The Ultimate Guide to Wall Cladding Manufacturer (2025)
Introduction: Navigating the Global Market for wall cladding manufacturer
Navigating the complex landscape of sourcing wall cladding manufacturers can be a daunting task for international B2B buyers. With diverse materials, design options, and regulatory standards varying significantly across regions, making an informed decision becomes critical. This guide aims to demystify the global market for wall cladding manufacturers by addressing essential factors such as material types, applications, supplier vetting processes, and cost considerations. By providing a comprehensive overview, we empower buyers from Africa, South America, the Middle East, and Europe—particularly those from Germany and France—to make strategic purchasing decisions that align with their project requirements.
Understanding the nuances of wall cladding materials, from natural stone to engineered composites, is crucial for selecting the right product for your needs. Furthermore, the guide delves into the applications of wall cladding in various sectors, including commercial, residential, and industrial settings, highlighting the advantages of each material type.
Additionally, the guide emphasizes the importance of rigorous supplier vetting to ensure quality, reliability, and compliance with international standards. By exploring cost implications and potential return on investment, buyers will be better equipped to negotiate contracts and establish long-term partnerships with manufacturers. Ultimately, this comprehensive resource serves as a vital tool for B2B buyers looking to navigate the global market effectively and confidently.
Understanding wall cladding manufacturer Types and Variations
Type Name | Key Distinguishing Features | Primary B2B Applications | Brief Pros & Cons for Buyers |
---|---|---|---|
Natural Stone Cladding | Made from granite, marble, or slate; offers durability and aesthetics. | High-end residential and commercial buildings | Pros: Luxurious appearance, long-lasting. Cons: Higher cost, requires skilled installation. |
Vinyl Wall Cladding | Lightweight, versatile, and available in various colors and styles. | Residential, commercial, and industrial applications | Pros: Cost-effective, low maintenance. Cons: Less durable than other materials, may fade over time. |
Fiber Cement Cladding | Composed of cement, sand, and cellulose fibers; resistant to fire and pests. | Commercial buildings, multifamily housing | Pros: Durable, weather-resistant. Cons: Heavier, can be more expensive than vinyl. |
Metal Cladding | Available in aluminum, steel, or copper; often used for modern aesthetics. | Industrial buildings, warehouses, and contemporary designs | Pros: Strong, recyclable, modern look. Cons: Prone to denting, can be noisy in rain. |
Wood Cladding | Natural wood finishes that provide warmth and character; can be treated for longevity. | Residential homes, boutique hotels, and restaurants | Pros: Eco-friendly, aesthetic appeal. Cons: Requires regular maintenance, susceptible to rot and pests. |
What are the Characteristics and Suitability of Natural Stone Cladding?
Natural stone cladding is synonymous with luxury and durability. It is made from materials like granite, marble, or slate, making it ideal for high-end residential and commercial projects. Buyers should consider the stone’s origin, as this can influence both price and sustainability. While it offers a stunning visual appeal and long lifespan, the initial investment and installation costs can be significant. Additionally, sourcing skilled installers is crucial to ensure proper application.
How Does Vinyl Wall Cladding Fit Into B2B Applications?
Vinyl wall cladding is an attractive option for buyers seeking cost-effective solutions. Its lightweight nature and variety of styles make it suitable for residential and commercial applications alike. Vinyl is low-maintenance and can mimic other materials, providing versatility. However, buyers should be aware that its lifespan may be shorter compared to other options, and it may fade in direct sunlight. Understanding local climate conditions can help buyers assess its long-term viability.
Why Choose Fiber Cement Cladding for Commercial Buildings?
Fiber cement cladding combines durability with aesthetic appeal, making it a popular choice for commercial buildings and multifamily housing. Its composition allows it to withstand extreme weather conditions, fire, and pest damage. When purchasing, buyers should evaluate the product’s thickness and finish, as these factors can impact overall performance. While more expensive than vinyl, the long-term savings on maintenance and repairs can justify the initial investment.
What are the Advantages of Metal Cladding in Modern Architecture?
Metal cladding is increasingly favored for its modern aesthetic and strength. Available in materials like aluminum and steel, it’s particularly suited for industrial buildings and warehouses. Buyers appreciate its recyclability and low maintenance, but should consider potential downsides such as denting and noise during rain. Understanding the insulation properties of metal can also influence purchasing decisions, especially in regions with extreme temperatures.
How Does Wood Cladding Enhance Aesthetic Appeal?
Wood cladding offers a natural and warm aesthetic, making it ideal for residential homes, boutique hotels, and restaurants. It can be treated for durability, but requires regular maintenance to prevent rot and pest infestations. Buyers should consider the type of wood and treatment processes to ensure longevity. While it may come with a higher price tag, the environmental benefits and unique character it brings can be significant selling points in B2B transactions.
Related Video: Insulation and Cladding Pipe – Tutorial
Key Industrial Applications of wall cladding manufacturer
Industry/Sector | Specific Application of Wall Cladding Manufacturer | Value/Benefit for the Business | Key Sourcing Considerations for this Application |
---|---|---|---|
Construction | Exterior Wall Cladding for Commercial Buildings | Enhances aesthetics and energy efficiency, reducing heating and cooling costs. | Compliance with local building codes and regulations; durability and weather resistance. |
Food Processing | Hygienic Wall Cladding for Processing Areas | Ensures easy cleaning and sanitation, minimizing contamination risks. | Material safety certifications; resistance to chemicals and moisture. |
Healthcare | Wall Cladding in Hospitals and Clinics | Provides a sterile environment, aiding in infection control and patient safety. | Non-toxic materials; seamless installation for hygiene maintenance. |
Retail | Decorative Wall Cladding in Showrooms | Creates an engaging customer experience, enhancing brand visibility. | Customization options; durability against wear and tear from high foot traffic. |
Manufacturing | Insulated Wall Cladding for Factories | Improves energy efficiency and worker comfort, leading to increased productivity. | Thermal performance ratings; compatibility with existing structures. |
How is Wall Cladding Used in the Construction Industry?
