Unlock Savings: The Ultimate Guide to Beds Custom (2025)
Introduction: Navigating the Global Market for beds custom
Navigating the global market for custom beds can be a daunting task for international B2B buyers, especially when seeking the perfect balance between quality, cost, and supplier reliability. As you embark on sourcing custom beds tailored to meet specific needs, whether for hospitality, healthcare, or residential projects, understanding the complexities of this market is crucial. This guide provides comprehensive insights into various types of custom beds, their applications, and essential factors to consider when selecting suppliers.
From understanding the intricacies of materials and design to evaluating pricing structures and delivery logistics, this resource is designed to empower you with the knowledge necessary for informed purchasing decisions. It addresses common challenges faced by buyers in regions such as Africa, South America, the Middle East, and Europe, including navigating cultural preferences and compliance with regional standards.
By equipping you with actionable insights into supplier vetting processes, cost analysis, and market trends, this guide ensures that you are well-prepared to make choices that not only meet your operational needs but also enhance customer satisfaction. Whether you’re looking for innovative designs to elevate your hotel’s guest experience or durable solutions for healthcare facilities, understanding the landscape of custom bed sourcing is the first step towards successful procurement.
Understanding beds custom Types and Variations
Type Name | Key Distinguishing Features | Primary B2B Applications | Brief Pros & Cons for Buyers |
---|---|---|---|
Custom Luxury Beds | High-end materials, unique designs | Luxury hotels, upscale residences | Pros: Exceptional quality, bespoke designs. Cons: High cost, longer lead times. |
Modular Beds | Configurable components, space-saving | Co-living spaces, hostels | Pros: Versatile, easy to transport. Cons: May lack aesthetic appeal. |
Adjustable Beds | Electric mechanisms for head/foot lift | Healthcare facilities, hotels | Pros: Enhanced comfort, caters to diverse needs. Cons: Higher maintenance requirements. |
Eco-Friendly Beds | Sustainable materials, non-toxic finishes | Eco-conscious hotels, resorts | Pros: Environmentally friendly, attracts eco-minded clientele. Cons: Limited design options. |
Platform Beds | Low-profile, no box spring needed | Budget hotels, guesthouses | Pros: Cost-effective, minimalist design. Cons: Less comfort without additional cushioning. |
What Are the Characteristics of Custom Luxury Beds?
Custom luxury beds are defined by their high-end materials and unique designs tailored to the buyer’s specifications. These beds often feature premium fabrics, handcrafted elements, and personalized dimensions to fit specific spaces or themes. They are particularly suitable for luxury hotels and upscale residences where aesthetics and comfort are paramount. When purchasing, B2B buyers should consider the quality of materials, craftsmanship, and the potential for customization, as these factors significantly impact the overall guest experience.
How Do Modular Beds Benefit Co-Living Spaces?
Modular beds are designed for versatility, featuring configurable components that can adapt to different space requirements. This makes them ideal for co-living spaces and hostels where maximizing space is crucial. Buyers should focus on the ease of assembly and disassembly, as well as the durability of materials. The primary advantage of modular beds is their ability to cater to changing needs, but buyers should also be aware that they may not provide the same aesthetic appeal as more traditional designs.
Why Are Adjustable Beds Important in Healthcare Facilities?
Adjustable beds are equipped with electric mechanisms that allow users to elevate the head or foot sections, offering enhanced comfort and support. These beds are essential in healthcare facilities and hotels, particularly for guests with mobility issues or specific health needs. B2B buyers should evaluate the reliability of the electric components, ease of use, and maintenance requirements. While adjustable beds provide significant comfort benefits, they do require ongoing maintenance, which can be a consideration for budget-conscious buyers.
What Makes Eco-Friendly Beds Attractive for Hotels?
Eco-friendly beds are constructed using sustainable materials and non-toxic finishes, making them a popular choice for eco-conscious hotels and resorts. These beds not only reduce the environmental impact but also appeal to guests who prioritize sustainability. Buyers should investigate the sourcing of materials and certifications to ensure authenticity. Although eco-friendly options may offer limited designs compared to conventional beds, they can enhance a hotel’s brand image and attract a growing segment of environmentally aware travelers.
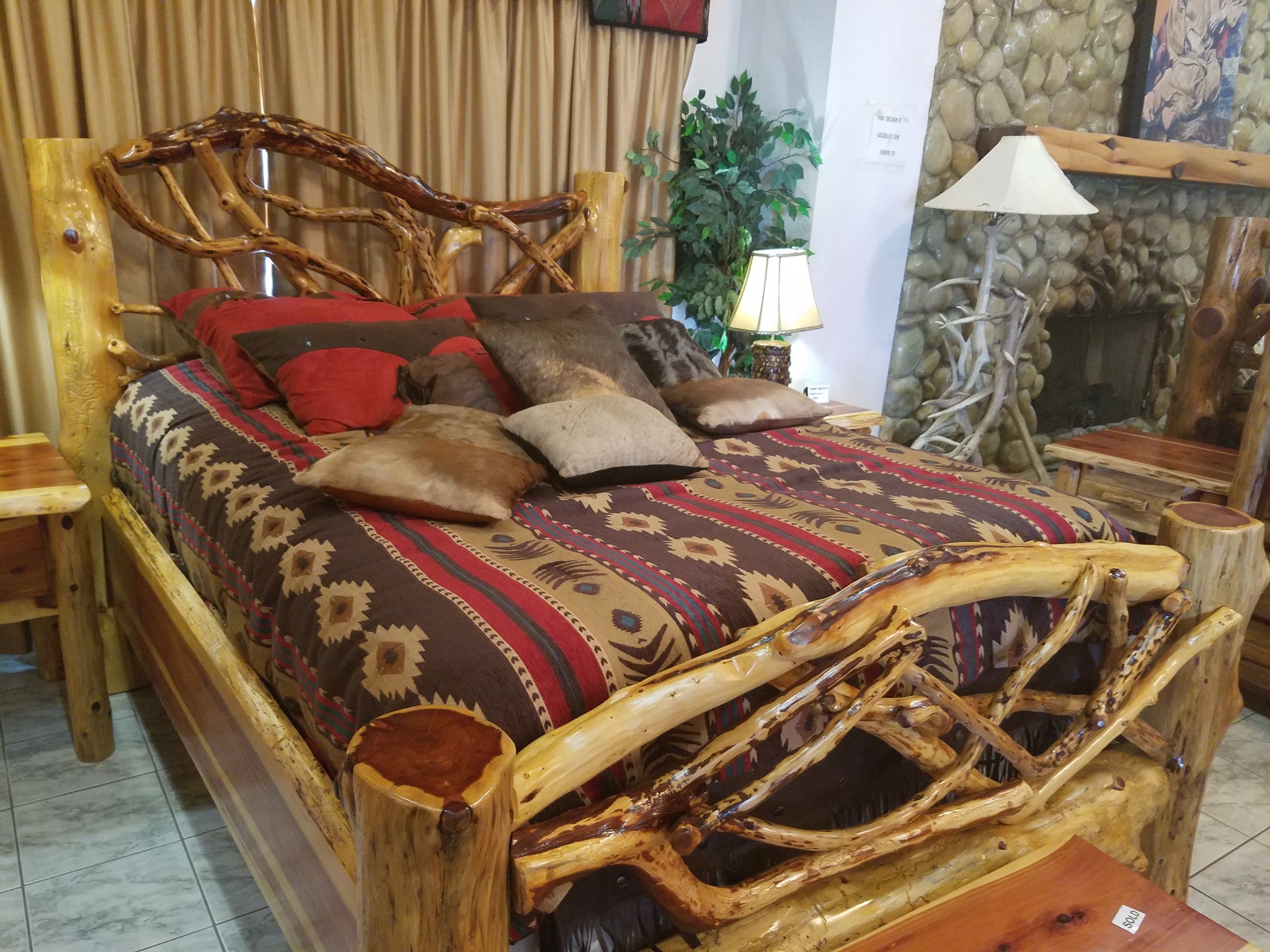
A stock image related to beds custom.
