The Ultimate Guide to Stainless Steel Manufacturer (2025)
Introduction: Navigating the Global Market for stainless steel manufacturer
Navigating the complexities of sourcing stainless steel manufacturers can be a daunting task for international B2B buyers, especially when considering the diverse quality standards, cost structures, and logistical challenges across different regions. With the global demand for stainless steel on the rise, businesses in Africa, South America, the Middle East, and Europe (including Germany and Mexico) must equip themselves with the right knowledge to make informed purchasing decisions. This guide addresses these challenges by providing a comprehensive overview of stainless steel manufacturing, including types of stainless steel, their applications in various industries, and insights into supplier vetting processes.
Buyers will find actionable insights on evaluating manufacturers based on quality certifications, production capabilities, and customer reviews, ensuring they choose reliable partners. Additionally, we will explore the cost factors involved in purchasing stainless steel, including pricing trends, shipping costs, and potential tariffs that could impact overall budgets. By understanding these elements, international B2B buyers can navigate the global market confidently, reduce risks, and enhance their procurement strategies. This guide is designed to empower you with the tools and knowledge necessary to make strategic decisions that align with your business needs and goals.
Understanding stainless steel manufacturer Types and Variations
Type Name | Key Distinguishing Features | Primary B2B Applications | Brief Pros & Cons for Buyers |
---|---|---|---|
Flat-Rolled Stainless Steel | Produced in sheets and coils, available in various finishes | Automotive, construction, appliances | Pros: Versatile; easy to fabricate. Cons: May require additional processing. |
Long Products | Includes bars, rods, and wires; often hot or cold drawn | Construction, manufacturing, engineering | Pros: High strength; suitable for structural applications. Cons: Limited shapes and sizes. |
Stainless Steel Pipe & Tube | Available in seamless and welded forms; various diameters | Oil & gas, food processing, HVAC | Pros: Corrosion-resistant; good flow characteristics. Cons: Higher costs for specialty grades. |
Stainless Steel Fittings | Includes elbows, tees, and flanges; designed for joining pipes | Plumbing, construction, industrial systems | Pros: Ensures leak-proof connections. Cons: Complexity in selection for specific applications. |
Custom Stainless Steel Fabrications | Tailored designs based on specific requirements | Aerospace, medical devices, specialized machinery | Pros: Meets unique specifications; enhances operational efficiency. Cons: Higher lead times and costs. |
What are the Key Characteristics of Flat-Rolled Stainless Steel?
Flat-rolled stainless steel is produced in sheets or coils, making it highly adaptable for various manufacturing processes. Its availability in different finishes, such as brushed or polished, allows it to meet aesthetic as well as functional requirements. This type is widely used in the automotive and appliance industries, where both durability and appearance are paramount. Buyers should consider the specific finish and gauge required for their applications, as these factors can significantly impact performance and cost.
How Do Long Products Differ in Stainless Steel Manufacturing?
Long products encompass stainless steel bars, rods, and wires, which can be hot or cold drawn. They are primarily utilized in construction and manufacturing due to their high tensile strength and durability. These products are ideal for structural applications, such as beams or reinforcements. When purchasing long products, buyers should evaluate the specific mechanical properties required for their projects, as well as the availability of custom lengths and diameters.
Why are Stainless Steel Pipe & Tube Essential for B2B Applications?
Stainless steel pipes and tubes are crucial for industries like oil and gas, food processing, and HVAC systems. They can be produced in both seamless and welded forms, offering flexibility in design and application. Their excellent corrosion resistance makes them suitable for transporting fluids under various conditions. Buyers must assess the required specifications, such as pressure ratings and diameter, to ensure compatibility with existing systems and processes.
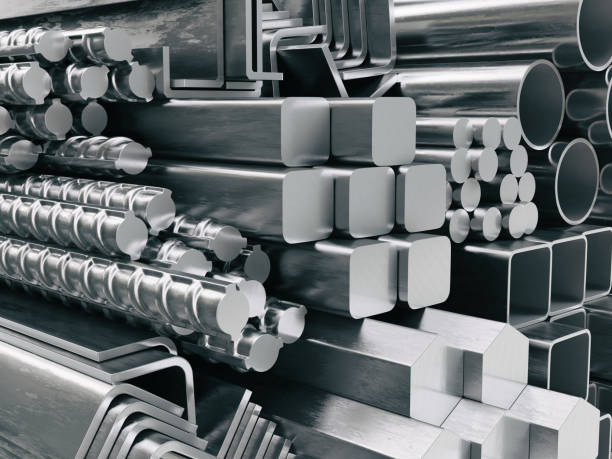
A stock image related to stainless steel manufacturer.
What Role Do Stainless Steel Fittings Play in Industrial Systems?
Stainless steel fittings, including elbows, tees, and flanges, are vital for creating secure connections in piping systems. They are designed to withstand high pressures and prevent leaks, making them essential in plumbing and industrial applications. When sourcing fittings, buyers should consider the compatibility with existing materials and the specific pressure ratings required for their systems. The complexity of selecting the right fittings can pose challenges, emphasizing the need for thorough product knowledge.
How Can Custom Stainless Steel Fabrications Benefit B2B Buyers?