In the construction sector, wall cladding serves as a critical component for the exterior of commercial buildings. It enhances the aesthetic appeal while providing insulation, which can significantly reduce energy consumption. International buyers, particularly in regions like Europe, must consider local building codes and the climatic conditions of their projects. Additionally, the durability and weather resistance of materials are essential to ensure longevity and reduce maintenance costs.
What Role Does Wall Cladding Play in Food Processing Facilities?
For the food processing industry, hygienic wall cladding is vital in processing areas. It is designed to minimize contamination risks by allowing for easy cleaning and sanitation. Buyers from Africa and South America should prioritize materials that are certified safe for food contact and resistant to chemicals and moisture. This ensures compliance with health regulations and promotes a safe working environment for employees.
Why is Wall Cladding Important in Healthcare Settings?
In healthcare, wall cladding contributes to creating a sterile environment in hospitals and clinics. It aids in infection control by providing seamless surfaces that are easy to clean and maintain. Buyers in the Middle East should focus on non-toxic materials that meet stringent health and safety standards. Ensuring that wall cladding is installed without seams is crucial for hygiene, making it a top consideration for healthcare facilities.
How Can Retail Spaces Benefit from Decorative Wall Cladding?
In the retail industry, decorative wall cladding is used to enhance the customer experience in showrooms and stores. It plays a significant role in brand visibility and creates an engaging atmosphere for shoppers. Buyers from Europe, particularly in Germany and France, should look for customization options to align with their brand identity. Additionally, durability is critical, as cladding must withstand high foot traffic without showing signs of wear and tear.
What Advantages Does Insulated Wall Cladding Offer in Manufacturing?
Manufacturing facilities benefit from insulated wall cladding, which improves energy efficiency and worker comfort. This type of cladding helps maintain optimal indoor temperatures, thereby increasing productivity. International buyers should consider thermal performance ratings when sourcing materials to ensure they meet the specific energy efficiency goals of their operations. Compatibility with existing structures is also a key factor, facilitating smoother installations and reducing downtime.
Related Video: Fortex Cladding Installation Demo
3 Common User Pain Points for ‘wall cladding manufacturer’ & Their Solutions
Scenario 1: Uncertainty in Material Durability and Performance
The Problem:
International B2B buyers often face uncertainty regarding the durability and performance of wall cladding materials, especially when sourcing from manufacturers in different regions. Factors such as climate, local building codes, and material specifications can significantly impact the longevity and effectiveness of wall cladding. For instance, a buyer in Africa may be concerned about how well a specific cladding material can withstand high humidity and heat, while a buyer in Europe may prioritize insulation properties to comply with stringent energy efficiency standards.
The Solution:
To alleviate these concerns, buyers should conduct thorough research into the manufacturer’s credentials and product performance data. Request detailed technical specifications, including test results for climate resilience and thermal performance, and ensure they meet local regulations. Engage in direct communication with the manufacturer to discuss specific project needs and seek samples or case studies demonstrating the product’s effectiveness in similar environments. Establishing a partnership with a reputable supplier who offers comprehensive warranties can also provide additional peace of mind regarding material longevity.
Scenario 2: Complications in Customization and Design Options
The Problem:
Customization is often a critical requirement for B2B buyers looking to implement unique design aesthetics in their projects. However, many manufacturers may offer limited options or have complicated processes for customization, leading to frustration and delays. For example, a construction firm in South America may struggle to find a wall cladding manufacturer that can accommodate bespoke designs while still maintaining production efficiency and cost-effectiveness.
The Solution:
To overcome this pain point, buyers should prioritize manufacturers who specialize in customizable solutions and have a streamlined process for order modifications. When evaluating potential suppliers, look for those that provide a range of materials, finishes, and colors, along with a user-friendly design consultation service. Engaging with manufacturers who utilize advanced technology such as CAD (Computer-Aided Design) can significantly enhance the customization process. Additionally, maintaining open lines of communication with the manufacturer throughout the design phase can help ensure that all requirements are met without compromising on timelines.
Scenario 3: Inconsistent Quality Control Across Regions
The Problem:
Quality control can vary significantly across different manufacturing facilities, which poses a challenge for B2B buyers sourcing wall cladding from international suppliers. A buyer in the Middle East might experience inconsistencies in product quality, leading to potential project delays and increased costs. These inconsistencies can stem from different manufacturing standards, supply chain issues, or lack of adequate testing measures.
The Solution:
To mitigate the risks associated with inconsistent quality, buyers should conduct due diligence on potential manufacturers, focusing on their quality assurance processes. Inquire about certifications such as ISO 9001 or compliance with local and international standards. It’s also beneficial to request third-party test results and references from past clients to gauge the reliability of the manufacturer. Establishing a quality agreement that includes regular inspections and audits during the production process can further ensure that the final products meet the expected standards. Buyers should also consider local representatives who can facilitate communication and oversee quality checks on-site, thereby bridging the gap between the manufacturer and the buyer.
Strategic Material Selection Guide for wall cladding manufacturer
When selecting materials for wall cladding, it is essential to consider various factors that influence performance, compliance, and cost. Below, we analyze four common materials used in wall cladding, focusing on their key properties, advantages, disadvantages, and specific considerations for international B2B buyers from diverse regions such as Africa, South America, the Middle East, and Europe.
What Are the Key Properties of Aluminum Composite Panels?
Aluminum Composite Panels (ACP) are widely used in modern architecture due to their lightweight nature and aesthetic appeal. They typically consist of two thin layers of aluminum enclosing a non-aluminum core. Key properties include excellent corrosion resistance, a temperature rating suitable for a wide range of climates, and good thermal insulation.
