs.
What Advantages Do Folding Plastic Chairs Offer for Temporary Setups?
Folding plastic chairs are designed for easy storage and transportation, making them ideal for trade shows and temporary setups. Their compact nature allows for space-saving solutions in venues with limited storage. However, buyers should assess the stability and weight capacity of these chairs, as they may not be as sturdy as other types.
Related Video: All Types Of Moulded Chair Price, Review 2024 ! Nilkamal, Cello, Mango Brand Plastic Chairs.
Key Industrial Applications of plastic chair manufacturer
Industry/Sector | Specific Application of Plastic Chair Manufacturer | Value/Benefit for the Business | Key Sourcing Considerations for this Application |
---|---|---|---|
Education | Classroom and Auditorium Seating | Durable, lightweight, and easy to clean, enhancing student comfort and engagement. | Compliance with safety standards; ergonomic design; bulk purchasing options. |
Hospitality | Outdoor and Indoor Dining Furniture | Weather-resistant and stylish options that enhance the dining experience and customer satisfaction. | Aesthetic variety; UV resistance; availability of custom branding. |
Healthcare | Patient Waiting Areas and Examination Rooms | Hygienic, easy-to-sanitize surfaces that promote a safe and clean environment for patients. | Material certifications; antibacterial properties; compliance with health regulations. |
Event Management | Temporary Seating Solutions for Conferences and Events | Versatile and portable seating that can be easily set up and dismantled, maximizing space utilization. | Weight and stackability; rental options; quick delivery timelines. |
Retail | Waiting Areas and Checkout Spaces | Comfortable seating that enhances customer experience and encourages longer store visits. | Design aesthetics; color variety; durability for high-traffic areas. |
How Are Plastic Chairs Used in the Education Sector?
In educational institutions, plastic chairs are commonly used in classrooms and auditoriums. They provide a lightweight and durable seating solution that can withstand the rigors of daily use. The ease of cleaning is particularly beneficial in environments where hygiene is paramount. For international buyers in regions like Africa and South America, sourcing chairs that comply with local safety standards and ergonomic designs is crucial to ensure student comfort and engagement.
What is the Role of Plastic Chairs in the Hospitality Industry?
In the hospitality sector, plastic chairs are ideal for both indoor and outdoor dining areas. Their weather-resistant properties make them suitable for outdoor settings, while a variety of styles can enhance the overall aesthetic of a restaurant. Buyers should consider options that offer UV resistance and custom branding capabilities, as these features can significantly boost customer satisfaction and brand visibility.
Why Are Plastic Chairs Important in Healthcare Settings?
Plastic chairs play a vital role in healthcare settings, particularly in patient waiting areas and examination rooms. Their hygienic surfaces are easy to sanitize, which is essential for maintaining a clean environment. When sourcing for healthcare applications, buyers must ensure that the materials used are certified and possess antibacterial properties, aligning with health regulations to promote patient safety.
How Do Plastic Chairs Support Event Management?
In event management, plastic chairs provide temporary seating solutions that are both versatile and portable. They can be quickly set up and dismantled, making them ideal for conferences, weddings, and other gatherings. Key considerations for buyers include the weight and stackability of the chairs, as well as the availability of rental options to accommodate varying event sizes and budgets.
What Benefits Do Plastic Chairs Offer to Retail Environments?
In retail spaces, plastic chairs enhance customer experience by providing comfortable seating in waiting areas and checkout spaces. This encourages longer visits and increased customer satisfaction. Buyers should focus on design aesthetics, color variety, and durability to ensure that the chairs can withstand high-traffic areas, ultimately contributing to a positive shopping experience.
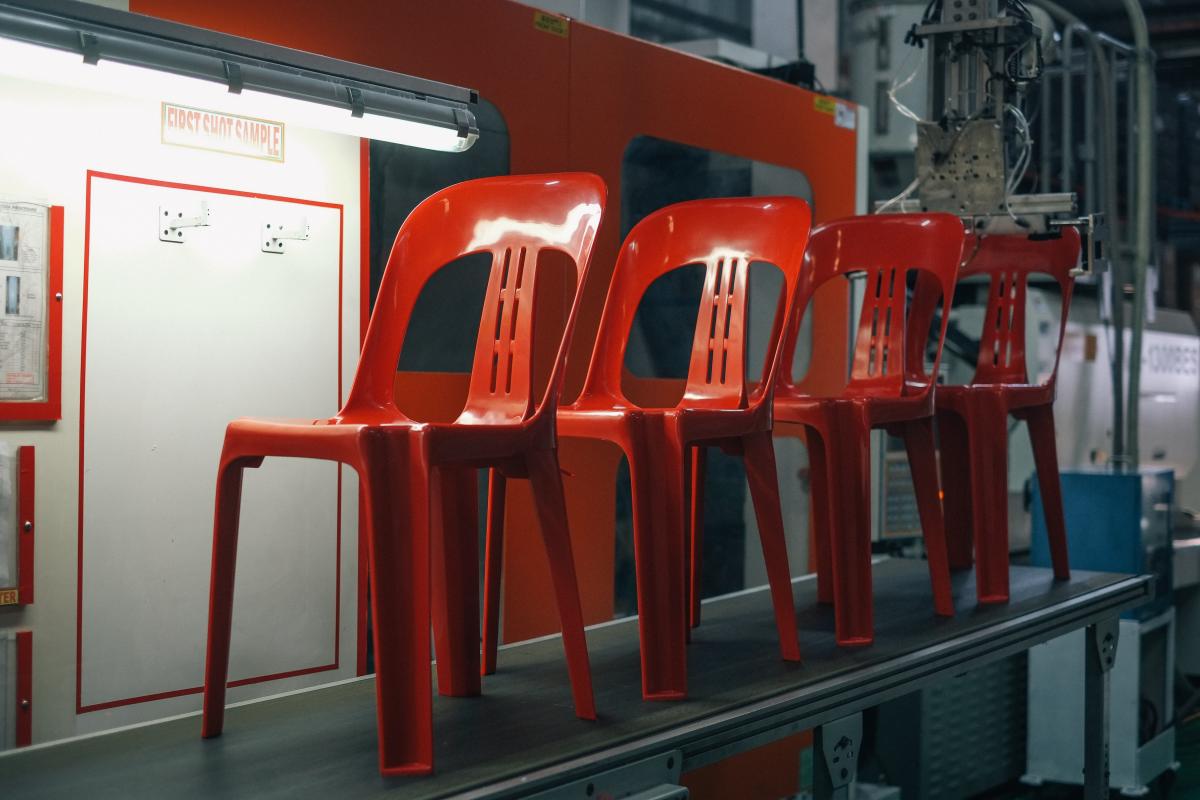
A stock image related to plastic chair manufacturer.
