The Ultimate Guide to Silicon Carbide Manufacturer (2025)
Introduction: Navigating the Global Market for silicon carbide manufacturer
Navigating the complexities of sourcing silicon carbide manufacturers can be a daunting task for international B2B buyers, particularly those based in Africa, South America, the Middle East, and Europe. As industries increasingly rely on silicon carbide for its superior thermal conductivity and durability in applications ranging from electronics to automotive components, understanding how to effectively identify and engage with reliable suppliers is critical. This guide aims to demystify the global market for silicon carbide manufacturing by providing actionable insights and resources.
In the following sections, we will explore various types of silicon carbide products, their applications across different sectors, and the best practices for vetting suppliers to ensure quality and compliance with international standards. Additionally, we will discuss cost factors, including pricing strategies and negotiation tactics, that can empower buyers to make informed purchasing decisions.
Whether you are a procurement manager in Spain seeking advanced materials for semiconductor production or a business owner in South Africa looking to diversify your supply chain, this comprehensive guide is designed to equip you with the knowledge needed to navigate the global landscape of silicon carbide manufacturing effectively. By leveraging the insights provided, you can enhance your sourcing strategy, mitigate risks, and ultimately drive greater value for your organization.
Understanding silicon carbide manufacturer Types and Variations
Type Name | Key Distinguishing Features | Primary B2B Applications | Brief Pros & Cons for Buyers |
---|---|---|---|
Bulk Silicon Carbide | High purity, large-scale production, cost-effective | Abrasives, ceramics, refractories | Pros: Cost-efficient, high availability. Cons: Limited customization. |
Silicon Carbide Wafers | Thin, flat discs for semiconductor applications | Electronics, photovoltaics | Pros: High performance in high-temperature applications. Cons: Higher cost, specialized suppliers. |
Silicon Carbide Powder | Varied particle sizes, used for grinding and polishing | Metalworking, surface finishing | Pros: Versatile applications, customizable grades. Cons: Requires careful handling and storage. |
Silicon Carbide Ceramics | Engineered materials with exceptional hardness and thermal resistance | Aerospace, automotive, industrial equipment | Pros: High durability, excellent thermal stability. Cons: More expensive, requires specialized processing. |
Silicon Carbide Fibers | Lightweight, high-strength fibers for composite materials | Aerospace, defense, automotive | Pros: Enhances material strength, lightweight. Cons: Limited suppliers, higher production costs. |
What Are the Characteristics of Bulk Silicon Carbide?
Bulk silicon carbide is produced in large quantities and is characterized by its high purity levels and cost-effectiveness. This type is primarily used in abrasives, ceramics, and refractories. When considering bulk silicon carbide, buyers should evaluate the supplier’s ability to provide consistent quality and availability, as well as pricing dynamics in the market. Its cost-efficiency makes it an attractive option for large-scale applications, although it may lack the customization found in other forms.
How Do Silicon Carbide Wafers Differ from Other Types?
Silicon carbide wafers are thin, flat discs specifically designed for the semiconductor industry. They offer high performance, particularly in high-temperature applications, making them ideal for electronics and photovoltaics. Buyers should consider the wafer’s specifications, such as thickness and diameter, as well as the supplier’s expertise in semiconductor-grade materials. While they provide superior performance, the associated costs can be higher, and sourcing may be more specialized.
What Is the Role of Silicon Carbide Powder in B2B Applications?
Silicon carbide powder comes in various particle sizes, making it suitable for grinding and polishing applications across multiple industries, including metalworking and surface finishing. This versatility allows buyers to select specific grades tailored to their needs. However, careful handling and storage are crucial due to the powder’s abrasive nature. Companies should assess the supplier’s ability to provide customized grades and ensure compliance with safety standards.
Why Are Silicon Carbide Ceramics Important for Industrial Uses?
Silicon carbide ceramics are engineered materials renowned for their exceptional hardness and thermal resistance. They find applications in aerospace, automotive, and industrial equipment due to their durability and thermal stability. When purchasing, buyers should consider the manufacturing processes involved, as specialized techniques are often required. While they offer significant advantages in performance, the higher costs associated with silicon carbide ceramics can be a key consideration.
What Advantages Do Silicon Carbide Fibers Offer in Composite Materials?
Silicon carbide fibers are lightweight yet incredibly strong, making them ideal for enhancing composite materials in industries such as aerospace, defense, and automotive. Their unique properties allow for the development of materials that require both strength and reduced weight. Buyers should focus on the supplier’s capability to provide high-quality fibers and consider the implications of higher production costs. The limited number of suppliers can also affect availability and pricing.
Related Video: Silicon Carbide: From Powder to Powerhouse!
Key Industrial Applications of silicon carbide manufacturer
Industry/Sector | Specific Application of Silicon Carbide Manufacturer | Value/Benefit for the Business | Key Sourcing Considerations for this Application |
---|---|---|---|
Automotive | Electric Vehicle (EV) Components | Enhanced efficiency and performance of EV systems | Quality certification, supply chain reliability, cost |
Aerospace | High-Temperature Gas Turbines | Improved thermal resistance and durability | Material specifications, compliance with industry standards |
Electronics | Power Electronics | Higher efficiency and reduced energy loss | Availability of customized solutions, lead times |
Renewable Energy | Solar Inverters | Increased energy conversion efficiency | Technical support, integration capabilities |
Semiconductor | Wafer Fabrication | Superior electrical properties for faster devices | Supplier reputation, scalability, and pricing |
How is Silicon Carbide Used in the Automotive Industry?
