Unlock Savings: The Ultimate Guide to Classic Trucks Custom (2025)
Introduction: Navigating the Global Market for classic trucks custom
Navigating the complex landscape of sourcing classic trucks custom can be a daunting challenge for international B2B buyers. With increasing demand for vintage vehicles that blend nostalgia with modern functionality, understanding the nuances of this niche market is essential. This guide serves as a comprehensive resource, addressing key aspects such as types of classic trucks, customization options, potential applications in various industries, supplier vetting procedures, and cost considerations.
International buyers from regions like Africa, South America, the Middle East, and Europe face unique challenges when sourcing these specialized vehicles. Factors such as import regulations, cultural preferences, and availability of parts can significantly impact purchasing decisions. By providing in-depth insights into the market dynamics and practical strategies for effective sourcing, this guide empowers buyers to make informed choices that align with their business objectives.
Whether you are looking to enhance your fleet with classic trucks for promotional purposes or seeking to invest in restoration projects, understanding the global market landscape is crucial. This resource not only offers clarity on where to find reliable suppliers but also highlights the importance of evaluating customization capabilities to meet specific business needs. By leveraging this guide, B2B buyers can confidently navigate the global market for classic trucks custom, ensuring they achieve both quality and value in their acquisitions.
Understanding classic trucks custom Types and Variations
Type Name | Key Distinguishing Features | Primary B2B Applications | Brief Pros & Cons for Buyers |
---|---|---|---|
Vintage Pickup Trucks | Classic styling, open cargo bed, robust performance | Agriculture, construction, logistics | Pros: Versatile; Cons: Limited payload capacity |
Panel Trucks | Enclosed cargo area, distinct retro aesthetics | Delivery services, mobile businesses | Pros: Weather-resistant; Cons: Lower maneuverability |
Rat Rods | Customized aesthetics, unique designs, often modified | Specialty advertising, events | Pros: Eye-catching; Cons: May lack reliability |
Classic Tow Trucks | Heavy-duty build, towing capacity, vintage design | Transportation, recovery services | Pros: Strong towing capability; Cons: Higher maintenance costs |
Classic Flatbed Trucks | Flat cargo area, simple construction, easy loading | Freight transport, heavy machinery | Pros: Easy to customize; Cons: Less protection for cargo |
What Are the Key Characteristics of Vintage Pickup Trucks?
Vintage pickup trucks are characterized by their classic styling, open cargo bed, and robust performance. They are often built with durable materials, making them suitable for a variety of industries, including agriculture and construction. B2B buyers should consider their versatility, as these trucks can serve multiple purposes, from transporting goods to serving as mobile workshops. However, one key purchasing consideration is their limited payload capacity compared to modern trucks, which may impact operational efficiency.
How Do Panel Trucks Serve B2B Needs?
Panel trucks are defined by their enclosed cargo area and retro aesthetics, making them ideal for delivery services and mobile businesses. Their design offers protection for goods against weather conditions, which is crucial for businesses that transport perishable items or sensitive equipment. When considering a panel truck, B2B buyers should weigh the benefits of weather resistance against potential drawbacks, such as lower maneuverability in tight urban settings.
What Makes Rat Rods Unique for B2B Applications?
Rat rods stand out due to their customized aesthetics and unique designs, often featuring unconventional modifications. These trucks are particularly appealing for specialty advertising and events where visual impact is paramount. While they can attract attention and generate brand recognition, B2B buyers should be aware of the potential reliability issues that may arise from extensive modifications, which could affect their operational dependability.
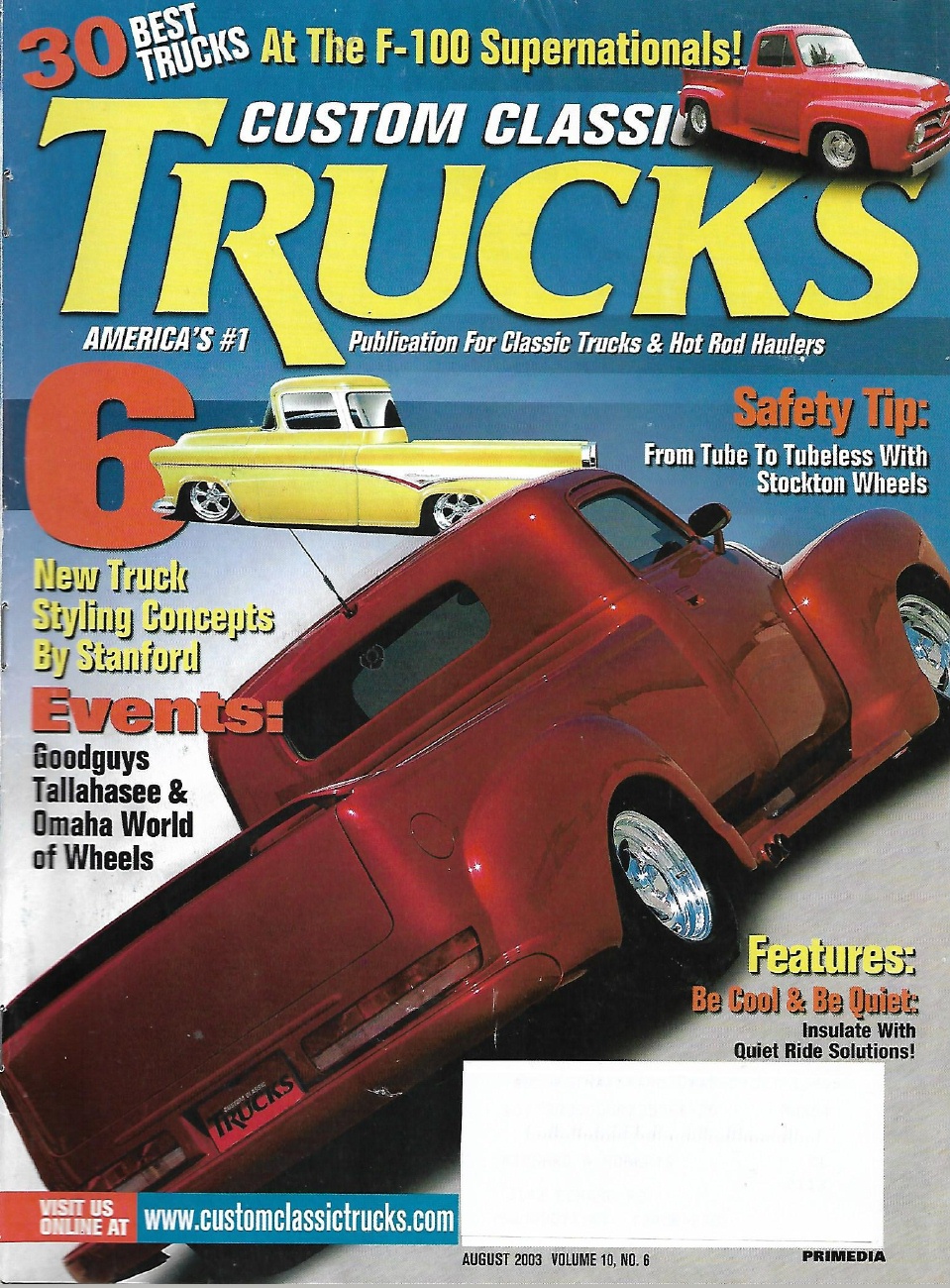
A stock image related to classic trucks custom.
