The Ultimate Guide to Wheelchair Manufacturer (2025)
Introduction: Navigating the Global Market for wheelchair manufacturer
In the quest for sourcing high-quality wheelchairs that cater to diverse needs, international B2B buyers often face the challenge of navigating a fragmented global market. The complexity arises from varying standards, materials, and functionalities that differ significantly across regions, particularly in Africa, South America, the Middle East, and Europe. This guide is designed to demystify the process of selecting wheelchair manufacturers by providing a comprehensive overview of available types, their applications, and the critical factors to consider when vetting suppliers.
By exploring the nuances of wheelchair manufacturing, including adaptive designs and innovative technologies, buyers will gain insights into the most suitable options for their target markets. The guide also addresses essential considerations such as pricing structures, shipping logistics, and regulatory compliance, empowering businesses to make informed purchasing decisions.
With a focus on actionable strategies and expert recommendations, this resource aims to equip international buyers with the knowledge needed to effectively identify and partner with reputable wheelchair manufacturers. Whether you are in France seeking advanced mobility solutions or in the UAE looking to meet local demand, this guide serves as a valuable tool for ensuring that your procurement process aligns with both market expectations and consumer needs.
Understanding wheelchair manufacturer Types and Variations
Type Name | Key Distinguishing Features | Primary B2B Applications | Brief Pros & Cons for Buyers |
---|---|---|---|
Manual Wheelchairs | Lightweight, propelled by user or attendant | Hospitals, rehabilitation centers, home care | Pros: Cost-effective, easy to transport. Cons: Requires physical effort. |
Electric Wheelchairs | Powered by batteries, controlled via joystick | Long-term care facilities, personal use | Pros: Less physical effort, higher mobility. Cons: Higher initial cost, requires charging. |
Pediatric Wheelchairs | Designed for children, adjustable features | Pediatric hospitals, schools, home care | Pros: Customizable for growth, specialized support. Cons: Limited availability in some regions. |
Sports Wheelchairs | Lightweight, designed for athletic activities | Sports clubs, rehabilitation programs | Pros: Enhanced performance, specialized design. Cons: Higher price point, niche market. |
All-Terrain Wheelchairs | Durable, designed for rough outdoor conditions | Adventure tourism, outdoor rehabilitation | Pros: Versatile use, robust construction. Cons: Heavier, may be more expensive. |
What Are the Characteristics of Manual Wheelchairs?
Manual wheelchairs are characterized by their lightweight construction and the need for physical propulsion by the user or an attendant. These wheelchairs are ideal for environments where space is limited, such as hospitals and rehabilitation centers. When purchasing manual wheelchairs, B2B buyers should consider factors such as weight, foldability, and the ease of maneuverability. Additionally, the cost-effectiveness of manual options makes them a popular choice for organizations with budget constraints.
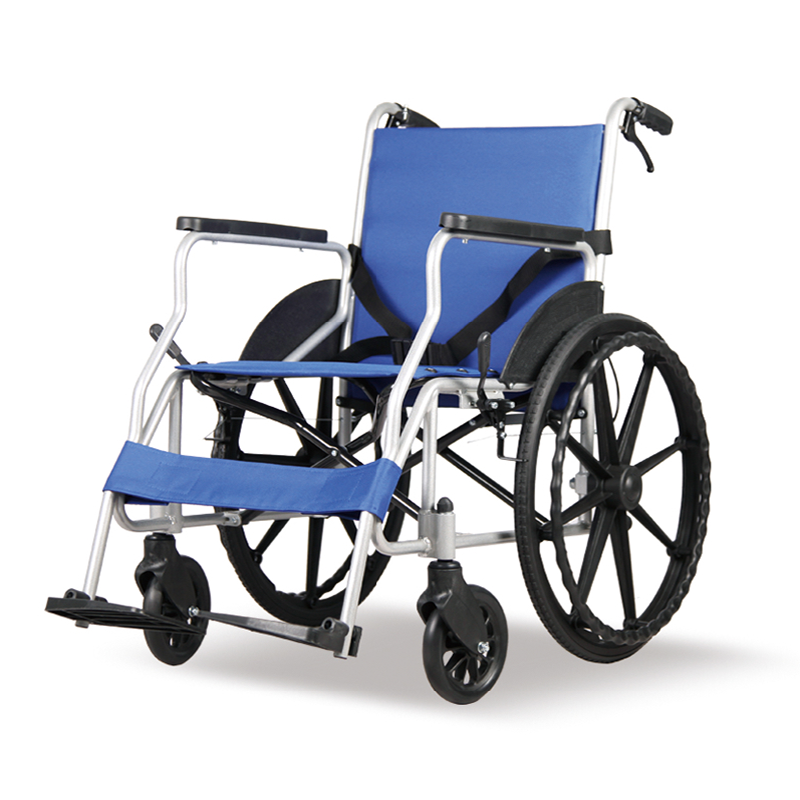
A stock image related to wheelchair manufacturer.
How Do Electric Wheelchairs Differ in Functionality?
Electric wheelchairs, also known as power chairs, are equipped with battery-powered motors and are controlled via a joystick. These wheelchairs offer greater mobility for users who may have difficulty with manual propulsion. They are commonly used in long-term care facilities and for personal use. B2B buyers should assess battery life, charging time, and the overall durability of the wheelchair when making purchasing decisions. While they tend to have a higher upfront cost, the reduced physical strain and increased independence they provide are significant advantages.
What Makes Pediatric Wheelchairs Unique?
Pediatric wheelchairs are specifically designed for children, featuring adjustable components to accommodate growth and provide specialized support. These wheelchairs are essential in pediatric hospitals and schools where tailored solutions are necessary. B2B buyers should look for options that offer customization in size and support features. While the availability of pediatric wheelchairs may be limited in certain regions, investing in them can greatly enhance the mobility and quality of life for young users.
