Unlock Quality: The Ultimate Knife Manufacturer Guide (2025)
Introduction: Navigating the Global Market for knife manufacturer
Navigating the global market for knife manufacturing can be a daunting task for international B2B buyers, especially when sourcing high-quality products that meet diverse needs and compliance standards. With a vast array of knife types available, from culinary to industrial, understanding the specific applications and supplier capabilities is crucial. This guide serves as a comprehensive resource, equipping buyers with insights into the various knife categories, their applications, and the essential factors to consider when vetting suppliers.
By delving into critical aspects such as manufacturing processes, material quality, and cost considerations, this guide empowers decision-makers to make informed purchasing choices. Buyers from regions like Africa, South America, the Middle East, and Europe—countries such as Australia and Italy—will find tailored advice that addresses their unique market dynamics and regulatory environments.
In today’s competitive landscape, knowledge is power. With this guide, B2B buyers can confidently navigate the complexities of sourcing knives, ensuring they select the right suppliers that align with their operational needs and quality expectations. Whether you are looking to expand your product offerings or streamline your supply chain, understanding the global knife manufacturing market is essential for success.
Understanding knife manufacturer Types and Variations
Type Name | Key Distinguishing Features | Primary B2B Applications | Brief Pros & Cons for Buyers |
---|---|---|---|
Custom Knife Manufacturers | Tailored designs, unique materials, and specific functionalities. | Specialty culinary, bespoke gifts, luxury markets. | Pros: Unique products, high customer satisfaction. Cons: Higher costs, longer lead times. |
Mass Production Knife Manufacturers | High volume production, standardized designs, and lower costs. | Retail, large-scale food service, and industrial applications. | Pros: Cost-effective, quick turnaround. Cons: Limited customization options, lower quality. |
Artisan Knife Makers | Handcrafted, often using traditional techniques and premium materials. | High-end culinary, collectors, and specialty shops. | Pros: Superior craftsmanship, unique styles. Cons: Expensive, variable availability. |
Industrial Knife Manufacturers | Focus on durable materials and functionality for industrial use. | Manufacturing, packaging, and heavy-duty applications. | Pros: Long-lasting, designed for specific tasks. Cons: Can be over-engineered for simple uses. |
Culinary Knife Brands | Specialized in kitchen knives, often featuring ergonomic designs. | Restaurants, catering, and home cooking. | Pros: High performance, often backed by chefs. Cons: Can be pricey, requires maintenance. |
What Are the Characteristics of Custom Knife Manufacturers?
Custom knife manufacturers specialize in creating knives tailored to the specific needs and preferences of their clients. They offer unique designs, materials, and functionalities, making them ideal for specialty culinary applications, bespoke gifts, and luxury markets. Buyers should consider the longer lead times and higher costs associated with custom knives, but the end product often results in a higher level of customer satisfaction due to its uniqueness and personalization.
How Do Mass Production Knife Manufacturers Operate?
Mass production knife manufacturers focus on high-volume production of standardized knife designs. This approach allows them to offer competitive pricing, making their products suitable for retail, large-scale food service, and industrial applications. While these knives are cost-effective and readily available, buyers should be aware of the limitations in customization and potential compromises in quality compared to custom or artisan options.
What Makes Artisan Knife Makers Stand Out?
Artisan knife makers are known for their handcrafted knives, often employing traditional techniques and high-quality materials. These knives are popular among high-end culinary professionals, collectors, and specialty shops. While the craftsmanship and unique styles of artisan knives are unparalleled, buyers should be prepared for higher prices and variable availability, which can affect purchasing decisions.
What Are the Key Features of Industrial Knife Manufacturers?
Industrial knife manufacturers produce knives designed for durability and functionality in demanding environments. Their products are commonly used in manufacturing, packaging, and heavy-duty applications. Buyers should consider that while these knives are built to last and perform specific tasks effectively, they may be over-engineered for simpler uses, which could lead to unnecessary costs.
Why Choose Culinary Knife Brands?
Culinary knife brands focus on producing high-performance kitchen knives, often incorporating ergonomic designs for ease of use. These knives are essential for restaurants, catering services, and home cooking enthusiasts. Although they may come with a higher price tag, the quality and performance of culinary knives are often backed by endorsements from professional chefs, making them a worthwhile investment for serious buyers.
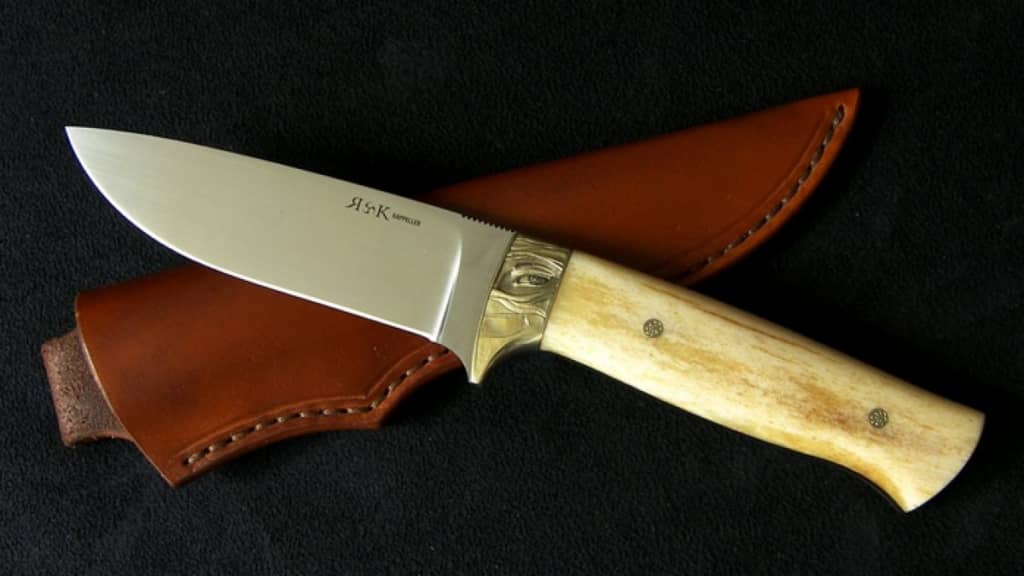
A stock image related to knife manufacturer.
