The Ultimate Guide to Traffic Cones Supplier (2025)
Introduction: Navigating the Global Market for traffic cones supplier
Navigating the global market for traffic cones suppliers can be a daunting task for international B2B buyers, especially when faced with diverse regulations, quality standards, and logistical challenges. As companies strive to enhance safety and improve traffic management, sourcing high-quality traffic cones that meet specific requirements becomes critical. This guide serves as a comprehensive resource, covering various types of traffic cones, their applications across different sectors, and essential supplier vetting criteria.
In this guide, we delve into the nuances of selecting the right traffic cone suppliers, highlighting factors such as material durability, visibility, and compliance with local and international safety standards. We also provide insights into cost considerations, ensuring you understand the financial implications of your purchasing decisions. By addressing common challenges and offering actionable strategies, this resource empowers B2B buyers from Africa, South America, the Middle East, and Europe—such as those in Thailand and the UK—to make informed choices.
Ultimately, our goal is to equip you with the knowledge necessary to navigate the complexities of sourcing traffic cones effectively. Whether you’re looking for suppliers that cater to specific regulations or seeking competitive pricing without compromising on quality, this guide will serve as your roadmap to successful procurement in the global market.
Understanding traffic cones supplier Types and Variations
Type Name | Key Distinguishing Features | Primary B2B Applications | Brief Pros & Cons for Buyers |
---|---|---|---|
Standard Traffic Cones | Bright orange color, lightweight, stackable | Road construction, event management | Pros: Cost-effective, easy to transport. Cons: Less durable than heavier options. |
Reflective Traffic Cones | Reflective strips for visibility at night | Nighttime road work, emergency services | Pros: Enhanced visibility, improves safety. Cons: May be more expensive than standard cones. |
Heavy-Duty Traffic Cones | Made from durable materials, often weighted | High-traffic areas, construction zones | Pros: Resistant to wind and impact. Cons: More difficult to move and store. |
Collapsible Traffic Cones | Flexible design for easy storage and transport | Temporary setups, emergency response | Pros: Space-saving, lightweight. Cons: May not withstand harsh weather conditions. |
Customizable Traffic Cones | Options for branding or specific colors | Marketing events, construction sites | Pros: Enhances brand visibility, tailored for specific needs. Cons: Higher production costs and longer lead times. |
What Are Standard Traffic Cones and Their Applications?
Standard traffic cones are the most commonly used type, characterized by their bright orange color and lightweight design. They are stackable, making them easy to transport and store. These cones are primarily used in road construction and event management to direct traffic and ensure safety. When considering a purchase, buyers should note their cost-effectiveness and ease of use, though they may not be suitable for high-wind areas due to their lightweight nature.
How Do Reflective Traffic Cones Improve Safety?
Reflective traffic cones feature reflective strips that enhance visibility, especially at night or in low-light conditions. They are ideal for nighttime road work and emergency services, where visibility is crucial for safety. Buyers should consider these cones if their operations extend into the evening or night, as the increased visibility can significantly reduce accidents. However, they tend to be pricier than standard cones, which is a factor to keep in mind.
Why Choose Heavy-Duty Traffic Cones for High-Traffic Areas?
Heavy-duty traffic cones are constructed from robust materials and often weighted to withstand harsh conditions, including high winds and impacts. These cones are typically used in high-traffic areas and construction zones where durability is paramount. When purchasing, buyers should evaluate the long-term investment in durability against the higher upfront costs. These cones are less portable but provide better stability and longevity.
What Are the Benefits of Collapsible Traffic Cones?
Collapsible traffic cones are designed for easy storage and transport, making them ideal for temporary setups and emergency responses. Their flexible design allows them to be compacted, saving valuable space. While they are lightweight and convenient, buyers should be aware that they may not be as resilient against harsh weather conditions. These cones are best suited for situations where quick deployment and storage are essential.
How Can Customizable Traffic Cones Enhance Brand Visibility?
Customizable traffic cones offer options for branding or specific colors, making them perfect for marketing events and construction sites. These cones allow businesses to enhance their brand visibility while providing safety and direction. Buyers should consider the benefits of customization against the higher production costs and longer lead times. Customizable cones are an excellent investment for companies looking to merge functionality with branding efforts.
Related Video: Traffic Lights Explained – Learn What US Traffic Signals Mean
Key Industrial Applications of traffic cones supplier
Industry/Sector | Specific Application of Traffic Cones Supplier | Value/Benefit for the Business | Key Sourcing Considerations for this Application |
---|---|---|---|
Construction | Site Safety and Traffic Management | Enhances worker safety and minimizes accidents | Compliance with local safety regulations; durability in various weather conditions |
Event Management | Crowd Control and Directional Guidance | Ensures safety and efficient flow of attendees | Visibility and reflective properties; ease of transport and setup |
Road Maintenance and Repair | Temporary Road Closure and Diversion | Reduces traffic disruptions and enhances public safety | Compliance with national road safety standards; availability in bulk |
Emergency Services | Accident Scene Management and Traffic Control | Facilitates quick response and safety for first responders | High visibility; stability in adverse weather; rapid deployment capability |
Logistics and Transportation | Loading Dock and Delivery Area Management | Improves operational efficiency and safety during loading/unloading | Customization options for branding; durability for repeated use |
How Are Traffic Cones Used in Construction Projects?
In the construction industry, traffic cones are essential for site safety and traffic management. They are employed to delineate hazardous areas, redirect traffic, and ensure the safety of workers and pedestrians. By using high-visibility cones, construction companies can significantly reduce the likelihood of accidents, thus protecting both their workforce and the public. For international buyers, sourcing cones that meet local safety regulations and can withstand various weather conditions is crucial to maintaining compliance and operational efficiency.
What Role Do Traffic Cones Play in Event Management?
For event management, traffic cones are vital for crowd control and directional guidance. They help in organizing attendee flow, marking entrances and exits, and ensuring safety in large gatherings. Effective use of traffic cones can enhance the overall experience for event participants by minimizing confusion and potential hazards. Buyers should consider the visibility and reflective properties of the cones, ensuring they are easily seen in various lighting conditions, which is especially important in outdoor events.
