The Ultimate Guide to Woodworking Machinery Supplier (2025)
Introduction: Navigating the Global Market for woodworking machinery supplier
In an increasingly interconnected world, sourcing the right woodworking machinery supplier can be a daunting challenge for international B2B buyers. Whether you are in Africa, South America, the Middle East, or Europe, navigating the complexities of global supply chains requires a strategic approach. This guide aims to demystify the process, providing essential insights into the types of woodworking machinery available, their various applications, and how to effectively vet potential suppliers.
Buyers often grapple with concerns about quality, cost, and reliability when selecting machinery for their operations. This comprehensive resource empowers you to make informed purchasing decisions by outlining key factors such as market trends, supplier credentials, and pricing strategies. By understanding these elements, businesses can mitigate risks and enhance their operational efficiency.
Furthermore, the guide addresses the unique challenges faced by buyers in specific regions, including logistical considerations and compliance with local regulations. By tapping into this knowledge, you can streamline your procurement process, ensuring that your woodworking machinery meets both your operational needs and budget constraints.
Ultimately, this guide serves as a valuable tool for B2B buyers looking to establish long-term partnerships with trustworthy suppliers, paving the way for sustainable growth and innovation in the woodworking industry.
Understanding woodworking machinery supplier Types and Variations
Type Name | Key Distinguishing Features | Primary B2B Applications | Brief Pros & Cons for Buyers |
---|---|---|---|
Original Equipment Manufacturers (OEMs) | Produce machinery to specification, often branded | Large-scale production, custom solutions | Pros: High quality, tailored features. Cons: Higher costs, longer lead times. |
Distributors and Resellers | Carry multiple brands, offer a variety of machinery | Small to medium enterprises, local markets | Pros: Wide selection, competitive pricing. Cons: Limited technical support, may lack exclusivity. |
Specialized Machinery Suppliers | Focus on niche markets, specific types of machinery | Custom woodworking, artisan shops | Pros: Expertise in niche areas, tailored solutions. Cons: Limited product range, potentially higher costs. |
Used Machinery Dealers | Offer pre-owned equipment, often at lower prices | Startups, budget-conscious companies | Pros: Cost savings, immediate availability. Cons: Potential hidden defects, limited warranties. |
Online Marketplaces | Platforms for buying and selling new and used machinery | Global reach, diverse options | Pros: Convenience, extensive listings. Cons: Variable seller reliability, lack of hands-on inspection. |
What are Original Equipment Manufacturers (OEMs) in Woodworking Machinery?
OEMs in woodworking machinery provide high-quality machinery that is often customized to meet specific production needs. These suppliers typically work directly with larger companies, ensuring that machinery is built to exact specifications. B2B buyers should consider OEMs if they require specialized equipment that can increase efficiency and production quality. However, the trade-off may be higher costs and longer lead times, which could impact cash flow and project timelines.
How do Distributors and Resellers Operate in the Woodworking Machinery Market?
Distributors and resellers play a crucial role in the woodworking machinery supply chain by offering a variety of brands and models. They cater primarily to small and medium enterprises (SMEs) looking for flexibility in their purchases. Buyers benefit from competitive pricing and a broad selection but may encounter limitations in technical support and the depth of product knowledge. When selecting a distributor, it’s essential to assess their reputation and the range of brands they carry to ensure alignment with your business needs.
Why Choose Specialized Machinery Suppliers for Unique Woodworking Needs?
Specialized machinery suppliers focus on specific niches within the woodworking industry, such as custom woodworking and artisan crafts. These suppliers often possess deep expertise in their product areas, allowing them to offer tailored solutions that meet unique operational requirements. While they provide valuable insights and specialized machinery, B2B buyers should be aware of the potentially higher costs and narrower product range. It’s crucial to evaluate whether the specialized capabilities align with your production goals.
What Should You Know About Used Machinery Dealers?
Used machinery dealers present an attractive option for startups and budget-conscious companies looking to minimize upfront costs. These dealers offer pre-owned equipment, which can be a cost-effective way to acquire necessary machinery quickly. However, buyers must be diligent in inspecting equipment for hidden defects and understanding warranty limitations. Conducting thorough due diligence can help mitigate risks associated with purchasing used machinery.
How Do Online Marketplaces Facilitate Woodworking Machinery Transactions?
Online marketplaces have transformed the woodworking machinery buying process by providing a platform for both new and used equipment. They allow buyers to access a global network of suppliers, offering a diverse range of options. While these platforms provide convenience and extensive listings, buyers should remain cautious about seller reliability and the inability to physically inspect machinery before purchase. Establishing clear communication with sellers and seeking reviews can enhance the buying experience in this digital landscape.
Related Video: SCM Startech 27 Drilling Machine | Scott+Sargeant Woodworking Machinery\n| scosarg.com
Key Industrial Applications of woodworking machinery supplier
Industry/Sector | Specific Application of woodworking machinery supplier | Value/Benefit for the Business | Key Sourcing Considerations for this Application |
---|---|---|---|
Furniture Manufacturing | CNC Routing and Milling Machines | Enhanced precision and efficiency in production | Consider machine specifications, support, and training. |
Construction and Carpentry | Portable Sawmills | Cost-effective lumber production on-site | Evaluate mobility, power source, and maintenance needs. |
Wood Packaging and Pallet Production | Automated Pallet Nailing Machines | Increased throughput and reduced labor costs | Assess machine compatibility with local wood types. |
Musical Instrument Manufacturing | Wood Thickness Planers | Consistent quality and finish for sound quality | Focus on tolerance levels and material types. |
DIY and Hobbyist Markets | Hobbyist Woodworking Tools | Accessibility for small-scale projects | Look for user-friendly features and local availability. |
How is CNC Routing and Milling Machines Used in Furniture Manufacturing?