In the automotive sector, silicon carbide (SiC) is primarily utilized in electric vehicle (EV) components such as inverters and chargers. SiC enhances the efficiency of power conversion, allowing for lighter and more compact designs. This results in a significant reduction in energy loss, which is critical for maximizing the range of electric vehicles. For international buyers, especially from regions like Africa and South America, sourcing SiC components requires attention to quality certifications and reliability of the supply chain, ensuring that the materials meet stringent performance standards.
What Role Does Silicon Carbide Play in Aerospace Applications?
Silicon carbide is essential in aerospace applications, particularly in high-temperature gas turbines. The material’s superior thermal resistance enables it to withstand extreme temperatures and pressures, improving the overall durability and efficiency of turbine systems. This translates to better fuel efficiency and lower emissions, which are increasingly important in aerospace engineering. Buyers from Europe and the Middle East should focus on suppliers that comply with aerospace industry standards and can provide detailed material specifications to ensure safety and performance.
How is Silicon Carbide Transforming the Electronics Sector?
In the electronics industry, silicon carbide is used extensively in power electronics, including rectifiers and MOSFETs. The unique properties of SiC allow for higher switching frequencies and lower energy losses compared to traditional silicon, leading to improved overall efficiency. This is particularly beneficial for applications in renewable energy systems and electric vehicles. B2B buyers must consider the availability of customized solutions and the supplier’s ability to meet specific integration requirements to optimize performance.
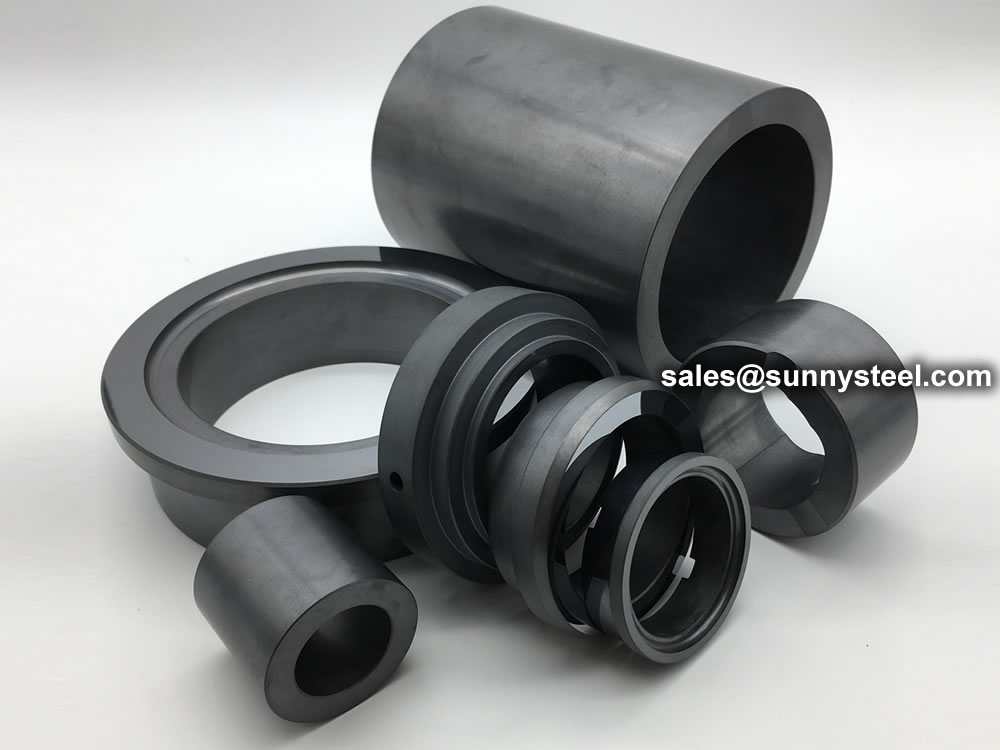
A stock image related to silicon carbide manufacturer.
Why is Silicon Carbide Important for Renewable Energy Technologies?
Silicon carbide is increasingly being utilized in solar inverters, where it enhances energy conversion efficiency. The ability of SiC to operate at higher voltages and temperatures allows for more compact and efficient inverter designs, which are crucial for maximizing the output of solar panels. For international buyers, particularly from regions with growing renewable energy markets, sourcing SiC components necessitates a focus on technical support and the ability to integrate with existing systems, ensuring optimal performance and reliability.
What Advantages Does Silicon Carbide Offer in Semiconductor Manufacturing?
In semiconductor manufacturing, silicon carbide is favored for wafer fabrication due to its superior electrical properties. SiC wafers enable the production of faster and more efficient electronic devices, which are essential for modern applications like 5G technology and high-performance computing. For B2B buyers, particularly in Europe and the Middle East, evaluating supplier reputation and scalability is critical. Ensuring that suppliers can meet demand while maintaining competitive pricing is essential for long-term partnerships in this rapidly evolving industry.
Related Video: What is Silicon Carbide?
3 Common User Pain Points for ‘silicon carbide manufacturer’ & Their Solutions
Scenario 1: Navigating Quality Control Challenges in Silicon Carbide Procurement
The Problem:
B2B buyers often face significant challenges when it comes to ensuring the quality of silicon carbide (SiC) products. This is particularly true for international buyers from regions like Africa and South America, where access to reliable suppliers can be limited. These buyers may receive products that do not meet the required specifications, leading to costly delays and potential project failures. The lack of standardized testing and certification processes across different manufacturers exacerbates this issue, leaving buyers uncertain about the reliability of their suppliers.
