Unlock Savings: The Complete Guide to Work Boot Manufacturer (2025)
Introduction: Navigating the Global Market for work boot manufacturer
Navigating the complexities of the global market for work boot manufacturing can be a daunting task for international B2B buyers, especially those from diverse regions like Africa, South America, the Middle East, and Europe. One of the key challenges buyers face is sourcing high-quality work boots that not only meet safety standards but also cater to the specific needs of various industries, from construction to mining. This comprehensive guide aims to address these challenges by providing actionable insights into the types of work boots available, their applications, and essential considerations for supplier vetting.
In the following sections, we will delve into critical factors such as material selection, comfort features, and compliance with international safety regulations. Furthermore, we will explore cost considerations, including pricing strategies and potential hidden costs associated with importing work boots. By equipping B2B buyers with the necessary knowledge to make informed purchasing decisions, this guide serves as a vital resource for organizations looking to enhance workplace safety and employee satisfaction.
Understanding the nuances of the work boot market empowers buyers to navigate supplier landscapes effectively, ensuring they select manufacturers that align with their operational requirements and budget constraints. Whether you are a procurement manager in Egypt or a business owner in Brazil, this guide will facilitate your journey in sourcing the right work boots for your workforce.
Understanding work boot manufacturer Types and Variations
Type Name | Key Distinguishing Features | Primary B2B Applications | Brief Pros & Cons for Buyers |
---|---|---|---|
Steel-Toe Work Boots | Reinforced toe protection, heavy-duty materials | Construction, manufacturing, logistics | Pros: High durability and safety; Cons: Heavier than alternatives. |
Waterproof Work Boots | Waterproof materials, slip-resistant soles | Outdoor work, agriculture, mining | Pros: Keeps feet dry in wet conditions; Cons: May be less breathable. |
Electrical Hazard Boots | Insulated against electrical shocks | Electrical work, utility services | Pros: Enhanced safety against electric hazards; Cons: May lack other protective features. |
Composite-Toe Work Boots | Lightweight composite materials instead of steel | Warehousing, assembly lines | Pros: Lighter than steel-toe; Cons: May not provide the same level of protection. |
Slip-Resistant Work Boots | Specialized tread patterns for grip | Food service, healthcare, maintenance | Pros: Reduces slip and fall accidents; Cons: Tread may wear down faster. |
What Are the Characteristics of Steel-Toe Work Boots?
Steel-toe work boots are designed for maximum protection in high-risk environments. Featuring reinforced toe caps made from steel, these boots are essential in industries such as construction and manufacturing where heavy objects may fall. When purchasing, buyers should consider the weight of the boots, as they can be heavier than other types, potentially causing fatigue over long hours. Additionally, checking for comfort features like cushioning and arch support is crucial for prolonged wear.
How Do Waterproof Work Boots Benefit B2B Buyers?
Waterproof work boots are constructed from materials that prevent water penetration, making them ideal for outdoor work, agriculture, and mining. These boots often feature slip-resistant soles to enhance traction on wet surfaces. B2B buyers should evaluate the breathability of these boots, as prolonged wear in wet conditions can lead to discomfort. It’s also important to consider the ease of cleaning, especially for industries that may expose boots to mud or chemicals.
Why Choose Electrical Hazard Boots for Safety?
Electrical hazard boots are specifically designed to provide insulation against electrical shocks, making them vital for workers in electrical and utility services. These boots typically feature non-conductive soles and materials to ensure safety. When sourcing these boots, buyers must ensure compliance with safety standards relevant to their industry. Consideration should also be given to the boot’s overall comfort and fit, as these factors can affect worker productivity and safety.
What Are the Advantages of Composite-Toe Work Boots?
Composite-toe work boots utilize lightweight materials like carbon fiber or Kevlar instead of steel for toe protection. This makes them a popular choice in warehousing and assembly lines where comfort and agility are priorities. B2B buyers should assess the level of protection offered, as composite-toe boots may not withstand as much impact as their steel counterparts. Additionally, these boots often provide better thermal insulation, which can be beneficial in colder environments.
How Do Slip-Resistant Work Boots Enhance Workplace Safety?
Slip-resistant work boots feature specialized tread patterns designed to improve grip on slippery surfaces, making them crucial in sectors like food service, healthcare, and maintenance. These boots help reduce the risk of slip-and-fall accidents, which can lead to significant workplace injuries. Buyers should consider the durability of the tread, as frequent use can lead to quicker wear. Additionally, evaluating the overall comfort and support of the boot can enhance employee safety and satisfaction.
Key Industrial Applications of work boot manufacturer
Industry/Sector | Specific Application of Work Boot Manufacturer | Value/Benefit for the Business | Key Sourcing Considerations for this Application |
---|---|---|---|
Construction | Safety footwear for on-site workers | Reduces workplace injuries, ensuring compliance with safety regulations | Material durability, slip resistance, and compliance with local safety standards |
Manufacturing | Protective footwear in factory environments | Enhances worker safety, boosts productivity by preventing foot injuries | Customization options, ease of cleaning, and ergonomic design |
Agriculture | Waterproof and insulated boots for farm workers | Protects against harsh weather and hazardous materials, improving worker comfort | Waterproofing technology, insulation properties, and agricultural-specific features |
Oil & Gas | Heavy-duty boots for hazardous environments | Provides necessary protection against chemicals and heavy machinery | Chemical resistance, steel toe options, and compliance with industry regulations |
Logistics & Warehousing | Safety boots for warehouse personnel | Minimizes accidents and enhances operational efficiency | Lightweight design, ease of wear, and traction for various surfaces |
How Are Work Boots Used in the Construction Industry?
In the construction sector, work boots are essential for protecting workers from potential injuries caused by heavy materials and equipment. These boots often feature reinforced toes and slip-resistant soles to enhance safety on uneven surfaces. For international buyers, especially in regions like Africa and South America, it’s crucial to consider local safety regulations and climate conditions when sourcing. Ensuring compliance with safety standards can significantly reduce the risk of workplace injuries.
What Role Do Work Boots Play in Manufacturing?
Manufacturing environments require durable and protective footwear to safeguard workers from machinery hazards and heavy items. Work boots designed for this sector typically include features such as steel toes and puncture-resistant soles. Buyers from the Middle East and Europe should prioritize boots that offer both comfort and protection, as these factors directly influence productivity. Customization options, such as company branding or specific ergonomic designs, can also enhance employee satisfaction and safety.
