The Ultimate Guide to Prefabricated Container House China (2025)
Introduction: Navigating the Global Market for prefabricated container house china
In an increasingly competitive global landscape, sourcing high-quality prefabricated container houses from China presents both opportunities and challenges for international B2B buyers. Whether you’re looking to provide affordable housing solutions in Africa or create innovative commercial spaces in Europe, understanding the nuances of this market is crucial. This guide comprehensively covers various types of prefabricated container houses, their diverse applications, and the essential steps for vetting suppliers effectively.
Navigating the complexities of international procurement can be daunting, especially when it comes to ensuring quality and compliance with local regulations. This guide empowers B2B buyers by offering actionable insights into supplier evaluation, cost considerations, and logistical challenges. With detailed analyses tailored to the unique needs of buyers from regions such as South America, the Middle East, and Europe, we aim to equip you with the knowledge needed to make informed purchasing decisions.
By diving into the specifics of sourcing prefabricated container houses from China, this guide serves as a valuable resource for businesses looking to capitalize on innovative construction solutions. From understanding material costs to exploring customization options, our insights will help you streamline your procurement process and ultimately enhance your business operations.
Understanding prefabricated container house china Types and Variations
Type Name | Key Distinguishing Features | Primary B2B Applications | Brief Pros & Cons for Buyers |
---|---|---|---|
Modular Container Homes | Pre-designed units that can be stacked or joined | Residential, workforce housing | Pros: Fast assembly, customizable; Cons: Limited space if not expanded. |
Mobile Container Offices | Transportable office spaces with utilities | Construction sites, remote locations | Pros: Flexibility, quick deployment; Cons: Less durable than permanent structures. |
Shipping Container Conversions | Upcycled shipping containers for various uses | Retail, pop-up shops, cafes | Pros: Eco-friendly, cost-effective; Cons: Requires insulation for comfort. |
Luxury Container Homes | High-end finishes and amenities | High-end residential, vacation homes | Pros: Aesthetic appeal, durability; Cons: Higher initial costs. |
Container Storage Solutions | Secure storage units made from containers | Warehousing, inventory management | Pros: Security, weather-resistant; Cons: Static location limits mobility. |
What Are Modular Container Homes and Their B2B Relevance?
Modular container homes are prefabricated units that can be stacked or connected to create larger living spaces. They are ideal for residential projects or workforce housing, particularly in regions where rapid deployment is essential. B2B buyers should consider the customization options available, which allow for tailored designs to meet specific requirements. Additionally, these homes can be assembled quickly, reducing construction time significantly.
How Do Mobile Container Offices Serve Businesses?
Mobile container offices provide flexible workspace solutions that can be easily transported to various locations. They are especially useful for construction sites and remote work environments where traditional office setups are impractical. Buyers should evaluate the utilities included, such as electricity and plumbing, as well as the overall durability of the office to withstand various weather conditions. The ability to relocate these offices as needed offers significant operational advantages.
What Are the Benefits of Shipping Container Conversions?
Shipping container conversions involve repurposing old shipping containers into functional spaces like retail stores, cafes, or even art galleries. This type of prefabricated structure appeals to businesses looking for cost-effective and eco-friendly solutions. B2B buyers should assess insulation needs, as these containers may require additional work to ensure comfort in extreme temperatures. The unique aesthetic of converted containers can also attract customers, enhancing brand visibility.
Why Choose Luxury Container Homes for High-End Projects?
Luxury container homes are designed with premium finishes and amenities, making them suitable for high-end residential projects and vacation rentals. These units provide both aesthetic appeal and structural durability, catering to a market that values both style and functionality. B2B buyers should weigh the initial costs against the long-term investment potential, as these homes can command higher rental or resale prices. The growing trend of sustainable luxury living also enhances their appeal.
What Are Container Storage Solutions and Their Applications?
Container storage solutions are designed to provide secure and weather-resistant storage options for businesses. These units are often used for warehousing and inventory management, offering a straightforward solution to space constraints. Buyers should consider the location and accessibility of these storage units, as well as the security features that can protect valuable assets. The static nature of these containers may limit flexibility, but their robustness makes them a reliable choice for long-term storage needs.
Related Video: The whole installation process of China prefab Flat-pack container house in 6 minutes.
Key Industrial Applications of prefabricated container house china
Industry/Sector | Specific Application of Prefabricated Container House China | Value/Benefit for the Business | Key Sourcing Considerations for this Application |
---|---|---|---|
Construction | Temporary Site Offices | Cost-effective and quick setup for project management | Durability, insulation properties, and customization options |
Mining | Worker Accommodation Units | Enhanced living conditions for remote workers | Compliance with local regulations and safety standards |
Healthcare | Mobile Clinics | Rapid deployment in underserved areas | Mobility, sanitation features, and modular design |
Education | Classroom Modules | Flexible learning spaces for schools in rural areas | Customization for educational needs and transportability |
Disaster Relief | Emergency Shelters | Quick response to natural disasters | Ease of transport, quick assembly, and resilience to elements |
How Are Prefabricated Container Houses Used in Construction Projects?
In the construction industry, prefabricated container houses serve as temporary site offices. They provide a cost-effective solution for project management teams needing quick setup and mobility. These units can be customized to include necessary amenities, such as meeting rooms and break areas, which enhances the work environment. For international buyers, especially in regions like Africa and South America, sourcing these units requires attention to durability and insulation properties, ensuring that they can withstand local climatic conditions.
What Role Do Prefabricated Container Houses Play in Mining Operations?