Why Choose Classic Tow Trucks for Heavy-Duty Needs?
Classic tow trucks are built with a heavy-duty framework, offering significant towing capacity alongside vintage design. They are essential for transportation and recovery services, providing businesses with reliable solutions for moving broken-down vehicles or heavy equipment. However, buyers should consider the higher maintenance costs associated with older vehicles, as these can impact overall operational budgets.
What Are the Benefits of Classic Flatbed Trucks?
Classic flatbed trucks feature a flat cargo area that allows for easy loading and unloading, making them suitable for freight transport and heavy machinery. Their simple construction provides a blank canvas for customization, enabling businesses to tailor the truck to specific needs. While the ease of customization is a significant advantage, B2B buyers must also consider the lack of protection for cargo, which could be a downside for certain types of transport.
Related Video: Custom Classic Chevy C10 Muscle Truck Build – Start To Finish
Key Industrial Applications of classic trucks custom
Industry/Sector | Specific Application of classic trucks custom | Value/Benefit for the Business | Key Sourcing Considerations for this Application |
---|---|---|---|
Agriculture | Custom transport for farm produce and equipment | Enhanced efficiency in logistics and distribution | Durable construction to withstand harsh environments; local regulations on vehicle modifications |
Construction | Heavy-duty transport for construction materials | Improved project timelines and reduced downtime | Compliance with safety standards; ability to customize for specific loads and conditions |
Tourism and Hospitality | Vintage truck rentals for tours and events | Unique customer experiences that boost engagement | Aesthetic appeal; reliability for long-distance travel; maintenance support and parts availability |
Logistics and Freight | Customized delivery trucks for regional distribution | Increased capacity and flexibility in operations | Fuel efficiency; adaptability to various cargo types; robust after-sales service options |
Retail | Mobile retail units for pop-up shops | Expanded market reach and customer engagement | Custom branding options; compliance with local laws for mobile sales; ease of maneuverability in urban areas |
How Are Classic Trucks Custom Used in Agriculture?
In the agriculture sector, classic trucks custom are often utilized for transporting farm produce and equipment. These vehicles are tailored to meet the unique demands of rural terrains and heavy loads. By using custom trucks, agricultural businesses can enhance their logistics efficiency, ensuring timely delivery of goods to markets. Buyers from regions like Africa and South America should consider the truck’s durability, especially in remote areas, and ensure compliance with local agricultural transportation regulations.
What Are the Benefits of Classic Trucks Custom in Construction?
Custom classic trucks play a crucial role in the construction industry, primarily for transporting heavy materials like concrete, steel, and tools. Their robust design allows them to handle significant weights, thereby improving project timelines by ensuring that materials arrive on-site as needed. For international buyers, particularly in the Middle East, it’s essential to source trucks that comply with local safety standards and can be customized for specific load requirements, helping to minimize downtime on construction projects.
How Do Classic Trucks Custom Enhance Tourism and Hospitality?
In the tourism and hospitality sector, classic trucks custom are increasingly popular for vintage truck rentals used in tours and events. These trucks provide a unique and memorable experience for customers, enhancing engagement and driving interest. When sourcing these vehicles, businesses should focus on aesthetics, reliability for long-distance travel, and the availability of maintenance support. Buyers in Europe, for example, might prioritize historical authenticity alongside modern safety features to appeal to discerning tourists.
What Role Do Classic Trucks Custom Play in Logistics and Freight?
In logistics and freight, customized classic trucks are essential for regional distribution. Their flexibility allows businesses to adapt to various cargo types, thus increasing operational capacity. For B2B buyers, particularly in South America and Africa, considerations such as fuel efficiency and robust after-sales service are critical. Ensuring that the trucks can be tailored to specific logistical needs, including load sizes and delivery routes, will enhance overall supply chain performance.
How Can Retail Benefit from Mobile Classic Trucks Custom?
Retail businesses are leveraging classic trucks custom to create mobile retail units for pop-up shops. This approach allows brands to expand their market reach and engage with customers in diverse locations. When sourcing these custom trucks, businesses should consider options for branding, compliance with local mobile sales laws, and the vehicle’s maneuverability in urban settings. This strategy is particularly effective in regions like Europe, where consumer experience and accessibility are paramount.
Related Video: 10 Nifty Uses for Oscillating Multitool Saws
3 Common User Pain Points for ‘classic trucks custom’ & Their Solutions
Scenario 1: Navigating Regulatory Compliance in Classic Truck Customization
The Problem:
B2B buyers in regions such as Europe and the Middle East often face significant regulatory challenges when customizing classic trucks. Different countries have varying standards regarding emissions, safety, and roadworthiness. For instance, a buyer might invest in a classic truck custom project, only to discover that the modifications made do not comply with local laws, resulting in costly fines or the inability to register the vehicle. This scenario is particularly frustrating for international buyers who may not be fully aware of local regulations.
