Transform Your Business: The Complete Apparel Custom Guide (2025)
Introduction: Navigating the Global Market for apparel custom
In the dynamic landscape of the global apparel custom market, international B2B buyers face a myriad of challenges, from sourcing the right materials to navigating complex supplier networks. As businesses strive to create unique clothing lines that resonate with diverse consumer preferences, understanding the intricacies of apparel customization becomes paramount. This guide is designed to empower buyers in Africa, South America, the Middle East, and Europe—regions characterized by rich cultural tapestries and evolving fashion demands.
Within this comprehensive resource, we will explore various types of apparel customization, including bespoke tailoring, screen printing, and embroidery. Each section will provide insights into the applications of these techniques across different sectors, ensuring that you can align your sourcing strategies with market trends. Additionally, we will delve into critical aspects of supplier vetting, helping you identify reliable partners who uphold quality and ethical practices. Cost considerations will also be addressed, offering clarity on pricing structures and enabling you to budget effectively for your custom apparel projects.
By leveraging the actionable insights provided in this guide, B2B buyers can make informed purchasing decisions that not only enhance their product offerings but also foster sustainable growth in a competitive global market. Whether you’re looking to establish a brand presence or expand your existing portfolio, this guide serves as your roadmap to navigating the complexities of apparel custom with confidence.
Understanding apparel custom Types and Variations
Type Name | Key Distinguishing Features | Primary B2B Applications | Brief Pros & Cons for Buyers |
---|---|---|---|
Screen Printing | Uses stencils to apply ink on fabric in layers | Promotional apparel, event merchandise | Pros: Cost-effective for large runs; vibrant colors. Cons: Less effective for detailed designs. |
Embroidery | Stitches designs directly onto fabric | Corporate uniforms, branded clothing | Pros: Durable and professional appearance. Cons: Higher cost for small batches. |
Sublimation Printing | Transfers dye onto fabric using heat, resulting in vivid prints | Sportswear, fashion apparel | Pros: Full-color designs with no texture change. Cons: Limited to polyester fabrics. |
Cut and Sew Customization | Tailoring garments from scratch based on specific designs | High-end fashion, bespoke clothing | Pros: Unique designs tailored to client specifications. Cons: Longer lead times and higher costs. |
Heat Transfer Printing | Applies designs using heat and pressure on pre-made garments | Promotional items, custom t-shirts | Pros: Quick turnaround; good for small orders. Cons: May not be as durable as embroidery. |
What Are the Key Characteristics of Screen Printing?
Screen printing is a popular method where ink is pushed through a stencil onto the fabric, layer by layer. This technique is particularly suitable for promotional apparel and event merchandise due to its cost-effectiveness when producing large quantities. B2B buyers should consider the minimum order quantities, as screen printing is most economical for bulk orders. However, it may not be ideal for intricate designs, as the process can limit detail.
How Does Embroidery Stand Out in Apparel Customization?
Embroidery involves stitching designs directly onto the fabric, offering a professional and durable finish. This method is widely used for corporate uniforms and branded clothing, providing a polished look that enhances brand image. B2B buyers must weigh the higher costs associated with embroidery, especially for small runs, against the long-lasting quality it provides. It’s essential to consider fabric type and thread color to ensure the best outcome.
Why Choose Sublimation Printing for Custom Apparel?
Sublimation printing is a dye transfer process that results in vibrant, full-color designs. This method is particularly well-suited for sportswear and fashion apparel, as it allows for all-over prints without altering the fabric’s texture. For B2B buyers, understanding the limitations is crucial, as sublimation is primarily compatible with polyester fabrics. Additionally, buyers should consider the potential for faster production times compared to other methods.
What Are the Benefits of Cut and Sew Customization?
Cut and sew customization involves creating garments from scratch based on specific designs, making it ideal for high-end fashion and bespoke clothing. This method allows for complete creative control over the design and fit, which is a significant advantage for brands looking to differentiate themselves. However, B2B buyers should be prepared for longer lead times and higher costs associated with this level of customization. It is essential to have a clear design and material specifications to streamline the process.
When Should You Consider Heat Transfer Printing?
Heat transfer printing is a method where designs are applied to pre-made garments using heat and pressure. This technique is advantageous for promotional items and custom t-shirts due to its quick turnaround and suitability for smaller orders. B2B buyers should consider the durability of heat transfer prints, as they may not last as long as embroidery. It’s also vital to evaluate the fabric type to ensure compatibility with the transfer materials used.
Related Video: Finding and Working With Apparel Manufacturers For Your Clothing Brand The Easy Way
Key Industrial Applications of apparel custom
Industry/Sector | Specific Application of apparel custom | Value/Benefit for the Business | Key Sourcing Considerations for this Application |
---|---|---|---|
Fashion Retail | Customized apparel lines for seasonal collections | Increased brand loyalty and customer engagement | Supplier reliability, minimum order quantities, and lead times |
Sports & Activewear | Personalized sports uniforms and gear | Enhanced team identity and performance | Material quality, customization options, and production capabilities |
Corporate Uniforms | Tailored uniforms for employees | Improved brand image and employee morale | Fabric durability, sizing accuracy, and compliance with safety standards |
Promotional Merchandise | Branded apparel for events and giveaways | Effective marketing tool and increased visibility | Cost-effectiveness, design flexibility, and turnaround time |
Hospitality & Tourism | Custom apparel for staff and merchandise | Enhanced customer experience and brand recognition | Style consistency, fabric comfort, and regional cultural relevance |
How is Apparel Custom Used in Fashion Retail?
In the fashion retail sector, apparel custom plays a crucial role in creating unique seasonal collections. Retailers can design garments that reflect current trends while catering to the specific tastes of their target audience. This customization helps brands differentiate themselves in a saturated market, driving customer loyalty and engagement. For international B2B buyers, key considerations include finding reliable suppliers capable of meeting minimum order quantities and maintaining quick lead times to keep up with fashion cycles.
What are the Benefits of Custom Apparel in Sports & Activewear?