Related Video: Introducing Plastic Chair Manufacturing
3 Common User Pain Points for ‘plastic chair manufacturer’ & Their Solutions
Scenario 1: Difficulty Sourcing Environmentally Friendly Plastic Chairs
The Problem: Many B2B buyers are increasingly concerned about the environmental impact of their purchasing decisions, particularly regarding plastic products. With the rise of regulations in regions like the EU targeting plastic pollution, buyers often struggle to find manufacturers who offer sustainable options. This concern is compounded by the fear of choosing a supplier that may not comply with current or future environmental standards, leading to potential legal and reputational risks.
The Solution: To address this pain point, B2B buyers should prioritize manufacturers that specialize in environmentally friendly materials, such as recycled or biobased plastics. When sourcing plastic chairs, conduct thorough research to identify suppliers who have certifications such as ISO 14001 for environmental management. Additionally, ask for transparency in the supply chain, including details on the sourcing of materials and production processes. Engaging in dialogue with manufacturers about their sustainability initiatives can provide insights into their commitment to eco-friendly practices. Consider visiting production facilities or asking for product samples to ensure the quality and sustainability of the chairs meet your standards.
Scenario 2: Concerns Over Product Durability and Safety
The Problem: Buyers often worry about the durability and safety of plastic chairs, particularly in commercial settings where heavy use is expected. Questions arise about whether the chairs can withstand significant weight, resist fading from sunlight, or endure harsh weather conditions if used outdoors. This concern is heightened in regions with extreme weather, where chairs may be exposed to sun, rain, or humidity, leading to a fear of premature failure and increased replacement costs.
The Solution: To mitigate these concerns, buyers should seek out manufacturers that provide detailed product specifications and performance testing results. Look for chairs that come with warranties, as these can serve as a testament to the manufacturer’s confidence in their product’s durability. Request information about the materials used, such as UV-resistant additives or reinforced structures that enhance strength. Additionally, inquire about the manufacturer’s compliance with safety standards such as ANSI/BIFMA, which evaluates the safety and durability of commercial furniture. If possible, arrange for a trial period where you can assess the chairs in your specific environment before making a bulk purchase.
Scenario 3: Difficulty in Customization and Bulk Ordering
The Problem: Many international buyers face challenges when trying to customize plastic chairs to fit their unique branding or design specifications. Additionally, they may encounter issues related to minimum order quantities that do not align with their needs, making it difficult to balance costs with desired features. This can be particularly frustrating for buyers who want to create a cohesive look in their establishments but are limited by the offerings of suppliers.
The Solution: To overcome these customization hurdles, buyers should proactively communicate their specific requirements to potential manufacturers. This includes discussing color options, branding elements, and ergonomic features. Look for manufacturers that offer a range of customizable options and are open to collaborative design processes. Inquire about their capabilities for small batch productions, as some manufacturers may offer flexibility in minimum order quantities, particularly for first-time buyers or in pilot projects. Establishing a strong relationship with the manufacturer can also facilitate better negotiation on terms and enhance the likelihood of receiving tailored solutions that meet your operational needs.
Strategic Material Selection Guide for plastic chair manufacturer
What Are the Key Materials Used in Plastic Chair Manufacturing?
When selecting materials for plastic chairs, manufacturers typically consider several common types of plastics, each with distinct properties and applications. Below, we analyze four prevalent materials: Polypropylene (PP), Polyethylene (PE), Polyvinyl Chloride (PVC), and Acrylonitrile Butadiene Styrene (ABS). Understanding their characteristics, advantages, and limitations can significantly aid international B2B buyers in making informed purchasing decisions.
How Does Polypropylene (PP) Perform in Chair Manufacturing?
Polypropylene is a versatile thermoplastic known for its robustness and resistance to impact and chemicals. It has a temperature rating of up to 100°C and demonstrates excellent fatigue resistance, making it suitable for chairs that require frequent use.
Pros: Polypropylene is lightweight, cost-effective, and easy to mold, which simplifies manufacturing processes. Its durability ensures longevity, making it an attractive option for both residential and commercial applications.