The Solution:
To mitigate quality control issues, it’s crucial for buyers to implement a thorough vetting process for silicon carbide manufacturers. Start by requesting detailed product specifications, including material properties, manufacturing processes, and certifications. Look for suppliers who adhere to international standards such as ISO 9001, which indicates a commitment to quality management systems. Additionally, consider conducting third-party audits or inspections to verify the quality of the materials before shipment. Building a strong relationship with a reliable supplier can also facilitate better communication regarding quality expectations and improvements. Lastly, leverage technology by utilizing online platforms that provide reviews and ratings of suppliers to make more informed decisions.
Scenario 2: Addressing Supply Chain Disruptions in Silicon Carbide Sourcing
The Problem:
Supply chain disruptions can severely impact the availability of silicon carbide, especially for manufacturers in the Middle East and Europe who rely on consistent delivery schedules. Global events, such as geopolitical tensions or pandemics, can lead to unforeseen delays, making it challenging for B2B buyers to maintain production timelines. As a result, companies may find themselves scrambling to find alternative sources or facing increased costs due to expedited shipping or last-minute sourcing.
The Solution:
To effectively manage supply chain disruptions, buyers should develop a diversified sourcing strategy. This involves identifying multiple silicon carbide manufacturers across different regions, reducing reliance on a single supplier. Additionally, establish relationships with local distributors who may have stock readily available, thus minimizing lead times. Implementing just-in-time inventory practices can also help manage stock levels while keeping costs down. Regularly reviewing and assessing the supply chain landscape will enable buyers to adapt quickly to changes, ensuring that they can secure silicon carbide products even in challenging circumstances.
Scenario 3: Overcoming Technical Challenges in Silicon Carbide Applications
The Problem:
B2B buyers often encounter technical challenges when integrating silicon carbide into their products, particularly in industries such as automotive and electronics. This is especially relevant for buyers in Europe, where technological advancements demand high-performance materials. Misunderstanding the properties of silicon carbide—such as its thermal conductivity, electrical resistance, and mechanical strength—can lead to suboptimal product performance and increased failure rates.
The Solution:
To overcome technical challenges, buyers should invest in education and training regarding silicon carbide applications. Collaborating closely with the manufacturer’s technical team can provide valuable insights into how to best utilize the material. Requesting application-specific guidance and data sheets can enhance understanding and implementation. Additionally, consider engaging in joint development programs where both the buyer and manufacturer work together to refine the application process, ensuring optimal performance. Utilizing simulation tools and prototyping can also help test and validate designs before full-scale production, reducing the risk of errors and failures in the final product.
Strategic Material Selection Guide for silicon carbide manufacturer
What Are the Key Materials Used in Silicon Carbide Manufacturing?
When selecting materials for silicon carbide (SiC) manufacturing, it is crucial to consider various properties that affect performance, durability, and cost. Below, we analyze four common materials used in the production of silicon carbide components, focusing on their key properties, advantages, disadvantages, and specific considerations for international B2B buyers.
How Does Silicon Carbide Compare to Other Materials?
1. Silicon Carbide (SiC)
- Key Properties: SiC is known for its high thermal conductivity, excellent electrical insulation, and resistance to thermal shock. It can withstand temperatures exceeding 1,600°C and has a high breakdown electric field.
- Pros & Cons: The primary advantage of SiC is its superior performance in high-temperature and high-voltage applications. However, it is more expensive to produce than traditional silicon and requires specialized manufacturing processes, which can complicate production.
- Impact on Application: SiC is ideal for power electronics, semiconductor devices, and high-performance applications such as electric vehicles and renewable energy systems. Its compatibility with high-frequency operations makes it suitable for RF devices.
- Considerations for International Buyers: Buyers must ensure compliance with international standards such as ASTM and JIS, especially for applications in regulated industries. The high cost may be a barrier for some markets, particularly in developing regions.
2. Alumina (Al2O3)
- Key Properties: Alumina exhibits excellent hardness, high melting point (over 2,000°C), and good chemical stability. It is also an electrical insulator.
- Pros & Cons: Alumina is less expensive and easier to manufacture than SiC, making it a cost-effective alternative for certain applications. However, it has lower thermal conductivity and is not suitable for high-power applications.
- Impact on Application: Commonly used in insulators, substrates, and wear-resistant components, alumina is effective in applications where high mechanical strength is required but may not perform well in high-temperature electronics.
- Considerations for International Buyers: Buyers should be aware of the varying grades of alumina and their compliance with local standards, especially in Europe and the Middle East, where quality assurance is critical.
3. Silicon (Si)
- Key Properties: Silicon is a semiconductor material with a melting point of about 1,410°C. It has moderate thermal conductivity and is widely used in electronic applications.
- Pros & Cons: Silicon is significantly cheaper and easier to process than SiC, making it the go-to material for many electronic components. However, it cannot handle the same high temperatures or voltages as SiC, limiting its application scope.
- Impact on Application: Silicon is primarily used in traditional semiconductor devices, such as diodes and transistors. Its lower performance in extreme conditions makes it less suitable for advanced applications like electric vehicles.
- Considerations for International Buyers: Compliance with international semiconductor standards is essential, and buyers should consider the supply chain implications of sourcing silicon from various regions.
4. Gallium Nitride (GaN)
- Key Properties: GaN has a high thermal conductivity and a wide bandgap, allowing it to operate at higher voltages and temperatures than silicon.
- Pros & Cons: GaN is ideal for high-frequency applications and offers superior efficiency in power conversion. However, it is more expensive than both silicon and alumina, and its manufacturing process can be complex.
- Impact on Application: GaN is commonly used in RF applications, power amplifiers, and LED technology. Its ability to operate at high temperatures makes it suitable for advanced telecommunications.
- Considerations for International Buyers: Buyers should evaluate the cost-benefit ratio for GaN in their specific applications, as well as compliance with regional regulations in Africa, South America, and Europe.
