The Ultimate Guide to Telecommunication Manufacturer (2025)
Introduction: Navigating the Global Market for telecommunication manufacturer
The telecommunications manufacturing sector is a cornerstone of modern connectivity, yet sourcing the right telecom equipment can be a daunting challenge for B2B buyers, particularly in regions like Africa, South America, the Middle East, and Europe. With diverse technologies and applications ranging from fiber optics to wireless communications, understanding the landscape is crucial for making informed purchasing decisions. This guide aims to demystify the complexities of the telecommunications manufacturing market by providing a comprehensive overview of various types of equipment, their applications, and essential supplier vetting processes.
By exploring key topics such as cost structures, technological advancements, and market trends, this guide equips international buyers with the insights needed to navigate the global market effectively. Buyers will gain an understanding of how to assess suppliers, evaluate product specifications, and identify the best solutions tailored to their operational needs.
As telecommunication demands continue to evolve, particularly with the rise of 5G and other innovations, staying informed is more critical than ever. This guide serves as an essential resource for decision-makers seeking to enhance their telecommunications capabilities, ultimately empowering them to build stronger, more connected enterprises. Whether you are looking to expand your existing infrastructure or invest in new technologies, this guide will provide you with the knowledge necessary to make sound, strategic decisions.
Understanding telecommunication manufacturer Types and Variations
Type Name | Key Distinguishing Features | Primary B2B Applications | Brief Pros & Cons for Buyers |
---|---|---|---|
Network Equipment Manufacturers | Produce devices like routers, switches, and modems. | Corporate WANs, data centers, ISPs | Pros: High reliability; Cons: High upfront costs. |
Wireless Communication Providers | Specialize in mobile and wireless technology solutions. | Mobile networks, IoT applications | Pros: Flexibility; Cons: Variable coverage quality. |
Telecom Infrastructure Suppliers | Focus on building and maintaining telecom networks. | National telecom networks, large enterprises | Pros: Comprehensive solutions; Cons: Long deployment times. |
Software-Defined Networking (SDN) | Offer software solutions for network management and optimization. | Cloud services, large-scale data management | Pros: Scalability; Cons: Requires skilled personnel. |
Managed Service Providers (MSPs) | Provide outsourced telecom services and support. | SMEs, multi-location businesses | Pros: Cost-effective; Cons: Less control over services. |
What Are the Key Characteristics of Network Equipment Manufacturers?
Network Equipment Manufacturers (NEMs) design and produce essential hardware such as routers, switches, and modems that facilitate data transmission in corporate and internet service provider (ISP) networks. Their products are characterized by high reliability and performance, making them suitable for data centers and wide area networks (WANs). When considering a purchase, B2B buyers should evaluate the manufacturer‘s reputation, warranty options, and ongoing support services to ensure long-term satisfaction.
How Do Wireless Communication Providers Differ from Other Manufacturers?
Wireless Communication Providers focus on mobile and wireless technology solutions, including cellular networks and Internet of Things (IoT) applications. Their offerings are distinguished by their ability to provide flexible connectivity options, which are vital for businesses requiring mobility. However, coverage quality can vary significantly by region, making it essential for buyers to assess local service availability and network performance before making a commitment.
What Role Do Telecom Infrastructure Suppliers Play in the Industry?
Telecom Infrastructure Suppliers specialize in the construction and maintenance of telecom networks, serving national and large-scale enterprise needs. They offer a comprehensive range of services, from building physical infrastructure to providing ongoing maintenance. While these suppliers can deliver robust solutions, B2B buyers must be prepared for potentially lengthy deployment times and should consider the supplier‘s experience with similar projects in their region.
Why Is Software-Defined Networking (SDN) Important for Modern Telecommunications?
Software-Defined Networking (SDN) manufacturers provide innovative software solutions that allow organizations to manage and optimize their networks more efficiently. This technology is particularly beneficial for cloud service providers and businesses with large-scale data management needs, as it enhances scalability and adaptability. However, implementing SDN requires skilled personnel, so buyers should assess their internal capabilities or consider training to maximize the benefits of this technology.
How Can Managed Service Providers (MSPs) Benefit B2B Buyers?
Managed Service Providers (MSPs) deliver outsourced telecom services, allowing businesses to focus on core operations while relying on experts to handle their telecommunications needs. This approach is especially advantageous for small and medium-sized enterprises (SMEs) and those with multiple locations, as it can be a cost-effective solution. However, buyers should be aware that outsourcing may lead to less control over specific services, necessitating careful selection of an MSP that aligns with their business goals.
Key Industrial Applications of telecommunication manufacturer
Industry/Sector | Specific Application of telecommunication manufacturer | Value/Benefit for the Business | Key Sourcing Considerations for this Application |
---|---|---|---|
Healthcare | Telehealth Solutions | Enhanced patient care and remote monitoring capabilities | Compliance with local regulations, integration with existing systems, data security features |
Transportation and Logistics | Fleet Management Systems | Improved operational efficiency and real-time tracking | Scalability, compatibility with different vehicle types, reliability under varying conditions |
Energy and Utilities | Smart Grid Communication Systems | Optimized energy distribution and reduced operational costs | Robustness against environmental factors, interoperability with legacy systems, regulatory compliance |
Agriculture | Precision Agriculture Technologies | Increased crop yields and resource efficiency | Adaptability to different farming practices, support for IoT devices, data analytics capabilities |
Education | Distance Learning Platforms | Broader access to education and improved learning outcomes | User-friendly interfaces, support for multiple languages, reliable bandwidth requirements |
How are Telecommunications Manufacturers Used in Healthcare?
Telecommunication manufacturers play a pivotal role in the healthcare sector by providing telehealth solutions that facilitate remote patient consultations and monitoring. This technology addresses the critical need for accessible healthcare, especially in underserved regions in Africa and South America. Buyers in this sector must ensure that their solutions comply with local regulations, integrate seamlessly with existing healthcare systems, and prioritize data security to protect sensitive patient information.