Pros & Cons: ACPs are durable and relatively easy to install, making them a popular choice for both commercial and residential applications. However, they can be more expensive than traditional materials and may require specialized installation techniques, which could increase manufacturing complexity.
Impact on Application: ACPs are compatible with various media, including moisture and UV exposure, making them suitable for diverse environments. However, buyers should consider local climate conditions, as extreme temperatures can affect the material’s longevity.
Considerations for International Buyers: Compliance with standards such as ASTM and DIN is crucial. Buyers in Europe, particularly in Germany and France, may prefer manufacturers that adhere to stringent fire safety regulations.
How Do Fiber Cement Boards Perform in Wall Cladding?
Fiber Cement Boards are composed of a mixture of cement, cellulose fibers, and sand, providing a robust and versatile cladding solution. They exhibit high durability, excellent fire resistance, and minimal expansion or contraction with temperature changes.
Pros & Cons: These boards are highly resistant to pests and moisture, making them ideal for humid climates. However, they can be heavy and may require additional structural support, which could complicate installation and increase costs.
Impact on Application: Fiber cement is suitable for various environments, including coastal areas where saltwater corrosion is a concern. Its compatibility with different finishes allows for customization in aesthetics.
Considerations for International Buyers: Buyers should be aware of local building codes and standards, especially in regions with strict environmental regulations. In South America, for instance, compliance with local sustainability standards may influence purchasing decisions.
What Are the Advantages of Using Vinyl Siding?
Vinyl siding is a popular choice due to its affordability and low maintenance requirements. Made from polyvinyl chloride (PVC), it offers good resistance to moisture and fading.
Pros & Cons: The primary advantage of vinyl siding is its cost-effectiveness and ease of installation. However, it may not be as durable as other materials, particularly in extreme weather conditions, and can be prone to warping or cracking.
Impact on Application: Vinyl is suitable for a variety of applications, but its performance can be affected by temperature fluctuations. Buyers in hotter climates should consider UV resistance to ensure longevity.
Considerations for International Buyers: In Europe, particularly in Germany, there is a growing trend towards eco-friendly materials. Buyers may need to ensure that the vinyl siding meets environmental standards and certifications.
How Do Natural Stone Panels Compare in Terms of Performance?
Natural Stone Panels, such as granite or limestone, provide a timeless aesthetic and unparalleled durability. They are naturally resistant to weathering, fire, and pests, making them a premium choice for wall cladding.
Pros & Cons: The key advantage of natural stone is its longevity and aesthetic appeal. However, it is significantly heavier than other materials, which can complicate installation and increase structural requirements. Additionally, the cost can be prohibitive for some projects.
Impact on Application: Natural stone is suitable for both interior and exterior applications, providing excellent performance in various climates. However, buyers should consider the local availability of stone types to reduce transportation costs.
Considerations for International Buyers: Compliance with local regulations regarding quarrying and sustainability is essential. In the Middle East, for example, buyers may need to ensure that the sourced stone meets specific environmental standards.
Summary Table of Material Selection for Wall Cladding
Material | Typical Use Case for wall cladding manufacturer | Key Advantage | Key Disadvantage/Limitation | Relative Cost (Low/Med/High) |
---|---|---|---|---|
Aluminum Composite Panels | High-rise buildings, commercial facades | Lightweight and aesthetic appeal | Higher cost and installation complexity | High |
Fiber Cement Boards | Residential and commercial buildings | Excellent durability and fire resistance | Heavy and requires structural support | Medium |
Vinyl Siding | Residential homes, low-rise buildings | Cost-effective and low maintenance | Less durable in extreme weather | Low |
Natural Stone Panels | Luxury homes, high-end commercial properties | Timeless aesthetic and durability | High cost and installation complexity | High |
This guide provides a comprehensive overview for international B2B buyers, enabling informed decisions based on material properties, application suitability, and compliance considerations.
In-depth Look: Manufacturing Processes and Quality Assurance for wall cladding manufacturer
What Are the Main Stages of Manufacturing Wall Cladding?
The manufacturing process for wall cladding involves several critical stages that ensure the final product meets quality and design standards. Understanding these stages is essential for B2B buyers who need reliable, durable, and aesthetically pleasing materials.
1. Material Preparation
The first step in wall cladding production is material preparation. This phase involves selecting high-quality raw materials, such as metals, composites, or natural stones. Suppliers often conduct rigorous material testing to ensure compliance with international standards. Sourcing materials locally can also mitigate shipping costs and lead times, which is particularly beneficial for buyers from Africa and South America.
2. Forming Techniques
Once the materials are prepared, the next stage is forming. This can involve various techniques, including extrusion, molding, or panel cutting, depending on the type of wall cladding being manufactured. Advanced technologies such as CNC (Computer Numerical Control) machining are often employed to ensure precision and consistency. B2B buyers should inquire about the specific forming techniques used by their suppliers, as this can significantly impact the durability and finish of the cladding.
3. Assembly Process
The assembly process is crucial for ensuring that the wall cladding panels fit together seamlessly. This may involve welding, adhesive bonding, or mechanical fastening. The choice of assembly technique can affect the overall strength and longevity of the product. Buyers should seek suppliers that offer customizable solutions to cater to specific architectural designs and building requirements.
4. Finishing Touches
Finishing is the final manufacturing stage, which includes surface treatments such as painting, coating, or laminating. These processes enhance the aesthetic appeal and weather resistance of the cladding. B2B buyers should consider the types of finishes available and their respective warranties, as this can influence maintenance costs and longevity.
How Is Quality Assurance Implemented in Wall Cladding Manufacturing?