CNC routing and milling machines are pivotal in the furniture manufacturing sector. They allow for precise cuts and intricate designs, enabling manufacturers to produce high-quality furniture at scale. This technology addresses common issues such as material waste and inconsistencies in production. For international buyers, particularly in regions like Europe and South America, sourcing machinery that can handle local wood varieties and comply with regional regulations is crucial. Additionally, ensuring that suppliers offer adequate training and after-sales support can significantly enhance operational efficiency.
What Role Do Portable Sawmills Play in Construction and Carpentry?
Portable sawmills are increasingly utilized in construction and carpentry, providing a flexible solution for on-site lumber production. This application is especially beneficial in remote areas of Africa and South America, where access to quality lumber can be challenging. By allowing builders to convert raw logs into usable timber, these machines reduce transportation costs and enhance project timelines. Buyers should consider the portability, power source, and ease of operation when sourcing these machines, as well as the availability of spare parts in their regions.
How Do Automated Pallet Nailing Machines Benefit Wood Packaging and Pallet Production?
Automated pallet nailing machines streamline the production of wooden pallets, significantly increasing throughput while reducing labor costs. This application is vital for businesses in the wood packaging sector, particularly in the Middle East and Europe, where demand for pallets is high. These machines can solve issues related to manual nailing inefficiencies and labor shortages. Buyers should focus on sourcing machines that are compatible with local wood types and can be easily integrated into existing production lines to maximize efficiency.
Why Are Wood Thickness Planers Important in Musical Instrument Manufacturing?
In the musical instrument manufacturing industry, wood thickness planers play a critical role in ensuring the quality of sound. These machines provide consistent thickness, which is essential for achieving the desired acoustic properties. For international buyers, particularly in Europe where craftsmanship is highly valued, sourcing planers that can handle a variety of wood types and thicknesses is essential. Understanding the tolerance levels and the specific requirements for different instruments can help buyers make informed purchasing decisions.
How Do Hobbyist Woodworking Tools Cater to DIY and Hobbyist Markets?
Hobbyist woodworking tools are designed to make woodworking accessible to DIY enthusiasts and small-scale producers. These tools enable users to undertake various projects, from furniture building to decorative items. For buyers in regions like Brazil and Mexico, selecting user-friendly and versatile tools is key to attracting this market segment. Availability of local support and training resources can also enhance the purchasing experience, ensuring that hobbyists can maximize their use of the machinery.
3 Common User Pain Points for ‘woodworking machinery supplier’ & Their Solutions
Scenario 1: Inconsistent Quality of Machinery Deliveries
The Problem: B2B buyers often face the challenge of receiving woodworking machinery that does not meet their quality expectations. This can arise from inadequate supplier vetting, where the machinery might be subpar or not compliant with international standards. Buyers in regions such as Africa and South America may find that local suppliers have limited capabilities to deliver high-quality machinery consistently, leading to production delays, increased costs, and potential reputational damage.
The Solution: To mitigate this issue, buyers should establish a rigorous supplier evaluation process. This includes requesting samples or demonstration units before committing to a full order. Additionally, conducting factory audits can provide insights into the production processes and quality control measures employed by the supplier. Buyers should also prioritize suppliers with internationally recognized certifications, such as ISO 9001, which indicates a commitment to quality management practices. Engaging with industry peers or networks can provide valuable recommendations and insights into reputable suppliers.
Scenario 2: High Operational Costs Due to Inefficient Machinery
The Problem: Another common pain point is the high operational costs associated with inefficient woodworking machinery. This is particularly significant for buyers in the Middle East and Europe, where energy costs can be substantial. Machinery that consumes excessive power or requires frequent maintenance can severely impact a company’s bottom line, reducing profitability and competitiveness in the market.
The Solution: To address this, B2B buyers should focus on sourcing energy-efficient machines that are designed to minimize operational costs. When evaluating suppliers, inquire about the energy consumption ratings of their machinery and request performance data that demonstrates cost savings over time. Additionally, consider investing in advanced machinery that incorporates automation and smart technology, which can optimize production processes and reduce waste. Buyers can also negotiate service agreements that include regular maintenance, ensuring that the machinery operates efficiently over its lifespan.
Scenario 3: Difficulty in Accessing Spare Parts and Technical Support
The Problem: Many B2B buyers encounter issues related to the availability of spare parts and technical support for their woodworking machinery. This challenge is particularly pronounced in regions like Africa and South America, where logistics can be complex and suppliers may not offer reliable after-sales support. The inability to quickly obtain spare parts can lead to extended downtime, disrupting production schedules and increasing operational costs.
The Solution: To overcome this hurdle, buyers should select suppliers who provide comprehensive after-sales support, including a clear commitment to spare parts availability. Before finalizing a purchase, inquire about the lead times for spare parts and whether the supplier has a local presence or reliable logistics partnerships that can facilitate faster deliveries. Additionally, establishing a relationship with a local distributor or service provider can enhance support capabilities. Consider negotiating long-term service contracts that include provisions for spare parts supply and technical assistance, ensuring that your operations remain uninterrupted in case of machinery breakdowns.
Strategic Material Selection Guide for woodworking machinery supplier
What are the Key Properties of Steel in Woodworking Machinery?
Steel is one of the most commonly used materials in woodworking machinery due to its excellent strength and durability. Key properties include high tensile strength, which allows it to withstand significant stress and pressure during operation. Additionally, steel has good temperature resistance, making it suitable for applications involving heat generation, such as cutting and milling. However, steel is prone to corrosion, especially in humid environments, which can be a concern for buyers in regions like Africa and the Middle East.
Pros and Cons of Using Steel
The primary advantage of steel is its durability, which translates to a longer lifespan for machinery components. It is also relatively cost-effective compared to other materials, making it a popular choice among manufacturers. However, the manufacturing complexity can be higher due to the need for specialized equipment for cutting and shaping steel. Furthermore, its weight can be a limitation in mobile woodworking applications.
Impact on Application
Steel is compatible with a wide range of woodworking operations, including cutting, shaping, and assembling wood products. Buyers should consider the specific media compatibility, such as adhesives and finishes, which may react with steel and affect performance.
How Does Aluminum Compare as a Material for Woodworking Machinery?
