Unlock Quality: The Ultimate Carbon Fiber Manufacturer Guide (2025)
Introduction: Navigating the Global Market for carbon fiber manufacturer
In today’s competitive landscape, sourcing a reliable carbon fiber manufacturer can be a daunting challenge for international B2B buyers, especially in regions like Africa, South America, the Middle East, and Europe. With the growing demand for high-performance materials across various industries, understanding the nuances of the carbon fiber market is essential. This comprehensive guide is designed to empower decision-makers by providing in-depth insights into the types of carbon fiber available, their diverse applications, and practical strategies for supplier vetting and cost management.
Buyers will learn about the various grades of carbon fiber, including standard, intermediate, and high-modulus options, and how these materials can be tailored for specific applications such as aerospace, automotive, and sports equipment. Additionally, we will explore the critical factors that influence pricing, including raw material sourcing and production techniques, helping you to better estimate costs and negotiate effectively with suppliers.
By equipping international B2B buyers with actionable insights and best practices, this guide aims to streamline your purchasing decisions in the carbon fiber sector. Whether you are a manufacturer in Nigeria looking to enhance product performance or a procurement officer in Germany seeking sustainable material solutions, our expert analysis will ensure that you navigate the global market with confidence and clarity.
Understanding carbon fiber manufacturer Types and Variations
Type Name | Key Distinguishing Features | Primary B2B Applications | Brief Pros & Cons for Buyers |
---|---|---|---|
Standard Modulus | Offers good strength-to-weight ratio, cost-effective | Aerospace, automotive, sporting goods | Pros: Affordable, widely available. Cons: Lower stiffness compared to other types. |
Intermediate Modulus | Balances strength and stiffness; versatile | Industrial applications, marine, automotive | Pros: Good performance, suitable for various uses. Cons: Higher cost than standard modulus. |
High Modulus | Extremely stiff, superior tensile strength | Aerospace, high-performance automotive | Pros: Excellent performance in demanding applications. Cons: Expensive, limited availability. |
Ultra-High Modulus | Exceptional stiffness, specialized manufacturing | Aerospace, advanced engineering | Pros: Unmatched performance in critical applications. Cons: Very high cost, niche market. |
Prepreg Carbon Fiber | Pre-impregnated with resin, ready for molding | Aerospace, sports equipment, automotive parts | Pros: Consistent quality, reduced labor costs. Cons: Short shelf life, requires controlled storage. |
What Are the Characteristics of Standard Modulus Carbon Fiber Manufacturers?
Standard modulus carbon fiber manufacturers produce fibers that provide a good balance between strength and cost. This type is widely used in industries such as aerospace and automotive, where affordability is crucial without significantly compromising performance. When considering purchasing from standard modulus manufacturers, B2B buyers should evaluate the supplier’s production capabilities and certifications to ensure consistent quality.
How Does Intermediate Modulus Carbon Fiber Meet B2B Needs?
Intermediate modulus carbon fiber manufacturers create fibers that strike a balance between strength and stiffness. This versatility makes them suitable for a range of industrial applications, including marine and automotive sectors. B2B buyers should consider the specific performance requirements of their applications and the potential for customization when selecting suppliers of intermediate modulus fibers.
What Are the Advantages of High Modulus Carbon Fiber Manufacturers?
High modulus carbon fiber manufacturers focus on producing fibers with exceptional stiffness and tensile strength, making them ideal for high-performance applications in aerospace and automotive industries. While the cost is significantly higher, the performance benefits can justify the investment for critical projects. Buyers should assess the long-term value and specific performance metrics when engaging with these manufacturers.
Why Consider Ultra-High Modulus Carbon Fiber Manufacturers?
Ultra-high modulus carbon fiber manufacturers create specialized products that offer unmatched stiffness and performance, primarily for aerospace and advanced engineering applications. Due to their niche nature and high production costs, these fibers are typically reserved for very specific use cases. B2B buyers must ensure that their projects warrant the investment in ultra-high modulus fibers and consider the supplier’s expertise in this specialized area.
What Are the Benefits of Working with Prepreg Carbon Fiber Manufacturers?
Prepreg carbon fiber manufacturers provide fibers that are pre-impregnated with resin, allowing for straightforward molding processes. This type is commonly used in aerospace and sports equipment due to its consistent quality and reduced labor costs. However, buyers should be mindful of the short shelf life and the need for controlled storage conditions. Evaluating the supplier’s ability to maintain quality and manage inventory effectively is crucial for successful procurement.
Related Video: Complete Carbon Fiber Process Lines from Harper International
Key Industrial Applications of carbon fiber manufacturer
Industry/Sector | Specific Application of Carbon Fiber Manufacturer | Value/Benefit for the Business | Key Sourcing Considerations for this Application |
---|---|---|---|
Aerospace | Aircraft Components | Lightweight materials enhance fuel efficiency and reduce operational costs. | Compliance with stringent aviation regulations; sourcing from certified manufacturers. |
Automotive | High-Performance Vehicle Parts | Improved strength-to-weight ratio leads to better performance and safety. | Need for customization; adherence to safety standards and certifications. |
Sports Equipment | High-End Bicycles and Sports Gear | Enhanced durability and performance for competitive athletes. | Focus on innovative designs; sourcing from specialized carbon fiber manufacturers. |
Renewable Energy | Wind Turbine Blades | Increased energy efficiency and reduced maintenance costs due to lightweight materials. | Consideration of environmental impact; long lead times for production. |
Construction | Structural Reinforcement | Improved strength and longevity of buildings while reducing material costs. | Need for local sourcing options; compliance with building regulations and standards. |
How is Carbon Fiber Used in Aerospace Applications?
In the aerospace industry, carbon fiber is crucial for manufacturing lightweight aircraft components such as wings, fuselages, and tail assemblies. By utilizing carbon fiber, manufacturers can significantly reduce the weight of these components, leading to improved fuel efficiency and lower operational costs. International B2B buyers should ensure that their suppliers comply with stringent aviation regulations, as the quality and safety of aerospace materials are paramount. Additionally, sourcing from certified manufacturers guarantees adherence to industry standards.
