Unlock Quality & Cost Savings: Your Mixer Manufacturer Guide (2025)
Introduction: Navigating the Global Market for mixer manufacturer
In today’s competitive landscape, sourcing high-quality mixers for diverse applications presents a significant challenge for international B2B buyers. Whether you’re in the music industry, food processing, or manufacturing, the demand for reliable mixer manufacturers is paramount. This comprehensive guide delves into the global market for mixer manufacturers, exploring various types, applications, and vital considerations for supplier vetting.
By examining critical factors such as cost structures, quality assurance, and technological advancements, this resource equips buyers from Africa, South America, the Middle East, and Europe with the insights needed to make informed purchasing decisions. As you navigate through the complexities of sourcing mixers, you’ll discover how to identify reputable suppliers, assess product specifications, and negotiate favorable terms that align with your operational needs.
Furthermore, this guide emphasizes the importance of understanding regional market dynamics, ensuring that you can effectively leverage local and international trends to your advantage. By empowering B2B buyers with actionable knowledge, we aim to facilitate smoother procurement processes and enhance overall supply chain efficiency. Prepare to transform your sourcing strategy and position your business for success in the global mixer market.
Understanding mixer manufacturer Types and Variations
Type Name | Key Distinguishing Features | Primary B2B Applications | Brief Pros & Cons for Buyers |
---|---|---|---|
Analog Mixers | Traditional knobs and sliders, no digital processing | Live sound, broadcasting, recording studios | Pros: Simple operation, warm sound quality. Cons: Limited flexibility, not suitable for complex setups. |
Digital Mixers | Integrated digital effects, programmable settings | Live performances, studio recordings | Pros: Versatile, precise control, many features. Cons: Steeper learning curve, higher cost. |
DJ Mixers | Designed for seamless track blending, often with USB support | Nightclubs, events, mobile DJ setups | Pros: User-friendly, real-time mixing capabilities. Cons: Limited to specific applications, may lack advanced features. |
USB Mixers | Connect directly to computers, often with built-in sound cards | Podcasting, streaming, home studios | Pros: Easy integration with software, portable. Cons: May have limited inputs/outputs, quality varies widely. |
Mixer Consoles | Large format, multiple channels, often with extensive routing | Large venues, theatrical productions | Pros: High channel count, extensive features. Cons: Bulky, requires more training to operate effectively. |
What are the characteristics of Analog Mixers for B2B buyers?
Analog mixers are the go-to choice for many traditional audio applications due to their straightforward design and tactile interface. They utilize physical knobs and sliders, providing a warm, natural sound that many audio professionals prefer. These mixers are particularly suited for live sound applications, broadcasting, and recording studios where simplicity and reliability are paramount. B2B buyers should consider the specific needs of their audio environment, as analog mixers may not offer the flexibility required for more complex setups.
How do Digital Mixers benefit B2B applications?
Digital mixers incorporate advanced technology, allowing users to manage multiple audio sources with precision. They often come with integrated effects and programmable settings, making them ideal for both live performances and studio recordings. Their versatility is a significant advantage for B2B buyers who need to adapt to varying audio requirements. However, the higher cost and steeper learning curve associated with digital mixers should be weighed against their extensive feature set.
What should B2B buyers know about DJ Mixers?
DJ mixers are specifically designed for blending tracks in real-time, making them essential for nightclubs, events, and mobile DJ setups. They offer user-friendly interfaces, often with USB support for seamless integration with digital audio workstations. While DJ mixers excel in live environments, their limitations in more complex audio setups may make them less suitable for broader applications. Buyers should assess whether their primary focus is on live performance or if they require additional features for studio work.
How do USB Mixers cater to modern B2B needs?
USB mixers provide a convenient solution for connecting directly to computers, making them ideal for podcasting, streaming, and home studios. With built-in sound cards, they simplify the recording process and are often portable, catering to the needs of mobile professionals. However, B2B buyers should be cautious of the varying quality and limited inputs/outputs that some USB mixers may offer, ensuring they select a model that meets their specific audio requirements.
What are the advantages and considerations for Mixer Consoles in B2B settings?
Mixer consoles are large-format mixers designed for extensive audio routing and multiple channels, making them suitable for large venues and theatrical productions. They offer a high channel count and a range of features that enable complex audio management. However, their bulkiness and the training required to operate them effectively can be a drawback for some buyers. Organizations should evaluate their operational capacity and the scale of their audio needs when considering mixer consoles.
Related Video: Bath shower mixer – Diverter: maintenance and replacement
Key Industrial Applications of mixer manufacturer
Industry/Sector | Specific Application of Mixer Manufacturer | Value/Benefit for the Business | Key Sourcing Considerations for this Application |
---|---|---|---|
Food and Beverage | Mixing ingredients for food production | Ensures uniformity and quality in products | Compliance with food safety standards, material quality |
Pharmaceuticals | Formulating medicines and supplements | Enhances the efficacy and consistency of products | Regulatory compliance, precision in mixing processes |
Cosmetics and Personal Care | Blending raw materials for cosmetic products | Improves product stability and consumer appeal | Sourcing high-quality ingredients, eco-friendly options |
Chemical Manufacturing | Mixing chemicals for industrial processes | Increases efficiency and safety in production | Chemical compatibility, durability of equipment |
Construction Materials | Mixing compounds for concrete and other materials | Ensures strength and durability of final products | Material sourcing, adherence to industry standards |
How is Mixer Manufacturing Applied in the Food and Beverage Sector?
In the food and beverage industry, mixer manufacturers play a crucial role in ensuring that ingredients are blended uniformly for production. For instance, mixers are used to combine powders, liquids, and solids in the manufacturing of sauces, beverages, and baked goods. This uniformity not only enhances product quality but also meets consumer expectations for taste and texture. International buyers should consider sourcing mixers that comply with local food safety regulations and are made from materials suitable for food contact.
What Role Do Mixers Play in Pharmaceuticals?
