Unlock Savings: The Ultimate Forester Manufacturer Guide (2025)
Introduction: Navigating the Global Market for forester manufacturer
In today’s competitive landscape, sourcing reliable forester manufacturers poses a significant challenge for international B2B buyers, particularly in regions such as Africa, South America, the Middle East, and Europe. With the increasing demand for sustainable forestry practices and high-quality timber products, understanding the nuances of the global market is essential. This guide serves as a comprehensive resource, detailing the various types of forester manufacturers, their applications, and the critical factors to consider when selecting the right supplier.
Navigating through the complexities of supplier vetting, cost considerations, and quality assurance can be daunting. However, this guide empowers B2B buyers with actionable insights and strategic approaches to enhance their purchasing decisions. From evaluating potential partners to understanding the implications of local regulations and international trade agreements, we cover every aspect necessary for informed decision-making.
In addition to offering an overview of the forester manufacturing landscape, this guide provides practical tips on how to assess product quality, negotiate favorable terms, and establish long-term relationships with suppliers. By leveraging the information presented, businesses can not only optimize their procurement processes but also ensure that they align with their sustainability goals and operational needs. Whether you’re a seasoned buyer or new to the forestry sector, this guide is designed to equip you with the knowledge and tools necessary to thrive in the global market for forester manufacturing.
Understanding forester manufacturer Types and Variations
Type Name | Key Distinguishing Features | Primary B2B Applications | Brief Pros & Cons for Buyers |
---|---|---|---|
Timber Harvesting Equipment | Specializes in machinery for cutting and processing timber. | Forestry operations, logging companies | Pros: High efficiency, specialized tools. Cons: High initial investment. |
Reforestation Technology | Focuses on equipment and systems for planting and nurturing trees. | Environmental NGOs, government projects | Pros: Supports sustainability, long-term investment. Cons: Slower ROI, requires maintenance. |
Wood Processing Machinery | Offers equipment for converting raw timber into finished products. | Furniture manufacturers, construction firms | Pros: Versatile applications, high demand for processed wood. Cons: Requires skilled operators, maintenance costs. |
Forest Management Software | Provides software solutions for planning and managing forest resources. | Forestry consultants, land management firms | Pros: Data-driven decisions, improved efficiency. Cons: Requires training, ongoing software costs. |
Biomass Energy Solutions | Focuses on converting wood waste into energy or biofuel. | Energy companies, manufacturing industries | Pros: Renewable energy source, reduces waste. Cons: Technology can be complex, regulatory challenges. |
What Are the Key Characteristics of Timber Harvesting Equipment?
Timber harvesting equipment is essential for businesses engaged in logging and forestry. This category includes feller bunchers, skidders, and harvesters designed to maximize efficiency in cutting and transporting timber. Buyers should consider factors such as machinery capacity, fuel efficiency, and maintenance support. Given the initial investment, it’s crucial to assess the equipment’s return on investment (ROI) based on projected timber yields.
How Does Reforestation Technology Contribute to Sustainable Practices?
Reforestation technology encompasses a range of tools, including seeders and drones for planting and monitoring forests. This equipment is critical for organizations focused on environmental conservation and sustainability. When purchasing, B2B buyers should evaluate the technology’s adaptability to local ecosystems, ease of use, and long-term operational costs. While these solutions promote ecological balance, they typically have a slower ROI due to the time required for trees to mature.
Why Is Wood Processing Machinery Vital for Manufacturing?
Wood processing machinery is pivotal for converting raw timber into various products like furniture, flooring, and construction materials. This category includes saws, planers, and sanders that cater to diverse manufacturing needs. Buyers must consider production capacity, versatility, and the availability of skilled labor for operation. Although these machines can be costly, their ability to produce high-quality finished goods often justifies the investment.
What Are the Benefits of Using Forest Management Software?
Forest management software provides tools for tracking and managing forest resources efficiently. These solutions help organizations optimize timber yields, monitor forest health, and plan sustainable practices. B2B buyers should assess software features, user-friendliness, and integration capabilities with existing systems. While there are ongoing costs associated with software licenses and training, the data-driven insights gained can significantly enhance decision-making processes.
How Do Biomass Energy Solutions Support Renewable Energy Initiatives?
Biomass energy solutions convert wood waste into energy or biofuel, making them a valuable resource for energy companies and industries looking to reduce waste. This technology can range from small-scale systems to large biomass plants. When evaluating these solutions, buyers should consider the technology’s scalability, regulatory compliance, and potential partnerships with local governments. Although they can involve complex setups, the long-term benefits of renewable energy and waste reduction are substantial.
Related Video: Variations In Construction Projects Explained
Key Industrial Applications of forester manufacturer
Industry/Sector | Specific Application of forester manufacturer | Value/Benefit for the Business | Key Sourcing Considerations for this Application |
---|---|---|---|
Timber and Lumber | High-capacity timber processing machinery | Increased efficiency and reduced waste | Compliance with local regulations, machinery durability |
Furniture Manufacturing | Custom wood components production | Enhanced product quality and customization | Supplier reliability, material sourcing transparency |
Construction | Structural timber solutions | Improved sustainability and cost-effectiveness | Certifications, delivery timelines, after-sales support |
Agriculture | Agroforestry equipment | Optimized land use and resource management | Availability of parts, adaptability to local conditions |
Energy | Biomass production systems | Renewable energy generation and waste reduction | Technology compatibility, training for local workforce |
How is Forester Manufacturing Applied in the Timber and Lumber Industry?
In the timber and lumber industry, forester manufacturers provide high-capacity timber processing machinery designed to maximize output and minimize waste. These machines can handle large volumes of logs efficiently, solving common issues such as slow processing times and high operational costs. For international buyers, particularly in regions like Africa and South America, it is crucial to consider compliance with local regulations and the durability of machinery in varied climates.
What Role Does Forester Manufacturing Play in Furniture Manufacturing?