How Do Platform Beds Serve Budget Hotels?
Platform beds are characterized by their low-profile design and the absence of a box spring, making them a cost-effective option for budget hotels and guesthouses. They provide a minimalist aesthetic that can be appealing in modern settings. B2B buyers should consider the durability and comfort level of platform beds, especially regarding mattress compatibility. While they are economically advantageous, buyers must recognize that platform beds may require additional cushioning to achieve desired comfort levels for guests.
Related Video: Ikea MALM bed variations explained
Key Industrial Applications of beds custom
Industry/Sector | Specific Application of beds custom | Value/Benefit for the Business | Key Sourcing Considerations for this Application |
---|---|---|---|
Hospitality | Custom beds for hotels and resorts | Enhanced guest satisfaction leading to repeat business | Quality of materials, design versatility, local regulations |
Healthcare | Specialized beds for hospitals and clinics | Improved patient comfort and care efficiency | Compliance with health standards, ease of sanitization |
Education | Custom dormitory beds for universities | Maximized space and student comfort | Durability, modular design, cost-effectiveness |
Residential Construction | Tailored beds for luxury apartments and homes | Unique design appeal, increased property value | Customization options, delivery timelines, warranty |
Commercial Spaces | Custom beds for serviced apartments and Airbnbs | Attractive accommodations that boost occupancy rates | Flexibility in design, quality assurance, scalability |
How Are Custom Beds Used in the Hospitality Industry?
In the hospitality sector, custom beds are integral to creating a memorable guest experience. Hotels and resorts often require beds that not only meet comfort standards but also align with their unique branding. Custom beds can be tailored in size, material, and design to enhance the aesthetic appeal of rooms. For international buyers, sourcing quality materials that comply with local regulations is essential, as is ensuring that the beds can withstand the rigors of frequent use without compromising on comfort.
What Are the Applications of Custom Beds in Healthcare Facilities?
In healthcare settings, custom beds are designed to meet specific patient needs, such as adjustable features for comfort and ease of access. Hospitals and clinics benefit from beds that facilitate better patient care, including features like integrated storage for medical equipment. Buyers in this sector must consider compliance with health and safety standards, as well as the ease of sanitization to maintain hygiene. Customization can also accommodate various patient conditions, ensuring that the beds provide optimal support.
Why Are Custom Beds Important for Educational Institutions?
Educational institutions, particularly universities, utilize custom beds in dormitories to maximize space and improve student comfort. Custom dormitory beds can include features such as integrated study areas, storage solutions, and modular designs that adapt to changing student needs. For international buyers, key considerations include durability and cost-effectiveness, as well as the ability to meet the specific demands of student life while fostering an environment conducive to study and relaxation.
How Do Custom Beds Enhance Residential Construction Projects?
