The Ultimate Guide to Welding Wire Supplier (2025)
Introduction: Navigating the Global Market for welding wire supplier
In the competitive landscape of global manufacturing, sourcing high-quality welding wire suppliers can present a formidable challenge for international B2B buyers. From the bustling markets of Africa to the emerging economies of South America and the established industries in Europe and the Middle East, the demand for reliable welding materials has never been more critical. This guide serves as a comprehensive resource, equipping buyers with the knowledge needed to navigate the complexities of the welding wire market. It covers a wide range of topics, including various types of welding wires, their specific applications, effective supplier vetting processes, and insights into cost structures.
Understanding the nuances of welding wire procurement is essential for making informed purchasing decisions. This guide empowers B2B buyers by providing actionable insights that help them identify reputable suppliers, evaluate product quality, and negotiate favorable terms. Whether you are a manufacturer in Poland seeking to enhance your production capabilities or a construction firm in the Middle East aiming to streamline operations, this resource addresses your unique challenges. By leveraging the information presented, you can confidently approach your sourcing strategies and forge partnerships that drive efficiency and success in your projects.
As we delve deeper into this guide, you will find essential tools and tips to ensure that your investment in welding materials yields maximum returns while meeting industry standards.
Understanding welding wire supplier Types and Variations
Type Name | Key Distinguishing Features | Primary B2B Applications | Brief Pros & Cons for Buyers |
---|---|---|---|
Solid Welding Wire Supplier | Made from a single metal, typically low carbon steel | General fabrication, structural welding | Pros: High strength, easy to use. Cons: Limited to specific applications. |
Flux-Cored Welding Wire Supplier | Contains a core of flux material for better arc stability | Heavy-duty applications, outdoor welding | Pros: Excellent penetration, less sensitivity to wind. Cons: More expensive and requires special equipment. |
Stainless Steel Welding Wire Supplier | Offers corrosion resistance, ideal for high-temperature applications | Food processing, chemical industries | Pros: Durable and resistant to oxidation. Cons: Higher cost compared to carbon steel. |
Aluminum Welding Wire Supplier | Lightweight and specifically designed for aluminum alloys | Automotive, aerospace, and marine industries | Pros: Good conductivity and corrosion resistance. Cons: Requires precise welding techniques. |
MIG Welding Wire Supplier | Versatile wire used in Metal Inert Gas welding | Automotive repair, fabrication, and construction | Pros: Fast welding speed, suitable for various metals. Cons: Requires shielding gas and may need more maintenance. |
What Are the Characteristics of Solid Welding Wire Suppliers?
Solid welding wire suppliers provide wires made from a single metal, predominantly low carbon steel. This type of wire is characterized by its high tensile strength and ease of use, making it suitable for general fabrication and structural welding. When purchasing solid welding wire, B2B buyers should consider the wire’s diameter and its compatibility with the welding equipment in use. Solid wires are ideal for projects requiring consistent quality and strength but may not be suitable for more specialized applications.
How Do Flux-Cored Welding Wire Suppliers Differ?
Flux-cored welding wire suppliers offer wires that contain a core of flux material, which enhances arc stability and reduces spatter. This type of wire is particularly advantageous for heavy-duty applications and outdoor welding, where environmental factors may impede the welding process. Buyers should assess the specific flux type and the wire’s diameter to ensure compatibility with their welding machines. While flux-cored wires provide excellent penetration and are less sensitive to wind, they generally come at a higher price point and may require specialized equipment.
What Are the Benefits of Using Stainless Steel Welding Wire Suppliers?
Stainless steel welding wire suppliers focus on wires designed for corrosion resistance and high-temperature applications. These wires are essential in industries such as food processing and chemicals, where durability and resistance to oxidation are critical. B2B buyers should evaluate the wire’s grade and ensure it meets the specific requirements of their projects. While stainless steel wires are more costly than carbon steel options, their longevity and performance in harsh environments often justify the investment.
Why Choose Aluminum Welding Wire Suppliers?
Aluminum welding wire suppliers specialize in lightweight wires designed for aluminum alloys, commonly used in the automotive, aerospace, and marine sectors. These wires are known for their excellent conductivity and corrosion resistance. Buyers should consider the specific alloy and wire diameter, as aluminum welding requires precise techniques to avoid defects. While aluminum wires offer numerous advantages, the need for meticulous welding practices can be a drawback for some businesses.
What Makes MIG Welding Wire Suppliers a Popular Choice?
MIG welding wire suppliers provide versatile wires used in Metal Inert Gas (MIG) welding. This type of wire is favored for its fast welding speed and adaptability to various metals, making it ideal for automotive repair and construction projects. When selecting MIG wires, B2B buyers should focus on the wire’s diameter and the corresponding shielding gas required. Although MIG wires are easy to work with, they do require maintenance and careful handling to ensure optimal performance.
Related Video: BEST Flux Core Wire! +Welding Tips for Beginner Welders
Key Industrial Applications of welding wire supplier
Industry/Sector | Specific Application of welding wire supplier | Value/Benefit for the Business | Key Sourcing Considerations for this Application |
---|---|---|---|
Automotive Manufacturing | Fabrication of vehicle frames and components | Enhances structural integrity and safety | Material specifications, certifications, and supplier reliability |
Construction | Joining steel beams and metal structures | Ensures durability and longevity of structures | Compliance with local standards and availability of varied wire types |
Oil and Gas | Pipeline welding and repair | Reduces downtime and maintains operational efficiency | Resistance to corrosion and extreme temperatures |
Shipbuilding | Assembly of hulls and maritime structures | Increases ship safety and performance | Quality control processes and international shipping capabilities |
Aerospace | Welding of aircraft components and fuselage | Critical for safety and performance in flight | Strict adherence to aerospace standards and traceability of materials |
What Are the Key Applications of Welding Wire in Automotive Manufacturing?