Forester manufacturers supply custom wood components that enhance the quality and customization of furniture products. This application allows furniture manufacturers to differentiate their offerings and meet specific client needs. Buyers from Europe and the Middle East should prioritize supplier reliability and the transparency of material sourcing to ensure ethical practices and consistent quality in their supply chain.
How Can Forester Manufacturing Benefit the Construction Sector?
In construction, forester manufacturers provide structural timber solutions that contribute to more sustainable building practices. These solutions not only reduce material costs but also support eco-friendly initiatives, addressing the growing demand for sustainable construction methods. For buyers in Africa and Europe, key considerations include obtaining certifications for sustainability and ensuring timely delivery to meet project deadlines.
What Advantages Does Forester Manufacturing Offer for Agriculture?
Forester manufacturing plays a significant role in agriculture through the provision of agroforestry equipment that optimizes land use and resource management. This equipment aids in the integration of trees into agricultural systems, enhancing biodiversity and soil health. International buyers should consider the availability of replacement parts and the adaptability of equipment to local environmental conditions when sourcing these solutions.
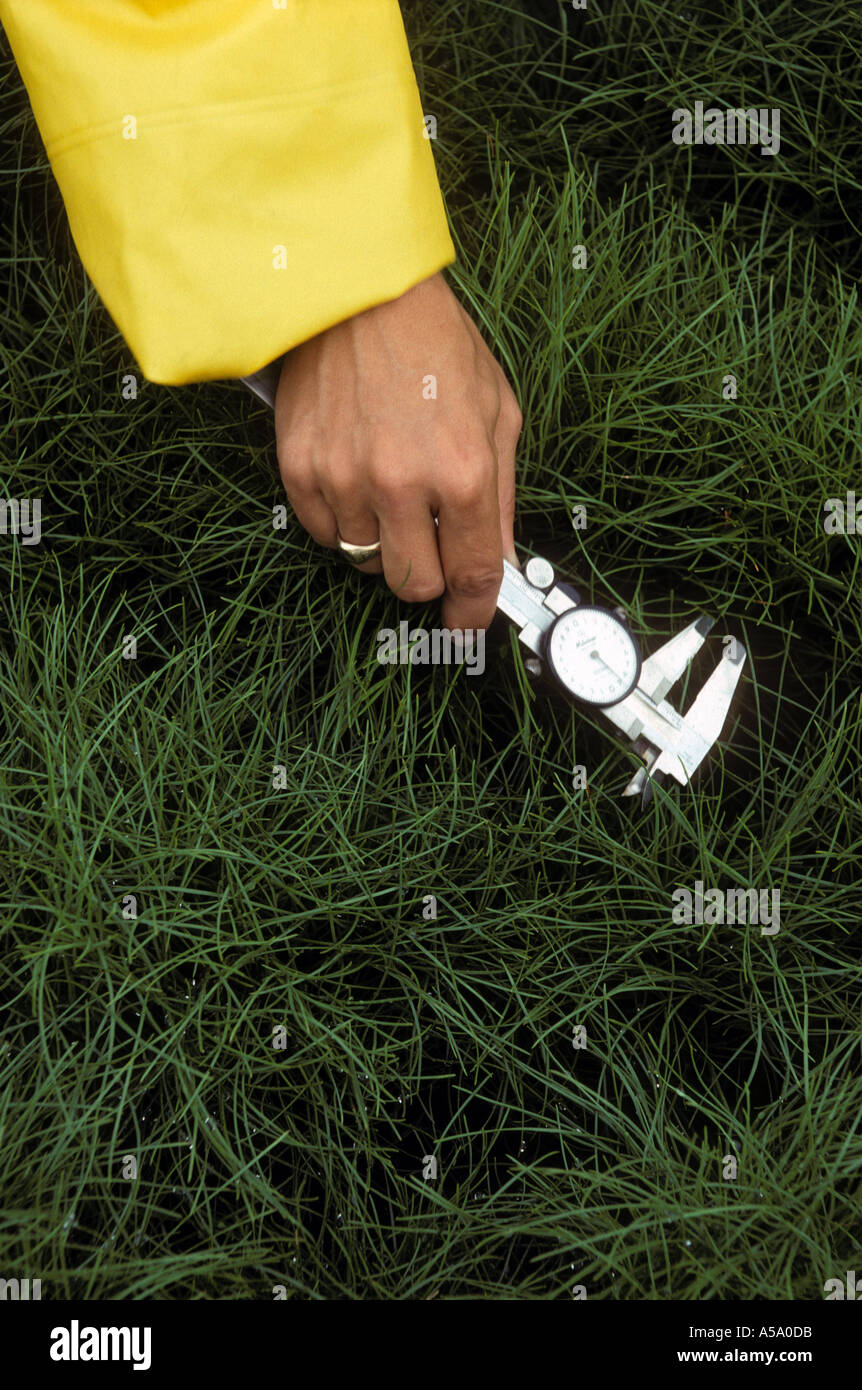
A stock image related to forester manufacturer.
How is Forester Manufacturing Used in the Energy Sector?
In the energy sector, forester manufacturers facilitate biomass production systems that convert organic materials into renewable energy. This application helps businesses transition to greener energy sources while simultaneously reducing waste. Buyers from regions like South America and Europe should evaluate the compatibility of technology with local energy systems and ensure that adequate training is available for the local workforce to operate the equipment effectively.
Related Video: Types Of Flowmeters And Their Industrial Applications.
3 Common User Pain Points for ‘forester manufacturer’ & Their Solutions
Scenario 1: Inconsistent Quality of Timber Products
The Problem: One of the most pressing challenges that B2B buyers face when sourcing from forester manufacturers is the inconsistency in the quality of timber products. This issue often arises from variations in raw materials, manufacturing processes, or even differences in supplier standards. For buyers in regions such as Africa or South America, where regulatory frameworks can be less stringent, this inconsistency can lead to significant operational setbacks. Projects can be delayed, costs can escalate due to rework or returns, and ultimately, client satisfaction can plummet.