Why Are Sports Wheelchairs Important for Athletes?
Sports wheelchairs are engineered for performance and agility, making them suitable for athletic activities. They are lightweight and designed to withstand the rigors of competitive sports, often found in sports clubs and rehabilitation programs. B2B buyers should consider the specific sports requirements, such as stability and maneuverability, when selecting these wheelchairs. Although they come at a higher price point, the benefits of enhanced performance and specialized design make them a valuable investment for organizations promoting adaptive sports.
What Are the Benefits of All-Terrain Wheelchairs?
All-terrain wheelchairs are built to handle rough outdoor conditions, featuring robust construction and durable materials. They are particularly useful for adventure tourism and outdoor rehabilitation programs. B2B buyers should evaluate the wheelchair’s weight capacity, terrain adaptability, and ease of transport when making a selection. While these wheelchairs may be heavier and more expensive, their versatility and ability to provide mobility in challenging environments can significantly enhance user experience.
Related Video: The Manual Wheelchair Comparison: Chair Accessories
Key Industrial Applications of wheelchair manufacturer
Industry/Sector | Specific Application of wheelchair manufacturer | Value/Benefit for the Business | Key Sourcing Considerations for this Application |
---|---|---|---|
Healthcare | Hospitals and Rehabilitation Centers | Enhanced patient mobility and recovery outcomes | Compliance with health regulations, durability, and comfort |
Education | Schools for Special Needs | Improved access and inclusion for disabled students | Customization options, safety features, and ease of use |
Hospitality and Tourism | Hotels and Resorts | Increased accessibility for guests with mobility issues | Design aesthetics, ease of transport, and rental agreements |
Public Transport | Buses and Trains | Compliance with accessibility standards, increased ridership | Weight capacity, maneuverability, and maintenance support |
Sports and Recreation | Adaptive Sports Programs | Promotion of inclusivity in sports and physical activities | Durability, performance specifications, and customization |
How Are Wheelchairs Used in Healthcare Settings?
In hospitals and rehabilitation centers, wheelchairs play a crucial role in enhancing patient mobility. These facilities often require wheelchairs that are not only comfortable but also durable to withstand daily use. International buyers from regions like Africa and the Middle East should consider sourcing wheelchairs that comply with local health regulations and standards. Ensuring that the wheelchairs offer features such as adjustable seating and easy maneuverability can significantly improve patient recovery outcomes.
What Are the Applications of Wheelchairs in Educational Institutions?
In schools catering to special needs students, wheelchairs are vital for ensuring accessibility and inclusion. They allow students with mobility challenges to participate fully in educational activities. Buyers in South America and Europe should prioritize sourcing customizable wheelchairs that meet specific safety requirements and are easy for staff and students to operate. Additionally, considerations for lightweight designs can facilitate easier transport within school premises.
How Do Wheelchairs Enhance Accessibility in Hospitality?
Hotels and resorts are increasingly recognizing the importance of accessibility for all guests. Wheelchairs in these settings enable individuals with mobility issues to enjoy their stay without barriers. For B2B buyers in the hospitality sector, factors such as the aesthetic appeal of wheelchairs and ease of transport are essential. It’s crucial to negotiate rental agreements that allow for flexibility in sourcing, ensuring that the needs of all guests are met.
Why Are Wheelchairs Important for Public Transport Systems?
Public transport systems, including buses and trains, must comply with accessibility standards to accommodate all passengers. Wheelchairs are integral to this effort, ensuring that individuals with mobility challenges can travel comfortably. Buyers in Europe and the Middle East should focus on sourcing wheelchairs that meet weight capacity requirements and offer high maneuverability. Additionally, ongoing maintenance support is vital to ensure these wheelchairs remain functional and safe for public use.
What Role Do Wheelchairs Play in Adaptive Sports Programs?
Adaptive sports programs utilize specialized wheelchairs to promote inclusivity in physical activities for individuals with disabilities. These wheelchairs need to be durable and high-performing to withstand rigorous use. B2B buyers looking to invest in this sector should consider sourcing wheelchairs that offer customization options tailored to specific sports. Ensuring that these products meet performance specifications is essential for enhancing participants’ experience and encouraging broader participation in sports activities.
Related Video: Sci6 Q3 – Characteristics and Uses of Simple Machines
3 Common User Pain Points for ‘wheelchair manufacturer’ & Their Solutions
Scenario 1: Inadequate Customization Options for Diverse Needs
The Problem: B2B buyers often encounter challenges when sourcing wheelchairs that cater to a wide range of user needs. Different markets—such as those in Africa, South America, the Middle East, and Europe—have varying requirements based on local demographics, health conditions, and cultural considerations. For instance, a healthcare provider in a remote region might require wheelchairs that can navigate uneven terrain, while urban facilities may prioritize lightweight and compact models for easy transport. The lack of customization options can lead to dissatisfaction, increased returns, and wasted resources.
The Solution: To address this issue, B2B buyers should prioritize wheelchair manufacturers that offer customizable solutions. Begin by conducting thorough market research to identify specific needs in your region. Engage with local healthcare professionals and end-users to gather feedback on essential features such as seat width, height adjustment, and additional accessories (e.g., footrests or armrests). Once you understand these requirements, approach manufacturers that provide modular designs or bespoke manufacturing services. Establish partnerships with suppliers who are open to co-developing products tailored to your market’s unique demands. This proactive approach not only enhances user satisfaction but also builds long-term relationships with manufacturers that can adapt to changing needs.
Scenario 2: Difficulty in Ensuring Compliance with Local Regulations
The Problem: Navigating the regulatory landscape is a significant pain point for B2B buyers in the wheelchair industry. Different regions have distinct safety and quality standards that manufacturers must meet, which can complicate sourcing decisions. For example, European buyers must comply with the EU Medical Device Regulation, while those in Africa may deal with varying national standards. Failing to ensure compliance can result in costly fines, product recalls, and damage to reputation.