In the automotive sector, welding wire suppliers play a crucial role in the fabrication of vehicle frames and components. These wires are used to join various metals, ensuring that the final products meet stringent safety standards. The quality of the welding wire directly affects the structural integrity of the vehicle, making it essential for suppliers to provide materials that are reliable and compliant with industry standards. International buyers, especially from regions like Europe and South America, should prioritize suppliers that offer certifications and demonstrate a history of quality assurance.
How Is Welding Wire Utilized in Construction Projects?
Welding wire is extensively used in the construction industry for joining steel beams and other metal structures. This application is vital for ensuring the durability and longevity of buildings and bridges. Suppliers must provide welding wires that can withstand various environmental conditions, as construction projects often face exposure to moisture and temperature fluctuations. For international buyers, understanding local building codes and sourcing wires that comply with these regulations is crucial to avoid costly rework and ensure safety.
What Role Does Welding Wire Play in the Oil and Gas Sector?
In the oil and gas industry, welding wire is essential for pipeline welding and repair. The ability to create strong, leak-proof joints is critical to maintaining operational efficiency and minimizing downtime. Suppliers must offer wires that are resistant to corrosion and capable of withstanding extreme temperatures, as these pipelines often operate under harsh conditions. International buyers should consider suppliers with a proven track record in this sector, ensuring that materials meet the specific demands of oil and gas applications.
How Is Welding Wire Important in Shipbuilding?
Welding wire is integral to the shipbuilding industry, particularly in the assembly of hulls and other maritime structures. This application requires high-quality wires that can endure the stresses of marine environments. The safety and performance of ships depend significantly on the quality of the welds made using these wires. Buyers from regions like the Middle East and Africa should focus on suppliers who can demonstrate robust quality control processes and have experience in maritime applications.
Why Is Welding Wire Critical in Aerospace Applications?
In aerospace, welding wire is utilized for joining aircraft components and fuselage sections, where safety and performance are paramount. The strict standards of the aerospace industry require suppliers to provide materials that not only meet regulatory requirements but also exhibit excellent mechanical properties. International buyers need to ensure that their suppliers can provide traceability of materials and comply with aerospace certification standards, as any failure in this sector can have severe consequences.
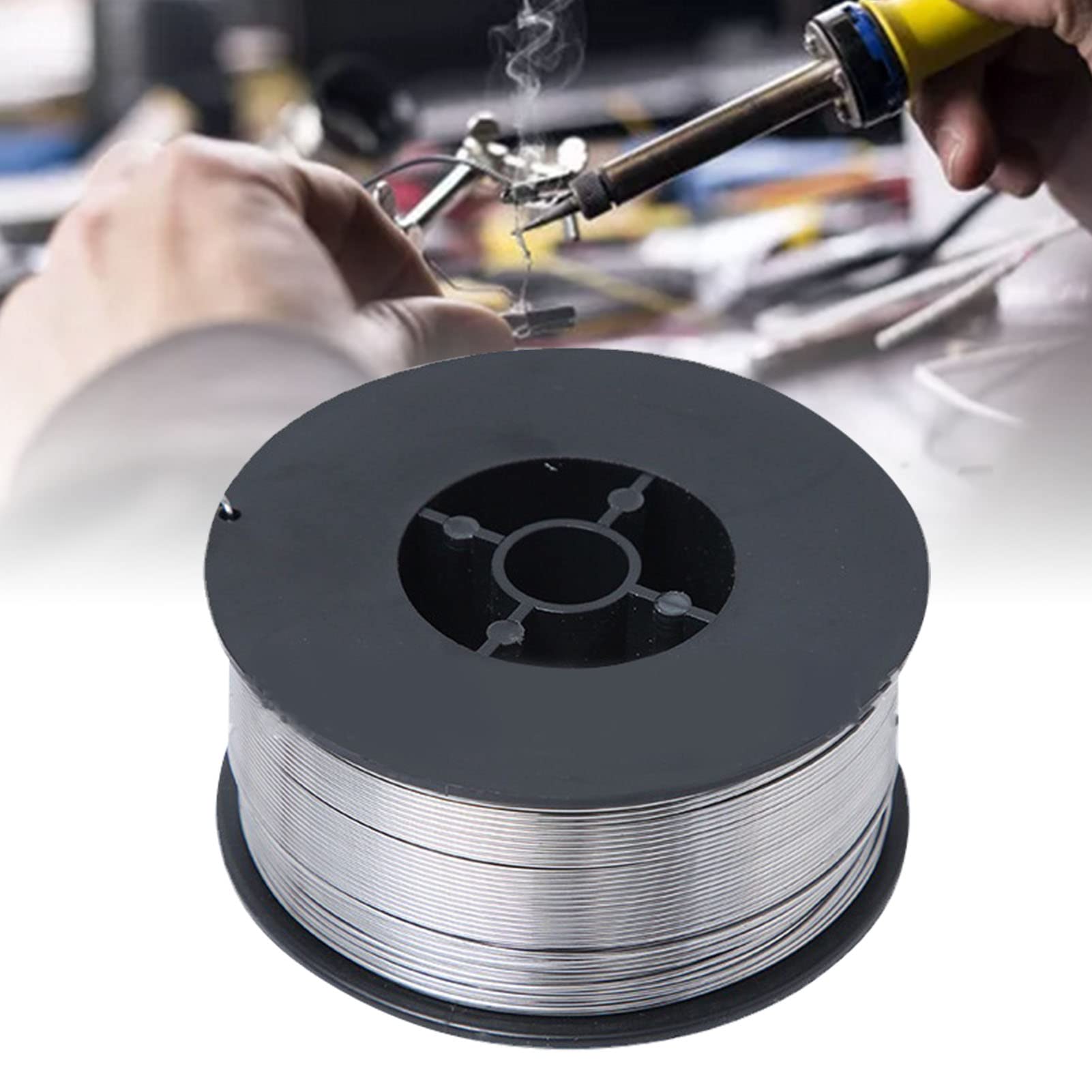
A stock image related to welding wire supplier.