The Solution: To mitigate this pain point, buyers should prioritize suppliers who adhere to internationally recognized quality standards, such as FSC (Forest Stewardship Council) certification. When engaging with manufacturers, it is crucial to request detailed product specifications and quality assurance processes. Establishing a clear communication channel for quality control can also be beneficial. Before finalizing contracts, consider conducting on-site visits or audits to verify the manufacturing processes and quality checks in place. Additionally, implementing a trial order can help assess quality before committing to larger quantities.
Scenario 2: Complicated Supply Chain Logistics
The Problem: For international B2B buyers, particularly those in the Middle East and Europe, navigating the complexities of supply chain logistics can be daunting. Issues such as shipping delays, customs clearance challenges, and fluctuating freight costs can create significant hurdles. These logistical problems can disrupt project timelines and increase overall costs, ultimately affecting profitability.
The Solution: To streamline supply chain logistics, buyers should develop a robust logistics strategy that includes a detailed timeline and clear communication with the forester manufacturer. Engaging with a logistics partner experienced in handling forestry products can provide insights into optimizing shipping routes and managing customs documentation. Additionally, consider establishing a buffer stock to mitigate the impact of potential delays. Leveraging technology, such as supply chain management software, can also improve visibility into inventory levels and shipping statuses, allowing for proactive adjustments to be made in real time.
Scenario 3: Limited Customization Options for Timber Products
The Problem: Many B2B buyers encounter limitations when it comes to customizing timber products to meet specific project requirements. This is particularly relevant for buyers in diverse markets like Europe and Africa, where local preferences and building regulations can vary significantly. Standardized products may not align with local architectural styles or construction methods, leading to missed opportunities for differentiation and market competitiveness.
The Solution: To address this issue, buyers should engage with forester manufacturers that offer flexible customization options. During initial discussions, it’s essential to communicate specific project needs, including dimensions, finishes, and wood types. Requesting samples or prototypes can also help assess whether the manufacturer can meet customization requirements. Furthermore, building a strong partnership with manufacturers can facilitate more tailored solutions. Regularly sharing feedback on product performance and market trends can encourage manufacturers to innovate and expand their customization capabilities, ultimately benefiting both parties.
Strategic Material Selection Guide for forester manufacturer
When selecting materials for forester manufacturing, international B2B buyers need to consider various factors that influence product performance, cost, and compliance with regional standards. Here, we analyze four common materials used in this industry: aluminum, steel, composite materials, and wood. Each material has unique properties, advantages, and limitations that can significantly impact the end product’s suitability for specific applications.
What Are the Key Properties of Aluminum in Forester Manufacturing?
Aluminum is known for its lightweight nature and excellent corrosion resistance. It typically has a temperature rating up to 600°F (315°C) and can withstand moderate pressure levels. This makes aluminum an ideal choice for components that require both durability and ease of handling.
Pros & Cons: The primary advantage of aluminum is its high strength-to-weight ratio, which contributes to lower shipping costs and easier installation. However, aluminum can be more expensive than other materials, and its manufacturing complexity may increase production times.
Impact on Application: Aluminum is particularly suitable for outdoor applications where exposure to moisture and chemicals is a concern, such as in forestry equipment. Its compatibility with various media, including oils and fuels, enhances its versatility.
Considerations for International Buyers: Buyers in regions like Africa and South America should ensure compliance with local standards such as ASTM or ISO. Additionally, the availability of aluminum may vary by region, impacting lead times and costs.
How Does Steel Compare as a Material for Forester Manufacturers?
Steel is widely recognized for its strength and durability, making it a popular choice in forester manufacturing. It has high-temperature resistance, often exceeding 1,500°F (815°C), and is suitable for high-pressure applications.
Pros & Cons: Steel’s primary advantage lies in its robustness, which allows for the production of heavy-duty equipment. However, it is susceptible to corrosion unless treated or coated, which can add to manufacturing complexity and costs.
Impact on Application: Steel is ideal for applications requiring high structural integrity, such as frames and supports in forestry machinery. Its compatibility with various media, including water and oils, makes it a reliable choice.
Considerations for International Buyers: Buyers in Europe and the Middle East should be aware of compliance with standards such as DIN or JIS for steel products. Additionally, sourcing treated steel may be necessary to mitigate corrosion issues, especially in humid climates.
What Are the Benefits of Using Composite Materials in Forester Manufacturing?
Composite materials, which combine different substances to enhance performance, are increasingly popular in forester manufacturing. They offer excellent resistance to environmental factors and can withstand a wide range of temperatures.
Pros & Cons: The key advantage of composites is their lightweight nature and high strength, making them suitable for applications where weight is a concern. However, they can be more expensive to produce and may require specialized manufacturing processes.
Impact on Application: Composites are particularly effective in applications exposed to harsh environmental conditions, such as forestry equipment used in wet or corrosive environments. Their compatibility with various media enhances their usability.
Considerations for International Buyers: Buyers should consider the availability of composite materials in their region and ensure compliance with relevant standards. Additionally, understanding the specific manufacturing processes involved is crucial for effective sourcing.
Why Is Wood Still a Viable Option for Forester Manufacturers?
Wood remains a traditional yet effective material in forester manufacturing. It offers good thermal insulation and is readily available in many regions.
Pros & Cons: The primary advantage of wood is its sustainability and lower cost compared to metals and composites. However, wood is less durable and can be susceptible to rot and pests, requiring treatment or maintenance.
Impact on Application: Wood is suitable for applications such as temporary structures or components where aesthetics are important. Its compatibility with natural environments makes it a preferred choice in eco-friendly designs.
Considerations for International Buyers: Buyers must ensure compliance with local regulations regarding sustainable sourcing and treatment of wood. In regions like Africa and South America, the availability of specific wood types may influence material selection.