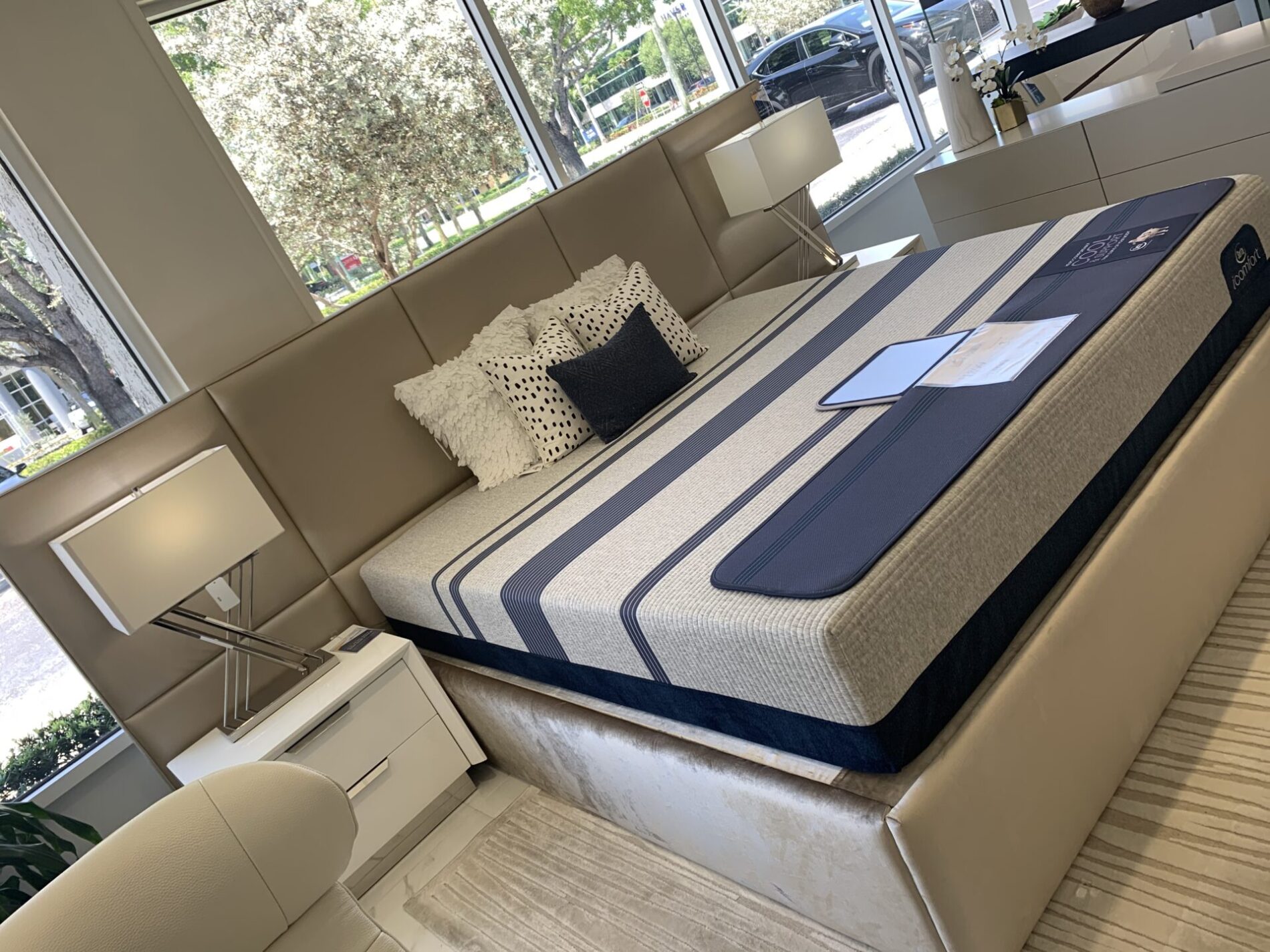
A stock image related to beds custom.
In the residential construction sector, custom beds are pivotal in luxury apartments and homes. They allow for unique designs that can significantly enhance the property’s appeal and market value. Customization options, such as bespoke headboards and integrated storage, cater to the specific tastes and requirements of homeowners. Buyers should prioritize sourcing from manufacturers who offer high-quality materials and flexible design solutions to ensure that the final product meets their expectations and enhances the overall living experience.
What Role Do Custom Beds Play in Commercial Spaces?
Custom beds in serviced apartments and Airbnbs can greatly influence guest satisfaction and occupancy rates. These beds can be tailored to fit the specific style and theme of the accommodation, thereby enhancing the overall guest experience. International buyers should look for suppliers who can provide flexibility in design and quality assurance, ensuring that the beds are both attractive and durable. Additionally, scalability is important for businesses looking to expand their offerings without compromising on quality.
Related Video: Sci6 Q3 – Characteristics and Uses of Simple Machines
3 Common User Pain Points for ‘beds custom’ & Their Solutions
Scenario 1: Sizing Issues with Custom Beds in Hospitality Settings
The Problem: A common challenge faced by B2B buyers, particularly in the hospitality sector, is the difficulty in ensuring that custom beds fit perfectly within the designated spaces of hotel rooms. Many buyers receive dimensions from architects or designers, but these specifications can often be vague or altered during the construction phase. This leads to beds that are either too large, causing obstruction, or too small, resulting in guest dissatisfaction. For hotels, where comfort and aesthetics are paramount, these sizing issues can severely impact guest experience and lead to costly renovations.
The Solution: To avoid sizing issues, B2B buyers should implement a thorough measurement and verification process. This involves conducting site visits to confirm room dimensions before finalizing bed orders. Additionally, it is essential to engage with manufacturers who offer flexible customization options, allowing adjustments even after initial specifications are provided. Buyers should also request 3D visualizations or CAD drawings of the custom beds to better understand how they will fit within the space. This proactive approach ensures that the final product meets both functional and aesthetic requirements, leading to a seamless installation process.
Scenario 2: Quality Concerns and Material Selection for Custom Beds
The Problem: Another significant pain point is the uncertainty around the quality of materials used in custom bed manufacturing. B2B buyers often worry about the durability and maintenance of the beds, especially in high-traffic environments like hotels or hospitals. With varying standards of quality across manufacturers, buyers may find it challenging to assess which materials will withstand daily use while maintaining comfort and appearance. This can result in additional costs for replacements or repairs, impacting the overall budget and long-term profitability.
The Solution: To address quality concerns, buyers should prioritize sourcing materials from reputable suppliers who provide detailed specifications and certifications for their products. It’s advisable to request samples to evaluate the texture, durability, and ease of maintenance. Engaging in discussions with manufacturers about their sourcing processes and quality control measures can further build confidence. Additionally, buyers can consult industry reviews and case studies that highlight the performance of specific materials in similar settings. By making informed decisions based on thorough research and direct communication with suppliers, buyers can ensure that they invest in high-quality custom beds that meet their long-term operational needs.
Scenario 3: Lead Time and Delivery Challenges for Custom Bed Orders
The Problem: Custom bed orders typically come with longer lead times, which can be a significant pain point for B2B buyers needing quick turnarounds. Delays in delivery can disrupt hotel openings or renovations, leading to lost revenue opportunities and a tarnished reputation. Buyers often find themselves in a bind, trying to balance the demand for unique, high-quality products with the necessity of timely delivery.
The Solution: To mitigate lead time issues, buyers should establish clear timelines and expectations with manufacturers right from the start. It is crucial to communicate deadlines and understand the manufacturer’s production capabilities. Buyers can also explore manufacturers that offer expedited services for custom orders or those who maintain a stock of frequently requested designs. Building relationships with multiple suppliers can also provide alternative options should delays occur. Additionally, incorporating buffer time into project schedules can help accommodate potential delays without compromising deadlines. By proactively managing timelines and supplier relationships, buyers can significantly reduce the risk of delivery issues impacting their operations.
Strategic Material Selection Guide for beds custom
What Are the Key Materials for Custom Beds?