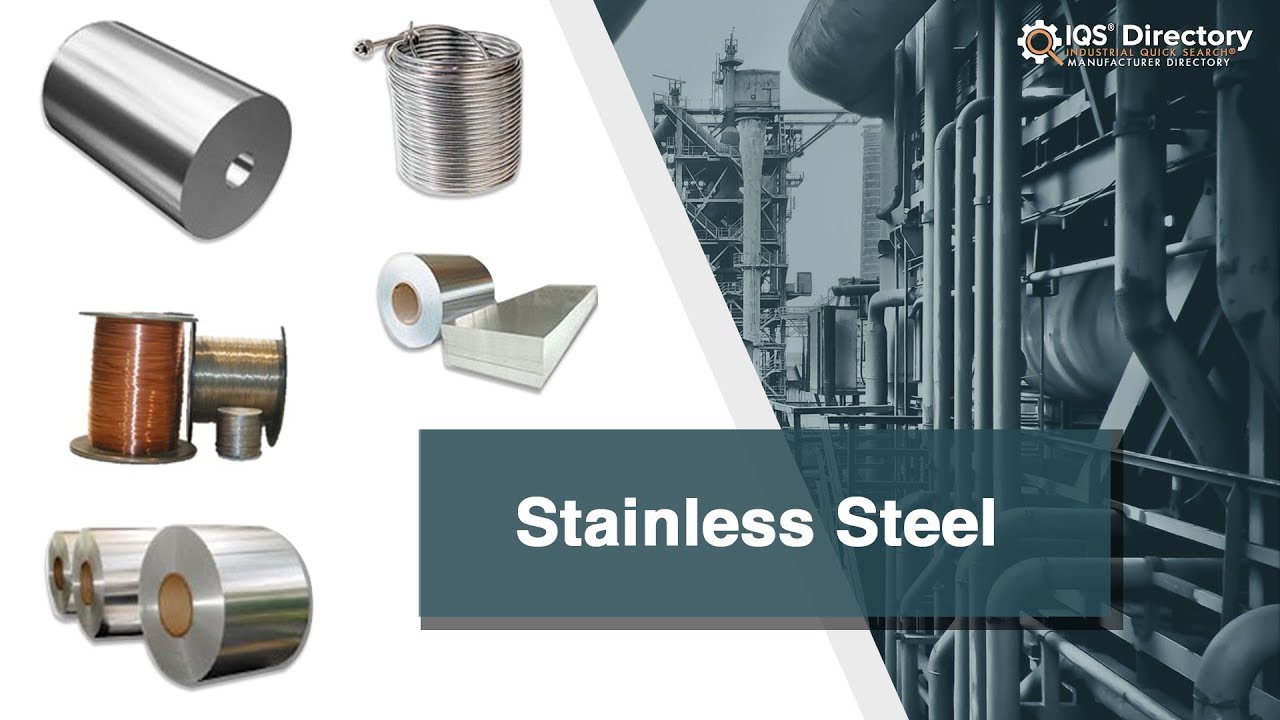
A stock image related to stainless steel manufacturer.
Custom stainless steel fabrications offer tailored solutions to meet unique operational needs, particularly in specialized industries like aerospace and medical devices. These fabrications can enhance efficiency and performance by aligning closely with specific requirements. However, buyers should be mindful of longer lead times and potentially higher costs associated with custom orders. Understanding the exact specifications and potential applications is crucial for maximizing the benefits of such tailored solutions.
Related Video: Steel Types – Stainless Steel Vs Carbon Steel Explained.
Key Industrial Applications of stainless steel manufacturer
Industry/Sector | Specific Application of Stainless Steel Manufacturer | Value/Benefit for the Business | Key Sourcing Considerations for this Application |
---|---|---|---|
Food and Beverage | Equipment for food processing and storage | Ensures hygiene, durability, and compliance with health regulations | Certifications (e.g., FDA, ISO), corrosion resistance, and ease of cleaning |
Construction and Architecture | Structural components and architectural features | Provides strength, aesthetic appeal, and longevity | Load-bearing capacity, local regulations, and design specifications |
Oil and Gas | Pipelines and storage tanks | High resistance to corrosion and extreme temperatures | Material grades (e.g., 316L), welding capabilities, and certifications |
Automotive | Exhaust systems and structural parts | Enhances performance, reduces weight, and improves durability | Supply chain reliability, custom specifications, and compliance with safety standards |
Medical Devices | Surgical instruments and implants | Ensures biocompatibility and sterilization capability | Quality certifications (e.g., ISO 13485), precision engineering, and traceability |
How is Stainless Steel Used in the Food and Beverage Industry?
In the food and beverage sector, stainless steel is crucial for manufacturing equipment like mixers, storage tanks, and transport containers. Its non-reactive nature ensures that food products maintain their taste and quality, while its durability minimizes maintenance costs. International buyers must prioritize sourcing stainless steel that meets health regulations and standards, such as FDA compliance, as well as consider the material’s corrosion resistance and ease of cleaning to ensure long-term functionality.
What Role Does Stainless Steel Play in Construction and Architecture?
Stainless steel is widely utilized in construction for its structural integrity and aesthetic versatility. It is used in beams, columns, and architectural features that require a balance of strength and design. For buyers in Africa and South America, understanding local building codes and material specifications is vital. They should also ensure that the selected stainless steel can withstand environmental conditions, such as humidity and temperature fluctuations, which are prevalent in these regions.
Why is Stainless Steel Important in the Oil and Gas Sector?
In the oil and gas industry, stainless steel is essential for pipelines, storage tanks, and pressure vessels due to its high resistance to corrosion and the ability to withstand extreme temperatures and pressures. Buyers must consider the specific grades of stainless steel, such as 316L, which offer superior performance in harsh environments. Additionally, sourcing from manufacturers with certifications for quality and safety is crucial to ensure compliance with industry standards.
How is Stainless Steel Used in Automotive Applications?
