Unlock Quality & Cost Savings with a Plywood Manufacturer (2025)
Introduction: Navigating the Global Market for plywood manufacturer
Navigating the complexities of the global plywood market can be a daunting task for international B2B buyers, especially when it comes to sourcing high-quality plywood manufacturers that meet specific project needs. This guide aims to demystify the plywood procurement process, addressing common challenges such as varying standards, material types, and supplier reliability. From understanding the different types of plywood—like hardwood, softwood, and engineered variants—to exploring their diverse applications in construction, furniture, and packaging, this comprehensive resource equips buyers with the insights needed to make informed decisions.
International B2B buyers from regions such as Africa, South America, the Middle East, and Europe—including key markets like Turkey and Spain—will benefit from our detailed exploration of supplier vetting processes, cost considerations, and market trends. By highlighting crucial factors such as environmental sustainability and compliance with international standards, this guide empowers businesses to select the right manufacturers that align with their operational goals and ethical practices. Whether you’re looking to enhance your supply chain or simply seeking reliable partners for your plywood needs, this guide serves as an invaluable tool for navigating the global market landscape effectively.
Understanding plywood manufacturer Types and Variations
Type Name | Key Distinguishing Features | Primary B2B Applications | Brief Pros & Cons for Buyers |
---|---|---|---|
Hardwood Plywood | Made from hardwood species, high durability, and aesthetic appeal | Furniture, cabinetry, and flooring | Pros: High strength, attractive finish. Cons: Higher cost compared to softwood. |
Softwood Plywood | Constructed from softwood species, lighter and more affordable | Construction, packaging, and temporary structures | Pros: Cost-effective, easy to work with. Cons: Less durable than hardwood. |
Marine Plywood | Water-resistant adhesive and high-quality wood, designed for humid environments | Boat building, outdoor furniture, and marine applications | Pros: Exceptional water resistance, long-lasting. Cons: Higher price point. |
Film-Faced Plywood | Coated with a film to enhance durability and surface finish | Concrete formwork, construction, and industrial uses | Pros: Smooth surface, reusable. Cons: Limited aesthetic options. |
Birch Plywood | Made from birch veneer, known for its strength and fine grain | High-end furniture, cabinetry, and decorative applications | Pros: Excellent strength-to-weight ratio, attractive appearance. Cons: More expensive than other types. |
What Are the Characteristics of Hardwood Plywood?
Hardwood plywood is constructed from various hardwood species, providing exceptional durability and a visually appealing finish. This type of plywood is ideal for applications requiring strength and aesthetics, such as furniture and cabinetry. When purchasing hardwood plywood, buyers should consider the wood species, thickness, and intended use, as these factors affect both performance and cost. While hardwood plywood can be more expensive than other types, its longevity and aesthetic value often justify the investment.
How Does Softwood Plywood Compare to Other Types?
Softwood plywood is made from softer wood species, making it lighter and more affordable than hardwood options. It is commonly used in construction, packaging, and temporary structures due to its cost-effectiveness and ease of handling. Buyers should assess the intended application and required strength when considering softwood plywood, as it may not be suitable for high-stress environments. While it presents a budget-friendly option, its lower durability compared to hardwood should be taken into account.
What Makes Marine Plywood Unique?
Marine plywood is specifically designed for use in humid and wet environments, featuring water-resistant adhesives and high-quality wood. This type of plywood is ideal for boat building and outdoor applications where moisture exposure is a concern. Buyers should focus on the plywood’s water resistance rating and the quality of the wood used. Although marine plywood tends to be pricier, its durability and resistance to delamination make it a worthwhile investment for specialized applications.
Why Choose Film-Faced Plywood for Construction?
Film-faced plywood is coated with a durable film that enhances its surface finish and resistance to wear. It is primarily used in concrete formwork and industrial applications where a smooth, reusable surface is essential. Buyers should consider the film thickness and quality, as these factors impact the plywood’s performance and lifespan. While film-faced plywood offers excellent durability, it may lack the aesthetic appeal of other plywood types, making it less suitable for decorative applications.
What Are the Advantages of Birch Plywood?
Birch plywood is crafted from birch veneer, known for its fine grain and strength. It is often used in high-end furniture and cabinetry, where appearance and performance are critical. Buyers should evaluate the veneer quality and thickness when selecting birch plywood, as these elements affect both durability and cost. Although birch plywood is typically more expensive than other types, its attractive finish and excellent strength-to-weight ratio make it a preferred choice for premium applications.
Related Video: Manufacturing plywood boards: then and now
Key Industrial Applications of plywood manufacturer
Industry/Sector | Specific Application of plywood manufacturer | Value/Benefit for the Business | Key Sourcing Considerations for this Application |
---|---|---|---|
Construction | Structural components for buildings | Provides strength and durability for building frameworks | Compliance with local building codes and standards |
Furniture Manufacturing | Production of custom furniture pieces | Enhances aesthetic appeal and functionality of products | Availability of diverse wood types and finishes |
Transportation | Interior fittings for vehicles and ships | Lightweight yet strong materials for safe transport | Weight restrictions and material certification for safety standards |
Packaging | Protective packaging solutions | Cost-effective and sustainable alternative to plastic | Sourcing from environmentally responsible manufacturers |
Interior Design | Decorative wall panels and flooring | Adds value through visual appeal and design versatility | Customization options and adherence to design trends |
How is Plywood Used in the Construction Industry?
In the construction sector, plywood manufacturers supply structural components such as beams, panels, and formwork. Plywood is favored for its excellent strength-to-weight ratio, making it ideal for supporting structures. It addresses challenges related to moisture resistance and dimensional stability, essential for various climatic conditions, particularly in Africa and South America. Buyers should ensure that the plywood meets local building codes and is sourced from manufacturers who prioritize quality and sustainability.
What Role Does Plywood Play in Furniture Manufacturing?
Plywood is extensively used in the furniture manufacturing industry to create custom furniture pieces, including cabinets, tables, and chairs. Its versatility allows for intricate designs while maintaining durability. This material solves issues related to weight and ease of handling, making it a preferred choice for international buyers, particularly in Europe. When sourcing, consider the availability of various wood types and finishes that can enhance the aesthetic appeal of the final products.