What Role Do Telecommunications Manufacturers Play in Transportation and Logistics?
In the transportation and logistics industry, telecommunication manufacturers supply fleet management systems that enhance operational efficiency. These systems allow companies to track vehicles in real-time, optimizing routes and reducing fuel consumption. For international B2B buyers, key considerations include the scalability of solutions to accommodate growing fleets, compatibility with various vehicle types, and reliability in diverse environmental conditions, particularly in regions like the Middle East and Europe.
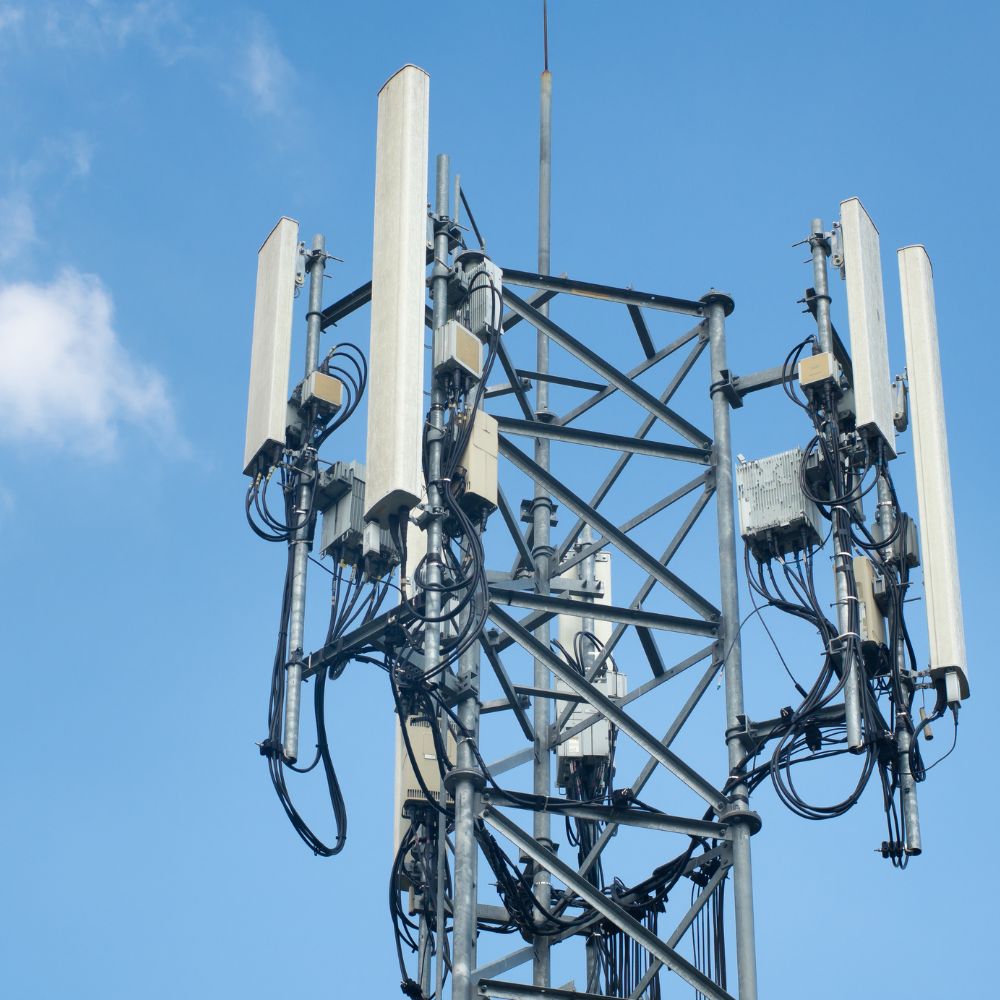
A stock image related to telecommunication manufacturer.
How Do Telecommunications Manufacturers Support Energy and Utilities?
Telecommunication manufacturers contribute significantly to the energy and utilities sector through smart grid communication systems. These systems enable optimized energy distribution and real-time monitoring of energy usage, which can significantly reduce operational costs. Buyers should focus on sourcing robust systems that can withstand environmental challenges, ensure interoperability with existing infrastructure, and comply with local regulatory standards.
What Impact Do Telecommunications Manufacturers Have on Agriculture?
In agriculture, telecommunication manufacturers provide precision agriculture technologies that utilize data-driven insights to improve crop yields and resource efficiency. This is particularly beneficial for farmers in developing regions, where access to advanced technology can transform productivity. Buyers should consider solutions that are adaptable to various farming practices, offer support for IoT devices, and include data analytics capabilities to make informed decisions.
How Are Telecommunications Manufacturers Transforming Education?
Telecommunication manufacturers are revolutionizing the education sector with distance learning platforms that broaden access to quality education. These platforms facilitate remote learning, which is essential in regions with limited educational infrastructure. B2B buyers in this space should prioritize user-friendly interfaces, support for multiple languages, and reliable bandwidth to ensure a seamless learning experience for students across diverse geographical locations.
Related Video: How does Industrial Wireless Communication Work?
3 Common User Pain Points for ‘telecommunication manufacturer’ & Their Solutions
Scenario 1: Navigating Complex Supplier Relationships in Telecommunications
The Problem: For B2B buyers in the telecommunications sector, establishing and maintaining effective relationships with manufacturers can be fraught with challenges. Buyers often face difficulties in communication due to language barriers, differing time zones, and varying cultural expectations. This can lead to misunderstandings about product specifications, delivery timelines, and service agreements, ultimately affecting project outcomes and operational efficiency.
The Solution: To mitigate these challenges, B2B buyers should prioritize establishing clear communication channels from the outset. This can involve appointing a dedicated liaison or project manager who is fluent in the relevant languages and familiar with the cultural norms of both parties. Additionally, leveraging technology such as collaborative platforms (e.g., Slack, Microsoft Teams) can facilitate real-time communication and document sharing, ensuring that all stakeholders are on the same page. Regular video conferences can also enhance relationship-building by allowing for face-to-face interaction, which can foster trust and clarity in negotiations and project updates.