In the mining sector, prefabricated container houses are utilized as worker accommodation units. These structures address the challenge of providing comfortable living conditions for workers stationed in remote locations. They can be equipped with essential amenities, ensuring a better quality of life while working away from home. When sourcing, international buyers must consider compliance with local regulations and safety standards, as these factors are critical to maintaining operational efficiency and worker satisfaction.
How Are Prefabricated Container Houses Transforming Healthcare Delivery?
Mobile clinics made from prefabricated container houses are revolutionizing healthcare delivery in underserved areas. These units can be rapidly deployed to provide essential medical services during health crises or in remote locations. Their design allows for easy transport and setup, making them ideal for emergency responses. Buyers in the healthcare sector should prioritize mobility, sanitation features, and modular design when sourcing, ensuring that the clinics can adapt to various healthcare needs.
What Are the Benefits of Using Prefabricated Container Houses in Education?
In the education sector, prefabricated container houses are increasingly used as classroom modules. They provide flexible learning spaces that can be deployed in rural areas where traditional school buildings are lacking. These units can be customized to meet specific educational requirements, such as incorporating technology or specialized learning environments. For international buyers, especially in Europe and the Middle East, it is important to focus on customization options and transportability to ensure that the units meet local educational standards.
How Do Prefabricated Container Houses Aid in Disaster Relief Efforts?
During natural disasters, prefabricated container houses serve as emergency shelters, providing immediate housing solutions for displaced populations. Their quick assembly and ease of transport make them invaluable in crisis situations. These shelters can be designed to withstand harsh weather conditions, ensuring safety for those affected. Buyers involved in disaster relief should consider the ease of transport, quick assembly, and resilience to elements when sourcing these units, as these factors significantly impact the effectiveness of relief efforts.
3 Common User Pain Points for ‘prefabricated container house china’ & Their Solutions
Scenario 1: Navigating Quality Control Challenges in Prefabricated Container Houses
The Problem:
International B2B buyers often face significant concerns regarding the quality of prefabricated container houses sourced from China. Inconsistent manufacturing standards, varying material quality, and differing regulations can lead to subpar products that do not meet the buyer’s specifications or local building codes. For example, a construction company in Africa may receive a shipment of container homes with structural weaknesses, resulting in costly delays and safety concerns.
The Solution:
To mitigate quality control issues, B2B buyers should implement a rigorous supplier evaluation process before committing to purchases. This includes visiting the manufacturing facility in China, if feasible, to inspect production practices and materials firsthand. Additionally, buyers should request detailed certifications and quality assurance documentation for the products, ensuring they comply with both international and local building regulations. Establishing a Quality Assurance (QA) team to conduct regular audits and inspections during the manufacturing process can help maintain consistent quality. Furthermore, consider partnering with third-party inspection services that specialize in prefabricated structures to conduct pre-shipment inspections, ensuring that the final products meet the required standards before they leave the factory.
Scenario 2: Overcoming Delivery and Logistics Issues with Container Houses
The Problem:
One common pain point for B2B buyers is the unpredictability of shipping and logistics when ordering prefabricated container houses from China. Delays in shipping schedules, customs clearance issues, and high freight costs can disrupt project timelines and inflate budgets. For instance, a developer in South America may find that their planned construction schedule is thrown off due to late deliveries, leading to lost contracts and frustrated clients.
The Solution:
To address these logistics challenges, buyers should engage with experienced freight forwarders who have expertise in international shipping and can navigate the complexities of customs regulations. Establishing a clear communication channel with suppliers regarding delivery timelines and potential delays is crucial. Buyers should also consider using Incoterms (International Commercial Terms) to clearly define responsibilities and liabilities related to shipping, reducing misunderstandings. Additionally, having contingency plans, such as alternative suppliers or local storage solutions, can help mitigate the impact of unforeseen delays. Regularly tracking shipments and maintaining open lines of communication with logistics providers can ensure that any issues are promptly addressed, keeping projects on schedule.
Scenario 3: Managing Regulatory Compliance and Local Adaptation
The Problem:
Another significant pain point for B2B buyers is navigating the regulatory landscape related to prefabricated container houses. Different countries have unique building codes, zoning laws, and environmental regulations that must be adhered to. For instance, a buyer in the Middle East might struggle to align their imported container homes with local seismic standards, potentially leading to legal repercussions and project failures.
The Solution:
To effectively manage compliance challenges, buyers should conduct thorough research on the local regulations governing prefabricated structures in their respective markets. This includes consulting with local architects and engineers who are familiar with the regional codes and can provide insights on necessary modifications to the container designs. Collaborating with local authorities early in the project can help clarify requirements and streamline the permitting process. Additionally, buyers should communicate their specific regulatory needs to their suppliers in China, ensuring that the container homes are designed and manufactured with these considerations in mind. Investing in customization options that accommodate local building codes can enhance the usability and acceptance of prefabricated container houses in the target market, ultimately leading to a more successful project outcome.
Strategic Material Selection Guide for prefabricated container house china
What Are the Key Materials for Prefabricated Container Houses in China?
When considering the construction of prefabricated container houses in China, the choice of materials is crucial for ensuring durability, cost-effectiveness, and compliance with international standards. Below, we analyze four common materials used in these structures, focusing on their properties, advantages, disadvantages, and specific considerations for international B2B buyers.
How Does Steel Perform in Prefabricated Container Houses?
Key Properties:
Steel is renowned for its high strength-to-weight ratio, making it ideal for structural applications. It can withstand extreme temperatures and pressure, with a typical yield strength of around 250 MPa. Steel is also highly resistant to corrosion when treated with protective coatings.