Why Are Work Boots Important in Agriculture?
Agricultural workers often face harsh conditions, making waterproof and insulated boots a necessity. These boots protect against wet and cold environments while ensuring comfort during long hours of work. For buyers in regions like Africa, sourcing boots that provide both insulation and waterproofing is vital. Furthermore, understanding the specific agricultural hazards in the region can guide purchasing decisions, ensuring that the selected footwear meets all necessary safety standards.
How Do Work Boots Protect Workers in Oil & Gas?
In the oil and gas industry, workers are exposed to various hazards, including chemicals and heavy equipment. Heavy-duty work boots are designed to withstand these challenges, often featuring chemical resistance and reinforced protection. International buyers should look for boots that comply with stringent industry regulations, ensuring maximum safety for their workers. Evaluating the materials and certifications of potential suppliers can lead to better sourcing decisions.
What Are the Benefits of Work Boots in Logistics and Warehousing?
In logistics and warehousing, safety boots are crucial for preventing slips, trips, and falls. These boots often feature lightweight designs and superior traction to enhance mobility in busy environments. Buyers from Europe and beyond should consider the specific needs of their warehouse operations when sourcing, focusing on comfort and durability to minimize workplace accidents. Investing in high-quality footwear can lead to improved employee morale and reduced turnover rates.
Related Video: What is Industrial Automation?
3 Common User Pain Points for ‘work boot manufacturer’ & Their Solutions
Scenario 1: Sourcing Quality Work Boots for Diverse Environments
The Problem: B2B buyers often struggle to find work boots that meet the specific safety and comfort requirements for various job sites. For instance, a construction company in Egypt may need boots that provide both slip resistance and electrical hazard protection, while a mining operation in South America may prioritize puncture resistance and insulation. This mismatch can lead to employee dissatisfaction and increased safety risks, ultimately affecting productivity and the bottom line.
The Solution: To effectively source high-quality work boots, buyers should conduct thorough market research to identify manufacturers specializing in specific safety features. Engaging with manufacturers who understand regional safety regulations can provide valuable insights into the appropriate certifications and standards required in different countries. Additionally, consider visiting trade shows or industry expos where you can assess the quality and features of work boots firsthand. Establishing a partnership with a manufacturer that offers customizable options can also allow you to tailor the boots to meet your specific environmental needs.
Scenario 2: Managing Bulk Orders and Supply Chain Logistics
The Problem: Many B2B buyers face challenges when placing bulk orders for work boots due to inconsistent supply chain logistics. For instance, a facility management company in the UK may encounter delays in delivery, leading to a shortage of essential safety gear for new hires. Such disruptions can cause compliance issues and may lead to potential liabilities if employees are not adequately equipped.
The Solution: To mitigate supply chain disruptions, B2B buyers should develop strong relationships with multiple suppliers to ensure redundancy. Create a detailed inventory management system that forecasts demand based on workforce changes, seasonal fluctuations, and project timelines. This proactive approach can help in placing orders well in advance. Additionally, negotiating clear delivery timelines and penalties for delays in contracts can encourage manufacturers to prioritize your orders and maintain reliable supply chains.
Scenario 3: Ensuring Proper Fit and Comfort for Employees
The Problem: Another common pain point for B2B buyers is ensuring that work boots fit properly and provide the necessary comfort for employees who wear them for long hours. An example could be a logistics company in the Middle East that finds a significant number of employees reporting foot fatigue and injuries due to ill-fitting footwear. This not only affects employee morale but can also lead to increased absenteeism and reduced productivity.
The Solution: To address fit and comfort issues, B2B buyers should implement a comprehensive sizing and fitting program prior to placing orders. This can involve providing employees with fitting guides, or arranging for size samples to be tried on before bulk purchases. Manufacturers that offer a wide range of sizes and widths can be particularly beneficial. Furthermore, consider investing in ergonomic options or work boots with customizable insoles that can accommodate individual foot shapes. Regular feedback from employees about comfort can inform future purchasing decisions and ensure that the footwear remains fit for purpose, thereby enhancing overall workplace safety and efficiency.
Strategic Material Selection Guide for work boot manufacturer
What Are the Key Properties of Leather in Work Boot Manufacturing?
Leather is a traditional material in work boot manufacturing, known for its durability and comfort. It typically offers excellent abrasion resistance and flexibility, making it suitable for various working environments. Leather can withstand a range of temperatures and provides some level of water resistance, especially when treated with appropriate coatings.
Pros and Cons of Leather
The primary advantage of leather is its durability; high-quality leather can last several years with proper care. It also molds to the wearer’s foot over time, enhancing comfort. However, leather can be expensive, and its production involves complex manufacturing processes. Additionally, it may not perform well in extreme wet conditions unless properly treated.
Impact on Application
Leather is compatible with various applications, especially in industries requiring a balance of comfort and protection, such as construction and manufacturing. However, buyers should be aware of the specific care requirements for leather footwear to maintain its performance over time.
Considerations for International Buyers
When sourcing leather work boots, international buyers should ensure compliance with local regulations regarding animal welfare and environmental sustainability. Standards such as ASTM and EN ISO may apply, depending on the region.
How Does Rubber Contribute to Work Boot Performance?
Rubber is another popular material in work boot manufacturing, particularly for outsoles. Known for its excellent slip resistance and shock absorption, rubber is ideal for environments where traction is essential.
Pros and Cons of Rubber
The key advantage of rubber is its durability and resistance to wear, making it suitable for heavy-duty applications. It is also relatively cost-effective compared to other materials. However, rubber can become stiff in cold temperatures, which may affect comfort. Additionally, manufacturing rubber boots can be less complex than leather, but the quality of rubber can vary significantly.
Impact on Application
Rubber is particularly effective in wet or oily environments, making it a preferred choice for industries like oil and gas, agriculture, and construction. Its ability to resist chemicals and abrasives enhances its application versatility.
Considerations for International Buyers
Buyers should consider the specific rubber compounds used in the boots, as different formulations may meet varying international standards. Compliance with ASTM or EN standards for slip resistance and chemical exposure is crucial, especially in regions with stringent safety regulations.