Summary Table of Material Selection for Silicon Carbide Manufacturing
Material | Typical Use Case for Silicon Carbide Manufacturer | Key Advantage | Key Disadvantage/Limitation | Relative Cost (Low/Med/High) |
---|---|---|---|---|
Silicon Carbide (SiC) | Power electronics, semiconductor devices | Superior performance in high temperatures | High production cost, complex manufacturing | High |
Alumina (Al2O3) | Insulators, substrates, wear-resistant components | Cost-effective, easy to manufacture | Lower thermal conductivity, limited high-power use | Medium |
Silicon (Si) | Traditional semiconductor devices | Low cost, easy processing | Limited high-temperature performance | Low |
Gallium Nitride (GaN) | RF applications, power amplifiers | High efficiency, handles high voltages | Expensive, complex manufacturing process | High |
This strategic material selection guide provides actionable insights for international B2B buyers, helping them navigate the complexities of silicon carbide manufacturing materials while considering their specific regional needs and compliance requirements.
In-depth Look: Manufacturing Processes and Quality Assurance for silicon carbide manufacturer
What Are the Main Stages in the Manufacturing Process of Silicon Carbide?
The manufacturing process of silicon carbide (SiC) involves several critical stages that ensure the final product meets the rigorous standards demanded by various industries. The primary stages include material preparation, forming, assembly, and finishing.
-
Material Preparation: This initial stage involves selecting high-purity silicon and carbon sources. These raw materials are often subjected to pre-treatment processes to remove impurities. For instance, the silicon may be sourced from metallurgical-grade silicon, which undergoes purification to achieve the desired quality.
-
Forming: In this stage, the prepared materials are mixed and subjected to high temperatures in a controlled environment. The most common method is the Acheson process, where silicon and carbon are reacted in an electric arc furnace. This step results in the formation of silicon carbide crystals. The size and morphology of these crystals can be manipulated by adjusting the process parameters, which is crucial for tailoring the material to specific applications.
-
Assembly: After forming, the silicon carbide is often processed into various shapes and sizes, depending on the end-use requirements. This may involve cutting, grinding, or sintering the material to achieve the desired physical properties.
-
Finishing: The final stage involves surface treatments and coatings that enhance the material’s performance. Techniques such as polishing and chemical vapor deposition (CVD) can be employed to improve surface quality and ensure that the final product meets the exact specifications required by clients.
How Is Quality Assurance Integrated Into the Manufacturing of Silicon Carbide?
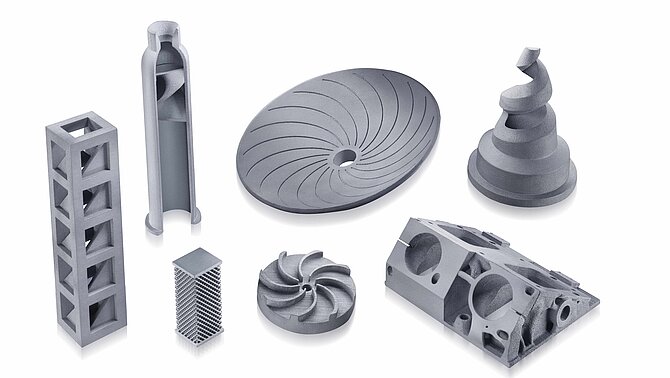
A stock image related to silicon carbide manufacturer.
Quality assurance (QA) is a vital aspect of the manufacturing process for silicon carbide, ensuring that the final products are reliable and meet international standards. Key components of QA include adhering to relevant international standards, implementing quality control checkpoints, and employing various testing methods.
-
International Standards: Many silicon carbide manufacturers adhere to international quality standards, such as ISO 9001, which outlines the requirements for a quality management system. Compliance with these standards ensures that manufacturers consistently produce high-quality products and continually improve their processes. Additionally, industry-specific standards such as CE marking for European markets and API specifications for oil and gas applications play a crucial role in ensuring product reliability.
-
Quality Control Checkpoints: Effective quality control involves several checkpoints throughout the manufacturing process:
– Incoming Quality Control (IQC): This checkpoint assesses the quality of raw materials before they enter the production line. Inspectors verify that materials meet specified standards and are free from defects.
– In-Process Quality Control (IPQC): During manufacturing, ongoing inspections are conducted to monitor the process and detect any deviations from the required standards. This proactive approach helps to identify and rectify issues before they escalate.
– Final Quality Control (FQC): Once the silicon carbide products are finished, a thorough inspection is carried out to ensure they meet all technical specifications. This may include dimensional checks, surface quality assessments, and other performance evaluations. -
Common Testing Methods: Various testing methods are employed to ensure the quality of silicon carbide products. These may include:
– Mechanical Testing: Evaluating the hardness, strength, and wear resistance of the material.
– Chemical Analysis: Testing for purity and composition using techniques such as X-ray fluorescence (XRF) or mass spectrometry.
– Thermal Analysis: Assessing thermal conductivity and thermal expansion properties to ensure suitability for high-temperature applications.
How Can B2B Buyers Verify Supplier Quality Control?
B2B buyers need to establish confidence in their suppliers’ quality control processes. Here are actionable strategies to verify supplier QC:
-
Supplier Audits: Conducting regular audits of potential suppliers can provide insights into their manufacturing processes, quality control systems, and adherence to international standards. Auditors should evaluate the supplier’s facilities, equipment, and staff qualifications to ensure they meet the required standards.
-
Requesting Quality Reports: Buyers can request detailed quality reports from suppliers, which should include data on previous inspections, test results, and compliance certifications. This documentation can help assess the supplier’s reliability and commitment to quality.