When selecting materials for custom beds, international B2B buyers must consider several factors, including durability, cost, and compliance with regional standards. Here, we analyze four common materials used in the construction of custom beds, providing insights that are particularly relevant for buyers from Africa, South America, the Middle East, and Europe.
How Does Wood Perform in Custom Bed Manufacturing?
Key Properties: Wood is a traditional material known for its strength and aesthetic appeal. It typically offers excellent load-bearing capabilities and can be treated for moisture resistance, making it suitable for various climates.
Pros & Cons:
– Pros: Wood is durable and can be refinished, which extends its lifespan. It is also relatively easy to work with, allowing for intricate designs.
– Cons: Wood can be susceptible to warping and pest damage if not properly treated. Additionally, the cost can vary significantly based on the type of wood used.
Impact on Application: Wood is compatible with various finishes and can be adapted for different styles, from rustic to modern. However, it may not be ideal for humid environments without appropriate treatment.
Considerations for International Buyers: Buyers should ensure compliance with local regulations regarding sustainable sourcing and wood treatment standards. For instance, in the EU, adherence to the EU Timber Regulation is crucial.
What Are the Benefits of Metal in Custom Beds?
Key Properties: Metal, particularly steel and aluminum, offers high strength-to-weight ratios and excellent durability. It is resistant to corrosion when treated properly, making it suitable for diverse environments.
Pros & Cons:
– Pros: Metal frames provide superior structural integrity and are less prone to damage from pests. They can also be designed in various styles, from minimalist to industrial.
– Cons: Metal can be heavier than wood, complicating transport and assembly. Additionally, it may not provide the same warmth or aesthetic appeal as wood.
Impact on Application: Metal beds are ideal for high-traffic environments such as hotels or hostels due to their durability. However, they may require additional padding or cushioning to enhance comfort.
Considerations for International Buyers: Compliance with international standards such as ASTM for metals is critical. Buyers should also consider the availability of local suppliers to minimize shipping costs.
How Does Upholstered Fabric Affect Custom Bed Design?
Key Properties: Upholstered beds are typically constructed using a wooden or metal frame covered with foam and fabric. This combination offers a high level of comfort and aesthetic flexibility.
Pros & Cons:
– Pros: Upholstered beds can be customized in terms of fabric, color, and design, appealing to diverse consumer preferences. They also provide excellent comfort due to the cushioning.
– Cons: Upholstered beds may require more maintenance and are susceptible to staining and wear over time. The manufacturing process can be more complex and labor-intensive.
Impact on Application: Upholstered beds are popular in luxury hotels and residential settings, where comfort and style are paramount. However, they may not be suitable for environments where hygiene is a concern without appropriate fabric treatments.
Considerations for International Buyers: Buyers should be aware of fabric certifications, such as Oeko-Tex, to ensure that materials are free from harmful substances. Additionally, understanding local preferences for fabric types can influence purchasing decisions.
What Role Does Composite Material Play in Custom Beds?
Key Properties: Composite materials, such as engineered wood or high-density fiberboard (HDF), combine the benefits of wood with enhanced durability and moisture resistance.
Pros & Cons:
– Pros: Composites are generally more cost-effective than solid wood and can be manufactured to be lightweight and strong. They also offer consistent quality and are less prone to warping.
– Cons: The aesthetic appeal may not match that of solid wood, and some composites may emit volatile organic compounds (VOCs) if not properly treated.
Impact on Application: Composite materials are suitable for budget-friendly options and can be used in various applications, from residential to commercial. However, they may not be as durable as solid wood or metal in the long run.
Considerations for International Buyers: Buyers should ensure that composite materials comply with local emission standards, such as CARB in California or the EU’s E1 standard for formaldehyde emissions.
Summary Table of Material Selection for Custom Beds
Material | Typical Use Case for beds custom | Key Advantage | Key Disadvantage/Limitation | Relative Cost (Low/Med/High) |
---|---|---|---|---|
Wood | Residential and luxury hotels | Aesthetic appeal and durability | Susceptible to warping and pests | Medium |
Metal | High-traffic environments | Superior structural integrity | Heavier and less warm aesthetic | Medium |
Upholstered Fabric | Luxury hotels and residences | High comfort and customization | Requires maintenance and can stain | High |
Composite | Budget-friendly options | Cost-effective and consistent quality | Lower aesthetic appeal | Low |
This strategic material selection guide provides B2B buyers with essential insights to make informed decisions when sourcing materials for custom beds, ensuring compliance with local standards and meeting market demands.
In-depth Look: Manufacturing Processes and Quality Assurance for beds custom
What Are the Main Stages of Manufacturing Custom Beds?
The manufacturing process for custom beds typically involves four main stages: material preparation, forming, assembly, and finishing. Understanding these stages is crucial for B2B buyers looking to ensure quality and durability in their purchases.
1. Material Preparation
The first step in manufacturing custom beds involves selecting and preparing the appropriate materials. Common materials include wood, metal, and various types of upholstery fabrics. Each material must meet specific standards for strength and durability.
- Wood Selection: For wooden frames, buyers should look for hardwoods such as oak or maple, known for their strength and longevity.
- Metal Components: When metal is used, it should be of high-grade steel or aluminum to provide stability and resistance to wear.
- Upholstery Fabric: Fabrics should be carefully chosen based on comfort, durability, and ease of cleaning. Common options include polyester blends and natural fibers.
Buyers should inquire about the source and sustainability of these materials, as this can impact both quality and environmental compliance.
2. How Are Custom Beds Formed?
The forming stage involves shaping the materials into components that will eventually come together to create the bed. This can include cutting, molding, and machining processes.
- Cutting: Precision cutting tools are used to ensure each component is made to exact specifications. CNC (Computer Numerical Control) machines are often employed for their accuracy.
- Molding and Shaping: For upholstered beds, foam and batting are shaped to fit the frame. The quality of this process directly affects the comfort of the final product.
- Welding and Fastening: In metal bed frames, welding techniques must ensure strength and stability. Rivets or bolts are often used for assembly, providing a secure connection between components.
Buyers should confirm that manufacturers use advanced technology and skilled labor in this stage to avoid defects.
3. What Does the Assembly Process Entail?
During the assembly stage, all components are put together to form the complete bed. This stage is critical as it determines the structural integrity and overall quality of the product.
- Sequential Assembly: Components are assembled in a specific order to ensure stability. For instance, the frame is built first, followed by the addition of slats or support beams.