How is Plywood Beneficial in Transportation?
In the transportation industry, plywood is utilized for interior fittings in vehicles, ships, and aircraft. Its lightweight nature contributes to fuel efficiency while providing robust support. Plywood manufacturers can help address safety concerns by offering materials that meet specific weight restrictions and certification standards. International buyers must ensure that the plywood sourced complies with regulations in their respective countries to avoid any legal complications.
Why is Plywood Important for Packaging Solutions?
Plywood is increasingly being adopted for protective packaging solutions, replacing traditional plastic materials. It offers a sustainable and cost-effective alternative that provides superior protection for goods during transit. This application is particularly relevant for businesses aiming to enhance their sustainability profile. Buyers should prioritize sourcing from manufacturers committed to environmentally responsible practices to align with global sustainability trends.
How Does Plywood Enhance Interior Design?
In interior design, plywood is used for decorative wall panels, flooring, and ceiling applications. Its natural aesthetic and versatility allow designers to create unique spaces that resonate with current design trends. Plywood solves the issue of heavy materials, providing a lightweight yet durable option for various interior applications. International B2B buyers should focus on customization options offered by manufacturers to meet specific design needs and ensure timely delivery to align with project timelines.
3 Common User Pain Points for ‘plywood manufacturer’ & Their Solutions
Scenario 1: Inconsistent Quality and Specifications in Plywood Supplies
The Problem: B2B buyers often encounter challenges with the quality and specifications of plywood products. Variability in thickness, density, and structural integrity can lead to significant issues in manufacturing processes, resulting in product failures, project delays, and increased costs. This inconsistency may stem from poor sourcing practices or unreliable suppliers, leaving buyers frustrated and hesitant about future orders.
The Solution: To combat this issue, international buyers should establish a robust quality assurance process when sourcing plywood. This includes requesting detailed product specifications, certifications, and test reports from manufacturers. Engaging in regular communication with suppliers about quality expectations and conducting periodic audits can ensure that the plywood meets the required standards. Additionally, consider sourcing from manufacturers that provide samples before placing large orders, allowing for thorough evaluation of the product quality. Collaborating with suppliers that adhere to international quality standards, such as ISO 9001, can further mitigate risks related to inconsistent quality.
Scenario 2: Long Lead Times and Unpredictable Delivery Schedules
The Problem: International buyers frequently face the challenge of long lead times and unpredictable delivery schedules when sourcing plywood. This can disrupt project timelines and affect overall business operations, especially in industries like construction and furniture manufacturing where timely delivery is critical. Delays can result from various factors, including supply chain disruptions, customs delays, and manufacturing inefficiencies.
The Solution: To alleviate concerns around delivery timelines, buyers should prioritize establishing strong relationships with reliable plywood manufacturers who have a track record of meeting deadlines. When negotiating contracts, incorporate clauses that specify delivery timelines and penalties for delays. Additionally, utilizing logistics partners with expertise in international shipping can streamline the import process, ensuring that plywood arrives on time. Buyers can also implement just-in-time inventory practices, allowing them to maintain lower stock levels while ensuring that materials are available precisely when needed. Regular updates from suppliers regarding production schedules and shipment tracking can further enhance transparency and reliability.
Scenario 3: Difficulty in Understanding Product Applications and Specifications
The Problem: Many B2B buyers struggle to understand the specific applications and technical specifications of different plywood types, leading to improper usage in projects. For instance, using standard plywood in high-moisture environments can lead to warping and structural failure. This lack of knowledge can result in costly mistakes and compromised project outcomes.
The Solution: To effectively navigate this challenge, buyers should invest time in educational resources and training offered by plywood manufacturers. This may include product manuals, webinars, or workshops that cover various plywood types, their properties, and appropriate applications. Buyers should also consider engaging with manufacturers that provide personalized consultation services to help select the right plywood for their specific needs. Utilizing an expert in the field can assist in understanding not only the physical properties but also the environmental and regulatory considerations relevant to each project. Establishing a feedback loop with suppliers can further enhance understanding and ensure that future orders align better with project requirements.
Strategic Material Selection Guide for plywood manufacturer
What Are the Key Properties of Common Plywood Materials?
When selecting materials for plywood manufacturing, understanding the properties of various wood types is essential for optimizing product performance. Here are four commonly used materials in the plywood industry:
1. Birch Plywood: What Are Its Key Properties and Applications?
Birch plywood is known for its strength and durability, making it suitable for high-stress applications. It has a temperature rating of up to 120°C and excellent resistance to warping. Birch also offers a smooth surface finish, ideal for decorative applications.
Pros: Birch plywood is highly durable, has a fine grain that accepts stains and finishes well, and is relatively lightweight. It is commonly used in furniture, cabinetry, and interior design.
Cons: The primary drawback is its cost, which is higher than many other plywood types. Additionally, birch is less resistant to moisture compared to marine-grade plywood, limiting its use in humid environments.
Impact on Application: Birch plywood is compatible with a variety of adhesives and finishes, making it versatile for both structural and aesthetic applications.
Considerations for International Buyers: Buyers should ensure compliance with international standards such as ASTM for quality assurance. In regions like Europe, where sustainability is emphasized, sourcing birch from certified forests can enhance marketability.
2. Okoume Plywood: How Does It Compare in Terms of Performance?
Okoume plywood is lightweight and has a high strength-to-weight ratio, making it an excellent choice for applications where weight is a concern, such as in the marine industry. It can withstand temperatures up to 70°C and has moderate resistance to moisture.
Pros: Its lightness facilitates easier handling and installation, while its aesthetic appeal makes it suitable for decorative applications. Okoume is also cost-effective compared to hardwood options.
Cons: The main limitation is its lower durability in extreme conditions, particularly in wet environments, which can lead to delamination if not properly treated.
Impact on Application: Okoume is often used in boat building and furniture, but its moisture sensitivity requires careful consideration of the end-use environment.
Considerations for International Buyers: Buyers should be aware of local regulations regarding the sourcing of Okoume, particularly in terms of sustainability and environmental impact. Compliance with standards like JIS can also be crucial for market entry in regions like Japan.