Aluminum is increasingly popular in woodworking machinery due to its lightweight nature and corrosion resistance. It has a lower density than steel, which makes it easier to handle and transport. Aluminum also offers good thermal conductivity, which can be beneficial in applications that generate heat.
Pros and Cons of Using Aluminum
The key advantage of aluminum is its resistance to corrosion, making it ideal for humid environments or regions with high moisture levels, such as parts of South America. However, aluminum is generally less durable than steel, which may lead to a shorter lifespan for certain components. Additionally, the cost of aluminum can be higher than that of steel, impacting overall project budgets.
Impact on Application
Aluminum is suitable for applications requiring lightweight components, such as portable woodworking machines. However, buyers should be aware of the specific standards for aluminum alloys, such as ASTM and DIN, to ensure compliance with international quality standards.
What are the Benefits of Using Composite Materials in Woodworking Machinery?
Composite materials, often made from a combination of wood fibers and resins, are gaining traction in the woodworking machinery sector. These materials are designed to offer enhanced performance characteristics, such as improved strength-to-weight ratios and reduced susceptibility to warping.
Pros and Cons of Using Composites
A significant advantage of composite materials is their versatility; they can be engineered to meet specific performance requirements. They are also resistant to moisture and do not corrode, making them suitable for various environmental conditions. However, composites can be more expensive to manufacture and may require specialized processing techniques, which could complicate production.
Impact on Application
Composites are particularly effective in applications where weight reduction is critical, such as in portable machinery. Buyers should also consider the environmental impact and recycling options for composite materials, especially in regions with strict sustainability regulations.
What Role Does Cast Iron Play in Woodworking Machinery Manufacturing?
Cast iron is another traditional material used in woodworking machinery, known for its excellent vibration dampening properties and stability. It can withstand high pressures and temperatures, making it suitable for heavy-duty applications.
Pros and Cons of Using Cast Iron
The primary advantage of cast iron is its durability and stability, which can enhance the performance of machinery. However, it is relatively heavy, which can limit its use in portable applications. Additionally, cast iron can be more expensive to produce and transport due to its weight.
Impact on Application
Cast iron is ideal for stationary woodworking machinery where stability is crucial. Buyers should consider the potential for rust and corrosion in humid environments, which may necessitate additional protective coatings.
Summary Table of Material Selection for Woodworking Machinery
Material | Typical Use Case for woodworking machinery supplier | Key Advantage | Key Disadvantage/Limitation | Relative Cost (Low/Med/High) |
---|---|---|---|---|
Steel | Structural components in stationary machinery | High durability and strength | Prone to corrosion | Medium |
Aluminum | Portable woodworking machines | Lightweight and corrosion-resistant | Less durable than steel | High |
Composite | Lightweight, portable machinery components | Versatile and moisture-resistant | Higher manufacturing complexity | High |
Cast Iron | Heavy-duty stationary machinery | Excellent stability and vibration dampening | Heavy and less portable | Medium |
In-depth Look: Manufacturing Processes and Quality Assurance for woodworking machinery supplier
What Are the Key Stages in Manufacturing Woodworking Machinery?
The manufacturing process of woodworking machinery involves several critical stages that ensure the production of high-quality and durable machines. Understanding these stages can help international B2B buyers make informed decisions when sourcing suppliers.
1. Material Preparation
Material preparation is the foundational step in the manufacturing process. It involves selecting high-quality raw materials, such as steel, aluminum, and various composites, which will be used in the machinery. Suppliers often perform thorough inspections of incoming materials to ensure they meet specified standards. For buyers, it is essential to verify that suppliers source materials from reputable vendors and maintain traceability of their materials to guarantee quality.
2. Forming
Once the materials are prepared, they undergo various forming processes, such as cutting, bending, and machining. Advanced techniques like CNC (Computer Numerical Control) machining are commonly employed to achieve precise dimensions and intricate designs. Buyers should inquire about the technology used in the forming stage to assess whether the supplier can meet specific customization requirements.
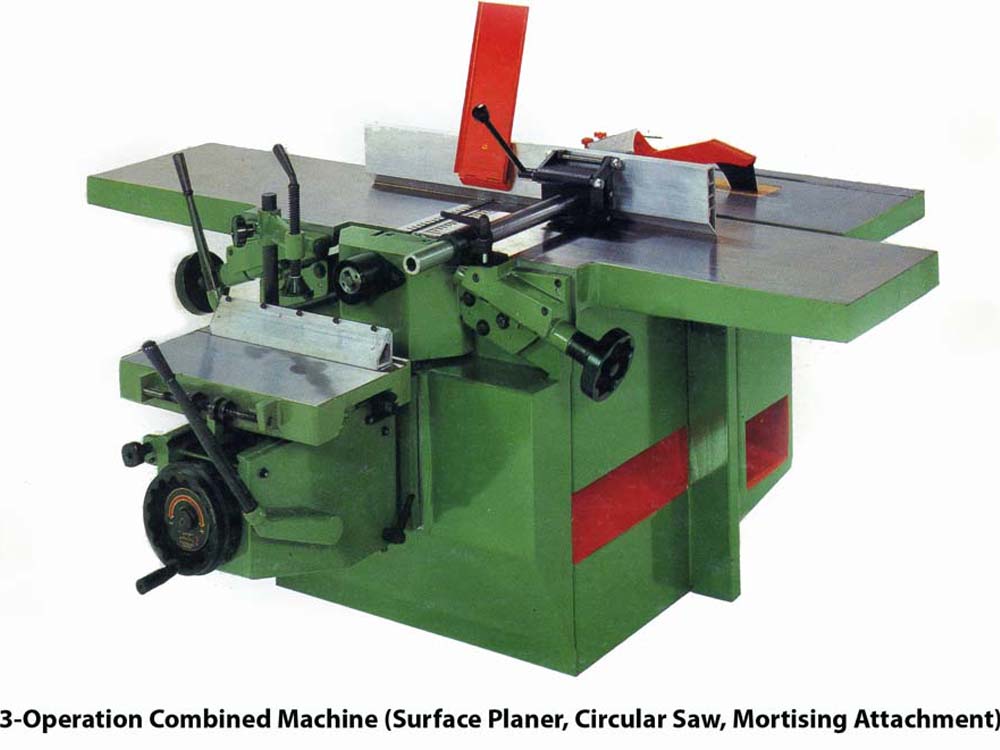
A stock image related to woodworking machinery supplier.