In pharmaceuticals, mixer manufacturers are essential for creating homogeneous mixtures of active ingredients and excipients in drug formulations. This precision in mixing is vital for the efficacy of medicines, as uneven distribution can lead to ineffective treatments. Buyers from Africa, South America, the Middle East, and Europe must prioritize mixers that meet stringent regulatory standards and offer features like precise control over mixing speeds and times, ensuring consistent results.
How Are Mixers Used in the Cosmetics Industry?
The cosmetics and personal care sector relies on mixer manufacturers to blend various raw materials, including oils, emulsifiers, and fragrances, to create lotions, creams, and makeup products. Effective mixing improves product stability, which is critical for shelf life and consumer satisfaction. B2B buyers should focus on sourcing mixers that allow for gentle processing to preserve the integrity of sensitive ingredients while also considering eco-friendly options to align with sustainability trends.
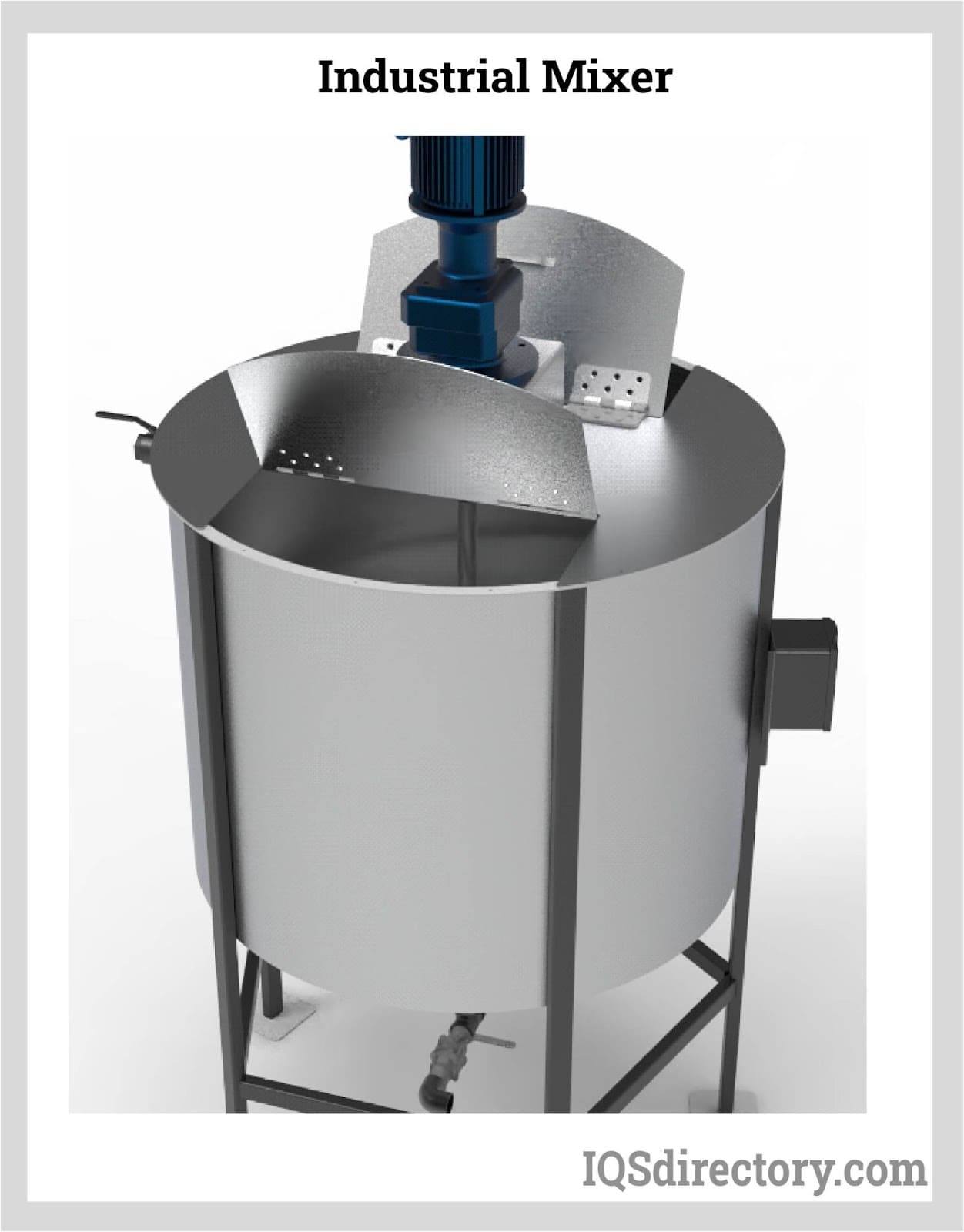
A stock image related to mixer manufacturer.
Why Are Mixers Important in Chemical Manufacturing?