The sports and activewear industry leverages apparel custom to produce personalized uniforms and gear that enhance team identity and performance. Customization allows teams to incorporate logos, colors, and even player names, fostering a sense of unity and pride among members. For B2B buyers, it’s essential to evaluate the quality of materials used, the range of customization options available, and the supplier’s production capabilities to ensure timely delivery for sports events.
Why Invest in Customized Corporate Uniforms?
Corporate uniforms customized for employees serve multiple purposes, from enhancing brand image to improving employee morale. A well-designed uniform reflects the company’s values and professionalism, making it an effective tool for branding. For international buyers, sourcing considerations include ensuring fabric durability, accurate sizing for diverse body types, and compliance with safety standards, especially in industries such as construction or healthcare.
How Can Promotional Merchandise Utilize Apparel Custom?
Promotional merchandise, including branded apparel for events and giveaways, benefits significantly from customization. This type of apparel acts as an effective marketing tool, increasing brand visibility and consumer engagement. When sourcing these items, B2B buyers should focus on cost-effectiveness, design flexibility, and the supplier’s ability to meet tight turnaround times, especially for events with short lead times.
What Role Does Custom Apparel Play in Hospitality & Tourism?
In the hospitality and tourism sector, custom apparel for staff and merchandise can significantly enhance the customer experience and brand recognition. Staff uniforms that reflect the theme or ethos of a hospitality venue can create a cohesive and inviting atmosphere for guests. B2B buyers should prioritize style consistency, fabric comfort, and an understanding of regional cultural relevance when sourcing custom apparel, ensuring that the final products resonate with the target audience.
Related Video: How To Create Cut and Sew Apparel From Start To Finish
3 Common User Pain Points for ‘apparel custom’ & Their Solutions
Scenario 1: Managing Lead Times in Apparel Customization
The Problem: One of the most significant challenges faced by B2B buyers in the apparel customization sector is the unpredictability of lead times. Buyers often encounter situations where suppliers promise quick turnaround times but fail to deliver, leading to delays in product launches or inventory shortages. This can be especially problematic for businesses in fast-paced markets like fashion or promotional merchandise, where timing is crucial for capitalizing on trends. Buyers in regions such as Africa and South America, where logistics can also be challenging, feel this pain point acutely, as extended lead times can significantly impact sales and brand reputation.
The Solution: To effectively manage lead times, B2B buyers should prioritize working with suppliers that provide transparent production timelines and have a proven track record of meeting deadlines. Establishing a clear communication channel is essential; regular check-ins and updates can help buyers stay informed about the production status. Additionally, implementing a buffer in inventory planning—such as ordering additional stock ahead of peak seasons—can mitigate risks associated with delays. Utilizing technology, such as supply chain management software, can provide real-time tracking of orders and enhance collaboration with suppliers, ensuring that both parties are aligned on expectations.
Scenario 2: Navigating Quality Control Challenges in Custom Apparel
The Problem: Quality control is another major pain point for B2B buyers in the custom apparel industry. Buyers often receive products that do not meet the specified standards, whether due to fabric quality, stitching issues, or color mismatches. This issue can lead to customer dissatisfaction and returns, which are particularly damaging for businesses looking to build long-term relationships in competitive markets like Europe and the Middle East. The challenge is compounded by language barriers and cultural differences that can arise when sourcing from international suppliers.
The Solution: To navigate quality control challenges, buyers should establish comprehensive quality assurance protocols before placing orders. This includes providing detailed specifications and samples for approval before mass production begins. It is also beneficial to conduct factory audits, either in-person or via third-party services, to assess the supplier’s capabilities and adherence to quality standards. Building strong relationships with suppliers can facilitate better understanding and adherence to quality expectations. Furthermore, consider implementing a system for collecting feedback from end customers regarding product quality, which can inform future orders and supplier evaluations.
Scenario 3: Understanding Cultural Differences in Custom Apparel Design
The Problem: B2B buyers often struggle with cultural differences that influence apparel design preferences. For instance, what is considered fashionable or acceptable in one region may not resonate in another. Buyers from diverse markets such as Africa, South America, and the Middle East may find it challenging to create designs that appeal to local tastes while also being compliant with cultural norms. This disconnect can lead to unsold inventory and wasted resources, making it crucial for buyers to understand these nuances.
The Solution: To overcome cultural barriers in apparel design, buyers should invest in market research that focuses on local trends, preferences, and cultural sensitivities. Collaborating with local designers or consultants can provide invaluable insights into what resonates with target demographics. Additionally, conducting focus groups or surveys with potential customers can validate design concepts before production. It’s also essential to stay informed about regional events, festivals, and holidays that may influence apparel choices. By aligning designs with local culture and preferences, buyers can significantly enhance the appeal of their custom apparel offerings, leading to increased sales and customer loyalty.
Strategic Material Selection Guide for apparel custom
What Are the Key Properties of Cotton in Apparel Customization?
Cotton is a staple material in the apparel industry, renowned for its softness and breathability. It has excellent moisture-wicking properties, making it suitable for a variety of climates, particularly in warmer regions like Africa and South America. Cotton typically has a temperature rating that allows for comfort in moderate heat, and it is biodegradable, which appeals to environmentally conscious brands.
Pros & Cons: Cotton is durable and easy to dye, which allows for vibrant colors and patterns. However, it can shrink and wrinkle easily, requiring careful handling during manufacturing. The cost of cotton is generally moderate, but fluctuations in supply can affect pricing, making it essential for buyers to consider sourcing stability.
Impact on Application: Cotton is compatible with a range of dyes and finishes, enhancing its versatility in design. However, it may not perform well in extreme weather conditions without additional treatments.
Considerations for International Buyers: Compliance with standards such as Oeko-Tex or GOTS is crucial for buyers focused on sustainability. In regions like the UAE and Europe, there is a growing demand for organic cotton, which may influence sourcing decisions.
How Does Polyester Compare as a Material for Apparel Customization?
Polyester is a synthetic fabric known for its strength and resistance to stretching and shrinking. It has a high temperature rating and is often used in activewear due to its moisture-wicking capabilities. Polyester also exhibits excellent resistance to mildew and abrasion, making it suitable for various applications.