Cons: While it has good resistance to chemicals, it can become brittle at lower temperatures. Additionally, it may not be suitable for outdoor use without UV stabilization, as prolonged exposure to sunlight can degrade its properties.
International Considerations: Buyers from Europe, particularly France, should be aware of compliance with EU regulations regarding plastic materials. The material must meet specific standards, such as EN 71 for safety in toys, which may apply to children’s chairs.
What Are the Advantages of Polyethylene (PE) in Chair Production?
Polyethylene, particularly High-Density Polyethylene (HDPE), is another popular choice for chair manufacturing. It offers excellent impact resistance and can withstand temperatures ranging from -40°C to 60°C.
Pros: PE is highly resistant to moisture, making it ideal for outdoor furniture. It is also recyclable, aligning with growing environmental concerns and regulations, especially in regions like Europe where sustainability is a priority.
Cons: While generally durable, PE can be susceptible to stress cracking under certain conditions. Its lower rigidity compared to other materials may limit its use in designs requiring structural integrity.
International Considerations: In South America, where outdoor furniture is in high demand, buyers should look for PE products that comply with local environmental regulations. Understanding the recycling capabilities of PE can also enhance marketability.
Why Choose Polyvinyl Chloride (PVC) for Plastic Chairs?
PVC is widely used in the furniture industry due to its versatility and cost-effectiveness. It can be formulated to achieve varying degrees of flexibility and rigidity, making it suitable for a range of chair designs.
Pros: PVC is resistant to moisture, chemicals, and UV light, which makes it ideal for outdoor applications. Its low cost and ease of manufacturing contribute to its popularity among manufacturers.
Cons: The environmental impact of PVC production and disposal is a significant concern. Additionally, it can become brittle over time, especially when exposed to extreme temperatures.
International Considerations: In the Middle East, where UV exposure is high, buyers should ensure that the PVC used is specifically treated for outdoor use. Buyers should also be aware of local regulations regarding the use of PVC, particularly in terms of environmental compliance.
What Makes Acrylonitrile Butadiene Styrene (ABS) a Good Choice?
ABS is a strong and durable thermoplastic that offers excellent impact resistance and toughness. It operates effectively in a temperature range of -20°C to 80°C.
Pros: ABS is known for its aesthetic appeal, allowing for a smooth finish and vibrant colors. It is also easy to mold, which provides flexibility in design and manufacturing.
Cons: ABS can be more expensive than other plastics, and its resistance to outdoor conditions is limited without additional treatments. It is also not as recyclable as other options.
International Considerations: In Europe, compliance with the REACH regulation is essential when using ABS. Buyers should ensure that the material does not contain harmful substances and meets the necessary safety standards.
Summary of Material Selection for Plastic Chairs
Material | Typical Use Case for Plastic Chair Manufacturer | Key Advantage | Key Disadvantage/Limitation | Relative Cost (Low/Med/High) |
---|---|---|---|---|
Polypropylene (PP) | Indoor and outdoor chairs | Lightweight and durable | Brittle at low temperatures | Low |
Polyethylene (PE) | Outdoor furniture | Moisture resistant and recyclable | Susceptible to stress cracking | Medium |
Polyvinyl Chloride (PVC) | Versatile chair designs | UV resistant and cost-effective | Environmental concerns | Low |
Acrylonitrile Butadiene Styrene (ABS) | High-end decorative chairs | Aesthetic appeal and toughness | Higher cost and limited recyclability | High |
This guide serves as a strategic tool for international B2B buyers, particularly those from Africa, South America, the Middle East, and Europe, enabling them to make informed decisions based on material properties, applications, and compliance requirements.
In-depth Look: Manufacturing Processes and Quality Assurance for plastic chair manufacturer
What Are the Key Stages in the Manufacturing Process of Plastic Chairs?
The manufacturing of plastic chairs involves several critical stages that ensure product quality, durability, and design integrity. Understanding these stages can help B2B buyers make informed decisions when sourcing from manufacturers.
Material Preparation
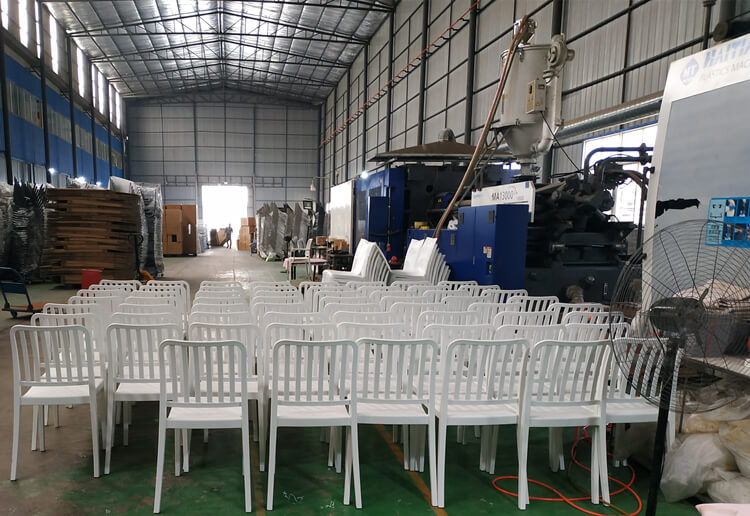
A stock image related to plastic chair manufacturer.