The Solution: To mitigate compliance risks, B2B buyers should implement a rigorous vetting process when selecting wheelchair manufacturers. Start by familiarizing yourself with the relevant regulations in your target market. Develop a checklist of compliance requirements that manufacturers must meet, including certifications such as ISO 13485 for medical devices. Request documentation from manufacturers that demonstrates their adherence to these standards, and consider conducting factory audits or site visits to verify compliance firsthand. Additionally, establish ongoing communication with manufacturers to stay updated on any changes in regulations. By prioritizing compliance, you safeguard your business against legal issues and foster trust with clients and stakeholders.
Scenario 3: Limited After-Sales Support and Service
The Problem: After-sales support is often overlooked, yet it plays a crucial role in the overall satisfaction of B2B buyers. Buyers may find themselves stranded with wheelchairs that require maintenance or repairs but lack access to timely support from the manufacturer. This can be particularly problematic in regions with limited service networks, where quick responses are essential for ensuring user mobility and comfort.
The Solution: To overcome this pain point, B2B buyers should prioritize manufacturers that offer comprehensive after-sales service and support. Inquire about the availability of local service centers or partnerships with regional repair shops. Establish clear service level agreements (SLAs) that outline response times and support options for maintenance and repairs. Additionally, consider manufacturers that provide training for local technicians or distributors, ensuring they are equipped to handle common issues. Implement a feedback mechanism to assess the quality of after-sales service and work with manufacturers to improve their support systems. By emphasizing after-sales support in your procurement strategy, you can enhance user experience and build lasting partnerships with reliable manufacturers.
Strategic Material Selection Guide for wheelchair manufacturer
When selecting materials for wheelchair manufacturing, it is essential to consider the properties, advantages, and limitations of various materials. This decision impacts not only the performance and durability of the wheelchair but also compliance with international standards and market preferences. Below, we analyze four common materials used in wheelchair manufacturing: aluminum, steel, titanium, and composite materials.
What Are the Key Properties of Aluminum for Wheelchair Manufacturing?
Aluminum is a popular choice for wheelchair frames due to its lightweight nature and excellent corrosion resistance. It typically has a temperature rating up to 150°C and can withstand moderate pressure. The material is also known for its ability to absorb shock, which enhances user comfort.
Pros & Cons: Aluminum is durable and easy to work with, making it suitable for various designs. However, its cost can be higher than steel, and while it is strong, it may not provide the same level of rigidity, which can be a concern for heavier users.
Impact on Application: Aluminum wheelchairs are particularly well-suited for outdoor use in humid or coastal environments due to their corrosion resistance.
Considerations for International Buyers: Buyers from regions like the Middle East, where humidity levels can be high, may prefer aluminum for its longevity. Compliance with standards such as ASTM B209 for aluminum alloys is crucial for ensuring quality.
How Does Steel Compare as a Material for Wheelchair Frames?
Steel is another common material used in wheelchair manufacturing, known for its strength and durability. It can withstand high temperatures and pressures, making it a robust choice for various applications.
Pros & Cons: The primary advantage of steel is its cost-effectiveness and high strength-to-weight ratio. However, it is heavier than aluminum, which may affect the portability of the wheelchair. Additionally, steel is prone to rust if not properly treated, which can be a significant drawback in humid climates.
Impact on Application: Steel wheelchairs are often used in environments where durability is paramount, such as in rehabilitation centers or hospitals.
Considerations for International Buyers: Buyers from Europe may need to ensure compliance with EN 10025 standards for structural steel, while those from Africa might consider local availability and treatment options to prevent corrosion.
What Are the Benefits of Using Titanium in Wheelchair Manufacturing?
Titanium is renowned for its exceptional strength-to-weight ratio and corrosion resistance, making it an ideal choice for high-performance wheelchairs. It can handle extreme temperatures and pressures, providing a reliable option for various applications.
Pros & Cons: The major advantage of titanium is its lightweight nature combined with high strength, allowing for a more agile wheelchair design. However, titanium is significantly more expensive than aluminum or steel, which could deter budget-conscious buyers.
Impact on Application: Titanium is particularly beneficial for athletes or users requiring specialized wheelchairs for sports, where performance is critical.
Considerations for International Buyers: Compliance with ASTM F136 standards for titanium alloys is essential, especially for buyers in Europe and the Middle East, where quality assurance is paramount.
How Do Composite Materials Enhance Wheelchair Design?
Composite materials, such as carbon fiber, are increasingly used in wheelchair manufacturing due to their lightweight and high-strength properties. They can withstand high temperatures and pressures, making them suitable for various applications.
Pros & Cons: The primary advantage of composites is their exceptional strength-to-weight ratio, which enhances maneuverability. However, they can be more expensive and may require specialized manufacturing processes, increasing complexity.
Impact on Application: Composite wheelchairs are often preferred in competitive sports or by users seeking the highest performance.
Considerations for International Buyers: Buyers should be aware of the specific standards that apply to composite materials, such as ASTM D3039 for tensile properties, especially in regions like Europe and South America, where regulations may vary.
Summary Table of Material Selection for Wheelchair Manufacturing
Material | Typical Use Case for wheelchair manufacturer | Key Advantage | Key Disadvantage/Limitation | Relative Cost (Low/Med/High) |
---|---|---|---|---|
Aluminum | Lightweight wheelchairs for outdoor use | Excellent corrosion resistance | Higher cost than steel | Medium |
Steel | Durable wheelchairs for rehabilitation | Cost-effective and strong | Heavier and prone to rust | Low |
Titanium | High-performance sports wheelchairs | Exceptional strength-to-weight ratio | High cost | High |
Composite | Competitive sports wheelchairs | Lightweight and strong | Expensive and complex to manufacture | High |
This guide provides a comprehensive overview of material selection for wheelchair manufacturing, helping international B2B buyers make informed decisions based on their specific market needs and compliance requirements.