Related Video: What is MIG Welding? (GMAW)
3 Common User Pain Points for ‘welding wire supplier’ & Their Solutions
Scenario 1: Inconsistent Quality of Welding Wire
The Problem: Many B2B buyers sourcing welding wire from international suppliers face the challenge of inconsistent quality. This inconsistency can lead to significant issues in production, including weld failures, rework, and increased costs. Buyers in regions like Africa and South America may have limited access to reliable suppliers, making it difficult to ensure that the welding wire meets the required standards for their specific applications.
The Solution: To mitigate quality issues, it is crucial to conduct thorough due diligence when selecting a welding wire supplier. Start by requesting certifications and quality assurance documentation, such as ISO 9001 or specific welding wire standards relevant to your industry. Establish a robust supplier evaluation process that includes a review of customer feedback and historical performance metrics. Additionally, consider requesting samples for testing before placing large orders. This proactive approach not only helps in verifying the quality of the welding wire but also builds a strong foundation for a long-term supplier relationship.
Scenario 2: High Shipping Costs and Delays
The Problem: B2B buyers, particularly from regions like the Middle East and Europe, often encounter high shipping costs and delays when importing welding wire. These issues can disrupt production schedules, leading to missed deadlines and financial losses. Buyers are frequently left scrambling to find last-minute alternatives, which can compromise project integrity and increase expenses.
The Solution: To address shipping challenges, buyers should explore local suppliers and distributors of welding wire who can provide competitive pricing without the added burden of international shipping costs. Establishing relationships with multiple suppliers can provide flexibility in sourcing. Additionally, consider negotiating bulk shipping agreements or utilizing freight forwarders who specialize in industrial goods to minimize shipping expenses. Implementing a just-in-time inventory system can also help manage costs and ensure that welding wire is available as needed without excess inventory.
Scenario 3: Difficulty in Specifying the Right Welding Wire Type
The Problem: Buyers often struggle with selecting the appropriate type of welding wire for their specific applications, leading to suboptimal welding results. Factors such as material compatibility, wire diameter, and coating type can greatly influence the effectiveness of the welding process. This challenge is particularly pronounced for buyers in diverse industries, such as construction and automotive, where precise specifications are critical.
The Solution: To overcome the difficulties in selecting the right welding wire, buyers should invest time in understanding the specific requirements of their welding projects. This includes consulting with welding engineers or technical experts who can provide insights into material compatibility and appropriate wire specifications. Additionally, suppliers often provide technical support and resources; take advantage of these offerings by engaging in discussions about your specific needs. Creating a detailed specification sheet that outlines the intended application, material types, and welding conditions can also facilitate clearer communication with suppliers, ensuring that you receive the most suitable welding wire for your projects.
Strategic Material Selection Guide for welding wire supplier
When selecting welding wire materials, international B2B buyers must consider various factors that affect performance, cost, and compliance with industry standards. Below, we analyze four common materials used in welding wire production, focusing on their properties, advantages and disadvantages, applications, and specific considerations for buyers from regions like Africa, South America, the Middle East, and Europe.
What Are the Key Properties of Mild Steel Welding Wire?
Mild steel welding wire is one of the most widely used materials in welding applications due to its favorable properties. It typically has a high tensile strength, good ductility, and excellent weldability, making it suitable for a variety of applications. Mild steel wires can withstand moderate temperatures and pressures, but they are less resistant to corrosion compared to other materials.
Pros:
– Cost-effective and widely available.
– Excellent weldability and mechanical properties.
Cons:
– Limited corrosion resistance, requiring protective coatings in certain environments.
– Not suitable for high-temperature applications.
Impact on Application:
Mild steel welding wire is ideal for general fabrication and construction, particularly in environments where corrosion is not a primary concern.
Considerations for International Buyers:
Buyers should ensure compliance with standards like ASTM A36 and consider local environmental conditions that may affect the longevity of mild steel products.
How Does Stainless Steel Welding Wire Compare?
Stainless steel welding wire is known for its superior corrosion resistance and strength at elevated temperatures. This material is particularly suitable for applications in industries such as food processing, chemical manufacturing, and marine environments where exposure to corrosive elements is common.
Pros:
– Exceptional corrosion resistance and durability.
– High strength and temperature resistance.
Cons:
– Higher cost compared to mild steel.
– More complex manufacturing processes, which can affect lead times.
Impact on Application:
Stainless steel welding wire is crucial for applications requiring hygiene and resistance to harsh chemicals, making it a preferred choice in sectors like pharmaceuticals and food production.
Considerations for International Buyers:
Buyers should look for compliance with standards such as ASTM A312 and ensure that the wire meets specific grades (e.g., 304, 316) based on application needs.
What Are the Advantages of Flux-Cored Welding Wire?
Flux-cored welding wire offers a unique advantage in that it can be used in outdoor conditions without the need for shielding gas, making it ideal for construction and repair applications. This type of wire is typically filled with flux, which helps to protect the weld pool from contamination.
Pros:
– Versatile and can be used in various positions.