The first step in the production of plastic chairs is the preparation of raw materials. Common materials include high-density polyethylene (HDPE), polypropylene (PP), and polycarbonate (PC). These materials are selected based on their strength, flexibility, and resistance to environmental factors.
- Material Sourcing: It’s essential for manufacturers to source materials from reputable suppliers. This not only ensures quality but also compliance with international environmental standards.
- Testing Raw Materials: Before production, raw materials undergo rigorous testing to assess their physical properties, including tensile strength and UV resistance, which are vital for outdoor chairs.
What Techniques Are Used in Forming Plastic Chairs?
The forming stage is where the actual shape of the chair is created. Various techniques are utilized, each with its advantages:
- Injection Molding: This is the most common technique for producing plastic chairs. It involves injecting molten plastic into a mold, where it cools and solidifies into the desired shape. This method is efficient for high-volume production and allows for intricate designs.
- Blow Molding: Used primarily for hollow chair designs, blow molding involves inflating a heated plastic tube inside a mold. This technique is ideal for creating lightweight and stackable chairs.
- Rotational Molding: This process allows for the production of large, hollow chairs with uniform wall thickness. It is particularly useful for outdoor furniture.
These techniques should be evaluated based on production volume, design complexity, and cost-effectiveness.
How Is the Assembly Process Managed in Plastic Chair Manufacturing?
Once the individual components are formed, they are assembled into complete chairs. This stage typically involves:
- Component Assembly: Parts such as the seat, backrest, and legs are assembled, often using screws, adhesives, or snap-fit designs for a secure fit.
- Quality Checks: Throughout the assembly process, manufacturers perform in-line inspections to ensure parts fit correctly and function as intended.
Effective assembly methods reduce the chances of defects and improve overall efficiency.
What Finishing Techniques Are Commonly Used for Plastic Chairs?
Finishing touches can enhance the appearance and durability of plastic chairs. Common techniques include:
- Surface Treatment: Processes like sanding, polishing, or applying UV protective coatings can significantly enhance aesthetics and longevity.
- Coloring: Manufacturers may use dyes during the molding process or apply paint or decals post-production for branding purposes.
- Quality Control: A final inspection ensures that the finishing meets the required standards before the product is packaged and shipped.
What Are the Quality Assurance Standards Relevant to Plastic Chair Manufacturing?
Quality assurance is critical in ensuring that plastic chairs meet both safety and performance standards. Various international and industry-specific standards are applicable:
- ISO 9001: This standard outlines a framework for quality management systems and is crucial for manufacturers aiming for global competitiveness. It ensures that products consistently meet customer and regulatory requirements.
- CE Marking: In Europe, CE marking indicates compliance with health, safety, and environmental protection standards. This is particularly important for B2B buyers from European countries such as France, ensuring that the products are safe for use.
- API Standards: For specialized applications, such as industrial or commercial use, adherence to American Petroleum Institute (API) standards may be necessary.
What Are the Key Quality Control Checkpoints During Manufacturing?
Quality control (QC) checkpoints are essential in maintaining product integrity throughout the manufacturing process. Key checkpoints include:
- Incoming Quality Control (IQC): This involves inspecting raw materials upon receipt to ensure they meet specified standards.
- In-Process Quality Control (IPQC): Regular inspections during the manufacturing process help identify defects early. This includes checking dimensions, assembly, and functionality.
- Final Quality Control (FQC): Before shipping, a comprehensive review of the finished product ensures it meets all quality standards and specifications.
How Can B2B Buyers Verify Supplier Quality Control Practices?
International buyers should take proactive steps to ensure that their suppliers adhere to stringent quality control practices:
- Supplier Audits: Conducting regular audits of the manufacturing facility can provide insights into their QC processes and adherence to international standards.
- Requesting Quality Reports: Buyers should ask for detailed QC reports that outline testing results, defect rates, and corrective actions taken.
- Third-Party Inspections: Engaging third-party inspection services can offer an unbiased evaluation of the manufacturing process and product quality.
What Are the QC and Certification Nuances for International B2B Buyers?
When sourcing plastic chairs from different regions, B2B buyers must be aware of various certification nuances:
- Regional Regulations: Each region may have specific regulations regarding plastic products, particularly concerning environmental impact and safety. Buyers from Africa, South America, the Middle East, and Europe should familiarize themselves with local laws.
- Certification Costs: Obtaining certifications can be costly and time-consuming. Buyers should inquire about the manufacturer’s certification status and any associated costs that may impact pricing.
- Sustainability Certifications: With growing emphasis on sustainability, manufacturers may also seek certifications that demonstrate environmentally friendly practices, such as ISO 14001 for environmental management.
By understanding these manufacturing processes and quality assurance practices, international B2B buyers can make informed decisions and ensure that they partner with reliable plastic chair manufacturers. This knowledge not only helps in sourcing high-quality products but also fosters long-term relationships built on trust and transparency.
Practical Sourcing Guide: A Step-by-Step Checklist for ‘plastic chair manufacturer’
In today’s competitive global market, sourcing the right plastic chair manufacturer is essential for ensuring quality, sustainability, and cost-effectiveness. This step-by-step checklist provides international B2B buyers, particularly from Africa, South America, the Middle East, and Europe, with actionable insights to navigate the sourcing process efficiently.
Step 1: Define Your Technical Specifications
Clearly outline the requirements for the plastic chairs you intend to purchase. Consider factors such as design, material types, weight capacity, and intended use (e.g., indoor vs. outdoor). This step is vital as it sets the foundation for evaluating potential suppliers and ensures that the final products meet your specific needs.