Scenario 2: Ensuring Compatibility with Existing Telecommunications Infrastructure
The Problem: Many international B2B buyers face compatibility issues when integrating new telecommunication equipment with their existing infrastructure. This is particularly common in regions with outdated technology or differing standards, such as those found in parts of Africa and South America. Incompatibility can lead to increased costs, extended timelines, and frustration among teams who are trying to implement new solutions.
The Solution: To avoid compatibility issues, buyers should conduct a thorough assessment of their current telecommunications infrastructure before making any purchases. This includes understanding the existing hardware and software, as well as any regional standards that may apply. Working closely with manufacturers to obtain detailed specifications and compatibility information for new equipment is crucial. Additionally, engaging in pilot testing or phased rollouts can allow organizations to evaluate integration issues in a controlled manner, minimizing disruptions to operations and providing valuable insights for full-scale deployment.
Scenario 3: Addressing High Operational Costs in Telecommunications
The Problem: Operational costs in telecommunications can be significant, particularly for businesses in developing regions where infrastructure investment is still catching up. B2B buyers may struggle with high costs associated with equipment procurement, maintenance, and energy consumption, which can strain budgets and limit growth opportunities.
The Solution: To tackle high operational costs, buyers should consider strategic sourcing options that include negotiating long-term contracts with manufacturers for better pricing and service level agreements. Moreover, exploring energy-efficient technologies, such as solar-powered equipment or energy-efficient routers, can significantly reduce ongoing operational expenses. Buyers can also take advantage of government incentives and programs aimed at supporting the telecommunications industry in their respective regions, which may offer financial assistance or subsidies for upgrading infrastructure. Conducting a total cost of ownership (TCO) analysis can further help buyers make informed decisions by evaluating not just the initial purchase price but also the long-term operational costs associated with different equipment options.
Strategic Material Selection Guide for telecommunication manufacturer
What Are the Key Materials Used in Telecommunications Manufacturing?
Telecommunications manufacturing relies on various materials, each with distinct properties that impact product performance, durability, and overall cost. Understanding these materials is crucial for international B2B buyers, especially those operating in diverse markets such as Africa, South America, the Middle East, and Europe.
How Does Copper Benefit Telecommunications Equipment?
Key Properties: Copper is renowned for its excellent electrical conductivity and thermal conductivity, making it ideal for wiring and connectors in telecommunications. It can withstand high temperatures and has a low resistance to electric current.
Pros & Cons: The primary advantage of copper is its superior performance in transmitting signals, which leads to minimal signal loss. However, copper is susceptible to corrosion, especially in humid environments, and can be more expensive than alternatives like aluminum. Additionally, its extraction and processing have significant environmental impacts.
Impact on Application: Copper is commonly used in wiring for telecommunication networks, including both wired and wireless systems. Its compatibility with various media, such as voice and data, makes it a versatile choice.
Considerations for International Buyers: Buyers must consider local regulations regarding copper use, as some regions enforce strict environmental standards. Compliance with international standards like ASTM or DIN is also essential to ensure product reliability and safety.
What Role Does Fiber Optic Material Play in Telecommunications?
Key Properties: Fiber optics utilize glass or plastic fibers to transmit data as light signals. They offer high bandwidth capabilities, low signal attenuation, and immunity to electromagnetic interference.
Pros & Cons: The key advantage of fiber optics is their ability to transmit vast amounts of data over long distances without degradation. However, they are more fragile than copper and require specialized handling and installation techniques, which can increase manufacturing complexity and costs.
Impact on Application: Fiber optics are essential for high-speed internet and data transmission applications, making them suitable for telecommunications networks that demand high performance.
Considerations for International Buyers: Buyers should be aware of the varying standards for fiber optic cables in different regions, such as JIS in Japan or EN in Europe. Understanding local market preferences and installation practices is crucial for successful implementation.
How Does Aluminum Compare as a Material for Telecommunications?
Key Properties: Aluminum is lightweight, corrosion-resistant, and has decent electrical conductivity, making it a popular alternative to copper in some applications.
Pros & Cons: The primary advantage of aluminum is its cost-effectiveness and lightweight nature, which makes it easier to handle and install. However, its conductivity is lower than that of copper, which can lead to increased signal loss over long distances.
Impact on Application: Aluminum is often used in overhead power lines and some types of cabling, particularly in less demanding applications where weight and cost are critical factors.
Considerations for International Buyers: International buyers should evaluate the local availability of aluminum and any associated tariffs or import duties. Compliance with regional standards is also necessary to avoid issues with product acceptance.
What Is the Importance of Polymeric Materials in Telecommunications?
Key Properties: Polymeric materials, such as polyethylene and PVC, are used for insulation and protective coatings in telecommunications cables. They offer good chemical resistance and flexibility.
Pros & Cons: The main advantage of polymers is their lightweight and cost-effective nature, making them suitable for a wide range of applications. However, they may not withstand extreme temperatures or harsh environmental conditions as well as metals do.
Impact on Application: Polymeric materials are commonly used in cable insulation and protective sheathing, which is critical for maintaining signal integrity and protecting against environmental factors.
Considerations for International Buyers: Buyers should consider the compatibility of polymeric materials with local environmental conditions, as well as compliance with standards like ISO or ASTM for safety and performance.
Summary Table of Key Materials for Telecommunications Manufacturing
Material | Typical Use Case for telecommunication manufacturer | Key Advantage | Key Disadvantage/Limitation | Relative Cost (Low/Med/High) |
---|---|---|---|---|
Copper | Wiring and connectors in telecom networks | Superior electrical conductivity | Susceptible to corrosion | High |
Fiber Optic | High-speed internet and data transmission | High bandwidth and low signal loss | Fragile and complex installation | High |
Aluminum | Overhead power lines and some cabling | Lightweight and cost-effective | Lower conductivity than copper | Medium |
Polymeric | Cable insulation and protective sheathing | Lightweight and flexible | Limited temperature resistance | Low |
This guide provides a comprehensive overview of the materials commonly used in telecommunications manufacturing, offering actionable insights for international B2B buyers to make informed decisions.