The automotive industry employs stainless steel in exhaust systems, chassis components, and decorative trims due to its strength and lightweight properties. This material enhances vehicle performance while reducing overall weight, contributing to fuel efficiency. Buyers should look for suppliers with a reliable supply chain and the ability to meet custom specifications, as well as compliance with safety and environmental regulations.
What is the Significance of Stainless Steel in Medical Devices?
In the medical field, stainless steel is favored for surgical instruments, implants, and other devices due to its biocompatibility and ability to be sterilized effectively. International buyers, particularly from Europe and the Middle East, must ensure that their suppliers hold relevant quality certifications, such as ISO 13485, and can provide traceability of materials. Precision engineering is also critical to meet stringent performance and safety requirements in medical applications.
Related Video: Seamless Stainless Steel Tubes | How It’s Made
3 Common User Pain Points for ‘stainless steel manufacturer’ & Their Solutions
Scenario 1: Navigating Quality Assurance Issues with Stainless Steel Suppliers
The Problem: One of the significant challenges B2B buyers face when sourcing stainless steel from manufacturers is ensuring consistent quality. Buyers may encounter issues such as variations in material specifications, non-compliance with industry standards, or discrepancies between the received product and what was promised. This can lead to production delays, increased costs, and potential safety hazards, especially in industries like construction and manufacturing where material integrity is critical.
The Solution: To overcome quality assurance issues, buyers should implement a comprehensive supplier evaluation process. Start by developing a detailed specifications document that outlines the exact requirements for the stainless steel needed, including grades, dimensions, and treatment processes. Additionally, buyers should request certifications from suppliers, such as ISO 9001 or specific mill test reports that demonstrate compliance with international standards. Establishing a robust communication channel with the manufacturer for regular updates and potential on-site audits can also help in maintaining quality assurance. Consider establishing long-term partnerships with a few vetted suppliers rather than frequently switching manufacturers to foster better quality control over time.
Scenario 2: Managing Supply Chain Disruptions in Stainless Steel Procurement
The Problem: International B2B buyers often face supply chain disruptions due to geopolitical factors, natural disasters, or logistical challenges. For instance, a sudden increase in demand or a shortage of raw materials can lead to delays in stainless steel delivery, affecting production schedules and leading to financial losses. Buyers from regions like Africa and South America may also experience challenges due to infrastructure issues, making timely delivery even more critical.
The Solution: To mitigate supply chain disruptions, buyers should diversify their supplier base by engaging multiple manufacturers across different regions. This strategy helps to ensure that if one supplier faces issues, others can fill the gap. Implementing a just-in-time inventory system can also be beneficial, allowing companies to keep minimal stock while ensuring that they can quickly reorder as needed. Additionally, leveraging technology for real-time tracking of shipments and maintaining open lines of communication with suppliers can help anticipate potential delays and adjust production schedules accordingly. Building strong relationships with logistics providers can also facilitate smoother transportation and delivery processes.
Scenario 3: Understanding Pricing Structures for Stainless Steel Products
The Problem: Buyers often find it challenging to navigate the complex pricing structures of stainless steel products. Prices can fluctuate based on various factors, including raw material costs, market demand, and manufacturing processes. This volatility can lead to budget overruns and make it difficult for buyers to forecast expenses accurately, particularly for large projects or contracts.
The Solution: To tackle pricing challenges, buyers should conduct thorough market research to understand the factors that influence stainless steel pricing. Establishing a clear pricing framework with suppliers, including fixed pricing agreements for long-term contracts, can provide predictability. Engaging in negotiations to include clauses for price adjustments based on material cost fluctuations can also safeguard against unexpected price hikes. Additionally, buyers can consider utilizing forward contracts or hedging strategies to lock in prices for future purchases, providing more stability in budgeting. Regularly reviewing and analyzing pricing data will help buyers make informed decisions and identify the best times to purchase, ultimately leading to cost savings.
Strategic Material Selection Guide for stainless steel manufacturer
What Are the Key Materials Used in Stainless Steel Manufacturing?
When selecting materials for stainless steel manufacturing, international B2B buyers must consider various grades and types to ensure optimal performance for their specific applications. Here, we will analyze four common stainless steel materials: 304, 316, 410, and 430. Each material has unique properties, advantages, and limitations that can significantly impact product performance and suitability.
How Does Stainless Steel 304 Perform in Various Applications?
Stainless steel 304 is one of the most widely used grades due to its excellent corrosion resistance and good formability. It can withstand temperatures up to 870°C (1600°F) and is suitable for a range of applications, including food processing, chemical equipment, and architectural structures.
Pros: It offers high durability, is relatively easy to fabricate, and has a lower cost compared to other stainless steel grades.
Cons: However, it is less resistant to chlorides, which can lead to pitting corrosion in marine environments or chemical processing applications.
Impact on Application: Buyers in coastal regions or industries dealing with corrosive chemicals should consider this limitation when selecting 304 stainless steel.
What Are the Benefits of Using Stainless Steel 316?
Stainless steel 316 is often regarded as the “marine grade” due to its enhanced corrosion resistance, especially against chlorides. It can handle temperatures up to 925°C (1700°F) and is commonly used in marine environments, pharmaceuticals, and food processing.
Pros: Its superior resistance to corrosion and high-temperature strength make it ideal for harsh environments.
Cons: The primary drawback is its higher cost compared to 304, which may be a significant consideration for budget-conscious buyers.
Impact on Application: For international buyers from regions with high humidity or saline conditions, 316 stainless steel is often the preferred choice to ensure longevity and reliability.
Why Choose Stainless Steel 410 for Specific Applications?
