Unlock Quality: The Ultimate Furniture Custom Guide (2025)
Introduction: Navigating the Global Market for furniture custom
In the dynamic landscape of global commerce, sourcing custom furniture solutions presents both opportunities and challenges for international B2B buyers. With the growing demand for unique, tailored designs that meet specific operational needs—such as sourcing ergonomic office furniture for enhanced productivity—businesses must navigate a complex marketplace filled with diverse suppliers and varying quality standards. This guide aims to demystify the process of acquiring custom furniture, providing comprehensive insights into the types of furniture available, their applications, and essential criteria for supplier vetting.
From understanding the nuances of material selection to evaluating production capabilities and cost structures, this guide empowers B2B buyers from Africa, South America, the Middle East, and Europe—including key markets like Spain and Germany—to make informed purchasing decisions. We will explore the critical aspects of the custom furniture market, including design trends, sustainability considerations, and logistical challenges, enabling businesses to align their procurement strategies with their brand identity and operational requirements.
By arming buyers with actionable insights, this guide serves as a valuable resource for navigating the intricacies of the global furniture custom market, ensuring that your investment translates into functional, stylish, and durable solutions that enhance your business environment. Whether you’re a seasoned buyer or new to the custom furniture landscape, understanding these elements is crucial for achieving success in today’s competitive marketplace.
Understanding furniture custom Types and Variations
Type Name | Key Distinguishing Features | Primary B2B Applications | Brief Pros & Cons for Buyers |
---|---|---|---|
Modular Furniture | Flexible configurations, easy assembly, and transport | Office spaces, co-working environments | Pros: Customizable; space-efficient. Cons: May lack durability if not designed well. |
Bespoke Furniture | Tailored designs based on specific client needs | High-end retail, luxury hotels | Pros: Unique, personalized designs. Cons: Higher cost and longer lead times. |
Eco-Friendly Furniture | Made from sustainable materials, often with minimal waste | Corporate offices, eco-conscious brands | Pros: Supports sustainability goals; marketable. Cons: Can be more expensive. |
Ergonomic Furniture | Designed for comfort and efficiency, often adjustable | Healthcare facilities, corporate offices | Pros: Enhances productivity; reduces injury risk. Cons: May require more investment. |
Multi-Functional Furniture | Combines multiple uses in a single piece | Small apartments, event spaces | Pros: Maximizes space; versatile. Cons: Complexity can affect usability. |
What is Modular Furniture and How Can It Benefit Your Business?
Modular furniture is characterized by its flexible configurations and ease of assembly, making it a popular choice for modern office spaces and co-working environments. This type of furniture can be easily reconfigured to adapt to changing needs, which is particularly valuable for businesses that experience growth or shifts in team dynamics. When purchasing modular furniture, B2B buyers should consider the quality of materials and design, ensuring that they strike a balance between flexibility and durability.
Why Choose Bespoke Furniture for Your High-End Projects?
Bespoke furniture refers to custom-made pieces tailored to the specific needs and preferences of the buyer. This type of furniture is ideal for high-end retail spaces and luxury hotels where unique aesthetics can significantly enhance the customer experience. While bespoke furniture offers unparalleled uniqueness and personalization, B2B buyers must be prepared for higher costs and longer lead times, making it essential to plan ahead when integrating these pieces into their projects.
How Can Eco-Friendly Furniture Align with Your Sustainability Goals?
Eco-friendly furniture is crafted from sustainable materials and often focuses on reducing waste during production. As businesses increasingly prioritize sustainability, this type of furniture is becoming a preferred choice for corporate offices and brands that want to reflect their eco-conscious values. While eco-friendly options can sometimes be more expensive, they serve as a strong marketing tool and can enhance a brand’s reputation among environmentally aware consumers.
What Are the Benefits of Ergonomic Furniture in the Workplace?
Ergonomic furniture is designed to promote comfort and efficiency, often featuring adjustable elements to cater to individual user needs. This type of furniture is particularly beneficial in healthcare facilities and corporate offices, where enhancing employee productivity and reducing the risk of injury are top priorities. When considering ergonomic solutions, B2B buyers should evaluate the range of adjustability and the quality of materials to ensure long-term benefits for their workforce.
How Does Multi-Functional Furniture Maximize Space?
Multi-functional furniture combines various uses into a single piece, making it ideal for small apartments and event spaces where maximizing available space is crucial. This type of furniture can serve multiple purposes, such as a sofa that converts into a bed or a table that doubles as a storage unit. While it offers versatility, buyers should carefully assess the complexity of the designs to ensure usability and practicality in their intended environments.
Related Video: Ikea MALM bed variations explained
Key Industrial Applications of furniture custom
Industry/Sector | Specific Application of furniture custom | Value/Benefit for the Business | Key Sourcing Considerations for this Application |
---|---|---|---|
Hospitality | Customized hotel furniture | Enhances guest experience and brand differentiation | Local regulations, sustainability, and design trends |
Corporate Offices | Tailored office workstations | Boosts employee productivity and morale | Ergonomics, scalability, and material quality |
Retail | Bespoke retail displays and fixtures | Increases product visibility and sales | Durability, aesthetic alignment, and lead times |
Healthcare | Specialized patient room furniture | Improves patient comfort and operational efficiency | Compliance with health standards and customization |
Education | Custom classroom and library furniture | Facilitates collaborative learning environments | Flexibility, durability, and adaptability |
How is Customized Furniture Used in the Hospitality Sector?
In the hospitality industry, customized hotel furniture plays a crucial role in creating unique guest experiences. Hotels often require bespoke furniture that reflects their brand identity while meeting the specific needs of their clientele. This can include everything from stylish lobby seating to functional in-room desks. By investing in custom furniture, hotels can enhance their aesthetic appeal, improve guest comfort, and differentiate themselves from competitors. International buyers should consider local regulations regarding materials and design, as well as sustainability practices, to align with market expectations.