Summary Table of Material Selection for Forester Manufacturing
Material | Typical Use Case for Forester Manufacturer | Key Advantage | Key Disadvantage/Limitation | Relative Cost (Low/Med/High) |
---|---|---|---|---|
Aluminum | Lightweight components in forestry machinery | High strength-to-weight ratio | Higher cost and manufacturing complexity | Medium |
Steel | Structural frames and supports | Exceptional strength and durability | Corrosion susceptibility | Medium |
Composite | Equipment exposed to harsh environments | Lightweight and high strength | Higher production costs | High |
Wood | Temporary structures and aesthetic components | Sustainable and cost-effective | Less durable, requires treatment | Low |
This guide provides a comprehensive overview of material selection considerations for forester manufacturers, enabling international B2B buyers to make informed decisions tailored to their specific regional needs and applications.
In-depth Look: Manufacturing Processes and Quality Assurance for forester manufacturer
What Are the Main Stages of Manufacturing for Forester Equipment?
Manufacturing forester equipment involves several critical stages, each contributing to the overall quality and functionality of the final product. The primary stages include:
-
Material Preparation: This initial stage involves sourcing high-quality raw materials, such as steel, aluminum, and specialized composites. For international buyers, it’s crucial to understand the origin of these materials, as they can affect durability and performance. Suppliers should provide documentation on material certification and compliance with international standards.
-
Forming: During the forming stage, raw materials are shaped into the desired components using techniques such as stamping, forging, and extrusion. Advanced technologies like CNC (Computer Numerical Control) machining are often employed to ensure precision. B2B buyers should inquire about the machinery used and the technological capabilities of the manufacturer, as this directly impacts the quality of the components.
-
Assembly: The assembly process integrates various components into a finished product. This stage often involves both manual labor and automated processes to ensure consistency. Buyers should assess the assembly techniques used, including whether they adhere to lean manufacturing principles, which can enhance efficiency and reduce waste.
-
Finishing: The final stage includes surface treatments, painting, and coating to enhance corrosion resistance and aesthetic appeal. Techniques such as powder coating and anodizing are commonly used. Buyers should verify that the finishing processes comply with environmental regulations and standards relevant to their regions.
What Quality Assurance Practices Should B2B Buyers Expect?
Quality assurance is a fundamental aspect of the manufacturing process, ensuring that products meet specific standards and customer expectations. Here are key practices that buyers should look for:
How Does ISO 9001 Influence Quality Assurance in Manufacturing?
ISO 9001 is an internationally recognized standard that outlines criteria for a quality management system (QMS). Manufacturers adhering to ISO 9001 demonstrate a commitment to quality and customer satisfaction. B2B buyers should request certificates of compliance to ISO 9001 from potential suppliers, as this indicates robust processes for continuous improvement and risk management.
What Industry-Specific Certifications Are Important for Forester Equipment?
In addition to ISO 9001, industry-specific certifications are crucial for ensuring product safety and performance. For example:
- CE Marking: Required for products sold in the European Economic Area, CE marking indicates conformity with health, safety, and environmental protection standards.
- API Certification: Relevant for equipment used in the oil and gas sector, API (American Petroleum Institute) certification ensures that products meet industry standards for safety and reliability.
Understanding these certifications helps buyers gauge the credibility and market readiness of the manufacturer.
What Are the Key Quality Control Checkpoints in Manufacturing?
Quality control (QC) is integral to the manufacturing process, typically involving several checkpoints:
-
Incoming Quality Control (IQC): This initial inspection stage ensures that raw materials meet specified standards before production begins. Buyers should inquire about the criteria used for incoming inspections and any associated documentation.
-
In-Process Quality Control (IPQC): During manufacturing, IPQC involves regular inspections at various stages to identify and rectify defects early. This proactive approach can prevent costly rework and delays, which is especially beneficial for B2B buyers relying on timely deliveries.
-
Final Quality Control (FQC): This final inspection ensures that the finished product meets all specifications before shipping. Buyers should request detailed FQC reports, including any testing results that validate the product’s performance and safety.
Which Testing Methods Are Commonly Used in Quality Assurance?
Testing methods are crucial for verifying the quality and performance of forester equipment. Common testing techniques include:
- Mechanical Testing: Assessing properties such as tensile strength, hardness, and fatigue resistance to ensure durability.
- Dimensional Inspection: Utilizing tools like calipers and gauges to ensure that components meet specified tolerances.
- Functional Testing: Verifying that the equipment operates correctly under real-world conditions.
B2B buyers should ask manufacturers about their testing protocols and whether they employ third-party testing services to further validate the quality of their products.
How Can B2B Buyers Verify Supplier Quality Control Practices?
To ensure that a supplier’s quality control practices meet their standards, B2B buyers should consider the following strategies:
- Supplier Audits: Conducting regular audits of suppliers can provide insights into their manufacturing processes and QC practices. This is particularly important for buyers from regions with different regulatory environments.
- Requesting Quality Reports: Buyers should ask for comprehensive QC reports, including results from IQC, IPQC, and FQC stages. Analyzing these reports can help buyers assess the supplier’s commitment to quality.
- Third-Party Inspections: Engaging third-party inspection agencies can offer an unbiased evaluation of the supplier’s quality assurance practices. This is especially beneficial for international transactions, where buyers may face challenges in verifying local compliance.
What Are the Nuances of Quality Control Certifications for International Buyers?
International B2B buyers must navigate various certification requirements that can differ significantly from one region to another. For example, while CE marking is essential for the European market, buyers in Africa or South America may prioritize local standards that ensure compliance with regional regulations.
Understanding these nuances can help buyers make informed decisions when selecting suppliers. It’s essential to engage with manufacturers who are knowledgeable about the specific certifications required in the buyer’s target market and can provide the necessary documentation.
Conclusion: How to Choose a Reliable Forester Manufacturer?