What Role Does Carbon Fiber Play in the Automotive Sector?
In the automotive sector, carbon fiber is employed in high-performance vehicle parts such as body panels, chassis components, and interior elements. The material’s exceptional strength-to-weight ratio enhances vehicle performance and safety, making it a preferred choice for luxury and sports car manufacturers. For B2B buyers, customization is often necessary to meet specific design requirements. It is crucial to partner with suppliers who are well-versed in automotive safety standards and can provide the necessary certifications for their products.
How is Carbon Fiber Transforming Sports Equipment?
Carbon fiber is widely used in the production of high-end bicycles and sports gear, where its lightweight and durable properties can significantly improve performance. Athletes benefit from equipment that enhances speed and agility while providing greater resilience against wear and tear. B2B buyers in the sports equipment sector should focus on sourcing from specialized manufacturers who can offer innovative designs and materials tailored for high-performance applications. Understanding the latest trends in sports technology can also guide purchasing decisions.
Why is Carbon Fiber Important for Renewable Energy?
In renewable energy, particularly in wind energy, carbon fiber is utilized to manufacture wind turbine blades. The lightweight nature of carbon fiber allows for larger blades that can capture more wind energy, leading to increased efficiency and reduced maintenance costs. International buyers need to consider the environmental impact of their sourcing decisions and be aware of the longer lead times associated with carbon fiber production. Collaborating with manufacturers who prioritize sustainable practices can enhance the overall value proposition.
How is Carbon Fiber Used in Construction?
In the construction industry, carbon fiber is increasingly used for structural reinforcement, offering significant benefits in terms of strength and longevity. It allows for lighter and more durable building materials, ultimately reducing costs associated with heavy construction. For B2B buyers in this sector, local sourcing options can be essential to meet project timelines and regulatory requirements. Understanding local building codes and standards is critical when selecting carbon fiber products for construction applications, ensuring compliance and safety.
3 Common User Pain Points for ‘carbon fiber manufacturer’ & Their Solutions
Scenario 1: Navigating Quality Consistency in Carbon Fiber Products
The Problem: B2B buyers often grapple with inconsistent quality when sourcing carbon fiber materials. This inconsistency can lead to production delays, product recalls, or even end-user dissatisfaction. For instance, a manufacturer in Nigeria sourcing carbon fiber for aerospace components might receive batches that vary in tensile strength or surface finish. Such discrepancies can severely impact the performance and safety of the final product, putting the buyer’s reputation on the line.
The Solution: To mitigate this issue, buyers should establish a robust quality assurance protocol with their carbon fiber suppliers. This includes requesting detailed material specifications, certifications, and test results for each batch. Implementing a supplier audit process can also help ensure adherence to quality standards. Additionally, consider establishing long-term partnerships with reputable manufacturers who are willing to invest in consistent quality control measures. Utilizing third-party testing services can further validate the material before it enters the production process, ensuring that it meets necessary performance criteria.
Scenario 2: Managing Supply Chain Disruptions in Carbon Fiber Sourcing
The Problem: Supply chain disruptions are a common challenge for international B2B buyers, especially in regions like South America and the Middle East, where logistics can be complicated. A buyer might face unexpected delays due to shipping issues, political instability, or natural disasters that can halt production lines reliant on timely carbon fiber deliveries. These interruptions can lead to significant financial losses and missed deadlines.
The Solution: To combat supply chain vulnerabilities, buyers should diversify their sourcing strategy. Instead of relying on a single supplier, consider establishing relationships with multiple manufacturers across different regions. This strategy not only mitigates risk but also provides leverage in negotiations. Additionally, implementing a just-in-time inventory system can help manage costs and improve flexibility. Buyers should also stay informed about global supply chain trends and geopolitical developments that could affect sourcing. Utilizing logistics management software can provide real-time insights into shipping statuses, enabling better planning and response to potential disruptions.
Scenario 3: Understanding the Technical Specifications of Carbon Fiber
The Problem: Many B2B buyers lack the technical expertise required to fully understand the specifications of carbon fiber products, which can lead to poor purchasing decisions. For instance, a buyer in Europe may not recognize the significance of different resin systems or fiber orientations when selecting carbon fiber for automotive applications. This lack of knowledge can result in selecting materials that do not meet performance requirements or are unsuitable for specific applications.
The Solution: It is essential for buyers to invest in education regarding carbon fiber technologies and specifications. This can involve attending industry workshops, webinars, or training sessions offered by manufacturers. Collaborating with engineers or consultants who specialize in composite materials can also provide valuable insights into the most suitable products for specific applications. Additionally, buyers should demand clear, detailed product documentation from suppliers that outlines the properties and recommended uses of their carbon fiber offerings. This information can guide informed decision-making and ensure that the selected materials align with the intended application, thereby enhancing product performance and reliability.
Strategic Material Selection Guide for carbon fiber manufacturer
When selecting materials for carbon fiber manufacturing, international B2B buyers must consider various factors that influence performance, cost, and suitability for specific applications. Below, we analyze four common materials used in conjunction with carbon fiber, focusing on their key properties, advantages and disadvantages, and implications for buyers from diverse regions, including Africa, South America, the Middle East, and Europe.
What Are the Key Properties of Epoxy Resins in Carbon Fiber Manufacturing?
Epoxy resins are one of the most widely used materials in carbon fiber composites. They offer excellent adhesion, high strength, and superior chemical resistance, making them suitable for various applications, including aerospace and automotive industries. Their temperature resistance typically ranges from -50°C to 120°C, depending on the formulation.
Pros & Cons: The primary advantage of epoxy resins is their outstanding mechanical properties, which enhance the overall performance of carbon fiber composites. However, they can be more expensive than other resins and may require complex curing processes, which can increase manufacturing time and costs.