3. Assembly
The assembly stage involves bringing together all the components to form the complete machinery. This process can be complex, requiring skilled labor and precise coordination. Suppliers may utilize assembly lines or modular systems, depending on the scale of production. Buyers should ask about the assembly process and the qualifications of the workforce to ensure that the final product meets their expectations.
4. Finishing
Finishing processes, such as painting, coating, and surface treatment, enhance the machine’s durability and aesthetic appeal. This stage is crucial for preventing corrosion and wear over time. B2B buyers should verify the finishing techniques used by suppliers, as these can significantly impact the longevity and performance of the machinery.
How Is Quality Assurance Integrated into the Manufacturing of Woodworking Machinery?
Quality assurance (QA) is a vital aspect of the manufacturing process that ensures each piece of machinery meets both international and industry-specific standards. This focus on quality helps build trust between suppliers and buyers.
1. What Are the Relevant International Standards for Woodworking Machinery?
International standards like ISO 9001 are essential for manufacturers aiming to demonstrate their commitment to quality management systems. Compliance with ISO 9001 ensures that the supplier consistently provides products that meet customer and regulatory requirements. Additionally, industry-specific certifications, such as CE marking in Europe or API standards in certain applications, can further validate a supplier’s commitment to quality.
2. What Quality Control Checkpoints Should Buyers Be Aware Of?
Quality control (QC) checkpoints are crucial for identifying and addressing defects at various stages of the manufacturing process. Common checkpoints include:
-
Incoming Quality Control (IQC): This involves inspecting raw materials before they enter the production line. Buyers should ensure that suppliers have robust IQC processes to catch issues early.
-
In-Process Quality Control (IPQC): During manufacturing, IPQC monitors critical processes to prevent defects. Buyers can request documentation on IPQC procedures to understand how suppliers manage quality throughout production.
-
Final Quality Control (FQC): This step involves a thorough inspection of the finished product before it is shipped. Buyers should inquire about FQC practices, including the types of tests performed and acceptance criteria.
What Common Testing Methods Are Employed in Woodworking Machinery Manufacturing?
Testing methods play a crucial role in quality assurance. Suppliers typically employ various testing techniques, including:
-
Functional Testing: This assesses the machine’s operational performance and ensures it meets specified requirements.
-
Durability Testing: Machines are subjected to rigorous conditions to evaluate their longevity and reliability under normal operating conditions.
-
Safety Testing: Compliance with safety standards is paramount. Suppliers should conduct tests to ensure that machines are safe for operators and meet relevant safety regulations.
How Can B2B Buyers Verify Supplier Quality Control Processes?
For international B2B buyers, verifying a supplier’s quality control processes is essential to ensure that they are making a sound investment. Here are some actionable steps:
1. Conduct Supplier Audits
Regular audits can provide insights into a supplier’s manufacturing processes and quality assurance practices. Buyers should develop an audit checklist that includes inquiries about certifications, quality control checkpoints, and testing methods.
2. Request Quality Assurance Reports
Suppliers should be able to provide detailed QA reports that outline their quality control procedures, results from recent inspections, and compliance with international standards. These documents can serve as a valuable tool for buyers in assessing supplier reliability.
3. Engage Third-Party Inspectors
Hiring third-party inspection services can add an extra layer of assurance. These independent entities can evaluate the supplier’s processes and products, providing an unbiased assessment of quality.
What Nuances Should International Buyers Consider Regarding Quality Control?
When sourcing woodworking machinery suppliers from diverse regions such as Africa, South America, the Middle East, and Europe, buyers should be aware of certain nuances:
-
Cultural Differences: Variations in manufacturing practices and quality standards can exist across different regions. Buyers should take time to understand local practices and compliance requirements.
-
Regulatory Compliance: Each region may have unique regulations governing machinery safety and quality. Buyers should ensure that suppliers are compliant with local laws and international standards to avoid potential legal issues.
-
Language Barriers: Communication is key in establishing trust and understanding quality control processes. Buyers may need to engage translators or local intermediaries to facilitate clear communication.
By comprehensively understanding the manufacturing processes and quality assurance practices of woodworking machinery suppliers, B2B buyers can make informed decisions that align with their business needs and mitigate risks associated with sourcing machinery internationally.
Practical Sourcing Guide: A Step-by-Step Checklist for ‘woodworking machinery supplier’
This practical sourcing guide provides a comprehensive checklist for B2B buyers looking to procure woodworking machinery suppliers. By following these steps, international buyers from regions such as Africa, South America, the Middle East, and Europe can make informed decisions that meet their operational needs and enhance their supply chain efficiency.
Step 1: Define Your Technical Specifications
Before engaging with suppliers, it is essential to clearly outline your technical requirements. This includes machine types, sizes, capacities, and specific functionalities needed for your operations. A well-defined specification helps in identifying suppliers that can meet your exact needs and prevents costly miscommunications later in the procurement process.
- Consider production volume: Assess your current and projected production needs to determine the machinery specifications.
- Identify technology requirements: Specify any advanced technology or automation features that may enhance efficiency.
Step 2: Research Potential Suppliers
Conduct thorough research to identify potential woodworking machinery suppliers. Utilize industry directories, trade shows, and online marketplaces to compile a list of candidates. This initial vetting process is crucial for finding suppliers with a solid reputation and proven track record.
- Check online reviews: Look for testimonials and feedback from previous clients.
- Network within industry circles: Engage with industry peers to gain insights into reliable suppliers.