3. Marine Plywood: What Are Its Unique Features?
Marine plywood is specifically designed for high moisture environments, making it ideal for boat construction and other marine applications. It typically features a temperature rating of up to 80°C and is constructed with waterproof adhesives.
Pros: The primary advantage is its exceptional resistance to water and humidity, which prevents delamination and ensures longevity in wet conditions. It is also structurally strong.
Cons: The cost of marine plywood is significantly higher due to its specialized manufacturing process and materials. Additionally, it may be over-engineered for applications that do not require such high moisture resistance.
Impact on Application: Marine plywood is compatible with various marine paints and finishes, enhancing its usability in aquatic environments.
Considerations for International Buyers: Compliance with marine standards such as BS 1088 is essential for buyers in Europe and other regions. Buyers should also consider the sourcing of sustainable wood to align with environmental regulations.
4. Poplar Plywood: What Are Its Advantages and Disadvantages?
Poplar plywood is characterized by its lightweight nature and ease of machining. It has a temperature rating of around 60°C and is suitable for indoor applications.
Pros: Its affordability and ease of handling make it a popular choice for temporary structures, packaging, and interior applications. It also accepts paint and veneers well.
Cons: Poplar plywood is less durable than other hardwoods and is not suitable for outdoor use unless treated. Its lower density can also lead to a less robust final product.
Impact on Application: Poplar is often used in furniture and cabinetry, but its limitations in moisture resistance necessitate careful application planning.
Considerations for International Buyers: Buyers should ensure that poplar plywood meets local standards for quality and sustainability. In regions like South America, where poplar is commonly sourced, environmental certifications can enhance product appeal.
Summary Table of Material Selection for Plywood Manufacturing
Material | Typical Use Case for plywood manufacturer | Key Advantage | Key Disadvantage/Limitation | Relative Cost (Low/Med/High) |
---|---|---|---|---|
Birch | Furniture, cabinetry | Highly durable, fine grain | Higher cost, less moisture resistant | High |
Okoume | Marine applications, decorative items | Lightweight, cost-effective | Lower durability in wet conditions | Medium |
Marine Plywood | Boat construction, marine applications | Exceptional water resistance | High cost, potentially over-engineered | High |
Poplar | Temporary structures, interior applications | Affordable, easy to machine | Less durable, not suitable for outdoor use | Low |
This guide provides actionable insights for international B2B buyers, allowing them to make informed decisions when selecting materials for plywood manufacturing based on their specific needs and regional considerations.
In-depth Look: Manufacturing Processes and Quality Assurance for plywood manufacturer
What Are the Main Stages of the Plywood Manufacturing Process?
The plywood manufacturing process consists of several key stages: material preparation, forming, assembly, and finishing. Understanding these stages is crucial for B2B buyers looking to source high-quality plywood.
-
Material Preparation
The first stage involves selecting and preparing the raw materials. High-quality logs, typically hardwood or softwood, are debarked and cut into manageable lengths. This process often includes drying the wood to reduce moisture content, which is essential for minimizing warping and enhancing adhesion during the subsequent stages. The choice of wood species, such as birch, okoume, or poplar, can significantly affect the final product’s durability and appearance. -
Forming
In this stage, the prepared wood is sliced into thin veneers using rotary peeling, slicing, or sawing techniques. Rotary peeling is commonly used for mass production, where logs are rotated against a knife, producing a continuous veneer sheet. Slicing, on the other hand, offers a more aesthetic grain pattern, making it suitable for decorative plywood. The thickness of veneers can vary based on the intended application, and precise cutting is crucial to ensure uniformity. -
Assembly
Once the veneers are prepared, they are glued together in layers, with the grain direction of adjacent layers typically oriented at right angles. This cross-laminated structure enhances the plywood’s strength and stability, making it ideal for various applications. The assembly process may involve pressing the layers under heat and pressure to ensure a strong bond. The adhesive used is often phenolic or urea-formaldehyde, chosen for its durability and moisture resistance. -
Finishing
The final stage includes trimming the edges, sanding the surface, and applying any protective coatings or finishes. This process not only enhances the aesthetic appeal but also provides additional durability against environmental factors. Quality control measures during finishing ensure that the plywood meets the desired specifications regarding thickness, surface smoothness, and overall appearance.
How Is Quality Assurance Implemented in Plywood Manufacturing?
Quality assurance (QA) is vital for ensuring that plywood products meet international standards and buyer expectations. Various methodologies and standards govern the QA process in plywood manufacturing.
-
International Standards for Quality Assurance
Plywood manufacturers often adhere to ISO 9001 standards, which outline requirements for a quality management system. Compliance with these standards ensures that the manufacturing processes consistently produce high-quality products. Additionally, industry-specific certifications such as CE marking in Europe and API standards for certain applications further validate product quality and safety. -
Quality Control Checkpoints
Quality control involves multiple checkpoints throughout the manufacturing process:
- Incoming Quality Control (IQC): Raw materials are inspected upon arrival to ensure they meet specified standards. This includes checking the moisture content of the wood and the quality of adhesives used.
- In-Process Quality Control (IPQC): During the manufacturing process, regular inspections are conducted to monitor the thickness of veneers, adhesive application, and the pressing process. Any deviations are corrected immediately to prevent defects.
- Final Quality Control (FQC): Once the plywood is finished, a thorough inspection is conducted to assess its overall quality, including dimensional accuracy, surface finish, and compliance with safety standards.
- Common Testing Methods for Plywood Quality
Various testing methods are employed to verify the quality of plywood. These include:
- Moisture Content Testing: Ensuring the plywood has an optimal moisture level to prevent warping.
- Mechanical Testing: Assessing the strength and durability of the plywood through bending and shear tests.
- Adhesive Bond Testing: Evaluating the effectiveness of adhesive bonds under different conditions, including moisture exposure.
How Can B2B Buyers Verify Supplier Quality Control?
For international B2B buyers, particularly from regions such as Africa, South America, the Middle East, and Europe, verifying a supplier’s quality control processes is essential to ensure product reliability.