Impact on Application: Epoxy resins are compatible with a wide range of media, making them ideal for applications requiring chemical resistance. However, buyers must consider local regulations regarding the use of certain epoxy formulations, especially in Europe, where stringent compliance standards exist.
How Do Polyester Resins Compare for Carbon Fiber Applications?
Polyester resins are another common choice for carbon fiber applications, particularly in less demanding environments. They are known for their ease of use and lower cost compared to epoxy resins. Polyester resins typically have a temperature resistance of up to 80°C.
Pros & Cons: The main advantage of polyester resins is their cost-effectiveness, making them suitable for large-scale production. However, they have lower mechanical properties and chemical resistance than epoxy, which may limit their application in high-performance sectors.
Impact on Application: Polyester resins are often used in marine and automotive applications where high mechanical strength is not critical. Buyers from regions like South America and Africa may find these resins more accessible due to their lower price point, but they should weigh the trade-offs in performance.
What Are the Benefits of Vinyl Ester Resins in Carbon Fiber Manufacturing?
Vinyl ester resins combine the advantages of both epoxy and polyester resins, providing enhanced chemical resistance and mechanical properties. They are particularly effective in environments exposed to harsh chemicals and high temperatures, with a typical temperature resistance of up to 120°C.
Pros & Cons: Vinyl esters offer a good balance between performance and cost, making them a versatile choice for various applications. However, they can be more expensive than polyester resins and may require more complex handling during the manufacturing process.
Impact on Application: Their superior chemical resistance makes vinyl esters suitable for applications in the chemical processing industry. Buyers must consider compliance with local regulations, particularly in Europe, where specific standards may apply.
How Do Thermoplastic Composites Enhance Carbon Fiber Performance?
Thermoplastic composites are becoming increasingly popular in carbon fiber manufacturing due to their recyclability and toughness. They can withstand higher temperatures and offer excellent impact resistance, making them suitable for applications in the automotive and aerospace sectors.
Pros & Cons: The key advantage of thermoplastic composites is their ability to be reprocessed, which aligns with sustainability goals. However, they often come with higher costs and require specialized manufacturing processes, which may not be feasible for all manufacturers.
Impact on Application: Thermoplastic composites are particularly beneficial in applications that require high durability and impact resistance. Buyers from the Middle East and Africa should evaluate the availability of technology and expertise in their regions to leverage these materials effectively.
Material | Typical Use Case for carbon fiber manufacturer | Key Advantage | Key Disadvantage/Limitation | Relative Cost (Low/Med/High) |
---|---|---|---|---|
Epoxy Resins | Aerospace and automotive components | Outstanding mechanical properties | Higher cost and complex curing | High |
Polyester Resins | Marine and automotive applications | Cost-effective for large production | Lower mechanical strength | Low |
Vinyl Ester Resins | Chemical processing applications | Enhanced chemical resistance | More expensive than polyester | Medium |
Thermoplastic Composites | Automotive and aerospace sectors | Recyclable and tough | Higher costs and specialized processes | High |
In conclusion, the selection of materials for carbon fiber manufacturing is critical for ensuring optimal performance and compliance with industry standards. International B2B buyers should carefully assess the properties, advantages, and limitations of each material to make informed decisions that align with their specific applications and regional regulations.
In-depth Look: Manufacturing Processes and Quality Assurance for carbon fiber manufacturer
What Are the Main Stages of the Carbon Fiber Manufacturing Process?
The manufacturing of carbon fiber involves several critical stages, each contributing to the material’s overall quality and performance. Understanding these stages is essential for international B2B buyers to make informed purchasing decisions.
-
Material Preparation
The process begins with the preparation of precursor materials, typically polyacrylonitrile (PAN), pitch, or rayon. The selection of precursor impacts the final properties of the carbon fiber. The raw materials undergo a series of chemical treatments to ensure purity and consistency, which is vital for achieving desired mechanical properties. -
Forming
In the forming stage, the prepared precursor is spun into fibers. This can be achieved through various techniques such as wet spinning or dry spinning. The method chosen affects the fiber diameter and mechanical characteristics. It’s essential for buyers to inquire about the forming techniques used by suppliers, as these influence the fiber’s tensile strength and modulus. -
Assembly
Once the fibers are formed, they are assembled into tows or sheets. This assembly can be done through processes like weaving or braiding, depending on the intended application. Buyers should consider the assembly method as it impacts the fiber’s alignment and, consequently, the composite material’s strength. -
Finishing
The final stage involves surface treatment and finishing processes that enhance adhesion properties when combined with resin matrices. This may include processes like oxidation or coating. Understanding these finishing techniques is crucial, as they directly affect the performance of the final composite material in various applications.
What Quality Assurance Standards Should B2B Buyers Look For?
Quality assurance in carbon fiber manufacturing is paramount for ensuring that the final product meets industry standards and specific application requirements. B2B buyers must familiarize themselves with relevant international standards and industry-specific certifications.
-
International Standards
ISO 9001 is a widely recognized quality management standard that ensures consistent quality and continuous improvement in manufacturing processes. B2B buyers should prioritize suppliers with this certification, as it indicates a commitment to quality control. -
Industry-Specific Certifications
Depending on the application of the carbon fiber (e.g., aerospace, automotive, or construction), additional certifications such as CE marking or API standards may be necessary. These certifications ensure compliance with specific safety and performance requirements.
What Are the Key Quality Control Checkpoints in Carbon Fiber Manufacturing?
Quality control (QC) is a critical aspect of carbon fiber manufacturing, involving several checkpoints to ensure that products meet established specifications. Understanding these checkpoints helps B2B buyers assess supplier reliability.