What Are the Benefits of Custom Office Workstations in Corporate Offices?
Tailored office workstations are essential for corporate environments aiming to boost productivity and employee satisfaction. Custom office furniture can be designed to fit the specific layout of a workspace, allowing for efficient use of space and promoting collaboration. Ergonomic considerations are paramount, ensuring that the furniture supports the well-being of employees. When sourcing custom office solutions, international buyers must prioritize material quality and scalability to accommodate future growth, as well as ensure that the design aligns with current workplace trends.
How Do Customized Retail Displays Impact Sales?
In the retail sector, bespoke displays and fixtures can significantly enhance product visibility and overall sales performance. Customized furniture solutions allow retailers to showcase their products in a way that aligns with their branding and marketing strategies. For instance, a unique display can draw customers’ attention and encourage impulse purchases. Retailers looking to source custom furniture should focus on durability, aesthetic alignment with their brand, and lead times to ensure timely delivery, especially in competitive markets.
Why is Custom Furniture Important in Healthcare Settings?
In healthcare, specialized patient room furniture is vital for improving both comfort and operational efficiency. Custom solutions can include adjustable beds, accessible seating, and storage that meets specific healthcare standards. These tailored pieces not only enhance patient comfort but also streamline the workflow for medical staff. For international buyers in the healthcare sector, compliance with health regulations and the ability to customize furniture to meet specific needs are critical factors to consider when sourcing.
How Can Custom Classroom Furniture Enhance Learning Environments?
Educational institutions benefit significantly from custom classroom and library furniture designed to facilitate collaborative learning. Custom solutions can include modular tables, ergonomic seating, and flexible storage options that adapt to various teaching methods. This adaptability promotes an engaging learning atmosphere that can cater to different educational needs. Buyers from the education sector should prioritize flexibility, durability, and the ability to adapt to evolving educational practices when sourcing custom furniture solutions.
Related Video: Industrial automation with collaborative robots – Pick and place
3 Common User Pain Points for ‘furniture custom’ & Their Solutions
Scenario 1: Navigating Lengthy Lead Times for Custom Furniture Orders
The Problem: One of the most significant challenges faced by B2B buyers in the furniture custom sector is extended lead times. Buyers often require quick turnarounds for projects, but many manufacturers have lengthy production cycles, which can lead to delays in project timelines and increased costs. For instance, a hotel in Spain may need custom furniture for a new location opening in two months but faces a lead time of three months. Such delays can disrupt planned openings, resulting in lost revenue and dissatisfaction among stakeholders.
The Solution: To mitigate this issue, buyers should establish clear communication channels with manufacturers from the outset. It is crucial to inquire about production timelines and any potential bottlenecks during the ordering process. Additionally, consider working with manufacturers who offer expedited services or have local production facilities, which can significantly reduce shipping times. Leveraging technology such as project management tools can also aid in tracking progress and ensuring that all parties are aligned on timelines. Lastly, building a long-term relationship with a reliable supplier can lead to more favorable lead times in the future, as they become familiar with your needs and capabilities.
Scenario 2: Ensuring Quality and Craftsmanship in Custom Furniture
The Problem: Quality assurance is a common concern for B2B buyers, especially when sourcing custom furniture from different regions, such as Africa or the Middle East. Buyers often worry about receiving products that do not meet their specifications or expectations. For instance, a company in Germany may order custom office furniture that appears sturdy in design but falls short in durability upon delivery, leading to potential issues with usability and brand reputation.
The Solution: To ensure quality and craftsmanship, it is essential to conduct thorough due diligence on potential suppliers. This includes requesting samples and reviewing their production processes. Buyers should visit manufacturing facilities whenever possible or engage third-party inspection services to verify quality before shipment. Establishing clear specifications and utilizing detailed contracts that outline quality standards can also safeguard against subpar products. Consider incorporating a phased delivery approach, where initial orders are smaller, allowing buyers to evaluate quality before committing to larger quantities.
Scenario 3: Managing Cultural and Design Preferences in Global Projects
The Problem: For international B2B buyers, particularly those operating across diverse markets like South America and Europe, managing different cultural and design preferences can be a daunting task. A furniture company may struggle to create pieces that resonate with local aesthetics while maintaining a consistent brand identity. For example, a firm looking to furnish a luxury hotel in Dubai may find that the local market favors ornate designs, while their standard offerings are more minimalist and modern.
The Solution: To address this challenge, buyers should conduct comprehensive market research to understand local tastes and preferences. This can include engaging with local designers or consultants who can provide insights into cultural nuances and popular trends. Collaborating with manufacturers who offer flexible design options can also help bridge the gap between brand identity and local preferences. Encourage designers to create versatile pieces that can be easily adapted for different markets while retaining core brand elements. Moreover, consider holding focus groups with potential users to gather feedback on designs before finalizing orders, ensuring that the final products resonate with the target audience.
By addressing these common pain points effectively, B2B buyers can enhance their experience in the custom furniture market, ultimately leading to successful projects and satisfied clients.
Strategic Material Selection Guide for furniture custom
When selecting materials for custom furniture, international B2B buyers must consider various factors that impact product performance, compliance, and market preferences. Below, we analyze four common materials used in furniture custom, focusing on their key properties, advantages, disadvantages, and specific considerations for buyers from Africa, South America, the Middle East, and Europe.

A stock image related to furniture custom.
What Are the Key Properties of Wood in Custom Furniture?
Wood is one of the most traditional materials used in furniture making. Its properties vary significantly based on the type of wood, but generally, it offers excellent strength and aesthetic appeal.
- Key Properties: Wood has a natural ability to withstand moderate temperature variations and is generally not prone to corrosion. However, its performance can be affected by humidity and temperature fluctuations, leading to warping or cracking.