How Do Traffic Cones Benefit Road Maintenance Operations?
In road maintenance and repair, traffic cones are used for temporary road closures and diversions. They help manage traffic flow around construction zones, minimizing disruptions and enhancing public safety. By clearly marking off work areas, maintenance crews can operate more efficiently and safely. Buyers in this sector should prioritize sourcing cones that comply with national road safety standards and are available in bulk for large-scale projects, ensuring they have the necessary equipment for ongoing maintenance tasks.
Why Are Traffic Cones Important for Emergency Services?
Emergency services utilize traffic cones for accident scene management and traffic control. They are crucial for creating safe zones around incidents, allowing first responders to operate without interference from oncoming traffic. The use of cones in such scenarios not only protects emergency personnel but also ensures the safety of bystanders. Buyers should focus on cones that offer high visibility, stability in adverse weather, and rapid deployment capability to facilitate quick response times.
How Are Traffic Cones Used in Logistics and Transportation?
In logistics and transportation, traffic cones are employed to manage loading docks and delivery areas. They help define safe zones for loading and unloading, ensuring that operations run smoothly and safely. This application improves operational efficiency and minimizes the risk of accidents during busy delivery times. For international buyers, customization options for branding and the durability of the cones for repeated use should be key considerations when sourcing products for logistics operations.
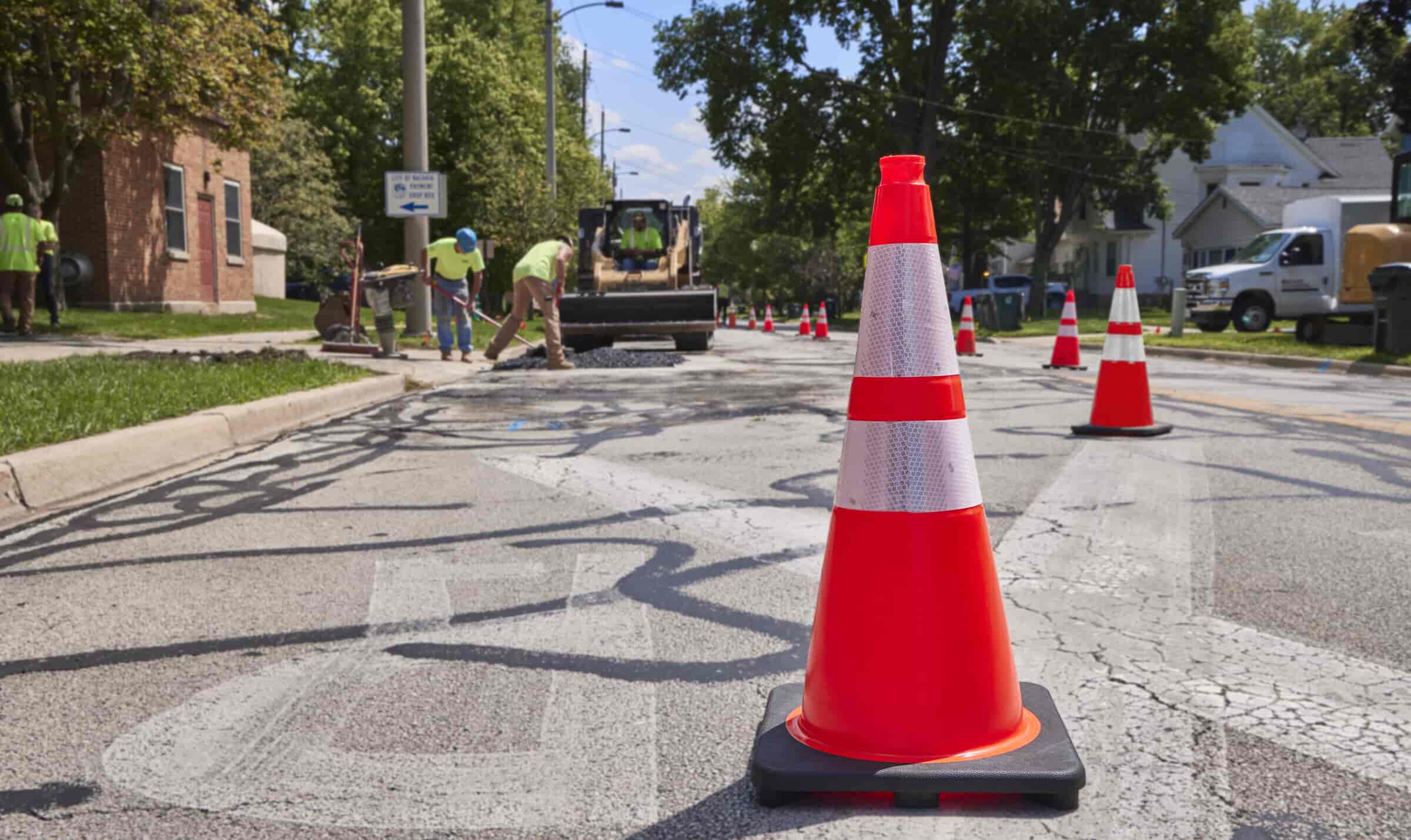
A stock image related to traffic cones supplier.
Related Video: Uses and Gratifications Theory
3 Common User Pain Points for ‘traffic cones supplier’ & Their Solutions
Scenario 1: Difficulty in Meeting Regulatory Compliance for Traffic Management
The Problem: B2B buyers often face challenges in ensuring that the traffic cones they procure meet local and international safety standards. For example, a construction company in South America may be unaware that the reflective properties of the cones they ordered do not comply with local regulations. This can lead to safety hazards, potential legal liabilities, and project delays, creating frustration and financial strain.
The Solution: To mitigate this risk, buyers should conduct thorough research on the specific regulatory requirements in their region before purchasing traffic cones. Engaging with a reputable supplier who provides detailed documentation on compliance can ensure that the cones meet the necessary safety standards. Buyers should request certifications and test results for the cones’ visibility and durability. Additionally, establishing a relationship with a local supplier can provide ongoing support and updates about any changes in regulations, thereby keeping projects compliant and safe.
