Ultimate Guide to Finding the Best Truck Supplier (2025)
Introduction: Navigating the Global Market for truck supplier
As the global demand for efficient logistics solutions rises, sourcing reliable truck suppliers has become a critical challenge for B2B buyers, especially in regions like Africa, South America, the Middle East, and Europe. With a myriad of options available, international buyers often struggle to identify suppliers that not only meet their quality standards but also fit their specific operational needs. This comprehensive guide addresses this challenge head-on, providing insights into various types of truck suppliers, their applications, and the essential criteria for supplier vetting.
From understanding the nuances of different truck models to evaluating the cost implications of various suppliers, this guide equips buyers with the knowledge necessary for making informed purchasing decisions. It delves into aspects such as supplier reliability, customer support, and warranty options, which are crucial for maintaining business continuity. By offering actionable insights and practical tips, this resource empowers international B2B buyers to navigate the complexities of the global truck supply market confidently.
Furthermore, we will explore the latest trends impacting the trucking industry, such as sustainability initiatives and technological advancements, helping buyers align their purchasing strategies with future market demands. Whether you are based in Thailand or France, this guide aims to enhance your procurement process and optimize your supply chain efficiency.
Understanding truck supplier Types and Variations
Type Name | Key Distinguishing Features | Primary B2B Applications | Brief Pros & Cons for Buyers |
---|---|---|---|
OEM Truck Suppliers | Manufacturer of original equipment; high quality | Fleet purchases, specialized transport | Pros: Reliability, warranty support. Cons: Higher costs. |
Aftermarket Parts Suppliers | Focus on replacement and enhancement parts; cost-effective | Maintenance and upgrades for existing trucks | Pros: Lower prices, variety. Cons: Quality can vary. |
Used Truck Dealers | Resell pre-owned trucks; varied conditions | Budget-conscious operations, smaller fleets | Pros: Cost savings, immediate availability. Cons: Potential for hidden issues. |
Specialized Truck Builders | Custom-built trucks for specific industries; tailored solutions | Niche markets, specialized logistics | Pros: Customization, efficiency. Cons: Longer lead times, higher initial investment. |
Leasing Companies | Offer trucks on a rental basis; flexible terms | Short-term projects, startups | Pros: Lower upfront costs, flexibility. Cons: Long-term expenses can add up. |
What Are OEM Truck Suppliers and Their B2B Relevance?
OEM (Original Equipment Manufacturer) truck suppliers produce vehicles and parts according to the original specifications set by the manufacturer. They are known for their high quality, reliability, and warranty support. B2B buyers often prefer OEM suppliers for fleet purchases and specialized transport needs due to the assurance of compatibility and performance. However, the premium pricing can be a drawback for businesses operating on tight budgets.
How Do Aftermarket Parts Suppliers Benefit B2B Buyers?
Aftermarket parts suppliers provide a wide range of replacement and enhancement parts that are often more cost-effective than OEM options. These suppliers cater to businesses looking to maintain or upgrade their existing truck fleets without incurring high costs. While they offer a diverse selection, buyers should be cautious as the quality of parts can vary significantly between suppliers, making thorough research essential.
What Should You Know About Used Truck Dealers?
Used truck dealers specialize in reselling pre-owned vehicles, which can be a viable option for budget-conscious operations and smaller fleets. These dealers often provide immediate availability, allowing businesses to acquire trucks without the long wait associated with new purchases. However, buyers must carefully inspect vehicles for potential hidden issues, as the condition can vary widely.
Why Choose Specialized Truck Builders for Your Business?
Specialized truck builders focus on creating custom-built trucks tailored to specific industry needs. This allows businesses in niche markets or specialized logistics to achieve greater efficiency and operational effectiveness. While customization can lead to improved performance, potential buyers should be prepared for longer lead times and a higher initial investment compared to standard models.
How Do Leasing Companies Provide Flexibility to B2B Buyers?
Leasing companies offer trucks on a rental basis, providing flexibility for short-term projects or businesses just starting. This approach allows companies to lower their upfront costs and access newer models without the commitment of a purchase. However, buyers should consider that long-term leasing can lead to higher overall expenses, which may outweigh the initial savings.
Related Video: Belt Drive | Types of Belt Drives
Key Industrial Applications of truck supplier
Industry/Sector | Specific Application of Truck Supplier | Value/Benefit for the Business | Key Sourcing Considerations for this Application |
---|---|---|---|
Logistics & Transportation | Fleet Management and Delivery Solutions | Enhanced efficiency in logistics operations, reduced delivery times | Reliability of parts, compatibility with existing fleet, service support availability |
Construction | Heavy Equipment Transport | Safeguards timely project completion through reliable transport of materials | Load capacity, durability under harsh conditions, regulatory compliance |
Agriculture | Crop Transport and Distribution | Ensures timely delivery of produce, minimizing spoilage and maximizing profit | Adaptability to various terrains, fuel efficiency, maintenance support |
Mining | Mineral and Resource Hauling | Increases productivity by ensuring efficient transport of mined materials | Robustness for rough terrains, safety features, and after-sales service |
Waste Management | Waste Collection and Transportation | Promotes environmental sustainability through efficient waste removal | Compliance with environmental regulations, vehicle capacity, and serviceability |
How Are Trucks Used in the Logistics & Transportation Sector?