In-depth Look: Manufacturing Processes and Quality Assurance for telecommunication manufacturer
What Are the Main Stages in the Manufacturing Process of Telecommunication Equipment?
The manufacturing process for telecommunication equipment is multifaceted, typically involving several key stages: material preparation, forming, assembly, and finishing. Each stage is critical for ensuring that the final product meets the rigorous demands of the telecommunications industry.
1. Material Preparation
The first step in the manufacturing process involves sourcing and preparing raw materials. Telecommunication equipment often requires high-quality materials such as metals (aluminum, copper), plastics, and specialized components like fiber optics. Suppliers must ensure that materials comply with international standards to avoid issues during later stages. For instance, steel components may need to undergo treatments to prevent corrosion, while plastics could require specific certifications for environmental compliance.
2. Forming
Forming involves shaping the prepared materials into components. This can include processes such as machining, stamping, and extrusion. For telecommunications manufacturers, precision is paramount; even minor deviations can affect signal quality or equipment durability. Techniques like CNC (Computer Numerical Control) machining are commonly employed to achieve the necessary precision and repeatability.
3. Assembly
In the assembly stage, individual components are brought together to create functional units. This could involve soldering circuit boards, assembling enclosures, or integrating antennas. Manufacturers often employ automated assembly lines to enhance efficiency and reduce human error. However, manual assembly may still be necessary for complex components or quality-sensitive tasks.
4. Finishing
Finishing processes include painting, coating, or treating the assembled products to enhance their durability and aesthetic appeal. For example, telecommunication equipment often undergoes a process called electroplating to improve corrosion resistance. This stage also includes final inspections to ensure that the product meets all quality specifications before packaging and shipping.
How Is Quality Assurance Implemented in Telecommunication Manufacturing?
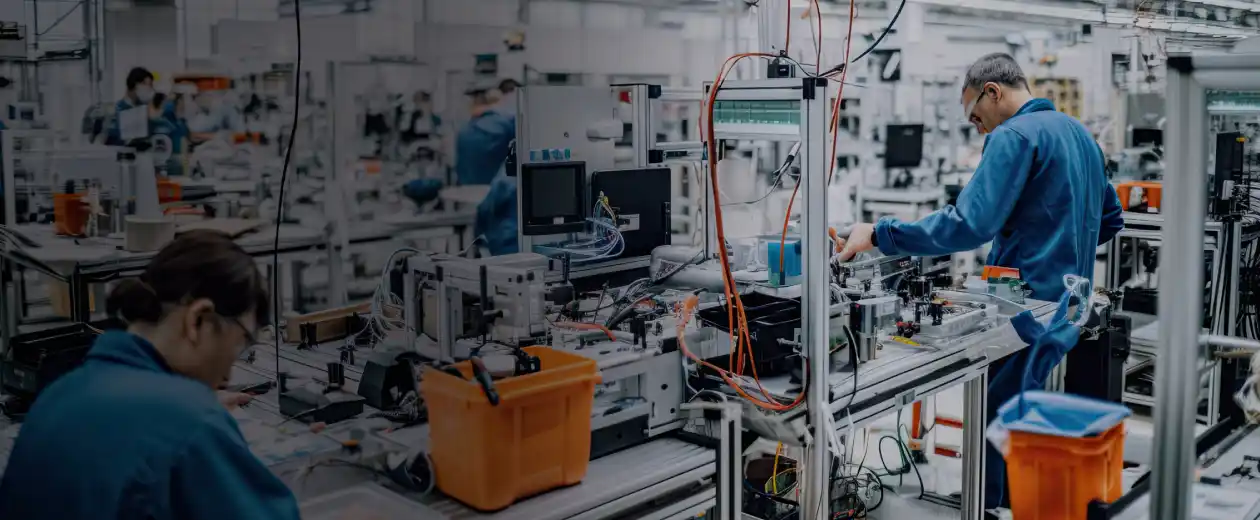
A stock image related to telecommunication manufacturer.
Quality assurance (QA) is a critical aspect of the manufacturing process, ensuring that products meet both industry standards and customer expectations. For B2B buyers, understanding the QA processes can be pivotal in selecting the right supplier.
Relevant International Standards for Quality Assurance
Telecommunication manufacturers often adhere to various international standards, with ISO 9001 being one of the most recognized. This standard focuses on effective quality management systems and continuous improvement. Additionally, industry-specific certifications such as CE (Conformité Européenne) for products sold in Europe and API (American Petroleum Institute) standards for oil and gas telecommunications equipment may be relevant.
Key Quality Control Checkpoints
Quality control (QC) is performed at multiple checkpoints throughout the manufacturing process, including:
-
Incoming Quality Control (IQC): This initial stage checks the quality of raw materials and components upon arrival. It is essential to verify that all materials meet specified standards before they enter the production line.
-
In-Process Quality Control (IPQC): During manufacturing, IPQC ensures that processes are being followed correctly and that any potential defects are caught early. Regular checks help maintain quality throughout the production cycle.
-
Final Quality Control (FQC): Once the product is assembled, FQC involves rigorous testing to ensure that it meets all specifications and functions as intended. This may include functional testing, environmental testing, and safety assessments.
What Common Testing Methods Are Used in Telecommunications Manufacturing?
Testing methods play a crucial role in quality assurance for telecommunication equipment. Manufacturers utilize a variety of testing techniques to verify product performance and compliance.
Common Testing Methods
-
Functional Testing: This assesses whether the equipment performs its intended functions, such as data transmission rates and signal integrity.
-
Environmental Testing: Given the diverse environments in which telecommunications equipment operates, manufacturers often conduct tests simulating extreme temperatures, humidity, and exposure to dust or moisture.
-
Electrical Testing: This includes checking voltage levels, current flow, and signal quality to ensure that the equipment operates safely and efficiently.
