The Ultimate Guide to Remote Control Manufacturer (2025)
Introduction: Navigating the Global Market for remote control manufacturer
Navigating the global market for remote control manufacturers can be a daunting task for international B2B buyers, particularly when sourcing reliable and innovative solutions for their specific needs. With the increasing demand for automation and smart devices across various industries, identifying the right remote control manufacturer becomes essential for ensuring operational efficiency and competitiveness. This guide provides a comprehensive overview of the remote control manufacturing landscape, covering various types of remote controls, their applications in different sectors, and critical factors to consider when vetting suppliers.
Buyers will gain insights into essential elements such as cost structures, quality assurance processes, and the latest technological advancements in remote control systems. By understanding the nuances of the market, including regional trends and regulatory considerations specific to Africa, South America, the Middle East, and Europe—especially in countries like Poland and the UK—B2B buyers can make informed purchasing decisions that align with their business objectives.
This guide aims to empower you with actionable insights and strategic advice, enabling you to confidently navigate the complexities of sourcing remote control solutions that meet your unique requirements. Whether you are seeking to enhance your product offerings or streamline operations, understanding the global market for remote control manufacturers is key to driving success in your business endeavors.
Understanding remote control manufacturer Types and Variations
Type Name | Key Distinguishing Features | Primary B2B Applications | Brief Pros & Cons for Buyers |
---|---|---|---|
Infrared Remote Controls | Uses infrared light for communication, line-of-sight needed | Consumer electronics, industrial machinery | Pros: Simple to use, low cost. Cons: Limited range, requires direct line of sight. |
RF (Radio Frequency) Remotes | Operates using radio waves, does not require line-of-sight | Home automation, security systems | Pros: Greater range, can penetrate obstacles. Cons: More expensive, potential interference. |
Bluetooth Remote Controls | Connects via Bluetooth technology, often rechargeable | Smart devices, audio systems | Pros: Wireless convenience, supports multiple devices. Cons: Limited range compared to RF, battery dependency. |
Wi-Fi Remote Controls | Utilizes Wi-Fi networks for control, often app-based | Smart home devices, surveillance systems | Pros: Remote access from anywhere, integration with IoT. Cons: Dependent on internet connectivity, setup complexity. |
Custom Remote Solutions | Tailored designs to meet specific client needs | Specialized industrial applications, unique products | Pros: Fully customized, specific functionality. Cons: Higher cost, longer lead times. |
What Are the Key Characteristics of Infrared Remote Controls?
Infrared remote controls are among the most common types used in consumer electronics. They operate by emitting infrared light signals that must be received by the device in direct line of sight. This makes them suitable for applications such as televisions, audio systems, and certain industrial machinery. When considering B2B purchases, buyers should evaluate the simplicity and low cost of these devices against their limitations in range and the need for direct visibility.
How Do RF (Radio Frequency) Remotes Differ in Functionality?
RF remotes utilize radio waves, allowing them to communicate with devices without requiring a direct line of sight. This feature makes them ideal for applications in home automation and security systems. B2B buyers should consider the increased range and ability to penetrate walls, which provide flexibility in device placement. However, they may face higher costs and potential interference from other devices operating on similar frequencies.
What Advantages Do Bluetooth Remote Controls Offer to Businesses?
Bluetooth remote controls connect wirelessly to devices, providing a convenient solution for smart devices and audio systems. They are typically rechargeable and can support multiple devices simultaneously. Businesses should weigh the benefits of wireless convenience and ease of use against the limitations of range and reliance on battery life. This makes them suitable for environments where mobility and ease of access are priorities.
Why Are Wi-Fi Remote Controls Gaining Popularity in B2B Applications?
Wi-Fi remote controls leverage existing Wi-Fi networks to facilitate remote access and control of devices, often through mobile applications. This technology is particularly advantageous for smart home devices and surveillance systems, allowing users to manage devices from anywhere. B2B buyers must consider their reliance on internet connectivity and the potential complexity of setup, but the integration with IoT systems can significantly enhance operational efficiency.
What Should Buyers Know About Custom Remote Solutions?
Custom remote solutions are designed to meet specific client requirements, offering tailored functionality for specialized industrial applications or unique products. These solutions provide the advantage of being fully customized to fit exact needs, making them ideal for niche markets. However, buyers should be prepared for higher costs and longer lead times associated with the design and manufacturing processes. This option is best suited for businesses that require specific features not available in standard remote controls.
Related Video: How to Program Your X1 Remote Control to Your TV and Audio Device
Key Industrial Applications of remote control manufacturer
Industry/Sector | Specific Application of Remote Control Manufacturer | Value/Benefit for the Business | Key Sourcing Considerations for this Application |
---|---|---|---|
Manufacturing | Remote operation of machinery and equipment | Increases efficiency and reduces the risk of workplace injuries | Compliance with safety standards and remote connectivity |
Aerospace | Control of drones and UAVs | Enhances operational capabilities and data collection | Robustness and reliability in extreme conditions |
Construction | Remote monitoring of construction equipment | Optimizes resource allocation and minimizes downtime | Durability and ease of integration with existing systems |
Healthcare | Remote management of medical devices | Improves patient care and operational efficiency | Regulatory compliance and data security measures |
Agriculture | Control of agricultural drones and automated systems | Increases yield and reduces labor costs | Precision technology and compatibility with local systems |
How is Remote Control Technology Used in Manufacturing?
In the manufacturing sector, remote control technology is pivotal for operating machinery and equipment from a distance. This application enhances operational efficiency by allowing operators to manage processes without being physically present, thus reducing the risk of workplace injuries. For international buyers, especially in regions like Africa and South America, sourcing manufacturers that comply with local safety regulations and provide robust remote connectivity options is crucial. Buyers should also consider the adaptability of the technology to various machinery types.
What Role Does Remote Control Play in Aerospace Applications?