Stainless steel 410 is a martensitic stainless steel known for its hardness and wear resistance. It is suitable for applications requiring moderate corrosion resistance and high strength, such as cutlery, automotive components, and industrial equipment.
Pros: It is relatively inexpensive and can be heat-treated to enhance its hardness.
Cons: Its corrosion resistance is lower than that of austenitic grades like 304 and 316, making it unsuitable for highly corrosive environments.
Impact on Application: Buyers in industries where wear resistance is critical but exposure to corrosive elements is limited may find 410 stainless steel to be a cost-effective solution.
What Are the Key Considerations for Using Stainless Steel 430?
Stainless steel 430 is a ferritic grade known for its good corrosion resistance and formability. It is commonly used in automotive applications, kitchen appliances, and decorative items.
Pros: Its lower cost and decent corrosion resistance make it an attractive option for non-critical applications.
Cons: However, it has limited weldability and is less resistant to corrosion than austenitic grades.
Impact on Application: Buyers should consider the specific media compatibility and environmental conditions when opting for 430 stainless steel, particularly in applications where aesthetics and moderate corrosion resistance are required.
Summary Table of Stainless Steel Materials
Material | Typical Use Case for stainless steel manufacturer | Key Advantage | Key Disadvantage/Limitation | Relative Cost (Low/Med/High) |
---|---|---|---|---|
304 | Food processing, chemical equipment, architectural structures | Excellent corrosion resistance | Less resistant to chlorides | Medium |
316 | Marine environments, pharmaceuticals, food processing | Superior corrosion resistance | Higher cost than 304 | High |
410 | Cutlery, automotive components, industrial equipment | High hardness and wear resistance | Lower corrosion resistance | Low |
430 | Automotive applications, kitchen appliances, decorative items | Lower cost, good formability | Limited weldability | Low |
This strategic material selection guide provides international B2B buyers with essential insights into the various stainless steel materials available, enabling informed decisions that align with their specific application needs and regional conditions.
In-depth Look: Manufacturing Processes and Quality Assurance for stainless steel manufacturer
What Are the Main Stages in the Manufacturing Process of Stainless Steel?
The manufacturing process of stainless steel involves several key stages, each critical to ensuring the final product meets the necessary specifications and quality standards. Understanding these stages can help international B2B buyers assess the capabilities of a stainless steel supplier.
-
Material Preparation
The first stage involves selecting and preparing raw materials, primarily stainless steel scrap or ingots. The materials are often melted in an electric arc furnace (EAF) to achieve the desired chemical composition. This process may include the addition of alloying elements such as nickel and molybdenum to enhance corrosion resistance and strength. -
Forming
Once the material is melted and refined, it is cast into slabs, blooms, or billets. These are then subjected to various forming techniques, such as hot rolling or cold rolling, to shape the stainless steel into sheets, plates, or coils. Hot rolling is typically employed for larger dimensions and improved mechanical properties, while cold rolling provides a smoother finish and tighter tolerances. -
Assembly
In cases where stainless steel components are required, parts may be cut, shaped, and welded together. Advanced techniques such as laser cutting, plasma cutting, and welding (TIG or MIG) are commonly used to ensure precision and strength in the final assembly. -
Finishing
The final stage includes surface treatment processes like pickling, passivation, and polishing. These treatments are essential for removing impurities, enhancing corrosion resistance, and achieving the desired aesthetic finish. Techniques such as abrasive blasting or electro-polishing may also be utilized, depending on the end-use application.
Which Key Techniques Are Used in Stainless Steel Manufacturing?
B2B buyers should be aware of the various techniques employed in the manufacturing process, as these can significantly affect the quality and performance of stainless steel products.
- Casting Techniques: Continuous casting is widely used for producing slabs and billets, ensuring uniformity in thickness and composition.
- Rolling Techniques: Hot rolling allows for the shaping of large sheets while cold rolling enhances surface finish and dimensional accuracy.
- Welding Techniques: Different welding methods, including tungsten inert gas (TIG) and metal inert gas (MIG) welding, are employed based on the application and required strength.
- Surface Treatment Techniques: The choice of surface treatment, such as passivation, enhances the material’s resistance to corrosion, making it suitable for various applications, especially in industries like food processing and pharmaceuticals.
How Is Quality Assurance Implemented in Stainless Steel Manufacturing?
Quality assurance (QA) is vital in the manufacturing of stainless steel to ensure that products meet international and industry-specific standards. Here’s how it is typically implemented.
-
International Standards
Compliance with standards such as ISO 9001 is crucial for manufacturers aiming to assure quality management systems. This certification indicates that a company follows best practices in quality control and continuous improvement. -
Industry-Specific Standards
Depending on the application, additional certifications may be required. For example:
– CE Marking: Indicates conformity with European health, safety, and environmental protection standards.
– API Standards: Particularly relevant for manufacturers supplying the oil and gas industry. -
Quality Control Checkpoints
Effective QA processes include multiple quality control checkpoints throughout the manufacturing cycle:
– Incoming Quality Control (IQC): Assessing the quality of raw materials before processing.
– In-Process Quality Control (IPQC): Monitoring the manufacturing process to ensure compliance with specifications.
– Final Quality Control (FQC): Conducting comprehensive inspections of finished products before shipment.
What Common Testing Methods Are Used to Ensure Quality?
Testing is a fundamental aspect of quality assurance in stainless steel manufacturing. B2B buyers should inquire about the following testing methods:
- Mechanical Testing: Includes tensile tests, hardness tests, and impact tests to evaluate the material’s strength and durability.