- Pros & Cons: Wood is highly durable and can last for decades if maintained properly. It is relatively easy to work with, allowing for intricate designs. However, the cost can vary widely depending on the type of wood, and high-quality hardwoods can be expensive. Additionally, wood requires regular maintenance to prevent damage from pests or moisture.
- Impact on Application: Wood is compatible with various finishes and can be tailored to meet specific aesthetic requirements. However, it may not be suitable for environments with extreme temperature or humidity levels.
- Considerations for International Buyers: Buyers should ensure compliance with local regulations regarding sustainable sourcing and treatment of wood. Standards such as the Forest Stewardship Council (FSC) certification are increasingly important in Europe.
How Does Metal Influence the Durability of Custom Furniture?
Metal is often used in furniture for its structural integrity and modern aesthetic. Common metals include steel, aluminum, and wrought iron.
- Key Properties: Metals are highly resistant to wear and tear, withstanding high pressure and temperature. They are also non-combustible and resistant to corrosion, especially when treated.
- Pros & Cons: Metal furniture is known for its durability and strength, making it suitable for high-traffic areas. However, it can be heavier and more complex to manufacture than wood. The initial cost may be higher, but its longevity can offset this expense.
- Impact on Application: Metal is ideal for contemporary designs and can be combined with other materials, such as glass or wood, to create unique pieces. However, it may not be suitable for environments with high humidity unless specifically treated.
- Considerations for International Buyers: Compliance with standards such as ASTM for metals is crucial, especially in regions like Europe where safety regulations are stringent.
What Are the Benefits of Using Upholstery Fabrics in Custom Furniture?
Upholstery fabrics add comfort and style to furniture, making them essential for seating solutions.
- Key Properties: Fabrics vary widely in durability, with some offering high abrasion resistance and others focusing on aesthetic appeal. They can also provide thermal insulation, making them suitable for various climates.
- Pros & Cons: Upholstered furniture is comfortable and can be customized in numerous colors and patterns. However, fabric can be more challenging to clean and maintain, and some materials may fade over time. The cost can also vary significantly based on fabric type.
- Impact on Application: Upholstered pieces are ideal for residential and commercial use, but the choice of fabric should consider the intended use—high-traffic areas may require more durable options.
- Considerations for International Buyers: Buyers should be aware of fabric standards, such as the flammability regulations in Europe, to ensure compliance and safety.
Why Choose Composite Materials for Custom Furniture?
Composite materials, such as engineered wood and MDF, are increasingly popular in furniture manufacturing due to their versatility.
- Key Properties: Composites are designed to provide uniform strength and stability, resisting warping and cracking better than solid wood. They can also be engineered to meet specific performance requirements.
- Pros & Cons: These materials are often more cost-effective than solid wood and can be produced in large quantities with consistent quality. However, they may not offer the same aesthetic appeal as natural wood and can be less durable over time.
- Impact on Application: Composites are suitable for a wide range of applications, from cabinetry to decorative furniture. However, they may not perform well in environments with high moisture.
- Considerations for International Buyers: Buyers should check for compliance with standards such as CARB (California Air Resources Board) for emissions, which is particularly relevant in markets like Europe.
Summary Table of Material Selection for Custom Furniture
Material | Typical Use Case for furniture custom | Key Advantage | Key Disadvantage/Limitation | Relative Cost (Low/Med/High) |
---|---|---|---|---|
Wood | Traditional furniture, cabinets | Aesthetic appeal and durability | Requires maintenance and can warp | Medium to High |
Metal | Modern furniture, frames | High strength and durability | Heavier and complex to manufacture | Medium to High |
Upholstery Fabrics | Sofas, chairs, cushions | Comfort and customization | Difficult to clean and maintain | Low to Medium |
Composite Materials | Cabinets, decorative furniture | Cost-effective and consistent quality | Less aesthetic appeal than wood | Low to Medium |
This strategic material selection guide provides valuable insights for international B2B buyers, enabling them to make informed decisions that align with their specific needs and market requirements.
In-depth Look: Manufacturing Processes and Quality Assurance for furniture custom
What Are the Key Stages in the Manufacturing Process of Custom Furniture?
The manufacturing process for custom furniture involves several critical stages that ensure the final product meets both design specifications and quality standards. Understanding these stages can significantly aid B2B buyers in making informed decisions.
-
Material Preparation: This initial stage involves sourcing high-quality raw materials, such as wood, metal, or upholstery fabric. Buyers should consider suppliers that prioritize sustainable sourcing, as this not only meets consumer demand but also complies with increasingly stringent environmental regulations. Proper material handling, including acclimatization for wood to prevent warping, is crucial.
-
Forming: In this phase, raw materials are shaped into specific components using various techniques such as cutting, bending, and molding. Advanced technologies like CNC (Computer Numerical Control) machining ensure precision and repeatability, which are essential for high-end custom furniture. For B2B buyers, understanding the machinery used can provide insights into the supplier’s capabilities.
-
Assembly: The assembly process combines different components into a finished product. Techniques such as joinery, doweling, and the use of adhesives are common. Buyers should assess the assembly methods employed by suppliers to ensure durability and structural integrity. This stage often involves skilled craftsmanship, which adds value to the final product.
-
Finishing: This final stage enhances the aesthetic appeal and durability of the furniture. Techniques include staining, painting, and applying protective coatings. B2B buyers should inquire about the finishing processes to ensure they align with their quality expectations and market preferences, especially in regions where specific finishes may be favored.
How Is Quality Assurance Implemented in Custom Furniture Manufacturing?
Quality assurance (QA) is a vital component in the manufacturing of custom furniture. It ensures that products not only meet design specifications but also adhere to international and industry-specific standards.