In the aerospace industry, remote control systems are essential for the operation of drones and unmanned aerial vehicles (UAVs). These systems allow for enhanced operational capabilities, such as data collection and surveillance, without risking human lives in hazardous environments. For B2B buyers in Europe and the Middle East, it is important to source remote control solutions that are reliable and robust enough to function in extreme weather conditions. Additionally, manufacturers must ensure that their products meet stringent aviation safety standards.
How is Remote Control Technology Transforming Construction?
Remote monitoring of construction equipment through remote control technology is revolutionizing the construction industry. This application allows project managers to optimize resource allocation and minimize equipment downtime, significantly improving project timelines and budgets. Buyers in regions like Europe, particularly Poland and the UK, should prioritize sourcing durable remote control systems that can seamlessly integrate with existing construction technologies. Understanding local regulations regarding equipment monitoring and safety is also essential.
In What Ways Does Remote Control Benefit Healthcare?
Remote management of medical devices through remote control technology is transforming healthcare delivery. This application enables healthcare providers to monitor patient conditions and device performance in real-time, improving patient care and operational efficiency. For international buyers, especially in Africa and South America, sourcing manufacturers that adhere to local regulatory compliance and data security measures is vital. The ability to integrate these systems with existing healthcare infrastructure can also enhance their effectiveness.
How is Remote Control Technology Enhancing Agriculture?
In the agriculture sector, remote control technology is used to operate drones and automated systems for tasks such as crop monitoring and precision farming. This application increases yield while reducing labor costs, making it essential for modern agricultural practices. Buyers from the Middle East and Europe should look for remote control solutions that incorporate precision technology and are compatible with local agricultural systems. Understanding the technological landscape and regulatory environment in their respective regions will also facilitate better sourcing decisions.
Related Video: Robotics applications by Universal Robots – Easy Automation with Collaborative Robots [ 2020 ]
3 Common User Pain Points for ‘remote control manufacturer’ & Their Solutions
Scenario 1: Challenges with Compatibility and Integration of Remote Controls
The Problem:
International B2B buyers often face compatibility issues when sourcing remote controls for various devices. For example, a company in the Middle East might need remote controls that can seamlessly integrate with multiple brands of televisions and sound systems. However, the lack of standardization in protocols and interfaces can lead to frustrations when trying to get the devices to work together. This issue can cause delays in product launches and increased costs due to the need for additional adapters or software solutions.
The Solution:
To overcome compatibility challenges, B2B buyers should prioritize working with manufacturers who offer customizable remote control solutions. When sourcing, ask manufacturers for detailed specifications about the compatibility of their products with existing systems. It’s beneficial to engage in discussions about the protocols they support, such as IR, RF, or Bluetooth. Additionally, buyers should request sample units for testing in their specific environment before making bulk purchases. This proactive approach can save time and ensure that the remote controls function correctly across various devices, thereby streamlining operations.
Scenario 2: Insufficient Technical Support and After-Sales Service
The Problem:
Another common pain point for B2B buyers is the lack of adequate technical support and after-sales service from remote control manufacturers. For instance, a company in South America might find themselves struggling to troubleshoot connectivity issues or software updates due to insufficient guidance from the manufacturer. Without timely support, companies can experience operational downtimes, affecting productivity and customer satisfaction.
The Solution:
To mitigate this issue, buyers should thoroughly evaluate the level of support offered by remote control manufacturers during the sourcing process. Inquire about the availability of dedicated technical support teams, response times, and whether they provide on-site assistance if needed. It’s also wise to assess whether the manufacturer has comprehensive documentation and training resources, such as user manuals and video tutorials. Establishing a clear communication line with the manufacturer prior to purchase can facilitate a smoother relationship and ensure that any post-purchase issues are addressed promptly.
Scenario 3: High Costs Associated with Custom Remote Control Solutions
The Problem:
B2B buyers often grapple with the high costs associated with custom remote control solutions. A European company may require specialized remote controls tailored for unique applications, such as industrial machinery or smart home systems. However, the expense of developing these custom solutions can be prohibitive, leading to budget constraints and potentially limiting innovation.
The Solution:
To manage costs while still obtaining high-quality custom solutions, buyers should consider collaborating with manufacturers who have a proven track record of producing cost-effective tailored products. Look for manufacturers who offer modular designs, allowing businesses to build upon existing models instead of starting from scratch. Additionally, negotiating bulk purchase agreements can lead to significant discounts. Buyers should also explore the possibility of phased implementation, where they can roll out custom solutions in stages, spreading costs over time while still benefiting from the enhancements that custom remote controls provide.
Strategic Material Selection Guide for remote control manufacturer
What are the Common Materials Used in Remote Control Manufacturing?
When selecting materials for remote control manufacturing, it is essential to consider various factors such as durability, cost, and application suitability. Below, we analyze four common materials used in the industry, focusing on their properties, advantages, disadvantages, and implications for international buyers.
How Does ABS Plastic Perform in Remote Control Applications?
Acrylonitrile Butadiene Styrene (ABS) plastic is widely used in remote control housings due to its excellent impact resistance and ease of manufacturing.
- Key Properties: ABS has a high-temperature rating, typically around 80°C, and is resistant to many chemicals, making it suitable for various environments.
- Pros & Cons: The material is lightweight and cost-effective, but it may not withstand extreme temperatures or UV exposure over time. Manufacturing complexity is low, allowing for efficient production.
- Impact on Application: ABS is compatible with electronic components, providing adequate insulation and protection against moisture.
- Considerations for International Buyers: Buyers should ensure compliance with international standards such as ASTM D6100 for plastics. In regions like Europe and the Middle East, environmental regulations may necessitate the use of recyclable materials.
What Role Does Polycarbonate Play in Remote Control Manufacturing?
Polycarbonate is another popular choice, especially for applications requiring high strength and transparency.
- Key Properties: With a temperature rating of up to 120°C and excellent impact resistance, polycarbonate is ideal for rugged environments.