Quality assurance (QA) is a fundamental aspect of the wall cladding manufacturing process. Implementing rigorous QA measures helps ensure that products meet or exceed industry standards.
Relevant International Standards for Wall Cladding
Manufacturers often adhere to international quality standards, such as ISO 9001, which outlines the requirements for a quality management system. In addition, industry-specific certifications like CE marking (for products sold in the European Economic Area) and API standards (for oil and gas applications) are crucial for ensuring product reliability and safety. B2B buyers should verify that their suppliers hold these certifications, as they demonstrate a commitment to quality and safety.
What Are the Key Quality Control Checkpoints?
Quality control (QC) involves several checkpoints throughout the manufacturing process:
-
Incoming Quality Control (IQC): This initial inspection ensures that raw materials meet specified standards before they enter the production line.
-
In-Process Quality Control (IPQC): During manufacturing, regular inspections are conducted to monitor production processes and identify any deviations from quality standards.
-
Final Quality Control (FQC): Once production is complete, finished products undergo rigorous testing to confirm they meet all specifications.
B2B buyers should ask suppliers about their QC protocols and how they address any identified issues during these checkpoints.
What Common Testing Methods Are Used in Wall Cladding Production?
Testing methods vary based on the type of wall cladding but generally include:
- Physical Testing: Evaluating properties such as tensile strength, impact resistance, and thermal performance.
- Chemical Testing: Ensuring that materials are free from harmful substances and comply with environmental regulations.
- Aesthetic Testing: Assessing color consistency, surface finish, and overall appearance.
Understanding these testing methods allows B2B buyers to gauge the quality of the products they are considering.
How Can B2B Buyers Verify Supplier Quality Control?
Verifying a supplier’s quality control processes is essential for B2B buyers, especially when sourcing materials internationally.
Audits and Reports
Regular audits of suppliers can provide insights into their manufacturing and QC processes. Buyers should request documentation of these audits, including any corrective actions taken. This information helps assess whether the supplier adheres to their stated quality standards.
Third-Party Inspections
Engaging third-party inspection services can provide an unbiased evaluation of the supplier’s QC processes. These services often offer comprehensive reports detailing compliance with relevant standards and identifying areas for improvement. Buyers from regions such as the Middle East and Europe may find this particularly useful due to stringent import regulations.
What Are the Quality Control and Certification Nuances for International Buyers?
For international B2B buyers, understanding the nuances of quality control and certifications is critical. Different regions may have varying standards and regulations that impact product compliance.
Regional Compliance Considerations
Buyers from Africa and South America should be aware of local regulations that may differ from those in Europe or the Middle East. For instance, CE marking is essential for products sold in the EU, while other regions may have their own certifications that need to be met. Ensuring that the supplier is familiar with and compliant with these regional standards can prevent costly delays and compliance issues.
Cultural and Communication Barriers
Effective communication is vital for ensuring that quality expectations are understood and met. B2B buyers should establish clear lines of communication with suppliers and consider language barriers that might affect quality assurance discussions. Establishing a partnership with suppliers who prioritize transparency and open dialogue can lead to better outcomes.
Conclusion
Understanding the manufacturing processes and quality assurance measures in wall cladding production equips international B2B buyers with the knowledge necessary to make informed purchasing decisions. By focusing on material preparation, forming techniques, assembly processes, and rigorous quality control measures, buyers can ensure they source high-quality products that meet their specific needs. Additionally, navigating the complexities of international standards and certifications will enhance the buyer-supplier relationship and ultimately lead to successful project outcomes.
Practical Sourcing Guide: A Step-by-Step Checklist for ‘wall cladding manufacturer’
In today’s competitive market, sourcing wall cladding manufacturers requires a strategic approach to ensure quality, compliance, and value. This guide serves as a practical checklist for international B2B buyers, particularly those from Africa, South America, the Middle East, and Europe. By following these steps, you can make informed decisions that align with your project needs and business objectives.
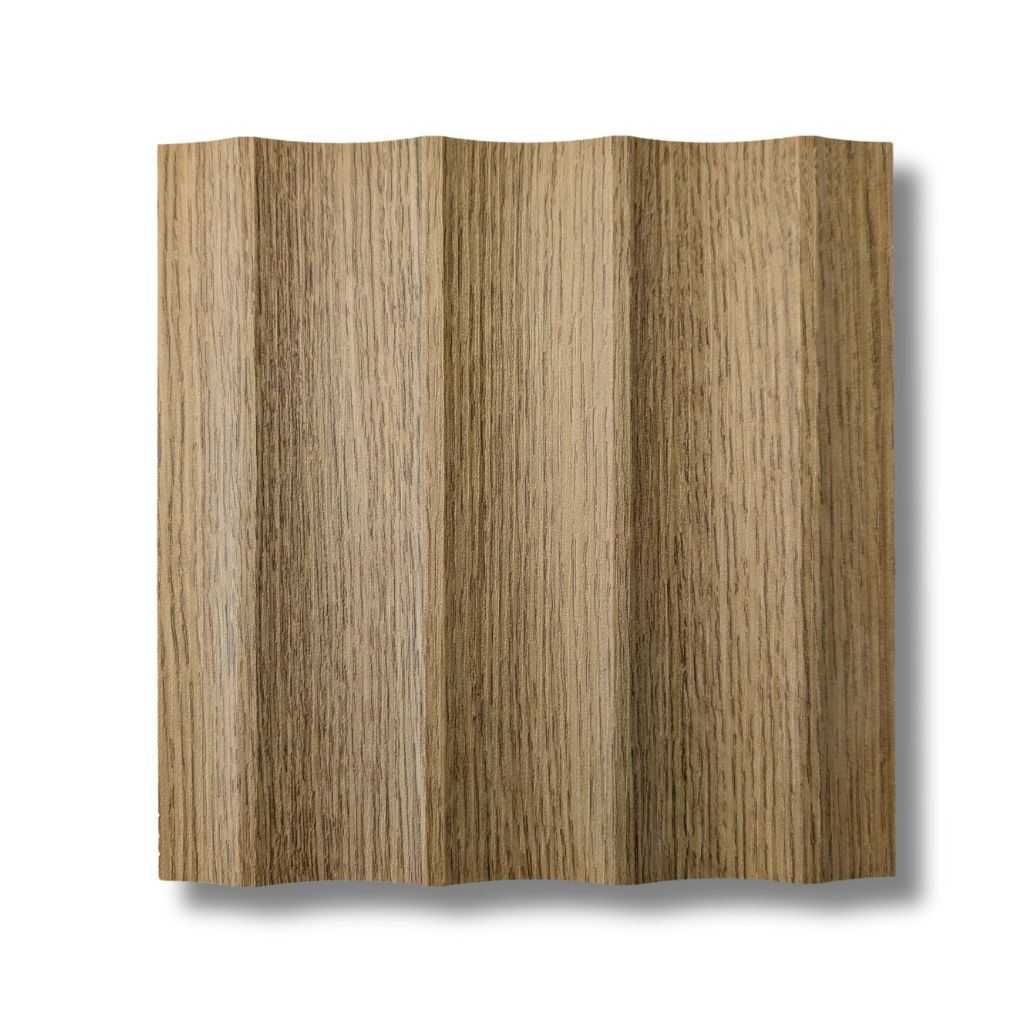
A stock image related to wall cladding manufacturer.