Related Video: Vintage Chef’s Knife Restoration
Key Industrial Applications of knife manufacturer
Industry/Sector | Specific Application of Knife Manufacturer | Value/Benefit for the Business | Key Sourcing Considerations for this Application |
---|---|---|---|
Food Processing | Precision cutting tools for meat and fish | Enhances efficiency and reduces waste in processing | Material quality, hygiene standards, and blade durability |
Manufacturing | Industrial knives for cutting materials | Increases production speed and product quality | Customization options, delivery timelines, and cost |
Agriculture | Knives for harvesting crops | Improves harvesting efficiency and reduces labor costs | Ergonomics, blade sharpness, and resistance to wear |
Construction | Cutting tools for building materials | Ensures safety and precision in construction tasks | Compliance with safety regulations and tool longevity |
Medical | Surgical knives and scalpels | Vital for precision in medical procedures | Sterilization processes, precision engineering, and certifications |
What Are the Key Applications of Knife Manufacturers in Food Processing?
In the food processing industry, knife manufacturers provide precision cutting tools specifically designed for meat and fish. These specialized knives enhance processing efficiency and minimize waste, which is crucial in meeting production targets. International buyers should prioritize sourcing knives made from high-quality materials that comply with hygiene standards, ensuring they are suitable for food contact. Additionally, blade durability is essential to withstand the rigors of constant use.
How Do Knife Manufacturers Cater to the Manufacturing Sector?
For the manufacturing sector, knife manufacturers produce industrial knives tailored for cutting various materials, including textiles, plastics, and metals. These tools are designed to increase production speed and improve product quality, directly impacting profitability. When sourcing, businesses should consider customization options to meet specific production needs, delivery timelines to avoid disruptions, and overall cost to ensure a favorable return on investment.
What Role Do Knives Play in Agricultural Efficiency?
In agriculture, knives are indispensable for harvesting crops. They improve harvesting efficiency and help reduce labor costs, making them essential tools for farmers and agricultural businesses. Buyers should focus on ergonomics, as comfortable handles can significantly affect productivity, blade sharpness for effective cutting, and resistance to wear to ensure longevity in the field. Understanding local agricultural practices can also inform the selection of the most suitable knife types.
Why Are Cutting Tools Important in the Construction Industry?
In the construction industry, cutting tools from knife manufacturers are vital for handling building materials such as wood, drywall, and insulation. These tools ensure safety and precision, which are critical for maintaining project timelines and quality standards. International buyers should verify compliance with local safety regulations and prioritize tools that offer longevity to minimize replacement costs. The choice of materials and design can also influence performance in challenging construction environments.
How Are Medical Knives Specialized for Healthcare Applications?
Knife manufacturers also supply surgical knives and scalpels essential for medical procedures. These tools are critical for precision and safety in surgeries, impacting patient outcomes. Buyers in the healthcare sector must focus on the sterilization processes employed during manufacturing, ensuring that the knives meet stringent health standards. Precision engineering is crucial, as is obtaining relevant certifications that demonstrate compliance with medical regulations.
3 Common User Pain Points for ‘knife manufacturer’ & Their Solutions
Scenario 1: Sourcing Quality Knives for Diverse Needs
The Problem: B2B buyers often face significant challenges when sourcing knives that meet specific quality standards and operational requirements. For instance, a restaurant chain looking to purchase chef knives may struggle with inconsistent quality, leading to dissatisfaction among chefs and ultimately affecting kitchen efficiency. Additionally, buyers from Africa or South America may encounter difficulties in finding manufacturers that can produce knives suitable for local culinary styles, which may require unique blade shapes and materials.
The Solution: To overcome these challenges, buyers should prioritize establishing relationships with reputable knife manufacturers that offer customization options. Conduct thorough research to identify manufacturers with a proven track record of quality assurance and customer satisfaction. Request samples of various knife models to assess their performance, durability, and ergonomics firsthand. Engaging in direct communication with manufacturers can also facilitate discussions about specific requirements, such as materials or blade designs tailored for regional cuisines. Leveraging trade shows and industry expos in Europe or the Middle East can also help buyers connect with potential manufacturers and see their products in action.
Scenario 2: Managing Supply Chain Disruptions
The Problem: Supply chain disruptions can severely impact B2B buyers in the knife manufacturing sector, particularly those sourcing from international markets. Political instability, shipping delays, or sudden price increases can lead to inconsistent supply, leaving businesses unable to meet customer demand. For example, a kitchenware retailer in Europe may face stock shortages during peak seasons, resulting in lost sales and diminished customer loyalty.