-
Incoming Quality Control (IQC)
This initial checkpoint examines the raw materials before they enter the production process. IQC involves verifying the quality and specifications of precursor materials through sampling and testing. -
In-Process Quality Control (IPQC)
During production, IPQC is implemented to monitor the manufacturing process continuously. This includes regular checks on fiber diameter, tensile strength, and other critical parameters. Buyers should ask suppliers about their IPQC protocols to ensure they maintain stringent quality standards throughout the manufacturing process. -
Final Quality Control (FQC)
Once the carbon fibers are produced, FQC involves comprehensive testing to ensure the final product meets all specifications. This stage may include mechanical testing, chemical analysis, and dimensional checks. B2B buyers should request FQC reports from suppliers to verify product quality.
How Can B2B Buyers Verify Supplier Quality Control Practices?
To ensure that carbon fiber suppliers adhere to high-quality standards, B2B buyers can take several steps to verify their QC practices.
-
Conducting Supplier Audits
Regular audits of potential suppliers can provide insights into their manufacturing processes and QC protocols. Buyers should prepare a checklist of key areas to evaluate, including compliance with international standards, employee training, and equipment calibration. -
Requesting Quality Assurance Reports
Suppliers should provide documentation of their quality assurance measures, including test results and compliance certifications. Buyers should review these reports to ensure they meet the required standards. -
Engaging Third-Party Inspectors
Hiring third-party inspection services can offer an unbiased evaluation of a supplier’s quality control processes. This step is particularly beneficial for international buyers who may not have local resources to conduct thorough inspections.
What Common Testing Methods Are Used in Carbon Fiber Quality Assurance?
Quality assurance in carbon fiber manufacturing relies on various testing methods to ensure product performance and reliability. Understanding these methods can help B2B buyers make informed decisions.
-
Tensile Testing
This method measures the strength and elasticity of carbon fibers by stretching them until they break. Tensile strength is a critical parameter that determines the fiber’s suitability for specific applications. -
Thermogravimetric Analysis (TGA)
TGA assesses the thermal stability and composition of carbon fibers by measuring weight changes as the temperature increases. This analysis helps determine the fiber’s performance under varying thermal conditions. -
Flexural Testing
This testing method evaluates the stiffness and strength of carbon fiber composites under bending loads. It is crucial for applications where the material will experience flexural stress.
What Quality Control Nuances Should International Buyers Consider?
International B2B buyers, especially those from regions like Africa, South America, the Middle East, and Europe, should be aware of specific nuances in quality control that can impact their purchasing decisions.
-
Regulatory Compliance
Different regions may have varying regulations regarding material safety and performance standards. Buyers should ensure that their suppliers comply with local regulations in their respective markets. -
Cultural Considerations
Understanding cultural differences can aid in effective communication regarding quality expectations. Buyers should establish clear guidelines and expectations to avoid misunderstandings. -
Supply Chain Reliability
The reliability of the supply chain is crucial for maintaining consistent quality. Buyers should evaluate the supplier’s sourcing and logistics strategies to ensure timely delivery and product integrity.
Conclusion
In summary, B2B buyers looking for carbon fiber manufacturers must have a comprehensive understanding of the manufacturing processes and quality assurance practices involved. By focusing on the main stages of production, relevant quality standards, and effective verification methods, buyers can make informed decisions that align with their specific needs and industry requirements. Engaging with suppliers who prioritize quality control will not only enhance product performance but also foster long-term business relationships.
Practical Sourcing Guide: A Step-by-Step Checklist for ‘carbon fiber manufacturer’
This sourcing guide is designed to help international B2B buyers navigate the complexities of procuring carbon fiber manufacturing services. By following this step-by-step checklist, buyers from regions such as Africa, South America, the Middle East, and Europe can make informed decisions and establish successful partnerships with suppliers.
Step 1: Define Your Technical Specifications
Before engaging with potential suppliers, it’s essential to clearly outline your technical requirements. This includes the type of carbon fiber needed (e.g., high modulus, high tensile strength), dimensions, and any specific processing techniques required. Having precise specifications will help you communicate effectively with suppliers and ensure they can meet your needs.
Step 2: Research the Market Landscape
Understanding the market landscape is crucial for identifying potential suppliers. Conduct thorough research to identify leading manufacturers in your target regions. Look for companies with a proven track record in carbon fiber production and consider their market reputation, customer reviews, and industry certifications. This groundwork will help you narrow down your options.
Step 3: Evaluate Potential Suppliers
Before committing to a supplier, it is vital to conduct a comprehensive evaluation. Request detailed company profiles, case studies, and references from existing clients, particularly those in your industry. Pay attention to their production capacity, technology used, and previous projects to gauge their capability to deliver quality products.
Step 4: Verify Supplier Certifications
Ensure that the suppliers you are considering possess relevant industry certifications. Certifications such as ISO 9001 for quality management systems or ISO 14001 for environmental management demonstrate a supplier’s commitment to maintaining high standards. This step mitigates risks associated with quality control and compliance issues.
Step 5: Assess Communication and Support
Effective communication is key to a successful supplier relationship. Assess how responsive and transparent potential suppliers are during initial discussions. Ensure they provide clear answers to your inquiries and demonstrate a willingness to support your needs throughout the sourcing process. Good communication will facilitate smoother negotiations and project execution.
Step 6: Request Samples and Perform Quality Testing
Before making a large purchase, always request samples of the carbon fiber products. Conduct thorough quality testing on these samples to evaluate their performance against your specifications. This step is crucial for ensuring that the materials will meet your standards and can be reliably used in your applications.
Step 7: Negotiate Terms and Establish Contracts
Once you’ve identified a suitable supplier, it’s time to negotiate terms. Discuss pricing, payment conditions, delivery schedules, and warranties. Establish clear contracts that outline all agreed-upon terms to protect both parties. This step is vital for ensuring that both you and the supplier have a shared understanding of expectations and responsibilities.
By following this checklist, B2B buyers can approach the sourcing of carbon fiber manufacturers with confidence, ensuring that they choose the right partners to meet their specific needs and drive successful outcomes.