-
Compliance Testing: Ensures that the equipment meets specific regulatory requirements, such as electromagnetic compatibility (EMC) and safety standards.
How Can B2B Buyers Verify Supplier Quality Control?
For international B2B buyers, especially those from regions like Africa, South America, the Middle East, and Europe, verifying a supplier’s quality control practices is vital. Here are actionable strategies:
Conducting Audits
Requesting regular audits of the supplier’s manufacturing and quality control processes can provide insights into their operational integrity. Buyers should look for suppliers with a history of passing third-party audits and those that can provide audit reports.
Reviewing Quality Control Reports
Buyers should ask for detailed QC reports that outline testing results, compliance with standards, and any corrective actions taken for non-conformities. This documentation can reveal the supplier’s commitment to quality.
Engaging Third-Party Inspectors
Consider employing third-party inspection services, especially for large orders or critical components. Independent inspectors can provide unbiased evaluations of the supplier’s processes and products.
What Are the Quality Control and Certification Nuances for International B2B Buyers?
Understanding the nuances of quality control and certification can help B2B buyers navigate the complexities of international procurement.
Regional Standards and Certifications
Different regions may have varying standards and certifications. For example, while CE marking is crucial for products entering the European market, other regions may have their own standards, such as the FCC in the United States or ICASA in South Africa. Buyers should ensure that their suppliers understand and comply with these regional requirements.
Language and Documentation
Documentation is often available in local languages, which may pose challenges for international buyers. Requesting translations of critical quality documents can help ensure that all parties have a clear understanding of compliance requirements.
Building Long-Term Relationships
Establishing strong relationships with suppliers can enhance transparency and reliability in quality control practices. Regular communication about quality expectations and feedback can foster a culture of quality awareness.
In conclusion, understanding the manufacturing processes and quality assurance practices in the telecommunications sector is essential for B2B buyers. By focusing on these aspects, international buyers can make informed decisions, ensuring that they partner with manufacturers who prioritize quality and compliance.
Practical Sourcing Guide: A Step-by-Step Checklist for ‘telecommunication manufacturer’
In the ever-evolving telecommunications industry, making informed sourcing decisions is critical for B2B buyers, particularly when engaging with manufacturers. This guide offers a practical checklist to streamline your procurement process, ensuring that you select the right telecommunication manufacturer that meets your organization’s needs.
Step 1: Define Your Technical Specifications
Before initiating the procurement process, it’s essential to clearly outline your technical requirements. This includes the types of equipment needed, compatibility with existing systems, and specific performance metrics. By defining these parameters upfront, you can effectively communicate your needs to potential suppliers, helping them provide tailored solutions.
Step 2: Conduct Market Research for Potential Suppliers
Thorough market research will help you identify suitable telecommunication manufacturers. Look for companies with a strong presence in your target regions, such as Africa, South America, the Middle East, and Europe. Utilize industry reports, trade publications, and online directories to gather information on suppliers and their product offerings.
Step 3: Evaluate Potential Suppliers
Before committing, vet suppliers thoroughly to ensure they align with your business needs. Request company profiles, case studies, and references from buyers in similar industries or regions. Key factors to consider include:
– Experience: Look for manufacturers with a proven track record in telecommunications.
– Product Range: Ensure they offer a comprehensive range of products that match your specifications.
Step 4: Verify Certifications and Compliance
Ensuring that potential suppliers have the necessary certifications is crucial. This may include ISO certifications, compliance with local regulations, and industry standards. Certifications not only indicate a manufacturer’s commitment to quality but also ensure that their products are safe and reliable.
Step 5: Assess Technological Capabilities
Evaluate the technological capabilities of the manufacturers you are considering. This includes their ability to produce cutting-edge equipment, such as 5G technology or fiber optics, which are vital for modern telecommunication needs. Additionally, inquire about their research and development efforts to gauge their innovation potential.
Step 6: Request Samples and Product Demonstrations
Before finalizing your decision, request product samples or demonstrations. This allows you to assess the quality and performance of the equipment firsthand. Pay attention to:
– Functionality: Ensure that the products meet your operational requirements.
– Usability: Consider how easy the equipment will be for your team to operate and maintain.
Step 7: Negotiate Terms and Establish Contracts
Once you have selected a supplier, engage in negotiations to finalize terms. Discuss pricing, delivery schedules, warranty periods, and after-sales support. Establishing a clear contract will protect both parties and ensure that expectations are met throughout the procurement process.
By following this step-by-step checklist, international B2B buyers can confidently navigate the complexities of sourcing telecommunications manufacturers, ensuring they choose a partner that aligns with their strategic objectives and operational requirements.
Comprehensive Cost and Pricing Analysis for telecommunication manufacturer Sourcing
What Are the Key Cost Components in Telecommunications Manufacturing?
Understanding the cost structure of telecommunications manufacturing is critical for international B2B buyers. The primary cost components include:
-
Materials: This encompasses raw materials like metals, plastics, and electronic components essential for manufacturing telecom equipment. Prices can fluctuate based on market demand and availability, making it crucial to monitor trends.
-
Labor: Labor costs vary widely based on geographic location and the skill level required. In regions like Africa and South America, labor may be less expensive, but this can also affect the quality of the output.
-
Manufacturing Overhead: Overhead costs include utilities, rent, equipment maintenance, and administrative expenses. Efficient management of these costs can significantly affect the overall pricing.
-
Tooling: Specialized tools and molds for manufacturing telecom devices can require substantial investment. Custom tooling can increase costs but may be necessary for high-volume production.
-
Quality Control (QC): Implementing robust QC processes ensures product reliability and compliance with international standards. However, higher QC standards can lead to increased costs, which should be factored into pricing.
-
Logistics: Transportation and warehousing play a crucial role in the overall cost structure. International shipping can introduce complexities and additional fees, especially when dealing with tariffs and customs regulations.
-
Margin: Manufacturers typically include a profit margin in their pricing. Understanding the expected margin in your negotiations can help in securing more favorable terms.
How Do Price Influencers Affect Telecommunications Manufacturing Costs?