- Pros & Cons: While it offers superior durability and clarity, polycarbonate can be more expensive than ABS and may require specialized manufacturing techniques.
- Impact on Application: Its high resistance to impact makes it suitable for remote controls used in industrial settings or outdoor environments.
- Considerations for International Buyers: Buyers should be aware of compliance with standards like ISO 7391 for safety and performance. In regions with high UV exposure, UV-resistant grades of polycarbonate may be necessary.
How Does Metal Influence the Design of Remote Controls?
Metals, such as aluminum and zinc alloys, are often used for structural components in remote controls.
- Key Properties: Metals offer excellent strength and thermal conductivity, with aluminum having a melting point of around 660°C.
- Pros & Cons: While metals provide durability and a premium feel, they can increase the overall weight and cost of the product. Manufacturing processes may also be more complex, requiring machining or die-casting.
- Impact on Application: Metal components can enhance the performance of remote controls by providing better shielding against electromagnetic interference.
- Considerations for International Buyers: Compliance with materials standards like ASTM B209 for aluminum is crucial. Buyers should also consider the impact of tariffs and import regulations in their regions.
What Are the Benefits of Using Silicone in Remote Control Manufacturing?
Silicone is commonly used for keypads and seals in remote controls due to its flexibility and resilience.
- Key Properties: Silicone can operate effectively in temperatures ranging from -50°C to 200°C and is resistant to moisture and UV radiation.
- Pros & Cons: It provides excellent tactile feedback and durability but can be more expensive than traditional plastics. The manufacturing process may involve more intricate molding techniques.
- Impact on Application: Silicone is ideal for waterproofing and enhancing user experience through its soft-touch properties.
- Considerations for International Buyers: Buyers should ensure compliance with FDA regulations if the product is intended for consumer use. Additionally, understanding local market preferences for tactile materials can influence purchasing decisions.
Summary Table of Material Selection for Remote Control Manufacturing
Material | Typical Use Case for remote control manufacturer | Key Advantage | Key Disadvantage/Limitation | Relative Cost (Low/Med/High) |
---|---|---|---|---|
ABS Plastic | Housing and structural components | Lightweight and cost-effective | Limited UV and temperature resistance | Low |
Polycarbonate | Durable housings and transparent components | High impact resistance and clarity | Higher cost and manufacturing complexity | Medium |
Metal | Structural components and shielding | Excellent strength and conductivity | Increased weight and cost | High |
Silicone | Keypads and seals | Flexibility and moisture resistance | Higher cost and complex molding | Medium |
This strategic material selection guide provides valuable insights for international B2B buyers, enabling informed decisions that align with compliance and market demands across diverse regions.
In-depth Look: Manufacturing Processes and Quality Assurance for remote control manufacturer
What Are the Main Stages of Manufacturing Remote Controls?
Manufacturing remote controls involves several critical stages, each essential for ensuring the final product meets quality and functionality standards. Understanding these stages can empower B2B buyers to make informed decisions when selecting suppliers.
1. Material Preparation: What Materials Are Used in Remote Control Manufacturing?
The manufacturing process begins with the preparation of raw materials. Common materials include plastics for the casing, metals for internal components, and rubber for buttons. Suppliers often source these materials based on durability, cost-effectiveness, and compliance with international safety standards. Buyers should inquire about the origin of materials and any certifications that guarantee their quality, especially when sourcing from regions with varying manufacturing standards.
2. Forming: How Are Remote Control Components Shaped?
Once materials are prepared, the next step is forming, which involves shaping the materials into usable components. Techniques such as injection molding are prevalent for creating plastic casings, while stamping or machining may be used for metal parts. The choice of forming technique impacts both the precision of the components and the overall production cost. B2B buyers should assess the technology employed by manufacturers to ensure it aligns with their quality expectations.
3. Assembly: What Assembly Techniques Are Commonly Used?
After forming, the assembly stage combines all components into a final product. This may involve manual assembly or automated processes, depending on the scale of production. Techniques such as surface mount technology (SMT) for circuit boards and ultrasonic welding for casing are common. Buyers should consider the manufacturer‘s assembly capabilities and workforce expertise, as these factors significantly influence the reliability and performance of the remote controls.
4. Finishing: How Is the Final Product Prepared for Market?
The finishing stage enhances the aesthetic and functional qualities of the remote controls. This includes processes such as painting, coating, and applying labels or decals. Quality in this stage is crucial as it affects the user experience. B2B buyers should examine how manufacturers ensure consistent quality in finishing, including any processes for testing durability and wear resistance.
What Quality Assurance Standards Should B2B Buyers Be Aware Of?
Quality assurance (QA) is paramount in remote control manufacturing, ensuring that products are reliable and meet customer expectations. Familiarity with relevant international standards can help buyers make informed supplier choices.