In the logistics and transportation sector, truck suppliers play a critical role in fleet management and delivery solutions. Trucks are essential for transporting goods across vast distances, ensuring that products reach their destinations on time. This sector often requires suppliers to provide reliable and efficient vehicles that can handle varying loads and road conditions. For international buyers, particularly from regions like Africa and South America, sourcing trucks that are durable and capable of navigating less developed infrastructure is paramount. Additionally, they should consider suppliers that offer comprehensive service support to minimize downtime.
What Role Do Trucks Play in Construction Applications?
In the construction industry, trucks are indispensable for heavy equipment transport. They facilitate the movement of essential materials such as concrete, steel, and machinery to job sites. A reliable truck supplier ensures that construction projects are completed on schedule by providing vehicles that can withstand heavy loads and rough terrains. For B2B buyers in Europe and the Middle East, it is essential to assess the load capacity and durability of trucks, as well as their compliance with local regulations to avoid costly delays.
How Are Trucks Utilized in Agriculture?
In agriculture, trucks are vital for crop transport and distribution. They ensure the timely delivery of produce from farms to markets, which is crucial for minimizing spoilage and maximizing profits. International buyers should look for truck suppliers that offer vehicles equipped for diverse agricultural needs, such as temperature control for perishable goods. Additionally, adaptability to various terrains and fuel efficiency are significant considerations, especially in regions with challenging road conditions.
What Are the Trucking Needs in the Mining Sector?
The mining industry relies heavily on trucks for mineral and resource hauling. These vehicles must be robust enough to transport heavy and often hazardous materials from remote locations. The efficiency of operations is directly tied to the reliability of the trucks used. For B2B buyers in Africa and the Middle East, sourcing trucks with enhanced safety features and after-sales service is crucial, as it ensures compliance with industry regulations and minimizes operational risks.
How Do Trucks Support Waste Management Efforts?
In waste management, trucks are essential for waste collection and transportation. They contribute to environmental sustainability by promoting efficient waste removal processes. Buyers in Europe, where environmental regulations are stringent, must ensure that the trucks sourced comply with these regulations. Key considerations include vehicle capacity, serviceability, and the ability to handle different types of waste, ensuring that waste management operations run smoothly and efficiently.
Related Video: Types Of Flowmeters And Their Industrial Applications.
3 Common User Pain Points for ‘truck supplier’ & Their Solutions
Scenario 1: Difficulty in Finding Quality Parts and Components
The Problem: Many international B2B buyers struggle to find reliable truck suppliers who can provide high-quality parts and components that meet their specific needs. This is particularly challenging in regions such as Africa and South America, where local supply chains may not be as robust, leading to longer lead times and increased costs. Buyers often face uncertainty regarding the quality of parts, which can impact vehicle performance and increase maintenance costs.
The Solution: To overcome this challenge, buyers should prioritize suppliers that offer comprehensive product catalogs along with detailed specifications and certifications. Conducting thorough research on potential suppliers, including reading customer reviews and case studies, can provide insights into their reliability and quality standards. Additionally, establishing relationships with suppliers who have a proven track record in the industry can facilitate better sourcing options. It’s also advisable to request samples or smaller orders initially to evaluate the quality before committing to larger purchases. Leveraging technology, such as digital marketplaces that specialize in truck parts, can also streamline the procurement process and provide access to a wider range of suppliers.
Scenario 2: Navigating Complex Regulations and Compliance Issues
The Problem: B2B buyers often encounter complex regulations and compliance requirements when sourcing trucks and parts, particularly when dealing with international suppliers. For example, buyers from the Middle East and Europe may need to adhere to specific environmental standards or safety regulations that vary significantly from one country to another. This complexity can lead to delays, fines, or even the rejection of shipments, causing significant disruptions in operations.
The Solution: To navigate these complexities, buyers should invest time in understanding the regulatory environment of both their home country and the supplier’s country. Engaging with a compliance consultant or utilizing legal expertise can provide valuable guidance on necessary documentation, certifications, and standards. It’s essential to communicate these requirements clearly with potential suppliers during the negotiation process. Additionally, establishing a partnership with suppliers who are experienced in international trade can simplify compliance. They can often assist with the necessary paperwork and ensure that all products meet the required standards, reducing the risk of costly delays.
Scenario 3: Managing Supply Chain Disruptions and Delays
The Problem: Supply chain disruptions are a common pain point for B2B buyers, especially when sourcing from international truck suppliers. Factors such as political instability, natural disasters, or even global pandemics can lead to unexpected delays in delivery, causing operational setbacks and affecting customer satisfaction. Buyers may find themselves in situations where their trucks are immobilized due to a lack of essential parts, which can severely impact their business operations.
The Solution: To mitigate the risk of supply chain disruptions, buyers should adopt a proactive approach by diversifying their supplier base. Working with multiple suppliers across different regions can provide alternative options in the event of delays. Additionally, implementing a just-in-time inventory strategy can help manage stock levels more effectively, ensuring that essential parts are always available without overstocking. Regular communication with suppliers regarding their production capabilities and potential issues can also help buyers stay informed and plan accordingly. Finally, investing in supply chain management software can provide real-time insights into inventory levels, shipment statuses, and potential bottlenecks, allowing for quicker decision-making and adaptation to changing circumstances.
Strategic Material Selection Guide for truck supplier
What Are the Key Properties of Common Materials Used in Truck Supply?