Step 1: Define Your Technical Specifications
Before initiating the sourcing process, it’s essential to outline your specific requirements for wall cladding. Consider the materials, dimensions, aesthetic preferences, and environmental standards applicable to your project. This clarity will not only streamline your search but also help potential suppliers understand your needs.
- Material Types: Identify whether you need metal, wood, composite, or other materials.
- Performance Standards: Specify any fire resistance, thermal insulation, or soundproofing requirements.
Step 2: Conduct Market Research
Understanding the market landscape is crucial for identifying potential manufacturers. Research industry trends, pricing structures, and key players in the wall cladding sector. This knowledge will empower you to negotiate better terms and select suppliers who are aligned with your goals.
- Regional Insights: Focus on suppliers from regions known for specific cladding materials, such as Europe for high-quality aluminum or Africa for locally sourced materials.
- Competitor Analysis: Review what similar companies are using in their projects to gauge performance and cost.
Step 3: Evaluate Potential Suppliers
Before committing, it’s crucial to vet suppliers thoroughly. Request company profiles, case studies, and references from buyers in a similar industry or region. Don’t just rely on their website; due diligence can reveal a lot about their reliability and service quality.
- Quality Assurance: Look for suppliers with ISO certifications or other industry-specific quality standards.
- Client Testimonials: Seek feedback from previous clients to understand the supplier’s strengths and weaknesses.
Step 4: Request Samples and Product Specifications
Once you have shortlisted potential manufacturers, request samples of their wall cladding products. This will allow you to assess the quality and craftsmanship firsthand. Additionally, ensure you receive detailed product specifications for a thorough comparison.
- Sample Evaluation: Check for durability, finish, and compliance with your technical requirements.
- Documentation: Verify that the specifications include installation guidelines and maintenance recommendations.
Step 5: Negotiate Terms and Conditions
Engage in discussions with your selected suppliers to negotiate pricing, delivery timelines, and payment terms. Clear communication at this stage is vital to avoid misunderstandings later on.
- Volume Discounts: Inquire about pricing breaks for bulk orders, which can significantly reduce costs.
- Delivery Schedules: Ensure timelines align with your project deadlines to avoid delays.
Step 6: Verify Supplier Certifications
Ensure that your chosen manufacturer complies with relevant industry regulations and standards. Certification verification is critical to guarantee that the products meet safety and quality benchmarks.
- Regulatory Compliance: Confirm that the supplier adheres to local and international standards, such as CE marking in Europe.
- Sustainability Credentials: If applicable, check for certifications related to sustainability and environmental impact, which can be crucial for projects in eco-sensitive regions.
Step 7: Establish a Communication Plan
Finally, create a communication plan to maintain ongoing dialogue with your supplier throughout the project lifecycle. Clear communication channels help address any issues promptly and foster a productive working relationship.
- Regular Updates: Schedule periodic check-ins to discuss project progress and any potential adjustments.
- Feedback Mechanism: Implement a process for providing feedback on product performance and service, which can enhance future collaborations.
By following this checklist, international B2B buyers can navigate the complexities of sourcing wall cladding manufacturers effectively, ensuring that their projects are executed smoothly and successfully.
Comprehensive Cost and Pricing Analysis for wall cladding manufacturer Sourcing
What Are the Key Cost Components in Wall Cladding Manufacturing?
Understanding the cost structure of wall cladding manufacturing is essential for international B2B buyers. The primary cost components include:
-
Materials: The choice of materials significantly impacts costs. Common materials for wall cladding include vinyl, wood, metal, and composite materials. Higher-quality materials typically incur higher costs but may offer better durability and aesthetics.
-
Labor: Labor costs vary based on the region and the complexity of the manufacturing process. In regions with higher labor costs, such as Europe, manufacturers may need to optimize their production processes to maintain competitive pricing.
-
Manufacturing Overhead: This includes expenses related to facility maintenance, utilities, and equipment depreciation. Efficient operations can help minimize overhead costs, impacting the final pricing for buyers.
-
Tooling: The initial investment in tooling can be substantial, especially for custom designs. Buyers should consider whether the tooling costs are amortized over a larger production run, potentially reducing per-unit costs.
-
Quality Control (QC): Ensuring product quality often requires dedicated QC processes, which can add to manufacturing costs. Certifications and standards compliance can further elevate costs but are crucial for maintaining product integrity.