What Role Does Synthetic Material Play in Work Boot Manufacturing?
Synthetic materials, such as nylon and polyester, are increasingly used in work boots, particularly for their lightweight properties and moisture-wicking capabilities. These materials often offer good abrasion resistance and can be engineered for specific performance characteristics.
Pros and Cons of Synthetic Materials
The primary advantage of synthetic materials is their cost-effectiveness and lightweight nature, which can enhance comfort for the wearer. They are often easier to clean and maintain compared to leather. However, synthetic materials may not provide the same level of durability or breathability as leather, and they can be less comfortable over long periods.
Impact on Application
Synthetic materials are well-suited for applications where weight and moisture management are critical, such as in logistics and warehousing. However, they may not perform as well in extreme conditions compared to leather or rubber.
Considerations for International Buyers
When sourcing synthetic work boots, buyers should verify that the materials meet local environmental regulations and standards for safety. Understanding the specific properties of the synthetic materials used is essential for ensuring they align with the intended application.
How Do Composite Materials Enhance Work Boot Functionality?
Composite materials, which may include combinations of plastics, carbon fibers, and other materials, are becoming popular in work boot manufacturing for their lightweight and non-metallic properties. These materials can provide excellent protection while reducing overall weight.
Pros and Cons of Composite Materials
Composite materials are advantageous because they are typically lighter than traditional materials and do not conduct electricity, making them suitable for electrical hazard environments. However, they may not offer the same level of durability as metal components and can be more expensive to produce.
Impact on Application
Composite materials are ideal for industries where weight and electrical hazards are concerns, such as electrical work and construction. Their non-metallic nature also makes them compliant with airport security regulations, allowing for easy passage through metal detectors.
Considerations for International Buyers
International buyers should ensure that composite materials comply with relevant safety standards, such as ASTM or EN ISO, particularly for protective footwear. Understanding the specific certifications related to composite materials can help in making informed purchasing decisions.
Material | Typical Use Case for Work Boot Manufacturer | Key Advantage | Key Disadvantage/Limitation | Relative Cost (Low/Med/High) |
---|---|---|---|---|
Leather | Construction, manufacturing | Durability and comfort | High cost, complex manufacturing | High |
Rubber | Oil and gas, agriculture | Excellent slip resistance | Can stiffen in cold temperatures | Medium |
Synthetic | Logistics, warehousing | Lightweight and cost-effective | Less durable than leather | Low |
Composite | Electrical work, construction | Lightweight, non-conductive | May lack durability | Medium |
In-depth Look: Manufacturing Processes and Quality Assurance for work boot manufacturer
What Are the Main Stages in the Manufacturing Process of Work Boots?
The manufacturing of work boots involves several critical stages, each essential for ensuring the quality and durability of the final product. Understanding these stages is vital for B2B buyers, particularly those from diverse regions such as Africa, South America, the Middle East, and Europe.
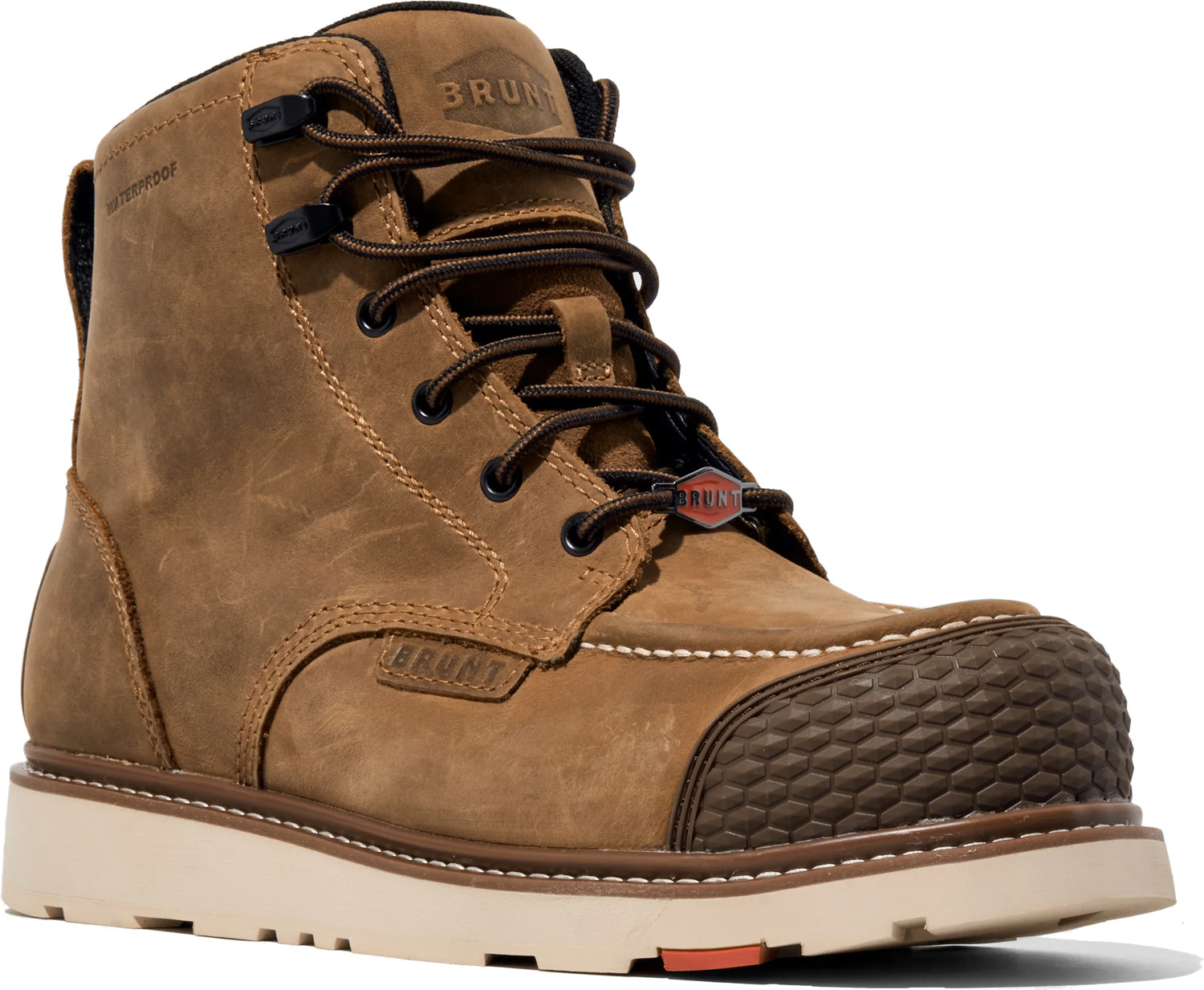
A stock image related to work boot manufacturer.