Pros & Cons: The durability of polyester makes it a cost-effective choice for mass production, but it can feel less breathable than natural fibers. Additionally, while polyester is generally low-cost, the environmental impact of synthetic fibers is a growing concern among consumers and brands.
Impact on Application: Polyester is compatible with a wide range of finishes, from moisture management to UV protection, making it highly versatile for different apparel needs. However, it may not be suitable for eco-conscious brands unless sourced from recycled materials.
Considerations for International Buyers: Buyers should be aware of standards like ASTM D5034 for fabric strength and consider the implications of sourcing polyester from regions with stringent environmental regulations.
What Are the Benefits of Using Wool in Apparel Customization?
Wool is a natural fiber prized for its thermal insulation and moisture-wicking properties. It is particularly effective in colder climates, making it a popular choice for winter apparel. Wool can regulate temperature, keeping the wearer warm in winter and cool in summer.
Pros & Cons: Wool is highly durable and resistant to wrinkles, but it can be more expensive than cotton or polyester. The manufacturing complexity can also be higher due to the need for specialized processing.
Impact on Application: Wool is compatible with various finishes, enhancing its performance in outdoor apparel. However, it may not be suitable for all climates, particularly in hotter regions.
Considerations for International Buyers: Buyers in Europe and the Middle East should ensure compliance with standards such as ISO 14001 for environmental management, as wool production can have significant ecological impacts.
How Does Nylon Fit into the Apparel Customization Landscape?
Nylon is another synthetic material known for its strength and elasticity. It has excellent abrasion resistance and is often used in activewear and outdoor apparel. Nylon has a high temperature rating, making it suitable for a variety of applications, including swimwear.
Pros & Cons: The primary advantage of nylon is its durability and lightweight nature. However, it can be less breathable than natural fibers, which may limit its use in certain applications. The cost of nylon is generally moderate, but sourcing from sustainable producers can increase expenses.
Impact on Application: Nylon is compatible with various treatments, such as water repellency and UV protection, enhancing its functionality in outdoor and performance apparel. However, buyers should consider the environmental impact of nylon production.
Considerations for International Buyers: Compliance with standards like JIS L 1096 for fabric testing is essential for ensuring quality. Buyers from Africa and South America should also be aware of local regulations regarding synthetic materials.
Summary Table of Material Selection for Apparel Customization
Material | Typical Use Case for apparel custom | Key Advantage | Key Disadvantage/Limitation | Relative Cost (Low/Med/High) |
---|---|---|---|---|
Cotton | Casual wear, t-shirts, and summer apparel | Breathable and soft | Prone to shrinking and wrinkling | Medium |
Polyester | Activewear, sports apparel, and outerwear | Durable and moisture-wicking | Less breathable than natural fibers | Low |
Wool | Winter apparel, suits, and outerwear | Excellent thermal insulation | Higher cost and complex manufacturing | High |
Nylon | Activewear, swimwear, and outdoor apparel | Strong and lightweight | Less breathable than cotton | Medium |
In-depth Look: Manufacturing Processes and Quality Assurance for apparel custom
What Are the Main Stages of Manufacturing Apparel Custom?
Manufacturing custom apparel involves several critical stages that ensure the final product meets the specific needs of international B2B buyers. Understanding these stages can help buyers make informed decisions when selecting suppliers.
-
Material Preparation: This initial stage is crucial, as the quality of the raw materials directly impacts the final product. Suppliers typically source fabrics, trims, and other materials based on the specifications provided by the buyer. It is essential for buyers to verify the suppliers’ material sourcing practices, including sustainability considerations and compliance with international regulations.
-
Forming: During this stage, the prepared materials are cut and shaped into patterns that form the basis of the apparel. Advanced cutting techniques, such as laser cutting and automated fabric cutting machines, are often employed to enhance precision and minimize waste. Buyers should inquire about the technology and methods used to ensure that their designs are accurately realized.
-
Assembly: This stage involves stitching the formed pieces together. Various techniques, such as flatlock stitching, overlocking, and double stitching, are utilized depending on the garment type. Buyers should assess the supplier’s capabilities in handling complex designs and finishes, ensuring they can meet the desired quality levels.
-
Finishing: The finishing stage includes processes like washing, dyeing, and adding labels or tags. This step not only enhances the garment’s aesthetic appeal but also its performance attributes, such as moisture-wicking or stain resistance. Buyers should be aware of the finishing techniques employed and how they align with their brand standards.
How Is Quality Assurance Implemented in Apparel Custom Manufacturing?
Quality assurance (QA) is a vital component of the custom apparel manufacturing process, ensuring that products meet the required standards before reaching the buyer. Here’s how QA is typically implemented:
-
Understanding International Standards: Familiarity with international quality standards, such as ISO 9001, is essential for B2B buyers. ISO 9001 provides a framework for quality management systems and ensures consistent quality in products and services. Buyers should seek suppliers who are certified, as this indicates a commitment to maintaining high standards.
-
Industry-Specific Certifications: In addition to general standards, some industries have specific certifications like CE (Conformité Européenne) for products sold in the European market or API (American Petroleum Institute) for oil and gas apparel. Buyers should verify that their suppliers hold relevant certifications that demonstrate compliance with industry regulations.
-
Quality Control Checkpoints: Suppliers typically implement multiple quality control (QC) checkpoints throughout the manufacturing process:
– Incoming Quality Control (IQC): This step involves inspecting raw materials upon receipt to ensure they meet specifications.
– In-Process Quality Control (IPQC): Ongoing inspections during production help identify defects early in the process.
– Final Quality Control (FQC): A thorough inspection of finished products ensures they meet the agreed-upon standards before shipment.
What Common Testing Methods Are Used in Apparel Manufacturing?
To ensure the quality and durability of custom apparel, various testing methods are employed. Here are some common tests that B2B buyers should consider:
-
Fabric Testing: This includes tests for color fastness, shrinkage, and tensile strength. Buyers should request testing reports to confirm that the fabric meets their durability and aesthetic requirements.
-
Performance Testing: Depending on the intended use of the apparel (e.g., sportswear, workwear), performance tests may be necessary. These could include moisture management, breathability, and abrasion resistance tests.