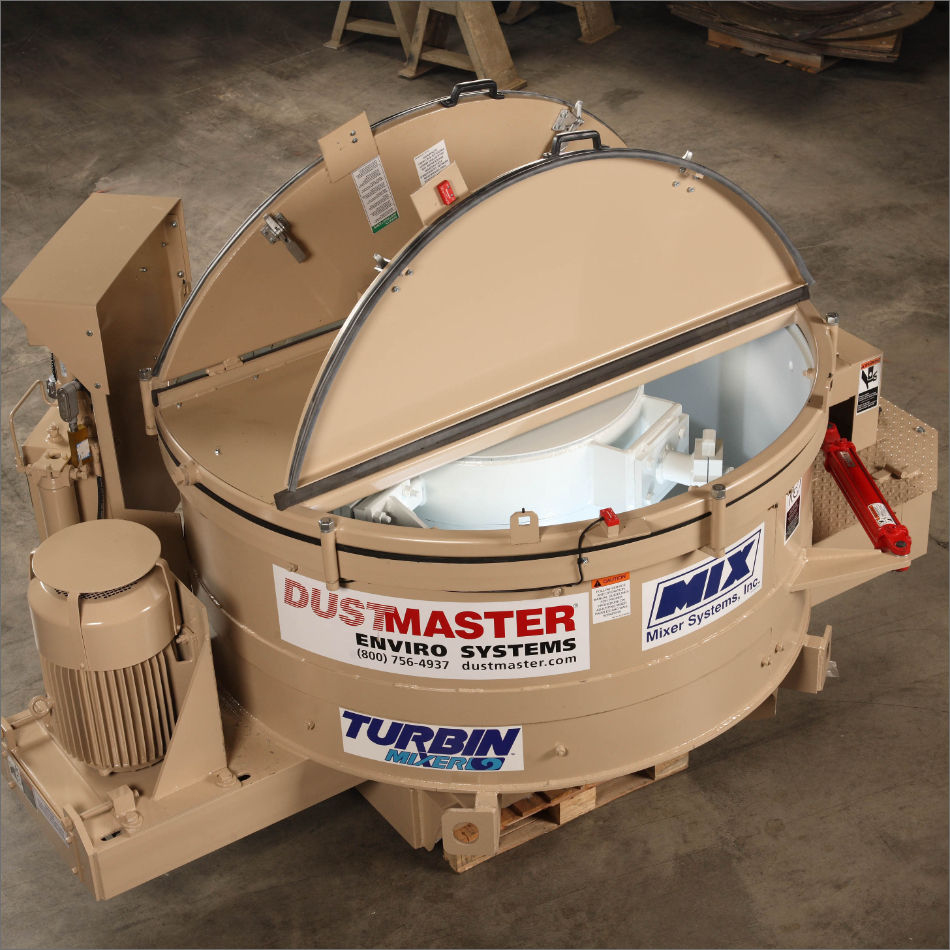
A stock image related to mixer manufacturer.
In chemical manufacturing, mixers are vital for combining various chemicals to create intermediate and final products. The efficiency and safety of production processes are significantly enhanced through the use of high-quality mixers that can handle aggressive substances. Buyers should evaluate the compatibility of mixers with specific chemicals and the durability of materials used in construction to ensure long-term operational reliability.
How Do Mixers Contribute to Construction Materials?
In the construction materials industry, mixer manufacturers provide equipment for blending components like cement, sand, and aggregates to produce concrete and other building materials. The quality of the mix directly impacts the strength and durability of the final product, making it essential for construction projects. Buyers should ensure that mixers can handle varying batch sizes and meet industry standards for material quality to achieve optimal results.
Related Video: Ribbon blender: Video for horizontal ribbon mixer SYLW(2), with double ribbons(single shaft)
3 Common User Pain Points for ‘mixer manufacturer’ & Their Solutions
Scenario 1: Difficulty in Finding the Right Mixer for Specific Applications
The Problem:
International B2B buyers often struggle to identify the ideal mixer that meets their unique operational needs. For instance, a beverage manufacturer in South America may require a mixer capable of handling viscous materials, while a cosmetics company in Europe might need one that ensures gentle mixing to preserve delicate ingredients. The challenge is compounded by a lack of detailed product specifications and the overwhelming variety of options available, leading to potential operational inefficiencies or financial losses if the wrong mixer is purchased.
The Solution:
To effectively source the right mixer, buyers should first conduct a thorough needs assessment, outlining the specific materials, desired mixing outcomes, and production scale. Engaging with a reputable mixer manufacturer to discuss these requirements is crucial. Buyers should request detailed product specifications, including viscosity handling capabilities and mixing technology (e.g., paddle mixers, ribbon blenders, etc.). Additionally, leveraging product demos or trials can provide firsthand experience before making a significant investment. Collaborating with manufacturers that offer customization options may also be beneficial, allowing for tailored solutions that fit unique production processes.
Scenario 2: Concerns Over Equipment Reliability and Maintenance
The Problem:
B2B buyers are often wary of the long-term reliability of mixers, particularly in high-demand environments. For example, a food processing plant in Africa might fear that equipment failures could lead to production downtime, affecting supply chains and profitability. Maintenance can also be a concern, as buyers may not have immediate access to local service support or spare parts, further complicating operational continuity.
The Solution:
To mitigate these risks, buyers should prioritize manufacturers that provide comprehensive warranties and robust after-sales support. Establishing a relationship with a supplier who offers regular maintenance services and readily available spare parts can enhance reliability. Buyers should inquire about the manufacturer’s track record in their industry and seek testimonials or case studies from similar companies. Additionally, investing in training for operational staff on proper mixer maintenance can prevent breakdowns and prolong equipment life, ensuring that the mixer remains a dependable asset in their production line.
Scenario 3: Navigating Compliance and Regulatory Standards
The Problem:
International B2B buyers often face challenges in ensuring that their mixers comply with local and international regulatory standards. For example, a pharmaceutical company in the Middle East may need to adhere to strict health and safety regulations, while a dairy producer in Europe must comply with food safety standards. Failure to meet these regulations can result in severe penalties, product recalls, or damage to brand reputation.
The Solution:
Buyers should conduct thorough research on the regulatory requirements specific to their industry and region before sourcing mixers. Engaging with manufacturers who are well-versed in compliance issues can provide valuable insights. It’s advisable to request certifications and documentation that demonstrate compliance with relevant standards, such as ISO or FDA regulations. Furthermore, buyers should consider suppliers that offer mixers designed with regulatory requirements in mind, such as easy-to-clean surfaces and materials that meet safety standards. Regular audits and updates from the manufacturer regarding changes in compliance can also ensure ongoing adherence to regulations, protecting both the company and its customers.
Strategic Material Selection Guide for mixer manufacturer
When selecting materials for mixer manufacturing, it is crucial to consider various factors that affect performance, durability, and cost. Below, we analyze four common materials used in mixer manufacturing, focusing on their properties, pros and cons, and specific considerations for international B2B buyers.
What Are the Key Properties of Stainless Steel in Mixer Manufacturing?
Stainless Steel is a widely used material in mixer manufacturing due to its excellent corrosion resistance and high strength. It typically has a temperature rating up to 800°F (427°C) and can withstand high pressure, making it suitable for various mixing applications.
Pros: Stainless steel is durable, easy to clean, and resistant to rust and staining, which is essential for food and beverage applications. It also has a long lifespan, which reduces replacement costs over time.