Step 2: Research Potential Manufacturers
Conduct thorough research to identify manufacturers that specialize in plastic chairs. Utilize online directories, trade shows, and industry forums. Look for companies that have experience in your target market and possess a good reputation for quality and service. Pay attention to their production capabilities and the range of products they offer.
Step 3: Evaluate Supplier Certifications and Compliance
Ensure that potential suppliers comply with relevant international standards and regulations. Check for certifications such as ISO 9001 for quality management and ISO 14001 for environmental management. This is crucial for ensuring that your supplier adheres to industry standards, minimizing risks related to product quality and environmental impact.
Step 4: Request Samples for Quality Assessment
Before making a large order, request samples of the plastic chairs. This allows you to assess the quality, durability, and comfort of the chairs firsthand. Ensure that the samples reflect the specifications you defined in Step 1. Testing the samples helps prevent issues later in the procurement process.
Step 5: Inquire About Sustainability Practices
In today’s market, sustainability is a key consideration. Ask manufacturers about their materials sourcing, production processes, and waste management practices. Look for suppliers who demonstrate a commitment to sustainable practices, such as using recycled materials or implementing energy-efficient manufacturing processes. This not only benefits the environment but can also enhance your brand’s reputation.
Step 6: Negotiate Terms and Pricing
Once you have identified a suitable manufacturer, engage in negotiations regarding pricing, payment terms, and delivery schedules. Ensure that you understand all costs involved, including shipping and customs duties. This step is important to establish a mutually beneficial agreement that aligns with your budget and timeline.
Step 7: Establish Clear Communication Channels
Create a communication plan with your chosen supplier to facilitate ongoing dialogue. This should include regular updates on production status, shipping, and any potential issues. Effective communication is essential for maintaining a strong relationship and ensuring that any concerns are addressed promptly.
By following these steps, international B2B buyers can streamline the sourcing process and establish successful partnerships with plastic chair manufacturers.
Comprehensive Cost and Pricing Analysis for plastic chair manufacturer Sourcing
What Are the Key Cost Components in Sourcing Plastic Chairs?
When sourcing plastic chairs, understanding the cost structure is crucial for B2B buyers. The primary cost components include:
-
Materials: The type of plastic used significantly affects the overall cost. High-density polyethylene (HDPE) or polypropylene are commonly utilized due to their durability and resistance to environmental factors. Sustainable materials, such as recycled plastics, may incur higher initial costs but can enhance brand value and appeal to eco-conscious consumers.
-
Labor: Labor costs vary by region and can influence pricing. In regions with lower labor costs, like parts of Africa and South America, the overall manufacturing costs can be reduced. Conversely, European manufacturers may have higher labor costs, impacting the final pricing of the chairs.
-
Manufacturing Overhead: This includes expenses related to factory operations, equipment maintenance, and utilities. Efficient production processes can lower overhead costs, allowing manufacturers to offer competitive pricing.
-
Tooling: Initial tooling costs can be significant, especially for custom designs or specifications. B2B buyers should account for these in their total cost estimates, as these costs are often amortized over production runs.
-
Quality Control (QC): Ensuring product quality can add to costs but is essential for maintaining standards. Implementing robust QC processes may increase upfront costs but can prevent costly returns and reputational damage.
-
Logistics: Shipping and handling costs are critical, particularly for international buyers. These costs can vary based on distance, shipping methods, and Incoterms used.
-
Margin: Manufacturers will typically include a profit margin, which can vary significantly based on their business model and market positioning.
How Do Price Influencers Impact the Cost of Plastic Chairs?
Several factors can influence the pricing of plastic chairs:
-
Volume/MOQ: Manufacturers often offer discounts for larger orders. Understanding the minimum order quantity (MOQ) can help buyers negotiate better terms and lower per-unit costs.
-
Specifications and Customization: Custom designs or unique features may lead to higher prices. Buyers should weigh the benefits of customization against the additional costs.
-
Materials and Quality Certifications: Higher-quality materials or certified sustainable options can increase costs but may be necessary for specific markets or customer segments.
-
Supplier Factors: The supplier’s reputation, reliability, and production capabilities can all impact pricing. Engaging with established suppliers can often lead to better quality and service.
-
Incoterms: The choice of Incoterms (International Commercial Terms) affects shipping costs and risk distribution. Understanding these terms is vital for calculating total costs effectively.
What Negotiation Strategies Can Help Buyers Optimize Costs?
For international B2B buyers, especially from Africa, South America, the Middle East, and Europe, effective negotiation is essential:
-
Build Relationships: Establishing long-term relationships with suppliers can lead to better pricing and terms. Suppliers are often more willing to negotiate with trusted partners.
-
Leverage Volume: When possible, consolidate orders to meet higher volume thresholds that could yield discounts.
-
Understand Total Cost of Ownership (TCO): Beyond the purchase price, consider logistics, maintenance, and potential disposal costs when evaluating suppliers. This holistic view can guide better sourcing decisions.
-
Stay Informed on Market Trends: Awareness of material price fluctuations, regulatory changes, and economic conditions can provide leverage during negotiations.
Why Is It Important to Be Aware of Pricing Nuances in Different Markets?
B2B buyers must recognize that pricing structures can vary significantly by region. For instance, compliance with environmental regulations in Europe may increase costs compared to markets with less stringent standards. Understanding these nuances allows buyers to make informed decisions that align with their budget and business goals.