Step 3: Evaluate Supplier Certifications and Compliance
Ensure that potential suppliers possess the necessary certifications and comply with international standards. This step is vital for guaranteeing product quality and safety, as well as for meeting regulatory requirements in your region.
- ISO certifications: Look for suppliers with ISO 9001 or other relevant certifications that indicate quality management systems.
- Safety standards: Verify compliance with safety regulations pertinent to woodworking machinery.
Step 4: Request Detailed Quotations
Once you have narrowed down your list of suppliers, request detailed quotations. This should include not only the price but also terms of payment, delivery timelines, and warranty information. A comprehensive quotation allows for better comparisons and helps in negotiating favorable terms.
- Breakdown of costs: Ensure quotations detail all costs, including shipping and customs duties.
- Warranty and service agreements: Clarify what after-sales support is offered.
Step 5: Conduct On-site Visits or Virtual Tours
If feasible, visit the supplier’s facility to inspect their operations firsthand. Alternatively, request a virtual tour to assess their manufacturing processes. This step is critical for verifying the supplier’s capabilities and quality control measures.
- Observe production practices: Evaluate their adherence to quality standards and safety protocols.
- Meet the team: Engage with the staff to gauge their expertise and professionalism.
Step 6: Assess Supply Chain Reliability
Analyze the supplier’s supply chain logistics, including their ability to deliver on time and maintain consistent quality. A reliable supply chain is crucial for uninterrupted operations and minimizing downtime.
- Lead times: Understand their production lead times and shipping logistics.
- Contingency plans: Inquire about their strategies for handling potential disruptions.
Step 7: Negotiate Terms and Finalize the Agreement
Once you have selected a supplier, initiate negotiations to finalize terms. This includes pricing, payment schedules, delivery timelines, and any other relevant conditions. A well-negotiated agreement protects your interests and fosters a collaborative relationship.
- Consider long-term partnerships: Discuss opportunities for volume discounts or long-term contracts.
- Clarify exit strategies: Ensure there are clear terms for contract termination if necessary.
By following this step-by-step checklist, B2B buyers can effectively source woodworking machinery suppliers that align with their operational needs and quality expectations.
Comprehensive Cost and Pricing Analysis for woodworking machinery supplier Sourcing
What Are the Key Cost Components in Woodworking Machinery Sourcing?
When sourcing woodworking machinery, understanding the various cost components is crucial for international B2B buyers. The cost structure typically includes:
-
Materials: This encompasses the raw materials used in machinery production, such as steel, aluminum, and specialized components. Prices can fluctuate based on global supply chain dynamics and local availability.
-
Labor: Labor costs vary significantly depending on the region where the machinery is manufactured. Countries with lower labor costs can offer more competitive pricing, but buyers should also consider the skill level and expertise of the workforce.
-
Manufacturing Overhead: This includes indirect costs such as utilities, rent, and administrative expenses that contribute to the overall cost of production. Efficient manufacturers often have lower overhead costs, which can positively impact pricing.
-
Tooling: Custom tooling may be necessary for specific machinery configurations, influencing the upfront costs. Buyers should assess whether standard tools can meet their needs to reduce expenses.
-
Quality Control (QC): Implementing rigorous QC processes ensures that machinery meets required standards, but it also adds to the cost. Buyers should inquire about the QC measures in place to ensure they are getting value for their investment.
-
Logistics: Shipping and handling costs can vary based on the distance from the supplier to the buyer, as well as the mode of transport. This factor is especially important for buyers in Africa and South America, where logistics infrastructure may impact delivery times and costs.
-
Margin: Suppliers typically include a profit margin in their pricing. Understanding the expected margin can help buyers evaluate whether the price is fair based on the quality and service provided.
How Do Price Influencers Impact Woodworking Machinery Costs?
Several factors can influence the pricing of woodworking machinery:
-
Volume and Minimum Order Quantity (MOQ): Larger orders often lead to discounts due to economies of scale. Buyers should negotiate MOQs to optimize their purchasing strategy.
-
Specifications and Customization: Custom-built machinery tailored to specific needs will generally come at a higher price. Buyers should clearly define their requirements to avoid unexpected costs.
-
Materials and Quality Certifications: The choice of materials and the presence of quality certifications (e.g., ISO, CE) can affect pricing. Higher quality materials and certified products may command a premium, but they often result in better performance and durability.
-
Supplier Factors: The reputation and reliability of the supplier can significantly impact pricing. Established suppliers may charge more due to their experience, while newer entrants might offer lower prices to gain market share.
-
Incoterms: Understanding the chosen Incoterms (International Commercial Terms) is essential for accurately assessing total costs. Terms like FOB (Free on Board) or CIF (Cost, Insurance, and Freight) can influence logistics costs and responsibilities.
What Are the Best Practices for Negotiating Prices in Woodworking Machinery Sourcing?
For international B2B buyers, particularly those from Africa, South America, the Middle East, and Europe, effective negotiation strategies can lead to better pricing:
-
Conduct Market Research: Gather data on current market prices and trends to strengthen your negotiating position. Understanding the competitive landscape can help identify fair pricing.
-
Build Relationships: Establishing a rapport with suppliers can lead to better pricing and terms. Long-term partnerships often yield more favorable conditions compared to one-off transactions.
-
Evaluate Total Cost of Ownership (TCO): Consider not just the initial purchase price but also maintenance, energy consumption, and potential downtime costs. A slightly higher upfront cost may be justified if the machinery offers lower operational costs over time.
-
Be Transparent About Your Needs: Clearly communicate your expectations and any budget constraints to suppliers. This transparency can facilitate more constructive discussions and potential compromises.
Why Is It Important to Consider Pricing Nuances for International Buyers?
International buyers must be aware of pricing nuances that can affect their sourcing decisions. Currency fluctuations, import tariffs, and local regulations can all impact the final cost of machinery. Additionally, understanding local market conditions in regions like Brazil or Mexico can aid buyers in making informed decisions that align with their financial strategies.