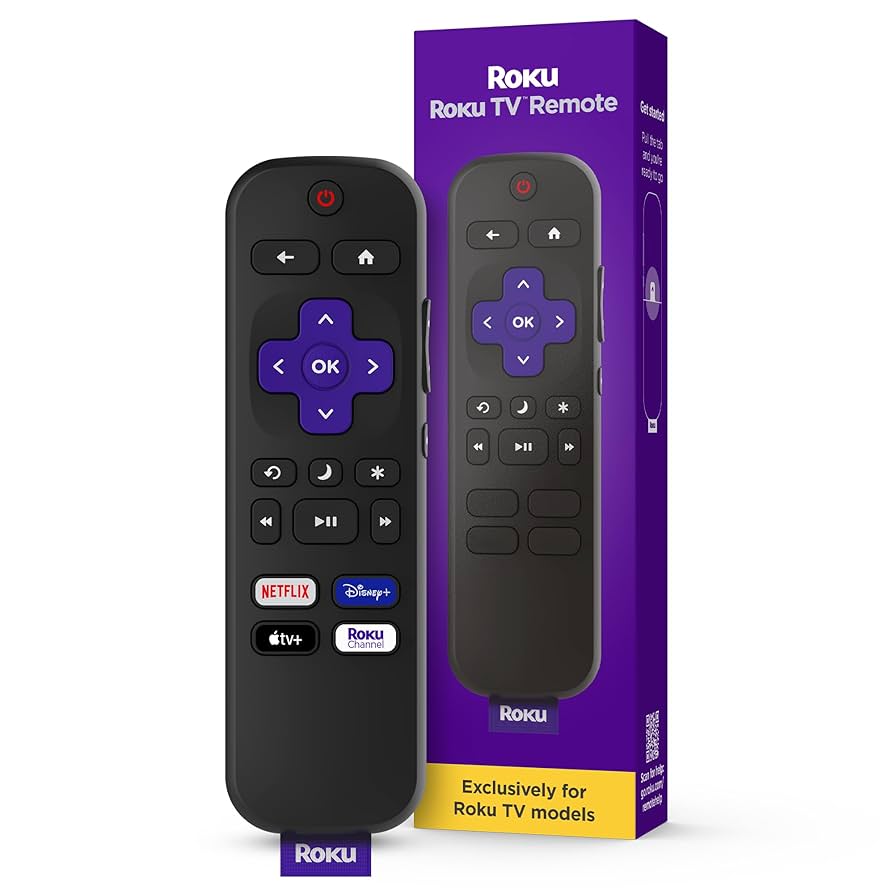
A stock image related to remote control manufacturer.
1. What Are the International Quality Standards for Remote Controls?
One of the primary international standards is ISO 9001, which outlines requirements for a quality management system (QMS). Compliance with this standard indicates that a manufacturer follows systematic processes aimed at enhancing customer satisfaction. Additionally, industry-specific standards such as CE marking for products sold in Europe and API standards for electronic devices may apply. Buyers should verify that their suppliers are compliant with these standards to ensure product safety and performance.
2. How Are Quality Control Checkpoints Structured?
Quality control (QC) is typically organized at various checkpoints throughout the manufacturing process. Key checkpoints include:
- Incoming Quality Control (IQC): This is the initial stage where raw materials are inspected for defects and compliance with specifications.
- In-Process Quality Control (IPQC): During manufacturing, components are monitored to ensure they meet quality standards. This can involve regular sampling and testing.
- Final Quality Control (FQC): Once the product is assembled, it undergoes rigorous testing to ensure functionality and safety before shipment.
Understanding these checkpoints allows buyers to assess the thoroughness of a supplier’s QC processes.
What Testing Methods Are Common in Remote Control Manufacturing?
Testing methods vary widely depending on the product specifications and regulatory requirements. B2B buyers should be aware of the common testing practices that manufacturers should implement.
1. What Types of Functional Testing Are Conducted?
Functional testing assesses whether the remote control operates as intended. This includes checking the response of buttons, range of signal transmission, and battery life. Manufacturers often employ automated testing systems to ensure consistent results across batches. Buyers should ask potential suppliers about their testing protocols and any certifications that validate the results.
2. What Environmental and Durability Tests Are Conducted?
Environmental testing evaluates how well the remote control withstands various conditions, such as temperature extremes, humidity, and exposure to dust or moisture. Durability testing assesses the product’s lifespan under normal use, including button wear and casing integrity. B2B buyers should inquire about these tests and request documentation that demonstrates the reliability of the products.
How Can B2B Buyers Verify Supplier Quality Control?
To ensure that a supplier’s quality assurance processes meet expectations, B2B buyers should take proactive steps in verifying their capabilities.
1. What Should Buyers Look for in Supplier Audits and Reports?
Conducting supplier audits is an effective way to evaluate a manufacturer’s quality control practices. Buyers should look for detailed reports that outline the manufacturer’s adherence to quality standards, including any non-conformities and corrective actions taken. Regular audits can help maintain a long-term relationship with suppliers who prioritize quality.
2. How Can Third-Party Inspections Enhance Quality Assurance?
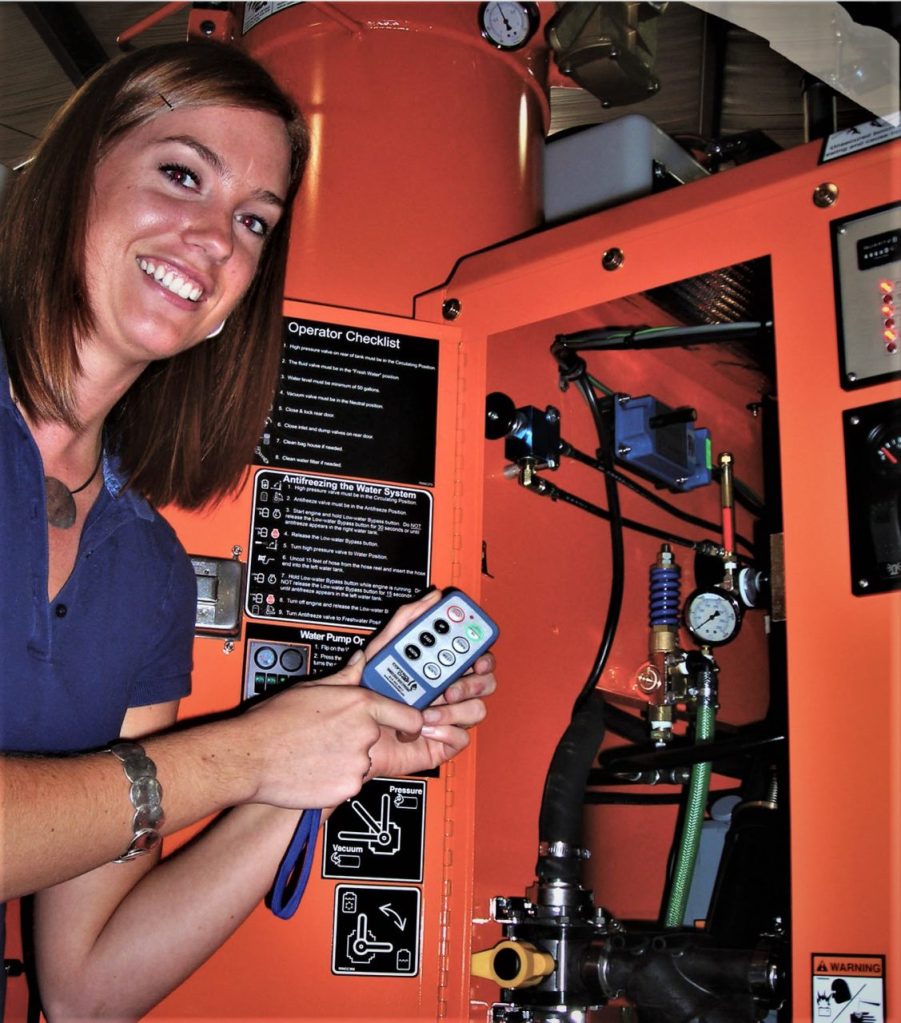
A stock image related to remote control manufacturer.
