Unlock Quality: The Ultimate Cement Mixer Manufacturer Guide (2025)
Introduction: Navigating the Global Market for cement mixer manufacturer
In the dynamic landscape of international construction, sourcing a reliable cement mixer manufacturer can pose significant challenges for B2B buyers, especially in regions like Africa, South America, the Middle East, and Europe. With a plethora of options available, understanding the nuances of quality, cost, and supplier credibility is crucial for making informed decisions. This guide serves as a comprehensive resource, delving into various types of cement mixers, their applications, and the essential criteria for vetting potential suppliers.
Buyers will gain insights into the latest industry trends and technologies that enhance productivity and efficiency in construction projects. Additionally, we will explore the cost factors involved in procuring cement mixers, including import duties and logistics, which can vary significantly across different regions. By addressing common pain points, such as navigating regulations and ensuring product reliability, this guide empowers international B2B buyers to streamline their purchasing process and mitigate risks.
Whether you are operating in bustling urban centers or remote construction sites, understanding the global market for cement mixers will enable you to make strategic decisions that align with your business objectives. With actionable insights tailored to the unique challenges faced by buyers from diverse markets, this guide positions you to leverage the best opportunities in the cement mixer industry.
Understanding cement mixer manufacturer Types and Variations
Type Name | Key Distinguishing Features | Primary B2B Applications | Brief Pros & Cons for Buyers |
---|---|---|---|
Drum Mixers | Rotating drum design; continuous mixing capability | Large-scale construction projects | Pros: High efficiency; suitable for large volumes. Cons: Less precision in mix quality. |
Planetary Mixers | Multiple mixing blades; thorough and uniform mixing | Precast concrete production | Pros: Excellent mix quality; ideal for complex mixes. Cons: Higher initial cost. |
Twin-Shaft Mixers | Two horizontal shafts; rapid and homogeneous mixing | Ready-mix concrete plants | Pros: Fast mixing time; consistent quality. Cons: Requires more maintenance. |
Portable Mixers | Compact and mobile; easy to transport and set up | Small projects and remote locations | Pros: Flexibility and ease of use; low investment. Cons: Limited mixing capacity. |
Volumetric Mixers | On-site mixing; adjustable material ratios | Custom concrete solutions | Pros: Fresh mixes on demand; reduces waste. Cons: Requires operator expertise. |
What are the Key Characteristics of Drum Mixers in Cement Production?
Drum mixers are characterized by their rotating drum design, which allows for continuous mixing of materials. This type of mixer is particularly suitable for large-scale construction projects where high efficiency is required. When considering a drum mixer, B2B buyers should evaluate factors such as the mixer’s capacity, the speed of mixing, and the overall durability. While drum mixers can handle significant volumes, they may compromise on mix precision, which could affect the final product quality in critical applications.
How Do Planetary Mixers Stand Out for Precast Concrete?
Planetary mixers feature multiple mixing blades that rotate around a central axis, ensuring thorough and uniform mixing. They are particularly advantageous for producing precast concrete, where consistency and quality are paramount. Buyers should consider the specific mixing requirements of their projects, as planetary mixers excel in creating complex mixes. However, they come with a higher initial investment, which could be a consideration for budget-conscious buyers.
Why are Twin-Shaft Mixers Ideal for Ready-Mix Concrete Plants?
Twin-shaft mixers utilize two horizontal shafts to achieve rapid and homogeneous mixing of materials. This design is particularly beneficial for ready-mix concrete plants, where speed and consistency are critical. B2B buyers should assess the maintenance requirements and operational costs associated with twin-shaft mixers, as they may require more upkeep compared to other types. Despite the higher maintenance needs, the fast mixing times and consistent output make them a preferred choice for many large-scale operations.
What Makes Portable Mixers a Good Choice for Small Projects?
Portable mixers are designed to be compact and mobile, making them easy to transport and set up at various job sites. They are ideal for small projects and remote locations where space and resources may be limited. B2B buyers should consider the mixer’s capacity and ease of use when making a purchasing decision. While portable mixers offer flexibility and a lower investment, they typically have limited mixing capacity, which may not meet the needs of larger projects.
How Do Volumetric Mixers Provide Custom Concrete Solutions?
Volumetric mixers allow for on-site mixing with adjustable material ratios, providing fresh concrete on demand. This feature is particularly beneficial for projects that require custom concrete solutions, as it reduces waste and increases efficiency. B2B buyers should evaluate the operator expertise needed to manage volumetric mixers effectively, as the success of this type relies heavily on skilled personnel. While they offer significant advantages in terms of flexibility and waste reduction, the need for knowledgeable operators can be a consideration for some businesses.
Related Video: Harbor Freight Cement Mixer 3.5 Cubic Ft Test
Key Industrial Applications of cement mixer manufacturer
Industry/Sector | Specific Application of cement mixer manufacturer | Value/Benefit for the Business | Key Sourcing Considerations for this Application |
---|---|---|---|
Construction | On-site concrete mixing for residential projects | Reduces transport costs and improves project timelines | Local regulations, equipment durability, and service availability |
Infrastructure | Large-scale road and bridge construction | Ensures consistent quality and strength of concrete | Capacity to handle large volumes, ease of operation, and maintenance support |
Mining and Quarrying | Production of high-strength concrete for structures | Enhances structural integrity and safety | Compliance with industry standards, material compatibility, and energy efficiency |
Precast Concrete | Manufacturing precast elements like beams and blocks | Speeds up construction processes and reduces waste | Customization options, production speed, and precision capabilities |
Agriculture | Mixing of soil and additives for construction of silos | Improves efficiency in building agricultural structures | Adaptability to various soil types, ease of transportation, and local availability |
How is Cement Mixer Manufacturer Used in the Construction Industry?