-
Third-Party Inspections: Engaging third-party inspection agencies can provide an unbiased evaluation of the supplier’s quality control processes. These agencies can conduct inspections and testing, providing buyers with independent verification of the supplier’s claims.
What Are the Nuances of Quality Control for International B2B Buyers?
International B2B buyers, particularly from regions like Africa, South America, the Middle East, and Europe, face unique challenges when dealing with silicon carbide suppliers. Understanding these nuances can help mitigate risks and ensure successful procurement.
-
Cultural and Regulatory Differences: Different regions may have varying quality expectations and regulatory requirements. Buyers should familiarize themselves with local standards and ensure that suppliers comply with them. For instance, products sold in Europe may need CE marking, while those in the Middle East may require compliance with specific local standards.
-
Language Barriers: Communication can be a challenge when dealing with international suppliers. Buyers should ensure that technical documentation, quality reports, and contracts are clear and understandable. Utilizing professional translation services can help bridge any gaps.
-
Supply Chain Transparency: Buyers should seek transparency in the supply chain to understand the sourcing of materials and the manufacturing process. This transparency can help identify potential quality issues and ensure that suppliers adhere to ethical sourcing practices.
-
Building Long-Term Relationships: Establishing strong relationships with suppliers can lead to better communication and improved quality assurance practices over time. Buyers should engage in regular discussions with suppliers to address concerns and collaborate on quality improvements.
By understanding the manufacturing processes and quality assurance mechanisms in place at silicon carbide manufacturers, international B2B buyers can make informed decisions, ensuring they source high-quality products that meet their specific needs.
Practical Sourcing Guide: A Step-by-Step Checklist for ‘silicon carbide manufacturer’
In today’s competitive market, sourcing silicon carbide manufacturers requires a strategic approach to ensure quality, reliability, and cost-effectiveness. This guide provides a practical checklist to assist international B2B buyers—particularly those from Africa, South America, the Middle East, and Europe—in navigating the procurement process effectively.
Step 1: Define Your Technical Specifications
Clearly outline the technical requirements for the silicon carbide products you need. This includes specifications on purity levels, particle size, and application-specific characteristics. Defining these parameters upfront will help streamline your search and ensure that potential suppliers can meet your needs.
Step 2: Conduct Market Research
Explore the global landscape of silicon carbide manufacturers. Utilize online resources, trade publications, and industry reports to identify potential suppliers. Pay attention to their market presence and reputation, as well as customer reviews and testimonials, which can provide insight into their reliability and product quality.
Step 3: Evaluate Potential Suppliers
Before committing, it’s crucial to vet suppliers thoroughly. Request company profiles, case studies, and references from buyers in a similar industry or region. Key aspects to consider include:
– Manufacturing capabilities: Assess whether the supplier has the technology and capacity to meet your volume and quality requirements.
– Financial stability: Ensure the supplier has a solid financial standing to avoid potential disruptions in supply.
Step 4: Verify Supplier Certifications
Confirm that potential suppliers hold relevant industry certifications, such as ISO 9001 or other quality management systems. These certifications demonstrate a commitment to quality and compliance with international standards. Additionally, inquire about any environmental certifications, particularly if sustainability is a priority for your business.
Step 5: Request Samples and Conduct Testing
Once you’ve shortlisted potential suppliers, request samples of their silicon carbide products. Conduct rigorous testing to evaluate their performance against your specifications. This step is critical to ensure that the materials meet your quality standards and functional requirements before placing a bulk order.
Step 6: Negotiate Terms and Conditions
Engage in negotiations with your selected supplier to establish favorable terms and conditions. Key factors to discuss include:
– Pricing and payment terms: Ensure clarity on pricing structures, discounts for bulk orders, and payment schedules.
– Delivery timelines: Agree on lead times for order fulfillment to align with your project schedules.
Step 7: Establish a Communication Plan
Effective communication is vital for a successful partnership. Set up regular check-ins and updates with your supplier to discuss production status, quality control, and any potential issues. Establishing a clear communication plan can prevent misunderstandings and foster a collaborative relationship.
By following this checklist, B2B buyers can ensure a thorough and strategic approach to sourcing silicon carbide manufacturers, ultimately leading to better product quality and supplier relationships.
Comprehensive Cost and Pricing Analysis for silicon carbide manufacturer Sourcing
What Are the Key Cost Components for Silicon Carbide Manufacturing?
When sourcing silicon carbide (SiC) from manufacturers, understanding the cost structure is crucial. Key cost components include:
-
Materials: The primary raw material for silicon carbide is silica and carbon, which can fluctuate in price due to market demand and availability. Suppliers that secure high-quality materials at competitive prices can significantly influence the overall cost.
-
Labor: Skilled labor is essential for the production of silicon carbide. Labor costs vary depending on the region. For example, manufacturers in Europe may face higher wage expectations than those in Africa or South America.
-
Manufacturing Overhead: This encompasses all indirect costs associated with production, such as utilities, depreciation of equipment, and facility maintenance. Manufacturers with efficient operations can keep these costs lower, impacting pricing favorably.
-
Tooling: The initial setup for silicon carbide production, including molds and specialized machinery, can be a substantial upfront investment. The amortization of these costs over production volume affects per-unit pricing.
-
Quality Control (QC): Stringent QC processes are necessary to ensure product reliability and compliance with international standards. Enhanced QC measures can increase costs, but they can also justify higher pricing through improved product performance.
-
Logistics: Shipping costs, including transportation and handling, are critical, particularly for international buyers. Understanding Incoterms can help buyers manage these costs effectively.
-
Margin: Manufacturers set their margins based on market conditions, competition, and their operational efficiencies. Buyers should be aware that prices may include substantial markups depending on the supplier’s market position.