Disclaimer: The prices and cost components mentioned are indicative and can vary based on market conditions, supplier negotiations, and specific buyer requirements. Always conduct thorough research and obtain detailed quotations for accurate pricing.
Alternatives Analysis: Comparing plastic chair manufacturer With Other Solutions
Understanding the Importance of Alternatives in Plastic Chair Manufacturing
In the evolving landscape of furniture production, particularly in the B2B sector, international buyers are increasingly seeking alternatives to traditional plastic chairs. These alternatives can range from different materials to innovative manufacturing techniques, each offering unique benefits and challenges. Understanding these alternatives is crucial for B2B buyers, particularly from regions such as Africa, South America, the Middle East, and Europe, where sustainability and cost-effectiveness play significant roles in procurement decisions.
Comparison Table of Plastic Chair Manufacturer and Alternatives
Comparison Aspect | Plastic Chair Manufacturer | Alternative 1: Metal Chair Manufacturer | Alternative 2: Wooden Chair Manufacturer |
---|---|---|---|
Performance | Lightweight, durable, weather-resistant | High durability, rust-resistant with proper treatment | Solid, aesthetically pleasing but can be heavy |
Cost | Generally low to moderate | Moderate to high, depending on metal type | Moderate, with variability based on wood type |
Ease of Implementation | Quick to manufacture and assemble | Requires more complex fabrication processes | Moderate; assembly can be straightforward but may require finishing |
Maintenance | Low maintenance, easy to clean | Moderate; may require rust prevention | Higher; needs regular treatment to prevent damage |
Best Use Case | Outdoor events, casual settings | Commercial use, long-term investments | High-end settings, eco-friendly markets |
Detailed Breakdown of Alternative Solutions
What Are the Benefits and Drawbacks of Metal Chairs?
Metal chairs, particularly those made from aluminum or steel, offer substantial durability and a modern aesthetic. They are ideal for commercial settings such as cafes or offices where longevity is a priority. However, their higher manufacturing costs and susceptibility to rust without proper treatment can be drawbacks. Additionally, they may not be as lightweight as plastic options, which can complicate transport and rearrangement.
How Do Wooden Chairs Compare?
Wooden chairs provide a classic and sophisticated look that appeals to high-end markets. They are often favored in settings such as restaurants or corporate offices focused on sustainability. However, the maintenance of wooden chairs can be a challenge; they require regular treatments to prevent wear from moisture and pests. Moreover, the cost can vary significantly based on the type of wood used, which can impact budget considerations for B2B buyers.
Conclusion: How Can B2B Buyers Choose the Right Solution?
When selecting the right seating solution, B2B buyers should consider their specific needs, including durability, cost, maintenance, and the intended environment for use. While plastic chairs offer advantages in terms of cost and ease of maintenance, alternatives like metal and wooden chairs present unique benefits that may align better with certain business objectives. Evaluating these factors in the context of sustainability initiatives and market trends can lead to more informed procurement decisions, ultimately enhancing customer satisfaction and operational efficiency.
Essential Technical Properties and Trade Terminology for plastic chair manufacturer
What Are the Key Technical Properties for Plastic Chairs?
When sourcing plastic chairs, international B2B buyers should be familiar with several critical technical properties. Understanding these specifications can significantly impact the quality, durability, and overall cost-effectiveness of the chairs.
1. Material Grade
The material grade refers to the type and quality of plastic used in manufacturing chairs, typically high-density polyethylene (HDPE), polypropylene (PP), or polycarbonate (PC). The choice of material affects the chair’s strength, weight capacity, and resistance to UV light, chemicals, and weather conditions. For instance, HDPE is known for its robustness and recyclability, making it suitable for outdoor use. Selecting the right material grade is vital for ensuring longevity and meeting safety standards.
2. Load Capacity
Load capacity indicates the maximum weight a chair can safely support. This specification is crucial for commercial environments such as restaurants, offices, and event venues. A chair with a higher load capacity not only ensures user safety but also enhances customer satisfaction. Buyers should verify this specification to avoid liability issues and ensure that the chairs meet their operational needs.
3. Tolerance Levels
Tolerance levels define the allowable variation in dimensions during the manufacturing process. This specification is important for ensuring that chairs fit together correctly when stacked or assembled. For B2B buyers, understanding tolerance levels can prevent issues related to assembly, stability, and overall aesthetics, especially in large-scale purchases.
4. Color Fastness
Color fastness refers to a material’s resistance to fading or discoloration when exposed to light, washing, or chemicals. This property is particularly important for plastic chairs used in outdoor settings or high-traffic areas. Chairs with high color fastness will maintain their appearance over time, reducing the need for replacements and ensuring a better return on investment.
5. Surface Finish
The surface finish of a plastic chair can influence both its aesthetic appeal and functionality. Options include matte, glossy, or textured finishes, each offering different benefits in terms of grip, ease of cleaning, and visual appeal. Buyers should consider the intended use and environment when selecting a finish, as it can affect user experience.
What Are Common Trade Terms in the Plastic Chair Manufacturing Industry?
Familiarizing yourself with industry terminology can facilitate smoother transactions and better communication with suppliers.
1. OEM (Original Equipment Manufacturer)
An OEM refers to a company that produces parts or products that are used in another company’s end product. For plastic chairs, this could mean a manufacturer that creates components for another brand’s chair line. Understanding OEM relationships can help buyers identify potential suppliers and assess product quality.