-
Safety Testing: For specific markets, safety tests may be required, especially in sectors like healthcare or industrial workwear. Ensuring compliance with safety standards is crucial for protecting end-users.
How Can B2B Buyers Verify Supplier Quality Control?
To ensure that suppliers adhere to quality standards, B2B buyers must adopt a proactive approach to verify QC processes. Here are several strategies:
-
Supplier Audits: Conducting regular audits of potential suppliers can provide insights into their manufacturing processes and quality assurance practices. Audits can be done by the buyer or by third-party inspectors who specialize in quality assessment.
-
Requesting Quality Reports: Buyers should ask suppliers for detailed quality reports that document the results of IQC, IPQC, and FQC. These reports provide transparency and help buyers understand the supplier’s QC practices.
-
Third-Party Inspections: Engaging third-party inspection services can offer an unbiased assessment of the manufacturing process. These organizations can conduct inspections at various stages of production to ensure compliance with the buyer’s specifications.
What Are the QC and Certification Nuances for International B2B Buyers?
International buyers, particularly those from regions like Africa, South America, the Middle East, and Europe, must navigate specific nuances in QC and certification processes:
-
Cultural and Regulatory Differences: Different regions may have varying standards for quality and safety. Buyers should familiarize themselves with local regulations and ensure that their suppliers comply with these standards.
-
Language and Communication Barriers: Clear communication is essential in QC processes. Buyers should consider working with suppliers who have multilingual staff or offer translation services to avoid misunderstandings.
-
Time Zone Considerations: Coordinating inspections and audits can be challenging due to time zone differences. Buyers should establish a clear timeline for QC activities and ensure that suppliers are aligned with these expectations.
Conclusion
Understanding the manufacturing processes and quality assurance standards for custom apparel is crucial for international B2B buyers. By being informed about the stages of manufacturing, quality control practices, testing methods, and verification strategies, buyers can make confident decisions when selecting suppliers. This knowledge not only helps in securing high-quality products but also fosters long-term partnerships that are essential for success in the competitive global market.
Practical Sourcing Guide: A Step-by-Step Checklist for ‘apparel custom’
The following guide provides a structured approach for international B2B buyers looking to procure custom apparel. By following these steps, you can ensure a successful sourcing process that meets your business needs while fostering strong supplier relationships.
Step 1: Define Your Technical Specifications
Clearly outlining your technical specifications is crucial for successful sourcing. This includes fabric types, sizing standards, color palettes, and design elements. By having these details upfront, you can communicate your needs effectively, ensuring that suppliers understand your expectations and can deliver accordingly.
- Fabric Requirements: Specify the type of fabric needed, such as organic cotton or polyester blends.
- Sizing Standards: Provide clear size charts to avoid discrepancies.
Step 2: Conduct Market Research
Understanding the market landscape is essential for informed decision-making. Research potential suppliers in regions like Africa, South America, the Middle East, and Europe to identify those with a strong reputation in custom apparel.
- Industry Trends: Stay updated on the latest trends in apparel to gauge what suppliers are offering.
- Competitor Analysis: Look at what similar companies are sourcing and which suppliers they are using.
Step 3: Evaluate Potential Suppliers
Before finalizing a supplier, it’s vital to conduct a thorough evaluation. Request company profiles, case studies, and references from other buyers in your industry or region. This step helps you assess their reliability and capability to meet your needs.
- Request Samples: Always ask for samples to evaluate the quality of the apparel.
- Check Certifications: Verify if suppliers have relevant certifications, such as ISO or Fair Trade.
Step 4: Negotiate Terms and Conditions
Once you’ve shortlisted potential suppliers, it’s time to negotiate the terms of the contract. This includes pricing, minimum order quantities, lead times, and payment terms. Clear agreements help prevent misunderstandings later on.
- Pricing Structure: Understand the pricing model, including any hidden costs.
- Flexibility in Orders: Discuss the possibility of smaller initial orders to test the relationship.
Step 5: Establish Quality Control Measures
Implementing quality control measures is vital to ensure that the final products meet your specifications. Discuss quality assurance processes with your suppliers and establish checkpoints throughout the production cycle.
- Quality Checks: Set up regular inspections during production.
- Final Inspection: Ensure a thorough inspection before shipping to avoid issues upon arrival.
Step 6: Plan for Logistics and Shipping
Effective logistics planning is essential for timely delivery. Discuss shipping options with your supplier to determine the best methods for your needs. Consider factors such as cost, delivery time, and customs regulations in your country.
- Shipping Methods: Evaluate different shipping options like air freight versus sea freight based on urgency and cost.
- Customs Procedures: Familiarize yourself with customs regulations to avoid delays.
Step 7: Maintain Open Communication
Establishing and maintaining open lines of communication with your supplier is key to a successful partnership. Regular updates regarding production progress, potential challenges, and feedback can help ensure that both parties are aligned.
- Regular Check-Ins: Schedule periodic meetings or calls to discuss ongoing projects.
- Feedback Loop: Create a system for providing feedback on product quality and service.
By following this practical sourcing guide, B2B buyers can navigate the complexities of procuring custom apparel effectively, ensuring that they select the right suppliers and achieve their business objectives.
Comprehensive Cost and Pricing Analysis for apparel custom Sourcing
Understanding the cost structure and pricing dynamics for custom apparel sourcing is essential for international B2B buyers, especially those operating in diverse markets like Africa, South America, the Middle East, and Europe. Here’s a breakdown of the critical components that influence costs and pricing in this sector.
What Are the Key Cost Components in Custom Apparel Sourcing?
When evaluating the costs involved in custom apparel sourcing, several critical components should be taken into account:
-
Materials: The choice of fabrics, trims, and accessories significantly impacts the overall cost. High-quality materials will generally yield a higher price but can enhance the final product’s durability and appeal.
-
Labor: Labor costs vary significantly by region. For example, countries in Southeast Asia may offer lower labor costs compared to Europe or the Middle East. Understanding local wage standards and labor practices is crucial for accurate budgeting.
-
Manufacturing Overhead: This includes utilities, rent, equipment depreciation, and other indirect costs associated with running a manufacturing facility. Overhead can vary widely between suppliers and regions.