-
Logistics: Shipping costs can vary greatly based on distance, shipping method, and volume. Buyers should explore different Incoterms to determine the most cost-effective shipping arrangements.
-
Margin: Manufacturers typically build a profit margin into their pricing. Understanding the expected margins within the industry can help buyers gauge whether prices are reasonable.
How Do Price Influencers Affect Wall Cladding Costs?
Several factors influence the pricing of wall cladding products:
-
Volume/MOQ: Manufacturers often provide discounts for bulk orders, making it advantageous for buyers to negotiate minimum order quantities (MOQs) that align with their needs.
-
Specifications and Customization: Customized products typically incur additional costs due to the need for specialized tooling and processes. Buyers should weigh the benefits of customization against the associated costs.
-
Material Quality and Certifications: Higher-quality materials and products that meet specific certifications (e.g., environmental standards) generally come at a premium. Buyers should assess whether the investment aligns with their project requirements.
-
Supplier Factors: The reputation and reliability of the supplier can affect pricing. Established suppliers may charge higher prices but offer greater assurance of quality and delivery timelines.
-
Incoterms: Understanding shipping terms is vital. Different Incoterms (like FOB, CIF) can shift costs between buyers and sellers, impacting the overall pricing structure.
What Tips Can Help Buyers Optimize Costs When Sourcing Wall Cladding?
International buyers can adopt several strategies to enhance cost-efficiency when sourcing wall cladding:
-
Negotiate Terms: Leverage your purchasing power by negotiating pricing, MOQs, and payment terms. A well-prepared buyer can secure better deals.
-
Evaluate Total Cost of Ownership (TCO): Consider not just the purchase price but also installation, maintenance, and durability. A higher upfront cost may result in lower long-term expenses.
-
Understand Pricing Nuances for International Sourcing: Be aware of currency fluctuations, import duties, and regional pricing differences. Buyers from Africa, South America, the Middle East, and Europe should factor these into their budgeting.
-
Conduct Thorough Supplier Research: Vet suppliers based on their production capabilities, quality control processes, and past performance. A reliable supplier can mitigate risks associated with delays and defects.
-
Stay Informed About Market Trends: Keeping abreast of industry trends can provide insights into pricing fluctuations and new materials, allowing buyers to make informed decisions.
Disclaimer on Indicative Prices
Prices for wall cladding materials can vary significantly based on the aforementioned factors and market conditions. It is advisable for buyers to conduct their own market research and obtain quotes from multiple suppliers to establish a realistic budget.
Alternatives Analysis: Comparing wall cladding manufacturer With Other Solutions
Introduction: What Are the Alternatives to Wall Cladding Manufacturers?
When considering wall cladding solutions, international B2B buyers must evaluate a range of options that can meet their specific needs. While traditional wall cladding manufacturers provide durable and aesthetically pleasing products, alternatives such as innovative wall systems, alternative materials, and modular solutions are gaining traction. Understanding the advantages and disadvantages of these alternatives is crucial for making an informed decision that aligns with project requirements and budget constraints.
Comparison Table of Wall Cladding Solutions
Comparison Aspect | Wall Cladding Manufacturer | Innovative Wall Systems | Alternative Material Solutions |
---|---|---|---|
Performance | High durability, insulation, and moisture resistance | High energy efficiency, customizable | Varies widely by material, may lack insulation |
Cost | Moderate to high initial investment | Often higher upfront costs but savings in energy | Generally lower, but may require more frequent replacement |
Ease of Implementation | Straightforward installation with professional help | Requires specialized installation skills | Often easier to install, depending on material |
Maintenance | Low maintenance, easy to clean | Low maintenance but may require specialized care | Maintenance can vary; some materials may degrade faster |
Best Use Case | Commercial and residential buildings needing longevity | Sustainable buildings focused on energy efficiency | Budget-conscious projects or temporary structures |
What Are the Pros and Cons of Innovative Wall Systems?
Innovative wall systems, such as insulated panels or modular wall units, offer significant advantages, particularly in terms of energy efficiency and customizability. These systems are designed to improve thermal performance, resulting in lower energy costs over time. However, they often come with higher initial costs and may require specialized skills for installation, which could increase project timelines. For projects emphasizing sustainability, these systems can be a compelling choice.
How Do Alternative Material Solutions Compare?
Alternative material solutions, which may include materials like bamboo, recycled plastics, or even metal cladding, can provide a more economical option for B2B buyers. These materials are often more affordable and can be easier to install, making them suitable for budget-conscious projects or temporary structures. However, the performance can vary significantly depending on the material chosen. Some may lack the insulation and durability that traditional wall cladding provides, leading to potential long-term costs that outweigh initial savings.
Conclusion: How to Choose the Right Wall Cladding Solution for Your Needs?
Selecting the right wall cladding solution requires a thorough understanding of both the manufacturer’s offerings and viable alternatives. B2B buyers should assess their specific project requirements, including budget, performance expectations, and long-term maintenance considerations. By comparing the characteristics of wall cladding manufacturers with innovative wall systems and alternative materials, buyers can make an informed choice that aligns with their goals, ensuring that the selected solution meets their operational and financial needs.
Essential Technical Properties and Trade Terminology for wall cladding manufacturer
What Are the Essential Technical Properties for Wall Cladding Manufacturing?
When sourcing wall cladding materials, understanding the technical properties is crucial for ensuring product quality and suitability for specific applications. Here are some key specifications to consider:
1. Material Grade
Material grade refers to the classification of the raw materials used in wall cladding, such as aluminum, vinyl, or composite materials. Different grades offer varying levels of durability, resistance to environmental factors, and aesthetic appeal. For B2B buyers, selecting the appropriate material grade can directly impact the longevity and maintenance costs of the cladding, making it essential to align material choice with project requirements.