The Solution: To mitigate supply chain risks, buyers should adopt a multi-sourcing strategy. This involves working with multiple knife manufacturers across different regions to diversify supply chains. Establishing relationships with local manufacturers in addition to international ones can help ensure a more stable supply, especially during crises. Buyers should also invest in demand forecasting tools to better predict inventory needs, allowing them to place orders in advance and avoid shortages. Additionally, building strong partnerships with logistics providers can facilitate smoother shipping processes, reducing lead times and improving overall supply chain reliability.
Scenario 3: Ensuring Compliance with Health and Safety Standards
The Problem: B2B buyers in the culinary industry must navigate complex health and safety regulations regarding food preparation equipment, including knives. For instance, a restaurant operating in the Middle East may face stringent guidelines for materials used in knife manufacturing, particularly regarding food safety and hygiene. Failure to comply can lead to hefty fines, reputational damage, and even closure of the business.
The Solution: Buyers should ensure that their knife manufacturers are compliant with local and international safety standards. This can be achieved by requesting certifications and documentation proving that the knives meet necessary health regulations, such as ISO or FDA certifications. Conducting factory visits or audits can further confirm adherence to safety protocols during the manufacturing process. Additionally, buyers should stay informed about changes in regulations in their respective regions and work closely with manufacturers to adapt products accordingly. Creating a robust compliance checklist can help streamline the sourcing process and ensure that all products meet the required standards before purchase.
By addressing these common pain points, B2B buyers can enhance their sourcing strategies, build stronger supplier relationships, and ultimately ensure the success of their operations in the knife manufacturing sector.
Strategic Material Selection Guide for knife manufacturer
What Are the Key Properties of Common Knife Manufacturing Materials?
When selecting materials for knife manufacturing, it is crucial to consider properties such as hardness, corrosion resistance, weight, and ease of maintenance. The following materials are commonly used in knife production, each with distinct characteristics that affect performance and suitability for various applications.
1. Stainless Steel: The Versatile Choice
Key Properties: Stainless steel is renowned for its corrosion resistance, which is vital for knives exposed to moisture and acidic environments. It typically has a hardness rating between 56-62 HRC (Rockwell Hardness Scale), making it durable enough for everyday use.
Pros & Cons: The primary advantage of stainless steel is its ability to resist rust and staining, which is essential for culinary and outdoor knives. However, it can be more challenging to sharpen compared to high-carbon steel. Additionally, the cost can vary widely depending on the grade, with higher-quality stainless steels being more expensive.
Impact on Application: Stainless steel knives are suitable for a variety of media, including food and outdoor materials. Their resistance to corrosion makes them ideal for culinary applications in humid climates, which is particularly relevant for buyers in Africa and South America.
Considerations for International Buyers: Buyers must ensure compliance with international standards such as ASTM and ISO for food safety. In regions like Europe, certifications may be required to validate the quality of stainless steel used.
2. High-Carbon Steel: The Sharp Edge
Key Properties: High-carbon steel is known for its exceptional hardness (up to 65 HRC) and edge retention. This material can achieve a razor-sharp edge, making it a favorite among professional chefs and outdoor enthusiasts.
Pros & Cons: The primary advantage is its ability to hold an edge longer than stainless steel. However, high-carbon steel is prone to rust and requires regular maintenance, including oiling to prevent corrosion. This can increase the total cost of ownership due to the need for upkeep.
Impact on Application: High-carbon steel knives are particularly effective in dry environments where moisture is minimal. For buyers in arid regions of the Middle East, this material can be an excellent choice for kitchen and utility knives.
Considerations for International Buyers: Buyers should be aware of the maintenance requirements and may need to invest in additional care products. Compliance with local regulations regarding the use of carbon steel in food preparation is also essential.
3. Ceramic: The Lightweight Alternative
Key Properties: Ceramic knives are lightweight and maintain their sharpness without needing frequent honing. They are typically made from zirconia, which is highly resistant to wear and corrosion.
Pros & Cons: The main advantage of ceramic knives is their ability to remain sharp for a long time, making them low-maintenance. However, they are brittle and can chip or break if dropped, limiting their use in rugged environments. Additionally, they are generally more expensive than steel alternatives.
Impact on Application: Ceramic knives are ideal for slicing fruits and vegetables, particularly in culinary settings. Their non-reactive surface makes them suitable for food preparation, especially in regions where food safety is paramount.
Considerations for International Buyers: Buyers must ensure that ceramic knives meet safety standards and are suitable for the intended use. In Europe, compliance with EU regulations regarding kitchenware is crucial.
4. Damascus Steel: The Aesthetic Choice
Key Properties: Damascus steel is known for its distinctive patterns and high strength. It combines various steel types to create a blade that is both beautiful and functional, typically achieving hardness levels of 58-61 HRC.
Pros & Cons: The aesthetic appeal of Damascus steel makes it a popular choice for high-end knives. However, it can be more expensive due to the complex manufacturing process. Additionally, while it offers good corrosion resistance, it may not perform as well as high-carbon steel in terms of edge retention.
Impact on Application: Damascus steel knives are often used in culinary applications where presentation is essential. They are well-suited for buyers in Europe, particularly in markets that value craftsmanship and design.
Considerations for International Buyers: Buyers should be aware of the authenticity of Damascus steel and ensure that it meets quality standards. Understanding the market for handcrafted knives in regions like Italy can also provide insights into customer preferences.