-
International Standards for Quality Control: Many manufacturers adhere to ISO 9001, which sets criteria for a quality management system. This standard emphasizes a process approach to continuous improvement and customer satisfaction. Buyers from Africa, South America, the Middle East, and Europe should verify if their suppliers are ISO certified, as this can indicate a commitment to quality.
-
Industry-Specific Certifications: Depending on the market, additional certifications such as CE (Conformité Européenne) for products sold in Europe or API (American Petroleum Institute) for specific industrial furniture may apply. Understanding these certifications can help buyers ensure compliance with local regulations and enhance their brand’s credibility.
What Are the Key Quality Control Checkpoints in Furniture Manufacturing?
Quality control is typically integrated throughout the manufacturing process with several critical checkpoints:
-
Incoming Quality Control (IQC): This initial check involves inspecting raw materials upon arrival. It ensures that materials meet predetermined specifications before they enter the production line. B2B buyers should request IQC reports to verify the quality of materials used.
-
In-Process Quality Control (IPQC): During the manufacturing process, periodic inspections are conducted to monitor quality at various stages. This may involve checking dimensions, structural integrity, and adherence to design specifications. Buyers should inquire about the frequency and methods of IPQC to understand how proactive the supplier is regarding quality.
-
Final Quality Control (FQC): Before shipping, a final inspection ensures that the finished product meets all quality standards. This includes checking for defects, proper assembly, and finish quality. Buyers can request FQC reports and sample products to assess quality firsthand.
How Can B2B Buyers Verify Supplier Quality Control?
Verifying the quality control practices of a supplier is essential for B2B buyers, especially when sourcing custom furniture internationally.
-
Supplier Audits: Conducting audits is one of the most effective ways to assess a supplier’s quality control processes. This can involve on-site visits to evaluate their manufacturing practices, quality management systems, and compliance with international standards.
-
Quality Reports: Suppliers should provide detailed quality reports that outline their QC processes, inspection results, and any corrective actions taken. Reviewing these documents can offer insight into the supplier’s commitment to quality.
-
Third-Party Inspections: Engaging third-party inspection agencies can provide an unbiased assessment of the supplier’s quality control. These agencies can conduct random inspections throughout the manufacturing process and offer certifications that verify compliance with international standards.
What Are the Quality Control Nuances for International B2B Buyers?
B2B buyers from different regions must consider specific quality control nuances that can impact their purchasing decisions.
-
Regional Compliance Standards: Each region has unique compliance standards that can affect the quality of custom furniture. For instance, European buyers may prioritize CE certification, while buyers in the Middle East might focus on specific local standards. Understanding these nuances is crucial for avoiding compliance issues.
-
Cultural Expectations: Different markets may have varying expectations regarding quality and design. For example, European buyers might favor minimalistic designs, while buyers from Africa may prefer vibrant colors and patterns. Recognizing these cultural preferences can guide buyers in selecting suppliers that align with their target market.
-
Communication and Transparency: Effective communication is vital when dealing with international suppliers. B2B buyers should establish clear expectations regarding quality and ensure that suppliers are transparent about their manufacturing processes and quality control measures. This can help mitigate misunderstandings and foster stronger business relationships.
Conclusion: Navigating the Manufacturing and Quality Assurance Landscape for Custom Furniture
Understanding the manufacturing processes and quality assurance practices involved in custom furniture production is essential for B2B buyers. By focusing on the key stages of manufacturing, relevant quality standards, and effective verification methods, buyers can make informed decisions that align with their business needs and market demands. Prioritizing quality assurance not only enhances the final product but also strengthens supplier relationships, ultimately leading to successful international business ventures.
Practical Sourcing Guide: A Step-by-Step Checklist for ‘furniture custom’
In the rapidly evolving global market, sourcing custom furniture requires a structured approach to ensure quality, cost-effectiveness, and timely delivery. This guide provides a step-by-step checklist tailored for B2B buyers from diverse regions, including Africa, South America, the Middle East, and Europe. By following these actionable insights, businesses can streamline their procurement processes and achieve better outcomes.
Step 1: Define Your Technical Specifications
Establishing clear technical specifications is essential for custom furniture procurement. This includes detailing materials, dimensions, finishes, and design elements that align with your brand’s vision. Be specific about any compliance requirements relevant to your region, such as safety standards or environmental certifications.
- Materials: Specify preferred types (e.g., solid wood, metal, upholstery).
- Dimensions: Provide exact measurements to avoid costly revisions later.
Step 2: Identify Your Budget Constraints
Understanding your budget is crucial for making informed sourcing decisions. Custom furniture can vary significantly in cost depending on materials and craftsmanship. Clearly outline your financial parameters to suppliers to facilitate realistic proposals.
- Costing Breakdown: Ask suppliers for detailed quotes that include material, labor, and shipping costs.
- Contingency Funds: Consider setting aside additional budget for unforeseen expenses.
Step 3: Evaluate Potential Suppliers
Before making a commitment, it’s vital to assess potential suppliers thoroughly. Request company profiles, case studies, and references from buyers in similar industries or regions. This evaluation ensures that the supplier can meet your quality standards and delivery timelines.
- Supplier Reputation: Investigate online reviews and industry forums for feedback.
- Production Capacity: Confirm that the supplier can handle your order volume within your required timeframe.
Step 4: Request Prototypes or Samples
Requesting prototypes or samples is a critical step in the custom furniture sourcing process. This allows you to evaluate the quality and craftsmanship before placing a larger order. It also provides an opportunity to make necessary adjustments based on tangible feedback.
- Material Quality: Inspect the materials used to ensure they match your specifications.
- Design Accuracy: Verify that the prototype aligns with your design vision.
Step 5: Confirm Lead Times and Delivery Terms
Understanding lead times and delivery terms is essential for project planning. Discuss and agree on realistic timelines for production and shipping to avoid disruptions in your operations.
- Shipping Options: Explore different shipping methods and their associated costs.