Cons: The primary drawback of stainless steel is its higher cost compared to other materials, which may not be suitable for budget-sensitive projects. Additionally, its manufacturing process can be complex, requiring specialized equipment and expertise.
Impact on Application: Stainless steel is ideal for applications involving food, pharmaceuticals, and chemicals due to its inert nature and ability to maintain hygiene.
Considerations for International Buyers: Buyers from Africa, South America, the Middle East, and Europe should ensure compliance with international standards such as ASTM and DIN for food-grade stainless steel. Understanding local regulations regarding food safety and material certifications is also vital.
How Does Aluminum Compare as a Material for Mixers?
Aluminum is another popular choice for mixer components, known for its lightweight and good thermal conductivity. It can handle temperatures up to 600°F (316°C) and is less resistant to corrosion than stainless steel.
Pros: The lightweight nature of aluminum makes it easier to handle and install, reducing shipping costs. It is also generally less expensive than stainless steel, making it a cost-effective option for many applications.
Cons: Aluminum is more prone to corrosion, especially in humid or acidic environments, which can lead to a shorter lifespan. It may also not be suitable for high-pressure applications.
Impact on Application: Aluminum is often used in applications where weight is a concern, such as portable mixers or equipment that requires frequent relocation.
Considerations for International Buyers: Buyers should verify that the aluminum used meets relevant standards such as JIS for industrial applications. Understanding the local environment’s impact on aluminum’s durability is also crucial.
What Are the Advantages of Using Plastic in Mixer Manufacturing?
Plastic materials, such as polypropylene or polycarbonate, are increasingly used in mixer manufacturing, particularly for components that require flexibility and resistance to chemicals.
Pros: Plastics are lightweight, resistant to corrosion, and can be molded into complex shapes, making them versatile for various designs. They are also generally less expensive than metals.
Cons: The primary limitation of plastic is its lower strength compared to metals, which may not withstand high temperatures or pressures. Additionally, some plastics can degrade over time when exposed to UV light or certain chemicals.
Impact on Application: Plastic is suitable for applications that require chemical resistance or where weight is a significant factor, such as in portable mixers.
Considerations for International Buyers: Buyers should ensure that the plastics used comply with local safety standards and regulations. Understanding the chemical compatibility of plastics with the intended media is essential.
Why is Cast Iron Still Relevant in Mixer Manufacturing?
Cast Iron is a traditional material used in mixer manufacturing, particularly for heavy-duty applications. It can withstand high temperatures and pressures, making it suitable for industrial mixers.
Pros: Cast iron is highly durable and provides excellent vibration dampening, which can enhance mixing performance. It is also relatively inexpensive compared to stainless steel.
Cons: The weight of cast iron can be a disadvantage for certain applications, making it less portable. Additionally, it is prone to rusting if not properly maintained.
Impact on Application: Cast iron is ideal for industrial applications where durability and strength are paramount, such as in construction or heavy machinery.
Considerations for International Buyers: Buyers should consider the local availability of cast iron and ensure it meets relevant industry standards. Understanding maintenance requirements to prevent rust is also crucial.
Summary Table of Material Selection for Mixer Manufacturing
Material | Typical Use Case for mixer manufacturer | Key Advantage | Key Disadvantage/Limitation | Relative Cost (Low/Med/High) |
---|---|---|---|---|
Stainless Steel | Food and beverage mixers | Excellent corrosion resistance | Higher cost and complex manufacturing | High |
Aluminum | Portable mixers | Lightweight and cost-effective | Prone to corrosion | Medium |
Plastic | Chemical-resistant applications | Versatile and inexpensive | Lower strength and UV sensitivity | Low |
Cast Iron | Heavy-duty industrial mixers | Highly durable and vibration dampening | Heavy and prone to rust | Medium |
This analysis provides a comprehensive overview of material selection for mixer manufacturing, helping international B2B buyers make informed decisions based on performance, cost, and compliance with local standards.
In-depth Look: Manufacturing Processes and Quality Assurance for mixer manufacturer
What Are the Main Stages of Manufacturing for Mixer Manufacturers?
The manufacturing process for mixers typically involves several key stages: material preparation, forming, assembly, and finishing. Understanding these stages can help international B2B buyers assess the quality and reliability of mixer manufacturers.
Material Preparation: Ensuring Quality from the Start
The first step in the manufacturing process is material preparation. High-quality raw materials, such as stainless steel, aluminum, and durable plastics, are essential for producing reliable mixers. Suppliers often conduct thorough inspections to ensure that materials meet specific standards before they enter the manufacturing phase. Buyers should inquire about the sourcing of these materials and any certifications that may be relevant, such as ISO certifications or compliance with local regulations.
How Is Forming Achieved in Mixer Manufacturing?
The forming stage involves shaping the prepared materials into the components required for mixers. This can include processes such as casting, forging, or machining. Advanced technologies, such as CNC (Computer Numerical Control) machining, are commonly employed to ensure precision in forming parts like mixing blades, housing, and motor mounts. Buyers should look for manufacturers that utilize modern technology, as this often correlates with higher precision and quality in the final product.
What Does the Assembly Process Look Like?
Once the components are formed, they move to the assembly stage. This is where the various parts are put together to create the final mixer product. Skilled technicians or automated systems are typically used in this phase to ensure that all components fit together correctly and function as intended. It is crucial for B2B buyers to ask about the assembly processes, including whether manufacturers employ lean manufacturing principles, which can reduce waste and improve efficiency.
Finishing Touches: Why Are They Important?
The finishing stage includes painting, coating, and polishing the mixer to enhance its aesthetic appeal and protect it from corrosion and wear. Various techniques may be employed, including powder coating or anodizing, depending on the materials used. Buyers should inquire about the finishing processes to ensure that the mixers they purchase will have a long lifespan and maintain their appearance over time.
What Are the Key Quality Assurance Standards for Mixer Manufacturers?
Quality assurance (QA) is critical in the manufacturing of mixers, especially when considering international standards. Buyers should look for manufacturers that adhere to recognized quality assurance protocols to ensure product reliability and safety.
Which International Standards Should Buyers Be Aware Of?