Summary Table of Knife Manufacturing Materials
Material | Typical Use Case for Knife Manufacturer | Key Advantage | Key Disadvantage/Limitation | Relative Cost (Low/Med/High) |
---|---|---|---|---|
Stainless Steel | Culinary and outdoor knives | Corrosion resistance | Difficult to sharpen | Medium |
High-Carbon Steel | Professional kitchen knives | Excellent edge retention | Prone to rust, requires maintenance | Medium |
Ceramic | Slicing fruits and vegetables | Low maintenance, stays sharp longer | Brittle, can chip or break | High |
Damascus Steel | High-end culinary knives | Aesthetic appeal | Expensive, variable performance | High |
This comprehensive material selection guide provides international B2B buyers with actionable insights to make informed decisions when sourcing knives for various applications.
In-depth Look: Manufacturing Processes and Quality Assurance for knife manufacturer
What Are the Main Stages of Knife Manufacturing Processes?
The manufacturing of knives involves several key stages, each critical to ensuring the final product meets both performance and quality expectations. The primary stages include material preparation, forming, assembly, and finishing.
-
Material Preparation
– The first step in knife manufacturing is selecting high-quality materials, typically stainless steel or carbon steel for the blade, and various materials for the handle, such as wood, plastic, or metal.
– Materials are often subjected to heat treatment to enhance their hardness and durability. This process involves heating the steel to a specific temperature and then cooling it rapidly, which alters its molecular structure for improved performance. -
Forming
– In this stage, the prepared materials are shaped into the desired knife form. This can be achieved through various methods, including forging, stamping, or CNC machining.
– Forging is a traditional method that involves hammering the steel into shape, which can enhance its strength. On the other hand, stamping involves cutting the blade shape from a sheet of steel, which is more efficient for mass production. -
Assembly
– Once the blade is formed, it undergoes assembly where the handle is attached. This process may involve using adhesives, screws, or rivets, depending on the knife design.
– Quality checks are performed during assembly to ensure that the blade is securely attached and that the knife operates smoothly. -
Finishing
– The finishing stage includes grinding, polishing, and coating the knife. Grinding sharpens the edge, while polishing enhances the aesthetic appeal.
– Coatings may be applied to improve corrosion resistance and provide a non-stick surface. This stage is crucial for both the functionality and longevity of the knife.
How Do International Standards Influence Quality Assurance in Knife Manufacturing?
Quality assurance (QA) is vital in knife manufacturing, ensuring that products meet specific performance and safety standards. International standards such as ISO 9001 provide a framework for consistent quality management systems.
-
International Standards and Certifications
– ISO 9001: This standard focuses on quality management systems and is applicable across industries. Compliance demonstrates a manufacturer’s commitment to quality processes.
– CE Marking: For products sold in Europe, CE marking indicates conformity with health, safety, and environmental protection standards. This is particularly important for knives that may be used in food preparation.
– API Standards: In certain contexts, such as manufacturing knives for industrial applications, adherence to API standards may be necessary, ensuring that products can withstand demanding environments. -
Quality Control Checkpoints
– Incoming Quality Control (IQC): This is the first checkpoint, where raw materials are inspected upon arrival. Manufacturers should ensure that materials meet specified standards before proceeding.
– In-Process Quality Control (IPQC): This involves monitoring processes during manufacturing to detect defects early. Regular checks during forming and assembly can prevent costly rework.
– Final Quality Control (FQC): The final inspection ensures that the finished product meets all specifications and performance criteria before shipping.
What Testing Methods Are Commonly Used in Knife Manufacturing Quality Control?
Testing is an integral part of the quality assurance process in knife manufacturing. Various methods are employed to ensure that knives meet the required standards for safety and performance.
-
Visual Inspection
– A thorough visual inspection of the knife can identify surface defects, irregularities, or inconsistencies in finish. This is often the first step in quality assessment. -
Sharpness Testing
– The sharpness of the knife is tested using standardized methods, such as cutting through specific materials (e.g., paper or rope) to evaluate performance. -
Durability Testing
– Durability tests may involve subjecting the knife to rigorous use conditions to evaluate its performance over time. This can include cutting tests and resistance to corrosion. -
Safety Testing
– Safety tests ensure that the knife meets regulatory standards for consumer safety. This may include assessing the risk of injury during use and ensuring the blade is securely attached.
How Can B2B Buyers Verify Supplier Quality Control Processes?
For B2B buyers, especially those from Africa, South America, the Middle East, and Europe, verifying a supplier’s quality control processes is crucial for ensuring product reliability.
-
Supplier Audits
– Conducting audits of potential suppliers can provide insight into their manufacturing processes and quality control measures. This includes reviewing documentation, observing operations, and assessing compliance with international standards. -
Quality Control Reports
– Requesting detailed quality control reports can help buyers understand the supplier’s QA processes. These reports should outline inspection results, testing methods, and any corrective actions taken. -
Third-Party Inspections
– Engaging third-party inspection services can provide an unbiased assessment of the manufacturer’s quality control practices. These inspections can be conducted at various stages of production. -
Certifications and Compliance
– Buyers should verify that the supplier holds relevant certifications such as ISO 9001 or CE marking. Checking for these certifications can provide assurance that the manufacturer adheres to recognized quality standards.
What Nuances Should International B2B Buyers Consider Regarding Quality Control?
Understanding the nuances of quality control in international trade is essential for B2B buyers. Different regions may have varying expectations regarding quality and compliance.