In the construction sector, cement mixer manufacturers provide essential equipment for on-site concrete mixing. This application is particularly beneficial for residential projects where transporting ready-mixed concrete can be costly and time-consuming. By using a cement mixer, contractors can produce the exact amount of concrete required, minimizing waste and enhancing project efficiency. International buyers from regions like Africa and South America should consider local regulations regarding emissions and noise levels when sourcing mixers, as well as the durability of the equipment to withstand varying environmental conditions.
What Role Does Cement Mixer Manufacturer Play in Infrastructure Development?
For large-scale infrastructure projects such as roads and bridges, cement mixers are vital for ensuring the consistent quality of concrete used. This application allows construction teams to mix concrete on-site, which is crucial for maintaining the structural integrity of large constructions. Buyers in Europe and the Middle East should prioritize sourcing mixers that can handle high volumes and possess features for ease of operation and maintenance. Additionally, understanding the local market’s demand for infrastructure can guide buyers in selecting the right equipment.
How is Cement Mixer Manufacturer Beneficial for Mining and Quarrying?
In the mining and quarrying sectors, cement mixers are used to produce high-strength concrete necessary for constructing robust structures such as retaining walls and tunnels. The ability to mix concrete on-site enhances safety and ensures that the material meets specific strength requirements. B2B buyers should focus on sourcing mixers that comply with industry standards and can handle various material types. Energy efficiency is another critical consideration, especially in regions where operational costs can significantly impact profitability.
How Do Cement Mixer Manufacturers Support Precast Concrete Production?
Cement mixers play a crucial role in the precast concrete industry by facilitating the rapid production of concrete elements like beams and blocks. This application streamlines the construction process, reducing overall project time and material waste. International buyers should look for manufacturers that offer customization options to meet specific project requirements. Furthermore, the precision capabilities of the mixers should align with the industry standards to ensure high-quality precast products.
What is the Impact of Cement Mixer Manufacturer on Agricultural Construction?
In agriculture, cement mixers are used to mix soil with additives for constructing silos and storage facilities. This application improves the efficiency of building agricultural structures, which are essential for storing crops. Buyers should consider the adaptability of the mixer to various soil types and its ease of transportation to remote areas. Ensuring local availability of parts and service can also significantly enhance operational efficiency and reduce downtime.
Related Video: Ready Mix Cement Concrete Mixer Truck Pouring Concrete Hino 500 Quester CWE 280
3 Common User Pain Points for ‘cement mixer manufacturer’ & Their Solutions
Scenario 1: Insufficient Product Knowledge Leading to Mismatched Expectations
The Problem:
B2B buyers often face the challenge of navigating the complexities of cement mixer specifications and features. This can lead to purchasing a product that does not meet their operational needs. For instance, a construction firm in Africa may require a heavy-duty mixer for large-scale projects, but without adequate product knowledge, they might opt for a smaller, less powerful model. This oversight can result in project delays, increased costs, and frustration.
The Solution:
To mitigate this issue, buyers should invest time in researching and understanding the specifications of different cement mixers before making a purchase. Engaging with manufacturers directly or attending trade shows can provide valuable insights into the capabilities of various models. Additionally, buyers should request detailed product documentation, including specifications and user manuals, to ensure they are fully informed. Establishing a strong relationship with the manufacturer can also facilitate better guidance on selecting the right mixer for specific applications. Conducting a needs assessment with a clear list of requirements will further help in pinpointing the ideal mixer.
Scenario 2: Reliability Concerns and Maintenance Issues
The Problem:
Many B2B buyers experience anxiety over the reliability of cement mixers, particularly in regions with fluctuating availability of spare parts and service support. A contractor in South America may invest in a high-end mixer only to find that it requires frequent repairs, leading to downtime and project delays. This is particularly problematic when local suppliers do not stock necessary parts, forcing buyers to source them from distant locations, often at inflated prices.
The Solution:
To address reliability concerns, buyers should prioritize manufacturers with a strong reputation for durability and customer support. Before making a purchase, it’s crucial to inquire about the availability of spare parts and after-sales service in their region. Establishing contracts for routine maintenance and support can help prevent unexpected breakdowns. Additionally, buyers should consider investing in mixers that come with extended warranties, which can provide peace of mind regarding repairs and maintenance. Creating a local network of trusted technicians who can perform repairs can also minimize downtime and ensure smoother operations.
Scenario 3: Environmental Compliance and Sustainability Challenges
The Problem:
As sustainability becomes a focal point for construction projects globally, B2B buyers are increasingly concerned about the environmental impact of the equipment they use. For example, a construction company in Europe may want to adhere to strict emissions regulations but finds that many available cement mixers do not meet these standards. This can create a dilemma between investing in compliant equipment and staying within budget constraints.
The Solution:
To navigate environmental compliance, buyers should proactively seek out manufacturers that prioritize sustainability in their product design. This includes inquiring about eco-friendly features, such as low-emission engines and energy-efficient operations. Buyers should also familiarize themselves with local regulations regarding emissions and waste management to ensure compliance. Forming partnerships with manufacturers that are committed to sustainable practices can lead to innovative solutions that reduce environmental impact while also being cost-effective. Finally, buyers should evaluate the total cost of ownership, considering not just the initial purchase price but also the long-term savings associated with sustainable operations and compliance with regulations.