Pros & Cons:
Steel’s durability is one of its main advantages, providing long-lasting performance. However, the initial cost can be high due to fabrication and treatment processes. Steel structures may also require regular maintenance to prevent rust, particularly in humid environments.
Impact on Application:
Steel is compatible with various media, including water and air, making it suitable for residential and commercial uses. Its strength allows for multi-story constructions, which is beneficial in urban settings.
Considerations for International Buyers:
Buyers from Africa, South America, the Middle East, and Europe should ensure compliance with local building codes and standards such as ASTM and DIN. In regions prone to corrosion, selecting galvanized or stainless steel is advisable.
What Role Does Insulation Material Play in Container Houses?
Key Properties:
Insulation materials like polyurethane foam or mineral wool provide excellent thermal resistance, with R-values ranging from 3.5 to 6.5 per inch. They also offer soundproofing benefits.
Pros & Cons:
The primary advantage of insulation is energy efficiency, significantly reducing heating and cooling costs. However, some insulation materials can be expensive and may require specialized installation techniques.
Impact on Application:
Proper insulation is crucial for maintaining comfortable living conditions, particularly in extreme climates. It prevents heat loss in cold regions and keeps interiors cool in hot climates.
Considerations for International Buyers:
International buyers should check for compliance with fire safety standards and environmental regulations, particularly in Europe and North America. Additionally, preferences for eco-friendly materials are increasing, particularly in markets like Europe.
How Does Plywood Contribute to Container House Construction?
Key Properties:
Plywood is lightweight yet strong, with good tensile strength and flexibility. It is also relatively resistant to moisture when treated, making it suitable for various environments.
Pros & Cons:
Plywood is cost-effective and easy to work with, allowing for quick assembly. However, it may not offer the same level of durability as steel or concrete, particularly in high-humidity areas where it can warp or rot.
Impact on Application:
Plywood is often used for interior finishes and partitions, contributing to the aesthetic appeal of container homes. It is compatible with various finishes and can be painted or stained.
Considerations for International Buyers:
Buyers should ensure that the plywood meets local standards for moisture resistance and sustainability, especially in regions with strict environmental regulations.
What About Concrete in Prefabricated Container Houses?
Key Properties:
Concrete is known for its compressive strength, typically exceeding 20 MPa. It is fire-resistant and can be molded into various shapes, providing design flexibility.
Pros & Cons:
The durability and low maintenance of concrete are significant advantages. However, it can be heavy and may require additional structural support, increasing overall costs.
Impact on Application:
Concrete is ideal for foundations and load-bearing walls, providing stability and longevity. It is also effective in sound insulation.
Considerations for International Buyers:
International buyers should be aware of local regulations regarding concrete standards and curing processes. In regions with seismic activity, specific reinforcement measures may be necessary.
Summary Table of Material Selection
Material | Typical Use Case for prefabricated container house china | Key Advantage | Key Disadvantage/Limitation | Relative Cost (Low/Med/High) |
---|---|---|---|---|
Steel | Structural framework and load-bearing elements | High strength and durability | High initial cost and maintenance | High |
Insulation | Thermal and sound insulation for comfort | Energy efficiency | Potentially high cost | Medium |
Plywood | Interior finishes and partitions | Cost-effective and easy to work | Less durable in humid conditions | Low |
Concrete | Foundations and load-bearing walls | Fire-resistant and stable | Heavy and may require extra support | Medium |
This strategic material selection guide aims to equip international B2B buyers with the knowledge necessary to make informed decisions when sourcing prefabricated container houses from China. Understanding the properties, advantages, and limitations of each material can lead to better project outcomes and compliance with local regulations.
In-depth Look: Manufacturing Processes and Quality Assurance for prefabricated container house china
What Are the Main Stages of Manufacturing Prefabricated Container Houses in China?
The manufacturing process of prefabricated container houses in China involves several critical stages that ensure both efficiency and quality. Understanding these stages helps international B2B buyers assess the capabilities of suppliers and make informed purchasing decisions.
1. Material Preparation: Sourcing and Quality Control
The first step in manufacturing prefabricated container houses is the preparation of materials. This typically includes sourcing high-quality steel, insulation, and other construction materials. Suppliers often engage in rigorous vetting processes to ensure that the materials meet international standards.
-
Key Techniques: Material testing is essential. Buyers should inquire about the types of tests conducted, such as tensile strength and corrosion resistance for steel.
-
Sourcing Considerations: For B2B buyers from regions like Africa and South America, understanding the supplier’s material sourcing practices can provide insights into the sustainability and durability of the final product.
2. Forming: Structural Fabrication Techniques
Once materials are prepared, the next phase is the forming of structural components. This involves cutting, bending, and welding steel containers into the desired shapes and sizes.
-
Key Techniques: Advanced machinery, such as CNC machines, is often used for precision cutting and forming. This technology ensures that each component fits perfectly during assembly, reducing the risk of structural weaknesses.
-
What to Look For: Buyers should assess whether the manufacturer uses automated processes to enhance accuracy and efficiency, which can significantly impact the final product’s quality.
3. Assembly: Combining Components for Structural Integrity
After forming, the individual components are assembled. This stage is crucial as it determines the structural integrity of the container house.
-
Key Techniques: Manufacturers may utilize modular assembly methods, where parts are prefabricated in sections and then transported to the site for quick assembly. This technique not only speeds up the construction process but also minimizes on-site labor costs.