-
Cultural Differences in Quality Expectations
– Buyers should be aware that quality expectations can vary significantly between regions. For instance, European buyers may prioritize strict compliance with safety standards, while buyers in other regions may focus more on cost-effectiveness. -
Regulatory Compliance
– Buyers must ensure that products comply with the regulations of their respective markets. This may include additional testing or certification requirements for specific regions, especially in the food service industry. -
Communication and Transparency
– Establishing clear communication channels with suppliers is vital. Buyers should ensure that suppliers are transparent about their quality control processes and willing to provide documentation and reports. -
Long-Term Relationships
– Building long-term relationships with suppliers can enhance trust and improve quality over time. Engaging in regular discussions about quality improvements can lead to better outcomes for both parties.
By understanding the manufacturing processes and quality assurance measures in knife manufacturing, international B2B buyers can make informed decisions, ensuring they procure reliable and high-quality products.
Practical Sourcing Guide: A Step-by-Step Checklist for ‘knife manufacturer’
When sourcing a knife manufacturer, it’s essential to follow a structured approach to ensure you partner with a reliable and quality-focused supplier. This checklist outlines key steps to guide you through the procurement process effectively.
Step 1: Define Your Technical Specifications
Clearly outline the specifications for the knives you need, including materials, dimensions, design features, and intended use. This step is crucial as it sets the foundation for your sourcing process and helps avoid misunderstandings with suppliers. Consider the following:
– Material Quality: Specify whether you require stainless steel, carbon steel, or other materials.
– Design Features: Identify any specific ergonomic or aesthetic requirements.
Step 2: Research Potential Suppliers
Conduct thorough research to compile a list of potential knife manufacturers. Utilize online directories, industry trade shows, and recommendations from industry peers. This step is vital to ensure you have a broad selection of suppliers to evaluate. Key considerations include:
– Market Presence: Look for manufacturers with a solid reputation and years of experience in the knife industry.
– Product Range: Ensure the suppliers can provide the specific type of knives you are looking for.
Step 3: Evaluate Supplier Certifications
Ensure that potential suppliers hold the necessary certifications, such as ISO 9001 for quality management systems. These certifications indicate a commitment to maintaining high manufacturing standards. Additionally:
– Industry-Specific Certifications: Check for any certifications specific to knife manufacturing or safety standards relevant to your market.
– Regulatory Compliance: Confirm compliance with local regulations, especially if importing knives into your region.
Step 4: Request Samples for Quality Assessment
Before making a large order, request samples from your shortlisted suppliers. This step allows you to evaluate the quality, craftsmanship, and performance of the knives firsthand. Pay attention to:
– Material and Finish: Assess the knife’s materials and surface finish for durability and aesthetic appeal.
– Functionality: Test the knives for their intended use to ensure they meet your specifications.
Step 5: Negotiate Terms and Pricing
Once you have identified a suitable supplier, engage in negotiations regarding pricing, lead times, payment terms, and minimum order quantities. Clear communication at this stage can help prevent misunderstandings later. Consider the following:
– Volume Discounts: Inquire about discounts for larger orders to maximize your budget.
– Payment Flexibility: Discuss payment terms that align with your cash flow, such as partial payments or net payment terms.
Step 6: Establish Clear Communication Channels
Set up clear communication channels with your selected supplier to facilitate ongoing dialogue. Good communication is essential for addressing any issues that may arise during production or shipping. Tips for effective communication include:
– Regular Updates: Request regular progress updates throughout the manufacturing process.
– Point of Contact: Designate a specific contact person on both sides for streamlined communication.
Step 7: Plan for Quality Control and Feedback
Implement a quality control process to ensure that the delivered products meet your specifications. This step is critical for maintaining quality standards and fostering a long-term partnership. Key actions include:
– Inspection Protocols: Establish clear inspection criteria upon receipt of goods.
– Feedback Mechanism: Provide constructive feedback to the supplier to help them improve their processes and products.
By following this step-by-step checklist, international B2B buyers can effectively source quality knife manufacturers that meet their specific needs and standards.
Comprehensive Cost and Pricing Analysis for knife manufacturer Sourcing
What Are the Key Cost Components in Knife Manufacturing?
When sourcing knives from manufacturers, understanding the cost structure is essential for international B2B buyers. The primary cost components include:
-
Materials: The choice of raw materials significantly impacts the overall cost. High-quality stainless steel or carbon steel typically incurs higher costs, but they provide durability and better performance, which can justify the investment.
-
Labor: Labor costs vary by region. Manufacturers in regions with lower labor costs, such as parts of Africa and South America, may offer competitive pricing. However, it’s essential to ensure that labor standards meet your quality and ethical expectations.
-
Manufacturing Overhead: This includes utilities, rent, and equipment maintenance. Manufacturers with optimized processes may have lower overhead costs, which can translate to better pricing for buyers.
-
Tooling: The initial investment in specialized tools for custom knife designs can be substantial. Buyers should consider these costs when evaluating quotes, especially for unique specifications.
-
Quality Control (QC): A rigorous QC process is vital for ensuring product quality. While it may add to the cost, investing in QC can prevent costly returns and enhance brand reputation.
-
Logistics: Shipping costs can vary significantly based on the destination and mode of transport. Understanding Incoterms (International Commercial Terms) is crucial, as they dictate who bears the cost at various points in the shipping process.
-
Margin: Manufacturers typically add a profit margin to their costs. This can vary based on market competition and demand for specific knife types.
How Do Price Influencers Impact Knife Sourcing?
Several factors influence the pricing of knives in the B2B market:
-
Volume/MOQ (Minimum Order Quantity): Ordering in bulk often leads to lower per-unit costs. Buyers should negotiate for better rates based on anticipated volume.
