The Ultimate Guide to Press Machine Manufacturer (2025)
Introduction: Navigating the Global Market for press machine manufacturer
Navigating the global market for press machine manufacturers can be a daunting task for international B2B buyers, particularly those from regions like Africa, South America, the Middle East, and Europe. The challenge lies not only in identifying reputable suppliers but also in understanding the diverse applications and specifications of press machines that best meet industry needs. This guide aims to demystify the complexities of sourcing press machines, offering insights into various types, their applications across different sectors, and the critical factors for supplier vetting.
In today’s competitive landscape, making informed purchasing decisions is paramount. This comprehensive resource will equip you with essential knowledge regarding the latest trends in press machine technology, pricing structures, and the most effective ways to negotiate with suppliers. Whether you are looking for hydraulic presses, mechanical presses, or specialized models, understanding their functionalities and applications will enable you to select the right equipment for your operations.
Additionally, we will explore how geographical considerations and regulatory requirements in different regions, such as Saudi Arabia and France, can impact your sourcing strategy. By leveraging this guide, B2B buyers will gain valuable insights that empower them to navigate the global market confidently, ensuring that they secure the best machinery for their production needs while optimizing costs and enhancing operational efficiency.
Understanding press machine manufacturer Types and Variations
Type Name | Key Distinguishing Features | Primary B2B Applications | Brief Pros & Cons for Buyers |
---|---|---|---|
Mechanical Press Machines | Utilize mechanical linkages for high force; often used for mass production. | Metal forming, stamping, and cutting | Pros: High speed, cost-effective for large volumes. Cons: Limited flexibility for small runs. |
Hydraulic Press Machines | Operate using hydraulic fluid pressure; versatile for various materials. | Forging, molding, and assembly tasks | Pros: Greater force control, suitable for diverse applications. Cons: Typically higher maintenance costs. |
Pneumatic Press Machines | Use compressed air for operation; ideal for lighter materials. | Plastic forming, packaging, and assembly | Pros: Faster cycle times, lower energy consumption. Cons: Limited force compared to hydraulic presses. |
Servo Press Machines | Feature electric motors for precise control and energy efficiency. | Automotive, electronics, and medical device manufacturing | Pros: High precision, programmable, energy-efficient. Cons: Higher initial investment. |
C-Frame Press Machines | Compact design with a C-shaped frame; suitable for smaller production spaces. | Small-scale metal forming and assembly | Pros: Space-efficient, easy to operate. Cons: Limited capacity for larger components. |
What Are the Characteristics of Mechanical Press Machines?
Mechanical press machines are characterized by their use of mechanical linkages that translate rotational motion into linear force. This design makes them particularly effective for high-speed operations, making them ideal for mass production applications such as metal stamping and cutting. When considering a mechanical press, B2B buyers should evaluate their production volume needs, as these machines are most cost-effective for large runs. However, their rigidity can limit flexibility for smaller or varied production tasks.
How Do Hydraulic Press Machines Differ from Other Types?
Hydraulic press machines stand out due to their reliance on hydraulic fluid to generate pressure, allowing for a more versatile application across different materials. These machines excel in tasks like forging, molding, and assembly, where precise force control is essential. B2B buyers should consider the hydraulic press’s maintenance requirements, as they can be higher than mechanical presses. However, the ability to handle a wide range of materials and thicknesses makes them a suitable choice for industries requiring versatility.
What Are the Advantages of Pneumatic Press Machines?
Pneumatic press machines operate using compressed air, making them ideal for lighter materials and applications such as plastic forming and packaging. Their key advantage lies in their faster cycle times and lower energy consumption, which can lead to cost savings in high-volume environments. B2B buyers should keep in mind the limitations in force compared to hydraulic presses, as this can restrict their use in heavy-duty applications. However, for tasks requiring speed and efficiency, pneumatic presses can be an excellent fit.
Why Choose Servo Press Machines for Precision Tasks?
Servo press machines utilize electric motors for precise control over the pressing process. This technology allows for programmable operations, making them suitable for industries such as automotive and electronics, where high precision is critical. While the initial investment is generally higher than that of traditional presses, the energy efficiency and low maintenance needs can result in long-term savings. B2B buyers should assess their need for precision and flexibility against budget constraints when considering servo presses.