Several factors can influence the pricing of telecommunications equipment:
-
Volume and Minimum Order Quantity (MOQ): Larger orders often lead to discounts, as manufacturers can spread fixed costs over more units. Buyers should evaluate their purchasing strategies to maximize volume discounts.
-
Specifications and Customization: Customized products generally come with higher costs. Buyers should clearly define their specifications to avoid unexpected expenses.
-
Materials Quality and Certifications: Higher quality materials and certifications (e.g., ISO, CE) can increase costs but are often essential for compliance and reliability. Buyers should weigh the benefits of these certifications against their budget.
-
Supplier Factors: The reputation, reliability, and location of the supplier can significantly impact pricing. A well-established supplier may offer higher prices but could also ensure better quality and service.
-
Incoterms: Understanding Incoterms (International Commercial Terms) is essential for clarifying responsibilities regarding shipping, insurance, and tariffs. This knowledge can prevent unexpected costs during international transactions.
What Are the Best Tips for Negotiating Telecommunications Manufacturing Prices?
To optimize sourcing costs, international B2B buyers should consider the following strategies:
-
Negotiate Terms: Leverage your purchasing power to negotiate better terms, including price reductions, payment plans, and delivery schedules. Building a strong relationship with suppliers can facilitate more favorable negotiations.
-
Focus on Cost-Efficiency: Analyze the Total Cost of Ownership (TCO) rather than just the initial purchase price. This includes considering maintenance, operational costs, and potential downtime due to equipment failure.
-
Understand Pricing Nuances in Different Regions: Buyers from Africa, South America, the Middle East, and Europe should be aware of regional pricing variations due to local market conditions, currency fluctuations, and trade regulations.
-
Request Detailed Quotes: Ensure that suppliers provide comprehensive quotes that break down costs by component. This transparency allows for better comparison and negotiation.
Disclaimer on Pricing
It is essential to note that prices in the telecommunications manufacturing sector can vary widely based on numerous factors, including market conditions, specific requirements, and supplier negotiations. Always conduct thorough research and consult multiple sources to obtain accurate and current pricing information.
Alternatives Analysis: Comparing telecommunication manufacturer With Other Solutions
Understanding Alternatives to Telecommunication Manufacturers
In the rapidly evolving world of telecommunications, international B2B buyers are often faced with the challenge of choosing the most suitable technology for their specific needs. While telecommunication manufacturers provide essential equipment and infrastructure for communication, various alternative solutions may also fulfill similar roles. This section explores a comparison of telecommunication manufacturers with two viable alternatives: Unified Communications as a Service (UCaaS) and Satellite Communication Systems. Each alternative presents unique advantages and drawbacks that can significantly impact operational efficiency and cost-effectiveness.
Comparison Aspect | Telecommunication Manufacturer | Unified Communications as a Service (UCaaS) | Satellite Communication Systems |
---|---|---|---|
Performance | High reliability and scalability | Variable, depends on internet connectivity | High coverage, but latency issues |
Cost | High initial investment; ongoing maintenance | Subscription-based, often lower upfront cost | High operational costs; equipment needs |
Ease of Implementation | Complex installation; requires technical expertise | User-friendly; quick deployment via cloud | Requires specialized equipment; longer setup |
Maintenance | Ongoing; requires skilled personnel | Minimal; managed by service provider | High; involves hardware upkeep and repairs |
Best Use Case | Large enterprises with significant communication needs | Small to medium businesses seeking flexibility | Remote areas with limited infrastructure |
What are the Advantages and Disadvantages of Unified Communications as a Service (UCaaS)?
Unified Communications as a Service (UCaaS) integrates various communication tools, including voice, video, and messaging, into a single cloud-based platform. This solution is particularly beneficial for small to medium-sized enterprises looking for flexibility without the burden of extensive infrastructure.
Pros:
– Cost-Effective: UCaaS typically operates on a subscription model, reducing upfront capital expenditure.
– Scalability: Businesses can easily scale their services up or down based on changing needs.
– Ease of Use: Intuitive interfaces and minimal setup make it accessible for users without extensive technical expertise.
Cons:
– Dependence on Internet Connectivity: Performance can be hampered by poor internet service, which may be a concern in regions with unreliable connections.
– Variable Performance: Quality of service can fluctuate based on the provider and network conditions.
How Do Satellite Communication Systems Compare?
Satellite Communication Systems provide a robust alternative, especially for organizations operating in remote areas where traditional infrastructure is lacking. They facilitate voice and data transmission via satellites orbiting the Earth.
Pros:
– Extensive Coverage: Satellite systems can reach virtually any location, making them ideal for rural or isolated areas.
– Independence from Local Infrastructure: They do not rely on terrestrial networks, which can be a significant advantage in disaster recovery scenarios.
Cons:
– High Operational Costs: The initial setup and ongoing maintenance can be expensive, potentially outweighing the benefits for some businesses.
– Latency Issues: Signals must travel to space and back, which can introduce delays that impact real-time communications.
How Can B2B Buyers Choose the Right Solution?
Selecting the right telecommunications solution involves carefully evaluating the specific needs and constraints of your organization. B2B buyers should consider factors such as the scale of their operations, geographical coverage requirements, budgetary constraints, and the level of technical expertise available.
For businesses in urban areas with reliable internet access, UCaaS may provide the flexibility and cost-effectiveness needed. In contrast, organizations operating in remote locations may find that satellite communication systems offer the necessary coverage despite higher costs. Ultimately, a thorough analysis of each option’s performance, cost, and maintenance needs will guide B2B buyers in making informed decisions that align with their operational goals.
Essential Technical Properties and Trade Terminology for telecommunication manufacturer
What Are the Key Technical Properties for Telecommunications Equipment?
When sourcing telecommunications equipment, understanding the essential technical properties is crucial for ensuring product quality and performance. Here are some critical specifications that international B2B buyers should consider:
1. Material Grade
Material grade refers to the quality of materials used in manufacturing telecommunications equipment, such as fiber optics, copper, and plastics. High-grade materials enhance durability, signal integrity, and resistance to environmental factors. For B2B buyers, selecting equipment made from superior materials is vital to minimize maintenance costs and ensure long-term reliability.