How Do Price Influencers Affect Silicon Carbide Sourcing?
Several factors can influence the pricing of silicon carbide:
-
Volume/MOQ: Purchasing in larger quantities often leads to lower per-unit costs. Establishing a minimum order quantity (MOQ) with suppliers can help in negotiating better pricing.
-
Specifications and Customization: Custom specifications may lead to increased costs due to additional processing or materials. Clearly defining your requirements can help avoid unnecessary expenses.
-
Materials and Quality Certifications: Higher quality materials or certifications (e.g., ISO) can lead to increased prices. Buyers should assess whether the additional costs align with their performance needs.
-
Supplier Factors: Supplier reputation, reliability, and geographical location can affect pricing. Engaging with multiple suppliers can provide leverage in negotiations.
-
Incoterms: Understanding delivery terms is crucial. Different Incoterms (e.g., FOB, CIF) can significantly impact total costs, including freight and insurance.
What Tips Can Help International Buyers Negotiate Better Prices?
When negotiating with silicon carbide manufacturers, especially in the international market, consider these strategies:
-
Leverage Total Cost of Ownership (TCO): Instead of focusing solely on the purchase price, evaluate the TCO, which includes logistics, maintenance, and disposal costs. This holistic view can uncover more cost-effective options.
-
Be Prepared to Negotiate: Understand the market conditions and have a clear idea of your budget. Showing that you are knowledgeable about the cost structure can strengthen your position.
-
Explore Local Suppliers: If sourcing from a different continent, consider local suppliers who may offer competitive prices without the added logistics costs.
-
Long-Term Relationships: Building a long-term relationship with suppliers can lead to better pricing and service. Consider discussing future purchase commitments in exchange for favorable pricing.
-
Stay Informed on Market Trends: Regularly monitor market trends and price fluctuations for raw materials. This information can provide leverage in negotiations and help predict future costs.
Disclaimer on Pricing
The prices discussed in this analysis are indicative and can vary based on numerous factors, including market conditions and individual supplier circumstances. Buyers should conduct thorough research and request formal quotes to obtain precise pricing information tailored to their specific needs.
Alternatives Analysis: Comparing silicon carbide manufacturer With Other Solutions
When considering the procurement of silicon carbide (SiC) components, international B2B buyers must evaluate not only the product itself but also alternative solutions that may fulfill their operational requirements. Understanding these alternatives allows companies to make informed decisions based on performance, cost, and suitability for specific applications. Below, we compare silicon carbide manufacturers with two viable alternatives: Gallium Nitride (GaN) and traditional silicon-based solutions.
Comparison Aspect | Silicon Carbide Manufacturer | Gallium Nitride (GaN) | Traditional Silicon Solutions |
---|---|---|---|
Performance | High thermal conductivity and efficiency; suitable for high-voltage applications | Excellent efficiency and high switching speeds; ideal for RF and power applications | Good performance but lower efficiency in high-frequency operations |
Cost | Generally higher initial investment due to advanced material costs | Moderate costs, often less than SiC but higher than traditional silicon | Lower upfront costs but may incur higher operational expenses over time |
Ease of Implementation | Requires specialized knowledge for integration into existing systems | Moderate; emerging technology with a growing support network | Widely understood; easy integration into existing systems |
Maintenance | Low maintenance due to durability; excellent lifespan | Low maintenance; reliable under high-stress conditions | Higher maintenance due to thermal management issues |
Best Use Case | Power electronics, electric vehicles, and high-frequency applications | RF amplifiers, power converters, and electric vehicles | General electronic applications, consumer electronics |
What Are the Advantages and Disadvantages of Gallium Nitride (GaN)?
Gallium Nitride is an emerging alternative to silicon carbide that offers impressive efficiency, especially in high-frequency applications. One of its primary advantages is its ability to operate at higher temperatures and voltages, which makes it suitable for use in RF amplifiers and power converters. However, GaN technology is still developing, which may pose challenges in terms of widespread availability and integration support. For companies looking to innovate while managing costs, GaN presents a competitive option, though it may require a degree of technical adaptation.
How Do Traditional Silicon Solutions Compare?
Traditional silicon solutions have been the industry standard for many years, providing a reliable and cost-effective approach for various electronic applications. The primary advantage of silicon is its low cost and ease of integration, making it accessible for most manufacturers. However, traditional silicon components tend to have limitations regarding efficiency and performance, particularly in high-frequency or high-voltage scenarios. Companies that prioritize cost over performance may find silicon a suitable choice, but this could lead to increased operational expenses due to lower efficiency.
Conclusion: How to Choose the Right Solution for Your Needs
Selecting the right solution—whether silicon carbide, Gallium Nitride, or traditional silicon—depends on several factors, including performance requirements, budget constraints, and specific application needs. B2B buyers should conduct a thorough analysis of their operational goals, including expected performance outcomes and long-term maintenance considerations. By weighing the pros and cons of each alternative, companies can make a strategic decision that aligns with their technological capabilities and market demands, ultimately leading to enhanced operational efficiency and cost-effectiveness.
Essential Technical Properties and Trade Terminology for silicon carbide manufacturer
What Are the Key Technical Properties of Silicon Carbide?
Silicon carbide (SiC) is a semiconductor material renowned for its superior thermal conductivity, hardness, and chemical stability. For international B2B buyers, especially from Africa, South America, the Middle East, and Europe, understanding the technical specifications of silicon carbide is crucial for making informed purchasing decisions.
1. Material Grade
Material grades refer to the specific composition and purity level of silicon carbide. Grades can vary from standard grades for general applications to high-purity grades used in demanding environments like aerospace and automotive industries. Higher grades typically offer better performance and durability. Buyers should assess the required material grade based on their application needs to ensure optimal performance.