- Contingency Plans: Establish what measures will be taken if delays occur.
Step 6: Negotiate Payment Terms
Negotiating favorable payment terms can enhance cash flow management. Discuss options such as deposits, milestone payments, or payment upon delivery to find a mutually beneficial arrangement.
- Payment Flexibility: Consider terms that allow for adjustments based on project progress.
- Currency Considerations: Be aware of currency fluctuations, especially in international transactions.
Step 7: Finalize Contracts and Agreements
Once you’ve selected a supplier, it’s time to finalize contracts and agreements. Ensure that all specifications, timelines, payment terms, and warranties are clearly outlined. This legal framework protects both parties and minimizes potential disputes.
- Review Clauses: Pay attention to clauses related to cancellations, modifications, and liability.
- Legal Compliance: Ensure the contract adheres to local laws and regulations pertinent to your business.
By adhering to this sourcing checklist, B2B buyers can effectively navigate the complexities of procuring custom furniture, ensuring that their investments yield high-quality products tailored to their needs.
Comprehensive Cost and Pricing Analysis for furniture custom Sourcing
What Are the Key Cost Components in Custom Furniture Sourcing?
When sourcing custom furniture, understanding the cost structure is essential for international B2B buyers. The primary cost components include:
-
Materials: The choice of materials significantly impacts overall costs. High-quality hardwoods, eco-friendly finishes, or specialty textiles can raise expenses. Buyers should consider sourcing materials locally to mitigate costs or opting for alternative materials that provide a similar aesthetic without the premium price.
-
Labor: Labor costs vary widely depending on the region and skill level of the workforce. In Africa and South America, labor can be more affordable, while skilled craftsmen in Europe might command higher wages. Understanding local labor markets is crucial for accurate budgeting.
-
Manufacturing Overhead: This includes utilities, rent, and other operational costs incurred during production. Overhead can vary by region, affecting the final price. Buyers should inquire about the supplier’s facility and the efficiency of their operations.
-
Tooling: Custom designs may require specific tools or molds, which can add to initial costs. This is especially relevant for intricate designs or large-volume orders. Buyers should factor these costs into their total investment.
-
Quality Control (QC): Ensuring product quality may involve additional costs, particularly if third-party inspections are required. Implementing a robust QC process is essential to avoid issues that could arise during shipping or after delivery.
-
Logistics: Shipping costs can significantly influence total expenses, particularly for international transactions. Factors such as distance, shipping method, and customs duties should be considered. Employing local logistics partners can streamline this process.
-
Margin: Suppliers typically add a margin to cover their costs and profit. Understanding the market rates and negotiating effectively can help secure better pricing.
How Do Price Influencers Impact Custom Furniture Sourcing?
Several factors influence pricing in the custom furniture sector:
-
Volume and Minimum Order Quantity (MOQ): Larger orders often lead to lower per-unit costs due to economies of scale. Buyers should assess their purchasing power and consider consolidating orders with other businesses to meet MOQs.
-
Specifications and Customization: The complexity of design specifications can affect pricing. Highly customized pieces may require more time and resources, leading to higher costs. Clear communication about design requirements can help manage expectations and costs.
-
Material Selection: The choice of materials not only influences aesthetics but also durability and cost. Sustainable or exotic materials may incur higher costs but can enhance product value in the long run.
-
Quality Certifications: Certifications can assure buyers of a product’s quality and sustainability, but they may also add to costs. Assess the relevance of certifications based on your market and customer demands.
-
Supplier Factors: The reputation, reliability, and experience of the supplier can impact pricing. Established suppliers may charge a premium for their expertise, while newer entrants may offer competitive pricing to gain market share.
-
Incoterms: Understanding international shipping terms is vital. Incoterms dictate who is responsible for shipping, insurance, and tariffs, affecting overall costs. Buyers should negotiate terms that minimize their risk and financial exposure.
What Are Effective Buyer Tips for Cost-Efficiency in Custom Furniture Sourcing?
To optimize costs while sourcing custom furniture, B2B buyers should consider the following strategies:
-
Negotiate Pricing: Engage in open discussions about pricing structures and be prepared to negotiate based on your order size and frequency. Building a relationship with suppliers can lead to better deals over time.
-
Evaluate Total Cost of Ownership (TCO): Look beyond the initial purchase price. Consider factors such as durability, maintenance, and potential resale value. Investing in quality can lead to lower long-term costs.
-
Understand Pricing Nuances for International Transactions: Be aware of currency fluctuations, tariffs, and import duties that may affect the final price. Staying informed about geopolitical developments can also provide insights into potential cost changes.
-
Conduct Market Research: Compare prices and offerings from multiple suppliers across different regions to identify competitive pricing. Utilize trade shows and online platforms to gather information and connect with potential partners.
Disclaimer
Prices indicated in this analysis are for illustrative purposes only and may vary based on specific project requirements, market conditions, and supplier negotiations. Always conduct thorough due diligence and obtain formal quotes to ensure accurate budgeting for your custom furniture sourcing needs.
Alternatives Analysis: Comparing furniture custom With Other Solutions
When considering furniture custom solutions, it is essential for international B2B buyers to evaluate viable alternatives that may meet their specific needs. Each option has its own set of advantages and drawbacks, making it critical to analyze the best fit for your business context, budget, and operational requirements. This section compares furniture custom with two alternative solutions: ready-made furniture and modular furniture systems.
Comparison Aspect | Furniture Custom | Ready-Made Furniture | Modular Furniture Systems |
---|---|---|---|
Performance | Tailored to specific needs | Standardized quality | Versatile and adaptable |
Cost | Higher initial investment | Generally lower cost | Moderate, depending on design |
Ease of Implementation | Longer lead times | Quick delivery | Requires planning and assembly |
Maintenance | Dependent on materials used | Often low maintenance | Moderate, depending on usage |
Best Use Case | Unique projects or branding | Bulk purchases, short-term | Dynamic spaces, reconfiguration |
What Are the Advantages and Disadvantages of Ready-Made Furniture for B2B Buyers?