When selecting materials for truck components, understanding the key properties of each material is essential for ensuring optimal performance. Common materials used in truck manufacturing include steel, aluminum, composite materials, and rubber. Each material has distinct properties that affect durability, weight, cost, and suitability for specific applications.
How Does Steel Compare as a Material for Truck Components?
Steel is widely recognized for its strength and durability. It typically has high tensile strength, making it suitable for applications where structural integrity is paramount. Steel components can withstand high temperatures and pressures, which is critical in heavy-duty truck applications.
Pros: Steel’s durability and cost-effectiveness make it a popular choice for truck frames, axles, and other structural components. It is easily sourced globally, making it accessible for international buyers.
Cons: However, steel is heavy, which can impact fuel efficiency. It is also susceptible to corrosion if not properly treated, requiring additional coatings or treatments, which can increase manufacturing complexity.
Impact on Application: Steel is compatible with various media, including oils and fuels, but its corrosion resistance must be considered in humid or saline environments.
What Are the Advantages of Using Aluminum in Truck Manufacturing?
Aluminum is increasingly favored for its lightweight properties, which can enhance fuel efficiency and payload capacity. It has good corrosion resistance and can handle moderate temperatures and pressures.
Pros: The primary advantage of aluminum is its weight reduction, which is beneficial for long-haul trucking. Its natural resistance to corrosion reduces maintenance costs over time.
Cons: The main disadvantage is its higher cost compared to steel, which can be a critical factor for budget-conscious buyers. Additionally, aluminum is not as strong as steel, which may limit its use in certain structural applications.
Impact on Application: Aluminum is suitable for components exposed to moisture, such as body panels and fuel tanks, but may not be ideal for high-stress applications without reinforcement.
How Do Composite Materials Enhance Truck Component Performance?
Composite materials, often made from a combination of fibers and resins, are gaining traction in truck manufacturing due to their high strength-to-weight ratio and excellent fatigue resistance.
Pros: Composites are lightweight and can be tailored for specific applications, offering versatility in design. They are resistant to corrosion and can withstand extreme temperatures, making them suitable for various environments.
Cons: The primary limitation is their cost, as composites can be significantly more expensive than traditional materials. Additionally, the manufacturing processes for composites can be complex, requiring specialized equipment and expertise.
Impact on Application: Composites are ideal for components that require both strength and lightness, such as aerodynamic body parts, but may not be suitable for load-bearing applications without careful engineering.
What Role Does Rubber Play in Truck Component Design?
Rubber is essential for various truck components, particularly those requiring flexibility and shock absorption, such as tires, seals, and suspension parts.
Pros: Rubber provides excellent resilience and can handle a wide range of temperatures. It is also effective in reducing vibrations, enhancing driver comfort and vehicle longevity.
Cons: However, rubber can degrade over time, particularly when exposed to UV light and extreme temperatures. It may also require more frequent replacement compared to metal components.
Impact on Application: Rubber is compatible with a variety of media, including oils and fuels, but its lifespan can be affected by environmental factors, making it crucial for buyers to consider operating conditions.
Summary Table of Material Selection for Truck Components
Material | Typical Use Case for Truck Supplier | Key Advantage | Key Disadvantage/Limitation | Relative Cost (Low/Med/High) |
---|---|---|---|---|
Steel | Truck frames and axles | High strength and durability | Heavy and prone to corrosion | Medium |
Aluminum | Body panels and fuel tanks | Lightweight and corrosion-resistant | Higher cost and lower strength | High |
Composite | Aerodynamic body parts | High strength-to-weight ratio | Expensive and complex to manufacture | High |
Rubber | Tires and suspension components | Excellent shock absorption and flexibility | Degrades over time | Low |
This strategic material selection guide provides actionable insights for international B2B buyers, helping them make informed decisions based on material properties, advantages, limitations, and application suitability. Understanding these factors is crucial for optimizing the performance and longevity of truck components in diverse operating environments.
In-depth Look: Manufacturing Processes and Quality Assurance for truck supplier
What Are the Main Stages in the Manufacturing Process for Truck Suppliers?
The manufacturing process for truck suppliers is a multi-stage operation that involves various techniques to ensure the production of high-quality vehicles. Understanding these stages can help international B2B buyers make informed decisions when selecting suppliers.
1. Material Preparation: Sourcing and Selection
The first stage in manufacturing trucks involves sourcing and selecting high-quality raw materials. Common materials include steel, aluminum, and composites, each chosen for their specific properties like strength, weight, and corrosion resistance. Suppliers often collaborate with certified vendors to ensure that materials meet international standards, such as ISO 9001, which governs quality management systems.
2. Forming: Shaping the Components
Once materials are prepared, the next step is forming. This stage includes processes like stamping, bending, and welding to create essential components such as the chassis, body panels, and structural elements. Advanced techniques, such as laser cutting and robotic welding, are increasingly employed to enhance precision and reduce manufacturing time. B2B buyers should inquire about the technologies used in this stage, as they can significantly affect the durability and performance of the final product.
3. Assembly: Integrating Components
The assembly stage involves the integration of various components into a complete truck. This process can be manual or automated, depending on the supplier’s capabilities. Automated assembly lines are often more efficient and can lead to a reduction in human error. During this phase, suppliers typically implement lean manufacturing principles to minimize waste and optimize resource use. Buyers should assess a supplier’s assembly methods to ensure they align with industry best practices.