2. Tolerance
Tolerance indicates the allowable deviation in dimensions during manufacturing. It is crucial in applications where precision is essential, such as in electronic components. Tighter tolerances often result in higher costs but ensure better fitting and performance. B2B buyers must specify their tolerance requirements to avoid issues in assembly and functionality.
3. Thermal Conductivity
Silicon carbide is known for its excellent thermal conductivity, which is essential in applications requiring efficient heat dissipation, such as power electronics and high-temperature devices. Understanding the thermal conductivity values can help buyers select the right silicon carbide products that will perform effectively under specific operational conditions.
4. Hardness
Hardness is a critical property of silicon carbide, which affects its wear resistance and durability. Measured on the Mohs scale, SiC is one of the hardest materials available, making it suitable for abrasive applications. Buyers in sectors like manufacturing and mining should prioritize hardness specifications to ensure longevity and reliability in their applications.
5. Dielectric Strength
Dielectric strength refers to the maximum electric field a material can withstand without breaking down. Silicon carbide exhibits high dielectric strength, making it an ideal choice for electrical and electronic applications. B2B buyers should consider this property when sourcing components for high-voltage applications to ensure safety and reliability.
What Are Common Trade Terms Used in Silicon Carbide Manufacturing?
Navigating the silicon carbide manufacturing landscape involves understanding specific trade terminology. Here are some essential terms that B2B buyers should be familiar with:
1. OEM (Original Equipment Manufacturer)
An OEM is a company that produces parts or equipment that may be marketed by another manufacturer. In the silicon carbide industry, OEMs often require specific SiC components for their products. Understanding OEM specifications can help buyers align their needs with manufacturers.
2. MOQ (Minimum Order Quantity)
MOQ refers to the smallest number of units a supplier is willing to sell. This term is crucial for B2B buyers, as it affects purchasing decisions and inventory management. Knowing the MOQ can help companies budget and plan their purchases effectively.
3. RFQ (Request for Quotation)
An RFQ is a document sent to suppliers requesting pricing and terms for specific products or services. For silicon carbide buyers, submitting an RFQ can facilitate competitive pricing and ensure they receive the best possible offers tailored to their specifications.
4. Incoterms (International Commercial Terms)
Incoterms are internationally recognized rules that define the responsibilities of buyers and sellers in international transactions. Familiarity with these terms helps B2B buyers understand shipping responsibilities, risk management, and cost implications associated with their purchases.
5. Lead Time
Lead time refers to the amount of time it takes from placing an order until the product is delivered. In the silicon carbide sector, understanding lead times is essential for project planning and inventory management. Buyers should inquire about lead times when negotiating contracts to ensure timely delivery.
By grasping these technical properties and trade terms, international B2B buyers can make informed decisions that align with their operational needs and strategic goals.
Navigating Market Dynamics and Sourcing Trends in the silicon carbide manufacturer Sector
What Are the Current Market Dynamics and Key Trends in the Silicon Carbide Manufacturing Sector?
The silicon carbide (SiC) manufacturing sector is experiencing significant growth, driven by the increasing demand for high-performance materials across various industries, including automotive, electronics, and renewable energy. With the global push towards electrification and energy efficiency, SiC has emerged as a critical component in power electronics, enabling faster switching and higher efficiency in devices such as electric vehicles (EVs) and solar inverters.
International B2B buyers, particularly from Africa, South America, the Middle East, and Europe, should pay attention to the burgeoning trends of automation and digitalization within the manufacturing processes. Advanced technologies such as artificial intelligence (AI) and the Internet of Things (IoT) are being integrated into silicon carbide manufacturing to enhance quality control and operational efficiency. This shift is not only improving production capabilities but also reducing costs, making it essential for buyers to consider suppliers who are investing in these technologies.
Additionally, the market is witnessing a consolidation trend, where larger manufacturers are acquiring smaller firms to expand their technological expertise and market reach. This consolidation can impact pricing and availability, making it vital for international buyers to establish strong relationships with reliable suppliers to ensure consistent sourcing and competitive pricing.
How Can Sustainability and Ethical Sourcing Impact Your Business in the Silicon Carbide Sector?
Sustainability has become a cornerstone of the silicon carbide manufacturing industry, as companies face increasing pressure to minimize their environmental impact. The production of SiC can involve significant energy consumption and waste generation, which has led to a growing emphasis on sustainable manufacturing practices. For B2B buyers, selecting suppliers that prioritize sustainability can enhance brand reputation and align with global sustainability goals.
Ethical sourcing is equally crucial in this sector. Buyers should seek manufacturers that adhere to responsible sourcing standards, ensuring that materials are sourced in a manner that respects human rights and the environment. Certifications such as ISO 14001 for environmental management and ISO 45001 for occupational health and safety are indicators of a supplier’s commitment to ethical practices.
Moreover, the rise of ‘green’ materials and processes in silicon carbide manufacturing is creating new opportunities for businesses. Suppliers that utilize renewable energy sources or recycled materials in their production processes can provide buyers with a competitive edge, meeting the growing consumer demand for environmentally friendly products.
What Is the Brief Evolution of the Silicon Carbide Manufacturing Sector?
The evolution of the silicon carbide manufacturing sector dates back to the early 1900s when it was initially used as an abrasive material. However, its semiconductor properties were recognized in the 1950s, paving the way for its application in electronics. Over the decades, advancements in manufacturing techniques and an increase in the understanding of its properties have led to its widespread use in high-temperature and high-voltage applications.