The Solution:
To navigate these regulatory hurdles, B2B buyers should conduct thorough research into the specific compliance requirements of their target market before beginning any customization project. Engaging a local compliance consultant can provide valuable insights into the necessary modifications that must be made to meet regulatory standards. Furthermore, buyers should consider sourcing classic trucks from manufacturers who already have a strong understanding of local regulations, as they can offer guidance on compliant modifications. Keeping documentation of all modifications and certifications can also streamline the registration process, making it easier to demonstrate compliance to authorities.
Scenario 2: Sourcing Quality Parts for Classic Truck Customization
The Problem:
One of the most significant challenges B2B buyers encounter is sourcing quality parts for classic truck customization. The classic truck market often suffers from a lack of availability of OEM parts, leading to a reliance on aftermarket components. This can result in variations in quality, which may affect the performance and durability of the finished product. Buyers may find themselves stuck with subpar parts that lead to increased maintenance costs and dissatisfied customers.
The Solution:
To overcome this issue, buyers should establish relationships with reputable suppliers who specialize in classic truck parts. Attending trade shows and industry expos can help buyers identify reliable manufacturers and wholesalers who provide high-quality components. Additionally, leveraging online platforms and forums dedicated to classic trucks can yield valuable recommendations from fellow enthusiasts and industry professionals. It’s also beneficial to implement a strict quality control process when receiving parts to ensure they meet the necessary specifications before installation.
Scenario 3: Managing Expectations with Customization Timelines
The Problem:
Another common pain point for B2B buyers dealing with classic trucks custom projects is managing timelines. Customization processes can often take longer than anticipated due to various factors such as parts delays, skilled labor shortages, or unexpected technical challenges. This can lead to frustration for buyers, especially if they have promised delivery dates to their customers or have planned marketing strategies around a specific launch date.
The Solution:
To effectively manage timelines, buyers should adopt a proactive project management approach. This includes setting realistic timelines based on thorough consultations with customization experts and suppliers. Implementing regular check-ins with all stakeholders involved in the project can help identify potential delays early on and allow for adjustments to be made. Additionally, buyers can benefit from creating a buffer period in their delivery schedules to account for unforeseen issues. Utilizing project management software can also streamline communication and task tracking, ensuring that all parties are aligned and informed throughout the customization process.
Strategic Material Selection Guide for classic trucks custom
When selecting materials for custom classic trucks, international B2B buyers must consider various factors that influence performance, durability, and compliance with regional standards. Below, we analyze four common materials used in the manufacturing of classic trucks, focusing on their properties, advantages, disadvantages, and specific considerations for buyers from Africa, South America, the Middle East, and Europe.
What Are the Key Properties of Steel in Classic Truck Customization?
Steel is a widely used material in the automotive industry due to its excellent mechanical properties. It exhibits high tensile strength, which is crucial for structural components, and can withstand high temperatures and pressures. Steel is also relatively easy to work with, allowing for various manufacturing processes such as welding and machining.
Pros & Cons:
Steel’s main advantages include its durability and cost-effectiveness, making it suitable for heavy-duty applications. However, it is susceptible to corrosion if not properly treated, which can be a significant drawback in regions with high humidity or salt exposure.
Impact on Application:
Steel is compatible with a range of media, including oils and fuels, making it ideal for engine components and chassis. Buyers should consider corrosion-resistant coatings or stainless steel options for enhanced longevity.
Considerations for International Buyers:
Buyers must ensure compliance with local standards such as ASTM (American Society for Testing and Materials) or DIN (Deutsches Institut für Normung). In regions like Europe, adherence to environmental regulations regarding coatings and treatments is also essential.
How Does Aluminum Compare for Classic Truck Custom Applications?
Aluminum is another popular choice for classic truck customization, known for its lightweight properties and resistance to corrosion. It has a lower density than steel, which can improve fuel efficiency and handling.
Pros & Cons:
The primary advantage of aluminum is its excellent corrosion resistance, which is particularly beneficial in coastal areas. However, it is generally more expensive than steel and can be more challenging to weld, which may increase manufacturing complexity.
Impact on Application:
Aluminum is suitable for components that require weight reduction without sacrificing strength, such as body panels and wheels. Its compatibility with various media is also favorable, though care must be taken with certain chemicals that may cause galvanic corrosion.
Considerations for International Buyers:
Buyers should look for aluminum alloys that meet specific standards like JIS (Japanese Industrial Standards) for quality assurance. Understanding regional preferences for aluminum grades is crucial, especially in markets like South America, where specific alloys may be favored.
What Are the Benefits and Limitations of Composite Materials?
Composite materials, such as fiberglass or carbon fiber, are increasingly being used in custom classic truck applications due to their unique properties. They offer excellent strength-to-weight ratios and are highly resistant to corrosion and environmental factors.
Pros & Cons:
The key advantage of composites is their lightweight nature, which can significantly enhance performance. However, they can be costly and may require specialized manufacturing techniques, which could complicate production.
Impact on Application:
Composites are ideal for aesthetic components like body kits and interior fittings, where weight savings and design flexibility are paramount. They are generally compatible with various media but require careful selection to avoid chemical degradation.
Considerations for International Buyers:
Buyers should be aware of the certifications required for composite materials in their respective regions. Compliance with standards such as ISO (International Organization for Standardization) is essential, particularly in Europe and the Middle East.
How Do Rubber and Plastics Fit Into Classic Truck Customization?
Rubber and plastics are often used for seals, gaskets, and interior components in classic trucks. Rubber is known for its elasticity and durability, while plastics can offer versatility in design and weight savings.
Pros & Cons:
Rubber provides excellent resistance to wear and tear, making it suitable for components exposed to friction. However, it can degrade over time due to UV exposure. Plastics, while lightweight and cost-effective, may not offer the same durability as metals or composites.
Impact on Application:
These materials are essential for ensuring proper sealing and insulation in various truck applications, contributing to overall vehicle performance. Compatibility with oils and fuels is crucial for rubber components.
Considerations for International Buyers:
Buyers should ensure that rubber and plastic materials meet local standards for automotive components, such as ASTM or ISO. Understanding regional preferences for specific types of rubber compounds or plastics can also influence material selection.