-
Tooling: Custom tooling or molds for specific designs can incur additional costs. These are usually one-time investments but can be significant for unique or intricate designs.
-
Quality Control (QC): Implementing quality assurance processes adds to the cost. However, investing in QC can prevent costly returns and reputational damage later.
-
Logistics: Shipping and handling costs, including freight and customs duties, must be factored into the total cost. The choice of shipping method (air vs. sea) will also influence pricing.
-
Margin: Suppliers typically add a margin to cover their risks and profit. Understanding market rates for margins in your specific product category can help in negotiations.
How Do Price Influencers Affect Custom Apparel Sourcing?
Several factors can influence the pricing of custom apparel, making it essential for buyers to consider these when sourcing:
-
Volume/MOQ (Minimum Order Quantity): Larger orders often lead to lower per-unit costs due to economies of scale. Negotiating favorable MOQs can significantly reduce overall expenses.
-
Specifications and Customization: Highly customized products or intricate specifications can lead to higher costs. It’s essential to balance customization with budget constraints.
-
Materials Quality and Certifications: Products that require certifications (e.g., organic, fair-trade) may have higher material costs. Buyers should assess the trade-offs between cost and compliance with standards.
-
Supplier Factors: The reputation, reliability, and location of the supplier can impact pricing. Suppliers with strong track records may charge a premium but offer better service and quality.
-
Incoterms: The choice of Incoterms (International Commercial Terms) can affect shipping costs and responsibilities. Understanding these terms is vital for calculating the total cost of ownership.
What Are Some Effective Buyer Tips for Custom Apparel Sourcing?
Navigating the complexities of apparel custom sourcing requires strategic approaches to ensure cost efficiency:
-
Negotiate Wisely: Always enter negotiations with a clear understanding of the market rates for each cost component. Leverage your volume to negotiate better terms and prices.
-
Focus on Total Cost of Ownership (TCO): Consider not just the initial pricing but also long-term costs, such as quality, durability, and potential returns. A lower upfront cost may lead to higher long-term expenses.
-
Understand Pricing Nuances: Familiarize yourself with regional pricing trends and the economic conditions of your suppliers. For example, currency fluctuations can affect costs and should be monitored closely.
-
Build Relationships: Establishing strong relationships with suppliers can lead to better pricing and terms over time. Trust and reliability can often yield more favorable conditions.
Conclusion
Understanding the comprehensive cost structure and pricing dynamics in custom apparel sourcing is crucial for international B2B buyers. By considering the various cost components, price influencers, and strategic buyer tips, businesses can make informed decisions that align with their budget and sourcing goals. Keep in mind that the prices mentioned here are indicative and can vary based on multiple factors, including market conditions and specific buyer-supplier agreements.
Alternatives Analysis: Comparing apparel custom With Other Solutions
Understanding the Importance of Alternative Solutions in Apparel Customization
In the dynamic landscape of the apparel industry, businesses often seek innovative solutions to meet their unique demands. While custom apparel offers tailored benefits, exploring alternative solutions can provide B2B buyers with a comprehensive understanding of their options. This section will compare ‘apparel custom’ with two viable alternatives: mass production and print-on-demand services. Each solution presents distinct advantages and challenges that can influence a buyer’s decision-making process.
Comparison Table of Apparel Custom and Alternative Solutions
Comparison Aspect | Apparel Custom | Mass Production | Print-on-Demand |
---|---|---|---|
Performance | High quality, tailored fit | Consistent quality, bulk output | Variable quality, dependent on supplier |
Cost | Higher upfront costs | Lower cost per unit | No upfront costs, higher per item |
Ease of Implementation | Complex, requires planning | Straightforward, established processes | Simple, minimal setup needed |
Maintenance | Ongoing design updates needed | Minimal, standard processes | Low, only when designs change |
Best Use Case | Unique brands, niche markets | High volume, uniform products | Small businesses, quick turnaround |
What Are the Pros and Cons of Mass Production in Apparel?
Mass production is a traditional manufacturing method characterized by high-volume output of standardized apparel items. One of the primary advantages of this approach is the reduced cost per unit, which appeals to businesses looking to maximize profit margins. Mass production is also highly efficient, allowing for quick turnaround times when orders are large. However, the major downside is the lack of customization; brands may struggle to differentiate themselves in a crowded market. Additionally, the environmental impact of mass production can be significant, leading to increased scrutiny from consumers who prioritize sustainability.
How Does Print-on-Demand Work as an Alternative to Apparel Custom?
Print-on-demand (POD) services enable businesses to create and sell customized apparel without holding inventory. This method offers significant flexibility, allowing brands to test various designs with minimal risk. The primary advantage of POD is the absence of upfront costs, as products are created only after an order is placed. However, the trade-off is often higher per-item costs and potential variability in quality, depending on the provider. This solution is ideal for small businesses or those entering new markets, as it allows for agile responses to changing consumer demands without the burden of excess inventory.
How Should B2B Buyers Choose the Right Apparel Solution?
Selecting the most suitable apparel solution hinges on various factors, including business goals, target market, and budget constraints. B2B buyers should conduct a thorough analysis of their specific needs and consider the pros and cons of each option. For brands that prioritize unique offerings and customer engagement, apparel customization may be the best fit. Conversely, businesses aiming for cost-effective solutions with high volume may lean towards mass production. Finally, those looking to test new designs or enter niche markets might find print-on-demand to be the most strategic approach. By aligning their choice with business objectives, buyers can enhance their competitive edge in the global apparel market.
Essential Technical Properties and Trade Terminology for apparel custom
What Are the Key Technical Properties in Apparel Customization?
Understanding the critical technical properties of apparel customization is essential for making informed purchasing decisions. Below are some of the most significant specifications that international B2B buyers should consider.
1. Material Grade: Why Is It Crucial for Apparel Quality?
Material grade refers to the quality and characteristics of the fabric used in production. Different grades can affect the durability, comfort, and overall appearance of the finished product. For instance, higher-grade materials tend to be more resistant to wear and tear, making them a better investment for businesses focused on long-term use. Buyers should assess material grades that align with their brand positioning and customer expectations.