4. Finishing: Ensuring Quality and Aesthetics
The finishing stage encompasses painting, coating, and surface treatments that enhance both the aesthetic appeal and longevity of the truck. This can include anti-corrosion treatments and the application of protective coatings. Quality assurance checks are essential in this phase to ensure that the final product meets both functional and aesthetic criteria. Buyers should verify that suppliers use environmentally friendly finishing processes to comply with regulations in their respective markets.
How Is Quality Assurance Implemented in Truck Manufacturing?
Quality assurance (QA) is a critical component of the manufacturing process, ensuring that products meet specified requirements and standards. For international B2B buyers, understanding these QA measures can provide confidence in their supplier’s reliability.
1. What International Standards Should Buyers Be Aware Of?
International standards such as ISO 9001 play a significant role in quality management. This standard ensures that organizations consistently provide products that meet customer and regulatory requirements. In addition to ISO standards, industry-specific certifications such as CE (Conformité Européenne) for European markets or API (American Petroleum Institute) for specific components are crucial. Buyers from Africa, South America, the Middle East, and Europe should ensure their suppliers hold relevant certifications to guarantee compliance with local laws and international trade regulations.
2. What Are the Key Quality Control Checkpoints?
Quality control (QC) involves several checkpoints throughout the manufacturing process:
-
Incoming Quality Control (IQC): This step involves inspecting raw materials upon arrival to ensure they meet specified standards before production begins.
-
In-Process Quality Control (IPQC): During the manufacturing process, continuous monitoring is conducted to catch defects early. This includes checks on dimensions, tolerances, and assembly quality.
-
Final Quality Control (FQC): Once the truck is assembled, it undergoes a final inspection to verify that all systems function correctly and that the product meets customer specifications.
3. What Common Testing Methods Are Used?
Various testing methods are implemented to ensure quality, including:
- Functional Testing: Evaluates the performance of critical systems, such as brakes and engine efficiency.
- Durability Testing: Simulates real-world conditions to assess the truck’s ability to withstand stress and wear over time.
- Safety Testing: Ensures compliance with safety regulations and standards to protect drivers and cargo.
How Can B2B Buyers Verify Supplier Quality Control?
For international buyers, verifying the quality control processes of suppliers is vital to ensure they are making sound investments. Here are actionable strategies:
1. Conducting Supplier Audits
Regular audits can provide insights into a supplier’s manufacturing and quality assurance processes. Buyers should request access to audit reports, which should outline compliance with international standards and any areas needing improvement.
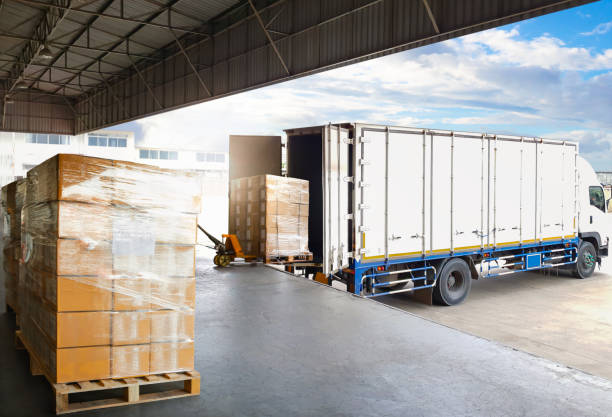
A stock image related to truck supplier.
2. Requesting Quality Assurance Reports
Suppliers should provide documentation detailing their QC processes, including test results and inspection reports. This transparency allows buyers to assess the reliability of the supplier’s quality measures.
3. Engaging Third-Party Inspection Services
Utilizing third-party inspection services can offer an unbiased evaluation of the supplier’s manufacturing processes and product quality. These services can conduct on-site inspections and provide detailed reports, which are invaluable for making informed purchasing decisions.
What Are the Quality Control Nuances for International B2B Buyers?
When dealing with suppliers from different regions, it’s essential to consider cultural and regulatory differences that may impact quality control:
-
Cultural Differences: Understanding the local business culture can help buyers communicate effectively about quality expectations and standards.
-
Regulatory Compliance: Different countries may have varying regulations concerning manufacturing and safety standards. Buyers must ensure that their suppliers comply with both local and international regulations.
-
Supply Chain Management: For buyers in Africa, South America, the Middle East, and Europe, managing a supply chain across borders can introduce complexities. Building relationships with suppliers that understand the local regulations and practices is crucial for ensuring consistent quality.
In conclusion, understanding the manufacturing processes and quality assurance practices of truck suppliers is essential for international B2B buyers. By being informed about these elements, buyers can make better decisions, ensuring that they partner with reliable suppliers who can meet their specific needs.
Practical Sourcing Guide: A Step-by-Step Checklist for ‘truck supplier’
In the competitive landscape of international truck procurement, having a structured approach to sourcing suppliers is essential. This checklist is designed to guide B2B buyers, particularly from Africa, South America, the Middle East, and Europe, through the critical steps in selecting a reliable truck supplier. Following these steps will help ensure that you make informed decisions that align with your business needs.
Step 1: Define Your Technical Specifications
Before you begin the sourcing process, it’s crucial to clarify your technical requirements. This includes determining the type of trucks you need, their capacities, and any specific features necessary for your operations.
– Considerations:
– Load capacity and engine specifications.
– Compliance with local regulations regarding emissions and safety.