When selecting a forester manufacturer, B2B buyers should prioritize those with robust manufacturing processes and comprehensive quality assurance practices. Verifying certifications, understanding testing methods, and assessing QC checkpoints are vital steps in ensuring that the equipment meets both performance and safety standards. By following these insights, international buyers can establish strong partnerships with manufacturers, ensuring reliable supply chains and high-quality products tailored to their specific needs.
Practical Sourcing Guide: A Step-by-Step Checklist for ‘forester manufacturer’
In the competitive landscape of sourcing for a forester manufacturer, international B2B buyers must navigate numerous considerations to ensure successful procurement. This step-by-step checklist serves as a practical guide to streamline your sourcing process, ensuring that you select the right partners to meet your operational needs.
Step 1: Define Your Technical Specifications
Clearly outline your technical requirements before initiating contact with potential suppliers. This includes the type of forestry equipment or services you need, specifications regarding materials, dimensions, and performance standards. A well-defined specification helps in communicating your needs effectively and aids suppliers in providing accurate quotations.
Step 2: Conduct Market Research
Understanding the market landscape is essential for making informed sourcing decisions. Analyze trends in the forestry manufacturing sector, identify leading suppliers, and compare pricing structures. Utilize industry reports and trade publications to gain insights into supplier performance, market demand, and emerging technologies that can enhance your operational efficiency.
Step 3: Verify Supplier Certifications
Before proceeding with any supplier, ensure they possess the necessary certifications and compliance with international standards. Look for certifications such as ISO 9001 for quality management and ISO 14001 for environmental management. These certifications not only validate the supplier’s commitment to quality but also reflect their adherence to sustainable practices, which is increasingly important in global sourcing.
Step 4: Evaluate Potential Suppliers
Before committing, it’s crucial to vet suppliers thoroughly. Request company profiles, case studies, and references from buyers in a similar industry or region. Consider visiting the supplier’s facility if possible, or conduct virtual audits to assess their manufacturing capabilities and quality control processes. This step mitigates risks associated with poor-quality products or unreliable service.
Step 5: Request and Compare Quotations
Once you have shortlisted potential suppliers, request detailed quotations that outline pricing, payment terms, delivery schedules, and warranty information. Be sure to compare not just the prices but also the value offered, including after-sales service and support. Look for suppliers who can demonstrate flexibility and willingness to negotiate terms to better suit your needs.
Step 6: Assess Logistics and Supply Chain Capabilities
Evaluate the logistics and supply chain capabilities of your shortlisted suppliers. Consider their shipping methods, lead times, and ability to handle customs and import regulations specific to your region, whether in Africa, South America, the Middle East, or Europe. A supplier with a robust logistics framework can help minimize delays and ensure timely delivery of products.
Step 7: Establish Clear Communication Channels
Effective communication is key to successful partnerships. Ensure that there are clear channels for ongoing dialogue with your chosen supplier. Establish regular updates regarding order status, production timelines, and any potential issues that may arise. Good communication fosters a strong relationship and can lead to better problem resolution and collaboration in the future.
By following this checklist, international B2B buyers can enhance their sourcing strategy for forester manufacturers, ensuring that they select reliable partners who can meet their specific needs while fostering long-term business relationships.
Comprehensive Cost and Pricing Analysis for forester manufacturer Sourcing
What Are the Key Cost Components in Forester Manufacturing?
Understanding the cost structure of forester manufacturers is essential for international B2B buyers. The primary cost components include:
-
Materials: The choice of raw materials—such as wood types, adhesives, and finishes—significantly influences the overall cost. Sustainable sourcing can enhance brand value but may come at a premium.
-
Labor: Labor costs vary by region and are impacted by local wage rates, skill levels, and labor laws. Countries in Africa and South America may offer competitive labor costs, while Europe might have higher wage expectations.
-
Manufacturing Overhead: This includes costs associated with utilities, rent, equipment maintenance, and administrative expenses. Efficient manufacturing processes can help minimize these overheads.
-
Tooling: Investment in tooling—molds, dies, and production fixtures—can be substantial. Buyers should consider the amortization of these costs over production runs to assess their impact on unit pricing.
-
Quality Control (QC): Ensuring product quality can incur additional costs. Manufacturers may implement rigorous QC processes that affect pricing, especially for products requiring certifications.
-
Logistics: Transportation costs are crucial in determining the final price. Factors such as shipping distances, mode of transport, and the chosen Incoterms can significantly influence logistics expenses.
-
Margin: The manufacturer’s profit margin varies based on market conditions and competition. Understanding the margin expectations can aid in negotiations.
How Do Price Influencers Affect Forester Manufacturing Sourcing?
Several factors influence pricing in the forester manufacturing sector:
-
Volume and Minimum Order Quantity (MOQ): Higher order volumes typically lead to lower per-unit costs. Buyers should negotiate MOQs that align with their demand forecasts to maximize cost-efficiency.
-
Specifications and Customization: Customized products often come with higher costs due to additional design and production requirements. Buyers should clearly define their specifications to avoid unexpected price increases.
-
Materials and Quality Certifications: The choice of materials and the presence of certifications (e.g., FSC, PEFC) can significantly affect pricing. Buyers looking for eco-friendly products should be prepared to pay a premium.
-
Supplier Factors: The supplier’s reputation, experience, and location can impact pricing. Established suppliers with a track record of quality may command higher prices, but they often deliver better reliability.
-
Incoterms: Understanding Incoterms is vital for international transactions. They define the responsibilities of buyers and sellers concerning shipping, insurance, and tariffs, which can affect the total landed cost.
What Buyer Tips Can Enhance Cost-Efficiency in Sourcing?
To navigate the complexities of cost and pricing in forester manufacturing, B2B buyers should consider the following tips:
-
Negotiate Wisely: Engage in open discussions with suppliers about pricing. Understanding their cost structure can provide leverage in negotiations.