Disclaimer: The prices mentioned in this analysis are indicative and can vary based on several factors including market conditions and supplier negotiations. Always seek updated quotes from suppliers to ensure accurate budgeting.
Alternatives Analysis: Comparing woodworking machinery supplier With Other Solutions
Understanding Alternative Solutions to Woodworking Machinery Suppliers
In the competitive landscape of woodworking, international B2B buyers often seek effective solutions that meet their operational needs. While traditional woodworking machinery suppliers offer a range of specialized tools, exploring alternative methods can provide additional flexibility, cost savings, and operational efficiency. This section compares woodworking machinery suppliers with two viable alternatives: CNC (Computer Numerical Control) machines and manual woodworking techniques.
Comparison Table of Woodworking Solutions
Comparison Aspect | Woodworking Machinery Supplier | CNC Machines | Manual Woodworking Techniques |
---|---|---|---|
Performance | High precision, reliable output | Exceptional precision, complex shapes | Variable, depends on skill level |
Cost | Higher initial investment | Moderate to high investment, plus software | Low initial cost, but labor-intensive |
Ease of Implementation | Requires training and setup | Requires specialized training and software installation | Minimal setup, but skill-dependent |
Maintenance | Regular maintenance required | Software updates and hardware maintenance | Low maintenance, but labor-intensive |
Best Use Case | Large-scale production | Complex, precision-demanding projects | Custom, artisanal woodworking |
What Are the Benefits and Drawbacks of CNC Machines?
CNC machines represent a significant advancement in woodworking technology, allowing for high precision and the ability to create complex designs that would be difficult or impossible to achieve with traditional tools. The main advantages of CNC machines include their exceptional accuracy and the ability to automate repetitive tasks, which can drastically reduce production times. However, the initial investment can be substantial, and there is a learning curve associated with operating the software and machinery. For businesses focused on high-volume production or intricate designs, CNC machines can be a worthy investment.
How Do Manual Woodworking Techniques Compare?
Manual woodworking techniques offer a more traditional approach that can appeal to artisans and small-scale producers. The primary advantages of this method include lower initial costs and the ability to create unique, handcrafted products that stand out in the market. This approach requires less investment in machinery, making it accessible for startups and small businesses. However, the performance can vary significantly based on the skill level of the workers, and production times may be longer compared to automated solutions. This method is ideal for businesses that prioritize craftsmanship over efficiency.
Conclusion: How to Choose the Right Solution for Your Woodworking Needs
When selecting between woodworking machinery suppliers and alternative solutions like CNC machines or manual techniques, B2B buyers should carefully consider their specific operational needs, budget constraints, and desired output quality. For companies focusing on large-scale production with a need for precision, CNC machines may provide the best return on investment. Conversely, businesses that value artisanal quality and lower startup costs might benefit more from manual woodworking techniques. By weighing these factors, international buyers can make informed decisions that align with their strategic goals.
Essential Technical Properties and Trade Terminology for woodworking machinery supplier
Understanding the technical properties and trade terminology in woodworking machinery is essential for international B2B buyers. This knowledge not only facilitates smoother negotiations but also ensures that suppliers meet the specific requirements of projects in diverse markets such as Africa, South America, the Middle East, and Europe.
What are the Key Technical Properties of Woodworking Machinery?
-
Material Grade
– The quality of materials used in machinery construction affects durability and performance. Common grades include carbon steel, stainless steel, and cast iron. A higher material grade typically translates to better resistance to wear and tear, which is crucial for long-term investments. -
Tolerance Levels
– Tolerance refers to the permissible limit of variation in a physical dimension. In woodworking machinery, tight tolerances ensure precision in cutting and shaping wood, which directly impacts product quality. Understanding tolerance levels helps buyers assess whether a machine meets their specific production standards. -
Power Rating
– This specification indicates the amount of energy required to operate the machine, usually measured in horsepower (HP) or kilowatts (kW). A higher power rating often allows for handling larger volumes of work or denser materials. Buyers should consider their production needs when evaluating power ratings to ensure optimal performance. -
Feed Speed
– Feed speed is the rate at which material moves through the machine, typically measured in meters per minute (m/min). A higher feed speed can enhance productivity, but it must be balanced with the quality of the cut. Buyers should analyze their workflow requirements to select machinery that aligns with their production pace. -
Cutting Depth and Width
– These specifications define the maximum depth and width of cuts the machine can achieve. Understanding these parameters is vital for buyers to ensure that the machinery can handle the dimensions of the wood products they intend to manufacture.
Which Trade Terms Should International B2B Buyers Understand?
-
OEM (Original Equipment Manufacturer)
– OEM refers to a company that produces parts and equipment that may be marketed by another manufacturer. For buyers, partnering with OEMs can ensure high-quality components and reliable machinery performance. It’s crucial to verify the OEM status of suppliers to avoid counterfeit products. -
MOQ (Minimum Order Quantity)
– MOQ is the smallest quantity of a product that a supplier is willing to sell. Understanding MOQ helps buyers plan their purchases effectively. This is particularly important for international transactions where shipping costs can escalate for smaller orders. -
RFQ (Request for Quotation)
– An RFQ is a document used to invite suppliers to bid on specific products or services. By issuing an RFQ, buyers can gather multiple quotes, compare prices, and negotiate better terms. This process is essential for making informed purchasing decisions in competitive markets. -
Incoterms (International Commercial Terms)
– Incoterms are a series of predefined commercial terms published by the International Chamber of Commerce. These terms define the responsibilities of buyers and sellers regarding shipping, insurance, and tariffs. Familiarity with Incoterms helps buyers minimize risks associated with international shipping. -
Lead Time
– Lead time is the duration from the placement of an order to its delivery. Understanding lead times is essential for effective project planning and inventory management. Buyers should consider lead times when negotiating contracts to ensure they meet their production schedules.
Conclusion
Grasping the essential technical properties and trade terminology related to woodworking machinery equips international B2B buyers with the tools needed to make informed decisions. By understanding these aspects, buyers can enhance their procurement strategies, ensuring they select machinery that meets their operational needs while navigating the complexities of international trade effectively.