Engaging third-party inspection services can provide an unbiased assessment of a manufacturer’s quality processes. These inspections can be particularly useful for buyers in regions with less stringent manufacturing regulations. Buyers should consider incorporating third-party inspections into their procurement process to ensure compliance with international quality standards.
What Are the Unique QC Considerations for International B2B Buyers?
International buyers, particularly from Africa, South America, the Middle East, and Europe, face unique challenges in the QC landscape.
1. How Do Regional Regulations Affect Quality Standards?
Different regions may have varying regulations that affect product compliance. For instance, CE certification is crucial for products sold in the European market, while other regions may have different requirements. Buyers should familiarize themselves with local regulations to ensure that products meet necessary standards for their markets.
2. What Role Does Cultural Understanding Play in Supplier Relationships?
Cultural differences can impact communication and expectations regarding quality assurance. Buyers should strive for clear communication and establish mutual understanding with suppliers regarding quality standards and practices. Building strong relationships can lead to better cooperation in addressing quality issues.
Conclusion: Ensuring Quality in Remote Control Manufacturing
For B2B buyers, understanding the manufacturing processes and quality assurance practices in remote control production is vital for making informed decisions. By focusing on material preparation, forming, assembly, and finishing, along with robust quality assurance standards, buyers can ensure they partner with reliable manufacturers. Engaging in due diligence, including audits and third-party inspections, will further enhance confidence in the quality of products sourced from international suppliers.
Practical Sourcing Guide: A Step-by-Step Checklist for ‘remote control manufacturer’
The purpose of this guide is to provide B2B buyers with a practical checklist for sourcing remote control manufacturers. This checklist is essential for ensuring that you partner with a reliable supplier who meets your technical requirements and aligns with your business goals.
Step 1: Define Your Technical Specifications
Clearly outline the technical specifications needed for your remote controls. This includes the type of technology (e.g., infrared, RF), features (e.g., programmable buttons, backlighting), and compatibility with existing systems. By defining these parameters upfront, you ensure that potential suppliers can meet your needs and avoid costly revisions later.
Step 2: Research and Shortlist Potential Suppliers
Conduct thorough research to identify potential remote control manufacturers. Use industry directories, trade shows, and online platforms to compile a list of candidates. Focus on suppliers who specialize in the specific type of remote control you need and have a proven track record in your target markets, such as Africa, South America, the Middle East, or Europe.
Step 3: Evaluate Supplier Certifications and Compliance
Verify that your shortlisted suppliers hold relevant certifications and comply with industry standards. This may include ISO certifications, CE marking for European markets, or specific safety standards applicable in your region. Ensuring compliance not only mitigates risk but also enhances product credibility in your target market.
Step 4: Request Samples and Conduct Quality Checks
Before finalizing any agreements, request product samples to assess quality. Evaluate the materials used, functionality, and overall design. Conducting quality checks at this stage can save you from future complications related to product defects or performance issues.
Step 5: Assess Pricing and Payment Terms
Obtain detailed pricing information from your shortlisted suppliers. Look beyond the initial cost per unit; consider bulk pricing, shipping fees, and payment terms. Assessing the total cost of ownership is crucial for budgeting and ensuring profitability in your sourcing strategy.
Step 6: Check References and Previous Client Feedback
Request references from previous clients who have sourced similar products from the suppliers you are considering. Inquire about their experiences regarding product quality, delivery timelines, and customer service. This insight can provide valuable context about the supplier’s reliability and performance.
Step 7: Negotiate Terms and Finalize Contracts
Once you have selected a supplier, engage in negotiations to finalize terms that are favorable for both parties. Address critical aspects such as lead times, warranties, and after-sales support. A well-structured contract helps safeguard your interests and clarifies expectations for both you and the manufacturer.
By following this checklist, B2B buyers can streamline their sourcing process for remote control manufacturers, ensuring that they select the right partners for their business needs.
Comprehensive Cost and Pricing Analysis for remote control manufacturer Sourcing
What Are the Key Cost Components in Remote Control Manufacturing?
When sourcing remote controls, understanding the cost structure is crucial for effective budgeting and negotiations. The primary cost components include:
-
Materials: The type of materials used (e.g., plastics, metals, electronic components) significantly impacts costs. Higher-quality materials may increase durability and performance but will also raise the price.
-
Labor: Labor costs vary by region, influenced by local wage rates and skill levels. In countries with lower labor costs, such as parts of Asia, manufacturing may be cheaper, but this can affect quality.
-
Manufacturing Overhead: This includes costs related to facility maintenance, utilities, and administrative expenses. Efficient operations can help reduce overhead costs.
-
Tooling: Initial tooling costs for molds and machinery can be substantial, particularly for custom designs. Buyers should consider these in the total cost of ownership.