Strategic Material Selection Guide for cement mixer manufacturer
When selecting materials for cement mixers, international B2B buyers must consider various factors that affect performance, durability, and compliance with regional standards. Here, we analyze four common materials used in cement mixer manufacturing: steel, aluminum, composite materials, and high-density polyethylene (HDPE). Each material has unique properties, advantages, and limitations that can significantly impact the end product’s effectiveness and suitability for diverse applications.
What Are the Key Properties of Steel in Cement Mixers?
Steel is the most common material used in the construction of cement mixers due to its strength and durability. It typically has a high temperature and pressure rating, making it suitable for heavy-duty applications. Steel’s corrosion resistance can be enhanced through galvanization or coatings, which is crucial for mixers operating in harsh environments.
Pros & Cons: Steel offers excellent durability and structural integrity, making it ideal for high-impact applications. However, its weight can increase manufacturing complexity and transportation costs. Additionally, while steel is generally cost-effective, the price can fluctuate based on global market conditions, which may affect budgeting for international buyers.
Impact on Application: Steel mixers are compatible with a wide range of media, including concrete, mortar, and other aggregates. However, buyers should consider the potential for rust in humid climates, especially in regions like Africa and South America.
How Does Aluminum Compare for Cement Mixer Manufacturing?
Aluminum is gaining popularity due to its lightweight properties and good corrosion resistance. It has a lower temperature rating compared to steel but is still suitable for many cement mixing applications.
Pros & Cons: The primary advantage of aluminum is its weight, which can lead to lower transportation costs and easier handling during assembly. However, aluminum can be more expensive than steel, and its lower strength may limit its use in high-capacity mixers.
Impact on Application: Aluminum mixers are particularly beneficial in environments where weight is a critical factor, such as in mobile mixers. Buyers should ensure that the aluminum used meets relevant standards, such as ASTM or DIN, to ensure product reliability.
What Are the Benefits of Composite Materials in Cement Mixers?
Composite materials, including fiberglass and reinforced plastics, are becoming increasingly popular in cement mixer manufacturing due to their corrosion resistance and lightweight characteristics.
Pros & Cons: Composites offer excellent resistance to corrosion and chemical damage, making them suitable for mixers exposed to aggressive materials. However, they can be more expensive to manufacture and may require specialized processes.
Impact on Application: These materials are particularly effective in environments with high humidity or exposure to corrosive substances. Buyers should verify that composites meet international standards to ensure compliance and reliability.
Why Consider High-Density Polyethylene (HDPE) for Cement Mixers?
High-density polyethylene (HDPE) is another material option known for its excellent chemical resistance and lightweight nature. It is often used in applications where corrosion is a significant concern.
Pros & Cons: HDPE is cost-effective and easy to mold, allowing for intricate designs. However, its lower strength compared to metals may limit its use in heavy-duty applications. Additionally, HDPE may not withstand high temperatures as effectively as steel or aluminum.
Impact on Application: HDPE mixers are suitable for mixing lighter aggregates and chemicals but may not be ideal for traditional concrete applications. International buyers should assess local regulations regarding the use of plastics in construction materials.
Summary Table of Material Selection for Cement Mixers
Material | Typical Use Case for cement mixer manufacturer | Key Advantage | Key Disadvantage/Limitation | Relative Cost (Low/Med/High) |
---|---|---|---|---|
Steel | Heavy-duty cement mixers | Excellent durability and strength | Heavier, can increase transport costs | Medium |
Aluminum | Mobile cement mixers | Lightweight, lower transport costs | Higher cost, lower strength | High |
Composite Materials | Corrosion-resistant applications | Great chemical resistance | More expensive, specialized manufacturing | High |
High-Density Polyethylene (HDPE) | Lighter aggregate mixing | Cost-effective, easy to mold | Lower strength, limited temperature resistance | Low |
By carefully evaluating these materials, international B2B buyers can make informed decisions that align with their operational requirements and regional standards.
In-depth Look: Manufacturing Processes and Quality Assurance for cement mixer manufacturer
What Are the Key Stages in the Manufacturing Process of Cement Mixers?
The manufacturing process of cement mixers involves several critical stages that ensure the final product meets quality and performance standards. The main stages include material preparation, forming, assembly, and finishing.
-
Material Preparation
– The first step involves sourcing high-quality raw materials, such as steel, which is essential for the durability of the mixer. Suppliers often conduct tests to ensure materials meet specific mechanical properties.
– Common materials used include carbon steel, stainless steel, and various alloys. B2B buyers should inquire about the origin of these materials and whether they comply with international standards. -
Forming
– In this stage, the raw materials are shaped into components using techniques such as welding, casting, or machining. For example, the drum of the mixer may be fabricated through steel forming processes like rolling or stamping.
– Advanced technologies like Computer Numerical Control (CNC) machines are often employed for precision in forming. Buyers should assess whether the manufacturer uses modern technology to enhance accuracy and reduce waste. -
Assembly
– The assembly stage involves fitting together all the components, including the drum, frame, motor, and other mechanical parts. This process may involve both manual labor and automated systems.
– Quality checks are integral during assembly to ensure that all parts fit correctly and function as intended. Buyers should verify if the manufacturer has a standardized assembly procedure to minimize defects. -
Finishing
– The final stage includes surface treatment, painting, and applying protective coatings to enhance durability and aesthetics. The finishing process also plays a crucial role in preventing rust and corrosion.
– Techniques such as powder coating or galvanization are commonly used. B2B buyers should inquire about the finishing processes used and their long-term effectiveness in different environmental conditions.
How Is Quality Assurance Integrated into Cement Mixer Manufacturing?
Quality assurance (QA) is a critical aspect of the manufacturing process, ensuring that cement mixers are safe, reliable, and compliant with international standards. Key components of QA include adherence to relevant standards, quality checkpoints, and testing methods.