Comprehensive Cost and Pricing Analysis for carbon fiber manufacturer Sourcing
When considering sourcing carbon fiber from manufacturers, international B2B buyers must navigate a complex landscape of costs and pricing structures. Understanding these elements is crucial for making informed purchasing decisions.
What Are the Key Cost Components of Carbon Fiber Manufacturing?
Materials
The primary component of carbon fiber production is the raw materials, which typically include polyacrylonitrile (PAN) or pitch. Prices fluctuate based on global supply and demand, with specific materials impacting the final product’s performance and cost. Buyers should consider sourcing materials locally where possible to minimize import tariffs and shipping costs.
Labor
Labor costs vary significantly by region. In countries with lower labor costs, such as some in Africa and South America, manufacturing can be less expensive. However, this may come at the expense of skill levels and expertise. Buyers should evaluate the trade-off between cost and quality.
Manufacturing Overhead
Overhead includes utilities, facility maintenance, and equipment depreciation. Efficient manufacturing processes can reduce these costs, so buyers should inquire about the supplier’s production methods and technologies.
Tooling
Custom tooling can represent a significant upfront investment, particularly for specialized products. Understanding the tooling costs and whether they will be amortized over the production run is essential for long-term pricing.
Quality Control (QC)
Investment in quality control is paramount in carbon fiber manufacturing due to the material’s applications in critical industries like aerospace and automotive. Buyers should ensure that suppliers adhere to international quality standards, which may influence costs.
Logistics
Shipping and handling costs can vary widely based on location and the chosen Incoterms. Buyers from regions like Europe may benefit from proximity to manufacturers in neighboring countries, reducing logistics expenses.
Margin
Manufacturers typically apply a margin that reflects their operational costs and desired profit. Understanding how different suppliers structure their margins can provide negotiation leverage.
How Do Pricing Influencers Affect Carbon Fiber Sourcing?
Volume and Minimum Order Quantity (MOQ)
Higher order volumes often lead to lower per-unit costs. Buyers should assess their needs carefully to negotiate favorable terms, especially if they can commit to larger quantities.
Specifications and Customization
Custom specifications can significantly impact price. Buyers should be clear about their requirements and be prepared to discuss how these specifications influence manufacturing processes and costs.
Quality and Certifications
Higher quality products often come at a premium. Buyers should prioritize suppliers with relevant certifications (e.g., ISO) that guarantee adherence to international standards, as this may reduce long-term risks.
Supplier Factors
The reputation and reliability of a supplier can also influence pricing. Established manufacturers with a proven track record may charge more but offer greater assurance of quality and service.
Incoterms
Understanding Incoterms is vital for cost calculations. Terms like FOB (Free On Board) or CIF (Cost, Insurance, and Freight) will determine who bears shipping costs and risks, directly impacting the overall price structure.
What Are Effective Buyer Tips for Negotiating Carbon Fiber Prices?
Negotiation Strategies
Buyers should come prepared with market data to support their pricing discussions. Establishing a relationship with suppliers can also yield better terms and conditions.
Focusing on Cost-Efficiency
Analyze the total cost of ownership (TCO) rather than just upfront pricing. Consider factors such as longevity, maintenance, and performance to make a more informed decision.
Understanding Pricing Nuances for International Buyers
Different regions may experience varying price dynamics based on local market conditions, currency fluctuations, and geopolitical factors. Buyers from Africa, South America, the Middle East, and Europe should factor these elements into their sourcing strategy.
Disclaimer on Pricing
Prices for carbon fiber manufacturing can vary widely based on the aforementioned factors. It is advisable for buyers to conduct thorough research and obtain multiple quotes to ensure competitive pricing aligned with their specific needs.
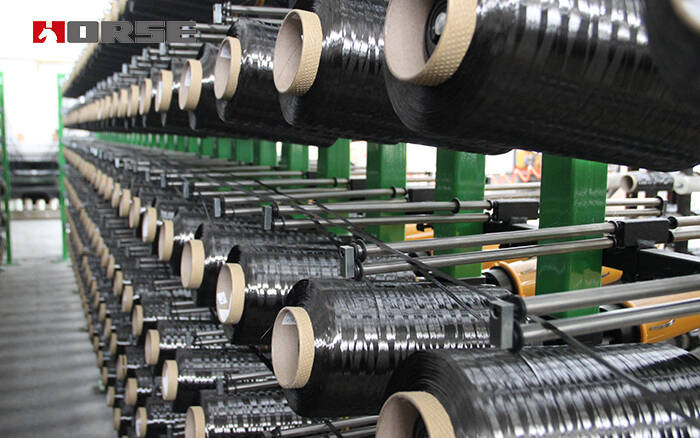
A stock image related to carbon fiber manufacturer.
Alternatives Analysis: Comparing carbon fiber manufacturer With Other Solutions
Understanding Alternatives to Carbon Fiber Manufacturing
When considering materials for industrial applications, carbon fiber has established itself as a leading solution due to its strength-to-weight ratio and durability. However, there are alternative materials and manufacturing methods that can also meet specific needs. This analysis aims to compare carbon fiber manufacturing with two viable alternatives: fiberglass and aluminum. Each option has unique characteristics that may better suit certain applications, particularly for international B2B buyers in regions like Africa, South America, the Middle East, and Europe.
Comparison Table of Carbon Fiber Manufacturer and Alternatives
Comparison Aspect | Carbon Fiber Manufacturer | Fiberglass | Aluminum |
---|---|---|---|
Performance | High strength-to-weight ratio, excellent fatigue resistance | Good strength, less rigid than carbon fiber | Strong, lightweight, corrosion-resistant |
Cost | High initial investment | Moderate cost | Moderate to high cost |
Ease of Implementation | Requires specialized techniques and equipment | Easier to mold and handle | Readily available and easy to machine |
Maintenance | Low maintenance required | Moderate maintenance needed | Low maintenance, but may require coatings |
Best Use Case | Aerospace, automotive, high-performance sporting goods | Marine applications, insulation, consumer goods | Structural components, automotive parts, packaging |
What are the Advantages and Disadvantages of Fiberglass Compared to Carbon Fiber?