-
Quality Control (QC): Implementing robust QC processes can prevent defects but adds to labor and overhead costs. Suppliers with established QC systems may charge a premium.
-
Logistics: Shipping costs, including freight, customs duties, and insurance, must be factored in. Incoterms chosen can affect who bears these costs.
-
Margin: Supplier margins vary widely based on competition, market demand, and supplier capabilities. Understanding typical margins in the industry helps in negotiations.
How Do Price Influencers Impact Remote Control Manufacturing Costs?
Several factors influence the pricing of remote controls, which can vary significantly based on the buyer’s specifications:
-
Volume/MOQ (Minimum Order Quantity): Higher order volumes often lead to lower per-unit costs. Suppliers typically offer discounts for bulk orders, making it advantageous for buyers to consolidate their purchases.
-
Specifications/Customization: Custom features or advanced technology can increase costs. Buyers should clearly define their requirements to avoid unexpected price increases.
-
Materials: The choice of materials not only affects the initial price but also impacts the long-term durability and performance of the product. Buyers should balance cost with quality to ensure value.
-
Quality and Certifications: Products that meet specific quality standards or certifications (e.g., ISO, CE) may command higher prices. Buyers in regulated markets should prioritize certified products.
-
Supplier Factors: The supplier’s reputation, production capacity, and location can all affect pricing. Established suppliers may offer better reliability but at a higher cost.
-
Incoterms: The chosen Incoterms dictate the responsibilities of buyers and sellers concerning shipping and logistics costs. Understanding these terms is essential for accurate pricing.
What Are the Best Negotiation Tips for International B2B Buyers?
For international B2B buyers, particularly from Africa, South America, the Middle East, and Europe, effective negotiation can lead to significant savings. Here are some actionable tips:
-
Conduct Market Research: Understand the market pricing for similar products to establish a baseline for negotiations. This knowledge empowers buyers to make informed decisions.
-
Leverage Volume Discounts: If possible, consolidate orders to increase volume and negotiate better rates. Suppliers are often more willing to provide discounts for larger orders.
-
Clarify Total Cost of Ownership (TCO): Consider all costs associated with the product, including shipping, tariffs, and after-sales support. A lower initial price may not always equate to better value.
-
Be Aware of Pricing Nuances: Different regions may have unique pricing strategies based on local economic conditions. Familiarize yourself with these to better understand your supplier’s pricing.
-
Build Relationships: Establishing a strong relationship with suppliers can lead to better terms and more favorable pricing in the long run. Trust and communication are key.
Conclusion: Understanding Pricing for Better Sourcing Decisions
As international buyers navigate the complexities of sourcing remote controls, an in-depth understanding of cost components, price influencers, and effective negotiation strategies will empower them to make informed decisions. While prices can vary widely based on numerous factors, a well-researched approach will ensure that buyers achieve cost-effective and high-quality solutions tailored to their needs. Always consult with multiple suppliers to gather comparative pricing and ensure you are getting the best deal possible.
Alternatives Analysis: Comparing remote control manufacturer With Other Solutions
Understanding Alternatives for Remote Control Solutions
When exploring remote control solutions, it is essential to consider various alternatives that may meet your business needs. Different technologies can provide similar functionalities, each with unique benefits and drawbacks. In this analysis, we will compare the traditional remote control manufacturing process with two viable alternatives: smartphone apps and smart home automation systems.
Comparison Table
Comparison Aspect | Remote Control Manufacturer | Smartphone App | Smart Home Automation System |
---|---|---|---|
Performance | High reliability, tailored to specific devices | Varies by device compatibility | Highly customizable, integrates multiple devices |
Cost | Higher initial investment | Generally low cost, free versions available | Moderate to high, depending on the system |
Ease of Implementation | Requires manufacturing and logistics | Easy to deploy, requires basic app development | Can be complex, needs professional installation |
Maintenance | Regular updates required, can be costly | Minimal maintenance, updates managed via app stores | Moderate, may require updates and system checks |
Best Use Case | Specialized industrial applications | Consumer electronics, home entertainment | Comprehensive smart home setups |
Detailed Breakdown of Alternatives
How Do Smartphone Apps Compare to Remote Control Manufacturing?
Smartphone apps offer a modern solution for remote control needs, enabling users to control devices through their mobile phones. The primary advantage of this alternative is its cost-effectiveness; many apps are free or available at a low cost, making them accessible to a broader audience. Additionally, the ease of implementation is significant, as users can download apps without needing specialized hardware. However, the performance may vary depending on device compatibility, and reliance on smartphones means that users must have their devices charged and nearby, which may not be ideal for all industrial applications.
What Are the Benefits of Smart Home Automation Systems Over Traditional Remote Controls?
Smart home automation systems represent another advanced alternative to traditional remote controls. These systems allow for seamless integration of multiple devices, providing high customization and control. They are particularly beneficial for comprehensive setups that require managing various functions within a home or office environment. However, the initial investment can be moderate to high, and the complexity of installation may necessitate professional assistance. Maintenance is also a consideration, as these systems may require updates and regular checks to ensure optimal performance.
Conclusion: How Can B2B Buyers Choose the Right Remote Control Solution?
Selecting the right remote control solution depends on your specific business needs, budget, and the intended application. For industries requiring high reliability and tailored solutions, traditional remote control manufacturing may be the best fit. Conversely, for businesses looking for cost-effective and flexible options, smartphone apps and smart home automation systems provide innovative alternatives. By evaluating the performance, cost, ease of implementation, and maintenance of each solution, B2B buyers can make informed decisions that align with their operational requirements and strategic goals.
Essential Technical Properties and Trade Terminology for remote control manufacturer
What Are the Key Technical Properties for Remote Control Manufacturing?