-
Relevant International Standards
– Manufacturers typically adhere to international standards such as ISO 9001, which outlines requirements for a quality management system. Compliance with these standards indicates a commitment to continuous improvement and customer satisfaction.
– Other certifications may include CE marking for compliance with European safety standards or API certification for specific industrial applications. Buyers should verify these certifications as part of their supplier evaluation. -
Quality Checkpoints in the Manufacturing Process
– Incoming Quality Control (IQC): This initial checkpoint assesses the quality of raw materials before they enter the production line. It is crucial for preventing defects in the final product.
– In-Process Quality Control (IPQC): During the manufacturing process, IPQC monitors critical parameters and dimensions to ensure they meet specifications. This stage involves regular inspections and measurements.
– Final Quality Control (FQC): The final checkpoint occurs after assembly, where the completed mixer undergoes comprehensive testing to ensure it meets performance standards. This may include load testing, operational checks, and safety assessments. -
Common Testing Methods for Cement Mixers
– Manufacturers may employ various testing methods, including non-destructive testing (NDT) techniques, stress tests, and functionality tests. These methods help identify potential weaknesses without damaging the product.
– B2B buyers should inquire about the specific testing protocols used and request documentation of test results to ensure compliance with industry standards.
How Can B2B Buyers Verify Supplier Quality Control?
Verifying a supplier’s quality control (QC) processes is essential for B2B buyers, especially when sourcing from international manufacturers. Here are actionable steps buyers can take:
-
Conduct Supplier Audits
– Performing on-site audits allows buyers to assess the manufacturing facilities, processes, and QA systems firsthand. This step is crucial for understanding the supplier’s capabilities and adherence to quality standards. -
Request Quality Assurance Reports
– Buyers should request detailed QA reports that outline the QC procedures, results of inspections, and any corrective actions taken for non-conformance. Reviewing these documents provides insights into the supplier’s commitment to quality. -
Engage Third-Party Inspection Services
– Utilizing third-party inspection services can provide an unbiased evaluation of the manufacturing processes and final products. This is particularly important for buyers from Africa, South America, and the Middle East, where local inspections may not be feasible.
What Are the Quality Control Nuances for International B2B Buyers?
International B2B buyers need to be aware of specific nuances regarding quality control, especially when sourcing cement mixers from various regions.
-
Cultural and Regulatory Differences
– Different regions may have varying regulations and cultural approaches to manufacturing and quality assurance. Buyers should familiarize themselves with local standards and practices to ensure compliance and avoid potential issues. -
Language Barriers
– Communication can be a challenge when dealing with international suppliers. Ensuring that all quality documentation is available in a language the buyer understands is crucial for transparency and clarity. -
Time Zone Considerations
– Coordinating audits and inspections across different time zones can complicate the verification process. Establishing clear communication channels and timelines is essential to ensure timely responses and actions.
Conclusion: Ensuring Quality in Cement Mixer Manufacturing
For international B2B buyers, understanding the manufacturing processes and quality assurance practices of cement mixer manufacturers is vital for making informed purchasing decisions. By focusing on key manufacturing stages, verifying quality control processes, and being aware of international nuances, buyers can enhance their procurement strategies and ensure they source reliable, high-quality equipment.
Practical Sourcing Guide: A Step-by-Step Checklist for ‘cement mixer manufacturer’
This sourcing guide aims to provide international B2B buyers with a structured approach to procuring cement mixers from manufacturers. By following these steps, buyers can ensure they select the right partner that meets their specific needs, quality standards, and budget constraints.
Step 1: Define Your Technical Specifications
Clearly outlining your technical requirements is crucial before engaging with manufacturers. This includes the type of cement mixer (drum or volumetric), capacity (in liters or cubic meters), and power source (electric or diesel). Providing detailed specifications helps potential suppliers offer accurate quotes and solutions tailored to your operational needs.
Step 2: Research and Identify Potential Suppliers
Conduct thorough research to identify reputable cement mixer manufacturers. Utilize online platforms, trade directories, and industry associations to compile a list of potential suppliers. Focus on manufacturers with a strong presence in your target regions, such as Africa, South America, the Middle East, and Europe, as they may have a better understanding of local market needs and regulations.
Step 3: Evaluate Supplier Experience and Reputation
Before moving forward, assess the experience and reputation of each potential supplier. Look for companies that have been in the industry for several years and have a track record of serving clients in your sector. Seek out customer reviews, case studies, and references to gauge their reliability and service quality. A manufacturer with a proven history is more likely to deliver consistent quality.
Step 4: Verify Certifications and Compliance
Ensure that potential suppliers possess the necessary certifications and comply with local and international standards. This includes ISO certifications, safety standards, and environmental compliance. Validating these credentials not only assures product quality but also mitigates risks associated with non-compliance, which can lead to legal issues or operational disruptions.
Step 5: Request Detailed Quotations
Once you have narrowed down your options, request detailed quotations from shortlisted suppliers. Ensure that these quotes include all relevant costs, such as shipping, customs duties, and installation fees. Compare these quotations carefully, taking note of payment terms, warranty conditions, and after-sales support, to make an informed decision.
Step 6: Conduct Factory Audits or Virtual Inspections
If feasible, conduct factory audits or virtual inspections to verify manufacturing capabilities and quality control processes. This step is vital for ensuring that the supplier adheres to the required production standards and can deliver the promised quality. Look for modern machinery, organized workflows, and adherence to safety protocols during your inspection.