- Quality Checks: After assembly, initial quality checks are performed to identify any issues such as misalignment or structural weaknesses. This may involve visual inspections and measurements.
B2B buyers should ask about the assembly techniques used and the qualifications of the assembly team to ensure a high-quality product.
4. How Is the Finishing Process Conducted?
The finishing stage involves adding final touches to the bed, which can include sanding, painting, and applying protective coatings.
- Sanding and Smoothing: This process is essential to remove any rough edges and prepare the surface for finishing.
- Painting and Staining: Non-toxic paints and stains are preferred for aesthetic appeal and safety. Buyers should inquire about the types of finishes used, particularly if they have specific requirements regarding VOC emissions.
- Protective Coatings: Applying a protective coating can enhance durability and resistance to scratches and stains.
Buyers should ensure that the finishing processes comply with international safety standards.
How Do Quality Assurance Practices Enhance Manufacturing?
Quality assurance (QA) practices are essential in ensuring that the final product meets international standards and customer expectations. Here are key aspects of QA relevant to custom bed manufacturing.
What Are the Relevant International Standards for Custom Beds?
International standards such as ISO 9001 set the benchmark for quality management systems. Compliance with these standards indicates that a manufacturer has consistent quality control processes in place.
- ISO 9001: This standard focuses on quality management principles, including customer focus, leadership, and continual improvement. Manufacturers certified under ISO 9001 are regularly audited to maintain their certification.
- CE Marking: For products sold in the European market, CE marking indicates compliance with health, safety, and environmental protection standards. B2B buyers in Europe should prioritize suppliers with CE certification.
What Are the Key Quality Control Checkpoints?
Effective quality control in custom bed manufacturing typically includes several checkpoints:
- Incoming Quality Control (IQC): This step involves inspecting raw materials upon arrival at the manufacturing facility. Materials that do not meet specifications are rejected.
- In-Process Quality Control (IPQC): Quality checks are performed at various stages of the production process to catch defects early. This may involve measuring dimensions and ensuring assembly integrity.
- Final Quality Control (FQC): Before the product is shipped, a final inspection is conducted. This ensures that the bed meets all design specifications and quality standards.
B2B buyers should inquire about the specific QC protocols used by manufacturers.
What Common Testing Methods Are Used?
Testing methods are critical to ensuring the durability and safety of custom beds. Common methods include:
- Load Testing: This involves applying weight to the bed frame to test its strength and stability.
- Durability Testing: Manufacturers may simulate years of use to assess wear and tear on materials.
- Fire Resistance Testing: Ensuring that materials meet fire safety standards is crucial, particularly in hospitality settings.
How Can B2B Buyers Verify Supplier Quality Control?
B2B buyers should take proactive steps to verify the quality control processes of potential suppliers. Here are effective strategies:
- Conduct Supplier Audits: Regular audits of suppliers can reveal their adherence to quality standards. Audits should cover manufacturing practices, material sourcing, and compliance with international standards.
- Request Quality Reports: Manufacturers should be willing to provide documentation of their quality control processes, including test results and inspection records.
- Engage Third-Party Inspectors: Hiring independent inspectors can provide an unbiased assessment of the manufacturing facility and its processes.
What Are the Quality Control Nuances for International Buyers?
International buyers, particularly from Africa, South America, the Middle East, and Europe, should be aware of specific nuances in quality control:
- Cultural Differences: Understanding local manufacturing practices and quality expectations can help buyers communicate effectively with suppliers.
- Regulatory Compliance: Different regions have varying regulations regarding materials and safety standards. Buyers should ensure that their suppliers comply with local regulations and international standards.
- Logistics and Shipping Considerations: Quality control does not end at the factory. Buyers must consider how products are packaged and shipped to prevent damage during transit.
By understanding the manufacturing processes and quality assurance practices involved in custom bed production, B2B buyers can make informed decisions that align with their quality expectations and business needs.
Practical Sourcing Guide: A Step-by-Step Checklist for ‘beds custom’
When procuring custom beds for your business, having a structured approach is vital to ensure quality, functionality, and compliance with your specific needs. This step-by-step checklist serves as a comprehensive guide for international B2B buyers, particularly those operating in diverse markets such as Africa, South America, the Middle East, and Europe.
Step 1: Define Your Technical Specifications
Establishing clear technical specifications is the cornerstone of any successful procurement process. This includes dimensions, materials, weight limits, and design features. Consider the unique requirements of your target market—different regions may have varying preferences for style, comfort, and durability.
- Identify customer needs: Conduct market research to understand what consumers in your region value in custom beds.
- Regulatory compliance: Ensure your specifications align with any local regulations regarding materials and safety standards.
Step 2: Conduct Market Research
Understanding the market landscape is essential for making informed purchasing decisions. Research trends in the bed industry, including popular materials, designs, and pricing structures.
- Analyze competitors: Look at what successful businesses in your sector are offering.
- Seek insights from industry reports: Utilize resources like market analyses or trade publications that focus on the furniture sector.
Step 3: Evaluate Potential Suppliers
Before committing to a supplier, thorough evaluation is crucial to mitigate risks. Request comprehensive information about their production capabilities, quality control processes, and prior work.
- Request company profiles: Look for case studies or testimonials from buyers in similar industries or regions.
- Check references: Reach out to former clients to gauge their satisfaction and the reliability of the supplier.
Step 4: Verify Supplier Certifications
Supplier certifications can serve as an indicator of quality and compliance with international standards. Look for certifications related to materials, manufacturing processes, and environmental practices.
- ISO Certifications: These indicate adherence to quality management standards.
- Sustainability Certifications: Such as FSC (Forest Stewardship Council) for wood products, which can be a significant selling point.
Step 5: Request Samples and Prototypes
Before making a bulk order, requesting samples or prototypes can save you time and money. This step allows you to assess the quality of materials and craftsmanship firsthand.
- Evaluate comfort and design: Test the prototypes to ensure they meet your specifications and customer expectations.
- Check for manufacturing consistency: Ensure that the samples reflect the quality you expect in mass production.
Step 6: Negotiate Terms and Conditions
Once you’ve selected a supplier, negotiating terms is crucial to protect your investment. Discuss pricing, lead times, payment terms, and warranties.
- Clarify payment structures: Understand the implications of different payment options, such as upfront payments versus installments.