-
Conducting Supplier Audits
Before placing an order, buyers should conduct thorough audits of potential suppliers. This includes assessing their manufacturing facilities, quality control practices, and adherence to international standards. Engaging a third-party inspection company can provide an unbiased evaluation. -
Requesting Quality Reports and Certifications
Buyers should request detailed quality reports that outline the results of various tests conducted on the plywood. Certificates of compliance with relevant international standards (ISO, CE, etc.) should also be requested to verify that the products meet specific quality benchmarks. -
Utilizing Third-Party Inspections
Engaging third-party inspection services can provide additional assurance regarding product quality. These organizations can perform random inspections during production and before shipment, ensuring that the plywood meets the agreed-upon specifications.
What Are the Quality Control Nuances for International B2B Buyers?
B2B buyers must be aware of several nuances regarding quality control when sourcing plywood internationally:
-
Understanding Local Regulations
Different countries have varying regulations concerning wood products. Buyers should be familiar with local standards in their region, such as CARB regulations in the United States or EUTR regulations in Europe, to ensure compliance when importing plywood. -
Cultural Considerations in Quality Perception
Cultural differences can influence perceptions of quality. For instance, European buyers may prioritize aesthetic qualities and sustainability, while Middle Eastern buyers might focus on durability under extreme conditions. Understanding these preferences can aid in selecting the right supplier. -
Building Relationships with Suppliers
Establishing a strong relationship with suppliers can enhance quality control. Regular communication and feedback loops help suppliers understand buyer expectations and improve their processes accordingly.
In conclusion, understanding the manufacturing processes and quality assurance protocols in plywood production is crucial for international B2B buyers. By focusing on these elements, buyers can make informed decisions that ensure they receive high-quality products that meet their specific needs.
Practical Sourcing Guide: A Step-by-Step Checklist for ‘plywood manufacturer’
To ensure a successful procurement process when sourcing plywood manufacturers, it is essential to follow a structured approach. This checklist will guide international B2B buyers, particularly from Africa, South America, the Middle East, and Europe, through the critical steps necessary to secure quality plywood products that meet your business needs.
Step 1: Define Your Technical Specifications
Begin by outlining your specific requirements for plywood. This includes dimensions, thickness, wood species (e.g., birch, okoume, or poplar), and any necessary certifications (e.g., FSC or PEFC). Clearly defining these specifications will help streamline the sourcing process and ensure that suppliers can meet your exact needs.
- Consider end-use applications: Whether for construction, furniture, or decorative purposes, the intended use will dictate the type of plywood required.
- Quality standards: Research industry standards relevant to your region to avoid compliance issues.
Step 2: Conduct Market Research
Explore the market to identify potential plywood manufacturers. Utilize online resources, industry directories, and trade shows to gather a list of suppliers. This step is crucial for understanding the competitive landscape and identifying manufacturers that align with your requirements.
- Evaluate regional suppliers: Focus on suppliers from regions known for quality plywood production, such as Europe and Southeast Asia.
- Industry trends: Stay informed about current trends in the plywood market to identify innovative suppliers who may offer unique products.
Step 3: Evaluate Potential Suppliers
Before committing, it’s crucial to vet suppliers thoroughly. Request company profiles, case studies, and references from buyers in a similar industry or region. Do not rely solely on their website; investigate their reputation in the market.
- Check for reviews and ratings: Look for testimonials or reviews from previous clients to gauge supplier reliability.
- Visit facilities if possible: In-person visits can provide insight into production capabilities and quality control processes.
Step 4: Verify Supplier Certifications
Ensure that potential suppliers possess the necessary certifications that validate their adherence to quality and environmental standards. Certifications such as ISO 9001 for quality management and ISO 14001 for environmental management are important indicators of a reputable manufacturer.
- Sustainability practices: Confirm that the manufacturer uses sustainable practices in sourcing wood, which is increasingly important for many buyers.
- Compliance with local regulations: Check if the supplier adheres to regulations in your region regarding product safety and environmental impact.
Step 5: Request Samples
Before placing a large order, request samples of the plywood products. This allows you to assess the quality, appearance, and suitability of the plywood for your intended application.
- Conduct quality tests: Evaluate the samples for strength, finish, and moisture resistance to ensure they meet your standards.
- Compare different suppliers: Utilize samples to compare various suppliers’ offerings directly.
Step 6: Negotiate Terms and Conditions
Once you have selected a supplier, engage in negotiations regarding pricing, payment terms, and delivery schedules. Clear and fair terms are essential to establish a strong business relationship.
- Consider long-term agreements: If the supplier meets your needs, discuss options for long-term contracts which can lead to better pricing and priority service.
- Review shipping and logistics: Ensure that the supplier can meet your shipping requirements and timelines, especially if you are importing from overseas.
Step 7: Finalize the Order and Monitor Delivery
After agreeing on the terms, finalize your order. Maintain open communication with the supplier throughout the production and shipping process to address any issues promptly.
- Track shipments: Use tracking systems to monitor the delivery process and address delays proactively.
- Quality assurance upon arrival: Inspect the plywood upon delivery to ensure it meets the agreed specifications before acceptance.
By following this step-by-step checklist, B2B buyers can efficiently navigate the sourcing process for plywood manufacturers, ensuring they select a partner that meets their quality and service expectations.
Comprehensive Cost and Pricing Analysis for plywood manufacturer Sourcing
What Are the Key Cost Components in Plywood Manufacturing?
Understanding the cost structure of plywood manufacturing is essential for international B2B buyers. The primary components include:
-
Materials: The cost of raw materials, such as various wood species (e.g., birch, okoume, or poplar), is a significant factor. Prices fluctuate based on availability, quality, and global market conditions. Buyers should consider sourcing from regions with abundant resources to minimize costs.
-
Labor: Labor costs vary significantly by region. In developing regions, such as parts of Africa and South America, labor may be cheaper, but buyers must also consider the skill levels and productivity of the workforce.
-
Manufacturing Overhead: This includes costs related to utilities, rent, and indirect labor. Efficient manufacturing processes can reduce overhead, allowing manufacturers to offer competitive pricing.