-
Evaluate Total Cost of Ownership (TCO): Beyond the purchase price, consider maintenance, transportation, and potential waste costs. A lower initial price might lead to higher TCO if the product requires frequent replacements or extensive shipping.
-
Be Aware of Pricing Nuances: Different regions may have varying pricing strategies due to local market conditions, tariffs, and economic factors. Buyers from Africa, South America, the Middle East, and Europe should conduct thorough market research.
-
Consider Long-Term Relationships: Building strong partnerships with suppliers can lead to better pricing agreements and priority service. Loyalty can be rewarded with volume discounts or improved payment terms.
-
Stay Informed About Market Trends: Keeping abreast of market fluctuations, material availability, and economic conditions can provide insights into when to purchase or negotiate better terms.
Important Disclaimer on Pricing Information
It is essential to note that pricing information in the forester manufacturing sector can vary significantly based on numerous factors. Prices mentioned are indicative and can fluctuate due to market conditions, supplier policies, and geopolitical influences. Always conduct thorough due diligence and engage with multiple suppliers to obtain accurate quotations tailored to your specific needs.
Alternatives Analysis: Comparing forester manufacturer With Other Solutions
In the competitive landscape of forestry manufacturing, B2B buyers must evaluate various solutions to identify the best fit for their operational needs. Understanding the alternatives available is crucial for making informed decisions that align with strategic business goals, particularly for international buyers from diverse regions such as Africa, South America, the Middle East, and Europe.
Comparison Table of ‘Forester Manufacturer’ and Alternatives
Comparison Aspect | Forester Manufacturer | Timber Harvesting Equipment | Forest Management Software |
---|---|---|---|
Performance | High durability and efficiency in production | Excellent for large-scale operations | Provides data-driven insights for management |
Cost | Moderate initial investment; long-term savings | High upfront costs; variable operational costs | Subscription or licensing fees can add up |
Ease of Implementation | Requires training; integration with existing systems | Complex setup; may need specialized operators | User-friendly interfaces; quick to deploy |
Maintenance | Low maintenance; periodic checks needed | High maintenance; regular servicing required | Minimal; updates are generally automated |
Best Use Case | Ideal for custom manufacturing needs | Best for large timber operations | Effective for strategic planning and resource allocation |
What are the Pros and Cons of Timber Harvesting Equipment?
Timber harvesting equipment, such as feller bunchers and skidders, is designed for efficiency in large-scale timber operations. Pros include the ability to handle heavy loads and operate in challenging terrains, which can significantly speed up logging processes. However, the cons are notable: the initial investment can be prohibitively high, and ongoing maintenance and operational costs can add financial strain, particularly for smaller businesses or those in developing regions.
How Does Forest Management Software Enhance Forestry Operations?
Forest management software provides an innovative approach to managing forestry resources. It leverages data analytics to offer insights into forest health, growth rates, and resource allocation. The pros of using such software include improved decision-making based on real-time data and the ability to plan long-term strategies effectively. However, the cons can include recurring subscription costs and the need for staff training to maximize the software’s capabilities.
Conclusion: How Can B2B Buyers Select the Right Solution for Their Needs?
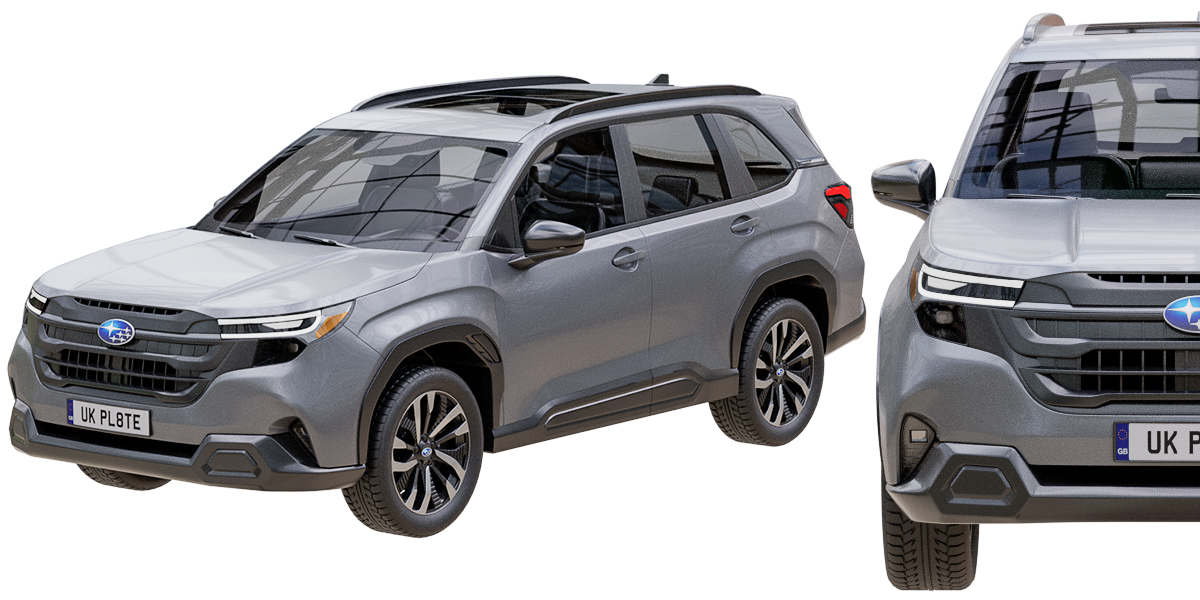
A stock image related to forester manufacturer.
When choosing between a forester manufacturer and alternative solutions, B2B buyers should consider their specific operational requirements and financial capabilities. For those focused on durable manufacturing with lower maintenance needs, a forester manufacturer may be the best fit. Conversely, businesses engaged in large-scale timber operations might find timber harvesting equipment more beneficial despite its higher initial costs. Lastly, organizations looking for data-driven management will benefit from forest management software, provided they are prepared for the associated costs and training. By thoroughly evaluating these alternatives, buyers can make informed decisions that align with their strategic objectives and operational realities.