Scenario 2: Inconsistent Quality and Durability of Traffic Cones
The Problem: Another common issue is the inconsistency in the quality and durability of traffic cones, which can vary significantly from one supplier to another. An international logistics company in Africa may order cones for a temporary road diversion, only to find that they are easily damaged in high winds or heavy traffic, leading to increased costs and operational disruptions.
The Solution: Buyers can address this pain point by implementing a comprehensive supplier evaluation process. This involves assessing potential suppliers based on their reputation, product reviews, and warranty offerings. It’s beneficial to request samples before making a large order, allowing buyers to test the cones in real-world conditions. Additionally, seeking out suppliers that use high-quality materials, such as UV-resistant plastics and reinforced bases, can help ensure that the cones withstand environmental challenges. Establishing long-term contracts with suppliers known for consistent quality can also provide peace of mind and stability in supply.
Scenario 3: Challenges in Logistics and Timely Delivery of Traffic Cones
The Problem: Timely delivery is crucial for B2B buyers, particularly in industries like construction or event management where delays can lead to significant financial losses. For instance, a company in Europe planning a large event may find that their traffic cone supplier cannot meet the required delivery schedule, jeopardizing the event’s safety and organization.
The Solution: To avoid logistics-related issues, buyers should establish clear communication with suppliers regarding delivery timelines and expectations. It is advisable to work with suppliers who have proven logistics capabilities and can provide real-time tracking of shipments. Buyers should also consider placing orders well in advance and exploring options for local suppliers who can deliver quickly. Creating contingency plans, such as identifying alternative suppliers who can step in if needed, can provide additional security against unexpected delays. Finally, leveraging technology, such as supply chain management software, can help buyers monitor orders and manage supplier relationships more effectively.
Strategic Material Selection Guide for traffic cones supplier
What Are the Key Materials Used in Traffic Cones?
Traffic cones are essential safety devices used in various applications, from road construction to event management. The choice of material significantly impacts their performance, durability, and cost. Below, we analyze four common materials used in traffic cone manufacturing: PVC, polyethylene, rubber, and fiberglass.
How Does PVC Perform as a Material for Traffic Cones?
Key Properties: PVC (Polyvinyl Chloride) is known for its excellent weather resistance and flexibility. It can withstand a wide temperature range, making it suitable for various climates.
Pros & Cons: PVC cones are relatively lightweight and cost-effective, making them popular for temporary applications. However, they may not be as durable as other materials, particularly in extreme conditions. Over time, PVC can become brittle when exposed to UV radiation, leading to potential breakage.
Impact on Application: PVC cones are suitable for short-term use in low-traffic areas. However, they may not hold up well in regions with extreme weather conditions, which is a critical consideration for buyers in Africa and the Middle East.
Considerations for International Buyers: Compliance with local standards such as ASTM D-638 for tensile strength is essential. Buyers should also consider the cone’s visibility and reflectivity, which may vary by region.
What Advantages Does Polyethylene Offer for Traffic Cones?
Key Properties: Polyethylene is a robust thermoplastic that offers excellent impact resistance and flexibility. It is also resistant to chemicals and moisture.
Pros & Cons: Polyethylene cones are highly durable and can withstand harsh environmental conditions, making them suitable for long-term use. However, they can be more expensive than PVC options, which may deter budget-conscious buyers.
Impact on Application: Ideal for high-traffic areas, polyethylene cones maintain their integrity even under significant stress. This makes them a preferred choice for construction sites and roadwork.
Considerations for International Buyers: Buyers should look for compliance with international standards such as ISO 9001 for quality management. The availability of color options for visibility in different environments is also crucial.
Why Choose Rubber for Traffic Cones?
Key Properties: Rubber is known for its high elasticity and durability. It can withstand extreme temperatures and is resistant to abrasion and impact.
Pros & Cons: Rubber cones are incredibly durable and can withstand heavy impacts, making them ideal for permanent installations. However, they are heavier and more expensive than other materials, which may limit their use in temporary setups.
Impact on Application: Rubber cones are excellent for high-traffic areas and can be used in various conditions without degradation. Their weight also helps them stay in place during windy conditions.
Considerations for International Buyers: Compliance with safety standards such as EN 13422 for road safety products is vital. Buyers should also consider the environmental impact of rubber sourcing and disposal.
What Role Does Fiberglass Play in Traffic Cone Manufacturing?
Key Properties: Fiberglass is a composite material known for its strength and lightweight properties. It is resistant to corrosion and UV radiation.
Pros & Cons: Fiberglass cones offer excellent durability and longevity, making them suitable for both temporary and permanent applications. However, they are typically more expensive than other materials, which could be a barrier for some buyers.
Impact on Application: Due to their strength and lightweight nature, fiberglass cones are often used in high-traffic areas and for long-term installations.
Considerations for International Buyers: Buyers should ensure that fiberglass cones meet the relevant safety standards, such as ASTM D-256 for impact resistance. The availability of reflective materials for enhanced visibility is also important.
Summary Table of Material Selection for Traffic Cones
Material | Typical Use Case for traffic cones supplier | Key Advantage | Key Disadvantage/Limitation | Relative Cost (Low/Med/High) |
---|---|---|---|---|
PVC | Temporary applications in low-traffic areas | Cost-effective and lightweight | Brittle over time, less durable | Low |
Polyethylene | High-traffic areas, long-term use | Durable, impact-resistant | Higher cost compared to PVC | Medium |
Rubber | Permanent installations, high-traffic areas | Extremely durable and stable | Heavier and more expensive | High |
Fiberglass | Long-term installations, high-traffic areas | Lightweight and corrosion-resistant | Higher initial investment | High |
This guide provides a comprehensive overview of the materials used in traffic cone manufacturing, helping international B2B buyers make informed decisions based on their specific needs and regional considerations.
In-depth Look: Manufacturing Processes and Quality Assurance for traffic cones supplier
What Are the Main Stages of Manufacturing Traffic Cones?
The manufacturing process for traffic cones involves several critical stages, each designed to ensure the final product meets safety and quality standards. Understanding these stages can help B2B buyers make informed purchasing decisions.