-
Tooling: Initial investments in machinery and tools can be substantial. However, advanced tooling can lead to higher precision and lower defect rates, ultimately impacting overall costs.
-
Quality Control (QC): Maintaining high standards of quality requires investments in QC processes. This is crucial for buyers needing certifications for construction or furniture applications.
-
Logistics: Shipping costs can vary significantly based on the distance, mode of transport, and Incoterms agreed upon. For international shipments, understanding logistics can help buyers manage additional costs effectively.
-
Margin: Manufacturers typically mark up prices to ensure profitability. Understanding the manufacturer’s cost structure helps buyers negotiate better terms.
How Do Price Influencers Impact Plywood Sourcing?
Several factors influence pricing in plywood sourcing:
-
Volume and Minimum Order Quantity (MOQ): Larger orders often lead to discounts. Buyers should evaluate their needs and consider bulk purchasing to achieve cost savings.
-
Specifications and Customization: Custom specifications can increase costs due to additional processing. Buyers should be clear about their requirements to avoid unnecessary expenses.
-
Materials and Quality Certifications: Higher quality materials and certifications (e.g., FSC, CE) can significantly affect pricing. Buyers in Europe may prioritize certified products, impacting their sourcing decisions.
-
Supplier Factors: The reputation and reliability of suppliers play a crucial role in pricing. Established suppliers may charge higher prices due to their proven track record, while newer suppliers might offer competitive rates to gain market share.
-
Incoterms: The choice of Incoterms (e.g., FOB, CIF) affects shipping costs and responsibilities. Buyers should select terms that align with their logistics capabilities and cost management strategies.
What Are Effective Buyer Tips for Negotiating Plywood Prices?
When negotiating prices for plywood sourcing, international B2B buyers can adopt several strategies:
-
Conduct Thorough Market Research: Understanding the market landscape helps buyers establish a baseline for negotiations. Knowledge of current prices, trends, and competitor offerings provides leverage.
-
Evaluate Total Cost of Ownership (TCO): Focus on the complete cost of acquiring plywood, including shipping, handling, and potential waste. This broader view can help justify higher upfront costs for higher quality or more efficient products.
-
Leverage Relationships: Building strong relationships with suppliers can lead to better pricing and terms. Frequent communication and trust can result in favorable negotiations.
-
Be Prepared to Walk Away: Establishing a clear budget and being willing to seek alternatives can enhance negotiating power. If a supplier cannot meet your price or quality requirements, being prepared to look elsewhere can drive better offers.
-
Consider Long-Term Contracts: Committing to long-term agreements can lead to price stability and discounts, as suppliers value consistent business.
Conclusion
Understanding the comprehensive cost structure and pricing dynamics in plywood manufacturing is vital for international B2B buyers. By focusing on key cost components, recognizing price influencers, and employing effective negotiation strategies, buyers can achieve better sourcing outcomes. Always remember that prices may vary, and it’s advisable to request indicative pricing from multiple suppliers to make informed decisions.
Alternatives Analysis: Comparing plywood manufacturer With Other Solutions
Understanding the Need for Alternatives in Plywood Manufacturing
In the competitive landscape of construction and furniture production, understanding the alternatives to traditional plywood manufacturing is crucial for international B2B buyers. As the demand for versatile and sustainable materials grows, exploring viable alternatives can enhance product offerings, reduce costs, and meet environmental standards. This section provides a comparative analysis of plywood against two prominent alternatives: oriented strand board (OSB) and medium-density fiberboard (MDF).
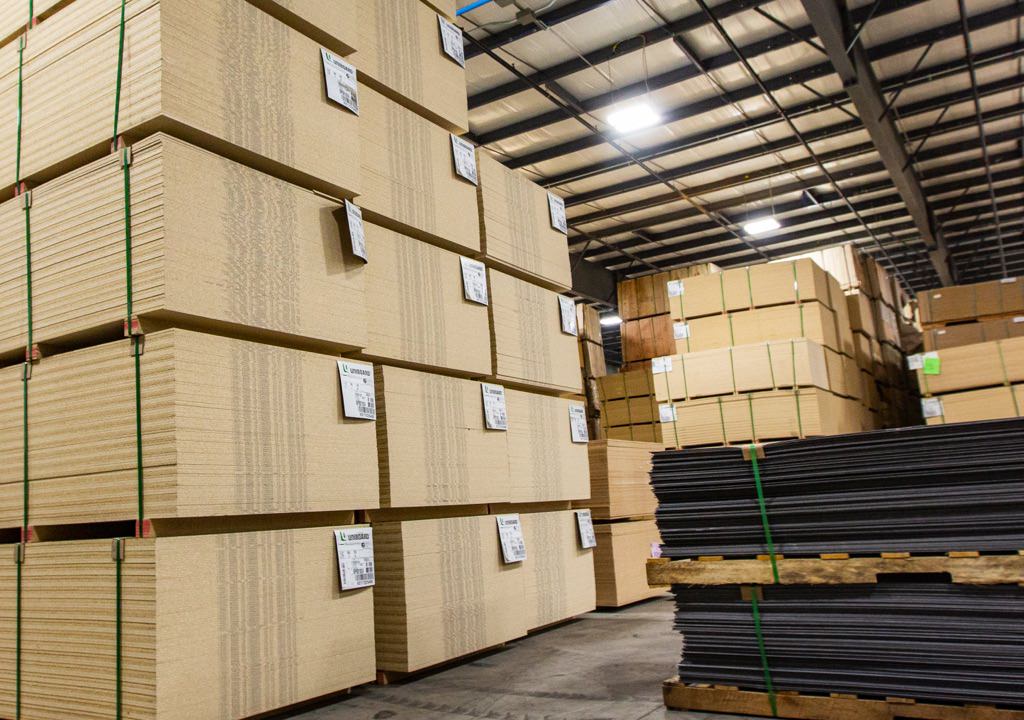
A stock image related to plywood manufacturer.