2. Tolerance: How Does It Impact Fit and Functionality?
Tolerance is the permissible limit of variation in measurements, which is critical in apparel manufacturing. It ensures that the final product maintains the desired fit and functionality. For instance, a tolerance of ±1 cm in garment size can significantly affect how the apparel fits the end consumer. Understanding tolerances can help buyers avoid costly returns and maintain customer satisfaction.
3. Color Fastness: Why Should Buyers Care?
Color fastness refers to the ability of a fabric to retain its color when exposed to various conditions, such as washing, light, and friction. High color fastness ratings are essential for maintaining the appearance of apparel over time. Buyers should prioritize suppliers who provide fabrics with strong color fastness to ensure that their products remain vibrant, which is especially important in markets where aesthetics are a key purchasing factor.
4. Breathability: What Role Does It Play in Comfort?
Breathability indicates how well a fabric allows moisture and air to pass through. This property is vital for comfort, particularly in climates that are hot and humid. Fabrics with high breathability can enhance the wearer’s experience, making them more likely to choose these garments repeatedly. Buyers should consider breathability when selecting fabrics for activewear or summer collections.
5. Shrinkage: How Can It Affect Inventory Management?
Shrinkage is the tendency of fabric to decrease in size after washing. Different materials have varying shrinkage rates, which can lead to discrepancies between the advertised and actual sizes of garments. Understanding shrinkage rates is essential for inventory management, as it can impact stock levels and customer returns. Buyers should request shrinkage data from suppliers to make informed decisions about their inventory.
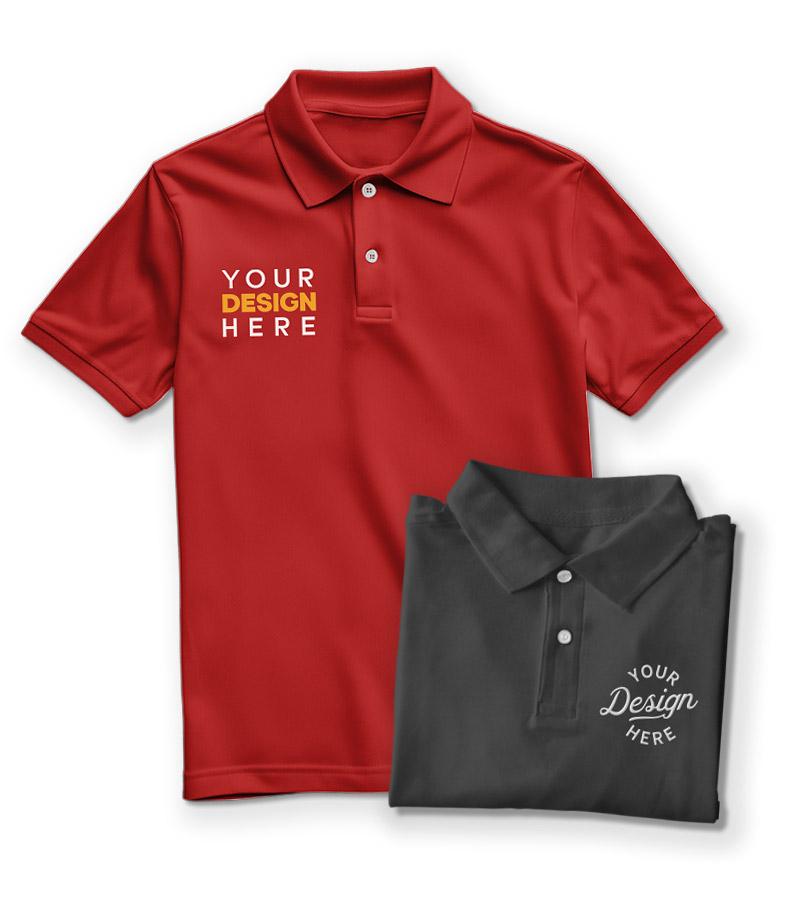
A stock image related to apparel custom.
What Are Common Trade Terms in Apparel Customization?
Familiarity with industry terminology is crucial for effective communication and negotiation in the apparel sector. Here are some common terms B2B buyers should understand.
1. OEM (Original Equipment Manufacturer): What Does It Mean for Your Supply Chain?
OEM refers to companies that produce goods based on the specifications of another brand. For apparel buyers, working with OEMs can offer customization options while leveraging the manufacturer’s expertise. This relationship can lead to cost savings and improved product quality, making it a popular choice for businesses looking to expand their product lines.
2. MOQ (Minimum Order Quantity): How Does It Affect Your Purchasing Strategy?
MOQ indicates the smallest quantity of a product that a supplier is willing to sell. Understanding MOQs is essential for budget planning and inventory management. Buyers should negotiate MOQs that align with their sales forecasts to avoid excess inventory or stockouts.
3. RFQ (Request for Quotation): How Can It Streamline Your Sourcing Process?
An RFQ is a formal request sent to suppliers to obtain pricing and terms for specific products. This process helps buyers compare offerings from different manufacturers, ensuring they secure the best deal. Using RFQs can streamline the sourcing process and facilitate better supplier relationships.
4. Incoterms (International Commercial Terms): Why Are They Important for Global Trade?
Incoterms are standardized trade terms that define the responsibilities of buyers and sellers in international transactions. They clarify who is responsible for shipping, insurance, and tariffs, which is particularly vital for international B2B transactions. Understanding Incoterms can help buyers negotiate better terms and avoid unexpected costs.
By familiarizing themselves with these technical properties and trade terms, international B2B buyers can make more informed decisions in the apparel customization space, ultimately leading to more successful business outcomes.
Navigating Market Dynamics and Sourcing Trends in the apparel custom Sector
What Are the Current Market Dynamics in the Apparel Custom Sector?
The apparel custom sector is experiencing transformative changes driven by globalization, technological advancements, and evolving consumer preferences. International B2B buyers, particularly from Africa, South America, the Middle East, and Europe, should be aware of the following key trends influencing the market landscape.