Material Preparation: What Materials Are Commonly Used?
The primary materials used in traffic cone manufacturing are high-density polyethylene (HDPE) and PVC. These materials are chosen for their durability, weather resistance, and visibility. The first step involves sourcing raw materials that conform to international standards. Suppliers should provide Material Safety Data Sheets (MSDS) to confirm compliance with safety regulations.
In this stage, suppliers typically conduct a quality check on raw materials to ensure they meet the required specifications. B2B buyers should inquire about the supplier’s sourcing practices and whether they perform inspections on the incoming materials.
How Are Traffic Cones Formed?
Once the materials are prepared, the next stage is forming. This is typically achieved through either injection molding or blow molding techniques:
-
Injection Molding: This method allows for precise shaping and is commonly used for producing the cone’s body. The heated plastic is injected into a mold, forming a solid structure. This method is efficient and results in high-quality cones with consistent dimensions.
-
Blow Molding: Used primarily for hollow cones, this process involves inflating hot plastic within a mold. It is advantageous for creating lightweight cones that are easy to transport.
B2B buyers should assess the manufacturing techniques used by suppliers, as these can significantly impact the quality and durability of the cones.
What Is the Assembly Process for Traffic Cones?
After the forming stage, the cones may require additional assembly. This can include attaching reflective bands or securing weights at the base for stability. Each assembly step is crucial for enhancing the functionality and safety of the cones.
Buyers should ensure that suppliers have a well-defined assembly process and that they maintain strict quality control during this stage. A thorough understanding of the assembly techniques can help mitigate risks associated with product recalls or safety issues.
How Are Traffic Cones Finished and Packaged?
The finishing stage involves applying any final touches, such as painting, branding, or applying reflective materials. This not only enhances visibility but also contributes to the aesthetic appeal of the cones. Proper finishing is essential for ensuring that cones meet international safety standards.
Packaging is equally important, as it protects the cones during transportation. Suppliers should use durable, weather-resistant packaging materials to prevent damage. B2B buyers should ask about packaging practices to ensure that products arrive in pristine condition.
What Are the Quality Assurance Protocols for Traffic Cone Suppliers?
Quality assurance is a vital aspect of the manufacturing process, ensuring that traffic cones meet safety and performance standards. B2B buyers must understand the quality control measures in place at their suppliers to make informed decisions.
Which International Standards Should B2B Buyers Look For?
International standards like ISO 9001 are critical in the manufacturing process. ISO 9001 specifies requirements for a quality management system (QMS) and helps ensure that products consistently meet customer and regulatory requirements. Suppliers should be certified to ISO 9001, indicating their commitment to quality.
In addition to ISO standards, industry-specific certifications such as CE marking for European markets or API standards for certain applications may be relevant. Buyers should verify that their suppliers possess the necessary certifications applicable to their specific market.
What Are the Key Quality Control Checkpoints?
Quality control checkpoints are integral to maintaining product quality throughout the manufacturing process. Common checkpoints include:
-
Incoming Quality Control (IQC): This involves inspecting raw materials upon arrival to ensure they meet specified standards.
-
In-Process Quality Control (IPQC): During manufacturing, ongoing inspections ensure that the production process adheres to quality standards.
-
Final Quality Control (FQC): This is the last step before products are shipped, where finished cones undergo rigorous testing for defects and compliance with specifications.
B2B buyers should inquire about the frequency and methods of these quality checks, as they are indicative of a supplier’s commitment to quality assurance.
What Common Testing Methods Are Used for Traffic Cones?
Testing methods for traffic cones may include:
-
Durability Testing: Assessing how well cones withstand various environmental conditions, including UV exposure and temperature variations.
-
Impact Resistance Testing: Evaluating how cones respond to physical impacts, ensuring they do not break or deform easily.
-
Reflectivity Testing: Measuring the effectiveness of reflective materials used on cones to ensure they are visible in low-light conditions.
Buyers can request documentation of these tests to verify compliance with quality standards.
How Can B2B Buyers Verify Supplier Quality Control?
Verifying a supplier’s quality control processes is essential for ensuring product reliability. B2B buyers can take several steps to assess supplier quality:
What Steps Should Buyers Take for Supplier Audits?
Conducting supplier audits is a proactive way to assess quality control measures. Buyers should consider:
-
On-Site Audits: Visiting the supplier’s manufacturing facility to observe processes and quality control measures firsthand.
-
Third-Party Inspections: Engaging independent auditors to evaluate the supplier’s practices and compliance with international standards.
-
Reviewing Quality Reports: Requesting access to quality control reports and audit findings can provide insights into the supplier’s performance history.
What Are the Nuances of Quality Control for International B2B Buyers?
For international buyers, understanding local regulations and compliance requirements is crucial. Different regions may have varying safety standards, and suppliers should be well-versed in these regulations. Buyers should ensure that their suppliers can navigate these complexities and provide products that meet local market needs.
In conclusion, understanding the manufacturing processes and quality assurance protocols for traffic cones is vital for B2B buyers. By focusing on material preparation, forming, assembly, finishing, and comprehensive quality control measures, buyers can make informed decisions that ensure the safety and reliability of their traffic cone purchases.
Practical Sourcing Guide: A Step-by-Step Checklist for ‘traffic cones supplier’
In the global market, sourcing traffic cones requires a strategic approach to ensure quality, compliance, and value for your investment. This checklist serves as a practical guide for international B2B buyers, particularly from Africa, South America, the Middle East, and Europe, to navigate the procurement process effectively.
Step 1: Define Your Technical Specifications
Before reaching out to suppliers, clearly outline the specifications of the traffic cones you require. Consider factors such as size, material, color, visibility, and durability. This clarity will help you communicate your needs effectively and ensure that suppliers can meet your expectations.
- Identify Regulations: Research local regulations regarding traffic cone specifications in your region to ensure compliance.
- Determine Usage Context: Specify whether the cones are for temporary roadwork, permanent installations, or emergency situations.
Step 2: Research Potential Suppliers
Conduct thorough research to identify reputable suppliers in the traffic cone industry. Utilize online platforms, industry directories, and trade shows to compile a list of potential candidates.