Ready-made furniture is widely available and often less expensive than custom solutions. It offers a range of styles and finishes, making it suitable for businesses needing quick solutions. However, the lack of customization can limit brand identity and functionality for specific use cases. Buyers should consider this option if they prioritize cost and speed over uniqueness.
How Do Modular Furniture Systems Offer Flexibility for Businesses?
Modular furniture systems provide a flexible and adaptable solution for dynamic workspaces. These systems allow businesses to reconfigure their environments easily, catering to changing needs. However, they may require more upfront planning and assembly than ready-made options. This alternative is ideal for companies looking to future-proof their workspace and invest in adaptable solutions.
How to Choose the Right Furniture Solution for Your Business Needs?
In conclusion, the choice between furniture custom, ready-made, and modular furniture systems depends on your specific business requirements. If your priority is uniqueness and alignment with brand identity, furniture custom is likely the best fit despite higher costs and longer lead times. Conversely, if immediate availability and budget constraints are paramount, ready-made options may suffice. For businesses anticipating growth and change, modular systems offer a balanced solution with flexibility for future reconfiguration. Assess your goals, budget, and operational needs carefully to determine the most suitable furniture solution for your organization.
Essential Technical Properties and Trade Terminology for furniture custom
What Are the Key Technical Properties of Custom Furniture?
Understanding the technical properties of custom furniture is crucial for international B2B buyers. These specifications not only affect the quality and durability of the furniture but also influence procurement decisions and cost considerations.
1. Material Grade
Material grade refers to the quality and type of materials used in the construction of furniture. Common materials include solid wood, engineered wood, metal, and upholstery fabrics. Higher-grade materials typically offer better durability and aesthetic appeal, which can justify higher costs. For buyers, knowing the material grade helps assess the long-term value and suitability of furniture for specific applications, such as office or hospitality environments.
2. Tolerance Levels
Tolerance levels indicate the permissible limits of variation in dimensions and weight. For instance, a tolerance of ±1mm in a table’s length can significantly impact assembly and fit within a designated space. Understanding tolerance levels is vital for ensuring that custom pieces align with existing setups and meet design specifications. Buyers should prioritize manufacturers who adhere to strict tolerance standards to avoid costly adjustments post-delivery.
3. Finish Quality
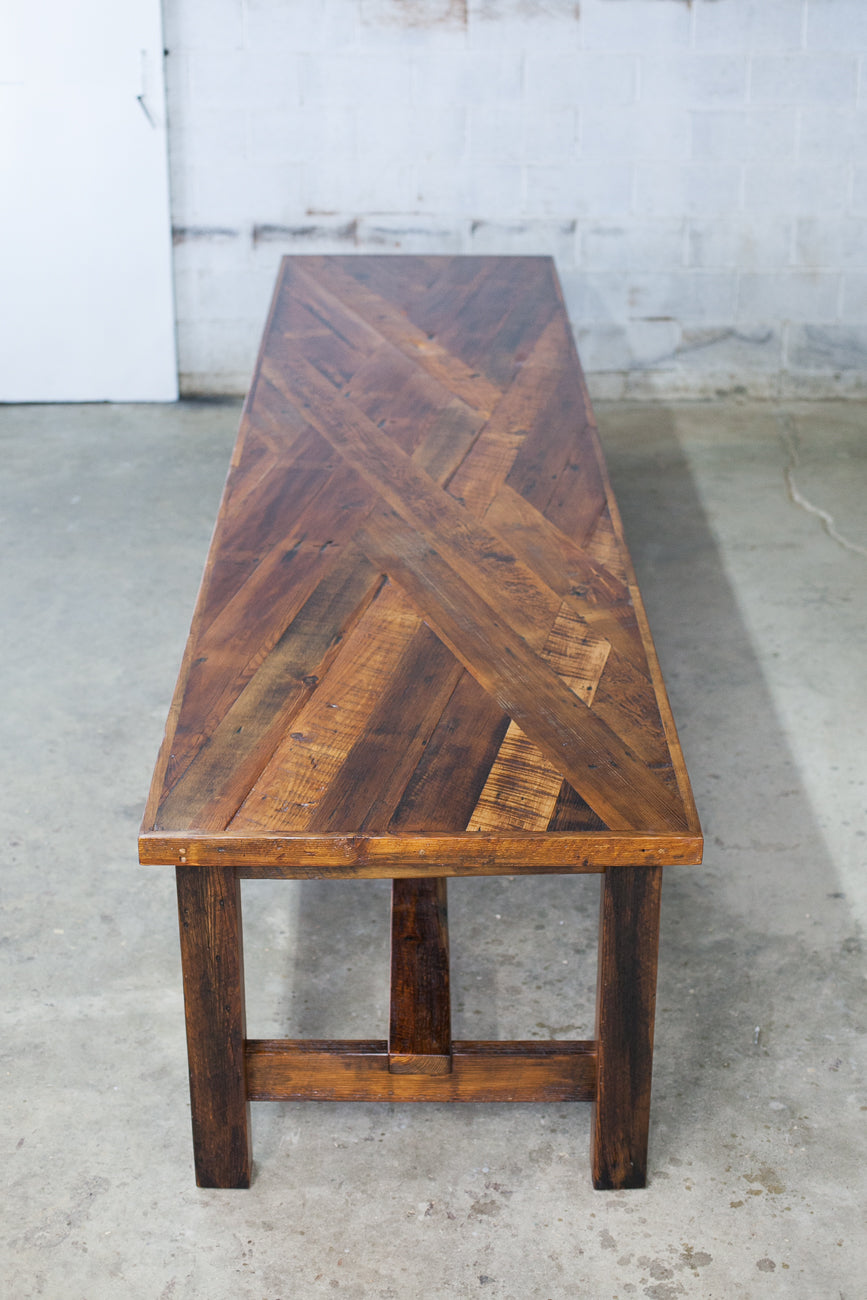
A stock image related to furniture custom.