- Chemical Analysis: Spectroscopic methods are employed to verify the composition of stainless steel, ensuring it meets required standards.
- Non-Destructive Testing (NDT): Techniques such as ultrasonic testing and X-ray inspection help detect internal flaws without damaging the material.
- Corrosion Testing: Accelerated corrosion tests can be conducted to assess how well the stainless steel will perform in real-world conditions.
How Can B2B Buyers Verify Supplier Quality Control?
For international B2B buyers, verifying the quality control measures of a stainless steel manufacturer is essential to ensure product reliability. Here are actionable steps to conduct this verification:
-
Supplier Audits: Conduct regular audits of potential suppliers to assess their manufacturing processes, quality control systems, and compliance with international standards.
-
Request Quality Reports: Ask suppliers to provide detailed quality control reports, including results from mechanical testing, chemical analysis, and inspection records.
-
Third-Party Inspections: Engage third-party inspection agencies to conduct independent quality assessments before finalizing orders. This can help ensure that the products meet the required specifications and standards.
-
Certifications and Documentation: Verify the authenticity of certifications such as ISO 9001 or CE marking. Ensure that suppliers can provide documentation that demonstrates compliance with industry-specific standards.
What Are the Quality Control and Certification Nuances for International Buyers?
International B2B buyers must navigate various quality control and certification nuances when sourcing stainless steel products. Here are some critical considerations:
-
Regional Compliance: Different regions may have specific requirements regarding certifications and quality standards. For example, European buyers might prioritize CE marking, while buyers in the Middle East may focus on compliance with local regulations.
-
Language and Documentation: Ensure that all quality assurance documentation is available in a language that can be easily understood. Misinterpretation of technical specifications can lead to costly errors.
- Cultural Differences: Understanding cultural attitudes towards quality and compliance can help facilitate better communication and collaboration with suppliers, especially in regions like Africa and South America.
By understanding these manufacturing processes and quality assurance practices, B2B buyers can make informed decisions when selecting a stainless steel supplier, ensuring they receive high-quality products that meet their specific needs.
Practical Sourcing Guide: A Step-by-Step Checklist for ‘stainless steel manufacturer’
In today’s global marketplace, procuring stainless steel materials requires a strategic approach to ensure quality, reliability, and value for money. This step-by-step checklist serves as a practical guide for international B2B buyers, particularly those from Africa, South America, the Middle East, and Europe, to successfully source stainless steel manufacturers.
Step 1: Define Your Technical Specifications
Before initiating the sourcing process, clearly outline the technical specifications of the stainless steel products you need. This includes dimensions, grades (e.g., 304, 316), and any specific compliance standards relevant to your industry.
– Why It Matters: A precise definition helps streamline the selection process and ensures that suppliers can meet your exact requirements, reducing the likelihood of costly errors later.
Step 2: Research Potential Suppliers
Conduct thorough research to identify potential stainless steel manufacturers that align with your specifications. Utilize industry directories, trade shows, and online platforms to compile a list of candidates.
– Tips for Effective Research:
– Focus on suppliers with a proven track record in your region.
– Look for customer reviews and testimonials to gauge reliability.
Step 3: Evaluate Supplier Certifications
Verify that potential suppliers possess the necessary certifications and accreditations, such as ISO 9001 for quality management and specific industry-related standards.
– Importance of Certifications: Certifications are indicators of a manufacturer’s commitment to quality and compliance, which is crucial for maintaining safety and performance in your applications.
Step 4: Request Samples and Product Specifications
Once you have shortlisted suppliers, request product samples and detailed specifications. This will allow you to assess the quality of the stainless steel products firsthand.
– What to Look For:
– Check for consistency in quality and adherence to the specified grades.
– Evaluate the surface finish and mechanical properties to ensure they meet your standards.
Step 5: Analyze Pricing and Payment Terms
Gather detailed quotes from potential suppliers and analyze pricing structures, including payment terms and any additional costs for shipping and customs.
– Why Pricing Matters: Understanding the total cost of ownership helps in making informed decisions, ensuring that you stay within budget while also considering quality.
Step 6: Conduct Supplier Audits
If possible, conduct on-site audits of the shortlisted suppliers. This helps verify their production capabilities, quality control processes, and overall operational standards.
– Benefits of Audits:
– Direct observation allows for deeper insights into the supplier’s practices.
– It builds a relationship and trust, which is vital for long-term partnerships.
Step 7: Establish Communication and Support
Ensure that the supplier has robust communication channels and support systems in place for after-sales service. Clear communication is essential for addressing any issues that may arise during production or delivery.
– Key Considerations:
– Assess their responsiveness and willingness to provide ongoing support.
– Establish points of contact for technical assistance and order tracking.
By following this structured checklist, B2B buyers can navigate the complexities of sourcing stainless steel manufacturers effectively, ensuring they make informed decisions that align with their business needs.
Comprehensive Cost and Pricing Analysis for stainless steel manufacturer Sourcing
What Are the Key Cost Components in Stainless Steel Manufacturing?
When sourcing stainless steel, understanding the cost structure is crucial for international buyers. The primary cost components include:
-
Materials: The cost of raw materials, primarily nickel, chromium, and iron, significantly impacts the overall pricing. Prices fluctuate based on global market conditions, so buyers should stay informed about market trends.
-
Labor: Labor costs vary by region. In countries with higher labor costs, such as Germany, the price of stainless steel may be higher compared to regions in Africa or South America where labor is less expensive.
-
Manufacturing Overhead: This includes expenses related to the production facilities, utilities, and administrative costs. Efficient manufacturing processes can help reduce overhead, allowing for more competitive pricing.