Understanding the technical specifications of remote controls is crucial for international B2B buyers. Here are several critical properties that should be considered when sourcing remote control products:
-
Material Grade
– The material used in remote controls significantly impacts durability and performance. Common materials include ABS plastic for housings, which offers good impact resistance and is lightweight. For internal components, materials like PCBA (Printed Circuit Board Assembly) must be chosen for their conductivity and reliability. Selecting the right material ensures the product can withstand environmental conditions, such as humidity and temperature variations, which is particularly important in regions like Africa and South America. -
Tolerance
– Tolerance refers to the allowable deviation from a specified measurement. In remote controls, tight tolerances are essential for ensuring that components fit together accurately and function correctly. For example, the spacing between buttons must be precise to avoid misoperation. In B2B settings, understanding tolerances can help buyers assess quality control processes and the potential for defects, which is vital in maintaining customer satisfaction. -
Battery Life
– Battery life is a key specification that determines how long a remote control can operate before needing a replacement. Specifications often list the expected battery life in hours or cycles. For buyers, longer battery life can translate into lower maintenance costs and improved user experience, making this a critical factor in the purchasing decision. -
Frequency Range
– Remote controls operate on specific radio frequencies (e.g., IR, RF, or Bluetooth). The frequency range affects the control distance and the ability to penetrate obstacles. Buyers should ensure that the frequency range aligns with their operational needs, especially in commercial applications where multiple devices may need to be controlled simultaneously. -
User Interface Design
– The ergonomics and layout of buttons are essential for user satisfaction. A well-designed interface improves usability and can reduce the learning curve for new users. B2B buyers should evaluate the user interface design, as it impacts the overall customer experience and can influence sales.
Which Trade Terms Should International Buyers Understand?
Familiarity with industry jargon can facilitate smoother negotiations and transactions. Here are some common terms that are essential for B2B buyers in the remote control manufacturing sector:
-
OEM (Original Equipment Manufacturer)
– OEM refers to a company that produces parts or equipment that may be marketed by another manufacturer. For buyers, partnering with an OEM can ensure that they receive high-quality components tailored to their specifications, often resulting in better product performance. -
MOQ (Minimum Order Quantity)
– MOQ is the smallest quantity of a product that a supplier is willing to sell. Understanding MOQ is crucial for buyers to manage inventory effectively and optimize costs. Suppliers in various regions may have different MOQs, impacting purchasing decisions. -
RFQ (Request for Quotation)
– An RFQ is a document issued by buyers requesting pricing information from suppliers. It typically includes detailed specifications and quantities. For international buyers, submitting an RFQ can streamline the procurement process and help in comparing offers from different manufacturers. -
Incoterms (International Commercial Terms)
– Incoterms are standardized international shipping terms that define the responsibilities of buyers and sellers. Familiarity with these terms helps buyers understand shipping costs, risks, and responsibilities, which is vital for effective logistics management across different regions. -
Lead Time
– Lead time refers to the time taken from placing an order to receiving the product. For B2B buyers, understanding lead times is crucial for inventory planning and meeting customer demands, especially in fast-moving markets. -
Certification Standards
– Certifications, such as CE, FCC, or RoHS, indicate compliance with safety and environmental regulations. Buyers should be aware of relevant certifications to ensure that products meet local market requirements and enhance their credibility.
By grasping these technical properties and trade terms, international B2B buyers can make informed purchasing decisions, ensuring they select high-quality remote controls that meet their operational needs.
Navigating Market Dynamics and Sourcing Trends in the remote control manufacturer Sector
What Are the Current Market Dynamics and Sourcing Trends in the Remote Control Manufacturing Sector?
The remote control manufacturing sector is experiencing significant transformation driven by technological advancements and changing consumer preferences. One of the key global drivers is the increasing demand for smart home devices, which is pushing manufacturers to innovate and integrate advanced features such as voice control and connectivity through IoT (Internet of Things). This trend is particularly evident in regions such as Europe and North America, where smart technology adoption is rapidly rising.
In terms of sourcing trends, international B2B buyers are increasingly looking for suppliers who can provide high-quality, customizable products at competitive prices. Emerging markets in Africa and South America are becoming attractive sourcing hubs due to their growing manufacturing capabilities and lower labor costs. Buyers are also prioritizing suppliers who demonstrate agility in adapting to market changes and who can provide just-in-time delivery to meet fluctuating demand.
Moreover, sustainability is becoming a crucial factor in purchasing decisions. Buyers are now more inclined to partner with manufacturers that emphasize eco-friendly practices and materials. This shift towards sustainability is not only a response to consumer demand but also aligns with regulatory frameworks in various regions, particularly in Europe, where stringent environmental regulations are in place.
How Is Sustainability Impacting Sourcing Decisions in the Remote Control Manufacturing Sector?
Sustainability and ethical sourcing have emerged as essential components in the remote control manufacturing sector. The environmental impact of manufacturing processes and product lifecycle has prompted buyers to seek suppliers who prioritize sustainable practices. This includes the use of recyclable materials, energy-efficient manufacturing processes, and waste reduction strategies.
Ethical supply chains are gaining importance as consumers and businesses alike demand transparency regarding sourcing practices. Buyers are increasingly interested in manufacturers who can provide certifications such as ISO 14001 for environmental management or the Forest Stewardship Council (FSC) certification for sustainable materials. These certifications not only enhance the credibility of the supplier but also align with the corporate social responsibility (CSR) goals of many international B2B buyers.
Additionally, the incorporation of ‘green’ materials, such as bioplastics and recycled components, is becoming a competitive differentiator. Suppliers who can innovate in this area are likely to attract more business, particularly from buyers in Europe and North America, where sustainability is a key purchasing criterion.
How Has the Remote Control Manufacturing Sector Evolved Over Time?
The remote control manufacturing sector has undergone significant evolution since its inception in the mid-20th century. Initially dominated by simple infrared technology, the industry has transitioned to more sophisticated wireless technologies, including RF (radio frequency) and Bluetooth. This evolution has been driven by consumer demand for more functionality and ease of use.