- Check Reviews and Ratings: Look for customer reviews and ratings to gauge supplier reliability and product quality.
- Explore Industry Connections: Network with industry peers to gather recommendations for trusted suppliers.
Step 3: Evaluate Supplier Certifications
It’s crucial to verify that potential suppliers hold relevant certifications and adhere to quality standards. This step ensures that the products you receive are safe and meet industry benchmarks.
- Request Documentation: Ask for certifications such as ISO 9001 or specific safety standards relevant to traffic management equipment.
- Verify Compliance: Ensure that suppliers can demonstrate compliance with international standards, particularly if you are importing products.
Step 4: Request Samples Before Bulk Ordering
Before committing to a large order, request samples of the traffic cones to assess quality firsthand. Evaluating the samples allows you to confirm that they meet your specifications.
- Test Durability and Visibility: Assess the cones for durability under various conditions and ensure they provide adequate visibility at night or in low-light situations.
- Compare with Competitors: If possible, compare samples from multiple suppliers to determine the best fit for your needs.
Step 5: Negotiate Terms and Pricing
Once you’ve identified a suitable supplier, engage in negotiations to discuss pricing, payment terms, and delivery schedules. Effective negotiation can lead to better deals and favorable terms.
- Discuss Volume Discounts: Inquire about discounts for bulk orders or long-term partnerships, which can significantly reduce costs.
- Clarify Payment Methods: Ensure that the payment methods align with your company’s policies and consider using escrow services for large transactions to mitigate risks.
Step 6: Establish Clear Communication Channels
Maintain open lines of communication with your supplier throughout the sourcing process. Clear communication helps to prevent misunderstandings and ensures that both parties are aligned.
- Set Up Regular Check-Ins: Schedule regular updates to discuss progress, address concerns, and adapt to any changes in requirements.
- Use Project Management Tools: Consider using collaborative tools to track orders, timelines, and communications effectively.
Step 7: Finalize the Purchase Agreement
Before making any payments, finalize a purchase agreement that outlines all terms and conditions, including delivery timelines, return policies, and warranty details. This contract serves as a safeguard for both parties.
- Include Contingency Clauses: Ensure the agreement includes clauses that protect your interests in case of delays or quality issues.
- Review Legal Compliance: If importing, ensure that all legal requirements are addressed to avoid any customs issues.
By following this checklist, international B2B buyers can streamline the sourcing process for traffic cones, ensuring a successful procurement that meets both operational and regulatory needs.
Comprehensive Cost and Pricing Analysis for traffic cones supplier Sourcing
What Are the Key Cost Components for Sourcing Traffic Cones?
When sourcing traffic cones, understanding the cost structure is essential for international B2B buyers. The primary components that contribute to the overall cost include:
-
Materials: The quality of materials used to manufacture traffic cones directly influences their durability and price. Common materials include PVC, polyethylene, and rubber, with each having distinct cost implications. High-quality, UV-resistant materials may come at a premium but offer better longevity, making them a worthwhile investment.
-
Labor: Labor costs can vary significantly based on the supplier’s location. Countries with lower labor costs, such as some in South America and Africa, may offer competitive pricing. However, ensure that labor practices meet international standards to avoid ethical concerns.
-
Manufacturing Overhead: This encompasses utilities, equipment depreciation, and other indirect costs associated with production. Suppliers with efficient manufacturing processes may be able to offer more competitive pricing.
-
Tooling: Custom tooling for unique cone designs can be a substantial upfront cost. If your project requires specialized cones, inquire about the initial investment and amortization over the expected order volume.
-
Quality Control (QC): Implementing robust QC measures ensures that the cones meet safety and regulatory standards. While this may add to the cost, it is vital for maintaining product integrity and avoiding costly recalls.
-
Logistics: Shipping and handling fees are crucial, especially for international buyers. Factors such as distance, shipping mode (air vs. sea), and customs duties can significantly impact the final price.
-
Margin: Suppliers typically include a profit margin in their pricing. Understanding market rates can help you assess whether a supplier’s margin is reasonable or inflated.
How Do Price Influencers Affect Traffic Cone Sourcing?
Several factors can influence the pricing of traffic cones, making it essential for buyers to consider:
-
Volume and Minimum Order Quantity (MOQ): Larger orders often lead to lower per-unit costs due to economies of scale. Suppliers may offer discounts for bulk purchases, so negotiate based on your projected needs.
-
Specifications and Customization: Custom designs or specifications can lead to increased costs. Clearly outline your requirements to receive accurate quotes and avoid surprises later.
-
Materials and Quality Certifications: Higher-quality materials typically come with a higher price tag. Additionally, certifications (like ISO or EN standards) may add costs but are crucial for compliance in many regions.
-
Supplier Factors: The reputation and reliability of the supplier can affect pricing. Established suppliers with proven track records may charge more but offer better service and quality assurance.
-
Incoterms: The choice of Incoterms (International Commercial Terms) can affect pricing significantly. Terms like FOB (Free on Board) or CIF (Cost, Insurance, and Freight) dictate who bears shipping costs and risks, impacting your overall expenditure.
What Are the Best Negotiation Tips for International Buyers?
To ensure cost-efficiency when sourcing traffic cones, consider the following negotiation strategies:
-
Research and Benchmarking: Conduct market research to understand standard pricing and quality benchmarks in your region. This knowledge equips you to negotiate more effectively.
-
Focus on Total Cost of Ownership (TCO): Instead of just the purchase price, consider the TCO, which includes maintenance, replacement, and disposal costs. Presenting TCO to suppliers can facilitate discussions on long-term savings.
-
Build Relationships: Establishing a rapport with suppliers can lead to better pricing and terms. Long-term partnerships often yield more favorable conditions than one-off transactions.
-
Be Transparent About Your Needs: Clearly communicate your requirements and constraints to suppliers. Transparency can foster trust and lead to better pricing options tailored to your needs.
Conclusion: Why Is It Important to Understand Pricing Nuances?