-
Material Preparation:
The first step is selecting and preparing the right materials, which typically include leather, synthetic fabrics, rubber, and various reinforcements. Each material undergoes rigorous quality checks to ensure it meets the required standards. For instance, leather may be tested for thickness, flexibility, and water resistance, while synthetic materials are assessed for durability and abrasion resistance. -
Forming:
During this stage, the prepared materials are shaped into components of the boot. Techniques such as cutting, stamping, and molding are employed. Advanced technologies like computer numerical control (CNC) machines may be used for precision cutting. This stage is crucial as it determines the overall fit and comfort of the boot. -
Assembly:
The assembly process involves stitching together the various components, including the upper, lining, insole, and outsole. This is typically done using heavy-duty sewing machines and may incorporate techniques like Goodyear welting, which enhances the boot’s longevity and water resistance. Quality assurance during assembly is vital to ensure that all parts are securely attached and that no defects are present. -
Finishing:
The finishing stage includes several processes such as polishing, waterproofing treatments, and adding additional features like slip-resistant soles or safety toe caps. This stage also involves applying any branding or labeling. Final inspections are conducted to ensure that each boot meets the specified aesthetic and functional standards.
How is Quality Assurance Implemented in Work Boot Manufacturing?
Quality assurance (QA) is integral to the work boot manufacturing process, ensuring that products not only meet but exceed international and industry-specific standards. For international B2B buyers, understanding the QA processes can significantly influence purchasing decisions.
-
International Standards:
Many work boot manufacturers adhere to international quality standards, such as ISO 9001, which outlines the criteria for a quality management system. Compliance with ISO standards assures buyers of consistent quality, effective processes, and continuous improvement. Additionally, industry-specific certifications like CE (Conformité Européenne) for safety footwear and API (American Petroleum Institute) standards for oil and gas industries are crucial for ensuring compliance with regional regulations. -
Quality Control Checkpoints:
– Incoming Quality Control (IQC): This checkpoint involves inspecting raw materials upon arrival at the manufacturing facility. Materials that do not meet specifications are rejected, reducing the risk of defects in the final product.
– In-Process Quality Control (IPQC): During the manufacturing process, regular inspections are performed to ensure that each stage adheres to quality standards. This might include checking the stitching integrity during assembly or measuring the thickness of materials.
– Final Quality Control (FQC): Before packaging, each pair of boots undergoes a final inspection. This includes checking for visual defects, comfort, and functionality, ensuring that the product meets the buyer’s requirements. -
Common Testing Methods:
Various testing methods are employed to ensure the boots meet safety and performance standards. Common tests include:
– Slip Resistance Testing: Evaluating the outsole’s grip on various surfaces.
– Waterproof Testing: Ensuring that the materials can withstand water exposure without compromising comfort.
– Impact Resistance Testing: Assessing the ability of safety toe caps to withstand heavy impacts.
How Can B2B Buyers Verify Supplier Quality Control?
For B2B buyers, particularly those in Africa, South America, the Middle East, and Europe, verifying the quality control practices of suppliers is essential for making informed purchasing decisions. Here are actionable insights on how to conduct this verification:
-
Supplier Audits:
Conducting on-site audits is one of the most effective ways to assess a supplier’s quality control processes. During an audit, buyers can evaluate the manufacturing environment, observe production practices, and review quality control documentation. -
Quality Control Reports:
Requesting detailed quality control reports from suppliers can provide insights into their QA processes and outcomes. These reports should include information on material inspections, testing results, and any corrective actions taken for defects. -
Third-Party Inspections:
Engaging third-party inspection agencies can provide an unbiased assessment of a supplier’s quality control practices. These agencies typically follow strict protocols and can conduct inspections at various stages of production. -
Certifications and Compliance:
Buyers should verify that suppliers hold relevant certifications and comply with applicable international standards. This can be done by requesting copies of certification documents and checking their validity through official channels.
What Are the Quality Control Nuances for International B2B Buyers?
When sourcing work boots from international manufacturers, buyers should be aware of specific nuances in quality control that may vary by region:
-
Regional Standards:
Different regions may have varying quality standards and regulations. For example, while CE marking is essential for products sold in the European market, buyers in the Middle East may need to comply with local safety regulations that differ significantly. -
Cultural Expectations:
Understanding cultural differences in business practices can affect quality expectations. For instance, buyers from European countries may expect a more rigorous quality assurance process compared to those from other regions. -
Communication Barriers:
Language differences can pose challenges in understanding quality standards and specifications. Clear communication and documentation are essential to ensure that both parties have a mutual understanding of quality expectations. -
Logistics and Supply Chain Considerations:
The logistics of international shipping can also impact quality assurance. Buyers should consider how products are stored and transported, as improper handling can lead to damage or defects before the product even reaches the end user.
By thoroughly understanding the manufacturing processes and quality assurance practices of work boot manufacturers, B2B buyers can make informed decisions that align with their needs and expectations. Prioritizing quality assurance not only ensures product reliability but also strengthens supplier relationships and enhances brand reputation in competitive markets.
Practical Sourcing Guide: A Step-by-Step Checklist for ‘work boot manufacturer’
Introduction
Sourcing work boots for your business involves a strategic approach to ensure you partner with the right manufacturer. This guide provides a step-by-step checklist that will help international B2B buyers, especially from Africa, South America, the Middle East, and Europe, navigate the complexities of procurement. By following these actionable steps, you can enhance your sourcing process and secure high-quality products that meet your specific needs.
Step 1: Define Your Technical Specifications
Before reaching out to manufacturers, clarify the technical specifications of the work boots you require. This includes material preferences, safety standards (such as ISO or ASTM certifications), and design features (like waterproofing or slip resistance).