2. Tolerance
Tolerance defines the allowable deviation from specified dimensions in manufacturing. It is critical for ensuring that panels fit correctly during installation, which affects both performance and aesthetics. A high level of tolerance can reduce installation time and costs, making it an important factor for B2B buyers who prioritize efficiency and quality in their projects.
3. Fire Resistance Rating
This property indicates how well the cladding material can withstand fire. Materials are classified based on their ability to resist flames and heat. For buyers in regions prone to wildfires or stringent building codes, understanding fire resistance ratings is vital for compliance and safety, ensuring that the cladding meets local regulations and minimizes risk.
4. Thermal Conductivity
Thermal conductivity measures how well a material can conduct heat. Low thermal conductivity is desirable for energy efficiency, as it helps maintain indoor temperatures and reduces heating and cooling costs. B2B buyers should consider this property when sourcing cladding to enhance building performance and sustainability.
5. Weather Resistance
This property indicates how well the cladding can withstand various weather conditions, including moisture, UV exposure, and temperature fluctuations. Selecting weather-resistant materials is crucial for ensuring the longevity of the cladding and reducing maintenance costs. Buyers should seek materials with proven performance in their specific climate conditions.
6. Surface Finish
The surface finish impacts both aesthetics and functionality, affecting factors like dirt resistance, ease of cleaning, and overall appearance. A high-quality finish can improve the visual appeal of a building, which is particularly important for commercial projects. Buyers should assess surface finish options to ensure they align with branding and maintenance strategies.
What Are Common Trade Terms in Wall Cladding Manufacturing?
Understanding industry jargon is essential for effective communication and negotiation in the B2B market. Here are some commonly used terms that buyers should know:
1. OEM (Original Equipment Manufacturer)
OEM refers to a company that produces parts or equipment that may be marketed by another manufacturer. In wall cladding, buyers may work with OEMs to source customized products tailored to their specifications. Knowing about OEM options can help buyers find solutions that meet unique project needs.
2. MOQ (Minimum Order Quantity)
MOQ is the smallest quantity of a product that a supplier is willing to sell. For international B2B buyers, understanding MOQ is critical for managing inventory costs and ensuring that purchasing aligns with project timelines. This knowledge can assist in negotiating better terms with suppliers.
3. RFQ (Request for Quotation)
An RFQ is a document that solicits bids from suppliers for specific products or services. For buyers, submitting an RFQ can streamline the sourcing process, enabling them to compare prices and capabilities from multiple manufacturers. It’s a strategic tool for ensuring competitive pricing and quality assurance.
4. Incoterms (International Commercial Terms)
Incoterms are a set of predefined commercial terms published by the International Chamber of Commerce (ICC) that clarify the responsibilities of buyers and sellers in international transactions. Familiarity with Incoterms can help buyers understand shipping, insurance, and risk management, ensuring smoother cross-border transactions.
5. Lead Time
Lead time refers to the time taken from placing an order to delivery. It is a critical factor for project planning and can impact timelines significantly. Buyers should inquire about lead times when sourcing wall cladding to ensure that materials arrive when needed, avoiding project delays.
6. Certification
Certification indicates that a product meets certain standards or regulations. For wall cladding, certifications can range from environmental impact to safety standards. Buyers should prioritize certified products to ensure compliance with industry regulations and enhance their credibility in the market.
By understanding these essential technical properties and trade terms, B2B buyers can make informed decisions, optimize procurement processes, and ultimately enhance the success of their projects.
Navigating Market Dynamics and Sourcing Trends in the wall cladding manufacturer Sector
What Are the Key Market Drivers Influencing the Wall Cladding Manufacturer Sector?
The wall cladding manufacturer sector is witnessing robust growth, propelled by several global drivers. Urbanization, particularly in Africa and South America, is driving demand for innovative building materials that enhance aesthetic appeal and energy efficiency. Additionally, the construction industry’s shift towards sustainable practices is reshaping sourcing trends, making eco-friendly materials a priority. Emerging technologies, such as Building Information Modeling (BIM) and advanced manufacturing techniques, are also influencing market dynamics by improving supply chain efficiency and project execution.
International B2B buyers should be aware of the increasing importance of digital platforms for sourcing wall cladding materials. E-commerce solutions and digital marketplaces are streamlining procurement processes, allowing buyers to compare products and prices from various manufacturers globally. This trend is particularly advantageous for buyers in regions like the Middle East and Europe, where access to a diverse range of suppliers can significantly enhance project outcomes.
How Is Sustainability Reshaping the Wall Cladding Manufacturing Landscape?
Sustainability is no longer a mere trend; it has become a critical aspect of the wall cladding manufacturer sector. The environmental impact of construction materials is under scrutiny, with buyers increasingly seeking options that minimize carbon footprints. This has led to a surge in demand for sustainable wall cladding solutions made from recycled materials or responsibly sourced timber.
Ethical sourcing is also gaining traction among international buyers. Companies are prioritizing suppliers who demonstrate transparency in their supply chains and adhere to fair labor practices. Green certifications, such as LEED (Leadership in Energy and Environmental Design) and FSC (Forest Stewardship Council), are becoming essential for manufacturers aiming to appeal to environmentally conscious B2B buyers. By opting for certified materials, buyers not only contribute to sustainability but also enhance their brand image in a competitive marketplace.
What Is the Historical Context of the Wall Cladding Industry?
The wall cladding industry has evolved significantly over the past few decades, transitioning from traditional materials like wood and brick to advanced composites and eco-friendly alternatives. This evolution has been driven by technological advancements and changing consumer preferences towards more sustainable construction practices.