– Good penetration and high deposition rates.
Cons:
– Can produce more smoke and spatter than solid wires.
– Requires careful handling and storage to prevent moisture absorption.
Impact on Application:
Flux-cored wires are particularly effective for heavy fabrication and structural welding, especially in outdoor conditions.
Considerations for International Buyers:
Ensure that the selected wire meets relevant standards like AWS A5.20 and consider the specific requirements of the project, including environmental conditions.
Why Choose Aluminum Welding Wire?
Aluminum welding wire is essential for applications requiring lightweight and corrosion-resistant materials. This wire is often used in the automotive and aerospace industries due to its excellent strength-to-weight ratio.
Pros:
– Lightweight and corrosion-resistant.
– Good electrical conductivity.
Cons:
– More expensive than other welding wires.
– Requires specific welding techniques and equipment.
Impact on Application:
Aluminum welding wire is ideal for applications in industries where weight reduction is critical, such as aerospace and automotive manufacturing.
Considerations for International Buyers:
Buyers should ensure compliance with standards like AWS A5.10 and be aware of the specific welding techniques required for aluminum, which may differ from those used for steel.
Summary Table of Welding Wire Materials
Material | Typical Use Case for welding wire supplier | Key Advantage | Key Disadvantage/Limitation | Relative Cost (Low/Med/High) |
---|---|---|---|---|
Mild Steel | General fabrication and construction | Cost-effective and widely available | Limited corrosion resistance | Low |
Stainless Steel | Food processing and chemical industries | Exceptional corrosion resistance | Higher cost and complex manufacturing | High |
Flux-Cored | Heavy fabrication and structural welding | Versatile and good penetration | More smoke and spatter | Medium |
Aluminum | Automotive and aerospace applications | Lightweight and corrosion-resistant | More expensive and requires specific techniques | High |
This strategic material selection guide provides critical insights for international B2B buyers, enabling them to make informed decisions based on material properties, application suitability, and compliance with industry standards.
In-depth Look: Manufacturing Processes and Quality Assurance for welding wire supplier
What Are the Main Stages in the Manufacturing Process of Welding Wire?
The manufacturing of welding wire involves several critical stages, each designed to ensure the final product meets the necessary specifications for strength and durability. The primary stages include:
-
Material Preparation:
– The process begins with selecting high-quality raw materials, typically consisting of steel, stainless steel, or aluminum. These materials are sourced from certified suppliers to ensure consistency and reliability.
– The raw materials undergo chemical analysis to verify their composition and mechanical properties, ensuring they meet industry standards. -
Forming:
– During this stage, the raw materials are processed into wire through methods such as drawing and rolling. Drawing involves pulling the material through a series of dies to achieve the desired diameter and tensile strength.
– Advanced techniques like cold drawing are often employed to enhance the mechanical properties of the wire, ensuring it can withstand high-stress applications. -
Assembly:
– After forming, the wire may be treated with various coatings such as copper or zinc to improve conductivity and corrosion resistance. This step is crucial for wires intended for specific applications, such as gas welding.
– The wires are then bundled and cut into specified lengths, depending on customer requirements. -
Finishing:
– The final stage involves quality checks and packaging. This includes ensuring the wire is free from defects and meets the specified tolerances.
– Proper labeling and packaging are essential for protecting the product during transportation and storage.
How Is Quality Assurance Implemented in Welding Wire Manufacturing?
Quality assurance (QA) in welding wire manufacturing is vital to ensure the product’s reliability and performance. Here’s how it typically works:
-
International Standards Compliance:
– Many manufacturers adhere to international quality management standards such as ISO 9001, which outlines the requirements for a quality management system (QMS).
– Additionally, industry-specific certifications, such as CE marking for products sold in Europe and API standards for oil and gas applications, may also be required. -
Quality Control Checkpoints:
– Incoming Quality Control (IQC): This step involves inspecting raw materials upon arrival to ensure they meet predetermined specifications.
– In-Process Quality Control (IPQC): Throughout the manufacturing process, various checkpoints are established to monitor critical parameters such as wire diameter, tensile strength, and surface quality.
– Final Quality Control (FQC): After production, the finished products undergo rigorous testing to verify their compliance with industry standards and customer specifications. -
Common Testing Methods:
– Manufacturers typically employ several testing methods, including tensile tests, bend tests, and chemical composition analyses. Non-destructive testing (NDT) techniques may also be used to assess the integrity of the wire without damaging it.
How Can B2B Buyers Verify Supplier Quality Control Processes?
For international B2B buyers, particularly those in Africa, South America, the Middle East, and Europe, verifying the quality control processes of a welding wire supplier is essential. Here are some actionable steps:
-
Supplier Audits:
– Conducting regular audits of potential suppliers allows buyers to assess their manufacturing processes and quality control systems firsthand. During these audits, buyers can evaluate compliance with international standards and internal QA protocols. -
Requesting Documentation and Reports:
– Buyers should ask for detailed documentation regarding the supplier’s quality assurance processes. This includes certificates of compliance, test reports for specific batches, and records of any corrective actions taken in response to quality issues. -
Third-Party Inspections:
– Engaging third-party inspection services can provide an unbiased evaluation of a supplier’s manufacturing and quality control practices. This is particularly useful for buyers who may not have the resources to conduct comprehensive audits themselves.
What Are the Nuances of Quality Control for International B2B Buyers?
When sourcing welding wire from international suppliers, buyers must be aware of several nuances that can affect quality control:
-
Regional Standards and Regulations:
– Different regions may have specific standards that welding wire must meet. For instance, European buyers may require CE marking, while those in the Middle East might look for compliance with Gulf Standards (GSO).