– Why it matters: Defining specifications helps streamline communication with potential suppliers and ensures that the products meet your operational demands.
Step 2: Research Potential Manufacturers
Conduct thorough research to identify potential work boot manufacturers. Utilize online platforms, industry directories, and trade shows to create a shortlist of candidates.
– What to look for: Focus on manufacturers with a strong reputation, positive reviews, and relevant experience in producing work boots. Consider their geographic location as well, which can affect shipping times and costs.
Step 3: Evaluate Supplier Certifications
Ensure that your selected manufacturers hold necessary certifications relevant to work boots, such as CE marking in Europe or ANSI standards in the U.S. This guarantees compliance with safety regulations.
– Verification tips: Request documentation and check if the certifications are up-to-date. This step is crucial to avoid legal liabilities and ensure product quality.
Step 4: Request Samples for Testing
Before making a bulk purchase, request samples of the work boots for testing. This allows you to evaluate the quality, comfort, and suitability of the product for your workforce.
– Testing criteria: Assess the durability, fit, and performance of the boots in real-world conditions. Feedback from employees who will wear the boots can provide valuable insights.
Step 5: Negotiate Pricing and Terms
Once you have identified a suitable manufacturer, engage in negotiations regarding pricing, payment terms, and delivery schedules.
– Key considerations: Ensure clarity on whether prices are inclusive of taxes and shipping. Also, discuss bulk order discounts or credit terms to maximize your budget.
Step 6: Establish a Communication Plan
Set up a clear communication plan with your chosen manufacturer. Regular updates on production status, potential delays, and quality checks are essential for a smooth procurement process.
– Effective communication: Utilize tools like emails, video calls, or project management software to maintain transparency and address any issues promptly.
Step 7: Finalize Contracts and Agreements
Before placing a large order, ensure that all agreements are documented in a formal contract. This should include details about product specifications, pricing, delivery timelines, and warranty provisions.
– Importance of contracts: A well-drafted contract protects both parties and minimizes risks associated with misunderstandings or disputes.
By following these structured steps, you can effectively source work boot manufacturers that align with your business needs and standards, ensuring a successful procurement process.
Comprehensive Cost and Pricing Analysis for work boot manufacturer Sourcing
What Are the Key Cost Components in Work Boot Manufacturing?
Understanding the cost structure is crucial for international B2B buyers looking to source work boots. The main components of manufacturing costs include:
-
Materials: The choice of materials significantly affects the overall cost. High-quality leather, rubber, and synthetic materials can drive prices up. Buyers should evaluate the trade-off between cost and durability.
-
Labor: Labor costs vary widely by region. In countries with lower labor costs, buyers may find more competitive pricing, but this might come at the expense of quality or compliance with international labor standards.
-
Manufacturing Overhead: This includes utilities, rent, and other indirect costs associated with production. A higher overhead can indicate a more established facility, which may provide better quality assurance.
-
Tooling: Custom tooling for specific designs can be expensive. If a buyer requires unique features or branding, they should factor in these costs early in the negotiation process.
-
Quality Control (QC): Implementing robust QC processes may add to the cost but is essential for ensuring product reliability and safety, especially in industries that require compliance with strict regulations.
-
Logistics: Shipping costs, including freight and customs duties, can vary significantly based on the destination. Incoterms (International Commercial Terms) play a crucial role in determining who is responsible for shipping costs, insurance, and risk during transportation.
-
Margin: Manufacturers typically apply a markup to cover their costs and ensure profitability. Understanding their pricing strategy can help buyers negotiate better deals.
How Do Price Influencers Affect Work Boot Costs?
Several factors can influence the pricing of work boots, including:
-
Volume/MOQ (Minimum Order Quantity): Buying in larger quantities often results in lower per-unit costs. Buyers should assess their needs and negotiate volume discounts.
-
Specifications and Customization: Custom features, such as specialized safety ratings or unique designs, will increase costs. Buyers should clarify their requirements upfront to avoid unexpected charges.
-
Materials and Quality Certifications: Higher-quality materials or certifications (e.g., ISO, ASTM) typically come with a higher price tag. Buyers should consider the long-term value of investing in certified products.
-
Supplier Factors: The reputation and reliability of suppliers can affect pricing. Established manufacturers may charge more due to their experience and quality assurance processes.
-
Incoterms: Understanding Incoterms is essential for international buyers. They determine the responsibilities of buyers and sellers in shipping arrangements, which can impact overall costs.
What Are Effective Buyer Tips for Cost-Efficiency in Sourcing Work Boots?
International B2B buyers can adopt several strategies to enhance cost-efficiency:
-
Negotiate Wisely: Leverage your understanding of the cost structure to negotiate better pricing. Highlight your purchasing power or potential for future orders to gain favorable terms.
-
Consider Total Cost of Ownership (TCO): Look beyond the initial purchase price. Factors like durability, maintenance, and potential replacement costs can significantly impact the overall expenditure.
-
Be Aware of Pricing Nuances: Understand that prices may vary based on regional economic conditions, currency fluctuations, and local market demand. Buyers from Africa, South America, the Middle East, and Europe should be prepared for price variations and factor them into their budgets.
-
Request Detailed Quotes: Ensure quotes clearly outline all costs, including shipping, taxes, and potential tariffs. This transparency helps in comparing offers from different suppliers accurately.
-
Stay Informed About Market Trends: Keeping up-to-date with industry trends can provide leverage in negotiations and help buyers identify the best times to purchase.
Disclaimer for Indicative Prices
Prices for work boots can fluctuate based on various factors, including market demand and raw material costs. Therefore, the figures discussed in this analysis are indicative and should be confirmed with suppliers during the sourcing process. Buyers are encouraged to conduct thorough market research and engage in direct negotiations to secure the best possible pricing for their needs.
Alternatives Analysis: Comparing work boot manufacturer With Other Solutions
When evaluating work boot manufacturers, it’s crucial to consider alternative solutions that could meet the safety and comfort needs of your workforce. This analysis will compare traditional work boot manufacturing with two viable alternatives: custom work boot solutions and safety footwear rental services. Each option presents unique advantages and challenges that can significantly influence your decision as an international B2B buyer.