In-depth Look: Manufacturing Processes and Quality Assurance for wheelchair manufacturer
What Are the Main Stages of Wheelchair Manufacturing?
The manufacturing process for wheelchairs involves several critical stages, ensuring that the final product meets the required standards for safety, durability, and usability. Understanding these stages can help international B2B buyers evaluate potential suppliers effectively.
-
Material Preparation
– The first step in wheelchair manufacturing is selecting high-quality materials. Common materials include aluminum, steel, and various polymers, which are chosen for their strength, weight, and resistance to corrosion.
– Suppliers often conduct pre-production testing on raw materials to ensure they meet specified standards. Buyers should inquire about the sourcing of these materials and any certifications that validate their quality. -
Forming
– This stage involves shaping the materials into the desired components. Techniques like welding, bending, and molding are commonly employed. For instance, aluminum components are often extruded, while steel frames may be welded together for added strength.
– Advanced technologies such as CNC (Computer Numerical Control) machining are increasingly used to enhance precision and reduce waste. B2B buyers should consider suppliers that utilize these technologies to ensure high-quality production. -
Assembly
– The assembly process combines all the manufactured parts into a complete wheelchair. This typically involves attaching wheels, footrests, and other accessories.
– Quality control measures are vital at this stage, as any misalignment can affect the wheelchair’s functionality and safety. Buyers should request information on the assembly techniques used and the experience of the assembly workforce. -
Finishing
– After assembly, wheelchairs undergo finishing processes, which may include painting, powder coating, or applying protective films. These finishes not only enhance aesthetics but also improve the durability of the wheelchair.
– Buyers should evaluate the finishing techniques employed by manufacturers, as high-quality finishes can significantly affect the longevity of the product.
How Do Quality Assurance Protocols Work in Wheelchair Manufacturing?
Quality assurance (QA) is crucial in ensuring that manufactured wheelchairs meet international safety and performance standards. B2B buyers must be familiar with the relevant standards and quality control checkpoints.
-
International Standards and Certifications
– Manufacturers often adhere to ISO 9001, a global standard that outlines requirements for a quality management system. Compliance with this standard indicates a commitment to consistent quality and customer satisfaction.
– Additionally, region-specific certifications such as CE marking in Europe and API standards in the Middle East are critical. These certifications ensure that the products meet local safety and performance regulations. -
Quality Control Checkpoints
– The quality control process typically includes several checkpoints:- Incoming Quality Control (IQC): This step checks the quality of raw materials before they enter production.
- In-Process Quality Control (IPQC): Continuous monitoring during the manufacturing process ensures that any defects are identified and rectified immediately.
- Final Quality Control (FQC): After assembly, the finished products undergo comprehensive testing to ensure they meet all specifications.
- Buyers should ask for detailed reports on these checkpoints and the acceptance criteria used by the manufacturers.
-
Common Testing Methods in Wheelchair Manufacturing
– Various testing methods are employed to validate the performance and safety of wheelchairs, including:- Static and Dynamic Load Testing: To ensure the wheelchair can support the weight of users and withstand daily use.
- Durability Testing: Simulating long-term use to assess the wear and tear of components.
- Safety Testing: Evaluating features such as braking systems and stability under different conditions.
- Buyers should request documentation of these tests and the results to ensure that the manufacturer meets required standards.
How Can B2B Buyers Verify Supplier Quality Control?
Ensuring that a supplier adheres to stringent quality control measures is essential for B2B buyers. Here are several strategies to verify the quality assurance practices of wheelchair manufacturers:
-
Conducting Audits
– Regular audits of suppliers can provide insights into their quality control processes. Buyers should establish a schedule for audits and ensure they cover all aspects of manufacturing and quality assurance.
– During the audit, buyers can assess the production environment, employee training, and adherence to quality standards. A thorough audit can help build trust and ensure that the supplier meets the required quality benchmarks. -
Reviewing Quality Control Reports
– Suppliers should provide detailed quality control reports, including data from IQC, IPQC, and FQC stages. These reports can highlight the frequency of defects, corrective actions taken, and overall compliance with standards.
– B2B buyers should review these reports critically to understand the supplier’s commitment to quality and identify any potential red flags. -
Utilizing Third-Party Inspection Services
– Engaging third-party inspection services can provide an unbiased assessment of the manufacturer’s quality control processes. These services can conduct inspections at various stages of production and provide detailed reports on compliance with international standards.
– This additional layer of verification can be especially beneficial for buyers from regions with differing regulatory requirements, such as Africa and South America.
What Are the Quality Control Nuances for International B2B Buyers?
International B2B buyers must navigate various quality control nuances when sourcing wheelchairs. Here are some considerations:
-
Understanding Regional Regulations
– Different regions may have specific regulations governing wheelchair manufacturing. For example, European countries have stringent CE marking requirements, while Middle Eastern countries may have unique API standards.
– Buyers should familiarize themselves with these regulations to ensure that the products they source comply with local laws. -
Cultural Considerations
– Cultural differences can impact quality perceptions and practices. Buyers should engage in open dialogues with suppliers to understand their quality philosophies and practices.
– Building strong relationships with suppliers can facilitate better communication and adherence to quality standards. -
Logistical Challenges
– When sourcing from different continents, logistical challenges such as shipping delays and customs regulations can affect product quality. Buyers should factor in these challenges when planning their procurement strategies.
– Establishing clear communication channels with suppliers can help mitigate these risks and ensure timely delivery of high-quality products.