Summary Table of Material Selection for Classic Trucks Custom
Material | Typical Use Case for classic trucks custom | Key Advantage | Key Disadvantage/Limitation | Relative Cost (Low/Med/High) |
---|---|---|---|---|
Steel | Chassis, structural components | High strength and durability | Susceptible to corrosion | Medium |
Aluminum | Body panels, wheels | Lightweight and corrosion-resistant | Higher cost and welding complexity | High |
Composites | Body kits, interior fittings | Excellent strength-to-weight ratio | High cost and specialized manufacturing | High |
Rubber/Plastics | Seals, gaskets, interior components | Good wear resistance and versatility | Rubber degradation over time | Low |
This guide provides a comprehensive overview of material options for classic truck customization, offering actionable insights for international B2B buyers in diverse markets. Understanding these materials’ properties, advantages, and limitations will facilitate informed decision-making and enhance product performance.
In-depth Look: Manufacturing Processes and Quality Assurance for classic trucks custom
What Are the Main Stages of Manufacturing Classic Custom Trucks?
The manufacturing process for classic custom trucks involves several key stages, each critical to ensuring the final product meets the desired specifications and quality standards. Understanding these stages is essential for B2B buyers looking to source reliable suppliers.
1. Material Preparation
Material preparation is the foundational step in the manufacturing process. This stage involves selecting high-quality raw materials, including steel, aluminum, and composite materials, which are crucial for the truck’s durability and performance. Suppliers typically conduct thorough assessments to ensure that materials comply with international standards such as ISO 9001.
Buyers should inquire about the sourcing of materials and the certifications held by suppliers to guarantee quality. For example, materials should ideally come from suppliers that adhere to environmental standards like ISO 14001, ensuring sustainable practices.
2. Forming Processes: What Techniques Are Used in Classic Truck Manufacturing?
Once materials are prepared, the next step is forming, which includes processes like stamping, bending, and welding.
-
Stamping: This technique is used to create body panels and other structural components. Precision stamping ensures that parts fit together seamlessly during assembly.
-
Bending: Used for creating frames and chassis, this technique requires specialized machinery that can handle the thickness and type of metal being used.
-
Welding: Critical for joining components, welding must be performed by certified professionals to ensure structural integrity. Different welding techniques, such as MIG and TIG, are often employed depending on the materials being used.
Understanding these techniques allows B2B buyers to assess the technological capabilities of potential suppliers.
3. Assembly: How Are Classic Trucks Assembled?
The assembly stage involves bringing together all the manufactured components into a cohesive unit. This process can be manual or automated, depending on the supplier’s capabilities.
-
Manual Assembly: Often preferred for custom trucks, this method allows for a high degree of customization and attention to detail. Skilled labor is essential here, and buyers should evaluate the expertise and training of the workforce.
-
Automated Assembly: While less common for custom builds, some suppliers may employ automation for repetitive tasks, improving efficiency and consistency.
During this stage, it’s important for buyers to inquire about the assembly line’s flexibility and the supplier’s ability to accommodate specific customization requests.
4. Finishing: What Quality Assurance Measures Are Taken?
The finishing process includes painting, coating, and detailing. This stage not only enhances aesthetics but also provides protection against corrosion and wear.
-
Painting: Suppliers often use advanced techniques such as powder coating to ensure a durable finish. Buyers should ask about the types of paints used and their compliance with environmental regulations.
-
Quality Control: Before the trucks leave the assembly line, suppliers typically conduct a final inspection to ensure that all specifications are met. This may include visual inspections, dimensional checks, and functional tests.
What Quality Control Standards Should B2B Buyers Be Aware Of?
Quality assurance (QA) is a critical aspect of the manufacturing process for classic custom trucks. Buyers should be familiar with both international and industry-specific standards to ensure they partner with reputable suppliers.
1. International Standards: What Certifications Should Suppliers Hold?
Many suppliers adhere to international quality standards such as ISO 9001, which outlines requirements for a quality management system. This certification ensures that suppliers maintain consistent quality in their processes.
Additionally, buyers should look for suppliers with certifications specific to the automotive industry, such as:
-
ISO/TS 16949: This standard focuses on the automotive sector’s quality management systems and is crucial for manufacturers of custom trucks.
-
CE Marking: For suppliers exporting to Europe, CE marking indicates compliance with health, safety, and environmental protection standards.
Understanding these certifications helps buyers assess the credibility and reliability of potential suppliers.
2. What Are the Key Quality Control Checkpoints?
Quality control checkpoints are essential to maintaining high standards throughout the manufacturing process. Common checkpoints include:
-
Incoming Quality Control (IQC): This step involves inspecting raw materials and components before they enter the manufacturing process. Buyers should request documentation of IQC results from suppliers.
-
In-Process Quality Control (IPQC): Conducted during the manufacturing process, IPQC helps identify defects early. Buyers can benefit from understanding how often these checks are performed and the criteria used.
-
Final Quality Control (FQC): Before trucks are shipped, FQC ensures that all specifications are met. Buyers should inquire about the specific tests conducted during this stage.
How Can B2B Buyers Verify Supplier Quality Control Practices?
Verifying a supplier’s quality control practices is essential for B2B buyers, especially when dealing with international suppliers. Here are some actionable steps:
1. Conducting Audits: What Should Buyers Look For?
Buyers should consider conducting on-site audits of potential suppliers. This process allows them to observe the manufacturing environment and QA processes firsthand. During the audit, buyers should evaluate:
-
Workforce Training: Ensure that employees are adequately trained in QA practices.
-
Equipment Maintenance: Check whether machinery is regularly maintained to uphold quality standards.
2. Requesting Quality Assurance Reports: What Information Should Be Included?
Suppliers should provide comprehensive QA reports that outline their testing methods, results, and compliance with standards. Buyers should look for:
-
Testing Methods: Details on the specific tests performed, such as tensile strength or fatigue testing.
-
Non-Conformance Reports: Information on any issues encountered and how they were resolved.
3. Engaging Third-Party Inspectors: How Can They Assist in Quality Verification?
Using third-party inspection services can provide an unbiased assessment of a supplier’s quality control practices. These inspectors can conduct various tests and audits, ensuring that suppliers adhere to both international and industry standards.