Historically, wall cladding served primarily a protective function; however, it now plays a crucial role in energy efficiency and aesthetic design. As international B2B buyers continue to seek innovative solutions, manufacturers are compelled to adapt their offerings to meet evolving market demands, paving the way for a more sustainable and dynamic industry landscape.
In conclusion, understanding the market dynamics and sourcing trends in the wall cladding manufacturer sector is essential for international B2B buyers. By focusing on sustainability, leveraging technology, and staying informed about evolving materials, buyers can make strategic decisions that align with both their project requirements and ethical standards.
Frequently Asked Questions (FAQs) for B2B Buyers of wall cladding manufacturer
-
How do I solve the challenge of sourcing wall cladding manufacturers in different regions?
To effectively source wall cladding manufacturers across various regions, start by conducting thorough market research to identify reputable suppliers. Utilize platforms like Alibaba, Global Sources, or industry-specific directories. Attend international trade shows and exhibitions to meet manufacturers directly. Networking with local construction and architecture firms can also provide valuable insights. Finally, leverage online forums and social media groups focused on construction materials to gather recommendations and experiences from other buyers. -
What is the best wall cladding material for humid climates?
For humid climates, materials such as fiber cement, vinyl, or treated wood are often recommended due to their resistance to moisture and mold. Fiber cement offers durability and low maintenance, while vinyl is lightweight and comes in various styles. Treated wood can provide aesthetic appeal but requires regular maintenance to prevent rot. Always consider local environmental conditions and consult with suppliers on the best material options tailored to specific regional needs. -
How can I ensure the quality of wall cladding products before making a purchase?
To ensure product quality, request samples from potential manufacturers before placing a bulk order. Look for manufacturers who provide certifications, such as ISO or ASTM standards, which indicate adherence to quality benchmarks. Additionally, consider conducting factory audits or hiring third-party inspection services to verify production processes and material quality. Building a strong relationship with your supplier can also facilitate better communication regarding quality expectations. -
What are the typical minimum order quantities (MOQ) for wall cladding?
Minimum order quantities for wall cladding can vary significantly based on the manufacturer and the type of material. Generally, MOQs can range from a few hundred square meters to several thousand, depending on production capabilities and material costs. It is advisable to discuss your specific needs with manufacturers to negotiate favorable terms. Some suppliers may offer lower MOQs for customized orders, especially if they are keen to establish a new business relationship. -
What payment terms should I expect when sourcing wall cladding internationally?
Payment terms can vary widely among international suppliers. Common practices include upfront payments (typically 30-50%) with the balance due before shipping, or payment upon delivery. Some manufacturers may also offer letters of credit or escrow services for added security. Always clarify payment methods and terms in advance to avoid misunderstandings. Consider using secure payment platforms to protect your transactions when dealing with new suppliers. -
How can I effectively vet wall cladding manufacturers before making a decision?
Vetting manufacturers involves checking their business credentials, including company registration, years of operation, and industry reputation. Request references from previous clients and look for reviews online. Verify their production capabilities by visiting their facility if possible, or through virtual tours. Ensure they have the necessary certifications for quality and compliance with international standards. Engaging in direct communication can also help gauge their responsiveness and reliability. -
What logistics considerations should I keep in mind when importing wall cladding?
When importing wall cladding, consider the logistics of shipping, including freight costs, delivery times, and customs clearance. Choose a reliable freight forwarder experienced in handling construction materials to navigate complex regulations. Understand the import duties and taxes applicable in your country. Additionally, factor in storage requirements and local transportation arrangements to ensure smooth delivery from the port to your project site. -
How can I customize wall cladding to fit my specific project requirements?
Customization options for wall cladding can include size, color, texture, and material type. Most manufacturers are open to custom orders, but it’s essential to communicate your specific needs clearly. Provide detailed specifications and consider collaborating with the manufacturer’s design team to achieve the desired outcome. Be mindful of potential impacts on MOQs and lead times, as custom orders may require additional production time.
Important Disclaimer & Terms of Use
⚠️ Important Disclaimer
The information provided in this guide, including content regarding manufacturers, technical specifications, and market analysis, is for informational and educational purposes only. It does not constitute professional procurement advice, financial advice, or legal advice.
While we have made every effort to ensure the accuracy and timeliness of the information, we are not responsible for any errors, omissions, or outdated information. Market conditions, company details, and technical standards are subject to change.
B2B buyers must conduct their own independent and thorough due diligence before making any purchasing decisions. This includes contacting suppliers directly, verifying certifications, requesting samples, and seeking professional consultation. The risk of relying on any information in this guide is borne solely by the reader.
Strategic Sourcing Conclusion and Outlook for wall cladding manufacturer
In conclusion, strategic sourcing plays a pivotal role for international B2B buyers in the wall cladding manufacturing sector. By prioritizing the selection of reliable suppliers, businesses can enhance product quality while optimizing costs. Key takeaways include the importance of conducting thorough supplier assessments, leveraging technology for supply chain transparency, and embracing sustainable practices that resonate with modern consumer preferences.
How Can B2B Buyers Enhance Their Sourcing Strategy for Wall Cladding?
International buyers from Africa, South America, the Middle East, and Europe, particularly in Germany and France, should focus on developing long-term relationships with manufacturers who demonstrate innovation and sustainability. This not only ensures a consistent supply of high-quality materials but also aligns with global trends towards eco-friendly construction solutions.
What Does the Future Hold for Wall Cladding Manufacturers?
Looking ahead, the wall cladding market is poised for growth, driven by urbanization and the demand for aesthetically pleasing, durable, and energy-efficient building solutions. B2B buyers are encouraged to stay informed about emerging technologies and materials that can enhance their projects. By embracing strategic sourcing, you can position your business to capitalize on these opportunities, ensuring competitive advantage in a rapidly evolving marketplace. Engage with manufacturers today to explore how strategic sourcing can elevate your projects and drive long-term success.