In conclusion, understanding the manufacturing processes and quality assurance measures for wheelchairs is vital for international B2B buyers. By focusing on material preparation, forming, assembly, and finishing, alongside rigorous quality control protocols, buyers can make informed decisions that ensure they procure reliable and compliant products.
Practical Sourcing Guide: A Step-by-Step Checklist for ‘wheelchair manufacturer’
The process of sourcing a wheelchair manufacturer involves multiple critical steps to ensure that buyers find the right partner for their needs. This guide provides a structured checklist to help international B2B buyers navigate the complexities of procurement, especially in diverse markets like Africa, South America, the Middle East, and Europe.
Step 1: Define Your Technical Specifications
Before reaching out to suppliers, it’s essential to clearly define what you need in terms of wheelchair specifications. Consider factors such as weight capacity, materials, types of wheels, and any specialized features required for your target market. This clarity will help you communicate effectively with potential manufacturers and ensure they can meet your demands.
Step 2: Conduct Market Research
Understanding the market landscape is crucial for making informed decisions. Investigate existing wheelchair manufacturers and their product offerings in the regions you are targeting. Pay attention to trends, competitive pricing, and customer reviews to identify potential suppliers who align with your requirements.
Step 3: Evaluate Potential Suppliers
Before committing, thoroughly vet suppliers to ensure they have a solid reputation. Request company profiles, case studies, and references from buyers in similar industries or regions. Look for manufacturers with proven experience in producing wheelchairs that meet international quality standards.
- Tip: Utilize platforms like Alibaba or ThomasNet to gather more information and reviews about potential suppliers.
Step 4: Verify Supplier Certifications
Quality assurance is paramount in the healthcare industry. Ensure that the manufacturers you consider hold relevant certifications, such as ISO 13485 for medical devices or CE marking for compliance in Europe. These certifications are indicative of a manufacturer’s commitment to quality and regulatory standards.
Step 5: Request Samples for Testing
Once you have narrowed down your choices, request samples of the wheelchairs you are considering. This allows you to evaluate the craftsmanship, comfort, and functionality of the products firsthand. Testing samples can help you ascertain whether the products meet the needs of your end-users.
Step 6: Discuss Pricing and Payment Terms
Engage in discussions about pricing structures and payment terms with your shortlisted suppliers. Be clear about your budget and inquire about bulk order discounts, payment schedules, and potential hidden costs. Understanding these financial aspects upfront can help prevent misunderstandings later in the procurement process.
Step 7: Assess Logistics and Shipping Capabilities
Finally, consider the logistics involved in procuring wheelchairs from your selected manufacturer. Evaluate their shipping capabilities, delivery times, and associated costs. A reliable supplier should have a clear logistics plan that ensures timely delivery while minimizing shipping risks, especially when dealing with international shipments.
By following this practical sourcing guide, B2B buyers can navigate the complexities of procuring wheelchairs effectively. Each step is designed to help you make informed decisions, ultimately leading to successful partnerships with manufacturers that meet your specifications and quality requirements.
Comprehensive Cost and Pricing Analysis for wheelchair manufacturer Sourcing
What Are the Key Cost Components in Wheelchair Manufacturing?
When sourcing wheelchairs, understanding the cost structure is crucial for B2B buyers. The primary cost components include:
-
Materials: The choice of materials significantly affects the overall cost. High-quality aluminum or carbon fiber frames, for example, tend to be more expensive than steel. Additionally, the cost of upholstery and wheels can vary based on durability and design.
-
Labor: Labor costs can fluctuate based on the region of manufacturing. Countries with lower labor costs may offer more competitive pricing, but this can also impact quality and production speed.
-
Manufacturing Overhead: This encompasses fixed costs such as utilities, rent, and equipment maintenance. Efficient manufacturing processes can help minimize these costs, which is beneficial for pricing.
-
Tooling: Custom tooling for specific designs can incur significant upfront costs. However, once established, these costs are amortized over the production run, making it essential to consider production volume.
-
Quality Control (QC): Implementing rigorous QC processes ensures product reliability but adds to costs. Certifications like ISO can also increase expenses while enhancing marketability.
-
Logistics: Shipping and handling fees vary widely depending on the distance, weight, and Incoterms chosen. Buyers must evaluate these costs as part of the total pricing.
-
Margin: Manufacturers typically add a markup to cover their operational costs and profit. This margin varies based on the manufacturer’s business model and market position.
How Do Price Influencers Impact Wheelchair Sourcing?
Several factors can significantly influence pricing in the wheelchair manufacturing sector:
-
Volume/MOQ (Minimum Order Quantity): Higher order volumes often lead to lower per-unit costs. Establishing a long-term relationship with manufacturers can lead to more favorable pricing structures.
-
Specifications and Customization: Custom designs or features increase production complexity and cost. Buyers should weigh the necessity of customization against budget constraints.
-
Material Selection: As noted earlier, material quality affects pricing. Buyers should consider the balance between cost and the expected lifespan of the wheelchair.
-
Quality and Certifications: Products that meet international standards or have specific certifications may command higher prices. However, such certifications can also enhance marketability and customer trust.
-
Supplier Factors: Reputation, reliability, and experience of the supplier can also affect pricing. Established suppliers may offer better quality assurance but at a premium.
-
Incoterms: Understanding the chosen Incoterms can clarify shipping responsibilities and costs. Different terms can significantly affect the overall landed cost of the product.
What Are Effective Buyer Tips for Negotiating Wheelchair Prices?
Navigating the complexities of pricing in wheelchair manufacturing requires strategic thinking:
-
Engage in Negotiation: Effective negotiation skills can lead to better pricing terms. Be prepared to discuss volume commitments or long-term contracts to leverage discounts.