Step 7: Establish Clear Communication Channels
Effective communication is essential throughout the sourcing process. Ensure that you establish clear communication channels with your chosen supplier to facilitate smooth interactions. Discuss timelines, delivery schedules, and any potential challenges upfront. A supplier that maintains open lines of communication is more likely to be responsive and reliable.
By following this checklist, B2B buyers can navigate the complexities of sourcing cement mixers and secure a partnership that aligns with their operational goals.
Comprehensive Cost and Pricing Analysis for cement mixer manufacturer Sourcing
What Are the Key Cost Components for Sourcing Cement Mixers?
When sourcing cement mixers, understanding the cost structure is vital for making informed purchasing decisions. The primary components of the cost include:
-
Materials: The cost of raw materials such as steel, rubber, and electronic components significantly impacts the overall pricing. Prices for these materials can fluctuate based on global market trends and supply chain disruptions.
-
Labor: Labor costs vary by region, influenced by local wage standards and labor laws. Manufacturers in regions with lower labor costs may offer more competitive pricing, but this can sometimes come at the expense of quality.
-
Manufacturing Overhead: This includes costs associated with factory operations, utilities, and administrative expenses. A manufacturer with efficient processes may have lower overhead costs, allowing for more competitive pricing.
-
Tooling: The initial investment in tools and molds for production can be substantial. Customization or specialized designs will increase these costs but may be necessary for meeting specific buyer requirements.
-
Quality Control (QC): Ensuring that each cement mixer meets safety and performance standards involves costs related to testing and inspections. Buyers should consider the implications of QC practices on product reliability and longevity.
-
Logistics: Shipping and handling costs can vary greatly depending on the distance from the manufacturer to the buyer and the chosen Incoterms. International buyers must account for potential tariffs and customs duties as well.
-
Margin: The manufacturer’s profit margin will also factor into the final price. Margins can vary based on market competition and the perceived value of the product.
How Do Price Influencers Impact Cement Mixer Costs?
Several factors influence the pricing of cement mixers, particularly for international buyers:
-
Volume and Minimum Order Quantity (MOQ): Larger orders often attract bulk discounts, making it essential for buyers to assess their needs against MOQ requirements. Negotiating for lower prices per unit based on volume can lead to significant savings.
-
Specifications and Customization: Custom features and specifications typically increase costs. Buyers should clearly define their requirements upfront to avoid unexpected price hikes during the production phase.
-
Material Quality and Certifications: Higher-quality materials and certifications (e.g., ISO standards) can lead to increased prices but often result in greater durability and performance. Buyers should weigh the long-term benefits against initial costs.
-
Supplier Factors: The reputation and reliability of the supplier can also influence pricing. Established manufacturers with a track record of quality may command higher prices, but they often offer better warranties and service.
-
Incoterms: The choice of Incoterms (e.g., FOB, CIF) affects the total landed cost. Understanding these terms can help buyers make more cost-effective shipping decisions.
What Buyer Tips Can Enhance Cost-Efficiency in Sourcing Cement Mixers?
To maximize cost-efficiency when sourcing cement mixers, consider the following strategies:
-
Negotiate Effectively: Always negotiate prices, especially if you are making a significant purchase. Building a good relationship with suppliers can also lead to better pricing in future transactions.
-
Total Cost of Ownership (TCO): Beyond the initial purchase price, assess the TCO, which includes maintenance, operational efficiency, and potential resale value. A lower upfront cost may lead to higher long-term expenses.
-
Understand Pricing Nuances for International Purchases: Buyers from Africa, South America, the Middle East, and Europe should be aware of regional differences in pricing strategies. Currency fluctuations and economic conditions can significantly affect costs.
-
Research Local and International Suppliers: A thorough comparison of local versus international suppliers can uncover hidden savings. Local suppliers may offer faster delivery and lower shipping costs, while international suppliers might provide a broader range of options.
Conclusion
Understanding the comprehensive cost structure and pricing dynamics of cement mixers is crucial for international B2B buyers. By considering the various cost components, price influencers, and employing strategic negotiation techniques, buyers can make informed decisions that align with their budget and operational needs. As always, it is advisable to seek multiple quotes and conduct thorough due diligence before finalizing any agreements.
Alternatives Analysis: Comparing cement mixer manufacturer With Other Solutions
Introduction to Alternative Solutions for Cement Mixing
In the realm of construction, the efficiency and effectiveness of mixing cement can significantly influence project outcomes. While traditional cement mixer manufacturers provide reliable solutions, it is essential for B2B buyers to explore alternative technologies and methods that may better suit their specific requirements. This section evaluates several alternatives, considering factors such as performance, cost, ease of implementation, maintenance, and best use cases.
Comparison Table of Cement Mixer Manufacturer and Alternatives
Comparison Aspect | Cement Mixer Manufacturer | Portable Concrete Mixer | Concrete Pumping Services |
---|---|---|---|
Performance | High mixing efficiency; suitable for large volumes | Moderate efficiency; best for small to medium projects | Very high efficiency; continuous flow for large projects |
Cost | Higher initial investment, but durable | Lower initial cost; affordable for small projects | Variable cost; pricing based on project scale and distance |
Ease of Implementation | Requires setup and space; needs skilled operators | Easy to transport and operate; minimal setup | Requires professional operators; logistical planning needed |
Maintenance | Regular maintenance needed; parts can be costly | Low maintenance; simple design | High maintenance; equipment downtime can be costly |
Best Use Case | Large-scale construction; batch mixing | Residential projects; small commercial applications | High-rise buildings; extensive infrastructure projects |
What Are the Advantages and Disadvantages of Portable Concrete Mixers?