One of the most widely recognized standards is ISO 9001, which outlines the requirements for a quality management system. Compliance with this standard indicates that a manufacturer has processes in place to ensure consistent quality in their products. Additionally, industry-specific standards such as CE marking (for European markets) and API standards (for the oil and gas industry) can also be relevant, depending on the intended application of the mixers.
How Are Quality Control Checkpoints Established?
Quality control (QC) checkpoints are essential throughout the manufacturing process. Common checkpoints include:
- Incoming Quality Control (IQC): This involves inspecting raw materials before they enter production to ensure they meet specified quality standards.
- In-Process Quality Control (IPQC): Conducted at various stages of production, this ensures that components are being manufactured correctly and that any issues are addressed immediately.
- Final Quality Control (FQC): This is the last inspection before products are shipped to customers, ensuring that the finished mixers meet all specifications and quality standards.
B2B buyers should ask potential suppliers about their QC processes and the frequency of inspections at each stage.
What Testing Methods Are Commonly Used in Mixer Manufacturing?
Quality assurance in mixer manufacturing also involves various testing methods to verify product performance and durability. Some common testing methods include:
- Performance Testing: Assessing the mixer’s efficiency and effectiveness in blending different materials.
- Durability Testing: Subjecting mixers to extreme conditions to evaluate their lifespan and resistance to wear and tear.
- Safety Testing: Ensuring that the product complies with safety regulations and does not pose any risks to users.
International B2B buyers should verify whether manufacturers provide testing reports and certifications to substantiate their claims regarding product quality.
How Can Buyers Verify Supplier Quality Control Practices?
For B2B buyers, particularly those operating in Africa, South America, the Middle East, and Europe, verifying a supplier’s quality control practices is essential. Here are some actionable steps:
-
Conduct Supplier Audits: Regular audits can help buyers assess the manufacturing processes and quality assurance practices of potential suppliers. This can include on-site visits to evaluate facilities and processes firsthand.
-
Request Quality Control Reports: Suppliers should be willing to provide documentation detailing their QC processes, including records of inspections and testing results.
-
Engage Third-Party Inspection Services: Utilizing third-party inspection services can provide an unbiased assessment of the quality of products before they are shipped. These services can offer detailed reports on compliance with international standards and specifications.
What Are the QC and Certification Nuances for International Buyers?
Understanding the nuances of quality control and certification is vital for international B2B buyers. Different regions may have varying standards and regulations, which can impact the import and use of mixers. Buyers should consider the following:
- Local Regulations: Familiarize yourself with the specific regulations and standards that apply to your region. This can help avoid compliance issues and ensure product safety.
- Cultural Considerations: Different regions may have varying expectations regarding quality and customer service. Understanding these cultural differences can help buyers manage relationships with suppliers more effectively.
By focusing on these critical areas—manufacturing processes, quality assurance standards, testing methods, and verification practices—B2B buyers can make informed decisions when selecting mixer manufacturers. This knowledge will not only enhance product quality but also foster long-term partnerships with reliable suppliers.
Practical Sourcing Guide: A Step-by-Step Checklist for ‘mixer manufacturer’
In today’s global market, sourcing the right mixer manufacturer is essential for businesses seeking to enhance their production capabilities. This guide provides a structured approach to help B2B buyers navigate the procurement process effectively. Below is a step-by-step checklist to streamline your sourcing efforts and ensure you make informed decisions.
Step 1: Define Your Technical Specifications
Clearly outlining your technical requirements is fundamental. This includes understanding the types of mixers you need—be it analog, digital, or specialized for specific applications. Consider factors such as capacity, compatibility with existing equipment, and any necessary features like stem separation technology or real-time mixing capabilities.
- Capacity Needs: Determine how many channels you require.
- Technical Features: List essential features, such as effects processing or remote control capabilities.
Step 2: Conduct Market Research for Suppliers
Take time to research potential suppliers in the mixer manufacturing sector. Utilize online resources, trade directories, and industry forums to compile a list of manufacturers that align with your requirements. Understanding the market landscape will help you identify reputable suppliers and emerging companies.
- Industry Reports: Review reports that analyze market trends and key players.
- Competitor Analysis: Look at where your competitors source their mixers.
Step 3: Evaluate Potential Suppliers
Before committing to any supplier, thorough evaluation is critical. Request detailed company profiles, product catalogs, and case studies showcasing their work with similar clients. Seek references from businesses within your region to assess the supplier’s reliability and product quality.
- Supplier Background: Investigate their history and reputation within the industry.
- Case Studies: Look for evidence of successful projects that align with your needs.
Step 4: Verify Certifications and Compliance
Ensure that potential suppliers adhere to relevant industry standards and regulations. Certifications such as ISO or CE mark can indicate a commitment to quality and safety. This step is especially crucial for international buyers who must comply with local regulations.
- Certification Verification: Request copies of certifications and check their validity.
- Compliance with Local Laws: Understand the regulations in your region regarding mixer equipment.
Step 5: Request Samples or Prototypes
Before finalizing any orders, request samples or prototypes of the mixers you intend to procure. Testing the product ensures it meets your specifications and quality expectations. This step is vital to mitigate risks associated with bulk purchases.
- Testing Performance: Evaluate the mixers in real-world scenarios relevant to your operations.
- Feedback from Teams: Gather input from your technical team on the usability and features.
Step 6: Negotiate Terms and Pricing
Once you’ve selected a supplier, engage in negotiations to establish favorable terms. Discuss pricing, payment terms, delivery schedules, and warranty policies. A clear agreement helps to prevent misunderstandings and sets the stage for a successful partnership.
- Transparent Pricing: Ensure all costs are disclosed, including shipping and potential tariffs.
- Delivery Expectations: Agree on timelines that align with your production schedule.
Step 7: Establish a Communication Plan
Effective communication is key to a successful supplier relationship. Establish a clear line of communication for updates, inquiries, and feedback throughout the procurement process. This will help address any issues that arise promptly and maintain a good working relationship.
- Regular Check-ins: Schedule periodic updates to discuss progress and challenges.
- Dedicated Contacts: Designate specific contacts on both sides for streamlined communication.