Comparison Table of Work Boot Solutions
Comparison Aspect | Work Boot Manufacturer | Custom Work Boot Solutions | Safety Footwear Rental Services |
---|---|---|---|
Performance | High durability and protection | Tailored fit for specific needs | Varies by supplier, generally reliable |
Cost | Moderate to high upfront cost | Higher initial investment, potential long-term savings | Lower upfront costs but recurring fees |
Ease of Implementation | Requires supplier selection and bulk ordering | Complex due to customization process | Simple, with quick setup and flexibility |
Maintenance | Regular maintenance needed for longevity | Minimal, as boots are often high-quality | Low, as the provider handles maintenance |
Best Use Case | Large teams needing uniformity | Specialized roles with unique requirements | Short-term projects or fluctuating workforce needs |
What Are the Advantages and Disadvantages of Custom Work Boot Solutions?
Custom work boot solutions offer the advantage of a tailored fit, which can enhance comfort and safety for specific job functions, such as construction or manufacturing. These boots are designed to meet the exact specifications of the wearer, reducing the risk of injuries due to improper fit. However, the initial investment is typically higher compared to standard work boots, which may not be feasible for every company. Moreover, the customization process can be time-consuming, delaying the availability of boots for new employees.
How Do Safety Footwear Rental Services Work?
Safety footwear rental services provide a flexible and cost-effective solution for companies with fluctuating workforce sizes or short-term projects. These services allow businesses to rent high-quality safety footwear as needed, which can be particularly beneficial for temporary workers or seasonal projects. The key advantage is the lower upfront cost and the fact that maintenance and replacements are handled by the rental provider. However, ongoing rental fees can accumulate over time, potentially leading to higher long-term costs compared to purchasing outright. Additionally, the range of available sizes and styles may vary, which can be a limitation for some users.
Conclusion: How to Choose the Right Solution for Your Needs?
When deciding between work boot manufacturers and alternative solutions, consider the specific needs of your workforce. Assess factors such as budget constraints, the nature of work performed, and the expected duration of use. For companies with a stable workforce requiring durable, protective footwear, investing in work boots from a reputable manufacturer may be the best choice. Conversely, if your organization experiences fluctuating workforce demands or needs specialized footwear for specific tasks, exploring custom solutions or rental services could provide the necessary flexibility and comfort. Ultimately, aligning the footwear solution with your operational requirements will lead to enhanced safety and productivity in the workplace.
Essential Technical Properties and Trade Terminology for work boot manufacturer
What Are the Essential Technical Properties of Work Boots for B2B Buyers?
When sourcing work boots, understanding the technical properties is crucial for ensuring quality and safety in demanding environments. Here are some key specifications that B2B buyers should consider:
1. Material Grade: What Types of Materials Are Used in Work Boots?
The material grade directly affects the durability, comfort, and safety of work boots. Common materials include:
- Leather: Offers durability and resistance to wear and tear.
- Synthetic Fabrics: Lightweight and often water-resistant, these materials provide flexibility and comfort.
- Rubber: Used for outsoles, providing excellent traction and slip resistance.
Choosing the right material can significantly impact the longevity and performance of the footwear, making it essential for buyers to inquire about material specifications.
2. Tolerance Levels: How Do Tolerance Levels Affect Fit and Comfort?
Tolerance refers to the allowable variations in the dimensions of the boots. A tighter tolerance often ensures a better fit and increased comfort, which is crucial for workers who are on their feet for long periods. Tolerance levels can affect:
- Sizing: Ensures that the boots fit correctly to reduce discomfort and potential injuries.
- Manufacturing Consistency: Helps maintain quality across large orders, which is particularly important for B2B contracts.
Understanding tolerance specifications helps buyers ensure they receive products that meet their exact needs.
3. Safety Standards: What Safety Standards Should Work Boots Meet?
Work boots must comply with specific safety standards, which can vary by region. Common standards include:
- ASTM (American Society for Testing and Materials): Sets standards for impact and compression resistance.
- ISO (International Organization for Standardization): Ensures quality and safety across international markets.
Buyers should verify that the boots meet relevant safety standards to protect workers effectively.
4. Slip Resistance: How Important Is Slip Resistance in Work Boots?
Slip resistance is critical for preventing workplace accidents. The outsole design and material play a significant role in slip resistance. Buyers should consider:
- Tread Patterns: Different patterns provide varying levels of grip on wet or oily surfaces.
- Material Composition: Certain rubber compounds offer better slip resistance than others.
Ensuring boots have adequate slip resistance is vital for worker safety, especially in hazardous environments.
5. Weight: Why Is the Weight of Work Boots a Consideration?
The weight of work boots can affect worker fatigue and comfort. Lightweight boots can enhance mobility and reduce fatigue during long shifts. However, it’s essential to balance weight with protection and durability, as heavier boots often provide better safety features.
What Are Common Trade Terminology and Jargon for Work Boot Manufacturers?
Understanding industry jargon can help B2B buyers communicate effectively with manufacturers. Here are some essential terms:
1. OEM (Original Equipment Manufacturer): What Does OEM Mean in the Footwear Industry?
OEM refers to companies that produce goods that are marketed under another company’s brand name. For work boot buyers, sourcing from OEMs can provide opportunities for customization and branding without the need for extensive manufacturing infrastructure.