– Understanding these regional requirements is crucial for ensuring that the purchased products can be used in the intended applications without legal or safety issues. -
Cultural and Communication Considerations:
– Effective communication is vital when dealing with suppliers from diverse cultural backgrounds. Misunderstandings regarding quality expectations can lead to disputes and product returns.
– Buyers should establish clear specifications and engage in regular communication to ensure alignment on quality standards and expectations. -
Logistics and Supply Chain Factors:
– The reliability of logistics and supply chain management can impact the quality of welding wire. Delays or poor handling during transportation can lead to damage or degradation of the product.
– Buyers should work with suppliers who have a proven track record of managing logistics effectively, ensuring that products arrive in optimal condition.
Conclusion
Understanding the manufacturing processes and quality assurance measures in welding wire production is essential for B2B buyers. By focusing on the key stages of manufacturing, verifying quality control processes, and being aware of international nuances, buyers can make informed decisions that enhance their operational efficiency and product quality. This strategic approach not only mitigates risks but also fosters stronger partnerships with reliable suppliers across Africa, South America, the Middle East, and Europe.
Practical Sourcing Guide: A Step-by-Step Checklist for ‘welding wire supplier’
In the competitive landscape of international B2B sourcing, particularly for welding wire suppliers, a structured approach is essential. This checklist is designed to guide buyers, especially those from Africa, South America, the Middle East, and Europe, through the critical steps of the procurement process. By following these actionable insights, you can ensure that your sourcing decisions are informed and strategic.
Step 1: Define Your Technical Specifications
Establishing clear technical specifications is the foundation of successful sourcing. Identify the types of welding wires you require (e.g., MIG, TIG, or stick welding wires) along with the materials (e.g., stainless steel, aluminum) and sizes. This clarity helps in communicating effectively with potential suppliers and ensures that the products meet your operational needs.
Step 2: Research Potential Suppliers
Conduct thorough research to identify potential suppliers that specialize in welding wire. Utilize industry directories, trade shows, and online platforms to compile a list of candidates. Focus on suppliers with a solid reputation in the market and those that cater to your specific region, as they may have a better understanding of local regulations and logistics.
Step 3: ✅ Verify Supplier Certifications
Confirm that your shortlisted suppliers hold relevant certifications and quality standards, such as ISO 9001 or AWS (American Welding Society) certifications. These credentials are indicators of the supplier’s commitment to quality and compliance with industry regulations, which can significantly reduce risks associated with product quality.
Step 4: Evaluate Supplier Experience and Reputation
Before making a decision, assess the experience and reputation of potential suppliers. Look for customer testimonials, case studies, and industry awards that demonstrate their reliability and performance. Engaging with previous clients or industry peers can provide valuable insights into the supplier’s capabilities and customer service.
Step 5: Request Product Samples
Always request product samples before finalizing a supplier. This step allows you to assess the quality and performance of the welding wire firsthand. Evaluate the samples based on your technical specifications, and consider conducting tests to ensure they meet your operational requirements.
Step 6: Discuss Pricing and Payment Terms
Engage in discussions about pricing structures and payment terms with your selected suppliers. Understand the pricing model (e.g., per unit, bulk discounts) and clarify any additional costs such as shipping or customs fees. Favor suppliers that offer transparent pricing and flexible payment options, which can help manage your cash flow effectively.
Step 7: Establish a Communication Plan
Establish a clear communication plan with your chosen supplier to ensure smooth collaboration. Define points of contact, preferred communication channels, and frequency of updates. A robust communication strategy minimizes misunderstandings and fosters a strong working relationship, essential for long-term partnership success.
By following this step-by-step checklist, international B2B buyers can streamline their sourcing process for welding wire suppliers, ensuring they make informed decisions that align with their technical needs and business goals.
Comprehensive Cost and Pricing Analysis for welding wire supplier Sourcing
What Are the Key Cost Components in Welding Wire Supplier Sourcing?
When sourcing welding wire, understanding the cost structure is vital for making informed purchasing decisions. The primary cost components include:
-
Materials: The type of raw materials used significantly influences the overall cost. Common materials include mild steel, stainless steel, and aluminum, each with varying price points based on market demand and availability.
-
Labor: Labor costs encompass wages paid to skilled workers involved in manufacturing the welding wire. These costs can vary widely depending on the region, with some countries having higher labor costs due to stricter labor laws and standards.
-
Manufacturing Overhead: This includes indirect costs related to production, such as utilities, rent, and equipment maintenance. Efficient manufacturing processes can help reduce these overheads, affecting the final price.
-
Tooling: The cost of tools and dies used in the manufacturing process can be significant, especially for customized wire types. Investment in high-quality tooling can lead to better precision and lower scrap rates.
-
Quality Control (QC): Ensuring that the welding wire meets specific standards involves costs related to testing and quality assurance. Certifications such as ISO or AWS can add to costs but may also enhance product credibility.
-
Logistics: Transportation costs, including shipping and handling, are crucial, especially for international buyers. Factors like distance, shipping method, and customs duties can significantly affect the total logistics cost.
-
Margin: Suppliers typically add a profit margin to cover their costs and generate revenue. Understanding the typical margins in the industry can help buyers negotiate better prices.
How Do Pricing Influencers Affect Welding Wire Costs?
Several factors influence the pricing of welding wire, which international buyers should consider:
-
Volume/MOQ (Minimum Order Quantity): Larger orders often lead to lower per-unit costs. Suppliers may provide discounts for bulk purchases, making it essential for buyers to assess their needs carefully.