Conclusion: What Should Buyers Keep in Mind?
When sourcing classic custom trucks, understanding the manufacturing processes and quality assurance measures is vital for B2B buyers. By focusing on the main stages of manufacturing, relevant quality standards, and verification methods, buyers can make informed decisions and establish successful partnerships with suppliers from Africa, South America, the Middle East, and Europe.
Practical Sourcing Guide: A Step-by-Step Checklist for ‘classic trucks custom’
The following guide provides a structured approach for international B2B buyers looking to procure custom classic trucks. This step-by-step checklist will help you navigate the complexities of sourcing while ensuring you make informed decisions that meet your business needs.
Step 1: Define Your Technical Specifications
Before you start sourcing, it’s essential to have a clear understanding of your technical specifications. Determine the type of classic truck you need, including model, engine specifications, and any customization options. Being specific helps narrow down potential suppliers and ensures that the products meet your operational requirements.
- Considerations:
- What load capacity do you require?
- Are there specific aesthetic features you want (e.g., paint color, interior design)?
Step 2: Research the Market Landscape
Understanding the market landscape is crucial for identifying potential suppliers. Conduct thorough market research to uncover key players in the classic truck custom segment, focusing on suppliers from Africa, South America, the Middle East, and Europe. Look for industry reports and trade publications to gather insights into market trends and supplier reputations.
- Action Points:
- Compile a list of suppliers and their specialties.
- Investigate customer reviews and feedback on their services.
Step 3: Evaluate Potential Suppliers
Before committing to a supplier, it’s vital to vet them thoroughly. Request company profiles, case studies, and references from buyers in a similar industry or region. This evaluation will help you gauge their reliability and capability to meet your specific needs.
- Key Aspects to Review:
- Supplier history and experience in custom classic trucks.
- Examples of previous projects that align with your requirements.
Step 4: Verify Supplier Certifications
Ensure that the suppliers you are considering have the necessary certifications and compliance with local and international regulations. Certifications can serve as a quality assurance mechanism, confirming that the suppliers adhere to industry standards.
- Important Certifications:
- ISO certifications (e.g., ISO 9001 for quality management).
- Specific automotive industry certifications relevant to custom trucks.
Step 5: Request Detailed Quotations
Once you have shortlisted potential suppliers, request detailed quotations. This step should include breakdowns of costs, timelines, and customization options. A comprehensive quotation will help you compare offers effectively.
- What to Look For:
- Transparency in pricing, including hidden costs.
- Timeline for delivery and any potential delays.
Step 6: Conduct Factory Visits or Virtual Tours
If possible, conduct factory visits or request virtual tours to assess the supplier’s manufacturing capabilities. Observing their operations can provide insights into their production processes and quality control measures.
- Focus Areas:
- Equipment and technology used in manufacturing.
- Workforce expertise and management practices.
Step 7: Negotiate Terms and Finalize Contracts
After selecting your preferred supplier, enter negotiations to finalize the terms of your contract. Discuss payment terms, warranty provisions, and after-sales support. Clear and mutually beneficial agreements are essential for long-term relationships.
- Negotiation Tips:
- Be prepared to discuss your budget constraints.
- Ensure that all agreed-upon terms are documented clearly in the contract.
By following this checklist, B2B buyers can effectively navigate the sourcing process for custom classic trucks, ensuring that they make informed decisions that align with their business goals.
Comprehensive Cost and Pricing Analysis for classic trucks custom Sourcing
What Are the Key Cost Components in Classic Trucks Custom Sourcing?
When sourcing classic trucks, understanding the cost structure is vital for international B2B buyers. The primary cost components include:
-
Materials: The choice of materials directly impacts the overall cost. For classic trucks, using high-quality steel or aluminum can increase durability but may also raise expenses. Consider sourcing local materials to reduce costs and support regional economies.
-
Labor: Labor costs can vary significantly by region. In countries with a high standard of living, labor costs will typically be higher. However, sourcing from regions with lower labor costs can lead to substantial savings. It’s important to assess the skill level of the workforce and ensure that they are adept at handling classic truck restorations.
-
Manufacturing Overhead: This includes costs associated with running the production facility, such as utilities and equipment maintenance. Buyers should inquire about the supplier’s efficiency in managing overheads, as this can influence pricing.
-
Tooling: Customizations often require specialized tooling, which can be a significant upfront investment. Buyers should be aware that these costs can be amortized over larger production runs, making it advantageous to negotiate minimum order quantities (MOQs) for better pricing.
-
Quality Control (QC): A robust QC process is essential for ensuring that the trucks meet specified standards. Suppliers with rigorous QC processes may charge more, but this can prevent costly returns and ensure customer satisfaction in the long run.
-
Logistics: Shipping costs can greatly affect the total price, especially for international buyers. Consider factors such as shipping methods, distances, and tariffs when calculating logistics expenses. Utilizing Incoterms can help clarify responsibilities and costs between buyers and suppliers.
-
Margin: Suppliers will include their profit margin in the pricing structure. Understanding the typical margins within the classic truck market can help buyers gauge whether they are receiving competitive offers.
How Do Price Influencers Impact Custom Truck Sourcing?
Various factors influence the pricing of custom classic trucks:
-
Volume and Minimum Order Quantities (MOQ): Larger orders often lead to lower per-unit costs. Buyers should negotiate MOQs that balance their needs with cost savings.
-
Specifications and Customization: Highly customized trucks will typically command higher prices. Buyers should clearly define specifications to avoid misunderstandings that could lead to unexpected costs.
-
Material Choices: The selection of materials can greatly influence pricing. Buyers should evaluate the trade-off between cost and quality, especially for components that affect performance and longevity.
-
Quality Certifications: Trucks that meet international quality standards or certifications may carry a premium price tag. However, this can enhance resale value and reduce liability risks.
-
Supplier Factors: Supplier reputation and experience can affect pricing. Established suppliers may charge more due to their proven track record, but they may also offer superior quality and reliability.
-
Incoterms: Understanding Incoterms is crucial for international transactions. They define the responsibilities of buyers and sellers regarding shipping costs, insurance, and risk. Properly negotiated Incoterms can help avoid unexpected expenses.