Navigating the complexities of traffic cone pricing is critical for international B2B buyers, particularly those from Africa, South America, the Middle East, and Europe. By understanding the cost components, price influencers, and effective negotiation strategies, buyers can make informed decisions that enhance their procurement process. Always keep in mind that prices can fluctuate based on market conditions, so it’s advisable to obtain multiple quotes and maintain flexibility in negotiations.
Alternatives Analysis: Comparing traffic cones supplier With Other Solutions
When considering the procurement of traffic management solutions, it is essential for B2B buyers to evaluate not only the traditional traffic cones supplier but also viable alternatives that may offer similar or enhanced functionality. This section will provide a comparative analysis of traffic cones suppliers against two alternative solutions: digital traffic management systems and inflatable traffic barriers. Each solution has its own set of advantages and considerations that can impact decision-making.
Comparison Aspect | Traffic Cones Supplier | Digital Traffic Management Systems | Inflatable Traffic Barriers |
---|---|---|---|
Performance | High visibility and durability; effective for short-term use | Real-time data collection and analysis; adaptable to traffic conditions | Highly visible; portable and easy to deploy |
Cost | Generally low upfront cost; ongoing replacement costs | Higher initial investment; potential for long-term savings through efficiency | Moderate cost; reusable, but may require maintenance |
Ease of Implementation | Simple to deploy and remove; requires minimal training | May require training for staff; software installation needed | Quick to deploy; minimal training required |
Maintenance | Regular replacement needed; can wear out from weather exposure | Software updates and maintenance required; ongoing costs | Durable but may need air pump maintenance |
Best Use Case | Short-term road work, events, or temporary traffic control | Large scale events, urban traffic management, or construction zones | Construction sites, emergency scenarios, or temporary detours |
What are the Advantages and Disadvantages of Digital Traffic Management Systems?
Digital traffic management systems leverage technology to monitor and manage traffic flows in real-time. These systems can provide valuable insights through data analytics and can adapt to changing traffic conditions automatically. The primary advantage lies in their ability to optimize traffic patterns and reduce congestion, leading to improved safety and efficiency. However, they do come with a higher initial investment and require staff training for effective utilization. Additionally, ongoing software maintenance can incur extra costs, making it crucial for buyers to assess whether the long-term benefits justify the upfront expenses.
How Do Inflatable Traffic Barriers Compare?
Inflatable traffic barriers serve as a flexible alternative to traditional traffic cones. These barriers are particularly useful in construction zones or emergency situations where quick deployment is necessary. They are highly visible, reducing the risk of accidents. Their moderate cost and reusability make them an economically viable option over time. However, they may require maintenance, such as ensuring that air pumps are functional, and may not withstand extreme weather conditions as well as rigid cones. Therefore, buyers should consider the specific requirements of their projects when evaluating this option.
How Can B2B Buyers Choose the Right Solution?
Choosing the right traffic management solution ultimately depends on the specific needs of the project, budget constraints, and the desired level of technology integration. For short-term applications, traditional traffic cones may suffice due to their low cost and ease of use. However, for more complex traffic scenarios, especially in urban environments, investing in digital traffic management systems may yield better long-term results. Inflatable barriers can serve as an excellent middle ground, offering flexibility and visibility without the commitment to high-tech solutions. Buyers should carefully analyze their use cases, potential traffic volumes, and budget to select the most appropriate solution for their operations.
Essential Technical Properties and Trade Terminology for traffic cones supplier
What Are the Essential Technical Properties of Traffic Cones?
When sourcing traffic cones, understanding their technical properties is crucial for ensuring safety and compliance. Here are several critical specifications to consider:
1. Material Grade: What Is the Best Material for Traffic Cones?
Traffic cones are typically made from high-density polyethylene (HDPE) or PVC. HDPE is favored for its durability and resistance to UV light, making it ideal for outdoor use. PVC, while less expensive, may not offer the same longevity. Buyers should assess the material grade based on the environmental conditions in their region, as well as the expected lifespan of the cones.
2. Height and Weight: How Do Dimensions Affect Usability?
Traffic cones come in various heights, typically ranging from 18 inches to 36 inches. The height affects visibility, while the weight impacts stability. A heavier cone is less likely to be blown over by wind, which is particularly important in regions prone to harsh weather. Buyers should choose sizes that meet local regulations and are suitable for their specific applications.
3. Reflectivity: Why Is Visibility Important?
Reflective bands on traffic cones enhance visibility, especially at night or in low-light conditions. The most common standard is the use of reflective sheeting that meets ASTM Type I or II specifications. Buyers should prioritize cones with adequate reflectivity to ensure safety in high-traffic areas.
4. Tolerance and Flexibility: What Should You Know?
Tolerance refers to the allowable variation in the dimensions of the cone. Flexibility is crucial for ensuring the cone can withstand impact without cracking. High-quality cones should meet industry standards for both tolerance and flexibility, ensuring they perform well under various conditions. This is particularly important for cones used in construction zones or areas with heavy vehicle traffic.
5. Base Design: How Does the Base Impact Stability?
The design of the cone’s base can significantly affect its stability. Wider bases provide better resistance to wind and impact. Buyers should consider cones with a solid or weighted base for increased stability, especially in outdoor applications.
What Trade Terminology Should You Know When Sourcing Traffic Cones?
Understanding industry-specific terminology can streamline the procurement process and enhance negotiations with suppliers. Here are some common trade terms:
1. OEM (Original Equipment Manufacturer): What Does It Mean?
OEM refers to companies that produce components that are used in the manufacturing of another company’s product. When sourcing traffic cones, buyers might deal with OEMs who supply the raw materials or components that go into the production of cones. Knowing if a supplier is an OEM can help in assessing quality and reliability.
2. MOQ (Minimum Order Quantity): Why Is It Significant?
MOQ is the smallest number of units a supplier is willing to sell. This term is crucial for budgeting and inventory management. Buyers should negotiate MOQs that align with their operational needs to avoid excess stock or financial strain.
3. RFQ (Request for Quotation): How Do You Use It?
An RFQ is a document sent to suppliers to request pricing and terms for a specific quantity of products. Crafting a detailed RFQ can help buyers obtain competitive pricing and ensure all necessary specifications are addressed, leading to better purchasing decisions.