-
Specifications and Customization: Unique designs or specifications can increase costs. Buyers should clearly communicate their needs to avoid unexpected price hikes.
-
Materials and Quality Certifications: Knives made from premium materials or those that meet specific certifications (e.g., ISO, CE) may command higher prices. Buyers should weigh the benefits against the additional costs.
-
Supplier Factors: The supplier’s reputation and experience can influence pricing. Established manufacturers with a track record of quality may charge more but offer better reliability.
-
Incoterms: Understanding the terms of shipping can help buyers manage costs effectively. For instance, choosing FOB (Free on Board) terms can provide more control over shipping expenses.
What Tips Can Help B2B Buyers Negotiate Better Prices?
For international buyers, particularly from Africa, South America, the Middle East, and Europe, effective negotiation strategies can lead to cost savings:
-
Conduct Market Research: Understanding market prices and supplier capabilities can empower buyers during negotiations.
-
Evaluate Total Cost of Ownership (TCO): Consider not only the purchase price but also logistics, maintenance, and potential warranty costs. A lower upfront price might not always result in overall savings.
-
Build Relationships: Establishing long-term partnerships with suppliers can lead to better pricing and priority service in future orders.
-
Flexibility in Specifications: Being open to alternative materials or designs can help negotiate lower prices.
-
Leverage Payment Terms: Discussing favorable payment terms can also reduce immediate costs, allowing better cash flow management.
Conclusion: What Should Buyers Keep in Mind?
While this analysis provides a foundational understanding of the cost and pricing dynamics in knife manufacturing, it’s important to approach sourcing with a clear strategy. Buyers should remember that indicative prices can vary widely based on the factors mentioned above. Always request detailed quotes and be prepared to negotiate terms that align with your budget and quality expectations.
Alternatives Analysis: Comparing knife manufacturer With Other Solutions
Understanding Alternative Solutions to Knife Manufacturing
In the competitive landscape of B2B procurement, international buyers often seek to evaluate multiple solutions that meet their operational needs. When it comes to knife manufacturing, understanding the alternatives available can lead to more informed decision-making. This analysis compares traditional knife manufacturing with alternative solutions such as automated cutting technologies and multi-functional kitchen tools.
Comparison Table of Knife Manufacturing and Alternatives
Comparison Aspect | Knife Manufacturer | Automated Cutting Technology | Multi-functional Kitchen Tools |
---|---|---|---|
Performance | High precision and durability | Consistent and rapid cuts | Versatile, but may lack precision |
Cost | Moderate to high (varies by material) | High initial investment but cost-effective over time | Generally low to moderate cost |
Ease of Implementation | Requires skilled labor and setup | Requires training and setup | Easy to use with minimal setup |
Maintenance | Regular maintenance needed | Low maintenance, but technical support required | Minimal maintenance required |
Best Use Case | Professional kitchens, culinary schools | Large-scale food processing, manufacturing | Home cooking, small-scale operations |
What Are the Advantages and Disadvantages of Automated Cutting Technology?
Automated cutting technology, which includes machines equipped with laser or water jet cutting capabilities, offers significant benefits in terms of performance. These systems provide rapid and consistent cutting, making them ideal for high-volume production environments. However, the initial investment can be substantial, which might not be feasible for smaller businesses or those just starting. Additionally, implementing these technologies may require specialized training for staff, which can add to the overall cost and complexity.
Why Consider Multi-functional Kitchen Tools?
Multi-functional kitchen tools are an attractive alternative for businesses that prioritize versatility and cost-effectiveness. These tools can serve various functions, such as slicing, dicing, and chopping, making them suitable for smaller kitchens or home use. They typically come at a lower price point compared to traditional knife manufacturing. However, the trade-off is that they may not offer the same level of precision and durability as professionally manufactured knives. This means they might not be suitable for high-demand culinary environments where performance is critical.
How to Choose the Right Solution for Your Needs
When determining the best solution for your business needs, consider factors such as the scale of operations, budget constraints, and specific use cases. If your operations involve large-scale production and require precision, investing in automated cutting technology may be worthwhile despite the higher upfront cost. Conversely, for small to medium-sized enterprises or those focused on versatility, multi-functional kitchen tools may provide a practical solution without the complexity of knife manufacturing processes. Ultimately, aligning your choice with your operational goals will help ensure efficient and effective procurement.
Essential Technical Properties and Trade Terminology for knife manufacturer
What Are the Key Technical Properties for Knife Manufacturers?
When considering knife manufacturing, understanding the essential technical properties is crucial for B2B buyers to make informed decisions. Here are some of the critical specifications to keep in mind:
1. Material Grade: Why Is It Important for Knife Quality?
The material grade refers to the type and quality of steel used in knife production, which directly affects durability, sharpness, and corrosion resistance. Common materials include stainless steel, carbon steel, and tool steel. Buyers should prioritize high-grade materials, as they enhance the knife’s longevity and performance, especially in professional settings where reliability is key.
2. Hardness: How Does It Impact Performance?
Hardness, measured on the Rockwell scale, indicates a knife’s ability to resist wear and maintain an edge. A hardness rating of 58-60 HRC (Rockwell Hardness Scale) is generally ideal for kitchen knives. Buyers must consider the intended use; for instance, culinary knives require a balance between hardness for sharpness and toughness to withstand impact.
3. Tolerance: What Does It Mean for Knife Precision?
Tolerance defines the acceptable limits of variation in dimensions during manufacturing. For knives, tight tolerances ensure that blades fit properly in handles and that cutting edges are uniform. This precision is vital for functionality and safety, as poorly manufactured knives can lead to accidents or subpar performance.