What Tips Can Help Buyers Optimize Cost-Efficiency in Classic Truck Sourcing?
For international B2B buyers, particularly from Africa, South America, the Middle East, and Europe, the following tips can enhance cost-efficiency:
-
Negotiate Effectively: Leverage your purchasing power by negotiating with multiple suppliers. Be transparent about your requirements and budget, and seek competitive quotes.
-
Consider Total Cost of Ownership (TCO): Instead of focusing solely on upfront costs, consider the TCO, which includes maintenance, fuel efficiency, and resale value. A higher initial investment in quality may lead to lower long-term costs.
-
Understand Pricing Nuances: Different markets may have distinct pricing strategies influenced by local demand, competition, and economic conditions. Familiarize yourself with these nuances to make informed decisions.
-
Build Strong Relationships with Suppliers: Establishing a good rapport with suppliers can lead to better terms, priority service, and more favorable pricing over time.
-
Stay Informed About Market Trends: Regularly monitor market trends and pricing fluctuations to anticipate changes. This knowledge can empower you to make timely purchasing decisions.
Disclaimer on Pricing
The prices mentioned in this analysis are indicative and may vary based on specific project requirements, market conditions, and supplier negotiations. Buyers should conduct thorough research and obtain tailored quotes for accurate cost assessments.
Alternatives Analysis: Comparing classic trucks custom With Other Solutions
In the pursuit of efficient logistics and transportation solutions, businesses often evaluate various options to meet their specific needs. Classic trucks custom are a popular choice due to their unique designs and adaptability. However, exploring alternatives can provide valuable insights and potentially better align with operational goals. This section compares classic trucks custom with other viable solutions, enabling international B2B buyers to make informed decisions.
Comparison Aspect | Classic Trucks Custom | Electric Delivery Vans | Heavy-Duty Trailers |
---|---|---|---|
Performance | High durability and flexibility for various loads | Excellent for urban environments with zero emissions | Superior load capacity for long-distance transport |
Cost | Higher initial investment; potential for long-term ROI | Moderate initial cost; lower operational costs due to energy savings | Lower upfront cost; high maintenance expenses |
Ease of Implementation | Requires customization and skilled labor | Easier integration with existing logistics | Straightforward to implement, but requires compatible vehicles |
Maintenance | Regular upkeep needed; parts may be harder to source | Generally lower maintenance; fewer moving parts | High maintenance needs due to wear and tear on heavy components |
Best Use Case | Ideal for businesses needing a tailored solution for niche markets | Best for urban deliveries and environmentally conscious companies | Optimal for bulk transportation over long distances |
What Are the Benefits and Drawbacks of Electric Delivery Vans?
Electric delivery vans are gaining traction, particularly in urban settings where environmental regulations are becoming stricter. These vehicles offer zero emissions, making them an excellent choice for companies aiming to reduce their carbon footprint. The operational costs are generally lower due to savings on fuel and maintenance. However, they may come with a moderate initial investment and limited range compared to traditional trucks, which could affect logistics planning for businesses needing to cover extensive areas.
How Do Heavy-Duty Trailers Compare in Terms of Logistics Efficiency?
Heavy-duty trailers provide a robust solution for businesses focused on transporting large quantities of goods over long distances. They are typically more cost-effective upfront than custom trucks, making them appealing for companies looking to minimize initial expenditures. However, they do require compatible vehicles, and the maintenance costs can be significant due to the heavy wear on components. Companies in industries such as construction or agriculture often find heavy-duty trailers to be a perfect fit for their logistics needs.
How Should B2B Buyers Choose Between Classic Trucks Custom and Alternatives?
When selecting the right transportation solution, B2B buyers must consider several factors, including their specific operational requirements, budget constraints, and long-term goals. Classic trucks custom may be the ideal choice for businesses needing tailored vehicles that can handle diverse loads and unique challenges. In contrast, electric delivery vans may suit companies focused on sustainability and urban delivery efficiency, while heavy-duty trailers can benefit businesses requiring high-capacity transport. Ultimately, aligning the choice with operational needs will lead to optimal performance and cost-effectiveness in logistics operations.
Essential Technical Properties and Trade Terminology for classic trucks custom
What Are the Key Technical Properties of Classic Trucks Custom?
When evaluating classic trucks for custom projects, several technical specifications are critical to ensure quality, durability, and performance. Understanding these properties can significantly impact the decision-making process for international B2B buyers.
1. Material Grade: Why Is It Important?
The material grade refers to the quality and type of materials used in the truck’s construction, such as steel or aluminum. Higher-grade materials offer better strength, corrosion resistance, and longevity, which are essential for trucks that may face varying environmental conditions. Buyers should prioritize trucks made from high-grade materials to reduce maintenance costs and extend the vehicle’s lifespan.
2. Tolerance Levels: How Do They Affect Performance?
Tolerance levels indicate the permissible limits of variation in dimensions and physical properties of components. For classic trucks, precise tolerances are vital for parts like the engine, chassis, and suspension systems. High tolerance levels ensure optimal fit and function, reducing the risk of mechanical failure. B2B buyers should seek manufacturers who adhere to stringent tolerance standards to guarantee performance and safety.
3. Weight Capacity: What Should Buyers Consider?
Weight capacity is a critical specification that defines how much load a truck can safely carry. This property is essential for businesses that plan to use classic trucks for transportation or logistics. Understanding the weight capacity helps buyers select vehicles that meet their operational requirements while ensuring compliance with local regulations regarding vehicle loads.
4. Engine Specifications: What Do They Include?
Engine specifications encompass details such as horsepower, torque, and fuel efficiency. These factors are crucial for determining the truck’s performance, especially for buyers in industries requiring heavy hauling or long-distance transportation. A well-defined engine specification not only impacts operational efficiency but also influences fuel costs and overall profitability.
5. Suspension System: Why Is It Critical for Custom Trucks?
The suspension system affects ride quality, load handling, and overall stability. For classic trucks, a robust suspension design is essential to accommodate varying loads and road conditions. Buyers should consider the type of suspension—whether it is leaf spring, coil spring, or air suspension—as it directly impacts the vehicle’s performance and comfort.
What Are Common Trade Terms in the Classic Truck Custom Industry?