-
Specifications and Customization: Customized welding wire specifications, such as diameter or coating type, can lead to higher costs. Standard products are generally more cost-effective, so buyers should evaluate if customization is necessary.
-
Material Quality and Certifications: Higher quality materials and certifications can increase costs but also improve performance and reliability. Buyers should weigh the benefits of investing in higher-quality products against their budget constraints.
-
Supplier Factors: The reputation and location of the supplier can influence pricing. Established suppliers with good track records may charge premium prices, whereas new or lesser-known suppliers might offer more competitive rates.
-
Incoterms: Understanding Incoterms is crucial for international transactions. These terms define responsibilities for shipping, insurance, and tariffs, which can significantly impact the total cost of acquisition.
What Tips Can Help Buyers Negotiate Better Prices?
To achieve cost-efficiency in welding wire sourcing, buyers should consider the following strategies:
-
Negotiate Terms: Don’t hesitate to negotiate pricing, payment terms, and delivery schedules with suppliers. Building a strong relationship can lead to better deals over time.
-
Evaluate Total Cost of Ownership (TCO): Look beyond the initial purchase price. Consider long-term factors like maintenance, performance, and potential waste, which can affect the total cost over the product’s lifespan.
-
Market Research: Stay informed about market trends and price fluctuations. Understanding the market landscape can empower buyers during negotiations and help identify the best times to purchase.
-
Engage Multiple Suppliers: Comparing quotes from various suppliers can uncover better deals. It also creates a competitive environment that may lead to more favorable terms.
-
Understand Regional Pricing Nuances: International buyers should be aware of regional differences in pricing structures, particularly in Africa, South America, the Middle East, and Europe. Local economic conditions, tariffs, and currency fluctuations can all affect pricing.
Disclaimer on Indicative Prices
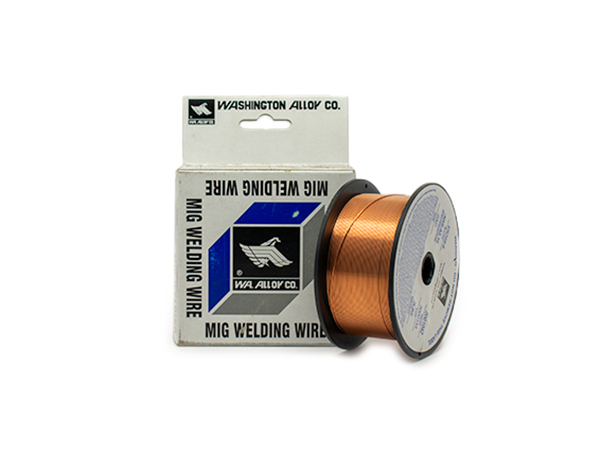
A stock image related to welding wire supplier.
Prices for welding wire can fluctuate based on market conditions, material availability, and supplier pricing strategies. It is advisable for buyers to obtain up-to-date quotes and conduct thorough due diligence before finalizing purchases.
Alternatives Analysis: Comparing welding wire supplier With Other Solutions
Exploring Alternatives to Welding Wire Suppliers: What Are Your Options?
In the competitive landscape of manufacturing and construction, choosing the right materials and suppliers is crucial for operational efficiency and product quality. While traditional welding wire suppliers have been the go-to option for many businesses, it’s essential to consider alternative solutions that may offer unique advantages. This section provides a comparative analysis of welding wire suppliers against other viable methods, helping international B2B buyers from regions like Africa, South America, the Middle East, and Europe make informed decisions.
Comparison Aspect | Welding Wire Supplier | Laser Welding Technology | Friction Stir Welding |
---|---|---|---|
Performance | High strength, versatile | Very high precision, low heat-affected zone | Excellent for aluminum and similar metals |
Cost | Moderate | High initial investment, lower operational costs | Moderate to high, depending on setup |
Ease of Implementation | Relatively easy | Requires specialized training and equipment | Requires specialized training and tooling |
Maintenance | Minimal | Higher due to complex systems | Moderate, depending on tooling wear |
Best Use Case | General fabrication needs | High-precision applications (aerospace, automotive) | Joining materials with low melting points |
How Does Laser Welding Technology Compare to Welding Wire Suppliers?
Laser welding technology utilizes focused laser beams to melt and fuse materials together. This method is known for its precision and minimal thermal distortion, making it ideal for applications where the integrity of the material must be preserved, such as in aerospace and automotive industries.
Pros:
– High-speed and high-quality welds.
– Ability to weld thin materials without warping.
Cons:
– Requires significant upfront investment in equipment.
– Operators need specialized training, which can lead to increased operational costs.
What Are the Benefits of Friction Stir Welding Over Traditional Welding Wire Suppliers?
Friction stir welding (FSW) is a solid-state joining process that uses a rotating tool to generate heat through friction, allowing materials to be joined without reaching their melting point. This method is particularly effective for metals that are difficult to weld using traditional methods.
Pros:
– Produces strong, high-quality joints with minimal defects.
– Particularly effective for aluminum and other non-ferrous materials.
Cons:
– The initial setup cost can be high.
– Tool wear can be significant, leading to increased maintenance and replacement costs.
Making the Right Choice: How Can B2B Buyers Select the Best Solution for Their Needs?
When considering alternatives to welding wire suppliers, B2B buyers must evaluate their specific project requirements, budget constraints, and operational capabilities. Factors such as the type of materials being welded, the precision required, and the volume of production will influence the best choice.
For general fabrication needs, traditional welding wire suppliers may still be the best option due to their ease of use and lower initial costs. However, for high-precision applications or specialized materials, investing in technologies like laser welding or friction stir welding could yield significant long-term benefits. Ultimately, a thorough assessment of these alternatives, aligned with the company’s strategic goals and operational capabilities, will lead to the most effective decision.