As technology advanced, so did the capabilities of remote controls. Today, they can control multiple devices, integrate with smart home systems, and even feature touch screens. This shift has opened new opportunities for manufacturers to innovate and cater to the evolving needs of consumers and businesses alike.
In conclusion, understanding these market dynamics, sustainability practices, and the historical context of remote control manufacturing can empower international B2B buyers to make informed sourcing decisions that align with their business objectives and values.
Frequently Asked Questions (FAQs) for B2B Buyers of remote control manufacturer
-
How do I choose the right remote control manufacturer for my business?
Selecting the right remote control manufacturer involves evaluating several key factors. Start by identifying your specific needs, such as product features, volume requirements, and customization options. Research potential suppliers through trade shows, online marketplaces, and industry referrals. Verify their manufacturing capabilities, quality certifications, and customer reviews. It’s also beneficial to request samples to assess product quality. Lastly, ensure they have a reliable supply chain and good communication practices to facilitate smooth transactions. -
What are the common minimum order quantities (MOQs) for remote control manufacturers?
Minimum order quantities (MOQs) can vary significantly among remote control manufacturers, typically ranging from 100 to 10,000 units, depending on the supplier and product specifications. For international buyers, MOQs may be influenced by factors like production costs, shipping logistics, and customization requirements. Always inquire about MOQs during the initial discussions and consider negotiating if your order size is smaller. Some manufacturers may offer flexibility for new clients or larger contracts in the future. -
What customization options should I consider when sourcing remote controls?
When sourcing remote controls, consider customization options such as design, size, color, and button configuration. Additionally, assess the manufacturer’s ability to incorporate specific technologies, like Bluetooth or infrared, into the design. Discussing software features, such as app integration or programmable buttons, can also enhance functionality. Ensure that the manufacturer can meet your quality standards while accommodating your design preferences, as this will play a crucial role in customer satisfaction. -
What payment terms are standard for international B2B purchases of remote controls?
Standard payment terms for international B2B purchases often include options such as a deposit (usually 30% to 50%) before production, with the balance due upon shipment. Some manufacturers may offer letters of credit or payment via escrow services to provide additional security. It’s essential to negotiate terms that are favorable for your cash flow while ensuring the supplier feels secure in the transaction. Always clarify terms before placing an order to avoid any misunderstandings.
-
How can I ensure quality assurance (QA) when sourcing remote controls?
To ensure quality assurance when sourcing remote controls, request information about the manufacturer’s QA processes and certifications, such as ISO 9001. Conducting factory audits or inspections before placing large orders can provide insights into their production practices. Additionally, establishing a clear contract that outlines quality standards and testing procedures will help maintain product integrity. Implementing a sample testing phase before full-scale production is also advisable to identify any potential issues early on. -
What logistics considerations should I keep in mind when importing remote controls?
When importing remote controls, consider logistics factors such as shipping methods (air vs. sea), customs clearance processes, and delivery timelines. Evaluate the total landed cost, including shipping, duties, and taxes, to understand your overall expenditure. Working with a freight forwarder experienced in electronics can streamline the shipping process. Additionally, ensure that the manufacturer provides proper documentation for customs to avoid delays and potential penalties.
-
How do I vet remote control suppliers for reliability and reputation?
Vetting remote control suppliers involves several steps. Start by checking their business credentials, such as registration, certifications, and industry affiliations. Look for customer reviews and testimonials on platforms like Alibaba or industry-specific forums. Engaging in direct communication can also provide insights into their responsiveness and professionalism. If possible, seek out references from other businesses that have worked with them, and consider conducting a site visit to their manufacturing facility for firsthand assessment. -
What are the typical lead times for production and delivery of remote controls?
Typical lead times for the production and delivery of remote controls can range from 4 to 12 weeks, depending on factors like order size, complexity of customization, and the manufacturer’s production capacity. It’s crucial to discuss lead times upfront and consider potential delays due to customs or logistical issues. Establishing a clear timeline in your contract can help manage expectations and ensure timely delivery. For urgent projects, inquire about expedited production options, though this may incur additional costs.
Important Disclaimer & Terms of Use
⚠️ Important Disclaimer
The information provided in this guide, including content regarding manufacturers, technical specifications, and market analysis, is for informational and educational purposes only. It does not constitute professional procurement advice, financial advice, or legal advice.
While we have made every effort to ensure the accuracy and timeliness of the information, we are not responsible for any errors, omissions, or outdated information. Market conditions, company details, and technical standards are subject to change.
B2B buyers must conduct their own independent and thorough due diligence before making any purchasing decisions. This includes contacting suppliers directly, verifying certifications, requesting samples, and seeking professional consultation. The risk of relying on any information in this guide is borne solely by the reader.
Strategic Sourcing Conclusion and Outlook for remote control manufacturer
What Are the Key Takeaways for Strategic Sourcing in Remote Control Manufacturing?
In conclusion, strategic sourcing remains a pivotal aspect for international B2B buyers in the remote control manufacturing sector. By establishing strong partnerships with reliable manufacturers, businesses can enhance their product quality, reduce costs, and improve supply chain efficiencies. It’s essential for buyers from Africa, South America, the Middle East, and Europe to leverage local market insights while also considering global trends to ensure competitive advantage.
How Can International Buyers Benefit from Strategic Sourcing?
As you navigate the complexities of sourcing remote controls, remember that prioritizing transparency, quality assurance, and sustainability will not only bolster your supply chain resilience but also align with consumer preferences. Engaging with manufacturers who prioritize innovation and adaptability can also lead to breakthroughs that position your business for long-term success.
What’s Next for B2B Buyers in the Remote Control Industry?
As we look ahead, the landscape of remote control manufacturing will continue to evolve, driven by technological advancements and shifting market demands. Now is the time for international buyers to act decisively—evaluate your sourcing strategies, embrace collaborative partnerships, and stay informed about emerging technologies. By doing so, you’ll be well-equipped to navigate the future of the industry and seize new opportunities as they arise.