What Makes C-Frame Press Machines Ideal for Small Production Spaces?
C-frame press machines feature a compact design that makes them suitable for smaller production environments. Their C-shaped frame provides easy access for operators, making them user-friendly for small-scale metal forming and assembly tasks. While they excel in space efficiency, buyers should consider the limitations in capacity for larger components. For businesses with limited floor space or those just starting in metalworking, C-frame presses can provide an effective solution without compromising on quality.
Related Video: Sapphire 6-in-1 Heat Press Machine Tutorial – How to use Sapphire 6-in-1 Heat Press Machine
Key Industrial Applications of press machine manufacturer
Industry/Sector | Specific Application of press machine manufacturer | Value/Benefit for the Business | Key Sourcing Considerations for this Application |
---|---|---|---|
Automotive Manufacturing | Stamping and forming of vehicle components | Increased production efficiency and reduced waste | Supplier reliability, machine versatility, and local support |
Electronics | Precision metal stamping for circuit boards and enclosures | High accuracy and reduced production costs | Compliance with international standards and rapid delivery |
Aerospace | Fabrication of aircraft parts through deep drawing processes | Enhanced safety and weight reduction | Certification requirements and material specifications |
Construction | Production of metal frames and structural components | Improved structural integrity and reduced labor costs | Local sourcing capabilities and after-sales support |
Packaging | Creation of custom packaging solutions through die-cutting | Increased packaging efficiency and reduced material costs | Customization options and eco-friendly material sourcing |
How Are Press Machines Used in Automotive Manufacturing?
In the automotive sector, press machines are essential for stamping and forming various vehicle components, such as body panels and brackets. These machines significantly enhance production efficiency by allowing high-volume manufacturing with minimal waste. For international buyers, especially in regions like Africa and South America, sourcing press machines that offer versatility and reliability is crucial. Considerations should include the supplier’s track record, the machine’s adaptability to different materials, and the availability of local technical support.
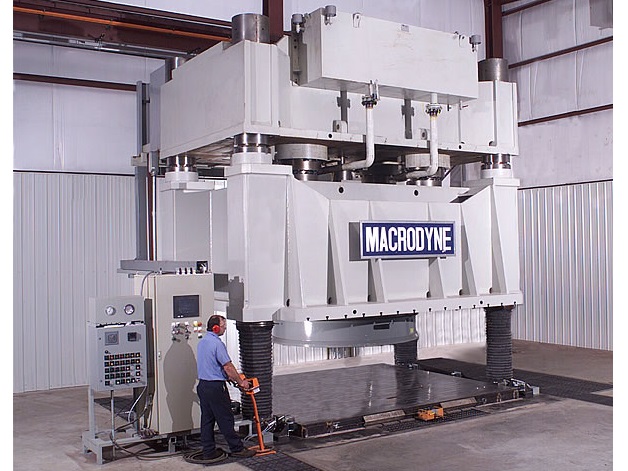
A stock image related to press machine manufacturer.
What Role Do Press Machines Play in Electronics Manufacturing?
Press machines are utilized in the electronics industry for precision metal stamping, crucial for producing circuit boards and enclosures. This application demands high accuracy to ensure the functionality of electronic devices while also reducing production costs. International buyers from Europe and the Middle East must prioritize suppliers that adhere to stringent quality standards and can deliver machines capable of rapid production cycles. Additionally, understanding the machine’s compliance with international regulations is vital for seamless operations.
How Are Press Machines Beneficial in Aerospace Manufacturing?
In the aerospace sector, press machines are employed for the fabrication of aircraft parts through deep drawing processes. This application is critical for enhancing safety and achieving weight reduction in aircraft components. Buyers in regions like Saudi Arabia and Europe should consider the certification requirements that manufacturers must meet, ensuring that the machines can handle specific material specifications and tolerances. Furthermore, the availability of skilled technicians for maintenance and support is an important factor in the sourcing process.
Why Are Press Machines Important in Construction?
Press machines are integral to the construction industry, particularly for producing metal frames and structural components. These machines contribute to improved structural integrity and can significantly reduce labor costs by automating processes. B2B buyers from Africa and South America should focus on sourcing machines that offer robust performance in varying environmental conditions. Additionally, evaluating the supplier’s ability to provide after-sales support and maintenance services can enhance operational efficiency.