4. Blade Geometry: Why Is It Critical for Functionality?
Blade geometry includes the shape, thickness, and grind of the blade, impacting its cutting ability and performance. Different geometries suit various tasks; for example, a flat grind is ideal for slicing, while a hollow grind is better for fine cutting. Understanding blade geometry helps buyers select knives tailored to specific applications.
5. Finish: How Does It Affect Aesthetics and Performance?
The finish of a knife involves surface treatments like polishing or coating that enhance appearance and performance. A well-finished knife not only looks appealing but also resists corrosion and minimizes friction during cutting. Buyers should inquire about finishes to ensure they meet their aesthetic and functional needs.
What Are Common Trade Terms in Knife Manufacturing?
Understanding industry jargon is essential for navigating B2B transactions effectively. Here are several common terms:
1. What Does OEM Mean in Knife Manufacturing?
OEM stands for Original Equipment Manufacturer. In the knife industry, it refers to companies that produce knives based on specifications provided by another brand. This relationship allows brands to offer custom-designed knives without investing in production capabilities.
2. What Is MOQ and Why Is It Important?
MOQ, or Minimum Order Quantity, signifies the smallest number of units a supplier is willing to produce or sell. Understanding MOQ is crucial for buyers, as it affects inventory management and initial capital investment. Knowing the MOQ helps businesses plan their purchasing strategies effectively.
3. How Does RFQ Impact the Buying Process?
RFQ stands for Request for Quotation. It is a formal process where buyers request pricing and terms from suppliers for specific products. Utilizing RFQs can lead to better negotiation outcomes, as suppliers often provide their best rates to secure orders.
4. What Are Incoterms and Their Relevance to B2B Transactions?
Incoterms are international commercial terms that define the responsibilities of buyers and sellers in shipping arrangements. They clarify who is responsible for shipping costs, insurance, and risk during transit. Familiarity with Incoterms is vital for international buyers to avoid misunderstandings and ensure smooth transactions.
5. What Is the Role of Lead Time in Knife Manufacturing?
Lead time refers to the time taken from placing an order to delivery. Understanding lead times helps buyers manage inventory levels and plan for demand fluctuations. Knowing the lead time is particularly important for businesses that rely on timely product availability for customer satisfaction.
In conclusion, grasping the essential technical properties and trade terminology in knife manufacturing can significantly enhance the decision-making process for B2B buyers. By focusing on these aspects, buyers can ensure they select high-quality products that meet their specific needs while navigating the complexities of international trade effectively.
Navigating Market Dynamics and Sourcing Trends in the knife manufacturer Sector
What Are the Current Market Dynamics and Key Trends in the Knife Manufacturing Sector?
The global knife manufacturing sector is experiencing transformative changes driven by various factors, including technological advancements, shifting consumer preferences, and economic trends. International B2B buyers, especially from Africa, South America, the Middle East, and Europe, should be aware of these dynamics as they shape sourcing strategies and market opportunities.
One significant trend is the integration of digital technologies into the manufacturing process. Automation and smart manufacturing are improving production efficiency and quality control. This is particularly relevant for buyers looking to source knives with consistent quality and performance. Additionally, e-commerce platforms are becoming increasingly vital for B2B transactions, allowing buyers to access a broader range of suppliers and streamline their purchasing processes.
Another critical driver is the rising demand for specialty knives, including culinary and outdoor knives. This trend is fueled by the growing interest in gourmet cooking and outdoor activities. Buyers should consider how these niche markets can provide opportunities for differentiation and higher margins. Furthermore, the globalization of supply chains is prompting buyers to explore sourcing options in emerging markets, where cost advantages can be realized without compromising quality.
How Are Sustainability and Ethical Sourcing Influencing the Knife Manufacturing Industry?
Sustainability and ethical sourcing have become paramount in the knife manufacturing sector. The environmental impact of production processes, including resource extraction and waste generation, is under scrutiny. Buyers are increasingly expected to prioritize suppliers who demonstrate a commitment to sustainable practices, such as using recycled materials or implementing energy-efficient manufacturing processes.
Moreover, ethical supply chains are gaining traction as consumers and businesses alike demand transparency in sourcing. This includes ensuring that raw materials, such as steel and wood, are sourced responsibly and do not contribute to deforestation or environmental degradation. Certifications like FSC (Forest Stewardship Council) for wood products and ISO 14001 for environmental management can help buyers identify suppliers committed to sustainable practices.
Investing in “green” certifications and materials not only enhances brand reputation but also meets the growing consumer demand for eco-friendly products. Buyers should proactively seek suppliers who can provide documentation on their sustainability efforts and ethical sourcing practices, as these factors increasingly influence purchasing decisions.
What Is the Brief Evolution and History of Knife Manufacturing Relevant to B2B Buyers?
The knife manufacturing industry has a rich history that dates back thousands of years, evolving from basic stone tools to sophisticated, high-performance blades. Initially, knives were crafted by hand, with each artisan developing unique techniques and styles. As demand grew, particularly during the Industrial Revolution, mass production techniques were introduced, leading to increased availability and standardization.
In the modern era, the knife manufacturing sector has embraced advanced materials and technologies, such as high-carbon stainless steel and precision engineering, enabling the production of knives that are not only durable but also tailored to specific uses. This evolution presents B2B buyers with a diverse array of options, from traditional handcrafted knives to contemporary designs optimized for performance.