Navigating Market Dynamics and Sourcing Trends in the woodworking machinery supplier Sector
What Are the Current Market Dynamics and Key Trends in the Woodworking Machinery Sector?
The woodworking machinery supplier sector is witnessing transformative changes driven by globalization, technological advancements, and shifting buyer preferences. A significant driver is the increasing demand for high-quality, precision-engineered machinery that enhances production efficiency. International buyers from regions like Africa, South America, the Middle East, and Europe are particularly focused on machinery that supports sustainable practices while ensuring compliance with international standards.
Emerging technologies such as IoT and automation are reshaping sourcing trends, enabling suppliers to offer smarter, connected machines that provide real-time data analytics for improved operational efficiency. Moreover, the rise of e-commerce platforms is changing the procurement landscape, allowing buyers to access a broader range of suppliers and product options than ever before. For instance, buyers in Brazil and Mexico can now leverage online marketplaces to compare prices and features, streamlining their decision-making process.
Additionally, the emphasis on customization is growing, with suppliers increasingly offering tailored solutions to meet specific production needs. This trend is particularly relevant for buyers looking to differentiate their products in competitive markets. Understanding these dynamics is crucial for international buyers to make informed sourcing decisions that align with their operational objectives.
How Is Sustainability Shaping the Woodworking Machinery Supply Chain?
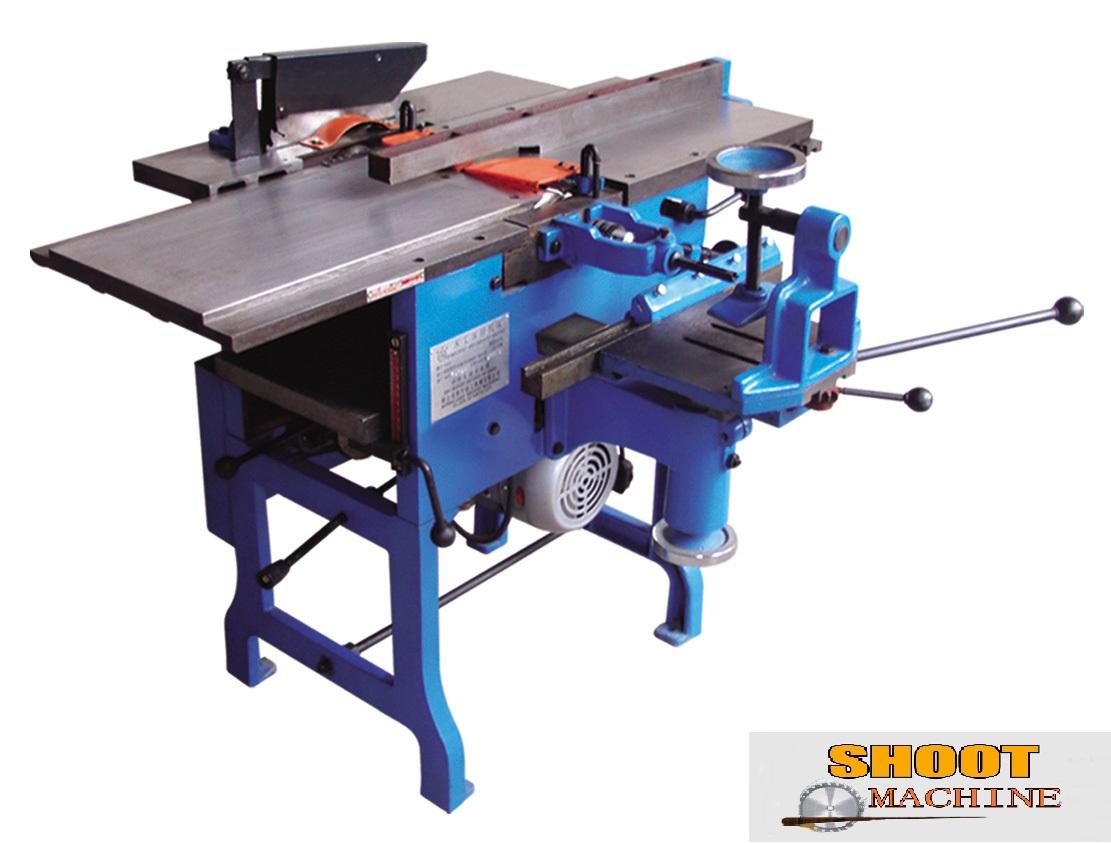
A stock image related to woodworking machinery supplier.
Sustainability is no longer just a buzzword; it has become a fundamental aspect of sourcing strategies in the woodworking machinery sector. The environmental impact of machinery production, including energy consumption and resource depletion, is under scrutiny. Buyers are increasingly prioritizing suppliers who demonstrate a commitment to sustainable practices, such as using renewable materials and minimizing waste during manufacturing processes.
Ethical sourcing is also gaining traction, with buyers seeking transparency in their supply chains. This includes understanding the provenance of materials and ensuring that suppliers adhere to fair labor practices. Certifications such as FSC (Forest Stewardship Council) and PEFC (Programme for the Endorsement of Forest Certification) are becoming essential criteria for B2B buyers, signaling a supplier’s dedication to responsible sourcing.
Furthermore, the integration of ‘green’ technologies in machinery design—such as energy-efficient motors and recyclable components—offers an additional selling point for suppliers. By aligning their offerings with the principles of sustainability, suppliers can not only meet the growing demands of environmentally conscious buyers but also differentiate themselves in a crowded marketplace.
How Has the Woodworking Machinery Supplier Sector Evolved Over Time?
The woodworking machinery supplier sector has evolved significantly over the past few decades, transitioning from manual to automated processes. Historically, woodworking relied heavily on skilled labor, with craftsmen using basic tools. However, the advent of technology in the late 20th century introduced sophisticated machinery that enhanced production capabilities.