How Do Press Machines Enhance Packaging Solutions?
In the packaging industry, press machines are used to create custom packaging solutions through die-cutting. This application not only increases packaging efficiency but also helps in reducing material costs by optimizing the use of resources. International buyers, particularly from Europe and the Middle East, should look for suppliers that offer customization options and eco-friendly material sourcing. Understanding the machine’s capabilities in producing varied packaging designs can lead to better market competitiveness.
3 Common User Pain Points for ‘press machine manufacturer’ & Their Solutions
Scenario 1: Difficulty in Finding the Right Specifications for Press Machines
The Problem: B2B buyers often struggle with selecting the appropriate specifications for press machines that align with their production needs. This challenge can stem from a lack of technical expertise or insufficient knowledge about the specific requirements of their manufacturing processes. For instance, a manufacturer in South America might need a machine that can handle high-density materials but may not be aware of the specific tonnage requirements or types of hydraulic systems that are most effective for their applications. This lack of clarity can lead to poor purchasing decisions, resulting in costly operational inefficiencies and production delays.
The Solution: To tackle this issue, buyers should engage in thorough needs analysis before initiating the procurement process. This involves consulting with production engineers and machine operators to gather insights into the specific material properties and production volumes required. Once the needs are clearly defined, buyers should reach out to multiple press machine manufacturers to request detailed technical specifications and performance data. It’s also beneficial to inquire about custom solutions that can be tailored to unique operational requirements. Additionally, leveraging online resources, such as webinars and technical whitepapers from manufacturers, can provide deeper insights into the specifications that best suit their needs.
Scenario 2: Concerns About After-Sales Support and Maintenance
The Problem: After-sales support and maintenance are critical concerns for B2B buyers, especially for complex machinery like press machines. Buyers from regions such as the Middle East may encounter challenges with limited local support or inadequate training for machine operation and maintenance. This can lead to prolonged downtimes if the machinery malfunctions, affecting production schedules and overall profitability. Furthermore, the fear of high maintenance costs or reliance on international support teams can deter buyers from making a purchase.
The Solution: To mitigate these concerns, buyers should prioritize manufacturers that offer comprehensive after-sales support, including training programs, regular maintenance services, and accessible spare parts. It’s advisable to seek out manufacturers with a proven track record of customer service in the buyer’s region. Buyers should also ask for case studies or testimonials from existing customers to evaluate the effectiveness of the support provided. Establishing a clear communication channel with the manufacturer for ongoing support and training can further enhance operational efficiency. Additionally, consider negotiating service level agreements (SLAs) that define the expected response times and service standards to ensure that support is readily available when needed.
Scenario 3: Navigating Compliance and Regulatory Standards in Different Regions
The Problem: International B2B buyers often face the complex task of ensuring that their press machines comply with various regional regulations and industry standards. For example, a buyer in Europe must navigate stringent environmental regulations and safety standards that may differ significantly from those in Africa or South America. This complexity can lead to delays in the purchasing process and potential fines if machines are not compliant with local laws.
The Solution: Buyers should proactively research and understand the specific compliance requirements for their region before engaging with manufacturers. This includes familiarizing themselves with industry standards such as ISO certifications, CE marking in Europe, or local safety regulations in their respective countries. Engaging with legal advisors or compliance experts can also provide clarity on the necessary standards. When communicating with manufacturers, buyers should explicitly inquire about the compliance certifications of the press machines being offered. Manufacturers should be able to provide documentation proving adherence to applicable regulations. Additionally, establishing a collaborative relationship with the manufacturer can facilitate ongoing compliance checks and adaptations as regulations evolve.
Strategic Material Selection Guide for press machine manufacturer
When selecting materials for press machines, international B2B buyers must consider several factors that directly impact performance, durability, and cost-effectiveness. Below, we analyze four common materials used in the manufacturing of press machines, focusing on their properties, advantages, disadvantages, and specific considerations relevant to international markets.
What Are the Key Properties of Steel in Press Machine Manufacturing?
Steel is one of the most widely used materials in press machine manufacturing due to its excellent mechanical properties. It typically exhibits high tensile strength, good ductility, and resistance to wear and impact. Steel can withstand high temperatures and pressures, making it suitable for various applications.