Essential Technical Properties and Trade Terminology for welding wire supplier
What Are the Key Technical Properties of Welding Wire That Buyers Should Know?
When sourcing welding wire, understanding its technical properties is crucial for ensuring the right fit for specific applications. Here are some of the most important specifications:
1. Material Grade
The material grade indicates the composition of the welding wire, affecting its strength, corrosion resistance, and suitability for different welding processes. Common grades include ER70S-6 for mild steel and ER308L for stainless steel. B2B buyers must select the appropriate grade to match their project requirements, as using the wrong material can lead to structural failures or increased costs.
2. Diameter
The diameter of the welding wire plays a significant role in determining the welding speed and the amount of heat input. Typical diameters range from 0.023 inches to 0.045 inches. Buyers should consider the thickness of the materials being welded, as a larger diameter is often required for thicker sections to ensure adequate fusion and penetration.
3. Tolerance
Tolerance refers to the allowable variation in the diameter of the welding wire. This specification is crucial for achieving consistent arc stability and ensuring uniform weld quality. Tight tolerances are often necessary for precision applications, making it essential for buyers to verify that suppliers can meet these specifications.
4. Coating Type
Welding wire can come with various coatings, such as flux-cored or solid wires. The coating affects the welding process, including the ease of use and the quality of the weld. Understanding the differences helps buyers choose the right type for their specific applications, whether they require deep penetration or a clean finish.
5. Mechanical Properties
Mechanical properties such as tensile strength and elongation are vital for assessing the wire’s performance under stress. These properties can influence the overall strength of the weld joint, which is particularly important in structural applications. Buyers should always request these specifications to ensure the wire meets the necessary industry standards.
What Are Common Trade Terms Related to Welding Wire Supply?
Familiarity with industry terminology can significantly streamline communication between B2B buyers and suppliers. Here are several essential terms:
1. OEM (Original Equipment Manufacturer)
This term refers to companies that manufacture products based on the specifications provided by another company. In the context of welding wire, buyers often work with OEMs to source specialized wire tailored for specific machinery or applications.
2. MOQ (Minimum Order Quantity)
MOQ is the smallest number of units that a supplier is willing to sell. Understanding MOQ is crucial for buyers to avoid overstocking or facing supply chain disruptions. Some suppliers may offer flexibility on MOQs, so it’s beneficial to negotiate based on project needs.
3. RFQ (Request for Quotation)
An RFQ is a formal document sent to suppliers to request pricing and terms for specific products. For welding wire suppliers, an RFQ should detail technical specifications, quantities, and delivery timelines to ensure accurate and competitive pricing.
4. Incoterms (International Commercial Terms)
Incoterms are a series of international rules that define the responsibilities of buyers and sellers in shipping agreements. Understanding terms such as FOB (Free On Board) or CIF (Cost, Insurance, and Freight) helps buyers navigate shipping costs and responsibilities, ensuring clarity in international transactions.
5. Certification Standards
This refers to the industry standards that welding wires must meet, such as ISO or AWS (American Welding Society) standards. Certification ensures that the wire complies with safety and quality regulations, which is vital for buyers who need assurance regarding the reliability of their materials.
By grasping these technical properties and trade terms, international B2B buyers can make informed decisions when sourcing welding wire, ultimately leading to improved project outcomes and cost efficiency.
Navigating Market Dynamics and Sourcing Trends in the welding wire supplier Sector
What Are the Current Market Dynamics and Key Trends in the Welding Wire Supplier Sector?
The welding wire supplier sector is experiencing significant transformation driven by several global trends. One of the primary drivers is the increasing demand for high-quality welding materials in industries such as construction, automotive, and manufacturing. As economies in Africa, South America, the Middle East, and Europe recover from the pandemic, there is a noticeable uptick in infrastructure projects, which requires reliable welding solutions.
Additionally, technological advancements are reshaping sourcing practices. The integration of Industry 4.0 technologies, including automation and data analytics, is enabling suppliers to optimize their production processes and improve supply chain efficiencies. This trend is particularly relevant for international B2B buyers looking for suppliers who can offer not only quality but also consistency and timely delivery.
Emerging sourcing trends include a shift towards online platforms for procurement. Digital marketplaces and e-commerce solutions are becoming more popular, allowing buyers from diverse regions, such as Spain and Poland, to connect with suppliers globally. Furthermore, the focus on supplier diversity is gaining traction, encouraging businesses to explore partnerships with local suppliers in emerging markets to mitigate risks associated with geopolitical uncertainties.
How Is Sustainability and Ethical Sourcing Impacting the Welding Wire Supplier Sector?
Sustainability has become a critical consideration for B2B buyers in the welding wire sector. The environmental impact of manufacturing processes is under scrutiny, leading to a growing demand for ethically sourced materials. Buyers are increasingly prioritizing suppliers that adhere to sustainable practices, including the use of recycled materials and energy-efficient manufacturing processes.
Certifications such as ISO 14001 for environmental management and other ‘green’ certifications are becoming essential for suppliers aiming to attract international clients. These certifications not only demonstrate a commitment to sustainability but also enhance the credibility of suppliers in competitive markets.
For international buyers, understanding the sustainability practices of potential suppliers is crucial. Engaging with suppliers who have robust environmental policies can help companies mitigate their own environmental impact and align with global sustainability goals, thus enhancing their corporate social responsibility profile.
What Is the Brief Evolution of the Welding Wire Supplier Sector?