-
Tooling: Costs related to the equipment and tools used in production can be significant, especially for custom orders. Buyers should inquire about tooling costs to avoid unexpected expenses.
-
Quality Control (QC): Implementing rigorous QC measures ensures product reliability and safety but adds to the overall cost. Certifications like ISO can enhance product value but may increase the price.
-
Logistics: Shipping and handling costs are particularly important for international buyers. Factors such as distance, shipping method, and customs duties should be considered in the total cost.
-
Margin: Manufacturers typically add a profit margin to cover all costs and ensure sustainability. This margin can vary based on supplier reputation and market demand.
How Do Price Influencers Affect Stainless Steel Sourcing Decisions?
Several factors influence the pricing of stainless steel, which buyers should consider:
-
Volume and Minimum Order Quantity (MOQ): Purchasing in larger quantities often leads to discounts. Buyers should negotiate MOQs that align with their needs while maximizing cost savings.
-
Specifications and Customization: Custom specifications can drive up costs due to additional processing and material requirements. Clearly defining needs can help manage these expenses.
-
Material Quality and Certifications: Higher quality materials and relevant certifications will generally incur higher costs. Buyers should weigh the importance of these factors against their budget.
-
Supplier Factors: The supplier’s reputation, reliability, and production capabilities can influence price. Conducting due diligence on potential suppliers can lead to better pricing and service.
-
Incoterms: Understanding Incoterms (International Commercial Terms) is vital for international transactions. They define the responsibilities of buyers and sellers regarding shipping, insurance, and tariffs, impacting the total landed cost.
What Tips Can Help Buyers Negotiate Better Prices in the Stainless Steel Market?
For international B2B buyers, particularly those from Africa, South America, the Middle East, and Europe, here are actionable tips for effective negotiation:
-
Research Market Prices: Stay informed about current market rates for stainless steel. Use resources like industry reports and supplier quotes to establish a baseline for negotiations.
-
Focus on Total Cost of Ownership (TCO): Consider all costs associated with sourcing stainless steel, including shipping, tariffs, and storage. A lower upfront price may not always equate to lower overall costs.
-
Build Long-term Relationships: Establishing strong relationships with suppliers can lead to better pricing and service. Regular communication and trust can foster favorable terms over time.
-
Be Transparent About Your Needs: Clearly communicate your requirements and expectations to suppliers. This transparency can help them provide tailored solutions that meet your budget.
-
Leverage Competitive Bids: Soliciting quotes from multiple suppliers can create competition, leading to better pricing. However, ensure that comparisons are based on equivalent specifications and terms.
Conclusion: Why Understanding Cost and Pricing is Essential for International Buyers
Navigating the complexities of stainless steel pricing is vital for international buyers to make informed sourcing decisions. By understanding cost components, recognizing price influencers, and employing strategic negotiation tactics, businesses can optimize their procurement processes and ensure they achieve the best possible value for their investment. It is essential to approach these negotiations with a clear understanding of the market dynamics and a focus on long-term supplier partnerships.
Alternatives Analysis: Comparing stainless steel manufacturer With Other Solutions
When considering the procurement of materials for industrial applications, it is essential for international B2B buyers to explore viable alternatives to traditional stainless steel manufacturing. This analysis will compare stainless steel with two alternatives: aluminum alloy manufacturing and polymer composites. Each of these materials has unique properties that can be advantageous depending on the specific requirements of the project.
Comparison Table of Stainless Steel and Alternatives
Comparison Aspect | Stainless Steel Manufacturer | Aluminum Alloy Manufacturing | Polymer Composites |
---|---|---|---|
Performance | High strength, corrosion-resistant | Lightweight, good strength-to-weight ratio | High strength, corrosion-resistant, customizable |
Cost | Moderate to high | Generally lower than stainless steel | Variable, can be high for specialized composites |
Ease of Implementation | Requires specialized processing | Easier to work with, can be extruded | Requires specialized knowledge for molding |
Maintenance | Low maintenance, durable | Moderate, can corrode in harsh environments | Low maintenance, but can degrade under UV exposure |
Best Use Case | Heavy-duty applications, food processing | Aerospace, automotive parts | Consumer goods, medical devices |
What Are the Advantages and Disadvantages of Aluminum Alloy Manufacturing?
Aluminum alloys are often favored for their lightweight nature and excellent strength-to-weight ratio. This makes them particularly useful in industries such as aerospace and automotive, where reducing weight can lead to significant fuel savings and improved performance. However, while aluminum is generally less expensive than stainless steel, it can be more susceptible to corrosion in certain environments unless treated. Additionally, the ease of implementation is a plus, as aluminum can be extruded and shaped using less specialized equipment compared to stainless steel.
How Do Polymer Composites Compare to Stainless Steel?
Polymer composites are increasingly being used in various sectors due to their high strength and corrosion resistance. They are particularly advantageous for consumer goods and medical devices where customization and light weight are crucial. The main downside of polymer composites is the potential for degradation when exposed to UV light and the need for specialized knowledge during the manufacturing process. While the initial costs can vary, high-performance composites can be more expensive than stainless steel, particularly for specialized applications.
Conclusion: How Can B2B Buyers Choose the Right Solution?
Choosing the right material is pivotal for B2B buyers aiming to optimize performance and cost-effectiveness. Buyers should evaluate their specific needs—such as strength, weight, environmental exposure, and budget constraints—before making a decision. Stainless steel remains a strong contender for heavy-duty applications, while aluminum alloys and polymer composites may offer better solutions for projects requiring lighter materials or specialized properties. A thorough understanding of each option’s advantages and limitations will empower buyers to make informed choices that align with their operational requirements.