Essential Technical Properties and Trade Terminology for forester manufacturer
What Are the Key Technical Properties for Forester Manufacturers?
When sourcing materials and products from forester manufacturers, understanding the technical properties is essential for making informed purchasing decisions. Here are some critical specifications that B2B buyers should consider:
1. Material Grade
Material grade refers to the quality and type of materials used in manufacturing. In the forestry sector, this could involve various wood types, such as hardwood or softwood, which differ in strength, durability, and application. For B2B buyers, knowing the material grade helps ensure that the products meet specific performance requirements for their intended use, such as construction or furniture making.
2. Tolerance
Tolerance indicates the allowable deviation from specified dimensions in manufacturing processes. For example, in timber products, a tolerance of ±0.5mm on thickness can significantly impact the fit and finish in construction applications. Understanding tolerance is crucial for buyers to ensure compatibility and quality in their projects, reducing the likelihood of costly rework.
3. Moisture Content
Moisture content is a critical property that affects the stability and durability of wood products. Typically expressed as a percentage, the ideal moisture content varies depending on the end-use, with lower moisture levels preferred for indoor applications. For international B2B buyers, knowing the moisture content can influence shipping decisions and storage conditions, preventing issues like warping or mold.
4. Density
Density is an essential property that indicates the weight of the material per unit volume. It affects the strength, durability, and thermal properties of wood products. B2B buyers should be aware of density specifications to select materials that will perform well under specific conditions, such as load-bearing applications or insulation needs.
5. Surface Finish
Surface finish refers to the treatment of the wood’s surface, which can affect aesthetics, durability, and maintenance. Common finishes include varnishes, stains, and sealants. Understanding the surface finish is vital for buyers looking for products that align with their design preferences and maintenance capabilities.
What Common Trade Terms Should B2B Buyers Know in Forestry Manufacturing?
Familiarity with industry jargon can streamline communication and ensure clarity in transactions. Here are several essential trade terms for B2B buyers in the forestry sector:
1. OEM (Original Equipment Manufacturer)
OEM refers to a company that produces parts or equipment that may be marketed by another manufacturer. In the forestry industry, an OEM might produce specialized machinery or components used in processing timber. B2B buyers should consider OEMs for high-quality, tailored solutions that meet their specific operational needs.
2. MOQ (Minimum Order Quantity)
MOQ is the smallest quantity of a product that a supplier is willing to sell. Understanding MOQ is crucial for B2B buyers to manage inventory levels and production schedules. It’s important to negotiate favorable terms that align with the buyer’s needs while also ensuring the supplier’s production efficiency.
3. RFQ (Request for Quotation)
An RFQ is a formal document sent to suppliers requesting pricing and terms for specific products or services. For international buyers, issuing an RFQ can help in comparing offers and ensuring that they receive competitive pricing and favorable terms.
4. Incoterms (International Commercial Terms)
Incoterms are a set of predefined commercial terms that define the responsibilities of buyers and sellers in international transactions. Understanding Incoterms is vital for B2B buyers to clarify shipping costs, risk, and delivery obligations, thus preventing misunderstandings during transactions.
5. Lead Time
Lead time is the amount of time it takes from placing an order to receiving the products. For B2B buyers, understanding lead times is essential for effective project planning and inventory management. Buyers should communicate their timeline requirements clearly to ensure timely delivery.
By grasping these essential technical properties and trade terms, international B2B buyers can enhance their purchasing strategies, ensuring they select the right products for their needs while facilitating smoother transactions with suppliers.
Navigating Market Dynamics and Sourcing Trends in the forester manufacturer Sector
What Are the Key Market Dynamics and Trends in the Forester Manufacturer Sector?
The forester manufacturing sector is undergoing significant transformation driven by global market dynamics, technological advancements, and changing consumer demands. International B2B buyers, especially those from Africa, South America, the Middle East, and Europe, should be aware of several key trends.
Firstly, the demand for sustainable and responsibly sourced timber is on the rise. This shift is largely influenced by increasing awareness of environmental issues and regulatory frameworks aimed at promoting sustainable forestry practices. Countries in Europe are particularly stringent about compliance with regulations such as the EU Timber Regulation (EUTR), which impacts sourcing decisions.
Secondly, the integration of technology in the forester manufacturing sector is becoming prevalent. Innovations like IoT (Internet of Things), AI (Artificial Intelligence), and blockchain are enhancing supply chain transparency and efficiency. These technologies enable manufacturers to track the origin of materials, monitor production processes, and ensure ethical practices, which is crucial for international buyers concerned about sustainability.
Lastly, geopolitical factors and trade policies are shaping sourcing strategies. For instance, trade agreements between regions can facilitate better access to markets and resources, while tariffs and trade disputes may pose challenges. B2B buyers must stay informed about these developments to make strategic sourcing decisions that align with their business goals.
How Can Sustainability and Ethical Sourcing Impact Your Business?
Sustainability and ethical sourcing are no longer optional for businesses in the forester manufacturing sector; they are essential for long-term success. The environmental impact of timber production is significant, contributing to deforestation, loss of biodiversity, and carbon emissions. Thus, adopting sustainable practices can mitigate these effects and improve a company’s public image.
For international B2B buyers, partnering with manufacturers who prioritize sustainability can lead to a competitive advantage. Buyers should seek suppliers with certifications such as FSC (Forest Stewardship Council) and PEFC (Programme for the Endorsement of Forest Certification), which verify that products come from responsibly managed forests. Utilizing materials that are certified not only meets consumer demand for transparency but also aligns with global sustainability goals.
Moreover, ethical supply chains are becoming a focal point in procurement strategies. Buyers must evaluate their suppliers’ practices to ensure they uphold human rights and labor standards. An investment in sustainable sourcing can also lead to innovation in product development, as manufacturers explore alternative materials and production methods that reduce environmental impact.