-
Buyer Insights: International buyers should inquire about the assembly process, including the use of skilled labor and adherence to safety standards, to ensure the longevity and safety of the container houses.
4. Finishing: Surface Treatment and Aesthetic Enhancements
The finishing stage includes surface treatments, insulation installation, and aesthetic enhancements such as painting and interior fittings.
-
Key Techniques: Manufacturers often use powder coating or galvanization for corrosion resistance, while interior fittings can be customized based on buyer specifications.
-
Considerations for Buyers: It’s essential to discuss finishing options with suppliers, as these can greatly affect the container house’s durability and visual appeal.
How Is Quality Assurance Implemented in the Manufacturing of Container Houses?
Quality assurance is integral to the manufacturing process of prefabricated container houses, ensuring that the final products meet both buyer expectations and regulatory standards.
What International Standards Are Relevant for Prefabricated Container Houses?
B2B buyers should be aware of various international standards that govern the manufacturing of container houses. Compliance with these standards not only ensures quality but also enhances the credibility of suppliers.
-
ISO 9001: This standard focuses on quality management systems and is critical for manufacturers to demonstrate their commitment to quality assurance.
-
CE Marking: For European buyers, CE marking indicates compliance with health, safety, and environmental protection standards.
-
API Standards: In certain markets, especially in the Middle East, adherence to API standards can be crucial for structural integrity and safety.
What Are the Key Quality Control Checkpoints During Manufacturing?
Quality control checkpoints are critical to maintaining high standards throughout the manufacturing process.
-
Incoming Quality Control (IQC): This involves inspecting raw materials upon arrival to ensure they meet specified criteria.
-
In-Process Quality Control (IPQC): Regular inspections during the manufacturing process help identify and rectify defects early on.
-
Final Quality Control (FQC): Before shipping, a thorough inspection ensures that the finished product adheres to all quality standards and specifications.
How Can B2B Buyers Verify Supplier Quality Control Practices?
B2B buyers must take proactive steps to verify the quality control practices of their suppliers. Here are some actionable methods:
-
Audits and Inspections: Conducting regular audits of the manufacturing facility can provide insights into the supplier’s operational standards. Buyers should request access to recent audit reports.
-
Third-Party Inspections: Engaging third-party inspection services can ensure unbiased assessments of the manufacturing processes and final products.
-
Documentation Review: Requesting quality control documentation, such as inspection reports and compliance certificates, can provide further assurance of quality.
What Nuances Should International Buyers Consider Regarding Quality Control?
When sourcing prefabricated container houses from China, international buyers should be aware of specific nuances that may affect quality control:
-
Regulatory Differences: Different regions may have varying regulatory requirements. Buyers from Europe or the Middle East should be particularly vigilant about compliance with local standards.
-
Cultural Considerations: Understanding cultural attitudes towards quality and craftsmanship can help buyers navigate supplier relationships more effectively.
-
Communication: Clear and open lines of communication with suppliers can facilitate better understanding and adherence to quality expectations.
Conclusion: Making Informed Decisions in Sourcing Container Houses
In conclusion, understanding the manufacturing processes and quality assurance practices of prefabricated container houses in China is vital for international B2B buyers. By focusing on the key stages of manufacturing and implementing thorough quality control measures, buyers can make informed decisions that lead to successful sourcing outcomes. Being proactive in verifying supplier practices and understanding international standards will further enhance the reliability and quality of the prefabricated container houses purchased.
Practical Sourcing Guide: A Step-by-Step Checklist for ‘prefabricated container house china’
To successfully procure prefabricated container houses from China, international B2B buyers must follow a structured approach to ensure quality, compliance, and value for money. This checklist serves as a practical guide to navigate the complexities of sourcing from overseas manufacturers, especially for buyers from Africa, South America, the Middle East, and Europe.
Step 1: Define Your Technical Specifications
Before reaching out to suppliers, clearly outline your technical requirements. This includes dimensions, materials, insulation standards, and any specific design features you need.
– Why it’s important: A well-defined specification helps prevent misunderstandings and ensures that the final product meets your expectations.
– What to look for: Ensure your specifications align with local building codes and climatic conditions relevant to your project.
Step 2: Conduct Market Research on Suppliers
Research potential suppliers extensively to understand their capabilities and market reputation. Utilize platforms like Alibaba, Made-in-China, or local trade shows to gather information.
– Why it’s important: Understanding the market landscape helps you identify reputable suppliers and avoid potential scams.
– What to look for: Focus on suppliers with verified credentials, strong online presence, and positive reviews from previous customers.
Step 3: Evaluate Potential Suppliers
Before committing, it’s crucial to vet suppliers thoroughly. Request company profiles, case studies, and references from buyers in a similar industry or region.
– Why it’s important: Vetting suppliers mitigates risks and ensures that you partner with reliable manufacturers.
– What to look for: Assess their production capacity, quality control processes, and previous project experiences relevant to prefabricated container houses.
Step 4: Verify Supplier Certifications and Compliance
Ensure that the supplier holds necessary certifications such as ISO 9001 for quality management systems and compliance with international safety standards.
– Why it’s important: Certifications demonstrate a commitment to quality and adherence to industry standards, which is critical for long-term reliability.
– What to look for: Ask for copies of certifications and verify them with issuing bodies if necessary.
Step 5: Request Samples and Conduct Quality Checks
Before placing a large order, request samples of the prefabricated container houses or components. Conduct thorough quality checks to assess materials and craftsmanship.
– Why it’s important: Samples provide a tangible understanding of what to expect and help identify any potential quality issues early.