2. MOQ (Minimum Order Quantity): How Does MOQ Affect Purchasing Decisions?
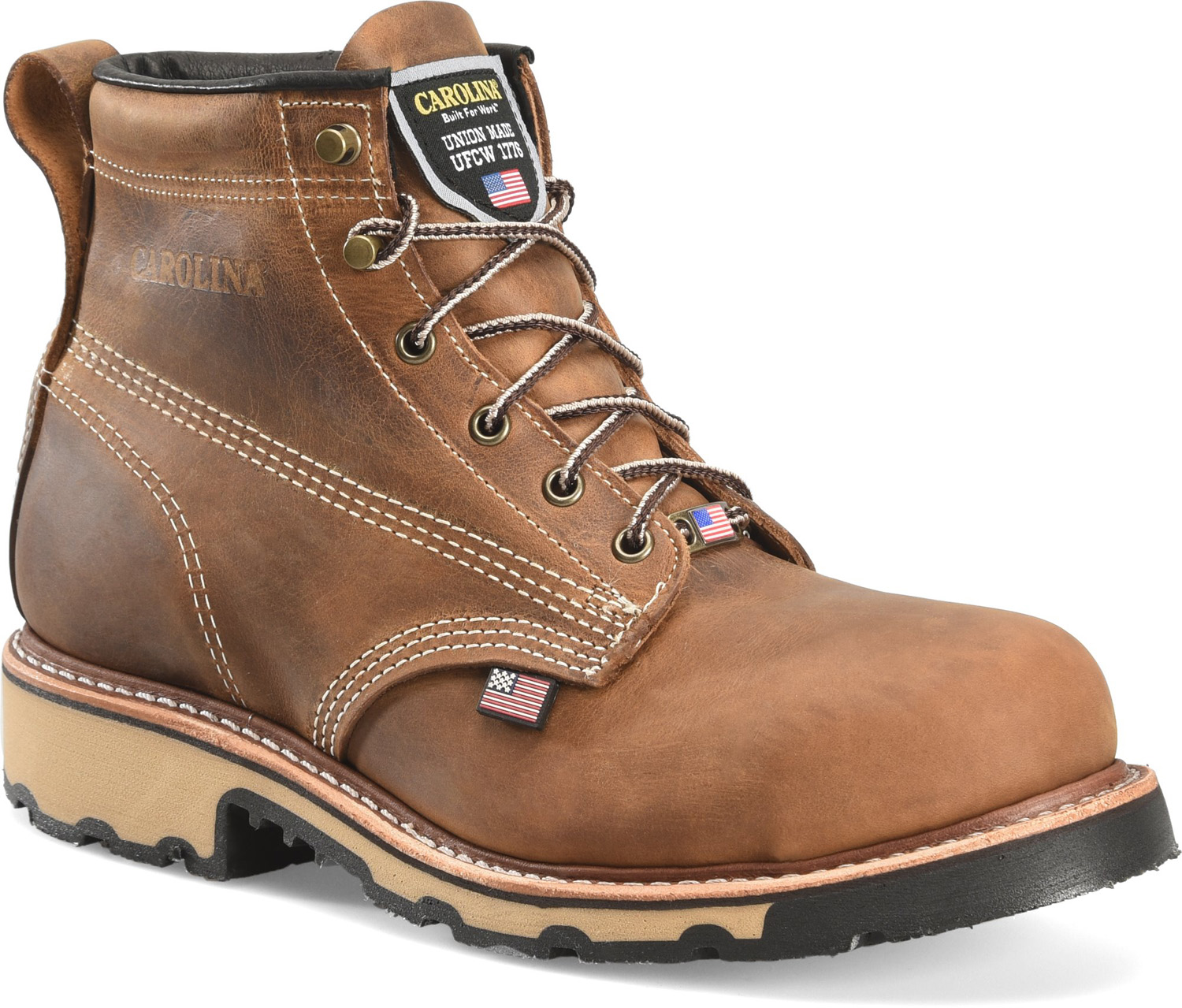
A stock image related to work boot manufacturer.
MOQ is the smallest quantity of a product that a supplier is willing to sell. Understanding the MOQ can help buyers plan their inventory and budget effectively. For businesses, negotiating lower MOQs can lead to more flexible purchasing options.
3. RFQ (Request for Quotation): Why Is RFQ Important in B2B Transactions?
An RFQ is a document sent to suppliers to request pricing and terms for specific products. This process is essential for comparing offers from different manufacturers, allowing buyers to make informed decisions based on price, quality, and delivery terms.
4. Incoterms: What Are Incoterms and Why Should B2B Buyers Understand Them?
Incoterms (International Commercial Terms) define the responsibilities of buyers and sellers in international trade. Familiarity with terms such as FOB (Free on Board) and CIF (Cost, Insurance, and Freight) can help buyers negotiate better shipping agreements and understand their liabilities.
By grasping these technical properties and trade terminologies, B2B buyers can make informed purchasing decisions and ensure they acquire high-quality work boots tailored to their specific needs.
Navigating Market Dynamics and Sourcing Trends in the work boot manufacturer Sector
What Are the Current Market Dynamics and Key Trends in the Work Boot Manufacturing Sector?
The work boot manufacturing sector is witnessing significant growth, driven by various global factors. The increasing demand for durable, safety-oriented footwear in industries such as construction, mining, and manufacturing highlights the necessity for high-quality work boots. In regions like Africa and South America, rapid industrialization is boosting the need for protective gear. Additionally, heightened awareness of workplace safety regulations, particularly in Europe and the Middle East, is compelling businesses to invest in compliant footwear solutions.
Emerging technologies are reshaping the sourcing landscape. Companies are increasingly leveraging digital platforms for procurement, allowing B2B buyers to compare product offerings and supplier credentials efficiently. The adoption of 3D printing technology is also gaining traction, enabling manufacturers to produce customized boots that cater to specific occupational needs. Furthermore, the rise of e-commerce channels is facilitating direct-to-consumer sales, enhancing brand visibility and customer engagement for international buyers.
Another key trend is the integration of data analytics in understanding consumer preferences and market demands. B2B buyers can leverage these insights to make informed purchasing decisions that align with market trends, ensuring they source products that meet both safety standards and consumer expectations.
How Does Sustainability and Ethical Sourcing Impact the Work Boot Manufacturing Industry?
Sustainability is becoming a critical consideration for B2B buyers in the work boot manufacturing sector. The environmental impact of manufacturing processes, including resource consumption and waste generation, is under increasing scrutiny. Ethical sourcing practices not only enhance brand reputation but also ensure compliance with international labor standards, which is essential for companies operating in diverse markets.
B2B buyers are increasingly seeking suppliers that demonstrate a commitment to sustainable practices. This includes the use of eco-friendly materials such as recycled plastics and organic cotton in boot production. Additionally, certifications like Global Organic Textile Standard (GOTS) and Cradle to Cradle (C2C) are becoming essential indicators of a manufacturer’s commitment to environmental stewardship.
Moreover, the demand for ‘green’ products is reshaping consumer behavior. Buyers from regions like Europe are more inclined to support brands that prioritize sustainability, making it vital for manufacturers to adopt transparent and responsible sourcing strategies. This not only helps in attracting eco-conscious clients but also aligns with global initiatives aimed at reducing carbon footprints.