The shift towards automation began in earnest with the introduction of CNC (Computer Numerical Control) machines, which revolutionized the industry by allowing for precise cuts and designs with minimal human intervention. This evolution has enabled suppliers to cater to a broader range of clients, from small workshops to large industrial manufacturers, thereby expanding their market reach.
In recent years, the focus has shifted towards integrating smart technologies into woodworking machinery, making it essential for international buyers to stay abreast of these advancements. Understanding the historical context helps buyers appreciate the innovations that have shaped current market dynamics, allowing for more strategic sourcing decisions.
Frequently Asked Questions (FAQs) for B2B Buyers of woodworking machinery supplier
-
How do I choose the right woodworking machinery supplier for my business needs?
Choosing the right woodworking machinery supplier involves assessing several key factors. Start by evaluating the supplier’s industry experience and reputation. Check for certifications and customer testimonials to ensure reliability. Additionally, consider their range of machinery and whether they offer customization options to fit your specific production requirements. Finally, initiate discussions about after-sales support, spare parts availability, and warranty terms to gauge their commitment to customer service. -
What are the essential certifications to look for in a woodworking machinery supplier?
When sourcing a woodworking machinery supplier, look for certifications that demonstrate adherence to international safety and quality standards. Key certifications include ISO 9001 for quality management systems and CE marking for compliance with European safety regulations. Additionally, consider suppliers with certifications specific to your region, such as ANSI in North America or AS/NZS in Australia. These certifications provide assurance that the machinery meets safety and performance benchmarks, reducing the risk of operational issues. -
What should I know about minimum order quantities (MOQ) when purchasing woodworking machinery?
Understanding MOQ is crucial for managing your budget and inventory effectively. Different suppliers have varying MOQs based on production capacity and machinery type. It is essential to clarify these terms upfront to avoid unexpected costs. If your needs do not meet the MOQ, discuss potential options like collaborative purchasing with other businesses or exploring flexible order arrangements. This can help minimize upfront investment while still securing the necessary machinery for your operations. -
How can I assess the quality assurance processes of a woodworking machinery supplier?
To evaluate a supplier’s quality assurance (QA) processes, request detailed information about their production methods and quality control measures. Inquire about their testing protocols, including inspections during manufacturing and final product testing. Suppliers who are transparent about their QA processes often provide documentation, such as test reports and compliance certificates. Additionally, consider scheduling a factory visit to observe their operations firsthand, which can give you greater confidence in their commitment to quality. -
What payment terms should I negotiate with a woodworking machinery supplier?
Negotiating favorable payment terms is crucial for managing cash flow. Common terms include a deposit upon order placement, with the balance due upon delivery or after installation. For larger orders, consider discussing installment payments linked to production milestones. Additionally, explore options for letters of credit or escrow services to mitigate risks. Ensure that any negotiated terms are documented clearly in the contract to avoid misunderstandings and ensure compliance. -
How do I handle logistics and shipping when sourcing woodworking machinery internationally?
Effective logistics management is key when importing woodworking machinery. Start by discussing shipping options with your supplier, who may have preferred carriers or freight forwarders. Consider the total landed cost, including shipping, customs duties, and insurance. Familiarize yourself with import regulations in your country to avoid delays. Partnering with a logistics expert can streamline the process, ensuring that machinery arrives safely and on time, while also helping navigate any bureaucratic hurdles. -
What are the common challenges faced when sourcing woodworking machinery from international suppliers?
Sourcing woodworking machinery internationally can present challenges such as language barriers, cultural differences, and varying business practices. Additionally, time zone differences can complicate communication. To mitigate these issues, establish clear communication channels and consider using professional translation services if necessary. Thoroughly research potential suppliers and utilize platforms that provide verified reviews and ratings. Building a strong relationship with your supplier can also help address challenges as they arise. -
How can I ensure that the machinery I purchase meets my specific production requirements?
To ensure that the machinery meets your production needs, start with a detailed assessment of your operational processes and requirements. Communicate these needs clearly to potential suppliers, including specifications related to capacity, speed, and material types. Request samples or demonstrations of the machinery to evaluate performance. Additionally, inquire about customization options, as many suppliers offer tailored solutions that can enhance efficiency and productivity in your specific application.
Important Disclaimer & Terms of Use
⚠️ Important Disclaimer
The information provided in this guide, including content regarding manufacturers, technical specifications, and market analysis, is for informational and educational purposes only. It does not constitute professional procurement advice, financial advice, or legal advice.
While we have made every effort to ensure the accuracy and timeliness of the information, we are not responsible for any errors, omissions, or outdated information. Market conditions, company details, and technical standards are subject to change.
B2B buyers must conduct their own independent and thorough due diligence before making any purchasing decisions. This includes contacting suppliers directly, verifying certifications, requesting samples, and seeking professional consultation. The risk of relying on any information in this guide is borne solely by the reader.
Strategic Sourcing Conclusion and Outlook for woodworking machinery supplier
In summary, effective strategic sourcing for woodworking machinery suppliers presents an invaluable opportunity for international B2B buyers, particularly those from Africa, South America, the Middle East, and Europe. Understanding the nuances of the global supply chain, including regional manufacturing capabilities and logistics considerations, can significantly enhance procurement efficiency and cost-effectiveness.
Buyers should prioritize establishing long-term partnerships with suppliers that demonstrate reliability and innovation. By leveraging local insights and aligning with suppliers who understand the unique demands of your market, businesses can ensure a competitive edge. Additionally, embracing digital tools and technologies will facilitate better communication and streamline sourcing processes, making it easier to adapt to changing market dynamics.
As you look towards the future, consider the evolving trends in sustainability and automation within the woodworking machinery sector. Engaging with suppliers who prioritize eco-friendly practices and offer advanced technological solutions will not only meet regulatory demands but also resonate with increasingly environmentally conscious consumers.
Embrace the potential of strategic sourcing by taking proactive steps today—evaluate your current suppliers, explore new partnerships, and invest in technologies that can drive your business forward. The woodworking machinery industry is ripe with opportunities; seize them to build a resilient and sustainable operation.