Understanding the historical context of knife manufacturing can provide buyers with insights into the craftsmanship and innovation behind various products, allowing them to make informed decisions that align with their brand values and customer expectations.
Frequently Asked Questions (FAQs) for B2B Buyers of knife manufacturer
-
How do I ensure the quality of knives from a manufacturer?
To ensure the quality of knives from a manufacturer, start by requesting samples to assess craftsmanship and materials. Evaluate the manufacturer’s certifications, such as ISO standards, which indicate compliance with quality management systems. Additionally, consider visiting the factory if possible or hiring a third-party inspection service to conduct quality checks before shipment. Gathering references from other buyers can also provide insights into the manufacturer’s reliability and product quality. -
What are the key factors to consider when choosing a knife manufacturer?
When choosing a knife manufacturer, consider factors such as production capacity, quality control processes, and compliance with international standards. Assess their specialization in the type of knives you need, whether culinary, tactical, or industrial. Communication is crucial; ensure the manufacturer can effectively respond to your queries and requirements. Lastly, review their experience in international trade, especially if you are sourcing from regions like Africa or South America, to understand their logistics capabilities. -
What is the typical minimum order quantity (MOQ) for knife manufacturers?
The minimum order quantity (MOQ) for knife manufacturers can vary widely depending on the manufacturer and the type of knives. Typically, MOQs range from 100 to 1,000 units. However, some manufacturers may accommodate smaller orders for an additional fee or may have flexible arrangements for new clients. It’s important to discuss your specific needs upfront to find a manufacturer willing to work within your order volume. -
How can I customize my knife orders with a manufacturer?
Customizing your knife orders typically involves discussing design specifications, such as blade type, handle materials, and branding options. Most manufacturers will require a detailed design brief or prototype to better understand your requirements. Be sure to inquire about the customization process, lead times, and any additional costs associated with bespoke designs. Establishing clear communication and expectations with the manufacturer will facilitate a smoother customization experience. -
What payment terms should I expect when working with knife manufacturers?
Payment terms with knife manufacturers can vary but often include options such as a deposit upfront (typically 30-50%) with the balance due upon shipment. Some manufacturers may offer flexible terms based on your relationship with them or order size. It’s advisable to clarify all payment methods accepted (e.g., bank transfer, letters of credit) and ensure that payment terms are documented in the contract to avoid disputes later. -
How do I vet a knife manufacturer before placing an order?
Vetting a knife manufacturer involves researching their background, including years in business, reputation, and client reviews. Request references and check their track record with previous clients. Additionally, verify their compliance with industry standards and certifications. Consider visiting their facility if feasible, or utilize third-party audit services to assess their production capabilities and quality control processes. This thorough vetting will help mitigate risks in your sourcing process. -
What logistics considerations should I keep in mind when sourcing knives internationally?
When sourcing knives internationally, consider factors such as shipping costs, customs regulations, and lead times. Understand the import/export restrictions in your country and ensure compliance with safety standards for knives. Choose a reliable freight forwarder familiar with the knife industry to streamline logistics. Additionally, factor in potential delays due to customs clearance, and plan your inventory accordingly to avoid stock shortages. -
What are the common quality assurance practices in knife manufacturing?
Common quality assurance practices in knife manufacturing include regular inspections during production, material testing, and final product checks. Manufacturers often implement a quality management system (QMS) to standardize processes and ensure consistency. Look for manufacturers that provide documentation of their quality assurance processes and certifications. Requesting a detailed quality assurance plan can also help you understand how they maintain product standards throughout the manufacturing process.
Important Disclaimer & Terms of Use
⚠️ Important Disclaimer
The information provided in this guide, including content regarding manufacturers, technical specifications, and market analysis, is for informational and educational purposes only. It does not constitute professional procurement advice, financial advice, or legal advice.
While we have made every effort to ensure the accuracy and timeliness of the information, we are not responsible for any errors, omissions, or outdated information. Market conditions, company details, and technical standards are subject to change.
B2B buyers must conduct their own independent and thorough due diligence before making any purchasing decisions. This includes contacting suppliers directly, verifying certifications, requesting samples, and seeking professional consultation. The risk of relying on any information in this guide is borne solely by the reader.
Strategic Sourcing Conclusion and Outlook for knife manufacturer
What Are the Key Takeaways for B2B Buyers in Knife Manufacturing?
In conclusion, strategic sourcing in the knife manufacturing sector is essential for maximizing value and ensuring quality. B2B buyers from Africa, South America, the Middle East, and Europe should prioritize suppliers that demonstrate reliability, compliance with international standards, and ethical practices. Building strong partnerships with manufacturers who invest in innovation and sustainability can lead to improved supply chain resilience and reduced costs.
How Can Buyers Enhance Their Strategic Sourcing Approaches?
To enhance sourcing strategies, buyers should leverage technology, such as digital procurement platforms, to streamline supplier evaluations and transactions. Additionally, conducting regular market research will help in identifying emerging trends and new suppliers that can offer competitive advantages. Engaging in collaborative negotiations can also create win-win scenarios, ensuring long-term success.
What Does the Future Hold for Knife Manufacturers and Buyers?
Looking ahead, the knife manufacturing industry is poised for growth, driven by advancements in materials and manufacturing techniques. International B2B buyers are encouraged to remain proactive in their sourcing strategies and stay informed about market dynamics. By embracing innovation and sustainability, businesses can not only meet consumer demands but also contribute to a more responsible industry.
Take action today by evaluating your current suppliers and exploring new opportunities that align with your strategic goals.