Portable Concrete Mixer
Portable concrete mixers are compact and easy to transport, making them ideal for smaller projects or job sites with limited access. They are generally more affordable than traditional cement mixers, allowing for lower upfront costs. However, their mixing capacity and efficiency are limited compared to larger models. Additionally, operators must monitor the mixing process closely to ensure quality, which could lead to variability in the final product.
How Do Concrete Pumping Services Compare?
Concrete Pumping Services
Concrete pumping services offer a highly efficient solution for delivering concrete to difficult-to-reach locations or for large-scale projects. The continuous flow of concrete reduces labor time and speeds up the overall construction process. However, the costs can vary widely depending on the distance and volume of concrete required. Moreover, hiring professional operators is necessary, which can add to project expenses. Logistics planning is also crucial, as any delays can impact project timelines.
Conclusion: How to Choose the Right Cement Mixing Solution for Your Needs
When selecting the most suitable cement mixing solution, B2B buyers must carefully consider their specific project requirements, including scale, budget, and logistical challenges. While cement mixer manufacturers provide robust options for larger operations, alternatives like portable mixers and concrete pumping services may offer greater flexibility and efficiency for certain projects. By evaluating performance, cost-effectiveness, ease of implementation, and maintenance needs, buyers can make informed decisions that optimize their construction processes and enhance project outcomes.
Essential Technical Properties and Trade Terminology for cement mixer manufacturer
What Are the Key Technical Properties of Cement Mixers?
Understanding the technical properties of cement mixers is crucial for B2B buyers to ensure they select equipment that meets their operational needs. Here are several essential specifications:
-
Material Grade
The material grade of a cement mixer, typically stainless steel or high-strength carbon steel, determines its durability and resistance to corrosion. For buyers in regions with harsh weather, such as the Middle East or Africa, selecting a mixer made from high-grade materials can prolong the lifespan of the equipment and reduce maintenance costs. -
Mixing Capacity
This refers to the volume of concrete the mixer can handle in a single batch, often measured in liters or cubic meters. Buyers should assess their project requirements to ensure that the mixing capacity aligns with their production needs. For example, larger construction projects in South America may require mixers with higher capacities for efficiency. -
Tolerance Levels
Tolerance levels indicate how much deviation from specified dimensions a component can have. This is critical for ensuring that the mixer operates smoothly and produces a consistent mix. Buyers should inquire about tolerance specifications to avoid issues related to equipment performance, particularly when precision is vital in construction projects. -
Power Requirements
The power specifications—usually indicated in kilowatts (kW)—determine the mixer’s energy consumption and performance efficiency. Understanding these requirements helps buyers in Europe, where energy costs may be higher, to evaluate the total cost of ownership over time. -
Mixing Speed
This property indicates how quickly the mixer can achieve the desired consistency. A higher mixing speed can lead to increased productivity, which is beneficial for large-scale operations. Buyers should consider the trade-off between mixing speed and the quality of the final product, especially in high-stakes construction environments.
What Are Common Trade Terms in the Cement Mixer Industry?
Familiarizing yourself with industry-specific terminology can streamline negotiations and enhance communication with suppliers. Here are some common terms:
-
OEM (Original Equipment Manufacturer)
An OEM is a company that produces parts and equipment that may be marketed by another manufacturer. Understanding OEM relationships can help buyers identify reliable sources for spare parts and ensure quality standards are maintained. -
MOQ (Minimum Order Quantity)
This term refers to the smallest amount of product that a supplier is willing to sell. For international buyers, especially in Africa and South America, knowing the MOQ can help in budgeting and planning inventory effectively. -
RFQ (Request for Quotation)
An RFQ is a document sent to suppliers to request pricing and terms for specific products. Buyers should prepare detailed RFQs to receive accurate and competitive quotes, facilitating better decision-making. -
Incoterms (International Commercial Terms)
Incoterms are internationally recognized rules that define the responsibilities of buyers and sellers in international transactions. Familiarity with Incoterms, such as FOB (Free on Board) or CIF (Cost, Insurance, and Freight), is crucial for buyers to understand shipping responsibilities and costs. -
Lead Time
This term refers to the time it takes from placing an order to delivery. Understanding lead times is essential for project planning, especially for buyers in Europe who may face longer shipping durations due to distance and logistics complexities. -
Warranty Period
The warranty period is the time frame during which a manufacturer guarantees the quality and performance of their product. Buyers should always clarify warranty terms to protect their investments and ensure they receive support in case of defects or failures.
By grasping these technical properties and trade terms, B2B buyers can make informed decisions that align with their operational needs and enhance their competitive edge in the market.
Navigating Market Dynamics and Sourcing Trends in the cement mixer manufacturer Sector
What Are the Current Market Dynamics and Key Trends in the Cement Mixer Manufacturing Sector?
The cement mixer manufacturing sector is experiencing significant growth driven by several global factors. Increasing urbanization, particularly in Africa and South America, is propelling demand for efficient construction equipment. As infrastructure projects expand, international B2B buyers must stay attuned to emerging technologies such as IoT-enabled mixers that optimize performance and reduce operational costs. Furthermore, the adoption of automation and robotics in manufacturing processes is enhancing production efficiency, allowing manufacturers to meet rising demands while maintaining quality.
Sourcing trends are also evolving, with a marked shift towards local suppliers in various regions. This trend, particularly noticeable in the Middle East and Africa, aims to reduce lead times and transportation costs while supporting local economies. Buyers are increasingly prioritizing suppliers that can demonstrate agility and responsiveness to market changes. Additionally, the integration of data analytics in supply chain management is becoming prevalent, enabling companies to forecast demand accurately and manage inventories more effectively.
How Can Sustainability and Ethical Sourcing Impact the Cement Mixer Industry?