Fiberglass is a composite material made from fine glass fibers, which are woven together and combined with a resin. Its advantages include lower costs and easier handling, making it a popular choice for many applications, especially in marine industries. However, fiberglass generally has a lower strength-to-weight ratio compared to carbon fiber, which may limit its use in high-performance contexts. It also tends to be less durable, especially when exposed to harsh environmental conditions.
How Does Aluminum Stack Up Against Carbon Fiber in Terms of Performance?
Aluminum is a versatile metal known for its lightweight and corrosion-resistant properties. It’s widely used in various industries, including automotive and aerospace. The primary advantages of aluminum include its availability and ease of machining, making it a cost-effective choice for many applications. However, while aluminum can be strong, it typically does not match the specific strength and stiffness of carbon fiber. Additionally, aluminum components can be heavier than those made from carbon fiber, which may affect performance in weight-sensitive applications.
Conclusion: How Can B2B Buyers Choose the Right Material for Their Needs?
Selecting the appropriate material for a project involves assessing various factors, including performance requirements, budget constraints, and the intended application. For B2B buyers, particularly those from Africa, South America, the Middle East, and Europe, understanding these alternatives is crucial. While carbon fiber offers unparalleled performance in specific sectors, alternatives like fiberglass and aluminum may provide more cost-effective solutions for other applications. Evaluating the unique needs of your project, alongside the characteristics of each material, will help you make an informed decision that balances performance, cost, and practicality.
Essential Technical Properties and Trade Terminology for carbon fiber manufacturer
What Are the Key Technical Properties of Carbon Fiber?
Understanding the essential technical properties of carbon fiber is crucial for international B2B buyers, particularly those in industries such as aerospace, automotive, and sporting goods. Here are some critical specifications that manufacturers should be aware of:
1. Material Grade
Material grade refers to the specific classification of carbon fiber based on its tensile strength, modulus, and other mechanical properties. Grades typically range from standard to high-performance, influencing the end-use applications. For buyers, selecting the appropriate material grade ensures that the carbon fiber will meet the performance requirements of their specific projects, such as weight savings in aerospace or enhanced durability in automotive applications.
2. Tensile Strength
Tensile strength measures the maximum amount of tensile (pulling) stress that a material can withstand before failure. Carbon fiber is renowned for its high tensile strength, often exceeding that of steel. For B2B buyers, understanding tensile strength is essential for applications where high load-bearing capacity is needed, ensuring that the products will maintain integrity under stress.
3. Modulus of Elasticity
The modulus of elasticity indicates how much a material will deform under a given stress. In carbon fiber, a higher modulus means less deformation, which is crucial in applications requiring stiffness and rigidity. Buyers should pay attention to this property to ensure their carbon fiber components will perform optimally without excessive bending or flexing.
4. Weight-to-Strength Ratio
The weight-to-strength ratio is a critical measure in many industries, especially in aerospace and automotive sectors where reducing weight is paramount. Carbon fiber offers an exceptional weight-to-strength ratio, allowing manufacturers to create lightweight yet strong components. For B2B buyers, this property translates into better fuel efficiency and performance in their applications.
5. Chemical Resistance
Carbon fiber is known for its excellent resistance to chemicals, making it suitable for various environments, including those exposed to corrosive substances. Buyers in industries like oil and gas or chemical processing should prioritize this property to ensure longevity and performance of their products in harsh conditions.
What Are Common Trade Terms Used in Carbon Fiber Manufacturing?
Familiarity with industry jargon is vital for effective communication and negotiation in the carbon fiber market. Here are some commonly used trade terms:
1. OEM (Original Equipment Manufacturer)
An OEM is a company that produces parts or equipment that may be marketed by another manufacturer. For B2B buyers, partnering with an OEM can streamline production processes and ensure that components meet specific quality standards required for their end products.
2. MOQ (Minimum Order Quantity)
MOQ refers to the smallest quantity of a product that a supplier is willing to sell. This term is crucial for B2B buyers as it impacts inventory management and cash flow. Understanding the MOQ helps buyers gauge whether a supplier’s offerings align with their production needs and budget constraints.
3. RFQ (Request for Quotation)
An RFQ is a document sent to suppliers requesting a quote for specific products or services. It typically includes details such as quantities, specifications, and delivery timelines. For international buyers, issuing RFQs can facilitate competitive pricing and better understand market rates for carbon fiber products.
4. Incoterms (International Commercial Terms)
Incoterms define the responsibilities of buyers and sellers in international transactions. These terms clarify who is responsible for shipping, insurance, and tariffs. B2B buyers must understand Incoterms to negotiate better terms and avoid unexpected costs when importing carbon fiber products from global suppliers.
5. Lead Time
Lead time is the time taken from placing an order to receiving it. This term is essential for project planning and inventory management. B2B buyers should inquire about lead times to ensure timely delivery of carbon fiber materials, which can significantly impact production schedules.
By familiarizing themselves with these technical properties and trade terminologies, B2B buyers can make more informed decisions, ensuring that their procurement processes for carbon fiber meet both quality and operational requirements.
Navigating Market Dynamics and Sourcing Trends in the carbon fiber manufacturer Sector
What Are the Key Market Dynamics in the Carbon Fiber Manufacturing Sector?
The global carbon fiber manufacturing sector is experiencing significant growth, driven by rising demand across various industries, including aerospace, automotive, and renewable energy. As international B2B buyers from regions like Africa, South America, the Middle East, and Europe engage with this market, understanding current and emerging trends becomes crucial. One notable trend is the increasing adoption of automation and Industry 4.0 technologies, which enhance production efficiency and reduce costs. These advancements enable manufacturers to scale operations while maintaining high-quality standards, making them more attractive to B2B buyers seeking reliable suppliers.