Pros & Cons:
The primary advantage of steel is its durability and strength, which translates to longer service life and lower maintenance costs. However, it is susceptible to corrosion, especially in humid or chemically aggressive environments, which can lead to increased maintenance needs. Additionally, the manufacturing complexity of steel components can increase costs.
Impact on Application:
Steel is compatible with a wide range of media, including hydraulic fluids and oils, making it versatile for different press machine applications. However, buyers must consider the specific environmental conditions of their operational regions, such as the prevalence of corrosive agents.
Considerations for International Buyers:
For buyers in regions like Africa and the Middle East, where humidity and corrosive environments may be prevalent, selecting corrosion-resistant steel grades (e.g., stainless steel) may be essential. Compliance with international standards such as ASTM and DIN is crucial for ensuring product quality and reliability.
How Does Aluminum Compare as a Material for Press Machines?
Aluminum is increasingly popular in press machine manufacturing due to its lightweight nature and excellent corrosion resistance. It also offers good thermal and electrical conductivity, which can be beneficial in certain applications.
Pros & Cons:
The key advantage of aluminum is its lightweight property, which can lead to reduced energy consumption during operation. However, aluminum has lower tensile strength compared to steel, which may limit its use in high-stress applications. Additionally, it can be more expensive than some steel options, impacting overall project budgets.
Impact on Application:
Aluminum is particularly suitable for applications where weight reduction is critical, such as in automotive and aerospace industries. Its corrosion resistance makes it ideal for environments with high moisture or chemical exposure.
Considerations for International Buyers:
Buyers from Europe, particularly in countries like France, may prefer aluminum for its sustainability benefits, as it is recyclable. Ensuring compliance with European Union regulations regarding material sourcing and recycling can also be a significant factor in the decision-making process.
What Are the Advantages of Using Composite Materials in Press Machines?
Composite materials, often made from a combination of polymers and reinforcing fibers, are gaining traction in the press machine sector due to their unique properties. They can be engineered to provide specific performance characteristics.
Pros & Cons:
The primary advantage of composites is their high strength-to-weight ratio, which allows for lightweight designs without sacrificing performance. However, they can be more expensive to manufacture and may require specialized knowledge for processing. Additionally, their long-term durability in high-temperature applications can be a concern.
Impact on Application:
Composites are particularly effective in applications where weight reduction and corrosion resistance are paramount. They are often used in specialized press machines for the aerospace and automotive industries.
Considerations for International Buyers:
For buyers in South America, where emerging markets are increasingly adopting advanced manufacturing technologies, understanding the specific composite materials available and their certifications is vital. Compliance with local and international standards is essential to ensure safety and performance.
How Does Cast Iron Perform as a Material for Press Machines?
Cast iron is another traditional material used in press machine manufacturing, known for its excellent wear resistance and ability to dampen vibrations.
Pros & Cons:
The key advantage of cast iron is its durability and ability to withstand high loads, making it suitable for heavy-duty applications. However, it is brittle and can fracture under extreme stress, which limits its use in certain scenarios. Additionally, cast iron can be heavy, potentially increasing operational costs.
Impact on Application:
Cast iron is ideal for applications requiring stability and vibration damping, such as in hydraulic presses. However, its weight may pose challenges in mobility and energy consumption.
Considerations for International Buyers:
For buyers in the Middle East, understanding the local manufacturing capabilities and the availability of high-quality cast iron is crucial. Compliance with regional standards for material quality and performance can also influence purchasing decisions.
Summary Table of Material Selection for Press Machines
Material | Typical Use Case for press machine manufacturer | Key Advantage | Key Disadvantage/Limitation | Relative Cost (Low/Med/High) |
---|---|---|---|---|
Steel | Heavy-duty industrial presses | High strength and durability | Susceptible to corrosion | Medium |
Aluminum | Lightweight automotive presses | Lightweight, good corrosion resistance | Lower tensile strength | High |
Composite | Specialized aerospace and automotive presses | High strength-to-weight ratio | Expensive and requires specialized processing | High |
Cast Iron | Hydraulic presses for heavy loads | Excellent wear resistance and stability | Brittle and heavy | Medium |
This guide provides a comprehensive overview of material selection considerations for press machine manufacturers, enabling international B2B buyers to make informed decisions tailored to their specific operational needs and regional requirements.
In-depth Look: Manufacturing Processes and Quality Assurance for press machine manufacturer
What Are the Main Stages of Manufacturing Processes for Press Machines?