-
Focus on Cost-Efficiency: Evaluate the Total Cost of Ownership (TCO) rather than just the purchase price. Consider factors such as maintenance, durability, and potential resale value.
-
Understand Pricing Nuances for International Buyers: Buyers from Africa, South America, the Middle East, and Europe should be aware of regional market dynamics and currency fluctuations that can affect pricing.
-
Research and Compare: Obtain quotes from multiple suppliers to gain insight into competitive pricing and product offerings. This not only aids in negotiation but also helps in understanding market standards.
-
Seek Local Expertise: Collaborating with local agents or experts can provide invaluable insights into regional pricing trends and sourcing practices, particularly in diverse markets like Europe and the Middle East.
Disclaimer on Indicative Prices
It is important to note that prices for wheelchairs can vary widely based on the aforementioned factors. The figures presented in market analyses are indicative and should not be construed as fixed pricing. Buyers are encouraged to conduct thorough research and due diligence to obtain accurate quotations tailored to their specific needs.
Alternatives Analysis: Comparing wheelchair manufacturer With Other Solutions
Understanding Alternatives to Wheelchair Manufacturers
In the realm of mobility solutions, particularly for individuals with disabilities, the choice of a wheelchair manufacturer is critical. However, various alternative solutions exist that may offer different advantages depending on specific needs, budgets, and operational contexts. This analysis presents a comparison of traditional wheelchair manufacturing against two notable alternatives: electric scooters and mobility-as-a-service (MaaS) platforms. Each option has its unique benefits and drawbacks, making it essential for B2B buyers to understand these differences in order to make informed decisions.
Comparison Aspect | Wheelchair Manufacturer | Electric Scooters | Mobility-as-a-Service (MaaS) |
---|---|---|---|
Performance | High durability, customizable for various terrains | Moderate; terrain-dependent | Varies based on provider, often reliable |
Cost | Higher initial investment, long-term value | Moderate initial cost, lower maintenance | Subscription-based, can be cost-effective over time |
Ease of Implementation | Requires manufacturing lead time and logistics | Readily available, easy to deploy | Requires integration with local transport systems |
Maintenance | Regular maintenance needed; parts availability can vary | Low maintenance, battery replacements necessary | Limited maintenance; dependent on service provider |
Best Use Case | Long-term mobility needs for individuals | Short-distance travel, urban settings | Flexible transport needs, accessible on-demand |
What Are the Advantages and Disadvantages of Electric Scooters?
Electric scooters have gained popularity in urban settings for their ease of use and relatively lower cost compared to traditional wheelchairs. They provide a moderate performance level, suitable for short distances and urban commuting. However, they may not be suitable for individuals who require a more robust solution for varied terrains or long-term mobility support. The cost can be appealing for short-term needs, but for individuals with chronic mobility issues, electric scooters may not offer the same level of support and comfort as a wheelchair.
How Does Mobility-as-a-Service (MaaS) Compare to Traditional Wheelchair Manufacturing?
Mobility-as-a-Service (MaaS) platforms provide a flexible transport solution that integrates various modes of transportation into a single accessible service. This can be particularly beneficial for urban areas where public transport is readily available. The cost structure is often subscription-based, allowing users to pay only for the services they utilize. However, MaaS can lack the personalized experience that comes with a wheelchair tailored to an individual’s specific needs. Furthermore, the reliability of service can vary based on the provider and local infrastructure, making it less predictable than owning a wheelchair.
Conclusion: How Should B2B Buyers Choose the Right Mobility Solution?
When selecting the most suitable mobility solution, B2B buyers must carefully evaluate their unique requirements, including the demographic they serve, the terrain, and the frequency of use. Wheelchair manufacturers provide durable and customizable options for long-term needs, while electric scooters offer flexibility for short-distance travel. Meanwhile, MaaS platforms can be an excellent choice for organizations looking to provide on-demand transport solutions. Ultimately, the decision should align with the operational goals, budget constraints, and specific mobility needs of the end-users to ensure the chosen solution maximizes efficiency and satisfaction.
Essential Technical Properties and Trade Terminology for wheelchair manufacturer
What Are the Key Technical Properties for Wheelchair Manufacturing?
When sourcing wheelchairs, understanding the technical properties is crucial for making informed purchasing decisions. Here are some essential specifications:
1. Material Grade
The material used in wheelchair construction significantly impacts durability, weight, and cost. Common materials include aluminum, steel, and titanium. Aluminum is lightweight and corrosion-resistant, making it ideal for portable models, while steel offers strength and stability, suitable for more robust designs. Understanding the material grade helps buyers assess the product’s longevity and performance in various environments.
2. Weight Capacity
This specification indicates the maximum weight the wheelchair can safely accommodate. It’s crucial for ensuring user safety and comfort. Most manufacturers provide weight capacities ranging from 100 kg to over 250 kg. B2B buyers must evaluate their target market’s needs, particularly in regions where body weight distributions may differ.
3. Seat Width and Depth
These dimensions are vital for user comfort and accessibility. A proper fit can prevent pressure sores and enhance mobility. Buyers should consider adjustable options or customizable dimensions to cater to diverse user needs, especially in regions with varying physical statures.
4. Tolerance Levels
Tolerance refers to the allowable deviations in manufacturing dimensions. High tolerance levels ensure that components fit together correctly, enhancing the wheelchair’s overall functionality and safety. Buyers should seek manufacturers who adhere to stringent tolerance specifications to minimize issues during assembly and use.
5. Wheel Size and Type
The size and type of wheels affect the wheelchair’s maneuverability and performance across different terrains. Larger wheels typically provide better shock absorption and are suitable for outdoor use, while smaller wheels may enhance indoor navigation. Buyers must assess the intended usage environment to choose the appropriate wheel configuration.
What Are the Common Trade Terms Used in Wheelchair Manufacturing?