– What to look for: Evaluate the durability, finish, and functionality of the samples against your specifications.
Step 6: Negotiate Payment Terms and Shipping Arrangements
Discuss payment terms upfront, including deposits, payment methods, and shipping costs. Understand the implications of different shipping options, including lead times and insurance.
– Why it’s important: Clear agreements on payment and shipping prevent disputes and ensure smoother transactions.
– What to look for: Aim for terms that protect your investment while being fair to the supplier, and consider using an escrow service for large payments.
Step 7: Plan for Post-Purchase Support and Warranty
Inquire about after-sales service, warranty terms, and support for installation or maintenance. Ensure that the supplier provides adequate documentation and assistance.
– Why it’s important: Strong after-sales support can save you time and money in the long run, especially if issues arise post-delivery.
– What to look for: A warranty that covers defects and an established process for handling claims or support requests.
By following these steps, international B2B buyers can effectively navigate the procurement process for prefabricated container houses from China, ensuring a successful and satisfactory sourcing experience.
Comprehensive Cost and Pricing Analysis for prefabricated container house china Sourcing
What Are the Key Cost Components in Prefabricated Container House Sourcing from China?
Understanding the cost structure for prefabricated container houses is crucial for B2B buyers, especially in regions like Africa, South America, the Middle East, and Europe. The primary components that contribute to the overall cost include:
-
Materials: The type of materials used—such as steel, insulation, and finishes—significantly affects pricing. Sourcing high-quality materials can increase upfront costs but may lead to savings in maintenance over time.
-
Labor: Labor costs in China can vary based on the region and the complexity of the design. Skilled labor for customization may demand higher wages, impacting the overall budget.
-
Manufacturing Overhead: This encompasses utilities, facilities, and administrative costs associated with production. Efficient manufacturers can minimize overhead, potentially leading to better pricing for buyers.
-
Tooling: For custom designs, tooling costs can be significant. This includes the expenses incurred for molds or specialized equipment required to manufacture specific components.
-
Quality Control (QC): Ensuring that the products meet international standards often requires a robust QC process, which can add to the cost. Investing in quality control can reduce the risk of costly defects and returns.
-
Logistics: Shipping fees, tariffs, and customs duties play a critical role in the total cost. Buyers should consider both the cost and time of logistics when evaluating suppliers.
-
Margin: Finally, the supplier’s profit margin will influence the final price. Buyers should be aware of the typical margins in the industry to negotiate effectively.
How Do Price Influencers Affect the Cost of Prefabricated Container Houses?
Several factors influence the pricing of prefabricated container houses sourced from China:
-
Volume and Minimum Order Quantity (MOQ): Larger orders typically benefit from lower per-unit costs due to economies of scale. Understanding the MOQ is crucial for cost-effective sourcing.
-
Specifications and Customization: Custom designs or specific features can significantly increase costs. Buyers should clarify their needs upfront to avoid unexpected expenses.
-
Material Quality and Certifications: Higher quality materials and certifications (like ISO or CE) may come at a premium but can enhance durability and compliance with international standards.
-
Supplier Factors: The reputation, location, and production capacity of the supplier can also affect pricing. Established suppliers with a good track record may charge more but offer better reliability.
-
Incoterms: The chosen Incoterms (e.g., FOB, CIF) can impact overall costs. Understanding these terms is essential for assessing who bears the costs at different stages of shipping.
What Are the Best Negotiation Strategies for International B2B Buyers?
Negotiating effectively can lead to significant savings for international buyers:
-
Research and Benchmarking: Before entering negotiations, gather data on market prices and competitor offerings to establish a baseline.
-
Build Relationships: Establishing a good rapport with suppliers can lead to better pricing and terms. Long-term relationships often yield more favorable negotiations.
-
Focus on Total Cost of Ownership (TCO): Instead of just looking at the initial price, consider the total cost, including maintenance, logistics, and potential resale value. Suppliers may be willing to negotiate on price if they see long-term value.
-
Be Transparent About Your Needs: Clearly communicate your requirements, including timelines and budget constraints. Suppliers appreciate transparency and may offer tailored solutions.
-
Flexibility in Orders: If possible, show flexibility in order size or timing, as this can lead to better terms from suppliers eager to fill their production schedules.
Conclusion: What Should International Buyers Keep in Mind?
Buyers must approach the sourcing of prefabricated container houses with a comprehensive understanding of the cost structure and the various factors influencing pricing. While indicative prices may serve as a guide, it is vital to conduct thorough due diligence, including site visits and supplier evaluations, to ensure the best outcomes. By leveraging negotiation strategies and focusing on the total cost of ownership, international buyers can optimize their investments in prefabricated container houses sourced from China.
Alternatives Analysis: Comparing prefabricated container house china With Other Solutions
Understanding Alternatives to Prefabricated Container Houses from China
When considering the procurement of prefabricated container houses from China, international B2B buyers should evaluate alternative solutions that may better suit their specific needs. These alternatives can vary in terms of performance, cost, and implementation, impacting overall project feasibility. Below, we provide a detailed comparison of prefabricated container houses with two viable alternatives: modular buildings and traditional construction methods.