Finish quality encompasses the surface treatment applied to furniture, including stains, paints, and protective coatings. A high-quality finish not only enhances the aesthetic but also affects durability, resistance to wear and tear, and ease of maintenance. For B2B buyers, evaluating finish quality is essential to ensure that the furniture can withstand the intended use, especially in high-traffic areas.
4. Load Capacity
Load capacity refers to the maximum weight a piece of furniture can support safely. This specification is particularly important for items like chairs, tables, and shelving units. B2B buyers must consider load capacity to ensure that the furniture meets the demands of its intended use, whether it’s for residential, commercial, or industrial applications.
5. Sustainability Standards
Sustainability standards pertain to the environmental impact of the materials and manufacturing processes used in furniture production. This includes certifications such as FSC (Forest Stewardship Council) for wood products. With a growing emphasis on eco-friendly practices, international buyers should prioritize manufacturers who comply with sustainability standards to align with global market trends and consumer preferences.
What Common Trade Terms Should B2B Buyers Know in the Furniture Custom Industry?
Familiarity with industry jargon can facilitate smoother transactions and negotiations in the custom furniture market. Here are some essential terms that B2B buyers should understand:
1. OEM (Original Equipment Manufacturer)
An OEM refers to a company that produces components or products that are then marketed by another company under its brand name. In the furniture industry, this could mean custom designs being manufactured by a third party. Understanding OEM relationships can help buyers identify potential partners and streamline sourcing processes.
2. MOQ (Minimum Order Quantity)
MOQ denotes the smallest quantity of a product that a supplier is willing to sell. This term is critical for B2B buyers as it influences purchasing decisions, especially for smaller businesses or startups. Being aware of MOQs can help buyers negotiate better terms or assess the feasibility of purchasing from certain suppliers.
3. RFQ (Request for Quotation)
An RFQ is a formal document sent to suppliers requesting pricing for specific products or services. It often includes details about specifications, quantities, and delivery timelines. B2B buyers should use RFQs to ensure they receive competitive pricing and clear information from multiple suppliers, enabling informed decision-making.
4. Incoterms (International Commercial Terms)
Incoterms are a set of international rules that define the responsibilities of buyers and sellers in international transactions. They cover aspects like shipping, insurance, and customs clearance. Familiarity with Incoterms helps B2B buyers mitigate risks and clarify obligations, ensuring smoother logistics and cost management.
5. Lead Time
Lead time refers to the period from placing an order to the delivery of the product. Understanding lead times is crucial for B2B buyers to plan their inventory and project timelines effectively. Buyers should communicate clearly with suppliers about lead times to ensure timely delivery and avoid operational disruptions.
By grasping these technical properties and trade terms, international B2B buyers can make informed decisions, negotiate effectively, and ultimately enhance their purchasing strategies in the custom furniture market.
Navigating Market Dynamics and Sourcing Trends in the furniture custom Sector
What Are the Key Market Dynamics and Trends Influencing the Custom Furniture Sector?
The custom furniture market is experiencing significant growth, driven by increasing consumer demand for personalized products and the rise of e-commerce platforms that facilitate international trade. This sector is particularly appealing to international B2B buyers in regions such as Africa, South America, the Middle East, and Europe, including countries like Spain and Germany. The growing middle class in these regions is increasingly seeking unique and high-quality furniture that reflects their personal or corporate identity, leading to a surge in demand for custom solutions.
Emerging technologies play a pivotal role in shaping sourcing trends within the custom furniture market. Innovations such as 3D printing and augmented reality are transforming the design and purchasing process, allowing buyers to visualize products before making commitments. Moreover, B2B platforms are enhancing transparency in the supply chain, enabling buyers to connect directly with manufacturers, which is particularly beneficial for those looking to source locally or regionally. This shift towards digital solutions is not just about convenience; it also fosters competitive pricing and faster turnaround times.
Another noteworthy trend is the increasing importance of design-led innovation. Buyers are now prioritizing aesthetics and functionality, often influenced by global design trends. This means that international buyers must stay abreast of contemporary styles, materials, and color palettes to ensure their offerings remain relevant in a competitive market.
How Important is Sustainability and Ethical Sourcing in the Custom Furniture Market?
Sustainability is no longer a mere buzzword; it is a fundamental expectation among consumers and businesses alike. For B2B buyers in the custom furniture sector, understanding the environmental impact of sourcing decisions is crucial. The furniture industry is known for its significant carbon footprint, stemming from deforestation, manufacturing processes, and transportation. By prioritizing sustainable practices, businesses can not only reduce their environmental impact but also enhance their brand reputation.
Ethical sourcing is closely linked to sustainability. Buyers are increasingly seeking suppliers that adhere to fair labor practices and environmental regulations. This shift is prompting manufacturers to obtain certifications such as Forest Stewardship Council (FSC) or Sustainable Forestry Initiative (SFI), which assure buyers of responsible sourcing. Furthermore, the use of recycled materials and eco-friendly finishes is gaining traction, with buyers looking for options that minimize harmful emissions and promote longevity.
Investing in sustainable and ethically sourced furniture can also lead to cost savings in the long run. By choosing suppliers who practice efficient resource management, B2B buyers can mitigate risks associated with supply chain disruptions and fluctuating material costs. Additionally, as regulatory pressures increase globally, aligning with sustainable practices will be essential for compliance and market competitiveness.
What is the Historical Context Behind the Current Trends in Custom Furniture?