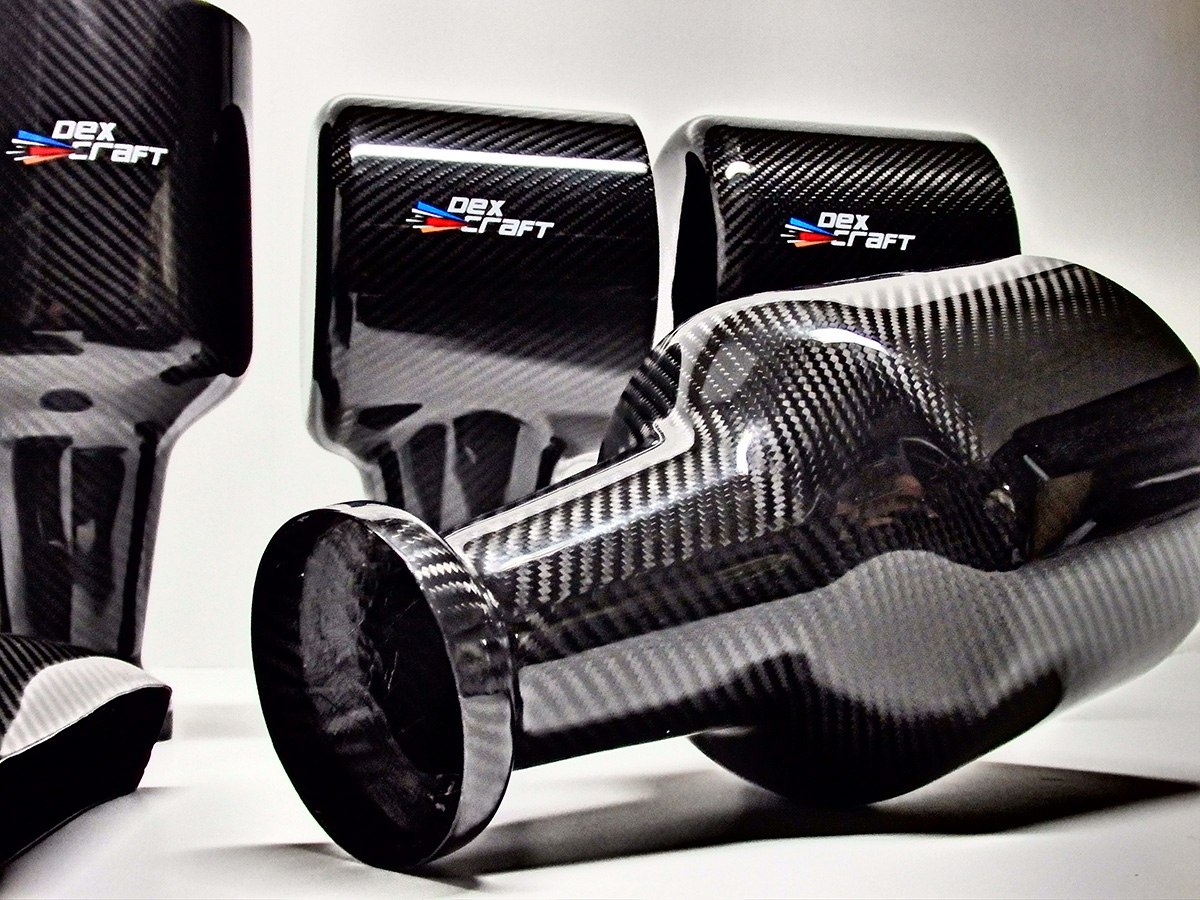
A stock image related to carbon fiber manufacturer.
Additionally, there is a shift towards lightweight materials that improve energy efficiency. This trend is particularly relevant in sectors such as automotive, where regulations mandate lower emissions. Buyers from Europe, like Germany, are already prioritizing partnerships with manufacturers that can provide innovative solutions to meet these environmental standards. In contrast, buyers in Africa and South America may focus on sourcing opportunities that align with their regional development goals, such as infrastructure projects that utilize carbon fiber for enhanced durability and performance.
How Is Sustainability Shaping Sourcing Trends in the Carbon Fiber Sector?
Sustainability is becoming a non-negotiable aspect of sourcing strategies in the carbon fiber manufacturing sector. The environmental impact of production processes, particularly concerning energy consumption and waste generation, has prompted buyers to prioritize ethical sourcing. International buyers are increasingly looking for manufacturers who utilize ‘green’ certifications, such as ISO 14001, which signifies a commitment to environmental management.
Furthermore, many companies are exploring bio-based carbon fibers as alternatives to traditional petroleum-based products. These innovative materials not only reduce the carbon footprint but also appeal to the growing consumer demand for sustainable products. B2B buyers from regions like the Middle East are particularly interested in suppliers who can demonstrate a commitment to sustainable practices, as they align with broader regional goals for environmental stewardship.
Establishing an ethical supply chain is also crucial, as it builds trust and enhances brand reputation. Buyers should assess potential suppliers on their sourcing practices, ensuring they prioritize transparency and traceability in their operations. This focus on sustainability not only meets regulatory requirements but also positions businesses favorably in a competitive marketplace.
How Has the Carbon Fiber Manufacturing Sector Evolved Over Time?
The carbon fiber manufacturing sector has undergone remarkable evolution since its inception in the late 20th century. Initially developed for aerospace applications due to its superior strength-to-weight ratio, carbon fiber technology has expanded into various sectors, including automotive and sports equipment. The shift from niche applications to widespread industrial use is a testament to its versatility and performance advantages.
As technological advancements continue to emerge, manufacturers are investing in research and development to improve production processes and reduce costs. This evolution has made carbon fiber more accessible to a broader range of industries, particularly in emerging markets. For B2B buyers, understanding this historical context can inform sourcing decisions, as it highlights the ongoing innovation and potential for future growth within the sector. By aligning with forward-thinking manufacturers, buyers can position themselves advantageously in the evolving landscape of carbon fiber applications.