What Is the Historical Context of the Forester Manufacturing Sector?
The forester manufacturing sector has evolved significantly over the decades, reflecting changes in technology, consumer preferences, and environmental awareness. Initially, the industry focused primarily on meeting the demand for timber and wood products without much regard for sustainability. However, as the negative impacts of deforestation and environmental degradation became more apparent, the sector began to adopt more sustainable practices.
In the late 20th century, the establishment of certification programs such as FSC marked a pivotal shift towards responsible forestry. These initiatives aimed to promote sustainable management of forests and ensure that timber sourced was not contributing to ecological harm. Today, the forester manufacturing sector is at the forefront of integrating advanced technologies to enhance sustainability, efficiency, and ethical sourcing, making it a critical focus for international B2B buyers looking to navigate this complex market landscape.
Frequently Asked Questions (FAQs) for B2B Buyers of forester manufacturer
-
How do I choose the right forester manufacturer for my needs?
Selecting the right forester manufacturer involves assessing their experience, product range, and industry reputation. Research potential suppliers by reviewing their certifications, customer testimonials, and case studies. Additionally, consider their geographical location and logistics capabilities, as these can affect delivery times and costs. Establish direct communication to discuss your specific requirements, including customization options and the ability to meet your volume needs. -
What are the typical minimum order quantities (MOQ) for forester manufacturers?
Minimum order quantities can vary significantly between manufacturers, typically ranging from 100 to 1,000 units. Larger manufacturers may offer lower MOQs due to their production capacity, while smaller firms may require higher MOQs to cover costs. When negotiating, inquire if they provide flexibility for first-time orders or smaller test batches, especially if you are entering a new market or product line. -
What customization options are available from forester manufacturers?
Many forester manufacturers offer customization options to meet specific buyer needs, including design alterations, material selection, and packaging preferences. It’s essential to communicate your exact specifications early in the negotiation process. Ask for samples or prototypes to evaluate the quality and suitability of customized products before placing a large order. -
What payment terms should I expect when sourcing from a forester manufacturer?
Payment terms can vary widely, typically including options like advance payments, letters of credit, or staggered payments based on shipment stages. Many manufacturers may require a deposit upfront, often around 30% of the total order value, with the balance due upon delivery. Discussing payment terms upfront can help avoid misunderstandings and establish a transparent financial relationship. -
How can I ensure quality assurance when purchasing from a forester manufacturer?
To ensure quality assurance, request detailed product specifications and quality control processes from the manufacturer. It’s advisable to conduct factory audits, either personally or through third-party services, to evaluate their production standards. Additionally, negotiate for quality inspection reports or certifications to verify compliance with international standards, which is crucial for maintaining product integrity in your market. -
What are the logistics considerations when sourcing from a forester manufacturer?
Logistics considerations include shipping methods, delivery timelines, and import/export regulations. Discuss the manufacturer’s shipping capabilities and whether they handle logistics or if you need to arrange your own. Additionally, consider the customs procedures in your country and any tariffs or duties applicable to the imported goods. Collaborating with a freight forwarder can simplify the process and ensure timely delivery. -
How do I vet a forester manufacturer to avoid scams?
To avoid scams, conduct thorough research on potential manufacturers. Look for verified business licenses and certifications, and check references from other clients. Using platforms like Alibaba or trade associations can provide insights into their credibility. Additionally, consider requesting a factory visit or third-party verification to assess their operations firsthand, ensuring you are partnering with a legitimate supplier. -
What should I know about international trade regulations when sourcing from a forester manufacturer?
Understanding international trade regulations is crucial for a smooth purchasing process. Familiarize yourself with the import regulations of your country, including tariffs, quotas, and compliance standards. It’s also important to understand the regulations concerning wood products, which may be subject to additional scrutiny to prevent illegal logging. Consulting with a trade expert or legal advisor can help navigate these complexities and ensure compliance with all necessary regulations.
Important Disclaimer & Terms of Use
⚠️ Important Disclaimer
The information provided in this guide, including content regarding manufacturers, technical specifications, and market analysis, is for informational and educational purposes only. It does not constitute professional procurement advice, financial advice, or legal advice.
While we have made every effort to ensure the accuracy and timeliness of the information, we are not responsible for any errors, omissions, or outdated information. Market conditions, company details, and technical standards are subject to change.
B2B buyers must conduct their own independent and thorough due diligence before making any purchasing decisions. This includes contacting suppliers directly, verifying certifications, requesting samples, and seeking professional consultation. The risk of relying on any information in this guide is borne solely by the reader.
Strategic Sourcing Conclusion and Outlook for forester manufacturer
In today’s competitive landscape, strategic sourcing for forester manufacturers is not just a procurement strategy; it’s a pathway to operational excellence and sustainable growth. International B2B buyers must prioritize relationships with suppliers who demonstrate reliability, quality, and adherence to ethical practices. By leveraging local resources and exploring new markets, companies can enhance their supply chain resilience and reduce costs.
What Are the Key Takeaways for B2B Buyers in the Forester Manufacturing Sector?
Understanding the unique challenges and opportunities within the forester industry is crucial. Buyers should focus on aligning their sourcing strategies with sustainability goals, as demand for eco-friendly products continues to rise globally. Additionally, utilizing data-driven insights to evaluate supplier performance can lead to more informed decision-making and foster long-term partnerships.
How Can International Buyers Prepare for Future Trends in Forester Manufacturing?
As the global market evolves, staying ahead of trends such as automation, digitalization, and changing regulatory landscapes will be essential. Buyers from Africa, South America, the Middle East, and Europe should actively engage in market research and networking to uncover emerging opportunities.
In conclusion, the future of forester manufacturing is bright for those who embrace strategic sourcing. By taking proactive steps now, international B2B buyers can position themselves as leaders in their markets. Engage with trusted suppliers, invest in innovative solutions, and commit to sustainable practices to ensure your success in this dynamic industry.