Sustainability is becoming a pivotal concern for B2B buyers in the cement mixer sector. The environmental impact of construction activities, including high carbon emissions from traditional cement production, necessitates a shift towards more sustainable practices. Buyers are encouraged to source from manufacturers that prioritize eco-friendly technologies and materials, such as recycled aggregates and low-carbon cement alternatives.
Moreover, the importance of ethical supply chains cannot be overstated. International buyers must ensure that their suppliers adhere to labor laws and environmental regulations. Certifications such as ISO 14001 for environmental management and the LEED certification for sustainable building practices are becoming critical benchmarks. By partnering with manufacturers who prioritize sustainability, buyers not only contribute to environmental preservation but also enhance their brand reputation in a market that increasingly values corporate social responsibility.
What Is the Brief Evolution of the Cement Mixer Manufacturing Sector?
The cement mixer manufacturing sector has evolved significantly over the last century. Initially, manual mixing was the norm, but the advent of mechanized mixers in the early 20th century revolutionized construction practices. As global demand for concrete surged, manufacturers began to innovate, introducing electric and diesel-powered mixers to enhance efficiency and productivity.
In recent decades, the focus has shifted towards technological advancements, with the integration of digital tools and automation reshaping production lines. This evolution has not only improved the performance and durability of cement mixers but has also aligned with the broader trends of sustainability and efficiency that are now defining the industry. As international B2B buyers navigate this landscape, understanding these historical shifts can provide valuable insights into current market dynamics and future opportunities.
Frequently Asked Questions (FAQs) for B2B Buyers of cement mixer manufacturer
-
How do I choose the right cement mixer manufacturer for my business needs?
Choosing the right cement mixer manufacturer involves evaluating several key factors. Start by assessing the manufacturer’s experience in the industry and their reputation among existing clients. Look for certifications or compliance with international quality standards, such as ISO 9001. Additionally, consider the range of products offered and whether they provide customization options to meet specific project requirements. Finally, request references and case studies to gauge the manufacturer’s reliability and customer service. -
What are the typical payment terms offered by cement mixer manufacturers?
Payment terms can vary significantly among manufacturers. Common options include upfront deposits ranging from 20-50% with the balance due upon delivery. Some manufacturers might offer net payment terms, such as 30 or 60 days post-delivery. It’s crucial to discuss and negotiate these terms upfront to avoid misunderstandings. Ensure you also inquire about acceptable payment methods, including bank transfers, letters of credit, or online payment platforms, especially if dealing with international suppliers. -
What is the minimum order quantity (MOQ) for cement mixers?
The minimum order quantity (MOQ) for cement mixers often depends on the manufacturer and the specific model. Generally, MOQs can range from one unit for smaller manufacturers to several units for larger ones. It’s essential to clarify this during negotiations, as some manufacturers may offer flexibility based on your business needs or future orders. Understanding the MOQ will help you plan your budget and inventory accordingly, particularly if you’re entering a new market. -
How can I ensure quality assurance when sourcing from cement mixer manufacturers?
To ensure quality assurance, request detailed information about the manufacturer’s quality control processes. This should include inspections during production and final testing before shipment. Ask for certifications that demonstrate compliance with international quality standards. Additionally, consider arranging for third-party inspections or audits, especially for large orders. Building a strong communication channel with the manufacturer can also help you address any quality concerns promptly. -
What are the logistics considerations for importing cement mixers from international manufacturers?
When importing cement mixers, consider logistics factors such as shipping costs, delivery timelines, and customs regulations. Work with logistics providers experienced in heavy machinery to navigate these complexities. Understand the Incoterms (International Commercial Terms) that define responsibilities between you and the manufacturer regarding shipping and insurance. Also, factor in potential delays at customs and ensure that all necessary documentation is in order to facilitate a smooth import process. -
Can I customize cement mixers to fit specific project requirements?
Many cement mixer manufacturers offer customization options to meet unique project needs. Customizations can include modifications to size, capacity, mixing technology, or additional features like mobile setups. When discussing customization, provide clear specifications and understand the associated costs and lead times. Collaborating closely with the manufacturer during the design phase can lead to better outcomes and ensure the final product aligns with your operational requirements. -
What certifications should I look for when selecting a cement mixer manufacturer?
When selecting a cement mixer manufacturer, look for certifications that indicate compliance with international standards. Key certifications include ISO 9001 for quality management systems and CE marking for products sold in Europe. Additionally, consider industry-specific certifications like ASTM or AASHTO if applicable to your region. These certifications not only validate the manufacturer’s commitment to quality but also enhance your business’s credibility when presenting the equipment to clients. -
How can I vet international cement mixer suppliers to avoid scams?
To vet international cement mixer suppliers, start by conducting thorough research on their background and reputation. Use platforms like LinkedIn, industry forums, and trade associations to gather insights. Request company documents, such as business licenses, and check for any legal disputes. Establish direct communication and ask for references from previous clients, ideally in your region. Additionally, consider visiting the manufacturing facility or using trusted third-party services to perform on-site evaluations to ensure legitimacy.
Important Disclaimer & Terms of Use
⚠️ Important Disclaimer
The information provided in this guide, including content regarding manufacturers, technical specifications, and market analysis, is for informational and educational purposes only. It does not constitute professional procurement advice, financial advice, or legal advice.
While we have made every effort to ensure the accuracy and timeliness of the information, we are not responsible for any errors, omissions, or outdated information. Market conditions, company details, and technical standards are subject to change.
B2B buyers must conduct their own independent and thorough due diligence before making any purchasing decisions. This includes contacting suppliers directly, verifying certifications, requesting samples, and seeking professional consultation. The risk of relying on any information in this guide is borne solely by the reader.