Comparison Aspect | Prefabricated Container House China | Modular Building | Traditional Construction |
---|---|---|---|
Performance | High structural integrity; quick setup; suitable for various climates | Flexible designs; energy-efficient; can be built off-site | Customizable; strong durability; longer lifespan |
Cost | Generally lower upfront costs; shipping fees can vary | Moderate initial investment; potential for higher long-term savings | Higher initial costs; labor-intensive; lengthy timelines |
Ease of Implementation | Quick assembly; minimal site preparation needed | Faster than traditional; may require specialized contractors | Time-consuming; extensive planning and permits |
Maintenance | Low maintenance; resistant to weather damage | Moderate maintenance; depends on materials used | High maintenance; depends on materials and design |
Best Use Case | Ideal for temporary housing and remote sites | Suitable for permanent or semi-permanent structures | Best for long-term, custom projects like commercial buildings |
What Are the Pros and Cons of Modular Buildings?
Modular buildings are constructed in sections off-site and then transported for assembly on-site. One significant advantage is their flexibility; they can be designed to meet specific needs and can incorporate energy-efficient technologies that reduce long-term operational costs. However, modular buildings may require specialized contractors for assembly and may not be as cost-effective in regions where skilled labor is scarce.
How Does Traditional Construction Compare?
Traditional construction methods involve on-site building from the ground up. This approach allows for a high degree of customization, enabling buyers to create unique designs tailored to specific requirements. However, the downsides include higher initial costs and extended timelines due to the complexity of the process. Additionally, traditional construction can be more susceptible to weather delays and requires substantial project management.
Making the Right Choice for Your B2B Needs
Choosing the right solution for your construction project involves evaluating your specific needs, budget constraints, and the intended use of the building. Prefabricated container houses from China can be an excellent choice for quick deployment and lower costs, particularly for temporary or remote applications. However, for projects requiring customization and longevity, modular buildings or traditional construction methods may provide better long-term value.
In conclusion, B2B buyers should consider not just the initial costs but also the total cost of ownership, including maintenance and operational efficiency, before making a final decision. Analyzing these alternatives in the context of specific project requirements will ensure a well-informed procurement strategy that aligns with business objectives.
Essential Technical Properties and Trade Terminology for prefabricated container house china
What Are the Key Technical Properties of Prefabricated Container Houses from China?
When considering the purchase of prefabricated container houses from China, understanding the technical properties is crucial for ensuring quality and suitability for specific applications. Here are some essential specifications to consider:
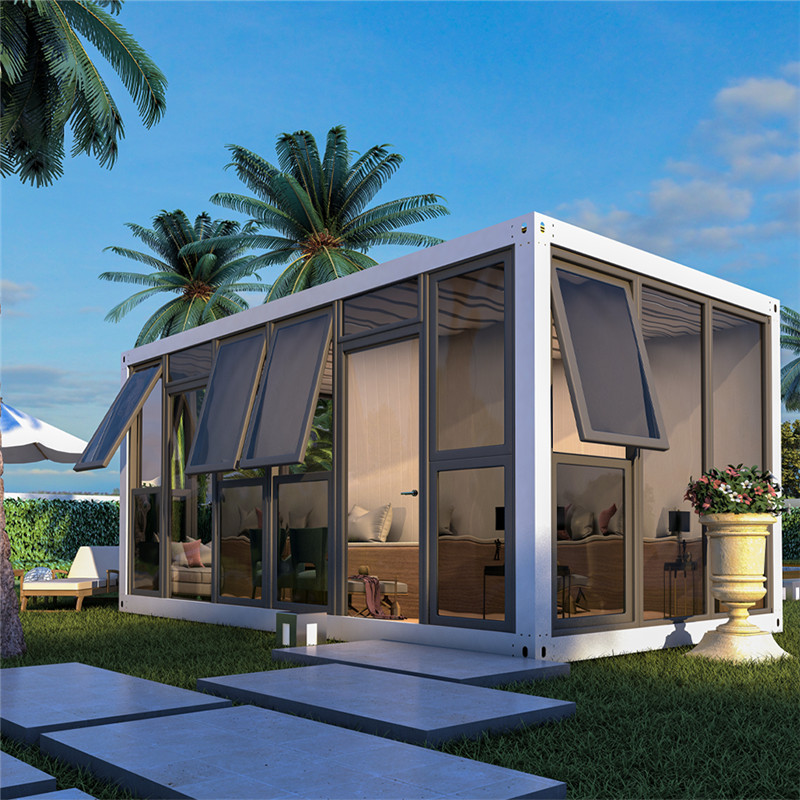
A stock image related to prefabricated container house china.
-
Material Grade
– Definition: The material grade refers to the quality and type of materials used in the construction of the container house, typically including steel, insulation, and cladding.
– Importance: Higher material grades ensure durability, resistance to corrosion, and better insulation properties, which are vital for maintaining the structural integrity and energy efficiency of the house, especially in extreme weather conditions. -
Dimensions and Tolerances
– Definition: Dimensions refer to the physical size of the container house, while tolerances indicate the allowable variations in these dimensions during manufacturing.
– Importance: Accurate dimensions and minimal tolerances are essential for ensuring that the container house fits into the intended space and meets local building codes. This is particularly important for B2B buyers who may need to integrate these structures into larger projects. -
Load-Bearing Capacity
– Definition: This property indicates the maximum weight that the structure can support without compromising safety.
– Importance: Understanding the load-bearing capacity is critical for applications in areas with heavy snow or other loads. It ensures that the container house can withstand environmental stresses, making it a key consideration for buyers in various regions. -
Thermal Performance
– Definition: This refers to the ability of the container house to maintain a stable internal temperature, influenced by the insulation materials used.
– Importance: Good thermal performance can significantly reduce energy costs and improve comfort for occupants. For buyers in hot or cold climates, this property is especially relevant. -
Fire Resistance Rating
– Definition: This rating assesses how well materials used in the container house can withstand fire.