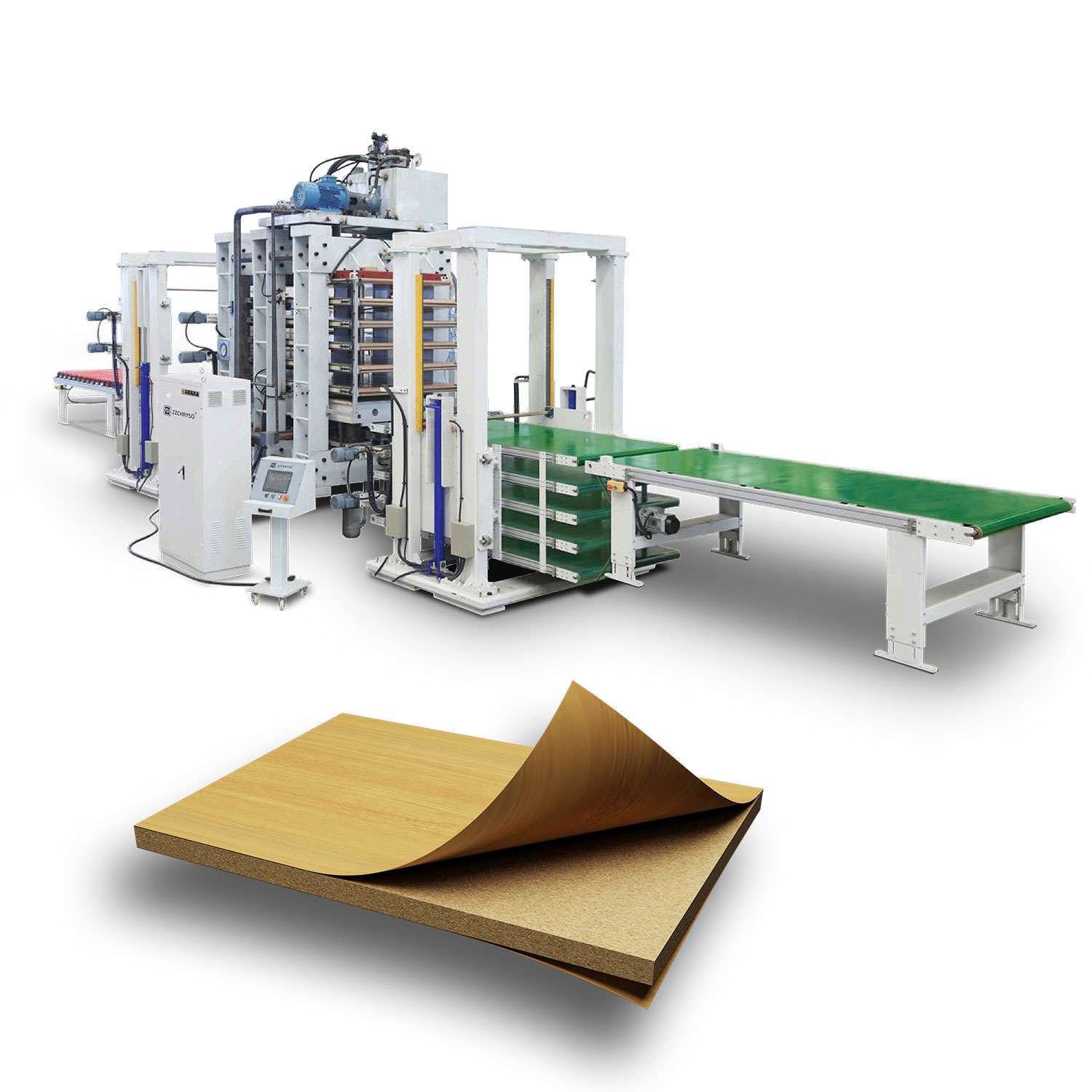
A stock image related to press machine manufacturer.
The manufacturing of press machines involves several critical stages that ensure the equipment meets the required specifications and performance standards. The primary stages include material preparation, forming, assembly, and finishing.
-
Material Preparation: This initial stage involves sourcing high-quality raw materials, such as steel or aluminum, which are essential for the durability and performance of press machines. Suppliers should provide certificates of compliance to verify the quality of materials used.