- Set clear delivery timelines: Establish expectations for production and shipping to avoid delays.
Step 7: Plan for Logistics and Distribution
Effective logistics planning ensures that your custom beds are delivered on time and in good condition. Work closely with your supplier to coordinate shipping and handling.
- Choose reliable logistics partners: Consider local and international shipping options that can accommodate your needs.
- Implement tracking systems: Utilize technology to monitor shipments and manage inventory effectively.
By following this checklist, B2B buyers can streamline their sourcing process for custom beds, ensuring they meet the demands of their market while maintaining high standards of quality and service.
Comprehensive Cost and Pricing Analysis for beds custom Sourcing
Understanding the cost structure and pricing for custom beds is crucial for international B2B buyers, particularly those from Africa, South America, the Middle East, and Europe. This analysis delves into the various components that influence pricing, providing actionable insights to help buyers make informed decisions.
What Are the Key Cost Components for Custom Beds?
When sourcing custom beds, several cost components must be considered:
-
Materials: The type and quality of materials significantly impact the overall cost. High-quality woods, metals, or upholstered fabrics will elevate expenses. Buyers should evaluate the cost of sustainable materials, which may have higher upfront costs but offer long-term benefits.
-
Labor: Labor costs vary by region and the complexity of the bed design. Countries with lower labor costs might provide a competitive advantage, but it’s essential to assess the skill level to ensure quality craftsmanship.
-
Manufacturing Overhead: This includes utilities, rent, and administrative expenses associated with production facilities. Understanding the overhead costs can help buyers evaluate the pricing of different suppliers.
-
Tooling: Custom designs often require specialized tools and molds, which can add to the initial cost. Buyers should inquire about tooling fees and whether these costs are amortized over larger orders.
-
Quality Control (QC): Implementing robust QC processes ensures that the beds meet specified standards. While this may increase costs, it can prevent expensive returns and replacements in the long run.
-
Logistics: Shipping costs can vary widely depending on the distance and method of transportation. Buyers should consider the logistics involved, including customs duties and taxes, especially when importing from different continents.
-
Margin: Suppliers typically include a profit margin in their pricing. Understanding the standard margins in different markets can help buyers negotiate better deals.
How Do Price Influencers Affect Custom Bed Pricing?
Several factors can influence the final price of custom beds:
-
Volume and Minimum Order Quantity (MOQ): Larger orders often lead to reduced per-unit costs. Buyers should explore the benefits of ordering in bulk versus smaller, more frequent orders.
-
Specifications and Customization: Highly customized products typically incur higher costs. Clear communication about design specifications can help avoid misunderstandings and additional costs.
-
Material Quality and Certifications: Beds made from certified sustainable materials or those meeting specific industry standards may cost more but can appeal to environmentally conscious consumers.
-
Supplier Factors: The reputation and reliability of suppliers can significantly influence pricing. Established suppliers may charge higher prices but often provide better quality assurance and reliability.
-
Incoterms: The chosen Incoterms can impact overall costs. Terms like FOB (Free on Board) or CIF (Cost, Insurance, and Freight) dictate the responsibilities of buyers and sellers, which can affect pricing and risk exposure.
What Are the Best Tips for Negotiating Custom Bed Prices?
Buyers should adopt several strategies to ensure cost efficiency when sourcing custom beds:
-
Negotiate Terms: Don’t hesitate to negotiate not just on price, but also on payment terms, delivery schedules, and warranties. Establishing a good relationship with suppliers can lead to better deals.
-
Consider Total Cost of Ownership (TCO): Beyond initial purchase price, consider maintenance, durability, and potential resale value. A higher upfront investment in quality materials can lead to lower TCO over time.
-
Stay Informed on Pricing Nuances: Each market has its pricing dynamics, influenced by local demand, currency fluctuations, and economic conditions. Staying informed about these factors can provide leverage during negotiations.
-
Request Multiple Quotes: Gathering quotes from various suppliers can provide a clearer picture of the market rate, helping buyers avoid overpaying.
Disclaimer on Indicative Prices
While indicative prices can provide a general sense of costs, they should be approached cautiously. Fluctuations in material costs, labor rates, and exchange rates can lead to significant changes in final pricing. Always confirm current pricing with suppliers before making purchasing decisions.
By understanding these cost components and price influencers, international B2B buyers can navigate the complexities of sourcing custom beds more effectively and achieve favorable outcomes for their businesses.
Alternatives Analysis: Comparing beds custom With Other Solutions
When exploring the market for customized beds, it’s essential to consider various alternatives that may meet the specific needs of businesses. This section provides a detailed comparison of ‘beds custom’ against alternative solutions, helping international B2B buyers, particularly from Africa, South America, the Middle East, and Europe, make informed decisions.
Comparison Table: How Do ‘Beds Custom’ Measure Against Alternatives?
Comparison Aspect | Beds Custom | Modular Bed Systems | Traditional Hotel Beds |
---|---|---|---|
Performance | High durability and personalization | Flexible configurations, moderate durability | Standardized quality, lower customization |
Cost | Higher initial investment | Moderate upfront costs | Generally lower cost |
Ease of Implementation | Requires professional installation | Easier assembly and disassembly | Simple setup, often pre-assembled |
Maintenance | Low maintenance with quality materials | Moderate maintenance; components may need replacement | Low maintenance, easy to clean |
Best Use Case | Luxury hotels seeking uniqueness | Hostels or budget hotels needing flexibility | Chain hotels with standardized offerings |
What Are the Pros and Cons of Modular Bed Systems?
Modular bed systems offer an alternative that provides flexibility in design and configuration. The key benefit of modular beds is their adaptability to various space requirements, making them ideal for hostels or budget accommodations. They can be easily reconfigured or expanded, which is particularly useful for businesses that anticipate fluctuating occupancy levels.
However, the durability of modular systems can be less than that of custom beds, as they often use less robust materials. While the initial cost may be moderate, ongoing replacement of components can add to the total expense over time. Overall, modular bed systems are best suited for businesses prioritizing flexibility and cost-effectiveness over luxury.
How Do Traditional Hotel Beds Compare?
Traditional hotel beds are a staple in the hospitality industry, known for their standardized quality and lower price point. These beds are typically pre-assembled and require minimal effort for setup, making them a convenient option for hotels looking to streamline operations.