2. MOQ (Minimum Order Quantity)
MOQ is the smallest quantity of a product that a supplier is willing to sell. Knowing the MOQ is crucial for budgeting and inventory management. Buyers should negotiate MOQs based on their needs to avoid excess inventory or missed opportunities.
3. RFQ (Request for Quotation)
An RFQ is a document issued by a buyer to solicit price offers from suppliers. It typically includes specifications, quantities, and terms of delivery. Submitting a well-defined RFQ helps buyers receive accurate and competitive quotes, facilitating better decision-making.
4. Incoterms (International Commercial Terms)
Incoterms are internationally recognized rules that define the responsibilities of buyers and sellers in international transactions. They clarify who is responsible for shipping, insurance, and tariffs. Familiarity with Incoterms can protect buyers from unexpected costs and legal complications.
5. Lead Time
Lead time refers to the duration between placing an order and receiving the product. Understanding lead times is essential for inventory planning and ensuring timely delivery. Buyers should discuss lead times with suppliers to align their production schedules with market demands.
6. Certification Standards
Certification standards, such as ISO or ASTM, indicate that a product meets specific safety and quality benchmarks. Familiarity with these certifications can help buyers ensure that the plastic chairs they are sourcing comply with industry regulations and customer expectations.
By understanding these technical properties and trade terms, international B2B buyers can make informed decisions when sourcing plastic chairs, ultimately enhancing their purchasing strategy and operational efficiency.
Navigating Market Dynamics and Sourcing Trends in the plastic chair manufacturer Sector
What Are the Current Market Dynamics and Key Trends in the Plastic Chair Manufacturing Sector?
The plastic chair manufacturing sector is experiencing a notable transformation influenced by several global drivers, including rising consumer demand for sustainable products, advancements in manufacturing technology, and evolving regulatory landscapes. As international B2B buyers from regions such as Africa, South America, the Middle East, and Europe (notably France and Colombia) seek to optimize sourcing strategies, understanding these dynamics becomes crucial.
One significant trend is the increasing integration of automation and smart technologies in production processes. Manufacturers are leveraging robotics and IoT (Internet of Things) to enhance efficiency, reduce costs, and improve product quality. This shift is particularly relevant for international buyers who prioritize suppliers that can deliver consistent quality and speed in production.
Additionally, there is a growing emphasis on customization in plastic chair designs to meet diverse consumer preferences across various markets. Buyers are now looking for manufacturers that can offer tailored solutions, reflecting local tastes and ergonomic needs. The rise of e-commerce has further fueled this trend, enabling manufacturers to reach broader markets and streamline their supply chains.
Another vital aspect is the regulatory environment, particularly in Europe, where stringent regulations regarding plastic use and waste management are becoming the norm. Compliance with these regulations not only ensures market access but also enhances the brand image of manufacturers, making them more attractive to ethically-minded buyers.
How Is Sustainability and Ethical Sourcing Influencing the Plastic Chair Manufacturing Sector?
Sustainability has emerged as a cornerstone in the plastic chair manufacturing sector, significantly impacting purchasing decisions for international B2B buyers. The environmental implications of plastic waste are driving manufacturers to adopt more sustainable practices, including the use of recycled materials and eco-friendly production methods.
Buyers are increasingly prioritizing suppliers that demonstrate commitment to sustainability through certifications such as ISO 14001 (Environmental Management) and other green certifications. These credentials not only reflect a manufacturer’s dedication to minimizing environmental impact but also provide assurance to buyers regarding ethical sourcing practices.
In terms of materials, the trend is shifting towards bioplastics and biodegradable options. Manufacturers are exploring alternatives that reduce reliance on fossil fuels and minimize the carbon footprint associated with traditional plastic production. For B2B buyers, sourcing from manufacturers that utilize sustainable materials aligns with corporate social responsibility goals and appeals to environmentally-conscious consumers.
Furthermore, the emphasis on ethical supply chains is becoming more pronounced. Buyers are demanding transparency in the sourcing of materials, ensuring that suppliers uphold fair labor practices and contribute positively to the communities in which they operate. This trend is particularly relevant for buyers in regions like Africa and South America, where social sustainability is closely linked to economic development.
What Is the Brief Evolution of the Plastic Chair Manufacturing Sector?
The evolution of the plastic chair manufacturing sector has been marked by significant technological advancements and changing consumer preferences. Initially, plastic chairs were primarily seen as affordable, lightweight, and easy-to-manufacture options for mass markets. However, as environmental concerns gained prominence in the late 20th century, the industry began to innovate towards more sustainable practices.
The introduction of advanced materials and production techniques, such as injection molding and 3D printing, has transformed the design possibilities for plastic chairs. Manufacturers are now able to create aesthetically pleasing, ergonomic, and customizable products that cater to diverse markets. This evolution reflects a broader shift in consumer expectations, where style, comfort, and sustainability are paramount.
In conclusion, international B2B buyers must navigate these dynamic market conditions by prioritizing suppliers that align with their values and operational needs. Emphasizing sustainability, ethical sourcing, and technological innovation will be crucial in securing competitive advantages in the plastic chair manufacturing sector.
Frequently Asked Questions (FAQs) for B2B Buyers of plastic chair manufacturer
-
How do I choose the right plastic chair manufacturer for my business needs?