4. Incoterms (International Commercial Terms): Why Are They Important?
Incoterms define the responsibilities of buyers and sellers in international shipping. Understanding these terms is essential for managing risks and costs associated with transportation. For instance, knowing whether the supplier is responsible for shipping costs can influence your overall budget.
5. Lead Time: How Does It Affect Your Supply Chain?
Lead time refers to the time taken from placing an order to receiving the goods. For traffic cones, understanding lead times is vital for planning and ensuring compliance with project deadlines. Buyers should communicate their timelines clearly to suppliers to avoid delays.
By mastering these technical properties and trade terms, international B2B buyers can make informed decisions when sourcing traffic cones, ensuring safety, compliance, and operational efficiency.
Navigating Market Dynamics and Sourcing Trends in the traffic cones supplier Sector
What Are the Current Market Dynamics and Sourcing Trends in the Traffic Cones Supplier Sector?
The global traffic cones market is influenced by several key drivers, including urbanization, infrastructure development, and increased focus on road safety. Urban areas across Africa, South America, the Middle East, and Europe are rapidly expanding, necessitating enhanced traffic management solutions. Consequently, there is a growing demand for high-quality traffic cones that meet safety regulations and standards. B2B buyers should focus on suppliers who offer innovative products that incorporate advanced materials and technologies, such as reflective coatings for better visibility and eco-friendly materials.
Emerging sourcing trends include the adoption of digital platforms for procurement, which streamline the purchasing process. This trend is particularly beneficial for international buyers, enabling them to compare suppliers, manage orders, and track shipments in real-time. Additionally, suppliers are increasingly utilizing data analytics to understand market demand and optimize inventory management. For B2B buyers, leveraging these technologies can lead to more informed purchasing decisions and cost savings.
How Is Sustainability Shaping Sourcing Practices in the Traffic Cones Supplier Sector?
Sustainability has become a crucial consideration in the traffic cones supplier sector. The environmental impact of manufacturing and disposing of traffic cones is under scrutiny, leading to a demand for sustainable sourcing practices. B2B buyers should prioritize suppliers who demonstrate commitment to reducing their carbon footprint through the use of recycled materials and eco-friendly production processes.
Ethical sourcing is equally important, as it enhances brand reputation and ensures compliance with international labor standards. Suppliers that possess certifications such as ISO 14001 (Environmental Management) or utilize materials that are certified as sustainable should be favored. Moreover, innovative materials like biodegradable plastics or cones made from recycled rubber are gaining traction, appealing to environmentally conscious buyers.
What Is the Historical Context Behind the Traffic Cones Supplier Sector?
The traffic cones supplier sector has evolved significantly over the past few decades. Initially, traffic cones were primarily made from rigid materials like metal and hard plastic, which posed challenges in terms of safety and visibility. The introduction of flexible, lightweight materials has transformed their design, making them safer for use in various environments.
Moreover, the rise of smart technologies has influenced the evolution of traffic management solutions, including traffic cones equipped with sensors and smart lighting. This historical progression highlights the importance of innovation in meeting the needs of modern urban infrastructure, presenting opportunities for B2B buyers to invest in advanced traffic management solutions that enhance safety and efficiency on roads.
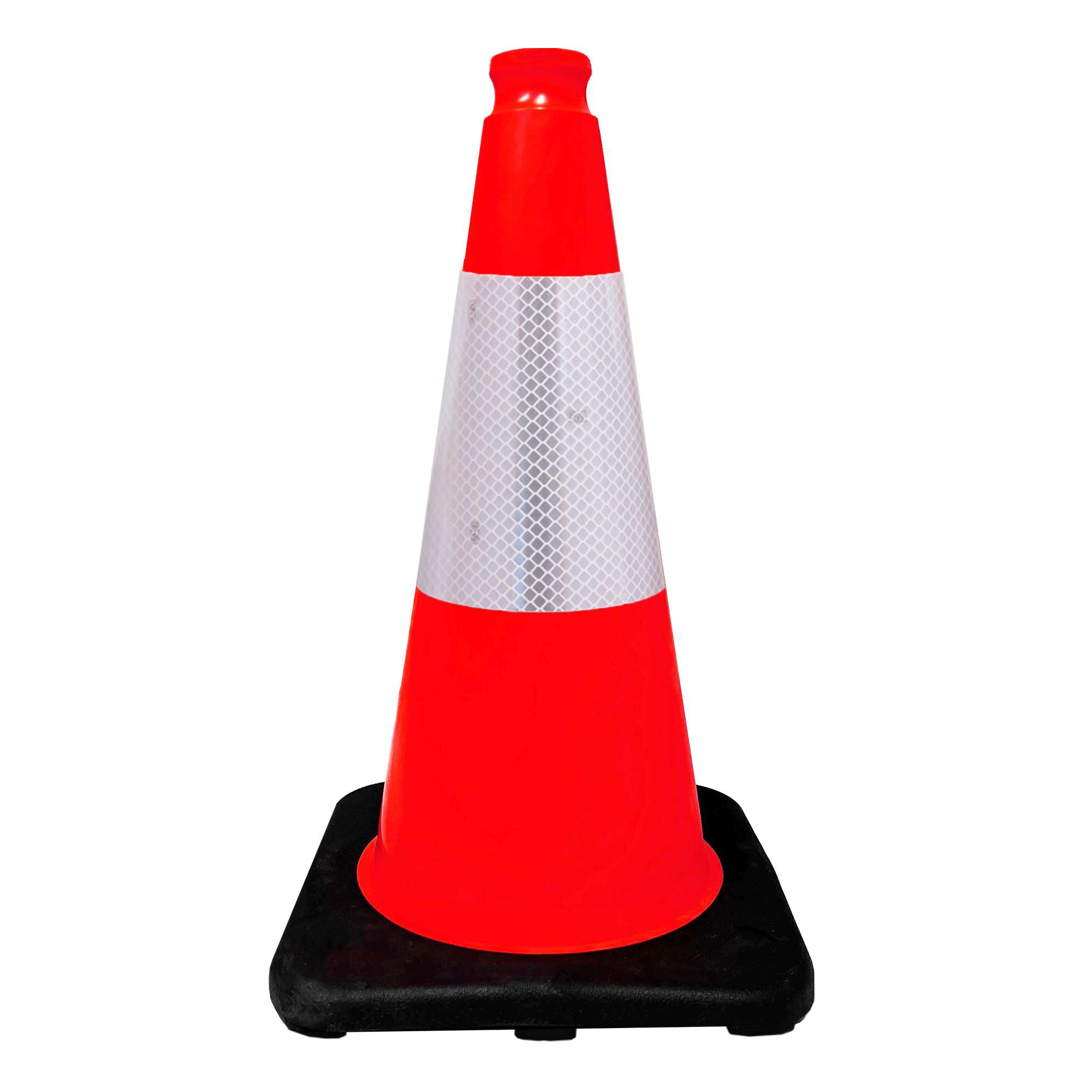
A stock image related to traffic cones supplier.