Step 2: Research Potential Suppliers
Conduct thorough research to identify potential suppliers. This can be done through online platforms, industry trade shows, and networking within industry associations.
– Look for:
– Supplier experience in your specific market.
– Reviews and testimonials from previous clients.
Step 3: Evaluate Supplier Certifications
Verifying supplier certifications is critical to ensuring compliance with industry standards. This may include ISO certifications, safety standards, and environmental compliance.
– Key Points:
– Check if the supplier has relevant certifications from recognized bodies.
– Understand how these certifications impact product quality and operational safety.
Step 4: Request Quotes and Compare Pricing
Once you’ve shortlisted potential suppliers, request detailed quotes. Ensure that these quotes include not only the price but also terms of delivery, warranties, and after-sales support.
– Important Aspects:
– Look for transparency in pricing to avoid hidden costs.
– Compare quotes based on total cost of ownership, not just upfront costs.
Step 5: Conduct Site Visits
If feasible, visiting the supplier’s facilities can provide invaluable insights. This allows you to assess their production capabilities, quality control processes, and overall operational efficiency.
– What to Observe:
– The condition of equipment and facilities.
– The professionalism and expertise of the staff.
Step 6: Check References and Client Feedback
Before making a final decision, reach out to previous clients of the supplier. This can give you an understanding of the supplier’s reliability, product quality, and customer service.
– Questions to Ask:
– How satisfied were they with the product and service?
– Were there any issues during the procurement process?
Step 7: Negotiate Terms and Finalize the Contract
After selecting a supplier, it’s time to negotiate the terms. Ensure that the contract covers delivery timelines, payment terms, warranties, and service agreements.
– Key Considerations:
– Be clear about penalties for non-compliance.
– Ensure that all agreements are documented to avoid misunderstandings.
By following this checklist, B2B buyers can systematically approach the sourcing of truck suppliers, minimizing risks and enhancing the likelihood of a successful procurement process.
Comprehensive Cost and Pricing Analysis for truck supplier Sourcing
What Are the Key Cost Components in Truck Supplier Sourcing?
When sourcing trucks from suppliers, understanding the cost structure is essential for making informed purchasing decisions. The primary cost components include:
-
Materials: The quality and type of materials used, such as steel and composites, can significantly affect pricing. Higher-quality materials typically lead to increased durability and performance but come at a higher cost.
-
Labor: Labor costs vary based on geographical location, skill levels, and local labor laws. For instance, sourcing from regions with lower labor costs can reduce overall expenses but may impact quality and delivery times.
-
Manufacturing Overhead: This encompasses utilities, rent, and equipment depreciation. Efficient manufacturing processes can help minimize these costs, leading to better pricing for buyers.
-
Tooling: Initial tooling costs for custom parts can be substantial. Buyers should inquire about these costs upfront, especially if they require specialized components.
-
Quality Control (QC): Ensuring that products meet specified standards involves additional costs. Robust QC processes may increase upfront costs but can save money in the long run by reducing defects and returns.
-
Logistics: Transportation costs are a critical factor, particularly for international buyers. These costs can fluctuate based on fuel prices, shipping methods, and distances.
-
Margin: Suppliers typically add a markup to cover their costs and profits. Understanding the supplier’s margin can provide insights into pricing flexibility during negotiations.
How Do Price Influencers Affect Truck Supplier Pricing?
Several factors can influence the final pricing of trucks, including:
-
Volume/MOQ (Minimum Order Quantity): Higher order volumes often lead to lower per-unit costs. Buyers should evaluate their needs and consider bulk purchasing to maximize savings.
-
Specifications and Customization: Customized trucks with specific features or modifications can lead to higher prices. Clearly defining requirements upfront can help avoid unexpected costs.
-
Materials and Quality Certifications: Trucks built with premium materials or those that meet specific industry certifications may carry higher costs. Buyers should assess whether these features align with their operational needs.
-
Supplier Factors: Supplier reliability, reputation, and experience can impact pricing. Working with established suppliers may offer better support and quality assurance but could come at a premium.
-
Incoterms: The chosen Incoterms (International Commercial Terms) can greatly influence total costs by determining who is responsible for shipping, insurance, and customs. Buyers should choose terms that align with their logistics capabilities and cost considerations.
What Are the Best Buyer Tips for Cost Efficiency in Truck Sourcing?
To ensure cost efficiency when sourcing trucks, consider the following tips:
-
Negotiate: Always engage in negotiations. Understanding the cost structure allows buyers to identify areas where suppliers may have flexibility, especially on margins or logistics.
-
Evaluate Total Cost of Ownership (TCO): Look beyond the initial purchase price. TCO includes maintenance, fuel consumption, and potential downtime. This holistic approach can lead to better long-term investments.
-
Understand Pricing Nuances for International Transactions: Currency fluctuations, import duties, and taxes can significantly affect overall costs. Buyers from Africa, South America, the Middle East, and Europe should factor these elements into their pricing strategies.
-
Research Market Trends: Keeping abreast of market trends in truck prices can provide leverage during negotiations. Understanding seasonal fluctuations and demand cycles can help in timing purchases for optimal pricing.
-
Leverage Technology: Utilize online platforms and tools that provide pricing transparency and comparative analysis. This can help identify competitive pricing and supplier options.