Strategic Sourcing Conclusion and Outlook for cement mixer manufacturer
In the ever-evolving landscape of construction equipment, strategic sourcing plays a pivotal role for international B2B buyers of cement mixers. By leveraging a comprehensive understanding of supplier capabilities, market dynamics, and regional trends, businesses can make informed decisions that lead to cost savings and enhanced operational efficiency. Buyers from Africa, South America, the Middle East, and Europe should prioritize building relationships with manufacturers that demonstrate reliability, innovation, and a commitment to sustainability.
How Can Strategic Sourcing Improve Your Cement Mixer Procurement?
Investing time in strategic sourcing not only mitigates risks associated with supply chain disruptions but also opens avenues for negotiating favorable terms and conditions. Buyers should actively engage with multiple suppliers, assess their production capacities, and evaluate their adherence to quality standards. Additionally, utilizing digital tools and platforms can streamline the sourcing process, making it easier to compare offerings and ensure alignment with specific project requirements.
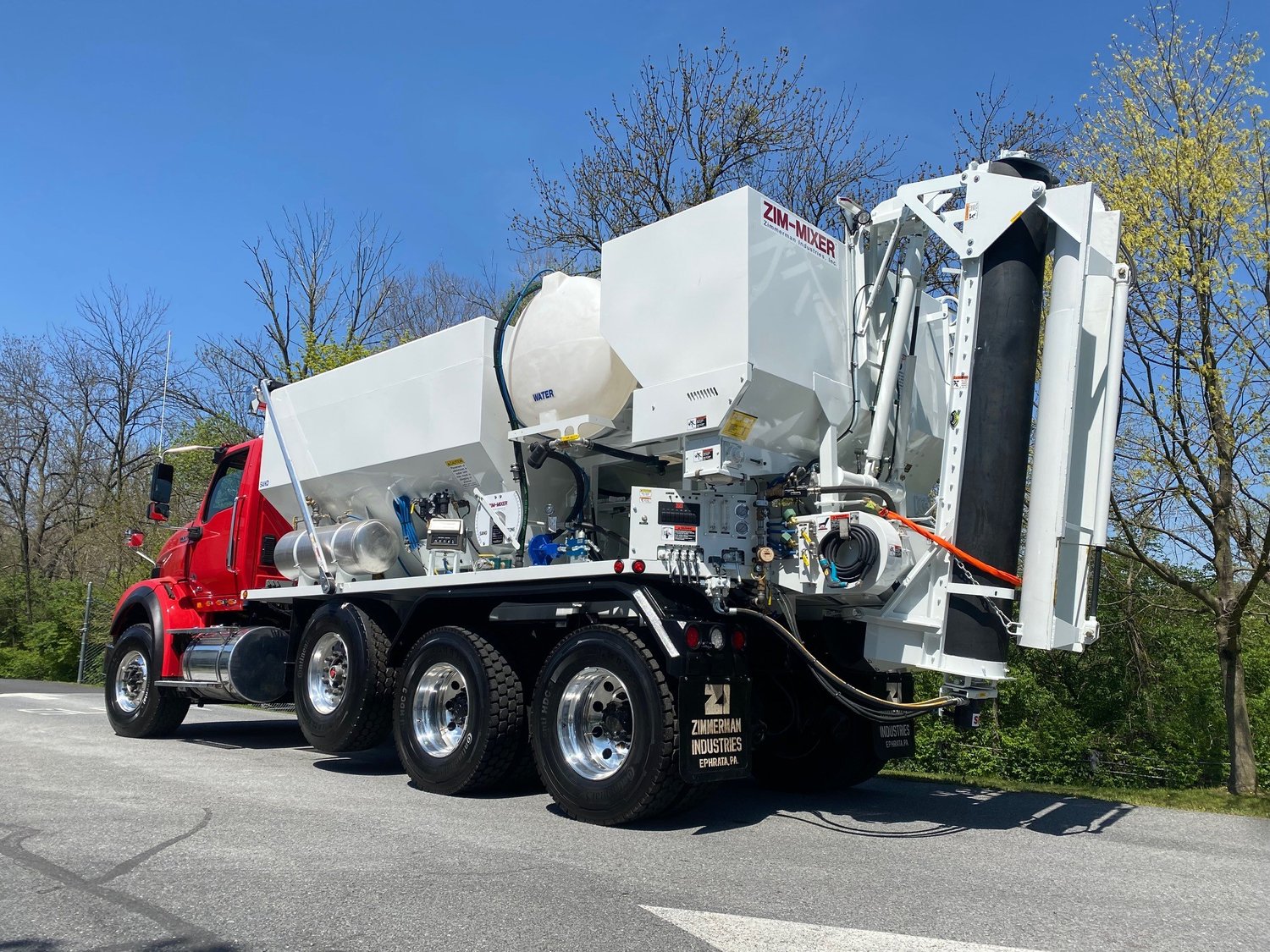
A stock image related to cement mixer manufacturer.
What Lies Ahead for Cement Mixer Manufacturers and Buyers?
As the demand for construction projects continues to rise globally, particularly in emerging markets, the outlook for cement mixer manufacturers remains promising. International B2B buyers are encouraged to stay ahead of trends by embracing technological advancements and sustainable practices in their sourcing strategies. By fostering strong partnerships and remaining agile in their procurement processes, companies can not only meet current demands but also prepare for future opportunities in an increasingly competitive market.
Now is the time for buyers to take decisive action—evaluate your sourcing strategies, explore new partnerships, and position your business for success in the dynamic world of construction equipment.