By understanding these market dynamics, sourcing trends, and the historical evolution of the traffic cones supplier sector, international B2B buyers can make informed decisions that align with their strategic goals and sustainability initiatives.
Frequently Asked Questions (FAQs) for B2B Buyers of traffic cones supplier
-
How do I ensure the quality of traffic cones from suppliers?
To ensure the quality of traffic cones, request samples before placing a large order. Verify that the cones meet relevant safety standards and specifications for your region. Additionally, consider conducting third-party inspections or audits at the supplier’s facility to assess their manufacturing processes and quality control measures. Establish clear quality expectations in your purchase agreement to hold suppliers accountable. -
What are the key features to look for in traffic cones for international use?
When sourcing traffic cones for international use, prioritize durability, visibility, and weight. Look for cones made from high-quality, weather-resistant materials that can withstand various climates. Reflective bands and bright colors enhance visibility, crucial for safety. Ensure the cones are lightweight enough for easy transport but heavy enough to withstand wind and accidental knocks. -
What customization options are available for traffic cones?
Many suppliers offer customization options such as color, size, and branding. You can request specific colors that align with your brand or local regulations. Some suppliers also allow for printing logos or safety messages directly onto the cones. Discuss your requirements during the initial inquiry to determine which customization options are feasible and cost-effective. -
What is the minimum order quantity (MOQ) for traffic cones from suppliers?
Minimum order quantities (MOQs) for traffic cones vary by supplier and depend on the type of cones and customization. Generally, MOQs can range from 100 to 1,000 units. It’s essential to discuss your needs upfront to understand the supplier’s MOQ policies. If your order is smaller than the MOQ, inquire about potential options for combining orders with other buyers or sourcing from different suppliers. -
What payment terms should I negotiate with traffic cone suppliers?
Negotiating favorable payment terms is crucial for maintaining cash flow. Common terms include a deposit upfront (typically 30-50%) with the balance due upon shipment or delivery. Consider negotiating for extended payment terms or discounts for early payments. Always ensure that the payment terms are clearly documented in the purchase agreement to avoid any misunderstandings. -
How can I vet suppliers of traffic cones effectively?
To vet suppliers, research their reputation through online reviews, industry forums, and references from previous clients. Request documentation of their certifications, such as ISO standards or compliance with local safety regulations. Conduct video calls or visits to their facilities, if possible, to assess their operations. Establishing a good relationship and open communication with the supplier can also provide insight into their reliability. -
What logistics considerations should I be aware of when importing traffic cones?
When importing traffic cones, consider shipping methods, costs, and timelines. Evaluate whether air freight or sea freight is more suitable based on your urgency and budget. Be aware of customs regulations and duties in your country to avoid unexpected delays and costs. Working with an experienced freight forwarder can streamline the logistics process and help navigate potential challenges. -
How do I handle disputes with traffic cone suppliers?
To handle disputes with suppliers effectively, maintain clear documentation of all communications, contracts, and agreements. Attempt to resolve issues amicably through direct communication, outlining your concerns and proposed solutions. If informal discussions fail, refer to the dispute resolution clause in your contract, which may involve mediation or arbitration. Engaging legal counsel can also provide guidance on your rights and obligations in the situation.
Important Disclaimer & Terms of Use
⚠️ Important Disclaimer
The information provided in this guide, including content regarding manufacturers, technical specifications, and market analysis, is for informational and educational purposes only. It does not constitute professional procurement advice, financial advice, or legal advice.
While we have made every effort to ensure the accuracy and timeliness of the information, we are not responsible for any errors, omissions, or outdated information. Market conditions, company details, and technical standards are subject to change.
B2B buyers must conduct their own independent and thorough due diligence before making any purchasing decisions. This includes contacting suppliers directly, verifying certifications, requesting samples, and seeking professional consultation. The risk of relying on any information in this guide is borne solely by the reader.
Strategic Sourcing Conclusion and Outlook for traffic cones supplier
In today’s competitive landscape, effective strategic sourcing is paramount for international B2B buyers seeking reliable traffic cones suppliers. By thoroughly vetting suppliers based on quality, cost, and compliance with local regulations, businesses can ensure they receive products that not only meet safety standards but also enhance operational efficiency. As global trade continues to evolve, leveraging technology and data analytics will provide buyers with deeper insights into supplier performance and market trends.
How Can Buyers Prepare for Future Sourcing Challenges?
To navigate potential disruptions in supply chains, especially in regions like Africa, South America, the Middle East, and Europe, companies should establish strong relationships with multiple suppliers. This diversification mitigates risks associated with single-source dependencies and fosters competitive pricing. Furthermore, engaging in collaborative planning with suppliers can lead to innovative solutions and improved service levels.
What’s Next for Traffic Cones Suppliers?
Looking ahead, international buyers are encouraged to stay informed about technological advancements in traffic management and safety equipment. As the market adapts to the increasing demand for smart traffic solutions, suppliers who invest in innovation will offer significant advantages. By prioritizing strategic sourcing, businesses can position themselves for long-term success in a dynamic market. Embrace the opportunity to refine your sourcing strategies today, ensuring your company thrives in the evolving landscape of traffic safety products.