Conclusion
Understanding the comprehensive cost and pricing analysis of truck supplier sourcing is crucial for international B2B buyers. By considering the outlined cost components and price influencers, and applying strategic negotiation and evaluation techniques, buyers can make informed decisions that align with their budget and operational needs. Always remember to seek multiple quotes and be aware of the total cost of ownership to ensure the best value for your investment.
Alternatives Analysis: Comparing truck supplier With Other Solutions
Understanding Alternative Solutions to Truck Suppliers
In the dynamic landscape of logistics and transportation, B2B buyers must explore various solutions beyond traditional truck suppliers. This section highlights viable alternatives that can meet transportation needs efficiently while considering factors such as performance, cost, and maintenance.
Comparison Table of Truck Supplier and Alternatives
Comparison Aspect | Truck Supplier | Alternative 1: Freight Brokerage | Alternative 2: Rail Freight |
---|---|---|---|
Performance | High load capacity; reliable delivery | Flexible routing; access to multiple carriers | Efficient for long distances; lower carbon footprint |
Cost | Higher initial investment; ongoing maintenance costs | Variable costs; often lower than direct trucking | Competitive for bulk shipments; lower per ton cost |
Ease of Implementation | Requires significant setup and training | Easy to engage; less overhead | Requires knowledge of rail logistics; limited access points |
Maintenance | Regular upkeep required; can be costly | Minimal maintenance; reliant on third-party carriers | Low maintenance; infrastructure managed by rail companies |
Best Use Case | Local and regional deliveries; urgent shipments | Short-term projects; diverse shipping needs | Bulk goods over long distances; environmentally conscious clients |
What Are the Pros and Cons of Using Freight Brokerage?
Freight brokerage serves as an intermediary between shippers and carriers, providing flexibility and a broad range of shipping options.
Pros:
– Cost Efficiency: Often more economical than maintaining a fleet, as brokers can negotiate better rates with various carriers.
– Flexibility: Brokers can quickly adapt to changing shipping needs and find suitable carriers for specific routes or cargo types.
Cons:
– Variable Costs: Costs can fluctuate based on market conditions, which may lead to unpredictable budgeting.
– Less Control: Companies may have less oversight over the shipping process, potentially affecting service quality.
How Does Rail Freight Compare to Truck Suppliers?
Rail freight involves transporting goods via train, which is particularly effective for bulk shipments over long distances.
Pros:
– Cost-Effectiveness for Bulk: Lower costs per ton make rail an attractive option for large shipments.
– Environmental Benefits: Rail transport is generally more fuel-efficient, reducing the carbon footprint of shipping operations.
Cons:
– Limited Accessibility: Rail transport may not be suitable for all locations, requiring additional logistics to move goods from rail stations to final destinations.
– Slower Transit Times: While efficient for bulk, rail can be slower than trucks, particularly for time-sensitive deliveries.
How Can B2B Buyers Choose the Right Solution?
Selecting the right transportation solution hinges on understanding specific business needs. Buyers should consider the nature of their goods, delivery timelines, and budget constraints. If the requirement involves transporting bulk goods over long distances, rail freight may be the most cost-effective and environmentally friendly option. Conversely, for urgent or localized deliveries, a truck supplier or freight brokerage may provide the necessary flexibility and reliability. Ultimately, a thorough assessment of each alternative’s pros and cons will empower buyers to make informed decisions that align with their operational goals.
Essential Technical Properties and Trade Terminology for truck supplier
What Are the Key Technical Properties for Truck Suppliers?
When sourcing trucks or truck parts, understanding critical technical specifications is essential for making informed purchasing decisions. Here are several key properties to consider:
1. Material Grade
Material grade refers to the type and quality of materials used in the construction of truck components. Common materials include steel, aluminum, and composite materials. Each material grade has specific properties such as strength, weight, and corrosion resistance, which can significantly affect the truck’s durability and performance. For B2B buyers, selecting the right material grade ensures the truck can withstand operational demands, especially in harsh environments common in regions like Africa and South America.
2. Tolerance
Tolerance defines the allowable variation in a part’s dimensions. In truck manufacturing, maintaining strict tolerances is crucial for ensuring that components fit together correctly and operate efficiently. Loose tolerances can lead to mechanical failures, increased wear, and safety hazards. Understanding tolerance requirements helps buyers ensure that parts meet specific performance standards, reducing the risk of costly repairs and downtime.
3. Weight Capacity
Weight capacity indicates the maximum load a truck can safely carry. This specification is vital for buyers in logistics and transportation, as it directly impacts operational efficiency and compliance with local regulations. Understanding the weight capacity allows B2B buyers to choose trucks that meet their logistical needs without risking overloading, which can lead to fines and damage.
4. Engine Specifications
Engine specifications include details such as horsepower, torque, and fuel efficiency. These factors determine the truck’s performance, including its ability to handle various terrains and loads. B2B buyers should consider engine specifications that align with their operational requirements, ensuring that the trucks purchased can operate efficiently while minimizing fuel costs.
5. Safety Features
Safety features encompass a range of technologies and systems designed to enhance the protection of the driver and cargo. Common safety features include anti-lock braking systems (ABS), stability control, and advanced driver-assistance systems (ADAS). Buyers should prioritize safety specifications, particularly in regions with challenging driving conditions, to protect their investments and comply with safety regulations.
What Are Common Trade Terms in the Truck Supply Industry?