By following this checklist, international B2B buyers can effectively source mixer manufacturers that meet their operational needs while ensuring quality and compliance.
Comprehensive Cost and Pricing Analysis for mixer manufacturer Sourcing
What Are the Key Cost Components in Mixer Manufacturing?
Understanding the cost structure of mixer manufacturing is essential for international B2B buyers. The primary cost components include:
-
Materials: Raw materials such as metals, plastics, and electronic components form the bulk of manufacturing costs. The choice of materials directly affects durability, performance, and ultimately the price.
-
Labor: Labor costs vary significantly by region. Countries with lower labor costs may offer more competitive pricing, but this can also impact quality. It’s crucial to assess the skill level of the workforce to ensure it meets your quality standards.
-
Manufacturing Overhead: This includes indirect costs such as utilities, rent, and administrative expenses. Efficient management of overhead can lead to lower prices for buyers.
-
Tooling: The cost of molds and other tooling is a significant upfront investment. Buyers should inquire about the tooling lifespan and the potential for reusability in future orders.
-
Quality Control (QC): Implementing stringent QC measures is essential to maintaining product reliability. However, this adds to the overall cost. Understanding the QC processes of a supplier can provide insights into the expected quality.
-
Logistics: Shipping, handling, and warehousing costs can be substantial, particularly for international buyers. Factors such as distance, shipping method, and customs duties should be considered.
-
Margin: Manufacturers typically apply a profit margin to their costs. This varies by supplier and can be influenced by market demand and competition.
How Do Price Influencers Affect Mixer Manufacturing Costs?
Several factors can influence the pricing of mixers, including:
-
Volume/MOQ: Manufacturers often offer better pricing for larger orders due to economies of scale. Understanding the minimum order quantities (MOQs) can help buyers optimize their purchasing strategy.
-
Specifications and Customization: Customized products typically incur higher costs due to additional design and manufacturing processes. Buyers should balance the need for customization with budget constraints.
-
Materials and Quality Certifications: High-quality materials and certifications (such as ISO standards) can significantly affect pricing. Buyers should evaluate whether the added costs align with their quality requirements.
-
Supplier Factors: Supplier reputation, reliability, and production capacity can influence pricing. Engaging with established suppliers may offer better assurance of quality and service.
-
Incoterms: Understanding the Incoterms (International Commercial Terms) that define the responsibilities of buyers and sellers can impact total costs, including shipping and insurance.
What Tips Can Help Buyers Optimize Costs When Sourcing Mixers?
For international B2B buyers, particularly from Africa, South America, the Middle East, and Europe, several strategies can enhance cost-efficiency:
-
Negotiate: Leverage your purchasing power by negotiating pricing and terms. Building a long-term relationship with suppliers can lead to better deals.
-
Consider Total Cost of Ownership (TCO): Evaluate not just the purchase price but also ongoing costs such as maintenance, repairs, and energy consumption. A lower initial cost may lead to higher long-term expenses.
-
Be Aware of Pricing Nuances: Pricing can vary by region due to local economic conditions, tariffs, and currency fluctuations. Staying informed about these factors can help in making better purchasing decisions.
-
Evaluate Multiple Suppliers: Don’t settle for the first quote. Comparing multiple suppliers can reveal significant price differences and provide leverage in negotiations.
-
Stay Informed on Market Trends: Keeping abreast of industry trends and technological advancements can provide insights into cost-saving opportunities and innovative solutions.
Disclaimer on Indicative Prices
Please note that the prices discussed in this analysis are indicative and can vary based on market conditions, supplier negotiations, and specific buyer requirements. Always conduct thorough research and request detailed quotes to ensure accurate pricing for your specific needs.
Alternatives Analysis: Comparing mixer manufacturer With Other Solutions
When evaluating the best solutions for mixing, it is crucial for international B2B buyers to consider not only the primary mixer manufacturer but also alternative technologies that can fulfill similar roles. This analysis will compare traditional mixer manufacturers with software-based solutions and hybrid systems, allowing buyers to make informed decisions based on specific needs and operational contexts.
Comparison Aspect | Mixer Manufacturer | VirtualDJ (Software Solution) | Hybrid DJ Systems (Hardware + Software) |
---|---|---|---|
Performance | High-quality audio mixing with robust hardware capabilities | Excellent real-time mixing with advanced features like stem separation | Good performance, but reliant on both hardware and software capabilities |
Cost | High initial investment, often requiring additional components | Generally lower cost, with free versions available for non-commercial use | Moderate to high cost, depending on the hardware used |
Ease of Implementation | Requires specialized knowledge for setup and operation | User-friendly with intuitive interfaces, suitable for beginners | Requires some technical skill for integration of hardware and software |
Maintenance | Regular maintenance needed; parts can be expensive | Minimal maintenance; software updates are straightforward | Requires ongoing maintenance of both hardware and software components |
Best Use Case | Professional settings needing high-quality sound | DJ events, parties, and casual settings with flexibility | Professional events that require a mix of traditional and modern DJ techniques |
What are the advantages and disadvantages of using VirtualDJ as an alternative?
VirtualDJ stands out as a software solution that offers extensive features for mixing without the need for physical hardware. Its advanced capabilities, such as real-time stem separation, allow DJs to create live mashups and seamless transitions, which can elevate the overall performance. Additionally, it is cost-effective, with free versions available, making it accessible for new DJs. However, it may not provide the same audio fidelity that high-end hardware mixers can offer, and users may face limitations in live performance settings where hardware reliability is crucial.
How do hybrid DJ systems compare to traditional mixers?
Hybrid DJ systems combine the advantages of both hardware and software, allowing DJs to leverage the tactile experience of physical controls while also utilizing the powerful features of software like VirtualDJ. This flexibility can enhance creative expression during performances. However, the complexity of setting up and maintaining both hardware and software can be daunting for some users, and the costs can add up, especially if high-quality hardware is required. This makes it essential for buyers to evaluate their technical skills and budget constraints when considering this option.
Conclusion: How to choose the right mixing solution for your business needs?