Comparison of Plywood Manufacturer with Alternatives
Comparison Aspect | Plywood Manufacturer | Oriented Strand Board (OSB) | Medium-Density Fiberboard (MDF) |
---|---|---|---|
Performance | High strength and durability | Strong, but varies by grade | Excellent for detailed finishes |
Cost | Moderate to high | Generally lower | Moderate |
Ease of Implementation | Requires skilled labor | Easier to work with | Easy to cut and shape |
Maintenance | Low maintenance | Low maintenance | Moderate; susceptible to water |
Best Use Case | Structural applications | Sheathing and flooring | Furniture and cabinetry |
In-Depth Look at Alternatives
What is Oriented Strand Board (OSB) and How Does it Compare?
Oriented strand board (OSB) is an engineered wood product made from strands of wood that are oriented in specific directions and bonded together with adhesives. OSB is known for its cost-effectiveness and is often used in construction as a sheathing material.
Pros:
– Cost-Effective: Typically lower in price compared to plywood, making it a popular choice for budget-conscious projects.
– Versatile: Suitable for a variety of applications, including flooring, wall sheathing, and roofing.
Cons:
– Variable Quality: The strength and durability can vary significantly based on the manufacturing process and quality of materials used.
– Moisture Sensitivity: OSB is more susceptible to moisture damage compared to plywood, which can limit its use in wet environments.
How Does Medium-Density Fiberboard (MDF) Serve as an Alternative?
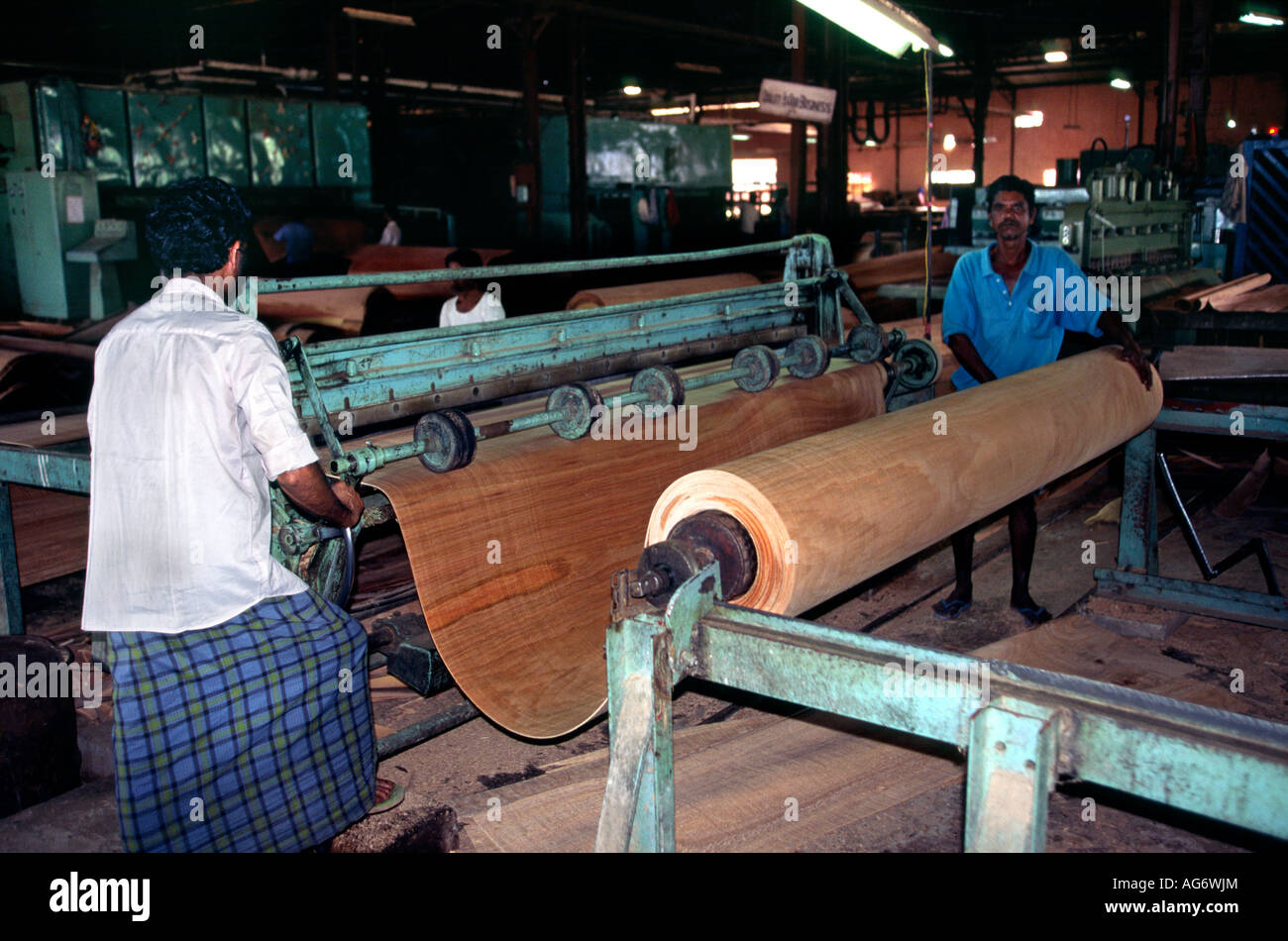
A stock image related to plywood manufacturer.
Medium-density fiberboard (MDF) is made from wood fibers that are bonded together under heat and pressure. It is known for its smooth surface, making it ideal for applications where a fine finish is desired.
Pros:
– Smooth Surface: Ideal for painting and veneering, making it perfect for furniture and cabinetry.
– Ease of Use: Easy to cut, shape, and install, which can save time during construction or manufacturing.
Cons:
– Lower Strength: Not suitable for structural applications due to its lower load-bearing capacity.
– Moisture Concerns: MDF is highly susceptible to water damage, which can limit its use in humid environments.
How Can B2B Buyers Choose the Right Solution?
When considering which material to use, B2B buyers should evaluate their specific project requirements, including performance needs, budget constraints, and environmental conditions. Plywood remains a robust choice for structural applications due to its durability and strength. However, for projects focused on cost savings and aesthetic finishes, OSB or MDF may present viable alternatives. Understanding the strengths and limitations of each material will enable buyers to make informed decisions that align with their operational goals and customer expectations.