Understanding industry jargon is crucial for effective communication and negotiation in the B2B truck supply market. Here are several common terms:
1. OEM (Original Equipment Manufacturer)
OEM refers to companies that produce parts or equipment that may be marketed by another manufacturer. In the truck supply context, OEM parts are often preferred for their quality and compatibility. Buyers should understand whether the parts they are purchasing are OEM or aftermarket, as this can affect warranty and performance.
2. MOQ (Minimum Order Quantity)
MOQ is the minimum quantity of goods a supplier is willing to sell. For B2B buyers, understanding MOQ is essential for budgeting and inventory management. Suppliers may set high MOQs to justify production costs, which can impact smaller buyers or those testing new products.
3. RFQ (Request for Quotation)
An RFQ is a document sent to suppliers requesting a price quote for specified products or services. This process is crucial for B2B buyers to compare prices and terms from different suppliers, ensuring they secure the best deal. Including detailed specifications in an RFQ can lead to more accurate and competitive quotes.
4. Incoterms (International Commercial Terms)
Incoterms are a set of international rules that define the responsibilities of buyers and sellers in international transactions. These terms clarify aspects such as shipping costs, insurance, and delivery points. For B2B buyers, understanding Incoterms is essential to avoid misunderstandings and ensure smooth logistics across borders.
5. Lead Time
Lead time refers to the amount of time it takes from placing an order to receiving the goods. In the truck supply industry, lead time can significantly impact operations, especially for businesses relying on timely deliveries. Buyers should always inquire about lead times to plan their operations effectively and avoid disruptions.
In summary, being knowledgeable about these technical properties and trade terms empowers B2B buyers to make informed decisions when sourcing trucks and parts, ultimately leading to enhanced operational efficiency and cost savings.
Navigating Market Dynamics and Sourcing Trends in the truck supplier Sector
What Are the Key Market Dynamics and Sourcing Trends in the Truck Supplier Sector?
The truck supplier sector is witnessing significant transformations driven by globalization, technological advancements, and changing consumer demands. International B2B buyers, particularly from regions like Africa, South America, the Middle East, and Europe, must stay attuned to these dynamics to make informed sourcing decisions. One of the primary global drivers is the increasing demand for logistics and transportation solutions, spurred by e-commerce growth and supply chain complexities. This trend is pushing suppliers to innovate, offering advanced products that integrate digital technologies such as IoT and telematics, enabling real-time tracking and fleet management.
Current sourcing trends emphasize the importance of agility and flexibility. Suppliers are increasingly adopting just-in-time (JIT) strategies to minimize inventory costs and meet fluctuating demands. Additionally, the rise of e-procurement platforms is streamlining the purchasing process, allowing buyers to access a wider range of suppliers and products from different geographies. This is particularly beneficial for buyers in emerging markets, where local suppliers may not always meet the required standards or availability.
Emerging technologies such as artificial intelligence and machine learning are also reshaping the sector. These technologies facilitate predictive analytics, enhancing demand forecasting and inventory management. For B2B buyers, leveraging data-driven insights can lead to more strategic sourcing decisions, optimizing costs, and improving supplier relationships.
How Is Sustainability Influencing Sourcing Decisions in the Truck Supplier Sector?
Sustainability is becoming a pivotal factor in the sourcing strategies of B2B buyers in the truck supplier sector. Environmental concerns are driving a shift towards ethical sourcing practices and sustainable materials. Buyers are increasingly prioritizing suppliers that demonstrate a commitment to reducing their environmental impact, whether through energy-efficient manufacturing processes or by using recycled materials.
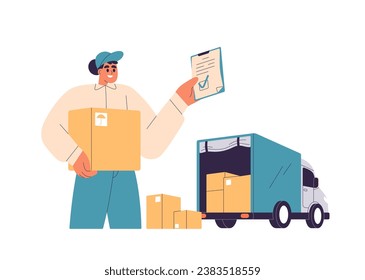
A stock image related to truck supplier.
The importance of ethical supply chains cannot be overstated. Buyers are now more vigilant about the social and ethical implications of their sourcing decisions. This includes ensuring fair labor practices and transparency throughout the supply chain. Certifications such as ISO 14001 for environmental management and Fair Trade accreditation are gaining traction, providing buyers with assurance that their suppliers adhere to recognized sustainability standards.
Moreover, the trend towards ‘green’ certifications and materials is reshaping product offerings in the truck supplier market. Buyers should look for suppliers who not only comply with environmental regulations but also invest in innovative solutions that reduce carbon footprints, such as lightweight materials that enhance fuel efficiency. This alignment with sustainability goals not only mitigates risks but also enhances brand reputation and customer loyalty.
What Is the Historical Context of Sourcing in the Truck Supplier Sector?
The truck supplier sector has evolved significantly over the decades, shaped by technological advancements and changing market demands. Initially dominated by a few key players, the sector has expanded with the advent of globalization, allowing international suppliers to enter local markets. This evolution has led to increased competition, driving innovation and efficiency across the industry.
In the early stages, sourcing was primarily focused on cost-efficiency, often at the expense of quality and sustainability. However, as global awareness of environmental issues grew, the sector began shifting towards more sustainable practices. Today, B2B buyers must navigate a complex landscape that balances cost, quality, and sustainability—factors that are now integral to successful sourcing strategies in the truck supplier sector.