Firstly, the rise of e-commerce platforms has made it easier for buyers to source custom apparel globally. B2B tech innovations such as AI-driven design tools and automated manufacturing processes are enabling quicker turnaround times and more personalized products. Additionally, the demand for unique and tailored apparel is surging, with buyers increasingly seeking suppliers who can offer customization options that cater to specific demographics and regional tastes.
Another significant driver is the shift towards on-demand manufacturing. This trend not only reduces inventory costs but also allows businesses to respond swiftly to market changes, a crucial factor for international buyers operating in rapidly evolving markets. Moreover, the apparel custom sector is seeing a notable increase in the utilization of data analytics to forecast trends and consumer behavior, providing buyers with insights to make informed sourcing decisions.
How Important Is Sustainability and Ethical Sourcing in B2B Apparel Custom?
Sustainability is no longer just a buzzword; it is a critical factor influencing purchasing decisions in the apparel custom sector. International buyers are increasingly prioritizing suppliers who adhere to ethical sourcing practices and demonstrate a commitment to minimizing environmental impact. This shift is particularly notable in markets such as Europe and the Middle East, where consumers demand transparency in the supply chain.
Buyers should look for suppliers who utilize environmentally friendly materials, such as organic cotton or recycled polyester, as well as those who have obtained certifications like Global Organic Textile Standard (GOTS) or OEKO-TEX. These certifications not only assure buyers of the product’s sustainability but also enhance brand reputation in a competitive marketplace.
Furthermore, adopting ethical sourcing practices can help mitigate risks associated with labor exploitation and environmental degradation. Establishing partnerships with suppliers committed to fair labor practices ensures a more resilient supply chain, which is crucial for maintaining brand integrity and customer loyalty. As sustainability becomes a focal point for consumers, B2B buyers who prioritize these values will likely gain a competitive advantage.
How Has the Apparel Custom Sector Evolved Over Time?
The evolution of the apparel custom sector has been marked by significant technological advancements and shifts in consumer behavior. Historically, custom apparel was often limited to local artisans and small-scale manufacturers. However, the globalization of trade and the advent of digital technologies have transformed this landscape, allowing for a more interconnected and efficient supply chain.
In the past two decades, the integration of technology into the design and production processes has accelerated the customization trend. Innovations such as 3D printing and computer-aided design (CAD) have empowered brands to offer a wider range of personalized options, catering to the diverse preferences of international consumers. This evolution has not only broadened the market but also intensified competition, pushing suppliers to innovate continually and adapt to changing demands.
As the sector continues to evolve, B2B buyers must stay informed about these dynamics and trends to make strategic sourcing decisions that align with their business goals and customer expectations. Understanding the historical context of the apparel custom sector can provide valuable insights into its future trajectory and emerging opportunities.
Frequently Asked Questions (FAQs) for B2B Buyers of apparel custom
-
How do I choose the right supplier for custom apparel?
Selecting the right supplier is crucial for successful custom apparel procurement. Start by researching potential suppliers’ backgrounds, focusing on their experience in your specific apparel category. Request samples to evaluate quality and craftsmanship. Engage in discussions about their production capabilities, lead times, and minimum order quantities (MOQs). Additionally, check for certifications that ensure compliance with international standards, especially if you’re sourcing from regions like Africa or the Middle East. Finally, consider their communication responsiveness and cultural compatibility, as these factors can significantly impact your partnership. -
What are the common minimum order quantities (MOQs) for custom apparel?
MOQs for custom apparel can vary significantly depending on the supplier, the complexity of the design, and the type of materials used. Generally, MOQs range from 50 to 1,000 units. Suppliers often set these limits to ensure cost-effectiveness in production. For B2B buyers from South America or Europe, it’s advisable to negotiate MOQs, especially if you’re testing new designs or entering a new market. Some suppliers may offer lower MOQs for specific items or during promotional periods, so exploring various options can yield favorable terms. -
What customization options are available for apparel?
Customization options for apparel are extensive and can include fabric selection, color choices, logo placement, and garment styles. Many suppliers also offer additional features like embroidery, screen printing, and sublimation printing. To ensure your brand stands out, consider unique embellishments or eco-friendly materials, which are increasingly popular among consumers in Europe and the Middle East. Be clear about your requirements when communicating with suppliers, and ask for design proofs to visualize the final product before proceeding with production. -
What payment terms should I expect when sourcing custom apparel?
Payment terms can differ widely among suppliers. Common practices include a deposit (usually 30-50%) upfront, with the balance due upon completion or before shipping. Ensure you clarify these terms in your contract to avoid misunderstandings. For international transactions, consider using secure payment methods like letters of credit or escrow services, which can protect both parties. Additionally, be aware of currency fluctuations and potential transaction fees when dealing with suppliers from different continents, such as Africa or South America. -
How can I ensure quality assurance in my custom apparel order?
Implementing a robust quality assurance (QA) process is essential when sourcing custom apparel. Start by defining clear quality standards and specifications in your contract. Request pre-production samples to verify materials and craftsmanship before full-scale production begins. Some suppliers may offer third-party QA inspections to assess quality at various production stages. Additionally, establish a communication plan for reporting issues or discrepancies, which can help resolve problems promptly and maintain a good supplier relationship.