– Importance: A high fire resistance rating is essential for compliance with safety regulations and for the protection of occupants. B2B buyers must ensure that the products they purchase meet local safety standards.
What Are Common Trade Terms Used in the Container House Industry?
Understanding trade terminology is equally important for international buyers to navigate the procurement process effectively. Here are some common terms:
-
OEM (Original Equipment Manufacturer)
– Definition: This term refers to a company that produces parts or equipment that may be marketed by another manufacturer.
– Usage: Buyers often work with OEMs to customize prefabricated container houses to their specifications, ensuring that the final product meets their unique needs. -
MOQ (Minimum Order Quantity)
– Definition: MOQ is the smallest quantity of a product that a supplier is willing to sell.
– Usage: Understanding MOQ is critical for B2B buyers to avoid over-committing to large orders that may not be necessary. It helps in budgeting and inventory management. -
RFQ (Request for Quotation)
– Definition: An RFQ is a document that a buyer sends to suppliers to request pricing and terms for specific products.
– Usage: Utilizing RFQs allows buyers to compare prices and terms from multiple suppliers, ensuring they secure the best deal. -
Incoterms (International Commercial Terms)
– Definition: Incoterms are a set of international rules that define the responsibilities of sellers and buyers regarding the delivery of goods.
– Usage: Familiarity with Incoterms helps buyers understand shipping costs, risk transfer, and delivery obligations, which are vital for effective international trade. -
Lead Time
– Definition: This refers to the time it takes from placing an order to the delivery of the product.
– Usage: Knowing the lead time helps buyers plan their projects more effectively and manage expectations regarding delivery schedules.
By grasping these technical properties and trade terms, B2B buyers can make more informed decisions when sourcing prefabricated container houses from China, ultimately leading to better investment outcomes.
Navigating Market Dynamics and Sourcing Trends in the prefabricated container house china Sector
What Are the Current Market Dynamics and Sourcing Trends in the Prefabricated Container House Sector?
The prefabricated container house market is experiencing significant growth, fueled by a combination of urbanization, housing shortages, and sustainability initiatives. As international B2B buyers from regions like Africa, South America, the Middle East, and Europe seek cost-effective and efficient housing solutions, the demand for prefabricated container homes is on the rise. Key drivers include the need for rapid deployment in disaster recovery scenarios and the growing preference for modular construction techniques, which allow for flexibility in design and reduced construction time.
Emerging trends in sourcing include the adoption of advanced technologies such as Building Information Modeling (BIM) and 3D printing, which streamline the design and manufacturing processes. International buyers are increasingly looking for suppliers that leverage these technologies to enhance precision and reduce waste. Moreover, the rise of e-commerce platforms has transformed how B2B transactions occur, enabling buyers to access a broader range of suppliers and products from China, often with enhanced transparency and competitive pricing.
Another significant trend is the shift towards customization. Buyers now expect more personalized options that cater to local needs and preferences, which drives manufacturers to offer a wider variety of designs and configurations. As a result, international B2B buyers must stay attuned to these market dynamics to ensure they partner with the right suppliers who can meet their specific requirements.
How Is Sustainability Influencing Sourcing Decisions in the Prefabricated Container House Sector?
Sustainability has become a cornerstone of sourcing strategies in the prefabricated container house sector. Environmental concerns regarding traditional construction methods have prompted buyers to prioritize suppliers who demonstrate a commitment to sustainable practices. This includes the use of eco-friendly materials, energy-efficient designs, and waste-reducing manufacturing processes.
Ethical sourcing is equally important, as international buyers are increasingly scrutinizing supply chains for transparency and fairness. Certifications such as ISO 14001 for environmental management and LEED (Leadership in Energy and Environmental Design) for sustainable building practices are becoming critical criteria for selecting suppliers. These certifications not only assure buyers of the environmental integrity of their purchases but also align with the growing consumer demand for sustainability in housing.
Moreover, the adoption of ‘green’ materials, such as recycled steel and low-VOC (volatile organic compounds) paints, is gaining traction. Buyers are encouraged to engage with suppliers who can provide documentation and proof of sustainable practices, ensuring that their investments contribute positively to environmental and social outcomes.
What Is the Historical Context of Prefabricated Container Houses?
The concept of prefabricated construction dates back to the early 20th century, but the use of shipping containers as building materials gained traction in the 1990s. Initially popularized by architects and designers looking for innovative solutions to housing shortages, container homes have evolved into a viable alternative for both residential and commercial applications.
In recent years, the globalization of manufacturing and advancements in technology have made it easier for suppliers in China to produce high-quality prefabricated container houses at competitive prices. This evolution has enabled international B2B buyers to access a diverse range of options, making container homes an increasingly attractive solution for various markets worldwide. As the industry continues to mature, the focus on sustainability and ethical sourcing will likely shape its future, presenting opportunities and challenges for global buyers.
Frequently Asked Questions (FAQs) for B2B Buyers of prefabricated container house china
-
How do I ensure the quality of prefabricated container houses from China?
To ensure the quality of prefabricated container houses from China, it’s crucial to conduct thorough supplier vetting. Request samples and detailed specifications before placing a bulk order. Consider visiting the manufacturing facility or hiring a third-party inspection service to evaluate the production process. Additionally, check for certifications such as ISO or CE, which indicate compliance with international quality standards. Establishing clear quality assurance protocols and communication channels will further mitigate risks. -
What are the most common customization options available for prefabricated container houses?