Understanding this historical context allows international buyers to appreciate the current dynamics and trends, equipping them to make informed decisions that align with both their operational needs and corporate social responsibility objectives.
Frequently Asked Questions (FAQs) for B2B Buyers of truck supplier
-
How do I evaluate the credibility of a truck supplier?
To evaluate a truck supplier’s credibility, start by researching their history and reputation in the industry. Look for customer reviews, testimonials, and case studies that highlight their reliability and service quality. Verify their certifications and compliance with international standards. Additionally, consider requesting references from other businesses that have worked with them. Engaging in direct communication can also provide insights into their responsiveness and customer support. -
What is the best way to negotiate payment terms with a truck supplier?
Negotiating payment terms requires a clear understanding of both parties’ needs. Start by discussing options such as letters of credit, advance payments, or net payment terms (e.g., net 30 or net 60 days). Be transparent about your cash flow constraints while expressing your commitment to a long-term relationship. Additionally, consider including incentives for early payments or penalties for late payments to create a mutually beneficial agreement. -
What are the minimum order quantities (MOQ) I should expect from truck suppliers?
Minimum order quantities (MOQ) can vary significantly depending on the supplier and the specific truck models or parts you’re sourcing. Typically, larger suppliers may have higher MOQs, while smaller or specialized suppliers may offer more flexible terms. It’s advisable to inquire about MOQs upfront and discuss your needs, as some suppliers may be willing to negotiate smaller orders, especially for first-time clients or bulk purchases over time. -
How can I ensure quality assurance when sourcing trucks internationally?
To ensure quality assurance, implement a multi-step process that includes supplier audits, factory visits, and third-party inspections. Request documentation of quality control processes and certifications, such as ISO standards. Additionally, consider starting with a smaller test order to evaluate the quality before committing to larger purchases. Establish clear specifications and performance standards in your contracts to hold suppliers accountable. -
What are the logistics considerations when importing trucks from abroad?
Logistics plays a crucial role in importing trucks. Consider factors such as shipping methods (e.g., container shipping or roll-on/roll-off), customs clearance procedures, and potential tariffs or duties in your country. Collaborate with experienced freight forwarders who can guide you through the process and help with documentation. Additionally, ensure that you have a clear understanding of delivery timelines and any potential delays that may arise during transit. -
How do I customize trucks according to my specific business needs?
Customizing trucks involves collaborating closely with your supplier to understand available options for modifications. Discuss your specific requirements, such as cargo capacity, engine specifications, or specialized features. Many suppliers offer customization services, but it’s important to confirm lead times and costs associated with these modifications. Ensure that all customization details are documented in your agreement to avoid misunderstandings later. -
What should I consider when assessing the total cost of ownership (TCO) for trucks?
When assessing the total cost of ownership (TCO) for trucks, consider not just the purchase price but also ongoing costs such as fuel consumption, maintenance, insurance, and depreciation. Evaluate the truck’s fuel efficiency and reliability, as these factors will significantly impact long-term expenses. Additionally, consider the potential resale value of the truck when calculating the overall investment. -
How do international trade regulations affect my truck sourcing?
International trade regulations can significantly impact your truck sourcing strategy. It’s essential to be aware of import/export restrictions, tariffs, and compliance requirements specific to your region. Research trade agreements between your country and the supplier’s country, as these may provide reduced tariffs or streamlined customs processes. Consulting with legal experts or trade consultants can help you navigate these regulations effectively and avoid potential pitfalls.
Important Disclaimer & Terms of Use
⚠️ Important Disclaimer
The information provided in this guide, including content regarding manufacturers, technical specifications, and market analysis, is for informational and educational purposes only. It does not constitute professional procurement advice, financial advice, or legal advice.
While we have made every effort to ensure the accuracy and timeliness of the information, we are not responsible for any errors, omissions, or outdated information. Market conditions, company details, and technical standards are subject to change.
B2B buyers must conduct their own independent and thorough due diligence before making any purchasing decisions. This includes contacting suppliers directly, verifying certifications, requesting samples, and seeking professional consultation. The risk of relying on any information in this guide is borne solely by the reader.
Strategic Sourcing Conclusion and Outlook for truck supplier
What Are the Key Takeaways for Strategic Sourcing in Truck Supply?
In today’s competitive landscape, strategic sourcing is essential for international B2B buyers in the truck supply sector. By prioritizing relationships with reliable suppliers, businesses can secure better pricing, access high-quality parts, and enhance supply chain resilience. Utilizing tools such as loyalty programs, financing options, and return policies can significantly improve purchasing decisions. Additionally, understanding regional market dynamics, especially in Africa, South America, the Middle East, and Europe, is crucial for identifying suppliers that align with specific operational needs.
How Can Buyers Prepare for Future Sourcing Needs?
As the truck supply industry evolves, the importance of agility and adaptability in sourcing strategies cannot be overstated. Buyers should stay informed about technological advancements and shifting market trends to anticipate their future needs. Engaging with suppliers that offer innovative solutions and sustainable practices can position businesses for long-term success.
What Steps Should International Buyers Take Next?
To maximize the benefits of strategic sourcing, international buyers are encouraged to conduct thorough market research and foster strong partnerships with suppliers. By doing so, they can ensure a steady supply of quality products while navigating the complexities of the global marketplace. Now is the time to explore new sourcing strategies and solidify your position in the truck supply industry. Embrace the future with confidence, and take action today to enhance your procurement processes.