2. Signal Loss
Signal loss, often measured in decibels (dB), indicates the reduction of signal strength as it travels through a medium. Lower signal loss is essential for maintaining high-quality data transmission, especially over long distances. Buyers should prioritize equipment with minimal signal loss to enhance performance and customer satisfaction in service delivery.
3. Tolerance Levels
Tolerance levels define the permissible limits of variation in dimensions and physical properties of the equipment. In telecommunications, precise tolerances are crucial for components like connectors and fiber optic cables to ensure proper functionality and compatibility. Understanding tolerance specifications helps buyers avoid costly mismatches and operational inefficiencies.
4. Frequency Range
The frequency range indicates the spectrum of frequencies over which a device can operate effectively. For instance, telecommunications systems may require equipment that supports multiple frequency bands to accommodate various services, such as voice, data, and video. Buyers must assess frequency specifications to ensure the equipment meets their operational needs and future scalability.
5. Power Consumption
Power consumption specifications detail the energy requirements of telecommunications equipment. Lower power consumption translates to reduced operational costs and a smaller carbon footprint. B2B buyers should evaluate power efficiency ratings to align with sustainability goals and budget constraints.
What Are Common Trade Terms Used in Telecommunications Manufacturing?
Familiarizing oneself with industry jargon can significantly streamline procurement processes and negotiations. Here are some common terms that international B2B buyers should know:
1. OEM (Original Equipment Manufacturer)
An OEM refers to a company that produces parts and equipment that may be marketed by another manufacturer. Understanding OEM relationships can help buyers identify reputable suppliers and gauge the quality of the products being offered.
2. MOQ (Minimum Order Quantity)
MOQ indicates the smallest quantity of a product that a supplier is willing to sell. This term is crucial for budgeting and inventory management, particularly for international buyers, as it can affect shipping costs and lead times.
3. RFQ (Request for Quotation)
An RFQ is a formal document sent to suppliers asking for pricing and terms for specific products. Including detailed specifications in an RFQ can help buyers receive accurate quotes and make informed purchasing decisions.
4. Incoterms (International Commercial Terms)
Incoterms are a set of internationally recognized rules that define the responsibilities of buyers and sellers for the delivery of goods. Understanding these terms is essential for negotiating shipping and liability arrangements, especially in cross-border transactions.
5. Lead Time
Lead time refers to the period between placing an order and receiving the product. Knowing lead times helps buyers plan their inventory needs and project timelines accurately, which is crucial for maintaining operational efficiency.
By grasping these technical properties and trade terms, B2B buyers can make more informed decisions when sourcing telecommunications equipment, ultimately leading to better partnerships and enhanced service delivery.
Navigating Market Dynamics and Sourcing Trends in the telecommunication manufacturer Sector
What Are the Current Market Dynamics and Key Trends in the Telecommunications Manufacturing Sector?
The telecommunications manufacturing sector is currently experiencing transformative shifts driven by digitalization, increased connectivity demands, and the rise of 5G technologies. As international B2B buyers from regions such as Africa, South America, the Middle East, and Europe navigate these changes, several key trends emerge.
-
Expansion of 5G Networks: The rollout of 5G is reshaping the landscape, enabling faster data transmission and improved connectivity. This technology is crucial for businesses seeking to enhance their operational efficiency and customer engagement. B2B buyers should focus on sourcing equipment that supports 5G capabilities, as it becomes a foundational element in telecommunications infrastructure.
-
Adoption of IoT Devices: The Internet of Things (IoT) is revolutionizing telecommunications by connecting various devices and systems. This trend highlights the importance of sourcing manufacturers who specialize in IoT-compatible equipment. Buyers should prioritize suppliers that offer integrated solutions for seamless connectivity.
-
Cloud-Based Solutions: The shift to cloud technologies is significant, with businesses increasingly utilizing cloud services for data management and communication. Buyers from diverse regions must consider suppliers that provide robust cloud infrastructure and related services, ensuring scalability and flexibility in their operations.
-
Emphasis on Cybersecurity: As telecommunication systems become more interconnected, the risk of cyber threats increases. B2B buyers need to assess the cybersecurity measures implemented by manufacturers. Partnering with suppliers that prioritize security can mitigate risks and protect sensitive data.
-
Sustainability Focus: A growing emphasis on sustainable practices is influencing sourcing decisions. Manufacturers that adopt eco-friendly materials and processes are becoming more attractive to buyers who value corporate social responsibility.
How Can Sustainability and Ethical Sourcing Impact B2B Telecommunications?
Sustainability and ethical sourcing are critical considerations for B2B buyers in the telecommunications sector. As environmental concerns gain prominence, the impact of manufacturing processes on the planet cannot be overlooked.
-
Environmental Impact: The telecommunications industry contributes to significant electronic waste and carbon emissions. Buyers should actively seek manufacturers that implement sustainable practices, such as recycling programs and energy-efficient production methods. This not only aids in reducing environmental footprints but also aligns with global sustainability goals.
-
Importance of Ethical Supply Chains: Ethical sourcing ensures that materials are obtained responsibly, respecting labor rights and environmental standards. Buyers from Africa, South America, the Middle East, and Europe are increasingly prioritizing suppliers who demonstrate transparency and compliance with ethical sourcing practices.
-
Green Certifications and Materials: Certifications like Energy Star, RoHS, and ISO 14001 are indicators of a manufacturer’s commitment to sustainability. By sourcing from companies that hold these certifications, buyers can enhance their brand reputation and appeal to environmentally conscious consumers. Additionally, opting for products made from recycled or sustainable materials can further strengthen a company’s position in the market.
What Is the Evolution of the Telecommunications Manufacturing Sector?