Selecting the right plastic chair manufacturer involves assessing several factors, including production capacity, quality certifications, and compliance with international standards. Research potential suppliers through trade shows, online directories, and industry reviews. Evaluate their experience in your target market, especially in regions like Africa, South America, the Middle East, and Europe. Request samples to assess quality and craftsmanship. Finally, consider their ability to customize designs to fit your brand and customer preferences. -
What are the customization options available for plastic chairs from manufacturers?
Many plastic chair manufacturers offer a range of customization options, including colors, sizes, and materials. Some may also provide branding opportunities such as logo printing or embossing. When discussing customization, be clear about your specific requirements, minimum order quantities, and lead times. It’s essential to communicate your vision effectively to ensure the final product aligns with your expectations and market demand.
-
What should I consider regarding minimum order quantities (MOQs) when sourcing plastic chairs?
Minimum order quantities (MOQs) can significantly impact your purchasing strategy. Different manufacturers may have varying MOQs based on production capabilities and material availability. When negotiating with suppliers, consider your budget, storage capacity, and the market demand for the chairs. If the MOQ is higher than you can accommodate, inquire about the possibility of a trial order or smaller batch sizes, particularly if you are testing new designs in your market. -
What are the typical payment terms when working with plastic chair manufacturers?
Payment terms can vary widely among plastic chair manufacturers, often depending on the supplier’s location and your relationship with them. Common payment structures include upfront deposits (typically 30% to 50%) followed by the balance upon delivery. It’s advisable to discuss and agree upon payment terms before finalizing contracts. Be cautious of manufacturers requiring full payment in advance, especially if you are sourcing from overseas, as it may carry higher risks. -
How can I ensure quality assurance when sourcing plastic chairs internationally?
To ensure quality assurance, establish clear quality standards and specifications before placing an order. Request samples for inspection and conduct factory visits if possible. Consider hiring a third-party inspection service to verify product quality before shipment. Additionally, ensure that the manufacturer complies with relevant international standards and certifications, such as ISO or ASTM. Document all quality expectations in your contract to hold suppliers accountable. -
What logistics considerations should I keep in mind when importing plastic chairs?
Logistics plays a crucial role in international sourcing. Consider factors such as shipping methods, lead times, and customs regulations in your country. Work with a reliable freight forwarder who understands the complexities of importing goods from different regions. Additionally, account for potential duties and taxes that may apply upon arrival. Establish a clear communication line with your supplier regarding shipping schedules and any documentation required for a smooth import process. -
How do I evaluate a plastic chair manufacturer’s sustainability practices?
Evaluating a manufacturer’s sustainability practices is increasingly important for B2B buyers. Request information about their sourcing of materials, waste management practices, and energy use during production. Look for certifications such as ISO 14001, which indicates a commitment to environmental management. Additionally, inquire about their involvement in recycling initiatives or use of recycled materials in their products. Supporting manufacturers with sustainable practices can enhance your brand image and appeal to environmentally conscious consumers. -
What are the common challenges faced when sourcing plastic chairs internationally, and how can I overcome them?
Common challenges include language barriers, cultural differences, and varying quality standards. To overcome these, invest time in understanding the market and customs of the manufacturer’s country. Establish clear communication channels and consider hiring local representatives if necessary. Additionally, thorough research and due diligence can help mitigate risks. Building strong relationships with suppliers can also facilitate smoother transactions and help address any issues that arise during the sourcing process.
Important Disclaimer & Terms of Use
⚠️ Important Disclaimer
The information provided in this guide, including content regarding manufacturers, technical specifications, and market analysis, is for informational and educational purposes only. It does not constitute professional procurement advice, financial advice, or legal advice.
While we have made every effort to ensure the accuracy and timeliness of the information, we are not responsible for any errors, omissions, or outdated information. Market conditions, company details, and technical standards are subject to change.
B2B buyers must conduct their own independent and thorough due diligence before making any purchasing decisions. This includes contacting suppliers directly, verifying certifications, requesting samples, and seeking professional consultation. The risk of relying on any information in this guide is borne solely by the reader.
Strategic Sourcing Conclusion and Outlook for plastic chair manufacturer
As international B2B buyers navigate the evolving landscape of the plastic chair manufacturing industry, the importance of strategic sourcing cannot be overstated. Understanding local regulations, especially in regions like Africa, South America, the Middle East, and Europe, is crucial for compliance and sustainability. The increasing focus on eco-friendly materials and practices, driven by initiatives such as the EU’s Single-Use Plastics Directive, presents both challenges and opportunities for manufacturers and buyers alike.
How Can Strategic Sourcing Enhance Your Competitive Edge?
Implementing a strategic sourcing approach enables buyers to optimize their supply chains, reduce costs, and ensure the ethical sourcing of materials. By fostering relationships with suppliers committed to sustainable practices, businesses can not only improve their market position but also contribute to a circular economy. Engaging with manufacturers that prioritize innovation in materials—like biodegradable plastics—will be essential as consumer demand for sustainable products rises.
What’s Next for International Buyers in the Plastic Chair Market?
Looking forward, international B2B buyers should prioritize partnerships with manufacturers who demonstrate a commitment to sustainability and regulatory compliance. This proactive approach will not only mitigate risks associated with supply chain disruptions but also align with growing global consumer preferences for eco-friendly products. As the market evolves, now is the time to reassess sourcing strategies and embrace the future of sustainable plastic manufacturing. Engage with suppliers who share your vision for a greener tomorrow—your business, and the planet, will thank you.