For international B2B buyers, the choice between a traditional mixer manufacturer, software solutions like VirtualDJ, or hybrid systems depends on specific operational needs, budget, and expertise. If high fidelity and professional-grade sound are paramount, investing in a reputable mixer manufacturer may be the best choice. Conversely, if flexibility and cost-effectiveness are more critical, software solutions could provide the necessary features without the hefty price tag. Hybrid systems offer a middle ground but require careful consideration of setup complexity and ongoing maintenance. Ultimately, understanding the unique requirements of your events and audience will guide you to the most suitable mixing solution.
Essential Technical Properties and Trade Terminology for mixer manufacturer
What Are the Essential Technical Properties for Mixer Manufacturers?
When evaluating mixers for industrial applications, understanding the technical specifications is crucial for making informed purchasing decisions. Here are several key properties that B2B buyers should consider:
1. Material Grade
The material grade of a mixer significantly influences its durability and performance. Common materials include stainless steel, aluminum, and high-density polyethylene (HDPE). Stainless steel is often preferred for its corrosion resistance and longevity, particularly in food processing or chemical industries. Buyers should assess the material’s suitability based on the specific application and environmental conditions.
2. Tolerance Levels
Tolerance refers to the permissible limit of variation in a mixer’s dimensions. High precision is vital in applications requiring exact mixing ratios. For example, in pharmaceutical manufacturing, deviations can affect product quality. Buyers should inquire about the manufacturer’s tolerance standards to ensure compliance with industry regulations and achieve desired outcomes.
3. Power Rating
The power rating, usually measured in watts or horsepower, indicates the mixer’s capacity to handle various materials. Higher power ratings allow for the mixing of denser substances and larger volumes. B2B buyers must match the power rating with their operational requirements to prevent equipment failure and ensure efficiency.
4. Mixing Speed and Control
Different applications require different mixing speeds. Variable speed control allows operators to adjust the speed according to the material being mixed, which is crucial for achieving uniformity. Buyers should consider mixers that offer flexible speed settings to enhance versatility and performance in diverse applications.
5. Safety Features
Safety is paramount in industrial environments. Features such as overload protection, emergency stop buttons, and safety interlocks prevent accidents and equipment damage. B2B buyers should prioritize mixers that comply with safety standards and regulations relevant to their industry.
What Are Common Trade Terminology and Concepts in Mixer Manufacturing?
Understanding industry jargon can help B2B buyers navigate the procurement process more effectively. Here are some essential terms:
1. OEM (Original Equipment Manufacturer)
An OEM is a company that produces parts or equipment that may be marketed by another manufacturer. In the mixer industry, buyers may work with OEMs to customize mixers to fit specific operational needs. Understanding OEM relationships can facilitate better sourcing decisions.
2. MOQ (Minimum Order Quantity)
MOQ refers to the smallest number of units a supplier is willing to sell. This term is crucial for B2B buyers when negotiating orders, especially for smaller companies that may not need large quantities. Knowing the MOQ helps buyers plan their purchasing strategy and manage inventory effectively.
3. RFQ (Request for Quotation)
An RFQ is a document that buyers send to suppliers requesting pricing and other details for specific products. It is an essential step in the procurement process, allowing buyers to compare offers and make informed decisions. Including detailed specifications in an RFQ can lead to more accurate quotes and better negotiations.
4. Incoterms (International Commercial Terms)
Incoterms are standardized terms used in international trade to define the responsibilities of buyers and sellers. They clarify who pays for shipping, insurance, and tariffs. B2B buyers should familiarize themselves with these terms to ensure smooth transactions and avoid unexpected costs.
5. Lead Time
Lead time refers to the time taken from placing an order to receiving the product. Understanding lead times is essential for effective inventory management and production scheduling. Buyers should communicate their timeline expectations to suppliers to ensure timely delivery and avoid operational disruptions.
By grasping these essential technical properties and trade terminology, B2B buyers can enhance their procurement strategies and make better-informed decisions when sourcing mixers for their operations.
Navigating Market Dynamics and Sourcing Trends in the mixer manufacturer Sector
What Are the Key Market Trends Shaping the Mixer Manufacturing Sector?
The global mixer manufacturing market is witnessing significant transformation, driven by technological advancements and changing consumer preferences. Key trends include the rise of automation in production processes, which enhances efficiency and reduces operational costs. Moreover, the integration of smart technologies, such as IoT-enabled mixers, is gaining traction, allowing for remote monitoring and control, which is particularly appealing to B2B buyers looking for operational efficiency.
International B2B buyers from Africa, South America, the Middle East, and Europe must also be aware of regional preferences that influence sourcing decisions. In Africa, for example, there is a growing demand for affordable and durable mixers suitable for local conditions. In contrast, buyers in Europe are increasingly favoring high-end, feature-rich mixers that offer advanced functionalities for professional use. Additionally, South American buyers are prioritizing mixers that can handle diverse materials, reflecting the region’s varied industrial needs.
Emerging sourcing trends include the shift towards direct sourcing from manufacturers to reduce costs and improve supply chain transparency. This trend is particularly relevant for buyers in regions with rapidly evolving markets, as it allows for tailored solutions that meet specific local demands.
How Is Sustainability Influencing Sourcing Decisions in the Mixer Manufacturing Sector?
Sustainability has become a cornerstone in the decision-making process for international B2B buyers in the mixer manufacturing sector. The environmental impact of production processes, including energy consumption and waste generation, is under scrutiny. As a result, manufacturers are increasingly adopting sustainable practices, such as utilizing recycled materials and reducing emissions during production.
The importance of ethical supply chains cannot be overstated. Buyers are now more inclined to partner with manufacturers that prioritize fair labor practices and social responsibility. Certifications such as ISO 14001 (Environmental Management) and FSC (Forest Stewardship Council) for materials used in mixers are becoming essential criteria for sourcing decisions. These certifications not only enhance brand reputation but also align with the values of environmentally conscious consumers and businesses.
Additionally, the move towards green materials, such as biodegradable plastics and energy-efficient components, is reshaping product offerings in the mixer market. B2B buyers are encouraged to seek out suppliers that demonstrate a commitment to sustainable practices, as this can lead to long-term cost savings and improved marketability.