Familiarizing yourself with industry terminology can streamline communication and negotiation processes in B2B transactions. Here are key terms to know:
1. OEM (Original Equipment Manufacturer)
OEM refers to companies that produce products that are marketed by another company under its brand name. In the wheelchair industry, partnering with an OEM can facilitate access to innovative designs and technology without the need for extensive in-house development. This is particularly advantageous for buyers looking to expand their product offerings.
2. MOQ (Minimum Order Quantity)
MOQ indicates the minimum number of units a supplier is willing to sell. Understanding MOQ is essential for budget management and inventory planning. Buyers should negotiate MOQs that align with their market demand to avoid overstocking or stockouts, which can be particularly challenging in regions with fluctuating demand.
3. RFQ (Request for Quotation)
An RFQ is a document sent to suppliers requesting detailed pricing and terms for specific products. Crafting a well-structured RFQ can lead to more accurate quotes and foster competitive pricing. Buyers should include clear specifications and quantities in their RFQs to receive the most relevant responses.
4. Incoterms (International Commercial Terms)
Incoterms are standardized trade terms that define the responsibilities of buyers and sellers regarding shipping and delivery. Familiarity with Incoterms like FOB (Free On Board) and CIF (Cost, Insurance, and Freight) can help buyers navigate logistics more effectively, especially in international transactions, reducing risks related to shipping costs and responsibilities.
5. Lead Time
Lead time refers to the time taken from placing an order to delivery. Understanding lead times is vital for effective inventory management and ensuring timely product availability. Buyers should factor lead times into their supply chain planning, especially in regions where logistics can be unpredictable.
By grasping these technical properties and trade terms, international B2B buyers can make more informed decisions, optimize procurement strategies, and foster stronger partnerships with wheelchair manufacturers.
Navigating Market Dynamics and Sourcing Trends in the wheelchair manufacturer Sector
What Are the Current Market Dynamics and Key Trends in the Wheelchair Manufacturing Sector?
The wheelchair manufacturing sector is witnessing a transformative phase driven by globalization, technological advancements, and evolving consumer preferences. Key market drivers include an aging population, increased awareness of disability rights, and the integration of smart technology into mobility devices. For international B2B buyers, particularly from Africa, South America, the Middle East, and Europe, understanding these dynamics is crucial for strategic sourcing decisions.
Emerging technologies such as IoT-enabled wheelchairs and enhanced materials like lightweight alloys and carbon fiber are reshaping product offerings. These innovations not only improve the performance and comfort of wheelchairs but also present new sourcing opportunities. B2B buyers should focus on manufacturers that invest in R&D to stay ahead of these trends. Additionally, the demand for customization is growing, prompting suppliers to offer more tailored solutions that cater to specific market needs.
In terms of market dynamics, regional disparities are notable. For instance, while Europe is focusing on advanced features and sustainability, regions like Africa and South America may prioritize affordability and accessibility. Understanding these regional nuances can provide valuable insights for sourcing strategies, allowing buyers to align their procurement with local market demands.
How Is Sustainability Shaping Sourcing Trends in Wheelchair Manufacturing?
Sustainability is becoming a pivotal factor in sourcing decisions for wheelchair manufacturers. The environmental impact of production processes and materials used in manufacturing is under scrutiny, pushing companies towards greener practices. Buyers are increasingly seeking suppliers who prioritize ethical sourcing and sustainable materials, as these practices not only enhance brand reputation but also meet regulatory requirements in various regions.
The importance of ethical supply chains cannot be overstated. Manufacturers that ensure fair labor practices and environmentally friendly production methods are gaining a competitive edge. Certifications such as ISO 14001 (Environmental Management) and Fair Trade can serve as indicators of a manufacturer’s commitment to sustainability. B2B buyers should prioritize partnerships with companies that hold such certifications, as they reflect a commitment to ethical practices.
Furthermore, the use of recycled materials and biodegradable components is on the rise. Buyers should inquire about the sourcing of materials and the lifecycle impacts of the products they are considering. This focus on sustainability not only aligns with global trends but also resonates with increasingly eco-conscious consumers.
How Has the Wheelchair Manufacturing Sector Evolved Over Time?
The evolution of the wheelchair manufacturing sector has been marked by significant technological advancements and changing societal attitudes towards disability. Initially, wheelchairs were primarily utilitarian, focusing solely on mobility. However, as awareness of the rights of individuals with disabilities grew, manufacturers began to prioritize comfort, design, and functionality.
The introduction of powered wheelchairs in the 20th century represented a major leap forward, enhancing independence for users. Today, the focus has shifted towards smart technology integration, offering features such as app connectivity and advanced mobility options. This evolution underscores the importance for B2B buyers to stay informed about historical trends, as they can influence current market offerings and sourcing decisions.
Understanding these historical shifts can provide valuable context for international buyers, helping them make informed choices that align with both current market demands and future innovations in the wheelchair manufacturing sector.
Frequently Asked Questions (FAQs) for B2B Buyers of wheelchair manufacturer
-
How do I ensure quality when sourcing wheelchairs from manufacturers?
To ensure quality when sourcing wheelchairs, consider implementing a multi-step vetting process. Start by researching potential manufacturers’ certifications, such as ISO and CE markings, which indicate adherence to international quality standards. Request product samples to evaluate craftsmanship, materials, and functionality. Additionally, consider visiting manufacturing facilities or using third-party inspection services to verify quality before placing large orders. Establishing clear quality assurance protocols in your purchase agreements can further safeguard against subpar products. -
What are the key factors to consider when selecting a wheelchair manufacturer?