Frequently Asked Questions (FAQs) for B2B Buyers of carbon fiber manufacturer
-
How do I select the right carbon fiber manufacturer for my business needs?
Selecting the right carbon fiber manufacturer requires evaluating several key factors. Start by assessing their industry experience and reputation; look for manufacturers with a track record of successful projects in your specific sector. Request samples to evaluate product quality and ensure they meet your specifications. Additionally, consider their production capabilities, customization options, and adherence to international standards. Engaging in direct communication can also provide insights into their responsiveness and customer service, which are crucial for long-term partnerships. -
What are the typical minimum order quantities (MOQs) for carbon fiber products?
Minimum order quantities (MOQs) for carbon fiber products can vary significantly based on the manufacturer, the type of product, and the complexity of the order. Generally, MOQs can range from a few hundred to several thousand units. It’s essential to discuss your specific needs with potential suppliers to understand their MOQ policies. For small to medium-sized enterprises, some manufacturers may offer flexible MOQs, especially for customized products, so be sure to negotiate based on your capacity and requirements. -
What customization options are available when sourcing carbon fiber products?
Many carbon fiber manufacturers offer a range of customization options, including variations in fiber type, weave patterns, and resin systems. Additionally, you can often specify dimensions, weight, and mechanical properties tailored to your application. When discussing your project with potential suppliers, be clear about your requirements, as this will help them provide the best solutions. Ensure that the manufacturer has experience in producing customized solutions, as this can significantly impact the performance and suitability of the final product. -
What payment terms should I expect when dealing with carbon fiber suppliers?
Payment terms can vary by manufacturer and region, but it’s common to encounter options such as advance payment, letter of credit, or net 30/60 days after delivery. For international transactions, be aware of potential currency fluctuations and additional fees. Establishing clear payment terms in your contract can help avoid misunderstandings. It’s also advisable to discuss payment milestones linked to production stages, which can provide security for both parties and ensure timely delivery of products. -
How can I ensure quality assurance in my carbon fiber products?
To ensure quality assurance, request certifications that demonstrate compliance with international standards, such as ISO 9001. Many manufacturers will have quality control processes in place; ask about their inspection protocols and testing methods for the carbon fiber products you plan to order. Conducting a factory audit can also provide insights into their production capabilities and quality assurance practices. Establishing a clear agreement on quality expectations before production starts is essential to mitigate risks. -
What logistics considerations should I keep in mind when sourcing carbon fiber internationally?
Logistics plays a crucial role in international sourcing of carbon fiber products. Consider the shipping methods available, as air freight may offer faster delivery but at a higher cost than sea freight. Factor in customs regulations and duties that may apply to your imports, particularly if you are sourcing from a different continent. Collaborating with a freight forwarder can simplify the logistics process, ensuring compliance with international trade regulations and minimizing delays. -
How can I vet potential carbon fiber suppliers effectively?
Vetting potential carbon fiber suppliers involves a thorough review of their credentials, customer testimonials, and case studies. Start by checking their website and online presence for information on their capabilities and industry experience. Request references from previous clients to gauge reliability and product quality. Additionally, consider using third-party verification services or industry trade shows to connect with reputable manufacturers. Establishing a solid relationship through open communication can also help you assess their commitment to customer satisfaction. -
What are the common applications of carbon fiber products in various industries?
Carbon fiber is widely used across numerous industries due to its strength-to-weight ratio and corrosion resistance. Common applications include aerospace components, automotive parts, sporting goods, and industrial machinery. In the energy sector, carbon fiber is utilized in wind turbine blades and other equipment. Understanding the specific applications relevant to your industry can guide your sourcing decisions and help you communicate your requirements effectively to manufacturers, ensuring you receive tailored solutions that meet your needs.
Important Disclaimer & Terms of Use
⚠️ Important Disclaimer
The information provided in this guide, including content regarding manufacturers, technical specifications, and market analysis, is for informational and educational purposes only. It does not constitute professional procurement advice, financial advice, or legal advice.
While we have made every effort to ensure the accuracy and timeliness of the information, we are not responsible for any errors, omissions, or outdated information. Market conditions, company details, and technical standards are subject to change.
B2B buyers must conduct their own independent and thorough due diligence before making any purchasing decisions. This includes contacting suppliers directly, verifying certifications, requesting samples, and seeking professional consultation. The risk of relying on any information in this guide is borne solely by the reader.
Strategic Sourcing Conclusion and Outlook for carbon fiber manufacturer
In navigating the complexities of sourcing carbon fiber, international B2B buyers from Africa, South America, the Middle East, and Europe must recognize the immense value of strategic sourcing. By understanding the unique characteristics and applications of carbon fiber, businesses can make informed decisions that enhance product performance and reduce overall costs. Establishing long-term partnerships with reliable manufacturers not only secures a consistent supply but also fosters innovation and adaptability in an ever-evolving market.
What Are the Key Benefits of Strategic Sourcing for Carbon Fiber?
Engaging in strategic sourcing allows companies to leverage economies of scale, optimize supply chains, and mitigate risks associated with fluctuating material costs. Buyers should prioritize manufacturers that demonstrate transparency, sustainability, and a commitment to quality. Furthermore, diversifying supplier bases across regions can safeguard against geopolitical uncertainties and supply chain disruptions.
How Can International B2B Buyers Prepare for the Future of Carbon Fiber Sourcing?
As the demand for lightweight, high-strength materials continues to rise, staying informed about market trends and technological advancements is crucial. Buyers should actively seek out innovative solutions, such as advancements in recycling and production techniques, to maintain competitive advantages.
In conclusion, as the global landscape for carbon fiber evolves, international B2B buyers are encouraged to embrace strategic sourcing as a key driver of success. By fostering collaborative relationships with manufacturers and remaining agile in their sourcing strategies, businesses can position themselves for sustainable growth in the carbon fiber market.