What is the Historical Context of Work Boot Manufacturing for B2B Buyers?
The work boot manufacturing sector has evolved significantly over the past century. Initially, work boots were designed primarily for functionality, focusing on durability and basic protection. However, as industries have advanced, so too have the requirements for safety footwear. The introduction of safety standards in the mid-20th century marked a pivotal change, leading to the development of specialized features such as steel toe caps, slip-resistant soles, and waterproof materials.
In recent decades, the emphasis has shifted towards comfort and ergonomic design, with manufacturers investing in innovative materials and technologies to enhance user experience. This evolution is particularly relevant for B2B buyers, as the demand for high-performance work boots has grown alongside the recognition of the importance of employee well-being in workplace productivity. As a result, today’s work boots not only meet safety regulations but also cater to the diverse needs of modern workers, reflecting the ongoing transformation within the industry.
Frequently Asked Questions (FAQs) for B2B Buyers of work boot manufacturer
-
How do I choose the right work boot manufacturer for my business needs?
Selecting the right work boot manufacturer involves evaluating their experience in the industry, product quality, and compliance with international safety standards. Assess their ability to meet your specific requirements, such as material preferences and design specifications. It’s also crucial to review their past client testimonials and case studies. Schedule a factory visit or request samples to ensure their production capabilities align with your expectations. Engaging in discussions about their customization options can also help you gauge their flexibility and responsiveness. -
What is the minimum order quantity (MOQ) for work boots from manufacturers?
The minimum order quantity (MOQ) can vary significantly among work boot manufacturers, often ranging from 100 to 1,000 pairs. Manufacturers may have different MOQs depending on the type of boot, materials used, and production processes. For bulk orders, negotiating the MOQ is often possible, especially if you can commit to a long-term partnership. Always clarify the MOQ upfront to avoid unexpected costs and ensure it aligns with your budget and inventory management strategies. -
What are the typical payment terms offered by work boot manufacturers?
Payment terms can vary widely, but common arrangements include a deposit of 30-50% upfront, with the balance due upon completion of production or before shipment. Some manufacturers may offer flexible terms based on your credit history or relationship with them. Ensure to discuss and agree upon payment methods, such as bank transfers or letters of credit, which are often preferred for international transactions. Understanding these terms upfront can help you manage cash flow effectively and avoid potential disputes. -
How can I ensure quality assurance when sourcing work boots internationally?
To ensure quality assurance when sourcing work boots, request certifications that demonstrate compliance with international safety standards, such as ISO or ASTM. Implement a quality control process that includes pre-production samples and in-line inspections during manufacturing. Consider hiring third-party inspection services to conduct quality checks before shipment. Additionally, maintaining open communication with the manufacturer throughout the production process can help address any concerns promptly. -
What customization options are available for work boots from manufacturers?
Many work boot manufacturers offer a range of customization options, including materials, colors, sizes, and specific features such as waterproofing or slip resistance. Some manufacturers may also provide branding options like logos and custom packaging. Discuss your requirements in detail during initial conversations to understand the extent of customization available and any associated costs. This can help ensure that the final product meets your branding and functional needs. -
What logistics considerations should I keep in mind when importing work boots?
When importing work boots, consider shipping methods (air vs. sea), lead times, and customs regulations in your destination country. Calculate total landed costs, including duties, taxes, and freight charges, to determine the overall expense. Partnering with a reliable freight forwarder can streamline the shipping process and help navigate customs clearance. Additionally, keeping track of shipment timelines is crucial to align with your inventory needs and avoid stockouts. -
What are the common challenges faced when sourcing work boots internationally?
Common challenges when sourcing work boots internationally include language barriers, cultural differences, and varying quality standards. Time zone differences can also complicate communication and lead to delays. To mitigate these challenges, consider working with experienced intermediaries or agents familiar with both local and international markets. Establishing clear communication channels and using technology for project management can also facilitate smoother interactions with manufacturers. -
How do I assess the reliability of a work boot manufacturer?
Assessing the reliability of a work boot manufacturer involves researching their reputation, certifications, and production capabilities. Look for reviews from other B2B buyers and check for any red flags, such as a lack of transparency or delayed responses. Request references from their previous clients and verify their track record in meeting deadlines and quality standards. A reliable manufacturer should also be willing to provide detailed information about their production processes and policies, including how they handle issues or defects.
Important Disclaimer & Terms of Use
⚠️ Important Disclaimer
The information provided in this guide, including content regarding manufacturers, technical specifications, and market analysis, is for informational and educational purposes only. It does not constitute professional procurement advice, financial advice, or legal advice.
While we have made every effort to ensure the accuracy and timeliness of the information, we are not responsible for any errors, omissions, or outdated information. Market conditions, company details, and technical standards are subject to change.
B2B buyers must conduct their own independent and thorough due diligence before making any purchasing decisions. This includes contacting suppliers directly, verifying certifications, requesting samples, and seeking professional consultation. The risk of relying on any information in this guide is borne solely by the reader.
Strategic Sourcing Conclusion and Outlook for work boot manufacturer
In conclusion, the strategic sourcing of work boots is pivotal for international B2B buyers, particularly in emerging markets across Africa, South America, the Middle East, and Europe. By leveraging effective sourcing strategies, businesses can enhance their supply chain resilience, reduce costs, and ensure compliance with regional safety standards. It is essential to engage with reputable manufacturers who prioritize quality, sustainability, and innovation in their product offerings.
What Are the Key Benefits of Strategic Sourcing for Work Boots?
Investing in strategic sourcing not only facilitates better pricing through competitive analysis but also fosters long-term relationships with suppliers. This can lead to improved service levels and the ability to adapt to changing market demands. As you consider your procurement strategies, focus on suppliers that offer customization options and can meet specific industry requirements, ensuring that the boots not only protect workers but also align with your brand values.
How Can International Buyers Prepare for the Future of Work Boot Procurement?
Looking ahead, international B2B buyers should remain vigilant about trends impacting the work boot industry, including technological advancements in materials and manufacturing processes. By staying informed and proactive, you can secure a competitive edge in the marketplace. Engage with suppliers who are committed to innovation and sustainability, and do not hesitate to explore partnerships that can enhance your operational efficiency. Embrace the future of work boot sourcing, and make informed decisions that will benefit your workforce and your bottom line.