When selecting a wheelchair manufacturer, evaluate their experience and specialization in producing the specific type of wheelchairs you require. Assess their production capacity to ensure they can meet your demands. Look for manufacturers that offer customization options, as this can be crucial for meeting the unique needs of your market. Additionally, consider their geographic location, as proximity can impact shipping costs and lead times. Lastly, check their reputation by reading reviews and requesting references from other B2B buyers. -
What are common payment terms when purchasing wheelchairs internationally?
Payment terms can vary by manufacturer and region, but common practices include a 30% deposit upfront with the remaining balance due upon shipment or delivery. Some manufacturers may offer net terms, allowing payment within 30 to 90 days after receipt of goods. Ensure you clarify payment methods accepted, such as bank transfers or letters of credit, to avoid complications. It’s also wise to discuss potential currency fluctuations and how they might affect your total costs, particularly for transactions involving multiple currencies. -
What are the minimum order quantities (MOQ) for wheelchair manufacturers?
Minimum order quantities can differ significantly among wheelchair manufacturers, often ranging from 50 to 500 units depending on the product type and customization level. Smaller manufacturers may be more flexible with MOQs, while larger companies may have stricter policies due to economies of scale. When negotiating, consider your market demands and discuss the possibility of lower MOQs for initial orders. Some manufacturers may also offer pilot programs to test products before committing to larger orders. -
How can I customize wheelchairs to meet specific market needs?
Customizing wheelchairs involves collaborating closely with manufacturers to define your specifications, such as size, weight capacity, and material preferences. Discuss design features that cater to the local market, such as color options or additional accessories. Many manufacturers are open to producing tailored solutions, but it’s essential to communicate your requirements clearly from the outset. Be mindful that customization may affect lead times and costs, so factor these into your planning and budgeting. -
What logistics considerations should I keep in mind when importing wheelchairs?
When importing wheelchairs, consider logistics factors such as shipping methods, costs, and lead times. Choose between air freight for speed or sea freight for cost-effectiveness, depending on your urgency and budget. Familiarize yourself with customs regulations in your target market to ensure compliance and avoid delays. Work with experienced freight forwarders who can assist with documentation and logistics management. Additionally, factor in warehousing solutions if you plan to store inventory before distribution.
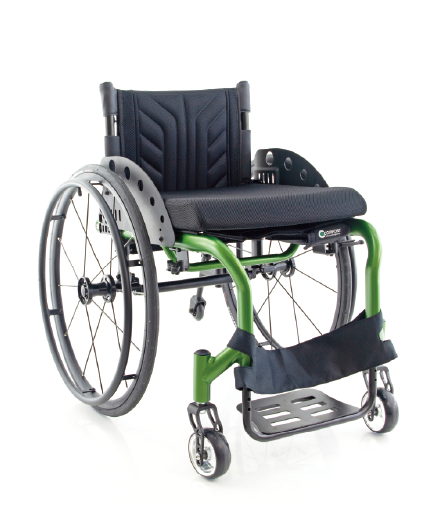
A stock image related to wheelchair manufacturer.
-
How do I assess the reliability of a wheelchair supplier?
To assess a wheelchair supplier’s reliability, begin by evaluating their track record, including years in business and customer testimonials. Request references from other B2B clients who have worked with them. Additionally, consider conducting background checks to verify their financial stability and production capabilities. Regular communication during the sourcing process can also provide insight into their responsiveness and professionalism. If possible, initiate a small order to test their reliability before committing to larger purchases. -
What are the common challenges in international sourcing of wheelchairs?
International sourcing of wheelchairs can present challenges such as language barriers, differing regulatory standards, and cultural differences in business practices. Logistics issues, including shipping delays and customs clearance, can also complicate the process. To mitigate these challenges, invest time in understanding the local market dynamics and regulatory environment of your supplier’s country. Establish strong communication channels and consider hiring local intermediaries to facilitate smoother transactions and navigate potential hurdles.
Important Disclaimer & Terms of Use
⚠️ Important Disclaimer
The information provided in this guide, including content regarding manufacturers, technical specifications, and market analysis, is for informational and educational purposes only. It does not constitute professional procurement advice, financial advice, or legal advice.
While we have made every effort to ensure the accuracy and timeliness of the information, we are not responsible for any errors, omissions, or outdated information. Market conditions, company details, and technical standards are subject to change.
B2B buyers must conduct their own independent and thorough due diligence before making any purchasing decisions. This includes contacting suppliers directly, verifying certifications, requesting samples, and seeking professional consultation. The risk of relying on any information in this guide is borne solely by the reader.
Strategic Sourcing Conclusion and Outlook for wheelchair manufacturer
As international B2B buyers navigate the complexities of sourcing wheelchairs, understanding the strategic sourcing landscape is paramount. By prioritizing partnerships with manufacturers that demonstrate reliability, innovation, and compliance with international standards, buyers can secure a competitive advantage. The emphasis on quality assurance, sustainability, and cost-effectiveness will not only enhance supply chain resilience but also contribute positively to brand reputation.
How Can Strategic Sourcing Enhance Your Competitive Edge in the Wheelchair Market?
Strategic sourcing is not merely a procurement function; it is a vital strategy that enables organizations to align their operational needs with market dynamics. For buyers in Africa, South America, the Middle East, and Europe, leveraging local suppliers can foster community engagement and reduce lead times. Additionally, investing in technology-driven solutions can streamline the procurement process, allowing for more informed decision-making.
What Should B2B Buyers Consider for Future Sourcing Success?
Looking ahead, B2B buyers should remain proactive in exploring emerging markets and innovative manufacturing practices. By keeping abreast of global trends and engaging in continuous supplier evaluation, businesses can ensure they are well-positioned to meet evolving customer demands.
In conclusion, the future of wheelchair manufacturing and sourcing is bright for those willing to embrace strategic partnerships and innovative solutions. Now is the time to act—evaluate your sourcing strategies, connect with reliable manufacturers, and position your business for sustainable growth in the global marketplace.