The downside of traditional beds is the lack of customization; they do not offer the same level of personalization as custom beds. This can be a disadvantage for hotels aiming to create a unique brand experience. Nevertheless, traditional beds are an excellent choice for chain hotels where consistency across locations is a priority.
Conclusion: Which Bed Solution Is Right for Your Business?
Choosing the right bed solution for your business ultimately depends on your specific needs and operational goals. If your priority is to create a unique and luxurious experience for guests, ‘beds custom’ may be the best fit despite the higher initial investment. For businesses that require flexibility and adaptability, modular bed systems could provide the ideal balance between cost and functionality. Conversely, traditional hotel beds may be more suitable for establishments focused on efficiency and consistency at a lower cost.
International B2B buyers should carefully evaluate these factors, considering their target market, budget constraints, and brand positioning to make the most informed decision.
Essential Technical Properties and Trade Terminology for beds custom
What Are the Key Technical Properties of Custom Beds?
When sourcing custom beds for international markets, understanding the essential technical properties is vital. Here are some critical specifications to consider:
-
Material Grade
– The material used in bed manufacturing, such as hardwood, softwood, metal, or upholstered fabrics, significantly influences durability and comfort. Higher-grade materials typically offer better longevity and aesthetic appeal, which is crucial for hotels and hospitality businesses aiming to enhance guest experiences. -
Tolerance Levels
– Tolerance refers to the allowable deviation from specified dimensions in manufacturing. For custom beds, maintaining tight tolerances ensures that components fit together seamlessly, enhancing structural integrity and aesthetic quality. This is particularly important for B2B buyers who need to ensure that beds integrate well with other furniture and fixtures. -
Load Capacity
– This specification denotes the maximum weight a bed can safely support. It is essential for ensuring the safety and satisfaction of end-users. Custom bed manufacturers should provide clear load capacity ratings to help buyers choose products that meet their needs, especially in environments like hotels where varying guest weights must be accommodated. -
Finishing Techniques
– The finish applied to a bed can affect both its appearance and durability. Common finishes include varnish, lacquer, or oil, each offering different levels of resistance to wear, moisture, and staining. B2B buyers should consider how the finishing technique aligns with their brand image and maintenance capabilities. -
Sustainability Certifications
– Increasingly, buyers are prioritizing eco-friendly materials and practices. Certifications such as FSC (Forest Stewardship Council) indicate that wood has been sourced sustainably. For international buyers, understanding these certifications can influence purchasing decisions and align with corporate social responsibility goals.
What Common Trade Terms Should B2B Buyers Know in the Custom Bed Industry?
Navigating the landscape of custom bed procurement involves understanding various industry terms. Here are several essential terms and their meanings:
-
OEM (Original Equipment Manufacturer)
– This term refers to companies that manufacture products for other brands to sell under their name. Understanding OEM relationships can help buyers identify reliable suppliers that can produce custom beds tailored to their specifications. -
MOQ (Minimum Order Quantity)
– MOQ defines the smallest number of units a supplier is willing to sell. For B2B buyers, knowing the MOQ is crucial for budget planning and inventory management, especially when entering new markets or testing new product lines. -
RFQ (Request for Quotation)
– An RFQ is a standard business process in which buyers request pricing information from suppliers for specific products. Crafting a detailed RFQ for custom beds ensures that suppliers understand the buyer’s needs and can provide accurate quotes, which is vital for cost management. -
Incoterms (International Commercial Terms)
– These are internationally recognized rules that define the responsibilities of buyers and sellers in international transactions. Familiarity with Incoterms helps B2B buyers understand shipping costs, risk management, and delivery responsibilities, ensuring smooth cross-border transactions. -
Lead Time
– Lead time refers to the amount of time it takes from placing an order to delivery. Understanding lead times is essential for B2B buyers to effectively manage inventory and meet customer expectations, especially in industries with fluctuating demand. -
Customization Options
– This term encompasses the various ways a bed can be tailored to meet specific buyer needs, including size, design, and materials. Knowing the available customization options allows buyers to better align products with their market demands and customer preferences.
By familiarizing themselves with these technical properties and trade terms, international B2B buyers can make informed decisions when sourcing custom beds, ultimately enhancing their product offerings and customer satisfaction.
Navigating Market Dynamics and Sourcing Trends in the beds custom Sector
What Are the Key Market Dynamics and Trends in the Custom Beds Sector?
The custom beds sector is experiencing notable growth driven by several global factors. Increasing consumer preferences for personalized products are compelling manufacturers to innovate and diversify their offerings. Custom beds are now not just about comfort but also about aesthetic appeal and functionality, particularly in hospitality and residential markets. International B2B buyers, particularly from regions like Africa, South America, the Middle East, and Europe, are capitalizing on these trends to enhance their product portfolios.
Emerging technologies such as 3D printing and smart manufacturing are transforming the sourcing landscape. Buyers can now access tailored solutions that meet specific design requirements and ergonomics. Digital platforms are facilitating direct connections between buyers and manufacturers, allowing for more competitive pricing and faster turnaround times. In this context, B2B buyers should focus on suppliers who leverage advanced technologies to ensure quality and efficiency in production.
Additionally, the ongoing global emphasis on health and wellness is influencing market dynamics. With an increased focus on sleep quality, buyers are seeking custom beds that incorporate features like adjustable firmness, temperature control, and hypoallergenic materials. The integration of IoT technologies in smart beds offers further customization, making it a lucrative opportunity for B2B buyers looking to enhance their offerings.
How Important Is Sustainability and Ethical Sourcing in the Custom Beds Sector?
Sustainability is becoming a cornerstone in the custom beds sector, driven by growing consumer awareness and regulatory pressures. B2B buyers are increasingly prioritizing suppliers who demonstrate commitment to environmentally friendly practices. This includes sourcing materials that are sustainably harvested, such as bamboo and organic cotton, as well as using non-toxic adhesives and finishes.
Ethical supply chains are also gaining traction. Buyers should seek manufacturers that adhere to fair labor practices and ensure safe working conditions. Certifications such as Global Organic Textile Standard (GOTS) and Forest Stewardship Council (FSC) are critical indicators of a supplier’s commitment to sustainability and ethical sourcing. By aligning with these standards, businesses can not only enhance their brand reputation but also meet the expectations of environmentally-conscious consumers.