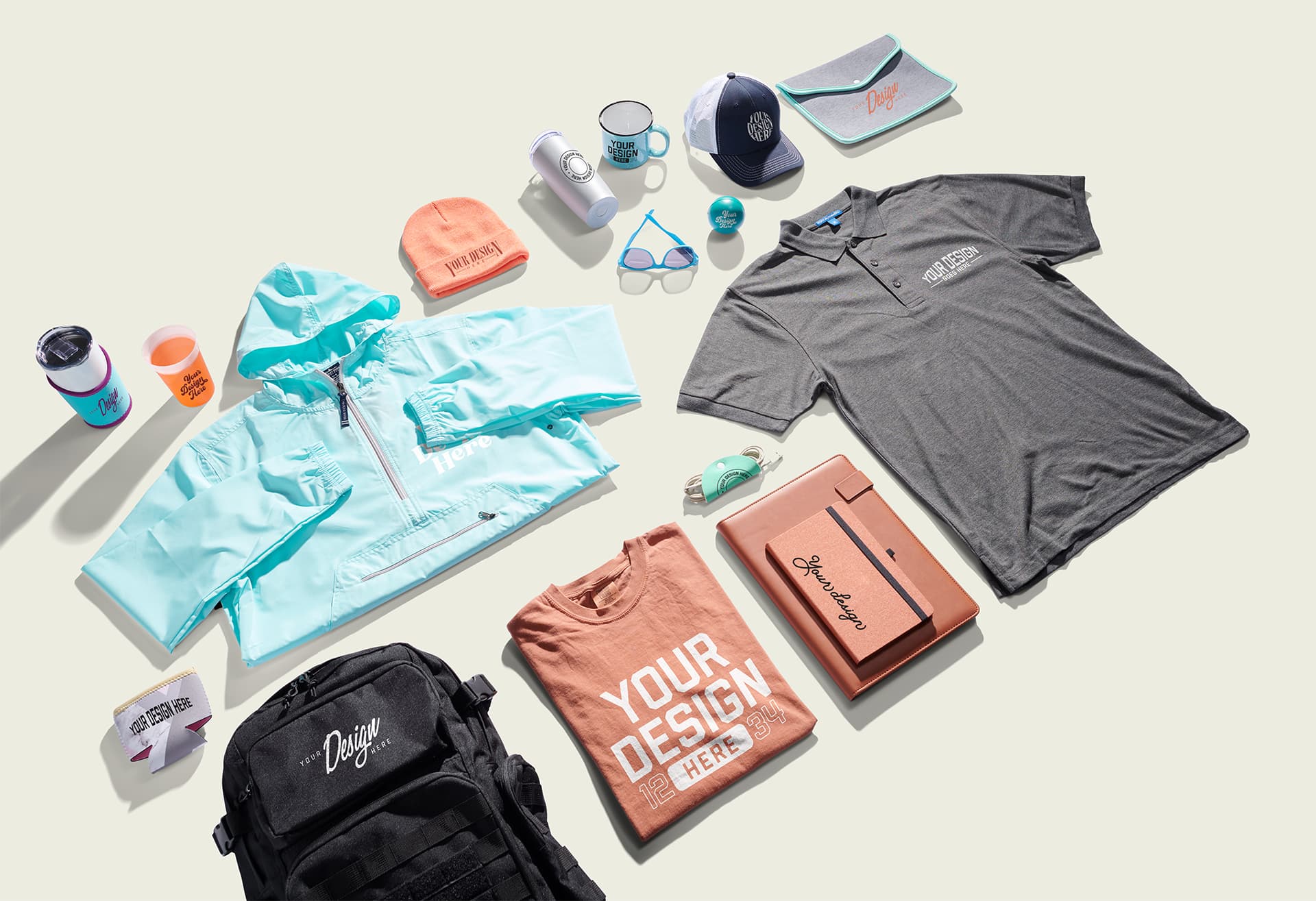
A stock image related to apparel custom.
-
What logistics considerations should I keep in mind for international apparel shipments?
When shipping custom apparel internationally, consider factors such as shipping methods, lead times, and customs regulations. Choose a reliable logistics partner experienced in handling apparel to ensure timely delivery. Understand the import duties and taxes applicable in your country, as these can significantly affect overall costs. For buyers in regions like the Middle East or South America, it’s wise to plan for potential delays caused by customs clearance. Establishing a clear timeline and communication strategy with your supplier can help mitigate these risks. -
What are the best practices for managing supplier relationships in the apparel industry?
Building and maintaining strong supplier relationships is key to successful apparel sourcing. Communicate openly and regularly about expectations, production timelines, and any challenges that arise. Consider scheduling periodic visits to the supplier’s facility to foster trust and understanding. Additionally, provide constructive feedback on quality and service to help them improve. Recognizing their efforts and successes can also strengthen your partnership, leading to better terms and collaboration on future projects. -
How can I adapt my sourcing strategy for different regions like Africa and Europe?
Adapting your sourcing strategy for different regions requires understanding local market dynamics, consumer preferences, and production capabilities. For Africa, consider the benefits of local sourcing, such as reduced shipping costs and shorter lead times. Focus on ethical sourcing and sustainability, which are increasingly important to consumers. In contrast, European buyers may prioritize advanced technology and design innovation. Tailor your approach by conducting market research and building relationships with local suppliers to ensure your strategy aligns with regional trends and demands.
Important Disclaimer & Terms of Use
⚠️ Important Disclaimer
The information provided in this guide, including content regarding manufacturers, technical specifications, and market analysis, is for informational and educational purposes only. It does not constitute professional procurement advice, financial advice, or legal advice.
While we have made every effort to ensure the accuracy and timeliness of the information, we are not responsible for any errors, omissions, or outdated information. Market conditions, company details, and technical standards are subject to change.
B2B buyers must conduct their own independent and thorough due diligence before making any purchasing decisions. This includes contacting suppliers directly, verifying certifications, requesting samples, and seeking professional consultation. The risk of relying on any information in this guide is borne solely by the reader.
Strategic Sourcing Conclusion and Outlook for apparel custom
In today’s competitive landscape, strategic sourcing in the apparel custom industry has become a cornerstone for success. By prioritizing supplier relationships, leveraging technology for improved efficiency, and embracing sustainable practices, international B2B buyers can significantly enhance their procurement processes. Understanding regional dynamics—whether in Africa, South America, the Middle East, or Europe—can provide unique opportunities to tailor sourcing strategies that align with market demands and consumer preferences.
How can B2B buyers leverage data for better sourcing decisions? Utilizing data analytics can help identify trends, manage risks, and optimize inventory. Additionally, fostering collaboration with suppliers ensures transparency and innovation, which are vital in adapting to the ever-evolving apparel landscape.
As we look ahead, the apparel custom sector is poised for growth, driven by digital transformation and shifting consumer behaviors. Now is the time for international buyers to embrace a proactive approach, focusing on strategic sourcing not just as a cost-saving measure, but as a value-adding strategy. Engage with trusted suppliers, explore new markets, and invest in sustainable practices to stay ahead in this dynamic industry. Your next step could redefine your sourcing strategy and lead to substantial business growth.