Familiarity with industry jargon is crucial for effective communication and negotiation in the B2B landscape. Here are some common terms that buyers should know:
1. OEM (Original Equipment Manufacturer): What Does It Mean?
OEM refers to the company that manufactures the original parts used in a vehicle. When purchasing classic trucks, buyers may encounter OEM components as they seek authenticity and reliability. Understanding OEM terminology helps buyers distinguish between original parts and aftermarket alternatives, impacting vehicle performance and resale value.
2. MOQ (Minimum Order Quantity): How Does It Affect Purchases?
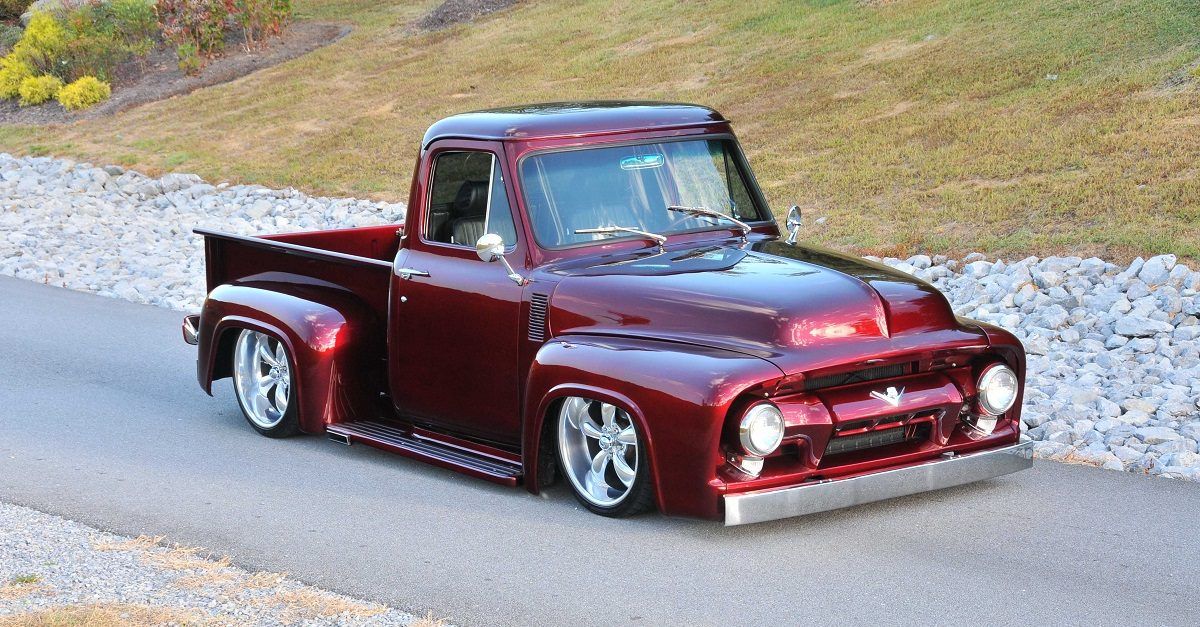
A stock image related to classic trucks custom.
MOQ denotes the smallest quantity of a product that a supplier is willing to sell. In the classic truck market, MOQs can influence purchasing decisions, especially for international buyers who may require a specific number of vehicles or parts. Knowing the MOQ helps in budgeting and planning inventory, ensuring that businesses can meet their operational needs without overcommitting resources.
3. RFQ (Request for Quotation): What Is Its Purpose?
An RFQ is a document sent to suppliers requesting pricing and availability for specific products or services. For B2B buyers, issuing an RFQ is a strategic way to gather competitive bids and make informed purchasing decisions. Crafting a clear and detailed RFQ can lead to better pricing and terms, enhancing the overall procurement process.
4. Incoterms: Why Are They Essential for International Trade?
Incoterms, or International Commercial Terms, define the responsibilities of buyers and sellers in international transactions. They outline who is responsible for shipping, insurance, and tariffs, which is crucial for cross-border trade involving classic trucks. Familiarity with Incoterms helps buyers avoid misunderstandings and negotiate better shipping terms, ensuring smoother transactions.
By understanding these technical properties and trade terminologies, international B2B buyers can make informed decisions that align with their operational needs and strategic goals in the classic trucks custom market.
Navigating Market Dynamics and Sourcing Trends in the classic trucks custom Sector
What Are the Key Trends Influencing the Classic Trucks Custom Market?
The classic trucks custom market is experiencing significant growth, driven by several global factors. The resurgence of interest in vintage vehicles, combined with a growing community of enthusiasts, is fostering a vibrant market for custom classic trucks. Additionally, the rise of e-commerce platforms has made it easier for international buyers from regions like Africa, South America, the Middle East, and Europe to access specialized parts and customization services. Digitalization in B2B processes, including the use of AI and big data, is enabling suppliers to better understand customer preferences and streamline sourcing strategies.
Emerging technologies are also reshaping the landscape of the classic trucks custom sector. For instance, 3D printing and advanced manufacturing techniques are allowing for the creation of bespoke parts that cater to specific customer needs. International buyers should be aware of these technological advancements, as they can enhance product quality and reduce lead times. Moreover, the growing trend of personalization is influencing purchasing decisions, encouraging buyers to seek unique features that reflect their individual styles.
How Can Sustainability and Ethical Sourcing Shape Your B2B Strategy?
Sustainability is becoming increasingly important in the classic trucks custom sector, particularly as consumers and businesses alike are more aware of environmental impacts. The sourcing of materials and components that are sustainable and ethically produced is not just a trend but a necessity for B2B buyers. This shift is particularly relevant for buyers from regions like Europe, where regulations and consumer expectations around sustainability are stringent.
Ethical supply chains are integral to ensuring that materials used in classic truck customization are sourced responsibly. B2B buyers should prioritize suppliers who hold certifications such as ISO 14001 for environmental management or those that utilize recycled materials. This not only enhances brand reputation but also aligns with the growing demand for transparency in sourcing practices. As a result, businesses that adopt sustainable practices can differentiate themselves in a competitive market, appealing to a customer base that values corporate responsibility.
What Is the Historical Context Behind the Classic Trucks Custom Sector?