Essential Technical Properties and Trade Terminology for stainless steel manufacturer
What Are the Key Technical Properties of Stainless Steel for B2B Buyers?
When sourcing stainless steel, understanding its technical properties is crucial for B2B buyers. Here are some essential specifications that can significantly impact purchasing decisions:
-
Material Grade
Stainless steel is categorized into various grades based on its composition and properties. Common grades include 304, 316, and 410. Grade 304 is known for its excellent corrosion resistance and is widely used in food processing, while Grade 316 offers better resistance to chlorides, making it ideal for marine applications. Understanding these grades helps buyers select the right material for specific applications. -
Mechanical Properties
Mechanical properties such as tensile strength, yield strength, and elongation are vital indicators of a material’s performance. For instance, tensile strength measures how much force a material can withstand while being stretched. Buyers should consider these properties when evaluating the suitability of stainless steel for their manufacturing processes. -
Tolerance
Tolerance refers to the allowable deviation in dimensions and weight of the stainless steel products. Tight tolerances are crucial for applications requiring precise fit and function, such as in the automotive or aerospace industries. Knowing the required tolerances can help buyers avoid costly rework or production delays. -
Corrosion Resistance
One of the most significant advantages of stainless steel is its resistance to corrosion. This property is influenced by the alloying elements, such as chromium and nickel. Buyers must assess the environmental conditions their products will face to ensure the selected stainless steel has adequate corrosion resistance for longevity and performance. -
Finish Type
The finish of stainless steel can affect its appearance and performance. Common finishes include brushed, polished, and matte. The finish chosen can influence not only aesthetics but also how the material interacts with its environment, including resistance to staining and ease of cleaning.
Which Trade Terms Should B2B Buyers Understand When Sourcing Stainless Steel?
Familiarity with trade terminology can streamline the procurement process and enhance communication with suppliers. Here are some key terms that B2B buyers should know:
-
OEM (Original Equipment Manufacturer)
This term refers to a company that produces parts or equipment that may be marketed by another manufacturer. Understanding OEM relationships is vital for buyers looking for specific components or materials that fit seamlessly into their existing products. -
MOQ (Minimum Order Quantity)
MOQ is the smallest quantity of a product that a supplier is willing to sell. This term is particularly important for international buyers who need to manage inventory costs and ensure they can meet production demands without overstocking. -
RFQ (Request for Quotation)
An RFQ is a document sent to suppliers requesting pricing and terms for specific quantities of products. This term is essential for buyers to ensure they receive competitive pricing and to facilitate negotiations with multiple suppliers. -
Incoterms (International Commercial Terms)
Incoterms are a set of predefined commercial terms published by the International Chamber of Commerce. They define the responsibilities of buyers and sellers in international transactions, including shipping, insurance, and tariffs. Familiarity with these terms can help buyers avoid misunderstandings and ensure smooth logistics. -
Lead Time
Lead time refers to the time it takes from placing an order to receiving the product. Understanding lead times is crucial for planning production schedules and managing customer expectations, particularly in industries with tight deadlines.
By comprehending these technical properties and trade terminologies, B2B buyers can make informed decisions when sourcing stainless steel, ultimately leading to better procurement outcomes and enhanced supply chain efficiency.
Navigating Market Dynamics and Sourcing Trends in the stainless steel manufacturer Sector
What Are the Current Market Dynamics and Key Trends in the Stainless Steel Manufacturing Sector?
The stainless steel manufacturing sector is influenced by a multitude of global drivers that shape its dynamics. One of the most significant factors is the increasing demand for stainless steel across various industries, including automotive, construction, and food processing. This demand is further propelled by urbanization in emerging markets, particularly in Africa and South America, where infrastructural developments are on the rise. Additionally, technological advancements, such as automation and data analytics, are transforming manufacturing processes, enhancing efficiency and reducing costs.
In terms of sourcing trends, international B2B buyers are increasingly leveraging digital platforms to streamline procurement processes. E-commerce solutions and B2B marketplaces are becoming essential tools, facilitating easier access to suppliers and enhancing transparency in transactions. Moreover, the trend toward localization of supply chains is gaining traction, as companies seek to mitigate risks associated with global supply disruptions. This is particularly relevant for buyers in the Middle East and Europe, where geopolitical factors can impact sourcing strategies.
How Does Sustainability and Ethical Sourcing Impact B2B in the Stainless Steel Industry?
Sustainability is a growing concern for international B2B buyers in the stainless steel sector. The environmental impact of manufacturing processes, including carbon emissions and resource depletion, has led to an increasing demand for sustainable practices. Buyers are now more inclined to partner with manufacturers that prioritize eco-friendly production methods and adhere to stringent environmental regulations.
Ethical sourcing is equally important, as companies seek to ensure that their supply chains are free from unethical practices such as child labor and exploitation. Certifications like ISO 14001 and responsible sourcing initiatives are becoming critical factors in the decision-making process for B2B buyers. These certifications not only demonstrate a commitment to sustainability but also enhance brand reputation, making ethical sourcing a vital aspect of modern procurement strategies.
What Is the Evolution of the Stainless Steel Manufacturing Sector and Its Relevance for B2B Buyers?
The stainless steel manufacturing sector has evolved significantly since its inception in the early 20th century. Initially used primarily in kitchenware and cutlery, stainless steel’s unique properties—such as corrosion resistance and durability—have led to its adoption in a myriad of applications. The post-World War II industrial boom saw a surge in demand, particularly in construction and automotive industries.