Today, with the rise of electric vehicles and renewable energy technologies, silicon carbide is at the forefront of modern materials science. Its ability to withstand extreme conditions while providing superior performance makes it indispensable in many high-tech applications. As the industry continues to grow, understanding its history can help international buyers appreciate the technological advancements and potential future developments that could influence their sourcing strategies.
Frequently Asked Questions (FAQs) for B2B Buyers of silicon carbide manufacturer
-
How do I choose the right silicon carbide manufacturer for my business?
Selecting the right silicon carbide manufacturer involves evaluating several key factors. Start by assessing the manufacturer’s experience in the industry and their product range to ensure they can meet your specific needs. Request samples and conduct quality checks to gauge the material’s performance. Additionally, consider their production capacity, compliance with international standards, and customer reviews. It’s also beneficial to understand their supply chain logistics, especially if you are sourcing from regions like Africa or South America, where transportation can be a challenge. -
What customization options are available for silicon carbide products?
Most silicon carbide manufacturers offer various customization options to cater to specific applications. This may include different grades of silicon carbide, particle sizes, and forms (e.g., powders, ceramics). When discussing customization, communicate your technical specifications and the intended application clearly. Some manufacturers may also provide tailored formulations based on your requirements. It’s advisable to collaborate closely during the design phase to ensure the final product meets your performance expectations. -
What are the minimum order quantities (MOQ) for silicon carbide products?
Minimum order quantities can vary significantly among silicon carbide manufacturers, often depending on the product type and the manufacturer’s production capabilities. Generally, MOQs can range from a few kilograms for specialty products to several tons for bulk orders. As an international buyer, it’s crucial to confirm the MOQ beforehand to align your purchasing strategy with your operational needs. If your order volume is low, some manufacturers may offer flexibility, especially for repeat customers or long-term partnerships. -
What payment terms can I expect when purchasing silicon carbide?
Payment terms for silicon carbide purchases typically depend on the manufacturer and the size of the order. Common arrangements include upfront payment, partial payment upon order confirmation, and balance payment before shipping. For international transactions, consider options such as letters of credit or escrow services to mitigate risks. Always clarify payment methods accepted, currency options, and any potential fees associated with international banking to avoid surprises during the transaction process. -
How can I ensure the quality of silicon carbide products?
To ensure product quality, request detailed specifications and certifications from the manufacturer, including compliance with international standards such as ISO 9001. Conducting third-party quality audits or inspections prior to shipment can also provide peace of mind. Additionally, consider establishing a quality assurance agreement that outlines acceptable quality levels and testing procedures. Regular communication with the manufacturer regarding quality expectations is essential for maintaining standards throughout the production process.
-
What logistics considerations should I be aware of when sourcing silicon carbide internationally?
When sourcing silicon carbide internationally, logistics play a crucial role in the overall supply chain. Consider factors such as shipping costs, lead times, and customs regulations in your country. It’s advisable to work with a freight forwarder who understands the specifics of your region, especially if you are importing to Africa or South America, where logistical challenges can arise. Additionally, ensure that the manufacturer provides clear labeling and documentation to facilitate smooth customs clearance. -
What certifications should I look for in a silicon carbide manufacturer?
Certifications are important indicators of a manufacturer’s reliability and product quality. Look for ISO certifications, which demonstrate adherence to international quality management standards. Additionally, certifications specific to your industry, such as RoHS for electronics or automotive standards, may be necessary. Verify the manufacturer’s compliance with environmental regulations as well, particularly if you are sourcing from regions with strict environmental laws, such as Europe. -
How can I build a long-term relationship with a silicon carbide supplier?
Building a long-term relationship with a silicon carbide supplier involves consistent communication, reliability, and mutual respect. Start by establishing clear expectations regarding product quality, delivery timelines, and payment terms. Regularly provide feedback on their products and services to foster improvements. Engaging in collaborative projects or sharing market insights can also strengthen your partnership. Consider negotiating favorable terms for bulk orders or long-term contracts to ensure a stable supply chain while benefiting from cost efficiencies.
Important Disclaimer & Terms of Use
⚠️ Important Disclaimer
The information provided in this guide, including content regarding manufacturers, technical specifications, and market analysis, is for informational and educational purposes only. It does not constitute professional procurement advice, financial advice, or legal advice.
While we have made every effort to ensure the accuracy and timeliness of the information, we are not responsible for any errors, omissions, or outdated information. Market conditions, company details, and technical standards are subject to change.
B2B buyers must conduct their own independent and thorough due diligence before making any purchasing decisions. This includes contacting suppliers directly, verifying certifications, requesting samples, and seeking professional consultation. The risk of relying on any information in this guide is borne solely by the reader.
Strategic Sourcing Conclusion and Outlook for silicon carbide manufacturer
As the silicon carbide market continues to evolve, international B2B buyers must prioritize strategic sourcing to enhance their competitive edge. The key takeaways emphasize the importance of establishing long-term relationships with reliable manufacturers. By leveraging regional insights, buyers from Africa, South America, the Middle East, and Europe can access innovative solutions that cater to their specific needs.
Understanding market dynamics and supplier capabilities is essential for informed decision-making. Buyers should seek manufacturers that not only provide high-quality silicon carbide products but also demonstrate a commitment to sustainability and technological advancement. This proactive approach will enable companies to mitigate risks associated with supply chain disruptions and ensure product availability.
Looking ahead, the silicon carbide industry is poised for growth, driven by increasing demand in sectors such as automotive, electronics, and renewable energy. Now is the time for international B2B buyers to engage with manufacturers, explore collaborative opportunities, and position themselves as leaders in their respective markets. Embrace strategic sourcing today to unlock the full potential of silicon carbide in your operations.