The classic trucks custom sector has evolved significantly over the decades, influenced by cultural shifts and technological advancements. Initially, the customization of trucks was a niche market, primarily driven by hobbyists and collectors in the United States. However, as global interest in classic vehicles surged, particularly in regions like Europe and South America, the market expanded.
The 1990s marked a turning point with the rise of automotive shows and online communities that celebrated classic trucks. This cultural phenomenon not only fostered a sense of community among enthusiasts but also created opportunities for businesses to offer customized solutions. Today, the classic trucks custom sector is a thriving market, blending nostalgia with innovation, and offering international B2B buyers a unique opportunity to tap into a diverse and passionate customer base.
Frequently Asked Questions (FAQs) for B2B Buyers of classic trucks custom
-
How do I ensure the quality of classic trucks custom before purchasing?
To ensure quality, start by thoroughly vetting potential suppliers. Request samples or previous work examples, and check for certifications relevant to your region. Engage in direct conversations to discuss quality control processes and standards. Additionally, consider visiting the manufacturing facility if possible or hiring a third-party inspection service to assess the trucks before shipment. This proactive approach helps mitigate risks associated with quality discrepancies. -
What are the best customization options available for classic trucks?
Customization options for classic trucks can vary widely, but popular modifications include engine upgrades, suspension enhancements, and aesthetic changes like paint jobs and interior fittings. Determine your specific needs based on your market requirements or personal preferences. Collaborate closely with suppliers who specialize in custom builds to explore unique options that align with your vision, ensuring they have the capability and experience to deliver your desired modifications. -
What is the minimum order quantity (MOQ) for classic trucks custom?
Minimum order quantities for classic trucks can vary depending on the supplier and the complexity of the customization. Generally, MOQs may range from a single unit to several trucks. It’s essential to communicate your needs upfront and negotiate terms with suppliers. Some manufacturers may offer lower MOQs for first-time buyers or promotional deals, so exploring multiple suppliers can yield better options tailored to your purchasing power. -
What payment terms should I expect when sourcing classic trucks custom?
Payment terms can differ significantly among suppliers. Typically, expect to pay a deposit upfront (often 30-50%) with the balance due upon completion or prior to shipping. Some suppliers might offer financing options or extended payment terms for larger orders. Always negotiate terms that suit your cash flow while ensuring the supplier is reputable. Clear communication about payment milestones can help prevent misunderstandings later in the transaction. -
How do I find reliable suppliers for classic trucks custom internationally?
Finding reliable suppliers involves extensive research and due diligence. Utilize platforms like Alibaba, Global Sources, or industry-specific trade shows to identify potential vendors. Look for reviews, ratings, and case studies that highlight their expertise in classic truck customization. Engage with suppliers directly to assess their responsiveness and willingness to meet your needs. Additionally, consider seeking recommendations from industry peers or trade associations for trusted contacts. -
What are the logistics considerations when importing classic trucks custom?
Logistics is critical when importing classic trucks. Start by understanding the shipping methods available, such as container shipping or roll-on/roll-off (RoRo). Consider customs regulations in your country regarding vehicle imports, including taxes and duties. Work with experienced freight forwarders who can handle the complexities of international transport and ensure compliance with all legal requirements. Planning for potential delays can also help streamline the process. -
How can I evaluate the supplier’s customization capabilities for classic trucks?
To evaluate a supplier’s customization capabilities, ask for a portfolio showcasing previous projects, focusing on similar specifications to your requirements. Inquire about their design and engineering processes, materials used, and technology they employ in customization. Request references from past clients who had similar customizations completed. This assessment will provide insight into the supplier’s experience and ability to meet your quality and design expectations. -
What are the common challenges faced in international trade of classic trucks custom?
International trade of classic trucks custom can present challenges such as fluctuating tariffs, varying compliance standards, and logistical issues like shipping delays. Cultural differences may also affect communication and business practices. To mitigate these challenges, stay informed about international trade regulations, establish clear communication with suppliers, and consider engaging local legal counsel to navigate the complexities. Building strong relationships with reliable partners can also help overcome potential hurdles effectively.
Important Disclaimer & Terms of Use
⚠️ Important Disclaimer
The information provided in this guide, including content regarding manufacturers, technical specifications, and market analysis, is for informational and educational purposes only. It does not constitute professional procurement advice, financial advice, or legal advice.
While we have made every effort to ensure the accuracy and timeliness of the information, we are not responsible for any errors, omissions, or outdated information. Market conditions, company details, and technical standards are subject to change.
B2B buyers must conduct their own independent and thorough due diligence before making any purchasing decisions. This includes contacting suppliers directly, verifying certifications, requesting samples, and seeking professional consultation. The risk of relying on any information in this guide is borne solely by the reader.
Strategic Sourcing Conclusion and Outlook for classic trucks custom
What are the Key Takeaways for Strategic Sourcing in Classic Trucks Custom?
In the evolving landscape of classic trucks custom, strategic sourcing stands as a pivotal approach for international B2B buyers. By establishing strong partnerships with reliable suppliers, businesses can enhance their procurement processes, ensuring quality and reducing costs. Buyers from Africa, South America, the Middle East, and Europe should prioritize suppliers who not only understand the unique demands of classic trucks but also demonstrate a commitment to innovation and sustainability.
How Can International Buyers Leverage Strategic Sourcing?
Emphasizing local sourcing where possible can yield significant advantages, such as reduced lead times and lower shipping costs. Additionally, leveraging technology—like data analytics and supply chain management tools—can streamline operations and improve decision-making. For buyers in regions like Indonesia and France, understanding local market trends and regulatory requirements is crucial in making informed sourcing decisions.
What is the Future Outlook for Classic Trucks Custom?
As the market for classic trucks custom continues to expand, the focus on sustainability and electrification will likely shape future procurement strategies. Buyers are encouraged to stay ahead by embracing these trends and considering suppliers who innovate in these areas. By fostering strong relationships and being adaptable to changing market dynamics, international B2B buyers can position themselves for success.
Engage actively in your sourcing journey—explore new suppliers, invest in technology, and stay informed about industry shifts. The future of classic trucks custom is promising, and the right strategic sourcing approach can unlock tremendous value for your business.