Moreover, sustainable practices can lead to cost savings in the long run. For instance, investing in energy-efficient manufacturing processes can reduce operational costs while also appealing to eco-minded buyers. Therefore, B2B buyers should carefully assess the sustainability credentials of their suppliers and consider partnerships that align with their corporate social responsibility (CSR) goals.
What Is the Evolution of the Custom Beds Market and Its Impact on B2B Buyers?
The custom beds market has evolved significantly over the past few decades. Initially dominated by traditional manufacturing methods, the sector is now characterized by rapid advancements in technology and design. The introduction of online customization tools has empowered consumers to engage in the design process, leading to a surge in demand for bespoke solutions.
In the 1990s, the focus was primarily on functionality and affordability. However, as consumer preferences shifted towards personalization and luxury, manufacturers began to innovate with materials and designs that cater to niche markets. This evolution has opened up new opportunities for B2B buyers, allowing them to differentiate their offerings in a competitive landscape.
Moreover, the rise of e-commerce has transformed the way businesses source custom beds. Buyers can now access global suppliers and compare products and prices effortlessly. This increased competition encourages innovation and quality improvements, benefiting the end consumer. As the market continues to evolve, B2B buyers must remain agile, adapting to trends and leveraging technology to maintain a competitive edge.
Frequently Asked Questions (FAQs) for B2B Buyers of beds custom
-
How do I choose the right custom bed supplier for my business?
Choosing the right custom bed supplier involves a thorough evaluation of their capabilities, reputation, and product offerings. Look for suppliers with experience in your specific market and those who can demonstrate quality craftsmanship. Request samples to assess material quality and durability. It’s also beneficial to check reviews and testimonials from other B2B clients. Additionally, ensure they have robust communication practices and are willing to collaborate on your specific design needs. -
What factors should I consider when customizing beds for my market?
When customizing beds, consider local preferences, climate, and cultural factors that influence design and functionality. For instance, in warmer climates, breathable materials are preferable, while in colder regions, insulated options may be favored. Additionally, assess the size preferences common in your market, such as standard versus larger sizes. Engaging with local stakeholders can provide insights into popular styles and features, ensuring your custom beds meet market demand effectively.
-
What are typical minimum order quantities (MOQs) for custom beds?
Minimum order quantities (MOQs) for custom beds can vary widely based on the supplier and the complexity of the designs. Generally, MOQs range from 50 to 500 units. Smaller manufacturers may accommodate lower MOQs for niche designs, while larger manufacturers often set higher MOQs to optimize production efficiency. Discussing your needs upfront with potential suppliers can help negotiate favorable terms that align with your business strategy. -
What payment terms should I expect when sourcing custom beds internationally?
Payment terms can differ significantly across suppliers and regions. Standard practices often include a deposit (typically 30-50%) upfront, with the balance due upon completion or delivery. Some suppliers may offer flexible terms based on your creditworthiness or history. It’s advisable to clarify payment methods accepted, including wire transfers, letters of credit, or payment platforms, to ensure smooth transactions and avoid potential delays. -
How can I ensure quality assurance when ordering custom beds?
To ensure quality assurance, establish clear specifications and standards in your contract with the supplier. Request detailed samples before full production and conduct quality checks at various stages of manufacturing. If possible, visit the factory to observe production processes. Additionally, consider hiring a third-party quality control service to inspect the final products before shipment, particularly when sourcing from countries with varying quality standards. -
What logistics considerations should I keep in mind for international bed shipments?
When planning for international shipments of custom beds, consider the dimensions and weight of the beds, as these factors affect shipping costs and methods. Research logistics providers experienced in handling large furniture items. Be aware of import duties, taxes, and regulations specific to your destination country. It’s also important to have a contingency plan for potential delays or damages during transit, ensuring you have insurance coverage for your shipments. -
What are the best practices for communicating with my custom bed supplier?
Effective communication is crucial for a successful partnership with your custom bed supplier. Use clear, concise language and ensure all specifications are documented in writing. Establish regular check-ins to discuss progress and address any concerns. Utilize visual aids, such as sketches or prototypes, to align expectations. Be open to feedback and maintain a collaborative attitude to foster a productive working relationship. -
How can I assess the sustainability practices of custom bed manufacturers?
To assess the sustainability practices of custom bed manufacturers, inquire about their sourcing of materials, waste management, and energy consumption. Look for certifications such as FSC (Forest Stewardship Council) for wood products or OEKO-TEX for textiles, which indicate adherence to environmental standards. Additionally, engage in discussions about their commitment to ethical labor practices and their overall impact on the environment. Sustainability is increasingly important in B2B partnerships, and aligning with eco-friendly manufacturers can enhance your brand’s reputation.
Important Disclaimer & Terms of Use
⚠️ Important Disclaimer
The information provided in this guide, including content regarding manufacturers, technical specifications, and market analysis, is for informational and educational purposes only. It does not constitute professional procurement advice, financial advice, or legal advice.
While we have made every effort to ensure the accuracy and timeliness of the information, we are not responsible for any errors, omissions, or outdated information. Market conditions, company details, and technical standards are subject to change.
B2B buyers must conduct their own independent and thorough due diligence before making any purchasing decisions. This includes contacting suppliers directly, verifying certifications, requesting samples, and seeking professional consultation. The risk of relying on any information in this guide is borne solely by the reader.
Strategic Sourcing Conclusion and Outlook for beds custom
In conclusion, the strategic sourcing of custom beds is vital for international B2B buyers looking to enhance their hospitality offerings. By prioritizing quality, sustainability, and supplier relationships, businesses can achieve significant cost efficiencies and bolster their brand reputation. The insights gathered from diverse markets—especially in Africa, South America, the Middle East, and Europe—highlight the importance of adapting sourcing strategies to local demands and trends.
What are the key benefits of strategic sourcing in the custom beds market? Effective sourcing not only reduces procurement costs but also fosters innovation in product design and materials. Buyers should leverage technology and data analytics to streamline their sourcing processes, ensuring they stay ahead of market trends and customer preferences.
As the demand for custom solutions continues to grow, international buyers must remain proactive. Engage with suppliers who align with your business values and can provide tailored solutions that meet your specific needs. The future of the custom beds market is promising, and now is the time to act. Invest in strategic sourcing initiatives that drive value and position your business for success in an increasingly competitive landscape.