-
Forming: This stage employs various techniques such as stamping, bending, or deep drawing to shape the raw materials into the desired components. Advanced technologies like Computer Numerical Control (CNC) machining are often utilized for precision in forming operations.
-
Assembly: After forming, the individual components are assembled into the complete press machine. This process requires skilled labor and adherence to precise specifications to ensure that all parts fit together correctly.
-
Finishing: The final stage includes surface treatments, such as painting or coating, to enhance durability and aesthetics. Quality control checks during this stage are crucial to ensure that the finish meets industry standards.
How Do Key Techniques Influence the Quality of Press Machines?
The techniques employed during the manufacturing process significantly affect the overall quality and performance of press machines. Some notable methods include:
- Hydraulic Press Technology: Utilizing hydraulic systems can enhance the machine’s ability to exert consistent pressure, crucial for various applications.
- Electromechanical Systems: These systems provide more precise control over the press operations, reducing the likelihood of errors during production.
- Robotic Automation: Integrating robotics can streamline the assembly process, improving efficiency and reducing labor costs while maintaining high-quality standards.
B2B buyers should inquire about the specific techniques used by manufacturers and their impact on the performance of the press machines.
What Quality Control Standards Should B2B Buyers Be Aware Of?
Quality assurance is paramount in the manufacturing of press machines, particularly when dealing with international suppliers. Familiarity with relevant international standards, such as ISO 9001, is essential for ensuring that manufacturers adhere to quality management systems.
- ISO 9001: This standard outlines the criteria for a quality management system and is recognized globally. It ensures that manufacturers consistently provide products that meet customer and regulatory requirements.
- CE Marking: Particularly important for buyers in Europe, CE marking indicates that the product complies with EU safety, health, and environmental protection standards.
- API Standards: For buyers in sectors like oil and gas, understanding the American Petroleum Institute (API) standards is vital for ensuring that the press machines meet industry-specific requirements.
What Are the Key QC Checkpoints in Press Machine Manufacturing?
Quality control (QC) is integrated into several checkpoints throughout the manufacturing process to ensure that the final product meets the necessary standards. The primary QC checkpoints include:
-
Incoming Quality Control (IQC): This initial checkpoint assesses the quality of raw materials and components upon arrival. Suppliers should provide documentation that confirms the materials meet required specifications.
-
In-Process Quality Control (IPQC): During the manufacturing stages, IPQC is employed to monitor processes and identify any deviations from quality standards. This may involve regular inspections and measurements.
-
Final Quality Control (FQC): Once the press machine is fully assembled, FQC is conducted to evaluate the final product against predefined quality criteria. This includes functional testing and visual inspections.
How Can B2B Buyers Verify Supplier Quality Control?
Verifying the quality control practices of potential suppliers is crucial for international B2B buyers. Here are actionable steps to ensure suppliers maintain high-quality standards:
-
Conduct Audits: Regular audits of the manufacturing facility can provide insights into the supplier’s quality management practices. Buyers can assess the effectiveness of the QC processes and compliance with international standards.
-
Request Quality Reports: Suppliers should provide detailed quality reports that document their QC processes, including results from IQC, IPQC, and FQC. Analyzing these reports can help buyers gauge the reliability of the supplier.
-
Utilize Third-Party Inspections: Engaging third-party inspection services can offer an unbiased assessment of the manufacturing processes and final products. This is particularly beneficial for buyers in regions like Africa and South America, where local standards may differ.
What Are the Quality Control Nuances for International B2B Buyers?
For international B2B buyers, particularly those from diverse regions like Africa, South America, the Middle East, and Europe, understanding the nuances of quality control is essential. Some factors to consider include:
-
Cultural and Regulatory Differences: Buyers should be aware of the varying quality standards and regulations in their regions. Understanding these differences can help facilitate smoother communication and expectations with suppliers.
-
Supply Chain Transparency: Ensuring transparency in the supply chain can aid in maintaining quality. Buyers should establish clear channels of communication with suppliers and request regular updates on production and quality checks.
-
Local Certifications: For regions such as the Middle East and Africa, local certifications may be required for compliance with regional regulations. Buyers should verify that suppliers possess the necessary certifications to operate in their specific markets.