Essential Technical Properties and Trade Terminology for plywood manufacturer
What Are the Essential Technical Properties of Plywood for B2B Buyers?
When sourcing plywood for industrial applications, understanding its technical properties is crucial. Here are some critical specifications that international B2B buyers should consider:
1. Material Grade
Material grade indicates the quality of the plywood based on factors like appearance, strength, and durability. Common grades include A, B, C, and D, with A being the highest quality, suitable for visible surfaces, and D being the lowest, often used for structural purposes. Buyers must choose the appropriate grade to meet their specific application requirements, ensuring longevity and aesthetic appeal.
2. Thickness Tolerance
Thickness tolerance refers to the permissible variation in the plywood’s thickness, typically expressed in millimeters. For example, a 12mm plywood may have a tolerance of ±0.5mm. This specification is vital for applications where precise measurements are critical, such as cabinetry or flooring, as improper thickness can lead to installation issues.
3. Moisture Content
Moisture content is a measure of the amount of water present in the plywood. Ideal moisture content ranges from 8% to 12% for interior applications. Higher moisture content can lead to warping and decay, while lower levels may cause cracking. Buyers must confirm moisture content to ensure plywood performs optimally in varying environmental conditions.
4. Bending Strength
Bending strength, measured in megapascals (MPa), indicates how much load the plywood can withstand before deforming. This property is particularly important for structural applications, such as in the construction of furniture or flooring. Understanding bending strength helps buyers select the right plywood for load-bearing applications, ensuring safety and stability.
5. Formaldehyde Emission Levels
Formaldehyde emissions are a concern due to health and environmental regulations. Plywood is categorized by its emission levels, such as E0, E1, and E2, with E0 being the lowest emission level. Buyers should prioritize low-emission plywood to comply with health standards and ensure a safer indoor environment.
What Common Trade Terms Should B2B Buyers Know in the Plywood Industry?
Navigating the plywood market requires familiarity with specific trade terminology. Here are several essential terms that can enhance your understanding:
1. OEM (Original Equipment Manufacturer)
OEM refers to a company that produces parts and equipment that may be marketed by another manufacturer. In the plywood industry, an OEM might supply plywood components to furniture manufacturers. Understanding OEM relationships can help buyers negotiate better pricing and quality assurance.
2. MOQ (Minimum Order Quantity)
MOQ is the smallest quantity of a product that a supplier is willing to sell. This term is crucial for buyers, especially small businesses, to understand their purchasing limits and plan their budgets accordingly. Knowing the MOQ can also help in negotiating bulk orders to reduce costs.
3. RFQ (Request for Quotation)
An RFQ is a document sent to suppliers to solicit price quotes for specific products. It is essential for buyers to issue RFQs to compare prices, terms, and conditions effectively. A well-structured RFQ can lead to better deals and foster relationships with suppliers.
4. Incoterms (International Commercial Terms)
Incoterms are a set of international rules that define the responsibilities of sellers and buyers for the delivery of goods. Terms like FOB (Free on Board) and CIF (Cost, Insurance, and Freight) determine who is responsible for shipping costs and liability during transit. Understanding Incoterms is crucial for buyers to manage risks and costs associated with international shipping.
5. Lead Time
Lead time refers to the period from placing an order to the delivery of the product. It is essential for planning and inventory management. Buyers should inquire about lead times to ensure timely project execution and avoid delays in their operations.
By comprehending these technical properties and trade terms, international B2B buyers can make informed purchasing decisions, ensuring that they select the right plywood products for their specific needs while navigating the complexities of the global market.
Navigating Market Dynamics and Sourcing Trends in the plywood manufacturer Sector
What Are the Current Market Dynamics and Key Trends in the Plywood Manufacturer Sector?
The plywood manufacturing sector is experiencing a significant transformation driven by various global factors. One of the primary drivers is the increasing demand for sustainable building materials due to heightened environmental awareness. The construction industry, particularly in regions like Europe and the Middle East, is pivoting towards eco-friendly solutions, which has led to a surge in the popularity of plywood as a versatile and sustainable option. Furthermore, the ongoing urbanization in Africa and South America is boosting the demand for plywood in residential and commercial constructions.
Emerging B2B technologies are reshaping sourcing trends within the plywood industry. Digital platforms for procurement are becoming commonplace, allowing international buyers to streamline their sourcing processes and access a broader range of manufacturers. Additionally, advancements in supply chain analytics are enabling better inventory management and cost optimization. Manufacturers are increasingly adopting automation and advanced manufacturing techniques, which enhance production efficiency and product quality, appealing to buyers looking for reliable and high-quality materials.
Market dynamics are also influenced by geopolitical factors and trade policies. For instance, tariffs and import restrictions can significantly impact pricing and availability. International B2B buyers must stay informed about these dynamics to make educated sourcing decisions. Additionally, the plywood market is seeing a shift towards more localized sourcing options, which can reduce lead times and transportation costs, particularly important for buyers in regions like Turkey and Spain.
How Can Sustainability and Ethical Sourcing Impact Your B2B Strategy in Plywood?
Sustainability is becoming a critical consideration for B2B buyers in the plywood sector. The environmental impact of plywood production, particularly concerning deforestation and carbon emissions, is prompting manufacturers to adopt more sustainable practices. Buyers are increasingly prioritizing suppliers that adhere to sustainable forestry practices and have certifications such as the Forest Stewardship Council (FSC) or Programme for the Endorsement of Forest Certification (PEFC). These certifications not only assure buyers of the ethical sourcing of materials but also enhance their brand reputation among environmentally conscious consumers.
Moreover, the importance of ethical supply chains cannot be overstated. Buyers who engage with manufacturers committed to social responsibility can ensure that their sourcing practices do not contribute to labor exploitation or environmental degradation. This commitment is not only a moral obligation but also a competitive advantage, as consumers are increasingly favoring brands that demonstrate environmental stewardship.
Incorporating ‘green’ materials into procurement strategies can lead to long-term cost savings and compliance with emerging regulations. As governments worldwide impose stricter environmental regulations, sourcing from certified suppliers will be essential for compliance and sustainability goals.