The welding wire supplier sector has evolved significantly over the last few decades. Initially dominated by local manufacturers, the industry began to globalize in the late 20th century as companies sought to expand their reach and cater to international markets. This shift was largely facilitated by advancements in transportation and communication technologies, which made it easier for suppliers to connect with buyers worldwide.
In recent years, the sector has seen increased competition due to the entry of new players from emerging markets, particularly in Asia and South America. This has led to a greater emphasis on quality, pricing, and innovation. As a result, established suppliers are investing in research and development to introduce advanced welding materials that meet the evolving demands of industries such as renewable energy and automotive manufacturing.
As the market continues to evolve, international B2B buyers must stay informed about these trends to make strategic sourcing decisions that align with their business objectives and sustainability commitments.
Frequently Asked Questions (FAQs) for B2B Buyers of welding wire supplier
-
How do I solve issues with inconsistent welding wire quality?
To address quality inconsistencies in welding wire, it’s crucial to establish clear specifications and quality standards upfront. Conduct thorough supplier vetting by requesting samples and certifications, such as ISO or AWS standards. Additionally, maintain regular communication with the supplier to discuss any quality concerns. Implement a quality assurance (QA) process that includes periodic inspections and testing of the welding wire upon receipt to ensure it meets your specifications. -
What is the best welding wire for stainless steel applications?
For stainless steel welding, the best wire is often ER308L for austenitic stainless steel. It offers excellent corrosion resistance and is suitable for a variety of welding processes. When sourcing, ensure the supplier provides detailed specifications regarding the wire composition and certifications. If your application requires specific properties, discuss customization options with your supplier to meet those needs effectively. -
What should I consider when vetting a welding wire supplier?
When vetting a welding wire supplier, consider their industry experience, certifications, and production capabilities. Request references from previous clients and assess their reputation in the market. Evaluate their compliance with international standards and their ability to meet your specific requirements regarding wire types and grades. Additionally, inspect their manufacturing facilities if possible, and inquire about their supply chain reliability and customer support. -
What are the typical minimum order quantities (MOQ) for welding wire?
Minimum order quantities (MOQ) for welding wire can vary significantly depending on the supplier and the type of wire. Generally, MOQs can range from 100 kg to several tons. When sourcing, discuss your specific needs with the supplier to negotiate favorable terms that align with your project requirements. Some suppliers may offer flexibility in MOQs for new clients or bulk orders, so it’s worthwhile to explore these options. -
What payment terms should I expect when sourcing welding wire internationally?
Payment terms for international welding wire suppliers often vary, but common practices include letters of credit, advance payments, or net 30-90 days after delivery. It’s essential to clarify payment terms upfront to avoid misunderstandings. Ensure that you also consider currency fluctuations and additional banking fees that may arise during international transactions. Establishing a good relationship with your supplier can lead to more favorable payment conditions. -
How can I ensure timely delivery of welding wire from international suppliers?
To ensure timely delivery, work closely with your supplier to establish a clear timeline and logistics plan. Use reliable shipping methods and consider working with freight forwarders who specialize in international trade. Confirm lead times during the ordering process and maintain open communication with the supplier regarding any potential delays. Additionally, track shipments regularly to anticipate any logistical challenges that may arise. -
What quality assurance measures should I implement for imported welding wire?
Implementing a robust quality assurance process is critical for imported welding wire. This should include pre-shipment inspections, testing for compliance with technical specifications, and reviewing the supplier’s quality control processes. Consider utilizing third-party inspection services to ensure that the product meets your standards before shipment. Establish a feedback loop with your supplier to address any quality issues promptly and continuously improve product quality. -
Can I customize welding wire specifications to meet my unique requirements?
Yes, many welding wire suppliers offer customization options to meet specific requirements. This could include adjustments to the chemical composition, diameter, or coating of the wire. When discussing customization, provide detailed specifications and any relevant application information to help the supplier understand your needs. Be prepared for potential minimum order requirements or longer lead times for custom products, but many suppliers are willing to accommodate unique requests.
Important Disclaimer & Terms of Use
⚠️ Important Disclaimer
The information provided in this guide, including content regarding manufacturers, technical specifications, and market analysis, is for informational and educational purposes only. It does not constitute professional procurement advice, financial advice, or legal advice.
While we have made every effort to ensure the accuracy and timeliness of the information, we are not responsible for any errors, omissions, or outdated information. Market conditions, company details, and technical standards are subject to change.
B2B buyers must conduct their own independent and thorough due diligence before making any purchasing decisions. This includes contacting suppliers directly, verifying certifications, requesting samples, and seeking professional consultation. The risk of relying on any information in this guide is borne solely by the reader.
Strategic Sourcing Conclusion and Outlook for welding wire supplier
In today’s competitive landscape, effective strategic sourcing remains paramount for international B2B buyers seeking welding wire suppliers. By leveraging comprehensive market analysis and supplier evaluations, businesses can enhance their procurement processes, ensuring access to high-quality materials at competitive prices. This not only drives operational efficiency but also contributes to long-term cost savings and improved project outcomes.
What should buyers consider for future sourcing strategies? As industries evolve, the demand for innovative welding solutions will rise. Buyers should focus on suppliers who prioritize sustainability, technological advancements, and compliance with international standards. Engaging in trade shows and industry events, such as WELDING KOREA + AUTOMATION, can facilitate valuable connections with potential suppliers and offer insights into emerging trends.
Looking ahead, the welding wire supply landscape will continue to change, influenced by global economic shifts and technological innovations. It is essential for buyers from Africa, South America, the Middle East, and Europe to remain proactive in their sourcing strategies. Embrace the opportunity to collaborate with forward-thinking suppliers who align with your business goals and values. The future of welding supply is bright for those who are willing to adapt and innovate.