What Historical Developments Have Shaped the Mixer Manufacturing Industry?
The mixer manufacturing industry has evolved significantly since its inception. Initially, mixers were simple mechanical devices designed for basic mixing tasks. However, advancements in technology during the late 20th century introduced electric mixers, revolutionizing production capabilities across various sectors, including food and beverage, pharmaceuticals, and construction.
As industries grew and diversified, so did the mixer manufacturing sector. The introduction of digital technology and automation in the 21st century further transformed the landscape, allowing for greater precision and efficiency. Today, the focus is on integrating smart technologies that enable real-time monitoring and data analysis, providing businesses with insights that were previously unattainable.
These historical advancements have laid the foundation for the current state of the mixer manufacturing sector, where innovation, sustainability, and ethical sourcing are paramount. Understanding this evolution is crucial for B2B buyers looking to navigate the complexities of the market and make informed sourcing decisions.
Frequently Asked Questions (FAQs) for B2B Buyers of mixer manufacturer
-
How do I select the right mixer manufacturer for my business needs?
When selecting a mixer manufacturer, start by defining your specific requirements, including the type of mixer, production capacity, and any unique features you may need. Research potential suppliers, focusing on their experience, reputation, and customer reviews. Request samples or demos to assess product quality and performance. Additionally, consider their ability to provide customization options and technical support, which can be crucial for long-term partnerships. -
What are the key factors to consider when vetting a mixer supplier?
Key factors include the manufacturer’s production capabilities, quality assurance processes, and compliance with international standards. Verify their certifications, such as ISO, and assess their financial stability to ensure they can meet your demands consistently. Additionally, evaluate their responsiveness to inquiries and willingness to engage in transparent communication, as these traits indicate a reliable business partner. -
What customization options are typically available from mixer manufacturers?
Most mixer manufacturers offer various customization options, including size, material, color, and functionality. Some may provide tailored solutions, such as specific mixing speeds, noise levels, or integrated technology for enhanced performance. Discuss your unique requirements upfront to determine the extent of customization available and ensure that the manufacturer can meet your expectations. -
What is the minimum order quantity (MOQ) for mixers from manufacturers?
Minimum order quantities can vary significantly depending on the manufacturer and the type of mixer. Generally, MOQs can range from a few units to several hundred. It’s crucial to discuss this during your initial conversations with suppliers, as they may offer flexibility based on your business needs, especially if you are a new customer or require a unique product. -
What payment terms should I expect when working with a mixer manufacturer?
Payment terms can vary widely among manufacturers. Common arrangements include a deposit upon order confirmation, followed by the balance due before shipment. Some suppliers may offer credit terms or payment plans for larger orders. Always clarify payment methods accepted (e.g., wire transfer, credit card) and ensure that terms are documented in your contract to avoid misunderstandings. -
How can I ensure quality assurance when sourcing mixers internationally?
To ensure quality assurance, request samples before placing a large order and evaluate the manufacturer’s quality control processes. Consider third-party inspections during production and before shipment to verify compliance with your specifications. Additionally, review the manufacturer’s warranty and return policies to safeguard your investment in case of defects or discrepancies. -
What logistics considerations should I keep in mind when importing mixers?
When importing mixers, consider shipping methods, lead times, and customs regulations specific to your country. Work with a logistics provider experienced in international shipping to navigate the complexities of import duties and taxes. Ensure that the manufacturer can provide all necessary documentation, including invoices and certificates of origin, to streamline the customs clearance process. -
What are the advantages of sourcing mixers from manufacturers in different regions?
Sourcing mixers from different regions can offer various advantages, such as cost savings, access to unique technologies, and diverse product offerings. For instance, manufacturers in Europe may provide high-quality engineering, while those in Asia might offer competitive pricing. Additionally, regional suppliers can enhance supply chain resilience and reduce lead times, contributing to improved operational efficiency.
Important Disclaimer & Terms of Use
⚠️ Important Disclaimer
The information provided in this guide, including content regarding manufacturers, technical specifications, and market analysis, is for informational and educational purposes only. It does not constitute professional procurement advice, financial advice, or legal advice.
While we have made every effort to ensure the accuracy and timeliness of the information, we are not responsible for any errors, omissions, or outdated information. Market conditions, company details, and technical standards are subject to change.
B2B buyers must conduct their own independent and thorough due diligence before making any purchasing decisions. This includes contacting suppliers directly, verifying certifications, requesting samples, and seeking professional consultation. The risk of relying on any information in this guide is borne solely by the reader.
Strategic Sourcing Conclusion and Outlook for mixer manufacturer
Why Is Strategic Sourcing Crucial for Mixer Manufacturers?
In the rapidly evolving landscape of mixer manufacturing, strategic sourcing emerges as a vital component for international B2B buyers. By leveraging advanced technologies and innovative features, such as real-time track separation and seamless transitions, manufacturers can enhance their product offerings and meet the diverse needs of DJs and audio professionals. Buyers should prioritize suppliers that not only offer cutting-edge technology but also demonstrate reliability, efficiency, and a deep understanding of market trends.
How Can International Buyers Benefit from Effective Sourcing Strategies?
For buyers in Africa, South America, the Middle East, and Europe, adopting a strategic sourcing approach can lead to significant cost savings and improved supply chain resilience. Engaging with manufacturers who provide comprehensive support—ranging from product training to ongoing technical assistance—will facilitate smoother operations and ultimately enhance customer satisfaction. This approach ensures that buyers are equipped with the latest innovations and capabilities in mixer technology.
What’s Next for B2B Buyers in the Mixer Industry?
Looking ahead, the mixer manufacturing sector is poised for continued growth, driven by technological advancements and increasing demand for high-quality sound solutions. International B2B buyers are encouraged to stay proactive, exploring new partnerships and leveraging data-driven insights to inform their sourcing decisions. By doing so, they will not only remain competitive but also play a pivotal role in shaping the future of the audio industry. Embrace the potential of strategic sourcing today to unlock new opportunities for success.