How Has the Plywood Manufacturing Sector Evolved Over Time?
The plywood manufacturing sector has undergone significant evolution since its inception. Initially developed in the early 20th century, plywood was primarily used for military applications and later expanded into the construction and furniture industries. Over the decades, advancements in adhesive technologies and wood processing techniques have improved the strength and durability of plywood, making it a preferred material in various applications.
The evolution has also been marked by a shift towards sustainability. Early production methods often led to environmental degradation, but today’s manufacturers are increasingly focused on sustainable practices. This shift is driven by both regulatory pressures and market demand for eco-friendly materials. The historical progression of the plywood industry reflects broader trends in consumer preferences and environmental responsibility, which are now central to B2B sourcing strategies.
In conclusion, international B2B buyers must navigate a complex landscape characterized by dynamic market trends, sustainability imperatives, and evolving sourcing technologies. Understanding these elements will be key to making informed purchasing decisions in the plywood manufacturing sector.
Frequently Asked Questions (FAQs) for B2B Buyers of plywood manufacturer
-
How do I choose the right plywood manufacturer for my business needs?
Choosing the right plywood manufacturer involves assessing several factors. Start by evaluating their product range, including types of plywood such as hardwood, softwood, and specialty panels. Check the manufacturer’s certifications for quality assurance and compliance with international standards. Additionally, consider their production capacity, lead times, and ability to customize products to meet your specific requirements. Lastly, request samples to assess quality and durability before making a commitment. -
What are the common types of plywood used in international B2B trade?
Common types of plywood in international B2B trade include hardwood plywood, softwood plywood, and marine plywood. Hardwood plywood is preferred for furniture and cabinetry due to its aesthetic appeal and strength. Softwood plywood is often used in construction and packaging applications, while marine plywood is designed for water resistance, making it ideal for boats and outdoor structures. Understanding the properties and applications of each type will help you choose the best fit for your projects. -
What is the minimum order quantity (MOQ) when sourcing plywood from manufacturers?
Minimum order quantities (MOQs) can vary significantly among plywood manufacturers, typically ranging from 100 to 500 sheets. Factors influencing MOQ include the type of plywood, the manufacturer’s production capacity, and the customization options required. When negotiating with suppliers, clarify MOQs upfront to avoid unexpected costs. Additionally, consider consolidating orders with other products to meet MOQ requirements if your needs are smaller. -
What payment terms should I expect when dealing with plywood manufacturers?
Payment terms vary by manufacturer but typically include options such as advance payment, letter of credit, or net 30/60 days after delivery. It’s essential to discuss and agree on payment terms before finalizing any orders. Ensure you understand the implications of each term, particularly regarding cash flow and risk management. If you’re dealing with international suppliers, be aware of currency fluctuations and additional fees that may apply. -
How can I ensure the quality of plywood when sourcing internationally?
To ensure plywood quality when sourcing internationally, request certification documents like ISO and CE markings that confirm compliance with international standards. Consider conducting factory audits or using third-party inspection services to assess production practices and material quality. Additionally, request samples for evaluation before placing large orders. Establishing a clear quality assurance process with your supplier can help mitigate risks associated with product defects. -
What logistics considerations should I be aware of when importing plywood?
When importing plywood, logistics considerations include shipping methods, customs regulations, and delivery timelines. Choose between air freight for speed or sea freight for cost-effectiveness, depending on your timeline and budget. Familiarize yourself with import tariffs, duties, and documentation required for customs clearance to avoid delays. Partnering with a reliable freight forwarder can streamline the logistics process and help navigate international shipping complexities. -
How can I verify the credibility of a plywood manufacturer?
Verifying a plywood manufacturer’s credibility involves conducting thorough research. Start by checking their business licenses, industry certifications, and customer reviews. Engage in direct communication to assess their responsiveness and willingness to provide references from past clients. Attending industry trade shows can also offer insights into their reputation and product offerings. A reputable manufacturer will be transparent about their processes and provide documentation to support their claims. -
Can plywood manufacturers provide customized solutions for my projects?
Many plywood manufacturers offer customization options to meet specific project requirements, such as thickness, size, and finish. Discuss your needs during initial negotiations to ensure the manufacturer can accommodate your requests. Be clear about your specifications and any relevant industry standards. Custom solutions may involve additional lead times and costs, so it’s essential to plan accordingly and confirm all details in writing before proceeding with the order.
Important Disclaimer & Terms of Use
⚠️ Important Disclaimer
The information provided in this guide, including content regarding manufacturers, technical specifications, and market analysis, is for informational and educational purposes only. It does not constitute professional procurement advice, financial advice, or legal advice.
While we have made every effort to ensure the accuracy and timeliness of the information, we are not responsible for any errors, omissions, or outdated information. Market conditions, company details, and technical standards are subject to change.
B2B buyers must conduct their own independent and thorough due diligence before making any purchasing decisions. This includes contacting suppliers directly, verifying certifications, requesting samples, and seeking professional consultation. The risk of relying on any information in this guide is borne solely by the reader.
Strategic Sourcing Conclusion and Outlook for plywood manufacturer
As the global demand for plywood continues to grow, international B2B buyers must prioritize strategic sourcing to ensure they secure high-quality materials at competitive prices. Engaging with reliable plywood manufacturers not only enhances supply chain efficiency but also mitigates risks associated with fluctuating market conditions. Key takeaways for buyers from Africa, South America, the Middle East, and Europe include the importance of understanding regional wood availability, compliance with environmental regulations, and leveraging technology for transparent supply chain management.
How can international buyers leverage strategic partnerships in plywood sourcing? Establishing long-term relationships with manufacturers can provide access to exclusive products and favorable pricing structures. Additionally, buyers should consider diversifying their supplier base to reduce dependency on single sources and enhance resilience against disruptions.
Looking ahead, the plywood industry is poised for innovation, with trends focusing on sustainability and eco-friendly practices. Buyers are encouraged to align their sourcing strategies with these emerging trends to meet consumer demands and regulatory standards. By taking proactive steps today, B2B buyers can position themselves for success in the dynamic global plywood market.