The telecommunications manufacturing sector has evolved significantly since the invention of the telegraph in the 19th century. Initially focused on basic communication tools, the industry has expanded to encompass a wide array of technologies, including telephones, satellites, and fiber optics. The emergence of digital communication in the late 20th century marked a pivotal shift, as manufacturers began to invest in advanced technologies to meet growing consumer demands.
In recent years, the sector has been propelled by the advent of mobile technology and the internet, leading to the development of sophisticated telecommunications equipment. The introduction of 5G networks represents the latest evolution, promising to revolutionize connectivity and open new avenues for B2B applications. As this industry continues to progress, international buyers must stay informed about technological advancements and adapt their sourcing strategies accordingly.
Frequently Asked Questions (FAQs) for B2B Buyers of telecommunication manufacturer
-
How do I evaluate the reliability of a telecommunication manufacturer?
To assess a telecommunication manufacturer’s reliability, examine their track record in delivering products on time and meeting quality standards. Look for customer testimonials and case studies that highlight their experience in your specific market. Additionally, verify their certifications and compliance with international standards, such as ISO or ITU regulations. Engaging in a pilot project can also provide insights into their operational capabilities and responsiveness to challenges. -
What are the key factors to consider when sourcing telecommunications equipment?
When sourcing telecommunications equipment, consider compatibility with existing infrastructure, technology standards (like 4G/5G), and future scalability. Evaluate the manufacturer’s production capacity and lead times to ensure they can meet your demand. Pricing, warranty terms, and after-sales support are also critical, as these can significantly impact your total cost of ownership and operational efficiency. -
What is the best telecommunication solution for enhancing connectivity in rural areas?
For enhancing connectivity in rural areas, consider solutions like satellite communication systems or wireless mesh networks, which can provide reliable service without extensive infrastructure. Partnering with manufacturers experienced in deploying these technologies in underserved regions can ensure effective implementation. Look for equipment that supports low-power operation and can withstand challenging environmental conditions to maximize durability and performance. -
How can I ensure product customization meets my specific needs?
To ensure product customization aligns with your requirements, clearly communicate your specifications and operational needs to the manufacturer. Request detailed proposals that outline the customization process, including timelines and costs. Engaging in collaborative design sessions can enhance understanding and ensure the final product meets your expectations. Always verify past customization projects to gauge the manufacturer’s capability in delivering tailored solutions. -
What are typical minimum order quantities (MOQs) for telecommunications equipment?
Minimum order quantities (MOQs) for telecommunications equipment can vary significantly based on the manufacturer and product type. Generally, MOQs may range from a few units for specialized items to hundreds for mass-produced equipment. When negotiating with suppliers, inquire about flexibility in MOQs, especially if your initial requirements are lower, and explore options for phased ordering to meet budget constraints.
-
What payment terms should I expect when dealing with international telecommunication suppliers?
Payment terms can differ widely among international telecommunication suppliers. Common arrangements include upfront payments, letters of credit, or net payment terms (like 30 or 60 days post-delivery). It’s crucial to negotiate terms that protect your investment while also considering factors such as the supplier’s reputation and your previous purchasing relationship. Always ensure that payment methods comply with international trade regulations to avoid delays. -
How can I assess the quality assurance processes of a telecommunication manufacturer?
To assess a manufacturer’s quality assurance processes, review their quality management system and certifications, such as ISO 9001. Request details on their testing protocols, including product lifecycle testing and compliance with international safety standards. Consider visiting their production facility to observe quality control measures firsthand. Engaging in discussions with their quality assurance team can also provide insights into their commitment to maintaining high standards. -
What logistics considerations should I keep in mind when importing telecommunication equipment?
When importing telecommunication equipment, consider logistics aspects such as shipping methods, customs regulations, and lead times. Ensure that the manufacturer provides clear shipping documentation to facilitate smooth customs clearance. Evaluate the total landed cost, which includes shipping, tariffs, and insurance, to avoid unexpected expenses. Partnering with a logistics provider experienced in handling telecommunications equipment can streamline the process and minimize risks.
Important Disclaimer & Terms of Use
⚠️ Important Disclaimer
The information provided in this guide, including content regarding manufacturers, technical specifications, and market analysis, is for informational and educational purposes only. It does not constitute professional procurement advice, financial advice, or legal advice.
While we have made every effort to ensure the accuracy and timeliness of the information, we are not responsible for any errors, omissions, or outdated information. Market conditions, company details, and technical standards are subject to change.
B2B buyers must conduct their own independent and thorough due diligence before making any purchasing decisions. This includes contacting suppliers directly, verifying certifications, requesting samples, and seeking professional consultation. The risk of relying on any information in this guide is borne solely by the reader.
Strategic Sourcing Conclusion and Outlook for telecommunication manufacturer
What Are the Key Takeaways for International B2B Buyers in Telecommunications?
In the rapidly evolving telecommunications landscape, strategic sourcing remains essential for international B2B buyers. By carefully selecting telecommunications manufacturers, businesses can leverage advanced technologies such as fiber optics and 5G, which enhance connectivity and operational efficiency. Understanding the diverse range of telecommunications networks and equipment is crucial for making informed decisions that align with specific regional needs, particularly in Africa, South America, the Middle East, and Europe.
How Can Strategic Sourcing Enhance Competitive Advantage?
Investing in strategic sourcing not only ensures access to cutting-edge telecommunications solutions but also fosters long-term partnerships with reliable manufacturers. This approach enables buyers to negotiate better terms, optimize costs, and secure superior support services. As telecommunications continue to integrate with emerging technologies like IoT and AI, aligning with the right suppliers will be pivotal for sustained growth and innovation.
What Does the Future Hold for Telecommunications in Global Markets?
Looking ahead, the telecommunications sector is poised for transformative growth driven by digitalization and increasing demand for high-speed connectivity. International B2B buyers are encouraged to proactively engage with leading manufacturers and explore emerging trends to stay ahead of the curve. By doing so, companies can not only meet current demands but also anticipate future challenges in this dynamic environment. Embrace strategic sourcing today to unlock new opportunities and ensure your business remains competitive in the global marketplace.