Common customization options for prefabricated container houses include size adjustments, layout configurations, and interior finishes. Buyers can also choose specific features like insulation, electrical wiring, plumbing systems, and exterior cladding materials. It’s advisable to discuss customization options with the supplier early in the procurement process to understand any implications on cost and lead time. Clear documentation of customization requests will help avoid misunderstandings during production. -
What is the minimum order quantity (MOQ) for prefabricated container houses from China?
The minimum order quantity (MOQ) for prefabricated container houses can vary significantly among suppliers, generally ranging from one unit to several dozen. Factors influencing MOQ include the supplier’s production capacity, the complexity of the design, and material availability. When negotiating with suppliers, clarify the MOQ upfront and explore whether they offer flexibility for smaller orders. This is particularly important for buyers in regions with fluctuating demand. -
What payment terms should I expect when sourcing from Chinese suppliers?
Payment terms can vary, but common arrangements include a 30% deposit upfront and the remaining 70% before shipment. Some suppliers may offer more favorable terms for larger orders or long-term contracts. It’s important to discuss payment options, including letters of credit or escrow services, to mitigate risks associated with international transactions. Always ensure that the payment terms are documented in the contract to protect both parties. -
How can I navigate logistics and shipping when importing container houses from China?
Navigating logistics and shipping involves selecting a reliable freight forwarder familiar with international regulations. Ensure that you understand the Incoterms (International Commercial Terms) used in your contract, as these dictate responsibilities for shipping, insurance, and tariffs. It’s advisable to prepare all necessary documentation, including customs declarations and import permits, well in advance to avoid delays. Consider the shipping method (sea, air, or land) based on urgency and budget constraints. -
What are the key factors to consider when selecting a supplier for prefabricated container houses?
Key factors to consider when selecting a supplier include their industry experience, production capabilities, and customer reviews. Evaluate their portfolio to assess the quality and variety of their products. Additionally, consider their responsiveness and communication style, as these aspects will impact your overall experience. Request references from previous clients and verify their compliance with international standards to ensure reliability. -
How do I address potential cultural and language barriers when dealing with Chinese suppliers?
To address cultural and language barriers, consider employing a bilingual intermediary or translator who understands both the local context and business etiquette. Familiarize yourself with Chinese business culture, which often values relationships and trust. Clear communication is essential; thus, use simple language and confirm understanding by summarizing key points. Establishing a good rapport can enhance collaboration and lead to better negotiation outcomes. -
What are the potential challenges of sourcing prefabricated container houses from China?
Potential challenges include quality control issues, cultural misunderstandings, and fluctuating costs due to currency exchange rates. Additionally, navigating the complexities of international shipping and customs can pose risks. To mitigate these challenges, conduct thorough research on suppliers, engage in regular communication, and consider establishing a local presence or partnership in China. Being proactive in addressing these issues can lead to smoother transactions and successful project outcomes.
Important Disclaimer & Terms of Use
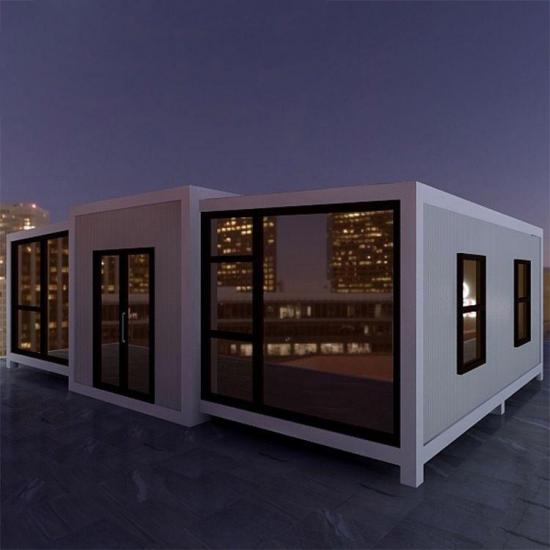
A stock image related to prefabricated container house china.
⚠️ Important Disclaimer
The information provided in this guide, including content regarding manufacturers, technical specifications, and market analysis, is for informational and educational purposes only. It does not constitute professional procurement advice, financial advice, or legal advice.
While we have made every effort to ensure the accuracy and timeliness of the information, we are not responsible for any errors, omissions, or outdated information. Market conditions, company details, and technical standards are subject to change.
B2B buyers must conduct their own independent and thorough due diligence before making any purchasing decisions. This includes contacting suppliers directly, verifying certifications, requesting samples, and seeking professional consultation. The risk of relying on any information in this guide is borne solely by the reader.
Strategic Sourcing Conclusion and Outlook for prefabricated container house china
In navigating the landscape of prefabricated container houses from China, international B2B buyers must prioritize strategic sourcing to harness the full potential of this innovative housing solution. The key takeaways from this guide highlight the importance of understanding local regulations, assessing supplier reliability, and evaluating the long-term value of modular construction. By leveraging these insights, buyers can secure cost-effective, sustainable housing options that meet their specific needs.
How can international buyers benefit from strategic sourcing in prefabricated container houses? The ability to engage with reputable suppliers not only ensures quality but also fosters partnerships that can lead to more resilient supply chains. Furthermore, as demand for affordable housing increases globally, particularly in regions like Africa, South America, the Middle East, and Europe, now is the opportune time to invest in these versatile structures.
Looking ahead, it is crucial for B2B buyers to stay informed about industry trends and technological advancements. Embrace the future of construction by exploring the vast opportunities that prefabricated container houses offer. Take the next step in your sourcing journey and capitalize on the benefits of this growing market.