The evolution of the custom furniture sector can be traced back to the artisanal craftsmanship of the past, where furniture was made to order by skilled artisans. Over the decades, this industry has adapted to various economic and social changes, including the rise of mass production in the 20th century, which shifted consumer preferences toward ready-made solutions. However, as consumers began to seek individuality in their living and working spaces, the demand for custom furniture re-emerged.
Today, the blend of traditional craftsmanship with modern technology has redefined the landscape. The rise of globalization has enabled international B2B buyers to access a diverse range of materials and designs from various cultures, enriching the custom furniture market. This historical context underscores the importance of balancing heritage and innovation, making it essential for buyers to understand the legacy of craftsmanship while embracing new technologies and trends.
Frequently Asked Questions (FAQs) for B2B Buyers of furniture custom
-
How do I solve issues with supplier reliability in furniture custom sourcing?
To address supplier reliability, conduct thorough research and vet potential suppliers through platforms like Alibaba or local trade shows. Request references and check reviews from other B2B buyers. Establish clear communication channels and set expectations upfront regarding quality, timelines, and after-sales support. Consider starting with a smaller order to evaluate their capabilities before committing to larger contracts. -
What is the best way to determine the right customization options for my furniture needs?
Start by identifying your target market’s preferences and trends. Engage directly with your customers or conduct surveys to gather insights on styles, materials, and functionalities they desire. Collaborate with designers to visualize concepts and consider creating prototypes to refine your offerings. This approach ensures your custom furniture aligns with market demands, increasing the likelihood of successful sales. -
What should I know about minimum order quantities (MOQ) when sourcing custom furniture?
MOQs can vary significantly between suppliers and are often influenced by production capabilities and material costs. It’s essential to discuss MOQs during the negotiation phase and understand how they align with your purchasing strategy. If the MOQ is too high, consider seeking manufacturers willing to accommodate smaller orders or exploring group purchasing options with other businesses to meet the MOQ. -
How do payment terms affect my international furniture custom sourcing?
Payment terms are crucial in international transactions, affecting cash flow and risk management. Common terms include upfront deposits, milestone payments, and balance upon delivery. Negotiate terms that protect your interests, such as using letters of credit or escrow services for larger orders. Additionally, familiarize yourself with currency exchange rates and potential fees associated with international transactions to avoid unexpected costs. -
What quality assurance measures should I implement when sourcing custom furniture?
Implement a robust quality assurance (QA) process that includes setting clear specifications, conducting inspections at various production stages, and requesting samples before full production. Consider hiring third-party inspection services, especially for larger orders, to ensure compliance with international standards. Establish a return policy for defective products to protect your investment and maintain customer satisfaction. -
How can I effectively manage logistics and shipping for custom furniture orders?
Start by understanding the logistics options available, including air freight for urgent shipments and sea freight for cost-effective solutions. Partner with reliable freight forwarders who specialize in furniture to handle customs clearance and ensure compliance with import regulations in your destination country. Plan for potential delays and incorporate buffer time into your delivery schedules to enhance customer satisfaction. -
What are the key considerations for choosing the right materials for custom furniture?
Selecting the right materials involves evaluating durability, aesthetic appeal, and sustainability. Research local preferences and trends in your target markets to choose materials that resonate with customers. Additionally, consider the environmental impact of your material choices, as sustainable practices are increasingly important to consumers. Collaborate with your suppliers to understand the sourcing and manufacturing processes of the materials. -
How do cultural differences impact furniture design and customization in international markets?
Cultural preferences can significantly influence furniture design, including color choices, styles, and functionality. Conduct market research to understand regional tastes and lifestyle needs. Collaborate with local designers or consultants who can provide insights into cultural nuances. This understanding will help you create products that appeal to diverse markets, ensuring your custom furniture resonates with customers across Africa, South America, the Middle East, and Europe.
Important Disclaimer & Terms of Use
⚠️ Important Disclaimer
The information provided in this guide, including content regarding manufacturers, technical specifications, and market analysis, is for informational and educational purposes only. It does not constitute professional procurement advice, financial advice, or legal advice.
While we have made every effort to ensure the accuracy and timeliness of the information, we are not responsible for any errors, omissions, or outdated information. Market conditions, company details, and technical standards are subject to change.
B2B buyers must conduct their own independent and thorough due diligence before making any purchasing decisions. This includes contacting suppliers directly, verifying certifications, requesting samples, and seeking professional consultation. The risk of relying on any information in this guide is borne solely by the reader.
Strategic Sourcing Conclusion and Outlook for furniture custom
In the evolving landscape of custom furniture sourcing, strategic sourcing remains a cornerstone for international B2B buyers. By leveraging regional manufacturing capabilities and understanding local market dynamics, businesses can achieve significant cost savings while ensuring quality and compliance with regional standards. This approach not only fosters stronger supplier relationships but also enhances supply chain resilience—an essential factor for navigating global economic uncertainties.
What Are the Key Takeaways for B2B Buyers in Custom Furniture?
- Quality and Compliance: Prioritize suppliers who adhere to international quality standards and local regulations. This not only mitigates risks but also ensures the longevity of your investments.
- Cultural Sensitivity: Understanding cultural preferences in design can enhance product appeal, particularly in diverse markets such as Africa and South America, where aesthetics vary significantly.
- Sustainability Practices: Increasingly, customers are prioritizing eco-friendly materials and processes. Aligning with suppliers who share these values can improve your brand image and appeal to environmentally conscious consumers.
How Can B2B Buyers Prepare for the Future of Custom Furniture Sourcing?
As we look ahead, the ability to adapt to market changes and customer preferences will be crucial. Engaging in continuous supplier evaluation and exploring emerging markets can open new avenues for innovation and efficiency. International B2B buyers are encouraged to embrace these practices and foster partnerships that not only meet current demands but also anticipate future trends in the custom furniture industry. The time to act is now—position your business for success by refining your strategic sourcing initiatives today.