Conclusion: Prioritizing Quality in Press Machine Manufacturing
For international B2B buyers, especially those in Africa, South America, the Middle East, and Europe, understanding the manufacturing processes and quality assurance practices of press machine manufacturers is crucial. By focusing on material preparation, forming techniques, assembly, and finishing stages, alongside robust quality control measures, buyers can ensure they select suppliers that deliver high-quality, reliable machinery. Conducting thorough audits, requesting detailed quality reports, and leveraging third-party inspections can further enhance buyer confidence in their suppliers, ultimately leading to successful procurement outcomes.
Practical Sourcing Guide: A Step-by-Step Checklist for ‘press machine manufacturer’
Introduction
Navigating the procurement process for press machines can be complex, especially for international B2B buyers from regions like Africa, South America, the Middle East, and Europe. This step-by-step checklist is designed to streamline your sourcing efforts, ensuring you find a reliable manufacturer that meets your specific needs. By following these actionable steps, you can make informed decisions that lead to successful partnerships.
Step 1: Define Your Technical Specifications
Before reaching out to suppliers, it’s essential to clearly define your technical requirements. This includes understanding the type of press machine you need, its capacity, power specifications, and any additional features necessary for your production process.
- Consider production volume: Assess how many units you plan to produce to determine the machine’s capacity.
- Identify material compatibility: Ensure the machine can handle the materials you intend to use.
Step 2: Conduct Market Research for Suppliers
Researching potential suppliers is crucial to identify the best manufacturers for your needs. Utilize online databases, industry reports, and trade shows to gather information about press machine manufacturers.
- Look for industry-specific directories: Websites like ThomasNet or Global Sources can provide valuable insights into reputable suppliers.
- Network within industry groups: Engage with peers in your industry to gain recommendations and insights about suppliers they trust.
Step 3: Evaluate Potential Suppliers
Before committing, it’s vital to thoroughly vet potential suppliers. Request detailed company profiles, case studies, and references from buyers in similar industries or regions.
- Check for customer testimonials: Look for reviews and case studies that highlight the supplier’s reliability and product quality.
- Inquire about production capabilities: Ensure they can meet your volume and quality requirements consistently.
Step 4: Verify Certifications and Compliance
Ensure that the manufacturers you are considering comply with relevant industry standards and certifications. This step is critical for ensuring product safety and quality.
- Look for ISO certifications: These indicate a commitment to quality management and consistent production practices.
- Check for regional compliance: Verify that the supplier meets local regulations in your area, especially if you are importing machinery.
Step 5: Request Detailed Quotes
After narrowing down your options, request detailed quotes from your shortlisted suppliers. A comprehensive quote should include pricing, delivery timelines, warranty terms, and after-sales support.
- Compare total costs: Look beyond the initial price to include shipping, customs duties, and installation costs.
- Assess payment terms: Understand the payment options and conditions offered by each supplier.
Step 6: Negotiate Terms and Conditions
Once you receive quotes, it’s time to negotiate terms that work best for both parties. Effective negotiation can lead to better pricing, payment terms, and warranty coverage.
- Be transparent about your budget: This can help suppliers tailor their offers to meet your financial constraints.
- Clarify expectations: Ensure both parties understand the scope of work, delivery schedules, and service commitments.
Step 7: Finalize the Contract and Place Order
After agreeing on terms, draft a formal contract that outlines all agreed-upon aspects. This document should cover specifications, pricing, delivery, and post-sales support.
- Include penalty clauses: These can protect you against delays or failures to meet agreed standards.
- Ensure clarity on intellectual property: If applicable, safeguard your designs and proprietary processes in the contract.
By following these steps, you can efficiently source a press machine manufacturer that aligns with your operational needs and business goals.
Important Disclaimer & Terms of Use
⚠️ Important Disclaimer
The information provided in this guide, including content regarding manufacturers, technical specifications, and market analysis, is for informational and educational purposes only. It does not constitute professional procurement advice, financial advice, or legal advice.
While we have made every effort to ensure the accuracy and timeliness of the information, we are not responsible for any errors, omissions, or outdated information. Market conditions, company details, and technical standards are subject to change.
B2B buyers must conduct their own independent and thorough due diligence before making any purchasing decisions. This includes contacting suppliers directly, verifying certifications, requesting samples, and seeking professional consultation. The risk of relying on any information in this guide is borne solely by the reader.