Today, the sector is characterized by innovation and diversification, with advancements in alloy compositions and manufacturing techniques driving performance improvements. For B2B buyers, understanding this evolution is crucial, as it provides insights into product capabilities and the potential for future developments. As the industry continues to adapt to changing market demands, staying informed about historical trends can help buyers make strategic sourcing decisions that align with their business goals.
Frequently Asked Questions (FAQs) for B2B Buyers of stainless steel manufacturer
-
How do I ensure I choose the right stainless steel manufacturer for my business needs?
To select the right stainless steel manufacturer, begin by assessing their reputation and experience in the industry. Look for certifications such as ISO 9001, which indicates quality management standards. Request samples of their products to evaluate quality and consider their production capabilities to ensure they can meet your specific requirements. Additionally, gather client testimonials and case studies to understand their reliability and service levels. -
What are the key factors to consider when vetting a stainless steel supplier?
When vetting a stainless steel supplier, consider their production capacity, quality control processes, and compliance with international standards. It’s crucial to inquire about their supply chain reliability and delivery timelines. Ensure they provide transparent communication and support for any customization needs. Furthermore, evaluate their financial stability to mitigate risks associated with long-term partnerships.
-
What customization options are available for stainless steel products?
Many stainless steel manufacturers offer a range of customization options, including different grades of stainless steel, finishes, and dimensions. Some may also provide services such as cutting, welding, and surface treatments. Discuss your specific requirements upfront to see how flexible the manufacturer is in accommodating bespoke orders. This can lead to a more tailored solution that meets your exact needs. -
What is the typical minimum order quantity (MOQ) for stainless steel products?
The minimum order quantity (MOQ) for stainless steel products can vary significantly among manufacturers. Generally, MOQs range from 1 ton to several tons, depending on the type of product and the manufacturer’s capabilities. If your order volume is low, consider negotiating with the supplier or looking for manufacturers that specialize in smaller batches to avoid incurring excessive costs. -
What payment terms should I expect when working with international stainless steel suppliers?
Payment terms for international stainless steel suppliers typically include options like advance payment, letter of credit, or payment upon delivery. It’s important to discuss and agree on payment terms that are mutually beneficial and secure for both parties. Be aware of any additional costs such as shipping, tariffs, and taxes that may affect the overall pricing. -
How can I ensure quality assurance when purchasing stainless steel products?
To ensure quality assurance, request detailed product specifications and certifications from the manufacturer. Inquire about their quality control processes and whether they conduct third-party inspections. Consider arranging for an on-site visit to the manufacturing facility if possible. Establishing clear communication regarding your quality expectations will also help maintain standards throughout the production process. -
What logistics considerations should I keep in mind when importing stainless steel?
When importing stainless steel, consider logistics factors such as shipping methods, lead times, and customs regulations. Research the best freight options—air, sea, or land—based on your delivery timelines and budget. Ensure that the manufacturer can provide the necessary documentation for customs clearance and be aware of any import duties that may apply in your country.
- How do trade agreements affect the importation of stainless steel products?
Trade agreements can significantly impact the cost and ease of importing stainless steel products. Agreements between countries may lower tariffs, streamline customs processes, and provide preferential treatment for certain goods. Stay informed about the trade policies and agreements relevant to your region and the countries you are sourcing from, as these can affect pricing and availability.
Important Disclaimer & Terms of Use
⚠️ Important Disclaimer
The information provided in this guide, including content regarding manufacturers, technical specifications, and market analysis, is for informational and educational purposes only. It does not constitute professional procurement advice, financial advice, or legal advice.
While we have made every effort to ensure the accuracy and timeliness of the information, we are not responsible for any errors, omissions, or outdated information. Market conditions, company details, and technical standards are subject to change.
B2B buyers must conduct their own independent and thorough due diligence before making any purchasing decisions. This includes contacting suppliers directly, verifying certifications, requesting samples, and seeking professional consultation. The risk of relying on any information in this guide is borne solely by the reader.
Strategic Sourcing Conclusion and Outlook for stainless steel manufacturer
In the realm of stainless steel manufacturing, strategic sourcing stands as a cornerstone for international B2B buyers, particularly those operating in diverse markets such as Africa, South America, the Middle East, and Europe. By focusing on key elements such as supplier reliability, quality assurance, and cost-effectiveness, businesses can enhance their procurement strategies to achieve greater operational efficiency and competitive advantage.
What Are the Key Benefits of Strategic Sourcing for B2B Buyers?
Strategic sourcing not only streamlines supply chain management but also fosters long-term partnerships with suppliers, ensuring consistent quality and innovation. For buyers in regions like Germany and Mexico, leveraging local suppliers can mitigate risks associated with logistics and tariffs, thereby enhancing supply chain resilience. Additionally, understanding market trends and regulatory requirements in various regions can help businesses make informed sourcing decisions that align with their operational goals.
How Can International Buyers Prepare for Future Trends?
Looking ahead, the stainless steel industry is poised for growth driven by sustainability and technological advancements. B2B buyers should prioritize suppliers who demonstrate a commitment to eco-friendly practices and invest in innovative manufacturing processes. Engaging in proactive sourcing strategies will not only position businesses to adapt to market changes but also to seize new opportunities that arise in this evolving landscape.
In conclusion, international B2B buyers are encouraged to embrace strategic sourcing as a vital tool for navigating the complexities of the stainless steel market. By doing so, they can secure their supply chains, optimize costs, and ultimately drive growth in their respective sectors. Start exploring strategic partnerships today to build a more resilient and innovative future.